LAND ROVER DISCOVERY 1995 Workshop Manual
Manufacturer: LAND ROVER, Model Year: 1995, Model line: DISCOVERY, Model: LAND ROVER DISCOVERY 1995Pages: 873, PDF Size: 12.89 MB
Page 491 of 873
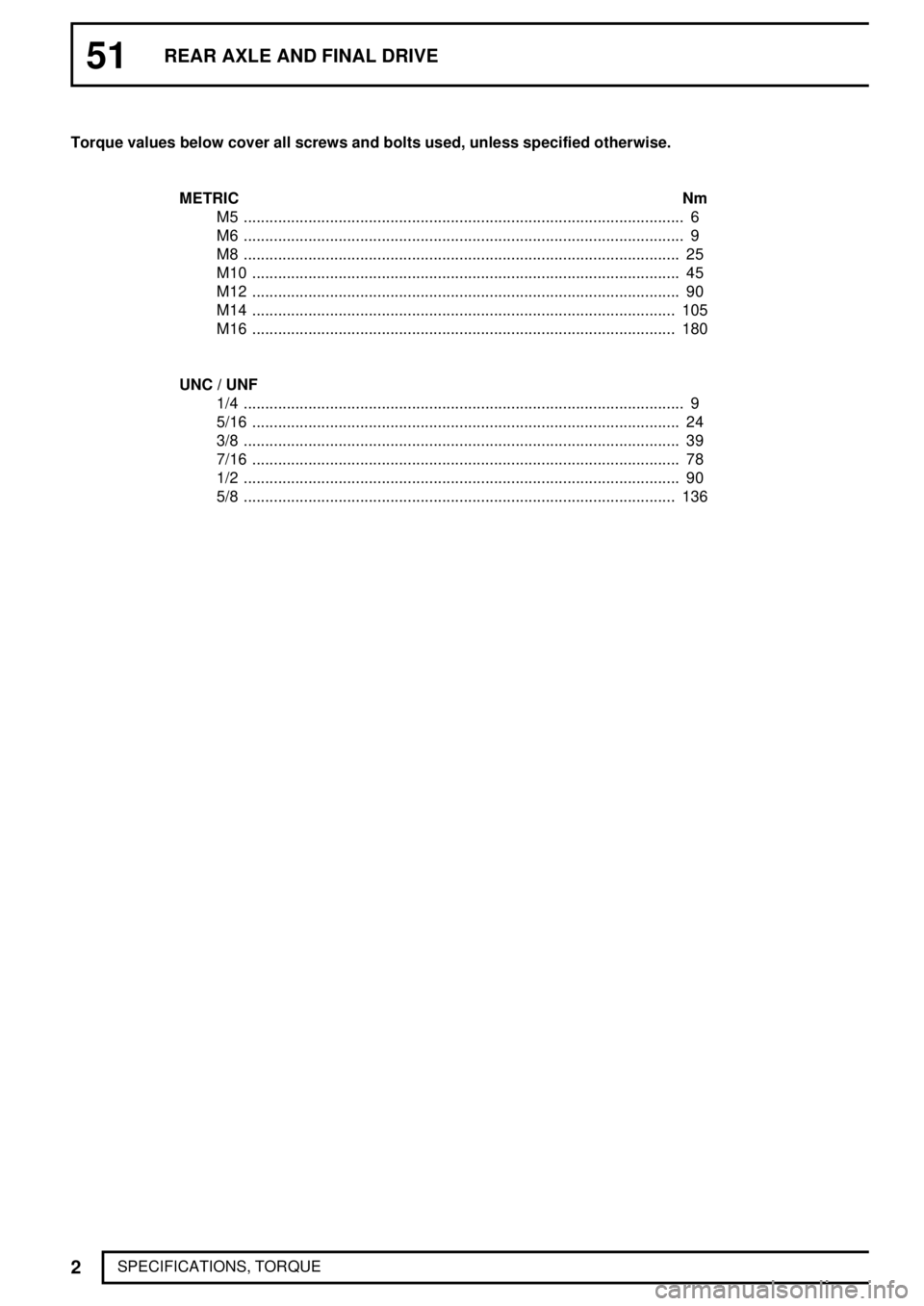
51REAR AXLE AND FINAL DRIVE
2
SPECIFICATIONS, TORQUE Torque values below cover all screws and bolts used, unless specified otherwise.
METRIC Nm
M5 6......................................................................................................
M6 9......................................................................................................
M8 25.....................................................................................................
M10 45...................................................................................................
M12 90...................................................................................................
M14 105..................................................................................................
M16 180..................................................................................................
UNC / UNF
1/4 9......................................................................................................
5/16 24...................................................................................................
3/8 39.....................................................................................................
7/16 78...................................................................................................
1/2 90.....................................................................................................
5/8 136....................................................................................................
Page 492 of 873
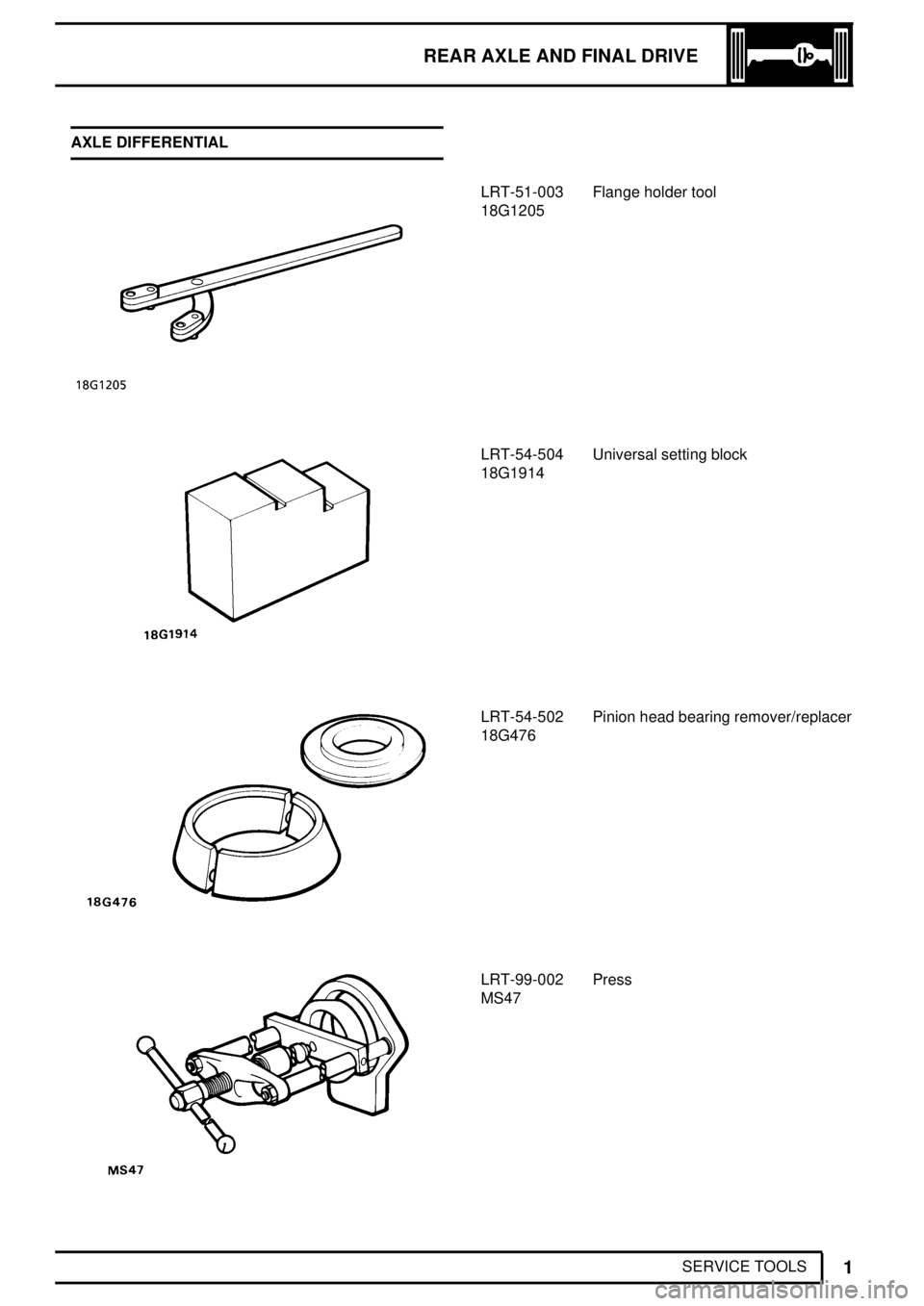
REAR AXLE AND FINAL DRIVE
1
SERVICE TOOLS AXLE DIFFERENTIAL
LRT-51-003 Flange holder tool
18G1205
LRT-54-504 Universal setting block
18G1914
LRT-54-502 Pinion head bearing remover/replacer
18G476
LRT-99-002 Press
MS47
Page 493 of 873
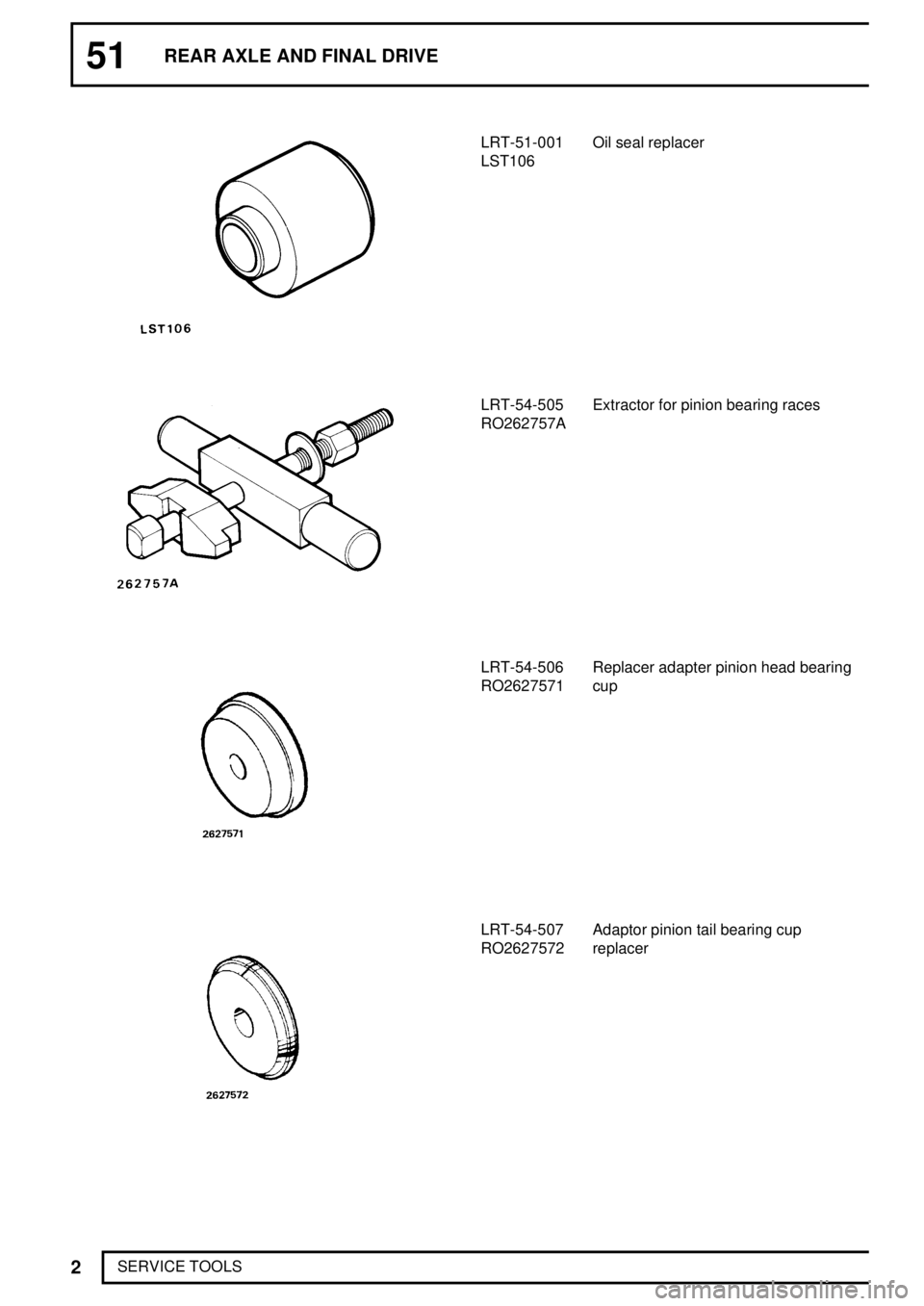
51REAR AXLE AND FINAL DRIVE
2
SERVICE TOOLS
LRT-51-001 Oil seal replacer
LST106
LRT-54-505 Extractor for pinion bearing races
RO262757A
LRT-54-506 Replacer adapter pinion head bearing
RO2627571 cup
LRT-54-507 Adaptor pinion tail bearing cup
RO2627572 replacer
Page 494 of 873
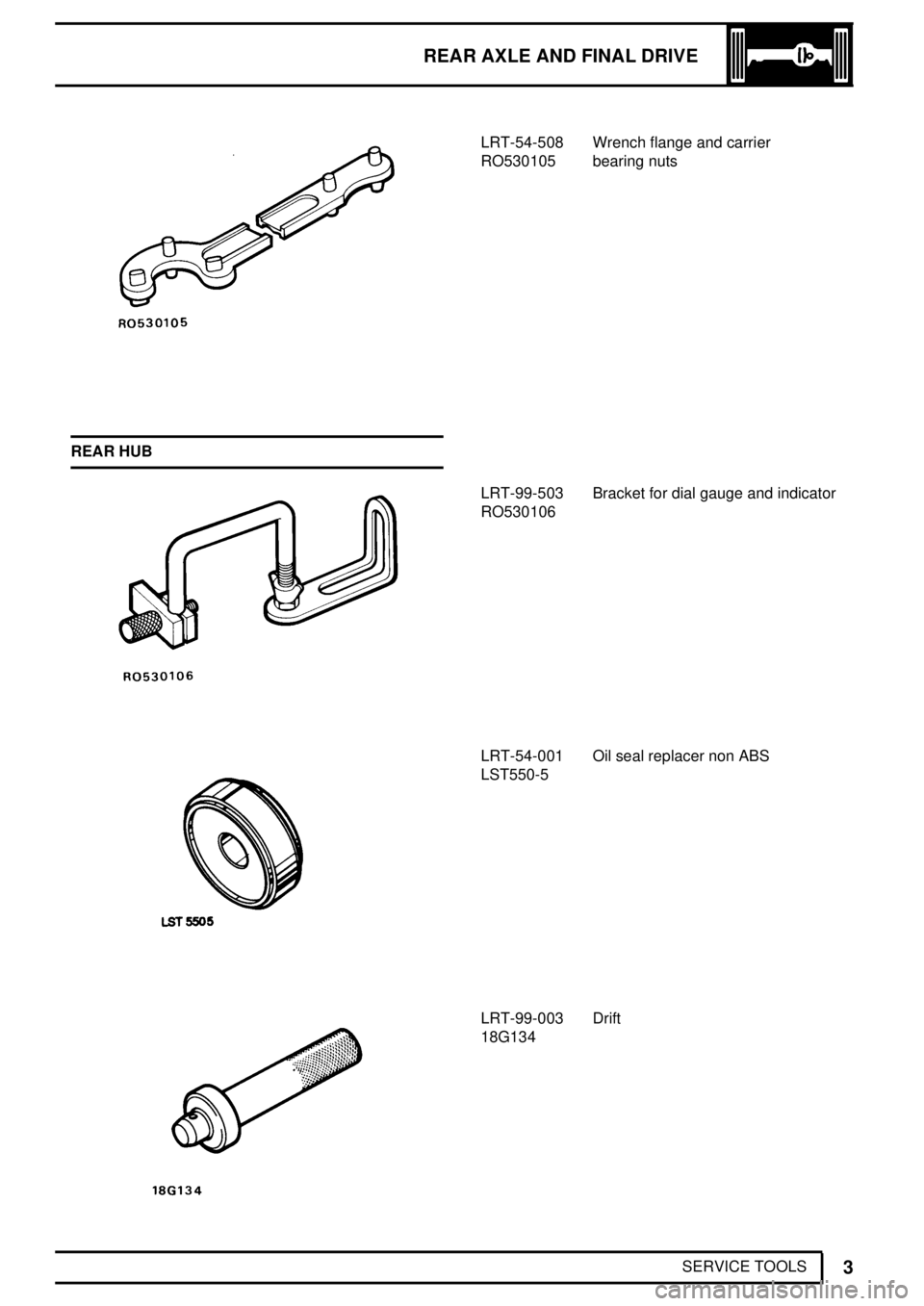
REAR AXLE AND FINAL DRIVE
3
SERVICE TOOLS
LRT-54-508 Wrench flange and carrier
RO530105 bearing nuts
REAR HUB
LRT-99-503 Bracket for dial gauge and indicator
RO530106
LRT-54-001 Oil seal replacer non ABS
LST550-5
LRT-99-003 Drift
18G134
Page 495 of 873
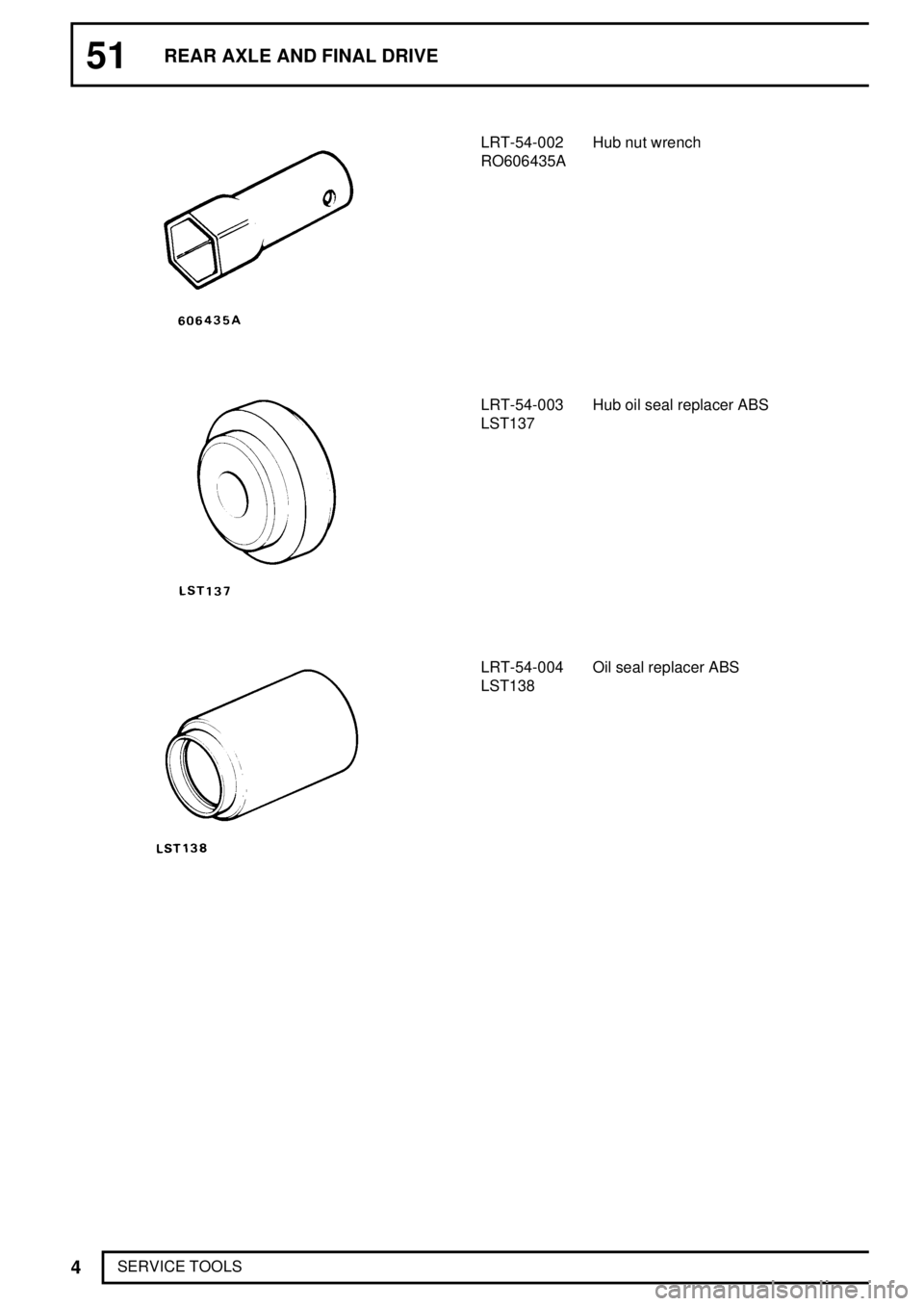
51REAR AXLE AND FINAL DRIVE
4
SERVICE TOOLS
LRT-54-002 Hub nut wrench
RO606435A
LRT-54-003 Hub oil seal replacer ABS
LST137
LRT-54-004 Oil seal replacer ABS
LST138
Page 496 of 873
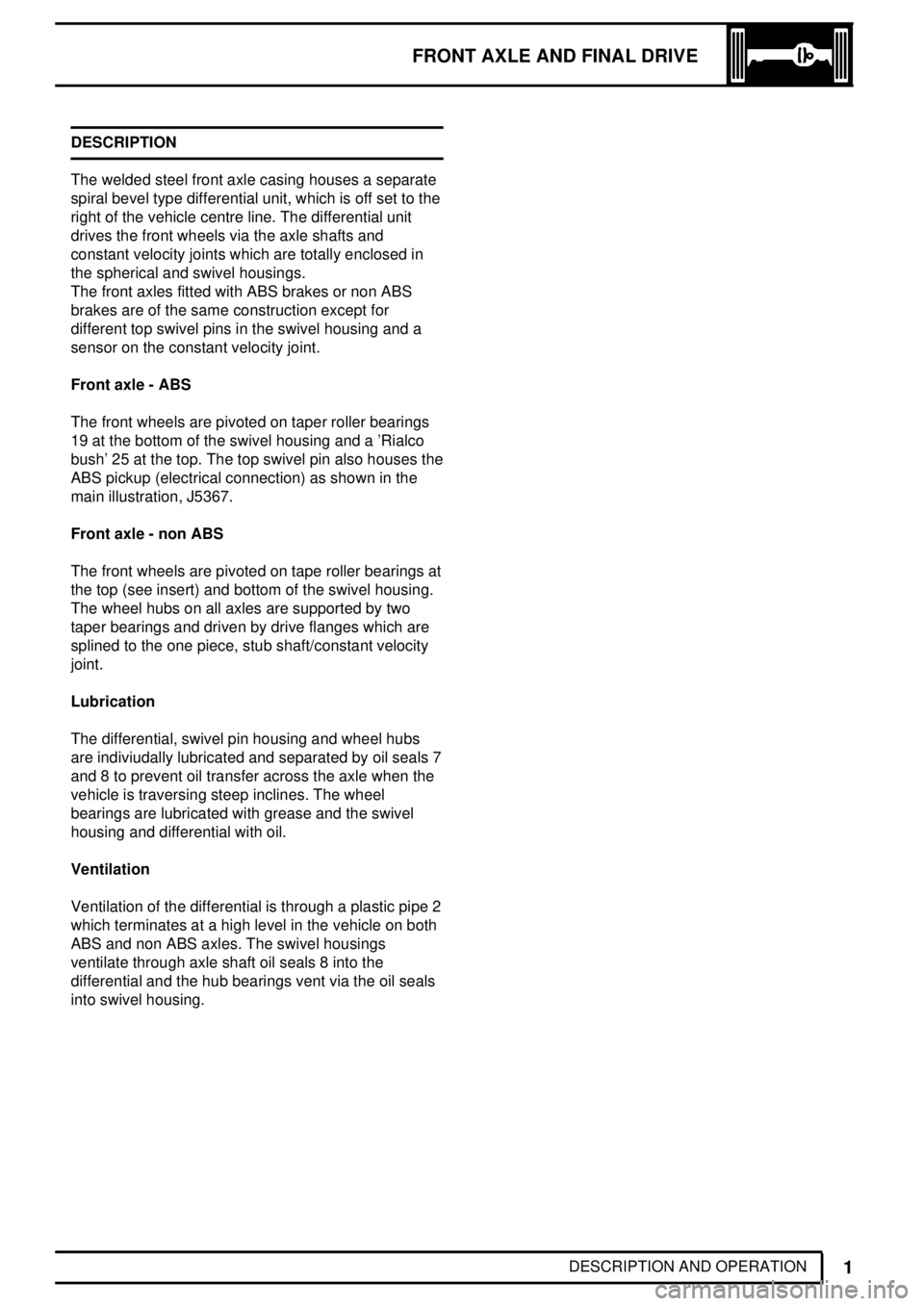
FRONT AXLE AND FINAL DRIVE
1
DESCRIPTION AND OPERATION DESCRIPTION
The welded steel front axle casing houses a separate
spiral bevel type differential unit, which is off set to the
right of the vehicle centre line. The differential unit
drives the front wheels via the axle shafts and
constant velocity joints which are totally enclosed in
the spherical and swivel housings.
The front axles fitted with ABS brakes or non ABS
brakes are of the same construction except for
different top swivel pins in the swivel housing and a
sensor on the constant velocity joint.
Front axle - ABS
The front wheels are pivoted on taper roller bearings
19 at the bottom of the swivel housing and a 'Rialco
bush' 25 at the top. The top swivel pin also houses the
ABS pickup (electrical connection) as shown in the
main illustration, J5367.
Front axle - non ABS
The front wheels are pivoted on tape roller bearings at
the top (see insert) and bottom of the swivel housing.
The wheel hubs on all axles are supported by two
taper bearings and driven by drive flanges which are
splined to the one piece, stub shaft/constant velocity
joint.
Lubrication
The differential, swivel pin housing and wheel hubs
are indiviudally lubricated and separated by oil seals 7
and 8 to prevent oil transfer across the axle when the
vehicle is traversing steep inclines. The wheel
bearings are lubricated with grease and the swivel
housing and differential with oil.
Ventilation
Ventilation of the differential is through a plastic pipe 2
which terminates at a high level in the vehicle on both
ABS and non ABS axles. The swivel housings
ventilate through axle shaft oil seals 8 into the
differential and the hub bearings vent via the oil seals
into swivel housing.
Page 497 of 873
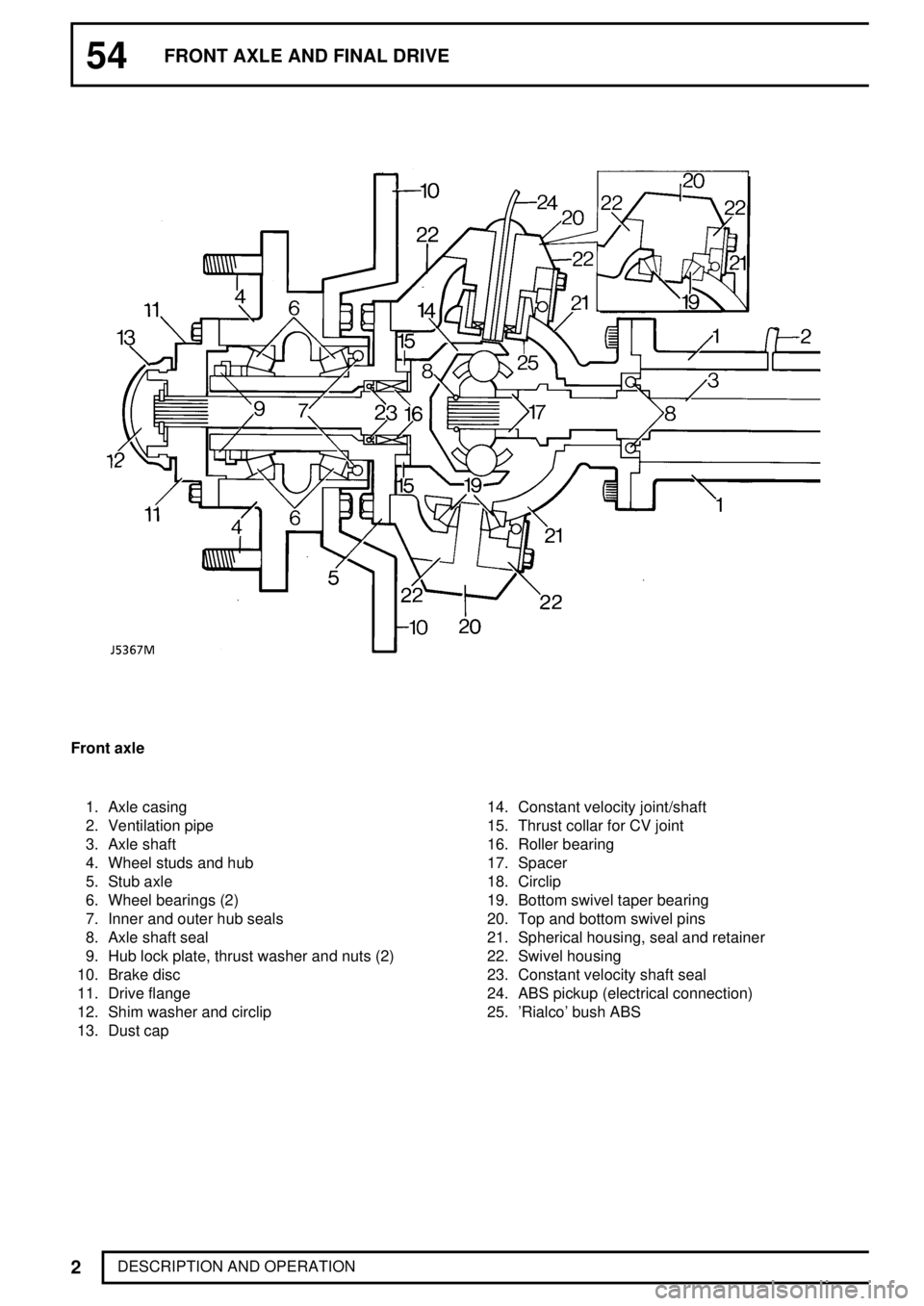
54FRONT AXLE AND FINAL DRIVE
2
DESCRIPTION AND OPERATION
Front axle
1. Axle casing
2. Ventilation pipe
3. Axle shaft
4. Wheel studs and hub
5. Stub axle
6. Wheel bearings (2)
7. Inner and outer hub seals
8. Axle shaft seal
9. Hub lock plate, thrust washer and nuts (2)
10. Brake disc
11. Drive flange
12. Shim washer and circlip
13. Dust cap14. Constant velocity joint/shaft
15. Thrust collar for CV joint
16. Roller bearing
17. Spacer
18. Circlip
19. Bottom swivel taper bearing
20. Top and bottom swivel pins
21. Spherical housing, seal and retainer
22. Swivel housing
23. Constant velocity shaft seal
24. ABS pickup (electrical connection)
25. 'Rialco' bush ABS
Page 498 of 873
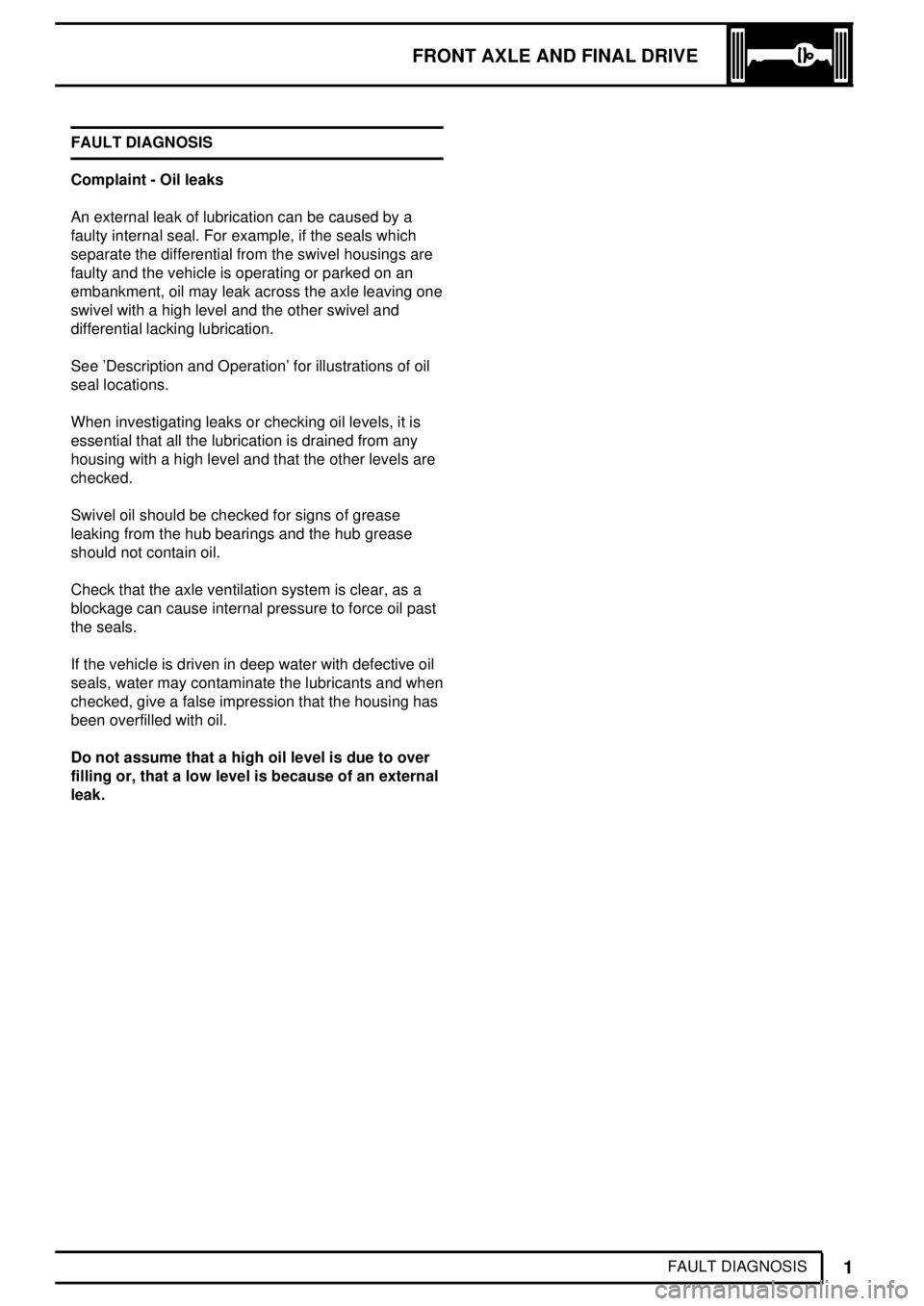
FRONT AXLE AND FINAL DRIVE
1
FAULT DIAGNOSIS FAULT DIAGNOSIS
Complaint - Oil leaks
An external leak of lubrication can be caused by a
faulty internal seal. For example, if the seals which
separate the differential from the swivel housings are
faulty and the vehicle is operating or parked on an
embankment, oil may leak across the axle leaving one
swivel with a high level and the other swivel and
differential lacking lubrication.
See 'Description and Operation' for illustrations of oil
seal locations.
When investigating leaks or checking oil levels, it is
essential that all the lubrication is drained from any
housing with a high level and that the other levels are
checked.
Swivel oil should be checked for signs of grease
leaking from the hub bearings and the hub grease
should not contain oil.
Check that the axle ventilation system is clear, as a
blockage can cause internal pressure to force oil past
the seals.
If the vehicle is driven in deep water with defective oil
seals, water may contaminate the lubricants and when
checked, give a false impression that the housing has
been overfilled with oil.
Do not assume that a high oil level is due to over
filling or, that a low level is because of an external
leak.
Page 499 of 873
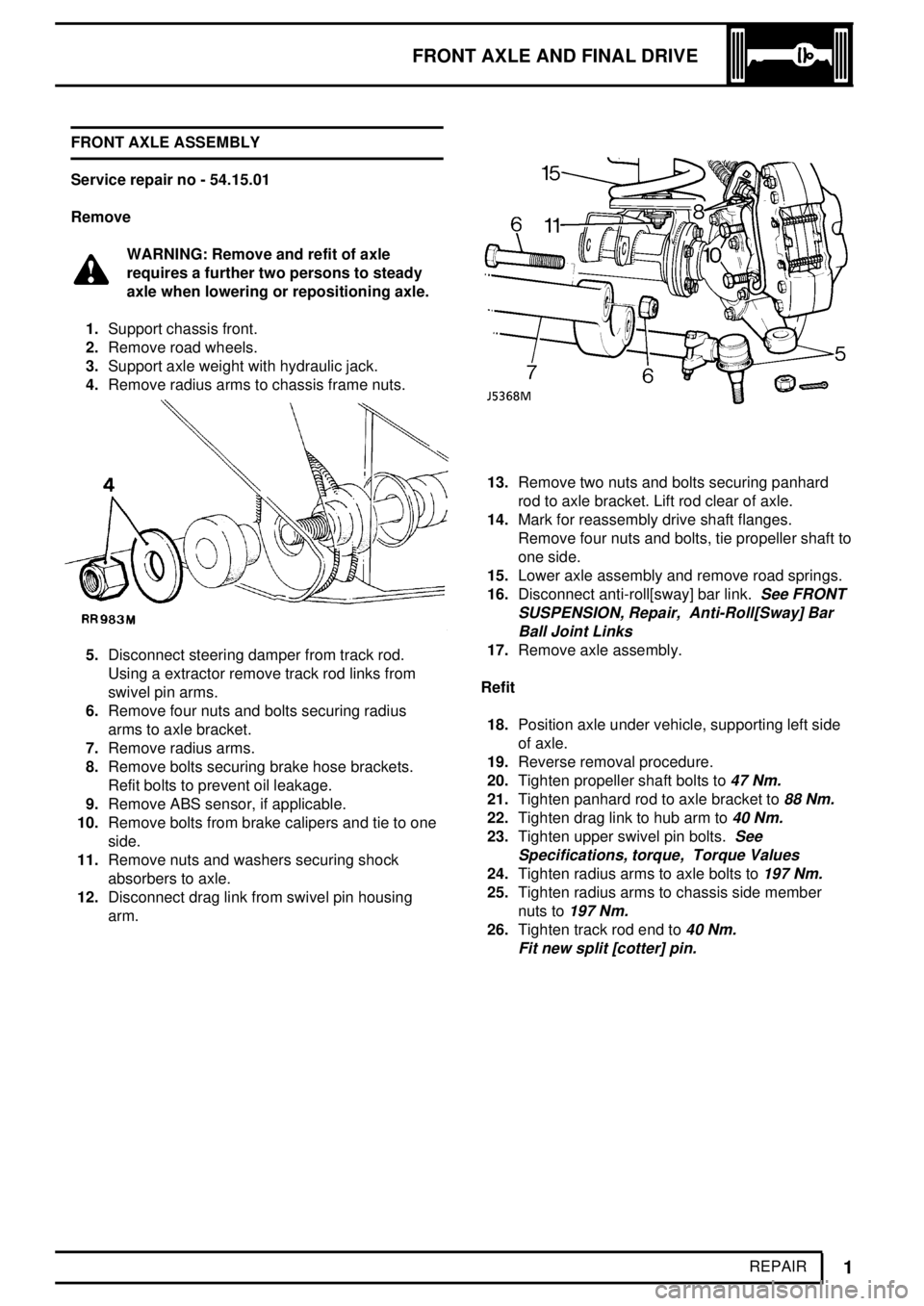
FRONT AXLE AND FINAL DRIVE
1
REPAIR FRONT AXLE ASSEMBLY
Service repair no - 54.15.01
Remove
WARNING: Remove and refit of axle
requires a further two persons to steady
axle when lowering or repositioning axle.
1.Support chassis front.
2.Remove road wheels.
3.Support axle weight with hydraulic jack.
4.Remove radius arms to chassis frame nuts.
5.Disconnect steering damper from track rod.
Using a extractor remove track rod links from
swivel pin arms.
6.Remove four nuts and bolts securing radius
arms to axle bracket.
7.Remove radius arms.
8.Remove bolts securing brake hose brackets.
Refit bolts to prevent oil leakage.
9.Remove ABS sensor, if applicable.
10.Remove bolts from brake calipers and tie to one
side.
11.Remove nuts and washers securing shock
absorbers to axle.
12.Disconnect drag link from swivel pin housing
arm.
13.Remove two nuts and bolts securing panhard
rod to axle bracket. Lift rod clear of axle.
14.Mark for reassembly drive shaft flanges.
Remove four nuts and bolts, tie propeller shaft to
one side.
15.Lower axle assembly and remove road springs.
16.Disconnect anti-roll[sway] bar link.
See FRONT
SUSPENSION, Repair, Anti-Roll[Sway] Bar
Ball Joint Links
17.Remove axle assembly.
Refit
18.Position axle under vehicle, supporting left side
of axle.
19.Reverse removal procedure.
20.Tighten propeller shaft bolts to
47 Nm.
21.Tighten panhard rod to axle bracket to88 Nm.
22.Tighten drag link to hub arm to40 Nm.
23.Tighten upper swivel pin bolts.See
Specifications, torque, Torque Values
24.Tighten radius arms to axle bolts to197 Nm.
25.Tighten radius arms to chassis side member
nuts to
197 Nm.
26.Tighten track rod end to40 Nm.
Fit new split [cotter] pin.
Page 500 of 873
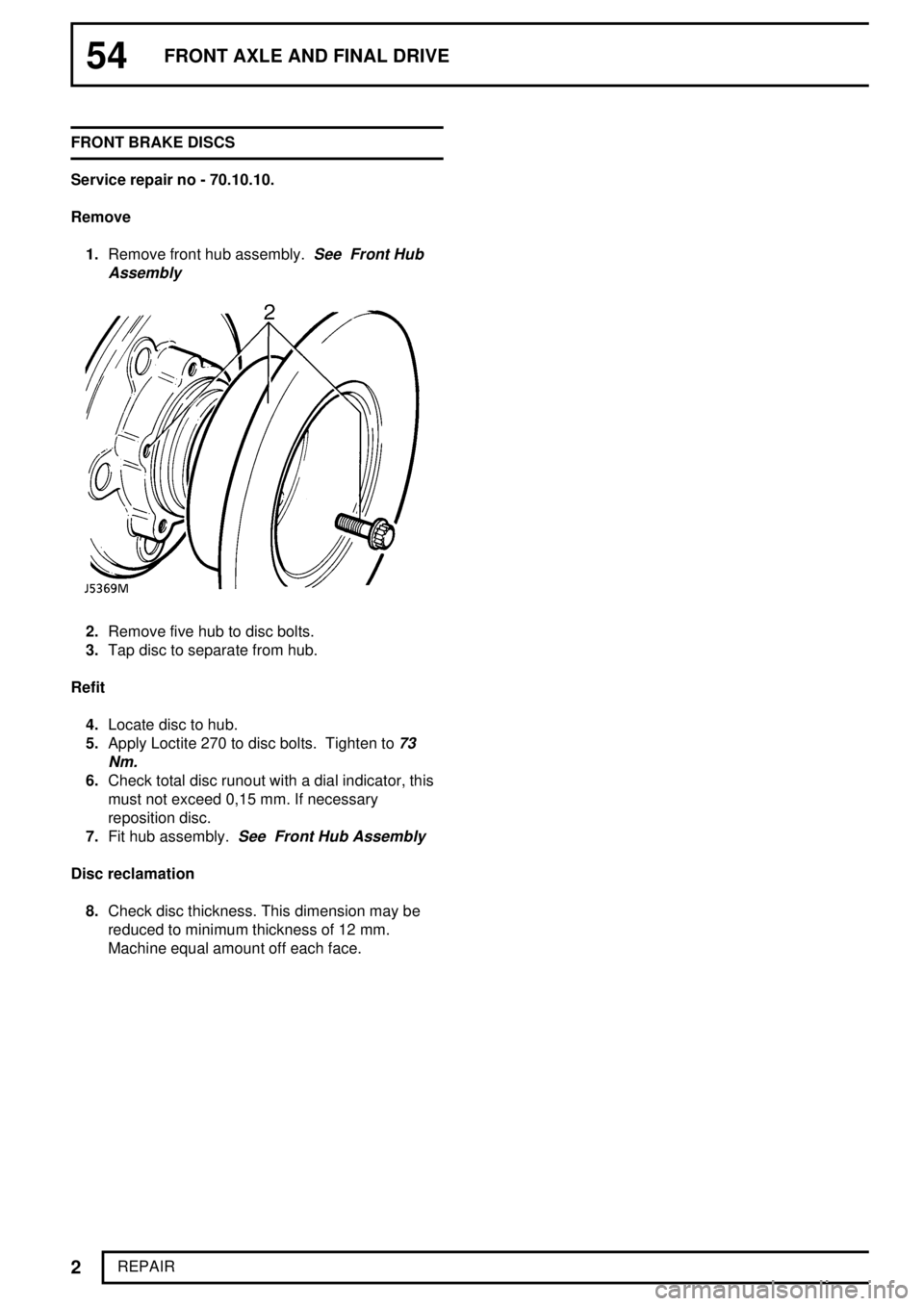
54FRONT AXLE AND FINAL DRIVE
2
REPAIR FRONT BRAKE DISCS
Service repair no - 70.10.10.
Remove
1.Remove front hub assembly.
See Front Hub
Assembly
2.Remove five hub to disc bolts.
3.Tap disc to separate from hub.
Refit
4.Locate disc to hub.
5.Apply Loctite 270 to disc bolts. Tighten to
73
Nm.
6.Check total disc runout with a dial indicator, this
must not exceed 0,15 mm. If necessary
reposition disc.
7.Fit hub assembly.
See Front Hub Assembly
Disc reclamation
8.Check disc thickness. This dimension may be
reduced to minimum thickness of 12 mm.
Machine equal amount off each face.