brake sensor LAND ROVER DISCOVERY 2002 Owner's Manual
[x] Cancel search | Manufacturer: LAND ROVER, Model Year: 2002, Model line: DISCOVERY, Model: LAND ROVER DISCOVERY 2002Pages: 1672, PDF Size: 46.1 MB
Page 815 of 1672
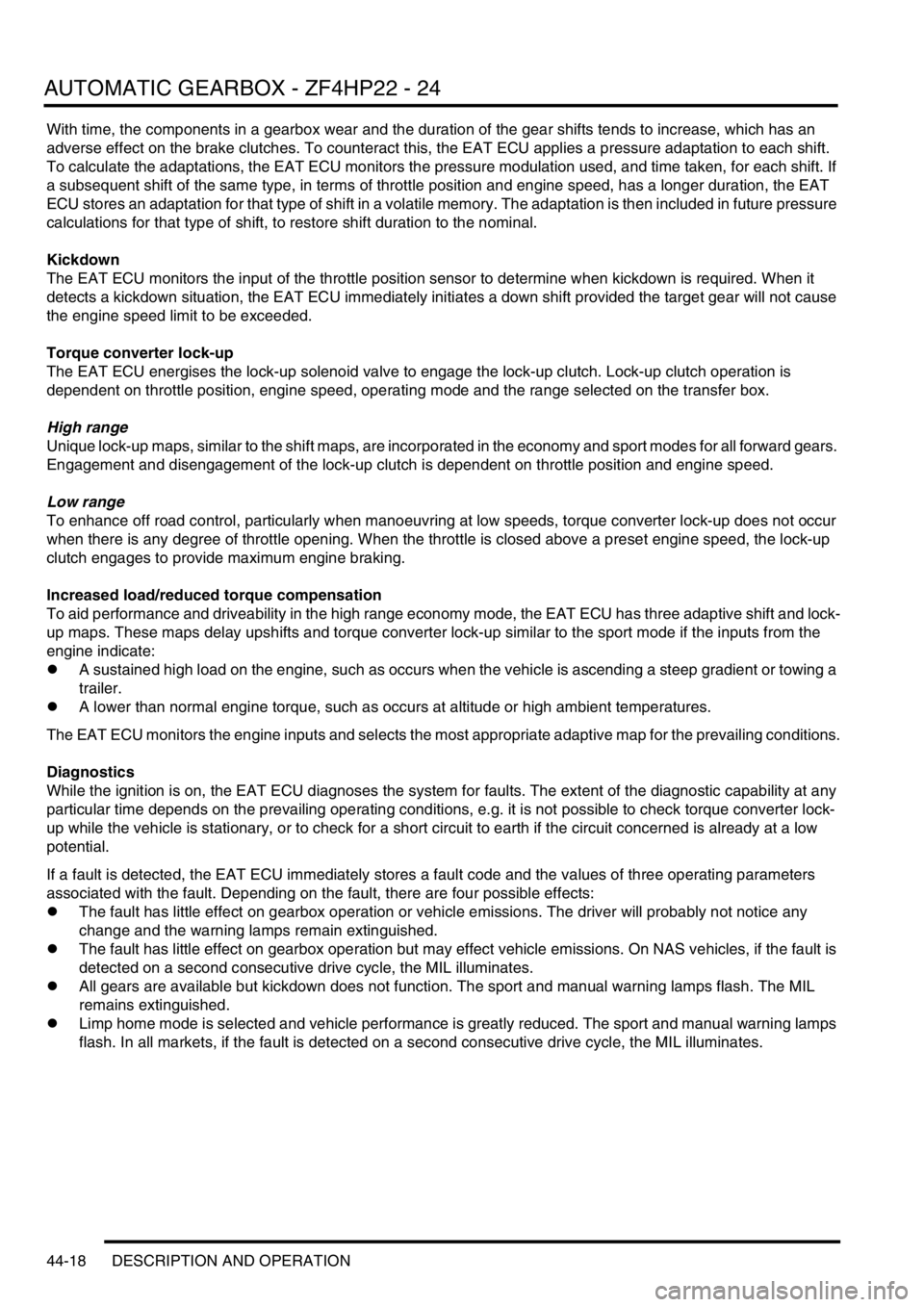
AUTOMATIC GEARBOX - ZF4HP22 - 24
44-18 DESCRIPTION AND OPERATION
With time, the components in a gearbox wear and the duration of the gear shifts tends to increase, which has an
adverse effect on the brake clutches. To counteract this, the EAT ECU applies a pressure adaptation to each shift.
To calculate the adaptations, the EAT ECU monitors the pressure modulation used, and time taken, for each shift. If
a subsequent shift of the same type, in terms of throttle position and engine speed, has a longer duration, the EAT
ECU stores an adaptation for that type of shift in a volatile memory. The adaptation is then included in future pressure
calculations for that type of shift, to restore shift duration to the nominal.
Kickdown
The EAT ECU monitors the input of the throttle position sensor to determine when kickdown is required. When it
detects a kickdown situation, the EAT ECU immediately initiates a down shift provided the target gear will not cause
the engine speed limit to be exceeded.
Torque converter lock-up
The EAT ECU energises the lock-up solenoid valve to engage the lock-up clutch. Lock-up clutch operation is
dependent on throttle position, engine speed, operating mode and the range selected on the transfer box.
High range
Unique lock-up maps, similar to the shift maps, are incorporated in the economy and sport modes for all forward gears.
Engagement and disengagement of the lock-up clutch is dependent on throttle position and engine speed.
Low range
To enhance off road control, particularly when manoeuvring at low speeds, torque converter lock-up does not occur
when there is any degree of throttle opening. When the throttle is closed above a preset engine speed, the lock-up
clutch engages to provide maximum engine braking.
Increased load/reduced torque compensation
To aid performance and driveability in the high range economy mode, the EAT ECU has three adaptive shift and lock-
up maps. These maps delay upshifts and torque converter lock-up similar to the sport mode if the inputs from the
engine indicate:
lA sustained high load on the engine, such as occurs when the vehicle is ascending a steep gradient or towing a
trailer.
lA lower than normal engine torque, such as occurs at altitude or high ambient temperatures.
The EAT ECU monitors the engine inputs and selects the most appropriate adaptive map for the prevailing conditions.
Diagnostics
While the ignition is on, the EAT ECU diagnoses the system for faults. The extent of the diagnostic capability at any
particular time depends on the prevailing operating conditions, e.g. it is not possible to check torque converter lock-
up while the vehicle is stationary, or to check for a short circuit to earth if the circuit concerned is already at a low
potential.
If a fault is detected, the EAT ECU immediately stores a fault code and the values of three operating parameters
associated with the fault. Depending on the fault, there are four possible effects:
lThe fault has little effect on gearbox operation or vehicle emissions. The driver will probably not notice any
change and the warning lamps remain extinguished.
lThe fault has little effect on gearbox operation but may effect vehicle emissions. On NAS vehicles, if the fault is
detected on a second consecutive drive cycle, the MIL illuminates.
lAll gears are available but kickdown does not function. The sport and manual warning lamps flash. The MIL
remains extinguished.
lLimp home mode is selected and vehicle performance is greatly reduced. The sport and manual warning lamps
flash. In all markets, if the fault is detected on a second consecutive drive cycle, the MIL illuminates.
Page 824 of 1672
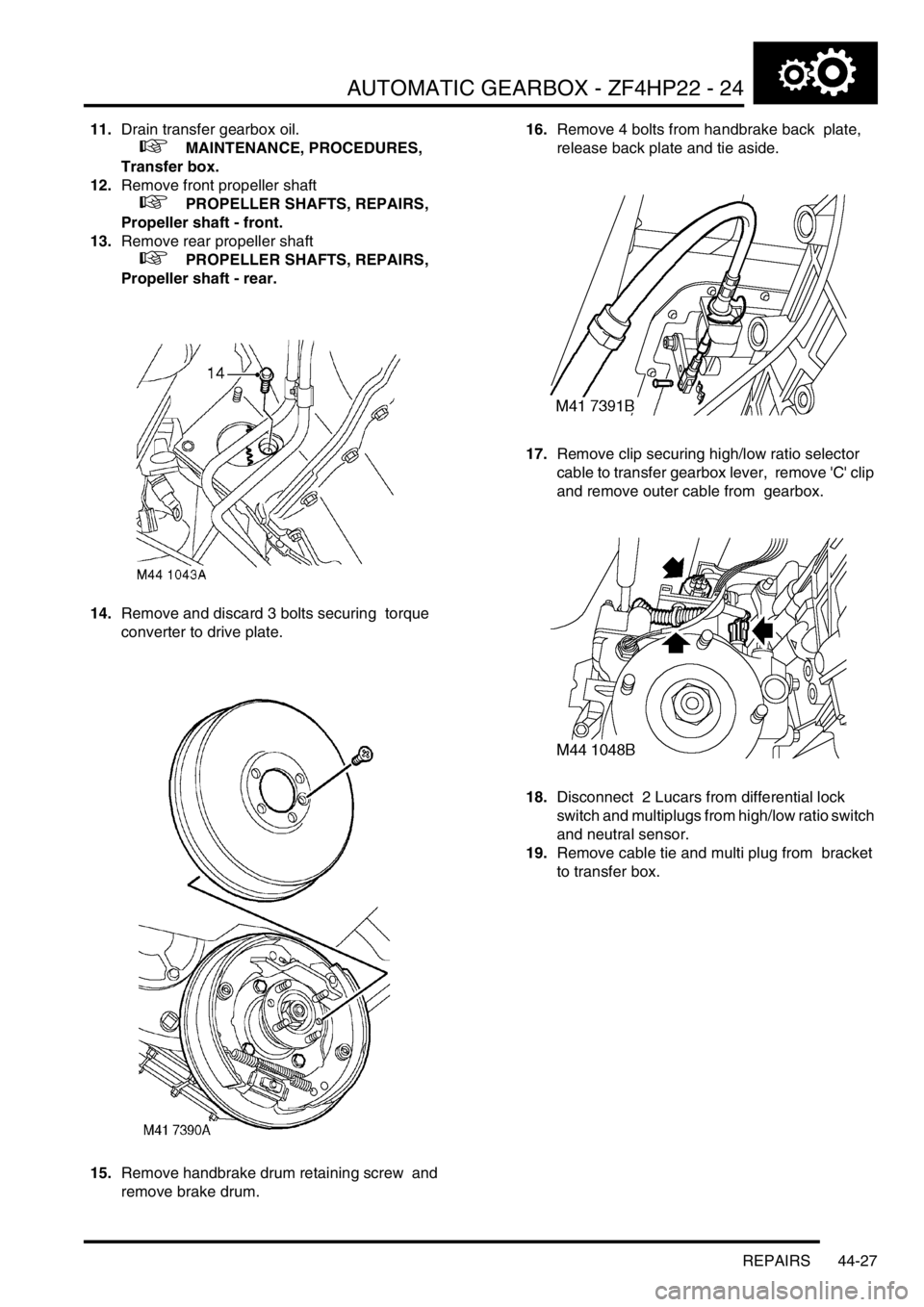
AUTOMATIC GEARBOX - ZF4HP22 - 24
REPAIRS 44-27
11.Drain transfer gearbox oil.
+ MAINTENANCE, PROCEDURES,
Transfer box.
12.Remove front propeller shaft
+ PROPELLER SHAFTS, REPAIRS,
Propeller shaft - front.
13.Remove rear propeller shaft
+ PROPELLER SHAFTS, REPAIRS,
Propeller shaft - rear.
14.Remove and discard 3 bolts securing torque
converter to drive plate.
15.Remove handbrake drum retaining screw and
remove brake drum. 16.Remove 4 bolts from handbrake back plate,
release back plate and tie aside.
17.Remove clip securing high/low ratio selector
cable to transfer gearbox lever, remove 'C' clip
and remove outer cable from gearbox.
18.Disconnect 2 Lucars from differential lock
switch and multiplugs from high/low ratio switch
and neutral sensor.
19.Remove cable tie and multi plug from bracket
to transfer box.
Page 827 of 1672
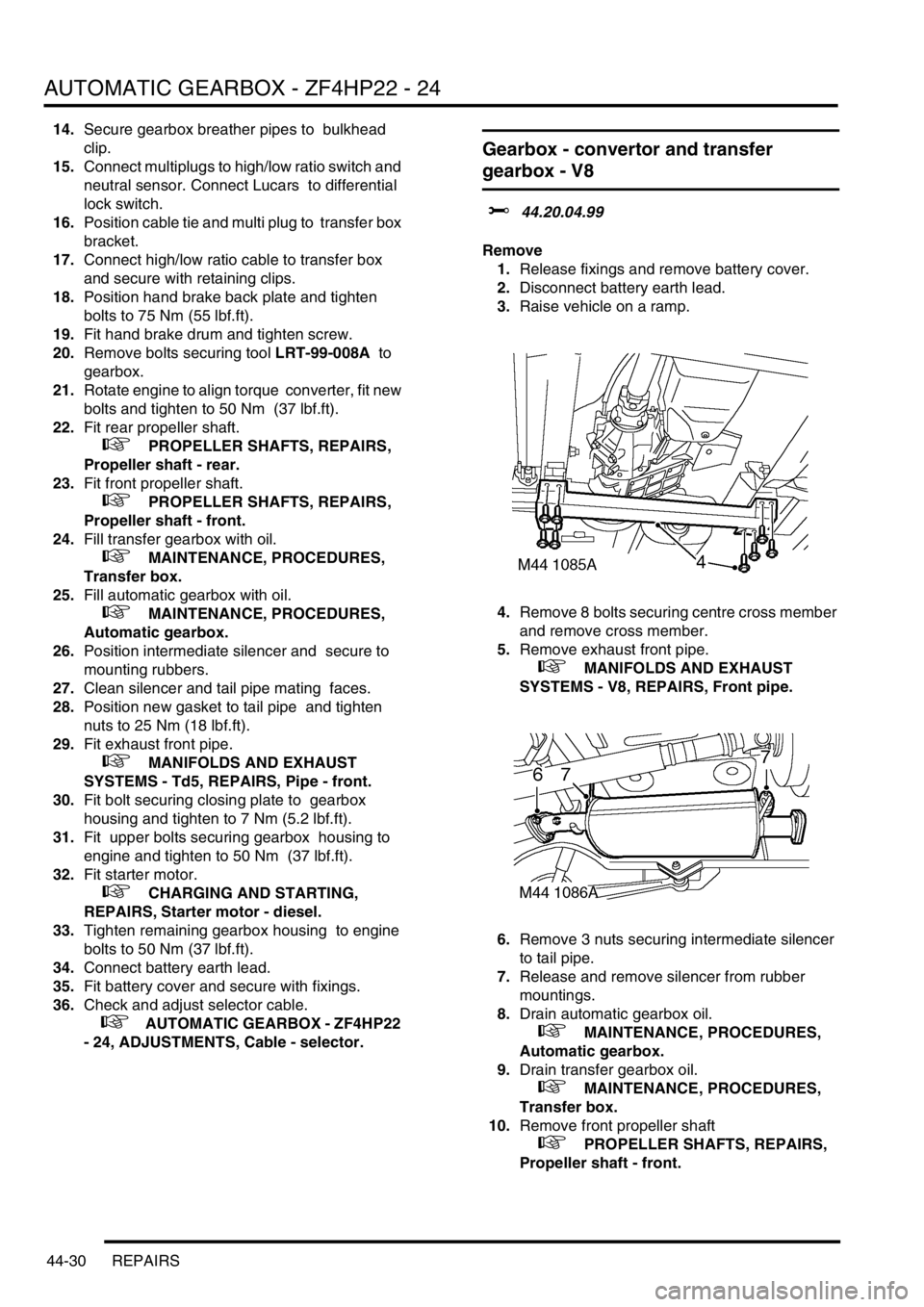
AUTOMATIC GEARBOX - ZF4HP22 - 24
44-30 REPAIRS
14.Secure gearbox breather pipes to bulkhead
clip.
15.Connect multiplugs to high/low ratio switch and
neutral sensor. Connect Lucars to differential
lock switch.
16.Position cable tie and multi plug to transfer box
bracket.
17.Connect high/low ratio cable to transfer box
and secure with retaining clips.
18.Position hand brake back plate and tighten
bolts to 75 Nm (55 lbf.ft).
19.Fit hand brake drum and tighten screw.
20.Remove bolts securing tool LRT-99-008A to
gearbox.
21.Rotate engine to align torque converter, fit new
bolts and tighten to 50 Nm (37 lbf.ft).
22.Fit rear propeller shaft.
+ PROPELLER SHAFTS, REPAIRS,
Propeller shaft - rear.
23.Fit front propeller shaft.
+ PROPELLER SHAFTS, REPAIRS,
Propeller shaft - front.
24.Fill transfer gearbox with oil.
+ MAINTENANCE, PROCEDURES,
Transfer box.
25.Fill automatic gearbox with oil.
+ MAINTENANCE, PROCEDURES,
Automatic gearbox.
26.Position intermediate silencer and secure to
mounting rubbers.
27.Clean silencer and tail pipe mating faces.
28.Position new gasket to tail pipe and tighten
nuts to 25 Nm (18 lbf.ft).
29.Fit exhaust front pipe.
+ MANIFOLDS AND EXHAUST
SYSTEMS - Td5, REPAIRS, Pipe - front.
30.Fit bolt securing closing plate to gearbox
housing and tighten to 7 Nm (5.2 lbf.ft).
31.Fit upper bolts securing gearbox housing to
engine and tighten to 50 Nm (37 lbf.ft).
32.Fit starter motor.
+ CHARGING AND STARTING,
REPAIRS, Starter motor - diesel.
33.Tighten remaining gearbox housing to engine
bolts to 50 Nm (37 lbf.ft).
34.Connect battery earth lead.
35.Fit battery cover and secure with fixings.
36.Check and adjust selector cable.
+ AUTOMATIC GEARBOX - ZF4HP22
- 24, ADJUSTMENTS, Cable - selector.
Gearbox - convertor and transfer
gearbox - V8
$% 44.20.04.99
Remove
1.Release fixings and remove battery cover.
2.Disconnect battery earth lead.
3.Raise vehicle on a ramp.
4.Remove 8 bolts securing centre cross member
and remove cross member.
5.Remove exhaust front pipe.
+ MANIFOLDS AND EXHAUST
SYSTEMS - V8, REPAIRS, Front pipe.
6.Remove 3 nuts securing intermediate silencer
to tail pipe.
7.Release and remove silencer from rubber
mountings.
8.Drain automatic gearbox oil.
+ MAINTENANCE, PROCEDURES,
Automatic gearbox.
9.Drain transfer gearbox oil.
+ MAINTENANCE, PROCEDURES,
Transfer box.
10.Remove front propeller shaft
+ PROPELLER SHAFTS, REPAIRS,
Propeller shaft - front.
Page 828 of 1672
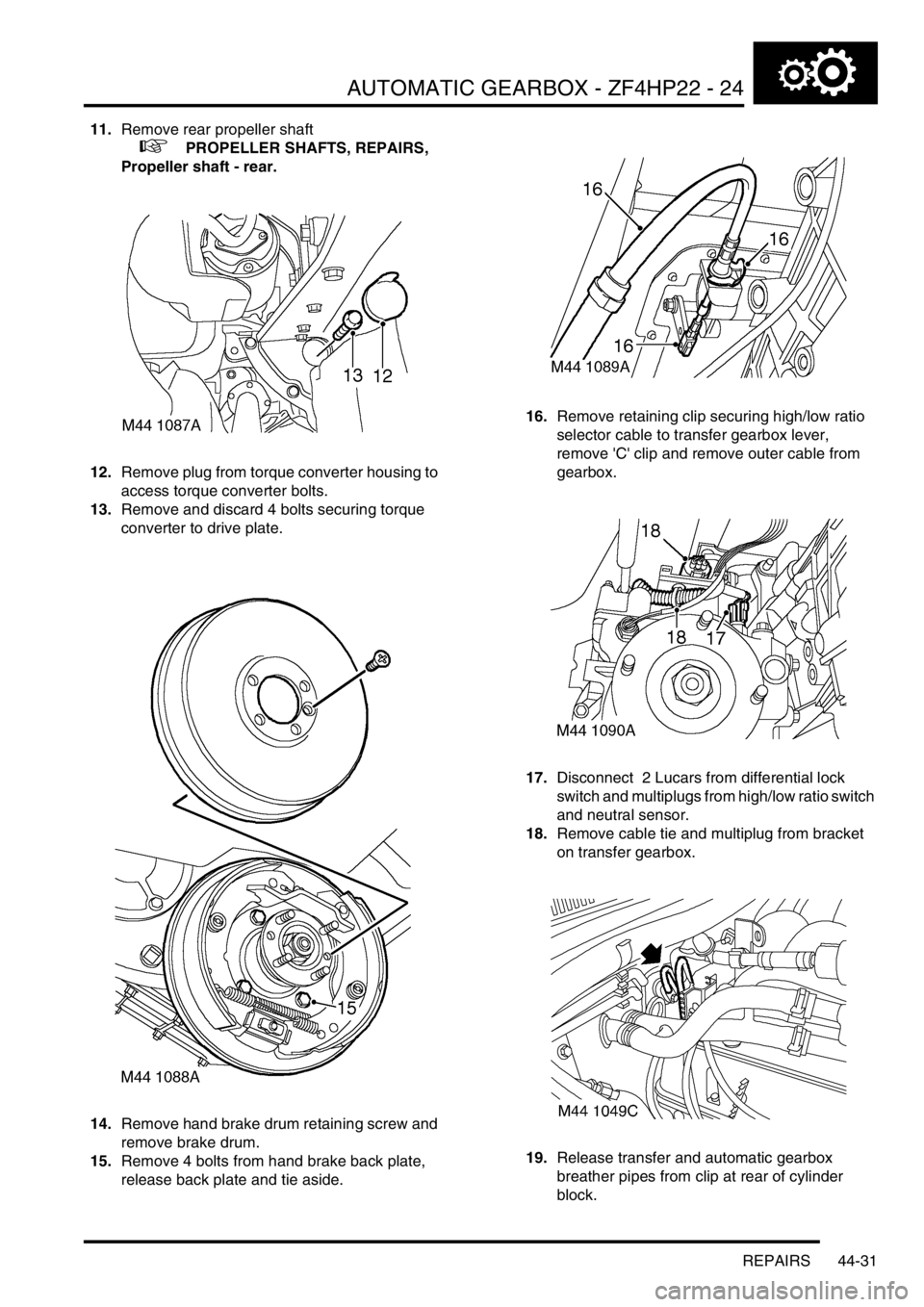
AUTOMATIC GEARBOX - ZF4HP22 - 24
REPAIRS 44-31
11.Remove rear propeller shaft
+ PROPELLER SHAFTS, REPAIRS,
Propeller shaft - rear.
12.Remove plug from torque converter housing to
access torque converter bolts.
13.Remove and discard 4 bolts securing torque
converter to drive plate.
14.Remove hand brake drum retaining screw and
remove brake drum.
15.Remove 4 bolts from hand brake back plate,
release back plate and tie aside. 16.Remove retaining clip securing high/low ratio
selector cable to transfer gearbox lever,
remove 'C' clip and remove outer cable from
gearbox.
17.Disconnect 2 Lucars from differential lock
switch and multiplugs from high/low ratio switch
and neutral sensor.
18.Remove cable tie and multiplug from bracket
on transfer gearbox.
19.Release transfer and automatic gearbox
breather pipes from clip at rear of cylinder
block.
Page 830 of 1672
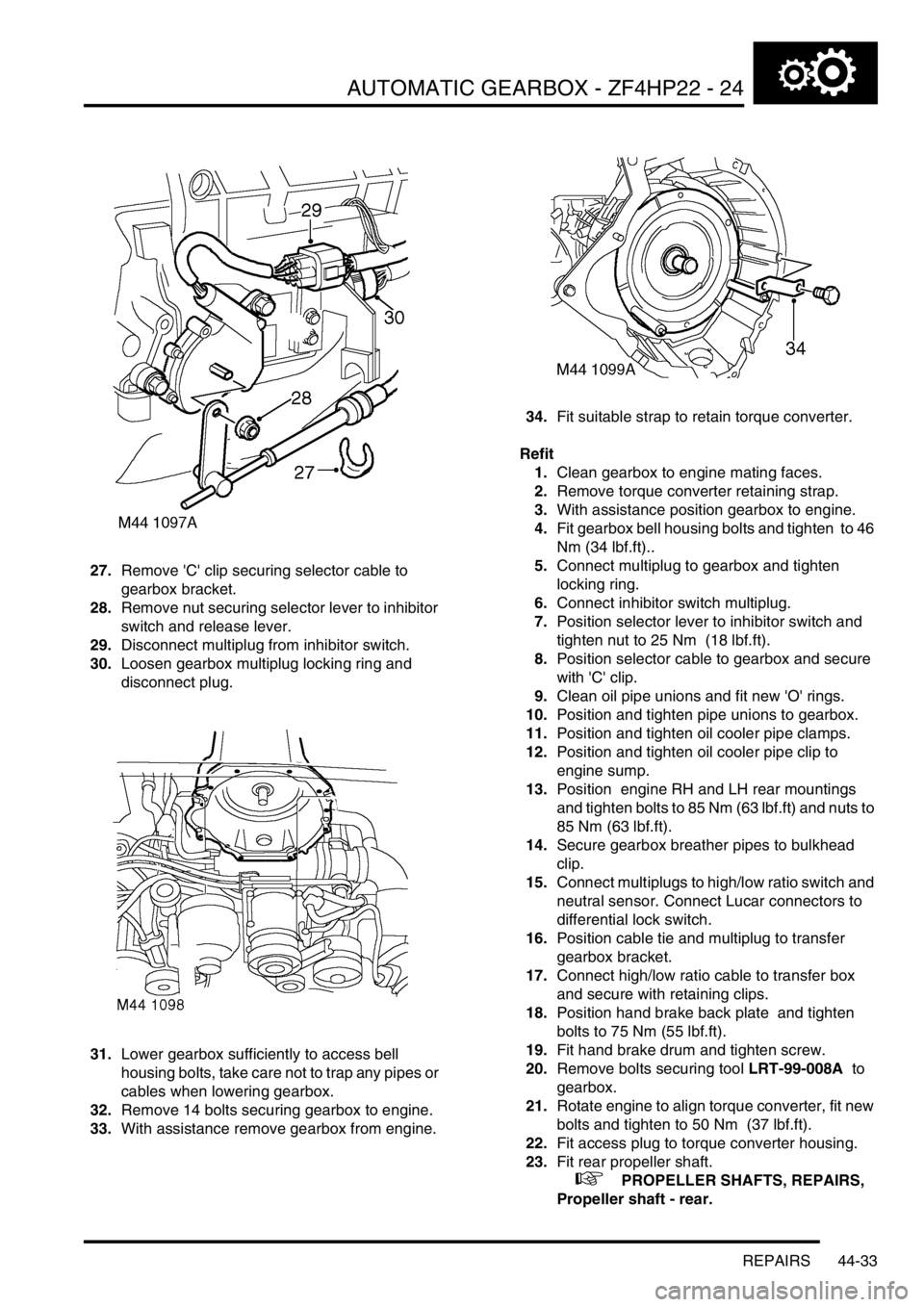
AUTOMATIC GEARBOX - ZF4HP22 - 24
REPAIRS 44-33
27.Remove 'C' clip securing selector cable to
gearbox bracket.
28.Remove nut securing selector lever to inhibitor
switch and release lever.
29.Disconnect multiplug from inhibitor switch.
30.Loosen gearbox multiplug locking ring and
disconnect plug.
31.Lower gearbox sufficiently to access bell
housing bolts, take care not to trap any pipes or
cables when lowering gearbox.
32.Remove 14 bolts securing gearbox to engine.
33.With assistance remove gearbox from engine.34.Fit suitable strap to retain torque converter.
Refit
1.Clean gearbox to engine mating faces.
2.Remove torque converter retaining strap.
3.With assistance position gearbox to engine.
4.Fit gearbox bell housing bolts and tighten to 46
Nm (34 lbf.ft)..
5.Connect multiplug to gearbox and tighten
locking ring.
6.Connect inhibitor switch multiplug.
7.Position selector lever to inhibitor switch and
tighten nut to 25 Nm (18 lbf.ft).
8.Position selector cable to gearbox and secure
with 'C' clip.
9.Clean oil pipe unions and fit new 'O' rings.
10.Position and tighten pipe unions to gearbox.
11.Position and tighten oil cooler pipe clamps.
12.Position and tighten oil cooler pipe clip to
engine sump.
13.Position engine RH and LH rear mountings
and tighten bolts to 85 Nm (63 lbf.ft) and nuts to
85 Nm (63 lbf.ft).
14.Secure gearbox breather pipes to bulkhead
clip.
15.Connect multiplugs to high/low ratio switch and
neutral sensor. Connect Lucar connectors to
differential lock switch.
16.Position cable tie and multiplug to transfer
gearbox bracket.
17.Connect high/low ratio cable to transfer box
and secure with retaining clips.
18.Position hand brake back plate and tighten
bolts to 75 Nm (55 lbf.ft).
19.Fit hand brake drum and tighten screw.
20.Remove bolts securing tool LRT-99-008A to
gearbox.
21.Rotate engine to align torque converter, fit new
bolts and tighten to 50 Nm (37 lbf.ft).
22.Fit access plug to torque converter housing.
23.Fit rear propeller shaft.
+ PROPELLER SHAFTS, REPAIRS,
Propeller shaft - rear.
Page 862 of 1672
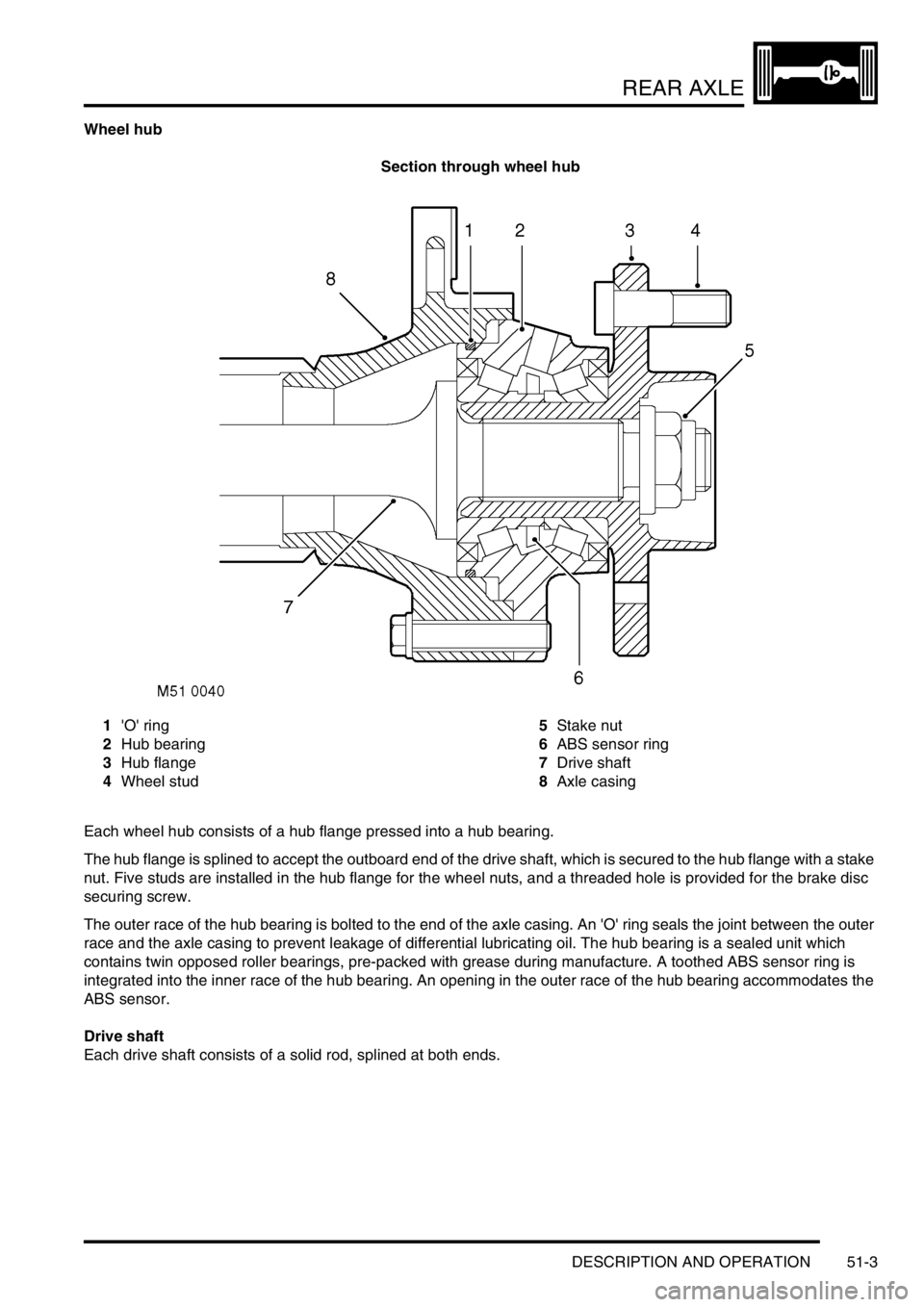
REAR AXLE
DESCRIPTION AND OPERATION 51-3
Wheel hub
Section through wheel hub
1'O' ring
2Hub bearing
3Hub flange
4Wheel stud5Stake nut
6ABS sensor ring
7Drive shaft
8Axle casing
Each wheel hub consists of a hub flange pressed into a hub bearing.
The hub flange is splined to accept the outboard end of the drive shaft, which is secured to the hub flange with a stake
nut. Five studs are installed in the hub flange for the wheel nuts, and a threaded hole is provided for the brake disc
securing screw.
The outer race of the hub bearing is bolted to the end of the axle casing. An 'O' ring seals the joint between the outer
race and the axle casing to prevent leakage of differential lubricating oil. The hub bearing is a sealed unit which
contains twin opposed roller bearings, pre-packed with grease during manufacture. A toothed ABS sensor ring is
integrated into the inner race of the hub bearing. An opening in the outer race of the hub bearing accommodates the
ABS sensor.
Drive shaft
Each drive shaft consists of a solid rod, splined at both ends.
Page 864 of 1672
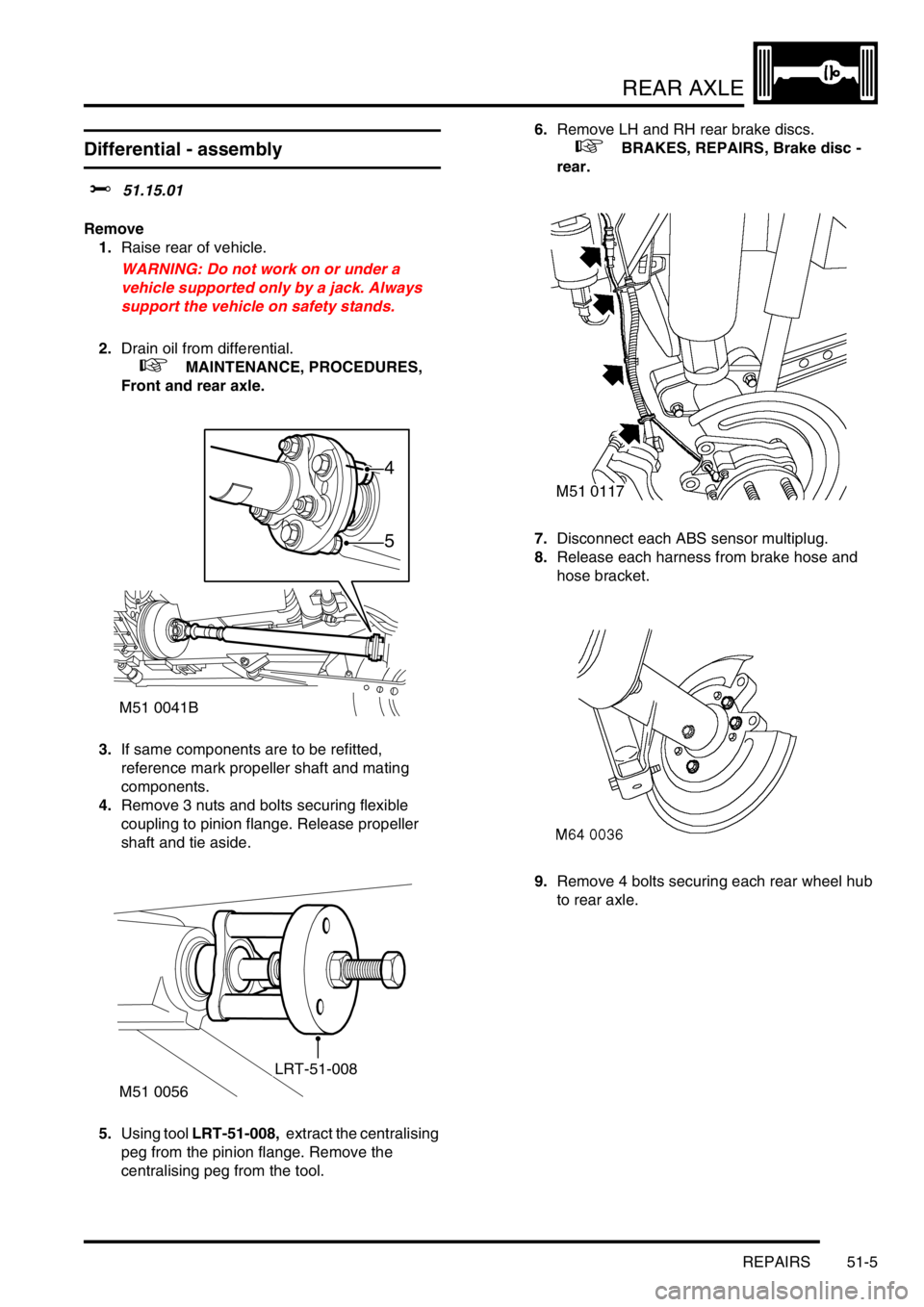
REAR AXLE
REPAIRS 51-5
REPAIRS
Differential - assembly
$% 51.15.01
Remove
1.Raise rear of vehicle.
WARNING: Do not work on or under a
vehicle supported only by a jack. Always
support the vehicle on safety stands.
2.Drain oil from differential.
+ MAINTENANCE, PROCEDURES,
Front and rear axle.
3.If same components are to be refitted,
reference mark propeller shaft and mating
components.
4.Remove 3 nuts and bolts securing flexible
coupling to pinion flange. Release propeller
shaft and tie aside.
5.Using tool LRT-51-008, extract the centralising
peg from the pinion flange. Remove the
centralising peg from the tool.6.Remove LH and RH rear brake discs.
+ BRAKES, REPAIRS, Brake disc -
rear.
7.Disconnect each ABS sensor multiplug.
8.Release each harness from brake hose and
hose bracket.
9.Remove 4 bolts securing each rear wheel hub
to rear axle.
M51 0041B
5
4
M51 0056
LRT-51-008
Page 865 of 1672
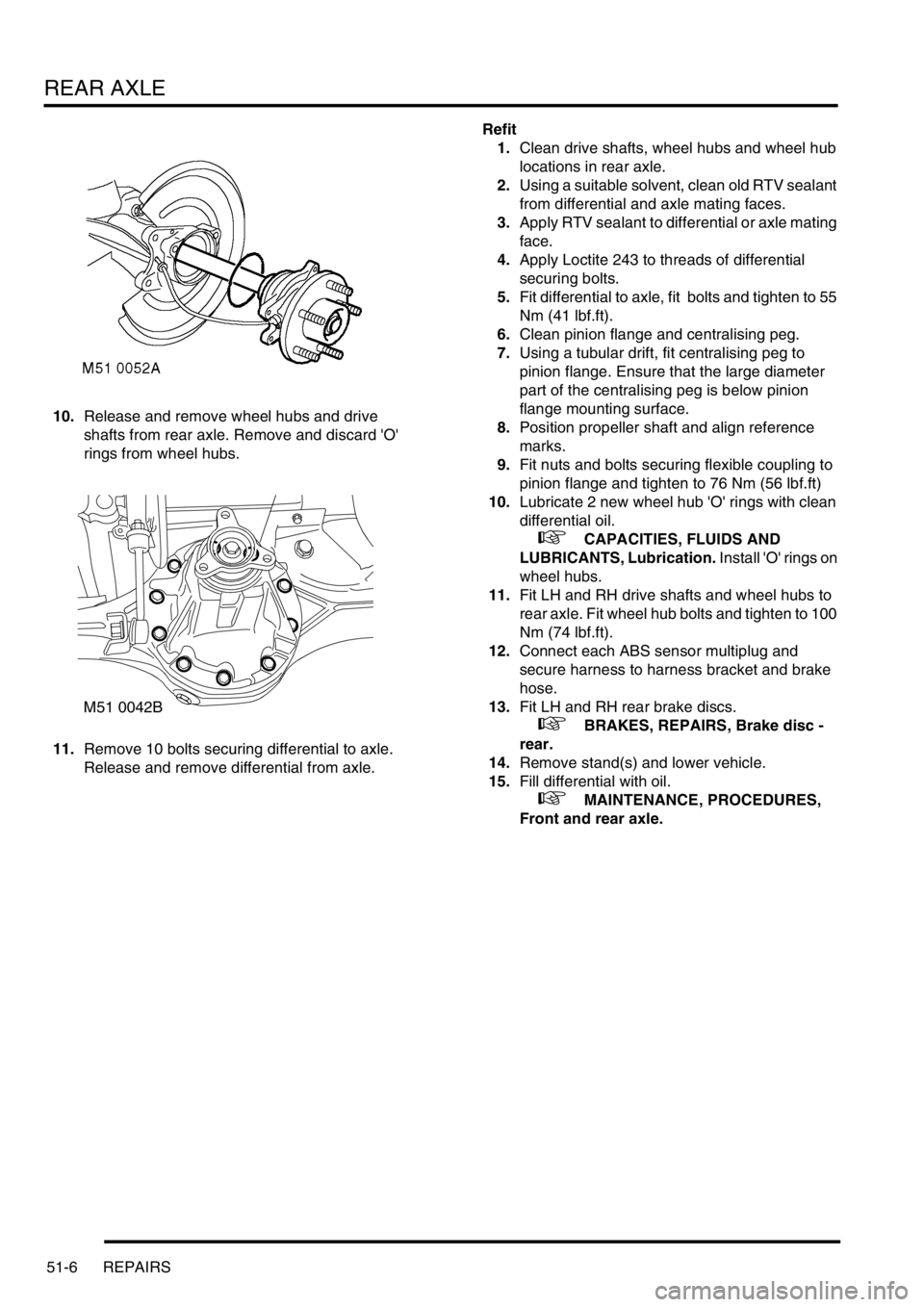
REAR AXLE
51-6 REPAIRS
10.Release and remove wheel hubs and drive
shafts from rear axle. Remove and discard 'O'
rings from wheel hubs.
11.Remove 10 bolts securing differential to axle.
Release and remove differential from axle. Refit
1.Clean drive shafts, wheel hubs and wheel hub
locations in rear axle.
2.Using a suitable solvent, clean old RTV sealant
from differential and axle mating faces.
3.Apply RTV sealant to differential or axle mating
face.
4.Apply Loctite 243 to threads of differential
securing bolts.
5.Fit differential to axle, fit bolts and tighten to 55
Nm (41 lbf.ft).
6.Clean pinion flange and centralising peg.
7.Using a tubular drift, fit centralising peg to
pinion flange. Ensure that the large diameter
part of the centralising peg is below pinion
flange mounting surface.
8.Position propeller shaft and align reference
marks.
9.Fit nuts and bolts securing flexible coupling to
pinion flange and tighten to 76 Nm (56 lbf.ft)
10.Lubricate 2 new wheel hub 'O' rings with clean
differential oil.
+ CAPACITIES, FLUIDS AND
LUBRICANTS, Lubrication. Install 'O' rings on
wheel hubs.
11.Fit LH and RH drive shafts and wheel hubs to
rear axle. Fit wheel hub bolts and tighten to 100
Nm (74 lbf.ft).
12.Connect each ABS sensor multiplug and
secure harness to harness bracket and brake
hose.
13.Fit LH and RH rear brake discs.
+ BRAKES, REPAIRS, Brake disc -
rear.
14.Remove stand(s) and lower vehicle.
15.Fill differential with oil.
+ MAINTENANCE, PROCEDURES,
Front and rear axle.
M51 0042B
Page 876 of 1672
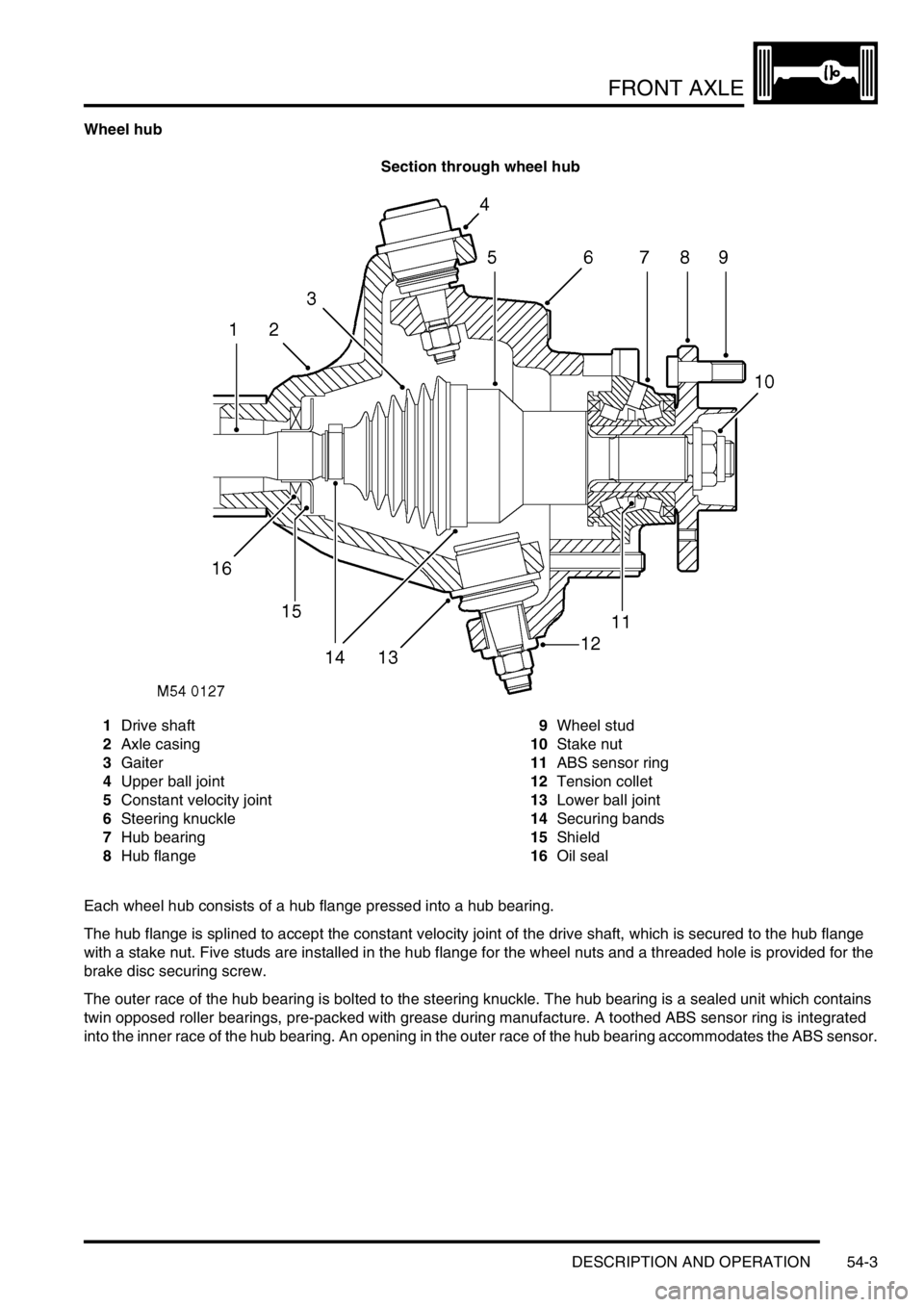
FRONT AXLE
DESCRIPTION AND OPERATION 54-3
Wheel hub
Section through wheel hub
1Drive shaft
2Axle casing
3Gaiter
4Upper ball joint
5Constant velocity joint
6Steering knuckle
7Hub bearing
8Hub flange9Wheel stud
10Stake nut
11ABS sensor ring
12Tension collet
13Lower ball joint
14Securing bands
15Shield
16Oil seal
Each wheel hub consists of a hub flange pressed into a hub bearing.
The hub flange is splined to accept the constant velocity joint of the drive shaft, which is secured to the hub flange
with a stake nut. Five studs are installed in the hub flange for the wheel nuts and a threaded hole is provided for the
brake disc securing screw.
The outer race of the hub bearing is bolted to the steering knuckle. The hub bearing is a sealed unit which contains
twin opposed roller bearings, pre-packed with grease during manufacture. A toothed ABS sensor ring is integrated
into the inner race of the hub bearing. An opening in the outer race of the hub bearing accommodates the ABS sensor.
Page 878 of 1672
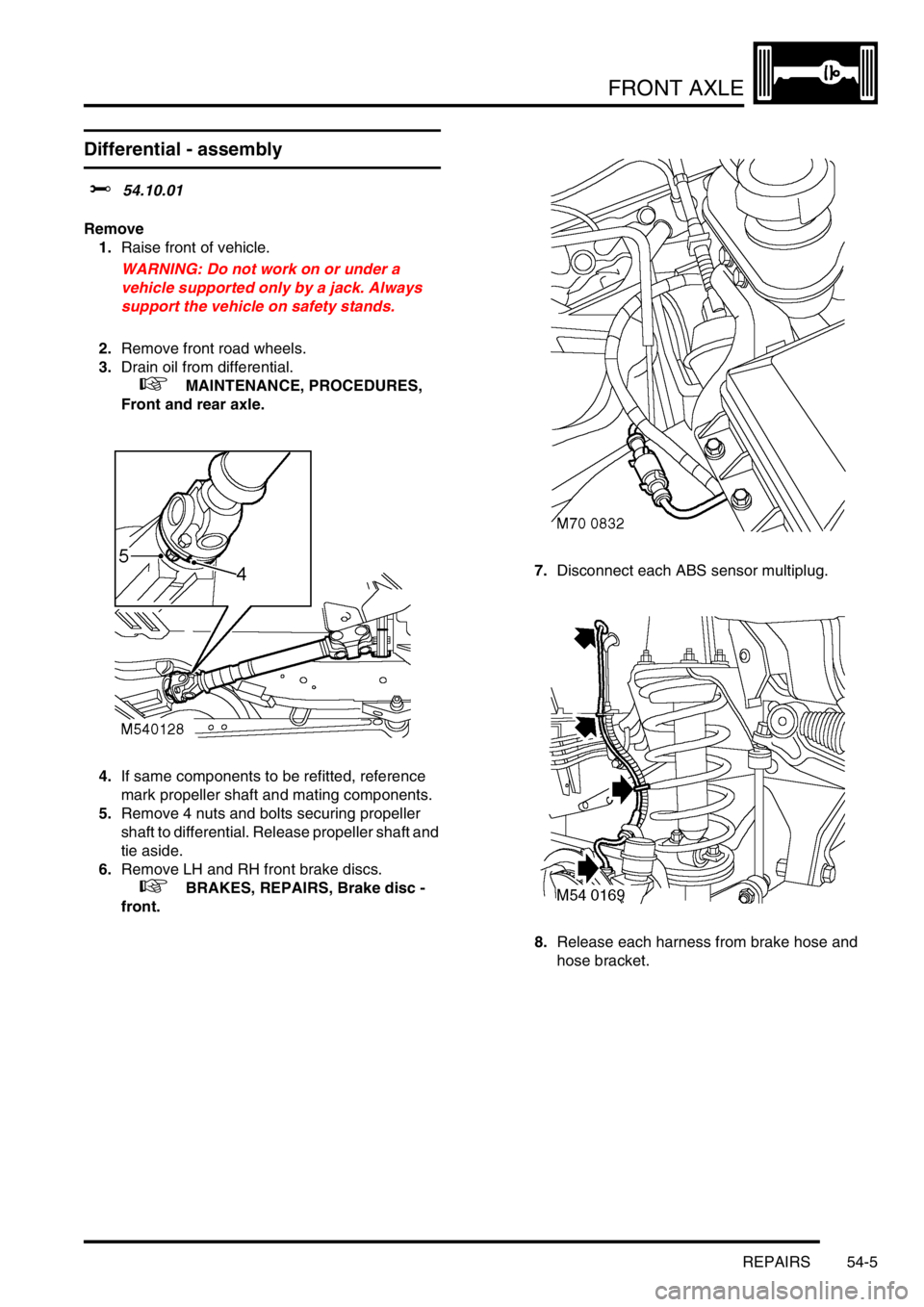
FRONT AXLE
REPAIRS 54-5
REPAIRS
Differential - assembly
$% 54.10.01
Remove
1.Raise front of vehicle.
WARNING: Do not work on or under a
vehicle supported only by a jack. Always
support the vehicle on safety stands.
2.Remove front road wheels.
3.Drain oil from differential.
+ MAINTENANCE, PROCEDURES,
Front and rear axle.
4.If same components to be refitted, reference
mark propeller shaft and mating components.
5.Remove 4 nuts and bolts securing propeller
shaft to differential. Release propeller shaft and
tie aside.
6.Remove LH and RH front brake discs.
+ BRAKES, REPAIRS, Brake disc -
front.7.Disconnect each ABS sensor multiplug.
8.Release each harness from brake hose and
hose bracket.