alternator LAND ROVER DISCOVERY 2002 Owner's Manual
[x] Cancel search | Manufacturer: LAND ROVER, Model Year: 2002, Model line: DISCOVERY, Model: LAND ROVER DISCOVERY 2002Pages: 1672, PDF Size: 46.1 MB
Page 303 of 1672
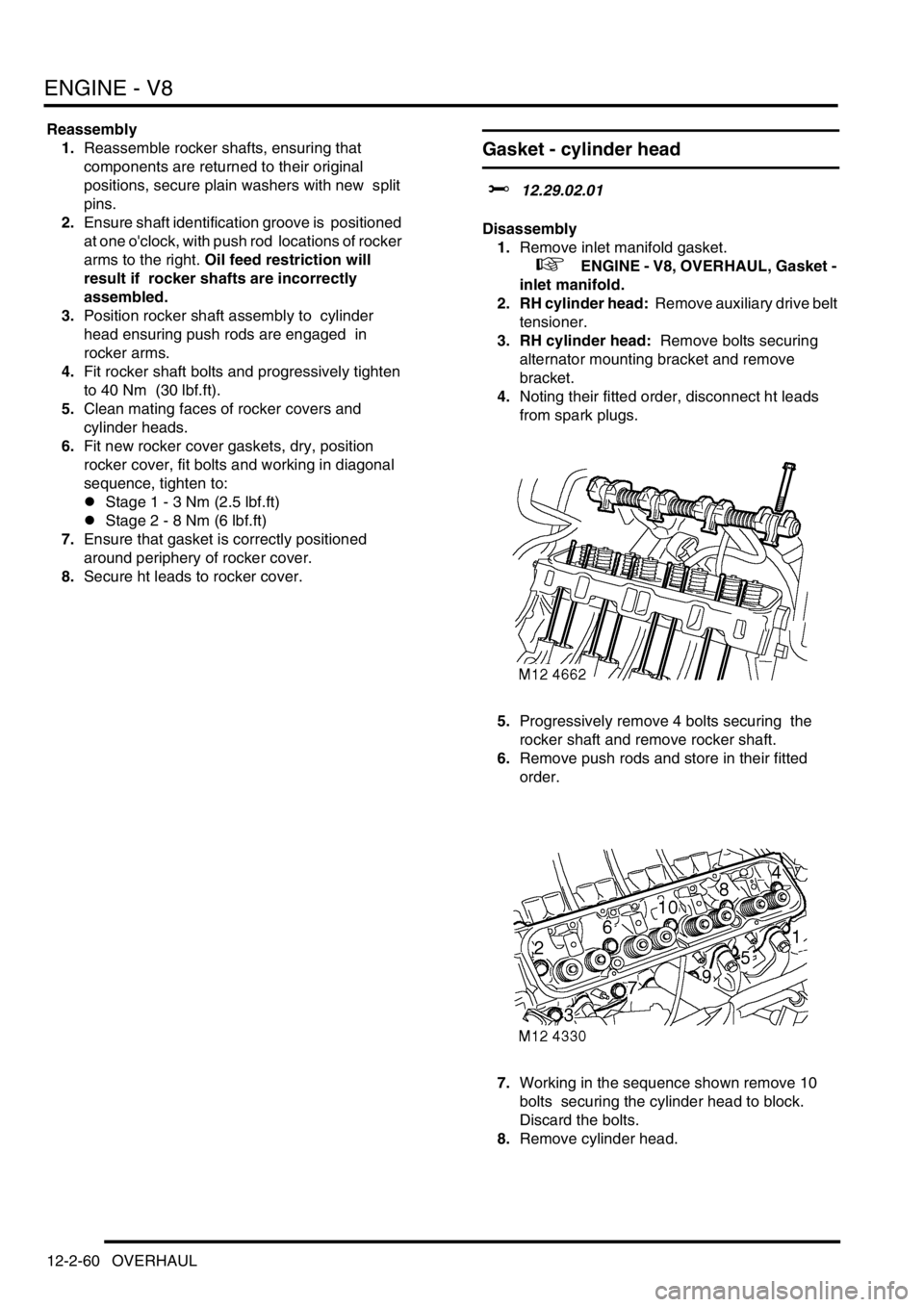
ENGINE - V8
12-2-60 OVERHAUL
Reassembly
1.Reassemble rocker shafts, ensuring that
components are returned to their original
positions, secure plain washers with new split
pins.
2.Ensure shaft identification groove is positioned
at one o'clock, with push rod locations of rocker
arms to the right. Oil feed restriction will
result if rocker shafts are incorrectly
assembled.
3.Position rocker shaft assembly to cylinder
head ensuring push rods are engaged in
rocker arms.
4.Fit rocker shaft bolts and progressively tighten
to 40 Nm (30 lbf.ft).
5.Clean mating faces of rocker covers and
cylinder heads.
6.Fit new rocker cover gaskets, dry, position
rocker cover, fit bolts and working in diagonal
sequence, tighten to:
lStage 1 - 3 Nm (2.5 lbf.ft)
lStage 2 - 8 Nm (6 lbf.ft)
7.Ensure that gasket is correctly positioned
around periphery of rocker cover.
8.Secure ht leads to rocker cover.
Gasket - cylinder head
$% 12.29.02.01
Disassembly
1.Remove inlet manifold gasket.
+ ENGINE - V8, OVERHAUL, Gasket -
inlet manifold.
2. RH cylinder head: Remove auxiliary drive belt
tensioner.
3. RH cylinder head: Remove bolts securing
alternator mounting bracket and remove
bracket.
4.Noting their fitted order, disconnect ht leads
from spark plugs.
5.Progressively remove 4 bolts securing the
rocker shaft and remove rocker shaft.
6.Remove push rods and store in their fitted
order.
7.Working in the sequence shown remove 10
bolts securing the cylinder head to block.
Discard the bolts.
8.Remove cylinder head.
Page 304 of 1672
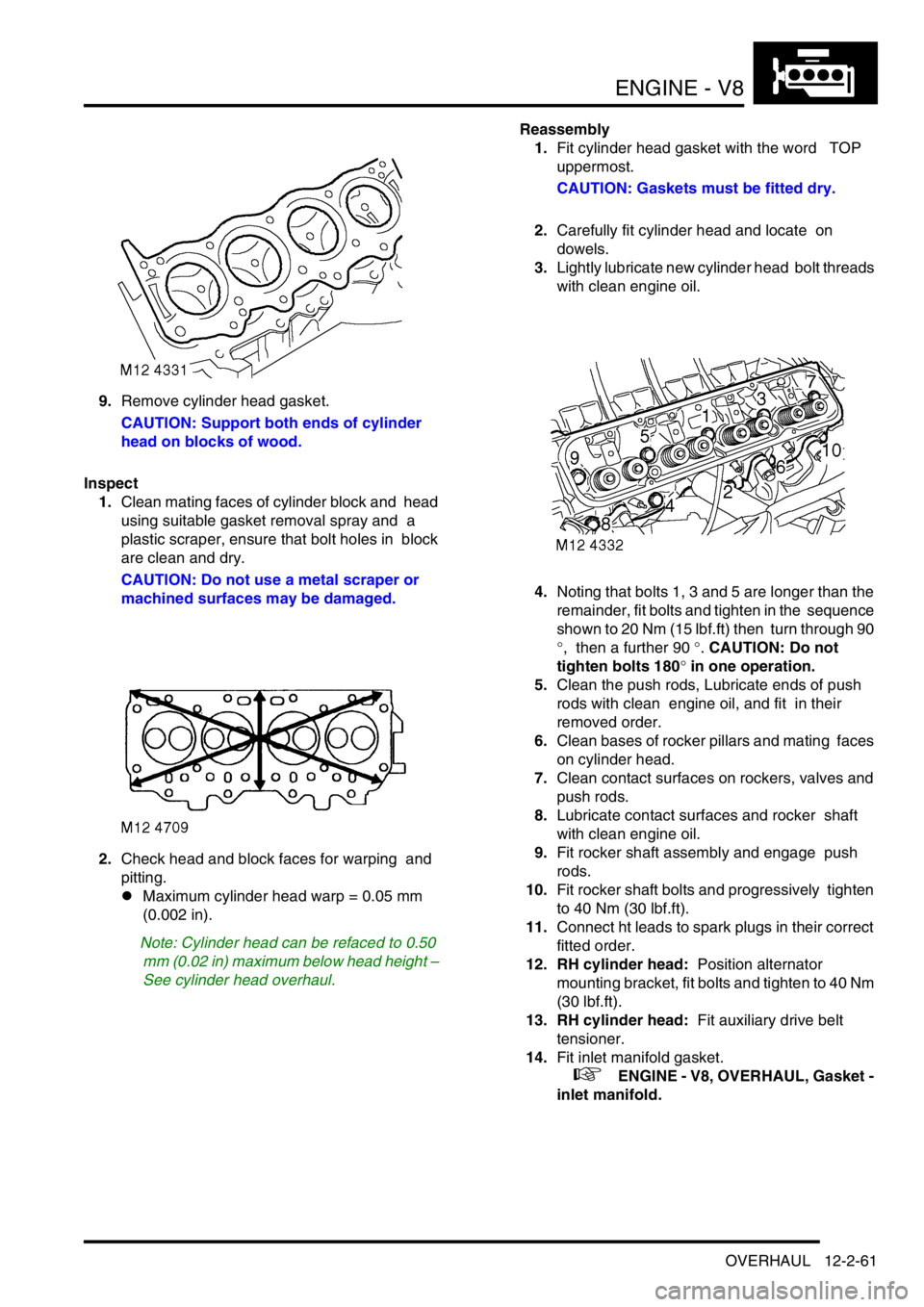
ENGINE - V8
OVERHAUL 12-2-61
9.Remove cylinder head gasket.
CAUTION: Support both ends of cylinder
head on blocks of wood.
Inspect
1.Clean mating faces of cylinder block and head
using suitable gasket removal spray and a
plastic scraper, ensure that bolt holes in block
are clean and dry.
CAUTION: Do not use a metal scraper or
machined surfaces may be damaged.
2.Check head and block faces for warping and
pitting.
lMaximum cylinder head warp = 0.05 mm
(0.002 in).
Note: Cylinder head can be refaced to 0.50
mm (0.02 in) maximum below head height –
See cylinder head overhaul.Reassembly
1.Fit cylinder head gasket with the word TOP
uppermost.
CAUTION: Gaskets must be fitted dry.
2.Carefully fit cylinder head and locate on
dowels.
3.Lightly lubricate new cylinder head bolt threads
with clean engine oil.
4.Noting that bolts 1, 3 and 5 are longer than the
remainder, fit bolts and tighten in the sequence
shown to 20 Nm (15 lbf.ft) then turn through 90
°, then a further 90 °. CAUTION: Do not
tighten bolts 180
° in one operation.
5.Clean the push rods, Lubricate ends of push
rods with clean engine oil, and fit in their
removed order.
6.Clean bases of rocker pillars and mating faces
on cylinder head.
7.Clean contact surfaces on rockers, valves and
push rods.
8.Lubricate contact surfaces and rocker shaft
with clean engine oil.
9.Fit rocker shaft assembly and engage push
rods.
10.Fit rocker shaft bolts and progressively tighten
to 40 Nm (30 lbf.ft).
11.Connect ht leads to spark plugs in their correct
fitted order.
12. RH cylinder head: Position alternator
mounting bracket, fit bolts and tighten to 40 Nm
(30 lbf.ft).
13. RH cylinder head: Fit auxiliary drive belt
tensioner.
14.Fit inlet manifold gasket.
+ ENGINE - V8, OVERHAUL, Gasket -
inlet manifold.
Page 322 of 1672
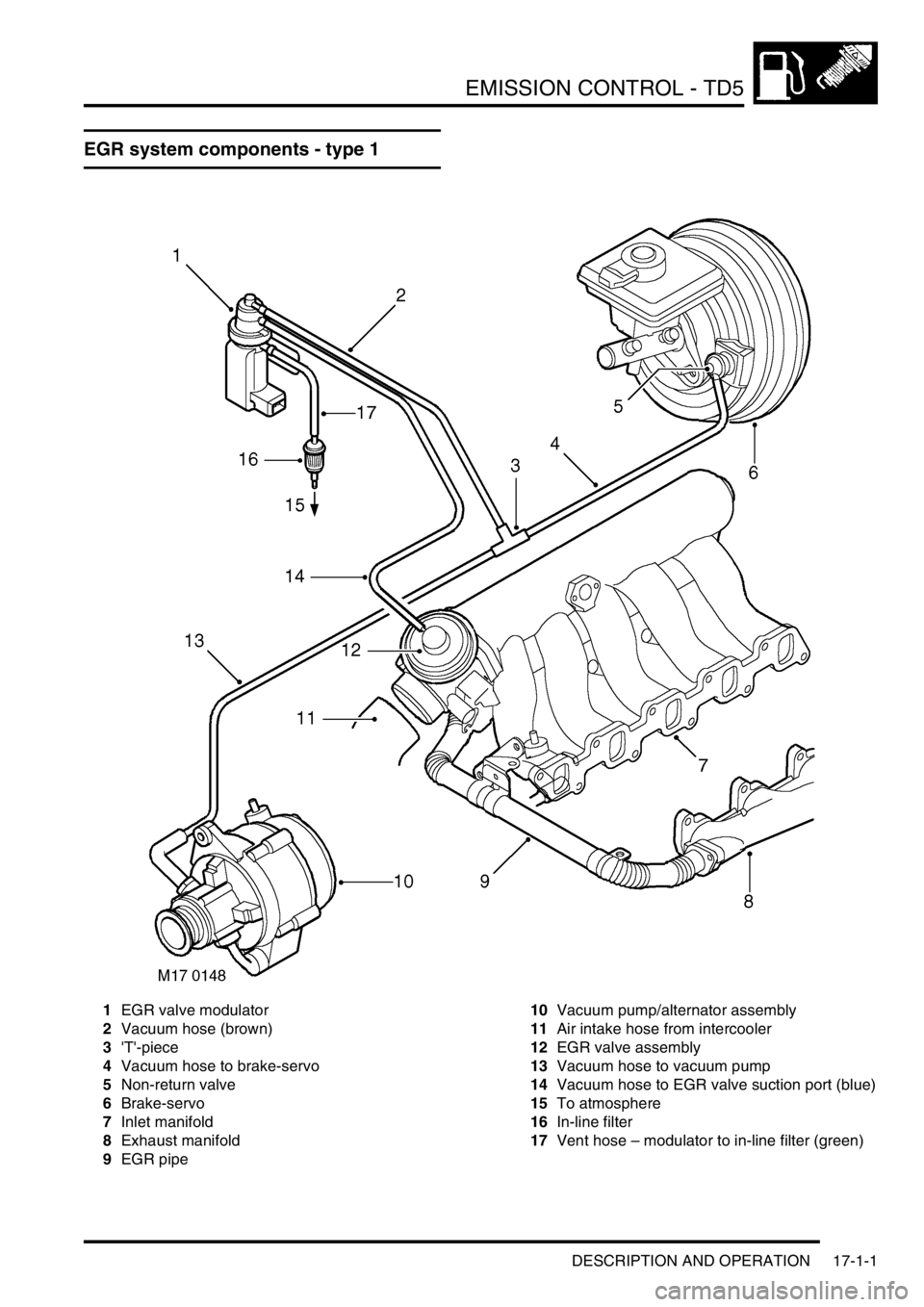
EMISSION CONTROL - TD5
DESCRIPTION AND OPERATION 17-1-1
EMISS ION CONTROL - Td5 DESCRIPTION AND OPERAT ION
EGR system components - type 1
1EGR valve modulator
2Vacuum hose (brown)
3'T'-piece
4Vacuum hose to brake-servo
5Non-return valve
6Brake-servo
7Inlet manifold
8Exhaust manifold
9EGR pipe10Vacuum pump/alternator assembly
11Air intake hose from intercooler
12EGR valve assembly
13Vacuum hose to vacuum pump
14Vacuum hose to EGR valve suction port (blue)
15To atmosphere
16In-line filter
17Vent hose – modulator to in-line filter (green)
Page 324 of 1672
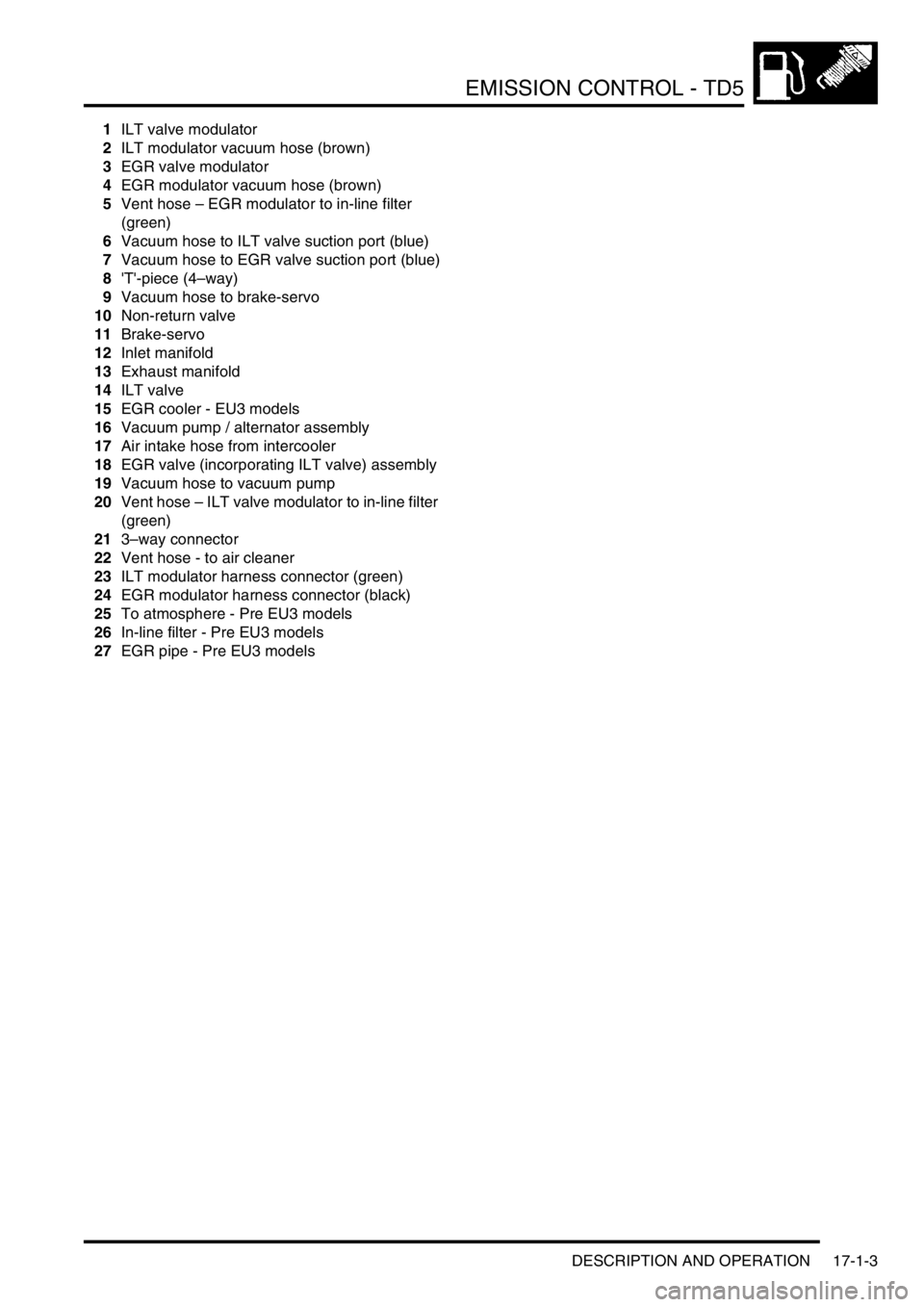
EMISSION CONTROL - TD5
DESCRIPTION AND OPERATION 17-1-3
1ILT valve modulator
2ILT modulator vacuum hose (brown)
3EGR valve modulator
4EGR modulator vacuum hose (brown)
5Vent hose – EGR modulator to in-line filter
(green)
6Vacuum hose to ILT valve suction port (blue)
7Vacuum hose to EGR valve suction port (blue)
8'T'-piece (4–way)
9Vacuum hose to brake-servo
10Non-return valve
11Brake-servo
12Inlet manifold
13Exhaust manifold
14ILT valve
15EGR cooler - EU3 models
16Vacuum pump / alternator assembly
17Air intake hose from intercooler
18EGR valve (incorporating ILT valve) assembly
19Vacuum hose to vacuum pump
20Vent hose – ILT valve modulator to in-line filter
(green)
213–way connector
22Vent hose - to air cleaner
23ILT modulator harness connector (green)
24EGR modulator harness connector (black)
25To atmosphere - Pre EU3 models
26In-line filter - Pre EU3 models
27EGR pipe - Pre EU3 models
Page 328 of 1672
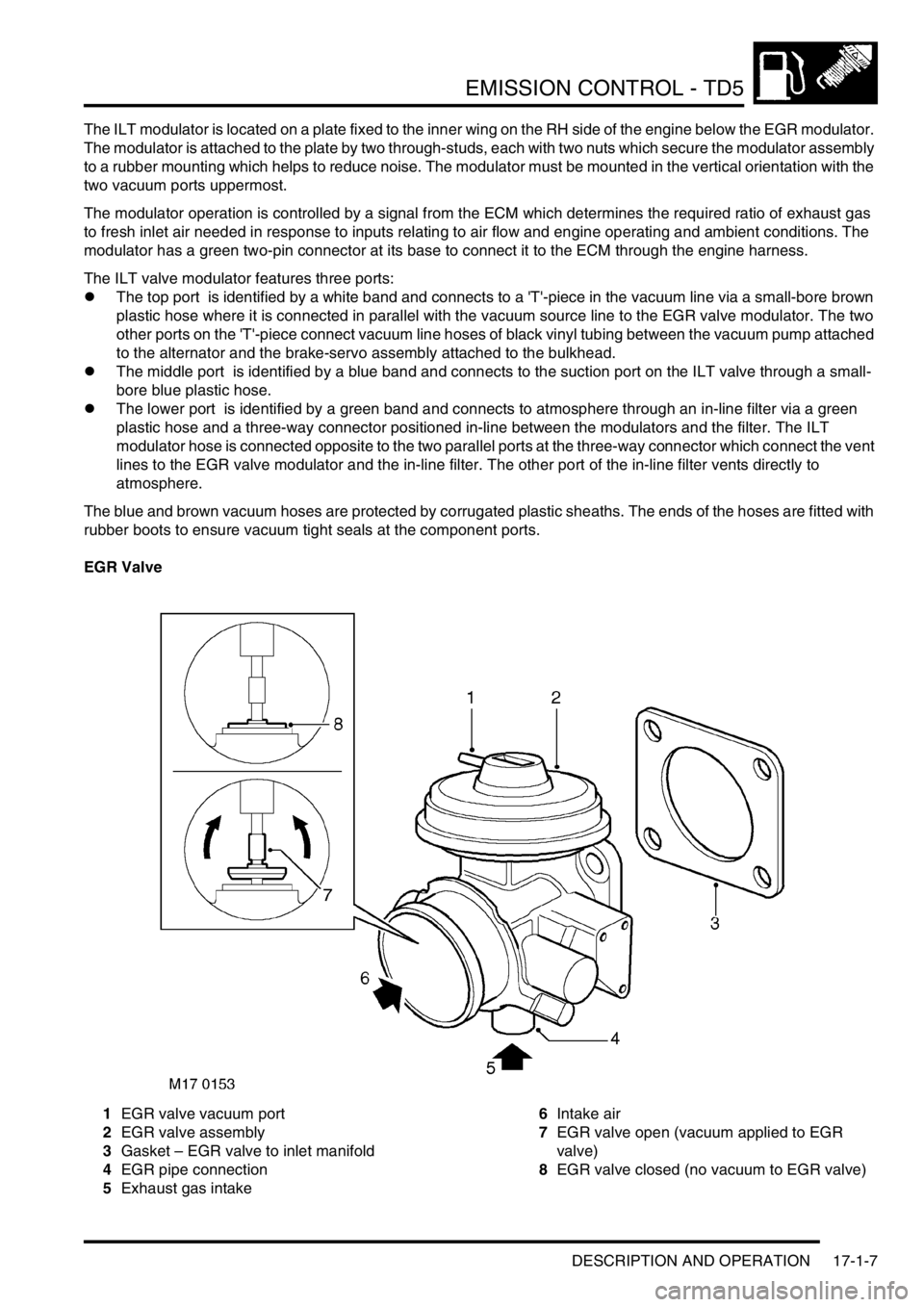
EMISSION CONTROL - TD5
DESCRIPTION AND OPERATION 17-1-7
The ILT modulator is located on a plate fixed to the inner wing on the RH side of the engine below the EGR modulator.
The modulator is attached to the plate by two through-studs, each with two nuts which secure the modulator assembly
to a rubber mounting which helps to reduce noise. The modulator must be mounted in the vertical orientation with the
two vacuum ports uppermost.
The modulator operation is controlled by a signal from the ECM which determines the required ratio of exhaust gas
to fresh inlet air needed in response to inputs relating to air flow and engine operating and ambient conditions. The
modulator has a green two-pin connector at its base to connect it to the ECM through the engine harness.
The ILT valve modulator features three ports:
lThe top port is identified by a white band and connects to a 'T'-piece in the vacuum line via a small-bore brown
plastic hose where it is connected in parallel with the vacuum source line to the EGR valve modulator. The two
other ports on the 'T'-piece connect vacuum line hoses of black vinyl tubing between the vacuum pump attached
to the alternator and the brake-servo assembly attached to the bulkhead.
lThe middle port is identified by a blue band and connects to the suction port on the ILT valve through a small-
bore blue plastic hose.
lThe lower port is identified by a green band and connects to atmosphere through an in-line filter via a green
plastic hose and a three-way connector positioned in-line between the modulators and the filter. The ILT
modulator hose is connected opposite to the two parallel ports at the three-way connector which connect the vent
lines to the EGR valve modulator and the in-line filter. The other port of the in-line filter vents directly to
atmosphere.
The blue and brown vacuum hoses are protected by corrugated plastic sheaths. The ends of the hoses are fitted with
rubber boots to ensure vacuum tight seals at the component ports.
EGR Valve
1EGR valve vacuum port
2EGR valve assembly
3Gasket – EGR valve to inlet manifold
4EGR pipe connection
5Exhaust gas intake6Intake air
7EGR valve open (vacuum applied to EGR
valve)
8EGR valve closed (no vacuum to EGR valve)
Page 489 of 1672
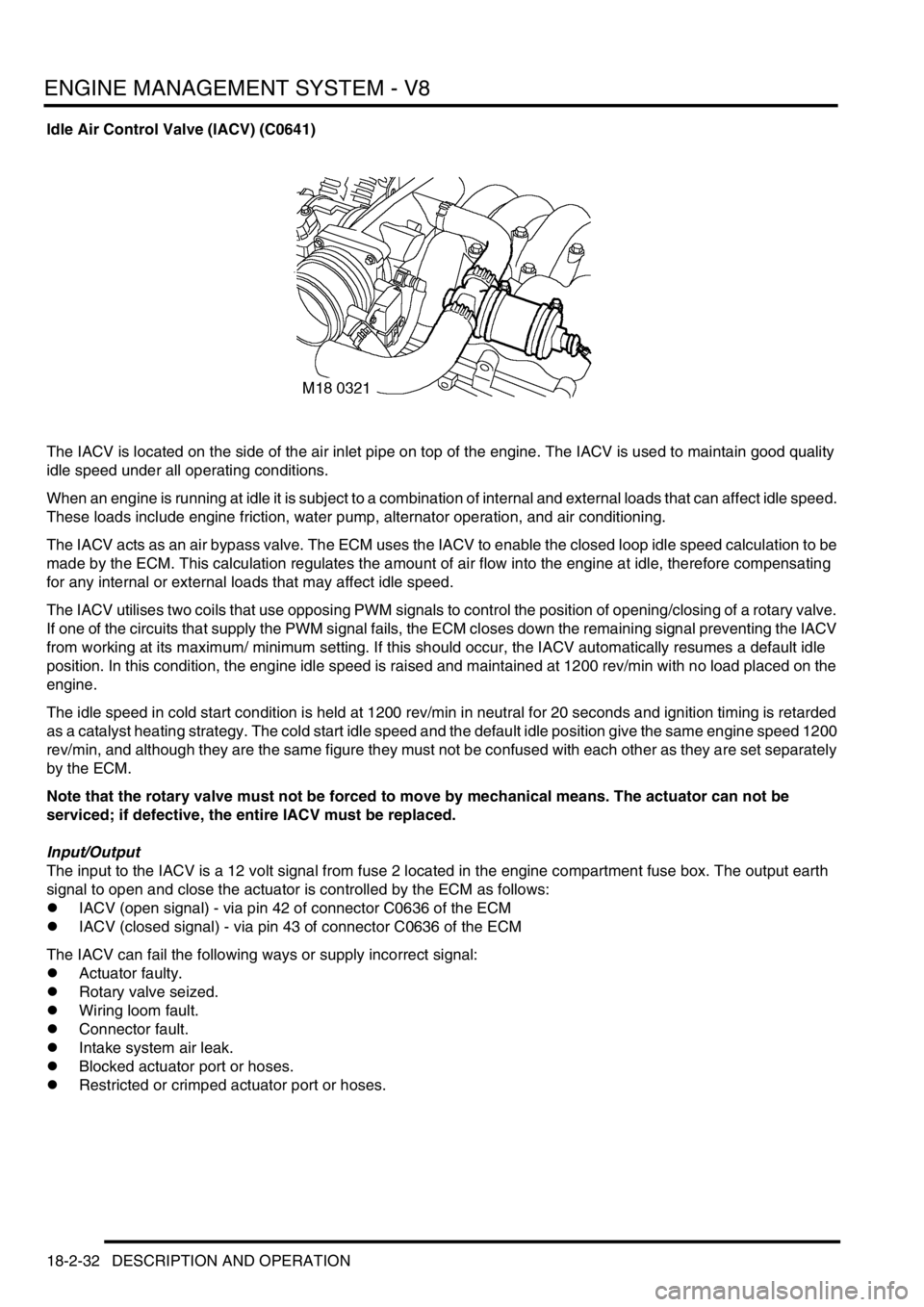
ENGINE MANAGEMENT SYSTEM - V8
18-2-32 DESCRIPTION AND OPERATION
Idle Air Control Valve (IACV) (C0641)
The IACV is located on the side of the air inlet pipe on top of the engine. The IACV is used to maintain good quality
idle speed under all operating conditions.
When an engine is running at idle it is subject to a combination of internal and external loads that can affect idle speed.
These loads include engine friction, water pump, alternator operation, and air conditioning.
The IACV acts as an air bypass valve. The ECM uses the IACV to enable the closed loop idle speed calculation to be
made by the ECM. This calculation regulates the amount of air flow into the engine at idle, therefore compensating
for any internal or external loads that may affect idle speed.
The IACV utilises two coils that use opposing PWM signals to control the position of opening/closing of a rotary valve.
If one of the circuits that supply the PWM signal fails, the ECM closes down the remaining signal preventing the IACV
from working at its maximum/ minimum setting. If this should occur, the IACV automatically resumes a default idle
position. In this condition, the engine idle speed is raised and maintained at 1200 rev/min with no load placed on the
engine.
The idle speed in cold start condition is held at 1200 rev/min in neutral for 20 seconds and ignition timing is retarded
as a catalyst heating strategy. The cold start idle speed and the default idle position give the same engine speed 1200
rev/min, and although they are the same figure they must not be confused with each other as they are set separately
by the ECM.
Note that the rotary valve must not be forced to move by mechanical means. The actuator can not be
serviced; if defective, the entire IACV must be replaced.
Input/Output
The input to the IACV is a 12 volt signal from fuse 2 located in the engine compartment fuse box. The output earth
signal to open and close the actuator is controlled by the ECM as follows:
lIACV (open signal) - via pin 42 of connector C0636 of the ECM
lIACV (closed signal) - via pin 43 of connector C0636 of the ECM
The IACV can fail the following ways or supply incorrect signal:
lActuator faulty.
lRotary valve seized.
lWiring loom fault.
lConnector fault.
lIntake system air leak.
lBlocked actuator port or hoses.
lRestricted or crimped actuator port or hoses.
Page 530 of 1672
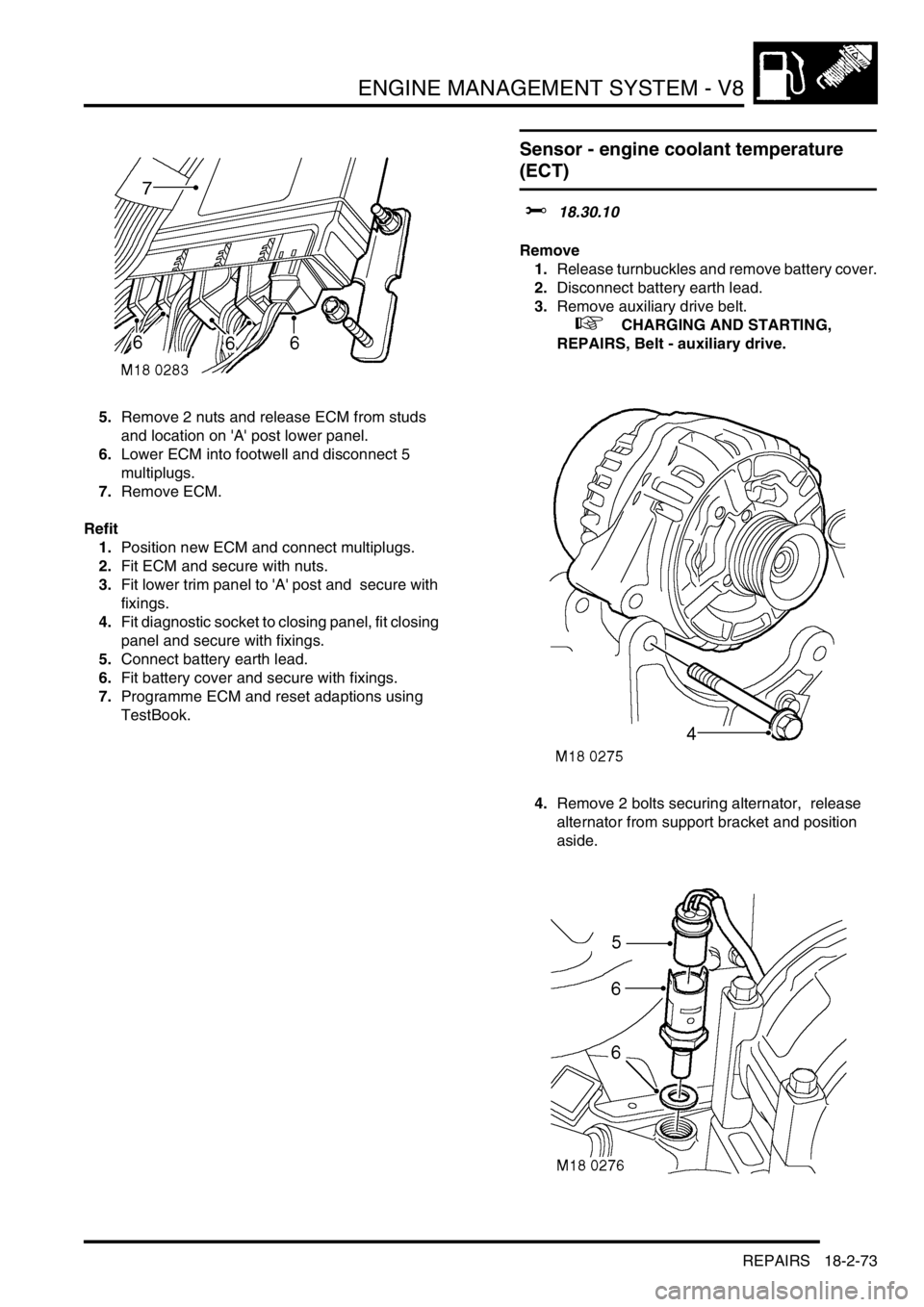
ENGINE MANAGEMENT SYSTEM - V8
REPAIRS 18-2-73
5.Remove 2 nuts and release ECM from studs
and location on 'A' post lower panel.
6.Lower ECM into footwell and disconnect 5
multiplugs.
7.Remove ECM.
Refit
1.Position new ECM and connect multiplugs.
2.Fit ECM and secure with nuts.
3.Fit lower trim panel to 'A' post and secure with
fixings.
4.Fit diagnostic socket to closing panel, fit closing
panel and secure with fixings.
5.Connect battery earth lead.
6.Fit battery cover and secure with fixings.
7.Programme ECM and reset adaptions using
TestBook.
Sensor - engine coolant temperature
(ECT)
$% 18.30.10
Remove
1.Release turnbuckles and remove battery cover.
2.Disconnect battery earth lead.
3.Remove auxiliary drive belt.
+ CHARGING AND STARTING,
REPAIRS, Belt - auxiliary drive.
4.Remove 2 bolts securing alternator, release
alternator from support bracket and position
aside.
Page 531 of 1672
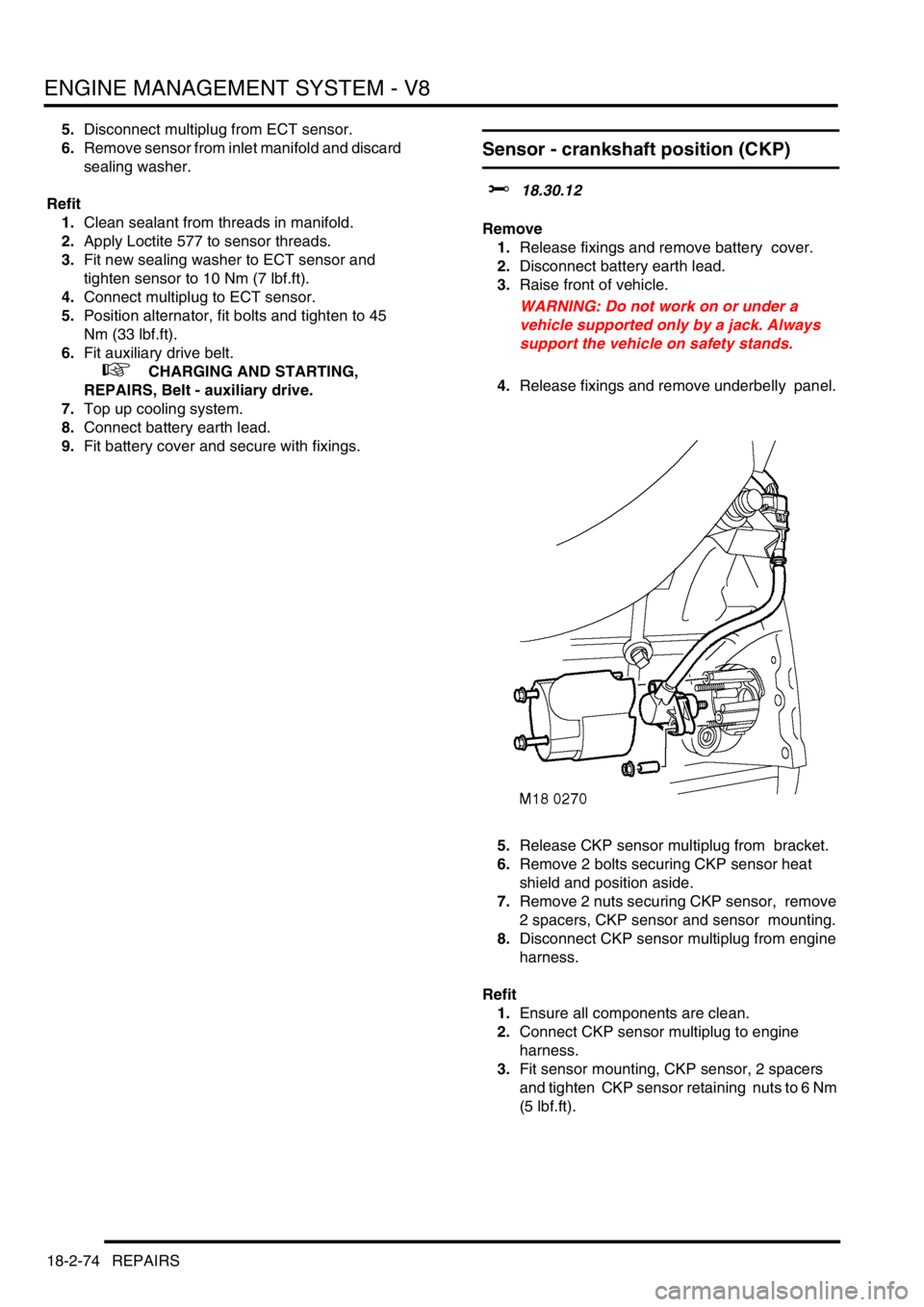
ENGINE MANAGEMENT SYSTEM - V8
18-2-74 REPAIRS
5.Disconnect multiplug from ECT sensor.
6.Remove sensor from inlet manifold and discard
sealing washer.
Refit
1.Clean sealant from threads in manifold.
2.Apply Loctite 577 to sensor threads.
3.Fit new sealing washer to ECT sensor and
tighten sensor to 10 Nm (7 lbf.ft).
4.Connect multiplug to ECT sensor.
5.Position alternator, fit bolts and tighten to 45
Nm (33 lbf.ft).
6.Fit auxiliary drive belt.
+ CHARGING AND STARTING,
REPAIRS, Belt - auxiliary drive.
7.Top up cooling system.
8.Connect battery earth lead.
9.Fit battery cover and secure with fixings.
Sensor - crankshaft position (CKP)
$% 18.30.12
Remove
1.Release fixings and remove battery cover.
2.Disconnect battery earth lead.
3.Raise front of vehicle.
WARNING: Do not work on or under a
vehicle supported only by a jack. Always
support the vehicle on safety stands.
4.Release fixings and remove underbelly panel.
5.Release CKP sensor multiplug from bracket.
6.Remove 2 bolts securing CKP sensor heat
shield and position aside.
7.Remove 2 nuts securing CKP sensor, remove
2 spacers, CKP sensor and sensor mounting.
8.Disconnect CKP sensor multiplug from engine
harness.
Refit
1.Ensure all components are clean.
2.Connect CKP sensor multiplug to engine
harness.
3.Fit sensor mounting, CKP sensor, 2 spacers
and tighten CKP sensor retaining nuts to 6 Nm
(5 lbf.ft).
Page 627 of 1672
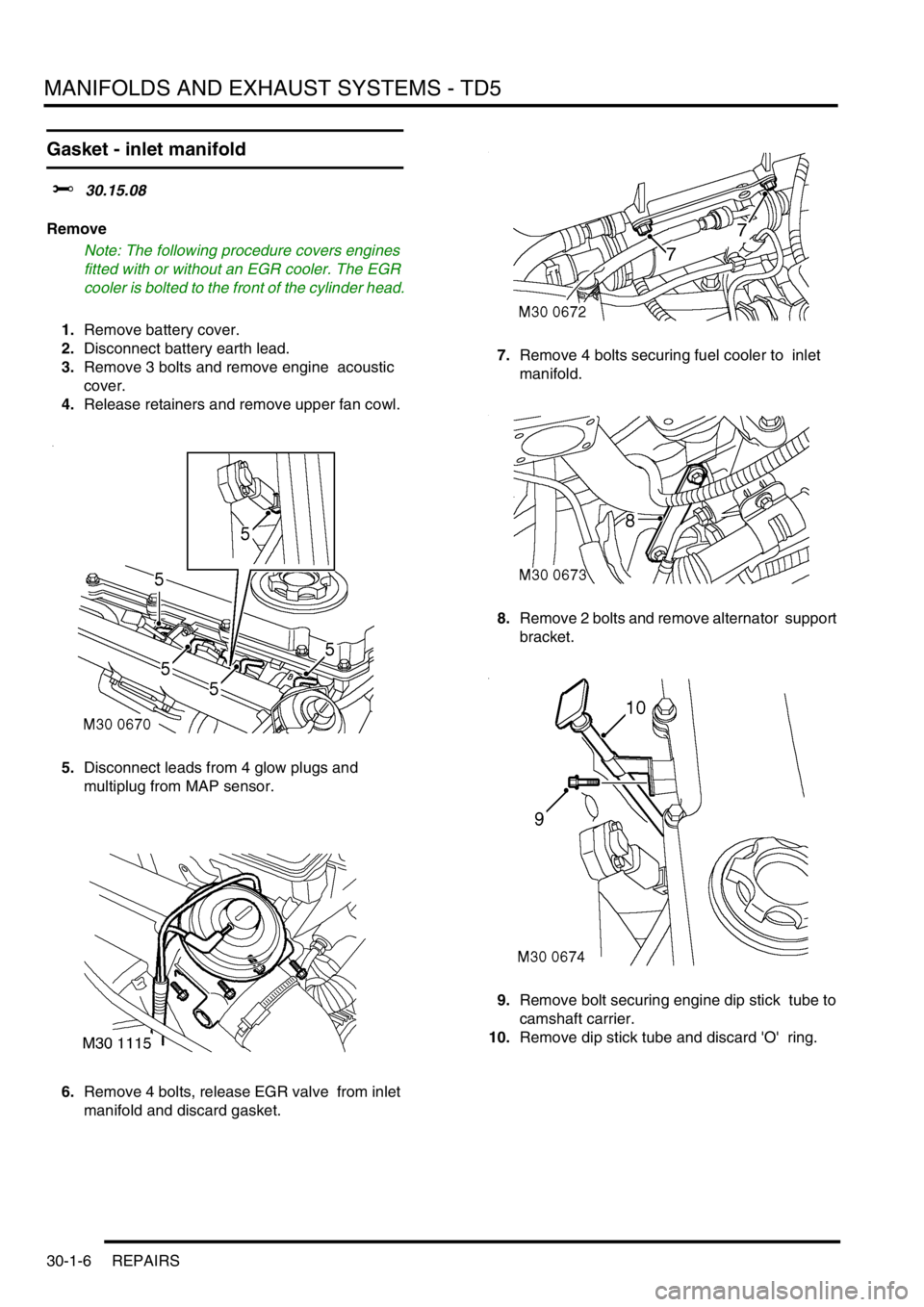
MANIFOLDS AND EXHAUST SYSTEMS - TD5
30-1-6 REPAIRS
Gasket - inlet manifold
$% 30.15.08
Remove
Note: The following procedure covers engines
fitted with or without an EGR cooler. The EGR
cooler is bolted to the front of the cylinder head.
1.Remove battery cover.
2.Disconnect battery earth lead.
3.Remove 3 bolts and remove engine acoustic
cover.
4.Release retainers and remove upper fan cowl.
5.Disconnect leads from 4 glow plugs and
multiplug from MAP sensor.
6.Remove 4 bolts, release EGR valve from inlet
manifold and discard gasket. 7.Remove 4 bolts securing fuel cooler to inlet
manifold.
8.Remove 2 bolts and remove alternator support
bracket.
9.Remove bolt securing engine dip stick tube to
camshaft carrier.
10.Remove dip stick tube and discard 'O' ring.
Page 628 of 1672
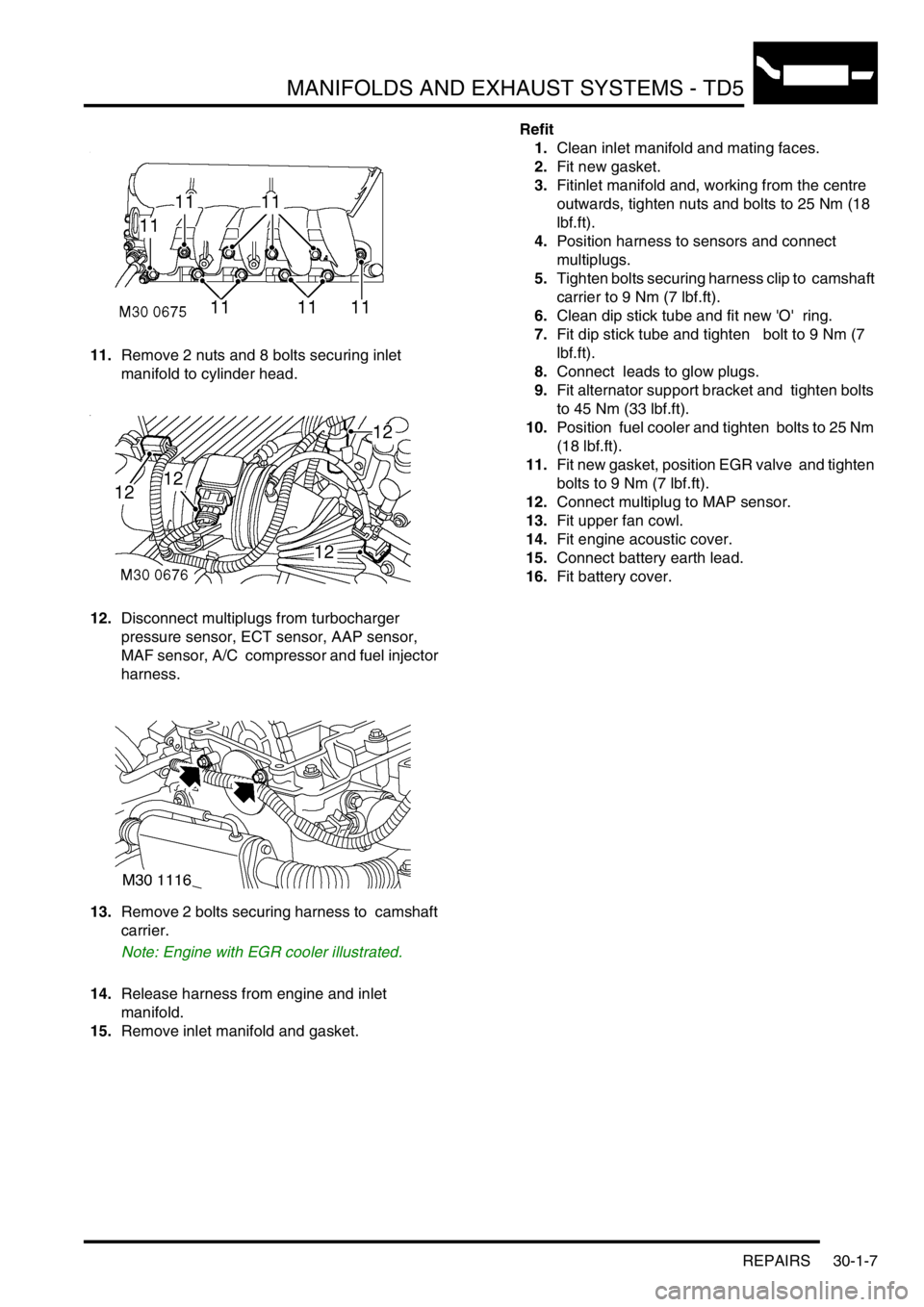
MANIFOLDS AND EXHAUST SYSTEMS - TD5
REPAIRS 30-1-7
11.Remove 2 nuts and 8 bolts securing inlet
manifold to cylinder head.
12.Disconnect multiplugs from turbocharger
pressure sensor, ECT sensor, AAP sensor,
MAF sensor, A/C compressor and fuel injector
harness.
13.Remove 2 bolts securing harness to camshaft
carrier.
Note: Engine with EGR cooler illustrated.
14.Release harness from engine and inlet
manifold.
15.Remove inlet manifold and gasket. Refit
1.Clean inlet manifold and mating faces.
2.Fit new gasket.
3.Fitinlet manifold and, working from the centre
outwards, tighten nuts and bolts to 25 Nm (18
lbf.ft).
4.Position harness to sensors and connect
multiplugs.
5.Tighten bolts securing harness clip to camshaft
carrier to 9 Nm (7 lbf.ft).
6.Clean dip stick tube and fit new 'O' ring.
7.Fit dip stick tube and tighten bolt to 9 Nm (7
lbf.ft).
8.Connect leads to glow plugs.
9.Fit alternator support bracket and tighten bolts
to 45 Nm (33 lbf.ft).
10.Position fuel cooler and tighten bolts to 25 Nm
(18 lbf.ft).
11.Fit new gasket, position EGR valve and tighten
bolts to 9 Nm (7 lbf.ft).
12.Connect multiplug to MAP sensor.
13.Fit upper fan cowl.
14.Fit engine acoustic cover.
15.Connect battery earth lead.
16.Fit battery cover.