check engine LAND ROVER DISCOVERY 1995 User Guide
[x] Cancel search | Manufacturer: LAND ROVER, Model Year: 1995, Model line: DISCOVERY, Model: LAND ROVER DISCOVERY 1995Pages: 873, PDF Size: 12.89 MB
Page 72 of 873
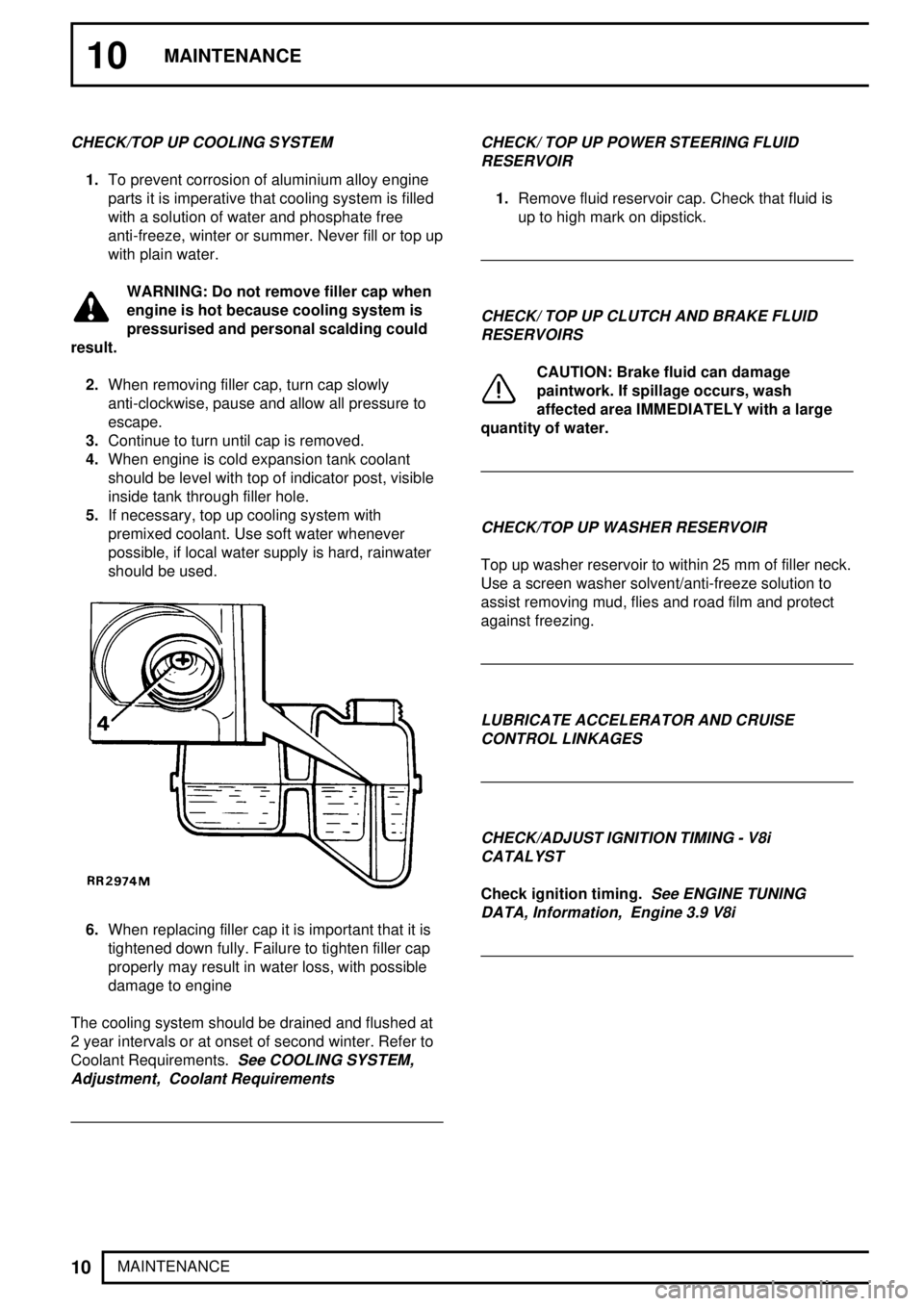
10MAINTENANCE
10
MAINTENANCE
CHECK/TOP UP COOLING SYSTEM
1.To prevent corrosion of aluminium alloy engine
parts it is imperative that cooling system is filled
with a solution of water and phosphate free
anti-freeze, winter or summer. Never fill or top up
with plain water.
WARNING: Do not remove filler cap when
engine is hot because cooling system is
pressurised and personal scalding could
result.
2.When removing filler cap, turn cap slowly
anti-clockwise, pause and allow all pressure to
escape.
3.Continue to turn until cap is removed.
4.When engine is cold expansion tank coolant
should be level with top of indicator post, visible
inside tank through filler hole.
5.If necessary, top up cooling system with
premixed coolant. Use soft water whenever
possible, if local water supply is hard, rainwater
should be used.
6.When replacing filler cap it is important that it is
tightened down fully. Failure to tighten filler cap
properly may result in water loss, with possible
damage to engine
The cooling system should be drained and flushed at
2 year intervals or at onset of second winter. Refer to
Coolant Requirements.
See COOLING SYSTEM,
Adjustment, Coolant RequirementsCHECK/ TOP UP POWER STEERING FLUID
RESERVOIR
1.Remove fluid reservoir cap. Check that fluid is
up to high mark on dipstick.
CHECK/ TOP UP CLUTCH AND BRAKE FLUID
RESERVOIRS
CAUTION: Brake fluid can damage
paintwork. If spillage occurs, wash
affected area IMMEDIATELY with a large
quantity of water.
CHECK/TOP UP WASHER RESERVOIR
Top up washer reservoir to within 25 mm of filler neck.
Use a screen washer solvent/anti-freeze solution to
assist removing mud, flies and road film and protect
against freezing.
LUBRICATE ACCELERATOR AND CRUISE
CONTROL LINKAGES
CHECK/ADJUST IGNITION TIMING - V8i
CATALYST
Check ignition timing.See ENGINE TUNING
DATA, Information, Engine 3.9 V8i
Page 73 of 873
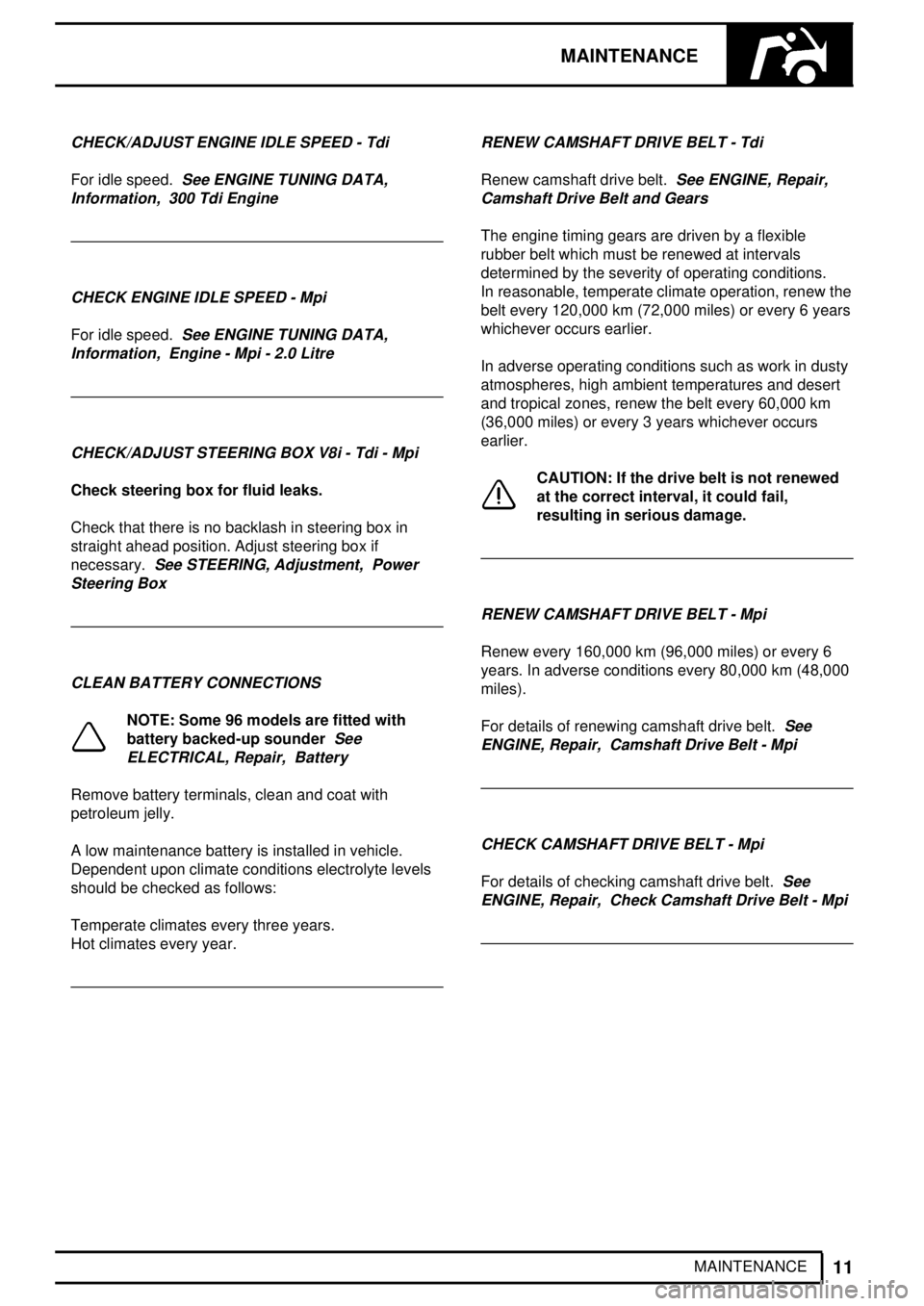
MAINTENANCE
11
MAINTENANCE
CHECK/ADJUST ENGINE IDLE SPEED - Tdi
For idle speed.See ENGINE TUNING DATA,
Information, 300 Tdi Engine
CHECK ENGINE IDLE SPEED - Mpi
For idle speed.See ENGINE TUNING DATA,
Information, Engine - Mpi - 2.0 Litre
CHECK/ADJUST STEERING BOX V8i - Tdi - Mpi
Check steering box for fluid leaks.
Check that there is no backlash in steering box in
straight ahead position. Adjust steering box if
necessary.
See STEERING, Adjustment, Power
Steering Box
CLEAN BATTERY CONNECTIONS
NOTE: Some 96 models are fitted with
battery backed-up sounder
See
ELECTRICAL, Repair, Battery
Remove battery terminals, clean and coat with
petroleum jelly.
A low maintenance battery is installed in vehicle.
Dependent upon climate conditions electrolyte levels
should be checked as follows:
Temperate climates every three years.
Hot climates every year.
RENEW CAMSHAFT DRIVE BELT - Tdi
Renew camshaft drive belt.See ENGINE, Repair,
Camshaft Drive Belt and Gears
The engine timing gears are driven by a flexible
rubber belt which must be renewed at intervals
determined by the severity of operating conditions.
In reasonable, temperate climate operation, renew the
belt every 120,000 km (72,000 miles) or every 6 years
whichever occurs earlier.
In adverse operating conditions such as work in dusty
atmospheres, high ambient temperatures and desert
and tropical zones, renew the belt every 60,000 km
(36,000 miles) or every 3 years whichever occurs
earlier.
CAUTION: If the drive belt is not renewed
at the correct interval, it could fail,
resulting in serious damage.
RENEW CAMSHAFT DRIVE BELT - Mpi
Renew every 160,000 km (96,000 miles) or every 6
years. In adverse conditions every 80,000 km (48,000
miles).
For details of renewing camshaft drive belt.
See
ENGINE, Repair, Camshaft Drive Belt - Mpi
CHECK CAMSHAFT DRIVE BELT - Mpi
For details of checking camshaft drive belt.See
ENGINE, Repair, Check Camshaft Drive Belt - Mpi
Page 74 of 873
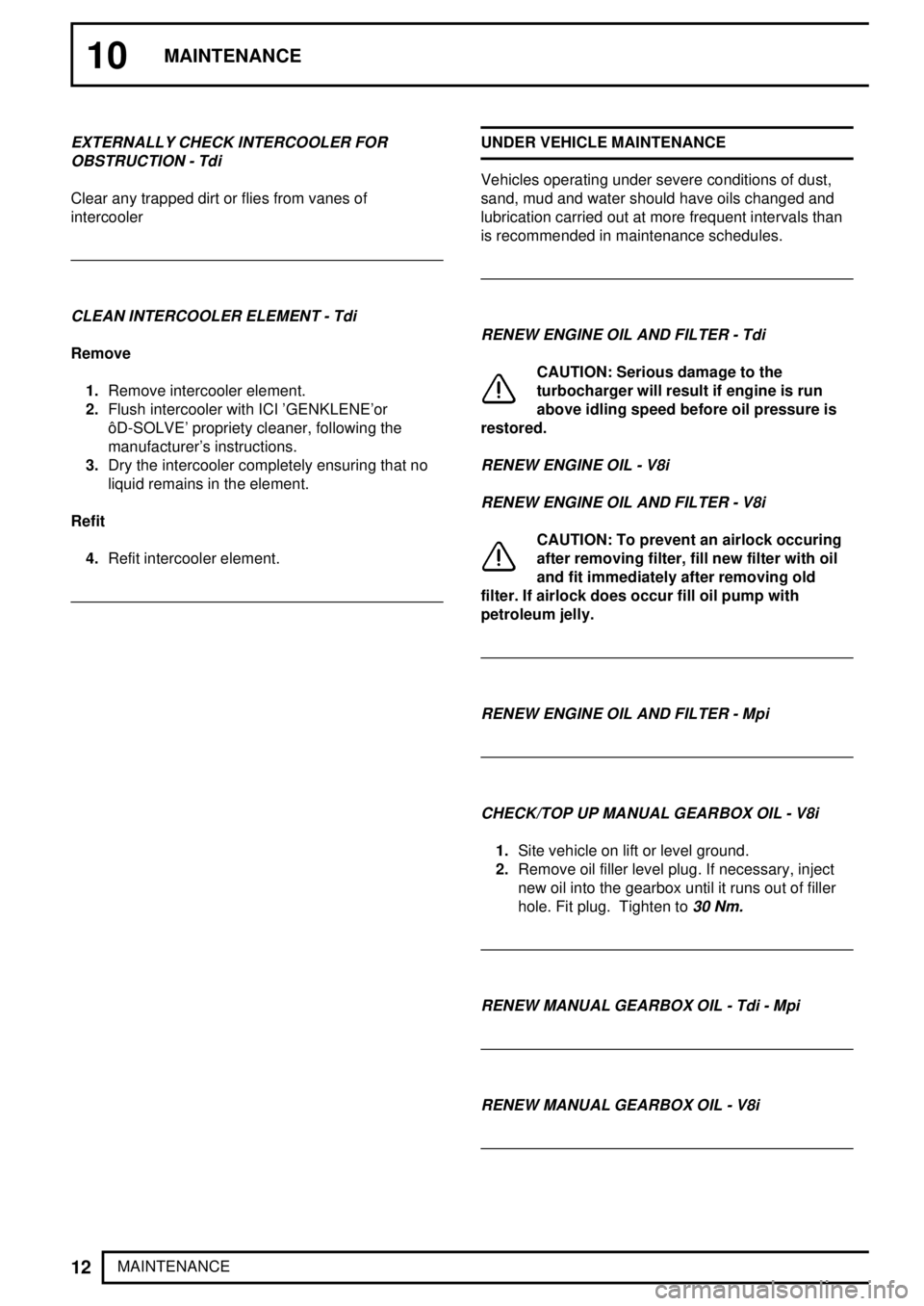
10MAINTENANCE
12
MAINTENANCE
EXTERNALLY CHECK INTERCOOLER FOR
OBSTRUCTION - Tdi
Clear any trapped dirt or flies from vanes of
intercooler
CLEAN INTERCOOLER ELEMENT - Tdi
Remove
1.Remove intercooler element.
2.Flush intercooler with ICI 'GENKLENE'or
à oD-SOLVE' propriety cleaner, following the
manufacturer's instructions.
3.Dry the intercooler completely ensuring that no
liquid remains in the element.
Refit
4.Refit intercooler element.UNDER VEHICLE MAINTENANCE
Vehicles operating under severe conditions of dust,
sand, mud and water should have oils changed and
lubrication carried out at more frequent intervals than
is recommended in maintenance schedules.
RENEW ENGINE OIL AND FILTER - Tdi
CAUTION: Serious damage to the
turbocharger will result if engine is run
above idling speed before oil pressure is
restored.
RENEW ENGINE OIL - V8i
RENEW ENGINE OIL AND FILTER - V8i
CAUTION: To prevent an airlock occuring
after removing filter, fill new filter with oil
and fit immediately after removing old
filter. If airlock does occur fill oil pump with
petroleum jelly.
RENEW ENGINE OIL AND FILTER - Mpi
CHECK/TOP UP MANUAL GEARBOX OIL - V8i
1.Site vehicle on lift or level ground.
2.Remove oil filler level plug. If necessary, inject
new oil into the gearbox until it runs out of filler
hole. Fit plug. Tighten to
30 Nm.
RENEW MANUAL GEARBOX OIL - Tdi - Mpi
RENEW MANUAL GEARBOX OIL - V8i
Page 75 of 873
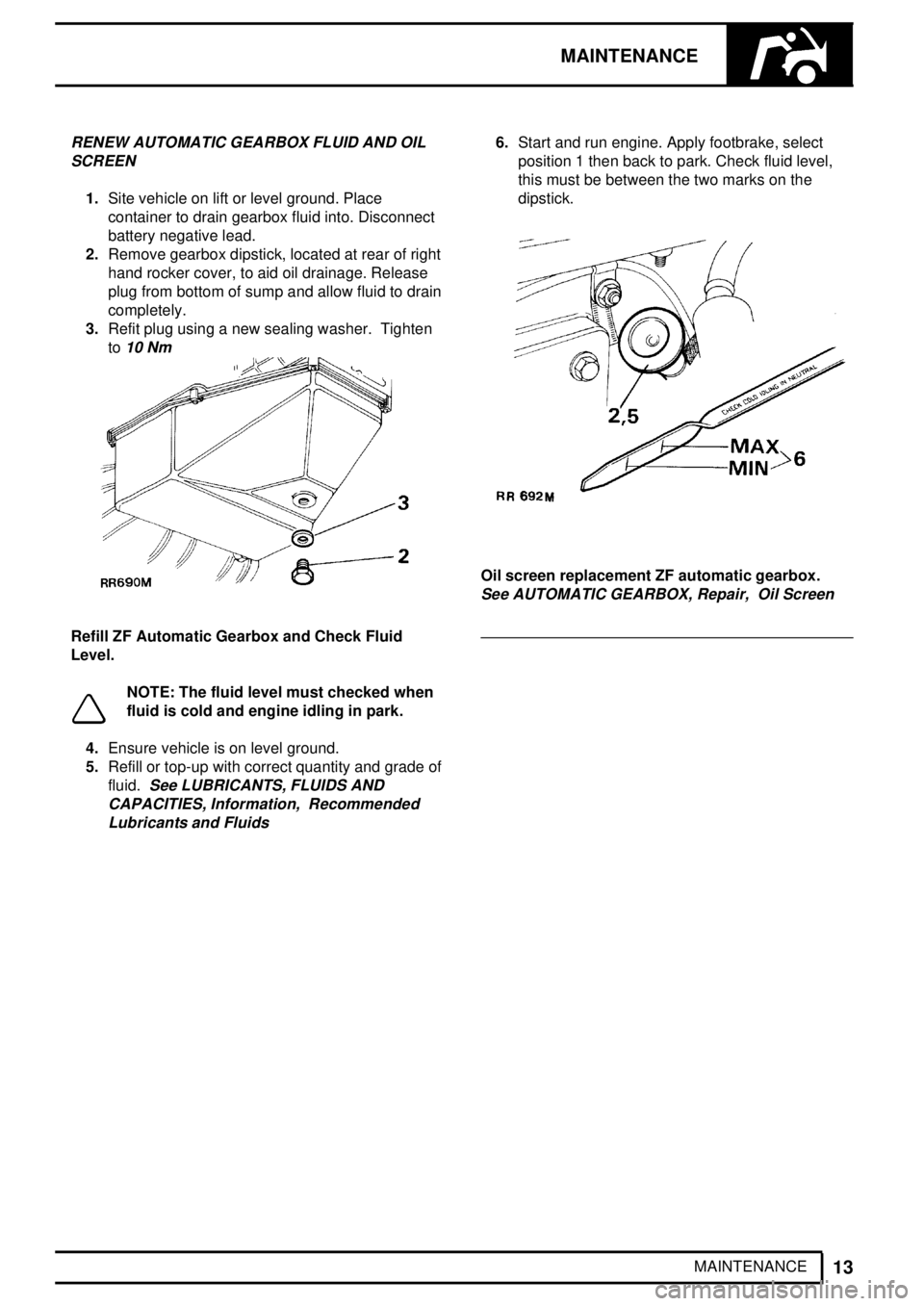
MAINTENANCE
13
MAINTENANCE
RENEW AUTOMATIC GEARBOX FLUID AND OIL
SCREEN
1.Site vehicle on lift or level ground. Place
container to drain gearbox fluid into. Disconnect
battery negative lead.
2.Remove gearbox dipstick, located at rear of right
hand rocker cover, to aid oil drainage. Release
plug from bottom of sump and allow fluid to drain
completely.
3.Refit plug using a new sealing washer. Tighten
to
10 Nm
Refill ZF Automatic Gearbox and Check Fluid
Level.
NOTE: The fluid level must checked when
fluid is cold and engine idling in park.
4.Ensure vehicle is on level ground.
5.Refill or top-up with correct quantity and grade of
fluid.
See LUBRICANTS, FLUIDS AND
CAPACITIES, Information, Recommended
Lubricants and Fluids
6.Start and run engine. Apply footbrake, select
position 1 then back to park. Check fluid level,
this must be between the two marks on the
dipstick.
Oil screen replacement ZF automatic gearbox.
See AUTOMATIC GEARBOX, Repair, Oil Screen
Page 79 of 873
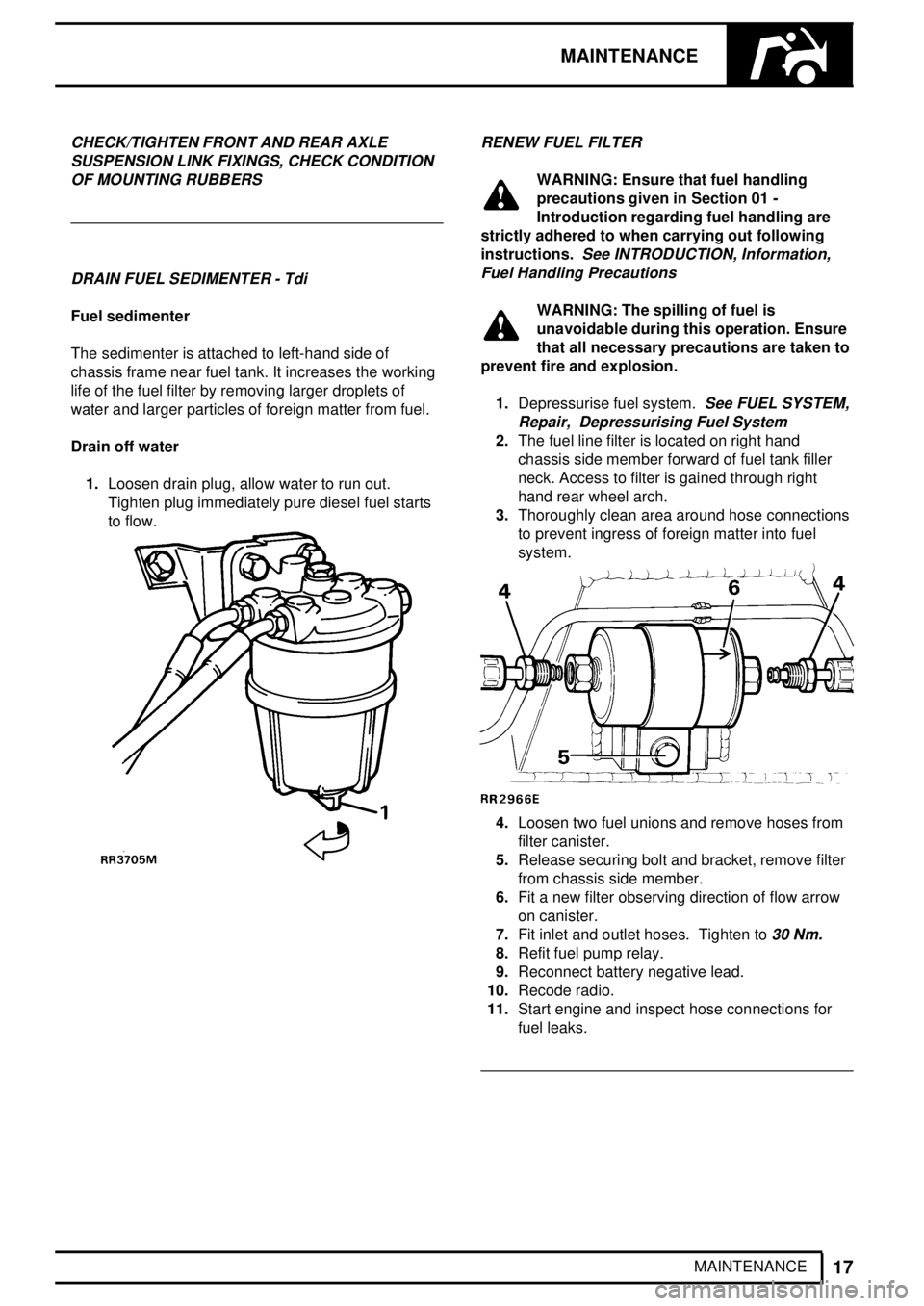
MAINTENANCE
17
MAINTENANCE
CHECK/TIGHTEN FRONT AND REAR AXLE
SUSPENSION LINK FIXINGS, CHECK CONDITION
OF MOUNTING RUBBERS
DRAIN FUEL SEDIMENTER - Tdi
Fuel sedimenter
The sedimenter is attached to left-hand side of
chassis frame near fuel tank. It increases the working
life of the fuel filter by removing larger droplets of
water and larger particles of foreign matter from fuel.
Drain off water
1.Loosen drain plug, allow water to run out.
Tighten plug immediately pure diesel fuel starts
to flow.
RENEW FUEL FILTER
WARNING: Ensure that fuel handling
precautions given in Section 01 -
Introduction regarding fuel handling are
strictly adhered to when carrying out following
instructions.
See INTRODUCTION, Information,
Fuel Handling Precautions
WARNING: The spilling of fuel is
unavoidable during this operation. Ensure
that all necessary precautions are taken to
prevent fire and explosion.
1.Depressurise fuel system.
See FUEL SYSTEM,
Repair, Depressurising Fuel System
2.The fuel line filter is located on right hand
chassis side member forward of fuel tank filler
neck. Access to filter is gained through right
hand rear wheel arch.
3.Thoroughly clean area around hose connections
to prevent ingress of foreign matter into fuel
system.
4.Loosen two fuel unions and remove hoses from
filter canister.
5.Release securing bolt and bracket, remove filter
from chassis side member.
6.Fit a new filter observing direction of flow arrow
on canister.
7.Fit inlet and outlet hoses. Tighten to
30 Nm.
8.Refit fuel pump relay.
9.Reconnect battery negative lead.
10.Recode radio.
11.Start engine and inspect hose connections for
fuel leaks.
Page 80 of 873
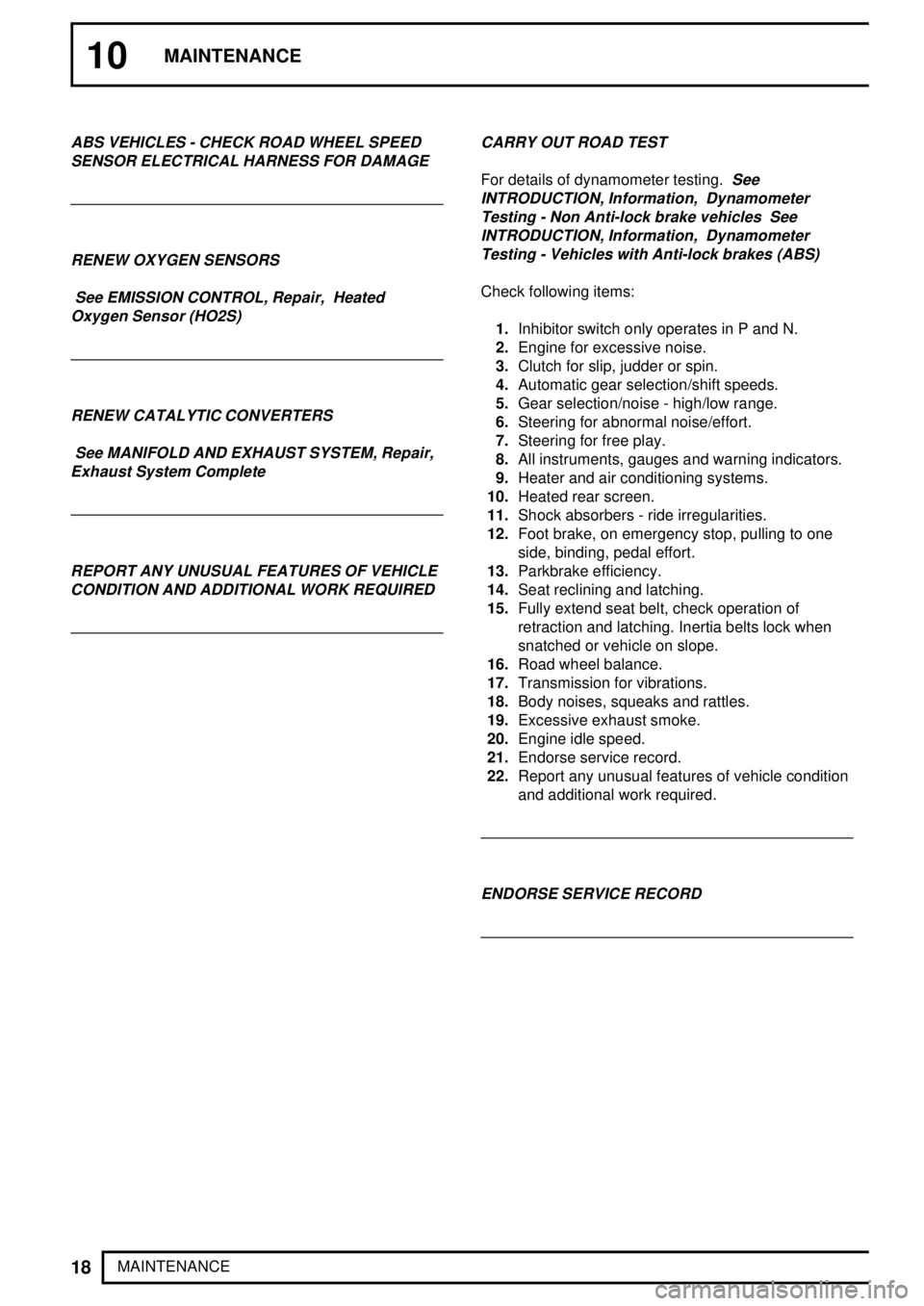
10MAINTENANCE
18
MAINTENANCE
ABS VEHICLES - CHECK ROAD WHEEL SPEED
SENSOR ELECTRICAL HARNESS FOR DAMAGE
RENEW OXYGEN SENSORS
See EMISSION CONTROL, Repair, Heated
Oxygen Sensor (HO2S)
RENEW CATALYTIC CONVERTERS
See MANIFOLD AND EXHAUST SYSTEM, Repair,
Exhaust System Complete
REPORT ANY UNUSUAL FEATURES OF VEHICLE
CONDITION AND ADDITIONAL WORK REQUIREDCARRY OUT ROAD TEST
For details of dynamometer testing.See
INTRODUCTION, Information, Dynamometer
Testing - Non Anti-lock brake vehicles See
INTRODUCTION, Information, Dynamometer
Testing - Vehicles with Anti-lock brakes (ABS)
Check following items:
1.Inhibitor switch only operates in P and N.
2.Engine for excessive noise.
3.Clutch for slip, judder or spin.
4.Automatic gear selection/shift speeds.
5.Gear selection/noise - high/low range.
6.Steering for abnormal noise/effort.
7.Steering for free play.
8.All instruments, gauges and warning indicators.
9.Heater and air conditioning systems.
10.Heated rear screen.
11.Shock absorbers - ride irregularities.
12.Foot brake, on emergency stop, pulling to one
side, binding, pedal effort.
13.Parkbrake efficiency.
14.Seat reclining and latching.
15.Fully extend seat belt, check operation of
retraction and latching. Inertia belts lock when
snatched or vehicle on slope.
16.Road wheel balance.
17.Transmission for vibrations.
18.Body noises, squeaks and rattles.
19.Excessive exhaust smoke.
20.Engine idle speed.
21.Endorse service record.
22.Report any unusual features of vehicle condition
and additional work required.
ENDORSE SERVICE RECORD
Page 81 of 873
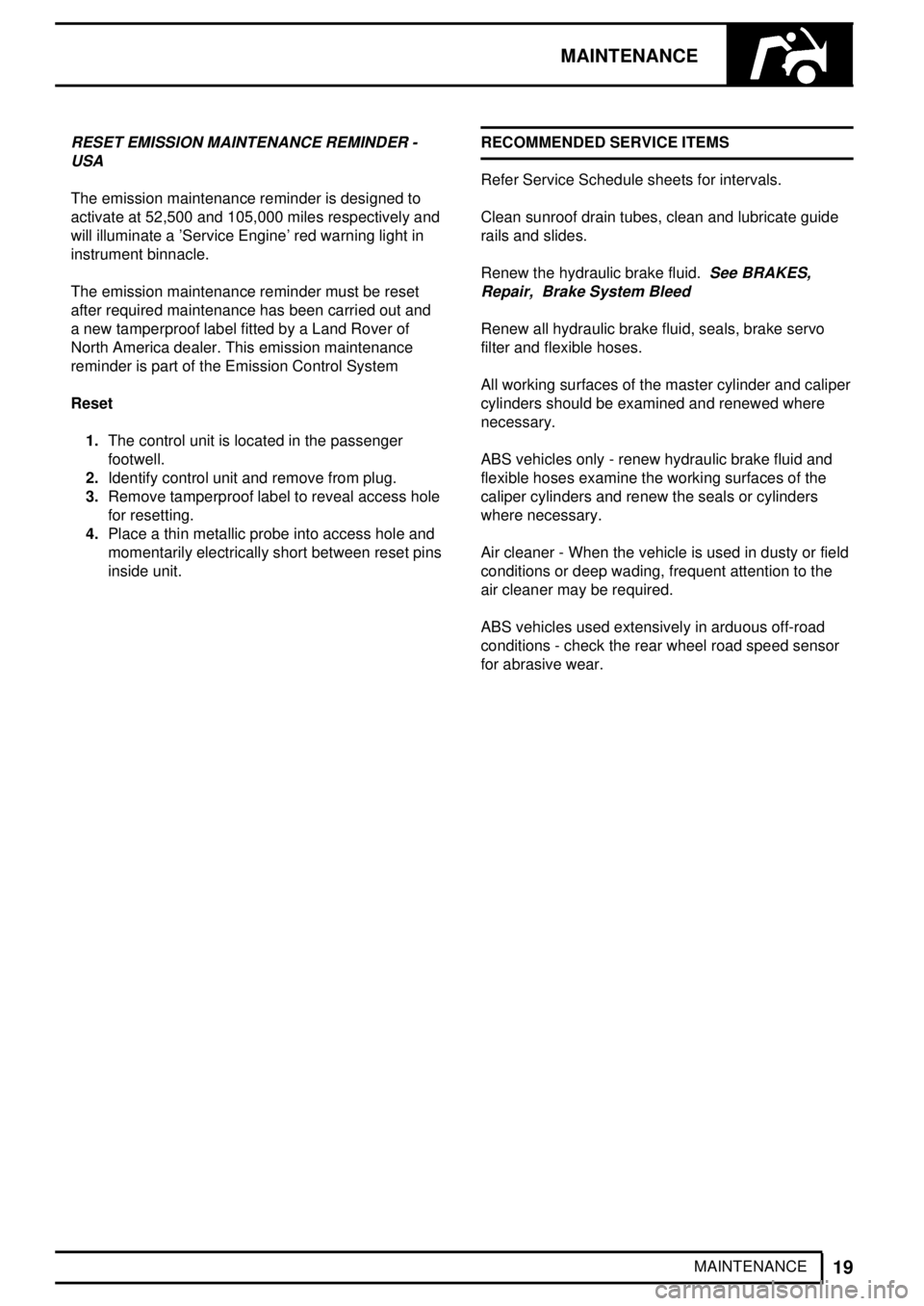
MAINTENANCE
19
MAINTENANCE
RESET EMISSION MAINTENANCE REMINDER -
USA
The emission maintenance reminder is designed to
activate at 52,500 and 105,000 miles respectively and
will illuminate a 'Service Engine' red warning light in
instrument binnacle.
The emission maintenance reminder must be reset
after required maintenance has been carried out and
a new tamperproof label fitted by a Land Rover of
North America dealer. This emission maintenance
reminder is part of the Emission Control System
Reset
1.The control unit is located in the passenger
footwell.
2.Identify control unit and remove from plug.
3.Remove tamperproof label to reveal access hole
for resetting.
4.Place a thin metallic probe into access hole and
momentarily electrically short between reset pins
inside unit.RECOMMENDED SERVICE ITEMS
Refer Service Schedule sheets for intervals.
Clean sunroof drain tubes, clean and lubricate guide
rails and slides.
Renew the hydraulic brake fluid.
See BRAKES,
Repair, Brake System Bleed
Renew all hydraulic brake fluid, seals, brake servo
filter and flexible hoses.
All working surfaces of the master cylinder and caliper
cylinders should be examined and renewed where
necessary.
ABS vehicles only - renew hydraulic brake fluid and
flexible hoses examine the working surfaces of the
caliper cylinders and renew the seals or cylinders
where necessary.
Air cleaner - When the vehicle is used in dusty or field
conditions or deep wading, frequent attention to the
air cleaner may be required.
ABS vehicles used extensively in arduous off-road
conditions - check the rear wheel road speed sensor
for abrasive wear.
Page 86 of 873
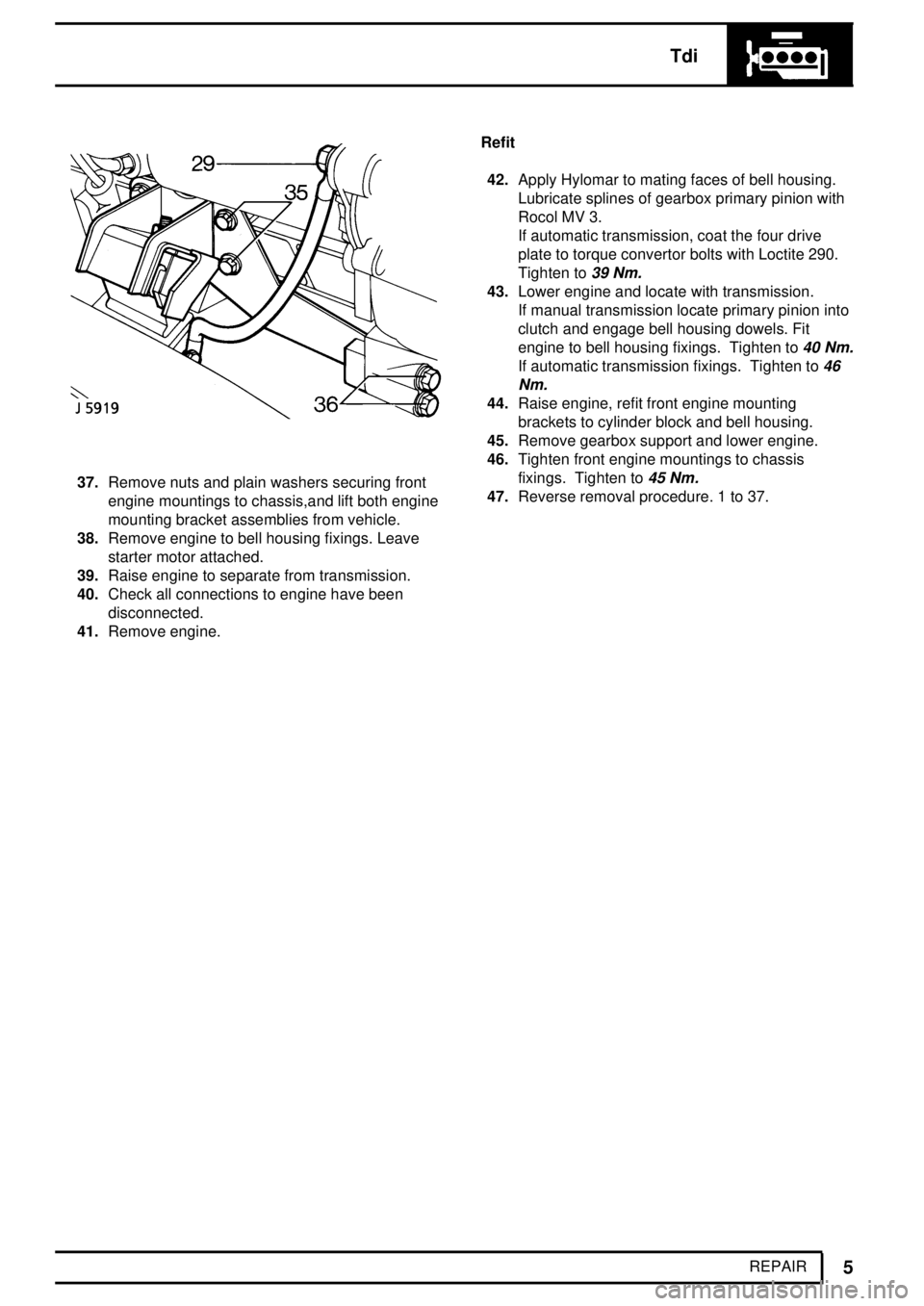
Tdi
5
REPAIR
37.Remove nuts and plain washers securing front
engine mountings to chassis,and lift both engine
mounting bracket assemblies from vehicle.
38.Remove engine to bell housing fixings. Leave
starter motor attached.
39.Raise engine to separate from transmission.
40.Check all connections to engine have been
disconnected.
41.Remove engine.Refit
42.Apply Hylomar to mating faces of bell housing.
Lubricate splines of gearbox primary pinion with
Rocol MV 3.
If automatic transmission, coat the four drive
plate to torque convertor bolts with Loctite 290.
Tighten to
39 Nm.
43.Lower engine and locate with transmission.
If manual transmission locate primary pinion into
clutch and engage bell housing dowels. Fit
engine to bell housing fixings. Tighten to
40 Nm.
If automatic transmission fixings. Tighten to46
Nm.
44.Raise engine, refit front engine mounting
brackets to cylinder block and bell housing.
45.Remove gearbox support and lower engine.
46.Tighten front engine mountings to chassis
fixings. Tighten to
45 Nm.
47.Reverse removal procedure. 1 to 37.
Page 89 of 873
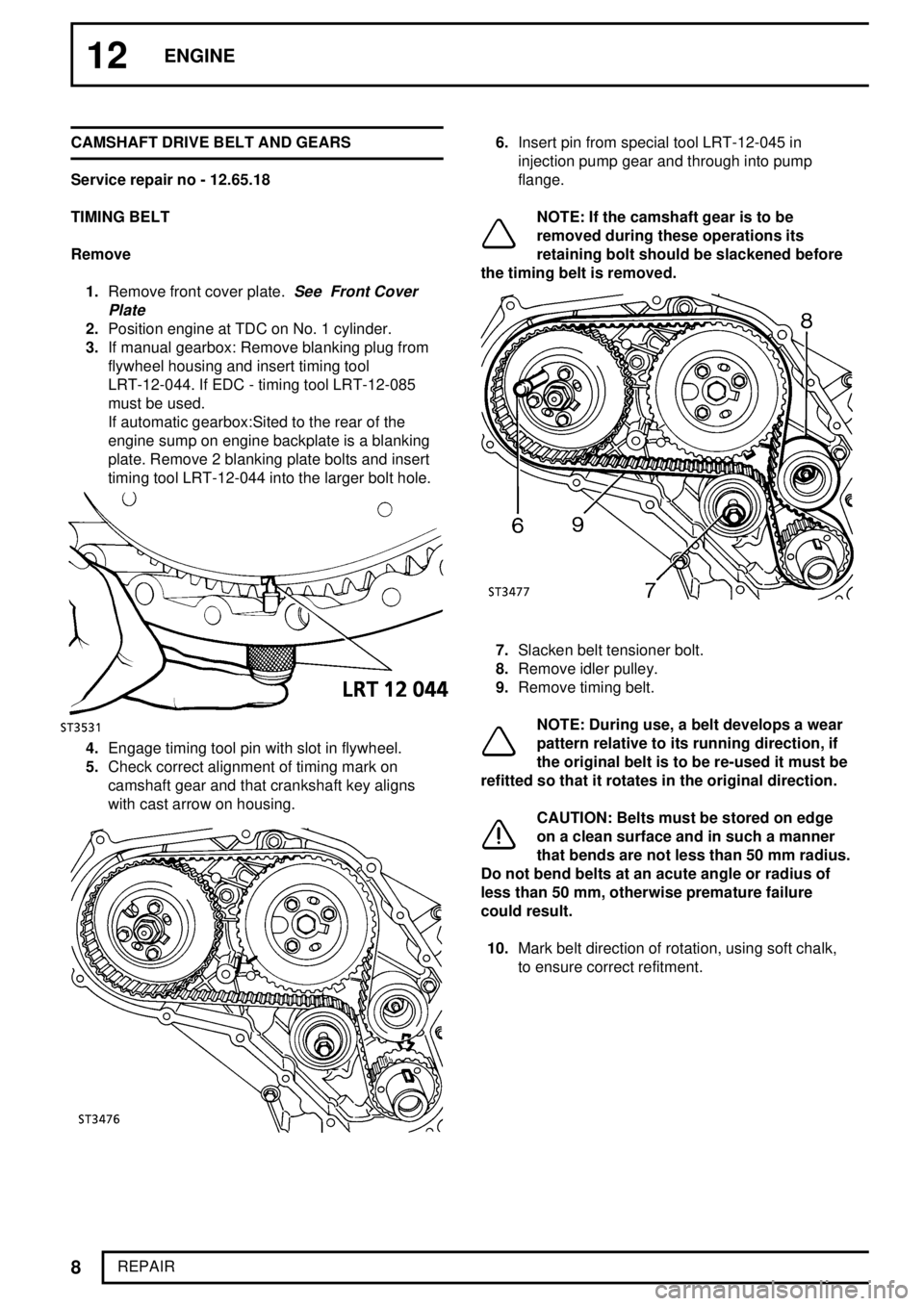
12ENGINE
8
REPAIR CAMSHAFT DRIVE BELT AND GEARS
Service repair no - 12.65.18
TIMING BELT
Remove
1.Remove front cover plate.
See Front Cover
Plate
2.Position engine at TDC on No. 1 cylinder.
3.If manual gearbox: Remove blanking plug from
flywheel housing and insert timing tool
LRT-12-044. If EDC - timing tool LRT-12-085
must be used.
If automatic gearbox:Sited to the rear of the
engine sump on engine backplate is a blanking
plate. Remove 2 blanking plate bolts and insert
timing tool LRT-12-044 into the larger bolt hole.
4.Engage timing tool pin with slot in flywheel.
5.Check correct alignment of timing mark on
camshaft gear and that crankshaft key aligns
with cast arrow on housing.
6.Insert pin from special tool LRT-12-045 in
injection pump gear and through into pump
flange.
NOTE: If the camshaft gear is to be
removed during these operations its
retaining bolt should be slackened before
the timing belt is removed.
7.Slacken belt tensioner bolt.
8.Remove idler pulley.
9.Remove timing belt.
NOTE: During use, a belt develops a wear
pattern relative to its running direction, if
the original belt is to be re-used it must be
refitted so that it rotates in the original direction.
CAUTION: Belts must be stored on edge
on a clean surface and in such a manner
that bends are not less than 50 mm radius.
Do not bend belts at an acute angle or radius of
less than 50 mm, otherwise premature failure
could result.
10.Mark belt direction of rotation, using soft chalk,
to ensure correct refitment.
Page 95 of 873
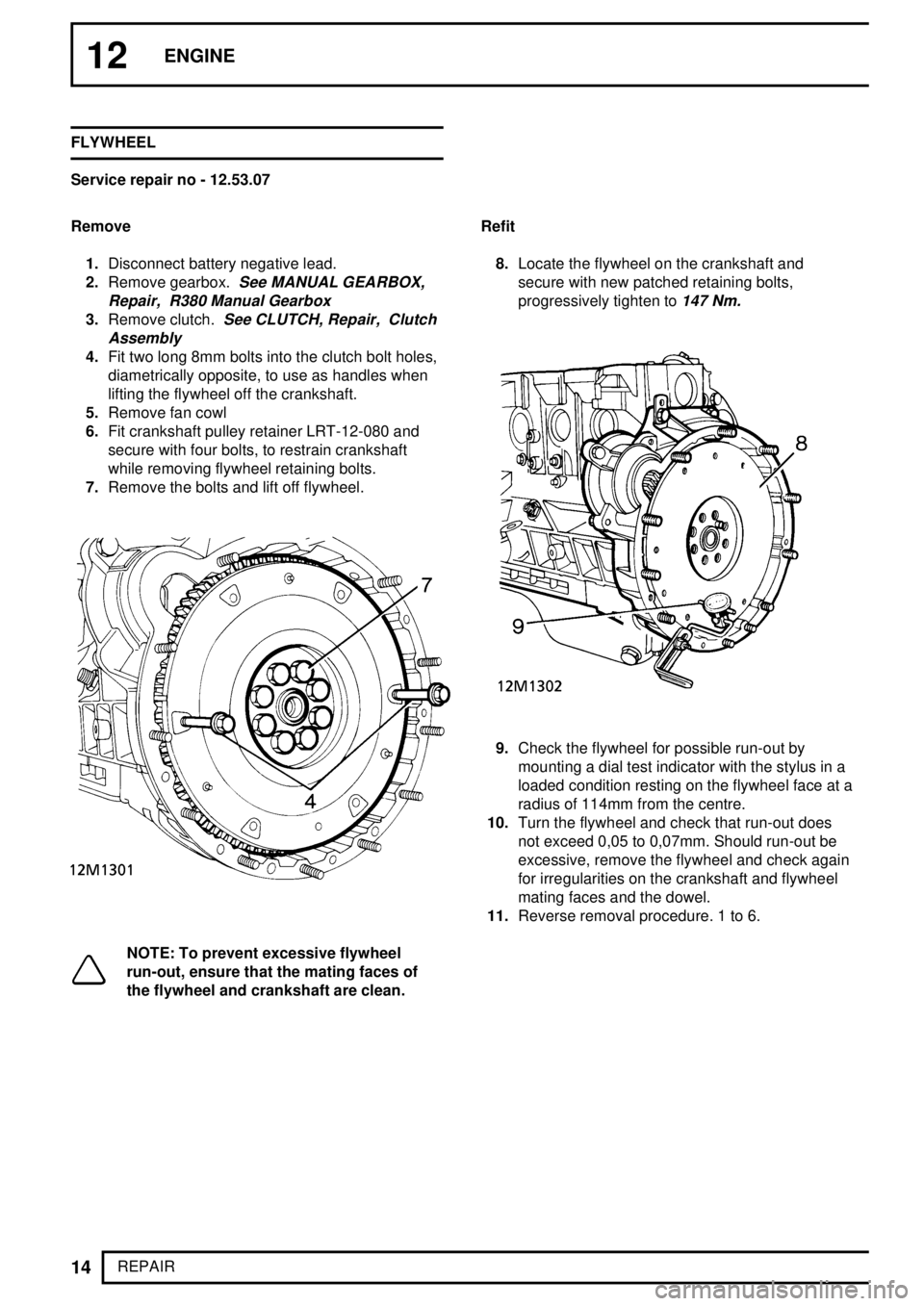
12ENGINE
14
REPAIR FLYWHEEL
Service repair no - 12.53.07
Remove
1.Disconnect battery negative lead.
2.Remove gearbox.
See MANUAL GEARBOX,
Repair, R380 Manual Gearbox
3.Remove clutch.See CLUTCH, Repair, Clutch
Assembly
4.Fit two long 8mm bolts into the clutch bolt holes,
diametrically opposite, to use as handles when
lifting the flywheel off the crankshaft.
5.Remove fan cowl
6.Fit crankshaft pulley retainer LRT-12-080 and
secure with four bolts, to restrain crankshaft
while removing flywheel retaining bolts.
7.Remove the bolts and lift off flywheel.
NOTE: To prevent excessive flywheel
run-out, ensure that the mating faces of
the flywheel and crankshaft are clean.Refit
8.Locate the flywheel on the crankshaft and
secure with new patched retaining bolts,
progressively tighten to
147 Nm.
9.Check the flywheel for possible run-out by
mounting a dial test indicator with the stylus in a
loaded condition resting on the flywheel face at a
radius of 114mm from the centre.
10.Turn the flywheel and check that run-out does
not exceed 0,05 to 0,07mm. Should run-out be
excessive, remove the flywheel and check again
for irregularities on the crankshaft and flywheel
mating faces and the dowel.
11.Reverse removal procedure. 1 to 6.