engine coolant LAND ROVER DISCOVERY 1999 Owner's Manual
[x] Cancel search | Manufacturer: LAND ROVER, Model Year: 1999, Model line: DISCOVERY, Model: LAND ROVER DISCOVERY 1999Pages: 1529, PDF Size: 34.8 MB
Page 197 of 1529
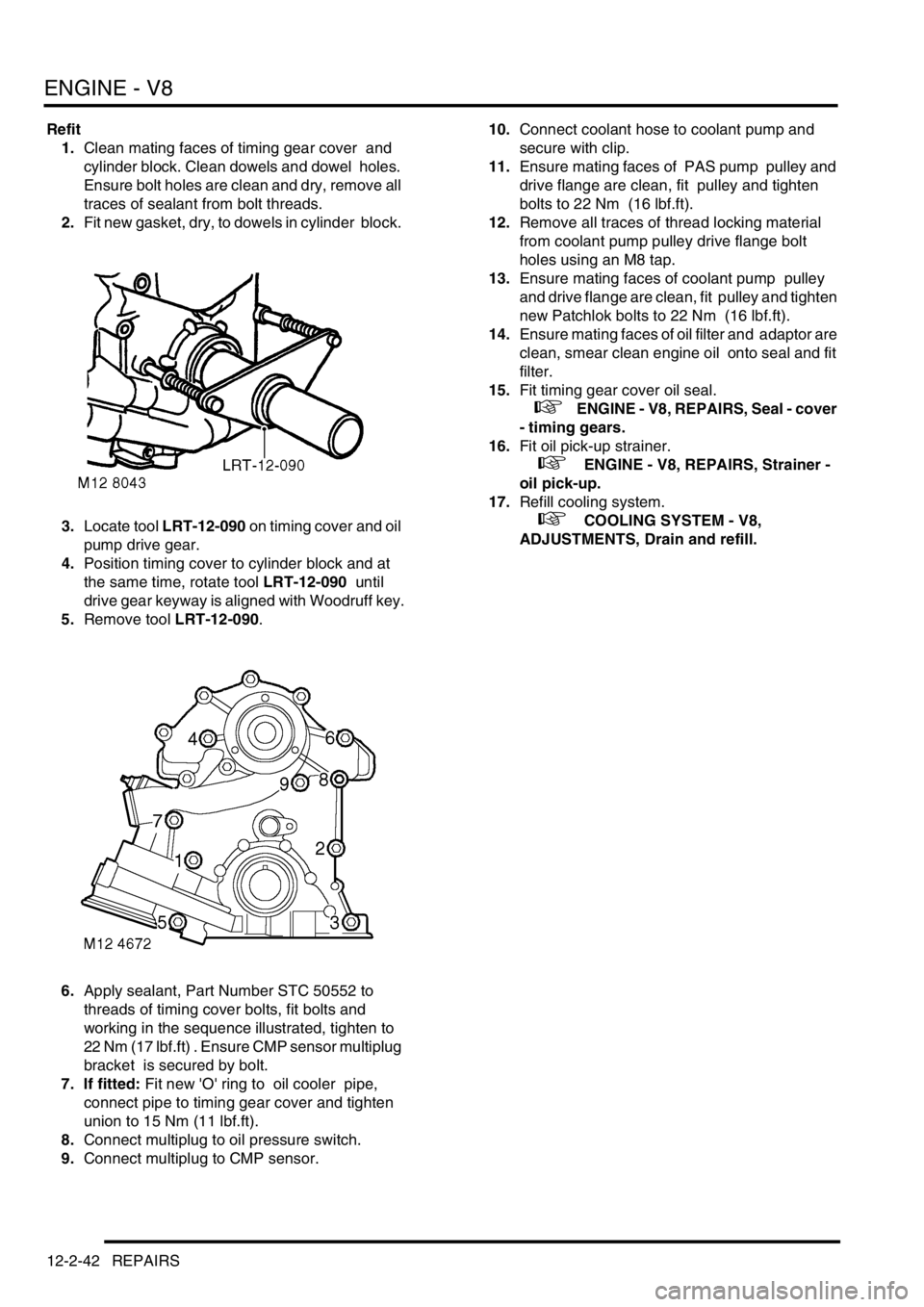
ENGINE - V8
12-2-42 REPAIRS
Refit
1.Clean mating faces of timing gear cover and
cylinder block. Clean dowels and dowel holes.
Ensure bolt holes are clean and dry, remove all
traces of sealant from bolt threads.
2.Fit new gasket, dry, to dowels in cylinder block.
3.Locate tool LRT-12-090 on timing cover and oil
pump drive gear.
4.Position timing cover to cylinder block and at
the same time, rotate tool LRT-12-090 until
drive gear keyway is aligned with Woodruff key.
5.Remove tool LRT-12-090.
6.Apply sealant, Part Number STC 50552 to
threads of timing cover bolts, fit bolts and
working in the sequence illustrated, tighten to
22 Nm (17 lbf.ft) . Ensure CMP sensor multiplug
bracket is secured by bolt.
7. If fitted: Fit new 'O' ring to oil cooler pipe,
connect pipe to timing gear cover and tighten
union to 15 Nm (11 lbf.ft).
8.Connect multiplug to oil pressure switch.
9.Connect multiplug to CMP sensor. 10.Connect coolant hose to coolant pump and
secure with clip.
11.Ensure mating faces of PAS pump pulley and
drive flange are clean, fit pulley and tighten
bolts to 22 Nm (16 lbf.ft).
12.Remove all traces of thread locking material
from coolant pump pulley drive flange bolt
holes using an M8 tap.
13.Ensure mating faces of coolant pump pulley
and drive flange are clean, fit pulley and tighten
new Patchlok bolts to 22 Nm (16 lbf.ft).
14.Ensure mating faces of oil filter and adaptor are
clean, smear clean engine oil onto seal and fit
filter.
15.Fit timing gear cover oil seal.
+ ENGINE - V8, REPAIRS, Seal - cover
- timing gears.
16.Fit oil pick-up strainer.
+ ENGINE - V8, REPAIRS, Strainer -
oil pick-up.
17.Refill cooling system.
+ COOLING SYSTEM - V8,
ADJUSTMENTS, Drain and refill.
Page 200 of 1529
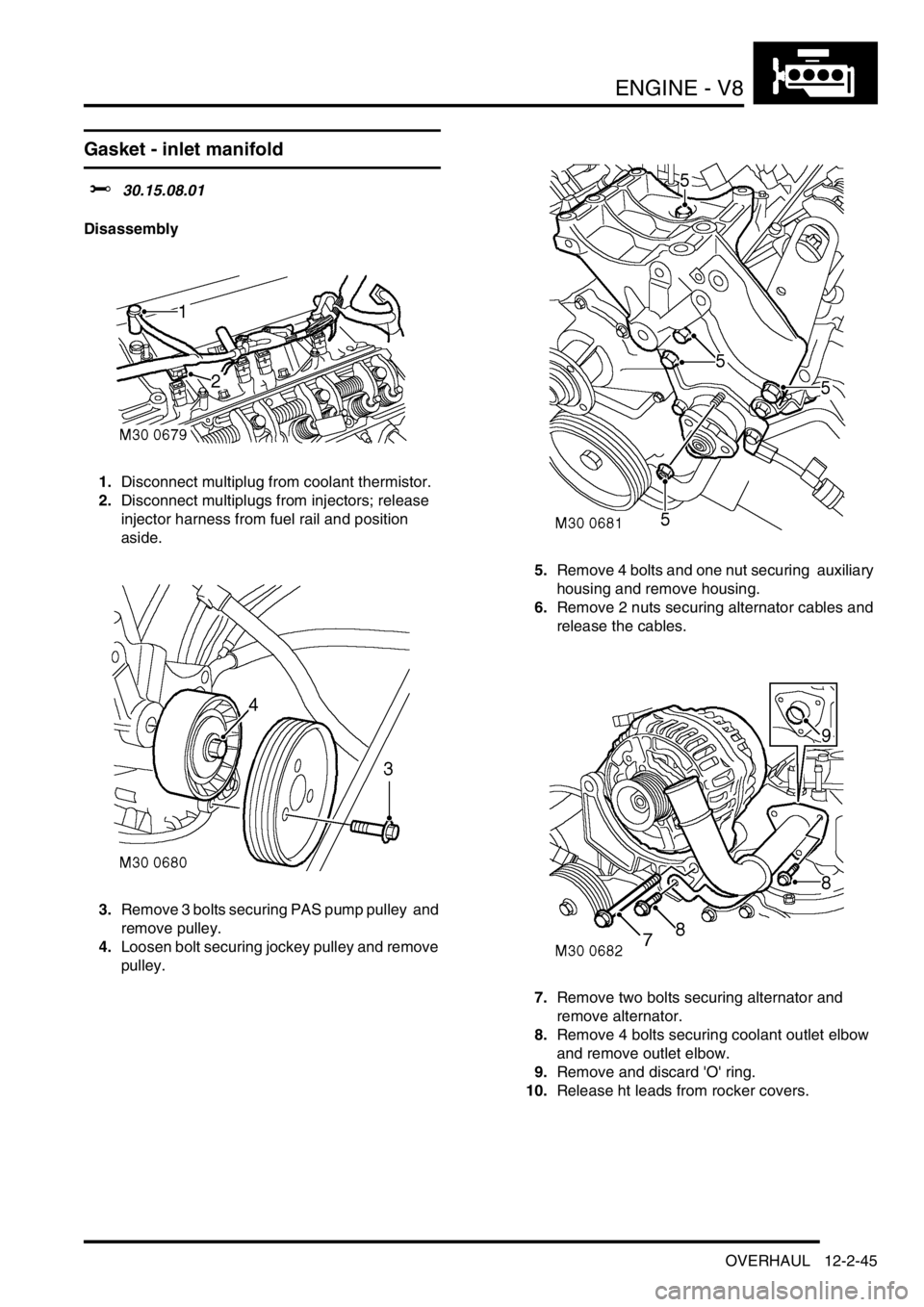
ENGINE - V8
OVERHAUL 12-2-45
OVERHAUL
Gasket - inlet manifold
$% 30.15.08.01
Disassembly
1.Disconnect multiplug from coolant thermistor.
2.Disconnect multiplugs from injectors; release
injector harness from fuel rail and position
aside.
3.Remove 3 bolts securing PAS pump pulley and
remove pulley.
4.Loosen bolt securing jockey pulley and remove
pulley. 5.Remove 4 bolts and one nut securing auxiliary
housing and remove housing.
6.Remove 2 nuts securing alternator cables and
release the cables.
7.Remove two bolts securing alternator and
remove alternator.
8.Remove 4 bolts securing coolant outlet elbow
and remove outlet elbow.
9.Remove and discard 'O' ring.
10.Release ht leads from rocker covers.
Page 202 of 1529
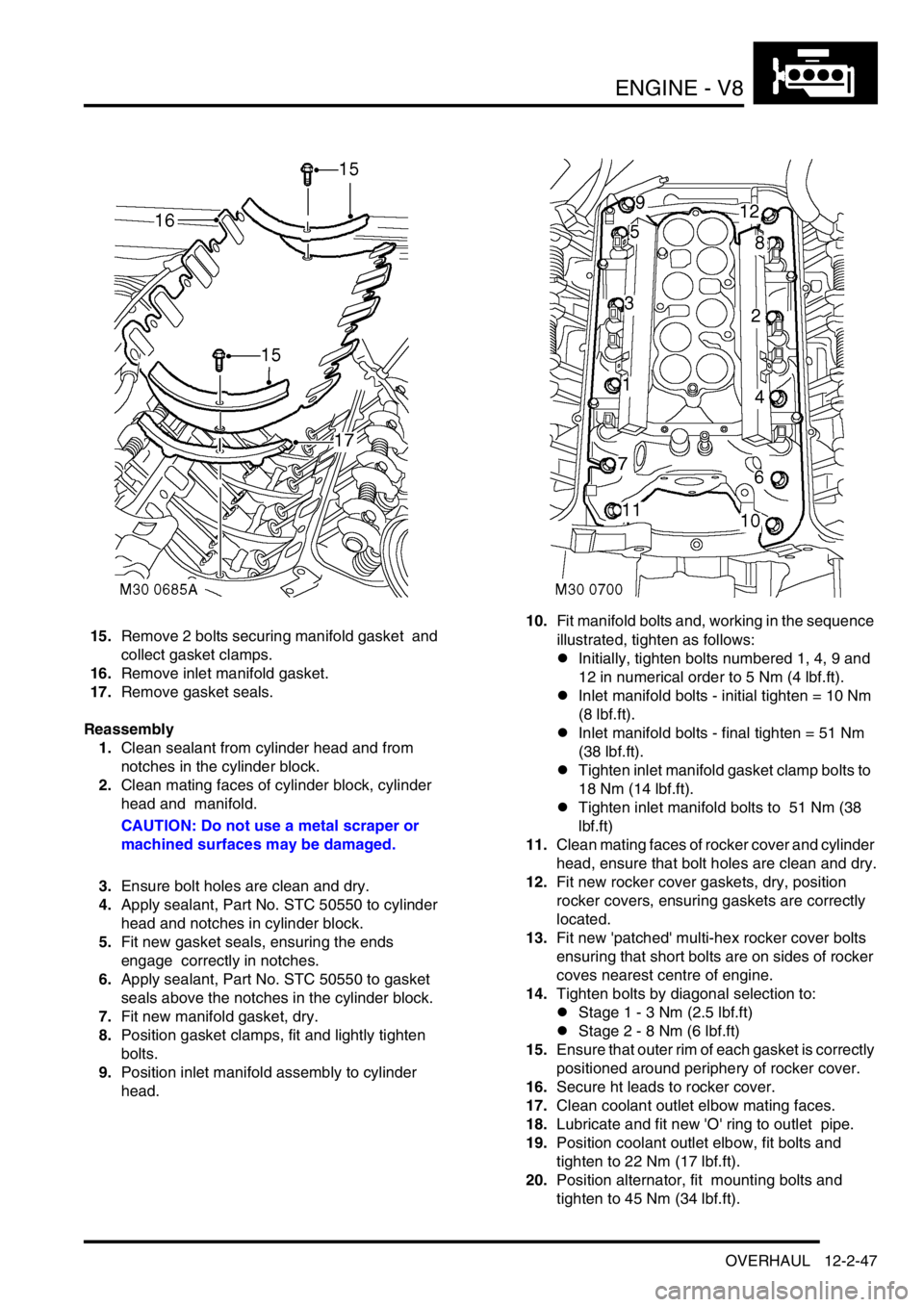
ENGINE - V8
OVERHAUL 12-2-47
15.Remove 2 bolts securing manifold gasket and
collect gasket clamps.
16.Remove inlet manifold gasket.
17.Remove gasket seals.
Reassembly
1.Clean sealant from cylinder head and from
notches in the cylinder block.
2.Clean mating faces of cylinder block, cylinder
head and manifold.
CAUTION: Do not use a metal scraper or
machined surfaces may be damaged.
3.Ensure bolt holes are clean and dry.
4.Apply sealant, Part No. STC 50550 to cylinder
head and notches in cylinder block.
5.Fit new gasket seals, ensuring the ends
engage correctly in notches.
6.Apply sealant, Part No. STC 50550 to gasket
seals above the notches in the cylinder block.
7.Fit new manifold gasket, dry.
8.Position gasket clamps, fit and lightly tighten
bolts.
9.Position inlet manifold assembly to cylinder
head. 10.Fit manifold bolts and, working in the sequence
illustrated, tighten as follows:
lInitially, tighten bolts numbered 1, 4, 9 and
12 in numerical order to 5 Nm (4 lbf.ft).
lInlet manifold bolts - initial tighten = 10 Nm
(8 lbf.ft).
lInlet manifold bolts - final tighten = 51 Nm
(38 lbf.ft).
lTighten inlet manifold gasket clamp bolts to
18 Nm (14 lbf.ft).
lTighten inlet manifold bolts to 51 Nm (38
lbf.ft)
11.Clean mating faces of rocker cover and cylinder
head, ensure that bolt holes are clean and dry.
12.Fit new rocker cover gaskets, dry, position
rocker covers, ensuring gaskets are correctly
located.
13.Fit new 'patched' multi-hex rocker cover bolts
ensuring that short bolts are on sides of rocker
coves nearest centre of engine.
14.Tighten bolts by diagonal selection to:
lStage 1 - 3 Nm (2.5 lbf.ft)
lStage 2 - 8 Nm (6 lbf.ft)
15.Ensure that outer rim of each gasket is correctly
positioned around periphery of rocker cover.
16.Secure ht leads to rocker cover.
17.Clean coolant outlet elbow mating faces.
18.Lubricate and fit new 'O' ring to outlet pipe.
19.Position coolant outlet elbow, fit bolts and
tighten to 22 Nm (17 lbf.ft).
20.Position alternator, fit mounting bolts and
tighten to 45 Nm (34 lbf.ft).
Page 203 of 1529
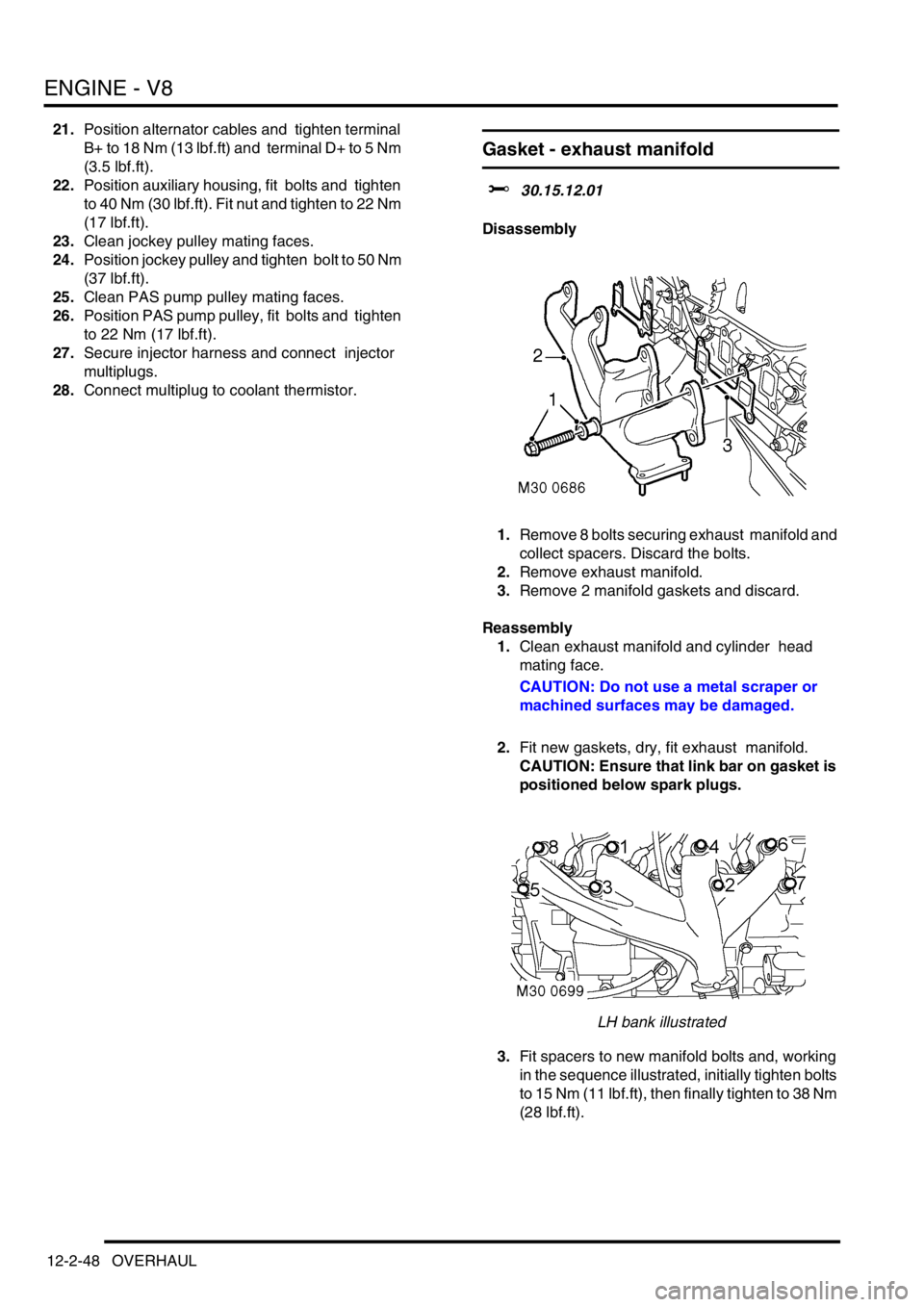
ENGINE - V8
12-2-48 OVERHAUL
21.Position alternator cables and tighten terminal
B+ to 18 Nm (13 lbf.ft) and terminal D+ to 5 Nm
(3.5 lbf.ft).
22.Position auxiliary housing, fit bolts and tighten
to 40 Nm (30 lbf.ft). Fit nut and tighten to 22 Nm
(17 lbf.ft).
23.Clean jockey pulley mating faces.
24.Position jockey pulley and tighten bolt to 50 Nm
(37 lbf.ft).
25.Clean PAS pump pulley mating faces.
26.Position PAS pump pulley, fit bolts and tighten
to 22 Nm (17 lbf.ft).
27.Secure injector harness and connect injector
multiplugs.
28.Connect multiplug to coolant thermistor.
Gasket - exhaust manifold
$% 30.15.12.01
Disassembly
1.Remove 8 bolts securing exhaust manifold and
collect spacers. Discard the bolts.
2.Remove exhaust manifold.
3.Remove 2 manifold gaskets and discard.
Reassembly
1.Clean exhaust manifold and cylinder head
mating face.
CAUTION: Do not use a metal scraper or
machined surfaces may be damaged.
2.Fit new gaskets, dry, fit exhaust manifold.
CAUTION: Ensure that link bar on gasket is
positioned below spark plugs.
LH bank illustrated
3.Fit spacers to new manifold bolts and, working
in the sequence illustrated, initially tighten bolts
to 15 Nm (11 lbf.ft), then finally tighten to 38 Nm
(28 lbf.ft).
Page 211 of 1529
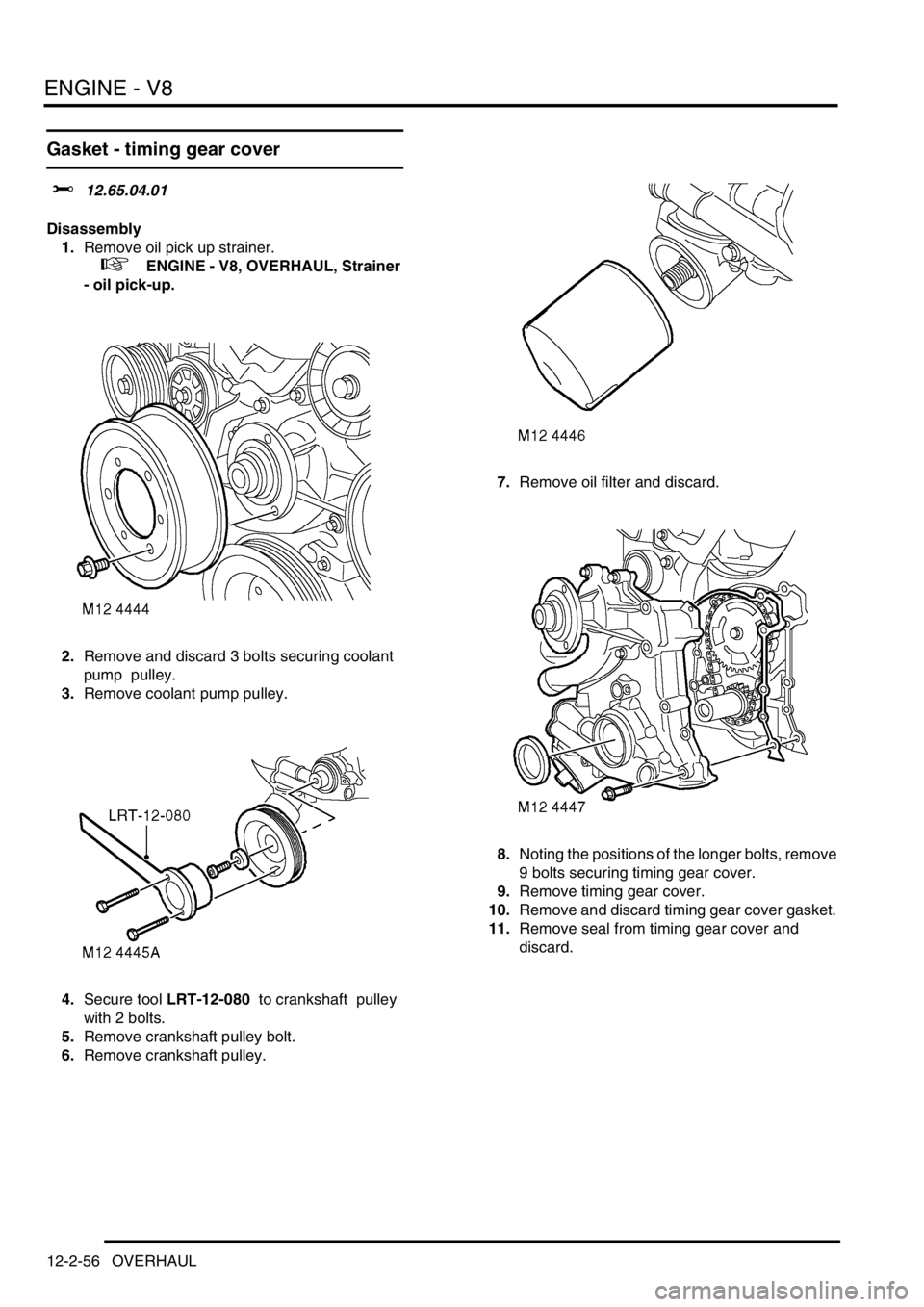
ENGINE - V8
12-2-56 OVERHAUL
Gasket - timing gear cover
$% 12.65.04.01
Disassembly
1.Remove oil pick up strainer.
+ ENGINE - V8, OVERHAUL, Strainer
- oil pick-up.
2.Remove and discard 3 bolts securing coolant
pump pulley.
3.Remove coolant pump pulley.
4.Secure tool LRT-12-080 to crankshaft pulley
with 2 bolts.
5.Remove crankshaft pulley bolt.
6.Remove crankshaft pulley. 7.Remove oil filter and discard.
8.Noting the positions of the longer bolts, remove
9 bolts securing timing gear cover.
9.Remove timing gear cover.
10.Remove and discard timing gear cover gasket.
11.Remove seal from timing gear cover and
discard.
Page 212 of 1529
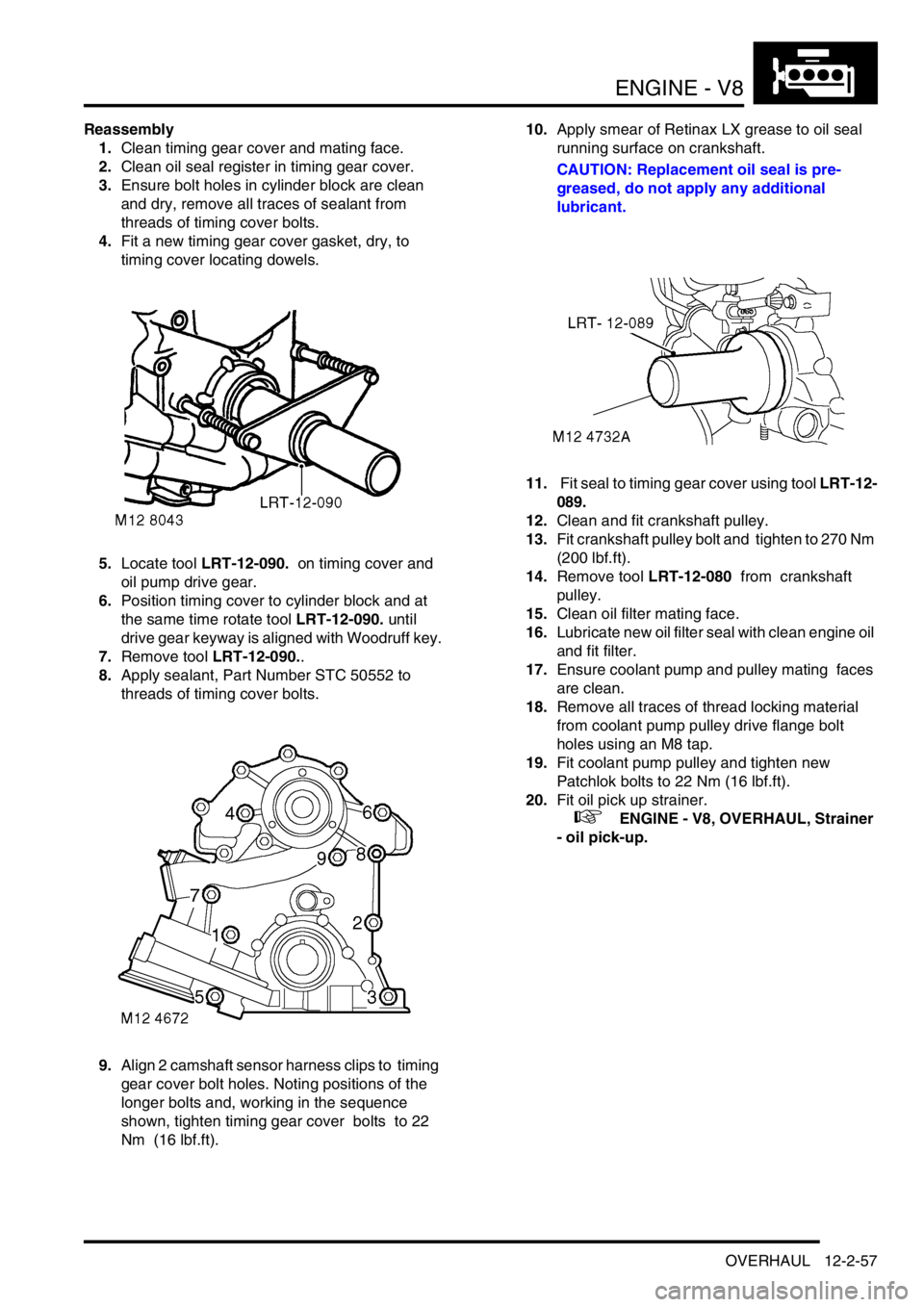
ENGINE - V8
OVERHAUL 12-2-57
Reassembly
1.Clean timing gear cover and mating face.
2.Clean oil seal register in timing gear cover.
3.Ensure bolt holes in cylinder block are clean
and dry, remove all traces of sealant from
threads of timing cover bolts.
4.Fit a new timing gear cover gasket, dry, to
timing cover locating dowels.
5.Locate tool LRT-12-090. on timing cover and
oil pump drive gear.
6.Position timing cover to cylinder block and at
the same time rotate tool LRT-12-090. until
drive gear keyway is aligned with Woodruff key.
7.Remove tool LRT-12-090..
8.Apply sealant, Part Number STC 50552 to
threads of timing cover bolts.
9.Align 2 camshaft sensor harness clips to timing
gear cover bolt holes. Noting positions of the
longer bolts and, working in the sequence
shown, tighten timing gear cover bolts to 22
Nm (16 lbf.ft). 10.Apply smear of Retinax LX grease to oil seal
running surface on crankshaft.
CAUTION: Replacement oil seal is pre-
greased, do not apply any additional
lubricant.
11. Fit seal to timing gear cover using tool LRT-12-
089.
12.Clean and fit crankshaft pulley.
13.Fit crankshaft pulley bolt and tighten to 270 Nm
(200 lbf.ft).
14.Remove tool LRT-12-080 from crankshaft
pulley.
15.Clean oil filter mating face.
16.Lubricate new oil filter seal with clean engine oil
and fit filter.
17.Ensure coolant pump and pulley mating faces
are clean.
18.Remove all traces of thread locking material
from coolant pump pulley drive flange bolt
holes using an M8 tap.
19.Fit coolant pump pulley and tighten new
Patchlok bolts to 22 Nm (16 lbf.ft).
20.Fit oil pick up strainer.
+ ENGINE - V8, OVERHAUL, Strainer
- oil pick-up.
Page 259 of 1529
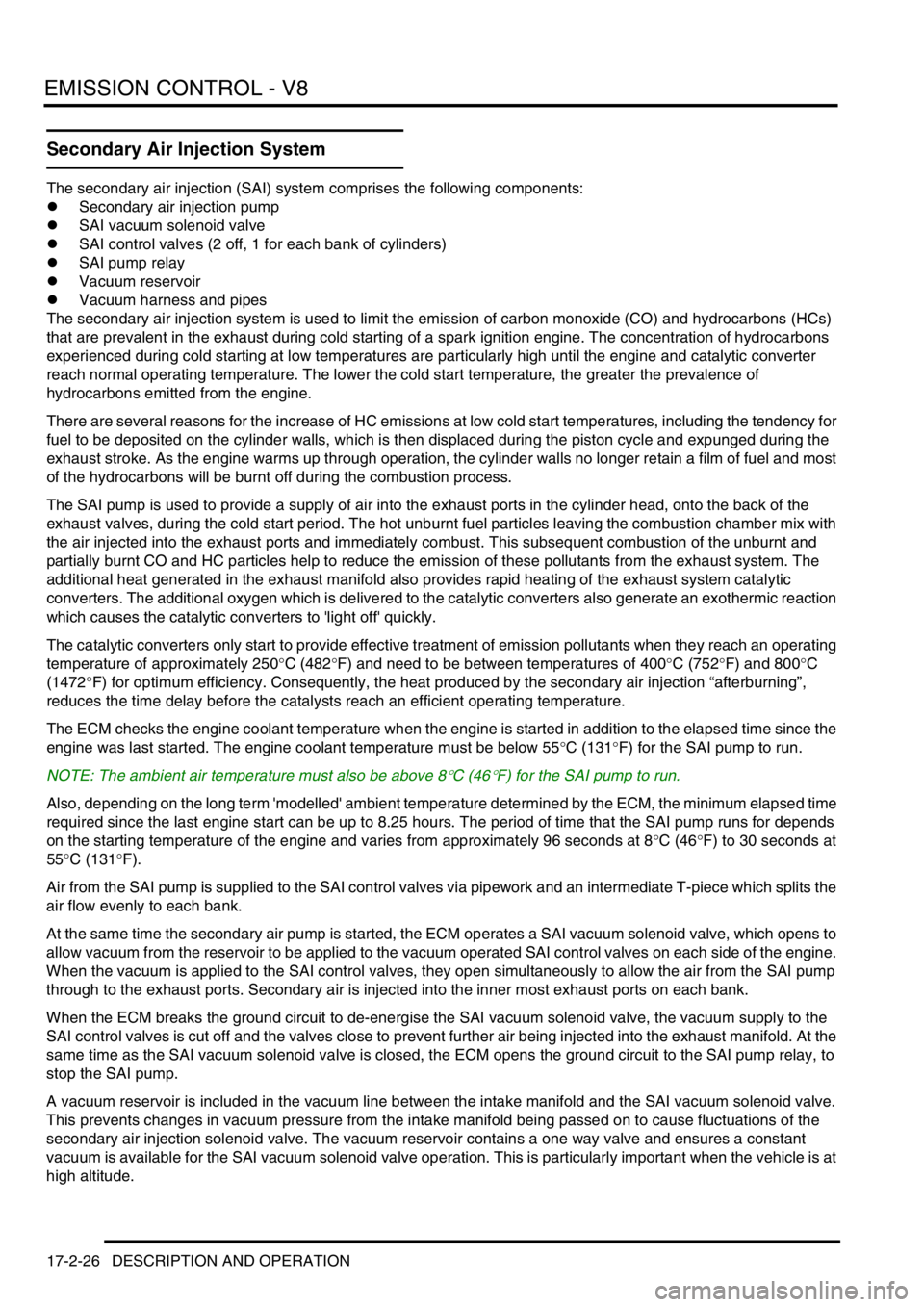
EMISSION CONTROL - V8
17-2-26 DESCRIPTION AND OPERATION
Secondary Air Injection System
The secondary air injection (SAI) system comprises the following components:
lSecondary air injection pump
lSAI vacuum solenoid valve
lSAI control valves (2 off, 1 for each bank of cylinders)
lSAI pump relay
lVacuum reservoir
lVacuum harness and pipes
The secondary air injection system is used to limit the emission of carbon monoxide (CO) and hydrocarbons (HCs)
that are prevalent in the exhaust during cold starting of a spark ignition engine. The concentration of hydrocarbons
experienced during cold starting at low temperatures are particularly high until the engine and catalytic converter
reach normal operating temperature. The lower the cold start temperature, the greater the prevalence of
hydrocarbons emitted from the engine.
There are several reasons for the increase of HC emissions at low cold start temperatures, including the tendency for
fuel to be deposited on the cylinder walls, which is then displaced during the piston cycle and expunged during the
exhaust stroke. As the engine warms up through operation, the cylinder walls no longer retain a film of fuel and most
of the hydrocarbons will be burnt off during the combustion process.
The SAI pump is used to provide a supply of air into the exhaust ports in the cylinder head, onto the back of the
exhaust valves, during the cold start period. The hot unburnt fuel particles leaving the combustion chamber mix with
the air injected into the exhaust ports and immediately combust. This subsequent combustion of the unburnt and
partially burnt CO and HC particles help to reduce the emission of these pollutants from the exhaust system. The
additional heat generated in the exhaust manifold also provides rapid heating of the exhaust system catalytic
converters. The additional oxygen which is delivered to the catalytic converters also generate an exothermic reaction
which causes the catalytic converters to 'light off' quickly.
The catalytic converters only start to provide effective treatment of emission pollutants when they reach an operating
temperature of approximately 250°C (482°F) and need to be between temperatures of 400°C (752°F) and 800°C
(1472°F) for optimum efficiency. Consequently, the heat produced by the secondary air injection “afterburning”,
reduces the time delay before the catalysts reach an efficient operating temperature.
The ECM checks the engine coolant temperature when the engine is started in addition to the elapsed time since the
engine was last started. The engine coolant temperature must be below 55°C (131°F) for the SAI pump to run.
NOTE: The ambient air temperature must also be above 8
°C (46°F) for the SAI pump to run.
Also, depending on the long term 'modelled' ambient temperature determined by the ECM, the minimum elapsed time
required since the last engine start can be up to 8.25 hours. The period of time that the SAI pump runs for depends
on the starting temperature of the engine and varies from approximately 96 seconds at 8°C (46°F) to 30 seconds at
55°C (131°F).
Air from the SAI pump is supplied to the SAI control valves via pipework and an intermediate T-piece which splits the
air flow evenly to each bank.
At the same time the secondary air pump is started, the ECM operates a SAI vacuum solenoid valve, which opens to
allow vacuum from the reservoir to be applied to the vacuum operated SAI control valves on each side of the engine.
When the vacuum is applied to the SAI control valves, they open simultaneously to allow the air from the SAI pump
through to the exhaust ports. Secondary air is injected into the inner most exhaust ports on each bank.
When the ECM breaks the ground circuit to de-energise the SAI vacuum solenoid valve, the vacuum supply to the
SAI control valves is cut off and the valves close to prevent further air being injected into the exhaust manifold. At the
same time as the SAI vacuum solenoid valve is closed, the ECM opens the ground circuit to the SAI pump relay, to
stop the SAI pump.
A vacuum reservoir is included in the vacuum line between the intake manifold and the SAI vacuum solenoid valve.
This prevents changes in vacuum pressure from the intake manifold being passed on to cause fluctuations of the
secondary air injection solenoid valve. The vacuum reservoir contains a one way valve and ensures a constant
vacuum is available for the SAI vacuum solenoid valve operation. This is particularly important when the vehicle is at
high altitude.
Page 260 of 1529
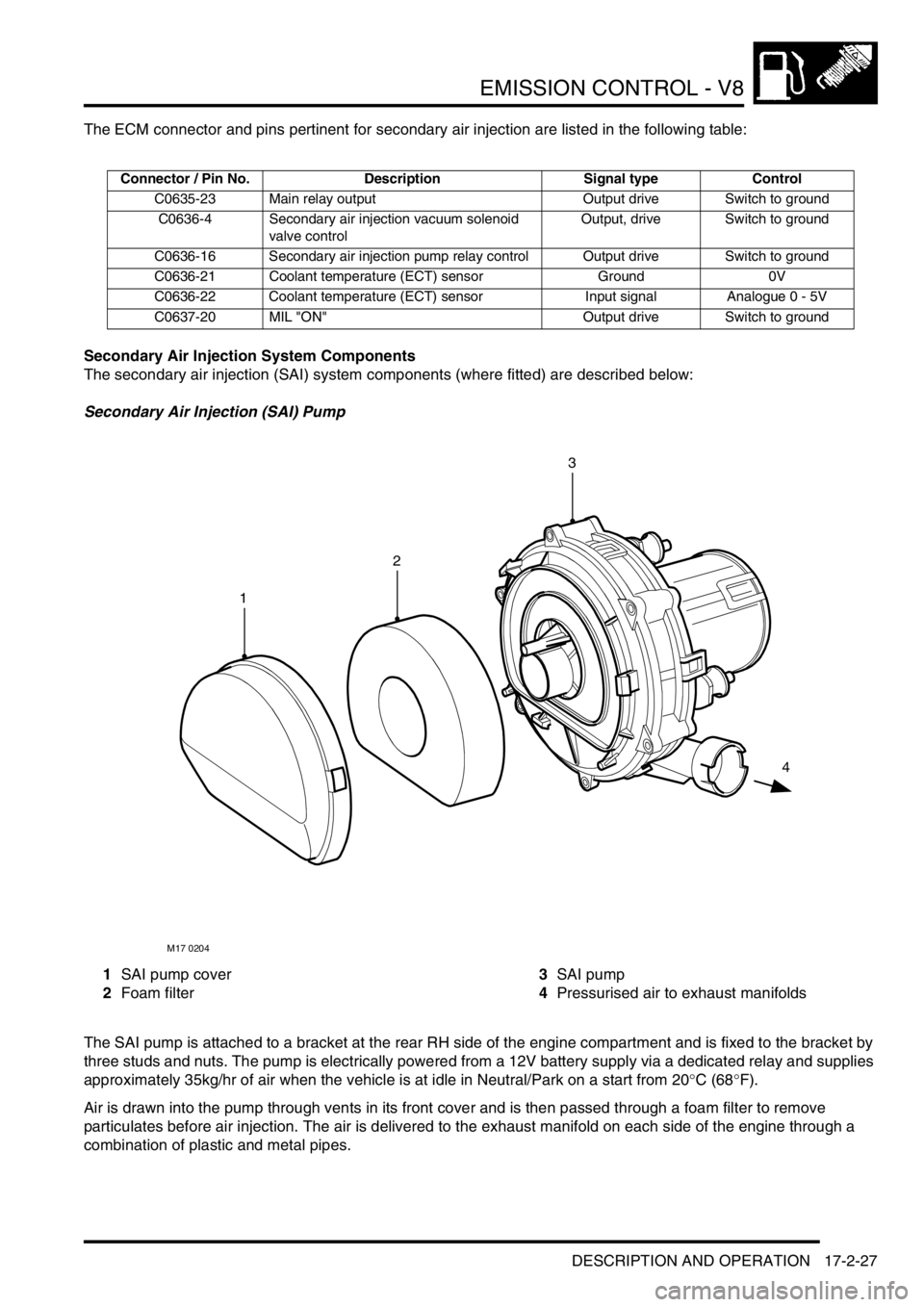
EMISSION CONTROL - V8
DESCRIPTION AND OPERATION 17-2-27
The ECM connector and pins pertinent for secondary air injection are listed in the following table:
Secondary Air Injection System Components
The secondary air injection (SAI) system components (where fitted) are described below:
Secondary Air Injection (SAI) Pump
1SAI pump cover
2Foam filter3SAI pump
4Pressurised air to exhaust manifolds
The SAI pump is attached to a bracket at the rear RH side of the engine compartment and is fixed to the bracket by
three studs and nuts. The pump is electrically powered from a 12V battery supply via a dedicated relay and supplies
approximately 35kg/hr of air when the vehicle is at idle in Neutral/Park on a start from 20°C (68°F).
Air is drawn into the pump through vents in its front cover and is then passed through a foam filter to remove
particulates before air injection. The air is delivered to the exhaust manifold on each side of the engine through a
combination of plastic and metal pipes.
Connector / Pin No. Description Signal type Control
C0635-23 Main relay output Output drive Switch to ground
C0636-4 Secondary air injection vacuum solenoid
valve controlOutput, drive Switch to ground
C0636-16 Secondary air injection pump relay control Output drive Switch to ground
C0636-21 Coolant temperature (ECT) sensor Ground 0V
C0636-22 Coolant temperature (ECT) sensor Input signal Analogue 0 - 5V
C0637-20 MIL "ON" Output drive Switch to ground
M17 0204
1
4
2
3
Page 272 of 1529
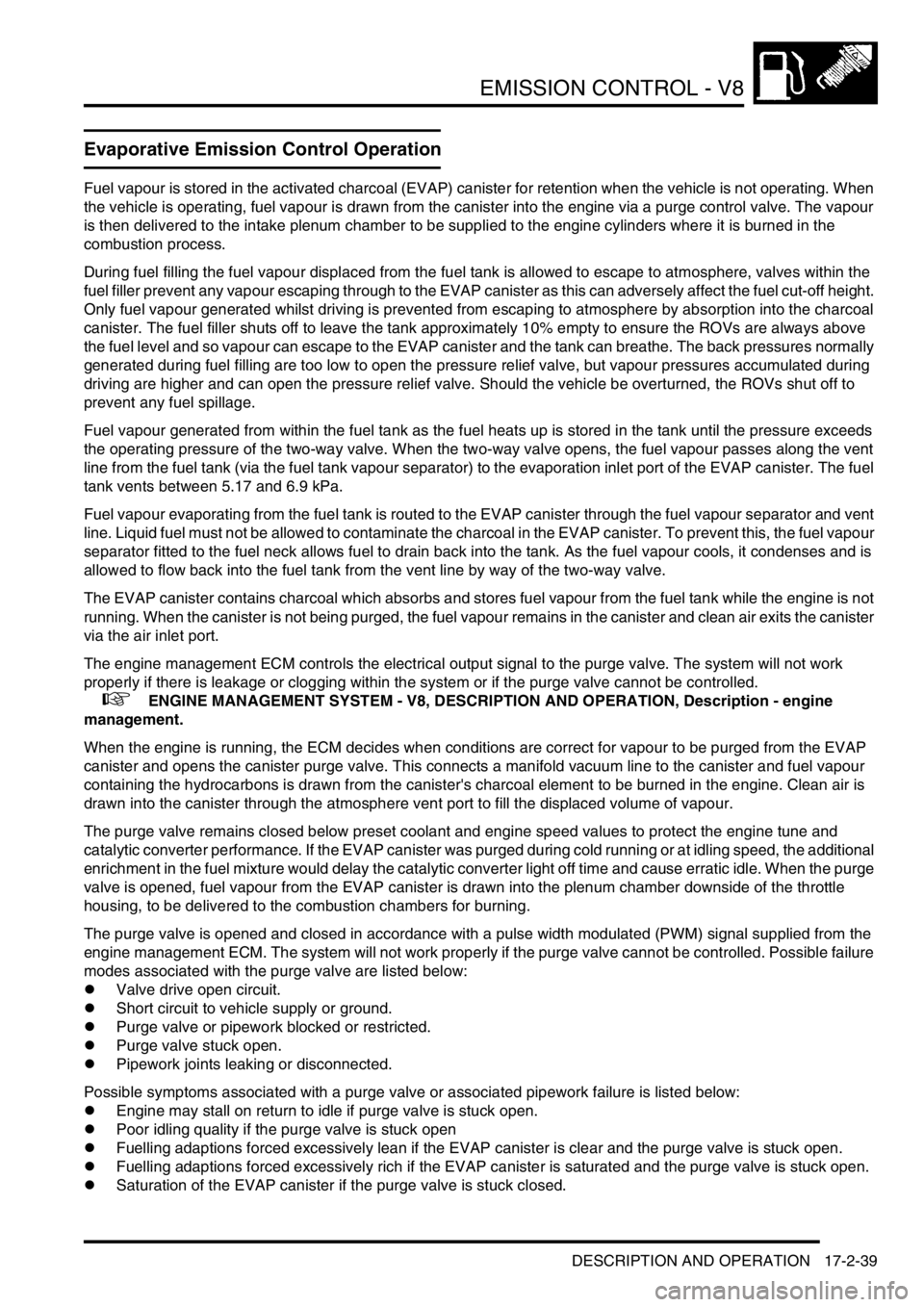
EMISSION CONTROL - V8
DESCRIPTION AND OPERATION 17-2-39
Evaporative Emission Control Operation
Fuel vapour is stored in the activated charcoal (EVAP) canister for retention when the vehicle is not operating. When
the vehicle is operating, fuel vapour is drawn from the canister into the engine via a purge control valve. The vapour
is then delivered to the intake plenum chamber to be supplied to the engine cylinders where it is burned in the
combustion process.
During fuel filling the fuel vapour displaced from the fuel tank is allowed to escape to atmosphere, valves within the
fuel filler prevent any vapour escaping through to the EVAP canister as this can adversely affect the fuel cut-off height.
Only fuel vapour generated whilst driving is prevented from escaping to atmosphere by absorption into the charcoal
canister. The fuel filler shuts off to leave the tank approximately 10% empty to ensure the ROVs are always above
the fuel level and so vapour can escape to the EVAP canister and the tank can breathe. The back pressures normally
generated during fuel filling are too low to open the pressure relief valve, but vapour pressures accumulated during
driving are higher and can open the pressure relief valve. Should the vehicle be overturned, the ROVs shut off to
prevent any fuel spillage.
Fuel vapour generated from within the fuel tank as the fuel heats up is stored in the tank until the pressure exceeds
the operating pressure of the two-way valve. When the two-way valve opens, the fuel vapour passes along the vent
line from the fuel tank (via the fuel tank vapour separator) to the evaporation inlet port of the EVAP canister. The fuel
tank vents between 5.17 and 6.9 kPa.
Fuel vapour evaporating from the fuel tank is routed to the EVAP canister through the fuel vapour separator and vent
line. Liquid fuel must not be allowed to contaminate the charcoal in the EVAP canister. To prevent this, the fuel vapour
separator fitted to the fuel neck allows fuel to drain back into the tank. As the fuel vapour cools, it condenses and is
allowed to flow back into the fuel tank from the vent line by way of the two-way valve.
The EVAP canister contains charcoal which absorbs and stores fuel vapour from the fuel tank while the engine is not
running. When the canister is not being purged, the fuel vapour remains in the canister and clean air exits the canister
via the air inlet port.
The engine management ECM controls the electrical output signal to the purge valve. The system will not work
properly if there is leakage or clogging within the system or if the purge valve cannot be controlled.
+ ENGINE MANAGEMENT SYSTEM - V8, DESCRIPTION AND OPERATION, Description - engine
management.
When the engine is running, the ECM decides when conditions are correct for vapour to be purged from the EVAP
canister and opens the canister purge valve. This connects a manifold vacuum line to the canister and fuel vapour
containing the hydrocarbons is drawn from the canister's charcoal element to be burned in the engine. Clean air is
drawn into the canister through the atmosphere vent port to fill the displaced volume of vapour.
The purge valve remains closed below preset coolant and engine speed values to protect the engine tune and
catalytic converter performance. If the EVAP canister was purged during cold running or at idling speed, the additional
enrichment in the fuel mixture would delay the catalytic converter light off time and cause erratic idle. When the purge
valve is opened, fuel vapour from the EVAP canister is drawn into the plenum chamber downside of the throttle
housing, to be delivered to the combustion chambers for burning.
The purge valve is opened and closed in accordance with a pulse width modulated (PWM) signal supplied from the
engine management ECM. The system will not work properly if the purge valve cannot be controlled. Possible failure
modes associated with the purge valve are listed below:
lValve drive open circuit.
lShort circuit to vehicle supply or ground.
lPurge valve or pipework blocked or restricted.
lPurge valve stuck open.
lPipework joints leaking or disconnected.
Possible symptoms associated with a purge valve or associated pipework failure is listed below:
lEngine may stall on return to idle if purge valve is stuck open.
lPoor idling quality if the purge valve is stuck open
lFuelling adaptions forced excessively lean if the EVAP canister is clear and the purge valve is stuck open.
lFuelling adaptions forced excessively rich if the EVAP canister is saturated and the purge valve is stuck open.
lSaturation of the EVAP canister if the purge valve is stuck closed.
Page 276 of 1529
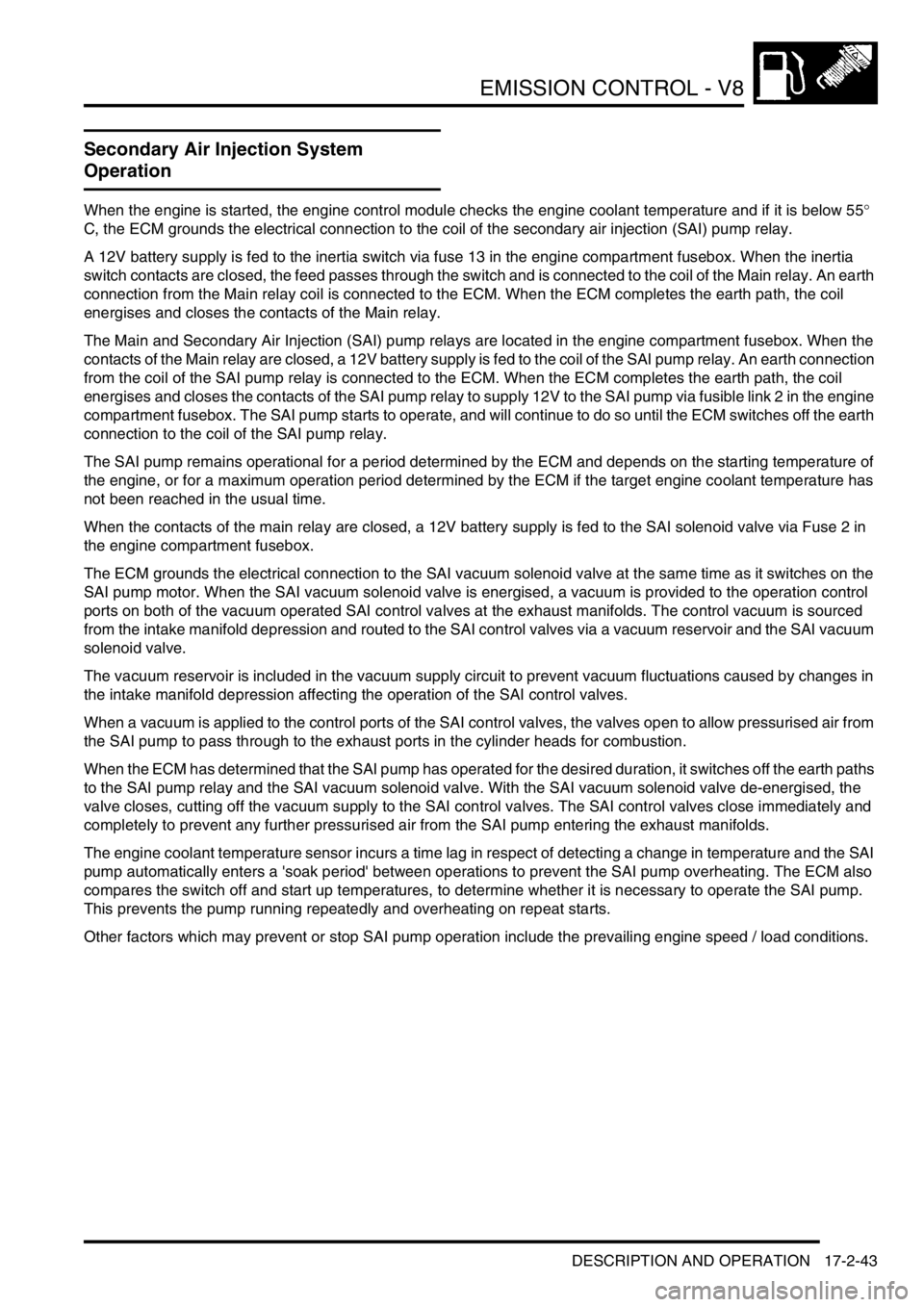
EMISSION CONTROL - V8
DESCRIPTION AND OPERATION 17-2-43
Secondary Air Injection System
Operation
When the engine is started, the engine control module checks the engine coolant temperature and if it is below 55°
C, the ECM grounds the electrical connection to the coil of the secondary air injection (SAI) pump relay.
A 12V battery supply is fed to the inertia switch via fuse 13 in the engine compartment fusebox. When the inertia
switch contacts are closed, the feed passes through the switch and is connected to the coil of the Main relay. An earth
connection from the Main relay coil is connected to the ECM. When the ECM completes the earth path, the coil
energises and closes the contacts of the Main relay.
The Main and Secondary Air Injection (SAI) pump relays are located in the engine compartment fusebox. When the
contacts of the Main relay are closed, a 12V battery supply is fed to the coil of the SAI pump relay. An earth connection
from the coil of the SAI pump relay is connected to the ECM. When the ECM completes the earth path, the coil
energises and closes the contacts of the SAI pump relay to supply 12V to the SAI pump via fusible link 2 in the engine
compartment fusebox. The SAI pump starts to operate, and will continue to do so until the ECM switches off the earth
connection to the coil of the SAI pump relay.
The SAI pump remains operational for a period determined by the ECM and depends on the starting temperature of
the engine, or for a maximum operation period determined by the ECM if the target engine coolant temperature has
not been reached in the usual time.
When the contacts of the main relay are closed, a 12V battery supply is fed to the SAI solenoid valve via Fuse 2 in
the engine compartment fusebox.
The ECM grounds the electrical connection to the SAI vacuum solenoid valve at the same time as it switches on the
SAI pump motor. When the SAI vacuum solenoid valve is energised, a vacuum is provided to the operation control
ports on both of the vacuum operated SAI control valves at the exhaust manifolds. The control vacuum is sourced
from the intake manifold depression and routed to the SAI control valves via a vacuum reservoir and the SAI vacuum
solenoid valve.
The vacuum reservoir is included in the vacuum supply circuit to prevent vacuum fluctuations caused by changes in
the intake manifold depression affecting the operation of the SAI control valves.
When a vacuum is applied to the control ports of the SAI control valves, the valves open to allow pressurised air from
the SAI pump to pass through to the exhaust ports in the cylinder heads for combustion.
When the ECM has determined that the SAI pump has operated for the desired duration, it switches off the earth paths
to the SAI pump relay and the SAI vacuum solenoid valve. With the SAI vacuum solenoid valve de-energised, the
valve closes, cutting off the vacuum supply to the SAI control valves. The SAI control valves close immediately and
completely to prevent any further pressurised air from the SAI pump entering the exhaust manifolds.
The engine coolant temperature sensor incurs a time lag in respect of detecting a change in temperature and the SAI
pump automatically enters a 'soak period' between operations to prevent the SAI pump overheating. The ECM also
compares the switch off and start up temperatures, to determine whether it is necessary to operate the SAI pump.
This prevents the pump running repeatedly and overheating on repeat starts.
Other factors which may prevent or stop SAI pump operation include the prevailing engine speed / load conditions.