check engine LAND ROVER DISCOVERY 1995 Service Manual
[x] Cancel search | Manufacturer: LAND ROVER, Model Year: 1995, Model line: DISCOVERY, Model: LAND ROVER DISCOVERY 1995Pages: 873, PDF Size: 12.89 MB
Page 196 of 873
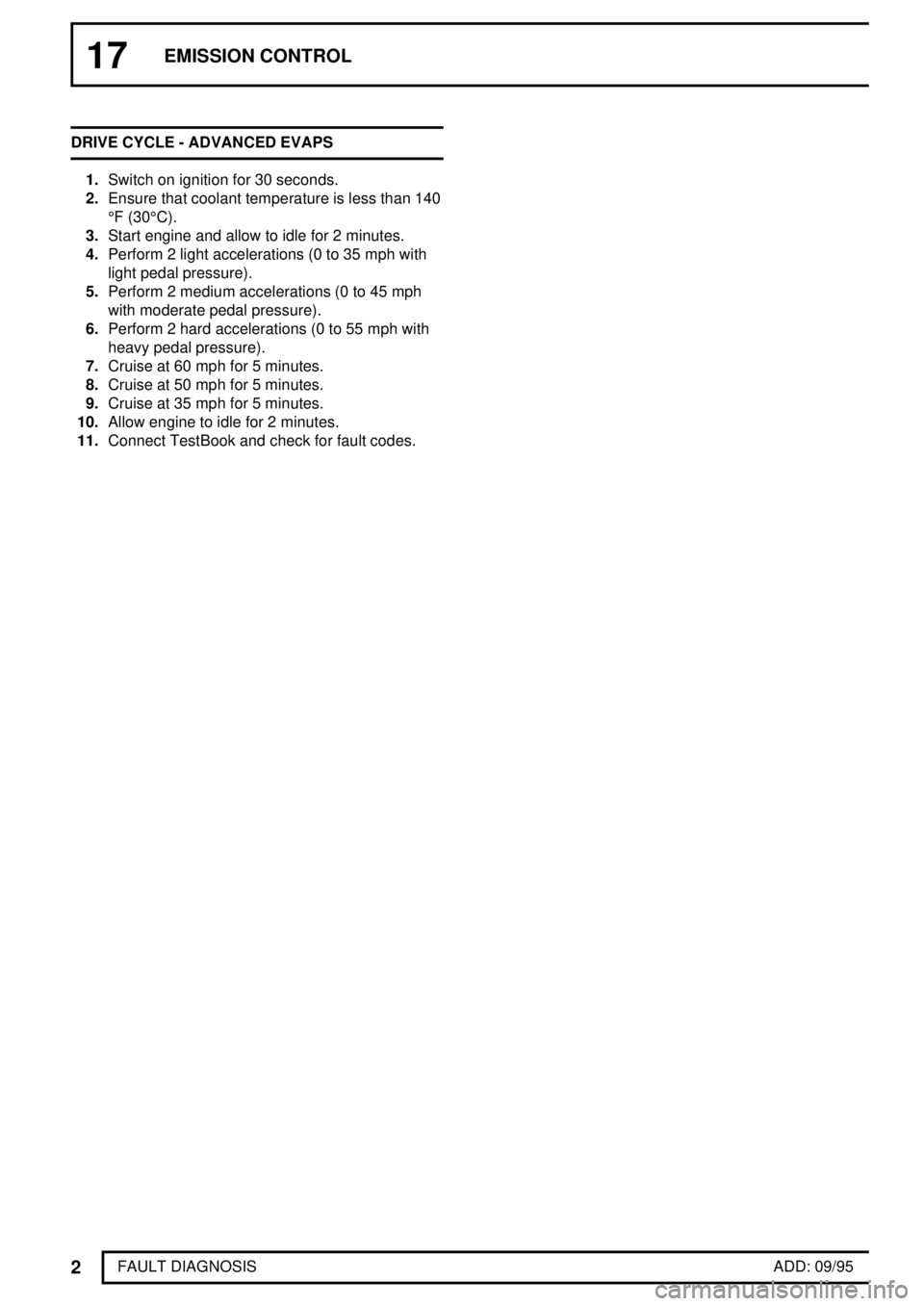
17EMISSION CONTROL
2
FAULT DIAGNOSISADD: 09/95 DRIVE CYCLE - ADVANCED EVAPS
1.Switch on ignition for 30 seconds.
2.Ensure that coolant temperature is less than 140
°F (30°C).
3.Start engine and allow to idle for 2 minutes.
4.Perform 2 light accelerations (0 to 35 mph with
light pedal pressure).
5.Perform 2 medium accelerations (0 to 45 mph
with moderate pedal pressure).
6.Perform 2 hard accelerations (0 to 55 mph with
heavy pedal pressure).
7.Cruise at 60 mph for 5 minutes.
8.Cruise at 50 mph for 5 minutes.
9.Cruise at 35 mph for 5 minutes.
10.Allow engine to idle for 2 minutes.
11.Connect TestBook and check for fault codes.
Page 216 of 873
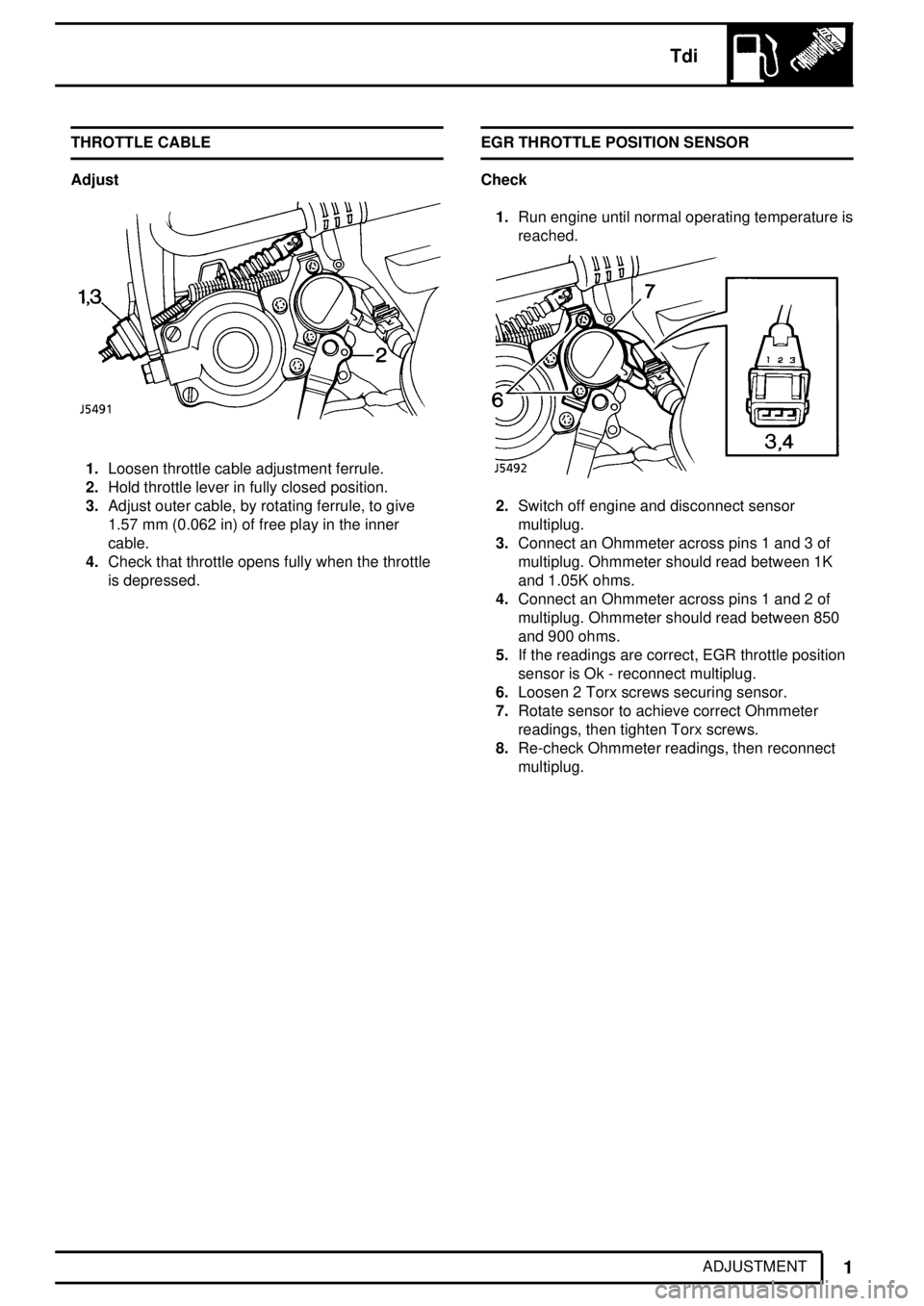
Tdi
1
ADJUSTMENT THROTTLE CABLE
Adjust
1.Loosen throttle cable adjustment ferrule.
2.Hold throttle lever in fully closed position.
3.Adjust outer cable, by rotating ferrule, to give
1.57 mm (0.062 in) of free play in the inner
cable.
4.Check that throttle opens fully when the throttle
is depressed.EGR THROTTLE POSITION SENSOR
Check
1.Run engine until normal operating temperature is
reached.
2.Switch off engine and disconnect sensor
multiplug.
3.Connect an Ohmmeter across pins 1 and 3 of
multiplug. Ohmmeter should read between 1K
and 1.05K ohms.
4.Connect an Ohmmeter across pins 1 and 2 of
multiplug. Ohmmeter should read between 850
and 900 ohms.
5.If the readings are correct, EGR throttle position
sensor is Ok - reconnect multiplug.
6.Loosen 2 Torx screws securing sensor.
7.Rotate sensor to achieve correct Ohmmeter
readings, then tighten Torx screws.
8.Re-check Ohmmeter readings, then reconnect
multiplug.
Page 217 of 873
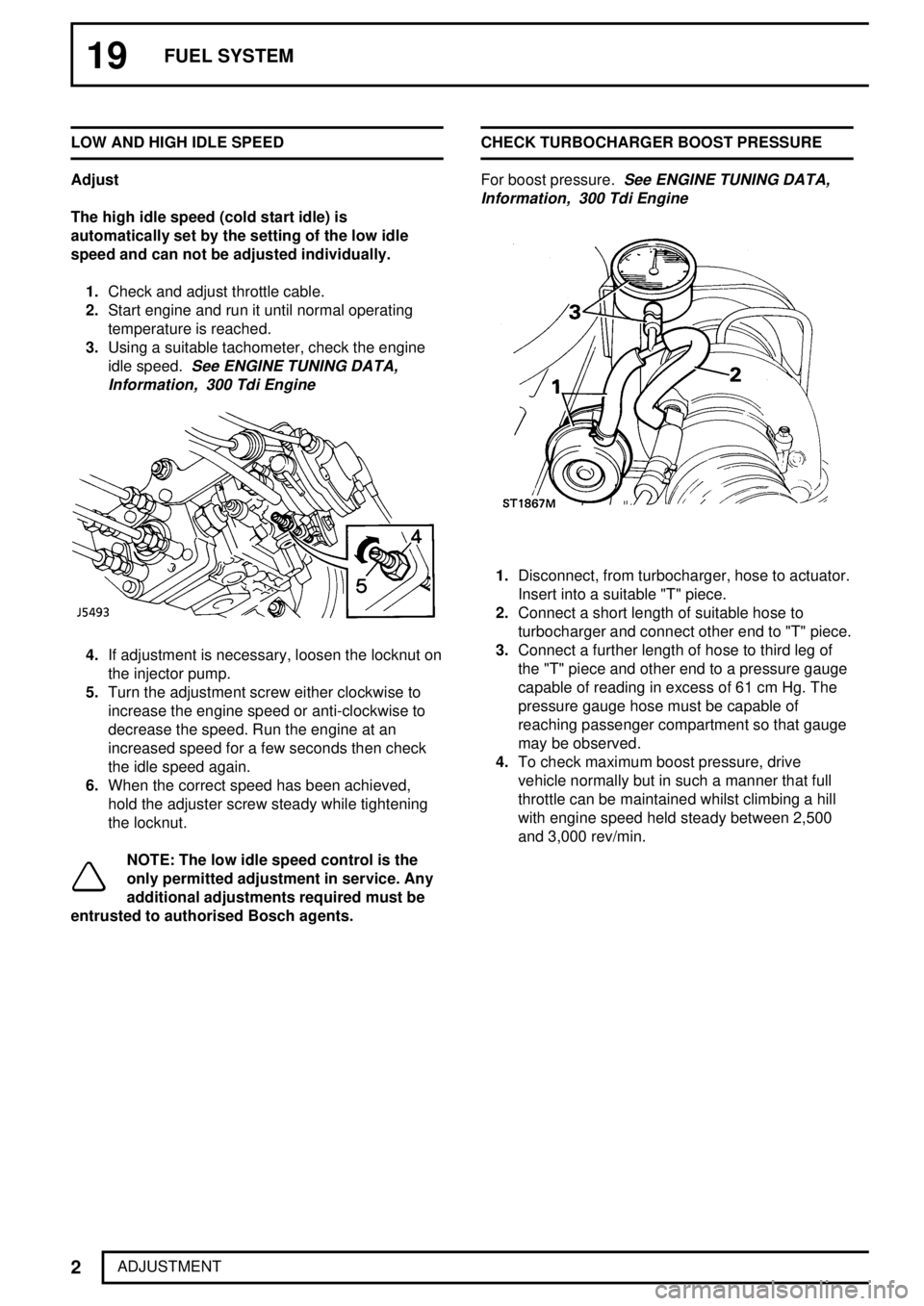
19FUEL SYSTEM
2
ADJUSTMENT LOW AND HIGH IDLE SPEED
Adjust
The high idle speed (cold start idle) is
automatically set by the setting of the low idle
speed and can not be adjusted individually.
1.Check and adjust throttle cable.
2.Start engine and run it until normal operating
temperature is reached.
3.Using a suitable tachometer, check the engine
idle speed.
See ENGINE TUNING DATA,
Information, 300 Tdi Engine
4.If adjustment is necessary, loosen the locknut on
the injector pump.
5.Turn the adjustment screw either clockwise to
increase the engine speed or anti-clockwise to
decrease the speed. Run the engine at an
increased speed for a few seconds then check
the idle speed again.
6.When the correct speed has been achieved,
hold the adjuster screw steady while tightening
the locknut.
NOTE: The low idle speed control is the
only permitted adjustment in service. Any
additional adjustments required must be
entrusted to authorised Bosch agents.CHECK TURBOCHARGER BOOST PRESSURE
For boost pressure.
See ENGINE TUNING DATA,
Information, 300 Tdi Engine
1.Disconnect, from turbocharger, hose to actuator.
Insert into a suitable "T" piece.
2.Connect a short length of suitable hose to
turbocharger and connect other end to "T" piece.
3.Connect a further length of hose to third leg of
the "T" piece and other end to a pressure gauge
capable of reading in excess of 61 cm Hg. The
pressure gauge hose must be capable of
reaching passenger compartment so that gauge
may be observed.
4.To check maximum boost pressure, drive
vehicle normally but in such a manner that full
throttle can be maintained whilst climbing a hill
with engine speed held steady between 2,500
and 3,000 rev/min.
Page 220 of 873
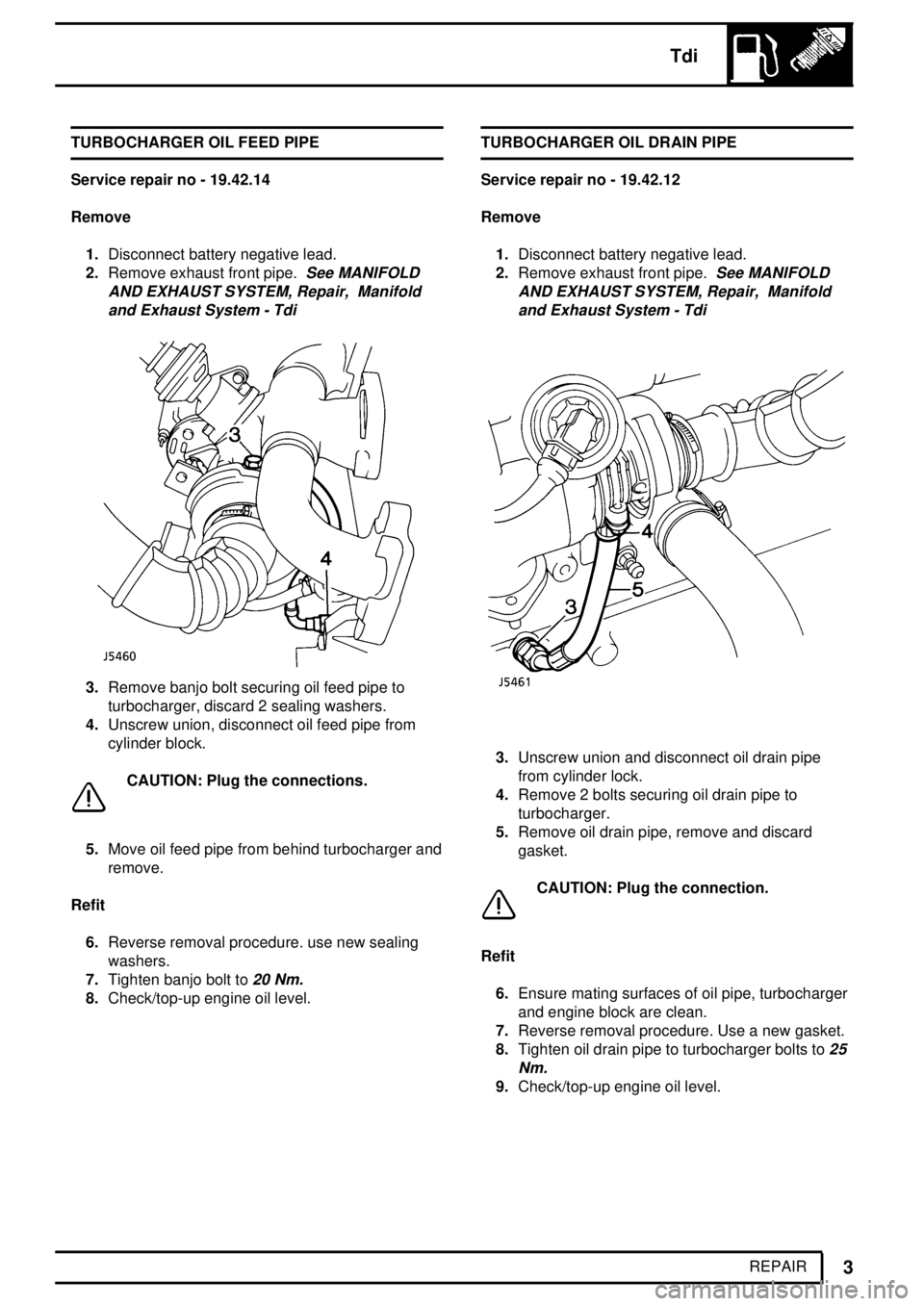
Tdi
3
REPAIR TURBOCHARGER OIL FEED PIPE
Service repair no - 19.42.14
Remove
1.Disconnect battery negative lead.
2.Remove exhaust front pipe.
See MANIFOLD
AND EXHAUST SYSTEM, Repair, Manifold
and Exhaust System - Tdi
3.Remove banjo bolt securing oil feed pipe to
turbocharger, discard 2 sealing washers.
4.Unscrew union, disconnect oil feed pipe from
cylinder block.
CAUTION: Plug the connections.
5.Move oil feed pipe from behind turbocharger and
remove.
Refit
6.Reverse removal procedure. use new sealing
washers.
7.Tighten banjo bolt to
20 Nm.
8.Check/top-up engine oil level.TURBOCHARGER OIL DRAIN PIPE
Service repair no - 19.42.12
Remove
1.Disconnect battery negative lead.
2.Remove exhaust front pipe.
See MANIFOLD
AND EXHAUST SYSTEM, Repair, Manifold
and Exhaust System - Tdi
3.Unscrew union and disconnect oil drain pipe
from cylinder lock.
4.Remove 2 bolts securing oil drain pipe to
turbocharger.
5.Remove oil drain pipe, remove and discard
gasket.
CAUTION: Plug the connection.
Refit
6.Ensure mating surfaces of oil pipe, turbocharger
and engine block are clean.
7.Reverse removal procedure. Use a new gasket.
8.Tighten oil drain pipe to turbocharger bolts to
25
Nm.
9.Check/top-up engine oil level.
Page 221 of 873
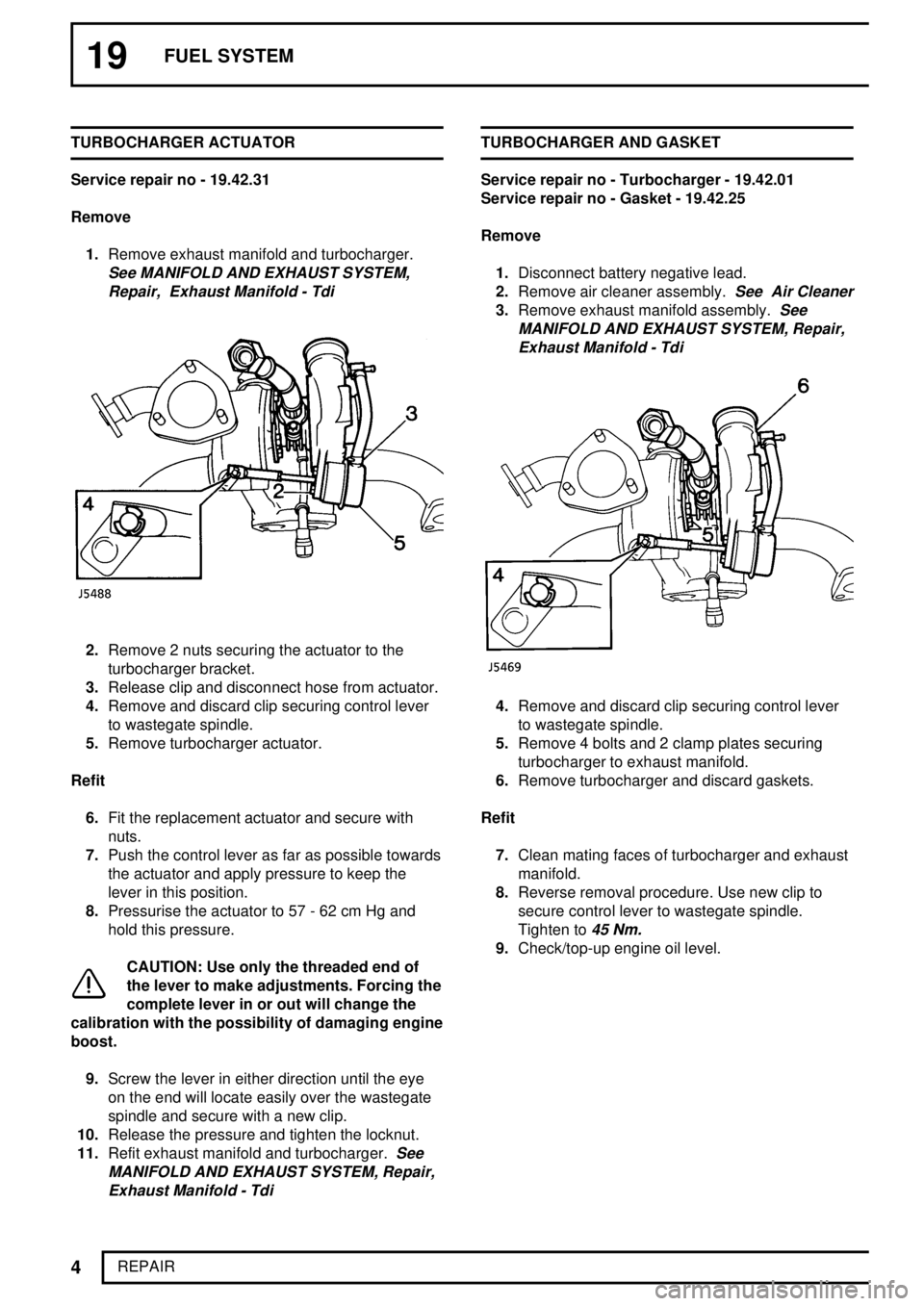
19FUEL SYSTEM
4
REPAIR TURBOCHARGER ACTUATOR
Service repair no - 19.42.31
Remove
1.Remove exhaust manifold and turbocharger.
See MANIFOLD AND EXHAUST SYSTEM,
Repair, Exhaust Manifold - Tdi
2.Remove 2 nuts securing the actuator to the
turbocharger bracket.
3.Release clip and disconnect hose from actuator.
4.Remove and discard clip securing control lever
to wastegate spindle.
5.Remove turbocharger actuator.
Refit
6.Fit the replacement actuator and secure with
nuts.
7.Push the control lever as far as possible towards
the actuator and apply pressure to keep the
lever in this position.
8.Pressurise the actuator to 57 - 62 cm Hg and
hold this pressure.
CAUTION: Use only the threaded end of
the lever to make adjustments. Forcing the
complete lever in or out will change the
calibration with the possibility of damaging engine
boost.
9.Screw the lever in either direction until the eye
on the end will locate easily over the wastegate
spindle and secure with a new clip.
10.Release the pressure and tighten the locknut.
11.Refit exhaust manifold and turbocharger.
See
MANIFOLD AND EXHAUST SYSTEM, Repair,
Exhaust Manifold - Tdi
TURBOCHARGER AND GASKET
Service repair no - Turbocharger - 19.42.01
Service repair no - Gasket - 19.42.25
Remove
1.Disconnect battery negative lead.
2.Remove air cleaner assembly.
See Air Cleaner
3.Remove exhaust manifold assembly.See
MANIFOLD AND EXHAUST SYSTEM, Repair,
Exhaust Manifold - Tdi
4.Remove and discard clip securing control lever
to wastegate spindle.
5.Remove 4 bolts and 2 clamp plates securing
turbocharger to exhaust manifold.
6.Remove turbocharger and discard gaskets.
Refit
7.Clean mating faces of turbocharger and exhaust
manifold.
8.Reverse removal procedure. Use new clip to
secure control lever to wastegate spindle.
Tighten to
45 Nm.
9.Check/top-up engine oil level.
Page 235 of 873
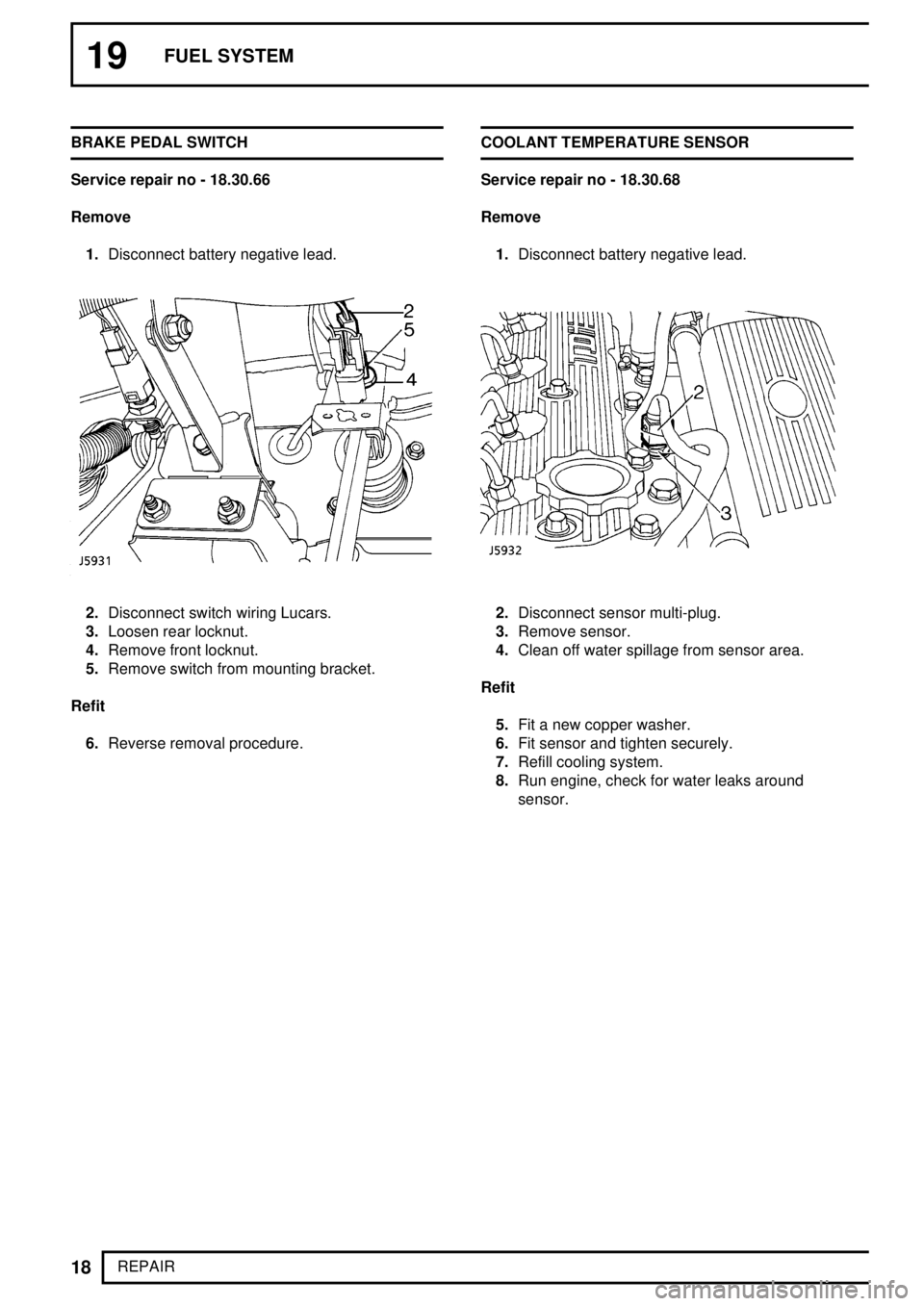
19FUEL SYSTEM
18
REPAIR BRAKE PEDAL SWITCH
Service repair no - 18.30.66
Remove
1.Disconnect battery negative lead.
2.Disconnect switch wiring Lucars.
3.Loosen rear locknut.
4.Remove front locknut.
5.Remove switch from mounting bracket.
Refit
6.Reverse removal procedure.COOLANT TEMPERATURE SENSOR
Service repair no - 18.30.68
Remove
1.Disconnect battery negative lead.2.Disconnect sensor multi-plug.
3.Remove sensor.
4.Clean off water spillage from sensor area.
Refit
5.Fit a new copper washer.
6.Fit sensor and tighten securely.
7.Refill cooling system.
8.Run engine, check for water leaks around
sensor.
Page 239 of 873
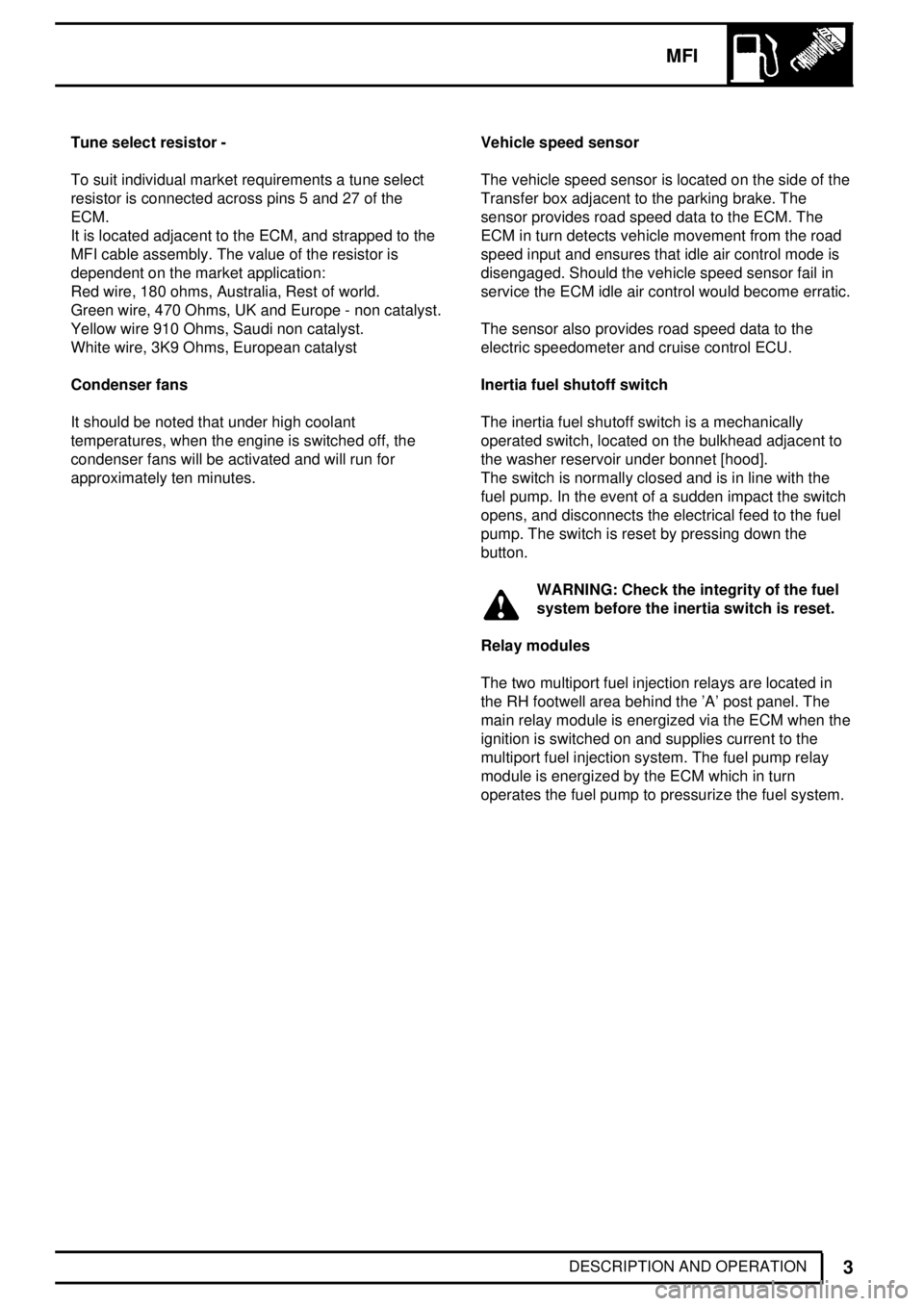
MFI
3
DESCRIPTION AND OPERATION Tune select resistor -
To suit individual market requirements a tune select
resistor is connected across pins 5 and 27 of the
ECM.
It is located adjacent to the ECM, and strapped to the
MFI cable assembly. The value of the resistor is
dependent on the market application:
Red wire, 180 ohms, Australia, Rest of world.
Green wire, 470 Ohms, UK and Europe - non catalyst.
Yellow wire 910 Ohms, Saudi non catalyst.
White wire, 3K9 Ohms, European catalyst
Condenser fans
It should be noted that under high coolant
temperatures, when the engine is switched off, the
condenser fans will be activated and will run for
approximately ten minutes.Vehicle speed sensor
The vehicle speed sensor is located on the side of the
Transfer box adjacent to the parking brake. The
sensor provides road speed data to the ECM. The
ECM in turn detects vehicle movement from the road
speed input and ensures that idle air control mode is
disengaged. Should the vehicle speed sensor fail in
service the ECM idle air control would become erratic.
The sensor also provides road speed data to the
electric speedometer and cruise control ECU.
Inertia fuel shutoff switch
The inertia fuel shutoff switch is a mechanically
operated switch, located on the bulkhead adjacent to
the washer reservoir under bonnet [hood].
The switch is normally closed and is in line with the
fuel pump. In the event of a sudden impact the switch
opens, and disconnects the electrical feed to the fuel
pump. The switch is reset by pressing down the
button.
WARNING: Check the integrity of the fuel
system before the inertia switch is reset.
Relay modules
The two multiport fuel injection relays are located in
the RH footwell area behind the 'A' post panel. The
main relay module is energized via the ECM when the
ignition is switched on and supplies current to the
multiport fuel injection system. The fuel pump relay
module is energized by the ECM which in turn
operates the fuel pump to pressurize the fuel system.
Page 243 of 873
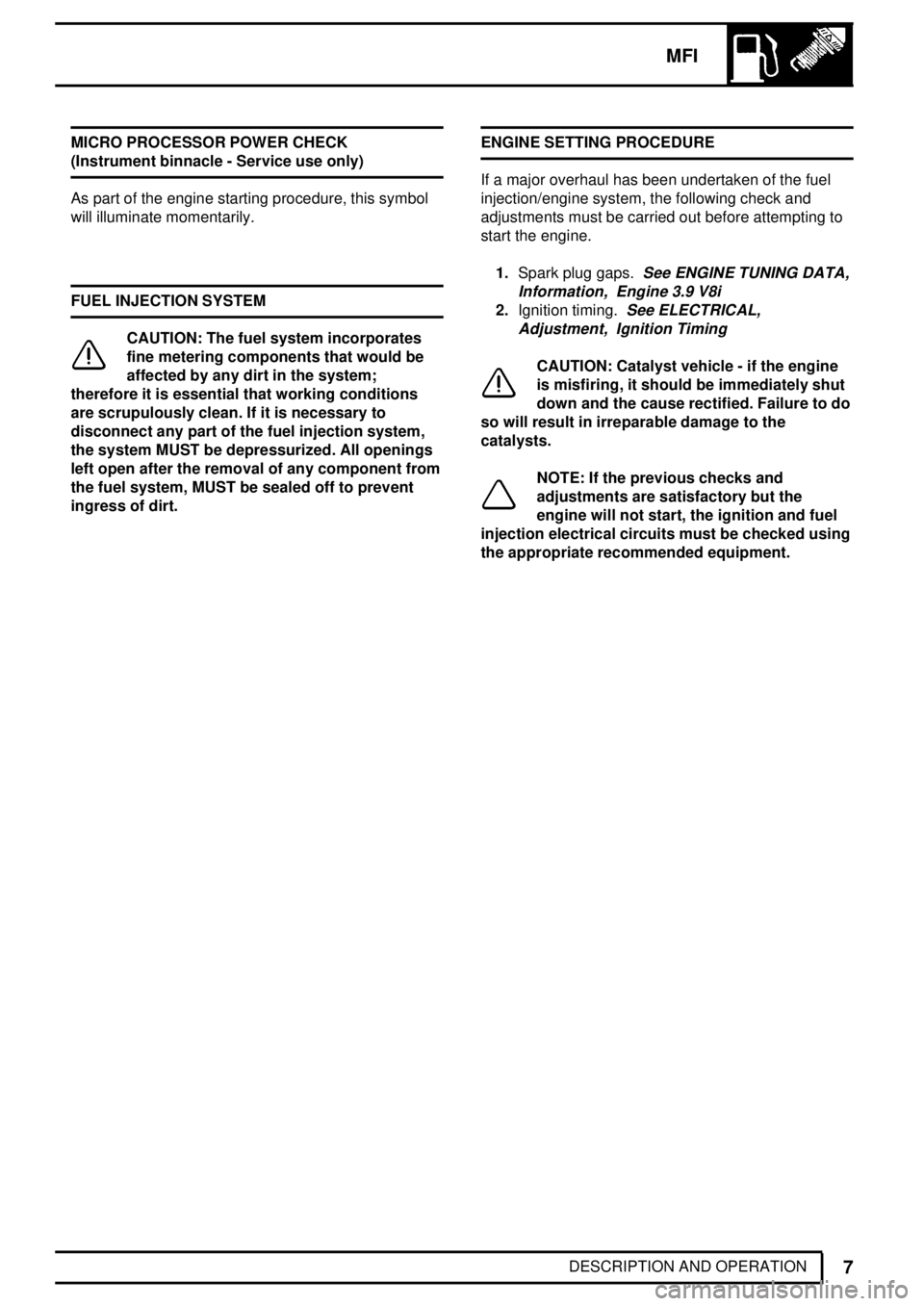
MFI
7
DESCRIPTION AND OPERATION MICRO PROCESSOR POWER CHECK
(Instrument binnacle - Service use only)
As part of the engine starting procedure, this symbol
will illuminate momentarily.
FUEL INJECTION SYSTEM
CAUTION: The fuel system incorporates
fine metering components that would be
affected by any dirt in the system;
therefore it is essential that working conditions
are scrupulously clean. If it is necessary to
disconnect any part of the fuel injection system,
the system MUST be depressurized. All openings
left open after the removal of any component from
the fuel system, MUST be sealed off to prevent
ingress of dirt.ENGINE SETTING PROCEDURE
If a major overhaul has been undertaken of the fuel
injection/engine system, the following check and
adjustments must be carried out before attempting to
start the engine.
1.Spark plug gaps.
See ENGINE TUNING DATA,
Information, Engine 3.9 V8i
2.Ignition timing.See ELECTRICAL,
Adjustment, Ignition Timing
CAUTION: Catalyst vehicle - if the engine
is misfiring, it should be immediately shut
down and the cause rectified. Failure to do
so will result in irreparable damage to the
catalysts.
NOTE: If the previous checks and
adjustments are satisfactory but the
engine will not start, the ignition and fuel
injection electrical circuits must be checked using
the appropriate recommended equipment.
Page 244 of 873
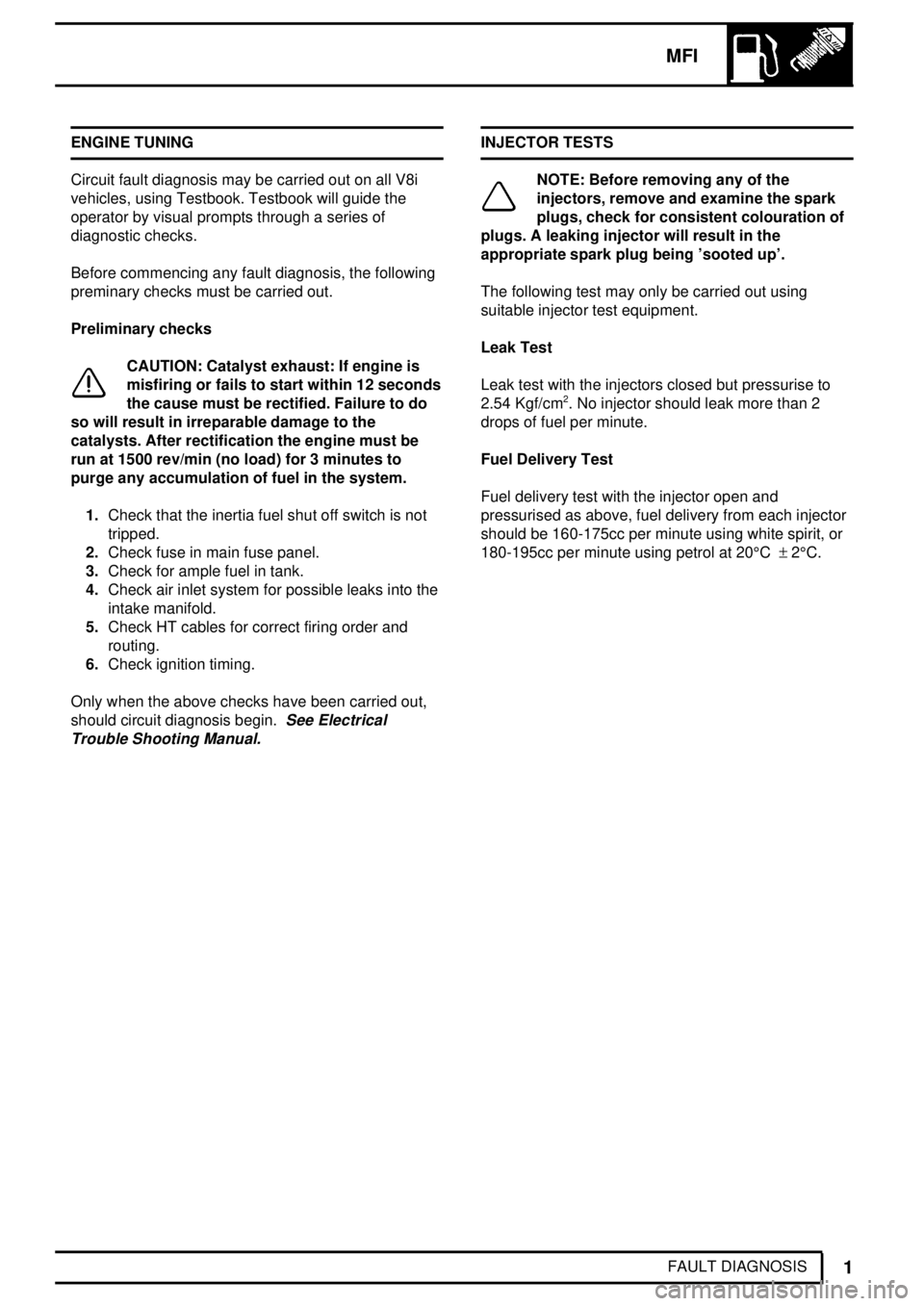
MFI
1
FAULT DIAGNOSIS ENGINE TUNING
Circuit fault diagnosis may be carried out on all V8i
vehicles, using Testbook. Testbook will guide the
operator by visual prompts through a series of
diagnostic checks.
Before commencing any fault diagnosis, the following
preminary checks must be carried out.
Preliminary checks
CAUTION: Catalyst exhaust: If engine is
misfiring or fails to start within 12 seconds
the cause must be rectified. Failure to do
so will result in irreparable damage to the
catalysts. After rectification the engine must be
run at 1500 rev/min (no load) for 3 minutes to
purge any accumulation of fuel in the system.
1.Check that the inertia fuel shut off switch is not
tripped.
2.Check fuse in main fuse panel.
3.Check for ample fuel in tank.
4.Check air inlet system for possible leaks into the
intake manifold.
5.Check HT cables for correct firing order and
routing.
6.Check ignition timing.
Only when the above checks have been carried out,
should circuit diagnosis begin.
See Electrical
Trouble Shooting Manual.
INJECTOR TESTS
NOTE: Before removing any of the
injectors, remove and examine the spark
plugs, check for consistent colouration of
plugs. A leaking injector will result in the
appropriate spark plug being 'sooted up'.
The following test may only be carried out using
suitable injector test equipment.
Leak Test
Leak test with the injectors closed but pressurise to
2.54 Kgf/cm
2. No injector should leak more than 2
drops of fuel per minute.
Fuel Delivery Test
Fuel delivery test with the injector open and
pressurised as above, fuel delivery from each injector
should be 160-175cc per minute using white spirit, or
180-195cc per minute using petrol at 20°C±2°C.
Page 245 of 873
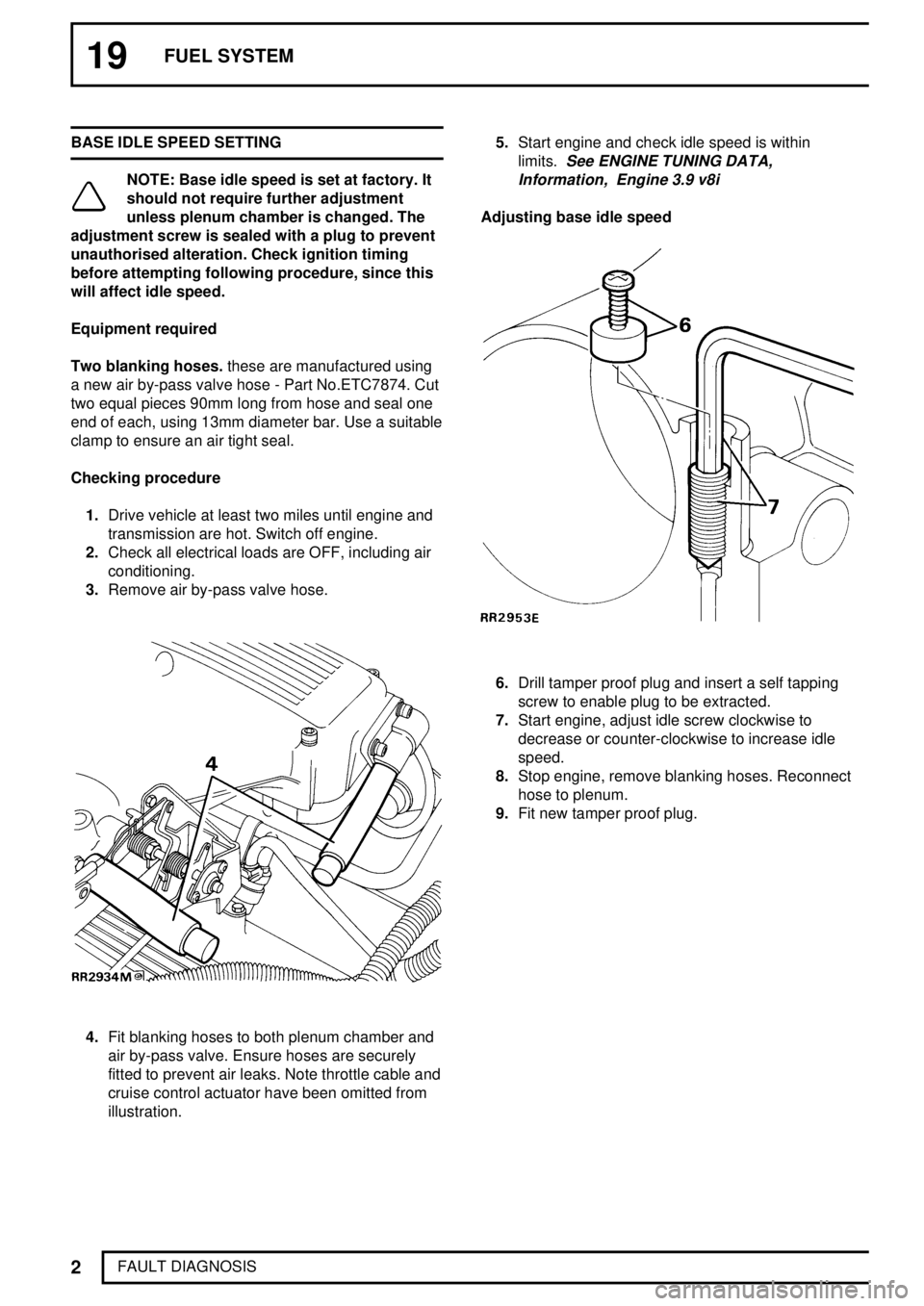
19FUEL SYSTEM
2
FAULT DIAGNOSIS BASE IDLE SPEED SETTING
NOTE: Base idle speed is set at factory. It
should not require further adjustment
unless plenum chamber is changed. The
adjustment screw is sealed with a plug to prevent
unauthorised alteration. Check ignition timing
before attempting following procedure, since this
will affect idle speed.
Equipment required
Two blanking hoses.these are manufactured using
a new air by-pass valve hose - Part No.ETC7874. Cut
two equal pieces 90mm long from hose and seal one
end of each, using 13mm diameter bar. Use a suitable
clamp to ensure an air tight seal.
Checking procedure
1.Drive vehicle at least two miles until engine and
transmission are hot. Switch off engine.
2.Check all electrical loads are OFF, including air
conditioning.
3.Remove air by-pass valve hose.
4.Fit blanking hoses to both plenum chamber and
air by-pass valve. Ensure hoses are securely
fitted to prevent air leaks. Note throttle cable and
cruise control actuator have been omitted from
illustration.5.Start engine and check idle speed is within
limits.
See ENGINE TUNING DATA,
Information, Engine 3.9 v8i
Adjusting base idle speed
6.Drill tamper proof plug and insert a self tapping
screw to enable plug to be extracted.
7.Start engine, adjust idle screw clockwise to
decrease or counter-clockwise to increase idle
speed.
8.Stop engine, remove blanking hoses. Reconnect
hose to plenum.
9.Fit new tamper proof plug.