compression ratio LAND ROVER DEFENDER 1996 Workshop Manual
[x] Cancel search | Manufacturer: LAND ROVER, Model Year: 1996, Model line: DEFENDER, Model: LAND ROVER DEFENDER 1996Pages: 455, PDF Size: 6.44 MB
Page 19 of 455
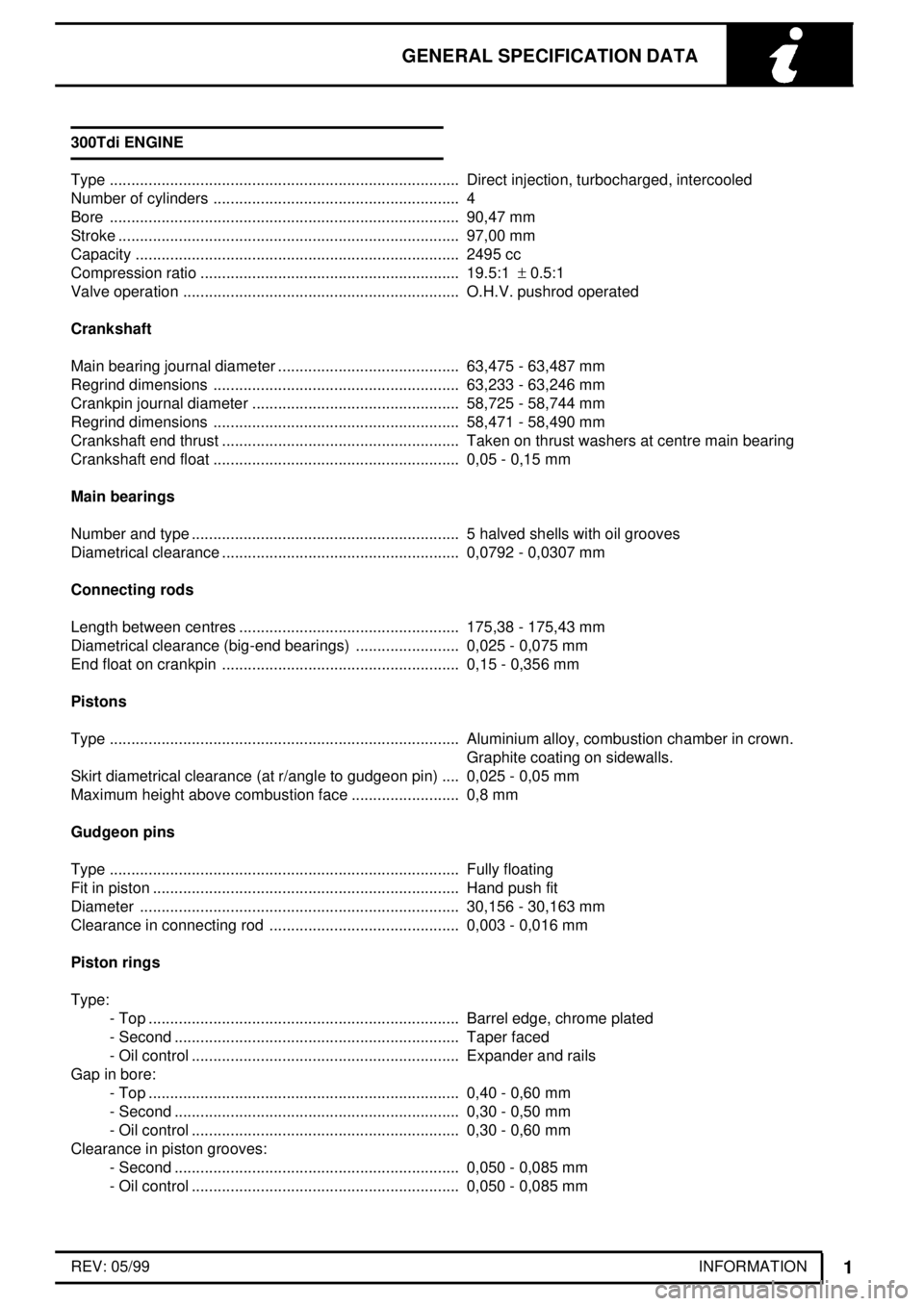
GENERAL SPECIFICATION DATA
1
INFORMATION REV: 05/99 300Tdi ENGINE
Type Direct injection, turbocharged, intercooled.................................................................................
Number of cylinders 4.........................................................
Bore 90,47 mm.................................................................................
Stroke 97,00 mm...............................................................................
Capacity 2495 cc...........................................................................
Compression ratio 19.5:1±0.5:1 ............................................................
Valve operation O.H.V. pushrod operated................................................................
Crankshaft
Main bearing journal diameter 63,475 - 63,487 mm..........................................
Regrind dimensions 63,233 - 63,246 mm.........................................................
Crankpin journal diameter 58,725 - 58,744 mm................................................
Regrind dimensions 58,471 - 58,490 mm.........................................................
Crankshaft end thrust Taken on thrust washers at centre main bearing.......................................................
Crankshaft end float 0,05 - 0,15 mm.........................................................
Main bearings
Number and type 5 halved shells with oil grooves..............................................................
Diametrical clearance 0,0792 - 0,0307 mm.......................................................
Connecting rods
Length between centres 175,38 - 175,43 mm...................................................
Diametrical clearance (big-end bearings) 0,025 - 0,075 mm........................
End float on crankpin 0,15 - 0,356 mm.......................................................
Pistons
Type Aluminium alloy, combustion chamber in crown..................................................................................
Graphite coating on sidewalls.
Skirt diametrical clearance (at r/angle to gudgeon pin) 0,025 - 0,05 mm....
Maximum height above combustion face 0,8 mm.........................
Gudgeon pins
Type Fully floating.................................................................................
Fit in piston Hand push fit.......................................................................
Diameter 30,156 - 30,163 mm..........................................................................
Clearance in connecting rod 0,003 - 0,016 mm............................................
Piston rings
Type:
- Top Barrel edge, chrome plated........................................................................
- Second Taper faced..................................................................
- Oil control Expander and rails..............................................................
Gap in bore:
- Top 0,40 - 0,60 mm........................................................................
- Second 0,30 - 0,50 mm..................................................................
- Oil control 0,30 - 0,60 mm..............................................................
Clearance in piston grooves:
- Second 0,050 - 0,085 mm..................................................................
- Oil control 0,050 - 0,085 mm..............................................................
Page 60 of 455
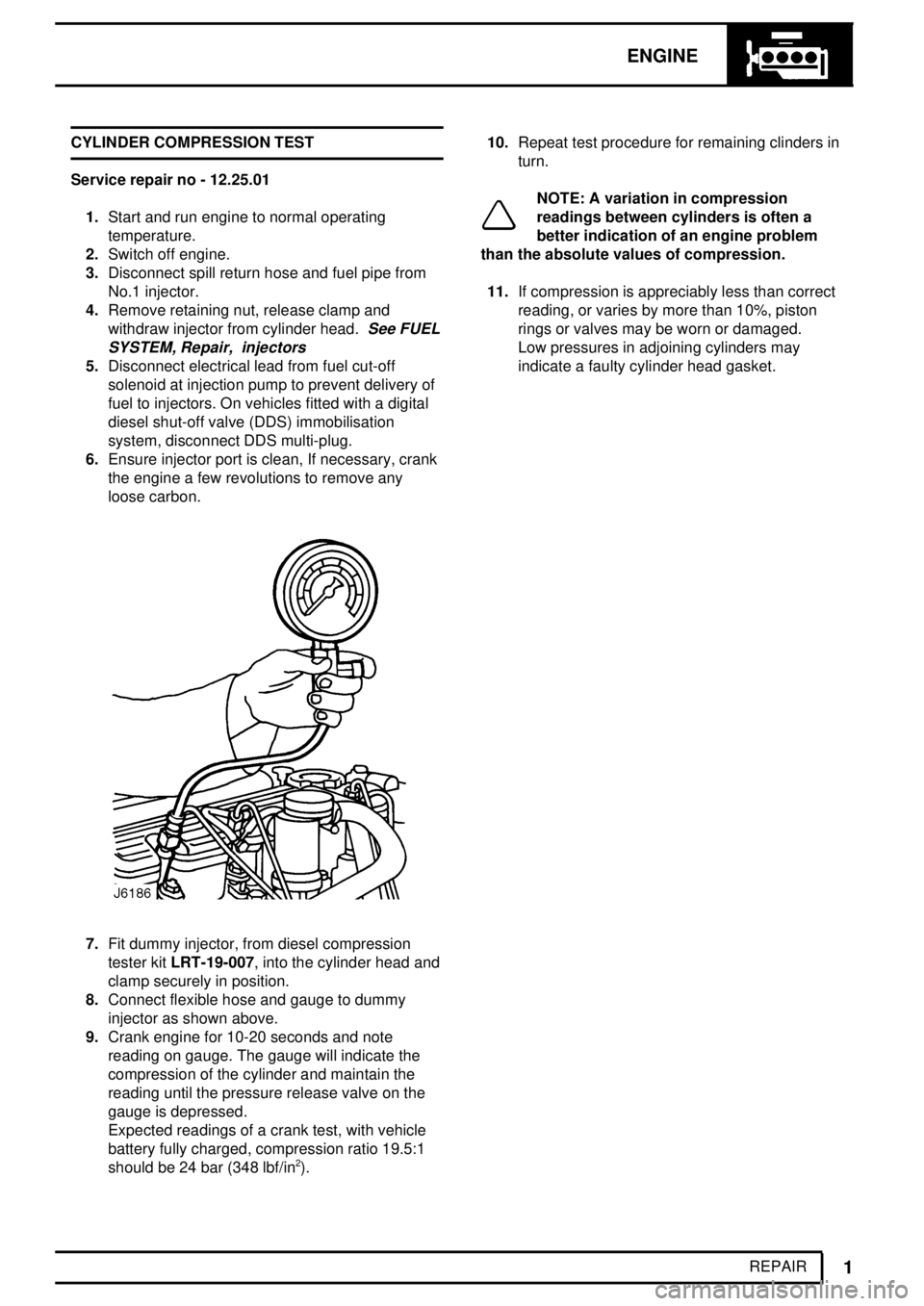
ENGINE
1
REPAIR CYLINDER COMPRESSION TEST
Service repair no - 12.25.01
1.Start and run engine to normal operating
temperature.
2.Switch off engine.
3.Disconnect spill return hose and fuel pipe from
No.1 injector.
4.Remove retaining nut, release clamp and
withdraw injector from cylinder head.
See FUEL
SYSTEM, Repair, injectors
5.Disconnect electrical lead from fuel cut-off
solenoid at injection pump to prevent delivery of
fuel to injectors. On vehicles fitted with a digital
diesel shut-off valve (DDS) immobilisation
system, disconnect DDS multi-plug.
6.Ensure injector port is clean, If necessary, crank
the engine a few revolutions to remove any
loose carbon.
7.Fit dummy injector, from diesel compression
tester kitLRT-19-007, into the cylinder head and
clamp securely in position.
8.Connect flexible hose and gauge to dummy
injector as shown above.
9.Crank engine for 10-20 seconds and note
reading on gauge. The gauge will indicate the
compression of the cylinder and maintain the
reading until the pressure release valve on the
gauge is depressed.
Expected readings of a crank test, with vehicle
battery fully charged, compression ratio 19.5:1
should be 24 bar (348 lbf/in
2).10.Repeat test procedure for remaining clinders in
turn.
NOTE: A variation in compression
readings between cylinders is often a
better indication of an engine problem
than the absolute values of compression.
11.If compression is appreciably less than correct
reading, or varies by more than 10%, piston
rings or valves may be worn or damaged.
Low pressures in adjoining cylinders may
indicate a faulty cylinder head gasket.
Page 96 of 455
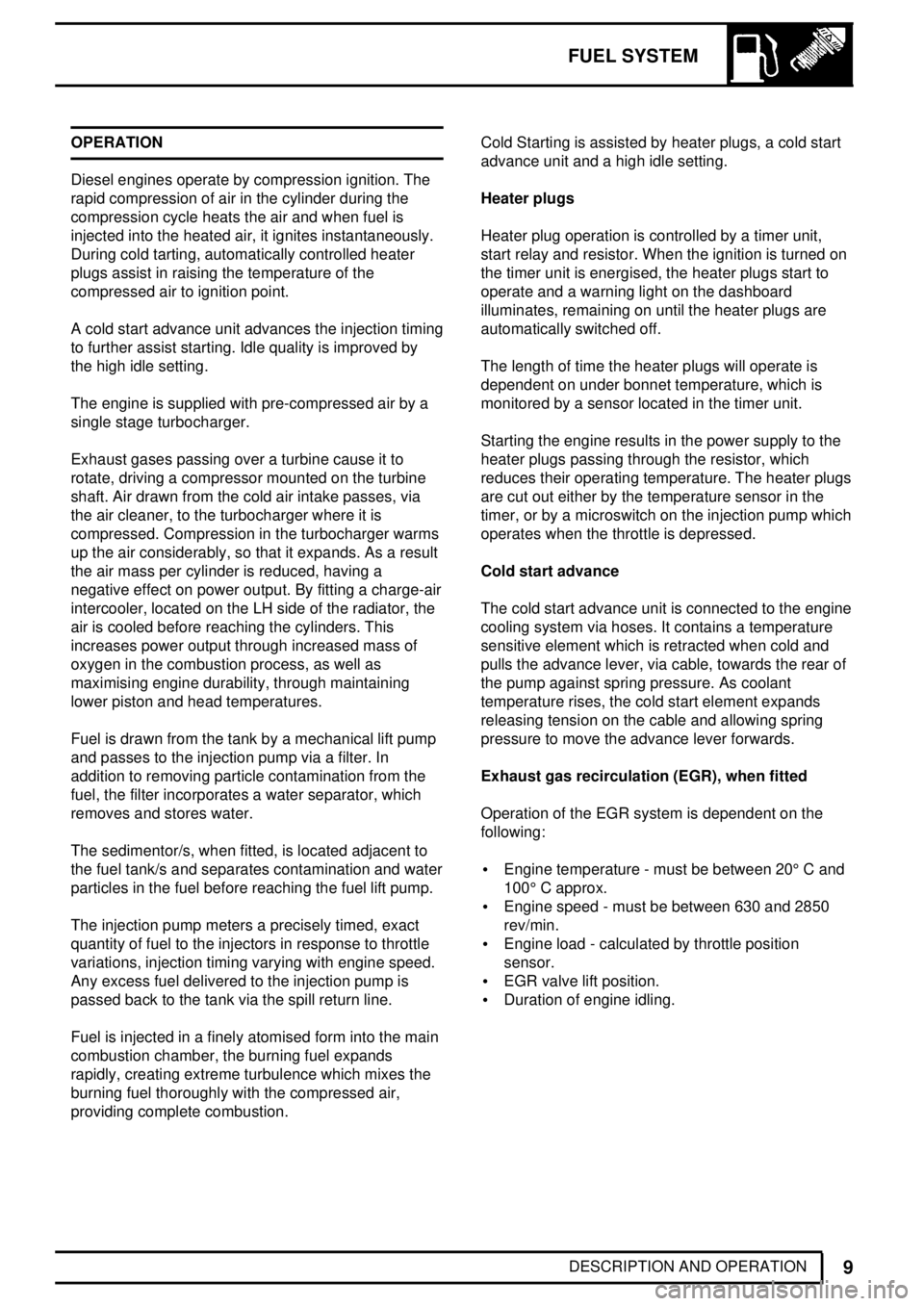
FUEL SYSTEM
9
DESCRIPTION AND OPERATION OPERATION
Diesel engines operate by compression ignition. The
rapid compression of air in the cylinder during the
compression cycle heats the air and when fuel is
injected into the heated air, it ignites instantaneously.
During cold tarting, automatically controlled heater
plugs assist in raising the temperature of the
compressed air to ignition point.
A cold start advance unit advances the injection timing
to further assist starting. Idle quality is improved by
the high idle setting.
The engine is supplied with pre-compressed air by a
single stage turbocharger.
Exhaust gases passing over a turbine cause it to
rotate, driving a compressor mounted on the turbine
shaft. Air drawn from the cold air intake passes, via
the air cleaner, to the turbocharger where it is
compressed. Compression in the turbocharger warms
up the air considerably, so that it expands. As a result
the air mass per cylinder is reduced, having a
negative effect on power output. By fitting a charge-air
intercooler, located on the LH side of the radiator, the
air is cooled before reaching the cylinders. This
increases power output through increased mass of
oxygen in the combustion process, as well as
maximising engine durability, through maintaining
lower piston and head temperatures.
Fuel is drawn from the tank by a mechanical lift pump
and passes to the injection pump via a filter. In
addition to removing particle contamination from the
fuel, the filter incorporates a water separator, which
removes and stores water.
The sedimentor/s, when fitted, is located adjacent to
the fuel tank/s and separates contamination and water
particles in the fuel before reaching the fuel lift pump.
The injection pump meters a precisely timed, exact
quantity of fuel to the injectors in response to throttle
variations, injection timing varying with engine speed.
Any excess fuel delivered to the injection pump is
passed back to the tank via the spill return line.
Fuel is injected in a finely atomised form into the main
combustion chamber, the burning fuel expands
rapidly, creating extreme turbulence which mixes the
burning fuel thoroughly with the compressed air,
providing complete combustion.Cold Starting is assisted by heater plugs, a cold start
advance unit and a high idle setting.
Heater plugs
Heater plug operation is controlled by a timer unit,
start relay and resistor. When the ignition is turned on
the timer unit is energised, the heater plugs start to
operate and a warning light on the dashboard
illuminates, remaining on until the heater plugs are
automatically switched off.
The length of time the heater plugs will operate is
dependent on under bonnet temperature, which is
monitored by a sensor located in the timer unit.
Starting the engine results in the power supply to the
heater plugs passing through the resistor, which
reduces their operating temperature. The heater plugs
are cut out either by the temperature sensor in the
timer, or by a microswitch on the injection pump which
operates when the throttle is depressed.
Cold start advance
The cold start advance unit is connected to the engine
cooling system via hoses. It contains a temperature
sensitive element which is retracted when cold and
pulls the advance lever, via cable, towards the rear of
the pump against spring pressure. As coolant
temperature rises, the cold start element expands
releasing tension on the cable and allowing spring
pressure to move the advance lever forwards.
Exhaust gas recirculation (EGR), when fitted
Operation of the EGR system is dependent on the
following:
·Engine temperature - must be between 20°C and
100°C approx.
·Engine speed - must be between 630 and 2850
rev/min.
·Engine load - calculated by throttle position
sensor.
·EGR valve lift position.
·Duration of engine idling.
Page 218 of 455
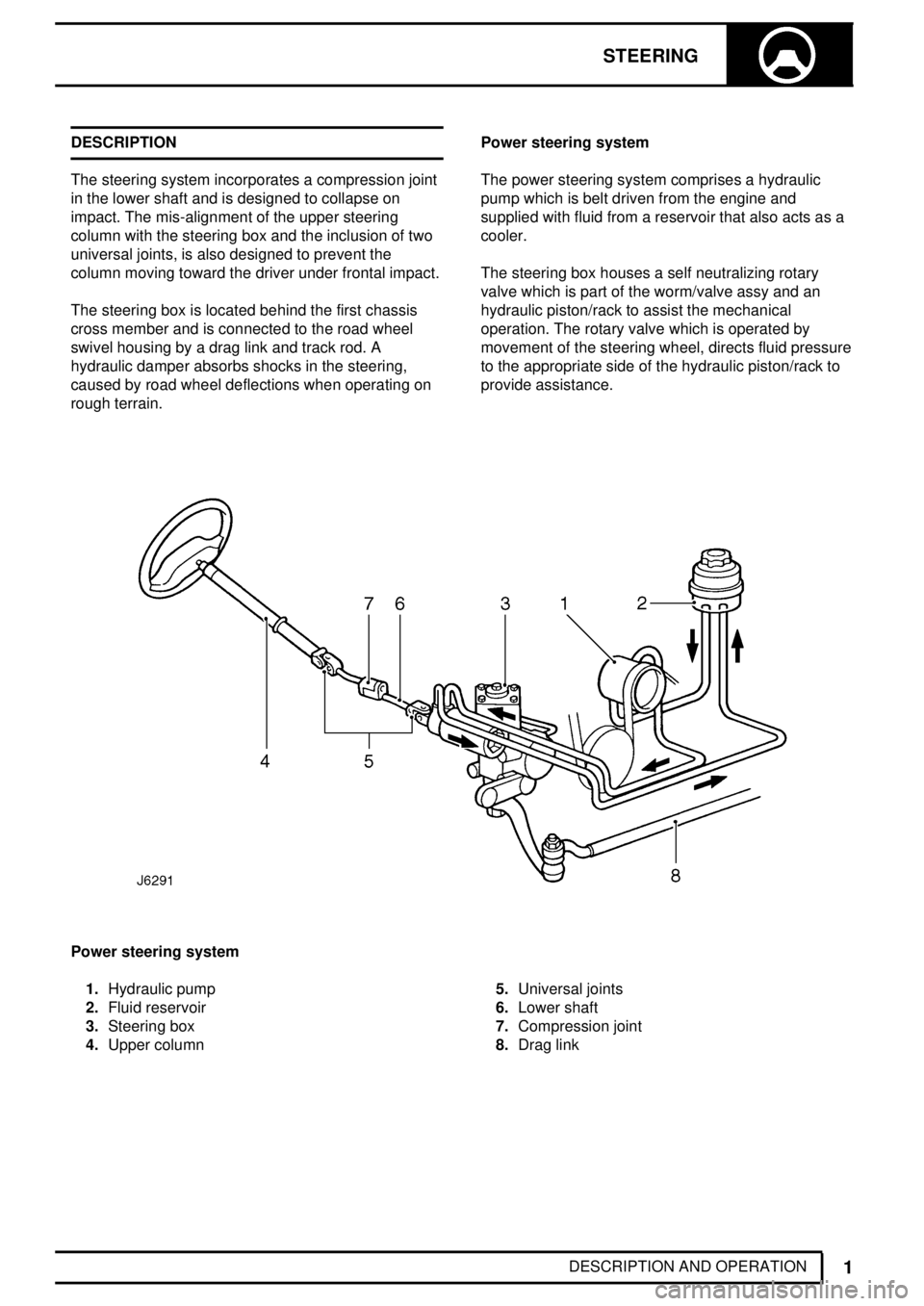
STEERING
1
DESCRIPTION AND OPERATION DESCRIPTION
The steering system incorporates a compression joint
in the lower shaft and is designed to collapse on
impact. The mis-alignment of the upper steering
column with the steering box and the inclusion of two
universal joints, is also designed to prevent the
column moving toward the driver under frontal impact.
The steering box is located behind the first chassis
cross member and is connected to the road wheel
swivel housing by a drag link and track rod. A
hydraulic damper absorbs shocks in the steering,
caused by road wheel deflections when operating on
rough terrain.Power steering system
The power steering system comprises a hydraulic
pump which is belt driven from the engine and
supplied with fluid from a reservoir that also acts as a
cooler.
The steering box houses a self neutralizing rotary
valve which is part of the worm/valve assy and an
hydraulic piston/rack to assist the mechanical
operation. The rotary valve which is operated by
movement of the steering wheel, directs fluid pressure
to the appropriate side of the hydraulic piston/rack to
provide assistance.
Power steering system
1.Hydraulic pump
2.Fluid reservoir
3.Steering box
4.Upper column5.Universal joints
6.Lower shaft
7.Compression joint
8.Drag link
Page 225 of 455
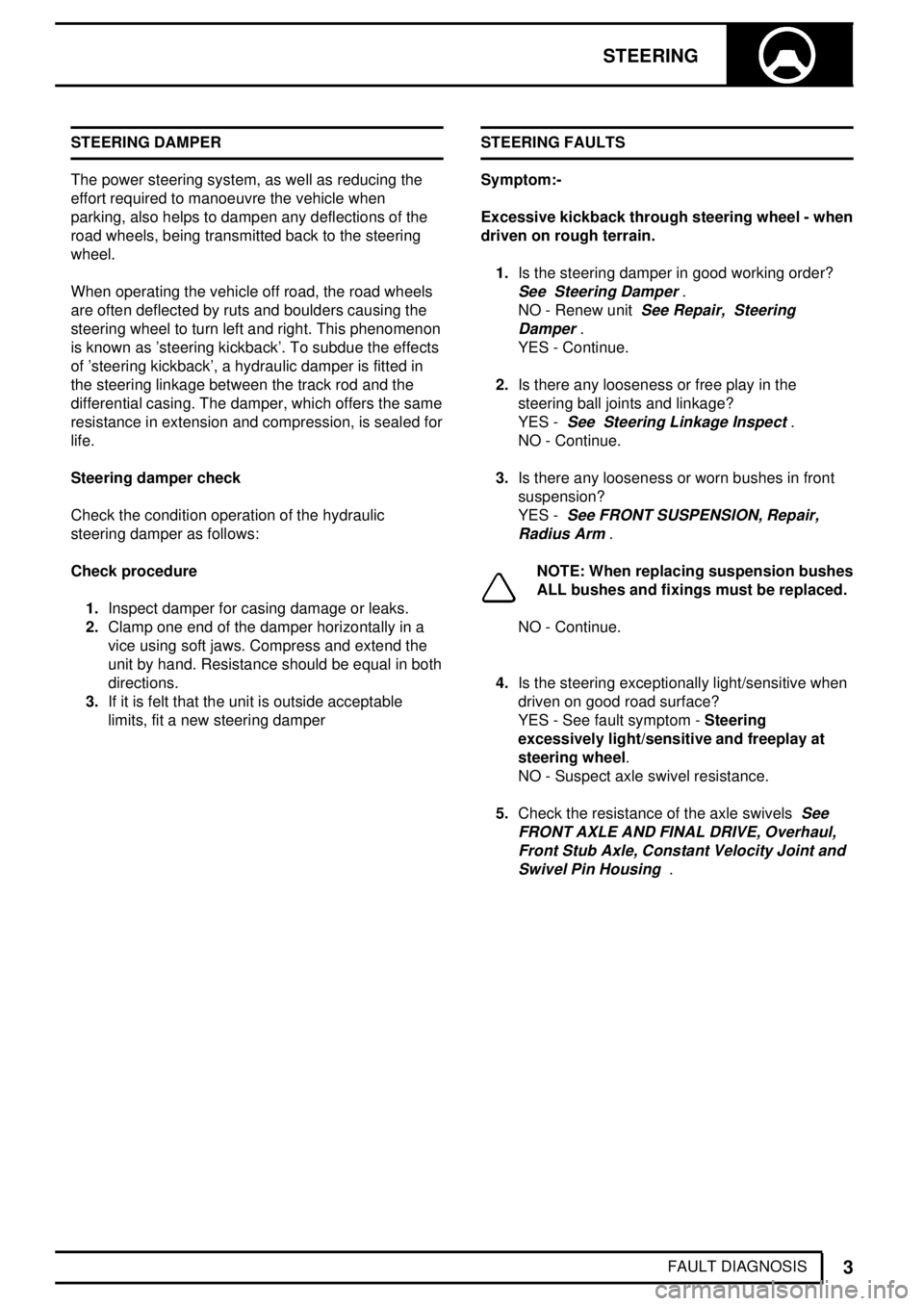
STEERING
3
FAULT DIAGNOSIS STEERING DAMPER
The power steering system, as well as reducing the
effort required to manoeuvre the vehicle when
parking, also helps to dampen any deflections of the
road wheels, being transmitted back to the steering
wheel.
When operating the vehicle off road, the road wheels
are often deflected by ruts and boulders causing the
steering wheel to turn left and right. This phenomenon
is known as 'steering kickback'. To subdue the effects
of 'steering kickback', a hydraulic damper is fitted in
the steering linkage between the track rod and the
differential casing. The damper, which offers the same
resistance in extension and compression, is sealed for
life.
Steering damper check
Check the condition operation of the hydraulic
steering damper as follows:
Check procedure
1.Inspect damper for casing damage or leaks.
2.Clamp one end of the damper horizontally in a
vice using soft jaws. Compress and extend the
unit by hand. Resistance should be equal in both
directions.
3.If it is felt that the unit is outside acceptable
limits, fit a new steering damperSTEERING FAULTS
Symptom:-
Excessive kickback through steering wheel - when
driven on rough terrain.
1.Is the steering damper in good working order?
See Steering Damper.
NO - Renew unit
See Repair, Steering
Damper
.
YES - Continue.
2.Is there any looseness or free play in the
steering ball joints and linkage?
YES -
See Steering Linkage Inspect.
NO - Continue.
3.Is there any looseness or worn bushes in front
suspension?
YES -
See FRONT SUSPENSION, Repair,
Radius Arm
.
NOTE: When replacing suspension bushes
ALL bushes and fixings must be replaced.
NO - Continue.
4.Is the steering exceptionally light/sensitive when
driven on good road surface?
YES - See fault symptom -Steering
excessively light/sensitive and freeplay at
steering wheel.
NO - Suspect axle swivel resistance.
5.Check the resistance of the axle swivels
See
FRONT AXLE AND FINAL DRIVE, Overhaul,
Front Stub Axle, Constant Velocity Joint and
Swivel Pin Housing
.