service indicator JEEP GRAND CHEROKEE 2003 WJ / 2.G Repair Manual
[x] Cancel search | Manufacturer: JEEP, Model Year: 2003, Model line: GRAND CHEROKEE, Model: JEEP GRAND CHEROKEE 2003 WJ / 2.GPages: 2199, PDF Size: 76.01 MB
Page 580 of 2199
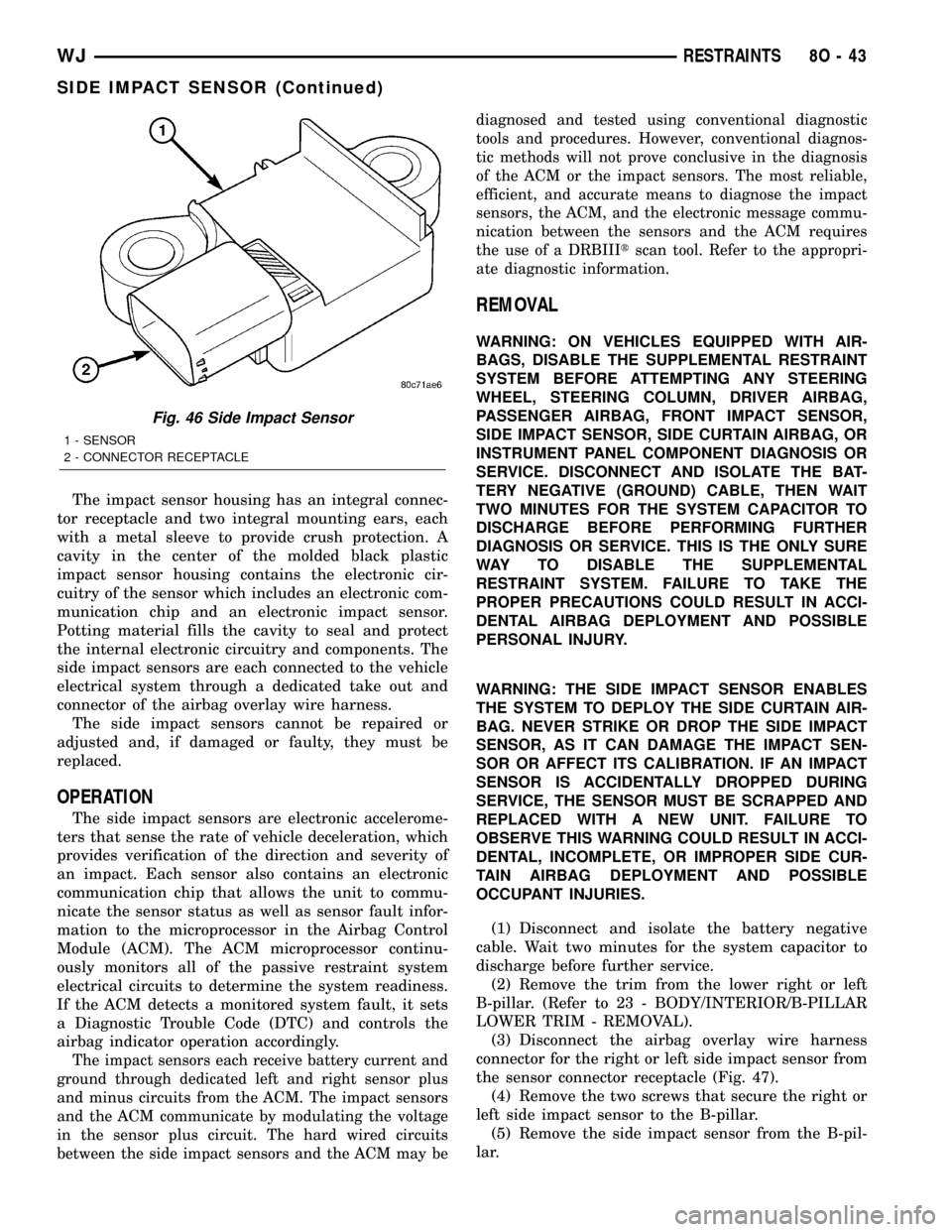
The impact sensor housing has an integral connec-
tor receptacle and two integral mounting ears, each
with a metal sleeve to provide crush protection. A
cavity in the center of the molded black plastic
impact sensor housing contains the electronic cir-
cuitry of the sensor which includes an electronic com-
munication chip and an electronic impact sensor.
Potting material fills the cavity to seal and protect
the internal electronic circuitry and components. The
side impact sensors are each connected to the vehicle
electrical system through a dedicated take out and
connector of the airbag overlay wire harness.
The side impact sensors cannot be repaired or
adjusted and, if damaged or faulty, they must be
replaced.
OPERATION
The side impact sensors are electronic accelerome-
ters that sense the rate of vehicle deceleration, which
provides verification of the direction and severity of
an impact. Each sensor also contains an electronic
communication chip that allows the unit to commu-
nicate the sensor status as well as sensor fault infor-
mation to the microprocessor in the Airbag Control
Module (ACM). The ACM microprocessor continu-
ously monitors all of the passive restraint system
electrical circuits to determine the system readiness.
If the ACM detects a monitored system fault, it sets
a Diagnostic Trouble Code (DTC) and controls the
airbag indicator operation accordingly.
The impact sensors each receive battery current and
ground through dedicated left and right sensor plus
and minus circuits from the ACM. The impact sensors
and the ACM communicate by modulating the voltage
in the sensor plus circuit. The hard wired circuits
between the side impact sensors and the ACM may bediagnosed and tested using conventional diagnostic
tools and procedures. However, conventional diagnos-
tic methods will not prove conclusive in the diagnosis
of the ACM or the impact sensors. The most reliable,
efficient, and accurate means to diagnose the impact
sensors, the ACM, and the electronic message commu-
nication between the sensors and the ACM requires
the use of a DRBIIItscan tool. Refer to the appropri-
ate diagnostic information.
REMOVAL
WARNING: ON VEHICLES EQUIPPED WITH AIR-
BAGS, DISABLE THE SUPPLEMENTAL RESTRAINT
SYSTEM BEFORE ATTEMPTING ANY STEERING
WHEEL, STEERING COLUMN, DRIVER AIRBAG,
PASSENGER AIRBAG, FRONT IMPACT SENSOR,
SIDE IMPACT SENSOR, SIDE CURTAIN AIRBAG, OR
INSTRUMENT PANEL COMPONENT DIAGNOSIS OR
SERVICE. DISCONNECT AND ISOLATE THE BAT-
TERY NEGATIVE (GROUND) CABLE, THEN WAIT
TWO MINUTES FOR THE SYSTEM CAPACITOR TO
DISCHARGE BEFORE PERFORMING FURTHER
DIAGNOSIS OR SERVICE. THIS IS THE ONLY SURE
WAY TO DISABLE THE SUPPLEMENTAL
RESTRAINT SYSTEM. FAILURE TO TAKE THE
PROPER PRECAUTIONS COULD RESULT IN ACCI-
DENTAL AIRBAG DEPLOYMENT AND POSSIBLE
PERSONAL INJURY.
WARNING: THE SIDE IMPACT SENSOR ENABLES
THE SYSTEM TO DEPLOY THE SIDE CURTAIN AIR-
BAG. NEVER STRIKE OR DROP THE SIDE IMPACT
SENSOR, AS IT CAN DAMAGE THE IMPACT SEN-
SOR OR AFFECT ITS CALIBRATION. IF AN IMPACT
SENSOR IS ACCIDENTALLY DROPPED DURING
SERVICE, THE SENSOR MUST BE SCRAPPED AND
REPLACED WITH A NEW UNIT. FAILURE TO
OBSERVE THIS WARNING COULD RESULT IN ACCI-
DENTAL, INCOMPLETE, OR IMPROPER SIDE CUR-
TAIN AIRBAG DEPLOYMENT AND POSSIBLE
OCCUPANT INJURIES.
(1) Disconnect and isolate the battery negative
cable. Wait two minutes for the system capacitor to
discharge before further service.
(2) Remove the trim from the lower right or left
B-pillar. (Refer to 23 - BODY/INTERIOR/B-PILLAR
LOWER TRIM - REMOVAL).
(3) Disconnect the airbag overlay wire harness
connector for the right or left side impact sensor from
the sensor connector receptacle (Fig. 47).
(4) Remove the two screws that secure the right or
left side impact sensor to the B-pillar.
(5) Remove the side impact sensor from the B-pil-
lar.
Fig. 46 Side Impact Sensor
1 - SENSOR
2 - CONNECTOR RECEPTACLE
WJRESTRAINTS 8O - 43
SIDE IMPACT SENSOR (Continued)
Page 592 of 2199
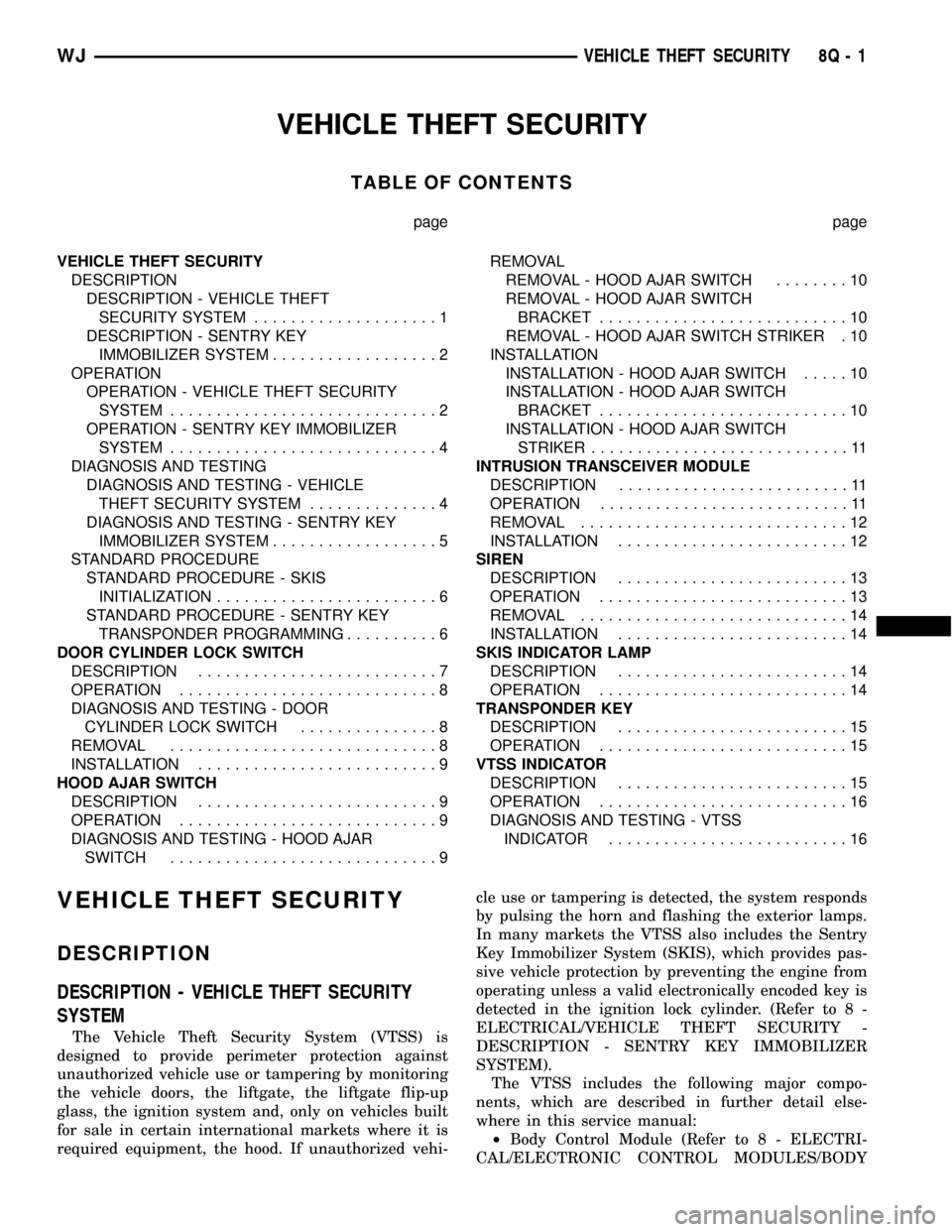
VEHICLE THEFT SECURITY
TABLE OF CONTENTS
page page
VEHICLE THEFT SECURITY
DESCRIPTION
DESCRIPTION - VEHICLE THEFT
SECURITY SYSTEM....................1
DESCRIPTION - SENTRY KEY
IMMOBILIZER SYSTEM..................2
OPERATION
OPERATION - VEHICLE THEFT SECURITY
SYSTEM.............................2
OPERATION - SENTRY KEY IMMOBILIZER
SYSTEM.............................4
DIAGNOSIS AND TESTING
DIAGNOSIS AND TESTING - VEHICLE
THEFT SECURITY SYSTEM..............4
DIAGNOSIS AND TESTING - SENTRY KEY
IMMOBILIZER SYSTEM..................5
STANDARD PROCEDURE
STANDARD PROCEDURE - SKIS
INITIALIZATION........................6
STANDARD PROCEDURE - SENTRY KEY
TRANSPONDER PROGRAMMING..........6
DOOR CYLINDER LOCK SWITCH
DESCRIPTION..........................7
OPERATION............................8
DIAGNOSIS AND TESTING - DOOR
CYLINDER LOCK SWITCH...............8
REMOVAL.............................8
INSTALLATION..........................9
HOOD AJAR SWITCH
DESCRIPTION..........................9
OPERATION............................9
DIAGNOSIS AND TESTING - HOOD AJAR
SWITCH.............................9REMOVAL
REMOVAL - HOOD AJAR SWITCH........10
REMOVAL - HOOD AJAR SWITCH
BRACKET...........................10
REMOVAL - HOOD AJAR SWITCH STRIKER . 10
INSTALLATION
INSTALLATION - HOOD AJAR SWITCH.....10
INSTALLATION - HOOD AJAR SWITCH
BRACKET...........................10
INSTALLATION - HOOD AJAR SWITCH
STRIKER............................11
INTRUSION TRANSCEIVER MODULE
DESCRIPTION.........................11
OPERATION...........................11
REMOVAL.............................12
INSTALLATION.........................12
SIREN
DESCRIPTION.........................13
OPERATION...........................13
REMOVAL.............................14
INSTALLATION.........................14
SKIS INDICATOR LAMP
DESCRIPTION.........................14
OPERATION...........................14
TRANSPONDER KEY
DESCRIPTION.........................15
OPERATION...........................15
VTSS INDICATOR
DESCRIPTION.........................15
OPERATION...........................16
DIAGNOSIS AND TESTING - VTSS
INDICATOR..........................16
VEHICLE THEFT SECURITY
DESCRIPTION
DESCRIPTION - VEHICLE THEFT SECURITY
SYSTEM
The Vehicle Theft Security System (VTSS) is
designed to provide perimeter protection against
unauthorized vehicle use or tampering by monitoring
the vehicle doors, the liftgate, the liftgate flip-up
glass, the ignition system and, only on vehicles built
for sale in certain international markets where it is
required equipment, the hood. If unauthorized vehi-cle use or tampering is detected, the system responds
by pulsing the horn and flashing the exterior lamps.
In many markets the VTSS also includes the Sentry
Key Immobilizer System (SKIS), which provides pas-
sive vehicle protection by preventing the engine from
operating unless a valid electronically encoded key is
detected in the ignition lock cylinder. (Refer to 8 -
ELECTRICAL/VEHICLE THEFT SECURITY -
DESCRIPTION - SENTRY KEY IMMOBILIZER
SYSTEM).
The VTSS includes the following major compo-
nents, which are described in further detail else-
where in this service manual:
²Body Control Module (Refer to 8 - ELECTRI-
CAL/ELECTRONIC CONTROL MODULES/BODY
WJVEHICLE THEFT SECURITY 8Q - 1
Page 593 of 2199
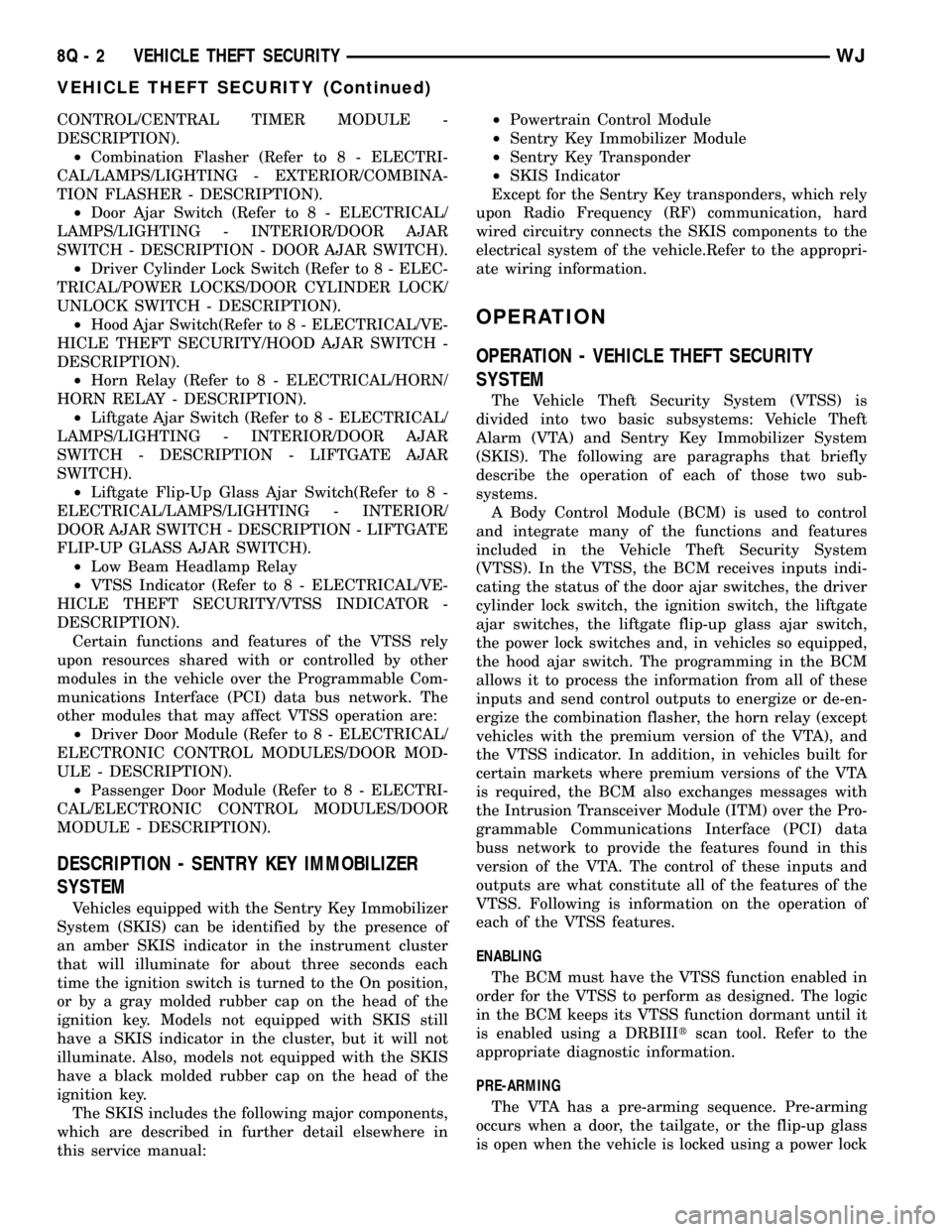
CONTROL/CENTRAL TIMER MODULE -
DESCRIPTION).
²Combination Flasher (Refer to 8 - ELECTRI-
CAL/LAMPS/LIGHTING - EXTERIOR/COMBINA-
TION FLASHER - DESCRIPTION).
²Door Ajar Switch (Refer to 8 - ELECTRICAL/
LAMPS/LIGHTING - INTERIOR/DOOR AJAR
SWITCH - DESCRIPTION - DOOR AJAR SWITCH).
²Driver Cylinder Lock Switch (Refer to 8 - ELEC-
TRICAL/POWER LOCKS/DOOR CYLINDER LOCK/
UNLOCK SWITCH - DESCRIPTION).
²Hood Ajar Switch(Refer to 8 - ELECTRICAL/VE-
HICLE THEFT SECURITY/HOOD AJAR SWITCH -
DESCRIPTION).
²Horn Relay (Refer to 8 - ELECTRICAL/HORN/
HORN RELAY - DESCRIPTION).
²Liftgate Ajar Switch (Refer to 8 - ELECTRICAL/
LAMPS/LIGHTING - INTERIOR/DOOR AJAR
SWITCH - DESCRIPTION - LIFTGATE AJAR
SWITCH).
²Liftgate Flip-Up Glass Ajar Switch(Refer to 8 -
ELECTRICAL/LAMPS/LIGHTING - INTERIOR/
DOOR AJAR SWITCH - DESCRIPTION - LIFTGATE
FLIP-UP GLASS AJAR SWITCH).
²Low Beam Headlamp Relay
²VTSS Indicator (Refer to 8 - ELECTRICAL/VE-
HICLE THEFT SECURITY/VTSS INDICATOR -
DESCRIPTION).
Certain functions and features of the VTSS rely
upon resources shared with or controlled by other
modules in the vehicle over the Programmable Com-
munications Interface (PCI) data bus network. The
other modules that may affect VTSS operation are:
²Driver Door Module (Refer to 8 - ELECTRICAL/
ELECTRONIC CONTROL MODULES/DOOR MOD-
ULE - DESCRIPTION).
²Passenger Door Module (Refer to 8 - ELECTRI-
CAL/ELECTRONIC CONTROL MODULES/DOOR
MODULE - DESCRIPTION).
DESCRIPTION - SENTRY KEY IMMOBILIZER
SYSTEM
Vehicles equipped with the Sentry Key Immobilizer
System (SKIS) can be identified by the presence of
an amber SKIS indicator in the instrument cluster
that will illuminate for about three seconds each
time the ignition switch is turned to the On position,
or by a gray molded rubber cap on the head of the
ignition key. Models not equipped with SKIS still
have a SKIS indicator in the cluster, but it will not
illuminate. Also, models not equipped with the SKIS
have a black molded rubber cap on the head of the
ignition key.
The SKIS includes the following major components,
which are described in further detail elsewhere in
this service manual:²Powertrain Control Module
²Sentry Key Immobilizer Module
²Sentry Key Transponder
²SKIS Indicator
Except for the Sentry Key transponders, which rely
upon Radio Frequency (RF) communication, hard
wired circuitry connects the SKIS components to the
electrical system of the vehicle.Refer to the appropri-
ate wiring information.
OPERATION
OPERATION - VEHICLE THEFT SECURITY
SYSTEM
The Vehicle Theft Security System (VTSS) is
divided into two basic subsystems: Vehicle Theft
Alarm (VTA) and Sentry Key Immobilizer System
(SKIS). The following are paragraphs that briefly
describe the operation of each of those two sub-
systems.
A Body Control Module (BCM) is used to control
and integrate many of the functions and features
included in the Vehicle Theft Security System
(VTSS). In the VTSS, the BCM receives inputs indi-
cating the status of the door ajar switches, the driver
cylinder lock switch, the ignition switch, the liftgate
ajar switches, the liftgate flip-up glass ajar switch,
the power lock switches and, in vehicles so equipped,
the hood ajar switch. The programming in the BCM
allows it to process the information from all of these
inputs and send control outputs to energize or de-en-
ergize the combination flasher, the horn relay (except
vehicles with the premium version of the VTA), and
the VTSS indicator. In addition, in vehicles built for
certain markets where premium versions of the VTA
is required, the BCM also exchanges messages with
the Intrusion Transceiver Module (ITM) over the Pro-
grammable Communications Interface (PCI) data
buss network to provide the features found in this
version of the VTA. The control of these inputs and
outputs are what constitute all of the features of the
VTSS. Following is information on the operation of
each of the VTSS features.
ENABLING
The BCM must have the VTSS function enabled in
order for the VTSS to perform as designed. The logic
in the BCM keeps its VTSS function dormant until it
is enabled using a DRBIIItscan tool. Refer to the
appropriate diagnostic information.
PRE-ARMING
The VTA has a pre-arming sequence. Pre-arming
occurs when a door, the tailgate, or the flip-up glass
is open when the vehicle is locked using a power lock
8Q - 2 VEHICLE THEFT SECURITYWJ
VEHICLE THEFT SECURITY (Continued)
Page 595 of 2199
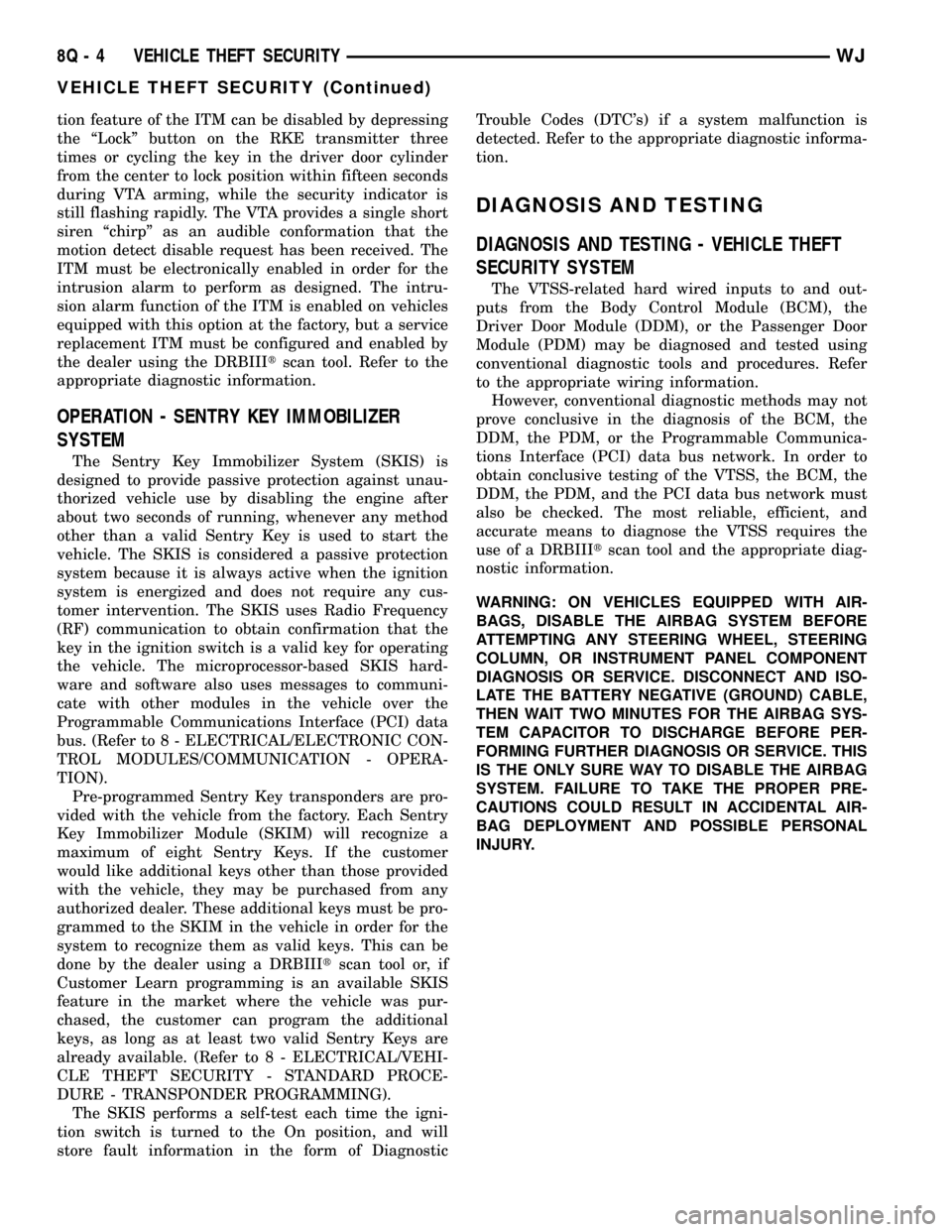
tion feature of the ITM can be disabled by depressing
the ªLockº button on the RKE transmitter three
times or cycling the key in the driver door cylinder
from the center to lock position within fifteen seconds
during VTA arming, while the security indicator is
still flashing rapidly. The VTA provides a single short
siren ªchirpº as an audible conformation that the
motion detect disable request has been received. The
ITM must be electronically enabled in order for the
intrusion alarm to perform as designed. The intru-
sion alarm function of the ITM is enabled on vehicles
equipped with this option at the factory, but a service
replacement ITM must be configured and enabled by
the dealer using the DRBIIItscan tool. Refer to the
appropriate diagnostic information.
OPERATION - SENTRY KEY IMMOBILIZER
SYSTEM
The Sentry Key Immobilizer System (SKIS) is
designed to provide passive protection against unau-
thorized vehicle use by disabling the engine after
about two seconds of running, whenever any method
other than a valid Sentry Key is used to start the
vehicle. The SKIS is considered a passive protection
system because it is always active when the ignition
system is energized and does not require any cus-
tomer intervention. The SKIS uses Radio Frequency
(RF) communication to obtain confirmation that the
key in the ignition switch is a valid key for operating
the vehicle. The microprocessor-based SKIS hard-
ware and software also uses messages to communi-
cate with other modules in the vehicle over the
Programmable Communications Interface (PCI) data
bus. (Refer to 8 - ELECTRICAL/ELECTRONIC CON-
TROL MODULES/COMMUNICATION - OPERA-
TION).
Pre-programmed Sentry Key transponders are pro-
vided with the vehicle from the factory. Each Sentry
Key Immobilizer Module (SKIM) will recognize a
maximum of eight Sentry Keys. If the customer
would like additional keys other than those provided
with the vehicle, they may be purchased from any
authorized dealer. These additional keys must be pro-
grammed to the SKIM in the vehicle in order for the
system to recognize them as valid keys. This can be
done by the dealer using a DRBIIItscan tool or, if
Customer Learn programming is an available SKIS
feature in the market where the vehicle was pur-
chased, the customer can program the additional
keys, as long as at least two valid Sentry Keys are
already available. (Refer to 8 - ELECTRICAL/VEHI-
CLE THEFT SECURITY - STANDARD PROCE-
DURE - TRANSPONDER PROGRAMMING).
The SKIS performs a self-test each time the igni-
tion switch is turned to the On position, and will
store fault information in the form of DiagnosticTrouble Codes (DTC's) if a system malfunction is
detected. Refer to the appropriate diagnostic informa-
tion.
DIAGNOSIS AND TESTING
DIAGNOSIS AND TESTING - VEHICLE THEFT
SECURITY SYSTEM
The VTSS-related hard wired inputs to and out-
puts from the Body Control Module (BCM), the
Driver Door Module (DDM), or the Passenger Door
Module (PDM) may be diagnosed and tested using
conventional diagnostic tools and procedures. Refer
to the appropriate wiring information.
However, conventional diagnostic methods may not
prove conclusive in the diagnosis of the BCM, the
DDM, the PDM, or the Programmable Communica-
tions Interface (PCI) data bus network. In order to
obtain conclusive testing of the VTSS, the BCM, the
DDM, the PDM, and the PCI data bus network must
also be checked. The most reliable, efficient, and
accurate means to diagnose the VTSS requires the
use of a DRBIIItscan tool and the appropriate diag-
nostic information.
WARNING: ON VEHICLES EQUIPPED WITH AIR-
BAGS, DISABLE THE AIRBAG SYSTEM BEFORE
ATTEMPTING ANY STEERING WHEEL, STEERING
COLUMN, OR INSTRUMENT PANEL COMPONENT
DIAGNOSIS OR SERVICE. DISCONNECT AND ISO-
LATE THE BATTERY NEGATIVE (GROUND) CABLE,
THEN WAIT TWO MINUTES FOR THE AIRBAG SYS-
TEM CAPACITOR TO DISCHARGE BEFORE PER-
FORMING FURTHER DIAGNOSIS OR SERVICE. THIS
IS THE ONLY SURE WAY TO DISABLE THE AIRBAG
SYSTEM. FAILURE TO TAKE THE PROPER PRE-
CAUTIONS COULD RESULT IN ACCIDENTAL AIR-
BAG DEPLOYMENT AND POSSIBLE PERSONAL
INJURY.
8Q - 4 VEHICLE THEFT SECURITYWJ
VEHICLE THEFT SECURITY (Continued)
Page 596 of 2199
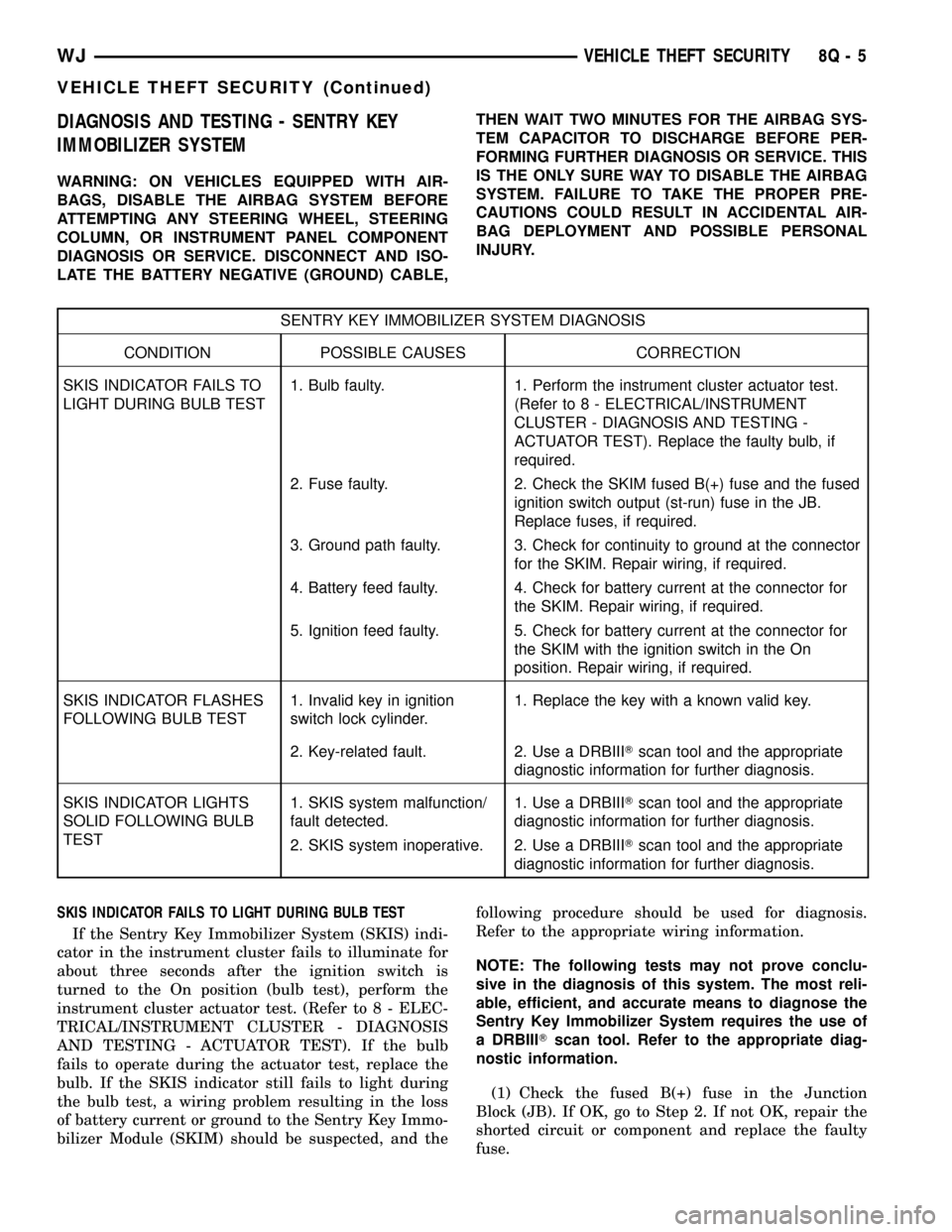
DIAGNOSIS AND TESTING - SENTRY KEY
IMMOBILIZER SYSTEM
WARNING: ON VEHICLES EQUIPPED WITH AIR-
BAGS, DISABLE THE AIRBAG SYSTEM BEFORE
ATTEMPTING ANY STEERING WHEEL, STEERING
COLUMN, OR INSTRUMENT PANEL COMPONENT
DIAGNOSIS OR SERVICE. DISCONNECT AND ISO-
LATE THE BATTERY NEGATIVE (GROUND) CABLE,THEN WAIT TWO MINUTES FOR THE AIRBAG SYS-
TEM CAPACITOR TO DISCHARGE BEFORE PER-
FORMING FURTHER DIAGNOSIS OR SERVICE. THIS
IS THE ONLY SURE WAY TO DISABLE THE AIRBAG
SYSTEM. FAILURE TO TAKE THE PROPER PRE-
CAUTIONS COULD RESULT IN ACCIDENTAL AIR-
BAG DEPLOYMENT AND POSSIBLE PERSONAL
INJURY.
SENTRY KEY IMMOBILIZER SYSTEM DIAGNOSIS
CONDITION POSSIBLE CAUSES CORRECTION
SKIS INDICATOR FAILS TO
LIGHT DURING BULB TEST1. Bulb faulty. 1. Perform the instrument cluster actuator test.
(Refer to 8 - ELECTRICAL/INSTRUMENT
CLUSTER - DIAGNOSIS AND TESTING -
ACTUATOR TEST). Replace the faulty bulb, if
required.
2. Fuse faulty. 2. Check the SKIM fused B(+) fuse and the fused
ignition switch output (st-run) fuse in the JB.
Replace fuses, if required.
3. Ground path faulty. 3. Check for continuity to ground at the connector
for the SKIM. Repair wiring, if required.
4. Battery feed faulty. 4. Check for battery current at the connector for
the SKIM. Repair wiring, if required.
5. Ignition feed faulty. 5. Check for battery current at the connector for
the SKIM with the ignition switch in the On
position. Repair wiring, if required.
SKIS INDICATOR FLASHES
FOLLOWING BULB TEST1. Invalid key in ignition
switch lock cylinder.1. Replace the key with a known valid key.
2. Key-related fault. 2. Use a DRBIIITscan tool and the appropriate
diagnostic information for further diagnosis.
SKIS INDICATOR LIGHTS
SOLID FOLLOWING BULB
TEST1. SKIS system malfunction/
fault detected.1. Use a DRBIIITscan tool and the appropriate
diagnostic information for further diagnosis.
2. SKIS system inoperative. 2. Use a DRBIIITscan tool and the appropriate
diagnostic information for further diagnosis.
SKIS INDICATOR FAILS TO LIGHT DURING BULB TEST
If the Sentry Key Immobilizer System (SKIS) indi-
cator in the instrument cluster fails to illuminate for
about three seconds after the ignition switch is
turned to the On position (bulb test), perform the
instrument cluster actuator test. (Refer to 8 - ELEC-
TRICAL/INSTRUMENT CLUSTER - DIAGNOSIS
AND TESTING - ACTUATOR TEST). If the bulb
fails to operate during the actuator test, replace the
bulb. If the SKIS indicator still fails to light during
the bulb test, a wiring problem resulting in the loss
of battery current or ground to the Sentry Key Immo-
bilizer Module (SKIM) should be suspected, and thefollowing procedure should be used for diagnosis.
Refer to the appropriate wiring information.
NOTE: The following tests may not prove conclu-
sive in the diagnosis of this system. The most reli-
able, efficient, and accurate means to diagnose the
Sentry Key Immobilizer System requires the use of
a DRBIIITscan tool. Refer to the appropriate diag-
nostic information.
(1) Check the fused B(+) fuse in the Junction
Block (JB). If OK, go to Step 2. If not OK, repair the
shorted circuit or component and replace the faulty
fuse.
WJVEHICLE THEFT SECURITY 8Q - 5
VEHICLE THEFT SECURITY (Continued)
Page 607 of 2199
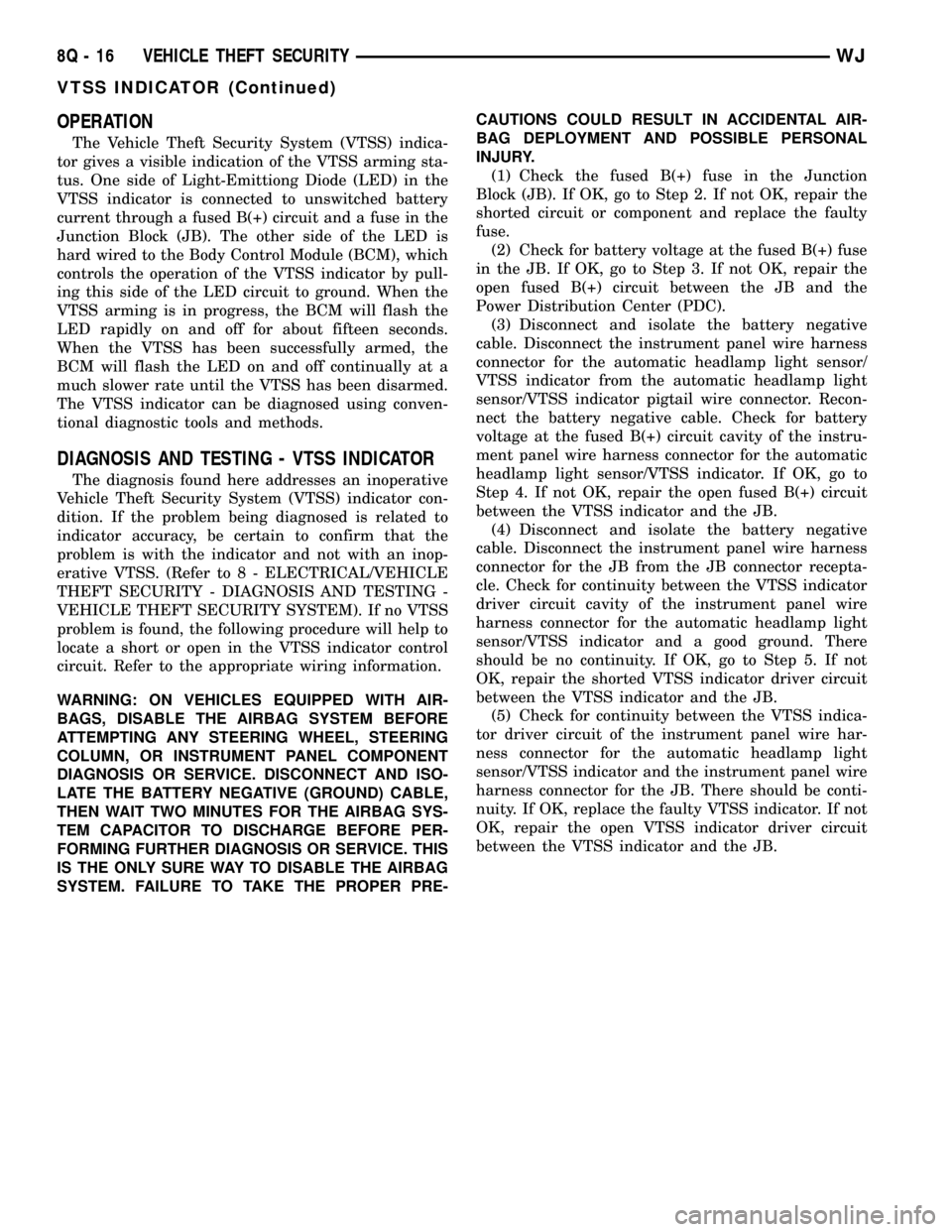
OPERATION
The Vehicle Theft Security System (VTSS) indica-
tor gives a visible indication of the VTSS arming sta-
tus. One side of Light-Emittiong Diode (LED) in the
VTSS indicator is connected to unswitched battery
current through a fused B(+) circuit and a fuse in the
Junction Block (JB). The other side of the LED is
hard wired to the Body Control Module (BCM), which
controls the operation of the VTSS indicator by pull-
ing this side of the LED circuit to ground. When the
VTSS arming is in progress, the BCM will flash the
LED rapidly on and off for about fifteen seconds.
When the VTSS has been successfully armed, the
BCM will flash the LED on and off continually at a
much slower rate until the VTSS has been disarmed.
The VTSS indicator can be diagnosed using conven-
tional diagnostic tools and methods.
DIAGNOSIS AND TESTING - VTSS INDICATOR
The diagnosis found here addresses an inoperative
Vehicle Theft Security System (VTSS) indicator con-
dition. If the problem being diagnosed is related to
indicator accuracy, be certain to confirm that the
problem is with the indicator and not with an inop-
erative VTSS. (Refer to 8 - ELECTRICAL/VEHICLE
THEFT SECURITY - DIAGNOSIS AND TESTING -
VEHICLE THEFT SECURITY SYSTEM). If no VTSS
problem is found, the following procedure will help to
locate a short or open in the VTSS indicator control
circuit. Refer to the appropriate wiring information.
WARNING: ON VEHICLES EQUIPPED WITH AIR-
BAGS, DISABLE THE AIRBAG SYSTEM BEFORE
ATTEMPTING ANY STEERING WHEEL, STEERING
COLUMN, OR INSTRUMENT PANEL COMPONENT
DIAGNOSIS OR SERVICE. DISCONNECT AND ISO-
LATE THE BATTERY NEGATIVE (GROUND) CABLE,
THEN WAIT TWO MINUTES FOR THE AIRBAG SYS-
TEM CAPACITOR TO DISCHARGE BEFORE PER-
FORMING FURTHER DIAGNOSIS OR SERVICE. THIS
IS THE ONLY SURE WAY TO DISABLE THE AIRBAG
SYSTEM. FAILURE TO TAKE THE PROPER PRE-CAUTIONS COULD RESULT IN ACCIDENTAL AIR-
BAG DEPLOYMENT AND POSSIBLE PERSONAL
INJURY.
(1) Check the fused B(+) fuse in the Junction
Block (JB). If OK, go to Step 2. If not OK, repair the
shorted circuit or component and replace the faulty
fuse.
(2) Check for battery voltage at the fused B(+) fuse
in the JB. If OK, go to Step 3. If not OK, repair the
open fused B(+) circuit between the JB and the
Power Distribution Center (PDC).
(3) Disconnect and isolate the battery negative
cable. Disconnect the instrument panel wire harness
connector for the automatic headlamp light sensor/
VTSS indicator from the automatic headlamp light
sensor/VTSS indicator pigtail wire connector. Recon-
nect the battery negative cable. Check for battery
voltage at the fused B(+) circuit cavity of the instru-
ment panel wire harness connector for the automatic
headlamp light sensor/VTSS indicator. If OK, go to
Step 4. If not OK, repair the open fused B(+) circuit
between the VTSS indicator and the JB.
(4) Disconnect and isolate the battery negative
cable. Disconnect the instrument panel wire harness
connector for the JB from the JB connector recepta-
cle. Check for continuity between the VTSS indicator
driver circuit cavity of the instrument panel wire
harness connector for the automatic headlamp light
sensor/VTSS indicator and a good ground. There
should be no continuity. If OK, go to Step 5. If not
OK, repair the shorted VTSS indicator driver circuit
between the VTSS indicator and the JB.
(5) Check for continuity between the VTSS indica-
tor driver circuit of the instrument panel wire har-
ness connector for the automatic headlamp light
sensor/VTSS indicator and the instrument panel wire
harness connector for the JB. There should be conti-
nuity. If OK, replace the faulty VTSS indicator. If not
OK, repair the open VTSS indicator driver circuit
between the VTSS indicator and the JB.
8Q - 16 VEHICLE THEFT SECURITYWJ
VTSS INDICATOR (Continued)
Page 632 of 2199
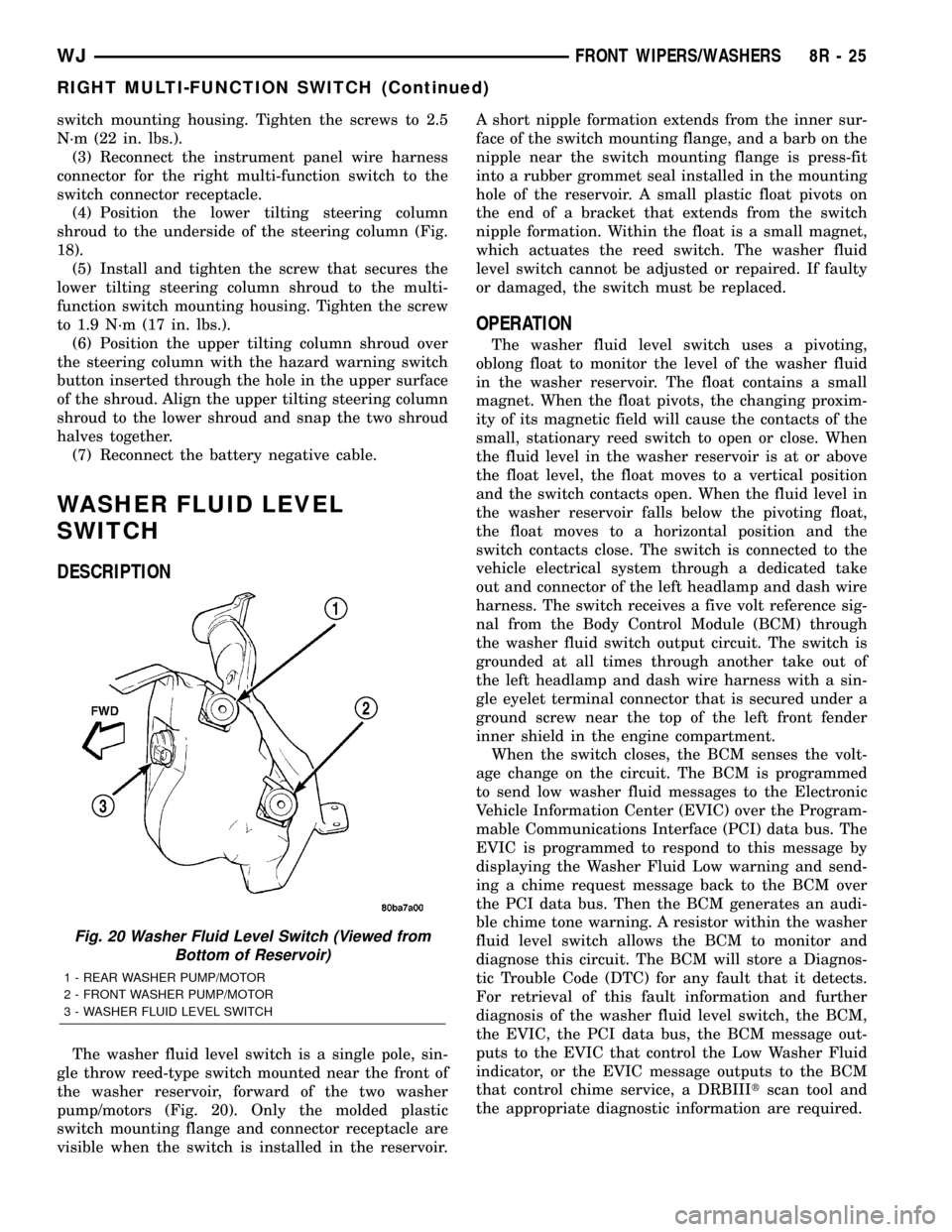
switch mounting housing. Tighten the screws to 2.5
N´m (22 in. lbs.).
(3) Reconnect the instrument panel wire harness
connector for the right multi-function switch to the
switch connector receptacle.
(4) Position the lower tilting steering column
shroud to the underside of the steering column (Fig.
18).
(5) Install and tighten the screw that secures the
lower tilting steering column shroud to the multi-
function switch mounting housing. Tighten the screw
to 1.9 N´m (17 in. lbs.).
(6) Position the upper tilting column shroud over
the steering column with the hazard warning switch
button inserted through the hole in the upper surface
of the shroud. Align the upper tilting steering column
shroud to the lower shroud and snap the two shroud
halves together.
(7) Reconnect the battery negative cable.
WASHER FLUID LEVEL
SWITCH
DESCRIPTION
The washer fluid level switch is a single pole, sin-
gle throw reed-type switch mounted near the front of
the washer reservoir, forward of the two washer
pump/motors (Fig. 20). Only the molded plastic
switch mounting flange and connector receptacle are
visible when the switch is installed in the reservoir.A short nipple formation extends from the inner sur-
face of the switch mounting flange, and a barb on the
nipple near the switch mounting flange is press-fit
into a rubber grommet seal installed in the mounting
hole of the reservoir. A small plastic float pivots on
the end of a bracket that extends from the switch
nipple formation. Within the float is a small magnet,
which actuates the reed switch. The washer fluid
level switch cannot be adjusted or repaired. If faulty
or damaged, the switch must be replaced.
OPERATION
The washer fluid level switch uses a pivoting,
oblong float to monitor the level of the washer fluid
in the washer reservoir. The float contains a small
magnet. When the float pivots, the changing proxim-
ity of its magnetic field will cause the contacts of the
small, stationary reed switch to open or close. When
the fluid level in the washer reservoir is at or above
the float level, the float moves to a vertical position
and the switch contacts open. When the fluid level in
the washer reservoir falls below the pivoting float,
the float moves to a horizontal position and the
switch contacts close. The switch is connected to the
vehicle electrical system through a dedicated take
out and connector of the left headlamp and dash wire
harness. The switch receives a five volt reference sig-
nal from the Body Control Module (BCM) through
the washer fluid switch output circuit. The switch is
grounded at all times through another take out of
the left headlamp and dash wire harness with a sin-
gle eyelet terminal connector that is secured under a
ground screw near the top of the left front fender
inner shield in the engine compartment.
When the switch closes, the BCM senses the volt-
age change on the circuit. The BCM is programmed
to send low washer fluid messages to the Electronic
Vehicle Information Center (EVIC) over the Program-
mable Communications Interface (PCI) data bus. The
EVIC is programmed to respond to this message by
displaying the Washer Fluid Low warning and send-
ing a chime request message back to the BCM over
the PCI data bus. Then the BCM generates an audi-
ble chime tone warning. A resistor within the washer
fluid level switch allows the BCM to monitor and
diagnose this circuit. The BCM will store a Diagnos-
tic Trouble Code (DTC) for any fault that it detects.
For retrieval of this fault information and further
diagnosis of the washer fluid level switch, the BCM,
the EVIC, the PCI data bus, the BCM message out-
puts to the EVIC that control the Low Washer Fluid
indicator, or the EVIC message outputs to the BCM
that control chime service, a DRBIIItscan tool and
the appropriate diagnostic information are required.
Fig. 20 Washer Fluid Level Switch (Viewed from
Bottom of Reservoir)
1 - REAR WASHER PUMP/MOTOR
2 - FRONT WASHER PUMP/MOTOR
3 - WASHER FLUID LEVEL SWITCH
WJFRONT WIPERS/WASHERS 8R - 25
RIGHT MULTI-FUNCTION SWITCH (Continued)
Page 1296 of 2199
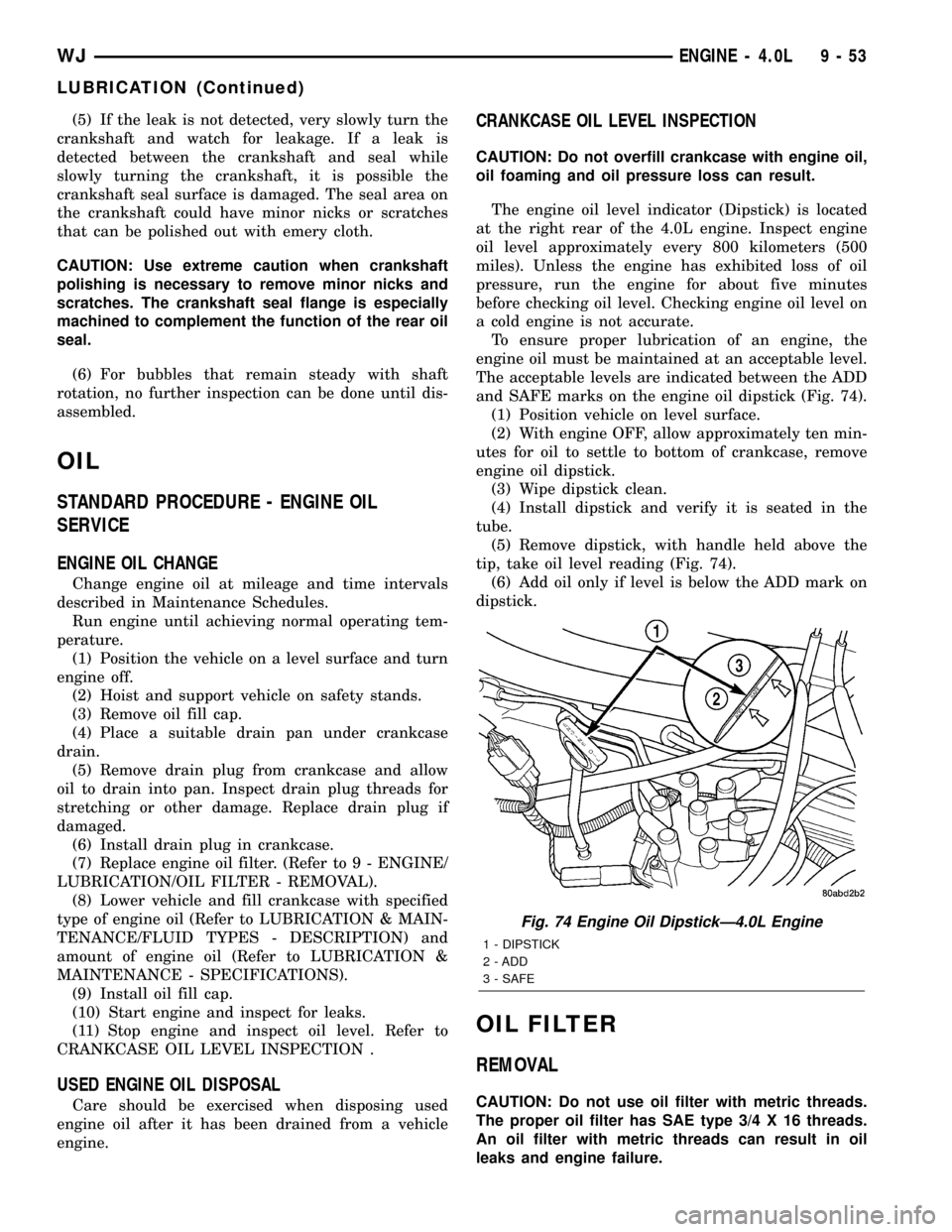
(5) If the leak is not detected, very slowly turn the
crankshaft and watch for leakage. If a leak is
detected between the crankshaft and seal while
slowly turning the crankshaft, it is possible the
crankshaft seal surface is damaged. The seal area on
the crankshaft could have minor nicks or scratches
that can be polished out with emery cloth.
CAUTION: Use extreme caution when crankshaft
polishing is necessary to remove minor nicks and
scratches. The crankshaft seal flange is especially
machined to complement the function of the rear oil
seal.
(6) For bubbles that remain steady with shaft
rotation, no further inspection can be done until dis-
assembled.
OIL
STANDARD PROCEDURE - ENGINE OIL
SERVICE
ENGINE OIL CHANGE
Change engine oil at mileage and time intervals
described in Maintenance Schedules.
Run engine until achieving normal operating tem-
perature.
(1) Position the vehicle on a level surface and turn
engine off.
(2) Hoist and support vehicle on safety stands.
(3) Remove oil fill cap.
(4) Place a suitable drain pan under crankcase
drain.
(5) Remove drain plug from crankcase and allow
oil to drain into pan. Inspect drain plug threads for
stretching or other damage. Replace drain plug if
damaged.
(6) Install drain plug in crankcase.
(7) Replace engine oil filter. (Refer to 9 - ENGINE/
LUBRICATION/OIL FILTER - REMOVAL).
(8) Lower vehicle and fill crankcase with specified
type of engine oil (Refer to LUBRICATION & MAIN-
TENANCE/FLUID TYPES - DESCRIPTION) and
amount of engine oil (Refer to LUBRICATION &
MAINTENANCE - SPECIFICATIONS).
(9) Install oil fill cap.
(10) Start engine and inspect for leaks.
(11) Stop engine and inspect oil level. Refer to
CRANKCASE OIL LEVEL INSPECTION .
USED ENGINE OIL DISPOSAL
Care should be exercised when disposing used
engine oil after it has been drained from a vehicle
engine.
CRANKCASE OIL LEVEL INSPECTION
CAUTION: Do not overfill crankcase with engine oil,
oil foaming and oil pressure loss can result.
The engine oil level indicator (Dipstick) is located
at the right rear of the 4.0L engine. Inspect engine
oil level approximately every 800 kilometers (500
miles). Unless the engine has exhibited loss of oil
pressure, run the engine for about five minutes
before checking oil level. Checking engine oil level on
a cold engine is not accurate.
To ensure proper lubrication of an engine, the
engine oil must be maintained at an acceptable level.
The acceptable levels are indicated between the ADD
and SAFE marks on the engine oil dipstick (Fig. 74).
(1) Position vehicle on level surface.
(2) With engine OFF, allow approximately ten min-
utes for oil to settle to bottom of crankcase, remove
engine oil dipstick.
(3) Wipe dipstick clean.
(4) Install dipstick and verify it is seated in the
tube.
(5) Remove dipstick, with handle held above the
tip, take oil level reading (Fig. 74).
(6) Add oil only if level is below the ADD mark on
dipstick.
OIL FILTER
REMOVAL
CAUTION: Do not use oil filter with metric threads.
The proper oil filter has SAE type 3/4 X 16 threads.
An oil filter with metric threads can result in oil
leaks and engine failure.
Fig. 74 Engine Oil DipstickÐ4.0L Engine
1 - DIPSTICK
2 - ADD
3 - SAFE
WJENGINE - 4.0L 9 - 53
LUBRICATION (Continued)
Page 1373 of 2199
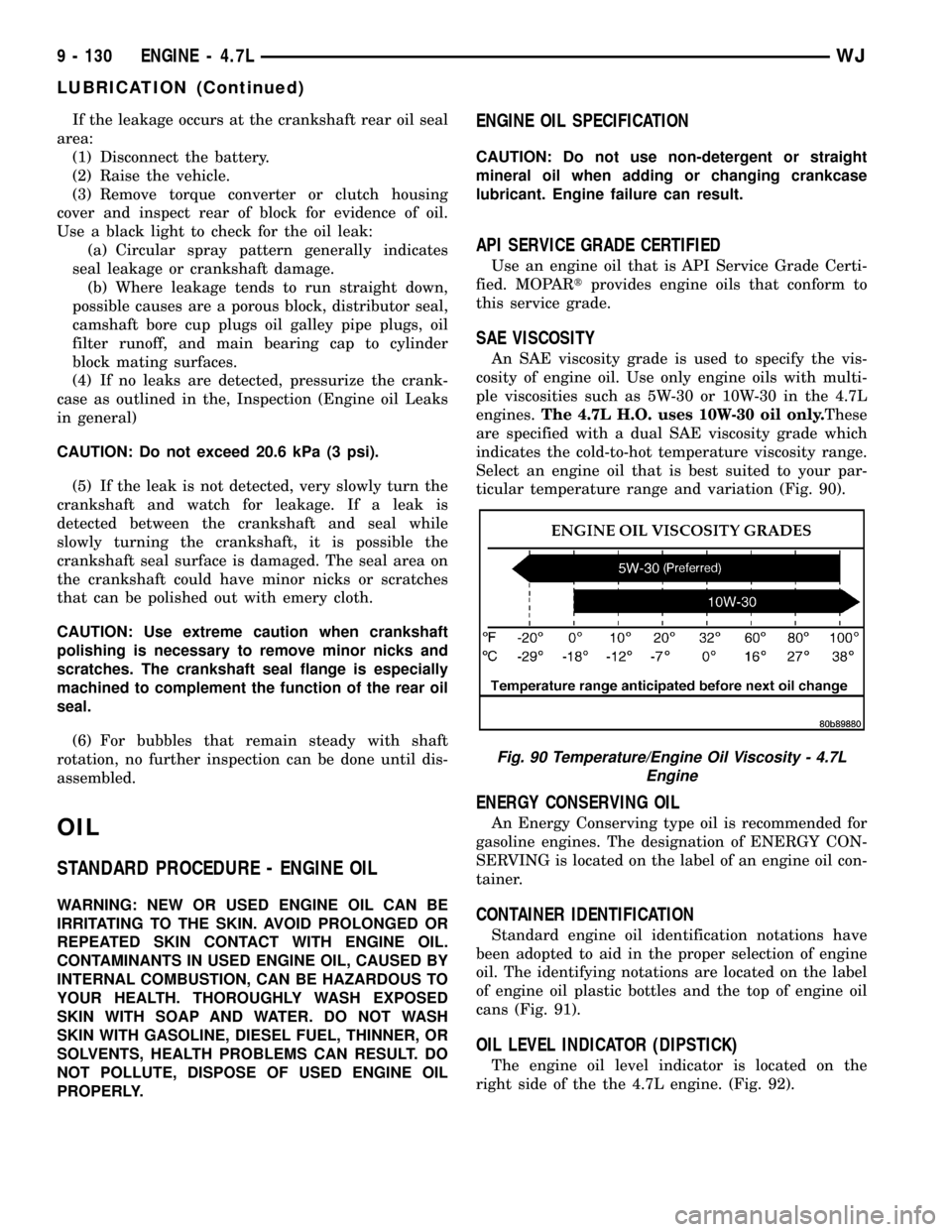
If the leakage occurs at the crankshaft rear oil seal
area:
(1) Disconnect the battery.
(2) Raise the vehicle.
(3) Remove torque converter or clutch housing
cover and inspect rear of block for evidence of oil.
Use a black light to check for the oil leak:
(a) Circular spray pattern generally indicates
seal leakage or crankshaft damage.
(b) Where leakage tends to run straight down,
possible causes are a porous block, distributor seal,
camshaft bore cup plugs oil galley pipe plugs, oil
filter runoff, and main bearing cap to cylinder
block mating surfaces.
(4) If no leaks are detected, pressurize the crank-
case as outlined in the, Inspection (Engine oil Leaks
in general)
CAUTION: Do not exceed 20.6 kPa (3 psi).
(5) If the leak is not detected, very slowly turn the
crankshaft and watch for leakage. If a leak is
detected between the crankshaft and seal while
slowly turning the crankshaft, it is possible the
crankshaft seal surface is damaged. The seal area on
the crankshaft could have minor nicks or scratches
that can be polished out with emery cloth.
CAUTION: Use extreme caution when crankshaft
polishing is necessary to remove minor nicks and
scratches. The crankshaft seal flange is especially
machined to complement the function of the rear oil
seal.
(6) For bubbles that remain steady with shaft
rotation, no further inspection can be done until dis-
assembled.
OIL
STANDARD PROCEDURE - ENGINE OIL
WARNING: NEW OR USED ENGINE OIL CAN BE
IRRITATING TO THE SKIN. AVOID PROLONGED OR
REPEATED SKIN CONTACT WITH ENGINE OIL.
CONTAMINANTS IN USED ENGINE OIL, CAUSED BY
INTERNAL COMBUSTION, CAN BE HAZARDOUS TO
YOUR HEALTH. THOROUGHLY WASH EXPOSED
SKIN WITH SOAP AND WATER. DO NOT WASH
SKIN WITH GASOLINE, DIESEL FUEL, THINNER, OR
SOLVENTS, HEALTH PROBLEMS CAN RESULT. DO
NOT POLLUTE, DISPOSE OF USED ENGINE OIL
PROPERLY.
ENGINE OIL SPECIFICATION
CAUTION: Do not use non-detergent or straight
mineral oil when adding or changing crankcase
lubricant. Engine failure can result.
API SERVICE GRADE CERTIFIED
Use an engine oil that is API Service Grade Certi-
fied. MOPARtprovides engine oils that conform to
this service grade.
SAE VISCOSITY
An SAE viscosity grade is used to specify the vis-
cosity of engine oil. Use only engine oils with multi-
ple viscosities such as 5W-30 or 10W-30 in the 4.7L
engines.The 4.7L H.O. uses 10W-30 oil only.These
are specified with a dual SAE viscosity grade which
indicates the cold-to-hot temperature viscosity range.
Select an engine oil that is best suited to your par-
ticular temperature range and variation (Fig. 90).
ENERGY CONSERVING OIL
An Energy Conserving type oil is recommended for
gasoline engines. The designation of ENERGY CON-
SERVING is located on the label of an engine oil con-
tainer.
CONTAINER IDENTIFICATION
Standard engine oil identification notations have
been adopted to aid in the proper selection of engine
oil. The identifying notations are located on the label
of engine oil plastic bottles and the top of engine oil
cans (Fig. 91).
OIL LEVEL INDICATOR (DIPSTICK)
The engine oil level indicator is located on the
right side of the the 4.7L engine. (Fig. 92).
Fig. 90 Temperature/Engine Oil Viscosity - 4.7L
Engine
9 - 130 ENGINE - 4.7LWJ
LUBRICATION (Continued)
Page 1861 of 2199
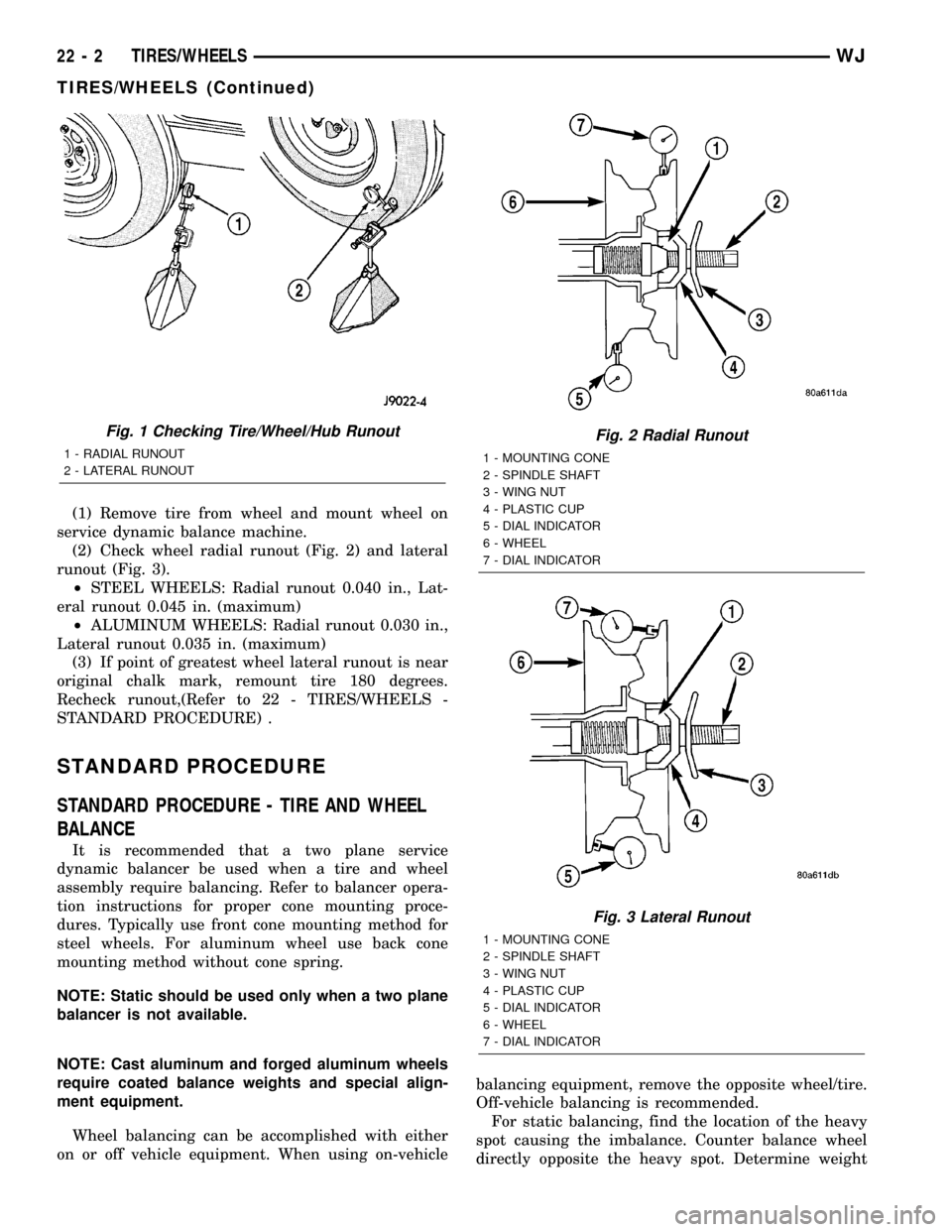
(1) Remove tire from wheel and mount wheel on
service dynamic balance machine.
(2) Check wheel radial runout (Fig. 2) and lateral
runout (Fig. 3).
²STEEL WHEELS: Radial runout 0.040 in., Lat-
eral runout 0.045 in. (maximum)
²ALUMINUM WHEELS: Radial runout 0.030 in.,
Lateral runout 0.035 in. (maximum)
(3) If point of greatest wheel lateral runout is near
original chalk mark, remount tire 180 degrees.
Recheck runout,(Refer to 22 - TIRES/WHEELS -
STANDARD PROCEDURE) .
STANDARD PROCEDURE
STANDARD PROCEDURE - TIRE AND WHEEL
BALANCE
It is recommended that a two plane service
dynamic balancer be used when a tire and wheel
assembly require balancing. Refer to balancer opera-
tion instructions for proper cone mounting proce-
dures. Typically use front cone mounting method for
steel wheels. For aluminum wheel use back cone
mounting method without cone spring.
NOTE: Static should be used only when a two plane
balancer is not available.
NOTE: Cast aluminum and forged aluminum wheels
require coated balance weights and special align-
ment equipment.
Wheel balancing can be accomplished with either
on or off vehicle equipment. When using on-vehiclebalancing equipment, remove the opposite wheel/tire.
Off-vehicle balancing is recommended.
For static balancing, find the location of the heavy
spot causing the imbalance. Counter balance wheel
directly opposite the heavy spot. Determine weight
Fig. 1 Checking Tire/Wheel/Hub Runout
1 - RADIAL RUNOUT
2 - LATERAL RUNOUT
Fig. 2 Radial Runout
1 - MOUNTING CONE
2 - SPINDLE SHAFT
3 - WING NUT
4 - PLASTIC CUP
5 - DIAL INDICATOR
6 - WHEEL
7 - DIAL INDICATOR
Fig. 3 Lateral Runout
1 - MOUNTING CONE
2 - SPINDLE SHAFT
3 - WING NUT
4 - PLASTIC CUP
5 - DIAL INDICATOR
6 - WHEEL
7 - DIAL INDICATOR
22 - 2 TIRES/WHEELSWJ
TIRES/WHEELS (Continued)