key LAND ROVER DEFENDER 1999 Workshop Manual
[x] Cancel search | Manufacturer: LAND ROVER, Model Year: 1999, Model line: DEFENDER, Model: LAND ROVER DEFENDER 1999Pages: 667, PDF Size: 8.76 MB
Page 14 of 667
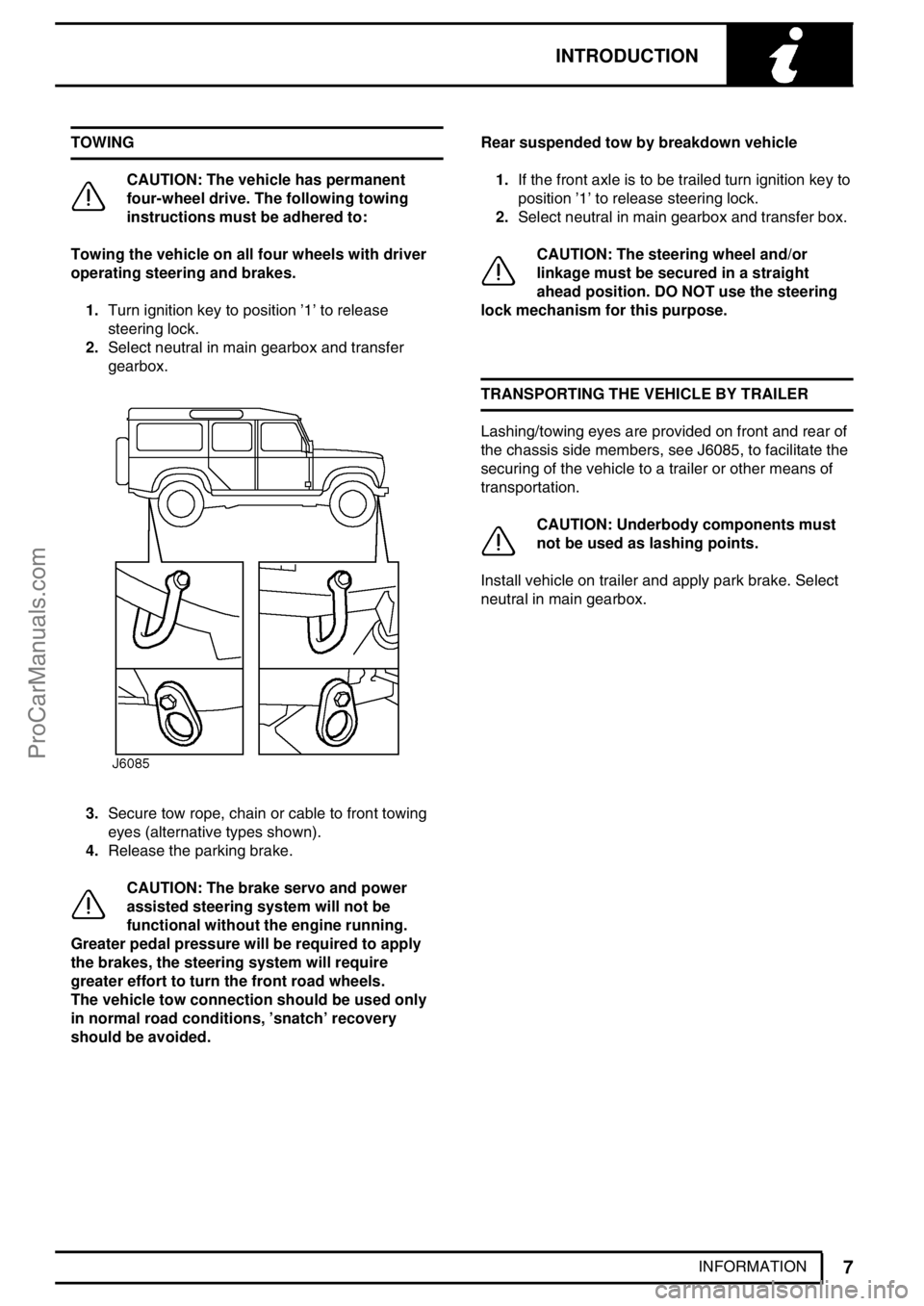
INTRODUCTION
7
INFORMATION TOWING
CAUTION: The vehicle has permanent
four-wheel drive. The following towing
instructions must be adhered to:
Towing the vehicle on all four wheels with driver
operating steering and brakes.
1.Turn ignition key to position’1’to release
steering lock.
2.Select neutral in main gearbox and transfer
gearbox.
3.Secure tow rope, chain or cable to front towing
eyes (alternative types shown).
4.Release the parking brake.
CAUTION: The brake servo and power
assisted steering system will not be
functional without the engine running.
Greater pedal pressure will be required to apply
the brakes, the steering system will require
greater effort to turn the front road wheels.
The vehicle tow connection should be used only
in normal road conditions,’snatch’recovery
should be avoided.Rear suspended tow by breakdown vehicle
1.If the front axle is to be trailed turn ignition key to
position’1’to release steering lock.
2.Select neutral in main gearbox and transfer box.
CAUTION: The steering wheel and/or
linkage must be secured in a straight
ahead position. DO NOT use the steering
lock mechanism for this purpose.
TRANSPORTING THE VEHICLE BY TRAILER
Lashing/towing eyes are provided on front and rear of
the chassis side members, see J6085, to facilitate the
securing of the vehicle to a trailer or other means of
transportation.
CAUTION: Underbody components must
not be used as lashing points.
Install vehicle on trailer and apply park brake. Select
neutral in main gearbox.
ProCarManuals.com
Page 42 of 667
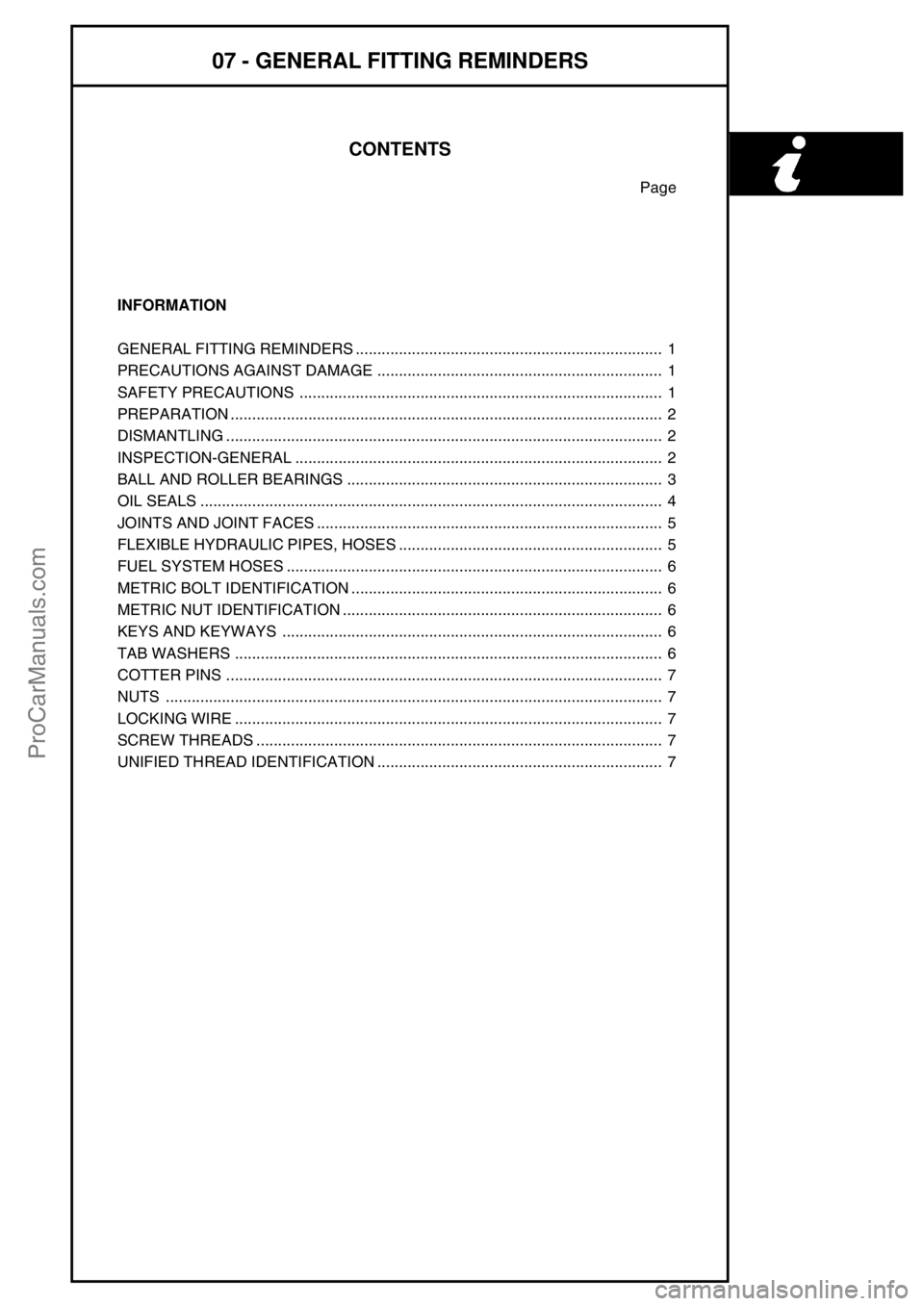
07 - GENERAL FITTING REMINDERS
CONTENTS
Page
INFORMATION
GENERAL FITTING REMINDERS 1.......................................................................
PRECAUTIONS AGAINST DAMAGE 1..................................................................
SAFETY PRECAUTIONS 1....................................................................................
PREPARATION 2....................................................................................................
DISMANTLING 2.....................................................................................................
INSPECTION-GENERAL 2.....................................................................................
BALL AND ROLLER BEARINGS 3.........................................................................
OIL SEALS 4...........................................................................................................
JOINTS AND JOINT FACES 5................................................................................
FLEXIBLE HYDRAULIC PIPES, HOSES 5.............................................................
FUEL SYSTEM HOSES 6.......................................................................................
METRIC BOLT IDENTIFICATION 6........................................................................
METRIC NUT IDENTIFICATION 6..........................................................................
KEYS AND KEYWAYS 6........................................................................................
TAB WASHERS 6...................................................................................................
COTTER PINS 7.....................................................................................................
NUTS7 ...................................................................................................................
LOCKING WIRE 7...................................................................................................
SCREW THREADS 7..............................................................................................
UNIFIED THREAD IDENTIFICATION 7..................................................................
ProCarManuals.com
Page 49 of 667
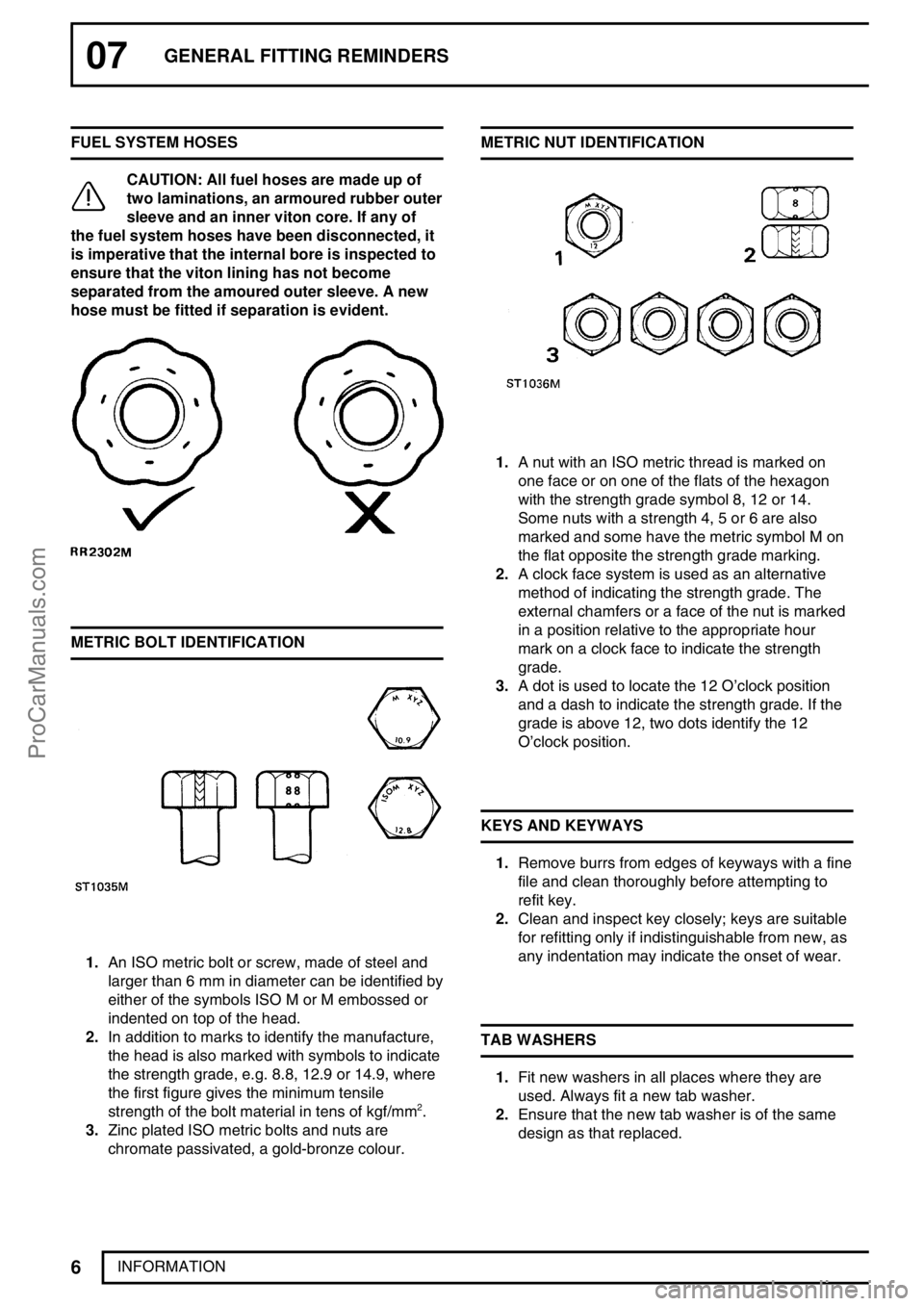
07GENERAL FITTING REMINDERS
6
INFORMATION FUEL SYSTEM HOSES
CAUTION: All fuel hoses are made up of
two laminations, an armoured rubber outer
sleeve and an inner viton core. If any of
the fuel system hoses have been disconnected, it
is imperative that the internal bore is inspected to
ensure that the viton lining has not become
separated from the amoured outer sleeve. A new
hose must be fitted if separation is evident.
METRIC BOLT IDENTIFICATION
1.An ISO metric bolt or screw, made of steel and
larger than 6 mm in diameter can be identified by
either of the symbols ISO M or M embossed or
indented on top of the head.
2.In addition to marks to identify the manufacture,
the head is also marked with symbols to indicate
the strength grade, e.g. 8.8, 12.9 or 14.9, where
the first figure gives the minimum tensile
strength of the bolt material in tens of kgf/mm
2.
3.Zinc plated ISO metric bolts and nuts are
chromate passivated, a gold-bronze colour.METRIC NUT IDENTIFICATION
1.A nut with an ISO metric thread is marked on
one face or on one of the flats of the hexagon
with the strength grade symbol 8, 12 or 14.
Some nuts with a strength 4, 5 or 6 are also
marked and some have the metric symbol M on
the flat opposite the strength grade marking.
2.A clock face system is used as an alternative
method of indicating the strength grade. The
external chamfers or a face of the nut is marked
in a position relative to the appropriate hour
mark on a clock face to indicate the strength
grade.
3.A dot is used to locate the 12 O’clock position
and a dash to indicate the strength grade. If the
grade is above 12, two dots identify the 12
O’clock position.
KEYS AND KEYWAYS
1.Remove burrs from edges of keyways with a fine
file and clean thoroughly before attempting to
refit key.
2.Clean and inspect key closely; keys are suitable
for refitting only if indistinguishable from new, as
any indentation may indicate the onset of wear.
TAB WASHERS
1.Fit new washers in all places where they are
used. Always fit a new tab washer.
2.Ensure that the new tab washer is of the same
design as that replaced.
ProCarManuals.com
Page 63 of 667
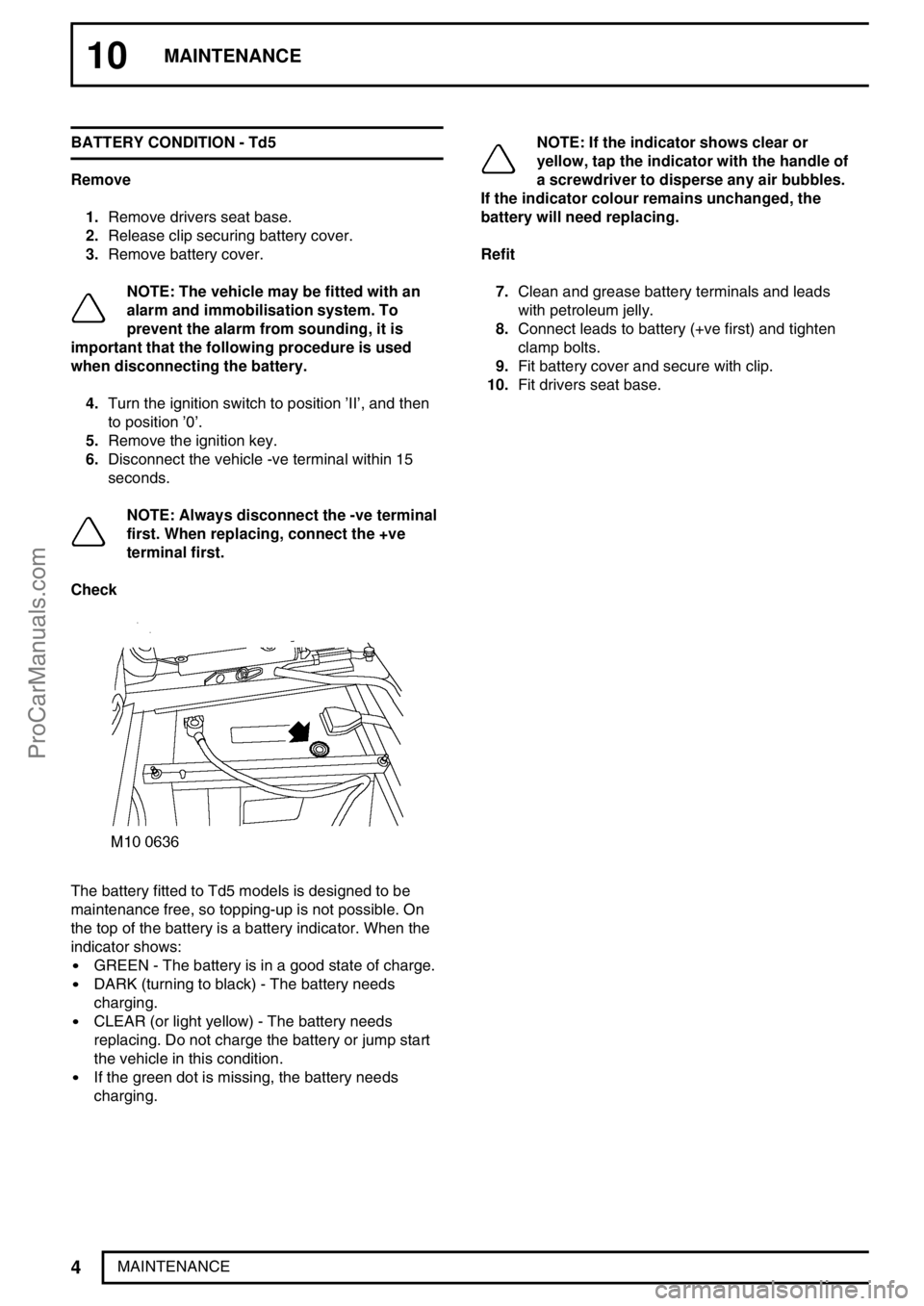
10MAINTENANCE
4
MAINTENANCE BATTERY CONDITION - Td5
Remove
1.Remove drivers seat base.
2.Release clip securing battery cover.
3.Remove battery cover.
NOTE: The vehicle may be fitted with an
alarm and immobilisation system. To
prevent the alarm from sounding, it is
important that the following procedure is used
when disconnecting the battery.
4.Turn the ignition switch to position’II’, and then
to position’0’.
5.Remove the ignition key.
6.Disconnect the vehicle -ve terminal within 15
seconds.
NOTE: Always disconnect the -ve terminal
first. When replacing, connect the +ve
terminal first.
Check
The battery fitted to Td5 models is designed to be
maintenance free, so topping-up is not possible. On
the top of the battery is a battery indicator. When the
indicator shows:
GREEN - The battery is in a good state of charge.
DARK (turning to black) - The battery needs
charging.
CLEAR (or light yellow) - The battery needs
replacing. Do not charge the battery or jump start
the vehicle in this condition.
If the green dot is missing, the battery needs
charging.
NOTE: If the indicator shows clear or
yellow, tap the indicator with the handle of
a screwdriver to disperse any air bubbles.
If the indicator colour remains unchanged, the
battery will need replacing.
Refit
7.Clean and grease battery terminals and leads
with petroleum jelly.
8.Connect leads to battery (+ve first) and tighten
clamp bolts.
9.Fit battery cover and secure with clip.
10.Fit drivers seat base.
ProCarManuals.com
Page 64 of 667
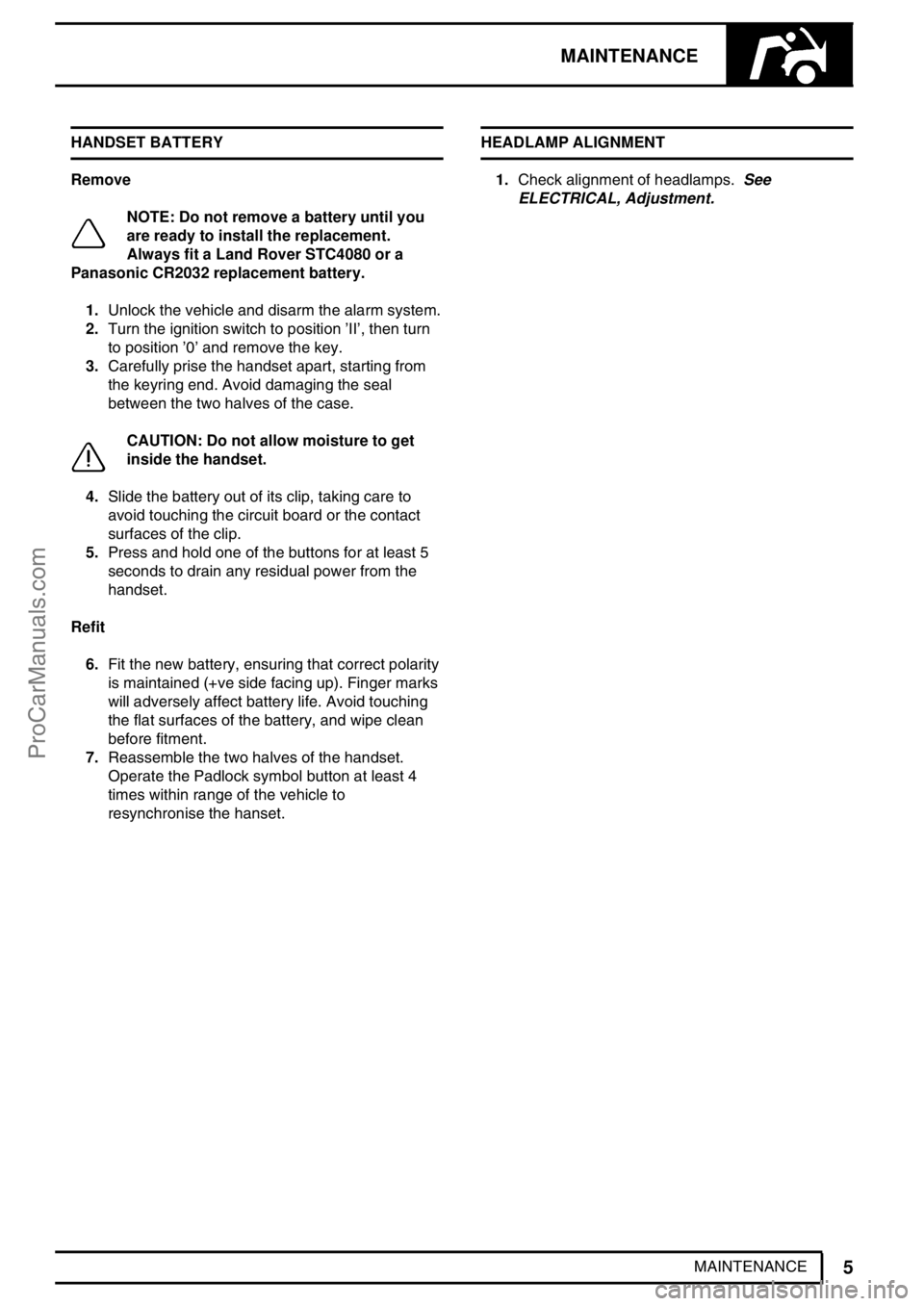
MAINTENANCE
5
MAINTENANCE HANDSET BATTERY
Remove
NOTE: Do not remove a battery until you
are ready to install the replacement.
Always fit a Land Rover STC4080 or a
Panasonic CR2032 replacement battery.
1.Unlock the vehicle and disarm the alarm system.
2.Turn the ignition switch to position’II’, then turn
to position’0’and remove the key.
3.Carefully prise the handset apart, starting from
the keyring end. Avoid damaging the seal
between the two halves of the case.
CAUTION: Do not allow moisture to get
inside the handset.
4.Slide the battery out of its clip, taking care to
avoid touching the circuit board or the contact
surfaces of the clip.
5.Press and hold one of the buttons for at least 5
seconds to drain any residual power from the
handset.
Refit
6.Fit the new battery, ensuring that correct polarity
is maintained (+ve side facing up). Finger marks
will adversely affect battery life. Avoid touching
the flat surfaces of the battery, and wipe clean
before fitment.
7.Reassemble the two halves of the handset.
Operate the Padlock symbol button at least 4
times within range of the vehicle to
resynchronise the hanset.HEADLAMP ALIGNMENT
1.Check alignment of headlamps.See
ELECTRICAL, Adjustment.
ProCarManuals.com
Page 90 of 667
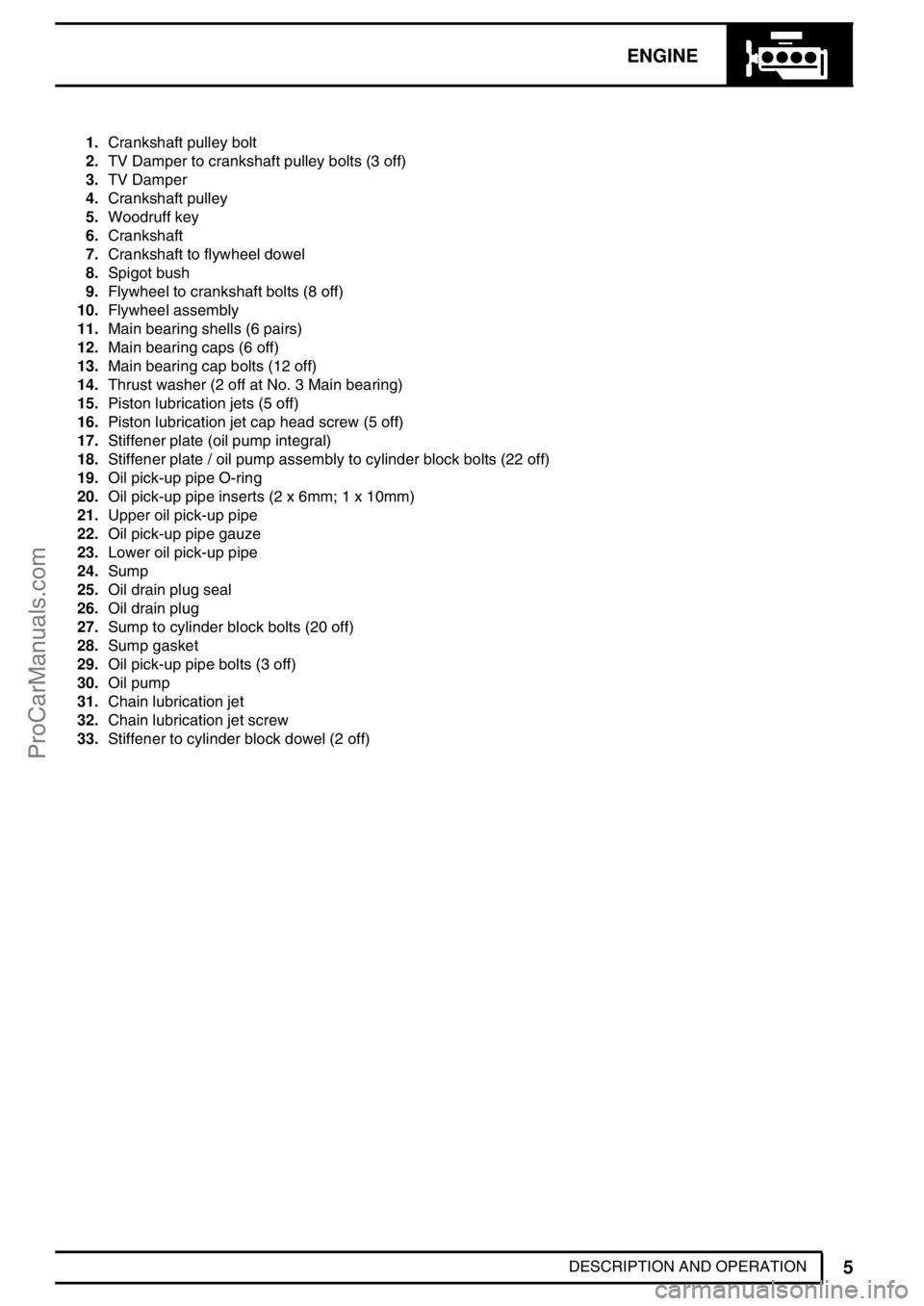
ENGINE
5
DESCRIPTION AND OPERATION 1.Crankshaft pulley bolt
2.TV Damper to crankshaft pulley bolts (3 off)
3.TV Damper
4.Crankshaft pulley
5.Woodruff key
6.Crankshaft
7.Crankshaft to flywheel dowel
8.Spigot bush
9.Flywheel to crankshaft bolts (8 off)
10.Flywheel assembly
11.Main bearing shells (6 pairs)
12.Main bearing caps (6 off)
13.Main bearing cap bolts (12 off)
14.Thrust washer (2 off at No. 3 Main bearing)
15.Piston lubrication jets (5 off)
16.Piston lubrication jet cap head screw (5 off)
17.Stiffener plate (oil pump integral)
18.Stiffener plate / oil pump assembly to cylinder block bolts (22 off)
19.Oil pick-up pipe O-ring
20.Oil pick-up pipe inserts (2 x 6mm; 1 x 10mm)
21.Upper oil pick-up pipe
22.Oil pick-up pipe gauze
23.Lower oil pick-up pipe
24.Sump
25.Oil drain plug seal
26.Oil drain plug
27.Sump to cylinder block bolts (20 off)
28.Sump gasket
29.Oil pick-up pipe bolts (3 off)
30.Oil pump
31.Chain lubrication jet
32.Chain lubrication jet screw
33.Stiffener to cylinder block dowel (2 off)
ProCarManuals.com
Page 116 of 667
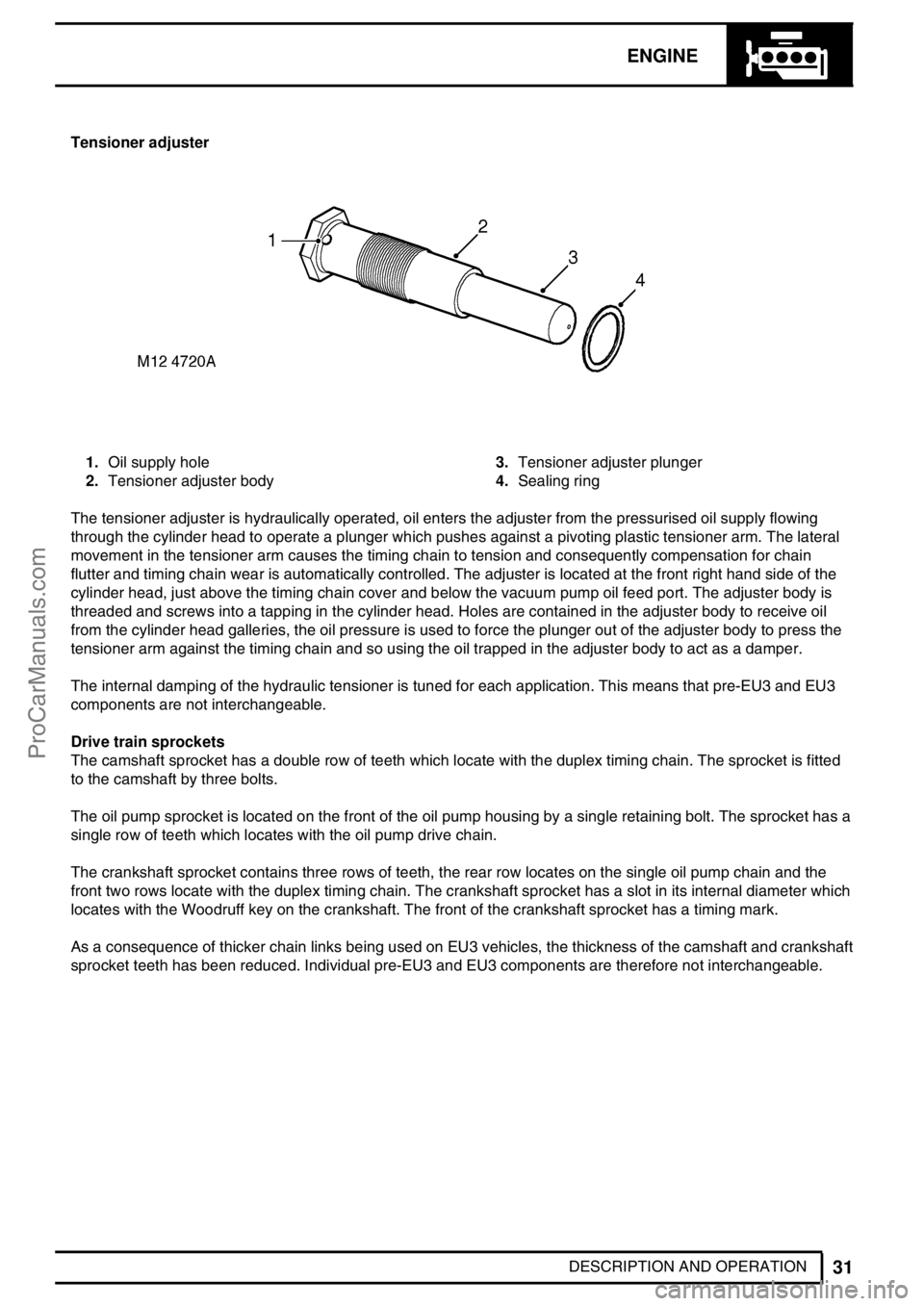
ENGINE
31
DESCRIPTION AND OPERATION Tensioner adjuster
1.Oil supply hole
2.Tensioner adjuster body3.Tensioner adjuster plunger
4.Sealing ring
The tensioner adjuster is hydraulically operated, oil enters the adjuster from the pressurised oil supply flowing
through the cylinder head to operate a plunger which pushes against a pivoting plastic tensioner arm. The lateral
movement in the tensioner arm causes the timing chain to tension and consequently compensation for chain
flutter and timing chain wear is automatically controlled. The adjuster is located at the front right hand side of the
cylinder head, just above the timing chain cover and below the vacuum pump oil feed port. The adjuster body is
threaded and screws into a tapping in the cylinder head. Holes are contained in the adjuster body to receive oil
from the cylinder head galleries, the oil pressure is used to force the plunger out of the adjuster body to press the
tensioner arm against the timing chain and so using the oil trapped in the adjuster body to act as a damper.
The internal damping of the hydraulic tensioner is tuned for each application. This means that pre-EU3 and EU3
components are not interchangeable.
Drive train sprockets
The camshaft sprocket has a double row of teeth which locate with the duplex timing chain. The sprocket is fitted
to the camshaft by three bolts.
The oil pump sprocket is located on the front of the oil pump housing by a single retaining bolt. The sprocket has a
single row of teeth which locates with the oil pump drive chain.
The crankshaft sprocket contains three rows of teeth, the rear row locates on the single oil pump chain and the
front two rows locate with the duplex timing chain. The crankshaft sprocket has a slot in its internal diameter which
locates with the Woodruff key on the crankshaft. The front of the crankshaft sprocket has a timing mark.
As a consequence of thicker chain links being used on EU3 vehicles, the thickness of the camshaft and crankshaft
sprocket teeth has been reduced. Individual pre-EU3 and EU3 components are therefore not interchangeable.
ProCarManuals.com
Page 166 of 667
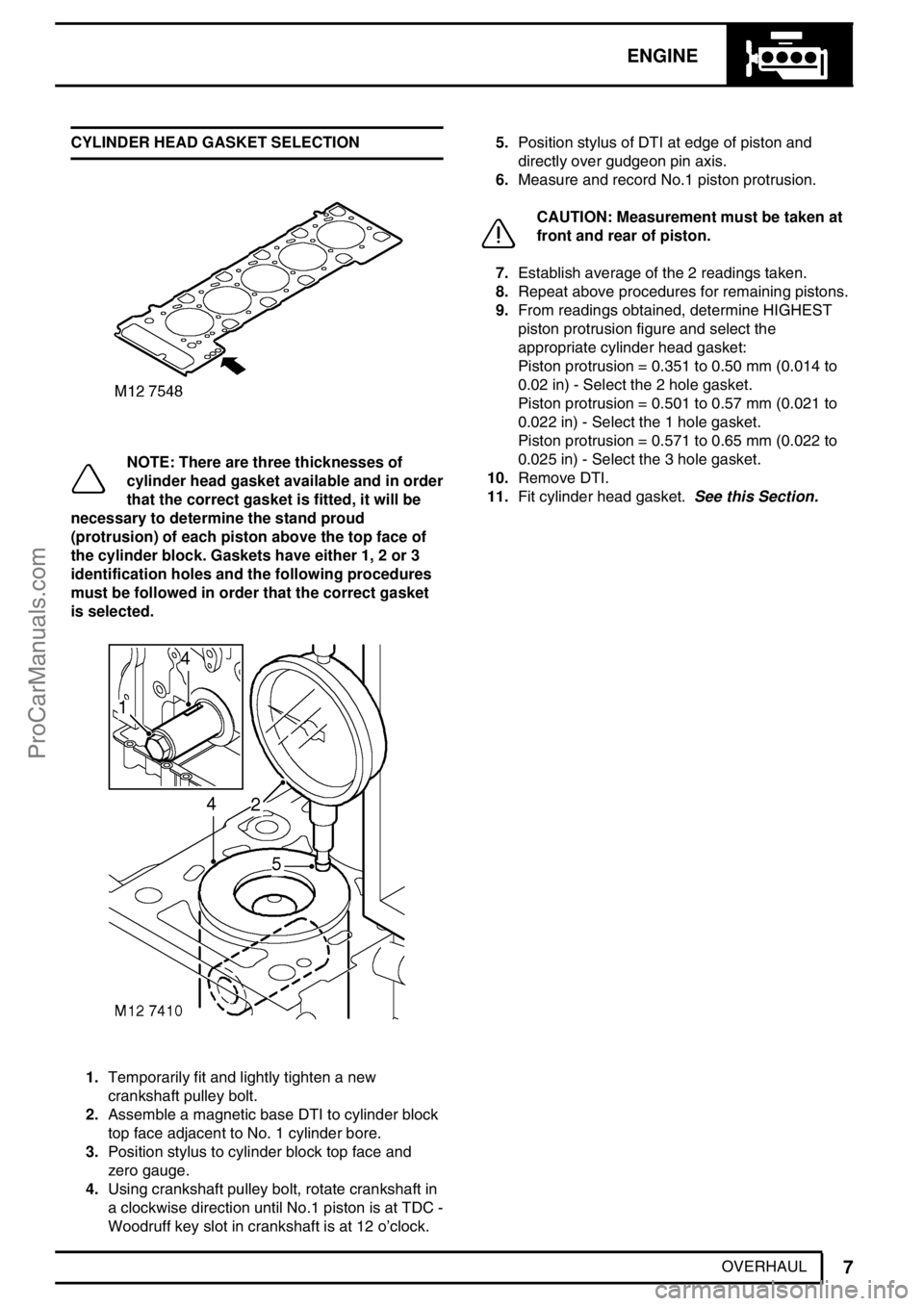
ENGINE
7
OVERHAUL CYLINDER HEAD GASKET SELECTION
NOTE: There are three thicknesses of
cylinder head gasket available and in order
that the correct gasket is fitted, it will be
necessary to determine the stand proud
(protrusion) of each piston above the top face of
the cylinder block. Gaskets have either 1, 2 or 3
identification holes and the following procedures
must be followed in order that the correct gasket
is selected.
1.Temporarily fit and lightly tighten a new
crankshaft pulley bolt.
2.Assemble a magnetic base DTI to cylinder block
top face adjacent to No. 1 cylinder bore.
3.Position stylus to cylinder block top face and
zero gauge.
4.Using crankshaft pulley bolt, rotate crankshaft in
a clockwise direction until No.1 piston is at TDC -
Woodruff key slot in crankshaft is at 12 o’clock.5.Position stylus of DTI at edge of piston and
directly over gudgeon pin axis.
6.Measure and record No.1 piston protrusion.
CAUTION: Measurement must be taken at
front and rear of piston.
7.Establish average of the 2 readings taken.
8.Repeat above procedures for remaining pistons.
9.From readings obtained, determine HIGHEST
piston protrusion figure and select the
appropriate cylinder head gasket:
Piston protrusion = 0.351 to 0.50 mm (0.014 to
0.02 in) - Select the 2 hole gasket.
Piston protrusion = 0.501 to 0.57 mm (0.021 to
0.022 in) - Select the 1 hole gasket.
Piston protrusion = 0.571 to 0.65 mm (0.022 to
0.025 in) - Select the 3 hole gasket.
10.Remove DTI.
11.Fit cylinder head gasket.See this Section.
ProCarManuals.com
Page 186 of 667
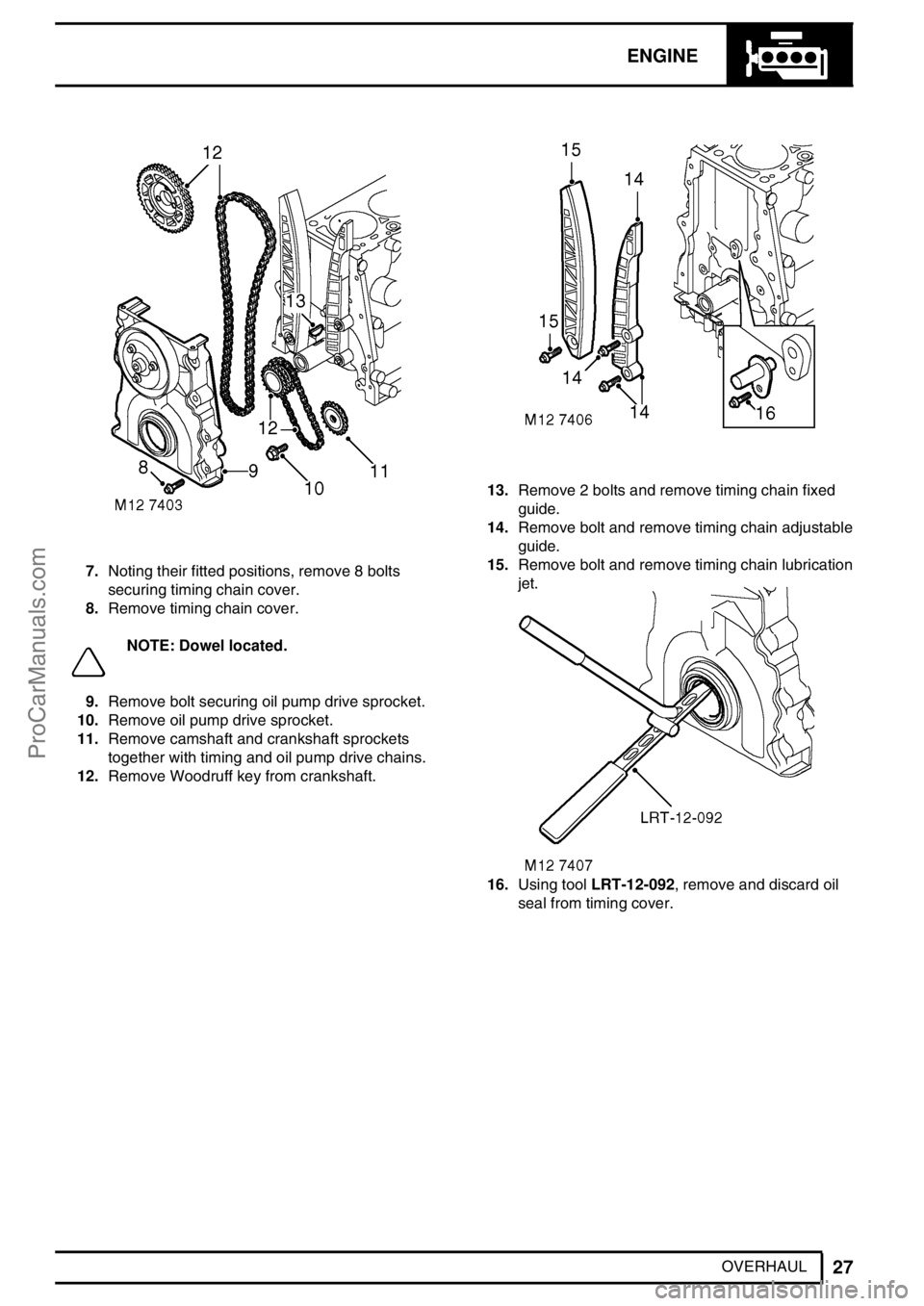
ENGINE
27
OVERHAUL
7.Noting their fitted positions, remove 8 bolts
securing timing chain cover.
8.Remove timing chain cover.
NOTE: Dowel located.
9.Remove bolt securing oil pump drive sprocket.
10.Remove oil pump drive sprocket.
11.Remove camshaft and crankshaft sprockets
together with timing and oil pump drive chains.
12.Remove Woodruff key from crankshaft.
13.Remove 2 bolts and remove timing chain fixed
guide.
14.Remove bolt and remove timing chain adjustable
guide.
15.Remove bolt and remove timing chain lubrication
jet.
16.Using toolLRT-12-092, remove and discard oil
seal from timing cover.
ProCarManuals.com
Page 187 of 667
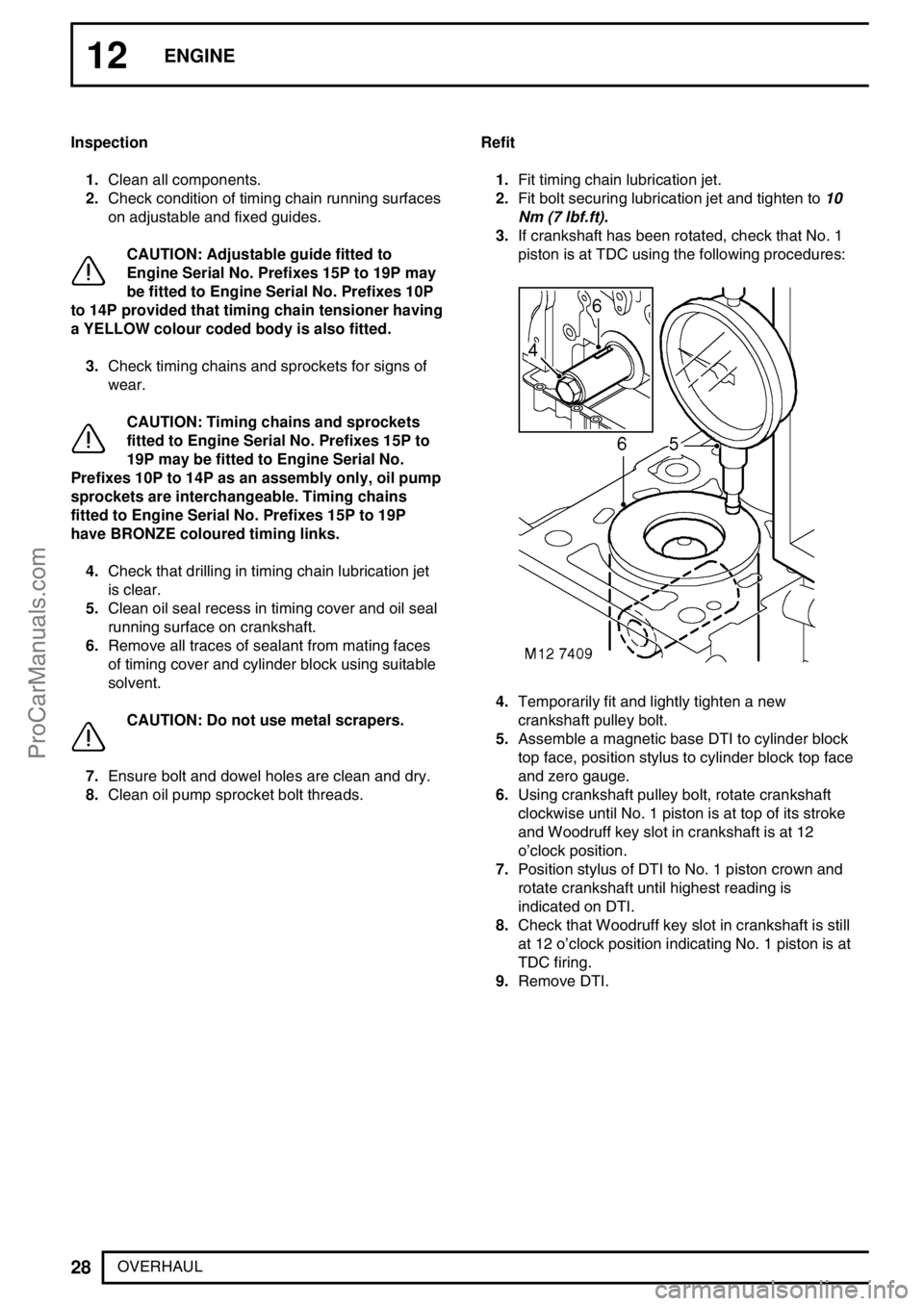
12ENGINE
28
OVERHAUL Inspection
1.Clean all components.
2.Check condition of timing chain running surfaces
on adjustable and fixed guides.
CAUTION: Adjustable guide fitted to
Engine Serial No. Prefixes 15P to 19P may
be fitted to Engine Serial No. Prefixes 10P
to 14P provided that timing chain tensioner having
a YELLOW colour coded body is also fitted.
3.Check timing chains and sprockets for signs of
wear.
CAUTION: Timing chains and sprockets
fitted to Engine Serial No. Prefixes 15P to
19P may be fitted to Engine Serial No.
Prefixes 10P to 14P as an assembly only, oil pump
sprockets are interchangeable. Timing chains
fitted to Engine Serial No. Prefixes 15P to 19P
have BRONZE coloured timing links.
4.Check that drilling in timing chain lubrication jet
is clear.
5.Clean oil seal recess in timing cover and oil seal
running surface on crankshaft.
6.Remove all traces of sealant from mating faces
of timing cover and cylinder block using suitable
solvent.
CAUTION: Do not use metal scrapers.
7.Ensure bolt and dowel holes are clean and dry.
8.Clean oil pump sprocket bolt threads.Refit
1.Fit timing chain lubrication jet.
2.Fit bolt securing lubrication jet and tighten to10
Nm (7 lbf.ft).
3.If crankshaft has been rotated, check that No. 1
piston is at TDC using the following procedures:
4.Temporarily fit and lightly tighten a new
crankshaft pulley bolt.
5.Assemble a magnetic base DTI to cylinder block
top face, position stylus to cylinder block top face
and zero gauge.
6.Using crankshaft pulley bolt, rotate crankshaft
clockwise until No. 1 piston is at top of its stroke
and Woodruff key slot in crankshaft is at 12
o’clock position.
7.Position stylus of DTI to No. 1 piston crown and
rotate crankshaft until highest reading is
indicated on DTI.
8.Check that Woodruff key slot in crankshaft is still
at 12 o’clock position indicating No. 1 piston is at
TDC firing.
9.Remove DTI.
ProCarManuals.com