relay JEEP GRAND CHEROKEE 2003 WJ / 2.G Workshop Manual
[x] Cancel search | Manufacturer: JEEP, Model Year: 2003, Model line: GRAND CHEROKEE, Model: JEEP GRAND CHEROKEE 2003 WJ / 2.GPages: 2199, PDF Size: 76.01 MB
Page 226 of 2199
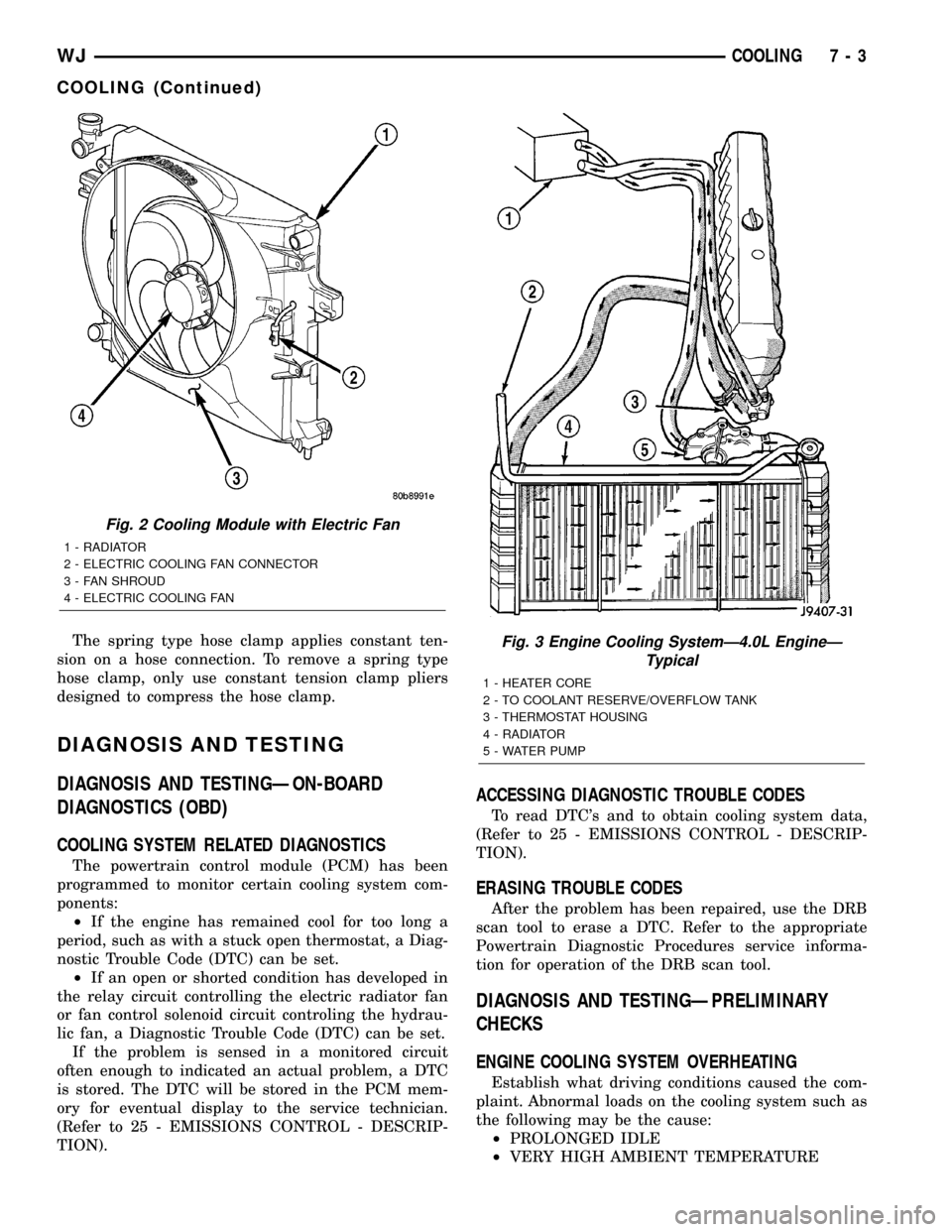
The spring type hose clamp applies constant ten-
sion on a hose connection. To remove a spring type
hose clamp, only use constant tension clamp pliers
designed to compress the hose clamp.
DIAGNOSIS AND TESTING
DIAGNOSIS AND TESTINGÐON-BOARD
DIAGNOSTICS (OBD)
COOLING SYSTEM RELATED DIAGNOSTICS
The powertrain control module (PCM) has been
programmed to monitor certain cooling system com-
ponents:
²If the engine has remained cool for too long a
period, such as with a stuck open thermostat, a Diag-
nostic Trouble Code (DTC) can be set.
²If an open or shorted condition has developed in
the relay circuit controlling the electric radiator fan
or fan control solenoid circuit controling the hydrau-
lic fan, a Diagnostic Trouble Code (DTC) can be set.
If the problem is sensed in a monitored circuit
often enough to indicated an actual problem, a DTC
is stored. The DTC will be stored in the PCM mem-
ory for eventual display to the service technician.
(Refer to 25 - EMISSIONS CONTROL - DESCRIP-
TION).
ACCESSING DIAGNOSTIC TROUBLE CODES
To read DTC's and to obtain cooling system data,
(Refer to 25 - EMISSIONS CONTROL - DESCRIP-
TION).
ERASING TROUBLE CODES
After the problem has been repaired, use the DRB
scan tool to erase a DTC. Refer to the appropriate
Powertrain Diagnostic Procedures service informa-
tion for operation of the DRB scan tool.
DIAGNOSIS AND TESTINGÐPRELIMINARY
CHECKS
ENGINE COOLING SYSTEM OVERHEATING
Establish what driving conditions caused the com-
plaint. Abnormal loads on the cooling system such as
the following may be the cause:
²PROLONGED IDLE
²VERY HIGH AMBIENT TEMPERATURE
Fig. 2 Cooling Module with Electric Fan
1 - RADIATOR
2 - ELECTRIC COOLING FAN CONNECTOR
3 - FAN SHROUD
4 - ELECTRIC COOLING FAN
Fig. 3 Engine Cooling SystemÐ4.0L EngineÐ
Typical
1 - HEATER CORE
2 - TO COOLANT RESERVE/OVERFLOW TANK
3 - THERMOSTAT HOUSING
4 - RADIATOR
5 - WATER PUMP
WJCOOLING 7 - 3
COOLING (Continued)
Page 258 of 2199
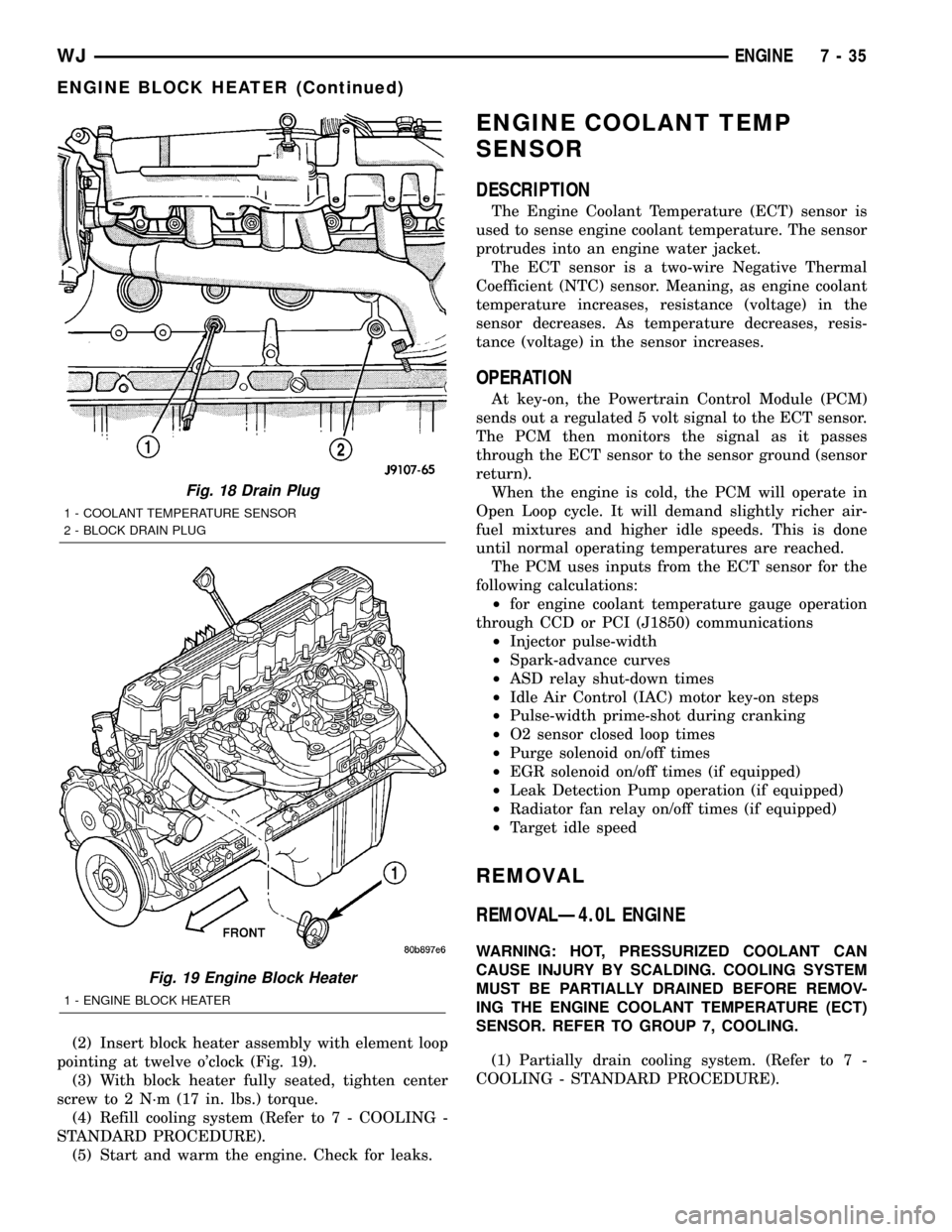
(2) Insert block heater assembly with element loop
pointing at twelve o'clock (Fig. 19).
(3) With block heater fully seated, tighten center
screw to 2 N´m (17 in. lbs.) torque.
(4) Refill cooling system (Refer to 7 - COOLING -
STANDARD PROCEDURE).
(5) Start and warm the engine. Check for leaks.
ENGINE COOLANT TEMP
SENSOR
DESCRIPTION
The Engine Coolant Temperature (ECT) sensor is
used to sense engine coolant temperature. The sensor
protrudes into an engine water jacket.
The ECT sensor is a two-wire Negative Thermal
Coefficient (NTC) sensor. Meaning, as engine coolant
temperature increases, resistance (voltage) in the
sensor decreases. As temperature decreases, resis-
tance (voltage) in the sensor increases.
OPERATION
At key-on, the Powertrain Control Module (PCM)
sends out a regulated 5 volt signal to the ECT sensor.
The PCM then monitors the signal as it passes
through the ECT sensor to the sensor ground (sensor
return).
When the engine is cold, the PCM will operate in
Open Loop cycle. It will demand slightly richer air-
fuel mixtures and higher idle speeds. This is done
until normal operating temperatures are reached.
The PCM uses inputs from the ECT sensor for the
following calculations:
²for engine coolant temperature gauge operation
through CCD or PCI (J1850) communications
²Injector pulse-width
²Spark-advance curves
²ASD relay shut-down times
²Idle Air Control (IAC) motor key-on steps
²Pulse-width prime-shot during cranking
²O2 sensor closed loop times
²Purge solenoid on/off times
²EGR solenoid on/off times (if equipped)
²Leak Detection Pump operation (if equipped)
²Radiator fan relay on/off times (if equipped)
²Target idle speed
REMOVAL
REMOVALÐ4.0L ENGINE
WARNING: HOT, PRESSURIZED COOLANT CAN
CAUSE INJURY BY SCALDING. COOLING SYSTEM
MUST BE PARTIALLY DRAINED BEFORE REMOV-
ING THE ENGINE COOLANT TEMPERATURE (ECT)
SENSOR. REFER TO GROUP 7, COOLING.
(1) Partially drain cooling system. (Refer to 7 -
COOLING - STANDARD PROCEDURE).
Fig. 18 Drain Plug
1 - COOLANT TEMPERATURE SENSOR
2 - BLOCK DRAIN PLUG
Fig. 19 Engine Block Heater
1 - ENGINE BLOCK HEATER
WJENGINE 7 - 35
ENGINE BLOCK HEATER (Continued)
Page 264 of 2199
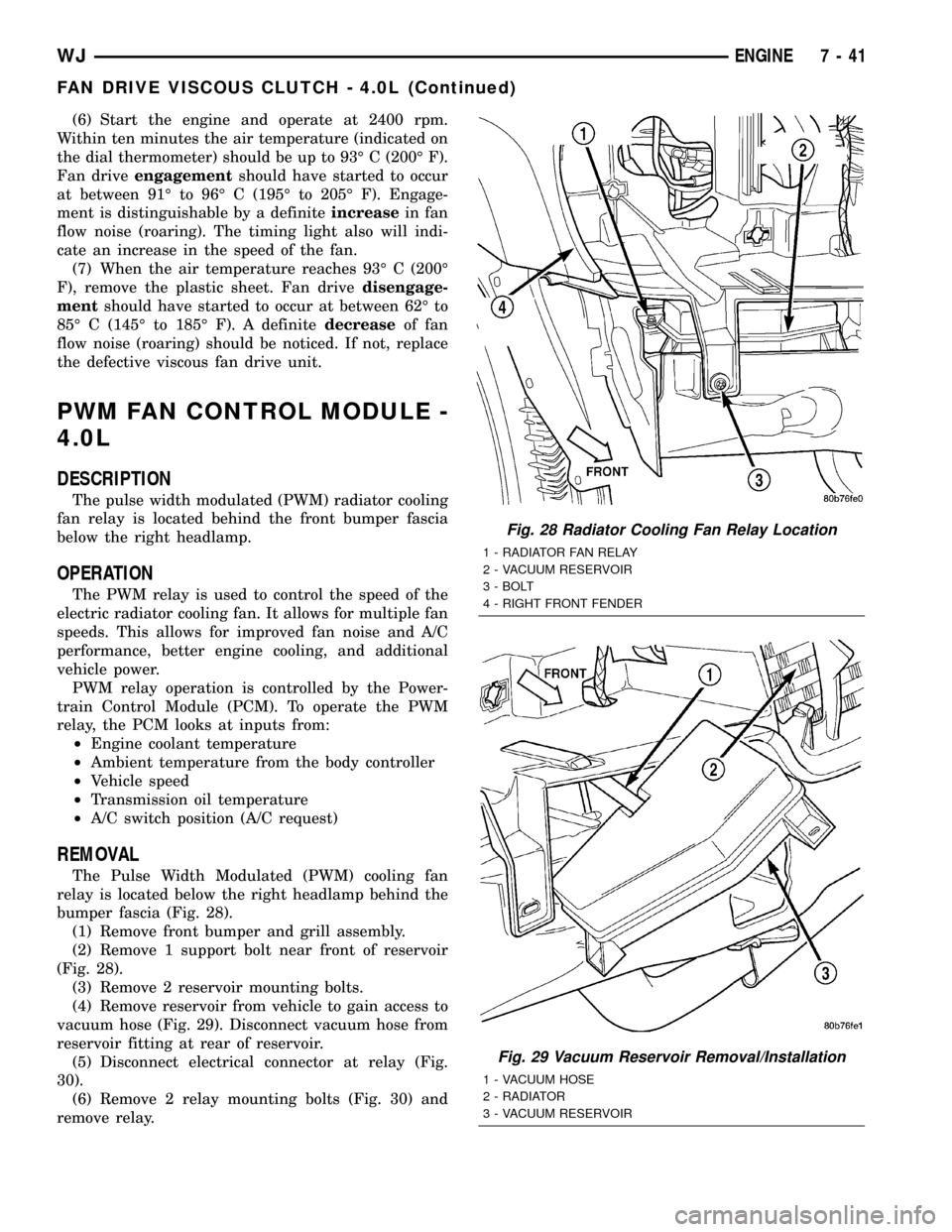
(6) Start the engine and operate at 2400 rpm.
Within ten minutes the air temperature (indicated on
the dial thermometer) should be up to 93É C (200É F).
Fan driveengagementshould have started to occur
at between 91É to 96É C (195É to 205É F). Engage-
ment is distinguishable by a definiteincreasein fan
flow noise (roaring). The timing light also will indi-
cate an increase in the speed of the fan.
(7) When the air temperature reaches 93É C (200É
F), remove the plastic sheet. Fan drivedisengage-
mentshould have started to occur at between 62É to
85É C (145É to 185É F). A definitedecreaseof fan
flow noise (roaring) should be noticed. If not, replace
the defective viscous fan drive unit.
PWM FAN CONTROL MODULE -
4.0L
DESCRIPTION
The pulse width modulated (PWM) radiator cooling
fan relay is located behind the front bumper fascia
below the right headlamp.
OPERATION
The PWM relay is used to control the speed of the
electric radiator cooling fan. It allows for multiple fan
speeds. This allows for improved fan noise and A/C
performance, better engine cooling, and additional
vehicle power.
PWM relay operation is controlled by the Power-
train Control Module (PCM). To operate the PWM
relay, the PCM looks at inputs from:
²Engine coolant temperature
²Ambient temperature from the body controller
²Vehicle speed
²Transmission oil temperature
²A/C switch position (A/C request)
REMOVAL
The Pulse Width Modulated (PWM) cooling fan
relay is located below the right headlamp behind the
bumper fascia (Fig. 28).
(1) Remove front bumper and grill assembly.
(2) Remove 1 support bolt near front of reservoir
(Fig. 28).
(3) Remove 2 reservoir mounting bolts.
(4) Remove reservoir from vehicle to gain access to
vacuum hose (Fig. 29). Disconnect vacuum hose from
reservoir fitting at rear of reservoir.
(5) Disconnect electrical connector at relay (Fig.
30).
(6) Remove 2 relay mounting bolts (Fig. 30) and
remove relay.
Fig. 28 Radiator Cooling Fan Relay Location
1 - RADIATOR FAN RELAY
2 - VACUUM RESERVOIR
3 - BOLT
4 - RIGHT FRONT FENDER
Fig. 29 Vacuum Reservoir Removal/Installation
1 - VACUUM HOSE
2 - RADIATOR
3 - VACUUM RESERVOIR
WJENGINE 7 - 41
FAN DRIVE VISCOUS CLUTCH - 4.0L (Continued)
Page 265 of 2199
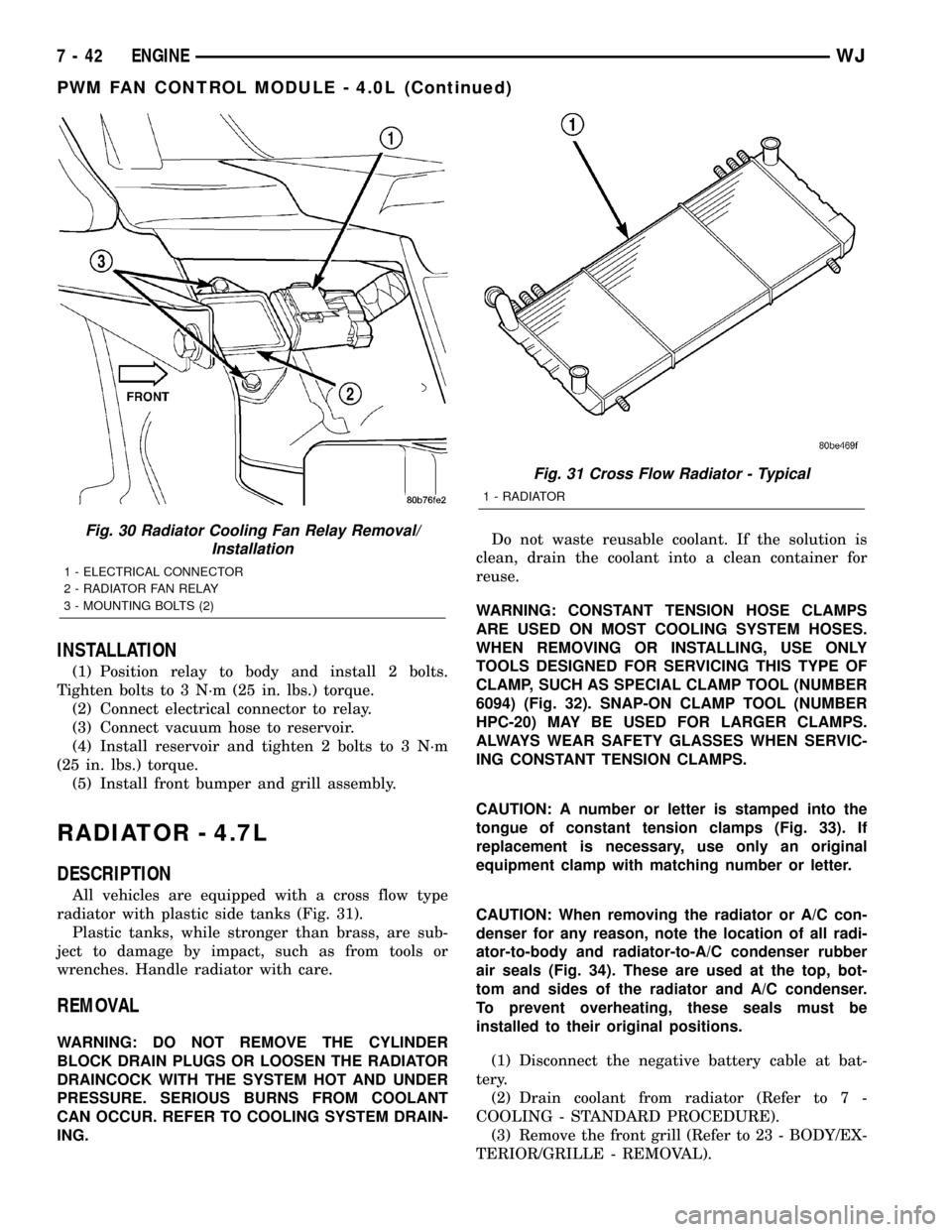
INSTALLATION
(1) Position relay to body and install 2 bolts.
Tighten bolts to 3 N´m (25 in. lbs.) torque.
(2) Connect electrical connector to relay.
(3) Connect vacuum hose to reservoir.
(4) Install reservoir and tighten 2 bolts to 3 N´m
(25 in. lbs.) torque.
(5) Install front bumper and grill assembly.
RADIATOR - 4.7L
DESCRIPTION
All vehicles are equipped with a cross flow type
radiator with plastic side tanks (Fig. 31).
Plastic tanks, while stronger than brass, are sub-
ject to damage by impact, such as from tools or
wrenches. Handle radiator with care.
REMOVAL
WARNING: DO NOT REMOVE THE CYLINDER
BLOCK DRAIN PLUGS OR LOOSEN THE RADIATOR
DRAINCOCK WITH THE SYSTEM HOT AND UNDER
PRESSURE. SERIOUS BURNS FROM COOLANT
CAN OCCUR. REFER TO COOLING SYSTEM DRAIN-
ING.Do not waste reusable coolant. If the solution is
clean, drain the coolant into a clean container for
reuse.
WARNING: CONSTANT TENSION HOSE CLAMPS
ARE USED ON MOST COOLING SYSTEM HOSES.
WHEN REMOVING OR INSTALLING, USE ONLY
TOOLS DESIGNED FOR SERVICING THIS TYPE OF
CLAMP, SUCH AS SPECIAL CLAMP TOOL (NUMBER
6094) (Fig. 32). SNAP-ON CLAMP TOOL (NUMBER
HPC-20) MAY BE USED FOR LARGER CLAMPS.
ALWAYS WEAR SAFETY GLASSES WHEN SERVIC-
ING CONSTANT TENSION CLAMPS.
CAUTION: A number or letter is stamped into the
tongue of constant tension clamps (Fig. 33). If
replacement is necessary, use only an original
equipment clamp with matching number or letter.
CAUTION: When removing the radiator or A/C con-
denser for any reason, note the location of all radi-
ator-to-body and radiator-to-A/C condenser rubber
air seals (Fig. 34). These are used at the top, bot-
tom and sides of the radiator and A/C condenser.
To prevent overheating, these seals must be
installed to their original positions.
(1) Disconnect the negative battery cable at bat-
tery.
(2) Drain coolant from radiator (Refer to 7 -
COOLING - STANDARD PROCEDURE).
(3) Remove the front grill (Refer to 23 - BODY/EX-
TERIOR/GRILLE - REMOVAL).
Fig. 30 Radiator Cooling Fan Relay Removal/
Installation
1 - ELECTRICAL CONNECTOR
2 - RADIATOR FAN RELAY
3 - MOUNTING BOLTS (2)
Fig. 31 Cross Flow Radiator - Typical
1 - RADIATOR
7 - 42 ENGINEWJ
PWM FAN CONTROL MODULE - 4.0L (Continued)
Page 270 of 2199
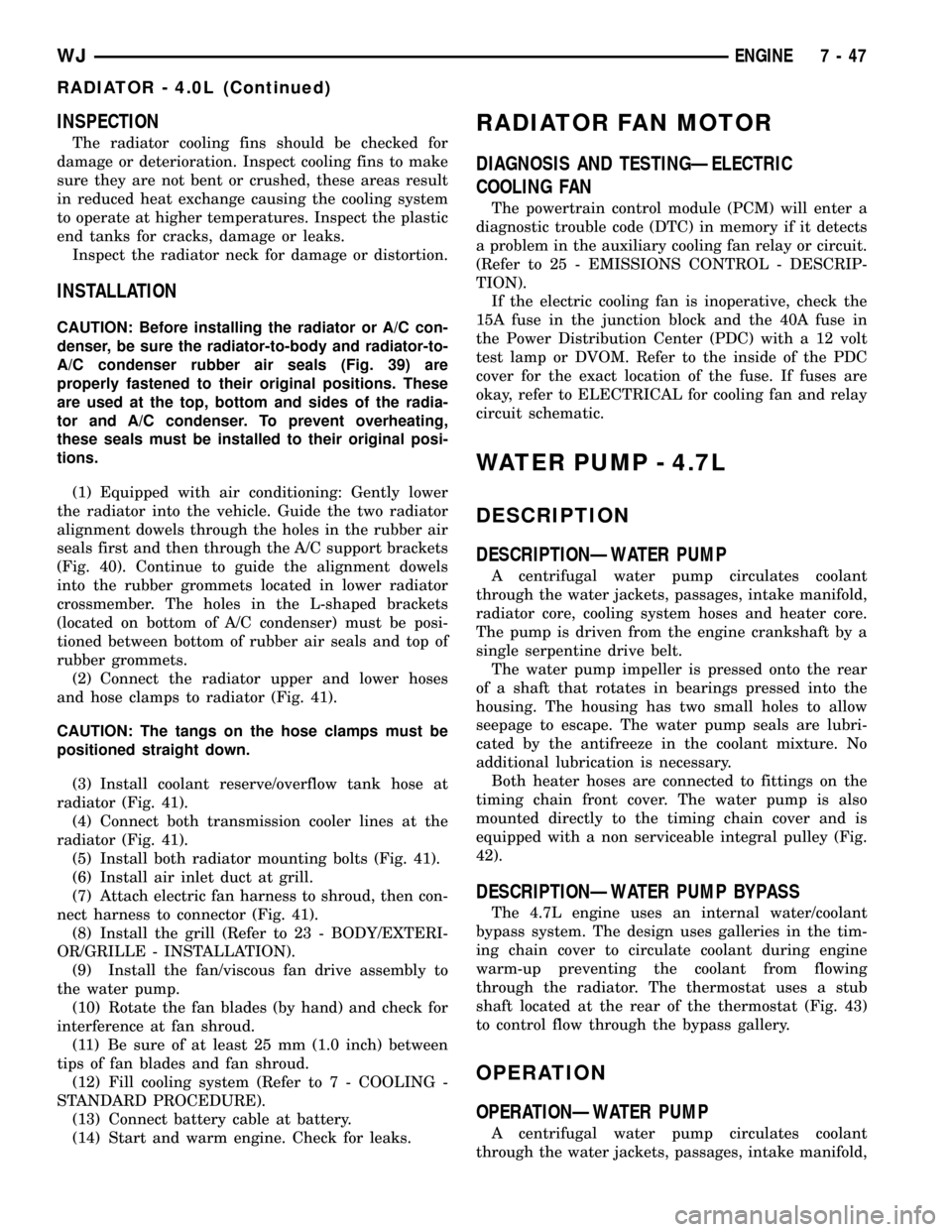
INSPECTION
The radiator cooling fins should be checked for
damage or deterioration. Inspect cooling fins to make
sure they are not bent or crushed, these areas result
in reduced heat exchange causing the cooling system
to operate at higher temperatures. Inspect the plastic
end tanks for cracks, damage or leaks.
Inspect the radiator neck for damage or distortion.
INSTALLATION
CAUTION: Before installing the radiator or A/C con-
denser, be sure the radiator-to-body and radiator-to-
A/C condenser rubber air seals (Fig. 39) are
properly fastened to their original positions. These
are used at the top, bottom and sides of the radia-
tor and A/C condenser. To prevent overheating,
these seals must be installed to their original posi-
tions.
(1) Equipped with air conditioning: Gently lower
the radiator into the vehicle. Guide the two radiator
alignment dowels through the holes in the rubber air
seals first and then through the A/C support brackets
(Fig. 40). Continue to guide the alignment dowels
into the rubber grommets located in lower radiator
crossmember. The holes in the L-shaped brackets
(located on bottom of A/C condenser) must be posi-
tioned between bottom of rubber air seals and top of
rubber grommets.
(2) Connect the radiator upper and lower hoses
and hose clamps to radiator (Fig. 41).
CAUTION: The tangs on the hose clamps must be
positioned straight down.
(3) Install coolant reserve/overflow tank hose at
radiator (Fig. 41).
(4) Connect both transmission cooler lines at the
radiator (Fig. 41).
(5) Install both radiator mounting bolts (Fig. 41).
(6) Install air inlet duct at grill.
(7) Attach electric fan harness to shroud, then con-
nect harness to connector (Fig. 41).
(8) Install the grill (Refer to 23 - BODY/EXTERI-
OR/GRILLE - INSTALLATION).
(9) Install the fan/viscous fan drive assembly to
the water pump.
(10) Rotate the fan blades (by hand) and check for
interference at fan shroud.
(11) Be sure of at least 25 mm (1.0 inch) between
tips of fan blades and fan shroud.
(12) Fill cooling system (Refer to 7 - COOLING -
STANDARD PROCEDURE).
(13) Connect battery cable at battery.
(14) Start and warm engine. Check for leaks.
RADIATOR FAN MOTOR
DIAGNOSIS AND TESTINGÐELECTRIC
COOLING FAN
The powertrain control module (PCM) will enter a
diagnostic trouble code (DTC) in memory if it detects
a problem in the auxiliary cooling fan relay or circuit.
(Refer to 25 - EMISSIONS CONTROL - DESCRIP-
TION).
If the electric cooling fan is inoperative, check the
15A fuse in the junction block and the 40A fuse in
the Power Distribution Center (PDC) with a 12 volt
test lamp or DVOM. Refer to the inside of the PDC
cover for the exact location of the fuse. If fuses are
okay, refer to ELECTRICAL for cooling fan and relay
circuit schematic.
WATER PUMP - 4.7L
DESCRIPTION
DESCRIPTIONÐWATER PUMP
A centrifugal water pump circulates coolant
through the water jackets, passages, intake manifold,
radiator core, cooling system hoses and heater core.
The pump is driven from the engine crankshaft by a
single serpentine drive belt.
The water pump impeller is pressed onto the rear
of a shaft that rotates in bearings pressed into the
housing. The housing has two small holes to allow
seepage to escape. The water pump seals are lubri-
cated by the antifreeze in the coolant mixture. No
additional lubrication is necessary.
Both heater hoses are connected to fittings on the
timing chain front cover. The water pump is also
mounted directly to the timing chain cover and is
equipped with a non serviceable integral pulley (Fig.
42).
DESCRIPTIONÐWATER PUMP BYPASS
The 4.7L engine uses an internal water/coolant
bypass system. The design uses galleries in the tim-
ing chain cover to circulate coolant during engine
warm-up preventing the coolant from flowing
through the radiator. The thermostat uses a stub
shaft located at the rear of the thermostat (Fig. 43)
to control flow through the bypass gallery.
OPERATION
OPERATIONÐWATER PUMP
A centrifugal water pump circulates coolant
through the water jackets, passages, intake manifold,
WJENGINE 7 - 47
RADIATOR - 4.0L (Continued)
Page 310 of 2199
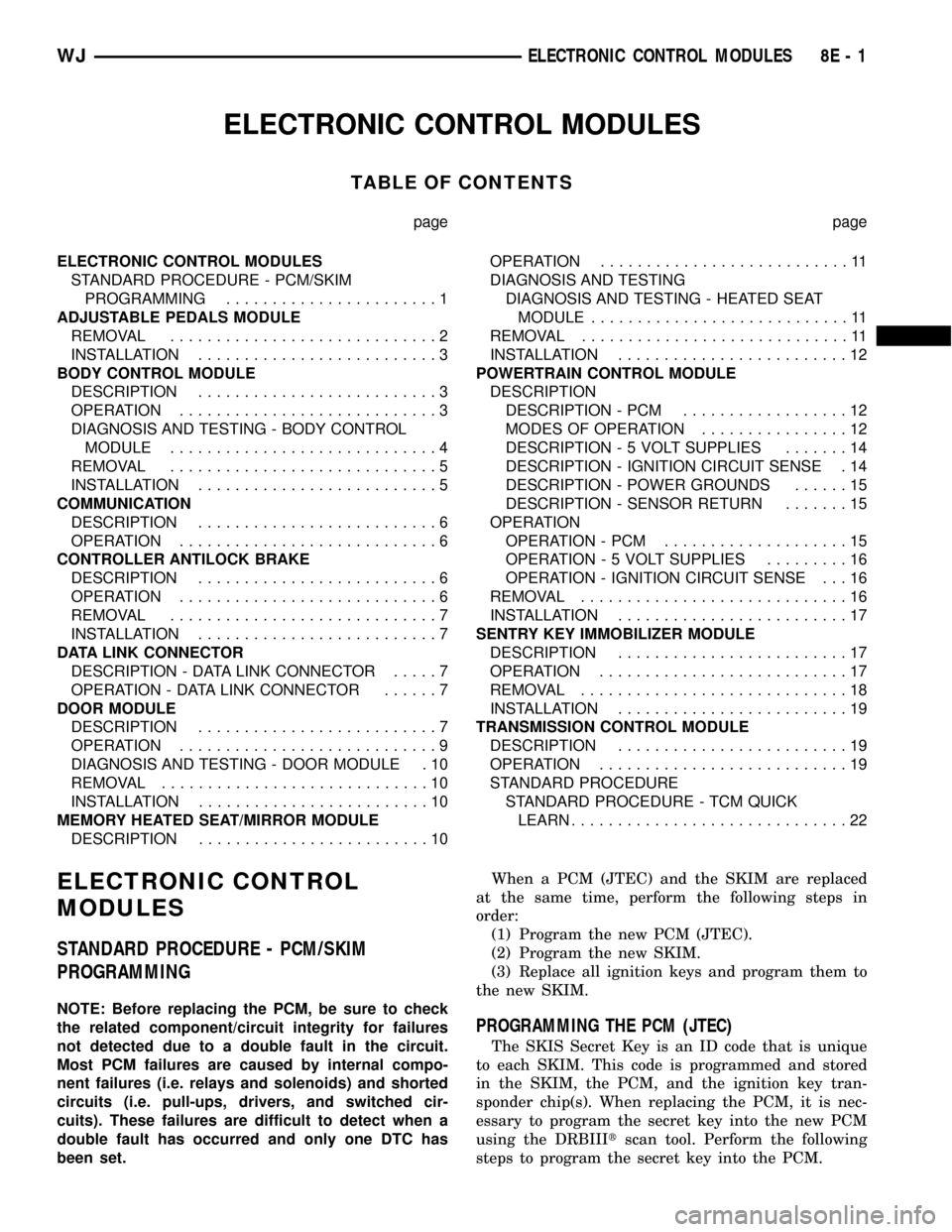
ELECTRONIC CONTROL MODULES
TABLE OF CONTENTS
page page
ELECTRONIC CONTROL MODULES
STANDARD PROCEDURE - PCM/SKIM
PROGRAMMING.......................1
ADJUSTABLE PEDALS MODULE
REMOVAL.............................2
INSTALLATION..........................3
BODY CONTROL MODULE
DESCRIPTION..........................3
OPERATION............................3
DIAGNOSIS AND TESTING - BODY CONTROL
MODULE.............................4
REMOVAL.............................5
INSTALLATION..........................5
COMMUNICATION
DESCRIPTION..........................6
OPERATION............................6
CONTROLLER ANTILOCK BRAKE
DESCRIPTION..........................6
OPERATION............................6
REMOVAL.............................7
INSTALLATION..........................7
DATA LINK CONNECTOR
DESCRIPTION - DATA LINK CONNECTOR.....7
OPERATION - DATA LINK CONNECTOR......7
DOOR MODULE
DESCRIPTION..........................7
OPERATION............................9
DIAGNOSIS AND TESTING - DOOR MODULE . 10
REMOVAL.............................10
INSTALLATION.........................10
MEMORY HEATED SEAT/MIRROR MODULE
DESCRIPTION.........................10OPERATION...........................11
DIAGNOSIS AND TESTING
DIAGNOSIS AND TESTING - HEATED SEAT
MODULE............................11
REMOVAL.............................11
INSTALLATION.........................12
POWERTRAIN CONTROL MODULE
DESCRIPTION
DESCRIPTION - PCM..................12
MODES OF OPERATION................12
DESCRIPTION - 5 VOLT SUPPLIES.......14
DESCRIPTION - IGNITION CIRCUIT SENSE . 14
DESCRIPTION - POWER GROUNDS......15
DESCRIPTION - SENSOR RETURN.......15
OPERATION
OPERATION - PCM....................15
OPERATION - 5 VOLT SUPPLIES.........16
OPERATION - IGNITION CIRCUIT SENSE . . . 16
REMOVAL.............................16
INSTALLATION.........................17
SENTRY KEY IMMOBILIZER MODULE
DESCRIPTION.........................17
OPERATION...........................17
REMOVAL.............................18
INSTALLATION.........................19
TRANSMISSION CONTROL MODULE
DESCRIPTION.........................19
OPERATION...........................19
STANDARD PROCEDURE
STANDARD PROCEDURE - TCM QUICK
LEARN..............................22
ELECTRONIC CONTROL
MODULES
STANDARD PROCEDURE - PCM/SKIM
PROGRAMMING
NOTE: Before replacing the PCM, be sure to check
the related component/circuit integrity for failures
not detected due to a double fault in the circuit.
Most PCM failures are caused by internal compo-
nent failures (i.e. relays and solenoids) and shorted
circuits (i.e. pull-ups, drivers, and switched cir-
cuits). These failures are difficult to detect when a
double fault has occurred and only one DTC has
been set.When a PCM (JTEC) and the SKIM are replaced
at the same time, perform the following steps in
order:
(1) Program the new PCM (JTEC).
(2) Program the new SKIM.
(3) Replace all ignition keys and program them to
the new SKIM.
PROGRAMMING THE PCM (JTEC)
The SKIS Secret Key is an ID code that is unique
to each SKIM. This code is programmed and stored
in the SKIM, the PCM, and the ignition key tran-
sponder chip(s). When replacing the PCM, it is nec-
essary to program the secret key into the new PCM
using the DRBIIItscan tool. Perform the following
steps to program the secret key into the PCM.
WJELECTRONIC CONTROL MODULES 8E - 1
Page 313 of 2199
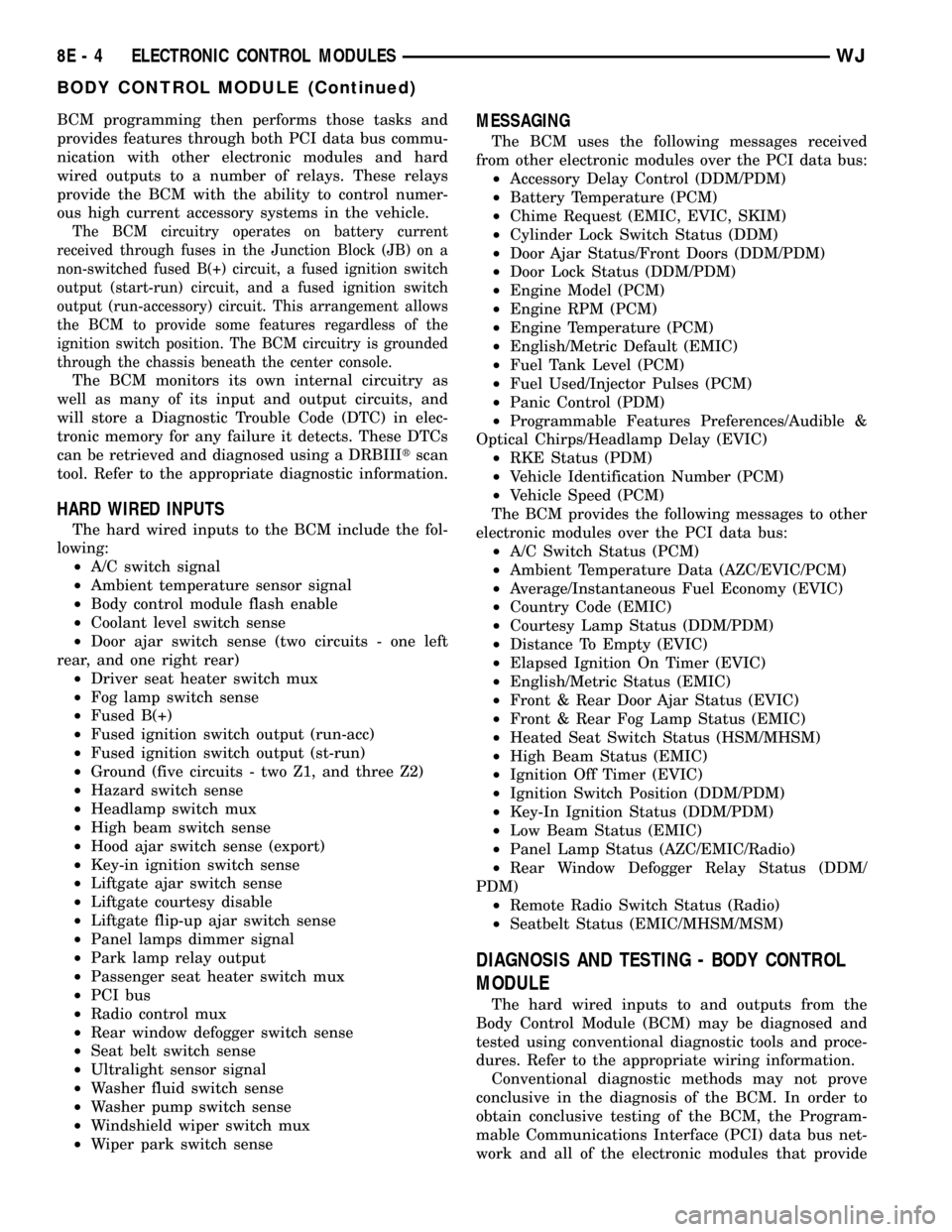
BCM programming then performs those tasks and
provides features through both PCI data bus commu-
nication with other electronic modules and hard
wired outputs to a number of relays. These relays
provide the BCM with the ability to control numer-
ous high current accessory systems in the vehicle.
The BCM circuitry operates on battery current
received through fuses in the Junction Block (JB) on a
non-switched fused B(+) circuit, a fused ignition switch
output (start-run) circuit, and a fused ignition switch
output (run-accessory) circuit. This arrangement allows
the BCM to provide some features regardless of the
ignition switch position. The BCM circuitry is grounded
through the chassis beneath the center console.
The BCM monitors its own internal circuitry as
well as many of its input and output circuits, and
will store a Diagnostic Trouble Code (DTC) in elec-
tronic memory for any failure it detects. These DTCs
can be retrieved and diagnosed using a DRBIIItscan
tool. Refer to the appropriate diagnostic information.
HARD WIRED INPUTS
The hard wired inputs to the BCM include the fol-
lowing:
²A/C switch signal
²Ambient temperature sensor signal
²Body control module flash enable
²Coolant level switch sense
²Door ajar switch sense (two circuits - one left
rear, and one right rear)
²Driver seat heater switch mux
²Fog lamp switch sense
²Fused B(+)
²Fused ignition switch output (run-acc)
²Fused ignition switch output (st-run)
²Ground (five circuits - two Z1, and three Z2)
²Hazard switch sense
²Headlamp switch mux
²High beam switch sense
²Hood ajar switch sense (export)
²Key-in ignition switch sense
²Liftgate ajar switch sense
²Liftgate courtesy disable
²Liftgate flip-up ajar switch sense
²Panel lamps dimmer signal
²Park lamp relay output
²Passenger seat heater switch mux
²PCI bus
²Radio control mux
²Rear window defogger switch sense
²Seat belt switch sense
²Ultralight sensor signal
²Washer fluid switch sense
²Washer pump switch sense
²Windshield wiper switch mux
²Wiper park switch sense
MESSAGING
The BCM uses the following messages received
from other electronic modules over the PCI data bus:
²Accessory Delay Control (DDM/PDM)
²Battery Temperature (PCM)
²Chime Request (EMIC, EVIC, SKIM)
²Cylinder Lock Switch Status (DDM)
²Door Ajar Status/Front Doors (DDM/PDM)
²Door Lock Status (DDM/PDM)
²Engine Model (PCM)
²Engine RPM (PCM)
²Engine Temperature (PCM)
²English/Metric Default (EMIC)
²Fuel Tank Level (PCM)
²Fuel Used/Injector Pulses (PCM)
²Panic Control (PDM)
²Programmable Features Preferences/Audible &
Optical Chirps/Headlamp Delay (EVIC)
²RKE Status (PDM)
²Vehicle Identification Number (PCM)
²Vehicle Speed (PCM)
The BCM provides the following messages to other
electronic modules over the PCI data bus:
²A/C Switch Status (PCM)
²Ambient Temperature Data (AZC/EVIC/PCM)
²Average/Instantaneous Fuel Economy (EVIC)
²Country Code (EMIC)
²Courtesy Lamp Status (DDM/PDM)
²Distance To Empty (EVIC)
²Elapsed Ignition On Timer (EVIC)
²English/Metric Status (EMIC)
²Front & Rear Door Ajar Status (EVIC)
²Front & Rear Fog Lamp Status (EMIC)
²Heated Seat Switch Status (HSM/MHSM)
²High Beam Status (EMIC)
²Ignition Off Timer (EVIC)
²Ignition Switch Position (DDM/PDM)
²Key-In Ignition Status (DDM/PDM)
²Low Beam Status (EMIC)
²Panel Lamp Status (AZC/EMIC/Radio)
²Rear Window Defogger Relay Status (DDM/
PDM)
²Remote Radio Switch Status (Radio)
²Seatbelt Status (EMIC/MHSM/MSM)
DIAGNOSIS AND TESTING - BODY CONTROL
MODULE
The hard wired inputs to and outputs from the
Body Control Module (BCM) may be diagnosed and
tested using conventional diagnostic tools and proce-
dures. Refer to the appropriate wiring information.
Conventional diagnostic methods may not prove
conclusive in the diagnosis of the BCM. In order to
obtain conclusive testing of the BCM, the Program-
mable Communications Interface (PCI) data bus net-
work and all of the electronic modules that provide
8E - 4 ELECTRONIC CONTROL MODULESWJ
BODY CONTROL MODULE (Continued)
Page 315 of 2199
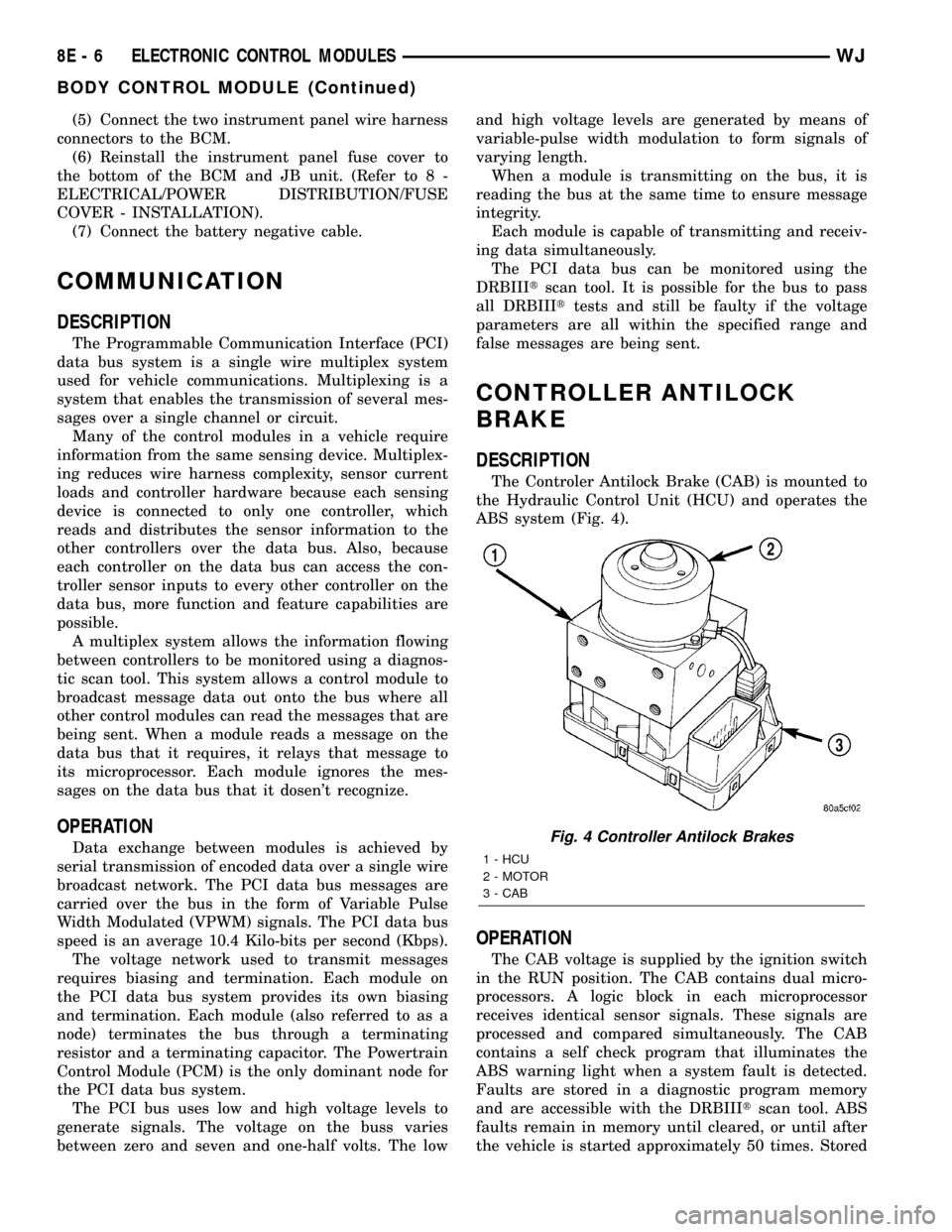
(5) Connect the two instrument panel wire harness
connectors to the BCM.
(6) Reinstall the instrument panel fuse cover to
the bottom of the BCM and JB unit. (Refer to 8 -
ELECTRICAL/POWER DISTRIBUTION/FUSE
COVER - INSTALLATION).
(7) Connect the battery negative cable.
COMMUNICATION
DESCRIPTION
The Programmable Communication Interface (PCI)
data bus system is a single wire multiplex system
used for vehicle communications. Multiplexing is a
system that enables the transmission of several mes-
sages over a single channel or circuit.
Many of the control modules in a vehicle require
information from the same sensing device. Multiplex-
ing reduces wire harness complexity, sensor current
loads and controller hardware because each sensing
device is connected to only one controller, which
reads and distributes the sensor information to the
other controllers over the data bus. Also, because
each controller on the data bus can access the con-
troller sensor inputs to every other controller on the
data bus, more function and feature capabilities are
possible.
A multiplex system allows the information flowing
between controllers to be monitored using a diagnos-
tic scan tool. This system allows a control module to
broadcast message data out onto the bus where all
other control modules can read the messages that are
being sent. When a module reads a message on the
data bus that it requires, it relays that message to
its microprocessor. Each module ignores the mes-
sages on the data bus that it dosen't recognize.
OPERATION
Data exchange between modules is achieved by
serial transmission of encoded data over a single wire
broadcast network. The PCI data bus messages are
carried over the bus in the form of Variable Pulse
Width Modulated (VPWM) signals. The PCI data bus
speed is an average 10.4 Kilo-bits per second (Kbps).
The voltage network used to transmit messages
requires biasing and termination. Each module on
the PCI data bus system provides its own biasing
and termination. Each module (also referred to as a
node) terminates the bus through a terminating
resistor and a terminating capacitor. The Powertrain
Control Module (PCM) is the only dominant node for
the PCI data bus system.
The PCI bus uses low and high voltage levels to
generate signals. The voltage on the buss varies
between zero and seven and one-half volts. The lowand high voltage levels are generated by means of
variable-pulse width modulation to form signals of
varying length.
When a module is transmitting on the bus, it is
reading the bus at the same time to ensure message
integrity.
Each module is capable of transmitting and receiv-
ing data simultaneously.
The PCI data bus can be monitored using the
DRBIIItscan tool. It is possible for the bus to pass
all DRBIIIttests and still be faulty if the voltage
parameters are all within the specified range and
false messages are being sent.
CONTROLLER ANTILOCK
BRAKE
DESCRIPTION
The Controler Antilock Brake (CAB) is mounted to
the Hydraulic Control Unit (HCU) and operates the
ABS system (Fig. 4).
OPERATION
The CAB voltage is supplied by the ignition switch
in the RUN position. The CAB contains dual micro-
processors. A logic block in each microprocessor
receives identical sensor signals. These signals are
processed and compared simultaneously. The CAB
contains a self check program that illuminates the
ABS warning light when a system fault is detected.
Faults are stored in a diagnostic program memory
and are accessible with the DRBIIItscan tool. ABS
faults remain in memory until cleared, or until after
the vehicle is started approximately 50 times. Stored
Fig. 4 Controller Antilock Brakes
1 - HCU
2 - MOTOR
3 - CAB
8E - 6 ELECTRONIC CONTROL MODULESWJ
BODY CONTROL MODULE (Continued)
Page 318 of 2199
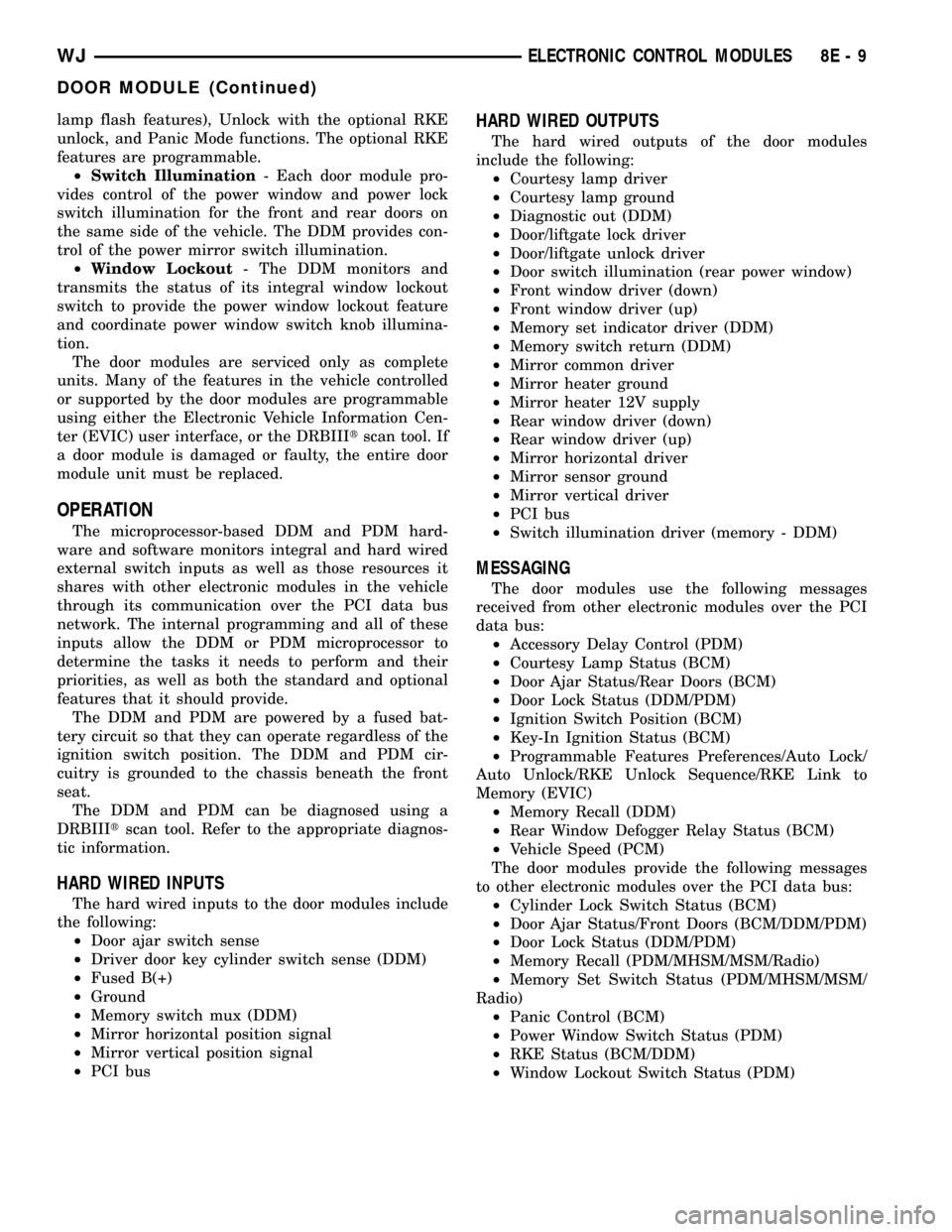
lamp flash features), Unlock with the optional RKE
unlock, and Panic Mode functions. The optional RKE
features are programmable.
²Switch Illumination- Each door module pro-
vides control of the power window and power lock
switch illumination for the front and rear doors on
the same side of the vehicle. The DDM provides con-
trol of the power mirror switch illumination.
²Window Lockout- The DDM monitors and
transmits the status of its integral window lockout
switch to provide the power window lockout feature
and coordinate power window switch knob illumina-
tion.
The door modules are serviced only as complete
units. Many of the features in the vehicle controlled
or supported by the door modules are programmable
using either the Electronic Vehicle Information Cen-
ter (EVIC) user interface, or the DRBIIItscan tool. If
a door module is damaged or faulty, the entire door
module unit must be replaced.
OPERATION
The microprocessor-based DDM and PDM hard-
ware and software monitors integral and hard wired
external switch inputs as well as those resources it
shares with other electronic modules in the vehicle
through its communication over the PCI data bus
network. The internal programming and all of these
inputs allow the DDM or PDM microprocessor to
determine the tasks it needs to perform and their
priorities, as well as both the standard and optional
features that it should provide.
The DDM and PDM are powered by a fused bat-
tery circuit so that they can operate regardless of the
ignition switch position. The DDM and PDM cir-
cuitry is grounded to the chassis beneath the front
seat.
The DDM and PDM can be diagnosed using a
DRBIIItscan tool. Refer to the appropriate diagnos-
tic information.
HARD WIRED INPUTS
The hard wired inputs to the door modules include
the following:
²Door ajar switch sense
²Driver door key cylinder switch sense (DDM)
²Fused B(+)
²Ground
²Memory switch mux (DDM)
²Mirror horizontal position signal
²Mirror vertical position signal
²PCI bus
HARD WIRED OUTPUTS
The hard wired outputs of the door modules
include the following:
²Courtesy lamp driver
²Courtesy lamp ground
²Diagnostic out (DDM)
²Door/liftgate lock driver
²Door/liftgate unlock driver
²Door switch illumination (rear power window)
²Front window driver (down)
²Front window driver (up)
²Memory set indicator driver (DDM)
²Memory switch return (DDM)
²Mirror common driver
²Mirror heater ground
²Mirror heater 12V supply
²Rear window driver (down)
²Rear window driver (up)
²Mirror horizontal driver
²Mirror sensor ground
²Mirror vertical driver
²PCI bus
²Switch illumination driver (memory - DDM)
MESSAGING
The door modules use the following messages
received from other electronic modules over the PCI
data bus:
²Accessory Delay Control (PDM)
²Courtesy Lamp Status (BCM)
²Door Ajar Status/Rear Doors (BCM)
²Door Lock Status (DDM/PDM)
²Ignition Switch Position (BCM)
²Key-In Ignition Status (BCM)
²Programmable Features Preferences/Auto Lock/
Auto Unlock/RKE Unlock Sequence/RKE Link to
Memory (EVIC)
²Memory Recall (DDM)
²Rear Window Defogger Relay Status (BCM)
²Vehicle Speed (PCM)
The door modules provide the following messages
to other electronic modules over the PCI data bus:
²Cylinder Lock Switch Status (BCM)
²Door Ajar Status/Front Doors (BCM/DDM/PDM)
²Door Lock Status (DDM/PDM)
²Memory Recall (PDM/MHSM/MSM/Radio)
²Memory Set Switch Status (PDM/MHSM/MSM/
Radio)
²Panic Control (BCM)
²Power Window Switch Status (PDM)
²RKE Status (BCM/DDM)
²Window Lockout Switch Status (PDM)
WJELECTRONIC CONTROL MODULES 8E - 9
DOOR MODULE (Continued)
Page 322 of 2199
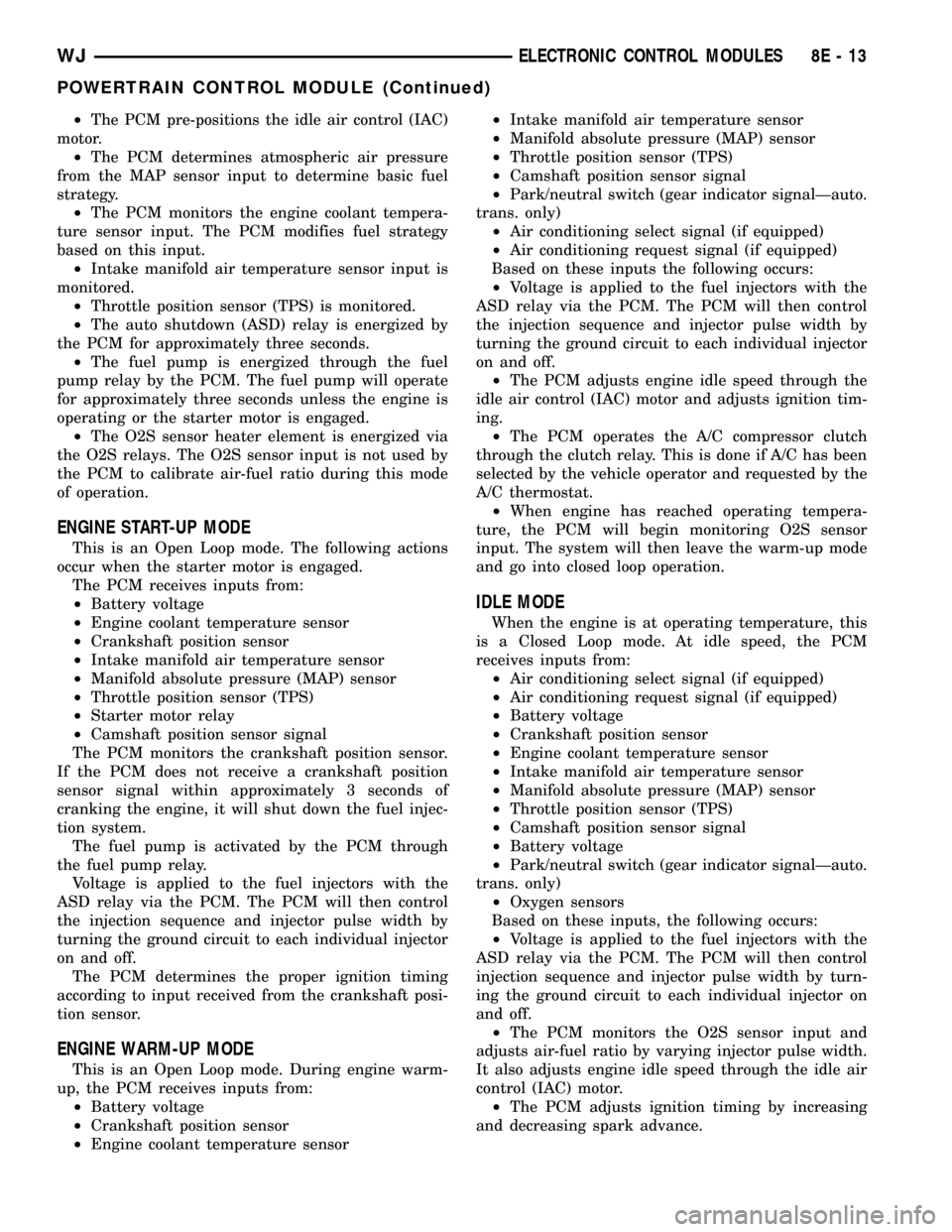
²The PCM pre-positions the idle air control (IAC)
motor.
²The PCM determines atmospheric air pressure
from the MAP sensor input to determine basic fuel
strategy.
²The PCM monitors the engine coolant tempera-
ture sensor input. The PCM modifies fuel strategy
based on this input.
²Intake manifold air temperature sensor input is
monitored.
²Throttle position sensor (TPS) is monitored.
²The auto shutdown (ASD) relay is energized by
the PCM for approximately three seconds.
²The fuel pump is energized through the fuel
pump relay by the PCM. The fuel pump will operate
for approximately three seconds unless the engine is
operating or the starter motor is engaged.
²The O2S sensor heater element is energized via
the O2S relays. The O2S sensor input is not used by
the PCM to calibrate air-fuel ratio during this mode
of operation.
ENGINE START-UP MODE
This is an Open Loop mode. The following actions
occur when the starter motor is engaged.
The PCM receives inputs from:
²Battery voltage
²Engine coolant temperature sensor
²Crankshaft position sensor
²Intake manifold air temperature sensor
²Manifold absolute pressure (MAP) sensor
²Throttle position sensor (TPS)
²Starter motor relay
²Camshaft position sensor signal
The PCM monitors the crankshaft position sensor.
If the PCM does not receive a crankshaft position
sensor signal within approximately 3 seconds of
cranking the engine, it will shut down the fuel injec-
tion system.
The fuel pump is activated by the PCM through
the fuel pump relay.
Voltage is applied to the fuel injectors with the
ASD relay via the PCM. The PCM will then control
the injection sequence and injector pulse width by
turning the ground circuit to each individual injector
on and off.
The PCM determines the proper ignition timing
according to input received from the crankshaft posi-
tion sensor.
ENGINE WARM-UP MODE
This is an Open Loop mode. During engine warm-
up, the PCM receives inputs from:
²Battery voltage
²Crankshaft position sensor
²Engine coolant temperature sensor²Intake manifold air temperature sensor
²Manifold absolute pressure (MAP) sensor
²Throttle position sensor (TPS)
²Camshaft position sensor signal
²Park/neutral switch (gear indicator signalÐauto.
trans. only)
²Air conditioning select signal (if equipped)
²Air conditioning request signal (if equipped)
Based on these inputs the following occurs:
²Voltage is applied to the fuel injectors with the
ASD relay via the PCM. The PCM will then control
the injection sequence and injector pulse width by
turning the ground circuit to each individual injector
on and off.
²The PCM adjusts engine idle speed through the
idle air control (IAC) motor and adjusts ignition tim-
ing.
²The PCM operates the A/C compressor clutch
through the clutch relay. This is done if A/C has been
selected by the vehicle operator and requested by the
A/C thermostat.
²When engine has reached operating tempera-
ture, the PCM will begin monitoring O2S sensor
input. The system will then leave the warm-up mode
and go into closed loop operation.
IDLE MODE
When the engine is at operating temperature, this
is a Closed Loop mode. At idle speed, the PCM
receives inputs from:
²Air conditioning select signal (if equipped)
²Air conditioning request signal (if equipped)
²Battery voltage
²Crankshaft position sensor
²Engine coolant temperature sensor
²Intake manifold air temperature sensor
²Manifold absolute pressure (MAP) sensor
²Throttle position sensor (TPS)
²Camshaft position sensor signal
²Battery voltage
²Park/neutral switch (gear indicator signalÐauto.
trans. only)
²Oxygen sensors
Based on these inputs, the following occurs:
²Voltage is applied to the fuel injectors with the
ASD relay via the PCM. The PCM will then control
injection sequence and injector pulse width by turn-
ing the ground circuit to each individual injector on
and off.
²The PCM monitors the O2S sensor input and
adjusts air-fuel ratio by varying injector pulse width.
It also adjusts engine idle speed through the idle air
control (IAC) motor.
²The PCM adjusts ignition timing by increasing
and decreasing spark advance.
WJELECTRONIC CONTROL MODULES 8E - 13
POWERTRAIN CONTROL MODULE (Continued)