LAND ROVER DISCOVERY 1999 Workshop Manual
Manufacturer: LAND ROVER, Model Year: 1999, Model line: DISCOVERY, Model: LAND ROVER DISCOVERY 1999Pages: 1529, PDF Size: 34.8 MB
Page 311 of 1529
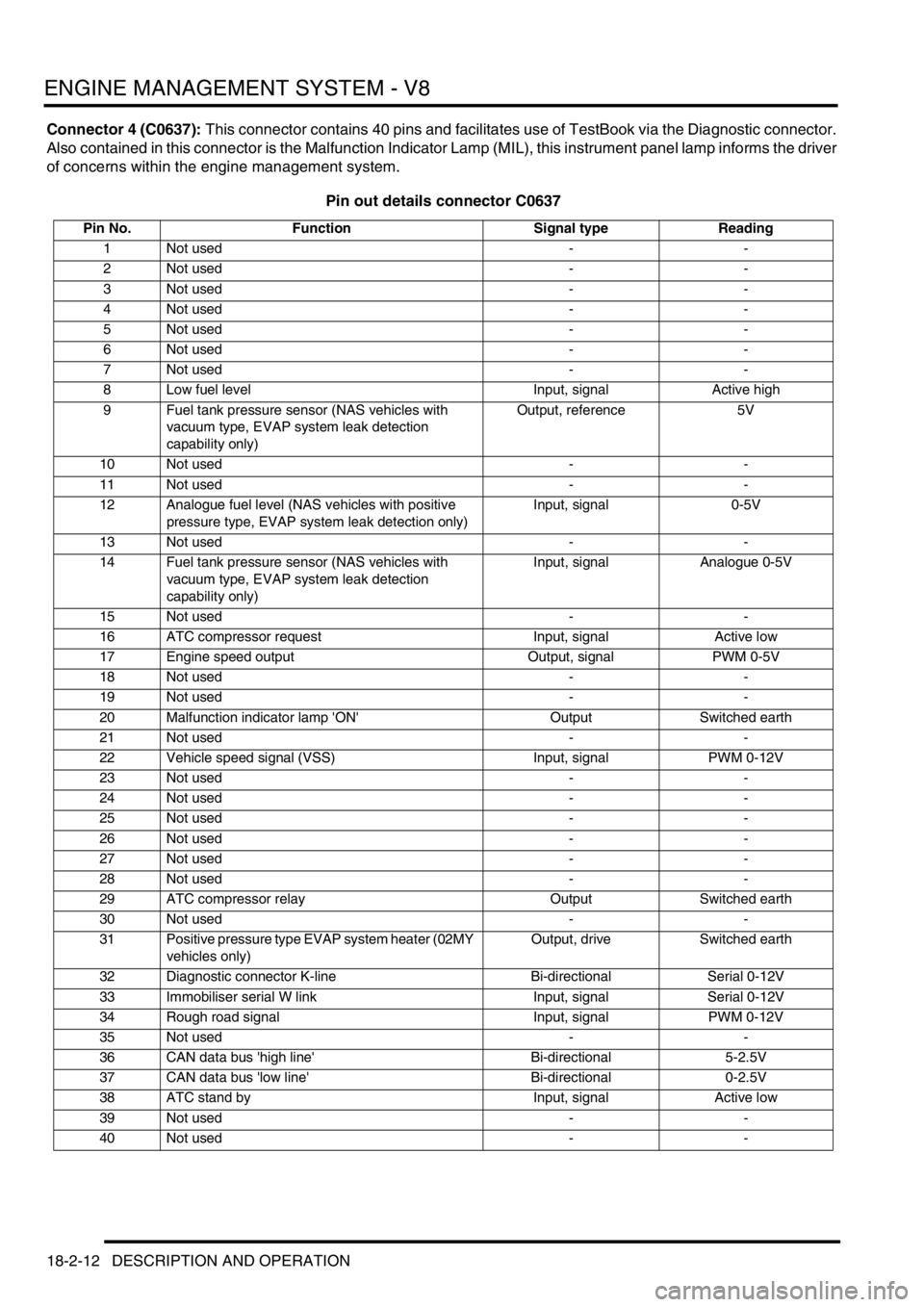
ENGINE MANAGEMENT SYSTEM - V8
18-2-12 DESCRIPTION AND OPERATION
Connector 4 (C0637): This connector contains 40 pins and facilitates use of TestBook via the Diagnostic connector.
Also contained in this connector is the Malfunction Indicator Lamp (MIL), this instrument panel lamp informs the driver
of concerns within the engine management system.
Pin out details connector C0637
Pin No. Function Signal type Reading
1 Not used - -
2 Not used - -
3 Not used - -
4 Not used - -
5 Not used - -
6 Not used - -
7 Not used - -
8 Low fuel level Input, signal Active high
9 Fuel tank pressure sensor (NAS vehicles with
vacuum type, EVAP system leak detection
capability only)Output, reference 5V
10 Not used - -
11 Not used - -
12 Analogue fuel level (NAS vehicles with positive
pressure type, EVAP system leak detection only)Input, signal 0-5V
13 Not used - -
14 Fuel tank pressure sensor (NAS vehicles with
vacuum type, EVAP system leak detection
capability only)Input, signal Analogue 0-5V
15 Not used - -
16 ATC compressor request Input, signal Active low
17 Engine speed output Output, signal PWM 0-5V
18 Not used - -
19 Not used - -
20 Malfunction indicator lamp 'ON' Output Switched earth
21 Not used - -
22 Vehicle speed signal (VSS) Input, signal PWM 0-12V
23 Not used - -
24 Not used - -
25 Not used - -
26 Not used - -
27 Not used - -
28 Not used - -
29 ATC compressor relay Output Switched earth
30 Not used - -
31 Positive pressure type EVAP system heater (02MY
vehicles only)Output, drive Switched earth
32 Diagnostic connector K-line Bi-directional Serial 0-12V
33 Immobiliser serial W link Input, signal Serial 0-12V
34 Rough road signal Input, signal PWM 0-12V
35 Not used - -
36 CAN data bus 'high line' Bi-directional 5-2.5V
37 CAN data bus 'low line' Bi-directional 0-2.5V
38 ATC stand by Input, signal Active low
39 Not used - -
40 Not used - -
Page 312 of 1529
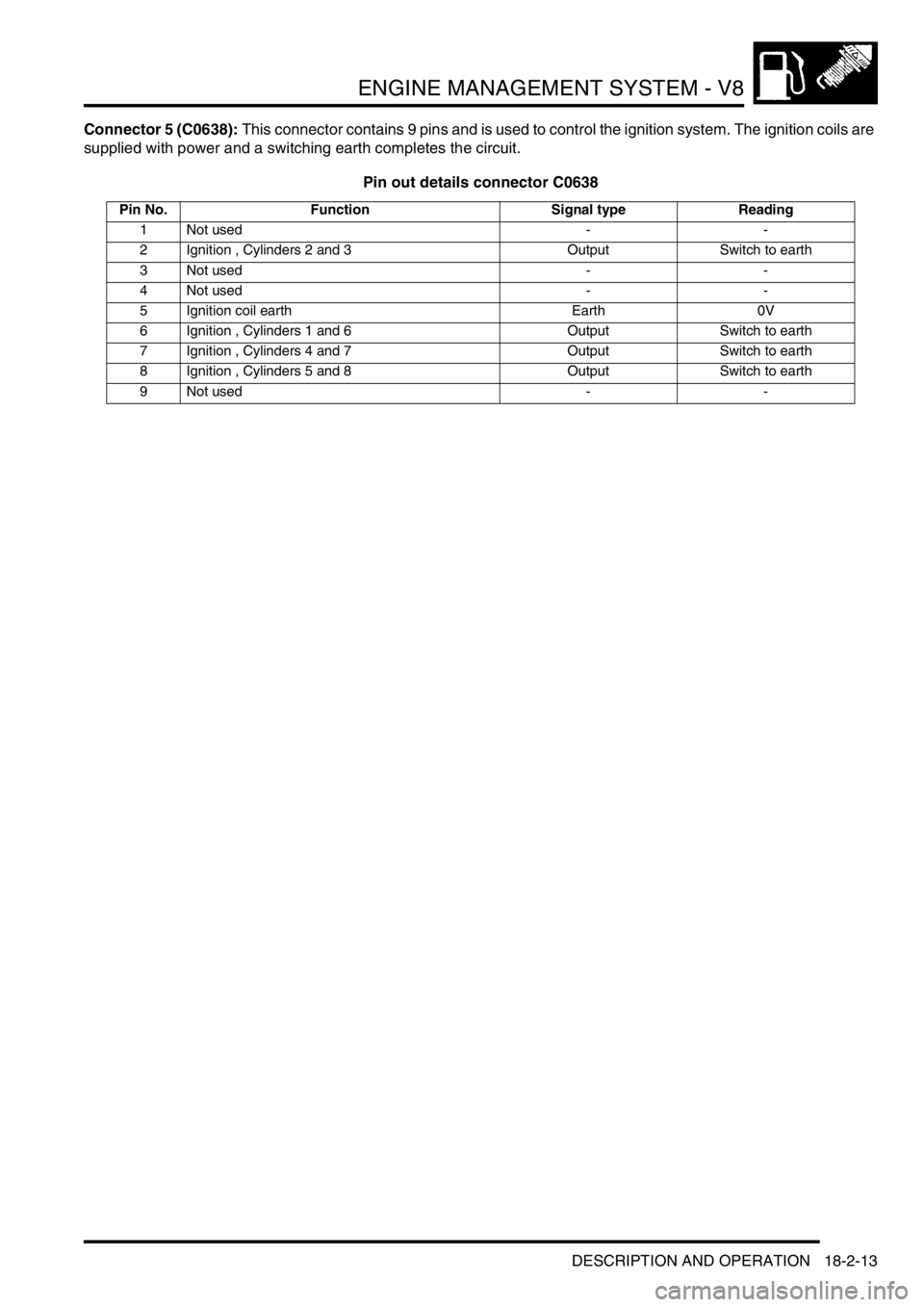
ENGINE MANAGEMENT SYSTEM - V8
DESCRIPTION AND OPERATION 18-2-13
Connector 5 (C0638): This connector contains 9 pins and is used to control the ignition system. The ignition coils are
supplied with power and a switching earth completes the circuit.
Pin out details connector C0638
Pin No. Function Signal type Reading
1 Not used - -
2 Ignition , Cylinders 2 and 3 Output Switch to earth
3 Not used - -
4 Not used - -
5 Ignition coil earth Earth 0V
6 Ignition , Cylinders 1 and 6 Output Switch to earth
7 Ignition , Cylinders 4 and 7 Output Switch to earth
8 Ignition , Cylinders 5 and 8 Output Switch to earth
9 Not used - -
Page 313 of 1529
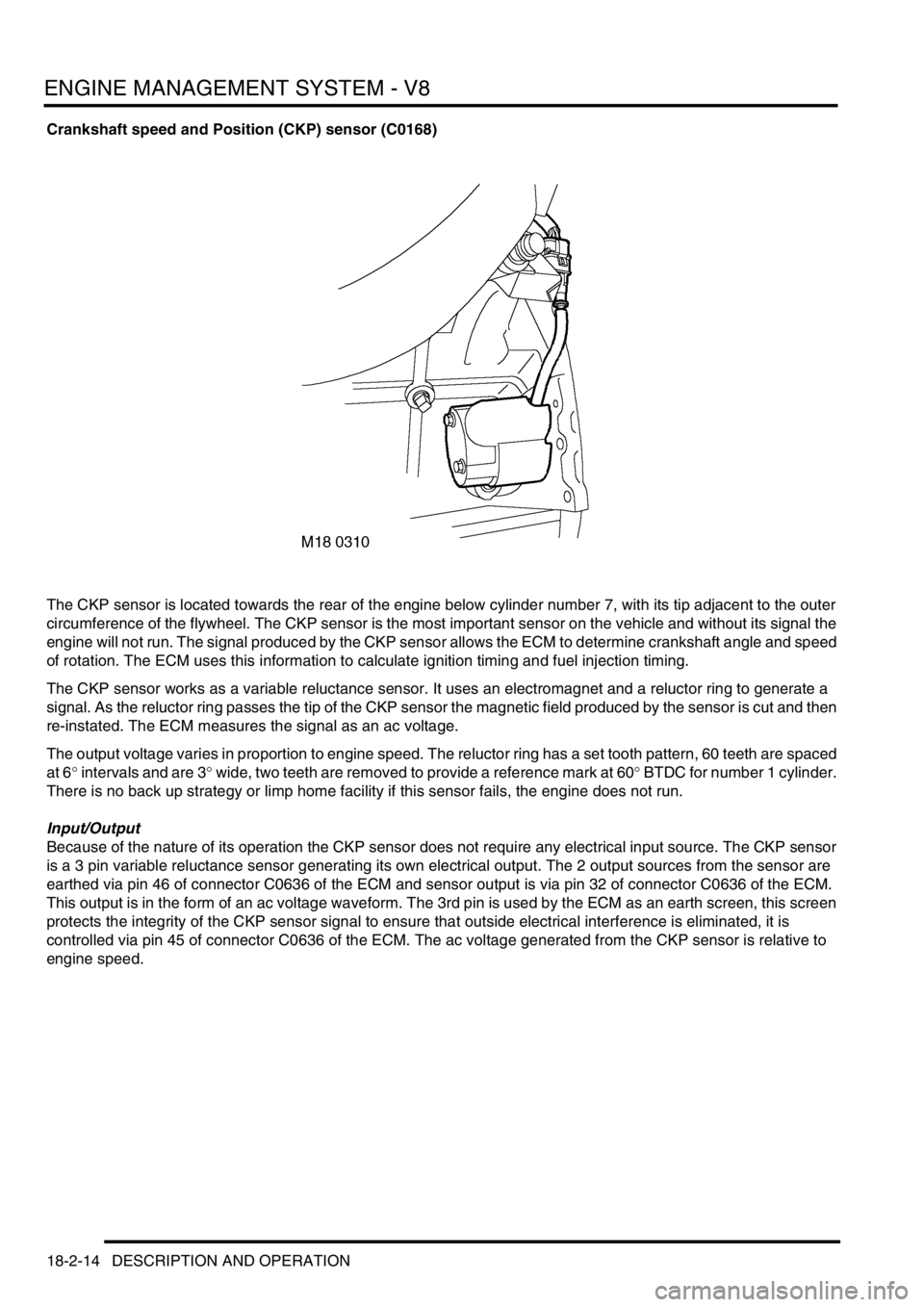
ENGINE MANAGEMENT SYSTEM - V8
18-2-14 DESCRIPTION AND OPERATION
Crankshaft speed and Position (CKP) sensor (C0168)
The CKP sensor is located towards the rear of the engine below cylinder number 7, with its tip adjacent to the outer
circumference of the flywheel. The CKP sensor is the most important sensor on the vehicle and without its signal the
engine will not run. The signal produced by the CKP sensor allows the ECM to determine crankshaft angle and speed
of rotation. The ECM uses this information to calculate ignition timing and fuel injection timing.
The CKP sensor works as a variable reluctance sensor. It uses an electromagnet and a reluctor ring to generate a
signal. As the reluctor ring passes the tip of the CKP sensor the magnetic field produced by the sensor is cut and then
re-instated. The ECM measures the signal as an ac voltage.
The output voltage varies in proportion to engine speed. The reluctor ring has a set tooth pattern, 60 teeth are spaced
at 6° intervals and are 3° wide, two teeth are removed to provide a reference mark at 60° BTDC for number 1 cylinder.
There is no back up strategy or limp home facility if this sensor fails, the engine does not run.
Input/Output
Because of the nature of its operation the CKP sensor does not require any electrical input source. The CKP sensor
is a 3 pin variable reluctance sensor generating its own electrical output. The 2 output sources from the sensor are
earthed via pin 46 of connector C0636 of the ECM and sensor output is via pin 32 of connector C0636 of the ECM.
This output is in the form of an ac voltage waveform. The 3rd pin is used by the ECM as an earth screen, this screen
protects the integrity of the CKP sensor signal to ensure that outside electrical interference is eliminated, it is
controlled via pin 45 of connector C0636 of the ECM. The ac voltage generated from the CKP sensor is relative to
engine speed.
Page 314 of 1529
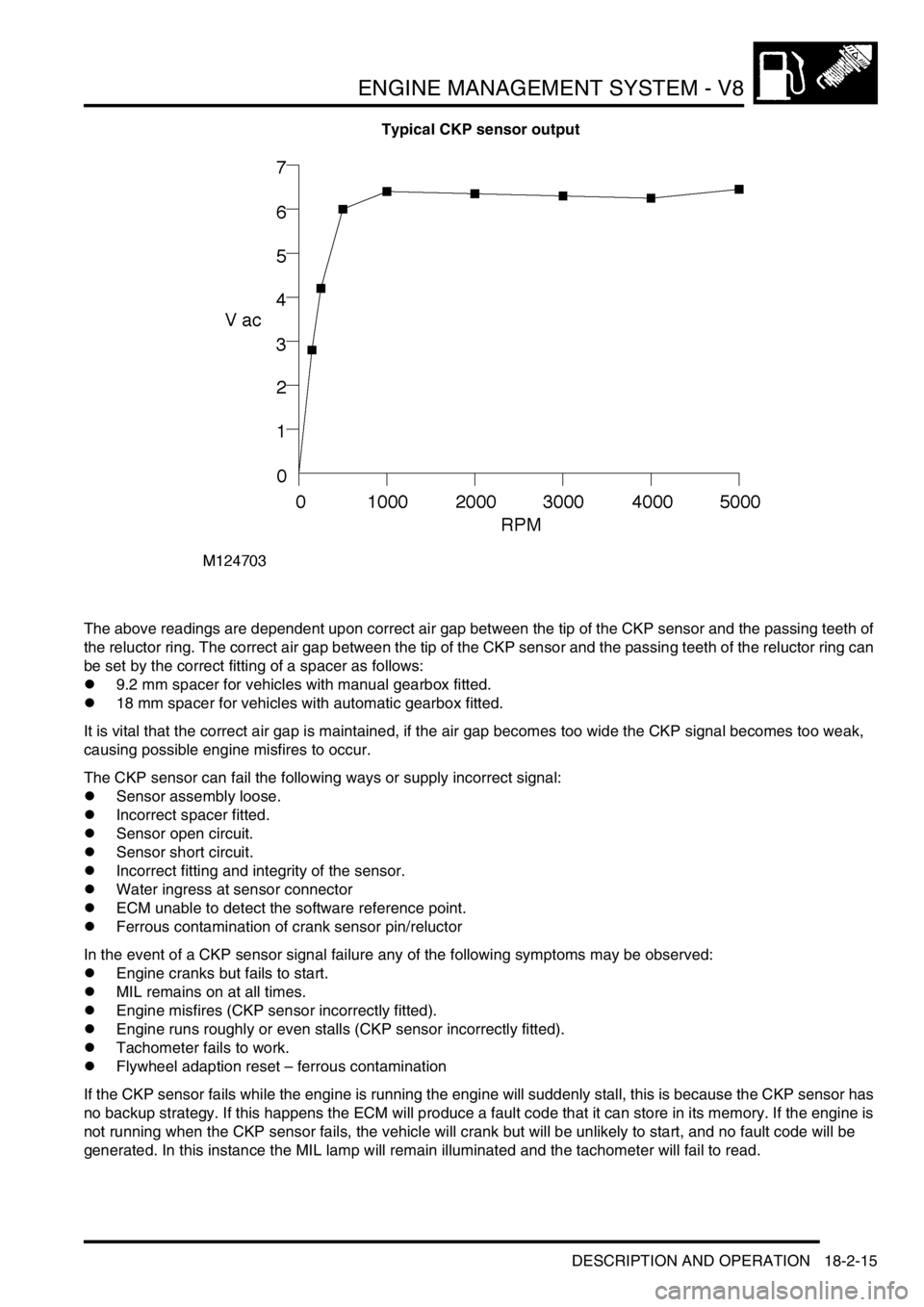
ENGINE MANAGEMENT SYSTEM - V8
DESCRIPTION AND OPERATION 18-2-15
Typical CKP sensor output
The above readings are dependent upon correct air gap between the tip of the CKP sensor and the passing teeth of
the reluctor ring. The correct air gap between the tip of the CKP sensor and the passing teeth of the reluctor ring can
be set by the correct fitting of a spacer as follows:
l9.2 mm spacer for vehicles with manual gearbox fitted.
l18 mm spacer for vehicles with automatic gearbox fitted.
It is vital that the correct air gap is maintained, if the air gap becomes too wide the CKP signal becomes too weak,
causing possible engine misfires to occur.
The CKP sensor can fail the following ways or supply incorrect signal:
lSensor assembly loose.
lIncorrect spacer fitted.
lSensor open circuit.
lSensor short circuit.
lIncorrect fitting and integrity of the sensor.
lWater ingress at sensor connector
lECM unable to detect the software reference point.
lFerrous contamination of crank sensor pin/reluctor
In the event of a CKP sensor signal failure any of the following symptoms may be observed:
lEngine cranks but fails to start.
lMIL remains on at all times.
lEngine misfires (CKP sensor incorrectly fitted).
lEngine runs roughly or even stalls (CKP sensor incorrectly fitted).
lTachometer fails to work.
lFlywheel adaption reset – ferrous contamination
If the CKP sensor fails while the engine is running the engine will suddenly stall, this is because the CKP sensor has
no backup strategy. If this happens the ECM will produce a fault code that it can store in its memory. If the engine is
not running when the CKP sensor fails, the vehicle will crank but will be unlikely to start, and no fault code will be
generated. In this instance the MIL lamp will remain illuminated and the tachometer will fail to read.
Page 315 of 1529
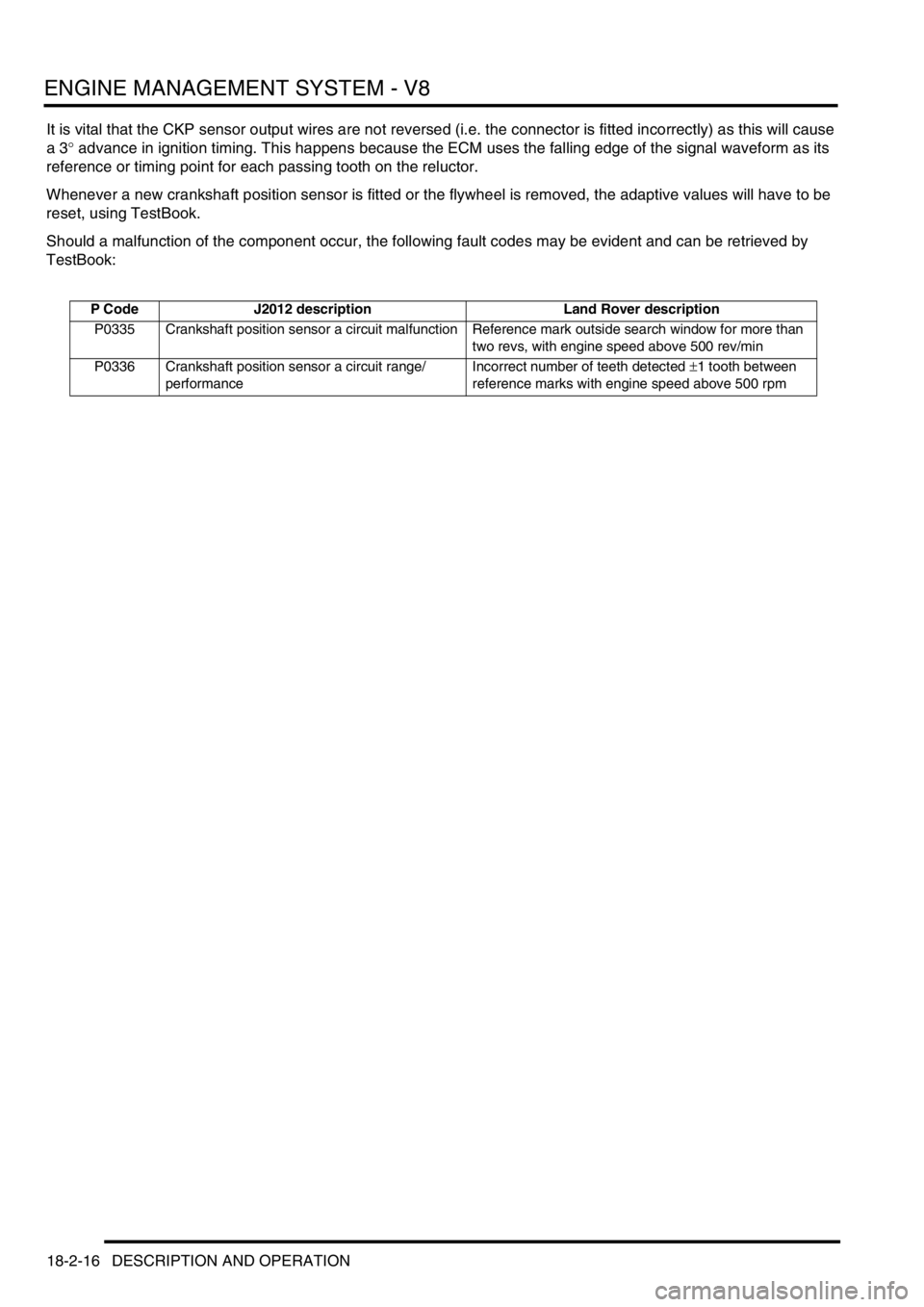
ENGINE MANAGEMENT SYSTEM - V8
18-2-16 DESCRIPTION AND OPERATION
It is vital that the CKP sensor output wires are not reversed (i.e. the connector is fitted incorrectly) as this will cause
a 3° advance in ignition timing. This happens because the ECM uses the falling edge of the signal waveform as its
reference or timing point for each passing tooth on the reluctor.
Whenever a new crankshaft position sensor is fitted or the flywheel is removed, the adaptive values will have to be
reset, using TestBook.
Should a malfunction of the component occur, the following fault codes may be evident and can be retrieved by
TestBook:
P Code J2012 description Land Rover description
P0335 Crankshaft position sensor a circuit malfunction Reference mark outside search window for more than
two revs, with engine speed above 500 rev/min
P0336 Crankshaft position sensor a circuit range/
performanceIncorrect number of teeth detected ±1 tooth between
reference marks with engine speed above 500 rpm
Page 316 of 1529
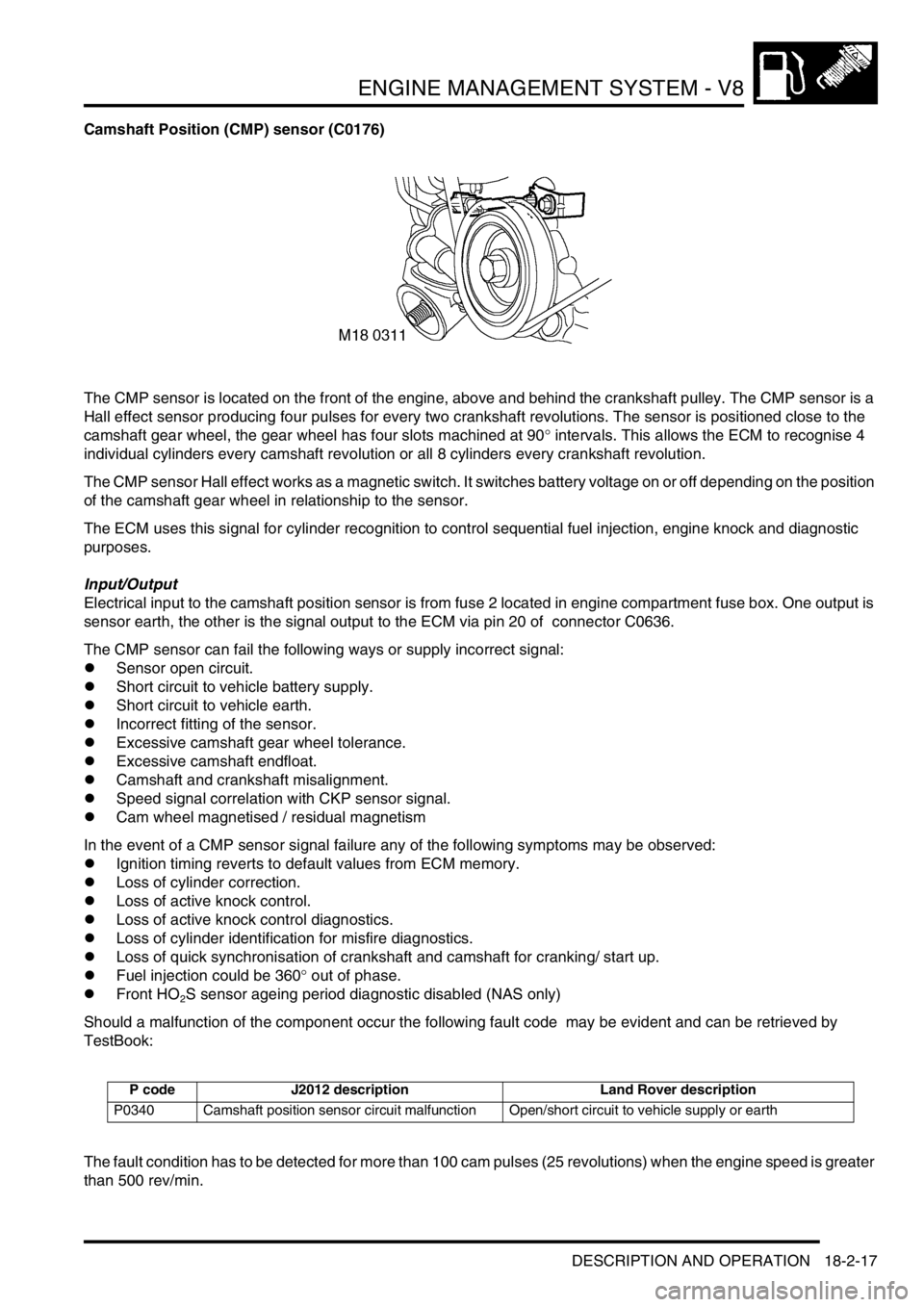
ENGINE MANAGEMENT SYSTEM - V8
DESCRIPTION AND OPERATION 18-2-17
Camshaft Position (CMP) sensor (C0176)
The CMP sensor is located on the front of the engine, above and behind the crankshaft pulley. The CMP sensor is a
Hall effect sensor producing four pulses for every two crankshaft revolutions. The sensor is positioned close to the
camshaft gear wheel, the gear wheel has four slots machined at 90° intervals. This allows the ECM to recognise 4
individual cylinders every camshaft revolution or all 8 cylinders every crankshaft revolution.
The CMP sensor Hall effect works as a magnetic switch. It switches battery voltage on or off depending on the position
of the camshaft gear wheel in relationship to the sensor.
The ECM uses this signal for cylinder recognition to control sequential fuel injection, engine knock and diagnostic
purposes.
Input/Output
Electrical input to the camshaft position sensor is from fuse 2 located in engine compartment fuse box. One output is
sensor earth, the other is the signal output to the ECM via pin 20 of connector C0636.
The CMP sensor can fail the following ways or supply incorrect signal:
lSensor open circuit.
lShort circuit to vehicle battery supply.
lShort circuit to vehicle earth.
lIncorrect fitting of the sensor.
lExcessive camshaft gear wheel tolerance.
lExcessive camshaft endfloat.
lCamshaft and crankshaft misalignment.
lSpeed signal correlation with CKP sensor signal.
lCam wheel magnetised / residual magnetism
In the event of a CMP sensor signal failure any of the following symptoms may be observed:
lIgnition timing reverts to default values from ECM memory.
lLoss of cylinder correction.
lLoss of active knock control.
lLoss of active knock control diagnostics.
lLoss of cylinder identification for misfire diagnostics.
lLoss of quick synchronisation of crankshaft and camshaft for cranking/ start up.
lFuel injection could be 360° out of phase.
lFront HO
2S sensor ageing period diagnostic disabled (NAS only)
Should a malfunction of the component occur the following fault code may be evident and can be retrieved by
TestBook:
The fault condition has to be detected for more than 100 cam pulses (25 revolutions) when the engine speed is greater
than 500 rev/min.
P code J2012 description Land Rover description
P0340 Camshaft position sensor circuit malfunction Open/short circuit to vehicle supply or earth
Page 317 of 1529
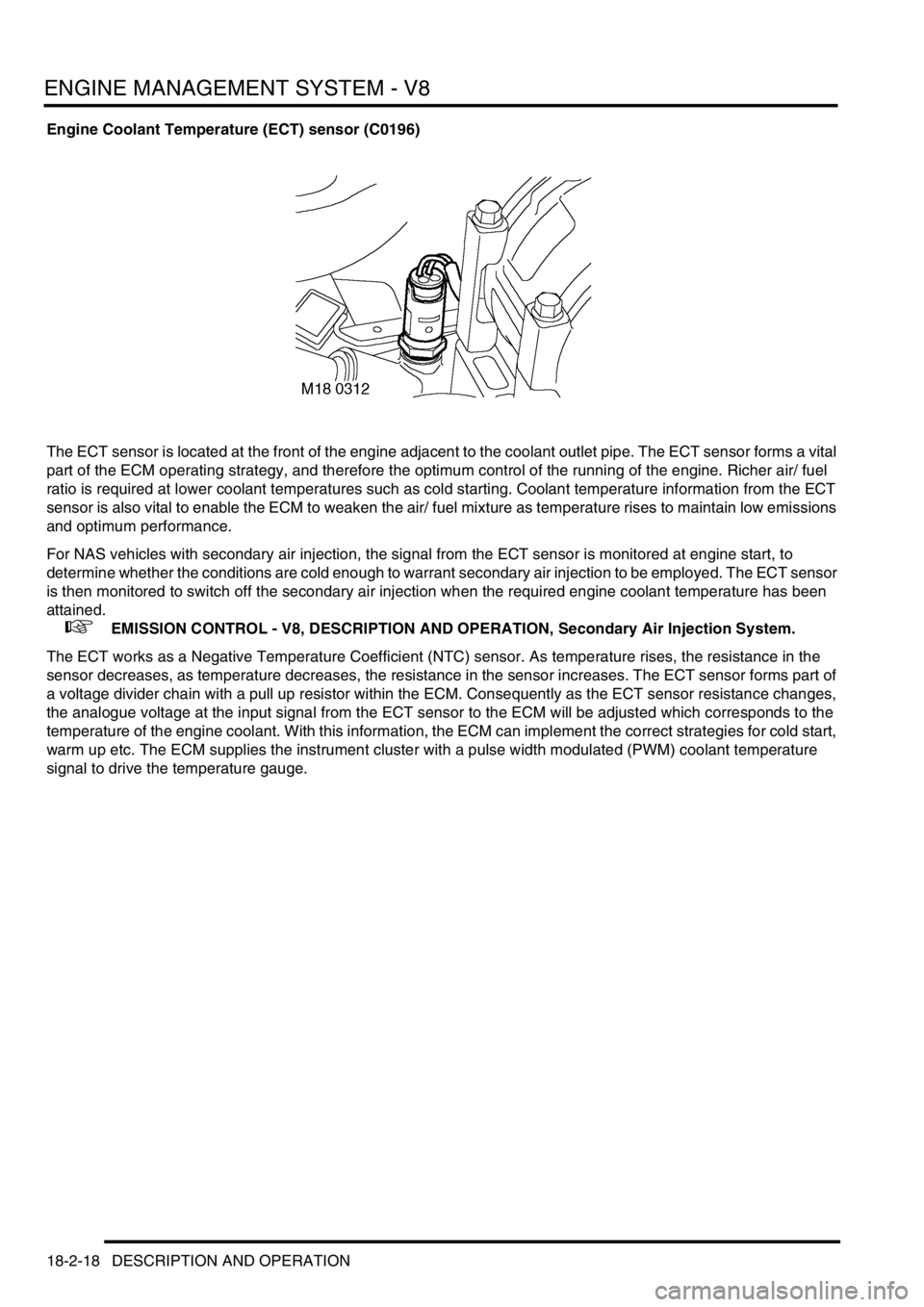
ENGINE MANAGEMENT SYSTEM - V8
18-2-18 DESCRIPTION AND OPERATION
Engine Coolant Temperature (ECT) sensor (C0196)
The ECT sensor is located at the front of the engine adjacent to the coolant outlet pipe. The ECT sensor forms a vital
part of the ECM operating strategy, and therefore the optimum control of the running of the engine. Richer air/ fuel
ratio is required at lower coolant temperatures such as cold starting. Coolant temperature information from the ECT
sensor is also vital to enable the ECM to weaken the air/ fuel mixture as temperature rises to maintain low emissions
and optimum performance.
For NAS vehicles with secondary air injection, the signal from the ECT sensor is monitored at engine start, to
determine whether the conditions are cold enough to warrant secondary air injection to be employed. The ECT sensor
is then monitored to switch off the secondary air injection when the required engine coolant temperature has been
attained.
+ EMISSION CONTROL - V8, DESCRIPTION AND OPERATION, Secondary Air Injection System.
The ECT works as a Negative Temperature Coefficient (NTC) sensor. As temperature rises, the resistance in the
sensor decreases, as temperature decreases, the resistance in the sensor increases. The ECT sensor forms part of
a voltage divider chain with a pull up resistor within the ECM. Consequently as the ECT sensor resistance changes,
the analogue voltage at the input signal from the ECT sensor to the ECM will be adjusted which corresponds to the
temperature of the engine coolant. With this information, the ECM can implement the correct strategies for cold start,
warm up etc. The ECM supplies the instrument cluster with a pulse width modulated (PWM) coolant temperature
signal to drive the temperature gauge.
Page 318 of 1529
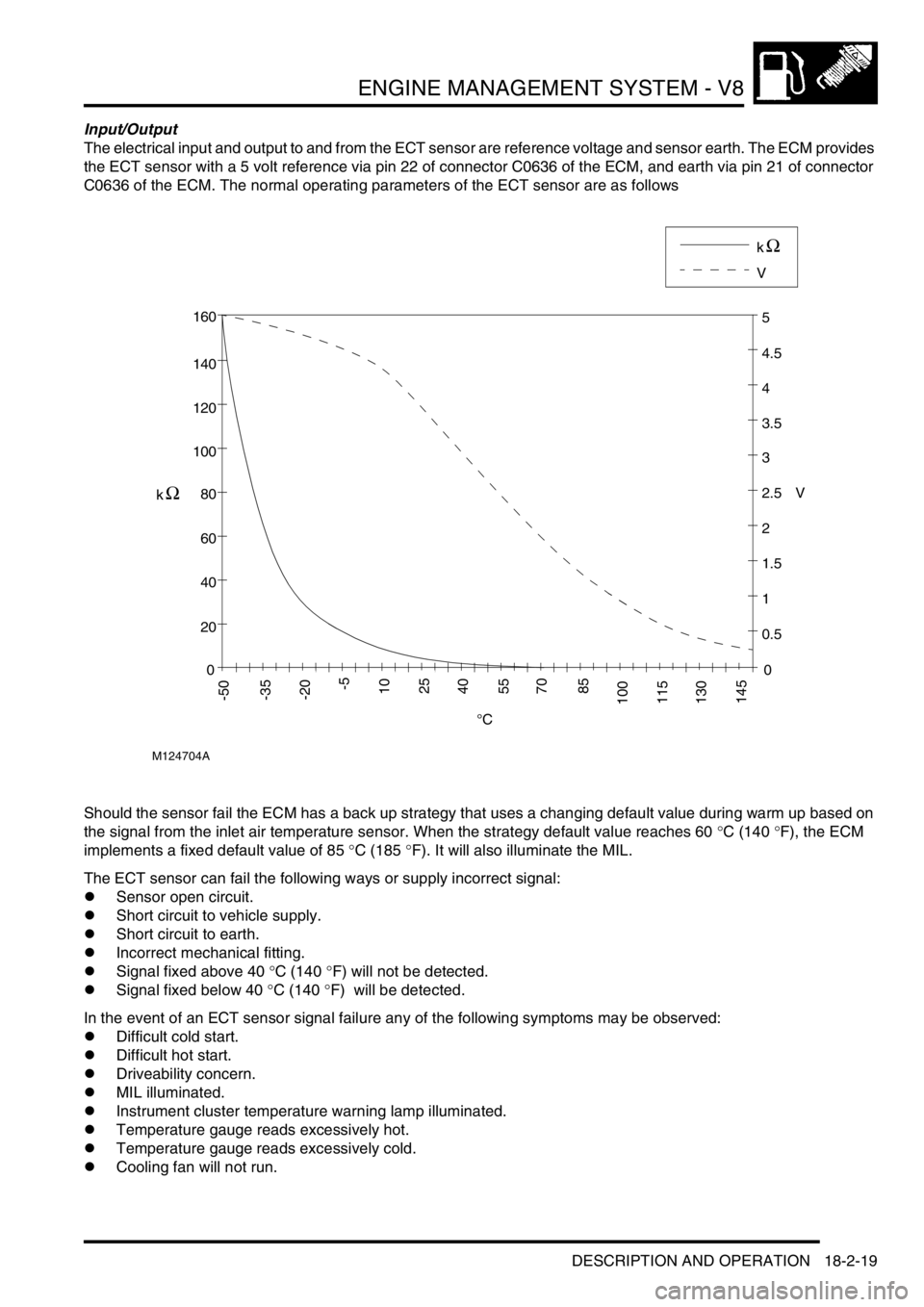
ENGINE MANAGEMENT SYSTEM - V8
DESCRIPTION AND OPERATION 18-2-19
Input/Output
The electrical input and output to and from the ECT sensor are reference voltage and sensor earth. The ECM provides
the ECT sensor with a 5 volt reference via pin 22 of connector C0636 of the ECM, and earth via pin 21 of connector
C0636 of the ECM. The normal operating parameters of the ECT sensor are as follows
Should the sensor fail the ECM has a back up strategy that uses a changing default value during warm up based on
the signal from the inlet air temperature sensor. When the strategy default value reaches 60 °C (140 °F), the ECM
implements a fixed default value of 85 °C (185 °F). It will also illuminate the MIL.
The ECT sensor can fail the following ways or supply incorrect signal:
lSensor open circuit.
lShort circuit to vehicle supply.
lShort circuit to earth.
lIncorrect mechanical fitting.
lSignal fixed above 40 °C (140 °F) will not be detected.
lSignal fixed below 40 °C (140 °F) will be detected.
In the event of an ECT sensor signal failure any of the following symptoms may be observed:
lDifficult cold start.
lDifficult hot start.
lDriveability concern.
lMIL illuminated.
lInstrument cluster temperature warning lamp illuminated.
lTemperature gauge reads excessively hot.
lTemperature gauge reads excessively cold.
lCooling fan will not run.
M124704A
0
20
40
60
80
100
120
140
160
0
0.5
1
1.5
2
2.5
3
3.5
4
4.5
5
VkΩ
kΩ
V
°C
145-50-35-20-5102540557085100115130
Page 319 of 1529
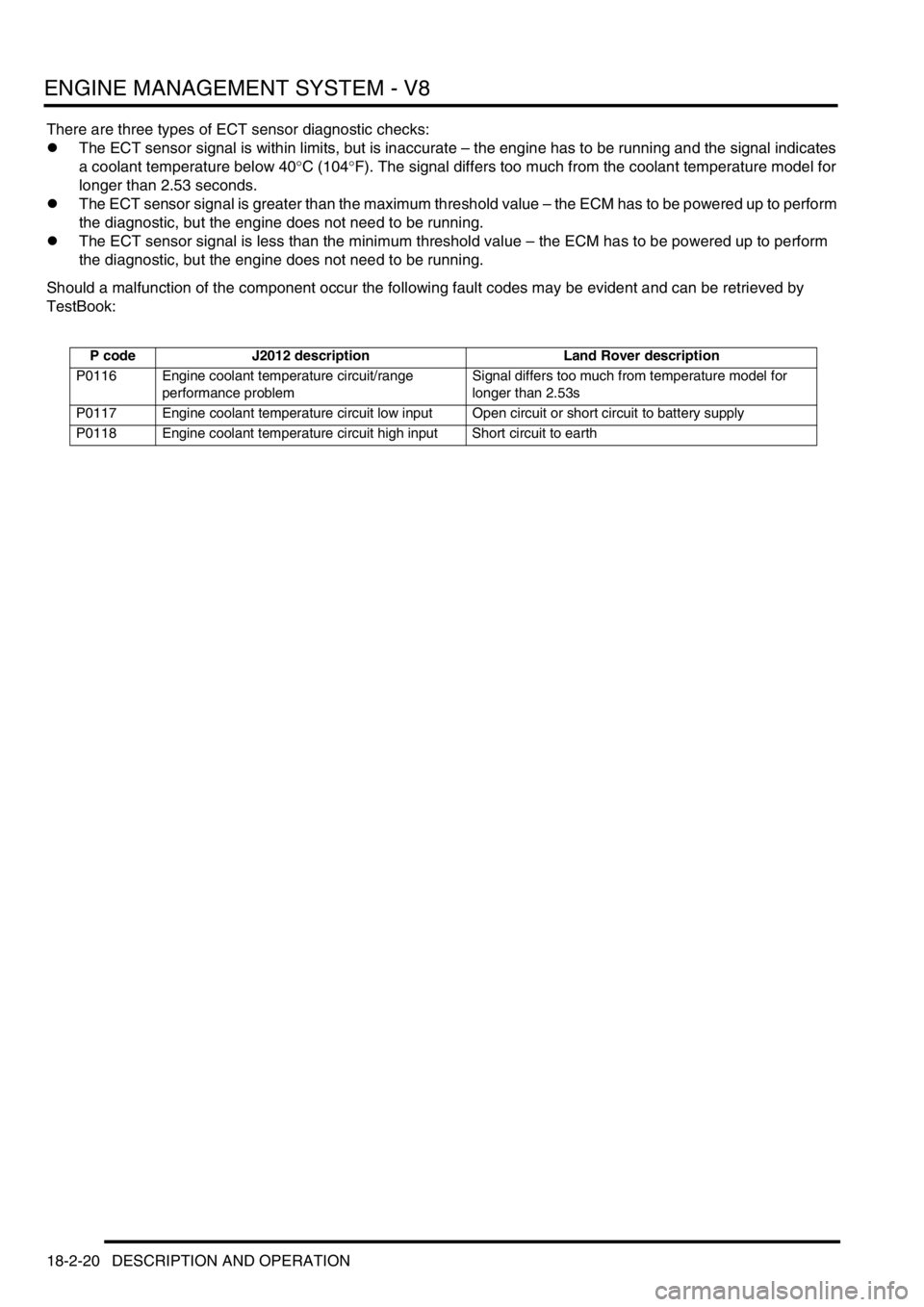
ENGINE MANAGEMENT SYSTEM - V8
18-2-20 DESCRIPTION AND OPERATION
There are three types of ECT sensor diagnostic checks:
lThe ECT sensor signal is within limits, but is inaccurate – the engine has to be running and the signal indicates
a coolant temperature below 40°C (104°F). The signal differs too much from the coolant temperature model for
longer than 2.53 seconds.
lThe ECT sensor signal is greater than the maximum threshold value – the ECM has to be powered up to perform
the diagnostic, but the engine does not need to be running.
lThe ECT sensor signal is less than the minimum threshold value – the ECM has to be powered up to perform
the diagnostic, but the engine does not need to be running.
Should a malfunction of the component occur the following fault codes may be evident and can be retrieved by
TestBook:
P code J2012 description Land Rover description
P0116 Engine coolant temperature circuit/range
performance problemSignal differs too much from temperature model for
longer than 2.53s
P0117 Engine coolant temperature circuit low input Open circuit or short circuit to battery supply
P0118 Engine coolant temperature circuit high input Short circuit to earth
Page 320 of 1529
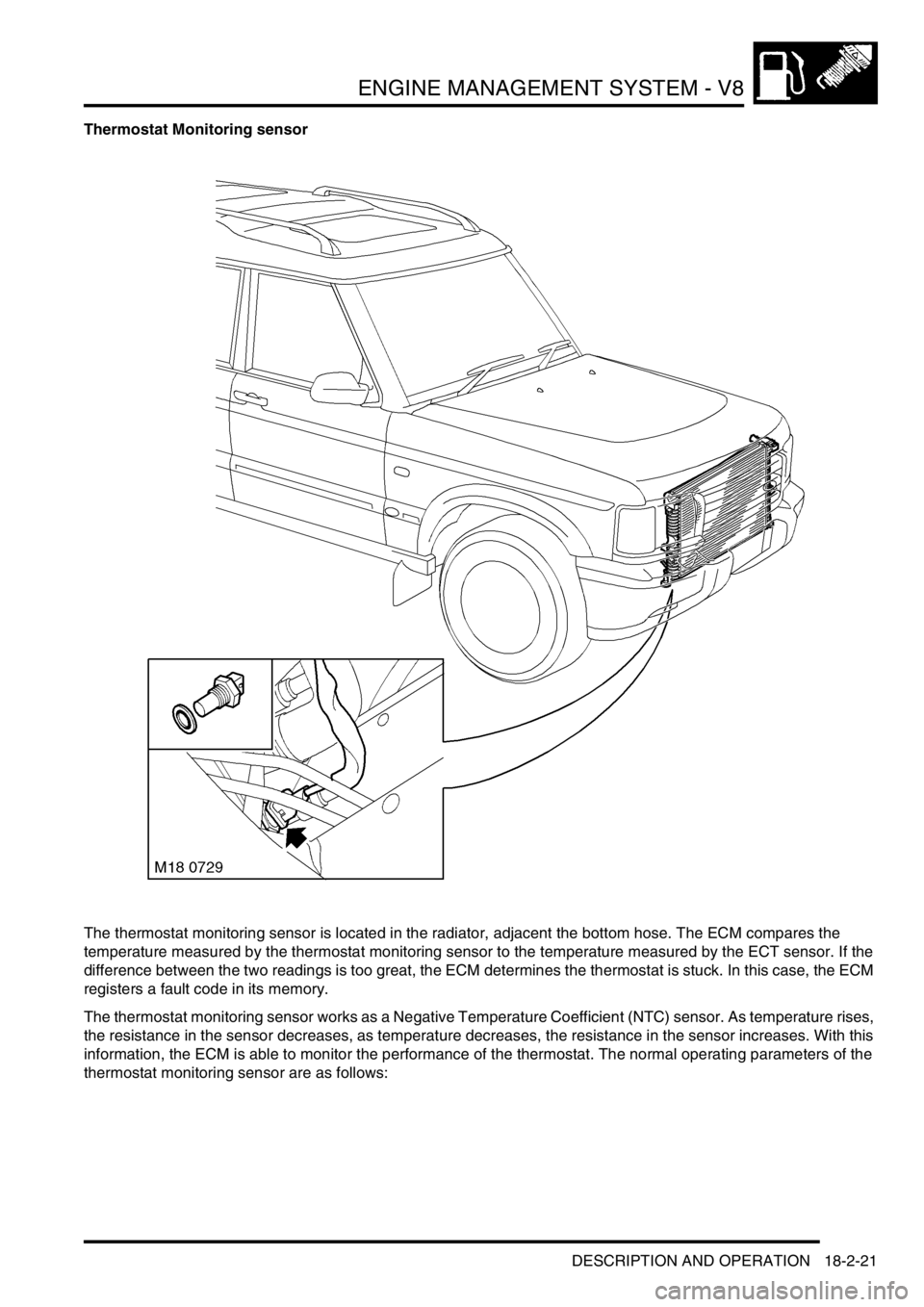
ENGINE MANAGEMENT SYSTEM - V8
DESCRIPTION AND OPERATION 18-2-21
Thermostat Monitoring sensor
The thermostat monitoring sensor is located in the radiator, adjacent the bottom hose. The ECM compares the
temperature measured by the thermostat monitoring sensor to the temperature measured by the ECT sensor. If the
difference between the two readings is too great, the ECM determines the thermostat is stuck. In this case, the ECM
registers a fault code in its memory.
The thermostat monitoring sensor works as a Negative Temperature Coefficient (NTC) sensor. As temperature rises,
the resistance in the sensor decreases, as temperature decreases, the resistance in the sensor increases. With this
information, the ECM is able to monitor the performance of the thermostat. The normal operating parameters of the
thermostat monitoring sensor are as follows: