remote control LAND ROVER DISCOVERY 2002 User Guide
[x] Cancel search | Manufacturer: LAND ROVER, Model Year: 2002, Model line: DISCOVERY, Model: LAND ROVER DISCOVERY 2002Pages: 1672, PDF Size: 46.1 MB
Page 893 of 1672
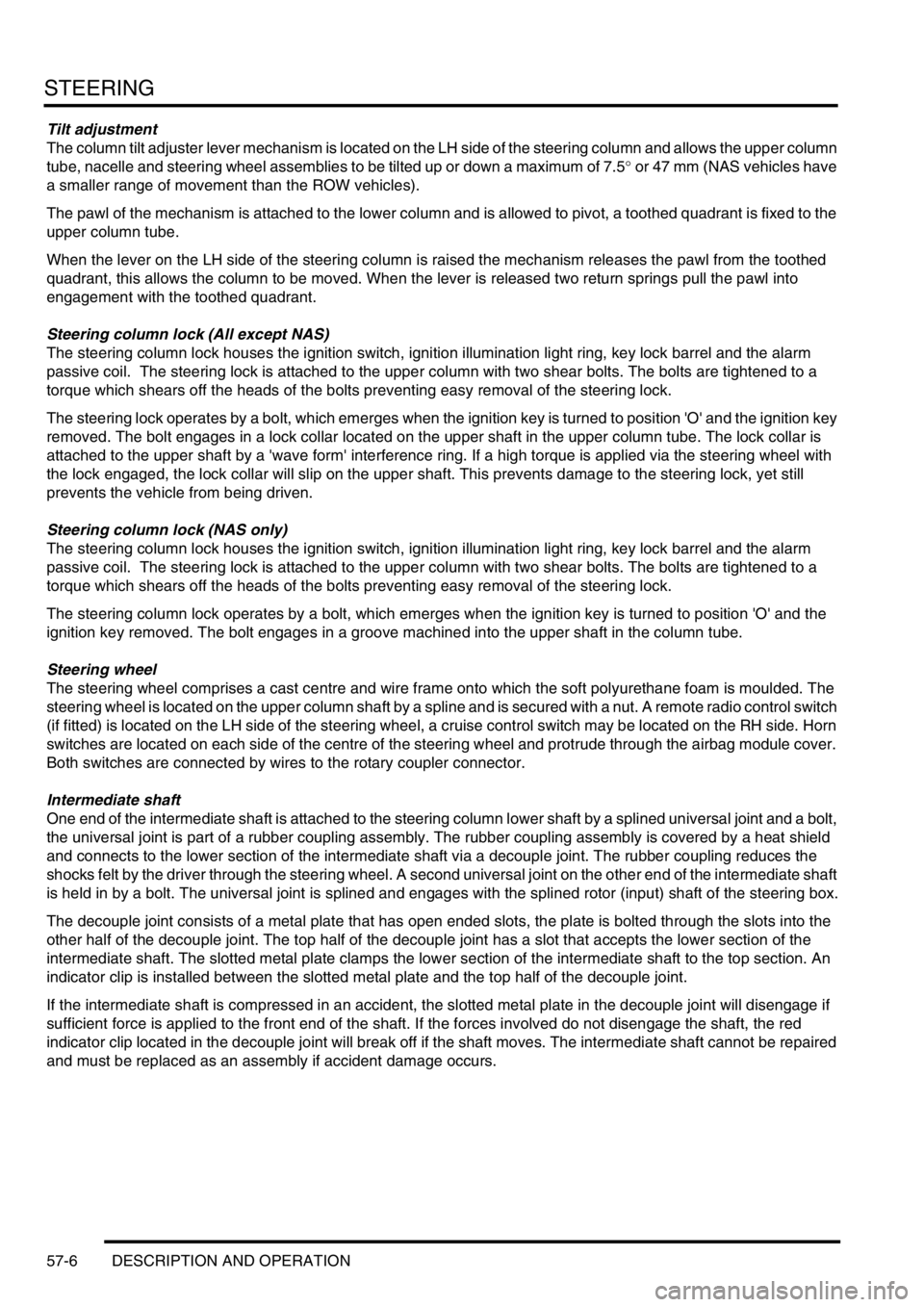
STEERING
57-6 DESCRIPTION AND OPERATION
Tilt adjustment
The column tilt adjuster lever mechanism is located on the LH side of the steering column and allows the upper column
tube, nacelle and steering wheel assemblies to be tilted up or down a maximum of 7.5
° or 47 mm (NAS vehicles have
a smaller range of movement than the ROW vehicles).
The pawl of the mechanism is attached to the lower column and is allowed to pivot, a toothed quadrant is fixed to the
upper column tube.
When the lever on the LH side of the steering column is raised the mechanism releases the pawl from the toothed
quadrant, this allows the column to be moved. When the lever is released two return springs pull the pawl into
engagement with the toothed quadrant.
Steering column lock (All except NAS)
The steering column lock houses the ignition switch, ignition illumination light ring, key lock barrel and the alarm
passive coil. The steering lock is attached to the upper column with two shear bolts. The bolts are tightened to a
torque which shears off the heads of the bolts preventing easy removal of the steering lock.
The steering lock operates by a bolt, which emerges when the ignition key is turned to position 'O' and the ignition key
removed. The bolt engages in a lock collar located on the upper shaft in the upper column tube. The lock collar is
attached to the upper shaft by a 'wave form' interference ring. If a high torque is applied via the steering wheel with
the lock engaged, the lock collar will slip on the upper shaft. This prevents damage to the steering lock, yet still
prevents the vehicle from being driven.
Steering column lock (NAS only)
The steering column lock houses the ignition switch, ignition illumination light ring, key lock barrel and the alarm
passive coil. The steering lock is attached to the upper column with two shear bolts. The bolts are tightened to a
torque which shears off the heads of the bolts preventing easy removal of the steering lock.
The steering column lock operates by a bolt, which emerges when the ignition key is turned to position 'O' and the
ignition key removed. The bolt engages in a groove machined into the upper shaft in the column tube.
Steering wheel
The steering wheel comprises a cast centre and wire frame onto which the soft polyurethane foam is moulded. The
steering wheel is located on the upper column shaft by a spline and is secured with a nut. A remote radio control switch
(if fitted) is located on the LH side of the steering wheel, a cruise control switch may be located on the RH side. Horn
switches are located on each side of the centre of the steering wheel and protrude through the airbag module cover.
Both switches are connected by wires to the rotary coupler connector.
Intermediate shaft
One end of the intermediate shaft is attached to the steering column lower shaft by a splined universal joint and a bolt,
the universal joint is part of a rubber coupling assembly. The rubber coupling assembly is covered by a heat shield
and connects to the lower section of the intermediate shaft via a decouple joint. The rubber coupling reduces the
shocks felt by the driver through the steering wheel. A second universal joint on the other end of the intermediate shaft
is held in by a bolt. The universal joint is splined and engages with the splined rotor (input) shaft of the steering box.
The decouple joint consists of a metal plate that has open ended slots, the plate is bolted through the slots into the
other half of the decouple joint. The top half of the decouple joint has a slot that accepts the lower section of the
intermediate shaft. The slotted metal plate clamps the lower section of the intermediate shaft to the top section. An
indicator clip is installed between the slotted metal plate and the top half of the decouple joint.
If the intermediate shaft is compressed in an accident, the slotted metal plate in the decouple joint will disengage if
sufficient force is applied to the front end of the shaft. If the forces involved do not disengage the shaft, the red
indicator clip located in the decouple joint will break off if the shaft moves. The intermediate shaft cannot be repaired
and must be replaced as an assembly if accident damage occurs.
Page 1016 of 1672
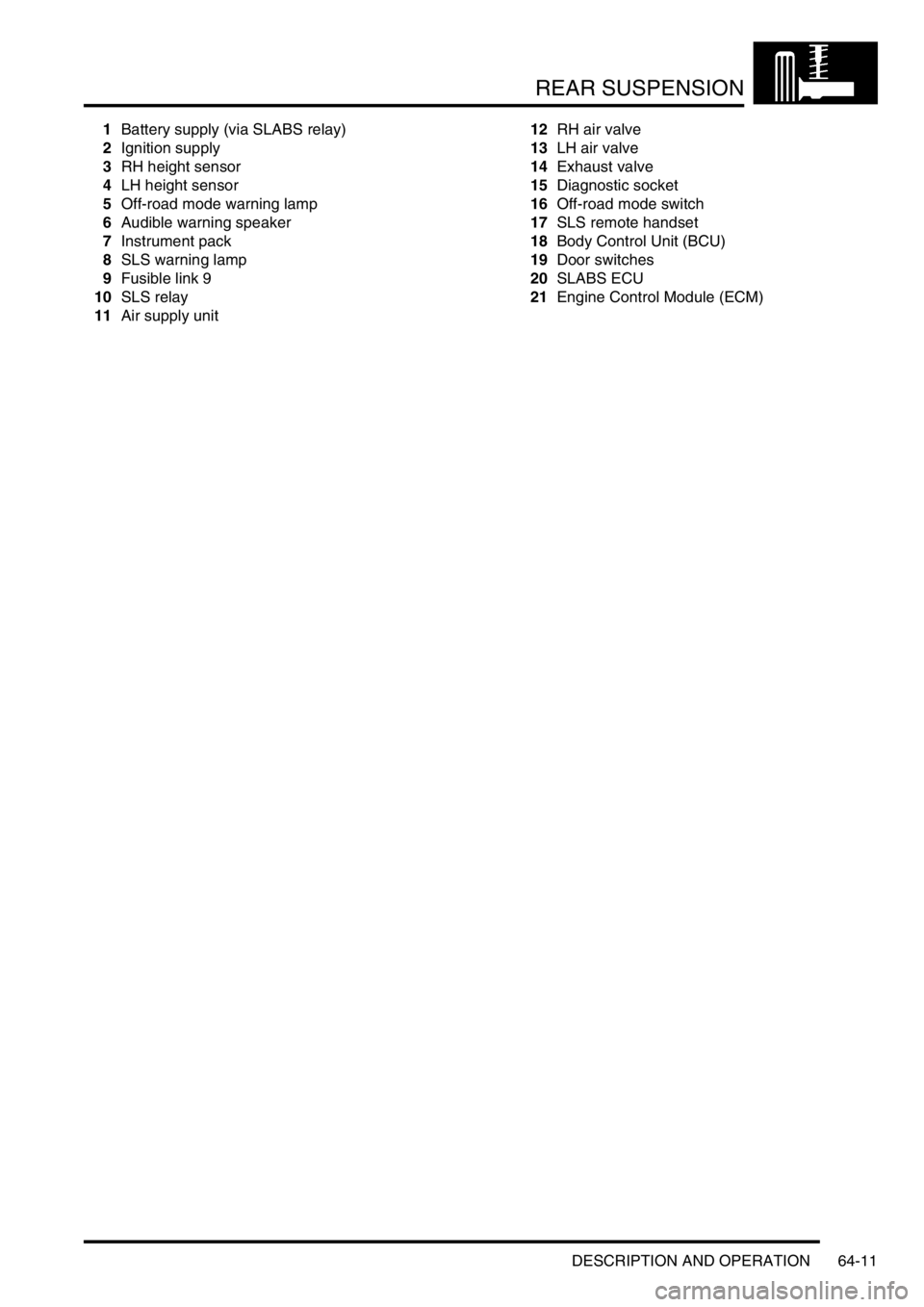
REAR SUSPENSION
DESCRIPTION AND OPERATION 64-11
1Battery supply (via SLABS relay)
2Ignition supply
3RH height sensor
4LH height sensor
5Off-road mode warning lamp
6Audible warning speaker
7Instrument pack
8SLS warning lamp
9Fusible link 9
10SLS relay
11Air supply unit12RH air valve
13LH air valve
14Exhaust valve
15Diagnostic socket
16Off-road mode switch
17SLS remote handset
18Body Control Unit (BCU)
19Door switches
20SLABS ECU
21Engine Control Module (ECM)
Page 1017 of 1672
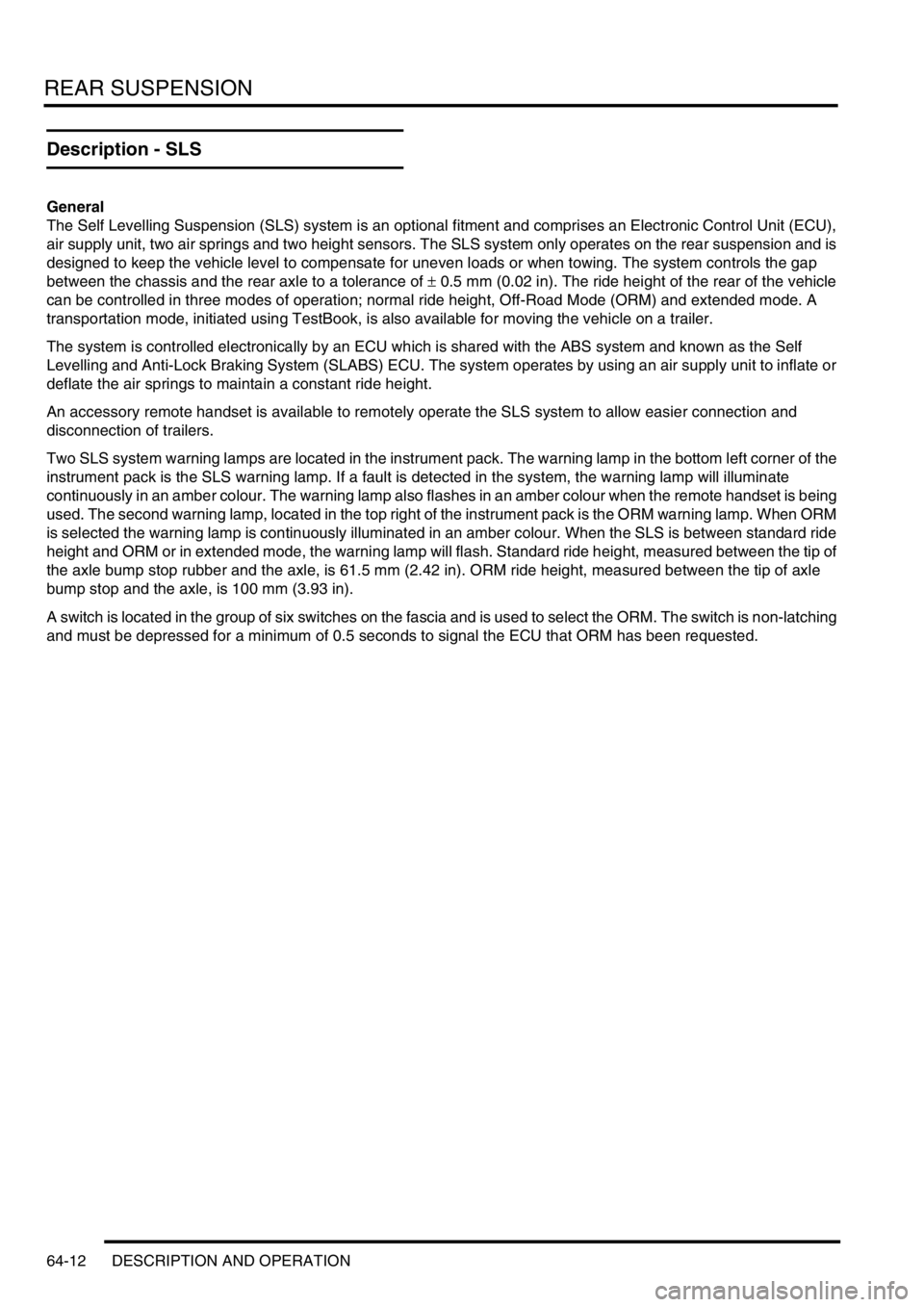
REAR SUSPENSION
64-12 DESCRIPTION AND OPERATION
Description - SLS
General
The Self Levelling Suspension (SLS) system is an optional fitment and comprises an Electronic Control Unit (ECU),
air supply unit, two air springs and two height sensors. The SLS system only operates on the rear suspension and is
designed to keep the vehicle level to compensate for uneven loads or when towing. The system controls the gap
between the chassis and the rear axle to a tolerance of
± 0.5 mm (0.02 in). The ride height of the rear of the vehicle
can be controlled in three modes of operation; normal ride height, Off-Road Mode (ORM) and extended mode. A
transportation mode, initiated using TestBook, is also available for moving the vehicle on a trailer.
The system is controlled electronically by an ECU which is shared with the ABS system and known as the Self
Levelling and Anti-Lock Braking System (SLABS) ECU. The system operates by using an air supply unit to inflate or
deflate the air springs to maintain a constant ride height.
An accessory remote handset is available to remotely operate the SLS system to allow easier connection and
disconnection of trailers.
Two SLS system warning lamps are located in the instrument pack. The warning lamp in the bottom left corner of the
instrument pack is the SLS warning lamp. If a fault is detected in the system, the warning lamp will illuminate
continuously in an amber colour. The warning lamp also flashes in an amber colour when the remote handset is being
used. The second warning lamp, located in the top right of the instrument pack is the ORM warning lamp. When ORM
is selected the warning lamp is continuously illuminated in an amber colour. When the SLS is between standard ride
height and ORM or in extended mode, the warning lamp will flash. Standard ride height, measured between the tip of
the axle bump stop rubber and the axle, is 61.5 mm (2.42 in). ORM ride height, measured between the tip of axle
bump stop and the axle, is 100 mm (3.93 in).
A switch is located in the group of six switches on the fascia and is used to select the ORM. The switch is non-latching
and must be depressed for a minimum of 0.5 seconds to signal the ECU that ORM has been requested.
Page 1023 of 1672
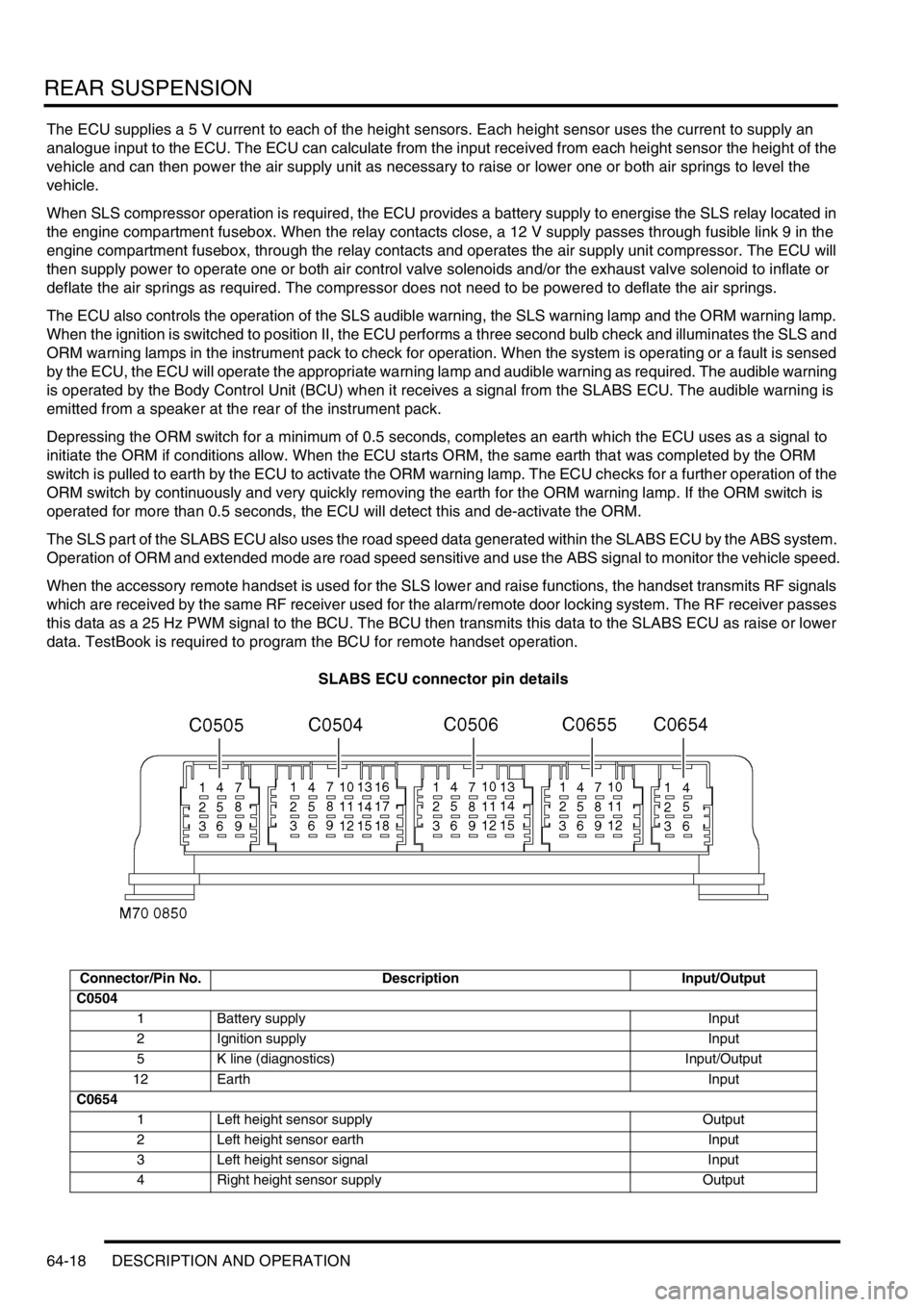
REAR SUSPENSION
64-18 DESCRIPTION AND OPERATION
The ECU supplies a 5 V current to each of the height sensors. Each height sensor uses the current to supply an
analogue input to the ECU. The ECU can calculate from the input received from each height sensor the height of the
vehicle and can then power the air supply unit as necessary to raise or lower one or both air springs to level the
vehicle.
When SLS compressor operation is required, the ECU provides a battery supply to energise the SLS relay located in
the engine compartment fusebox. When the relay contacts close, a 12 V supply passes through fusible link 9 in the
engine compartment fusebox, through the relay contacts and operates the air supply unit compressor. The ECU will
then supply power to operate one or both air control valve solenoids and/or the exhaust valve solenoid to inflate or
deflate the air springs as required. The compressor does not need to be powered to deflate the air springs.
The ECU also controls the operation of the SLS audible warning, the SLS warning lamp and the ORM warning lamp.
When the ignition is switched to position II, the ECU performs a three second bulb check and illuminates the SLS and
ORM warning lamps in the instrument pack to check for operation. When the system is operating or a fault is sensed
by the ECU, the ECU will operate the appropriate warning lamp and audible warning as required. The audible warning
is operated by the Body Control Unit (BCU) when it receives a signal from the SLABS ECU. The audible warning is
emitted from a speaker at the rear of the instrument pack.
Depressing the ORM switch for a minimum of 0.5 seconds, completes an earth which the ECU uses as a signal to
initiate the ORM if conditions allow. When the ECU starts ORM, the same earth that was completed by the ORM
switch is pulled to earth by the ECU to activate the ORM warning lamp. The ECU checks for a further operation of the
ORM switch by continuously and very quickly removing the earth for the ORM warning lamp. If the ORM switch is
operated for more than 0.5 seconds, the ECU will detect this and de-activate the ORM.
The SLS part of the SLABS ECU also uses the road speed data generated within the SLABS ECU by the ABS system.
Operation of ORM and extended mode are road speed sensitive and use the ABS signal to monitor the vehicle speed.
When the accessory remote handset is used for the SLS lower and raise functions, the handset transmits RF signals
which are received by the same RF receiver used for the alarm/remote door locking system. The RF receiver passes
this data as a 25 Hz PWM signal to the BCU. The BCU then transmits this data to the SLABS ECU as raise or lower
data. TestBook is required to program the BCU for remote handset operation.
SLABS ECU connector pin details
Connector/Pin No. Description Input/Output
C0504
1 Battery supply Input
2 Ignition supply Input
5 K line (diagnostics) Input/Output
12 EarthInput
C0654
1 Left height sensor supply Output
2 Left height sensor earth Input
3 Left height sensor signal Input
4 Right height sensor supply Output
Page 1024 of 1672
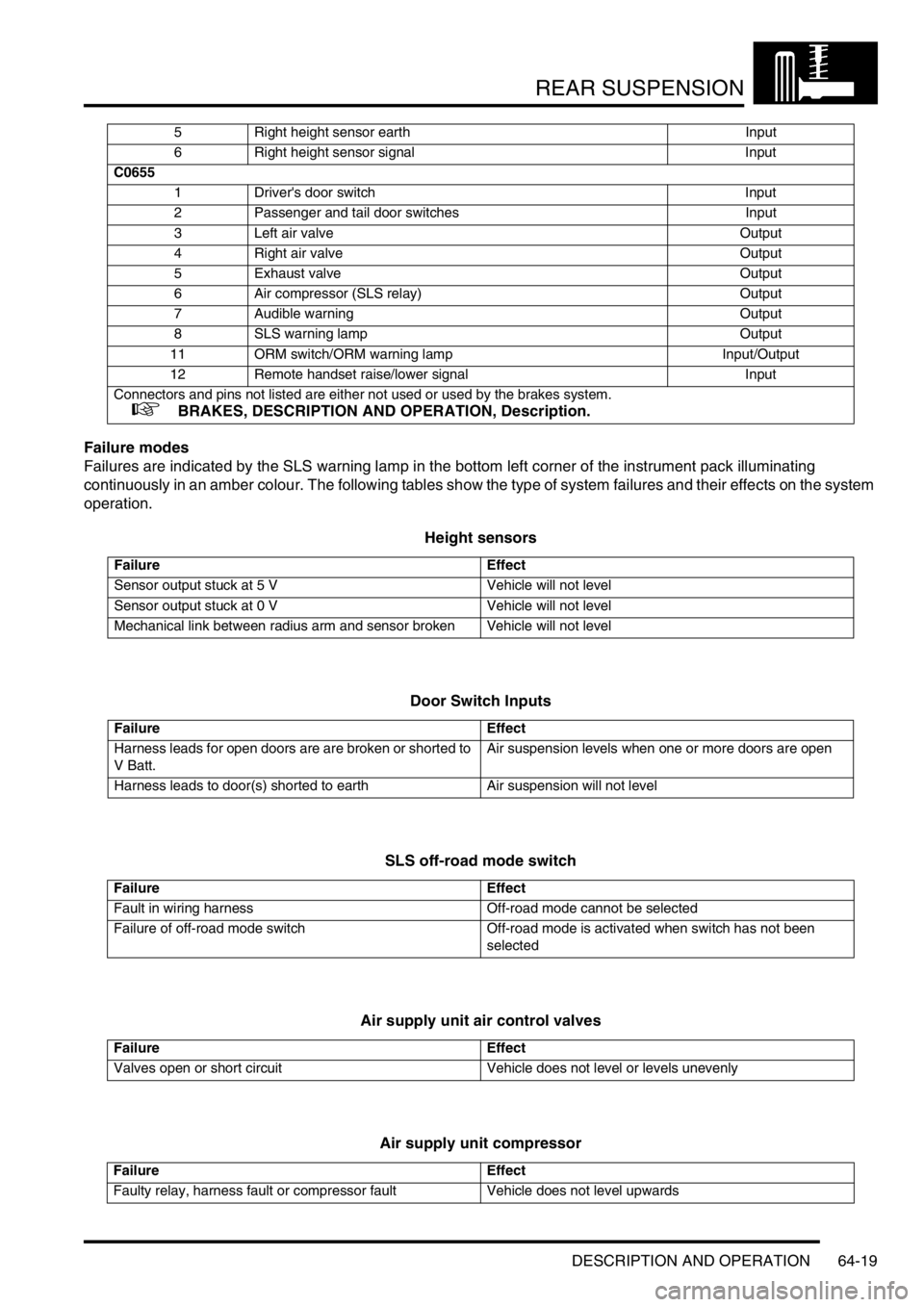
REAR SUSPENSION
DESCRIPTION AND OPERATION 64-19
Failure modes
Failures are indicated by the SLS warning lamp in the bottom left corner of the instrument pack illuminating
continuously in an amber colour. The following tables show the type of system failures and their effects on the system
operation.
Height sensors
Door Switch Inputs
SLS off-road mode switch
Air supply unit air control valves
Air supply unit compressor
5 Right height sensor earth Input
6 Right height sensor signal Input
C0655
1 Driver's door switch Input
2 Passenger and tail door switches Input
3 Left air valve Output
4 Right air valve Output
5 Exhaust valve Output
6 Air compressor (SLS relay) Output
7 Audible warning Output
8 SLS warning lamp Output
11 ORM switch/ORM warning lamp Input/Output
12 Remote handset raise/lower signal Input
Connectors and pins not listed are either not used or used by the brakes system.
+ BRAKES, DESCRIPTION AND OPERATION, Description.
Failure Effect
Sensor output stuck at 5 V Vehicle will not level
Sensor output stuck at 0 V Vehicle will not level
Mechanical link between radius arm and sensor broken Vehicle will not level
Failure Effect
Harness leads for open doors are are broken or shorted to
V Batt.Air suspension levels when one or more doors are open
Harness leads to door(s) shorted to earth Air suspension will not level
Failure Effect
Fault in wiring harness Off-road mode cannot be selected
Failure of off-road mode switch Off-road mode is activated when switch has not been
selected
Failure Effect
Valves open or short circuit Vehicle does not level or levels unevenly
Failure Effect
Faulty relay, harness fault or compressor fault Vehicle does not level upwards
Page 1025 of 1672
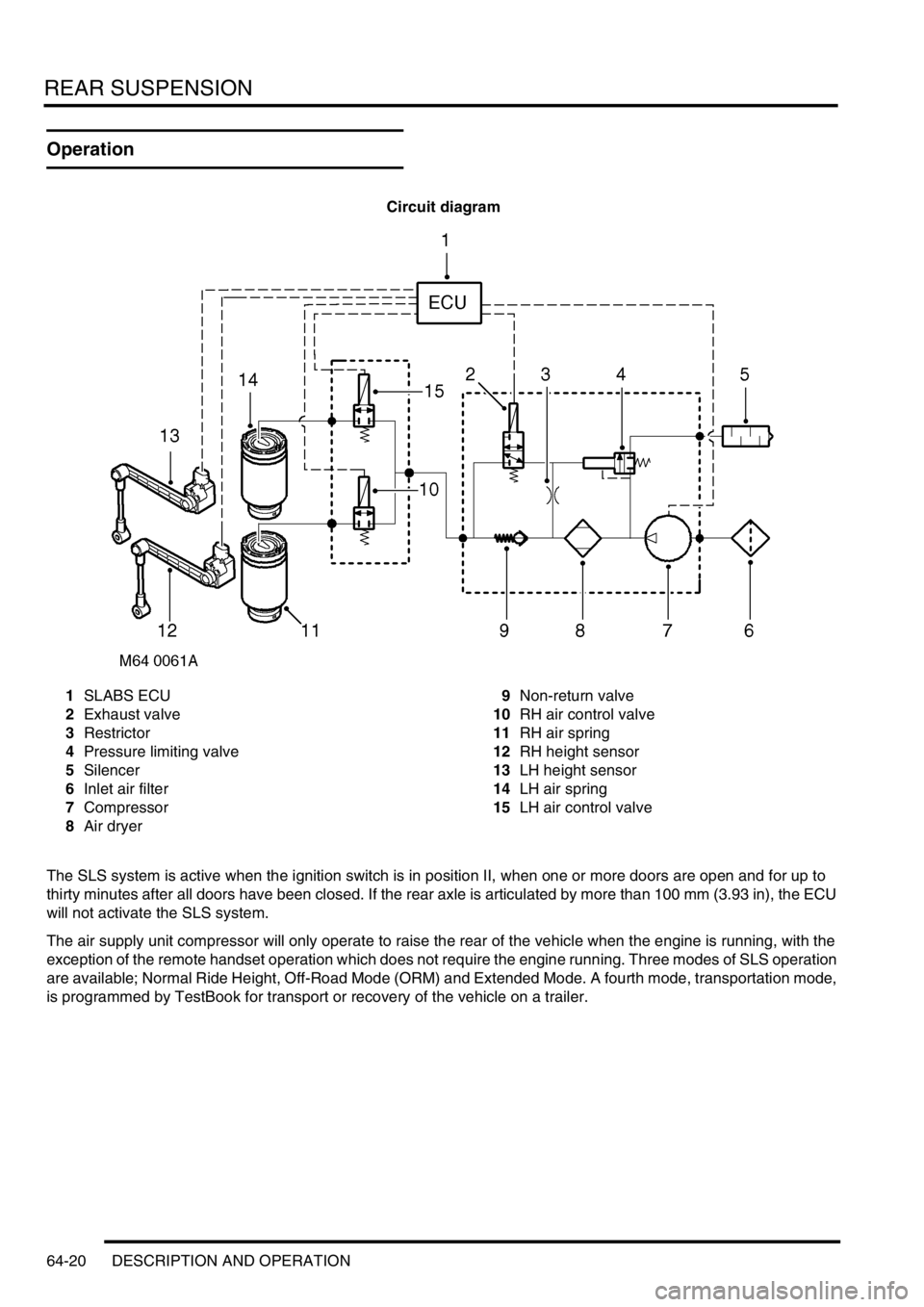
REAR SUSPENSION
64-20 DESCRIPTION AND OPERATION
Operation
Circuit diagram
1SLABS ECU
2Exhaust valve
3Restrictor
4Pressure limiting valve
5Silencer
6Inlet air filter
7Compressor
8Air dryer9Non-return valve
10RH air control valve
11RH air spring
12RH height sensor
13LH height sensor
14LH air spring
15LH air control valve
The SLS system is active when the ignition switch is in position II, when one or more doors are open and for up to
thirty minutes after all doors have been closed. If the rear axle is articulated by more than 100 mm (3.93 in), the ECU
will not activate the SLS system.
The air supply unit compressor will only operate to raise the rear of the vehicle when the engine is running, with the
exception of the remote handset operation which does not require the engine running. Three modes of SLS operation
are available; Normal Ride Height, Off-Road Mode (ORM) and Extended Mode. A fourth mode, transportation mode,
is programmed by TestBook for transport or recovery of the vehicle on a trailer.
Page 1026 of 1672
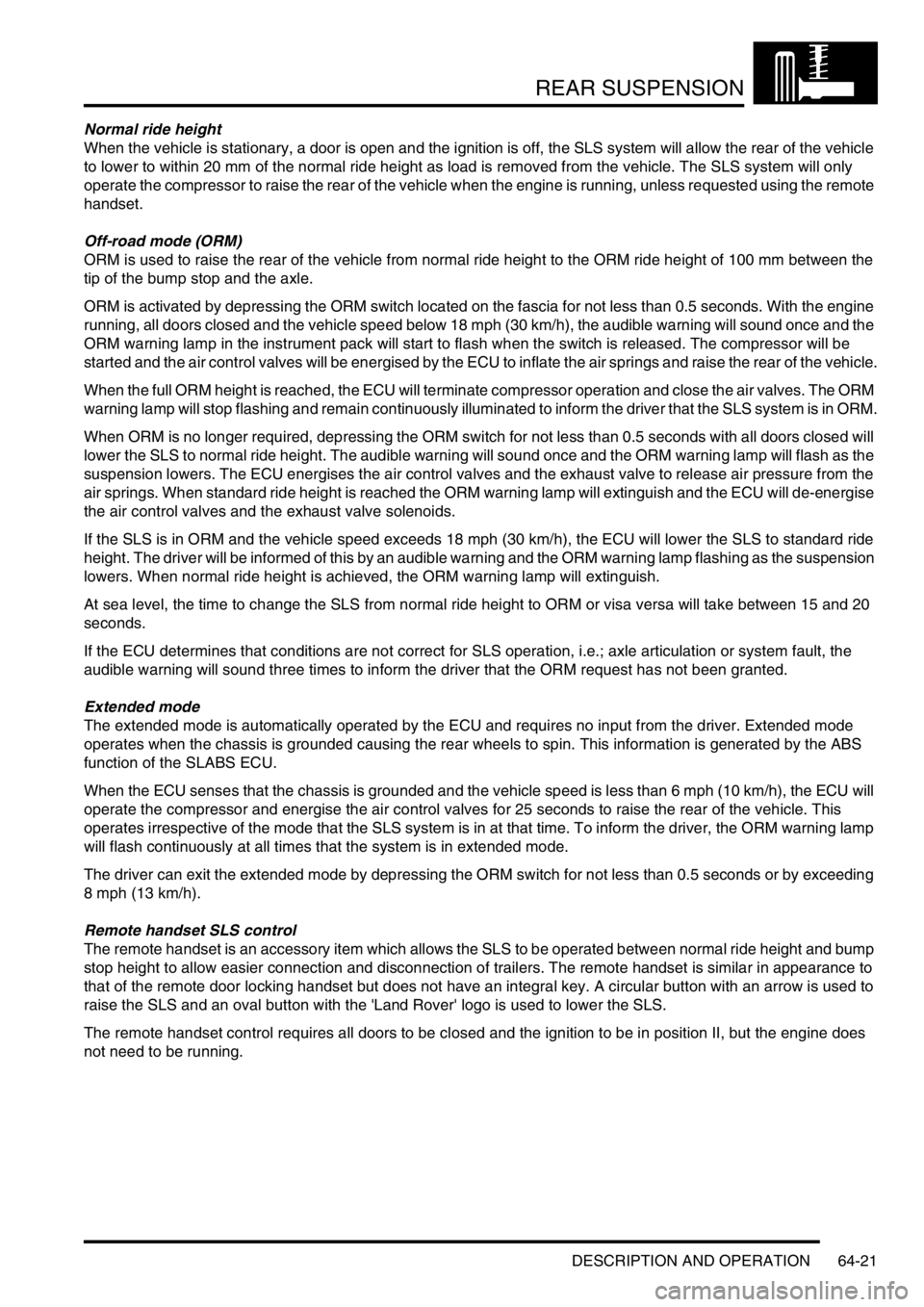
REAR SUSPENSION
DESCRIPTION AND OPERATION 64-21
Normal ride height
When the vehicle is stationary, a door is open and the ignition is off, the SLS system will allow the rear of the vehicle
to lower to within 20 mm of the normal ride height as load is removed from the vehicle. The SLS system will only
operate the compressor to raise the rear of the vehicle when the engine is running, unless requested using the remote
handset.
Off-road mode (ORM)
ORM is used to raise the rear of the vehicle from normal ride height to the ORM ride height of 100 mm between the
tip of the bump stop and the axle.
ORM is activated by depressing the ORM switch located on the fascia for not less than 0.5 seconds. With the engine
running, all doors closed and the vehicle speed below 18 mph (30 km/h), the audible warning will sound once and the
ORM warning lamp in the instrument pack will start to flash when the switch is released. The compressor will be
started and the air control valves will be energised by the ECU to inflate the air springs and raise the rear of the vehicle.
When the full ORM height is reached, the ECU will terminate compressor operation and close the air valves. The ORM
warning lamp will stop flashing and remain continuously illuminated to inform the driver that the SLS system is in ORM.
When ORM is no longer required, depressing the ORM switch for not less than 0.5 seconds with all doors closed will
lower the SLS to normal ride height. The audible warning will sound once and the ORM warning lamp will flash as the
suspension lowers. The ECU energises the air control valves and the exhaust valve to release air pressure from the
air springs. When standard ride height is reached the ORM warning lamp will extinguish and the ECU will de-energise
the air control valves and the exhaust valve solenoids.
If the SLS is in ORM and the vehicle speed exceeds 18 mph (30 km/h), the ECU will lower the SLS to standard ride
height. The driver will be informed of this by an audible warning and the ORM warning lamp flashing as the suspension
lowers. When normal ride height is achieved, the ORM warning lamp will extinguish.
At sea level, the time to change the SLS from normal ride height to ORM or visa versa will take between 15 and 20
seconds.
If the ECU determines that conditions are not correct for SLS operation, i.e.; axle articulation or system fault, the
audible warning will sound three times to inform the driver that the ORM request has not been granted.
Extended mode
The extended mode is automatically operated by the ECU and requires no input from the driver. Extended mode
operates when the chassis is grounded causing the rear wheels to spin. This information is generated by the ABS
function of the SLABS ECU.
When the ECU senses that the chassis is grounded and the vehicle speed is less than 6 mph (10 km/h), the ECU will
operate the compressor and energise the air control valves for 25 seconds to raise the rear of the vehicle. This
operates irrespective of the mode that the SLS system is in at that time. To inform the driver, the ORM warning lamp
will flash continuously at all times that the system is in extended mode.
The driver can exit the extended mode by depressing the ORM switch for not less than 0.5 seconds or by exceeding
8 mph (13 km/h).
Remote handset SLS control
The remote handset is an accessory item which allows the SLS to be operated between normal ride height and bump
stop height to allow easier connection and disconnection of trailers. The remote handset is similar in appearance to
that of the remote door locking handset but does not have an integral key. A circular button with an arrow is used to
raise the SLS and an oval button with the 'Land Rover' logo is used to lower the SLS.
The remote handset control requires all doors to be closed and the ignition to be in position II, but the engine does
not need to be running.
Page 1027 of 1672
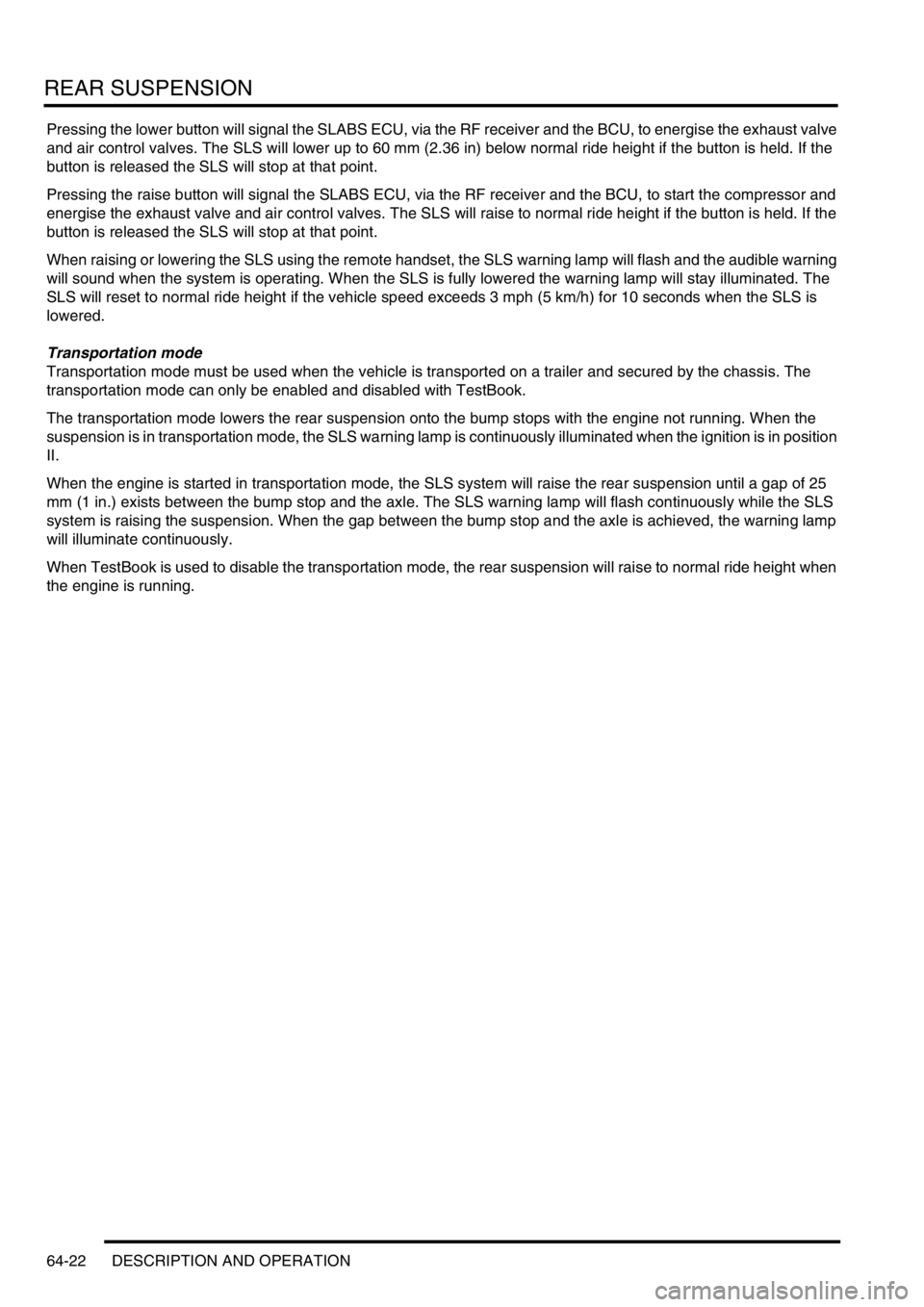
REAR SUSPENSION
64-22 DESCRIPTION AND OPERATION
Pressing the lower button will signal the SLABS ECU, via the RF receiver and the BCU, to energise the exhaust valve
and air control valves. The SLS will lower up to 60 mm (2.36 in) below normal ride height if the button is held. If the
button is released the SLS will stop at that point.
Pressing the raise button will signal the SLABS ECU, via the RF receiver and the BCU, to start the compressor and
energise the exhaust valve and air control valves. The SLS will raise to normal ride height if the button is held. If the
button is released the SLS will stop at that point.
When raising or lowering the SLS using the remote handset, the SLS warning lamp will flash and the audible warning
will sound when the system is operating. When the SLS is fully lowered the warning lamp will stay illuminated. The
SLS will reset to normal ride height if the vehicle speed exceeds 3 mph (5 km/h) for 10 seconds when the SLS is
lowered.
Transportation mode
Transportation mode must be used when the vehicle is transported on a trailer and secured by the chassis. The
transportation mode can only be enabled and disabled with TestBook.
The transportation mode lowers the rear suspension onto the bump stops with the engine not running. When the
suspension is in transportation mode, the SLS warning lamp is continuously illuminated when the ignition is in position
II.
When the engine is started in transportation mode, the SLS system will raise the rear suspension until a gap of 25
mm (1 in.) exists between the bump stop and the axle. The SLS warning lamp will flash continuously while the SLS
system is raising the suspension. When the gap between the bump stop and the axle is achieved, the warning lamp
will illuminate continuously.
When TestBook is used to disable the transportation mode, the rear suspension will raise to normal ride height when
the engine is running.
Page 1098 of 1672
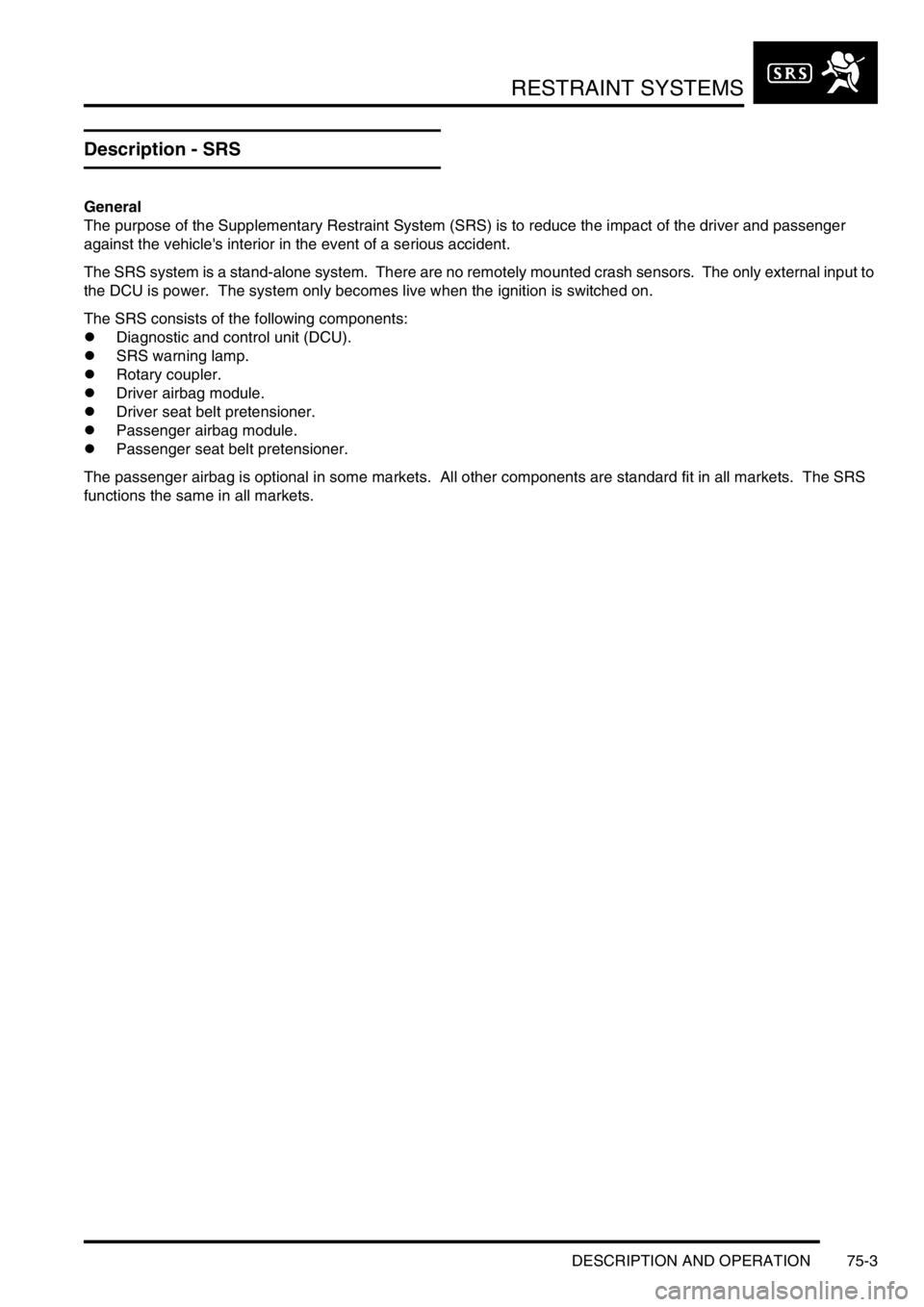
RESTRAINT SYSTEMS
DESCRIPTION AND OPERATION 75-3
Description - SRS
General
The purpose of the Supplementary Restraint System (SRS) is to reduce the impact of the driver and passenger
against the vehicle's interior in the event of a serious accident.
The SRS system is a stand-alone system. There are no remotely mounted crash sensors. The only external input to
the DCU is power. The system only becomes live when the ignition is switched on.
The SRS consists of the following components:
lDiagnostic and control unit (DCU).
lSRS warning lamp.
lRotary coupler.
lDriver airbag module.
lDriver seat belt pretensioner.
lPassenger airbag module.
lPassenger seat belt pretensioner.
The passenger airbag is optional in some markets. All other components are standard fit in all markets. The SRS
functions the same in all markets.
Page 1471 of 1672
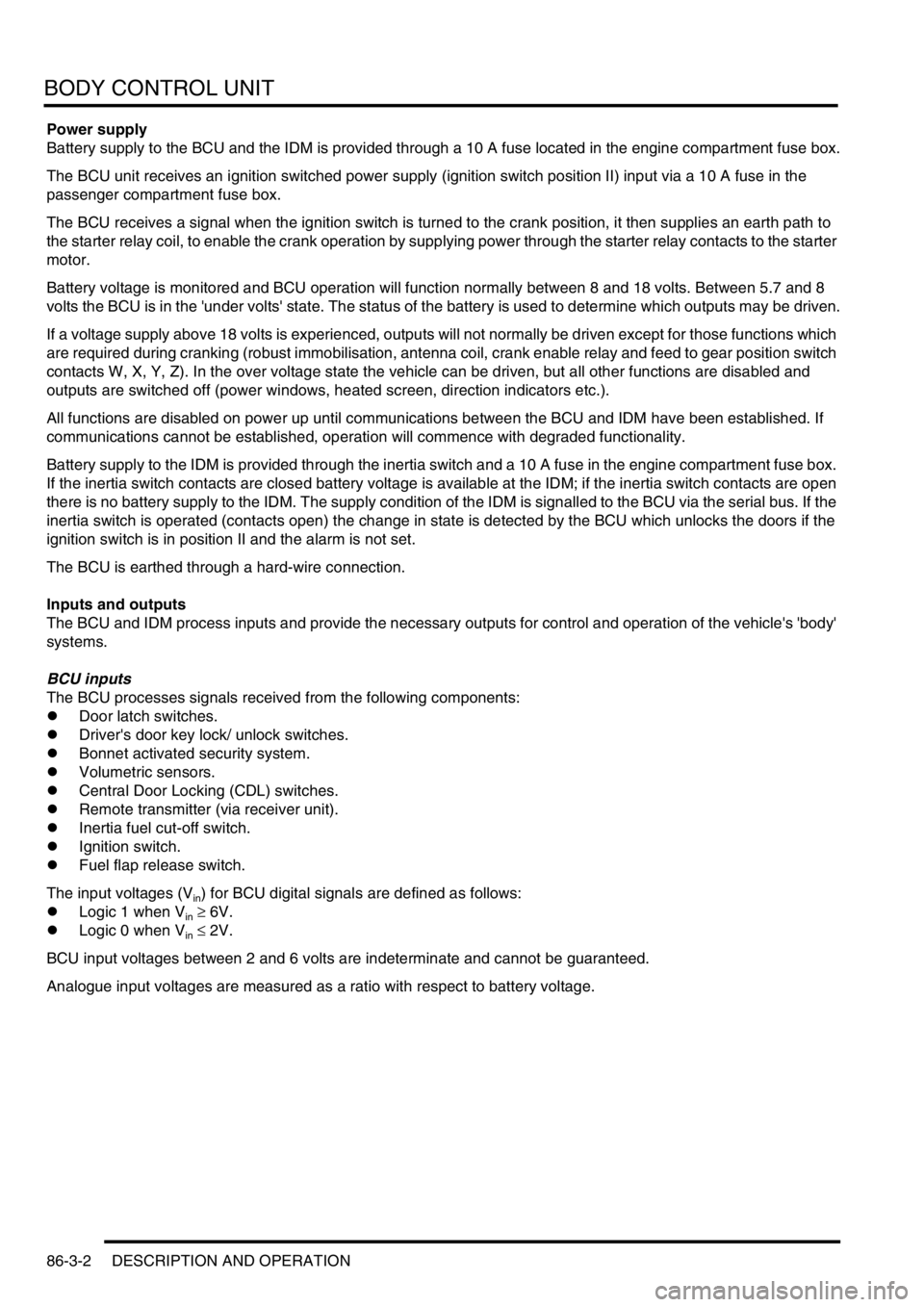
BODY CONTROL UNIT
86-3-2 DESCRIPTION AND OPERATION
Power supply
Battery supply to the BCU and the IDM is provided through a 10 A fuse located in the engine compartment fuse box.
The BCU unit receives an ignition switched power supply (ignition switch position II) input via a 10 A fuse in the
passenger compartment fuse box.
The BCU receives a signal when the ignition switch is turned to the crank position, it then supplies an earth path to
the starter relay coil, to enable the crank operation by supplying power through the starter relay contacts to the starter
motor.
Battery voltage is monitored and BCU operation will function normally between 8 and 18 volts. Between 5.7 and 8
volts the BCU is in the 'under volts' state. The status of the battery is used to determine which outputs may be driven.
If a voltage supply above 18 volts is experienced, outputs will not normally be driven except for those functions which
are required during cranking (robust immobilisation, antenna coil, crank enable relay and feed to gear position switch
contacts W, X, Y, Z). In the over voltage state the vehicle can be driven, but all other functions are disabled and
outputs are switched off (power windows, heated screen, direction indicators etc.).
All functions are disabled on power up until communications between the BCU and IDM have been established. If
communications cannot be established, operation will commence with degraded functionality.
Battery supply to the IDM is provided through the inertia switch and a 10 A fuse in the engine compartment fuse box.
If the inertia switch contacts are closed battery voltage is available at the IDM; if the inertia switch contacts are open
there is no battery supply to the IDM. The supply condition of the IDM is signalled to the BCU via the serial bus. If the
inertia switch is operated (contacts open) the change in state is detected by the BCU which unlocks the doors if the
ignition switch is in position II and the alarm is not set.
The BCU is earthed through a hard-wire connection.
Inputs and outputs
The BCU and IDM process inputs and provide the necessary outputs for control and operation of the vehicle's 'body'
systems.
BCU inputs
The BCU processes signals received from the following components:
lDoor latch switches.
lDriver's door key lock/ unlock switches.
lBonnet activated security system.
lVolumetric sensors.
lCentral Door Locking (CDL) switches.
lRemote transmitter (via receiver unit).
lInertia fuel cut-off switch.
lIgnition switch.
lFuel flap release switch.
The input voltages (V
in) for BCU digital signals are defined as follows:
lLogic 1 when V
in ≥ 6V.
lLogic 0 when V
in ≤ 2V.
BCU input voltages between 2 and 6 volts are indeterminate and cannot be guaranteed.
Analogue input voltages are measured as a ratio with respect to battery voltage.