warning light LAND ROVER DEFENDER 1999 Workshop Manual
[x] Cancel search | Manufacturer: LAND ROVER, Model Year: 1999, Model line: DEFENDER, Model: LAND ROVER DEFENDER 1999Pages: 667, PDF Size: 8.76 MB
Page 15 of 667
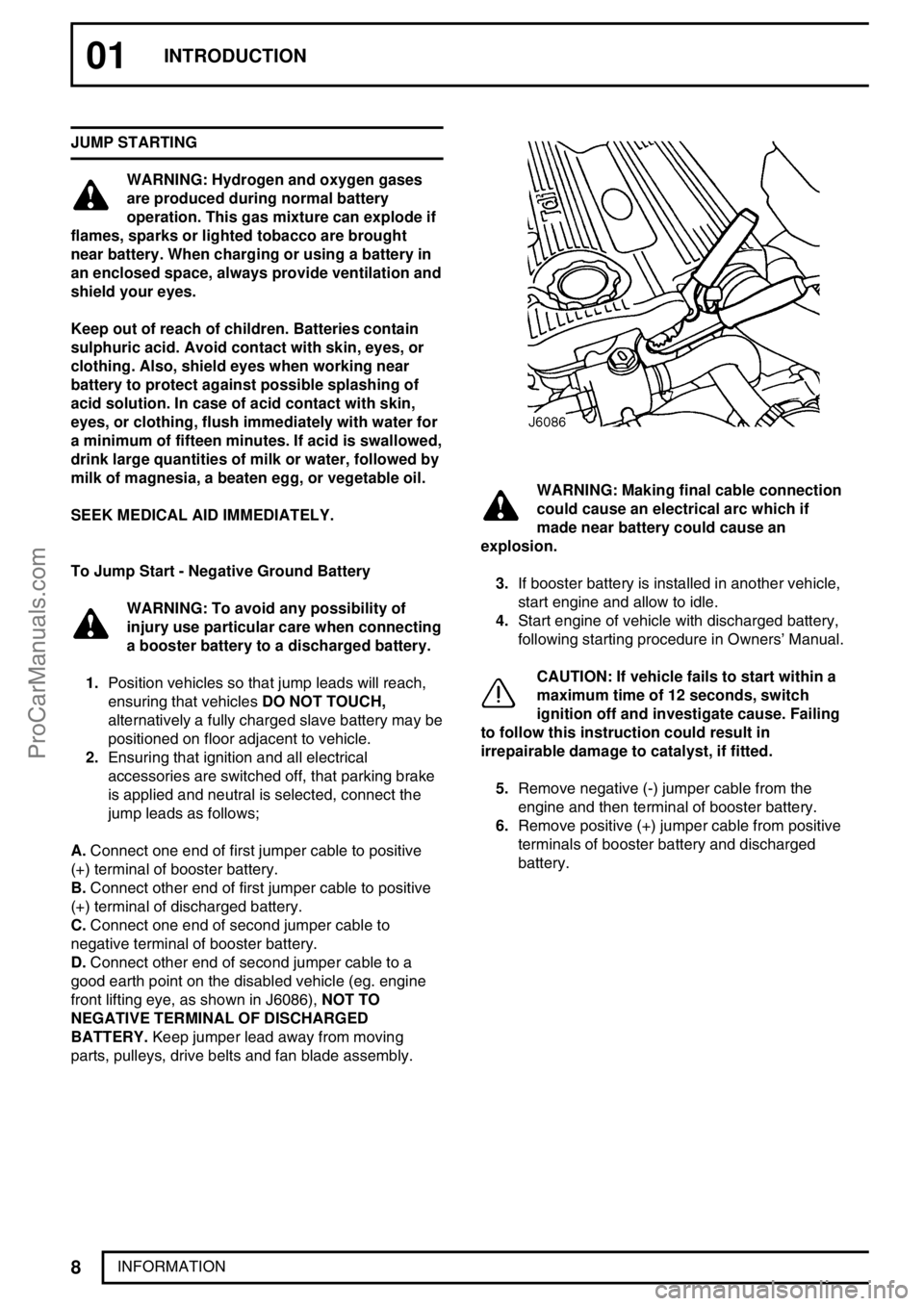
01INTRODUCTION
8
INFORMATION JUMP STARTING
WARNING: Hydrogen and oxygen gases
are produced during normal battery
operation. This gas mixture can explode if
flames, sparks or lighted tobacco are brought
near battery. When charging or using a battery in
an enclosed space, always provide ventilation and
shield your eyes.
Keep out of reach of children. Batteries contain
sulphuric acid. Avoid contact with skin, eyes, or
clothing. Also, shield eyes when working near
battery to protect against possible splashing of
acid solution. In case of acid contact with skin,
eyes, or clothing, flush immediately with water for
a minimum of fifteen minutes. If acid is swallowed,
drink large quantities of milk or water, followed by
milk of magnesia, a beaten egg, or vegetable oil.
SEEK MEDICAL AID IMMEDIATELY.
To Jump Start - Negative Ground Battery
WARNING: To avoid any possibility of
injury use particular care when connecting
a booster battery to a discharged battery.
1.Position vehicles so that jump leads will reach,
ensuring that vehiclesDO NOT TOUCH,
alternatively a fully charged slave battery may be
positioned on floor adjacent to vehicle.
2.Ensuring that ignition and all electrical
accessories are switched off, that parking brake
is applied and neutral is selected, connect the
jump leads as follows;
A.Connect one end of first jumper cable to positive
(+) terminal of booster battery.
B.Connect other end of first jumper cable to positive
(+) terminal of discharged battery.
C.Connect one end of second jumper cable to
negative terminal of booster battery.
D.Connect other end of second jumper cable to a
good earth point on the disabled vehicle (eg. engine
front lifting eye, as shown in J6086),NOT TO
NEGATIVE TERMINAL OF DISCHARGED
BATTERY.Keep jumper lead away from moving
parts, pulleys, drive belts and fan blade assembly.
WARNING: Making final cable connection
could cause an electrical arc which if
made near battery could cause an
explosion.
3.If booster battery is installed in another vehicle,
start engine and allow to idle.
4.Start engine of vehicle with discharged battery,
following starting procedure in Owners’Manual.
CAUTION: If vehicle fails to start within a
maximum time of 12 seconds, switch
ignition off and investigate cause. Failing
to follow this instruction could result in
irrepairable damage to catalyst, if fitted.
5.Remove negative (-) jumper cable from the
engine and then terminal of booster battery.
6.Remove positive (+) jumper cable from positive
terminals of booster battery and discharged
battery.
ProCarManuals.com
Page 32 of 667
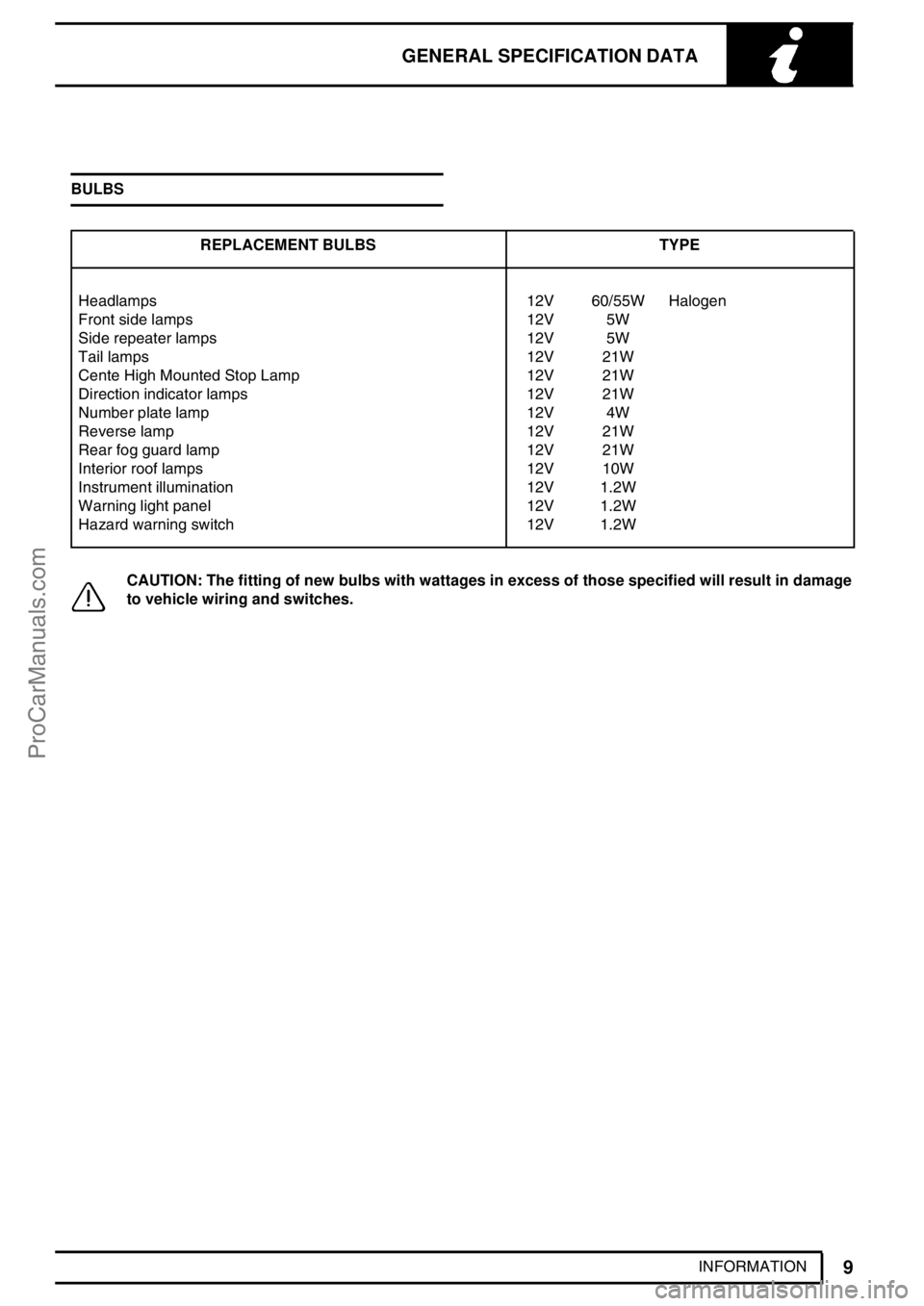
GENERAL SPECIFICATION DATA
9
INFORMATION BULBS
REPLACEMENT BULBS TYPE
Headlamps 12V 60/55W Halogen
Front side lamps 12V 5W
Side repeater lamps 12V 5W
Tail lamps 12V 21W
Cente High Mounted Stop Lamp 12V 21W
Direction indicator lamps 12V 21W
Number plate lamp 12V 4W
Reverse lamp 12V 21W
Rear fog guard lamp 12V 21W
Interior roof lamps 12V 10W
Instrument illumination 12V 1.2W
Warning light panel 12V 1.2W
Hazard warning switch 12V 1.2W
CAUTION: The fitting of new bulbs with wattages in excess of those specified will result in damage
to vehicle wiring and switches.
ProCarManuals.com
Page 61 of 667
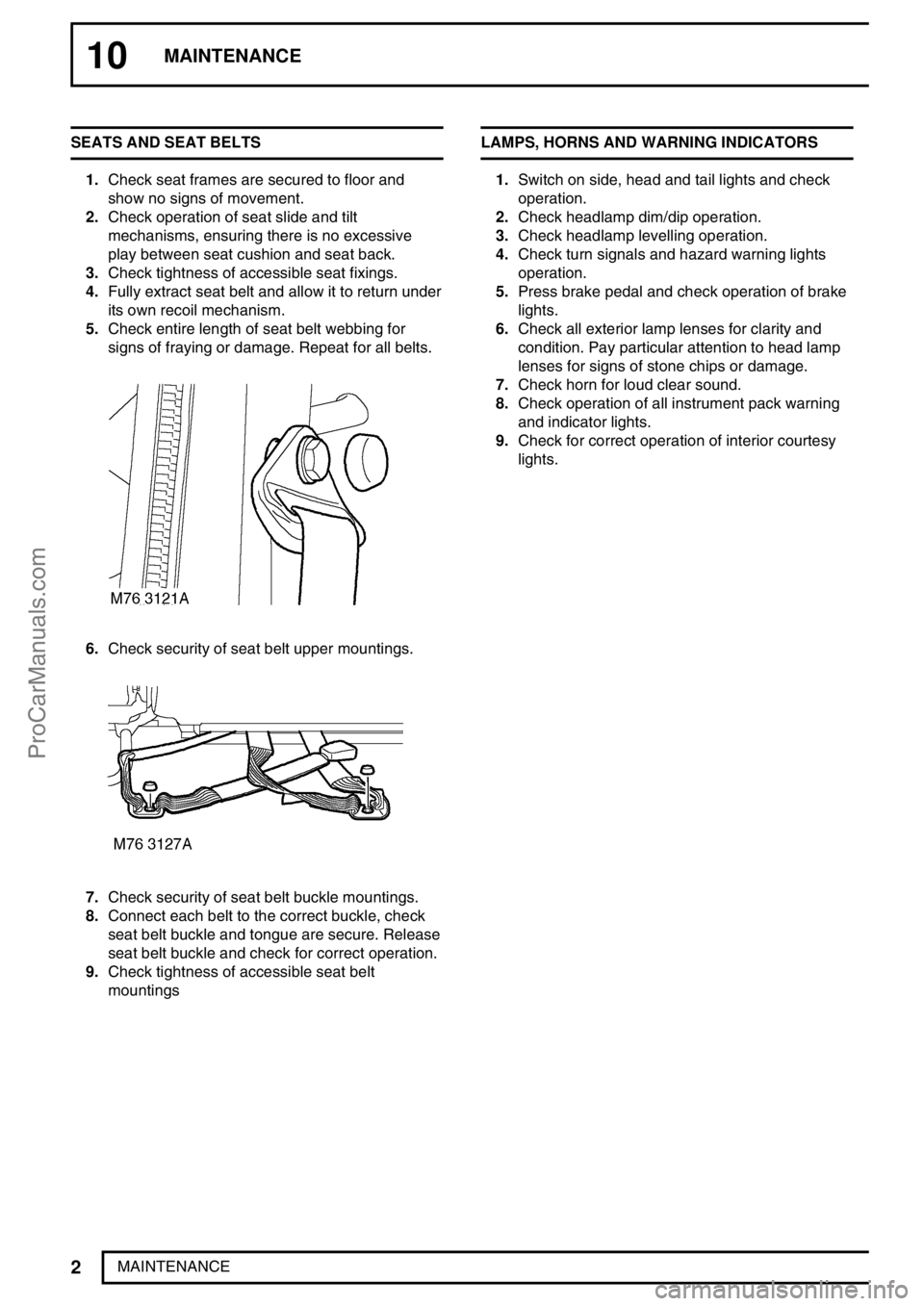
10MAINTENANCE
2
MAINTENANCE SEATS AND SEAT BELTS
1.Check seat frames are secured to floor and
show no signs of movement.
2.Check operation of seat slide and tilt
mechanisms, ensuring there is no excessive
play between seat cushion and seat back.
3.Check tightness of accessible seat fixings.
4.Fully extract seat belt and allow it to return under
its own recoil mechanism.
5.Check entire length of seat belt webbing for
signs of fraying or damage. Repeat for all belts.
6.Check security of seat belt upper mountings.
7.Check security of seat belt buckle mountings.
8.Connect each belt to the correct buckle, check
seat belt buckle and tongue are secure. Release
seat belt buckle and check for correct operation.
9.Check tightness of accessible seat belt
mountingsLAMPS, HORNS AND WARNING INDICATORS
1.Switch on side, head and tail lights and check
operation.
2.Check headlamp dim/dip operation.
3.Check headlamp levelling operation.
4.Check turn signals and hazard warning lights
operation.
5.Press brake pedal and check operation of brake
lights.
6.Check all exterior lamp lenses for clarity and
condition. Pay particular attention to head lamp
lenses for signs of stone chips or damage.
7.Check horn for loud clear sound.
8.Check operation of all instrument pack warning
and indicator lights.
9.Check for correct operation of interior courtesy
lights.
ProCarManuals.com
Page 106 of 667

ENGINE
21
DESCRIPTION AND OPERATION Oil pressure switch
The oil pressure switch is located in a port on the outlet side of the oil cooler housing. It detects when a safe
operating pressure has been reached during engine starting and initiates the illumination of a warning light in the
instrument pack if the pressure drops below a given value.
ProCarManuals.com
Page 181 of 667
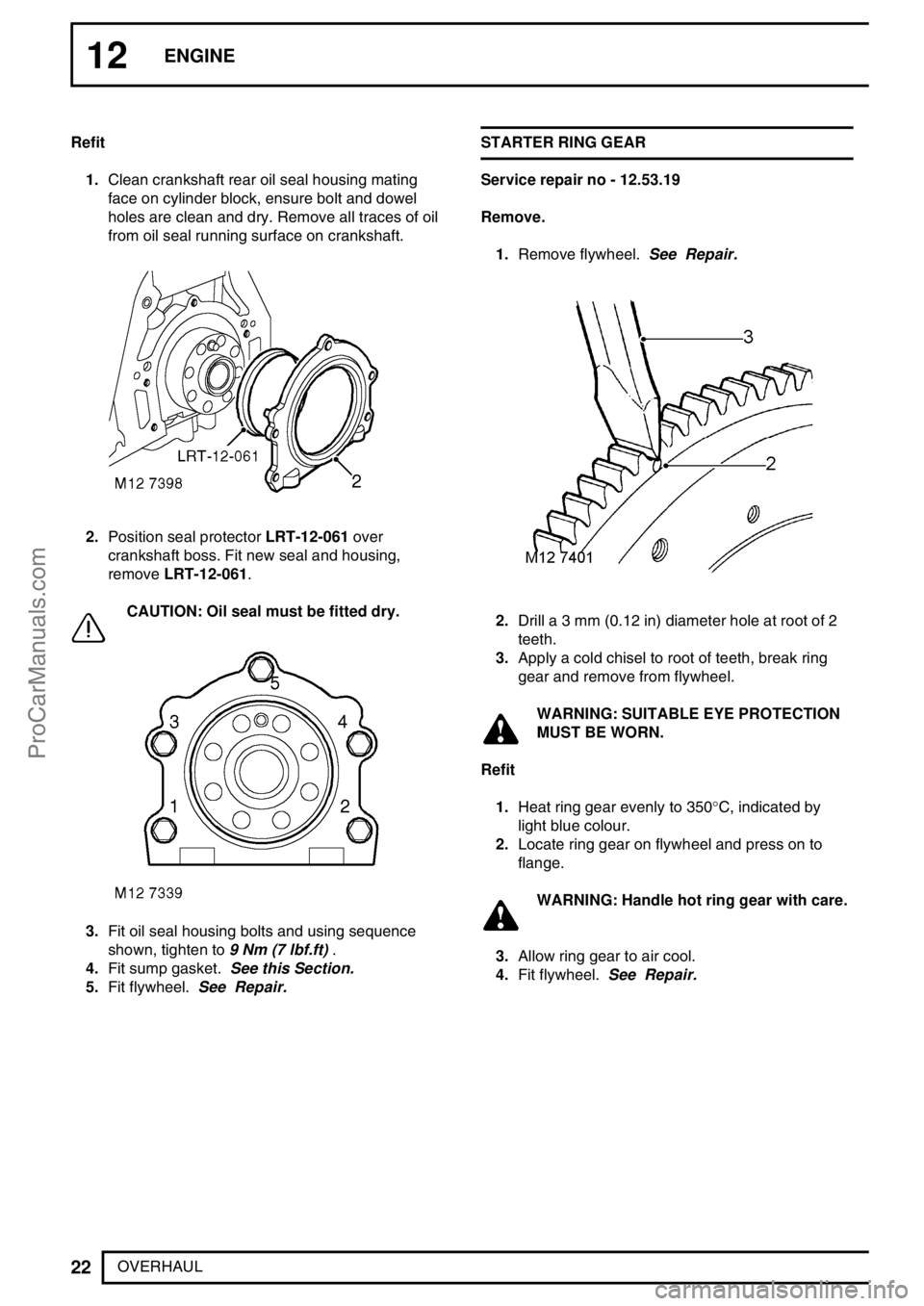
12ENGINE
22
OVERHAUL Refit
1.Clean crankshaft rear oil seal housing mating
face on cylinder block, ensure bolt and dowel
holes are clean and dry. Remove all traces of oil
from oil seal running surface on crankshaft.
2.Position seal protectorLRT-12-061over
crankshaft boss. Fit new seal and housing,
removeLRT-12-061.
CAUTION: Oil seal must be fitted dry.
3.Fit oil seal housing bolts and using sequence
shown, tighten to9 Nm (7 lbf.ft).
4.Fit sump gasket.See this Section.
5.Fit flywheel.See Repair.STARTER RING GEAR
Service repair no - 12.53.19
Remove.
1.Remove flywheel.See Repair.
2.Drill a 3 mm (0.12 in) diameter hole at root of 2
teeth.
3.Apply a cold chisel to root of teeth, break ring
gear and remove from flywheel.
WARNING: SUITABLE EYE PROTECTION
MUST BE WORN.
Refit
1.Heat ring gear evenly to 350°C, indicated by
light blue colour.
2.Locate ring gear on flywheel and press on to
flange.
WARNING: Handle hot ring gear with care.
3.Allow ring gear to air cool.
4.Fit flywheel.See Repair.
ProCarManuals.com
Page 246 of 667
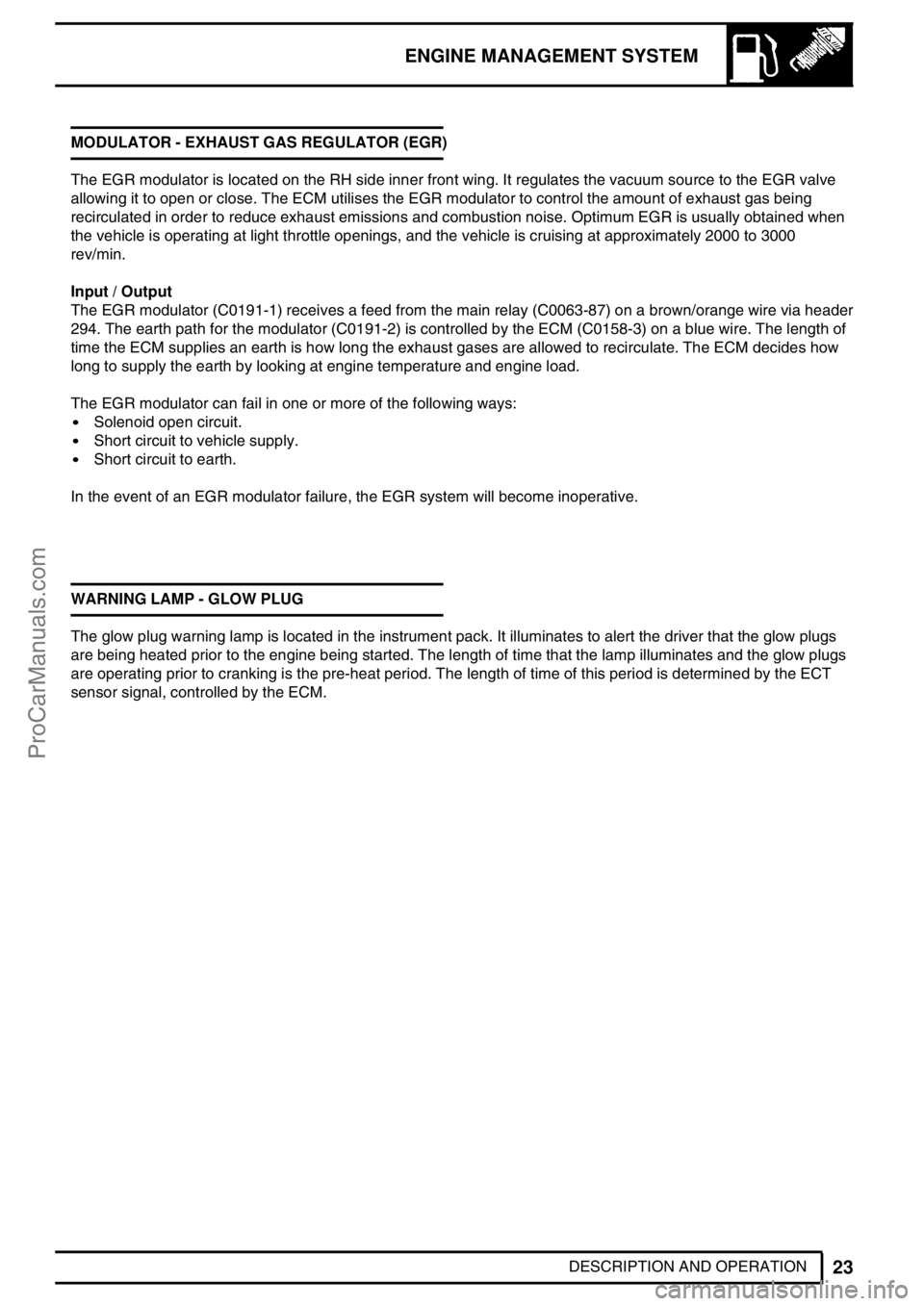
ENGINE MANAGEMENT SYSTEM
23
DESCRIPTION AND OPERATION MODULATOR - EXHAUST GAS REGULATOR (EGR)
The EGR modulator is located on the RH side inner front wing. It regulates the vacuum source to the EGR valve
allowing it to open or close. The ECM utilises the EGR modulator to control the amount of exhaust gas being
recirculated in order to reduce exhaust emissions and combustion noise. Optimum EGR is usually obtained when
the vehicle is operating at light throttle openings, and the vehicle is cruising at approximately 2000 to 3000
rev/min.
Input / Output
The EGR modulator (C0191-1) receives a feed from the main relay (C0063-87) on a brown/orange wire via header
294. The earth path for the modulator (C0191-2) is controlled by the ECM (C0158-3) on a blue wire. The length of
time the ECM supplies an earth is how long the exhaust gases are allowed to recirculate. The ECM decides how
long to supply the earth by looking at engine temperature and engine load.
The EGR modulator can fail in one or more of the following ways:
Solenoid open circuit.
Short circuit to vehicle supply.
Short circuit to earth.
In the event of an EGR modulator failure, the EGR system will become inoperative.
WARNING LAMP - GLOW PLUG
The glow plug warning lamp is located in the instrument pack. It illuminates to alert the driver that the glow plugs
are being heated prior to the engine being started. The length of time that the lamp illuminates and the glow plugs
are operating prior to cranking is the pre-heat period. The length of time of this period is determined by the ECT
sensor signal, controlled by the ECM.
ProCarManuals.com
Page 366 of 667
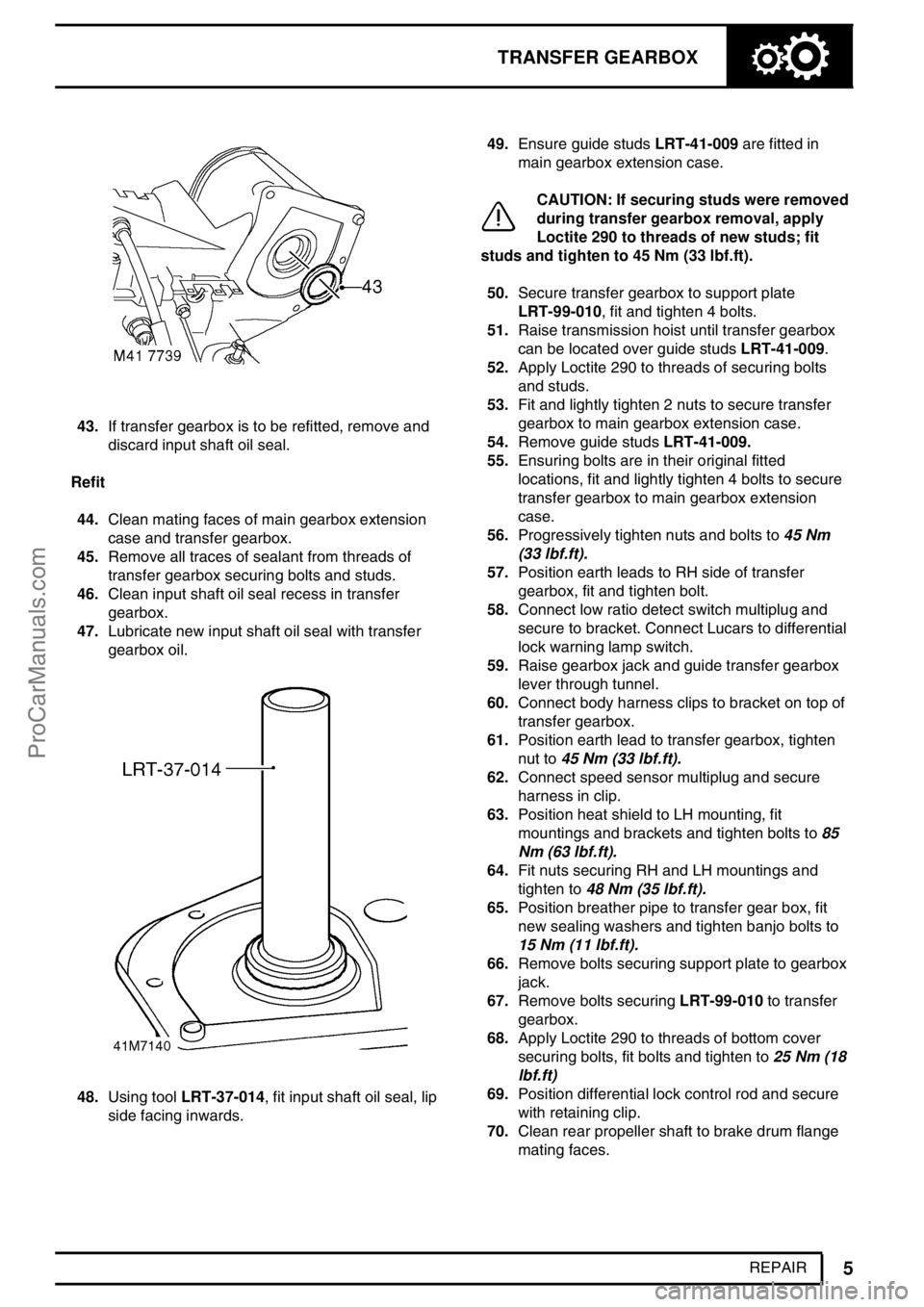
TRANSFER GEARBOX
5
REPAIR
43.If transfer gearbox is to be refitted, remove and
discard input shaft oil seal.
Refit
44.Clean mating faces of main gearbox extension
case and transfer gearbox.
45.Remove all traces of sealant from threads of
transfer gearbox securing bolts and studs.
46.Clean input shaft oil seal recess in transfer
gearbox.
47.Lubricate new input shaft oil seal with transfer
gearbox oil.
48.Using toolLRT-37-014, fit input shaft oil seal, lip
side facing inwards.49.Ensure guide studsLRT-41-009are fitted in
main gearbox extension case.
CAUTION: If securing studs were removed
during transfer gearbox removal, apply
Loctite 290 to threads of new studs; fit
studs and tighten to 45 Nm (33 lbf.ft).
50.Secure transfer gearbox to support plate
LRT-99-010, fit and tighten 4 bolts.
51.Raise transmission hoist until transfer gearbox
can be located over guide studsLRT-41-009.
52.Apply Loctite 290 to threads of securing bolts
and studs.
53.Fit and lightly tighten 2 nuts to secure transfer
gearbox to main gearbox extension case.
54.Remove guide studsLRT-41-009.
55.Ensuring bolts are in their original fitted
locations, fit and lightly tighten 4 bolts to secure
transfer gearbox to main gearbox extension
case.
56.Progressively tighten nuts and bolts to45 Nm
(33 lbf.ft).
57.Position earth leads to RH side of transfer
gearbox, fit and tighten bolt.
58.Connect low ratio detect switch multiplug and
secure to bracket. Connect Lucars to differential
lock warning lamp switch.
59.Raise gearbox jack and guide transfer gearbox
lever through tunnel.
60.Connect body harness clips to bracket on top of
transfer gearbox.
61.Position earth lead to transfer gearbox, tighten
nut to45 Nm (33 lbf.ft).
62.Connect speed sensor multiplug and secure
harness in clip.
63.Position heat shield to LH mounting, fit
mountings and brackets and tighten bolts to85
Nm (63 lbf.ft).
64.Fit nuts securing RH and LH mountings and
tighten to48 Nm (35 lbf.ft).
65.Position breather pipe to transfer gear box, fit
new sealing washers and tighten banjo bolts to
15 Nm (11 lbf.ft).
66.Remove bolts securing support plate to gearbox
jack.
67.Remove bolts securingLRT-99-010to transfer
gearbox.
68.Apply Loctite 290 to threads of bottom cover
securing bolts, fit bolts and tighten to25 Nm (18
lbf.ft)
69.Position differential lock control rod and secure
with retaining clip.
70.Clean rear propeller shaft to brake drum flange
mating faces.
ProCarManuals.com
Page 457 of 667
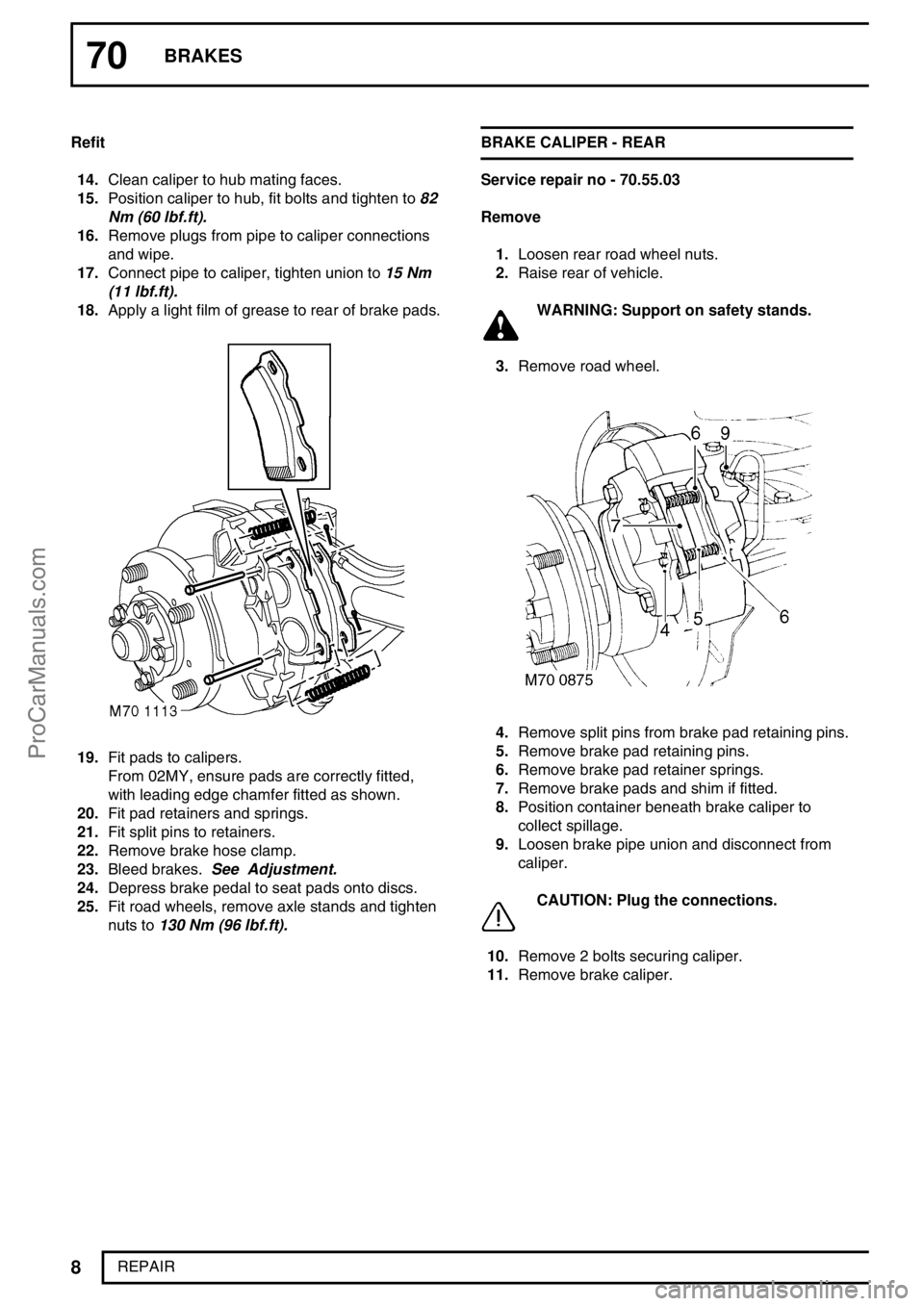
70BRAKES
8
REPAIR Refit
14.Clean caliper to hub mating faces.
15.Position caliper to hub, fit bolts and tighten to82
Nm (60 lbf.ft).
16.Remove plugs from pipe to caliper connections
and wipe.
17.Connect pipe to caliper, tighten union to15 Nm
(11 lbf.ft).
18.Apply a light film of grease to rear of brake pads.
19.Fit pads to calipers.
From 02MY, ensure pads are correctly fitted,
with leading edge chamfer fitted as shown.
20.Fit pad retainers and springs.
21.Fit split pins to retainers.
22.Remove brake hose clamp.
23.Bleed brakes.See Adjustment.
24.Depress brake pedal to seat pads onto discs.
25.Fit road wheels, remove axle stands and tighten
nuts to130 Nm (96 lbf.ft).BRAKE CALIPER - REAR
Service repair no - 70.55.03
Remove
1.Loosen rear road wheel nuts.
2.Raise rear of vehicle.
WARNING: Support on safety stands.
3.Remove road wheel.
4.Remove split pins from brake pad retaining pins.
5.Remove brake pad retaining pins.
6.Remove brake pad retainer springs.
7.Remove brake pads and shim if fitted.
8.Position container beneath brake caliper to
collect spillage.
9.Loosen brake pipe union and disconnect from
caliper.
CAUTION: Plug the connections.
10.Remove 2 bolts securing caliper.
11.Remove brake caliper.
ProCarManuals.com
Page 561 of 667
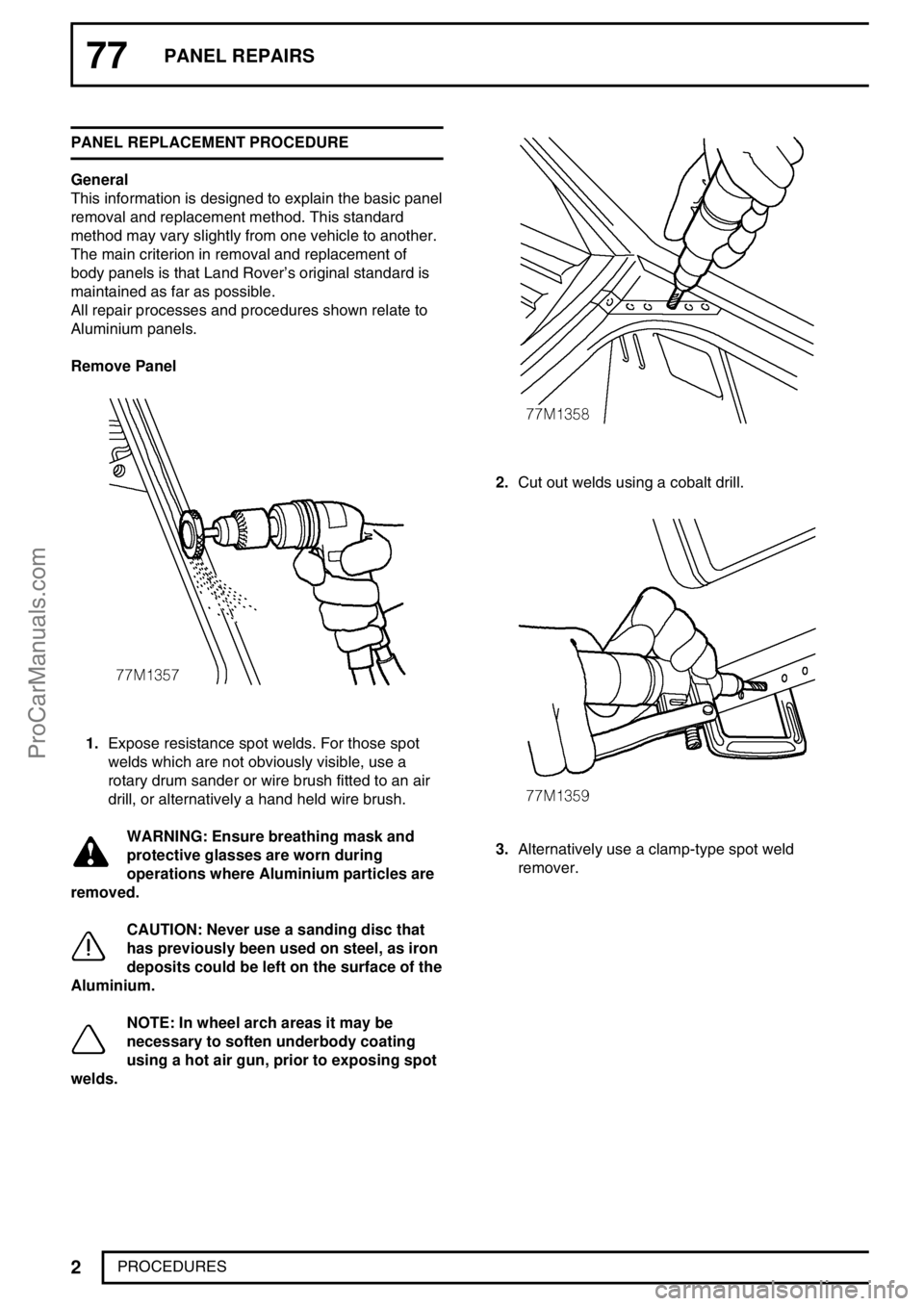
77PANEL REPAIRS
2
PROCEDURES PANEL REPLACEMENT PROCEDURE
General
This information is designed to explain the basic panel
removal and replacement method. This standard
method may vary slightly from one vehicle to another.
The main criterion in removal and replacement of
body panels is that Land Rover’s original standard is
maintained as far as possible.
All repair processes and procedures shown relate to
Aluminium panels.
Remove Panel
1.Expose resistance spot welds. For those spot
welds which are not obviously visible, use a
rotary drum sander or wire brush fitted to an air
drill, or alternatively a hand held wire brush.
WARNING: Ensure breathing mask and
protective glasses are worn during
operations where Aluminium particles are
removed.
CAUTION: Never use a sanding disc that
has previously been used on steel, as iron
deposits could be left on the surface of the
Aluminium.
NOTE: In wheel arch areas it may be
necessary to soften underbody coating
using a hot air gun, prior to exposing spot
welds.
2.Cut out welds using a cobalt drill.
3.Alternatively use a clamp-type spot weld
remover.
ProCarManuals.com
Page 609 of 667
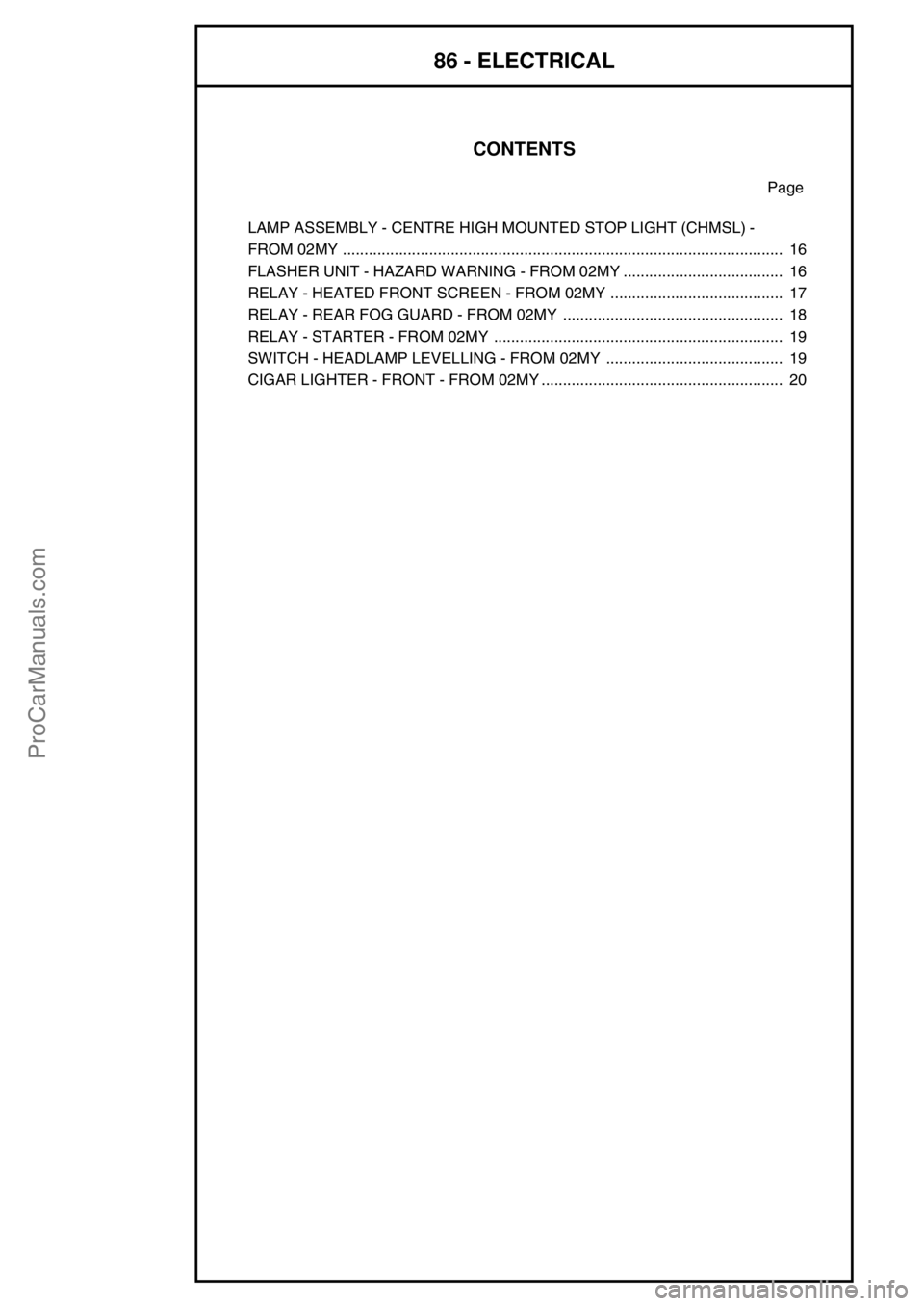
86 - ELECTRICAL
CONTENTS
Page
LAMP ASSEMBLY - CENTRE HIGH MOUNTED STOP LIGHT (CHMSL) -
FROM 02MY 16......................................................................................................
FLASHER UNIT - HAZARD WARNING - FROM 02MY 16.....................................
RELAY - HEATED FRONT SCREEN - FROM 02MY 17........................................
RELAY - REAR FOG GUARD - FROM 02MY 18...................................................
RELAY - STARTER - FROM 02MY 19...................................................................
SWITCH - HEADLAMP LEVELLING - FROM 02MY 19.........................................
CIGAR LIGHTER - FRONT - FROM 02MY 20........................................................
ProCarManuals.com