instrument panel JEEP LIBERTY 2002 KJ / 1.G Workshop Manual
[x] Cancel search | Manufacturer: JEEP, Model Year: 2002, Model line: LIBERTY, Model: JEEP LIBERTY 2002 KJ / 1.GPages: 1803, PDF Size: 62.3 MB
Page 7 of 1803
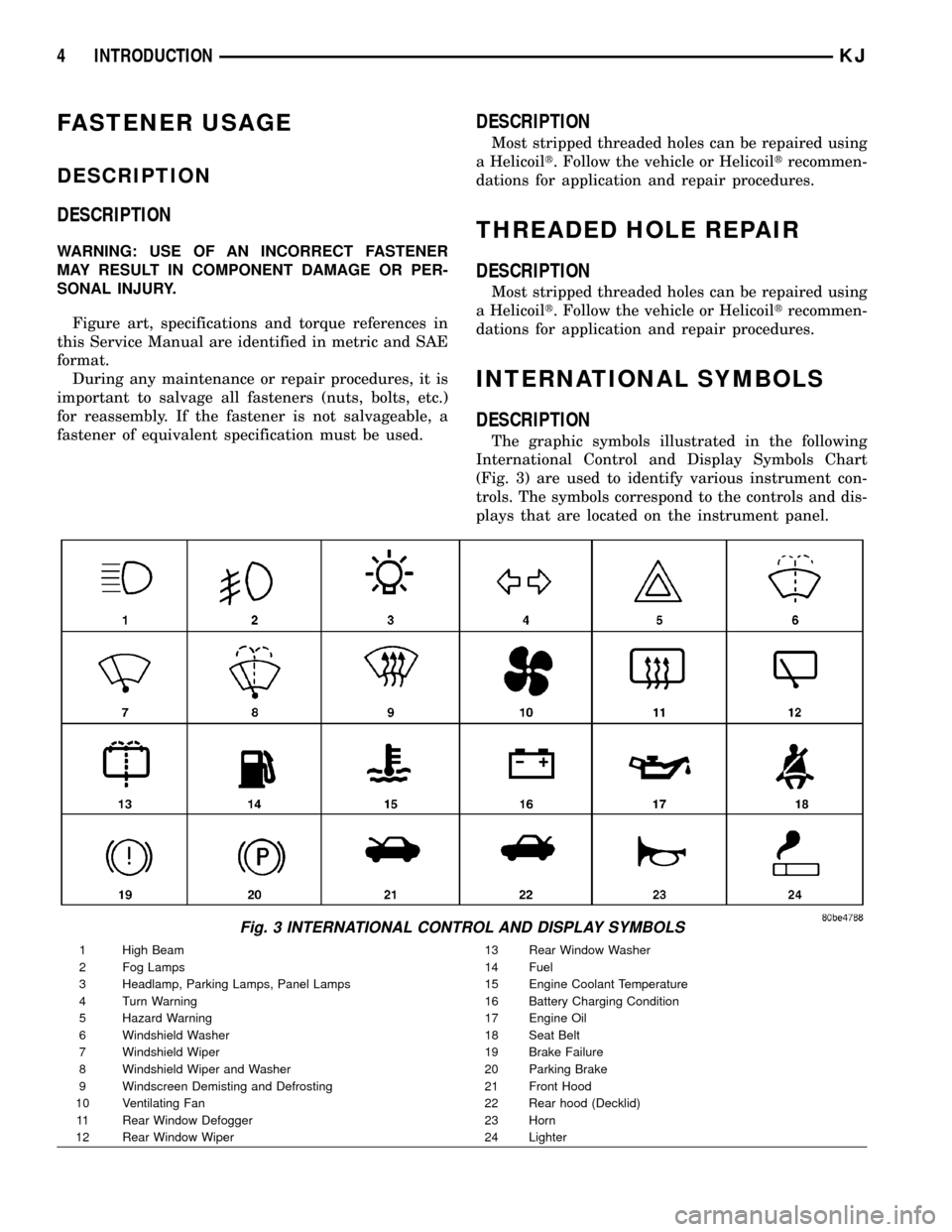
FASTENER USAGE
DESCRIPTION
DESCRIPTION
WARNING: USE OF AN INCORRECT FASTENER
MAY RESULT IN COMPONENT DAMAGE OR PER-
SONAL INJURY.
Figure art, specifications and torque references in
this Service Manual are identified in metric and SAE
format.
During any maintenance or repair procedures, it is
important to salvage all fasteners (nuts, bolts, etc.)
for reassembly. If the fastener is not salvageable, a
fastener of equivalent specification must be used.
DESCRIPTION
Most stripped threaded holes can be repaired using
a Helicoilt. Follow the vehicle or Helicoiltrecommen-
dations for application and repair procedures.
THREADED HOLE REPAIR
DESCRIPTION
Most stripped threaded holes can be repaired using
a Helicoilt. Follow the vehicle or Helicoiltrecommen-
dations for application and repair procedures.
INTERNATIONAL SYMBOLS
DESCRIPTION
The graphic symbols illustrated in the following
International Control and Display Symbols Chart
(Fig. 3) are used to identify various instrument con-
trols. The symbols correspond to the controls and dis-
plays that are located on the instrument panel.
Fig. 3 INTERNATIONAL CONTROL AND DISPLAY SYMBOLS
1 High Beam 13 Rear Window Washer
2 Fog Lamps 14 Fuel
3 Headlamp, Parking Lamps, Panel Lamps 15 Engine Coolant Temperature
4 Turn Warning 16 Battery Charging Condition
5 Hazard Warning 17 Engine Oil
6 Windshield Washer 18 Seat Belt
7 Windshield Wiper 19 Brake Failure
8 Windshield Wiper and Washer 20 Parking Brake
9 Windscreen Demisting and Defrosting 21 Front Hood
10 Ventilating Fan 22 Rear hood (Decklid)
11 Rear Window Defogger 23 Horn
12 Rear Window Wiper 24 Lighter
4 INTRODUCTIONKJ
Page 184 of 1803
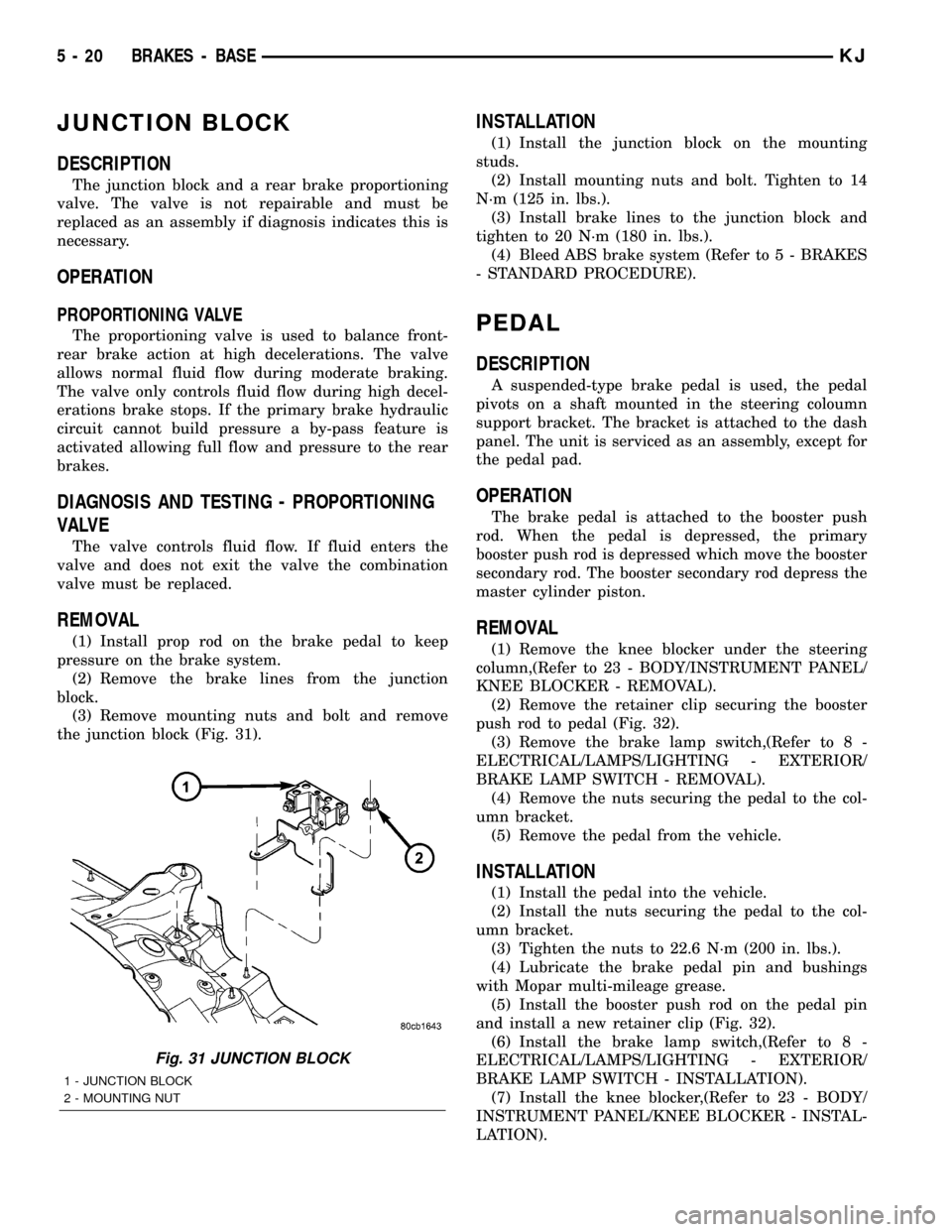
JUNCTION BLOCK
DESCRIPTION
The junction block and a rear brake proportioning
valve. The valve is not repairable and must be
replaced as an assembly if diagnosis indicates this is
necessary.
OPERATION
PROPORTIONING VALVE
The proportioning valve is used to balance front-
rear brake action at high decelerations. The valve
allows normal fluid flow during moderate braking.
The valve only controls fluid flow during high decel-
erations brake stops. If the primary brake hydraulic
circuit cannot build pressure a by-pass feature is
activated allowing full flow and pressure to the rear
brakes.
DIAGNOSIS AND TESTING - PROPORTIONING
VALVE
The valve controls fluid flow. If fluid enters the
valve and does not exit the valve the combination
valve must be replaced.
REMOVAL
(1) Install prop rod on the brake pedal to keep
pressure on the brake system.
(2) Remove the brake lines from the junction
block.
(3) Remove mounting nuts and bolt and remove
the junction block (Fig. 31).
INSTALLATION
(1) Install the junction block on the mounting
studs.
(2) Install mounting nuts and bolt. Tighten to 14
N´m (125 in. lbs.).
(3) Install brake lines to the junction block and
tighten to 20 N´m (180 in. lbs.).
(4) Bleed ABS brake system (Refer to 5 - BRAKES
- STANDARD PROCEDURE).
PEDAL
DESCRIPTION
A suspended-type brake pedal is used, the pedal
pivots on a shaft mounted in the steering coloumn
support bracket. The bracket is attached to the dash
panel. The unit is serviced as an assembly, except for
the pedal pad.
OPERATION
The brake pedal is attached to the booster push
rod. When the pedal is depressed, the primary
booster push rod is depressed which move the booster
secondary rod. The booster secondary rod depress the
master cylinder piston.
REMOVAL
(1) Remove the knee blocker under the steering
column,(Refer to 23 - BODY/INSTRUMENT PANEL/
KNEE BLOCKER - REMOVAL).
(2) Remove the retainer clip securing the booster
push rod to pedal (Fig. 32).
(3) Remove the brake lamp switch,(Refer to 8 -
ELECTRICAL/LAMPS/LIGHTING - EXTERIOR/
BRAKE LAMP SWITCH - REMOVAL).
(4) Remove the nuts securing the pedal to the col-
umn bracket.
(5) Remove the pedal from the vehicle.
INSTALLATION
(1) Install the pedal into the vehicle.
(2) Install the nuts securing the pedal to the col-
umn bracket.
(3) Tighten the nuts to 22.6 N´m (200 in. lbs.).
(4) Lubricate the brake pedal pin and bushings
with Mopar multi-mileage grease.
(5) Install the booster push rod on the pedal pin
and install a new retainer clip (Fig. 32).
(6) Install the brake lamp switch,(Refer to 8 -
ELECTRICAL/LAMPS/LIGHTING - EXTERIOR/
BRAKE LAMP SWITCH - INSTALLATION).
(7) Install the knee blocker,(Refer to 23 - BODY/
INSTRUMENT PANEL/KNEE BLOCKER - INSTAL-
LATION).
Fig. 31 JUNCTION BLOCK
1 - JUNCTION BLOCK
2 - MOUNTING NUT
5 - 20 BRAKES - BASEKJ
Page 187 of 1803
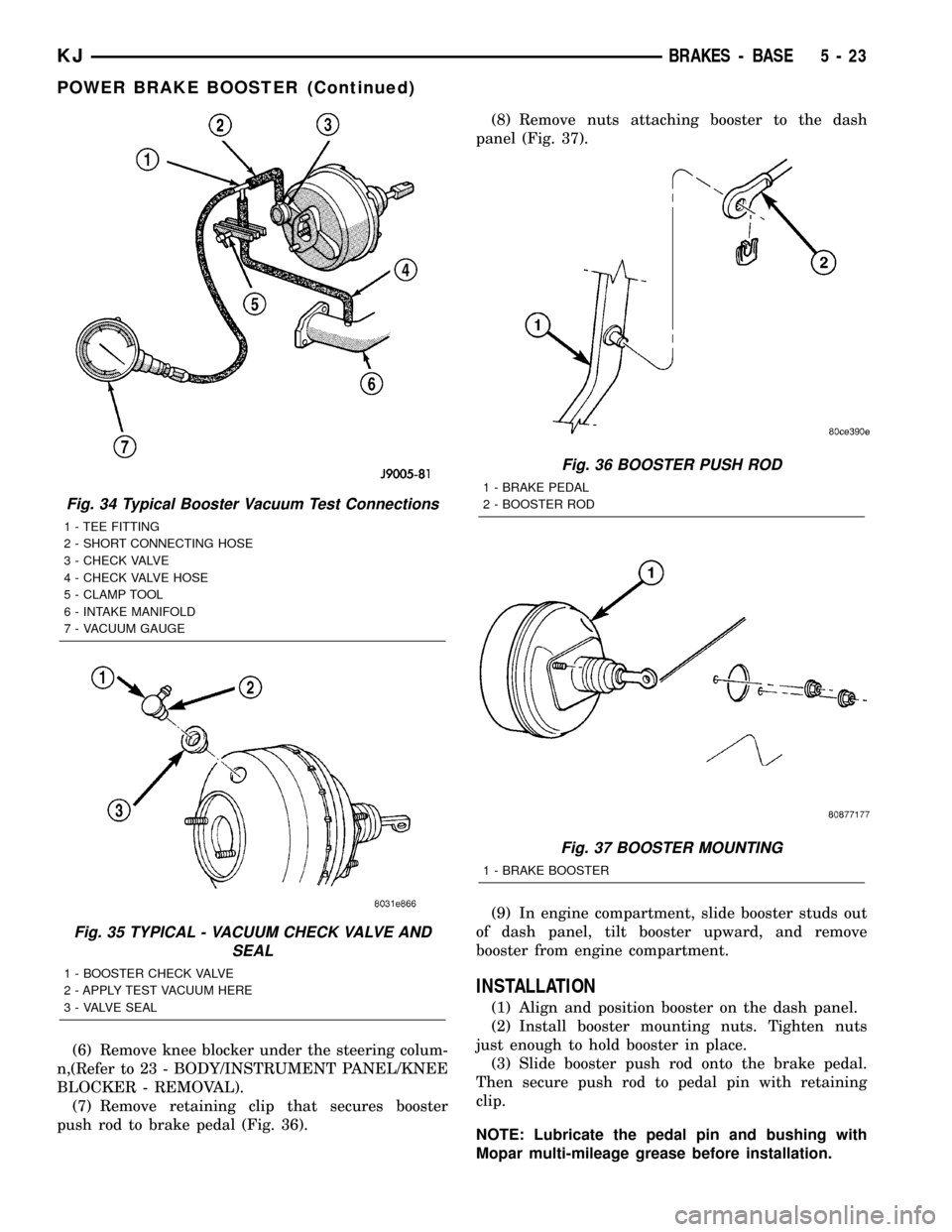
(6) Remove knee blocker under the steering colum-
n,(Refer to 23 - BODY/INSTRUMENT PANEL/KNEE
BLOCKER - REMOVAL).
(7) Remove retaining clip that secures booster
push rod to brake pedal (Fig. 36).(8) Remove nuts attaching booster to the dash
panel (Fig. 37).
(9) In engine compartment, slide booster studs out
of dash panel, tilt booster upward, and remove
booster from engine compartment.
INSTALLATION
(1) Align and position booster on the dash panel.
(2) Install booster mounting nuts. Tighten nuts
just enough to hold booster in place.
(3) Slide booster push rod onto the brake pedal.
Then secure push rod to pedal pin with retaining
clip.
NOTE: Lubricate the pedal pin and bushing with
Mopar multi-mileage grease before installation.
Fig. 34 Typical Booster Vacuum Test Connections
1 - TEE FITTING
2 - SHORT CONNECTING HOSE
3 - CHECK VALVE
4 - CHECK VALVE HOSE
5 - CLAMP TOOL
6 - INTAKE MANIFOLD
7 - VACUUM GAUGE
Fig. 35 TYPICAL - VACUUM CHECK VALVE AND
SEAL
1 - BOOSTER CHECK VALVE
2 - APPLY TEST VACUUM HERE
3 - VALVE SEAL
Fig. 36 BOOSTER PUSH ROD
1 - BRAKE PEDAL
2 - BOOSTER ROD
Fig. 37 BOOSTER MOUNTING
1 - BRAKE BOOSTER
KJBRAKES - BASE 5 - 23
POWER BRAKE BOOSTER (Continued)
Page 188 of 1803
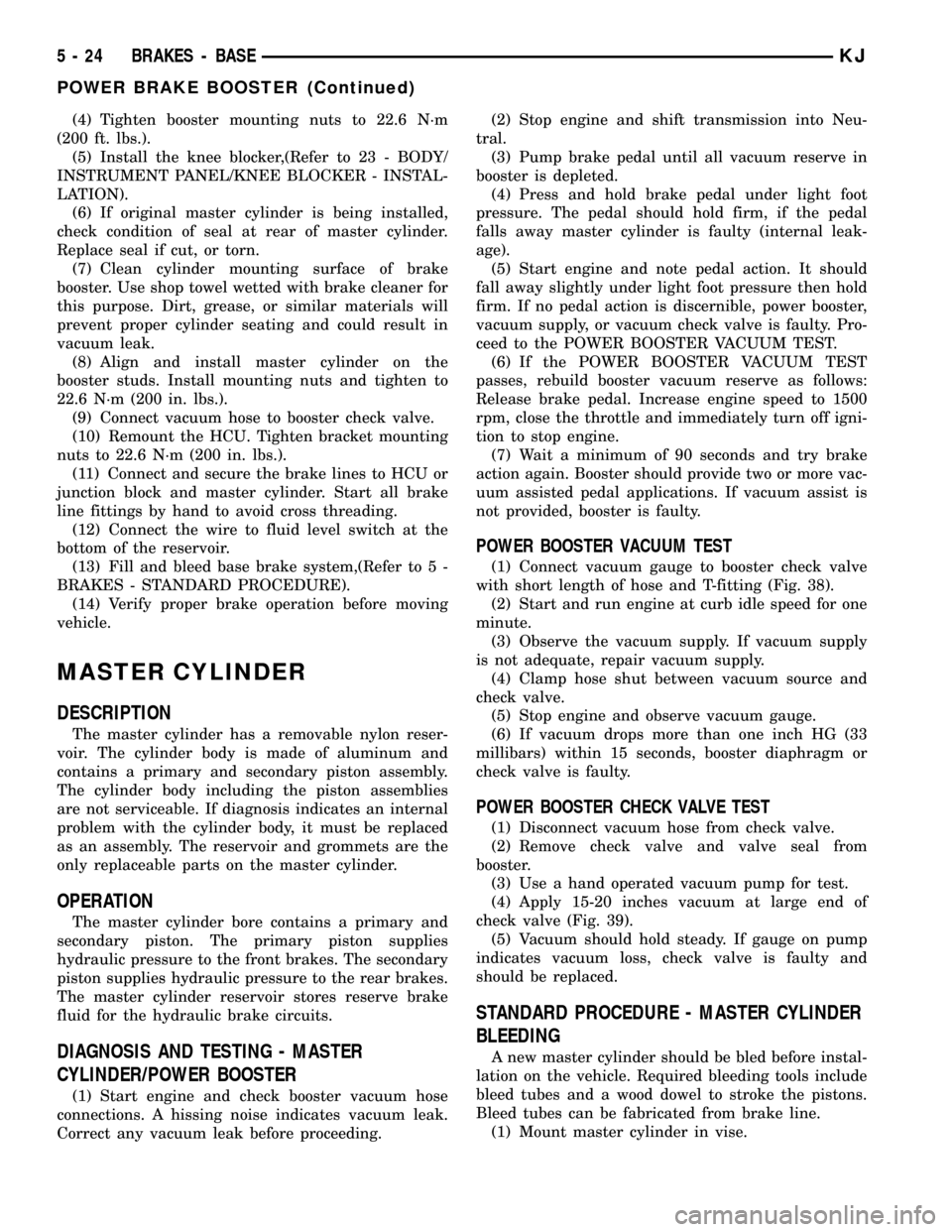
(4) Tighten booster mounting nuts to 22.6 N´m
(200 ft. lbs.).
(5) Install the knee blocker,(Refer to 23 - BODY/
INSTRUMENT PANEL/KNEE BLOCKER - INSTAL-
LATION).
(6) If original master cylinder is being installed,
check condition of seal at rear of master cylinder.
Replace seal if cut, or torn.
(7) Clean cylinder mounting surface of brake
booster. Use shop towel wetted with brake cleaner for
this purpose. Dirt, grease, or similar materials will
prevent proper cylinder seating and could result in
vacuum leak.
(8) Align and install master cylinder on the
booster studs. Install mounting nuts and tighten to
22.6 N´m (200 in. lbs.).
(9) Connect vacuum hose to booster check valve.
(10) Remount the HCU. Tighten bracket mounting
nuts to 22.6 N´m (200 in. lbs.).
(11) Connect and secure the brake lines to HCU or
junction block and master cylinder. Start all brake
line fittings by hand to avoid cross threading.
(12) Connect the wire to fluid level switch at the
bottom of the reservoir.
(13) Fill and bleed base brake system,(Refer to 5 -
BRAKES - STANDARD PROCEDURE).
(14) Verify proper brake operation before moving
vehicle.
MASTER CYLINDER
DESCRIPTION
The master cylinder has a removable nylon reser-
voir. The cylinder body is made of aluminum and
contains a primary and secondary piston assembly.
The cylinder body including the piston assemblies
are not serviceable. If diagnosis indicates an internal
problem with the cylinder body, it must be replaced
as an assembly. The reservoir and grommets are the
only replaceable parts on the master cylinder.
OPERATION
The master cylinder bore contains a primary and
secondary piston. The primary piston supplies
hydraulic pressure to the front brakes. The secondary
piston supplies hydraulic pressure to the rear brakes.
The master cylinder reservoir stores reserve brake
fluid for the hydraulic brake circuits.
DIAGNOSIS AND TESTING - MASTER
CYLINDER/POWER BOOSTER
(1) Start engine and check booster vacuum hose
connections. A hissing noise indicates vacuum leak.
Correct any vacuum leak before proceeding.(2) Stop engine and shift transmission into Neu-
tral.
(3) Pump brake pedal until all vacuum reserve in
booster is depleted.
(4) Press and hold brake pedal under light foot
pressure. The pedal should hold firm, if the pedal
falls away master cylinder is faulty (internal leak-
age).
(5) Start engine and note pedal action. It should
fall away slightly under light foot pressure then hold
firm. If no pedal action is discernible, power booster,
vacuum supply, or vacuum check valve is faulty. Pro-
ceed to the POWER BOOSTER VACUUM TEST.
(6) If the POWER BOOSTER VACUUM TEST
passes, rebuild booster vacuum reserve as follows:
Release brake pedal. Increase engine speed to 1500
rpm, close the throttle and immediately turn off igni-
tion to stop engine.
(7) Wait a minimum of 90 seconds and try brake
action again. Booster should provide two or more vac-
uum assisted pedal applications. If vacuum assist is
not provided, booster is faulty.
POWER BOOSTER VACUUM TEST
(1) Connect vacuum gauge to booster check valve
with short length of hose and T-fitting (Fig. 38).
(2) Start and run engine at curb idle speed for one
minute.
(3) Observe the vacuum supply. If vacuum supply
is not adequate, repair vacuum supply.
(4) Clamp hose shut between vacuum source and
check valve.
(5) Stop engine and observe vacuum gauge.
(6) If vacuum drops more than one inch HG (33
millibars) within 15 seconds, booster diaphragm or
check valve is faulty.
POWER BOOSTER CHECK VALVE TEST
(1) Disconnect vacuum hose from check valve.
(2) Remove check valve and valve seal from
booster.
(3) Use a hand operated vacuum pump for test.
(4) Apply 15-20 inches vacuum at large end of
check valve (Fig. 39).
(5) Vacuum should hold steady. If gauge on pump
indicates vacuum loss, check valve is faulty and
should be replaced.
STANDARD PROCEDURE - MASTER CYLINDER
BLEEDING
A new master cylinder should be bled before instal-
lation on the vehicle. Required bleeding tools include
bleed tubes and a wood dowel to stroke the pistons.
Bleed tubes can be fabricated from brake line.
(1) Mount master cylinder in vise.
5 - 24 BRAKES - BASEKJ
POWER BRAKE BOOSTER (Continued)
Page 201 of 1803
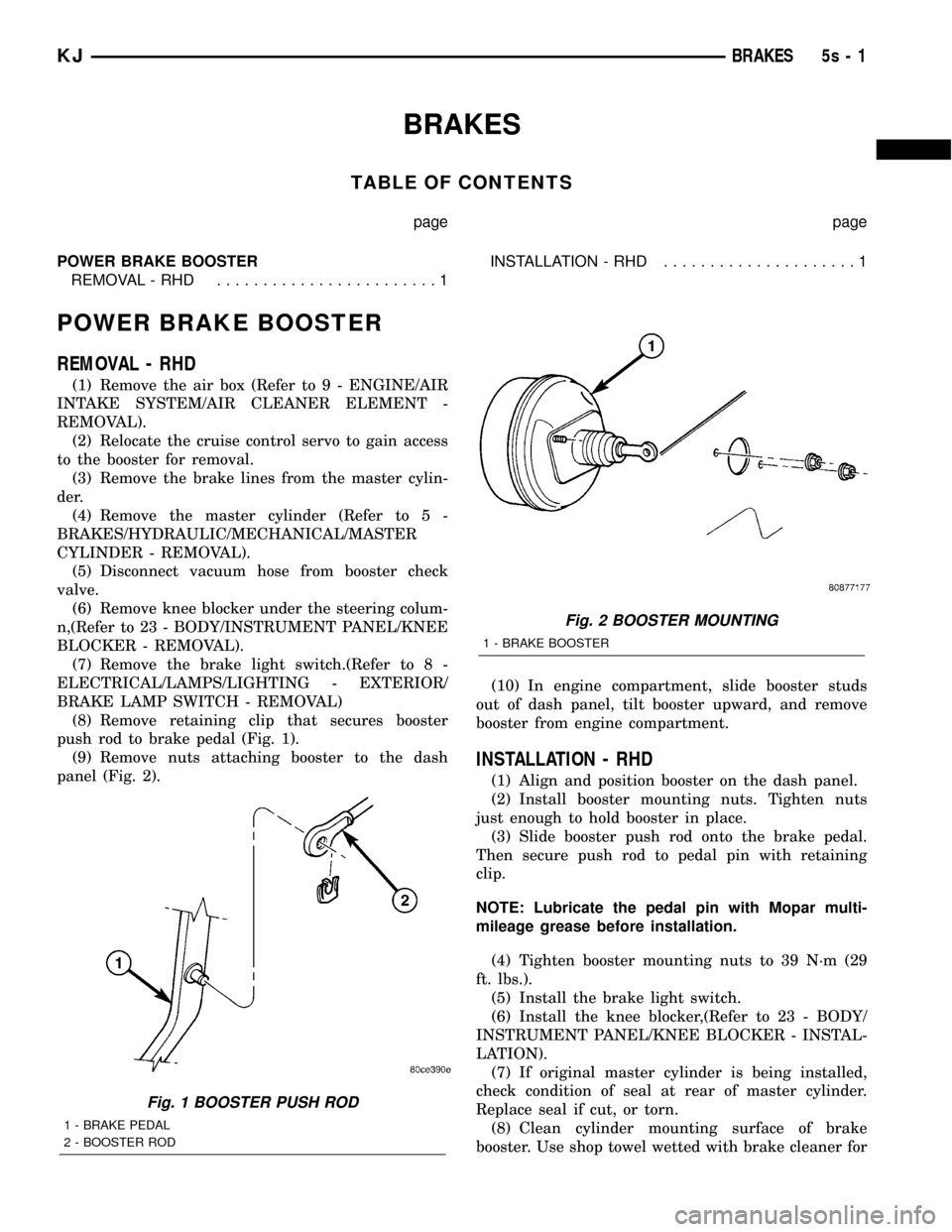
BRAKES
TABLE OF CONTENTS
page page
POWER BRAKE BOOSTER
REMOVAL - RHD........................1INSTALLATION - RHD.....................1
POWER BRAKE BOOSTER
REMOVAL - RHD
(1) Remove the air box (Refer to 9 - ENGINE/AIR
INTAKE SYSTEM/AIR CLEANER ELEMENT -
REMOVAL).
(2) Relocate the cruise control servo to gain access
to the booster for removal.
(3) Remove the brake lines from the master cylin-
der.
(4) Remove the master cylinder (Refer to 5 -
BRAKES/HYDRAULIC/MECHANICAL/MASTER
CYLINDER - REMOVAL).
(5) Disconnect vacuum hose from booster check
valve.
(6) Remove knee blocker under the steering colum-
n,(Refer to 23 - BODY/INSTRUMENT PANEL/KNEE
BLOCKER - REMOVAL).
(7) Remove the brake light switch.(Refer to 8 -
ELECTRICAL/LAMPS/LIGHTING - EXTERIOR/
BRAKE LAMP SWITCH - REMOVAL)
(8) Remove retaining clip that secures booster
push rod to brake pedal (Fig. 1).
(9) Remove nuts attaching booster to the dash
panel (Fig. 2).(10) In engine compartment, slide booster studs
out of dash panel, tilt booster upward, and remove
booster from engine compartment.
INSTALLATION - RHD
(1) Align and position booster on the dash panel.
(2) Install booster mounting nuts. Tighten nuts
just enough to hold booster in place.
(3) Slide booster push rod onto the brake pedal.
Then secure push rod to pedal pin with retaining
clip.
NOTE: Lubricate the pedal pin with Mopar multi-
mileage grease before installation.
(4) Tighten booster mounting nuts to 39 N´m (29
ft. lbs.).
(5) Install the brake light switch.
(6) Install the knee blocker,(Refer to 23 - BODY/
INSTRUMENT PANEL/KNEE BLOCKER - INSTAL-
LATION).
(7) If original master cylinder is being installed,
check condition of seal at rear of master cylinder.
Replace seal if cut, or torn.
(8) Clean cylinder mounting surface of brake
booster. Use shop towel wetted with brake cleaner for
Fig. 1 BOOSTER PUSH ROD
1 - BRAKE PEDAL
2 - BOOSTER ROD
Fig. 2 BOOSTER MOUNTING
1 - BRAKE BOOSTER
KJBRAKES 5s - 1
Page 203 of 1803
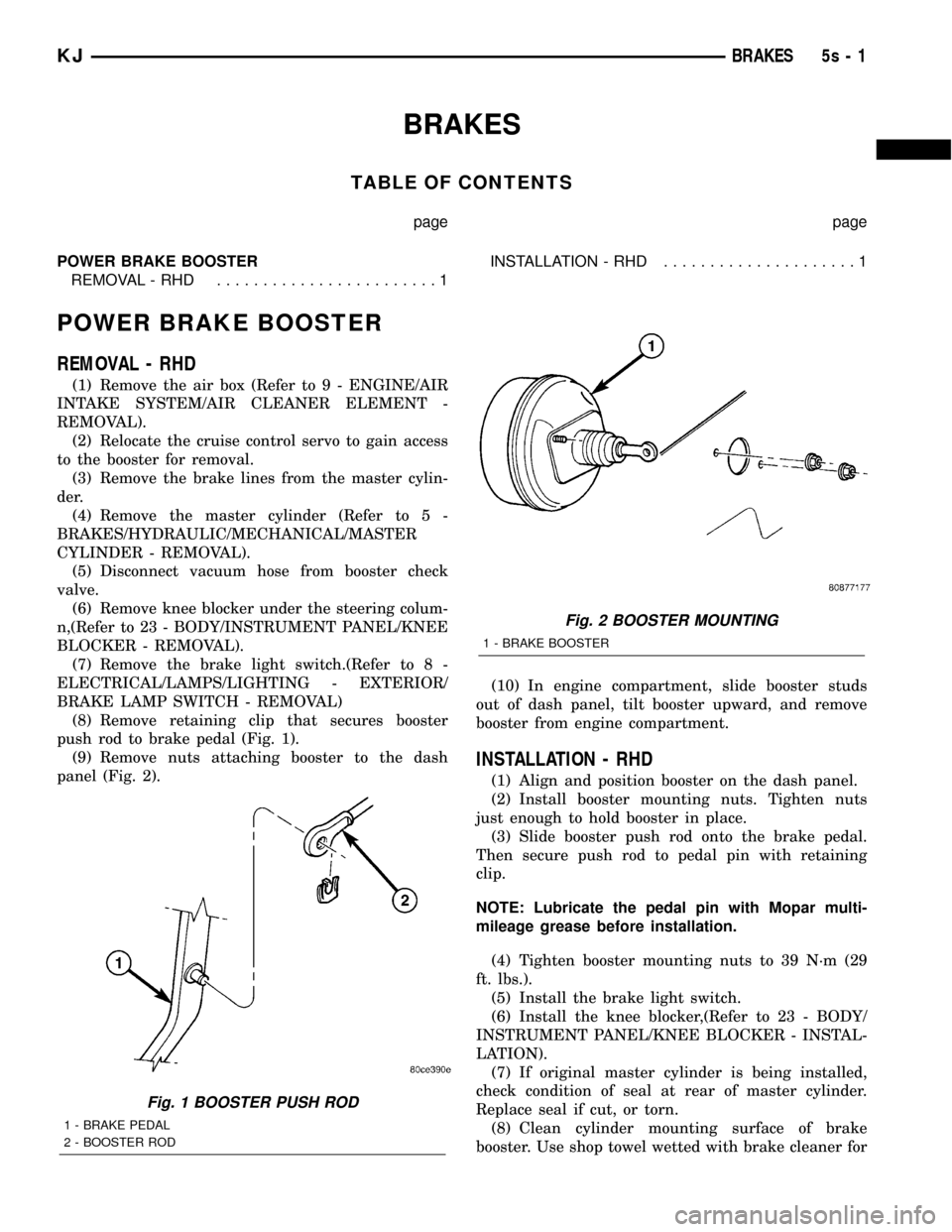
BRAKES
TABLE OF CONTENTS
page page
POWER BRAKE BOOSTER
REMOVAL - RHD........................1INSTALLATION - RHD.....................1
POWER BRAKE BOOSTER
REMOVAL - RHD
(1) Remove the air box (Refer to 9 - ENGINE/AIR
INTAKE SYSTEM/AIR CLEANER ELEMENT -
REMOVAL).
(2) Relocate the cruise control servo to gain access
to the booster for removal.
(3) Remove the brake lines from the master cylin-
der.
(4) Remove the master cylinder (Refer to 5 -
BRAKES/HYDRAULIC/MECHANICAL/MASTER
CYLINDER - REMOVAL).
(5) Disconnect vacuum hose from booster check
valve.
(6) Remove knee blocker under the steering colum-
n,(Refer to 23 - BODY/INSTRUMENT PANEL/KNEE
BLOCKER - REMOVAL).
(7) Remove the brake light switch.(Refer to 8 -
ELECTRICAL/LAMPS/LIGHTING - EXTERIOR/
BRAKE LAMP SWITCH - REMOVAL)
(8) Remove retaining clip that secures booster
push rod to brake pedal (Fig. 1).
(9) Remove nuts attaching booster to the dash
panel (Fig. 2).(10) In engine compartment, slide booster studs
out of dash panel, tilt booster upward, and remove
booster from engine compartment.
INSTALLATION - RHD
(1) Align and position booster on the dash panel.
(2) Install booster mounting nuts. Tighten nuts
just enough to hold booster in place.
(3) Slide booster push rod onto the brake pedal.
Then secure push rod to pedal pin with retaining
clip.
NOTE: Lubricate the pedal pin with Mopar multi-
mileage grease before installation.
(4) Tighten booster mounting nuts to 39 N´m (29
ft. lbs.).
(5) Install the brake light switch.
(6) Install the knee blocker,(Refer to 23 - BODY/
INSTRUMENT PANEL/KNEE BLOCKER - INSTAL-
LATION).
(7) If original master cylinder is being installed,
check condition of seal at rear of master cylinder.
Replace seal if cut, or torn.
(8) Clean cylinder mounting surface of brake
booster. Use shop towel wetted with brake cleaner for
Fig. 1 BOOSTER PUSH ROD
1 - BRAKE PEDAL
2 - BOOSTER ROD
Fig. 2 BOOSTER MOUNTING
1 - BRAKE BOOSTER
KJBRAKES 5s - 1
Page 215 of 1803
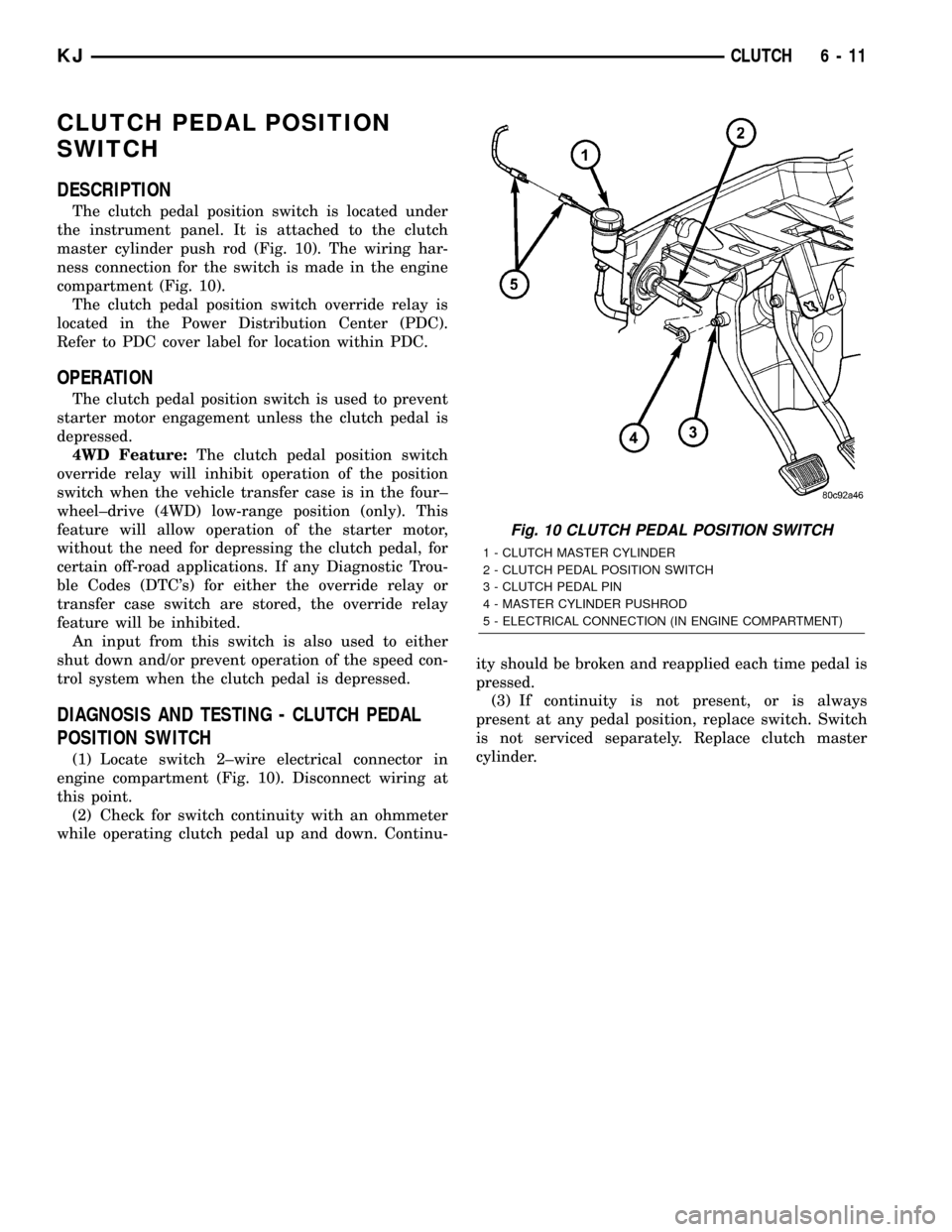
CLUTCH PEDAL POSITION
SWITCH
DESCRIPTION
The clutch pedal position switch is located under
the instrument panel. It is attached to the clutch
master cylinder push rod (Fig. 10). The wiring har-
ness connection for the switch is made in the engine
compartment (Fig. 10).
The clutch pedal position switch override relay is
located in the Power Distribution Center (PDC).
Refer to PDC cover label for location within PDC.
OPERATION
The clutch pedal position switch is used to prevent
starter motor engagement unless the clutch pedal is
depressed.
4WD Feature:The clutch pedal position switch
override relay will inhibit operation of the position
switch when the vehicle transfer case is in the four±
wheel±drive (4WD) low-range position (only). This
feature will allow operation of the starter motor,
without the need for depressing the clutch pedal, for
certain off-road applications. If any Diagnostic Trou-
ble Codes (DTC's) for either the override relay or
transfer case switch are stored, the override relay
feature will be inhibited.
An input from this switch is also used to either
shut down and/or prevent operation of the speed con-
trol system when the clutch pedal is depressed.
DIAGNOSIS AND TESTING - CLUTCH PEDAL
POSITION SWITCH
(1) Locate switch 2±wire electrical connector in
engine compartment (Fig. 10). Disconnect wiring at
this point.
(2) Check for switch continuity with an ohmmeter
while operating clutch pedal up and down. Continu-ity should be broken and reapplied each time pedal is
pressed.
(3) If continuity is not present, or is always
present at any pedal position, replace switch. Switch
is not serviced separately. Replace clutch master
cylinder.
Fig. 10 CLUTCH PEDAL POSITION SWITCH
1 - CLUTCH MASTER CYLINDER
2 - CLUTCH PEDAL POSITION SWITCH
3 - CLUTCH PEDAL PIN
4 - MASTER CYLINDER PUSHROD
5 - ELECTRICAL CONNECTION (IN ENGINE COMPARTMENT)
KJCLUTCH 6 - 11
Page 278 of 1803
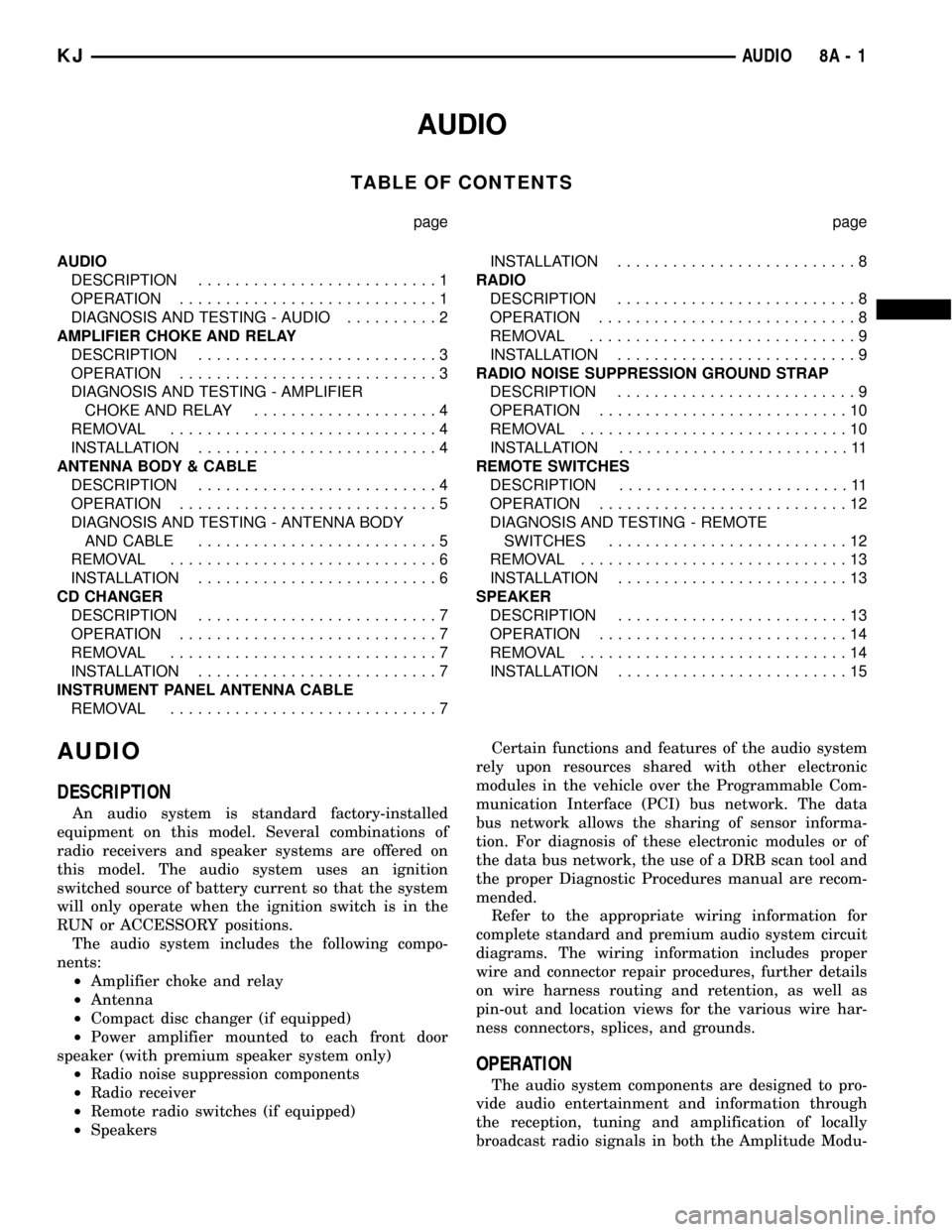
AUDIO
TABLE OF CONTENTS
page page
AUDIO
DESCRIPTION..........................1
OPERATION............................1
DIAGNOSIS AND TESTING - AUDIO..........2
AMPLIFIER CHOKE AND RELAY
DESCRIPTION..........................3
OPERATION............................3
DIAGNOSIS AND TESTING - AMPLIFIER
CHOKE AND RELAY....................4
REMOVAL.............................4
INSTALLATION..........................4
ANTENNA BODY & CABLE
DESCRIPTION..........................4
OPERATION............................5
DIAGNOSIS AND TESTING - ANTENNA BODY
AND CABLE..........................5
REMOVAL.............................6
INSTALLATION..........................6
CD CHANGER
DESCRIPTION..........................7
OPERATION............................7
REMOVAL.............................7
INSTALLATION..........................7
INSTRUMENT PANEL ANTENNA CABLE
REMOVAL.............................7INSTALLATION..........................8
RADIO
DESCRIPTION..........................8
OPERATION............................8
REMOVAL.............................9
INSTALLATION..........................9
RADIO NOISE SUPPRESSION GROUND STRAP
DESCRIPTION..........................9
OPERATION...........................10
REMOVAL.............................10
INSTALLATION.........................11
REMOTE SWITCHES
DESCRIPTION.........................11
OPERATION...........................12
DIAGNOSIS AND TESTING - REMOTE
SWITCHES..........................12
REMOVAL.............................13
INSTALLATION.........................13
SPEAKER
DESCRIPTION.........................13
OPERATION...........................14
REMOVAL.............................14
INSTALLATION.........................15
AUDIO
DESCRIPTION
An audio system is standard factory-installed
equipment on this model. Several combinations of
radio receivers and speaker systems are offered on
this model. The audio system uses an ignition
switched source of battery current so that the system
will only operate when the ignition switch is in the
RUN or ACCESSORY positions.
The audio system includes the following compo-
nents:
²Amplifier choke and relay
²Antenna
²Compact disc changer (if equipped)
²Power amplifier mounted to each front door
speaker (with premium speaker system only)
²Radio noise suppression components
²Radio receiver
²Remote radio switches (if equipped)
²SpeakersCertain functions and features of the audio system
rely upon resources shared with other electronic
modules in the vehicle over the Programmable Com-
munication Interface (PCI) bus network. The data
bus network allows the sharing of sensor informa-
tion. For diagnosis of these electronic modules or of
the data bus network, the use of a DRB scan tool and
the proper Diagnostic Procedures manual are recom-
mended.
Refer to the appropriate wiring information for
complete standard and premium audio system circuit
diagrams. The wiring information includes proper
wire and connector repair procedures, further details
on wire harness routing and retention, as well as
pin-out and location views for the various wire har-
ness connectors, splices, and grounds.
OPERATION
The audio system components are designed to pro-
vide audio entertainment and information through
the reception, tuning and amplification of locally
broadcast radio signals in both the Amplitude Modu-
KJAUDIO 8A - 1
Page 279 of 1803
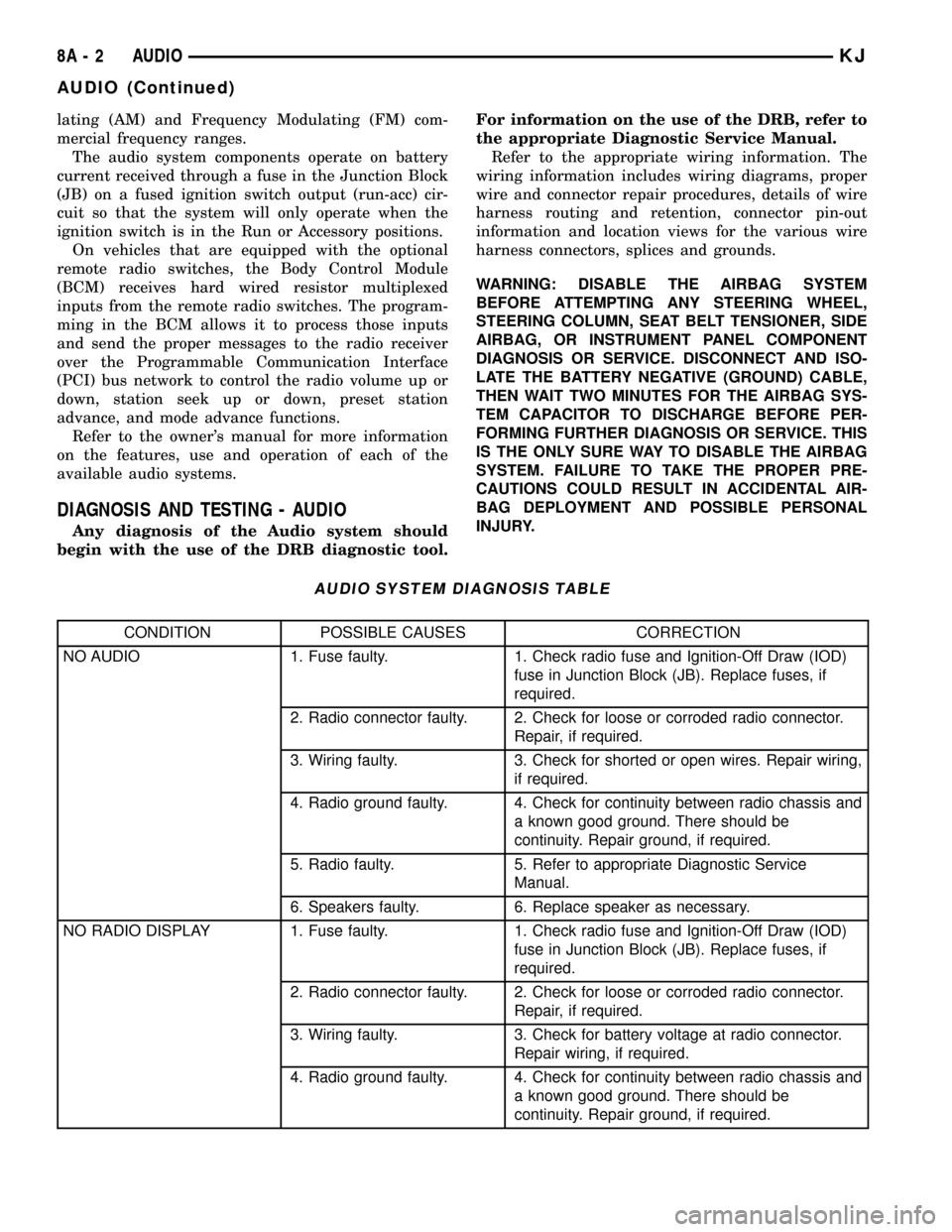
lating (AM) and Frequency Modulating (FM) com-
mercial frequency ranges.
The audio system components operate on battery
current received through a fuse in the Junction Block
(JB) on a fused ignition switch output (run-acc) cir-
cuit so that the system will only operate when the
ignition switch is in the Run or Accessory positions.
On vehicles that are equipped with the optional
remote radio switches, the Body Control Module
(BCM) receives hard wired resistor multiplexed
inputs from the remote radio switches. The program-
ming in the BCM allows it to process those inputs
and send the proper messages to the radio receiver
over the Programmable Communication Interface
(PCI) bus network to control the radio volume up or
down, station seek up or down, preset station
advance, and mode advance functions.
Refer to the owner's manual for more information
on the features, use and operation of each of the
available audio systems.
DIAGNOSIS AND TESTING - AUDIO
Any diagnosis of the Audio system should
begin with the use of the DRB diagnostic tool.For information on the use of the DRB, refer to
the appropriate Diagnostic Service Manual.
Refer to the appropriate wiring information. The
wiring information includes wiring diagrams, proper
wire and connector repair procedures, details of wire
harness routing and retention, connector pin-out
information and location views for the various wire
harness connectors, splices and grounds.
WARNING: DISABLE THE AIRBAG SYSTEM
BEFORE ATTEMPTING ANY STEERING WHEEL,
STEERING COLUMN, SEAT BELT TENSIONER, SIDE
AIRBAG, OR INSTRUMENT PANEL COMPONENT
DIAGNOSIS OR SERVICE. DISCONNECT AND ISO-
LATE THE BATTERY NEGATIVE (GROUND) CABLE,
THEN WAIT TWO MINUTES FOR THE AIRBAG SYS-
TEM CAPACITOR TO DISCHARGE BEFORE PER-
FORMING FURTHER DIAGNOSIS OR SERVICE. THIS
IS THE ONLY SURE WAY TO DISABLE THE AIRBAG
SYSTEM. FAILURE TO TAKE THE PROPER PRE-
CAUTIONS COULD RESULT IN ACCIDENTAL AIR-
BAG DEPLOYMENT AND POSSIBLE PERSONAL
INJURY.
AUDIO SYSTEM DIAGNOSIS TABLE
CONDITION POSSIBLE CAUSES CORRECTION
NO AUDIO 1. Fuse faulty. 1. Check radio fuse and Ignition-Off Draw (IOD)
fuse in Junction Block (JB). Replace fuses, if
required.
2. Radio connector faulty. 2. Check for loose or corroded radio connector.
Repair, if required.
3. Wiring faulty. 3. Check for shorted or open wires. Repair wiring,
if required.
4. Radio ground faulty. 4. Check for continuity between radio chassis and
a known good ground. There should be
continuity. Repair ground, if required.
5. Radio faulty. 5. Refer to appropriate Diagnostic Service
Manual.
6. Speakers faulty. 6. Replace speaker as necessary.
NO RADIO DISPLAY 1. Fuse faulty. 1. Check radio fuse and Ignition-Off Draw (IOD)
fuse in Junction Block (JB). Replace fuses, if
required.
2. Radio connector faulty. 2. Check for loose or corroded radio connector.
Repair, if required.
3. Wiring faulty. 3. Check for battery voltage at radio connector.
Repair wiring, if required.
4. Radio ground faulty. 4. Check for continuity between radio chassis and
a known good ground. There should be
continuity. Repair ground, if required.
8A - 2 AUDIOKJ
AUDIO (Continued)
Page 280 of 1803
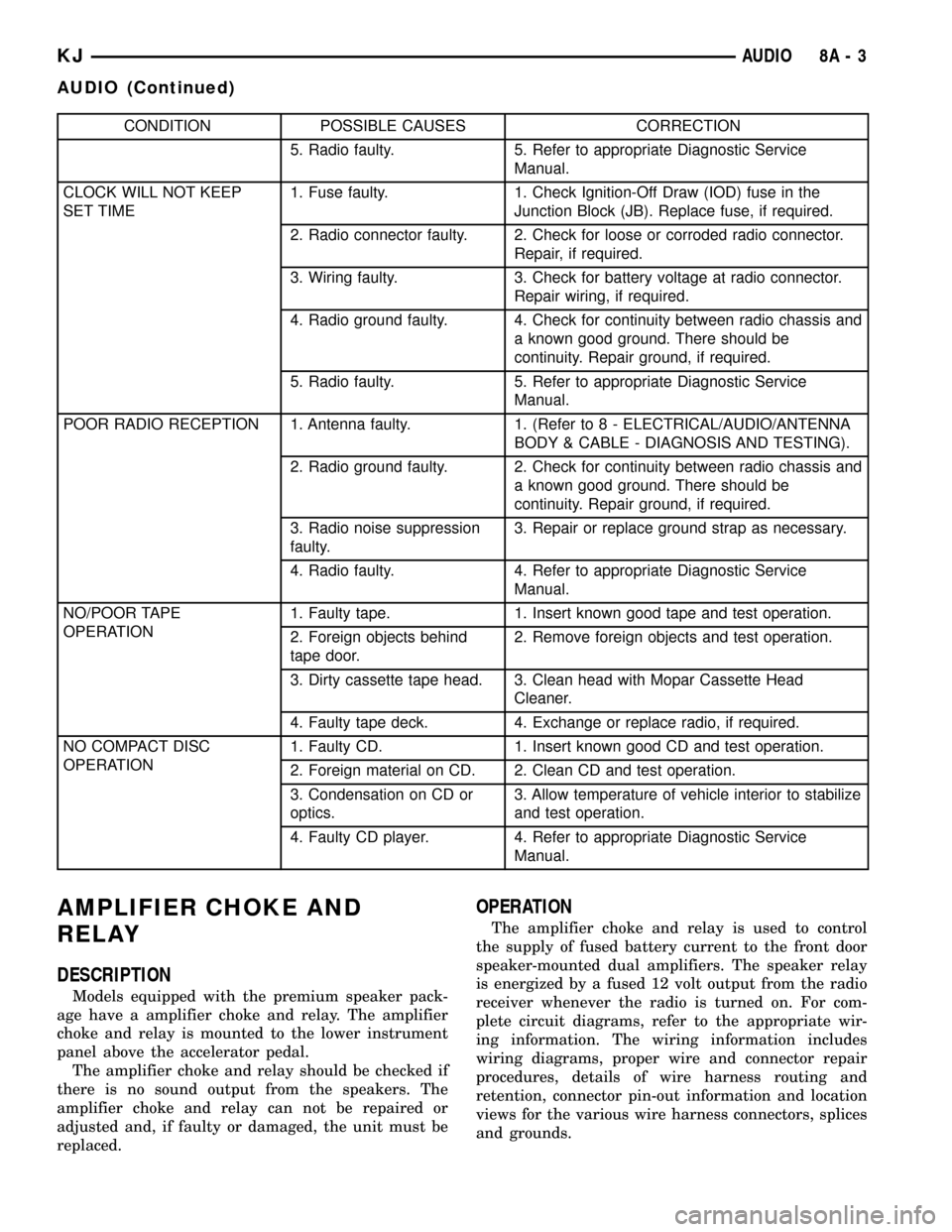
CONDITION POSSIBLE CAUSES CORRECTION
5. Radio faulty. 5. Refer to appropriate Diagnostic Service
Manual.
CLOCK WILL NOT KEEP
SET TIME1. Fuse faulty. 1. Check Ignition-Off Draw (IOD) fuse in the
Junction Block (JB). Replace fuse, if required.
2. Radio connector faulty. 2. Check for loose or corroded radio connector.
Repair, if required.
3. Wiring faulty. 3. Check for battery voltage at radio connector.
Repair wiring, if required.
4. Radio ground faulty. 4. Check for continuity between radio chassis and
a known good ground. There should be
continuity. Repair ground, if required.
5. Radio faulty. 5. Refer to appropriate Diagnostic Service
Manual.
POOR RADIO RECEPTION 1. Antenna faulty. 1. (Refer to 8 - ELECTRICAL/AUDIO/ANTENNA
BODY & CABLE - DIAGNOSIS AND TESTING).
2. Radio ground faulty. 2. Check for continuity between radio chassis and
a known good ground. There should be
continuity. Repair ground, if required.
3. Radio noise suppression
faulty.3. Repair or replace ground strap as necessary.
4. Radio faulty. 4. Refer to appropriate Diagnostic Service
Manual.
NO/POOR TAPE
OPERATION1. Faulty tape. 1. Insert known good tape and test operation.
2. Foreign objects behind
tape door.2. Remove foreign objects and test operation.
3. Dirty cassette tape head. 3. Clean head with Mopar Cassette Head
Cleaner.
4. Faulty tape deck. 4. Exchange or replace radio, if required.
NO COMPACT DISC
OPERATION1. Faulty CD. 1. Insert known good CD and test operation.
2. Foreign material on CD. 2. Clean CD and test operation.
3. Condensation on CD or
optics.3. Allow temperature of vehicle interior to stabilize
and test operation.
4. Faulty CD player. 4. Refer to appropriate Diagnostic Service
Manual.
AMPLIFIER CHOKE AND
RELAY
DESCRIPTION
Models equipped with the premium speaker pack-
age have a amplifier choke and relay. The amplifier
choke and relay is mounted to the lower instrument
panel above the accelerator pedal.
The amplifier choke and relay should be checked if
there is no sound output from the speakers. The
amplifier choke and relay can not be repaired or
adjusted and, if faulty or damaged, the unit must be
replaced.
OPERATION
The amplifier choke and relay is used to control
the supply of fused battery current to the front door
speaker-mounted dual amplifiers. The speaker relay
is energized by a fused 12 volt output from the radio
receiver whenever the radio is turned on. For com-
plete circuit diagrams, refer to the appropriate wir-
ing information. The wiring information includes
wiring diagrams, proper wire and connector repair
procedures, details of wire harness routing and
retention, connector pin-out information and location
views for the various wire harness connectors, splices
and grounds.
KJAUDIO 8A - 3
AUDIO (Continued)