sensor JEEP LIBERTY 2002 KJ / 1.G Repair Manual
[x] Cancel search | Manufacturer: JEEP, Model Year: 2002, Model line: LIBERTY, Model: JEEP LIBERTY 2002 KJ / 1.GPages: 1803, PDF Size: 62.3 MB
Page 319 of 1803
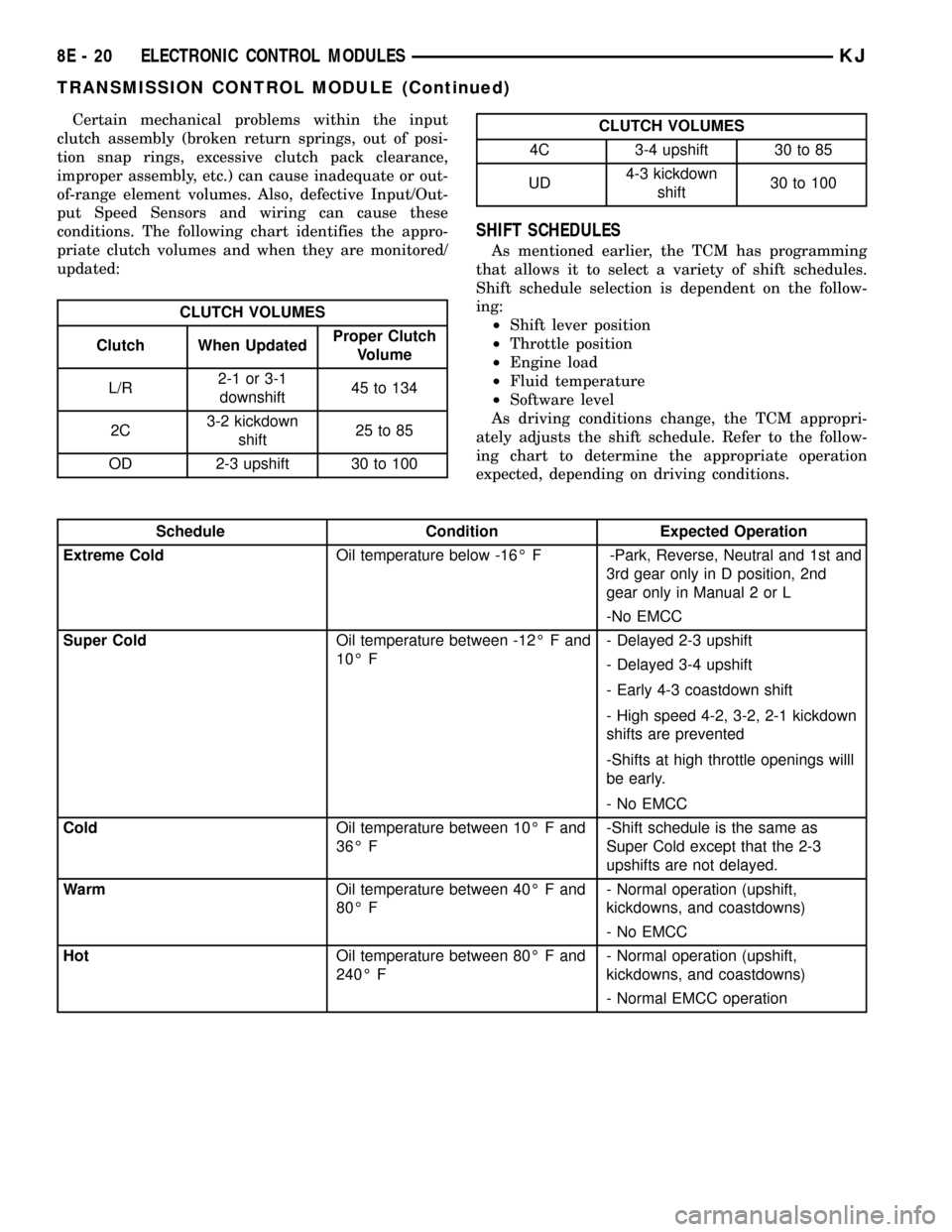
Certain mechanical problems within the input
clutch assembly (broken return springs, out of posi-
tion snap rings, excessive clutch pack clearance,
improper assembly, etc.) can cause inadequate or out-
of-range element volumes. Also, defective Input/Out-
put Speed Sensors and wiring can cause these
conditions. The following chart identifies the appro-
priate clutch volumes and when they are monitored/
updated:
CLUTCH VOLUMES
Clutch When UpdatedProper Clutch
Volume
L/R2-1 or 3-1
downshift45 to 134
2C3-2 kickdown
shift25 to 85
OD 2-3 upshift 30 to 100
CLUTCH VOLUMES
4C 3-4 upshift 30 to 85
UD4-3 kickdown
shift30 to 100
SHIFT SCHEDULES
As mentioned earlier, the TCM has programming
that allows it to select a variety of shift schedules.
Shift schedule selection is dependent on the follow-
ing:
²Shift lever position
²Throttle position
²Engine load
²Fluid temperature
²Software level
As driving conditions change, the TCM appropri-
ately adjusts the shift schedule. Refer to the follow-
ing chart to determine the appropriate operation
expected, depending on driving conditions.
Schedule Condition Expected Operation
Extreme ColdOil temperature below -16É F -Park, Reverse, Neutral and 1st and
3rd gear only in D position, 2nd
gear only in Manual 2 or L
-No EMCC
Super ColdOil temperature between -12É F and
10É F- Delayed 2-3 upshift
- Delayed 3-4 upshift
- Early 4-3 coastdown shift
- High speed 4-2, 3-2, 2-1 kickdown
shifts are prevented
-Shifts at high throttle openings willl
be early.
- No EMCC
ColdOil temperature between 10É F and
36É F-Shift schedule is the same as
Super Cold except that the 2-3
upshifts are not delayed.
WarmOil temperature between 40É F and
80É F- Normal operation (upshift,
kickdowns, and coastdowns)
- No EMCC
HotOil temperature between 80É F and
240É F- Normal operation (upshift,
kickdowns, and coastdowns)
- Normal EMCC operation
8E - 20 ELECTRONIC CONTROL MODULESKJ
TRANSMISSION CONTROL MODULE (Continued)
Page 320 of 1803
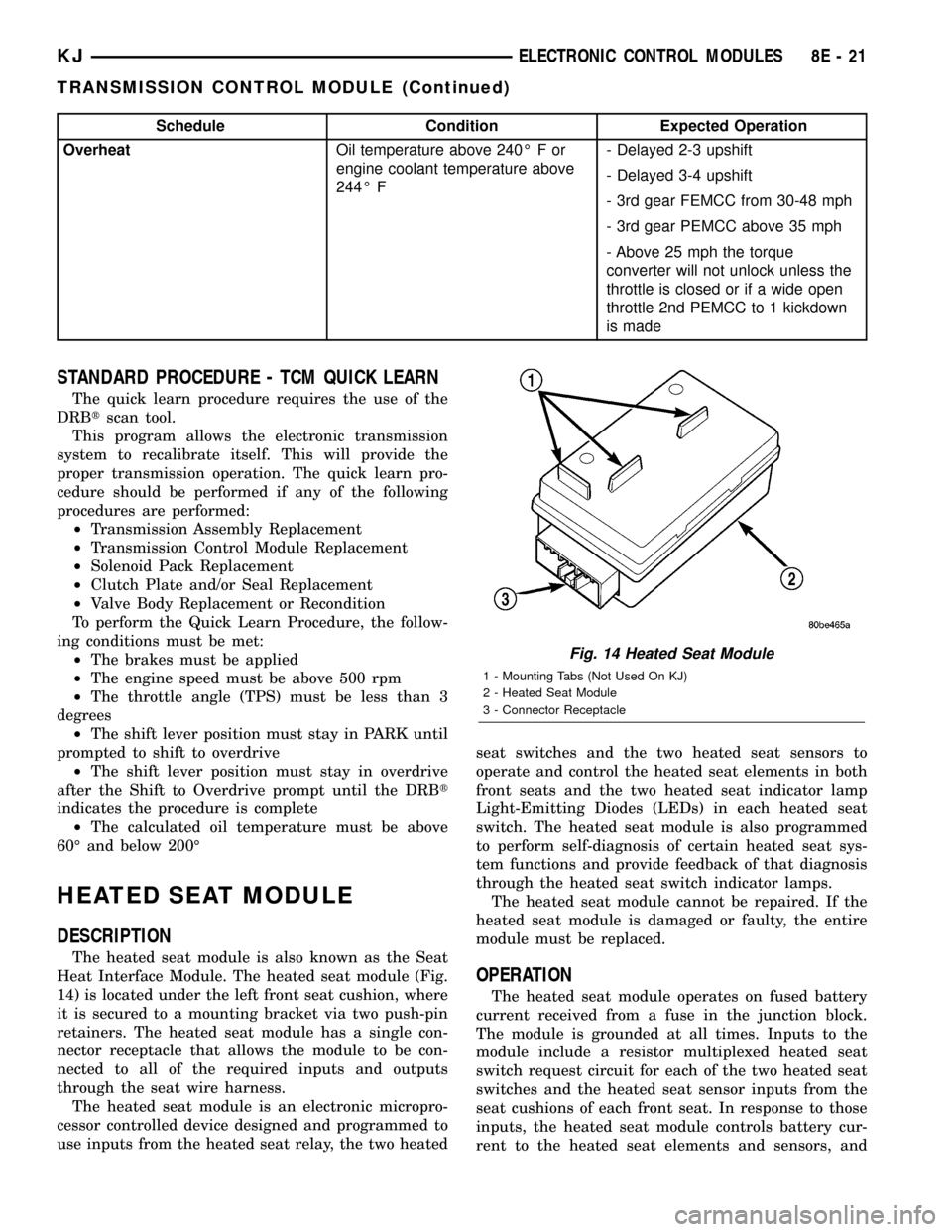
Schedule Condition Expected Operation
OverheatOil temperature above 240É F or
engine coolant temperature above
244É F- Delayed 2-3 upshift
- Delayed 3-4 upshift
- 3rd gear FEMCC from 30-48 mph
- 3rd gear PEMCC above 35 mph
- Above 25 mph the torque
converter will not unlock unless the
throttle is closed or if a wide open
throttle 2nd PEMCC to 1 kickdown
is made
STANDARD PROCEDURE - TCM QUICK LEARN
The quick learn procedure requires the use of the
DRBtscan tool.
This program allows the electronic transmission
system to recalibrate itself. This will provide the
proper transmission operation. The quick learn pro-
cedure should be performed if any of the following
procedures are performed:
²Transmission Assembly Replacement
²Transmission Control Module Replacement
²Solenoid Pack Replacement
²Clutch Plate and/or Seal Replacement
²Valve Body Replacement or Recondition
To perform the Quick Learn Procedure, the follow-
ing conditions must be met:
²The brakes must be applied
²The engine speed must be above 500 rpm
²The throttle angle (TPS) must be less than 3
degrees
²The shift lever position must stay in PARK until
prompted to shift to overdrive
²The shift lever position must stay in overdrive
after the Shift to Overdrive prompt until the DRBt
indicates the procedure is complete
²The calculated oil temperature must be above
60É and below 200É
HEATED SEAT MODULE
DESCRIPTION
The heated seat module is also known as the Seat
Heat Interface Module. The heated seat module (Fig.
14) is located under the left front seat cushion, where
it is secured to a mounting bracket via two push-pin
retainers. The heated seat module has a single con-
nector receptacle that allows the module to be con-
nected to all of the required inputs and outputs
through the seat wire harness.
The heated seat module is an electronic micropro-
cessor controlled device designed and programmed to
use inputs from the heated seat relay, the two heatedseat switches and the two heated seat sensors to
operate and control the heated seat elements in both
front seats and the two heated seat indicator lamp
Light-Emitting Diodes (LEDs) in each heated seat
switch. The heated seat module is also programmed
to perform self-diagnosis of certain heated seat sys-
tem functions and provide feedback of that diagnosis
through the heated seat switch indicator lamps.
The heated seat module cannot be repaired. If the
heated seat module is damaged or faulty, the entire
module must be replaced.
OPERATION
The heated seat module operates on fused battery
current received from a fuse in the junction block.
The module is grounded at all times. Inputs to the
module include a resistor multiplexed heated seat
switch request circuit for each of the two heated seat
switches and the heated seat sensor inputs from the
seat cushions of each front seat. In response to those
inputs, the heated seat module controls battery cur-
rent to the heated seat elements and sensors, and
Fig. 14 Heated Seat Module
1 - Mounting Tabs (Not Used On KJ)
2 - Heated Seat Module
3 - Connector Receptacle
KJELECTRONIC CONTROL MODULES 8E - 21
TRANSMISSION CONTROL MODULE (Continued)
Page 321 of 1803
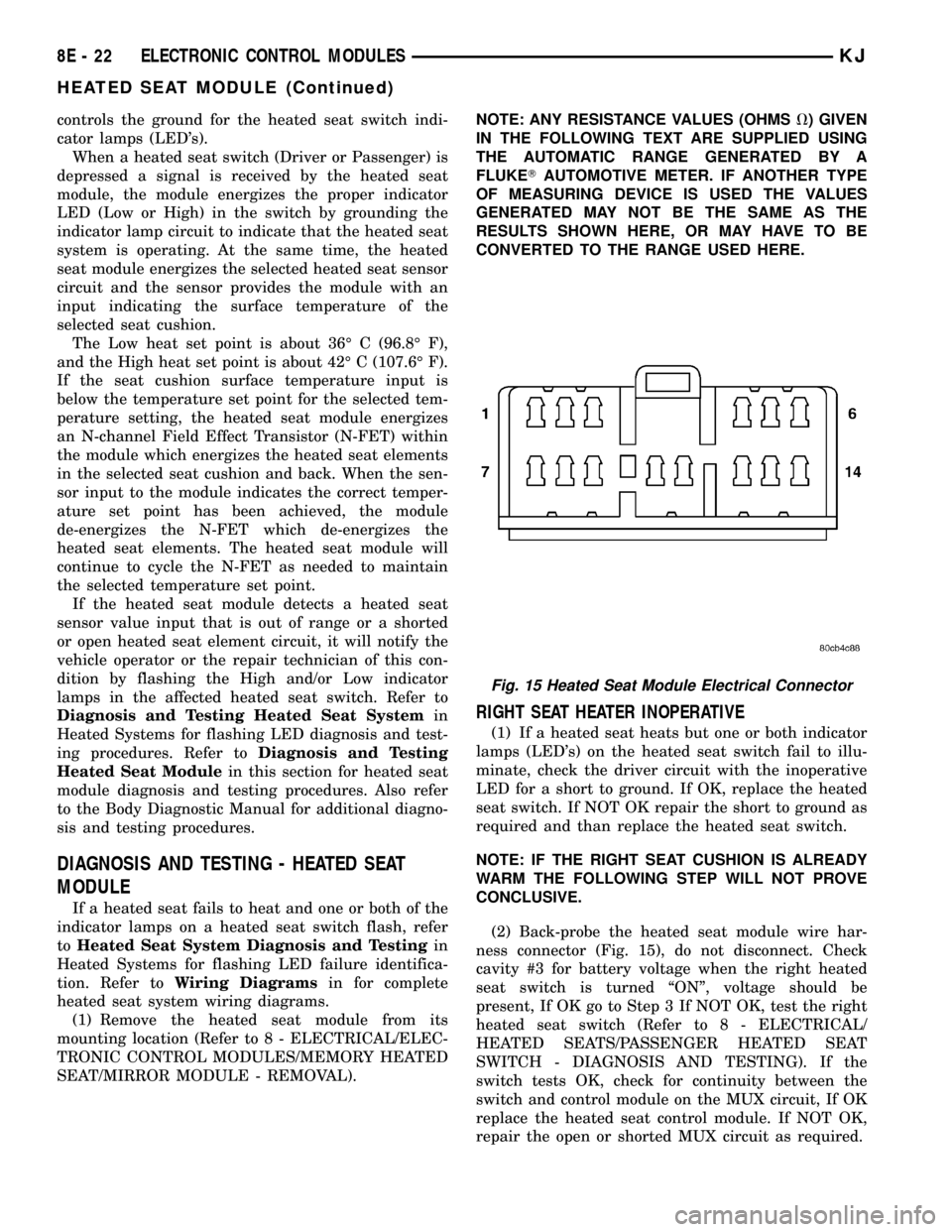
controls the ground for the heated seat switch indi-
cator lamps (LED's).
When a heated seat switch (Driver or Passenger) is
depressed a signal is received by the heated seat
module, the module energizes the proper indicator
LED (Low or High) in the switch by grounding the
indicator lamp circuit to indicate that the heated seat
system is operating. At the same time, the heated
seat module energizes the selected heated seat sensor
circuit and the sensor provides the module with an
input indicating the surface temperature of the
selected seat cushion.
The Low heat set point is about 36É C (96.8É F),
and the High heat set point is about 42É C (107.6É F).
If the seat cushion surface temperature input is
below the temperature set point for the selected tem-
perature setting, the heated seat module energizes
an N-channel Field Effect Transistor (N-FET) within
the module which energizes the heated seat elements
in the selected seat cushion and back. When the sen-
sor input to the module indicates the correct temper-
ature set point has been achieved, the module
de-energizes the N-FET which de-energizes the
heated seat elements. The heated seat module will
continue to cycle the N-FET as needed to maintain
the selected temperature set point.
If the heated seat module detects a heated seat
sensor value input that is out of range or a shorted
or open heated seat element circuit, it will notify the
vehicle operator or the repair technician of this con-
dition by flashing the High and/or Low indicator
lamps in the affected heated seat switch. Refer to
Diagnosis and Testing Heated Seat Systemin
Heated Systems for flashing LED diagnosis and test-
ing procedures. Refer toDiagnosis and Testing
Heated Seat Modulein this section for heated seat
module diagnosis and testing procedures. Also refer
to the Body Diagnostic Manual for additional diagno-
sis and testing procedures.
DIAGNOSIS AND TESTING - HEATED SEAT
MODULE
If a heated seat fails to heat and one or both of the
indicator lamps on a heated seat switch flash, refer
toHeated Seat System Diagnosis and Testingin
Heated Systems for flashing LED failure identifica-
tion. Refer toWiring Diagramsin for complete
heated seat system wiring diagrams.
(1) Remove the heated seat module from its
mounting location (Refer to 8 - ELECTRICAL/ELEC-
TRONIC CONTROL MODULES/MEMORY HEATED
SEAT/MIRROR MODULE - REMOVAL).NOTE: ANY RESISTANCE VALUES (OHMSV) GIVEN
IN THE FOLLOWING TEXT ARE SUPPLIED USING
THE AUTOMATIC RANGE GENERATED BY A
FLUKETAUTOMOTIVE METER. IF ANOTHER TYPE
OF MEASURING DEVICE IS USED THE VALUES
GENERATED MAY NOT BE THE SAME AS THE
RESULTS SHOWN HERE, OR MAY HAVE TO BE
CONVERTED TO THE RANGE USED HERE.
RIGHT SEAT HEATER INOPERATIVE
(1) If a heated seat heats but one or both indicator
lamps (LED's) on the heated seat switch fail to illu-
minate, check the driver circuit with the inoperative
LED for a short to ground. If OK, replace the heated
seat switch. If NOT OK repair the short to ground as
required and than replace the heated seat switch.
NOTE: IF THE RIGHT SEAT CUSHION IS ALREADY
WARM THE FOLLOWING STEP WILL NOT PROVE
CONCLUSIVE.
(2) Back-probe the heated seat module wire har-
ness connector (Fig. 15), do not disconnect. Check
cavity #3 for battery voltage when the right heated
seat switch is turned ªONº, voltage should be
present, If OK go to Step 3 If NOT OK, test the right
heated seat switch (Refer to 8 - ELECTRICAL/
HEATED SEATS/PASSENGER HEATED SEAT
SWITCH - DIAGNOSIS AND TESTING). If the
switch tests OK, check for continuity between the
switch and control module on the MUX circuit, If OK
replace the heated seat control module. If NOT OK,
repair the open or shorted MUX circuit as required.
Fig. 15 Heated Seat Module Electrical Connector
8E - 22 ELECTRONIC CONTROL MODULESKJ
HEATED SEAT MODULE (Continued)
Page 322 of 1803
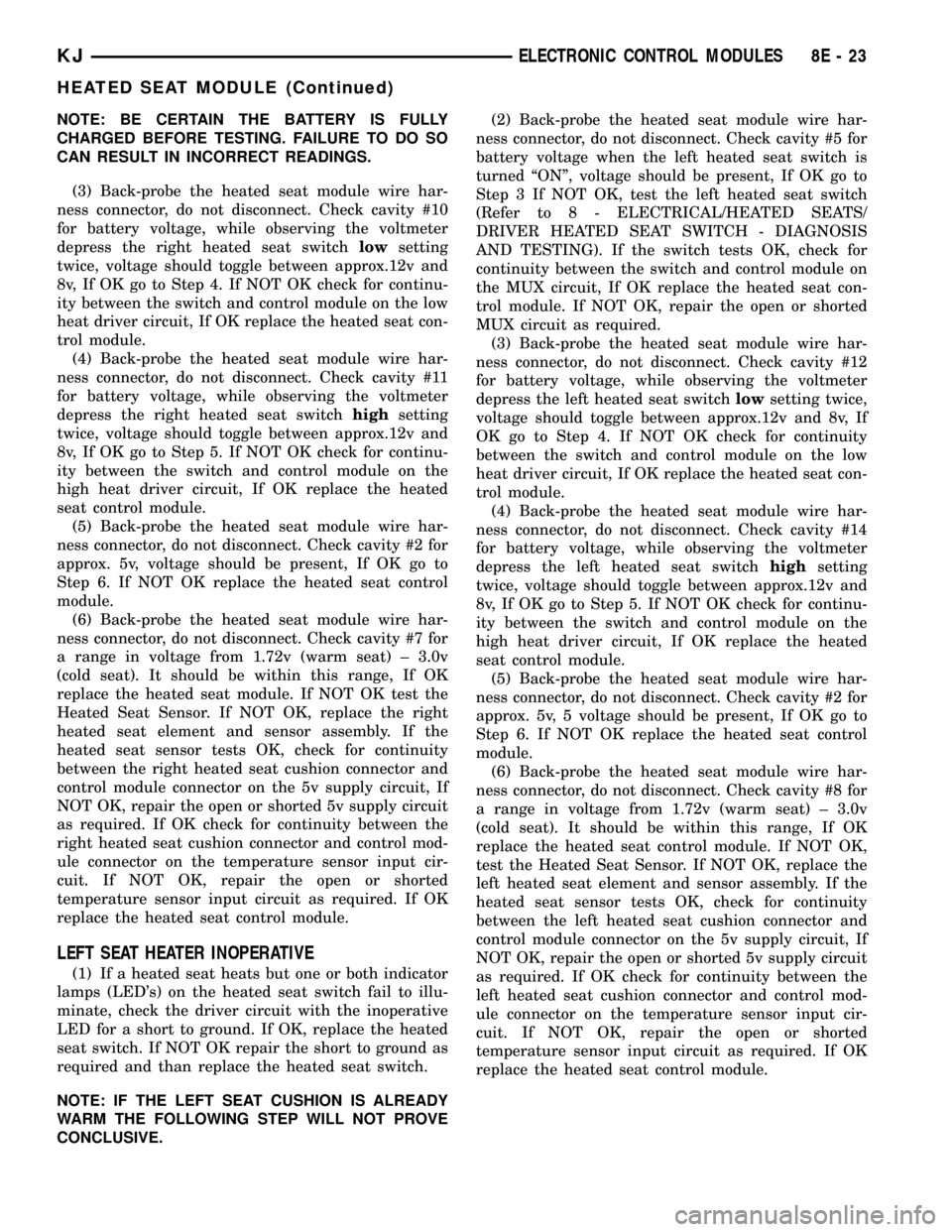
NOTE: BE CERTAIN THE BATTERY IS FULLY
CHARGED BEFORE TESTING. FAILURE TO DO SO
CAN RESULT IN INCORRECT READINGS.
(3) Back-probe the heated seat module wire har-
ness connector, do not disconnect. Check cavity #10
for battery voltage, while observing the voltmeter
depress the right heated seat switchlowsetting
twice, voltage should toggle between approx.12v and
8v, If OK go to Step 4. If NOT OK check for continu-
ity between the switch and control module on the low
heat driver circuit, If OK replace the heated seat con-
trol module.
(4) Back-probe the heated seat module wire har-
ness connector, do not disconnect. Check cavity #11
for battery voltage, while observing the voltmeter
depress the right heated seat switchhighsetting
twice, voltage should toggle between approx.12v and
8v, If OK go to Step 5. If NOT OK check for continu-
ity between the switch and control module on the
high heat driver circuit, If OK replace the heated
seat control module.
(5) Back-probe the heated seat module wire har-
ness connector, do not disconnect. Check cavity #2 for
approx. 5v, voltage should be present, If OK go to
Step 6. If NOT OK replace the heated seat control
module.
(6) Back-probe the heated seat module wire har-
ness connector, do not disconnect. Check cavity #7 for
a range in voltage from 1.72v (warm seat) ± 3.0v
(cold seat). It should be within this range, If OK
replace the heated seat module. If NOT OK test the
Heated Seat Sensor. If NOT OK, replace the right
heated seat element and sensor assembly. If the
heated seat sensor tests OK, check for continuity
between the right heated seat cushion connector and
control module connector on the 5v supply circuit, If
NOT OK, repair the open or shorted 5v supply circuit
as required. If OK check for continuity between the
right heated seat cushion connector and control mod-
ule connector on the temperature sensor input cir-
cuit. If NOT OK, repair the open or shorted
temperature sensor input circuit as required. If OK
replace the heated seat control module.
LEFT SEAT HEATER INOPERATIVE
(1) If a heated seat heats but one or both indicator
lamps (LED's) on the heated seat switch fail to illu-
minate, check the driver circuit with the inoperative
LED for a short to ground. If OK, replace the heated
seat switch. If NOT OK repair the short to ground as
required and than replace the heated seat switch.
NOTE: IF THE LEFT SEAT CUSHION IS ALREADY
WARM THE FOLLOWING STEP WILL NOT PROVE
CONCLUSIVE.(2) Back-probe the heated seat module wire har-
ness connector, do not disconnect. Check cavity #5 for
battery voltage when the left heated seat switch is
turned ªONº, voltage should be present, If OK go to
Step 3 If NOT OK, test the left heated seat switch
(Refer to 8 - ELECTRICAL/HEATED SEATS/
DRIVER HEATED SEAT SWITCH - DIAGNOSIS
AND TESTING). If the switch tests OK, check for
continuity between the switch and control module on
the MUX circuit, If OK replace the heated seat con-
trol module. If NOT OK, repair the open or shorted
MUX circuit as required.
(3) Back-probe the heated seat module wire har-
ness connector, do not disconnect. Check cavity #12
for battery voltage, while observing the voltmeter
depress the left heated seat switchlowsetting twice,
voltage should toggle between approx.12v and 8v, If
OK go to Step 4. If NOT OK check for continuity
between the switch and control module on the low
heat driver circuit, If OK replace the heated seat con-
trol module.
(4) Back-probe the heated seat module wire har-
ness connector, do not disconnect. Check cavity #14
for battery voltage, while observing the voltmeter
depress the left heated seat switchhighsetting
twice, voltage should toggle between approx.12v and
8v, If OK go to Step 5. If NOT OK check for continu-
ity between the switch and control module on the
high heat driver circuit, If OK replace the heated
seat control module.
(5) Back-probe the heated seat module wire har-
ness connector, do not disconnect. Check cavity #2 for
approx. 5v, 5 voltage should be present, If OK go to
Step 6. If NOT OK replace the heated seat control
module.
(6) Back-probe the heated seat module wire har-
ness connector, do not disconnect. Check cavity #8 for
a range in voltage from 1.72v (warm seat) ± 3.0v
(cold seat). It should be within this range, If OK
replace the heated seat control module. If NOT OK,
test the Heated Seat Sensor. If NOT OK, replace the
left heated seat element and sensor assembly. If the
heated seat sensor tests OK, check for continuity
between the left heated seat cushion connector and
control module connector on the 5v supply circuit, If
NOT OK, repair the open or shorted 5v supply circuit
as required. If OK check for continuity between the
left heated seat cushion connector and control mod-
ule connector on the temperature sensor input cir-
cuit. If NOT OK, repair the open or shorted
temperature sensor input circuit as required. If OK
replace the heated seat control module.
KJELECTRONIC CONTROL MODULES 8E - 23
HEATED SEAT MODULE (Continued)
Page 344 of 1803
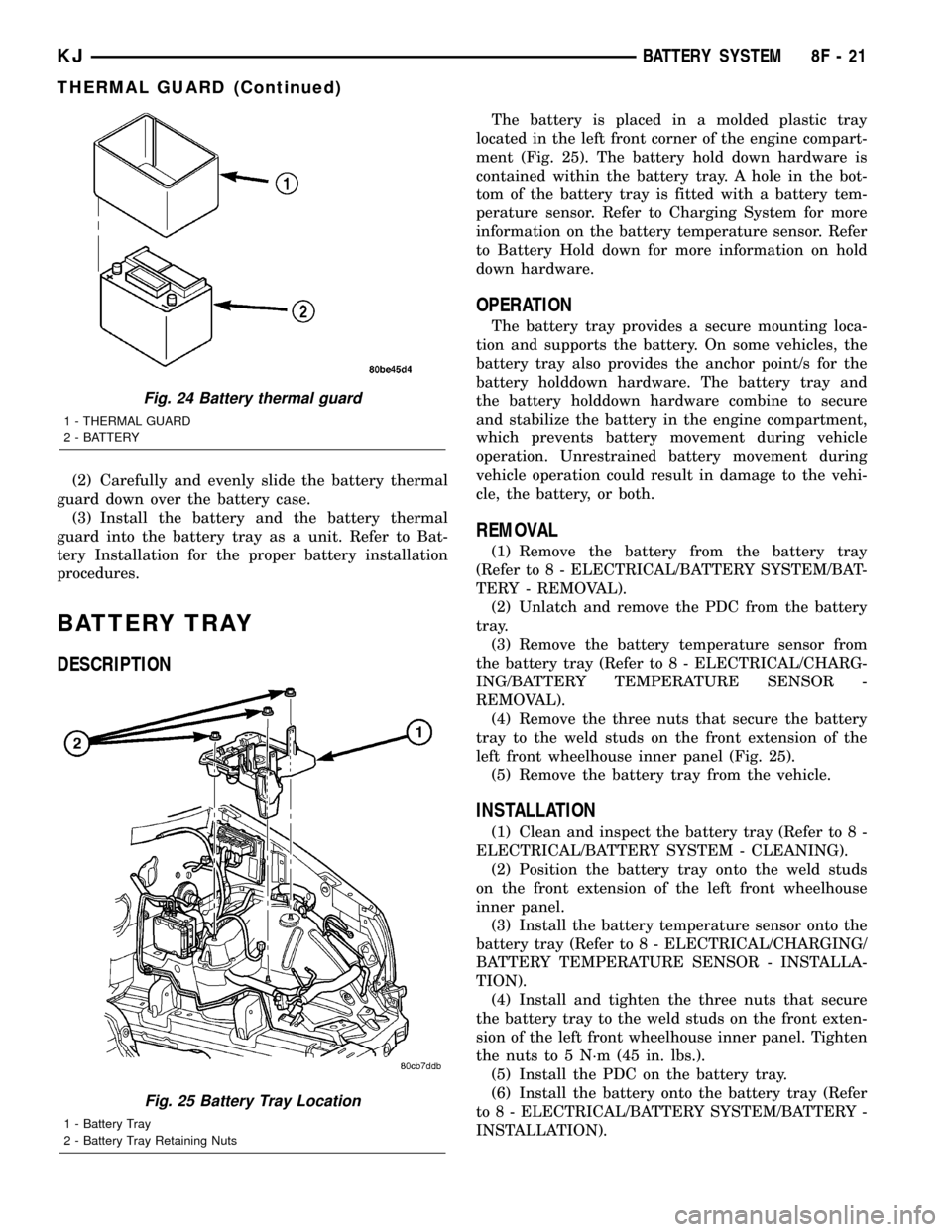
(2) Carefully and evenly slide the battery thermal
guard down over the battery case.
(3) Install the battery and the battery thermal
guard into the battery tray as a unit. Refer to Bat-
tery Installation for the proper battery installation
procedures.
BATTERY TRAY
DESCRIPTION
The battery is placed in a molded plastic tray
located in the left front corner of the engine compart-
ment (Fig. 25). The battery hold down hardware is
contained within the battery tray. A hole in the bot-
tom of the battery tray is fitted with a battery tem-
perature sensor. Refer to Charging System for more
information on the battery temperature sensor. Refer
to Battery Hold down for more information on hold
down hardware.
OPERATION
The battery tray provides a secure mounting loca-
tion and supports the battery. On some vehicles, the
battery tray also provides the anchor point/s for the
battery holddown hardware. The battery tray and
the battery holddown hardware combine to secure
and stabilize the battery in the engine compartment,
which prevents battery movement during vehicle
operation. Unrestrained battery movement during
vehicle operation could result in damage to the vehi-
cle, the battery, or both.
REMOVAL
(1) Remove the battery from the battery tray
(Refer to 8 - ELECTRICAL/BATTERY SYSTEM/BAT-
TERY - REMOVAL).
(2) Unlatch and remove the PDC from the battery
tray.
(3) Remove the battery temperature sensor from
the battery tray (Refer to 8 - ELECTRICAL/CHARG-
ING/BATTERY TEMPERATURE SENSOR -
REMOVAL).
(4) Remove the three nuts that secure the battery
tray to the weld studs on the front extension of the
left front wheelhouse inner panel (Fig. 25).
(5) Remove the battery tray from the vehicle.
INSTALLATION
(1) Clean and inspect the battery tray (Refer to 8 -
ELECTRICAL/BATTERY SYSTEM - CLEANING).
(2) Position the battery tray onto the weld studs
on the front extension of the left front wheelhouse
inner panel.
(3) Install the battery temperature sensor onto the
battery tray (Refer to 8 - ELECTRICAL/CHARGING/
BATTERY TEMPERATURE SENSOR - INSTALLA-
TION).
(4) Install and tighten the three nuts that secure
the battery tray to the weld studs on the front exten-
sion of the left front wheelhouse inner panel. Tighten
the nuts to 5 N´m (45 in. lbs.).
(5) Install the PDC on the battery tray.
(6) Install the battery onto the battery tray (Refer
to 8 - ELECTRICAL/BATTERY SYSTEM/BATTERY -
INSTALLATION).
Fig. 24 Battery thermal guard
1 - THERMAL GUARD
2 - BATTERY
Fig. 25 Battery Tray Location
1 - Battery Tray
2 - Battery Tray Retaining Nuts
KJBATTERY SYSTEM 8F - 21
THERMAL GUARD (Continued)
Page 345 of 1803
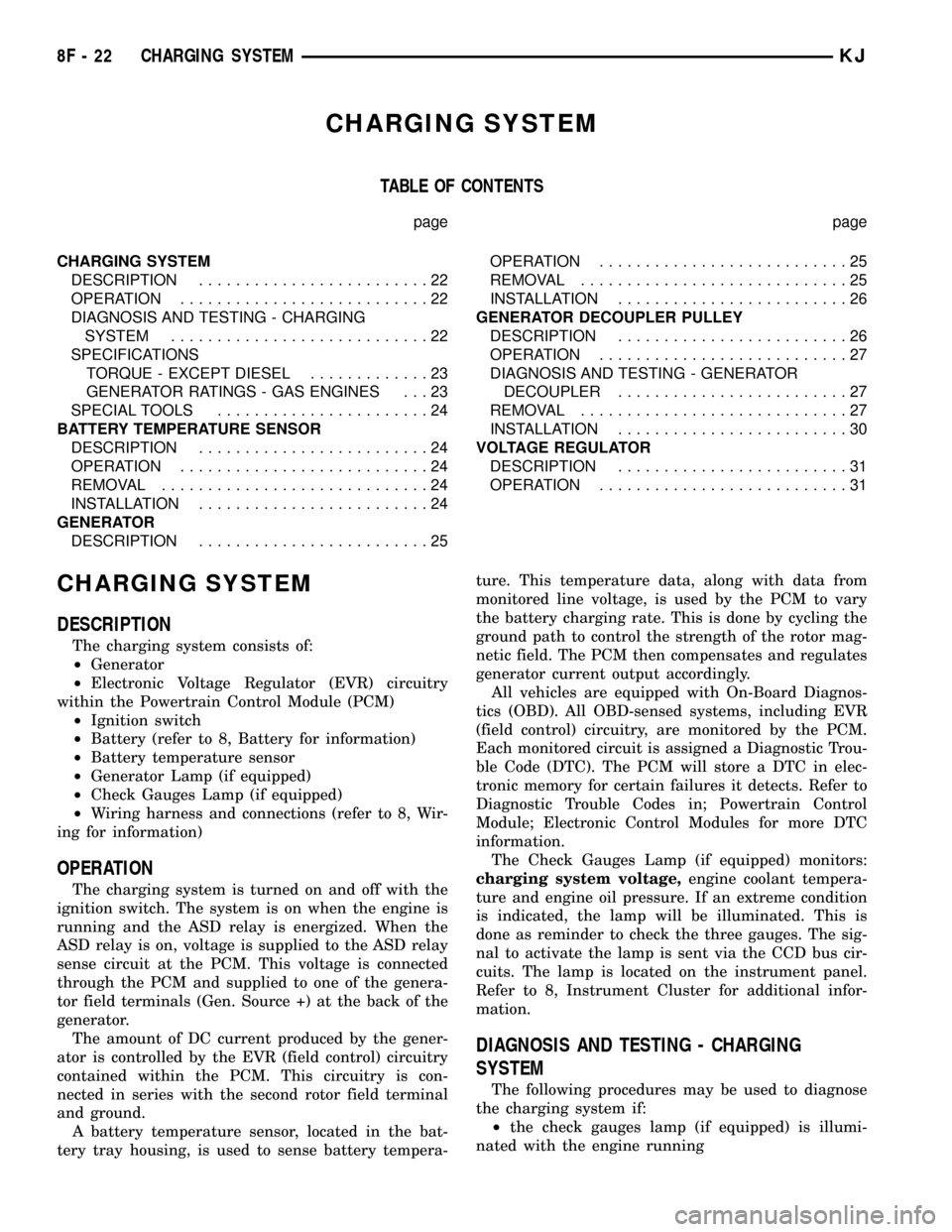
CHARGING SYSTEM
TABLE OF CONTENTS
page page
CHARGING SYSTEM
DESCRIPTION.........................22
OPERATION...........................22
DIAGNOSIS AND TESTING - CHARGING
SYSTEM............................22
SPECIFICATIONS
TORQUE - EXCEPT DIESEL.............23
GENERATOR RATINGS - GAS ENGINES . . . 23
SPECIAL TOOLS.......................24
BATTERY TEMPERATURE SENSOR
DESCRIPTION.........................24
OPERATION...........................24
REMOVAL.............................24
INSTALLATION.........................24
GENERATOR
DESCRIPTION.........................25OPERATION...........................25
REMOVAL.............................25
INSTALLATION.........................26
GENERATOR DECOUPLER PULLEY
DESCRIPTION.........................26
OPERATION...........................27
DIAGNOSIS AND TESTING - GENERATOR
DECOUPLER.........................27
REMOVAL.............................27
INSTALLATION.........................30
VOLTAGE REGULATOR
DESCRIPTION.........................31
OPERATION...........................31
CHARGING SYSTEM
DESCRIPTION
The charging system consists of:
²Generator
²Electronic Voltage Regulator (EVR) circuitry
within the Powertrain Control Module (PCM)
²Ignition switch
²Battery (refer to 8, Battery for information)
²Battery temperature sensor
²Generator Lamp (if equipped)
²Check Gauges Lamp (if equipped)
²Wiring harness and connections (refer to 8, Wir-
ing for information)
OPERATION
The charging system is turned on and off with the
ignition switch. The system is on when the engine is
running and the ASD relay is energized. When the
ASD relay is on, voltage is supplied to the ASD relay
sense circuit at the PCM. This voltage is connected
through the PCM and supplied to one of the genera-
tor field terminals (Gen. Source +) at the back of the
generator.
The amount of DC current produced by the gener-
ator is controlled by the EVR (field control) circuitry
contained within the PCM. This circuitry is con-
nected in series with the second rotor field terminal
and ground.
A battery temperature sensor, located in the bat-
tery tray housing, is used to sense battery tempera-ture. This temperature data, along with data from
monitored line voltage, is used by the PCM to vary
the battery charging rate. This is done by cycling the
ground path to control the strength of the rotor mag-
netic field. The PCM then compensates and regulates
generator current output accordingly.
All vehicles are equipped with On-Board Diagnos-
tics (OBD). All OBD-sensed systems, including EVR
(field control) circuitry, are monitored by the PCM.
Each monitored circuit is assigned a Diagnostic Trou-
ble Code (DTC). The PCM will store a DTC in elec-
tronic memory for certain failures it detects. Refer to
Diagnostic Trouble Codes in; Powertrain Control
Module; Electronic Control Modules for more DTC
information.
The Check Gauges Lamp (if equipped) monitors:
charging system voltage,engine coolant tempera-
ture and engine oil pressure. If an extreme condition
is indicated, the lamp will be illuminated. This is
done as reminder to check the three gauges. The sig-
nal to activate the lamp is sent via the CCD bus cir-
cuits. The lamp is located on the instrument panel.
Refer to 8, Instrument Cluster for additional infor-
mation.
DIAGNOSIS AND TESTING - CHARGING
SYSTEM
The following procedures may be used to diagnose
the charging system if:
²the check gauges lamp (if equipped) is illumi-
nated with the engine running
8F - 22 CHARGING SYSTEMKJ
Page 347 of 1803
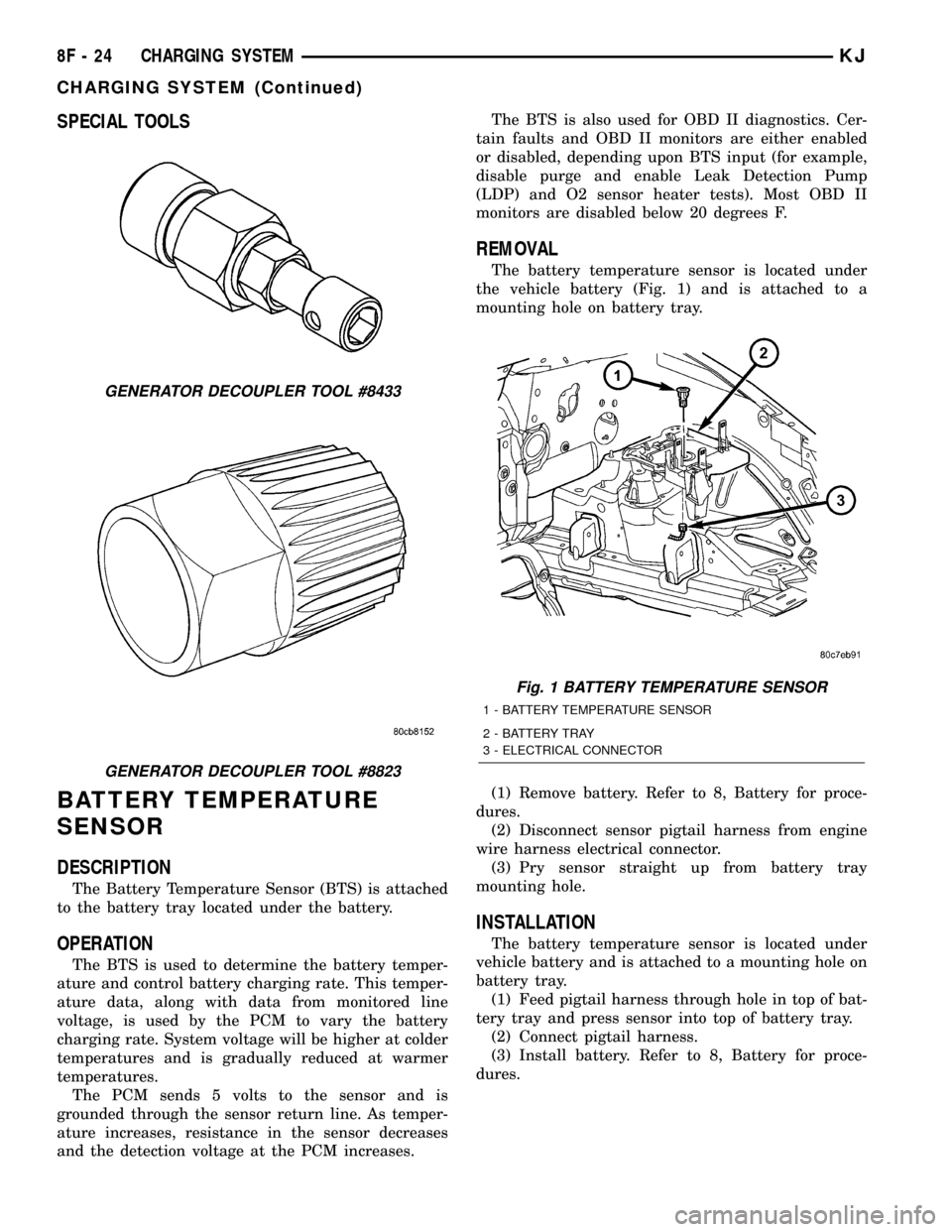
SPECIAL TOOLS
BATTERY TEMPERATURE
SENSOR
DESCRIPTION
The Battery Temperature Sensor (BTS) is attached
to the battery tray located under the battery.
OPERATION
The BTS is used to determine the battery temper-
ature and control battery charging rate. This temper-
ature data, along with data from monitored line
voltage, is used by the PCM to vary the battery
charging rate. System voltage will be higher at colder
temperatures and is gradually reduced at warmer
temperatures.
The PCM sends 5 volts to the sensor and is
grounded through the sensor return line. As temper-
ature increases, resistance in the sensor decreases
and the detection voltage at the PCM increases.The BTS is also used for OBD II diagnostics. Cer-
tain faults and OBD II monitors are either enabled
or disabled, depending upon BTS input (for example,
disable purge and enable Leak Detection Pump
(LDP) and O2 sensor heater tests). Most OBD II
monitors are disabled below 20 degrees F.
REMOVAL
The battery temperature sensor is located under
the vehicle battery (Fig. 1) and is attached to a
mounting hole on battery tray.
(1) Remove battery. Refer to 8, Battery for proce-
dures.
(2) Disconnect sensor pigtail harness from engine
wire harness electrical connector.
(3) Pry sensor straight up from battery tray
mounting hole.
INSTALLATION
The battery temperature sensor is located under
vehicle battery and is attached to a mounting hole on
battery tray.
(1) Feed pigtail harness through hole in top of bat-
tery tray and press sensor into top of battery tray.
(2) Connect pigtail harness.
(3) Install battery. Refer to 8, Battery for proce-
dures.
GENERATOR DECOUPLER TOOL #8433
GENERATOR DECOUPLER TOOL #8823
Fig. 1 BATTERY TEMPERATURE SENSOR
1 - BATTERY TEMPERATURE SENSOR
2 - BATTERY TRAY
3 - ELECTRICAL CONNECTOR
8F - 24 CHARGING SYSTEMKJ
CHARGING SYSTEM (Continued)
Page 354 of 1803
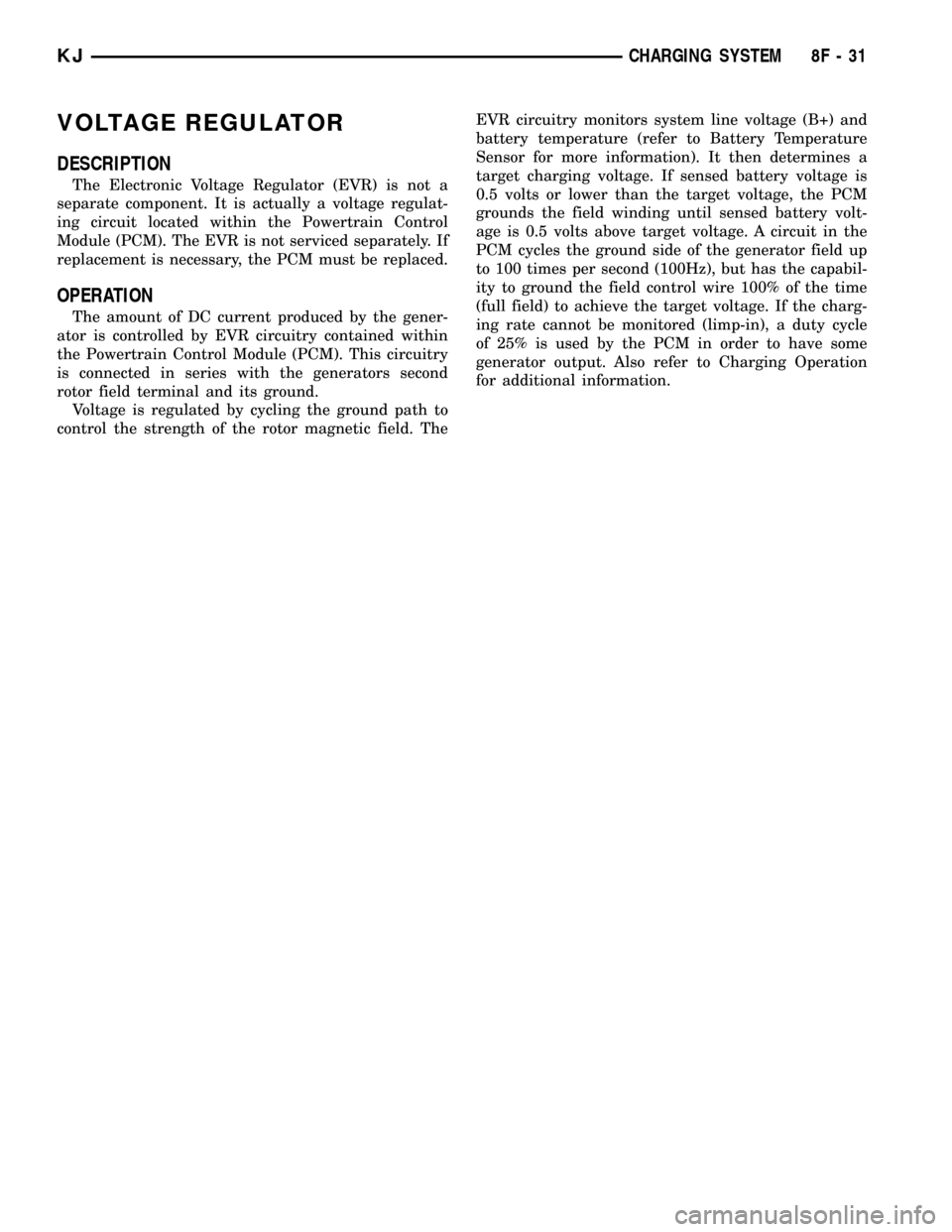
VOLTAGE REGULATOR
DESCRIPTION
The Electronic Voltage Regulator (EVR) is not a
separate component. It is actually a voltage regulat-
ing circuit located within the Powertrain Control
Module (PCM). The EVR is not serviced separately. If
replacement is necessary, the PCM must be replaced.
OPERATION
The amount of DC current produced by the gener-
ator is controlled by EVR circuitry contained within
the Powertrain Control Module (PCM). This circuitry
is connected in series with the generators second
rotor field terminal and its ground.
Voltage is regulated by cycling the ground path to
control the strength of the rotor magnetic field. TheEVR circuitry monitors system line voltage (B+) and
battery temperature (refer to Battery Temperature
Sensor for more information). It then determines a
target charging voltage. If sensed battery voltage is
0.5 volts or lower than the target voltage, the PCM
grounds the field winding until sensed battery volt-
age is 0.5 volts above target voltage. A circuit in the
PCM cycles the ground side of the generator field up
to 100 times per second (100Hz), but has the capabil-
ity to ground the field control wire 100% of the time
(full field) to achieve the target voltage. If the charg-
ing rate cannot be monitored (limp-in), a duty cycle
of 25% is used by the PCM in order to have some
generator output. Also refer to Charging Operation
for additional information.
KJCHARGING SYSTEM 8F - 31
Page 377 of 1803
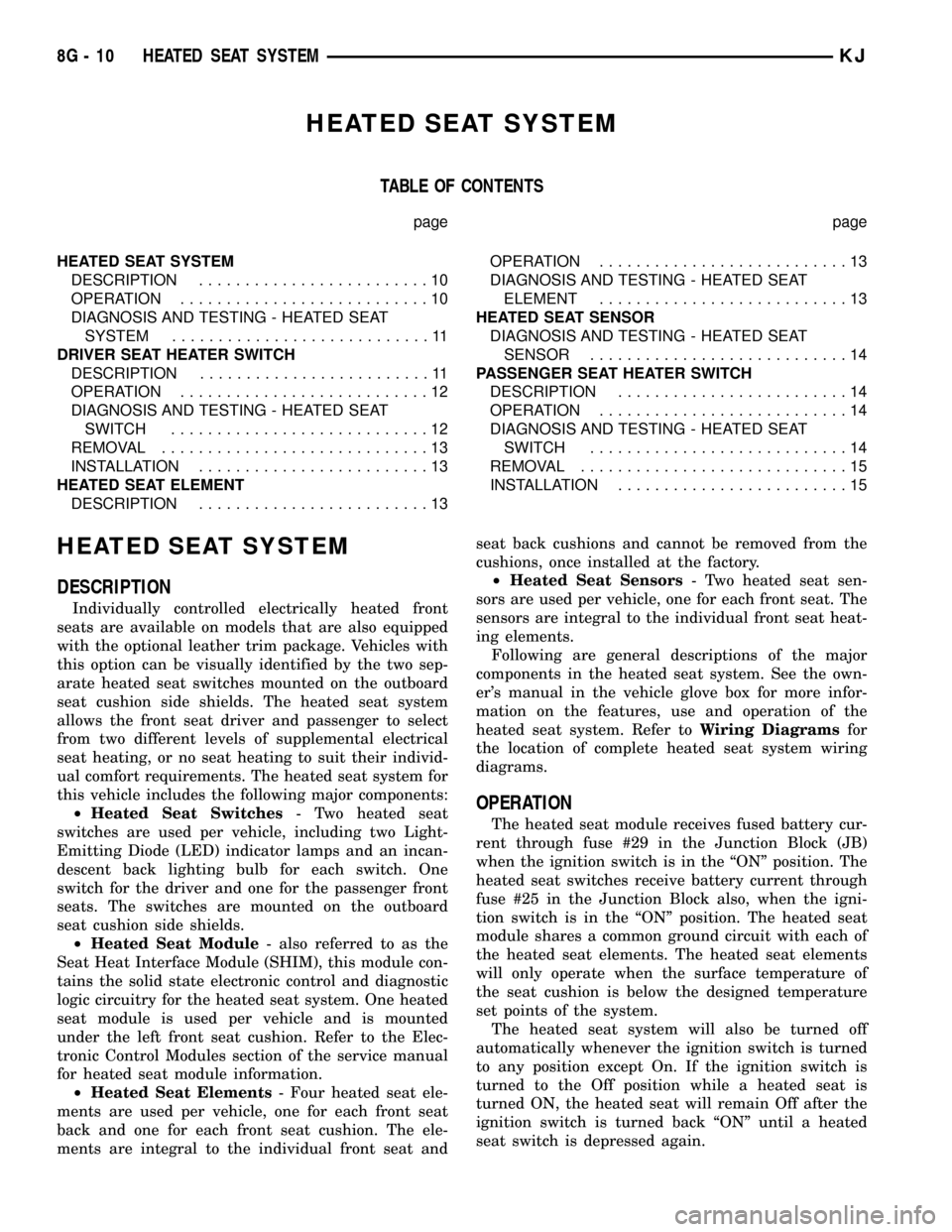
HEATED SEAT SYSTEM
TABLE OF CONTENTS
page page
HEATED SEAT SYSTEM
DESCRIPTION.........................10
OPERATION...........................10
DIAGNOSIS AND TESTING - HEATED SEAT
SYSTEM............................11
DRIVER SEAT HEATER SWITCH
DESCRIPTION.........................11
OPERATION...........................12
DIAGNOSIS AND TESTING - HEATED SEAT
SWITCH............................12
REMOVAL.............................13
INSTALLATION.........................13
HEATED SEAT ELEMENT
DESCRIPTION.........................13OPERATION...........................13
DIAGNOSIS AND TESTING - HEATED SEAT
ELEMENT...........................13
HEATED SEAT SENSOR
DIAGNOSIS AND TESTING - HEATED SEAT
SENSOR............................14
PASSENGER SEAT HEATER SWITCH
DESCRIPTION.........................14
OPERATION...........................14
DIAGNOSIS AND TESTING - HEATED SEAT
SWITCH............................14
REMOVAL.............................15
INSTALLATION.........................15
HEATED SEAT SYSTEM
DESCRIPTION
Individually controlled electrically heated front
seats are available on models that are also equipped
with the optional leather trim package. Vehicles with
this option can be visually identified by the two sep-
arate heated seat switches mounted on the outboard
seat cushion side shields. The heated seat system
allows the front seat driver and passenger to select
from two different levels of supplemental electrical
seat heating, or no seat heating to suit their individ-
ual comfort requirements. The heated seat system for
this vehicle includes the following major components:
²Heated Seat Switches- Two heated seat
switches are used per vehicle, including two Light-
Emitting Diode (LED) indicator lamps and an incan-
descent back lighting bulb for each switch. One
switch for the driver and one for the passenger front
seats. The switches are mounted on the outboard
seat cushion side shields.
²Heated Seat Module- also referred to as the
Seat Heat Interface Module (SHIM), this module con-
tains the solid state electronic control and diagnostic
logic circuitry for the heated seat system. One heated
seat module is used per vehicle and is mounted
under the left front seat cushion. Refer to the Elec-
tronic Control Modules section of the service manual
for heated seat module information.
²Heated Seat Elements- Four heated seat ele-
ments are used per vehicle, one for each front seat
back and one for each front seat cushion. The ele-
ments are integral to the individual front seat andseat back cushions and cannot be removed from the
cushions, once installed at the factory.
²Heated Seat Sensors- Two heated seat sen-
sors are used per vehicle, one for each front seat. The
sensors are integral to the individual front seat heat-
ing elements.
Following are general descriptions of the major
components in the heated seat system. See the own-
er's manual in the vehicle glove box for more infor-
mation on the features, use and operation of the
heated seat system. Refer toWiring Diagramsfor
the location of complete heated seat system wiring
diagrams.
OPERATION
The heated seat module receives fused battery cur-
rent through fuse #29 in the Junction Block (JB)
when the ignition switch is in the ªONº position. The
heated seat switches receive battery current through
fuse #25 in the Junction Block also, when the igni-
tion switch is in the ªONº position. The heated seat
module shares a common ground circuit with each of
the heated seat elements. The heated seat elements
will only operate when the surface temperature of
the seat cushion is below the designed temperature
set points of the system.
The heated seat system will also be turned off
automatically whenever the ignition switch is turned
to any position except On. If the ignition switch is
turned to the Off position while a heated seat is
turned ON, the heated seat will remain Off after the
ignition switch is turned back ªONº until a heated
seat switch is depressed again.
8G - 10 HEATED SEAT SYSTEMKJ
Page 378 of 1803
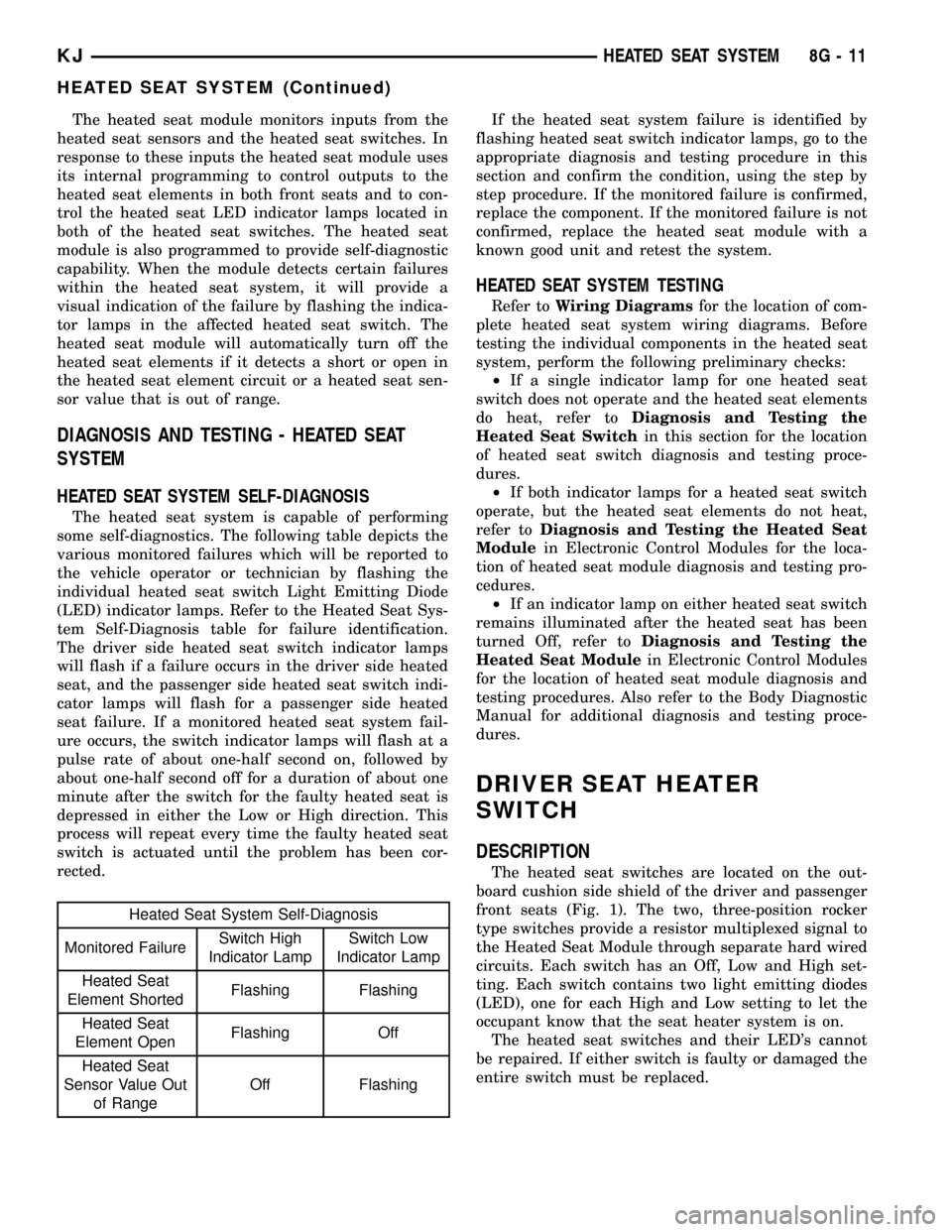
The heated seat module monitors inputs from the
heated seat sensors and the heated seat switches. In
response to these inputs the heated seat module uses
its internal programming to control outputs to the
heated seat elements in both front seats and to con-
trol the heated seat LED indicator lamps located in
both of the heated seat switches. The heated seat
module is also programmed to provide self-diagnostic
capability. When the module detects certain failures
within the heated seat system, it will provide a
visual indication of the failure by flashing the indica-
tor lamps in the affected heated seat switch. The
heated seat module will automatically turn off the
heated seat elements if it detects a short or open in
the heated seat element circuit or a heated seat sen-
sor value that is out of range.
DIAGNOSIS AND TESTING - HEATED SEAT
SYSTEM
HEATED SEAT SYSTEM SELF-DIAGNOSIS
The heated seat system is capable of performing
some self-diagnostics. The following table depicts the
various monitored failures which will be reported to
the vehicle operator or technician by flashing the
individual heated seat switch Light Emitting Diode
(LED) indicator lamps. Refer to the Heated Seat Sys-
tem Self-Diagnosis table for failure identification.
The driver side heated seat switch indicator lamps
will flash if a failure occurs in the driver side heated
seat, and the passenger side heated seat switch indi-
cator lamps will flash for a passenger side heated
seat failure. If a monitored heated seat system fail-
ure occurs, the switch indicator lamps will flash at a
pulse rate of about one-half second on, followed by
about one-half second off for a duration of about one
minute after the switch for the faulty heated seat is
depressed in either the Low or High direction. This
process will repeat every time the faulty heated seat
switch is actuated until the problem has been cor-
rected.
Heated Seat System Self-Diagnosis
Monitored FailureSwitch High
Indicator LampSwitch Low
Indicator Lamp
Heated Seat
Element ShortedFlashing Flashing
Heated Seat
Element OpenFlashing Off
Heated Seat
Sensor Value Out
of RangeOff FlashingIf the heated seat system failure is identified by
flashing heated seat switch indicator lamps, go to the
appropriate diagnosis and testing procedure in this
section and confirm the condition, using the step by
step procedure. If the monitored failure is confirmed,
replace the component. If the monitored failure is not
confirmed, replace the heated seat module with a
known good unit and retest the system.
HEATED SEAT SYSTEM TESTING
Refer toWiring Diagramsfor the location of com-
plete heated seat system wiring diagrams. Before
testing the individual components in the heated seat
system, perform the following preliminary checks:
²If a single indicator lamp for one heated seat
switch does not operate and the heated seat elements
do heat, refer toDiagnosis and Testing the
Heated Seat Switchin this section for the location
of heated seat switch diagnosis and testing proce-
dures.
²If both indicator lamps for a heated seat switch
operate, but the heated seat elements do not heat,
refer toDiagnosis and Testing the Heated Seat
Modulein Electronic Control Modules for the loca-
tion of heated seat module diagnosis and testing pro-
cedures.
²If an indicator lamp on either heated seat switch
remains illuminated after the heated seat has been
turned Off, refer toDiagnosis and Testing the
Heated Seat Modulein Electronic Control Modules
for the location of heated seat module diagnosis and
testing procedures. Also refer to the Body Diagnostic
Manual for additional diagnosis and testing proce-
dures.
DRIVER SEAT HEATER
SWITCH
DESCRIPTION
The heated seat switches are located on the out-
board cushion side shield of the driver and passenger
front seats (Fig. 1). The two, three-position rocker
type switches provide a resistor multiplexed signal to
the Heated Seat Module through separate hard wired
circuits. Each switch has an Off, Low and High set-
ting. Each switch contains two light emitting diodes
(LED), one for each High and Low setting to let the
occupant know that the seat heater system is on.
The heated seat switches and their LED's cannot
be repaired. If either switch is faulty or damaged the
entire switch must be replaced.
KJHEATED SEAT SYSTEM 8G - 11
HEATED SEAT SYSTEM (Continued)