sensor LAND ROVER DEFENDER 1996 User Guide
[x] Cancel search | Manufacturer: LAND ROVER, Model Year: 1996, Model line: DEFENDER, Model: LAND ROVER DEFENDER 1996Pages: 455, PDF Size: 6.44 MB
Page 103 of 455
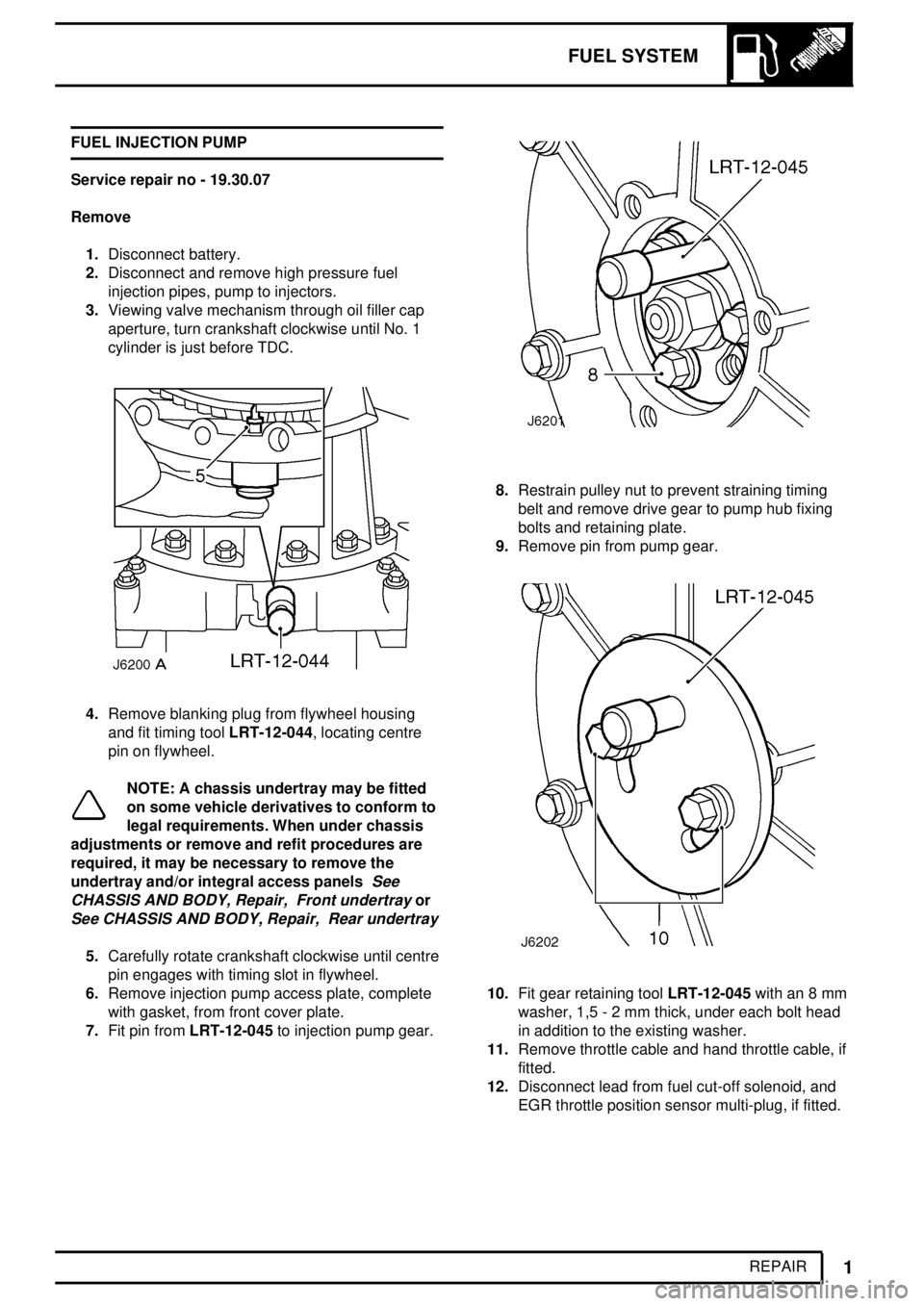
FUEL SYSTEM
1
REPAIR FUEL INJECTION PUMP
Service repair no - 19.30.07
Remove
1.Disconnect battery.
2.Disconnect and remove high pressure fuel
injection pipes, pump to injectors.
3.Viewing valve mechanism through oil filler cap
aperture, turn crankshaft clockwise until No. 1
cylinder is just before TDC.
4.Remove blanking plug from flywheel housing
and fit timing toolLRT-12-044, locating centre
pin on flywheel.
NOTE: A chassis undertray may be fitted
on some vehicle derivatives to conform to
legal requirements. When under chassis
adjustments or remove and refit procedures are
required, it may be necessary to remove the
undertray and/or integral access panels
See
CHASSIS AND BODY, Repair, Front undertray
or
See CHASSIS AND BODY, Repair, Rear undertray
5.Carefully rotate crankshaft clockwise until centre
pin engages with timing slot in flywheel.
6.Remove injection pump access plate, complete
with gasket, from front cover plate.
7.Fit pin fromLRT-12-045to injection pump gear.
8.Restrain pulley nut to prevent straining timing
belt and remove drive gear to pump hub fixing
bolts and retaining plate.
9.Remove pin from pump gear.
10.Fit gear retaining toolLRT-12-045with an 8 mm
washer, 1,5 - 2 mm thick, under each bolt head
in addition to the existing washer.
11.Remove throttle cable and hand throttle cable, if
fitted.
12.Disconnect lead from fuel cut-off solenoid, and
EGR throttle position sensor multi-plug, if fitted.
Page 104 of 455
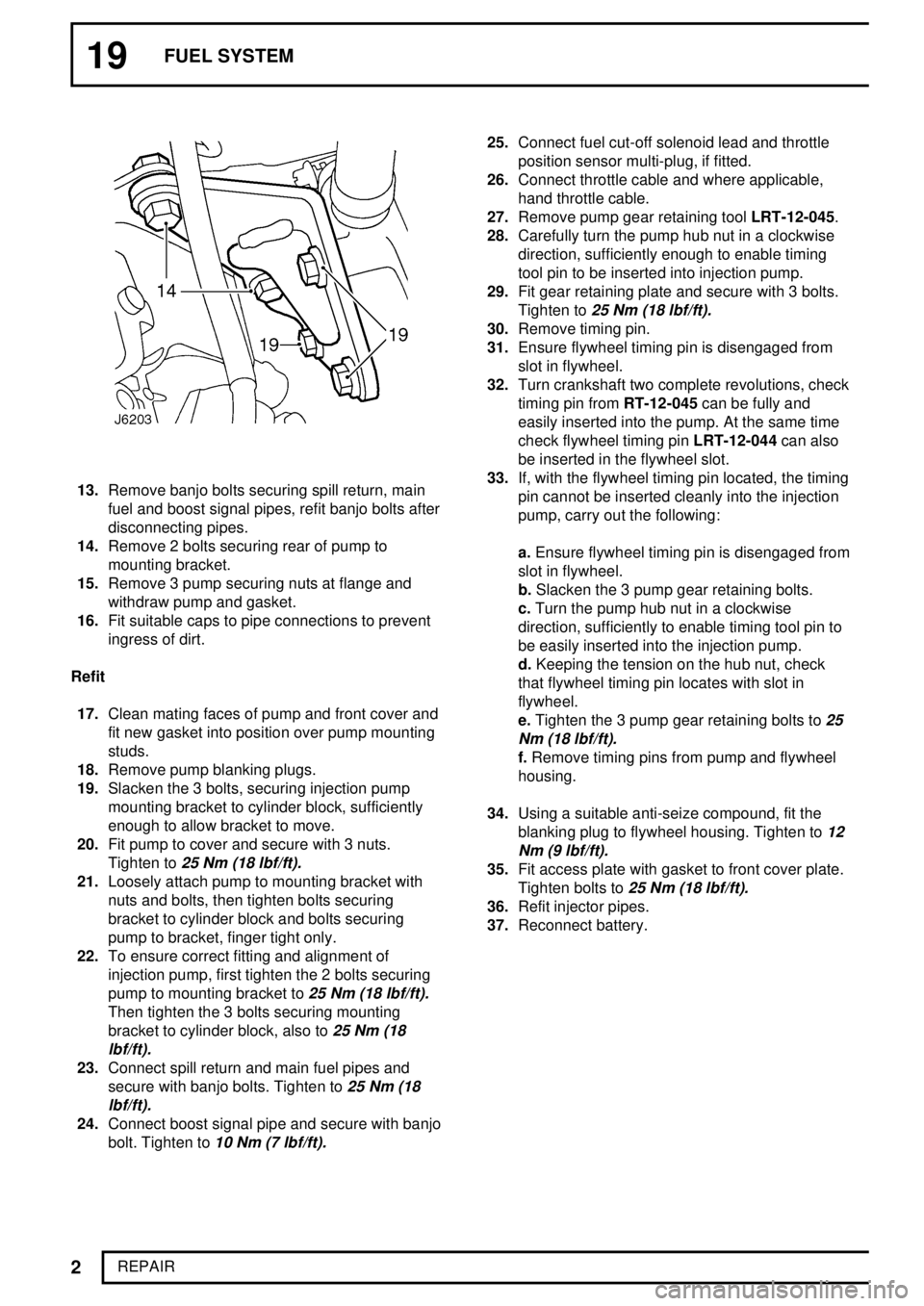
19FUEL SYSTEM
2
REPAIR
13.Remove banjo bolts securing spill return, main
fuel and boost signal pipes, refit banjo bolts after
disconnecting pipes.
14.Remove 2 bolts securing rear of pump to
mounting bracket.
15.Remove 3 pump securing nuts at flange and
withdraw pump and gasket.
16.Fit suitable caps to pipe connections to prevent
ingress of dirt.
Refit
17.Clean mating faces of pump and front cover and
fit new gasket into position over pump mounting
studs.
18.Remove pump blanking plugs.
19.Slacken the 3 bolts, securing injection pump
mounting bracket to cylinder block, sufficiently
enough to allow bracket to move.
20.Fit pump to cover and secure with 3 nuts.
Tighten to
25 Nm (18 lbf/ft).
21.Loosely attach pump to mounting bracket with
nuts and bolts, then tighten bolts securing
bracket to cylinder block and bolts securing
pump to bracket, finger tight only.
22.To ensure correct fitting and alignment of
injection pump, first tighten the 2 bolts securing
pump to mounting bracket to
25 Nm (18 lbf/ft).
Then tighten the 3 bolts securing mounting
bracket to cylinder block, also to
25 Nm (18
lbf/ft).
23.Connect spill return and main fuel pipes and
secure with banjo bolts. Tighten to
25 Nm (18
lbf/ft).
24.Connect boost signal pipe and secure with banjo
bolt. Tighten to
10 Nm (7 lbf/ft).
25.Connect fuel cut-off solenoid lead and throttle
position sensor multi-plug, if fitted.
26.Connect throttle cable and where applicable,
hand throttle cable.
27.Remove pump gear retaining toolLRT-12-045.
28.Carefully turn the pump hub nut in a clockwise
direction, sufficiently enough to enable timing
tool pin to be inserted into injection pump.
29.Fit gear retaining plate and secure with 3 bolts.
Tighten to
25 Nm (18 lbf/ft).
30.Remove timing pin.
31.Ensure flywheel timing pin is disengaged from
slot in flywheel.
32.Turn crankshaft two complete revolutions, check
timing pin fromRT-12-045can be fully and
easily inserted into the pump. At the same time
check flywheel timing pinLRT-12-044can also
be inserted in the flywheel slot.
33.If, with the flywheel timing pin located, the timing
pin cannot be inserted cleanly into the injection
pump, carry out the following:
a.Ensure flywheel timing pin is disengaged from
slot in flywheel.
b.Slacken the 3 pump gear retaining bolts.
c.Turn the pump hub nut in a clockwise
direction, sufficiently to enable timing tool pin to
be easily inserted into the injection pump.
d.Keeping the tension on the hub nut, check
that flywheel timing pin locates with slot in
flywheel.
e.Tighten the 3 pump gear retaining bolts to
25
Nm (18 lbf/ft).
f.Remove timing pins from pump and flywheel
housing.
34.Using a suitable anti-seize compound, fit the
blanking plug to flywheel housing. Tighten to
12
Nm (9 lbf/ft).
35.Fit access plate with gasket to front cover plate.
Tighten bolts to
25 Nm (18 lbf/ft).
36.Refit injector pipes.
37.Reconnect battery.
Page 120 of 455
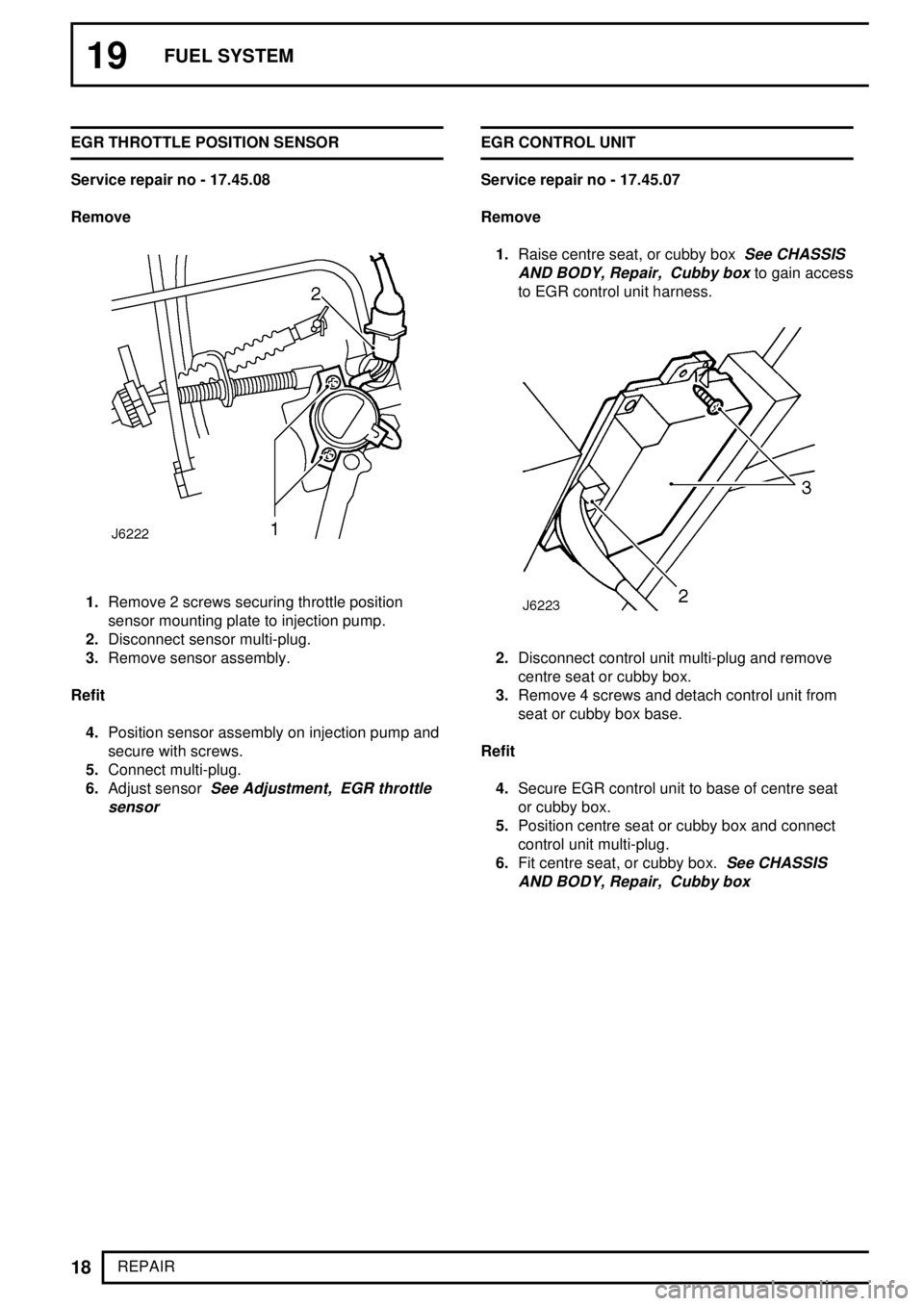
19FUEL SYSTEM
18
REPAIR EGR THROTTLE POSITION SENSOR
Service repair no - 17.45.08
Remove
1.Remove 2 screws securing throttle position
sensor mounting plate to injection pump.
2.Disconnect sensor multi-plug.
3.Remove sensor assembly.
Refit
4.Position sensor assembly on injection pump and
secure with screws.
5.Connect multi-plug.
6.Adjust sensor
See Adjustment, EGR throttle
sensor
EGR CONTROL UNIT
Service repair no - 17.45.07
Remove
1.Raise centre seat, or cubby box
See CHASSIS
AND BODY, Repair, Cubby box
to gain access
to EGR control unit harness.
2.Disconnect control unit multi-plug and remove
centre seat or cubby box.
3.Remove 4 screws and detach control unit from
seat or cubby box base.
Refit
4.Secure EGR control unit to base of centre seat
or cubby box.
5.Position centre seat or cubby box and connect
control unit multi-plug.
6.Fit centre seat, or cubby box.
See CHASSIS
AND BODY, Repair, Cubby box
Page 373 of 455
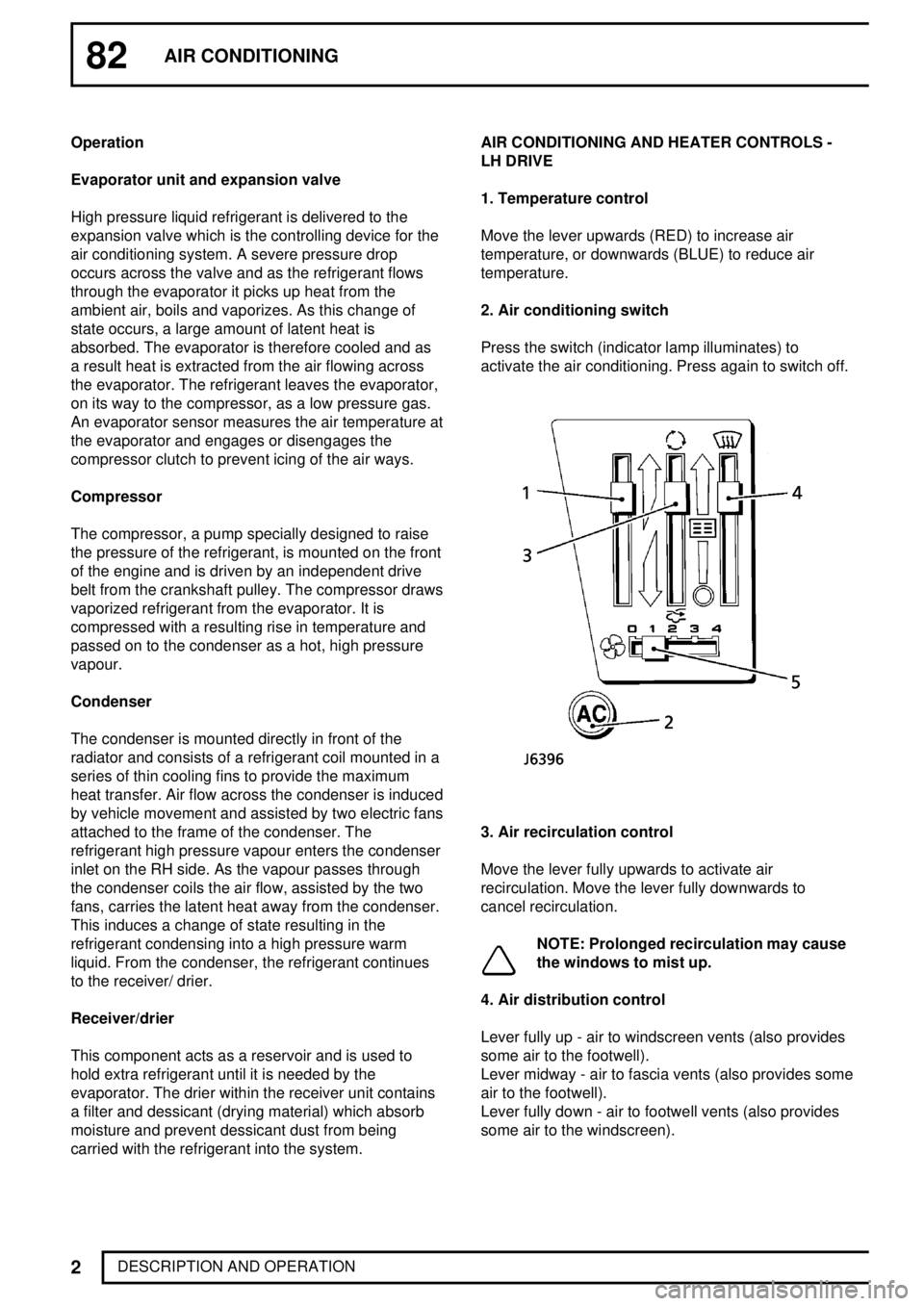
82AIR CONDITIONING
2
DESCRIPTION AND OPERATION Operation
Evaporator unit and expansion valve
High pressure liquid refrigerant is delivered to the
expansion valve which is the controlling device for the
air conditioning system. A severe pressure drop
occurs across the valve and as the refrigerant flows
through the evaporator it picks up heat from the
ambient air, boils and vaporizes. As this change of
state occurs, a large amount of latent heat is
absorbed. The evaporator is therefore cooled and as
a result heat is extracted from the air flowing across
the evaporator. The refrigerant leaves the evaporator,
on its way to the compressor, as a low pressure gas.
An evaporator sensor measures the air temperature at
the evaporator and engages or disengages the
compressor clutch to prevent icing of the air ways.
Compressor
The compressor, a pump specially designed to raise
the pressure of the refrigerant, is mounted on the front
of the engine and is driven by an independent drive
belt from the crankshaft pulley. The compressor draws
vaporized refrigerant from the evaporator. It is
compressed with a resulting rise in temperature and
passed on to the condenser as a hot, high pressure
vapour.
Condenser
The condenser is mounted directly in front of the
radiator and consists of a refrigerant coil mounted in a
series of thin cooling fins to provide the maximum
heat transfer. Air flow across the condenser is induced
by vehicle movement and assisted by two electric fans
attached to the frame of the condenser. The
refrigerant high pressure vapour enters the condenser
inlet on the RH side. As the vapour passes through
the condenser coils the air flow, assisted by the two
fans, carries the latent heat away from the condenser.
This induces a change of state resulting in the
refrigerant condensing into a high pressure warm
liquid. From the condenser, the refrigerant continues
to the receiver/ drier.
Receiver/drier
This component acts as a reservoir and is used to
hold extra refrigerant until it is needed by the
evaporator. The drier within the receiver unit contains
a filter and dessicant (drying material) which absorb
moisture and prevent dessicant dust from being
carried with the refrigerant into the system.AIR CONDITIONING AND HEATER CONTROLS -
LH DRIVE
1. Temperature control
Move the lever upwards (RED) to increase air
temperature, or downwards (BLUE) to reduce air
temperature.
2. Air conditioning switch
Press the switch (indicator lamp illuminates) to
activate the air conditioning. Press again to switch off.
3. Air recirculation control
Move the lever fully upwards to activate air
recirculation. Move the lever fully downwards to
cancel recirculation.
NOTE: Prolonged recirculation may cause
the windows to mist up.
4. Air distribution control
Lever fully up - air to windscreen vents (also provides
some air to the footwell).
Lever midway - air to fascia vents (also provides some
air to the footwell).
Lever fully down - air to footwell vents (also provides
some air to the windscreen).
Page 391 of 455
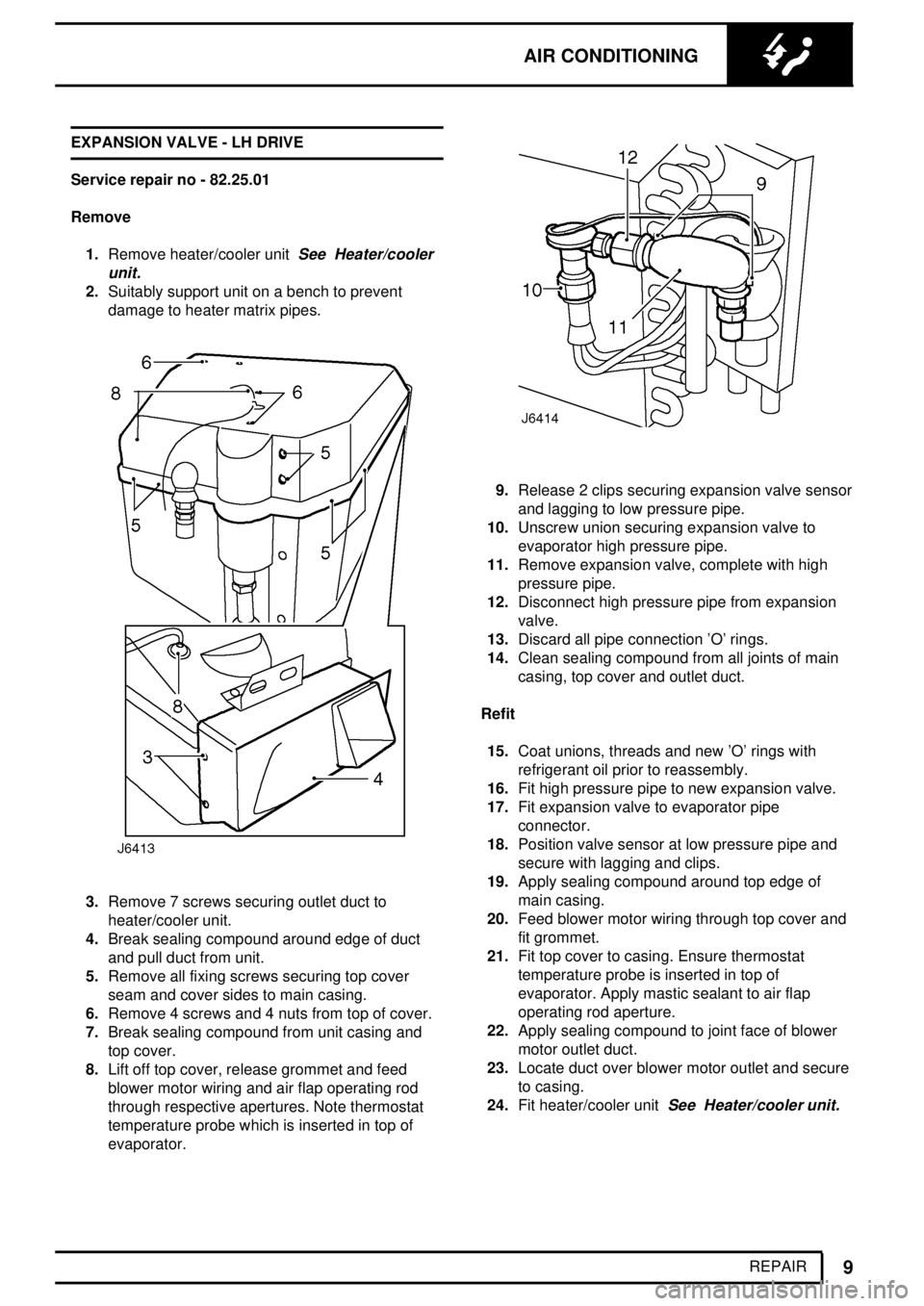
AIR CONDITIONING
9
REPAIR EXPANSION VALVE - LH DRIVE
Service repair no - 82.25.01
Remove
1.Remove heater/cooler unit
See Heater/cooler
unit.
2.Suitably support unit on a bench to prevent
damage to heater matrix pipes.
3.Remove 7 screws securing outlet duct to
heater/cooler unit.
4.Break sealing compound around edge of duct
and pull duct from unit.
5.Remove all fixing screws securing top cover
seam and cover sides to main casing.
6.Remove 4 screws and 4 nuts from top of cover.
7.Break sealing compound from unit casing and
top cover.
8.Lift off top cover, release grommet and feed
blower motor wiring and air flap operating rod
through respective apertures. Note thermostat
temperature probe which is inserted in top of
evaporator.
9.Release 2 clips securing expansion valve sensor
and lagging to low pressure pipe.
10.Unscrew union securing expansion valve to
evaporator high pressure pipe.
11.Remove expansion valve, complete with high
pressure pipe.
12.Disconnect high pressure pipe from expansion
valve.
13.Discard all pipe connection 'O' rings.
14.Clean sealing compound from all joints of main
casing, top cover and outlet duct.
Refit
15.Coat unions, threads and new 'O' rings with
refrigerant oil prior to reassembly.
16.Fit high pressure pipe to new expansion valve.
17.Fit expansion valve to evaporator pipe
connector.
18.Position valve sensor at low pressure pipe and
secure with lagging and clips.
19.Apply sealing compound around top edge of
main casing.
20.Feed blower motor wiring through top cover and
fit grommet.
21.Fit top cover to casing. Ensure thermostat
temperature probe is inserted in top of
evaporator. Apply mastic sealant to air flap
operating rod aperture.
22.Apply sealing compound to joint face of blower
motor outlet duct.
23.Locate duct over blower motor outlet and secure
to casing.
24.Fit heater/cooler unit
See Heater/cooler unit.
Page 398 of 455
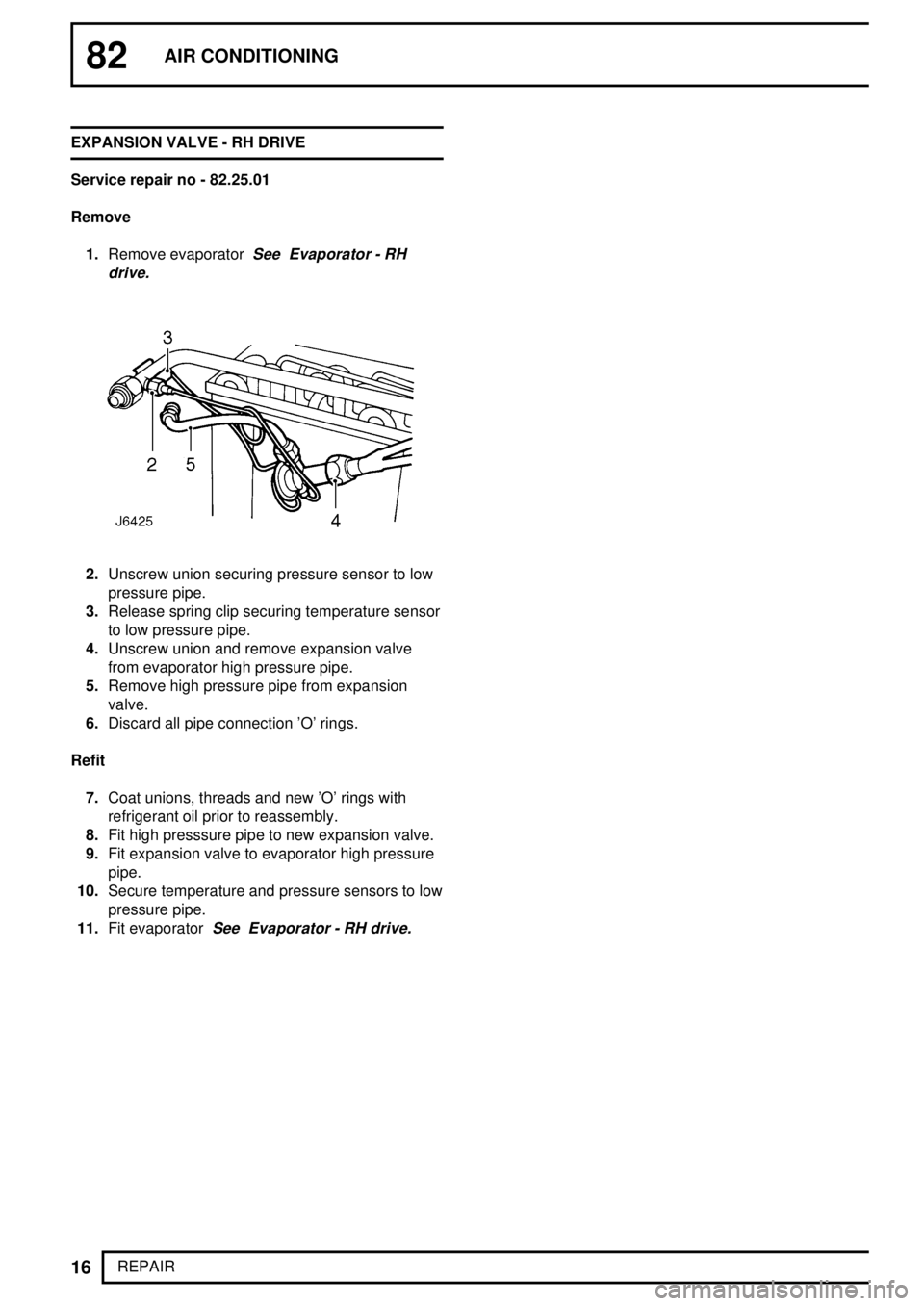
82AIR CONDITIONING
16
REPAIR EXPANSION VALVE - RH DRIVE
Service repair no - 82.25.01
Remove
1.Remove evaporator
See Evaporator - RH
drive.
2.Unscrew union securing pressure sensor to low
pressure pipe.
3.Release spring clip securing temperature sensor
to low pressure pipe.
4.Unscrew union and remove expansion valve
from evaporator high pressure pipe.
5.Remove high pressure pipe from expansion
valve.
6.Discard all pipe connection 'O' rings.
Refit
7.Coat unions, threads and new 'O' rings with
refrigerant oil prior to reassembly.
8.Fit high presssure pipe to new expansion valve.
9.Fit expansion valve to evaporator high pressure
pipe.
10.Secure temperature and pressure sensors to low
pressure pipe.
11.Fit evaporator
See Evaporator - RH drive.
Page 415 of 455
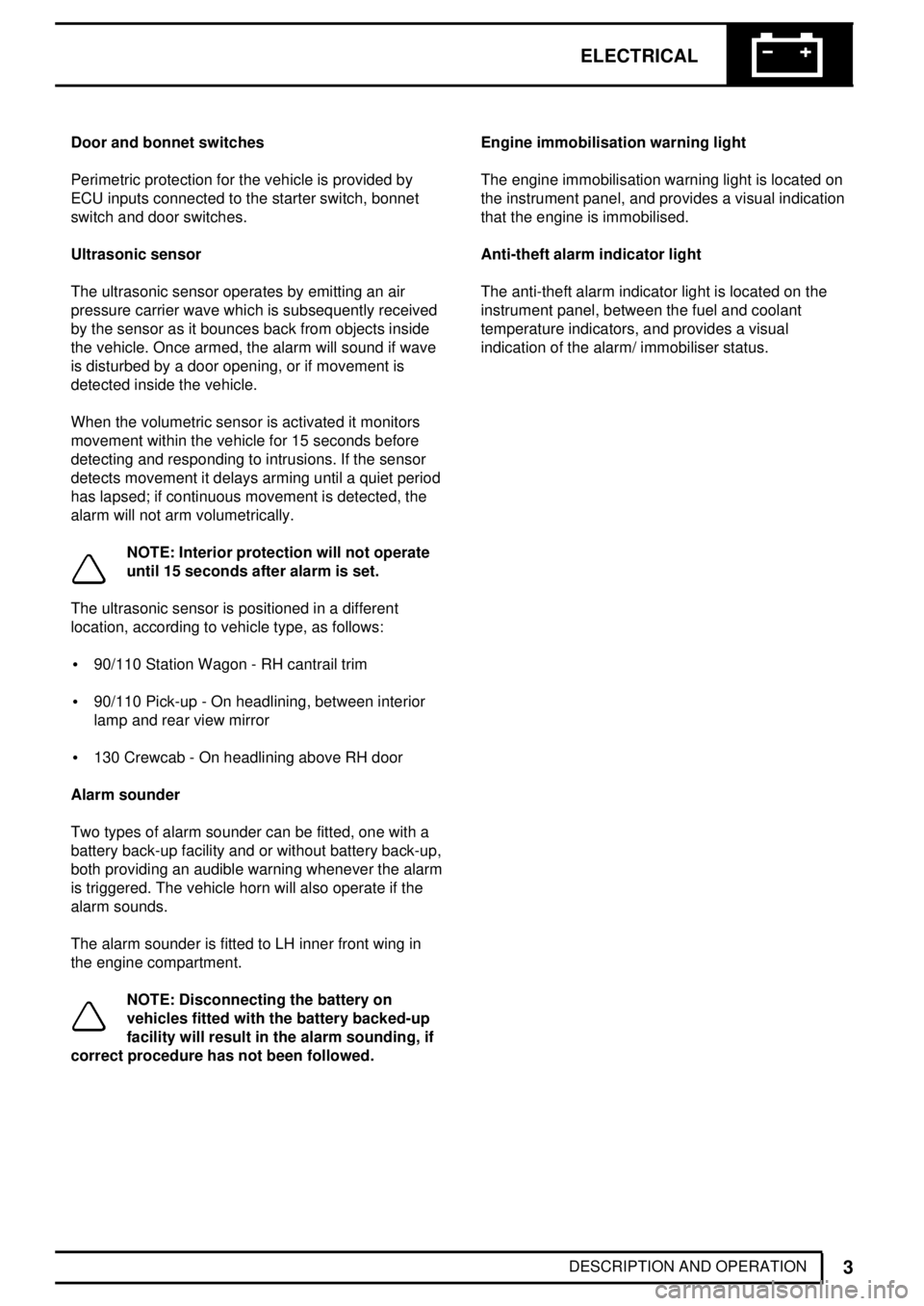
ELECTRICAL
3
DESCRIPTION AND OPERATION Door and bonnet switches
Perimetric protection for the vehicle is provided by
ECU inputs connected to the starter switch, bonnet
switch and door switches.
Ultrasonic sensor
The ultrasonic sensor operates by emitting an air
pressure carrier wave which is subsequently received
by the sensor as it bounces back from objects inside
the vehicle. Once armed, the alarm will sound if wave
is disturbed by a door opening, or if movement is
detected inside the vehicle.
When the volumetric sensor is activated it monitors
movement within the vehicle for 15 seconds before
detecting and responding to intrusions. If the sensor
detects movement it delays arming until a quiet period
has lapsed; if continuous movement is detected, the
alarm will not arm volumetrically.
NOTE: Interior protection will not operate
until 15 seconds after alarm is set.
The ultrasonic sensor is positioned in a different
location, according to vehicle type, as follows:
·90/110 Station Wagon - RH cantrail trim
·90/110 Pick-up - On headlining, between interior
lamp and rear view mirror
·130 Crewcab - On headlining above RH door
Alarm sounder
Two types of alarm sounder can be fitted, one with a
battery back-up facility and or without battery back-up,
both providing an audible warning whenever the alarm
is triggered. The vehicle horn will also operate if the
alarm sounds.
The alarm sounder is fitted to LH inner front wing in
the engine compartment.
NOTE: Disconnecting the battery on
vehicles fitted with the battery backed-up
facility will result in the alarm sounding, if
correct procedure has not been followed.Engine immobilisation warning light
The engine immobilisation warning light is located on
the instrument panel, and provides a visual indication
that the engine is immobilised.
Anti-theft alarm indicator light
The anti-theft alarm indicator light is located on the
instrument panel, between the fuel and coolant
temperature indicators, and provides a visual
indication of the alarm/ immobiliser status.
Page 416 of 455
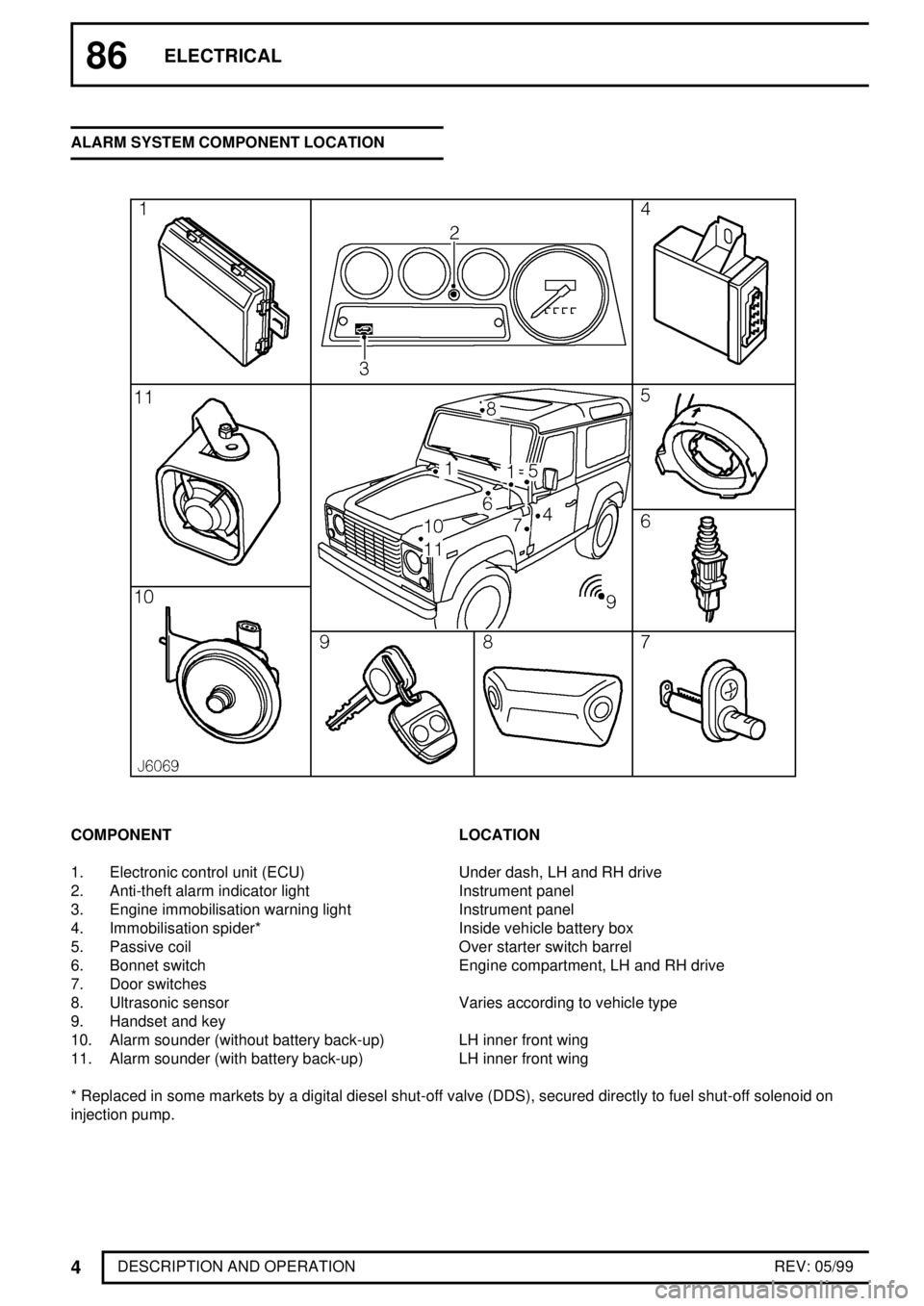
86ELECTRICAL
4
DESCRIPTION AND OPERATION REV: 05/99 ALARM SYSTEM COMPONENT LOCATION
COMPONENT LOCATION
1. Electronic control unit (ECU) Under dash, LH and RH drive
2. Anti-theft alarm indicator light Instrument panel
3. Engine immobilisation warning light Instrument panel
4. Immobilisation spider* Inside vehicle battery box
5. Passive coil Over starter switch barrel
6. Bonnet switch Engine compartment, LH and RH drive
7. Door switches
8. Ultrasonic sensor Varies according to vehicle type
9. Handset and key
10. Alarm sounder (without battery back-up) LH inner front wing
11. Alarm sounder (with battery back-up) LH inner front wing
* Replaced in some markets by a digital diesel shut-off valve (DDS), secured directly to fuel shut-off solenoid on
injection pump.
Page 417 of 455
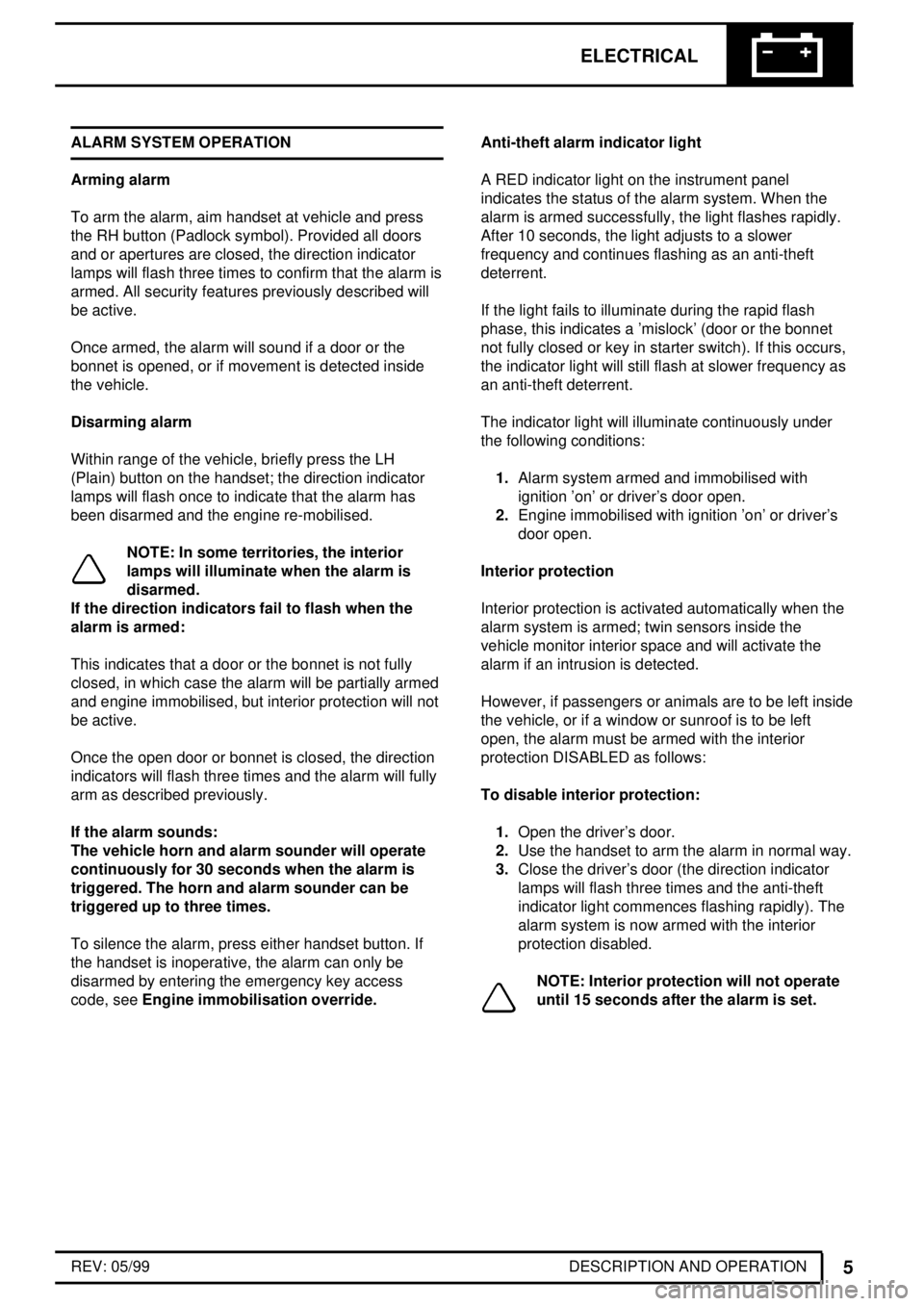
ELECTRICAL
5
DESCRIPTION AND OPERATION REV: 05/99 ALARM SYSTEM OPERATION
Arming alarm
To arm the alarm, aim handset at vehicle and press
the RH button (Padlock symbol). Provided all doors
and or apertures are closed, the direction indicator
lamps will flash three times to confirm that the alarm is
armed. All security features previously described will
be active.
Once armed, the alarm will sound if a door or the
bonnet is opened, or if movement is detected inside
the vehicle.
Disarming alarm
Within range of the vehicle, briefly press the LH
(Plain) button on the handset; the direction indicator
lamps will flash once to indicate that the alarm has
been disarmed and the engine re-mobilised.
NOTE: In some territories, the interior
lamps will illuminate when the alarm is
disarmed.
If the direction indicators fail to flash when the
alarm is armed:
This indicates that a door or the bonnet is not fully
closed, in which case the alarm will be partially armed
and engine immobilised, but interior protection will not
be active.
Once the open door or bonnet is closed, the direction
indicators will flash three times and the alarm will fully
arm as described previously.
If the alarm sounds:
The vehicle horn and alarm sounder will operate
continuously for 30 seconds when the alarm is
triggered. The horn and alarm sounder can be
triggered up to three times.
To silence the alarm, press either handset button. If
the handset is inoperative, the alarm can only be
disarmed by entering the emergency key access
code, seeEngine immobilisation override.Anti-theft alarm indicator light
A RED indicator light on the instrument panel
indicates the status of the alarm system. When the
alarm is armed successfully, the light flashes rapidly.
After 10 seconds, the light adjusts to a slower
frequency and continues flashing as an anti-theft
deterrent.
If the light fails to illuminate during the rapid flash
phase, this indicates a 'mislock' (door or the bonnet
not fully closed or key in starter switch). If this occurs,
the indicator light will still flash at slower frequency as
an anti-theft deterrent.
The indicator light will illuminate continuously under
the following conditions:
1.Alarm system armed and immobilised with
ignition 'on' or driver's door open.
2.Engine immobilised with ignition 'on' or driver's
door open.
Interior protection
Interior protection is activated automatically when the
alarm system is armed; twin sensors inside the
vehicle monitor interior space and will activate the
alarm if an intrusion is detected.
However, if passengers or animals are to be left inside
the vehicle, or if a window or sunroof is to be left
open, the alarm must be armed with the interior
protection DISABLED as follows:
To disable interior protection:
1.Open the driver's door.
2.Use the handset to arm the alarm in normal way.
3.Close the driver's door (the direction indicator
lamps will flash three times and the anti-theft
indicator light commences flashing rapidly). The
alarm system is now armed with the interior
protection disabled.
NOTE: Interior protection will not operate
until 15 seconds after the alarm is set.
Page 421 of 455
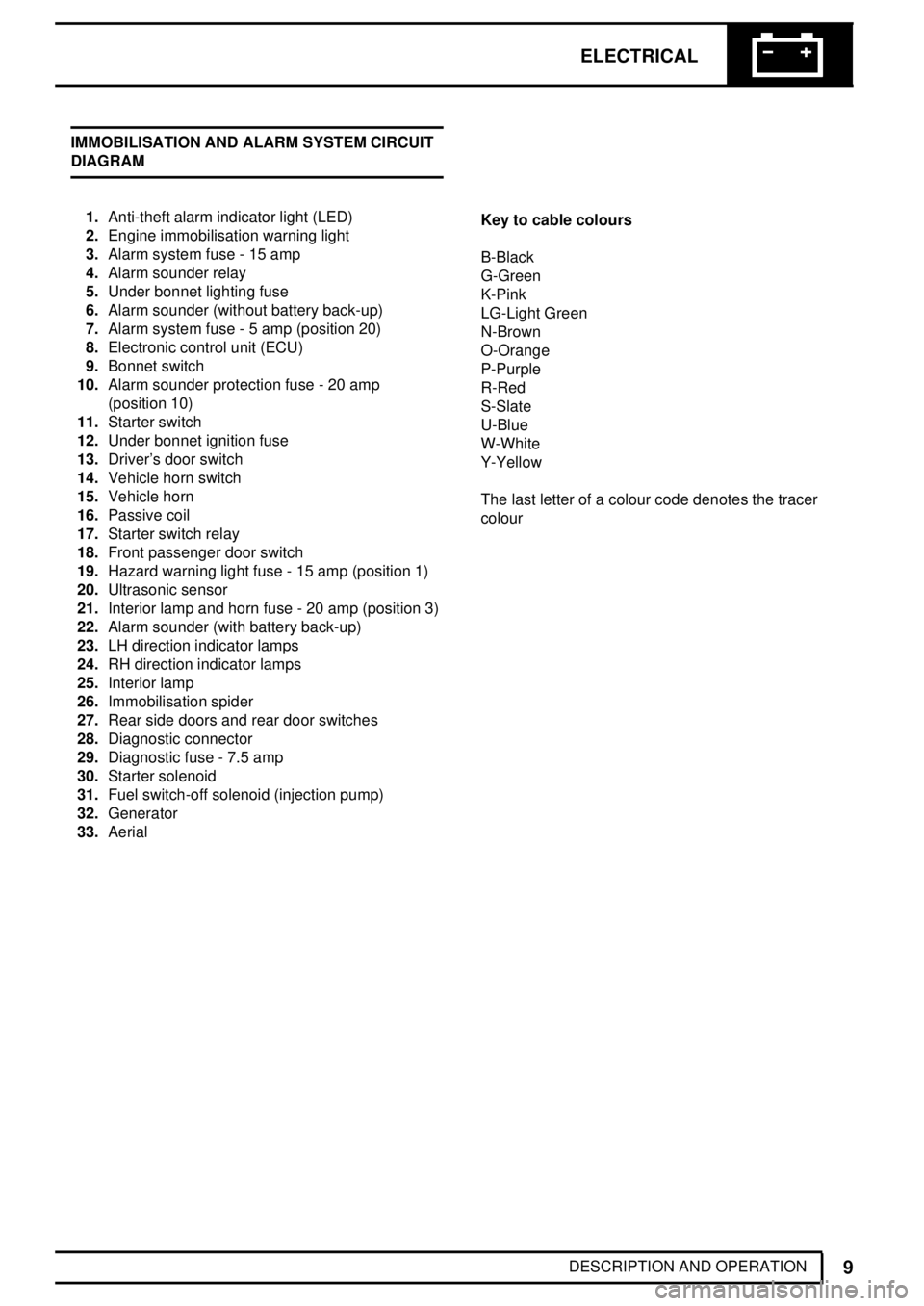
ELECTRICAL
9
DESCRIPTION AND OPERATION IMMOBILISATION AND ALARM SYSTEM CIRCUIT
DIAGRAM
1.Anti-theft alarm indicator light (LED)
2.Engine immobilisation warning light
3.Alarm system fuse - 15 amp
4.Alarm sounder relay
5.Under bonnet lighting fuse
6.Alarm sounder (without battery back-up)
7.Alarm system fuse - 5 amp (position 20)
8.Electronic control unit (ECU)
9.Bonnet switch
10.Alarm sounder protection fuse - 20 amp
(position 10)
11.Starter switch
12.Under bonnet ignition fuse
13.Driver's door switch
14.Vehicle horn switch
15.Vehicle horn
16.Passive coil
17.Starter switch relay
18.Front passenger door switch
19.Hazard warning light fuse - 15 amp (position 1)
20.Ultrasonic sensor
21.Interior lamp and horn fuse - 20 amp (position 3)
22.Alarm sounder (with battery back-up)
23.LH direction indicator lamps
24.RH direction indicator lamps
25.Interior lamp
26.Immobilisation spider
27.Rear side doors and rear door switches
28.Diagnostic connector
29.Diagnostic fuse - 7.5 amp
30.Starter solenoid
31.Fuel switch-off solenoid (injection pump)
32.Generator
33.AerialKey to cable colours
B-Black
G-Green
K-Pink
LG-Light Green
N-Brown
O-Orange
P-Purple
R-Red
S-Slate
U-Blue
W-White
Y-Yellow
The last letter of a colour code denotes the tracer
colour