LAND ROVER DEFENDER 1999 Workshop Manual
Manufacturer: LAND ROVER, Model Year: 1999, Model line: DEFENDER, Model: LAND ROVER DEFENDER 1999Pages: 667, PDF Size: 8.76 MB
Page 501 of 667
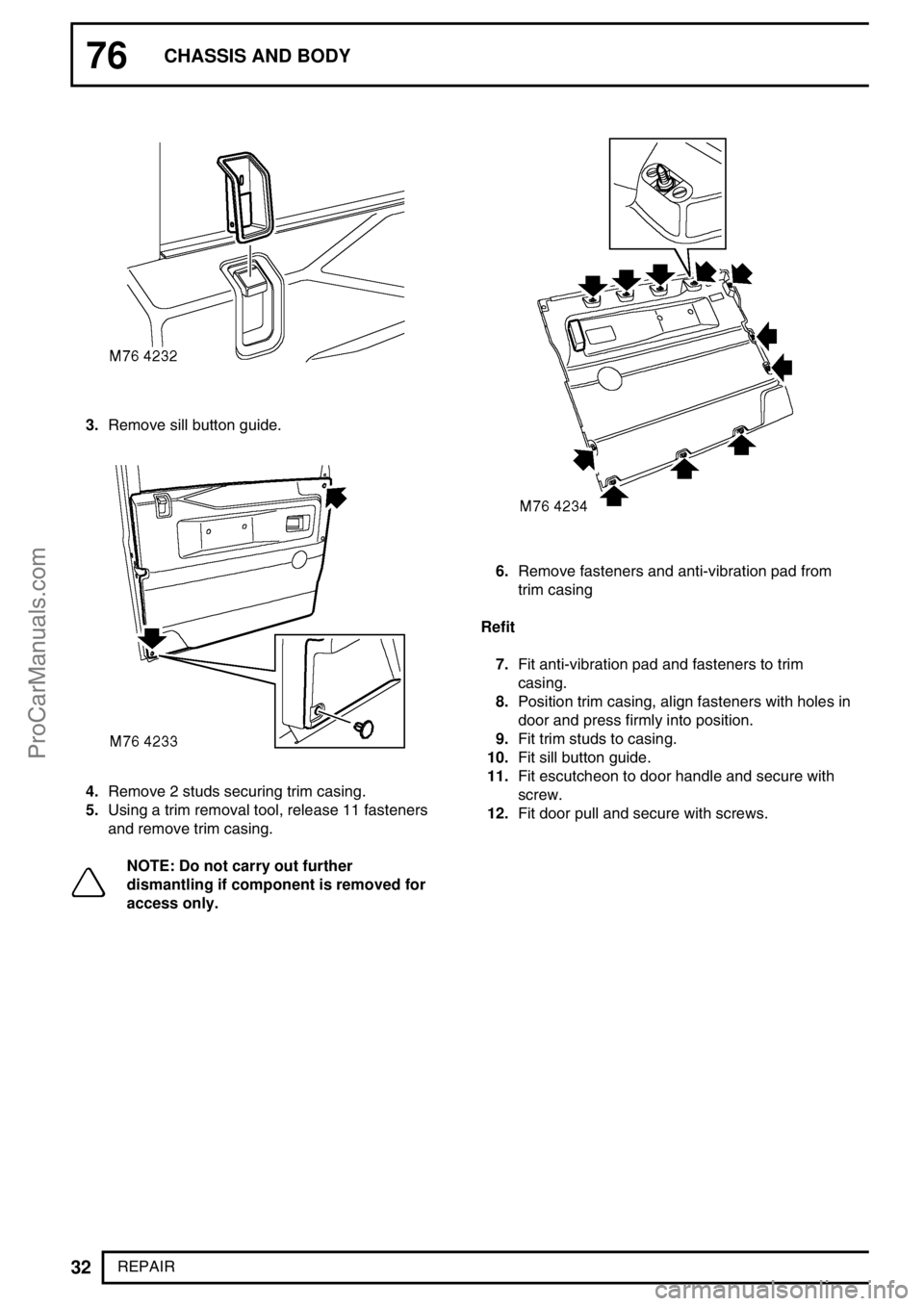
76CHASSIS AND BODY
32
REPAIR
3.Remove sill button guide.
4.Remove 2 studs securing trim casing.
5.Using a trim removal tool, release 11 fasteners
and remove trim casing.
NOTE: Do not carry out further
dismantling if component is removed for
access only.
6.Remove fasteners and anti-vibration pad from
trim casing
Refit
7.Fit anti-vibration pad and fasteners to trim
casing.
8.Position trim casing, align fasteners with holes in
door and press firmly into position.
9.Fit trim studs to casing.
10.Fit sill button guide.
11.Fit escutcheon to door handle and secure with
screw.
12.Fit door pull and secure with screws.
ProCarManuals.com
Page 502 of 667
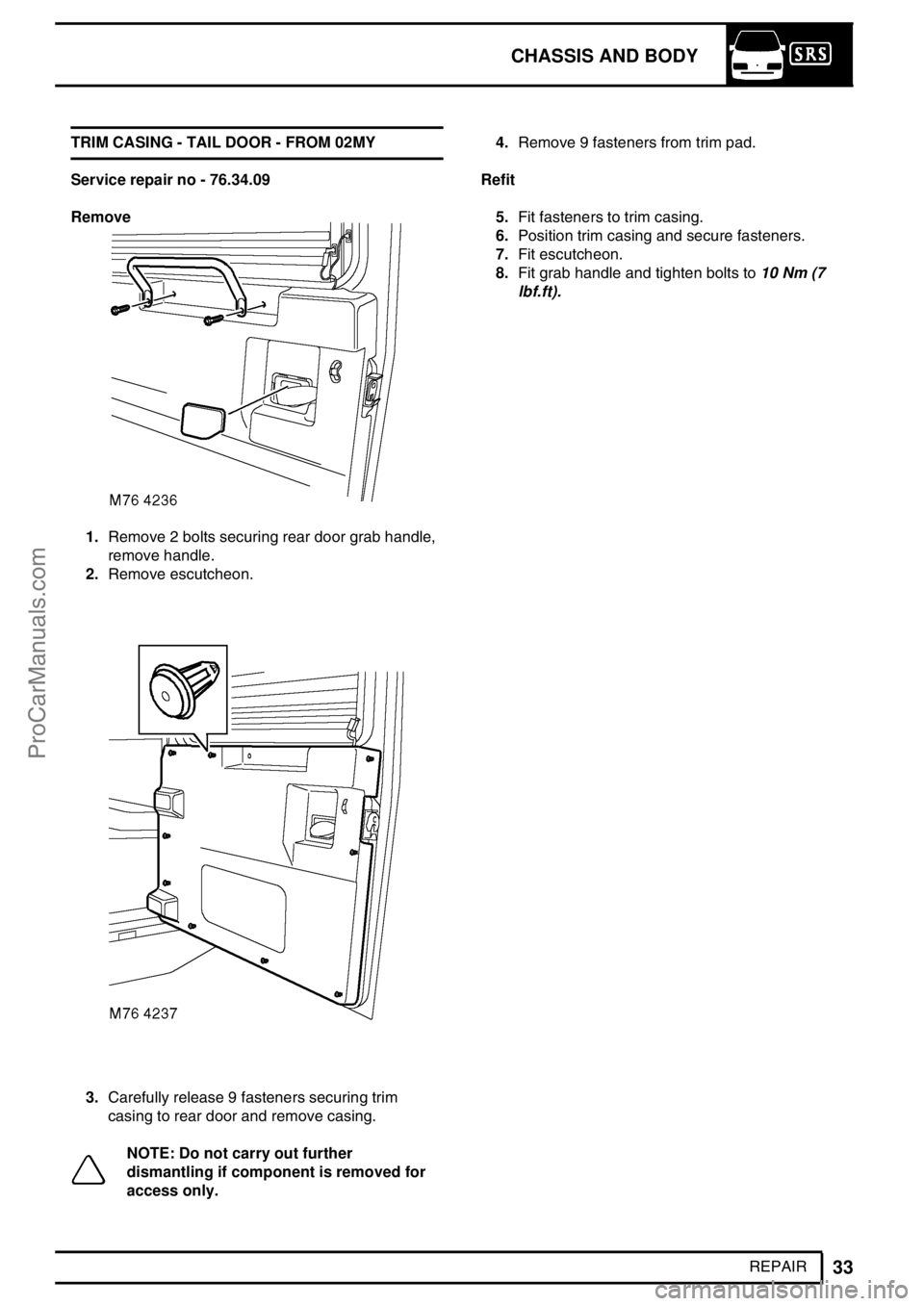
CHASSIS AND BODY
33
REPAIR TRIM CASING - TAIL DOOR - FROM 02MY
Service repair no - 76.34.09
Remove
1.Remove 2 bolts securing rear door grab handle,
remove handle.
2.Remove escutcheon.
3.Carefully release 9 fasteners securing trim
casing to rear door and remove casing.
NOTE: Do not carry out further
dismantling if component is removed for
access only.4.Remove 9 fasteners from trim pad.
Refit
5.Fit fasteners to trim casing.
6.Position trim casing and secure fasteners.
7.Fit escutcheon.
8.Fit grab handle and tighten bolts to10 Nm (7
lbf.ft).
ProCarManuals.com
Page 503 of 667
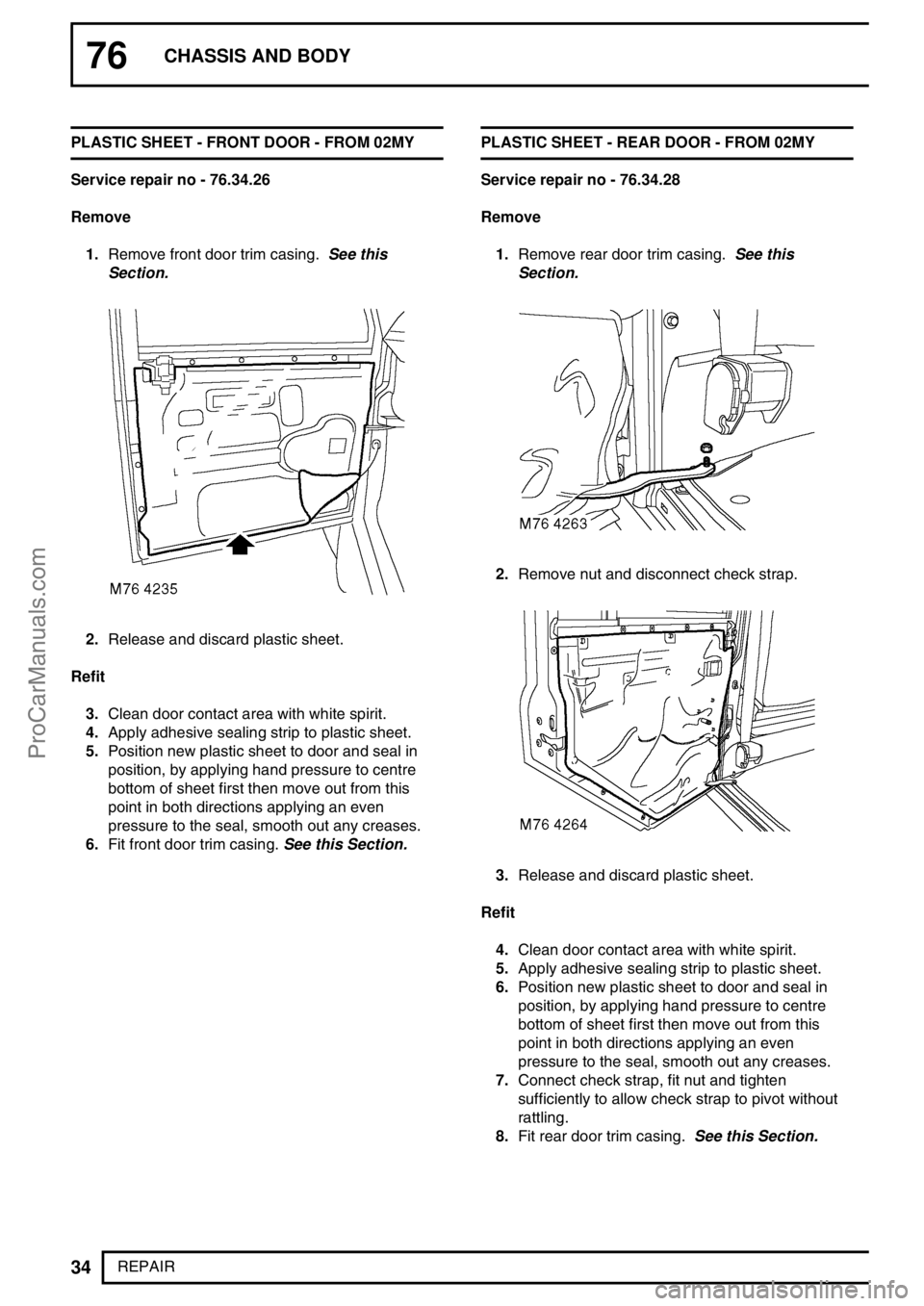
76CHASSIS AND BODY
34
REPAIR PLASTIC SHEET - FRONT DOOR - FROM 02MY
Service repair no - 76.34.26
Remove
1.Remove front door trim casing.See this
Section.
2.Release and discard plastic sheet.
Refit
3.Clean door contact area with white spirit.
4.Apply adhesive sealing strip to plastic sheet.
5.Position new plastic sheet to door and seal in
position, by applying hand pressure to centre
bottom of sheet first then move out from this
point in both directions applying an even
pressure to the seal, smooth out any creases.
6.Fit front door trim casing.See this Section.PLASTIC SHEET - REAR DOOR - FROM 02MY
Service repair no - 76.34.28
Remove
1.Remove rear door trim casing.See this
Section.
2.Remove nut and disconnect check strap.
3.Release and discard plastic sheet.
Refit
4.Clean door contact area with white spirit.
5.Apply adhesive sealing strip to plastic sheet.
6.Position new plastic sheet to door and seal in
position, by applying hand pressure to centre
bottom of sheet first then move out from this
point in both directions applying an even
pressure to the seal, smooth out any creases.
7.Connect check strap, fit nut and tighten
sufficiently to allow check strap to pivot without
rattling.
8.Fit rear door trim casing.See this Section.
ProCarManuals.com
Page 504 of 667
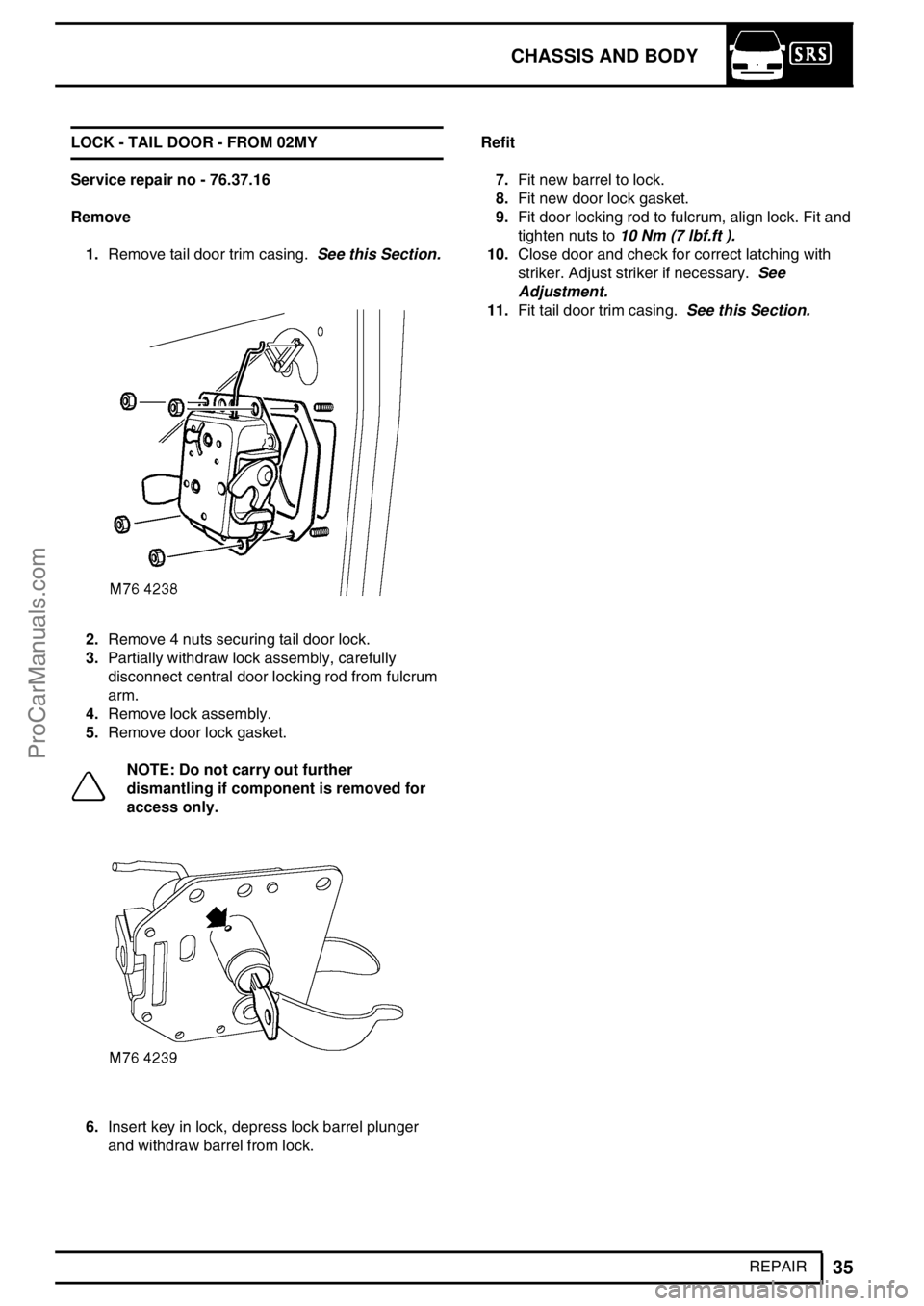
CHASSIS AND BODY
35
REPAIR LOCK - TAIL DOOR - FROM 02MY
Service repair no - 76.37.16
Remove
1.Remove tail door trim casing.See this Section.
2.Remove 4 nuts securing tail door lock.
3.Partially withdraw lock assembly, carefully
disconnect central door locking rod from fulcrum
arm.
4.Remove lock assembly.
5.Remove door lock gasket.
NOTE: Do not carry out further
dismantling if component is removed for
access only.
6.Insert key in lock, depress lock barrel plunger
and withdraw barrel from lock.Refit
7.Fit new barrel to lock.
8.Fit new door lock gasket.
9.Fit door locking rod to fulcrum, align lock. Fit and
tighten nuts to10 Nm (7 lbf.ft ).
10.Close door and check for correct latching with
striker. Adjust striker if necessary.See
Adjustment.
11.Fit tail door trim casing.See this Section.
ProCarManuals.com
Page 505 of 667
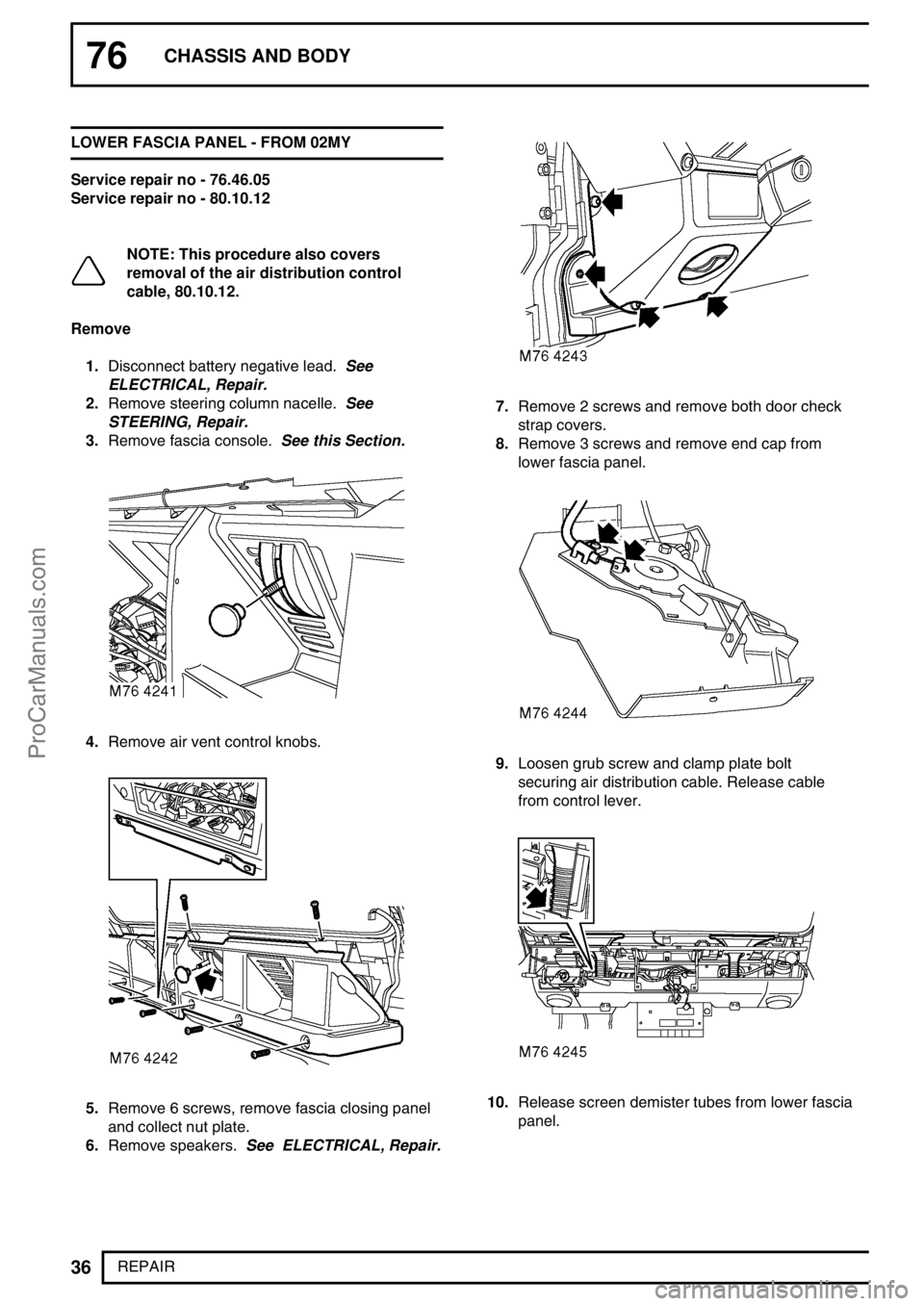
76CHASSIS AND BODY
36
REPAIR LOWER FASCIA PANEL - FROM 02MY
Service repair no - 76.46.05
Service repair no - 80.10.12
NOTE: This procedure also covers
removal of the air distribution control
cable, 80.10.12.
Remove
1.Disconnect battery negative lead.See
ELECTRICAL, Repair.
2.Remove steering column nacelle.See
STEERING, Repair.
3.Remove fascia console.See this Section.
4.Remove air vent control knobs.
5.Remove 6 screws, remove fascia closing panel
and collect nut plate.
6.Remove speakers.See ELECTRICAL, Repair.
7.Remove 2 screws and remove both door check
strap covers.
8.Remove 3 screws and remove end cap from
lower fascia panel.
9.Loosen grub screw and clamp plate bolt
securing air distribution cable. Release cable
from control lever.
10.Release screen demister tubes from lower fascia
panel.
ProCarManuals.com
Page 506 of 667
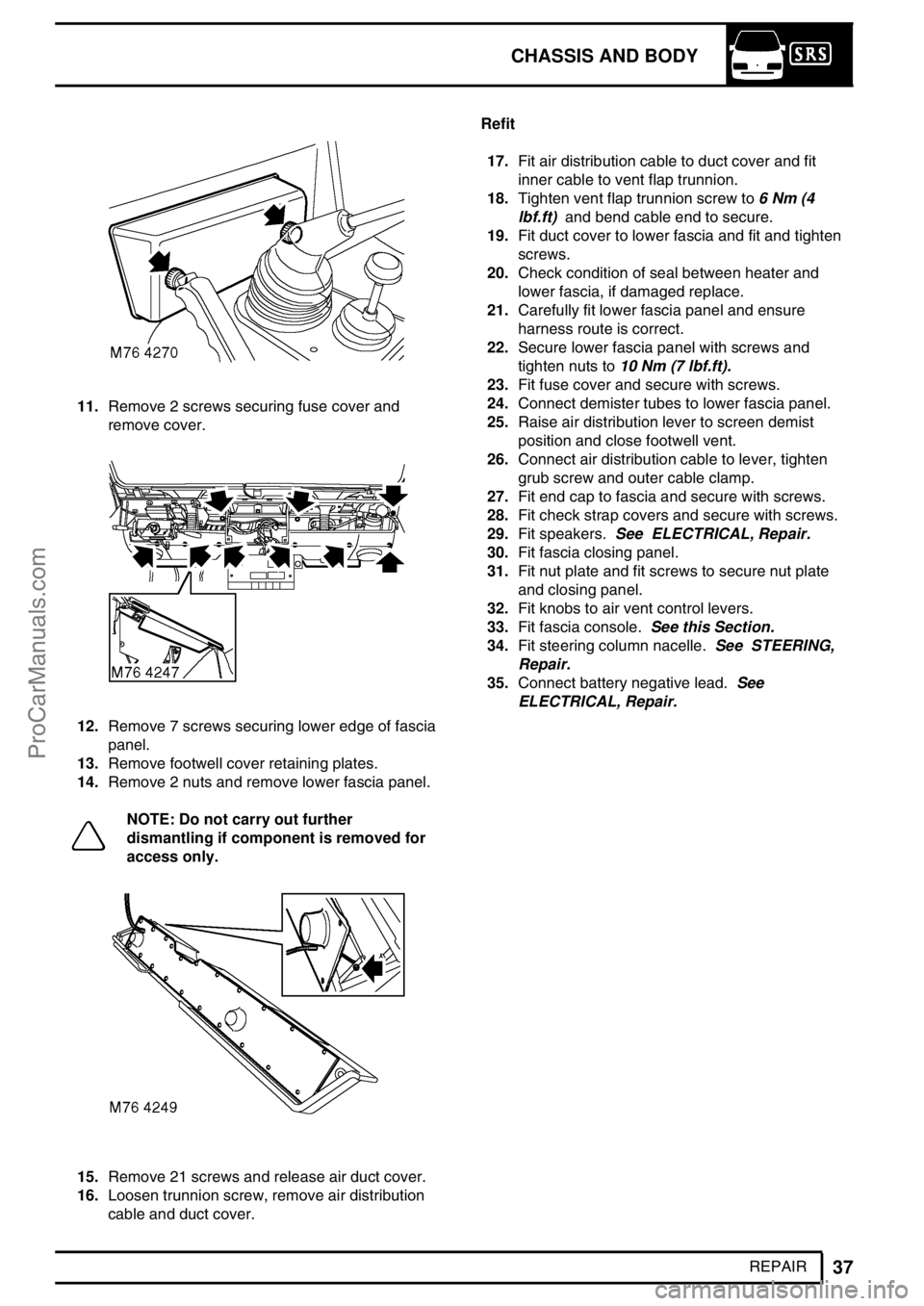
CHASSIS AND BODY
37
REPAIR
11.Remove 2 screws securing fuse cover and
remove cover.
12.Remove 7 screws securing lower edge of fascia
panel.
13.Remove footwell cover retaining plates.
14.Remove 2 nuts and remove lower fascia panel.
NOTE: Do not carry out further
dismantling if component is removed for
access only.
15.Remove 21 screws and release air duct cover.
16.Loosen trunnion screw, remove air distribution
cable and duct cover.Refit
17.Fit air distribution cable to duct cover and fit
inner cable to vent flap trunnion.
18.Tighten vent flap trunnion screw to6Nm(4
lbf.ft)and bend cable end to secure.
19.Fit duct cover to lower fascia and fit and tighten
screws.
20.Check condition of seal between heater and
lower fascia, if damaged replace.
21.Carefully fit lower fascia panel and ensure
harness route is correct.
22.Secure lower fascia panel with screws and
tighten nuts to10 Nm (7 lbf.ft).
23.Fit fuse cover and secure with screws.
24.Connect demister tubes to lower fascia panel.
25.Raise air distribution lever to screen demist
position and close footwell vent.
26.Connect air distribution cable to lever, tighten
grub screw and outer cable clamp.
27.Fit end cap to fascia and secure with screws.
28.Fit check strap covers and secure with screws.
29.Fit speakers.See ELECTRICAL, Repair.
30.Fit fascia closing panel.
31.Fit nut plate and fit screws to secure nut plate
and closing panel.
32.Fit knobs to air vent control levers.
33.Fit fascia console.See this Section.
34.Fit steering column nacelle.See STEERING,
Repair.
35.Connect battery negative lead.See
ELECTRICAL, Repair.
ProCarManuals.com
Page 507 of 667
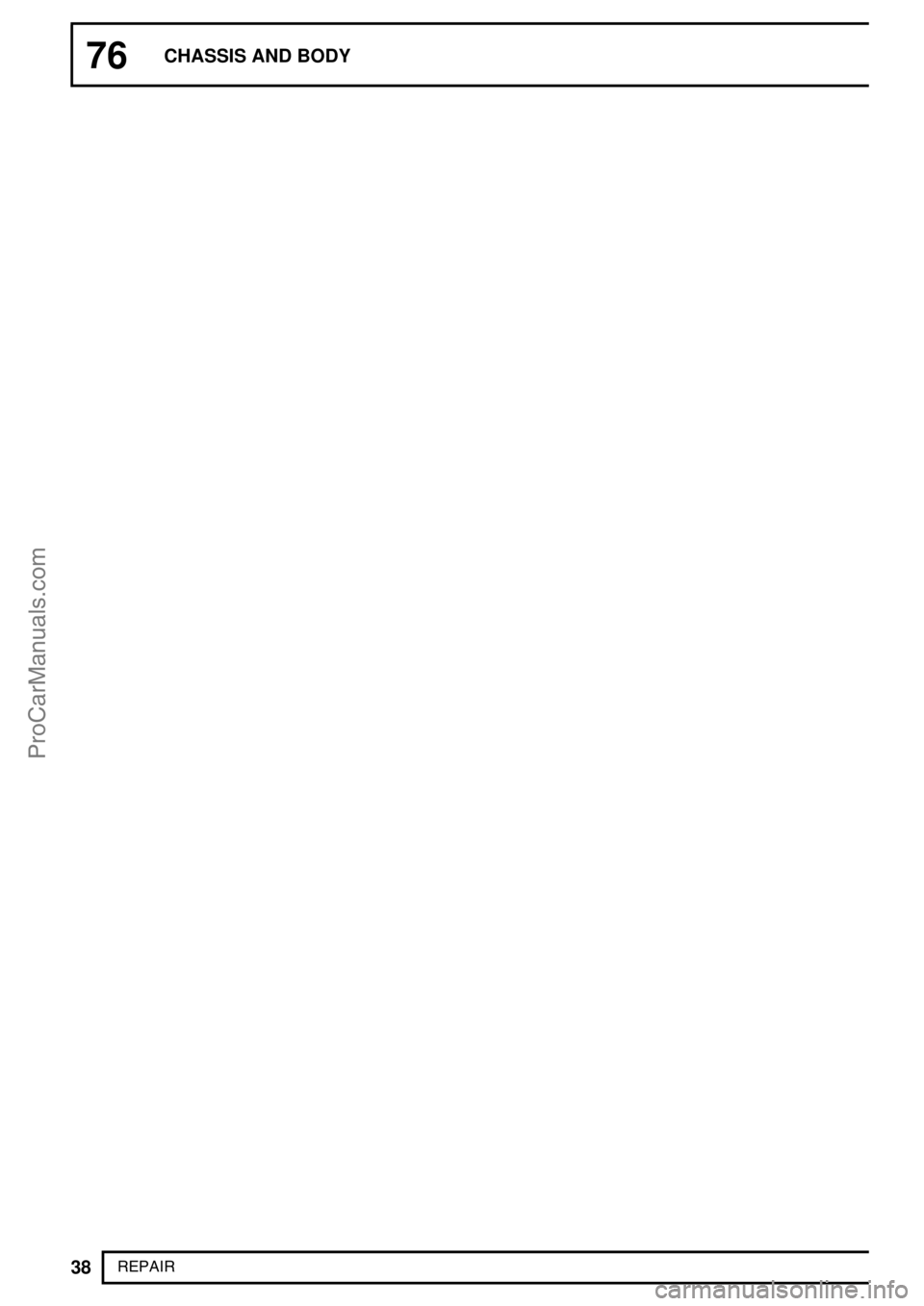
76CHASSIS AND BODY
38
REPAIR
ProCarManuals.com
Page 508 of 667
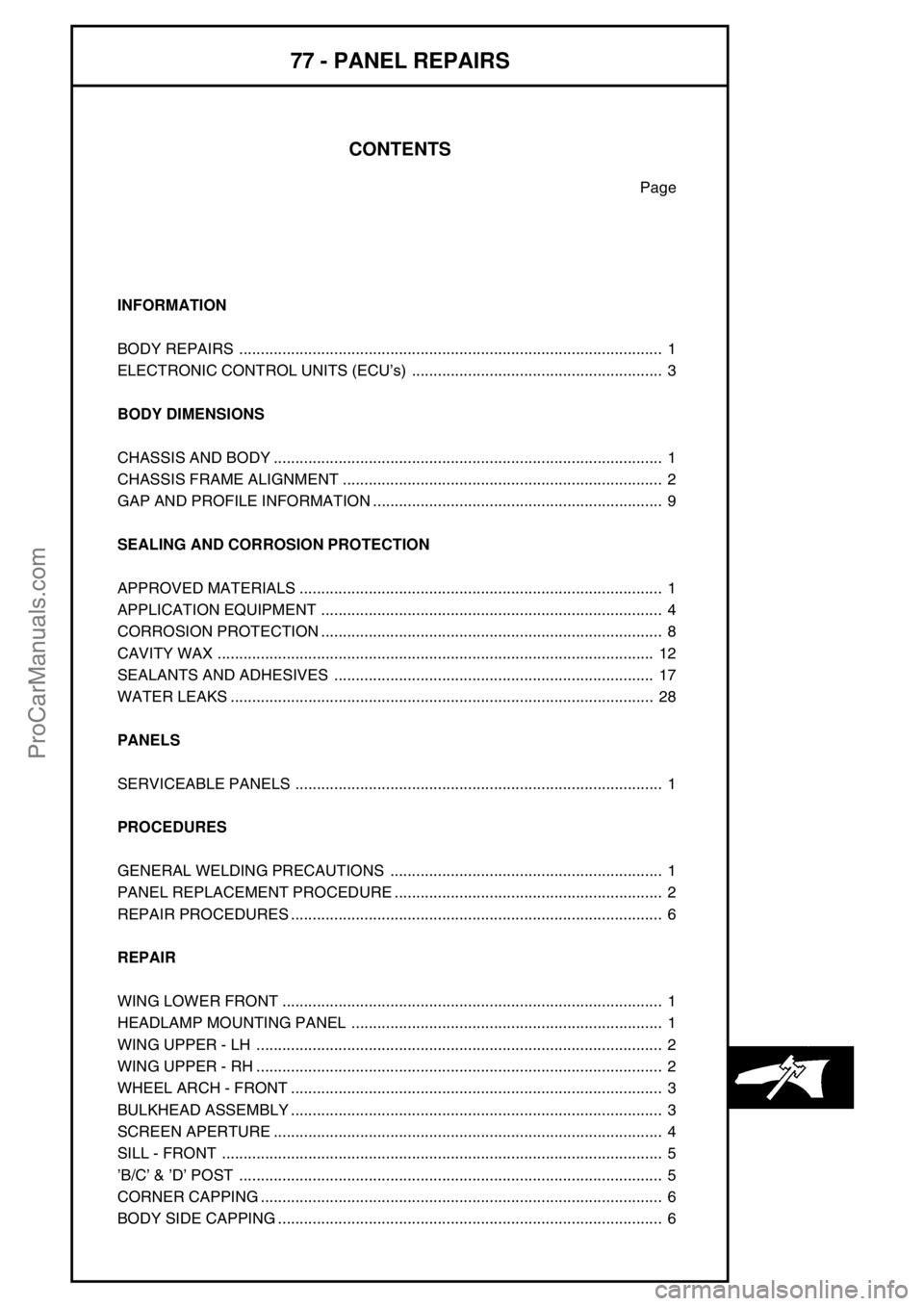
77 - PANEL REPAIRS
CONTENTS
Page
INFORMATION
BODY REPAIRS 1..................................................................................................
ELECTRONIC CONTROL UNITS (ECU’s) 3..........................................................
BODY DIMENSIONS
CHASSIS AND BODY 1..........................................................................................
CHASSIS FRAME ALIGNMENT 2..........................................................................
GAP AND PROFILE INFORMATION 9...................................................................
SEALING AND CORROSION PROTECTION
APPROVED MATERIALS 1....................................................................................
APPLICATION EQUIPMENT 4...............................................................................
CORROSION PROTECTION 8...............................................................................
CAVITY WAX 12.....................................................................................................
SEALANTS AND ADHESIVES 17..........................................................................
WATER LEAKS 28..................................................................................................
PANELS
SERVICEABLE PANELS 1.....................................................................................
PROCEDURES
GENERAL WELDING PRECAUTIONS 1...............................................................
PANEL REPLACEMENT PROCEDURE 2..............................................................
REPAIR PROCEDURES 6......................................................................................
REPAIR
WING LOWER FRONT 1........................................................................................
HEADLAMP MOUNTING PANEL 1........................................................................
WING UPPER - LH 2..............................................................................................
WING UPPER - RH 2..............................................................................................
WHEEL ARCH - FRONT 3......................................................................................
BULKHEAD ASSEMBLY 3......................................................................................
SCREEN APERTURE 4..........................................................................................
SILL - FRONT 5......................................................................................................
’B/C’&’D’POST 5..................................................................................................
CORNER CAPPING 6.............................................................................................
BODY SIDE CAPPING 6.........................................................................................
ProCarManuals.com
Page 509 of 667
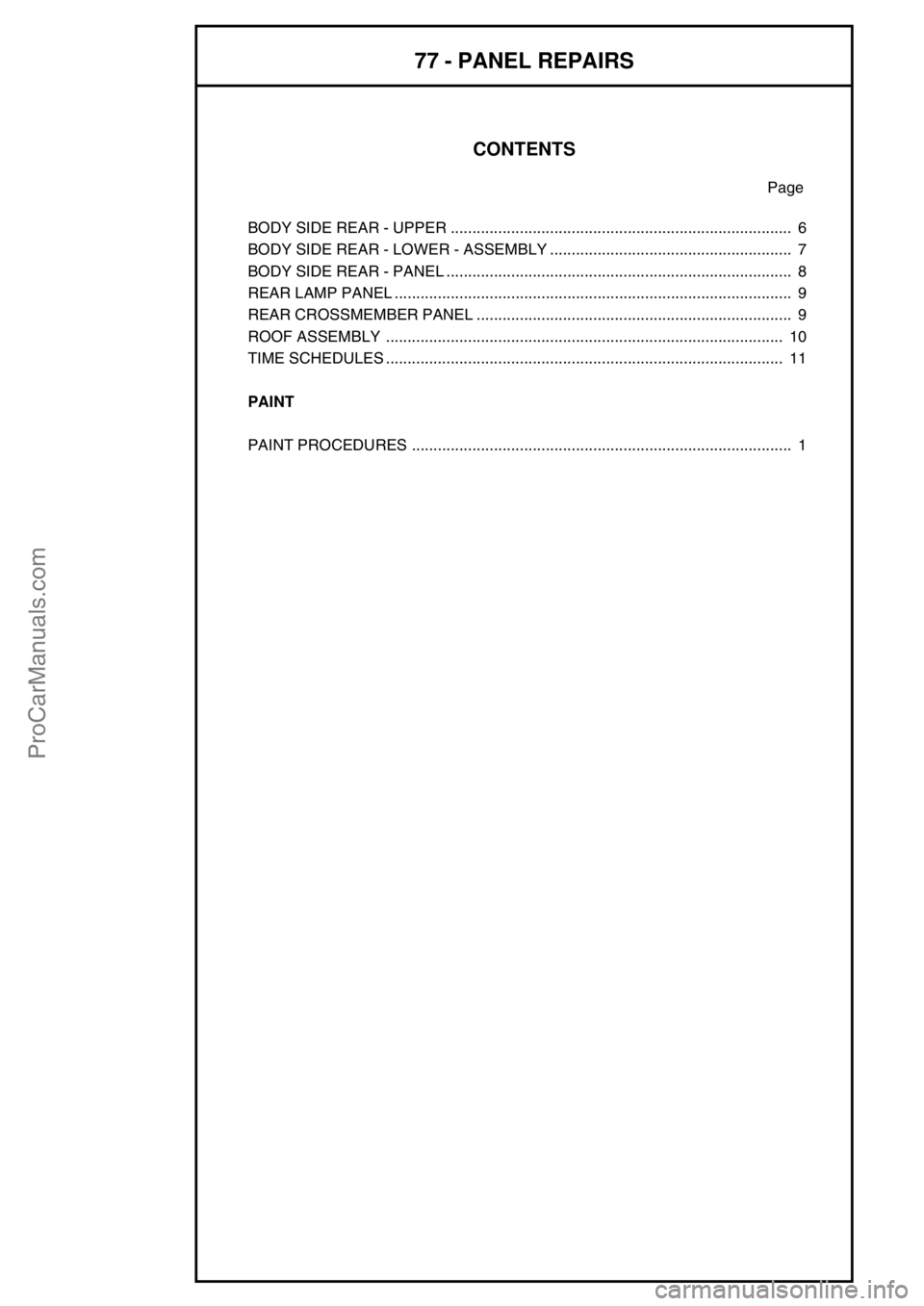
77 - PANEL REPAIRS
CONTENTS
Page
BODY SIDE REAR - UPPER 6...............................................................................
BODY SIDE REAR - LOWER - ASSEMBLY 7........................................................
BODY SIDE REAR - PANEL 8................................................................................
REAR LAMP PANEL 9............................................................................................
REAR CROSSMEMBER PANEL 9.........................................................................
ROOF ASSEMBLY 10............................................................................................
TIME SCHEDULES 11............................................................................................
PAINT
PAINT PROCEDURES 1........................................................................................
ProCarManuals.com
Page 510 of 667
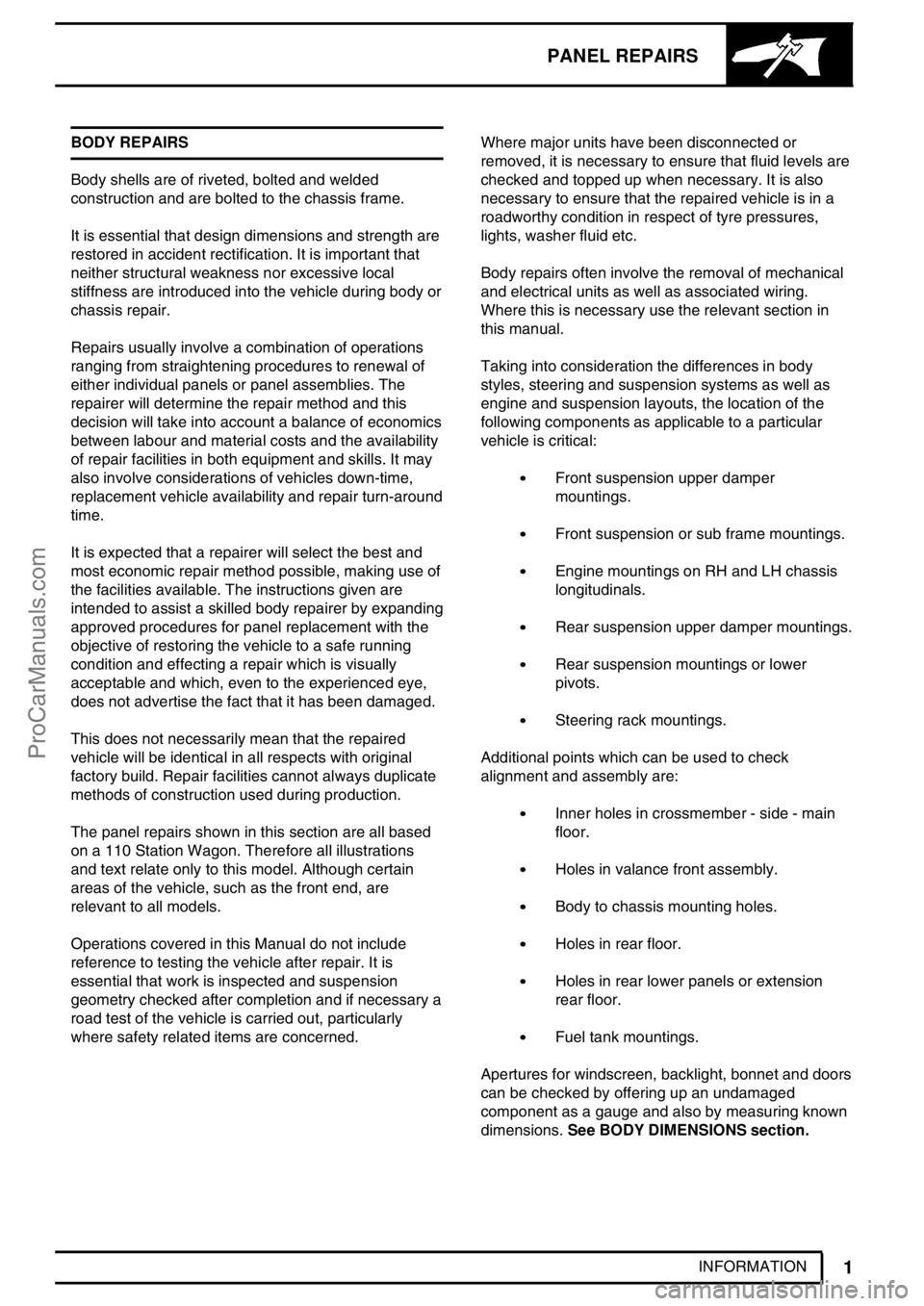
PANEL REPAIRS
1
INFORMATION BODY REPAIRS
Body shells are of riveted, bolted and welded
construction and are bolted to the chassis frame.
It is essential that design dimensions and strength are
restored in accident rectification. It is important that
neither structural weakness nor excessive local
stiffness are introduced into the vehicle during body or
chassis repair.
Repairs usually involve a combination of operations
ranging from straightening procedures to renewal of
either individual panels or panel assemblies. The
repairer will determine the repair method and this
decision will take into account a balance of economics
between labour and material costs and the availability
of repair facilities in both equipment and skills. It may
also involve considerations of vehicles down-time,
replacement vehicle availability and repair turn-around
time.
It is expected that a repairer will select the best and
most economic repair method possible, making use of
the facilities available. The instructions given are
intended to assist a skilled body repairer by expanding
approved procedures for panel replacement with the
objective of restoring the vehicle to a safe running
condition and effecting a repair which is visually
acceptable and which, even to the experienced eye,
does not advertise the fact that it has been damaged.
This does not necessarily mean that the repaired
vehicle will be identical in all respects with original
factory build. Repair facilities cannot always duplicate
methods of construction used during production.
The panel repairs shown in this section are all based
on a 110 Station Wagon. Therefore all illustrations
and text relate only to this model. Although certain
areas of the vehicle, such as the front end, are
relevant to all models.
Operations covered in this Manual do not include
reference to testing the vehicle after repair. It is
essential that work is inspected and suspension
geometry checked after completion and if necessary a
road test of the vehicle is carried out, particularly
where safety related items are concerned.Where major units have been disconnected or
removed, it is necessary to ensure that fluid levels are
checked and topped up when necessary. It is also
necessary to ensure that the repaired vehicle is in a
roadworthy condition in respect of tyre pressures,
lights, washer fluid etc.
Body repairs often involve the removal of mechanical
and electrical units as well as associated wiring.
Where this is necessary use the relevant section in
this manual.
Taking into consideration the differences in body
styles, steering and suspension systems as well as
engine and suspension layouts, the location of the
following components as applicable to a particular
vehicle is critical:
Front suspension upper damper
mountings.
Front suspension or sub frame mountings.
Engine mountings on RH and LH chassis
longitudinals.
Rear suspension upper damper mountings.
Rear suspension mountings or lower
pivots.
Steering rack mountings.
Additional points which can be used to check
alignment and assembly are:
Inner holes in crossmember - side - main
floor.
Holes in valance front assembly.
Body to chassis mounting holes.
Holes in rear floor.
Holes in rear lower panels or extension
rear floor.
Fuel tank mountings.
Apertures for windscreen, backlight, bonnet and doors
can be checked by offering up an undamaged
component as a gauge and also by measuring known
dimensions.See BODY DIMENSIONS section.
ProCarManuals.com