OBD port JEEP LIBERTY 2002 KJ / 1.G Workshop Manual
[x] Cancel search | Manufacturer: JEEP, Model Year: 2002, Model line: LIBERTY, Model: JEEP LIBERTY 2002 KJ / 1.GPages: 1803, PDF Size: 62.3 MB
Page 325 of 1803
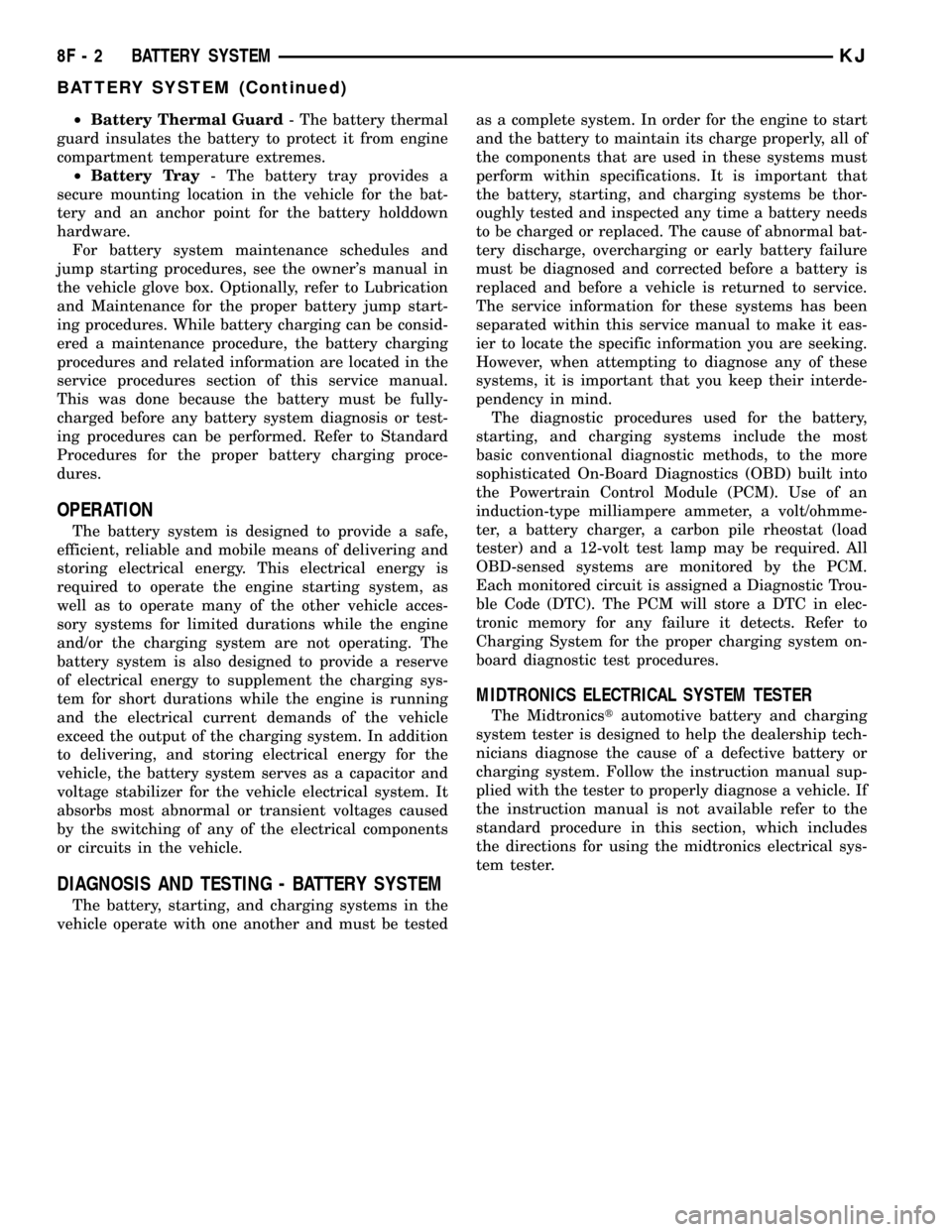
²Battery Thermal Guard- The battery thermal
guard insulates the battery to protect it from engine
compartment temperature extremes.
²Battery Tray- The battery tray provides a
secure mounting location in the vehicle for the bat-
tery and an anchor point for the battery holddown
hardware.
For battery system maintenance schedules and
jump starting procedures, see the owner's manual in
the vehicle glove box. Optionally, refer to Lubrication
and Maintenance for the proper battery jump start-
ing procedures. While battery charging can be consid-
ered a maintenance procedure, the battery charging
procedures and related information are located in the
service procedures section of this service manual.
This was done because the battery must be fully-
charged before any battery system diagnosis or test-
ing procedures can be performed. Refer to Standard
Procedures for the proper battery charging proce-
dures.
OPERATION
The battery system is designed to provide a safe,
efficient, reliable and mobile means of delivering and
storing electrical energy. This electrical energy is
required to operate the engine starting system, as
well as to operate many of the other vehicle acces-
sory systems for limited durations while the engine
and/or the charging system are not operating. The
battery system is also designed to provide a reserve
of electrical energy to supplement the charging sys-
tem for short durations while the engine is running
and the electrical current demands of the vehicle
exceed the output of the charging system. In addition
to delivering, and storing electrical energy for the
vehicle, the battery system serves as a capacitor and
voltage stabilizer for the vehicle electrical system. It
absorbs most abnormal or transient voltages caused
by the switching of any of the electrical components
or circuits in the vehicle.
DIAGNOSIS AND TESTING - BATTERY SYSTEM
The battery, starting, and charging systems in the
vehicle operate with one another and must be testedas a complete system. In order for the engine to start
and the battery to maintain its charge properly, all of
the components that are used in these systems must
perform within specifications. It is important that
the battery, starting, and charging systems be thor-
oughly tested and inspected any time a battery needs
to be charged or replaced. The cause of abnormal bat-
tery discharge, overcharging or early battery failure
must be diagnosed and corrected before a battery is
replaced and before a vehicle is returned to service.
The service information for these systems has been
separated within this service manual to make it eas-
ier to locate the specific information you are seeking.
However, when attempting to diagnose any of these
systems, it is important that you keep their interde-
pendency in mind.
The diagnostic procedures used for the battery,
starting, and charging systems include the most
basic conventional diagnostic methods, to the more
sophisticated On-Board Diagnostics (OBD) built into
the Powertrain Control Module (PCM). Use of an
induction-type milliampere ammeter, a volt/ohmme-
ter, a battery charger, a carbon pile rheostat (load
tester) and a 12-volt test lamp may be required. All
OBD-sensed systems are monitored by the PCM.
Each monitored circuit is assigned a Diagnostic Trou-
ble Code (DTC). The PCM will store a DTC in elec-
tronic memory for any failure it detects. Refer to
Charging System for the proper charging system on-
board diagnostic test procedures.
MIDTRONICS ELECTRICAL SYSTEM TESTER
The Midtronicstautomotive battery and charging
system tester is designed to help the dealership tech-
nicians diagnose the cause of a defective battery or
charging system. Follow the instruction manual sup-
plied with the tester to properly diagnose a vehicle. If
the instruction manual is not available refer to the
standard procedure in this section, which includes
the directions for using the midtronics electrical sys-
tem tester.
8F - 2 BATTERY SYSTEMKJ
BATTERY SYSTEM (Continued)
Page 355 of 1803
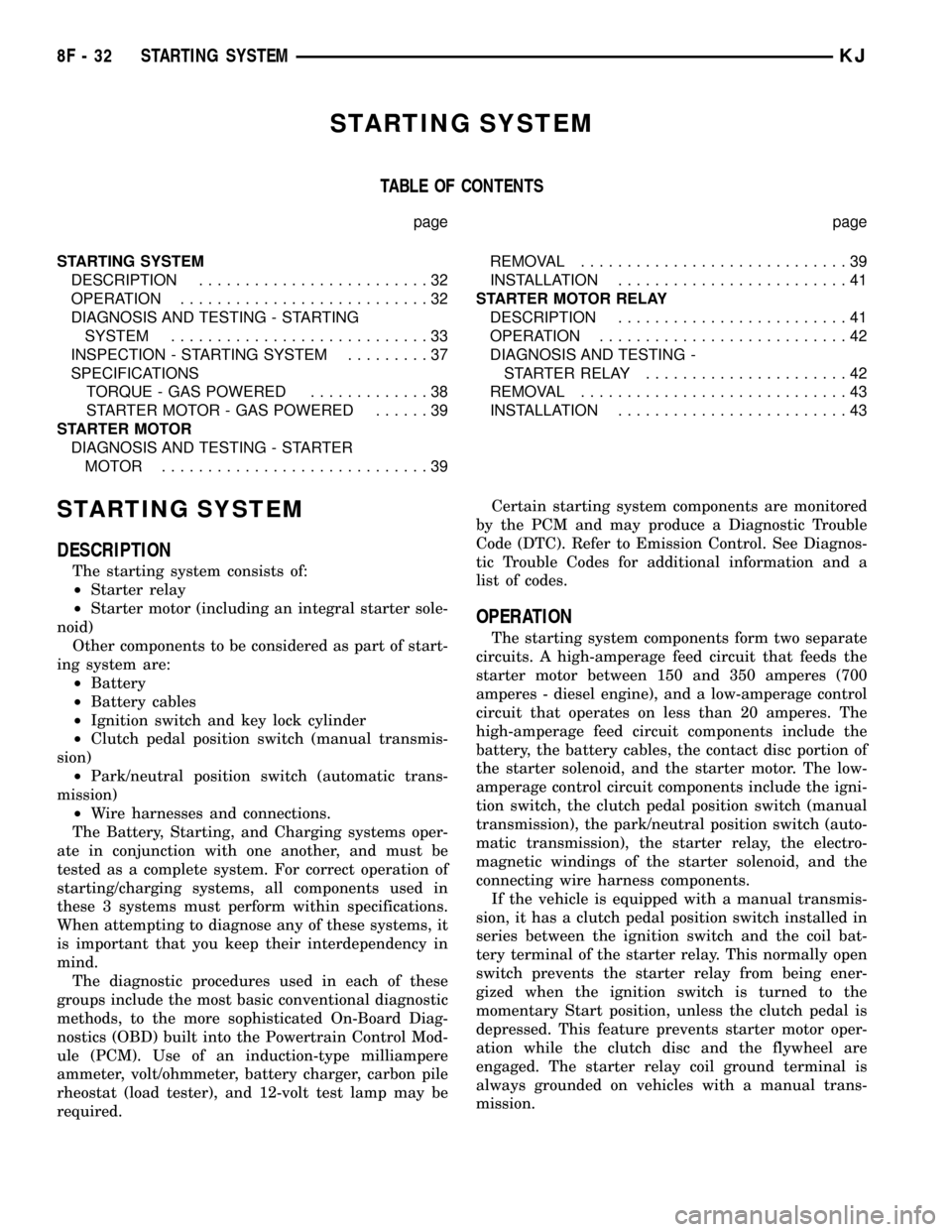
STARTING SYSTEM
TABLE OF CONTENTS
page page
STARTING SYSTEM
DESCRIPTION.........................32
OPERATION...........................32
DIAGNOSIS AND TESTING - STARTING
SYSTEM............................33
INSPECTION - STARTING SYSTEM.........37
SPECIFICATIONS
TORQUE - GAS POWERED.............38
STARTER MOTOR - GAS POWERED......39
STARTER MOTOR
DIAGNOSIS AND TESTING - STARTER
MOTOR .............................39REMOVAL.............................39
INSTALLATION.........................41
STARTER MOTOR RELAY
DESCRIPTION.........................41
OPERATION...........................42
DIAGNOSIS AND TESTING -
STARTER RELAY......................42
REMOVAL.............................43
INSTALLATION.........................43
STARTING SYSTEM
DESCRIPTION
The starting system consists of:
²Starter relay
²Starter motor (including an integral starter sole-
noid)
Other components to be considered as part of start-
ing system are:
²Battery
²Battery cables
²Ignition switch and key lock cylinder
²Clutch pedal position switch (manual transmis-
sion)
²Park/neutral position switch (automatic trans-
mission)
²Wire harnesses and connections.
The Battery, Starting, and Charging systems oper-
ate in conjunction with one another, and must be
tested as a complete system. For correct operation of
starting/charging systems, all components used in
these 3 systems must perform within specifications.
When attempting to diagnose any of these systems, it
is important that you keep their interdependency in
mind.
The diagnostic procedures used in each of these
groups include the most basic conventional diagnostic
methods, to the more sophisticated On-Board Diag-
nostics (OBD) built into the Powertrain Control Mod-
ule (PCM). Use of an induction-type milliampere
ammeter, volt/ohmmeter, battery charger, carbon pile
rheostat (load tester), and 12-volt test lamp may be
required.Certain starting system components are monitored
by the PCM and may produce a Diagnostic Trouble
Code (DTC). Refer to Emission Control. See Diagnos-
tic Trouble Codes for additional information and a
list of codes.
OPERATION
The starting system components form two separate
circuits. A high-amperage feed circuit that feeds the
starter motor between 150 and 350 amperes (700
amperes - diesel engine), and a low-amperage control
circuit that operates on less than 20 amperes. The
high-amperage feed circuit components include the
battery, the battery cables, the contact disc portion of
the starter solenoid, and the starter motor. The low-
amperage control circuit components include the igni-
tion switch, the clutch pedal position switch (manual
transmission), the park/neutral position switch (auto-
matic transmission), the starter relay, the electro-
magnetic windings of the starter solenoid, and the
connecting wire harness components.
If the vehicle is equipped with a manual transmis-
sion, it has a clutch pedal position switch installed in
series between the ignition switch and the coil bat-
tery terminal of the starter relay. This normally open
switch prevents the starter relay from being ener-
gized when the ignition switch is turned to the
momentary Start position, unless the clutch pedal is
depressed. This feature prevents starter motor oper-
ation while the clutch disc and the flywheel are
engaged. The starter relay coil ground terminal is
always grounded on vehicles with a manual trans-
mission.
8F - 32 STARTING SYSTEMKJ
Page 427 of 1803
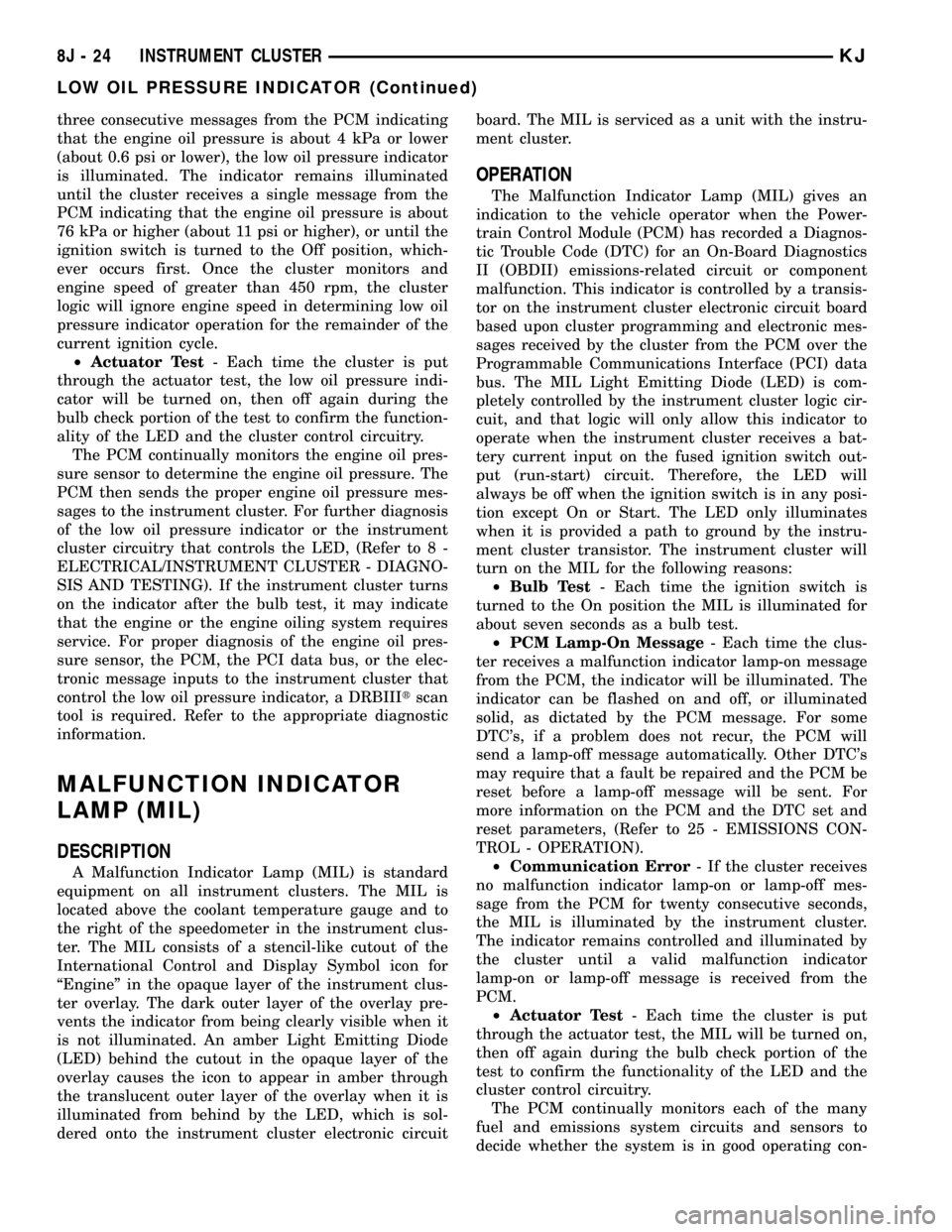
three consecutive messages from the PCM indicating
that the engine oil pressure is about 4 kPa or lower
(about 0.6 psi or lower), the low oil pressure indicator
is illuminated. The indicator remains illuminated
until the cluster receives a single message from the
PCM indicating that the engine oil pressure is about
76 kPa or higher (about 11 psi or higher), or until the
ignition switch is turned to the Off position, which-
ever occurs first. Once the cluster monitors and
engine speed of greater than 450 rpm, the cluster
logic will ignore engine speed in determining low oil
pressure indicator operation for the remainder of the
current ignition cycle.
²Actuator Test- Each time the cluster is put
through the actuator test, the low oil pressure indi-
cator will be turned on, then off again during the
bulb check portion of the test to confirm the function-
ality of the LED and the cluster control circuitry.
The PCM continually monitors the engine oil pres-
sure sensor to determine the engine oil pressure. The
PCM then sends the proper engine oil pressure mes-
sages to the instrument cluster. For further diagnosis
of the low oil pressure indicator or the instrument
cluster circuitry that controls the LED, (Refer to 8 -
ELECTRICAL/INSTRUMENT CLUSTER - DIAGNO-
SIS AND TESTING). If the instrument cluster turns
on the indicator after the bulb test, it may indicate
that the engine or the engine oiling system requires
service. For proper diagnosis of the engine oil pres-
sure sensor, the PCM, the PCI data bus, or the elec-
tronic message inputs to the instrument cluster that
control the low oil pressure indicator, a DRBIIItscan
tool is required. Refer to the appropriate diagnostic
information.
MALFUNCTION INDICATOR
LAMP (MIL)
DESCRIPTION
A Malfunction Indicator Lamp (MIL) is standard
equipment on all instrument clusters. The MIL is
located above the coolant temperature gauge and to
the right of the speedometer in the instrument clus-
ter. The MIL consists of a stencil-like cutout of the
International Control and Display Symbol icon for
ªEngineº in the opaque layer of the instrument clus-
ter overlay. The dark outer layer of the overlay pre-
vents the indicator from being clearly visible when it
is not illuminated. An amber Light Emitting Diode
(LED) behind the cutout in the opaque layer of the
overlay causes the icon to appear in amber through
the translucent outer layer of the overlay when it is
illuminated from behind by the LED, which is sol-
dered onto the instrument cluster electronic circuitboard. The MIL is serviced as a unit with the instru-
ment cluster.
OPERATION
The Malfunction Indicator Lamp (MIL) gives an
indication to the vehicle operator when the Power-
train Control Module (PCM) has recorded a Diagnos-
tic Trouble Code (DTC) for an On-Board Diagnostics
II (OBDII) emissions-related circuit or component
malfunction. This indicator is controlled by a transis-
tor on the instrument cluster electronic circuit board
based upon cluster programming and electronic mes-
sages received by the cluster from the PCM over the
Programmable Communications Interface (PCI) data
bus. The MIL Light Emitting Diode (LED) is com-
pletely controlled by the instrument cluster logic cir-
cuit, and that logic will only allow this indicator to
operate when the instrument cluster receives a bat-
tery current input on the fused ignition switch out-
put (run-start) circuit. Therefore, the LED will
always be off when the ignition switch is in any posi-
tion except On or Start. The LED only illuminates
when it is provided a path to ground by the instru-
ment cluster transistor. The instrument cluster will
turn on the MIL for the following reasons:
²Bulb Test- Each time the ignition switch is
turned to the On position the MIL is illuminated for
about seven seconds as a bulb test.
²PCM Lamp-On Message- Each time the clus-
ter receives a malfunction indicator lamp-on message
from the PCM, the indicator will be illuminated. The
indicator can be flashed on and off, or illuminated
solid, as dictated by the PCM message. For some
DTC's, if a problem does not recur, the PCM will
send a lamp-off message automatically. Other DTC's
may require that a fault be repaired and the PCM be
reset before a lamp-off message will be sent. For
more information on the PCM and the DTC set and
reset parameters, (Refer to 25 - EMISSIONS CON-
TROL - OPERATION).
²Communication Error- If the cluster receives
no malfunction indicator lamp-on or lamp-off mes-
sage from the PCM for twenty consecutive seconds,
the MIL is illuminated by the instrument cluster.
The indicator remains controlled and illuminated by
the cluster until a valid malfunction indicator
lamp-on or lamp-off message is received from the
PCM.
²Actuator Test- Each time the cluster is put
through the actuator test, the MIL will be turned on,
then off again during the bulb check portion of the
test to confirm the functionality of the LED and the
cluster control circuitry.
The PCM continually monitors each of the many
fuel and emissions system circuits and sensors to
decide whether the system is in good operating con-
8J - 24 INSTRUMENT CLUSTERKJ
LOW OIL PRESSURE INDICATOR (Continued)
Page 637 of 1803
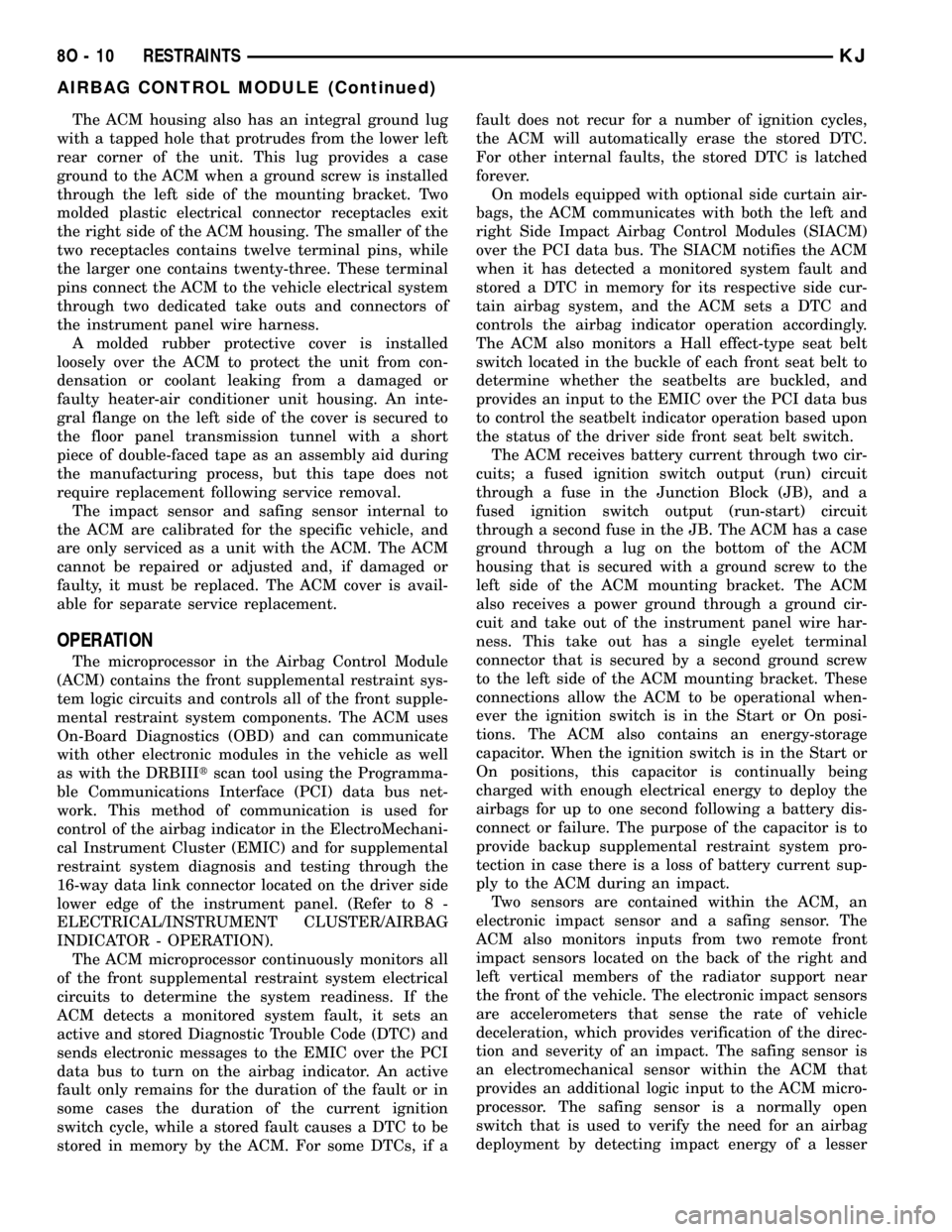
The ACM housing also has an integral ground lug
with a tapped hole that protrudes from the lower left
rear corner of the unit. This lug provides a case
ground to the ACM when a ground screw is installed
through the left side of the mounting bracket. Two
molded plastic electrical connector receptacles exit
the right side of the ACM housing. The smaller of the
two receptacles contains twelve terminal pins, while
the larger one contains twenty-three. These terminal
pins connect the ACM to the vehicle electrical system
through two dedicated take outs and connectors of
the instrument panel wire harness.
A molded rubber protective cover is installed
loosely over the ACM to protect the unit from con-
densation or coolant leaking from a damaged or
faulty heater-air conditioner unit housing. An inte-
gral flange on the left side of the cover is secured to
the floor panel transmission tunnel with a short
piece of double-faced tape as an assembly aid during
the manufacturing process, but this tape does not
require replacement following service removal.
The impact sensor and safing sensor internal to
the ACM are calibrated for the specific vehicle, and
are only serviced as a unit with the ACM. The ACM
cannot be repaired or adjusted and, if damaged or
faulty, it must be replaced. The ACM cover is avail-
able for separate service replacement.
OPERATION
The microprocessor in the Airbag Control Module
(ACM) contains the front supplemental restraint sys-
tem logic circuits and controls all of the front supple-
mental restraint system components. The ACM uses
On-Board Diagnostics (OBD) and can communicate
with other electronic modules in the vehicle as well
as with the DRBIIItscan tool using the Programma-
ble Communications Interface (PCI) data bus net-
work. This method of communication is used for
control of the airbag indicator in the ElectroMechani-
cal Instrument Cluster (EMIC) and for supplemental
restraint system diagnosis and testing through the
16-way data link connector located on the driver side
lower edge of the instrument panel. (Refer to 8 -
ELECTRICAL/INSTRUMENT CLUSTER/AIRBAG
INDICATOR - OPERATION).
The ACM microprocessor continuously monitors all
of the front supplemental restraint system electrical
circuits to determine the system readiness. If the
ACM detects a monitored system fault, it sets an
active and stored Diagnostic Trouble Code (DTC) and
sends electronic messages to the EMIC over the PCI
data bus to turn on the airbag indicator. An active
fault only remains for the duration of the fault or in
some cases the duration of the current ignition
switch cycle, while a stored fault causes a DTC to be
stored in memory by the ACM. For some DTCs, if afault does not recur for a number of ignition cycles,
the ACM will automatically erase the stored DTC.
For other internal faults, the stored DTC is latched
forever.
On models equipped with optional side curtain air-
bags, the ACM communicates with both the left and
right Side Impact Airbag Control Modules (SIACM)
over the PCI data bus. The SIACM notifies the ACM
when it has detected a monitored system fault and
stored a DTC in memory for its respective side cur-
tain airbag system, and the ACM sets a DTC and
controls the airbag indicator operation accordingly.
The ACM also monitors a Hall effect-type seat belt
switch located in the buckle of each front seat belt to
determine whether the seatbelts are buckled, and
provides an input to the EMIC over the PCI data bus
to control the seatbelt indicator operation based upon
the status of the driver side front seat belt switch.
The ACM receives battery current through two cir-
cuits; a fused ignition switch output (run) circuit
through a fuse in the Junction Block (JB), and a
fused ignition switch output (run-start) circuit
through a second fuse in the JB. The ACM has a case
ground through a lug on the bottom of the ACM
housing that is secured with a ground screw to the
left side of the ACM mounting bracket. The ACM
also receives a power ground through a ground cir-
cuit and take out of the instrument panel wire har-
ness. This take out has a single eyelet terminal
connector that is secured by a second ground screw
to the left side of the ACM mounting bracket. These
connections allow the ACM to be operational when-
ever the ignition switch is in the Start or On posi-
tions. The ACM also contains an energy-storage
capacitor. When the ignition switch is in the Start or
On positions, this capacitor is continually being
charged with enough electrical energy to deploy the
airbags for up to one second following a battery dis-
connect or failure. The purpose of the capacitor is to
provide backup supplemental restraint system pro-
tection in case there is a loss of battery current sup-
ply to the ACM during an impact.
Two sensors are contained within the ACM, an
electronic impact sensor and a safing sensor. The
ACM also monitors inputs from two remote front
impact sensors located on the back of the right and
left vertical members of the radiator support near
the front of the vehicle. The electronic impact sensors
are accelerometers that sense the rate of vehicle
deceleration, which provides verification of the direc-
tion and severity of an impact. The safing sensor is
an electromechanical sensor within the ACM that
provides an additional logic input to the ACM micro-
processor. The safing sensor is a normally open
switch that is used to verify the need for an airbag
deployment by detecting impact energy of a lesser
8O - 10 RESTRAINTSKJ
AIRBAG CONTROL MODULE (Continued)
Page 1728 of 1803
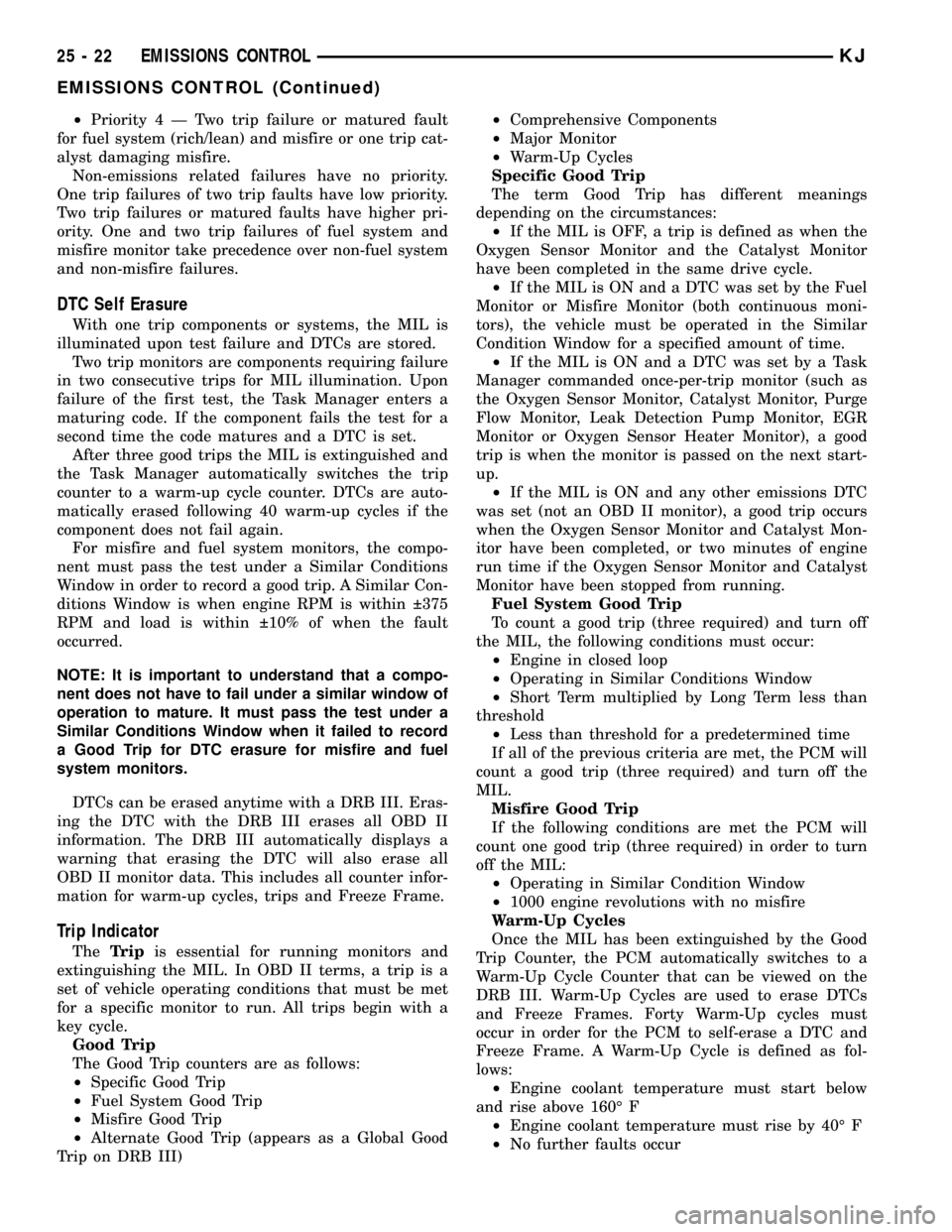
²Priority4ÐTwotrip failure or matured fault
for fuel system (rich/lean) and misfire or one trip cat-
alyst damaging misfire.
Non-emissions related failures have no priority.
One trip failures of two trip faults have low priority.
Two trip failures or matured faults have higher pri-
ority. One and two trip failures of fuel system and
misfire monitor take precedence over non-fuel system
and non-misfire failures.
DTC Self Erasure
With one trip components or systems, the MIL is
illuminated upon test failure and DTCs are stored.
Two trip monitors are components requiring failure
in two consecutive trips for MIL illumination. Upon
failure of the first test, the Task Manager enters a
maturing code. If the component fails the test for a
second time the code matures and a DTC is set.
After three good trips the MIL is extinguished and
the Task Manager automatically switches the trip
counter to a warm-up cycle counter. DTCs are auto-
matically erased following 40 warm-up cycles if the
component does not fail again.
For misfire and fuel system monitors, the compo-
nent must pass the test under a Similar Conditions
Window in order to record a good trip. A Similar Con-
ditions Window is when engine RPM is within 375
RPM and load is within 10% of when the fault
occurred.
NOTE: It is important to understand that a compo-
nent does not have to fail under a similar window of
operation to mature. It must pass the test under a
Similar Conditions Window when it failed to record
a Good Trip for DTC erasure for misfire and fuel
system monitors.
DTCs can be erased anytime with a DRB III. Eras-
ing the DTC with the DRB III erases all OBD II
information. The DRB III automatically displays a
warning that erasing the DTC will also erase all
OBD II monitor data. This includes all counter infor-
mation for warm-up cycles, trips and Freeze Frame.
Trip Indicator
TheTripis essential for running monitors and
extinguishing the MIL. In OBD II terms, a trip is a
set of vehicle operating conditions that must be met
for a specific monitor to run. All trips begin with a
key cycle.
Good Trip
The Good Trip counters are as follows:
²Specific Good Trip
²Fuel System Good Trip
²Misfire Good Trip
²Alternate Good Trip (appears as a Global Good
Trip on DRB III)²Comprehensive Components
²Major Monitor
²Warm-Up Cycles
Specific Good Trip
The term Good Trip has different meanings
depending on the circumstances:
²If the MIL is OFF, a trip is defined as when the
Oxygen Sensor Monitor and the Catalyst Monitor
have been completed in the same drive cycle.
²If the MIL is ON and a DTC was set by the Fuel
Monitor or Misfire Monitor (both continuous moni-
tors), the vehicle must be operated in the Similar
Condition Window for a specified amount of time.
²If the MIL is ON and a DTC was set by a Task
Manager commanded once-per-trip monitor (such as
the Oxygen Sensor Monitor, Catalyst Monitor, Purge
Flow Monitor, Leak Detection Pump Monitor, EGR
Monitor or Oxygen Sensor Heater Monitor), a good
trip is when the monitor is passed on the next start-
up.
²If the MIL is ON and any other emissions DTC
was set (not an OBD II monitor), a good trip occurs
when the Oxygen Sensor Monitor and Catalyst Mon-
itor have been completed, or two minutes of engine
run time if the Oxygen Sensor Monitor and Catalyst
Monitor have been stopped from running.
Fuel System Good Trip
To count a good trip (three required) and turn off
the MIL, the following conditions must occur:
²Engine in closed loop
²Operating in Similar Conditions Window
²Short Term multiplied by Long Term less than
threshold
²Less than threshold for a predetermined time
If all of the previous criteria are met, the PCM will
count a good trip (three required) and turn off the
MIL.
Misfire Good Trip
If the following conditions are met the PCM will
count one good trip (three required) in order to turn
off the MIL:
²Operating in Similar Condition Window
²1000 engine revolutions with no misfire
Warm-Up Cycles
Once the MIL has been extinguished by the Good
Trip Counter, the PCM automatically switches to a
Warm-Up Cycle Counter that can be viewed on the
DRB III. Warm-Up Cycles are used to erase DTCs
and Freeze Frames. Forty Warm-Up cycles must
occur in order for the PCM to self-erase a DTC and
Freeze Frame. A Warm-Up Cycle is defined as fol-
lows:
²Engine coolant temperature must start below
and rise above 160É F
²Engine coolant temperature must rise by 40É F
²No further faults occur
25 - 22 EMISSIONS CONTROLKJ
EMISSIONS CONTROL (Continued)
Page 1746 of 1803
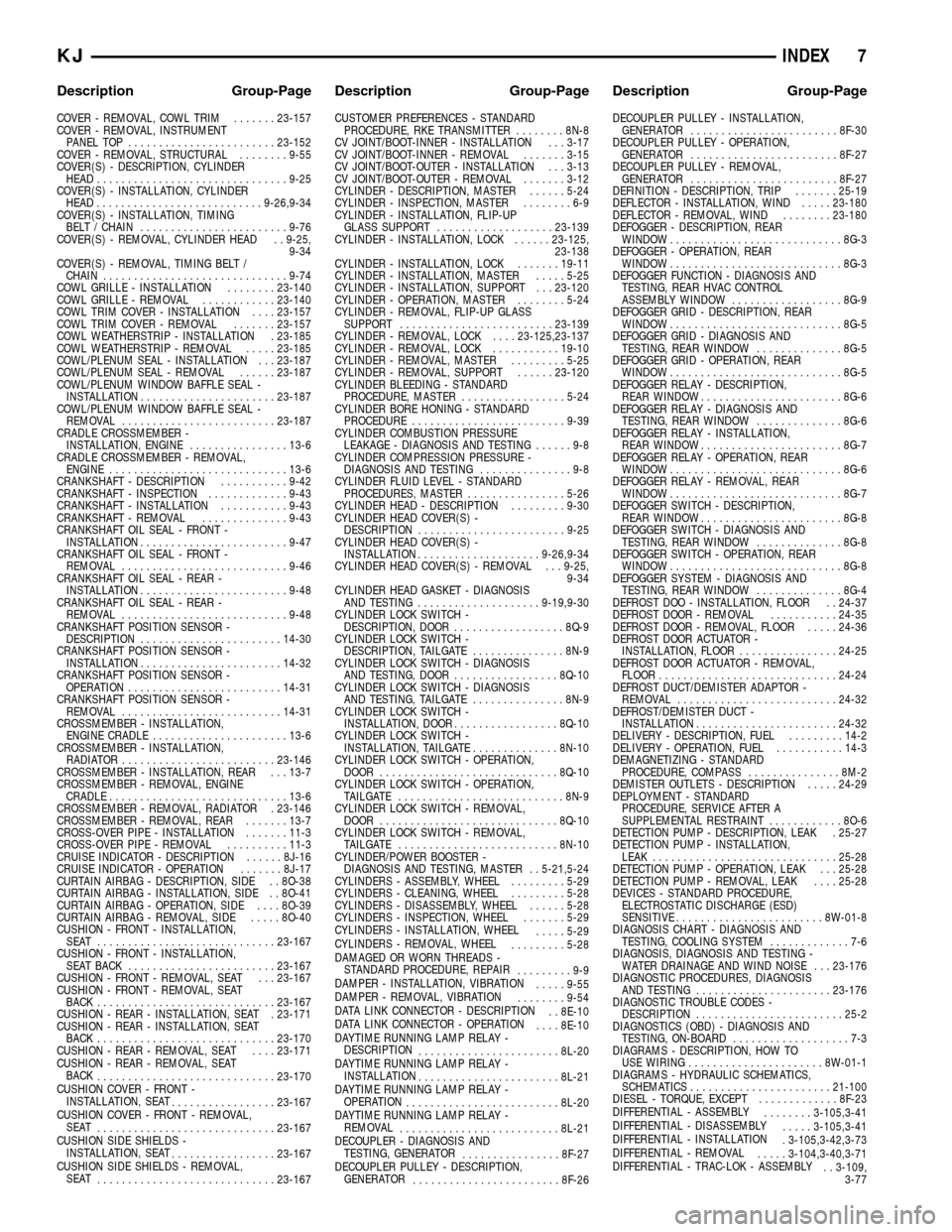
COVER - REMOVAL, COWL TRIM.......23-157
COVER - REMOVAL, INSTRUMENT
PANEL TOP........................23-152
COVER - REMOVAL, STRUCTURAL........9-55
COVER(S) - DESCRIPTION, CYLINDER
HEAD...............................9-25
COVER(S) - INSTALLATION, CYLINDER
HEAD...........................9-26,9-34
COVER(S) - INSTALLATION, TIMING
BELT / CHAIN........................9-76
COVER(S) - REMOVAL, CYLINDER HEAD . . 9-25,
9-34
COVER(S) - REMOVAL, TIMING BELT /
CHAIN..............................9-74
COWL GRILLE - INSTALLATION........23-140
COWL GRILLE - REMOVAL............23-140
COWL TRIM COVER - INSTALLATION....23-157
COWL TRIM COVER - REMOVAL.......23-157
COWL WEATHERSTRIP - INSTALLATION . 23-185
COWL WEATHERSTRIP - REMOVAL.....23-185
COWL/PLENUM SEAL - INSTALLATION . . . 23-187
COWL/PLENUM SEAL - REMOVAL......23-187
COWL/PLENUM WINDOW BAFFLE SEAL -
INSTALLATION......................23-187
COWL/PLENUM WINDOW BAFFLE SEAL -
REMOVAL.........................23-187
CRADLE CROSSMEMBER -
INSTALLATION, ENGINE................13-6
CRADLE CROSSMEMBER - REMOVAL,
ENGINE.............................13-6
CRANKSHAFT - DESCRIPTION...........9-42
CRANKSHAFT - INSPECTION.............9-43
CRANKSHAFT - INSTALLATION...........9-43
CRANKSHAFT - REMOVAL..............9-43
CRANKSHAFT OIL SEAL - FRONT -
INSTALLATION........................9-47
CRANKSHAFT OIL SEAL - FRONT -
REMOVAL...........................9-46
CRANKSHAFT OIL SEAL - REAR -
INSTALLATION........................9-48
CRANKSHAFT OIL SEAL - REAR -
REMOVAL...........................9-48
CRANKSHAFT POSITION SENSOR -
DESCRIPTION.......................14-30
CRANKSHAFT POSITION SENSOR -
INSTALLATION.......................14-32
CRANKSHAFT POSITION SENSOR -
OPERATION.........................14-31
CRANKSHAFT POSITION SENSOR -
REMOVAL..........................14-31
CROSSMEMBER - INSTALLATION,
ENGINE CRADLE......................13-6
CROSSMEMBER - INSTALLATION,
RADIATOR.........................23-146
CROSSMEMBER - INSTALLATION, REAR . . . 13-7
CROSSMEMBER - REMOVAL, ENGINE
CRADLE.............................13-6
CROSSMEMBER - REMOVAL, RADIATOR . 23-146
CROSSMEMBER - REMOVAL, REAR.......13-7
CROSS-OVER PIPE - INSTALLATION.......11-3
CROSS-OVER PIPE - REMOVAL..........11-3
CRUISE INDICATOR - DESCRIPTION......8J-16
CRUISE INDICATOR - OPERATION.......8J-17
CURTAIN AIRBAG - DESCRIPTION, SIDE . . 8O-38
CURTAIN AIRBAG - INSTALLATION, SIDE . . 8O-41
CURTAIN AIRBAG - OPERATION, SIDE....8O-39
CURTAIN AIRBAG - REMOVAL, SIDE.....8O-40
CUSHION - FRONT - INSTALLATION,
SEAT .............................23-167
CUSHION - FRONT - INSTALLATION,
SEAT BACK........................23-167
CUSHION - FRONT - REMOVAL, SEAT . . . 23-167
CUSHION - FRONT - REMOVAL, SEAT
BACK.............................23-167
CUSHION - REAR - INSTALLATION, SEAT . 23-171
CUSHION - REAR - INSTALLATION, SEAT
BACK.............................23-170
CUSHION - REAR - REMOVAL, SEAT....23-171
CUSHION - REAR - REMOVAL, SEAT
BACK
.............................23-170
CUSHION COVER - FRONT -
INSTALLATION, SEAT
.................23-167
CUSHION COVER - FRONT - REMOVAL,
SEAT
.............................23-167
CUSHION SIDE SHIELDS -
INSTALLATION, SEAT
.................23-167
CUSHION SIDE SHIELDS - REMOVAL,
SEAT
.............................23-167CUSTOMER PREFERENCES - STANDARD
PROCEDURE, RKE TRANSMITTER........8N-8
CV JOINT/BOOT-INNER - INSTALLATION . . . 3-17
CV JOINT/BOOT-INNER - REMOVAL.......3-15
CV JOINT/BOOT-OUTER - INSTALLATION . . . 3-13
CV JOINT/BOOT-OUTER - REMOVAL.......3-12
CYLINDER - DESCRIPTION, MASTER......5-24
CYLINDER - INSPECTION, MASTER........6-9
CYLINDER - INSTALLATION, FLIP-UP
GLASS SUPPORT...................23-139
CYLINDER - INSTALLATION, LOCK......23-125,
23-138
CYLINDER - INSTALLATION, LOCK.......19-11
CYLINDER - INSTALLATION, MASTER.....5-25
CYLINDER - INSTALLATION, SUPPORT . . . 23-120
CYLINDER - OPERATION, MASTER........5-24
CYLINDER - REMOVAL, FLIP-UP GLASS
SUPPORT.........................23-139
CYLINDER - REMOVAL, LOCK....23-125,23-137
CYLINDER - REMOVAL, LOCK...........19-10
CYLINDER - REMOVAL, MASTER.........5-25
CYLINDER - REMOVAL, SUPPORT......23-120
CYLINDER BLEEDING - STANDARD
PROCEDURE, MASTER.................5-24
CYLINDER BORE HONING - STANDARD
PROCEDURE.........................9-39
CYLINDER COMBUSTION PRESSURE
LEAKAGE - DIAGNOSIS AND TESTING......9-8
CYLINDER COMPRESSION PRESSURE -
DIAGNOSIS AND TESTING...............9-8
CYLINDER FLUID LEVEL - STANDARD
PROCEDURES, MASTER................5-26
CYLINDER HEAD - DESCRIPTION.........9-30
CYLINDER HEAD COVER(S) -
DESCRIPTION........................9-25
CYLINDER HEAD COVER(S) -
INSTALLATION....................9-26,9-34
CYLINDER HEAD COVER(S) - REMOVAL . . . 9-25,
9-34
CYLINDER HEAD GASKET - DIAGNOSIS
AND TESTING....................9-19,9-30
CYLINDER LOCK SWITCH -
DESCRIPTION, DOOR..................8Q-9
CYLINDER LOCK SWITCH -
DESCRIPTION, TAILGATE...............8N-9
CYLINDER LOCK SWITCH - DIAGNOSIS
AND TESTING, DOOR.................8Q-10
CYLINDER LOCK SWITCH - DIAGNOSIS
AND TESTING, TAILGATE...............8N-9
CYLINDER LOCK SWITCH -
INSTALLATION, DOOR.................8Q-10
CYLINDER LOCK SWITCH -
INSTALLATION, TAILGATE..............8N-10
CYLINDER LOCK SWITCH - OPERATION,
DOOR.............................8Q-10
CYLINDER LOCK SWITCH - OPERATION,
TAILGATE...........................8N-9
CYLINDER LOCK SWITCH - REMOVAL,
DOOR.............................8Q-10
CYLINDER LOCK SWITCH - REMOVAL,
TAILGATE..........................8N-10
CYLINDER/POWER BOOSTER -
DIAGNOSIS AND TESTING, MASTER . . 5-21,5-24
CYLINDERS - ASSEMBLY, WHEEL.........5-29
CYLINDERS - CLEANING, WHEEL.........5-28
CYLINDERS - DISASSEMBLY, WHEEL......5-28
CYLINDERS - INSPECTION, WHEEL.......5-29
CYLINDERS - INSTALLATION, WHEEL
.....5-29
CYLINDERS - REMOVAL, WHEEL
.........5-28
DAMAGED OR WORN THREADS -
STANDARD PROCEDURE, REPAIR
.........9-9
DAMPER - INSTALLATION, VIBRATION
.....9-55
DAMPER - REMOVAL, VIBRATION
........9-54
DATA LINK CONNECTOR - DESCRIPTION
. . 8E-10
DATA LINK CONNECTOR - OPERATION
....8E-10
DAYTIME RUNNING LAMP RELAY -
DESCRIPTION
.......................8L-20
DAYTIME RUNNING LAMP RELAY -
INSTALLATION
.......................8L-21
DAYTIME RUNNING LAMP RELAY -
OPERATION
.........................8L-20
DAYTIME RUNNING LAMP RELAY -
REMOVAL
..........................8L-21
DECOUPLER - DIAGNOSIS AND
TESTING, GENERATOR
................8F-27
DECOUPLER PULLEY - DESCRIPTION,
GENERATOR
........................8F-26DECOUPLER PULLEY - INSTALLATION,
GENERATOR........................8F-30
DECOUPLER PULLEY - OPERATION,
GENERATOR........................8F-27
DECOUPLER PULLEY - REMOVAL,
GENERATOR........................8F-27
DEFINITION - DESCRIPTION, TRIP.......25-19
DEFLECTOR - INSTALLATION, WIND.....23-180
DEFLECTOR - REMOVAL, WIND........23-180
DEFOGGER - DESCRIPTION, REAR
WINDOW............................8G-3
DEFOGGER - OPERATION, REAR
WINDOW............................8G-3
DEFOGGER FUNCTION - DIAGNOSIS AND
TESTING, REAR HVAC CONTROL
ASSEMBLY WINDOW..................8G-9
DEFOGGER GRID - DESCRIPTION, REAR
WINDOW............................8G-5
DEFOGGER GRID - DIAGNOSIS AND
TESTING, REAR WINDOW..............8G-5
DEFOGGER GRID - OPERATION, REAR
WINDOW............................8G-5
DEFOGGER RELAY - DESCRIPTION,
REAR WINDOW.......................8G-6
DEFOGGER RELAY - DIAGNOSIS AND
TESTING, REAR WINDOW..............8G-6
DEFOGGER RELAY - INSTALLATION,
REAR WINDOW.......................8G-7
DEFOGGER RELAY - OPERATION, REAR
WINDOW............................8G-6
DEFOGGER RELAY - REMOVAL, REAR
WINDOW............................8G-7
DEFOGGER SWITCH - DESCRIPTION,
REAR WINDOW.......................8G-8
DEFOGGER SWITCH - DIAGNOSIS AND
TESTING, REAR WINDOW..............8G-8
DEFOGGER SWITCH - OPERATION, REAR
WINDOW............................8G-8
DEFOGGER SYSTEM - DIAGNOSIS AND
TESTING, REAR WINDOW..............8G-4
DEFROST DOO - INSTALLATION, FLOOR . . 24-37
DEFROST DOOR - REMOVAL...........24-35
DEFROST DOOR - REMOVAL, FLOOR.....24-36
DEFROST DOOR ACTUATOR -
INSTALLATION, FLOOR................24-25
DEFROST DOOR ACTUATOR - REMOVAL,
FLOOR.............................24-24
DEFROST DUCT/DEMISTER ADAPTOR -
REMOVAL..........................24-32
DEFROST/DEMISTER DUCT -
INSTALLATION.......................24-32
DELIVERY - DESCRIPTION, FUEL.........14-2
DELIVERY - OPERATION, FUEL...........14-3
DEMAGNETIZING - STANDARD
PROCEDURE, COMPASS...............8M-2
DEMISTER OUTLETS - DESCRIPTION.....24-29
DEPLOYMENT - STANDARD
PROCEDURE, SERVICE AFTER A
SUPPLEMENTAL RESTRAINT............8O-6
DETECTION PUMP - DESCRIPTION, LEAK . 25-27
DETECTION PUMP - INSTALLATION,
LEAK..............................25-28
DETECTION PUMP - OPERATION, LEAK . . . 25-28
DETECTION PUMP - REMOVAL, LEAK....25-28
DEVICES - STANDARD PROCEDURE,
ELECTROSTATIC DISCHARGE (ESD)
SENSITIVE........................8W-01-8
DIAGNOSIS CHART - DIAGNOSIS AND
TESTING, COOLING SYSTEM.............7-6
DIAGNOSIS, DIAGNOSIS AND TESTING -
WATER DRAINAGE AND WIND NOISE . . . 23-176
DIAGNOSTIC PROCEDURES, DIAGNOSIS
AND TESTING......................23-176
DIAGNOSTIC TROUBLE CODES -
DESCRIPTION........................25-2
DIAGNOSTICS (OBD) - DIAGNOSIS AND
TESTING, ON-BOARD...................7-3
DIAGRAMS - DESCRIPTION, HOW TO
USE WIRING......................8W-01-1
DIAGRAMS - HYDRAULIC SCHEMATICS,
SCHEMATICS.......................21-100
DIESEL - TORQUE, EXCEPT.............8F-23
DIFFERENTIAL - ASSEMBLY
........3-105,3-41
DIFFERENTIAL - DISASSEMBLY
.....3-105,3-41
DIFFERENTIAL - INSTALLATION
. 3-105,3-42,3-73
DIFFERENTIAL - REMOVAL
.....3-104,3-40,3-71
DIFFERENTIAL - TRAC-LOK - ASSEMBLY
. . 3-109,
3-77
KJINDEX 7
Description Group-Page Description Group-Page Description Group-Page