turn signal LAND ROVER DISCOVERY 2002 Workshop Manual
[x] Cancel search | Manufacturer: LAND ROVER, Model Year: 2002, Model line: DISCOVERY, Model: LAND ROVER DISCOVERY 2002Pages: 1672, PDF Size: 46.1 MB
Page 114 of 1672
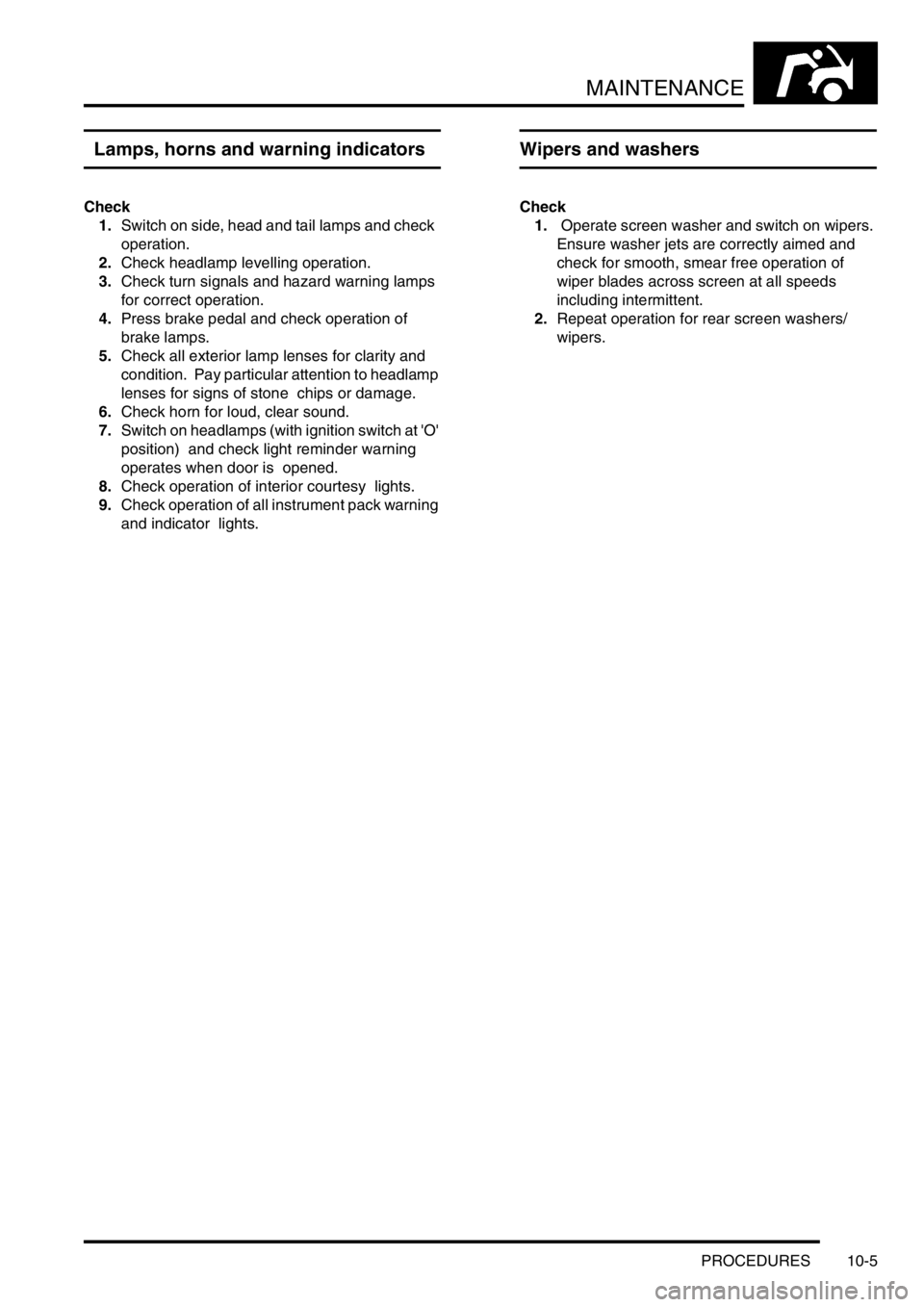
MAINTENANCE
PROCEDURES 10-5
Lamps, horns and warning indicators
Check
1.Switch on side, head and tail lamps and check
operation.
2.Check headlamp levelling operation.
3.Check turn signals and hazard warning lamps
for correct operation.
4.Press brake pedal and check operation of
brake lamps.
5.Check all exterior lamp lenses for clarity and
condition. Pay particular attention to headlamp
lenses for signs of stone chips or damage.
6.Check horn for loud, clear sound.
7.Switch on headlamps (with ignition switch at 'O'
position) and check light reminder warning
operates when door is opened.
8.Check operation of interior courtesy lights.
9.Check operation of all instrument pack warning
and indicator lights.
Wipers and washers
Check
1. Operate screen washer and switch on wipers.
Ensure washer jets are correctly aimed and
check for smooth, smear free operation of
wiper blades across screen at all speeds
including intermittent.
2.Repeat operation for rear screen washers/
wipers.
Page 327 of 1672
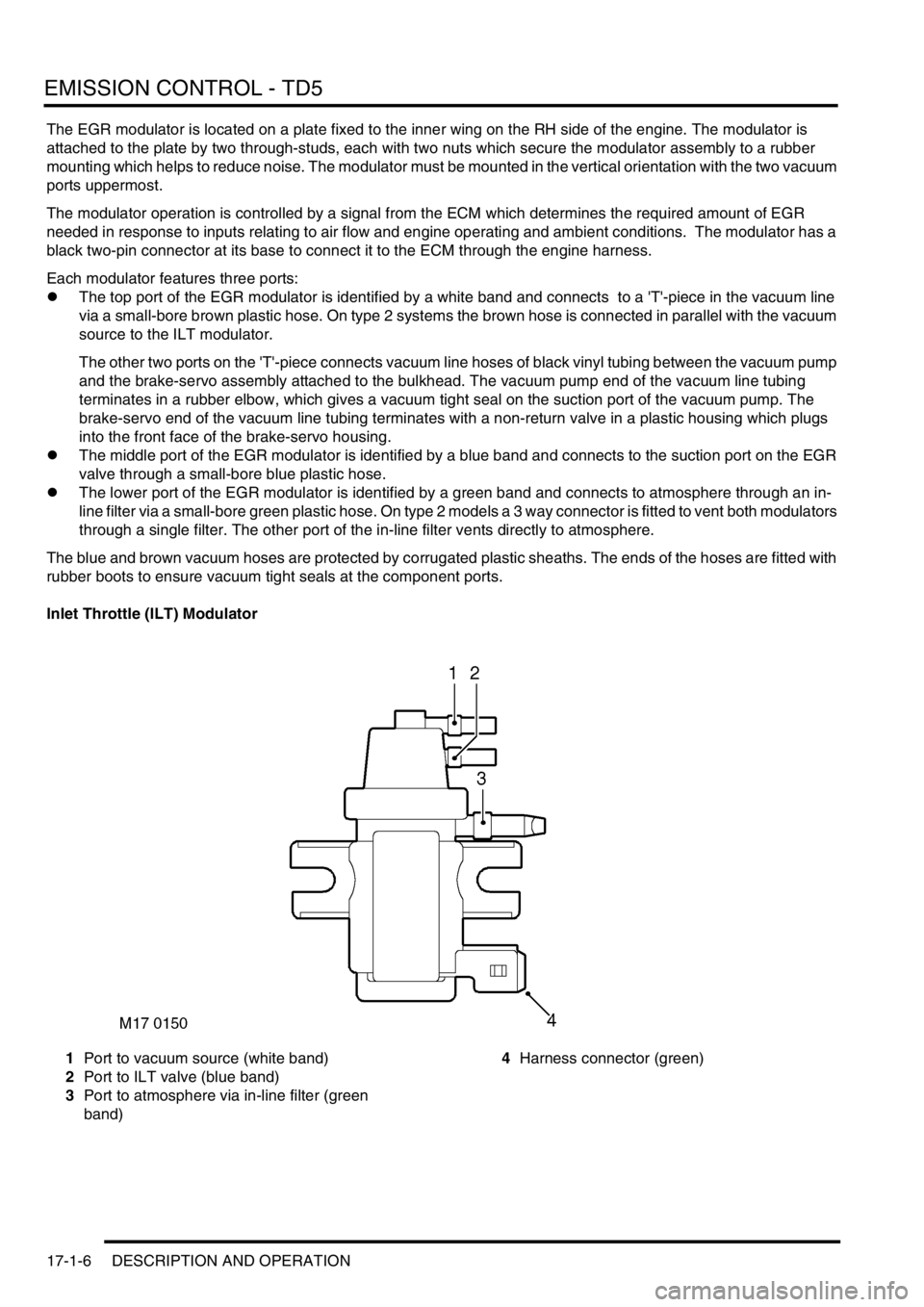
EMISSION CONTROL - TD5
17-1-6 DESCRIPTION AND OPERATION
The EGR modulator is located on a plate fixed to the inner wing on the RH side of the engine. The modulator is
attached to the plate by two through-studs, each with two nuts which secure the modulator assembly to a rubber
mounting which helps to reduce noise. The modulator must be mounted in the vertical orientation with the two vacuum
ports uppermost.
The modulator operation is controlled by a signal from the ECM which determines the required amount of EGR
needed in response to inputs relating to air flow and engine operating and ambient conditions. The modulator has a
black two-pin connector at its base to connect it to the ECM through the engine harness.
Each modulator features three ports:
lThe top port of the EGR modulator is identified by a white band and connects to a 'T'-piece in the vacuum line
via a small-bore brown plastic hose. On type 2 systems the brown hose is connected in parallel with the vacuum
source to the ILT modulator.
The other two ports on the 'T'-piece connects vacuum line hoses of black vinyl tubing between the vacuum pump
and the brake-servo assembly attached to the bulkhead. The vacuum pump end of the vacuum line tubing
terminates in a rubber elbow, which gives a vacuum tight seal on the suction port of the vacuum pump. The
brake-servo end of the vacuum line tubing terminates with a non-return valve in a plastic housing which plugs
into the front face of the brake-servo housing.
lThe middle port of the EGR modulator is identified by a blue band and connects to the suction port on the EGR
valve through a small-bore blue plastic hose.
lThe lower port of the EGR modulator is identified by a green band and connects to atmosphere through an in-
line filter via a small-bore green plastic hose. On type 2 models a 3 way connector is fitted to vent both modulators
through a single filter. The other port of the in-line filter vents directly to atmosphere.
The blue and brown vacuum hoses are protected by corrugated plastic sheaths. The ends of the hoses are fitted with
rubber boots to ensure vacuum tight seals at the component ports.
Inlet Throttle (ILT) Modulator
1Port to vacuum source (white band)
2Port to ILT valve (blue band)
3Port to atmosphere via in-line filter (green
band)4Harness connector (green)
Page 331 of 1672
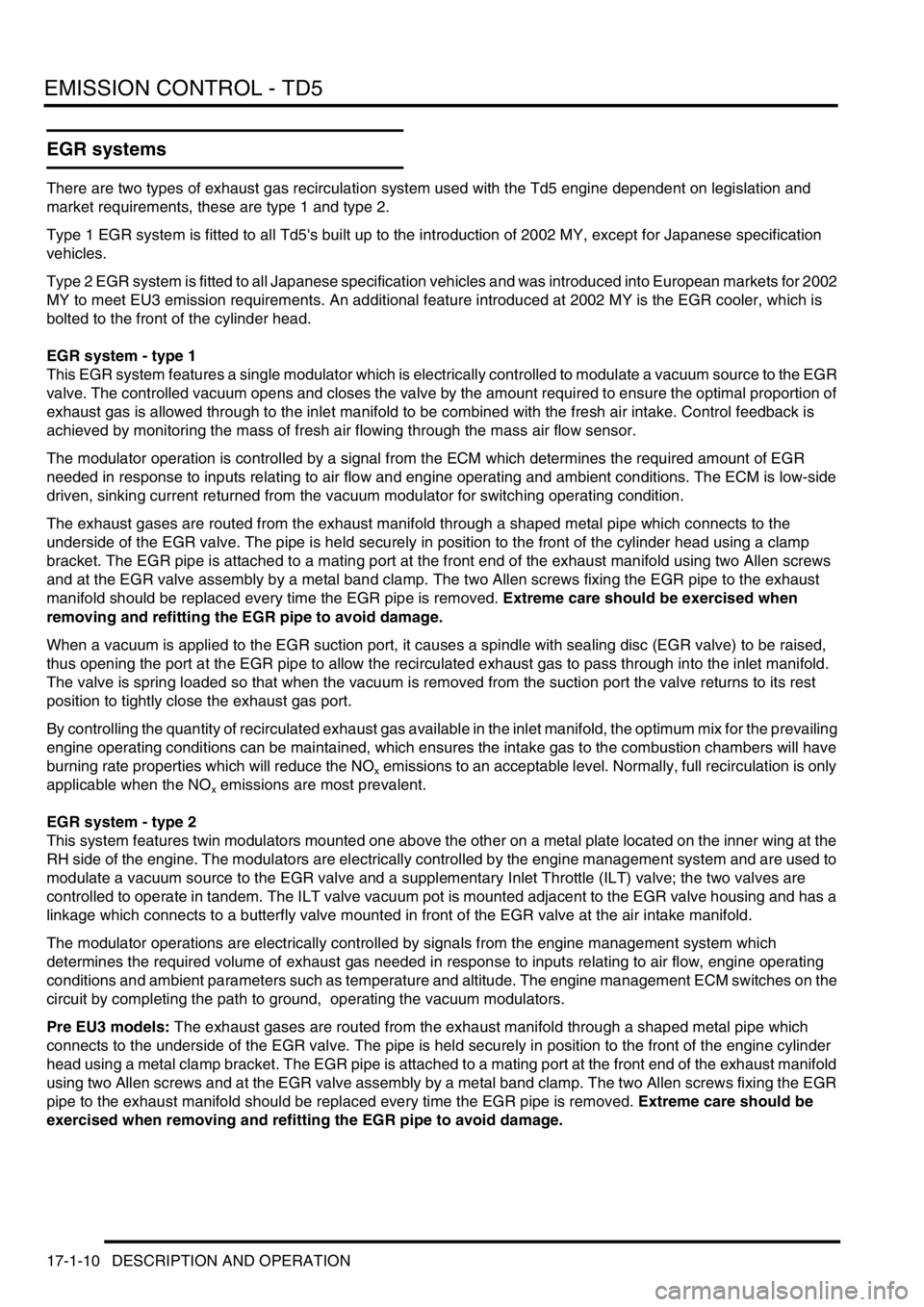
EMISSION CONTROL - TD5
17-1-10 DESCRIPTION AND OPERATION
EGR systems
There are two types of exhaust gas recirculation system used with the Td5 engine dependent on legislation and
market requirements, these are type 1 and type 2.
Type 1 EGR system is fitted to all Td5's built up to the introduction of 2002 MY, except for Japanese specification
vehicles.
Type 2 EGR system is fitted to all Japanese specification vehicles and was introduced into European markets for 2002
MY to meet EU3 emission requirements. An additional feature introduced at 2002 MY is the EGR cooler, which is
bolted to the front of the cylinder head.
EGR system - type 1
This EGR system features a single modulator which is electrically controlled to modulate a vacuum source to the EGR
valve. The controlled vacuum opens and closes the valve by the amount required to ensure the optimal proportion of
exhaust gas is allowed through to the inlet manifold to be combined with the fresh air intake. Control feedback is
achieved by monitoring the mass of fresh air flowing through the mass air flow sensor.
The modulator operation is controlled by a signal from the ECM which determines the required amount of EGR
needed in response to inputs relating to air flow and engine operating and ambient conditions. The ECM is low-side
driven, sinking current returned from the vacuum modulator for switching operating condition.
The exhaust gases are routed from the exhaust manifold through a shaped metal pipe which connects to the
underside of the EGR valve. The pipe is held securely in position to the front of the cylinder head using a clamp
bracket. The EGR pipe is attached to a mating port at the front end of the exhaust manifold using two Allen screws
and at the EGR valve assembly by a metal band clamp. The two Allen screws fixing the EGR pipe to the exhaust
manifold should be replaced every time the EGR pipe is removed. Extreme care should be exercised when
removing and refitting the EGR pipe to avoid damage.
When a vacuum is applied to the EGR suction port, it causes a spindle with sealing disc (EGR valve) to be raised,
thus opening the port at the EGR pipe to allow the recirculated exhaust gas to pass through into the inlet manifold.
The valve is spring loaded so that when the vacuum is removed from the suction port the valve returns to its rest
position to tightly close the exhaust gas port.
By controlling the quantity of recirculated exhaust gas available in the inlet manifold, the optimum mix for the prevailing
engine operating conditions can be maintained, which ensures the intake gas to the combustion chambers will have
burning rate properties which will reduce the NO
x emissions to an acceptable level. Normally, full recirculation is only
applicable when the NO
x emissions are most prevalent.
EGR system - type 2
This system features twin modulators mounted one above the other on a metal plate located on the inner wing at the
RH side of the engine. The modulators are electrically controlled by the engine management system and are used to
modulate a vacuum source to the EGR valve and a supplementary Inlet Throttle (ILT) valve; the two valves are
controlled to operate in tandem. The ILT valve vacuum pot is mounted adjacent to the EGR valve housing and has a
linkage which connects to a butterfly valve mounted in front of the EGR valve at the air intake manifold.
The modulator operations are electrically controlled by signals from the engine management system which
determines the required volume of exhaust gas needed in response to inputs relating to air flow, engine operating
conditions and ambient parameters such as temperature and altitude. The engine management ECM switches on the
circuit by completing the path to ground, operating the vacuum modulators.
Pre EU3 models: The exhaust gases are routed from the exhaust manifold through a shaped metal pipe which
connects to the underside of the EGR valve. The pipe is held securely in position to the front of the engine cylinder
head using a metal clamp bracket. The EGR pipe is attached to a mating port at the front end of the exhaust manifold
using two Allen screws and at the EGR valve assembly by a metal band clamp. The two Allen screws fixing the EGR
pipe to the exhaust manifold should be replaced every time the EGR pipe is removed. Extreme care should be
exercised when removing and refitting the EGR pipe to avoid damage.
Page 375 of 1672
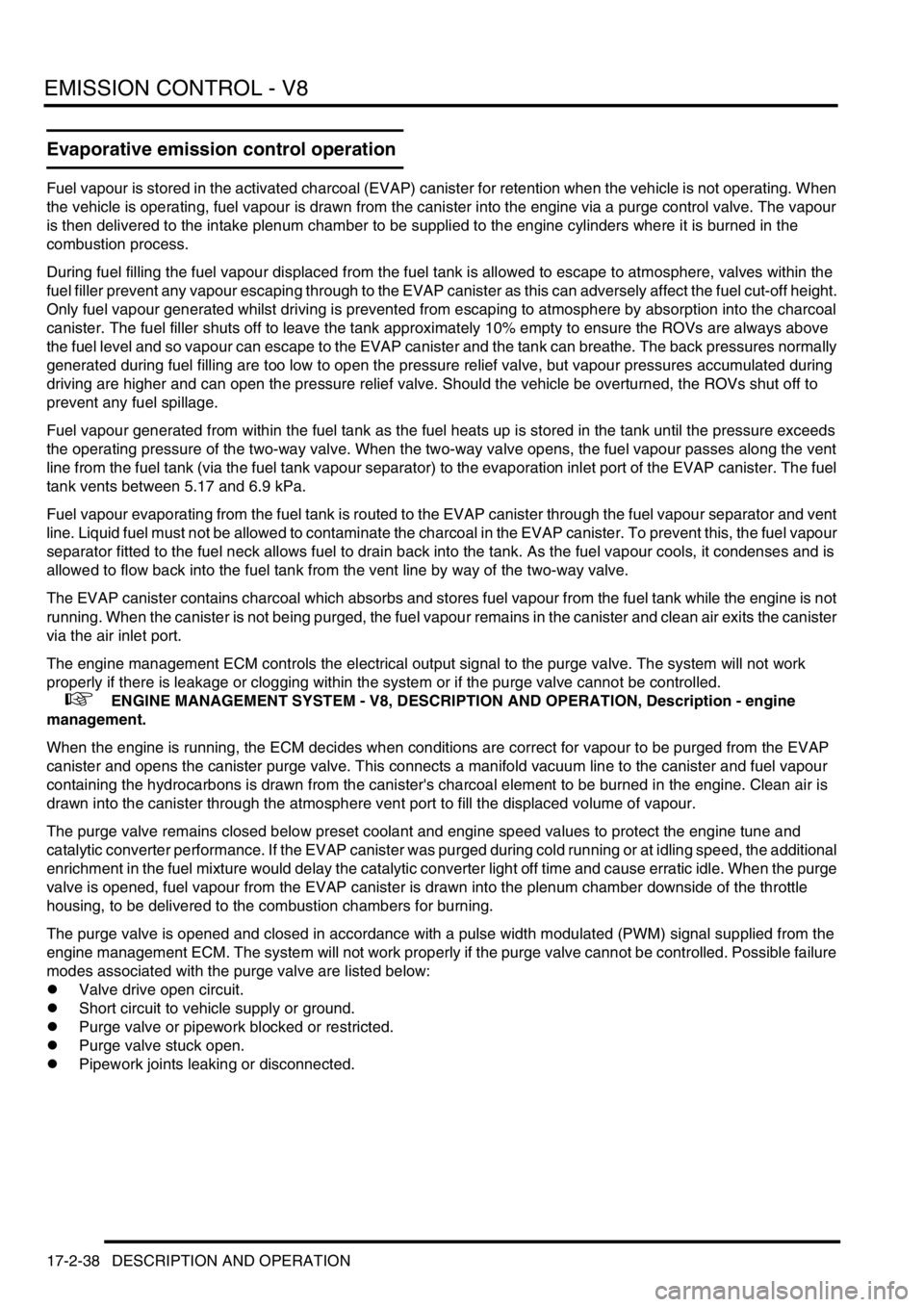
EMISSION CONTROL - V8
17-2-38 DESCRIPTION AND OPERATION
Evaporative emission control operation
Fuel vapour is stored in the activated charcoal (EVAP) canister for retention when the vehicle is not operating. When
the vehicle is operating, fuel vapour is drawn from the canister into the engine via a purge control valve. The vapour
is then delivered to the intake plenum chamber to be supplied to the engine cylinders where it is burned in the
combustion process.
During fuel filling the fuel vapour displaced from the fuel tank is allowed to escape to atmosphere, valves within the
fuel filler prevent any vapour escaping through to the EVAP canister as this can adversely affect the fuel cut-off height.
Only fuel vapour generated whilst driving is prevented from escaping to atmosphere by absorption into the charcoal
canister. The fuel filler shuts off to leave the tank approximately 10% empty to ensure the ROVs are always above
the fuel level and so vapour can escape to the EVAP canister and the tank can breathe. The back pressures normally
generated during fuel filling are too low to open the pressure relief valve, but vapour pressures accumulated during
driving are higher and can open the pressure relief valve. Should the vehicle be overturned, the ROVs shut off to
prevent any fuel spillage.
Fuel vapour generated from within the fuel tank as the fuel heats up is stored in the tank until the pressure exceeds
the operating pressure of the two-way valve. When the two-way valve opens, the fuel vapour passes along the vent
line from the fuel tank (via the fuel tank vapour separator) to the evaporation inlet port of the EVAP canister. The fuel
tank vents between 5.17 and 6.9 kPa.
Fuel vapour evaporating from the fuel tank is routed to the EVAP canister through the fuel vapour separator and vent
line. Liquid fuel must not be allowed to contaminate the charcoal in the EVAP canister. To prevent this, the fuel vapour
separator fitted to the fuel neck allows fuel to drain back into the tank. As the fuel vapour cools, it condenses and is
allowed to flow back into the fuel tank from the vent line by way of the two-way valve.
The EVAP canister contains charcoal which absorbs and stores fuel vapour from the fuel tank while the engine is not
running. When the canister is not being purged, the fuel vapour remains in the canister and clean air exits the canister
via the air inlet port.
The engine management ECM controls the electrical output signal to the purge valve. The system will not work
properly if there is leakage or clogging within the system or if the purge valve cannot be controlled.
+ ENGINE MANAGEMENT SYSTEM - V8, DESCRIPTION AND OPERATION, Description - engine
management.
When the engine is running, the ECM decides when conditions are correct for vapour to be purged from the EVAP
canister and opens the canister purge valve. This connects a manifold vacuum line to the canister and fuel vapour
containing the hydrocarbons is drawn from the canister's charcoal element to be burned in the engine. Clean air is
drawn into the canister through the atmosphere vent port to fill the displaced volume of vapour.
The purge valve remains closed below preset coolant and engine speed values to protect the engine tune and
catalytic converter performance. If the EVAP canister was purged during cold running or at idling speed, the additional
enrichment in the fuel mixture would delay the catalytic converter light off time and cause erratic idle. When the purge
valve is opened, fuel vapour from the EVAP canister is drawn into the plenum chamber downside of the throttle
housing, to be delivered to the combustion chambers for burning.
The purge valve is opened and closed in accordance with a pulse width modulated (PWM) signal supplied from the
engine management ECM. The system will not work properly if the purge valve cannot be controlled. Possible failure
modes associated with the purge valve are listed below:
lValve drive open circuit.
lShort circuit to vehicle supply or ground.
lPurge valve or pipework blocked or restricted.
lPurge valve stuck open.
lPipework joints leaking or disconnected.
Page 376 of 1672
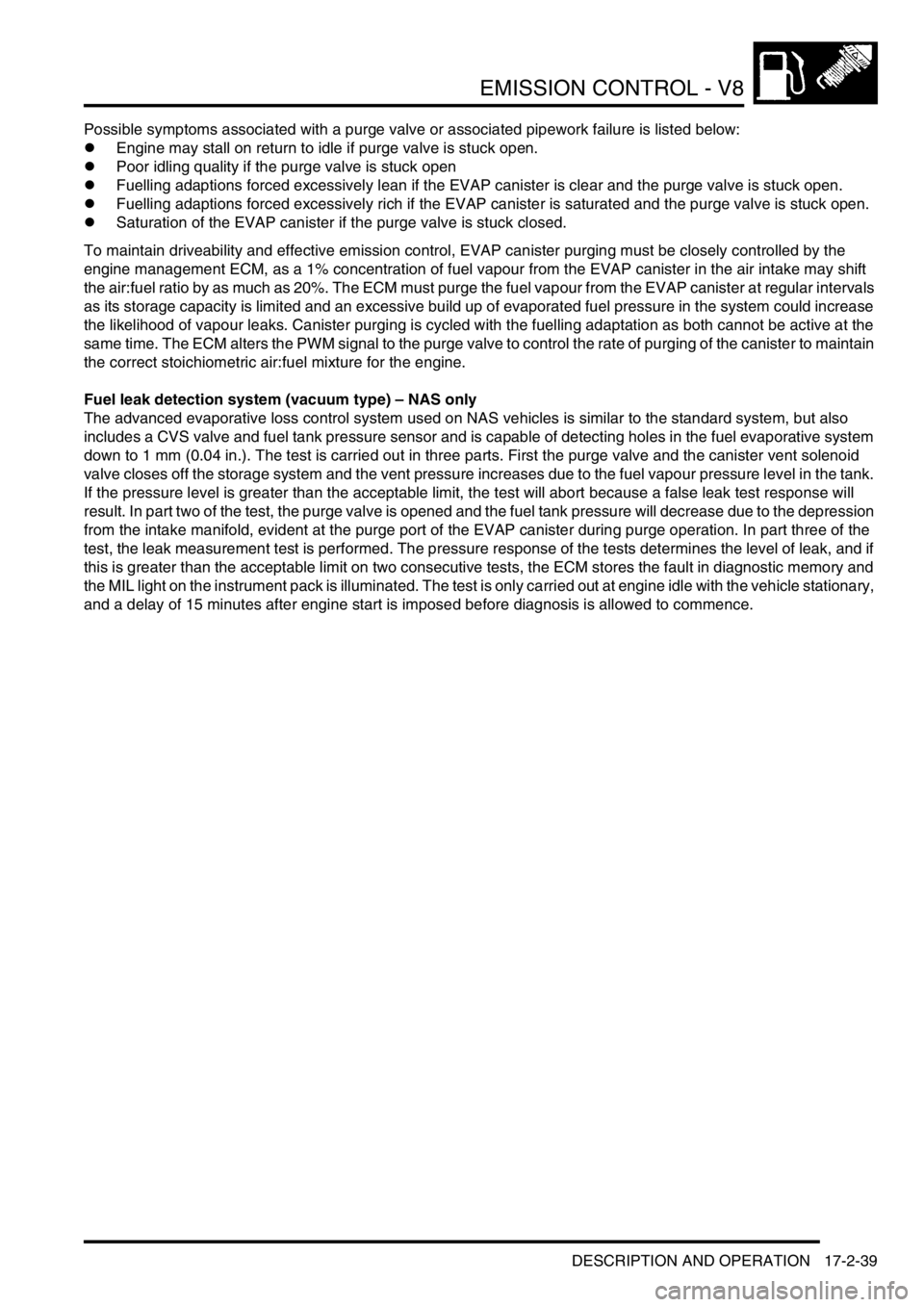
EMISSION CONTROL - V8
DESCRIPTION AND OPERATION 17-2-39
Possible symptoms associated with a purge valve or associated pipework failure is listed below:
lEngine may stall on return to idle if purge valve is stuck open.
lPoor idling quality if the purge valve is stuck open
lFuelling adaptions forced excessively lean if the EVAP canister is clear and the purge valve is stuck open.
lFuelling adaptions forced excessively rich if the EVAP canister is saturated and the purge valve is stuck open.
lSaturation of the EVAP canister if the purge valve is stuck closed.
To maintain driveability and effective emission control, EVAP canister purging must be closely controlled by the
engine management ECM, as a 1% concentration of fuel vapour from the EVAP canister in the air intake may shift
the air:fuel ratio by as much as 20%. The ECM must purge the fuel vapour from the EVAP canister at regular intervals
as its storage capacity is limited and an excessive build up of evaporated fuel pressure in the system could increase
the likelihood of vapour leaks. Canister purging is cycled with the fuelling adaptation as both cannot be active at the
same time. The ECM alters the PWM signal to the purge valve to control the rate of purging of the canister to maintain
the correct stoichiometric air:fuel mixture for the engine.
Fuel leak detection system (vacuum type) – NAS only
The advanced evaporative loss control system used on NAS vehicles is similar to the standard system, but also
includes a CVS valve and fuel tank pressure sensor and is capable of detecting holes in the fuel evaporative system
down to 1 mm (0.04 in.). The test is carried out in three parts. First the purge valve and the canister vent solenoid
valve closes off the storage system and the vent pressure increases due to the fuel vapour pressure level in the tank.
If the pressure level is greater than the acceptable limit, the test will abort because a false leak test response will
result. In part two of the test, the purge valve is opened and the fuel tank pressure will decrease due to the depression
from the intake manifold, evident at the purge port of the EVAP canister during purge operation. In part three of the
test, the leak measurement test is performed. The pressure response of the tests determines the level of leak, and if
this is greater than the acceptable limit on two consecutive tests, the ECM stores the fault in diagnostic memory and
the MIL light on the instrument pack is illuminated. The test is only carried out at engine idle with the vehicle stationary,
and a delay of 15 minutes after engine start is imposed before diagnosis is allowed to commence.
Page 377 of 1672
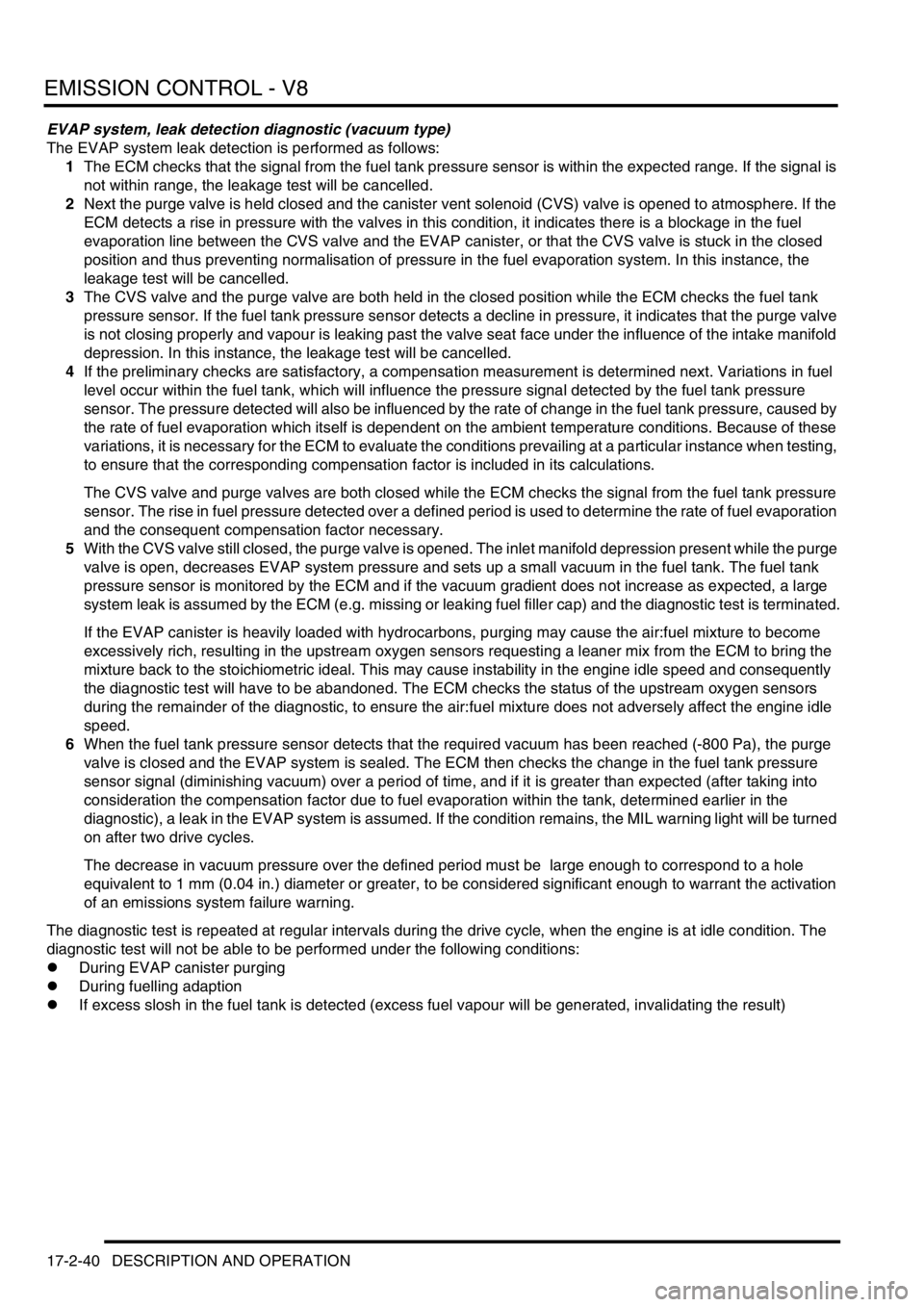
EMISSION CONTROL - V8
17-2-40 DESCRIPTION AND OPERATION
EVAP system, leak detection diagnostic (vacuum type)
The EVAP system leak detection is performed as follows:
1The ECM checks that the signal from the fuel tank pressure sensor is within the expected range. If the signal is
not within range, the leakage test will be cancelled.
2Next the purge valve is held closed and the canister vent solenoid (CVS) valve is opened to atmosphere. If the
ECM detects a rise in pressure with the valves in this condition, it indicates there is a blockage in the fuel
evaporation line between the CVS valve and the EVAP canister, or that the CVS valve is stuck in the closed
position and thus preventing normalisation of pressure in the fuel evaporation system. In this instance, the
leakage test will be cancelled.
3The CVS valve and the purge valve are both held in the closed position while the ECM checks the fuel tank
pressure sensor. If the fuel tank pressure sensor detects a decline in pressure, it indicates that the purge valve
is not closing properly and vapour is leaking past the valve seat face under the influence of the intake manifold
depression. In this instance, the leakage test will be cancelled.
4If the preliminary checks are satisfactory, a compensation measurement is determined next. Variations in fuel
level occur within the fuel tank, which will influence the pressure signal detected by the fuel tank pressure
sensor. The pressure detected will also be influenced by the rate of change in the fuel tank pressure, caused by
the rate of fuel evaporation which itself is dependent on the ambient temperature conditions. Because of these
variations, it is necessary for the ECM to evaluate the conditions prevailing at a particular instance when testing,
to ensure that the corresponding compensation factor is included in its calculations.
The CVS valve and purge valves are both closed while the ECM checks the signal from the fuel tank pressure
sensor. The rise in fuel pressure detected over a defined period is used to determine the rate of fuel evaporation
and the consequent compensation factor necessary.
5With the CVS valve still closed, the purge valve is opened. The inlet manifold depression present while the purge
valve is open, decreases EVAP system pressure and sets up a small vacuum in the fuel tank. The fuel tank
pressure sensor is monitored by the ECM and if the vacuum gradient does not increase as expected, a large
system leak is assumed by the ECM (e.g. missing or leaking fuel filler cap) and the diagnostic test is terminated.
If the EVAP canister is heavily loaded with hydrocarbons, purging may cause the air:fuel mixture to become
excessively rich, resulting in the upstream oxygen sensors requesting a leaner mix from the ECM to bring the
mixture back to the stoichiometric ideal. This may cause instability in the engine idle speed and consequently
the diagnostic test will have to be abandoned. The ECM checks the status of the upstream oxygen sensors
during the remainder of the diagnostic, to ensure the air:fuel mixture does not adversely affect the engine idle
speed.
6When the fuel tank pressure sensor detects that the required vacuum has been reached (-800 Pa), the purge
valve is closed and the EVAP system is sealed. The ECM then checks the change in the fuel tank pressure
sensor signal (diminishing vacuum) over a period of time, and if it is greater than expected (after taking into
consideration the compensation factor due to fuel evaporation within the tank, determined earlier in the
diagnostic), a leak in the EVAP system is assumed. If the condition remains, the MIL warning light will be turned
on after two drive cycles.
The decrease in vacuum pressure over the defined period must be large enough to correspond to a hole
equivalent to 1 mm (0.04 in.) diameter or greater, to be considered significant enough to warrant the activation
of an emissions system failure warning.
The diagnostic test is repeated at regular intervals during the drive cycle, when the engine is at idle condition. The
diagnostic test will not be able to be performed under the following conditions:
lDuring EVAP canister purging
lDuring fuelling adaption
lIf excess slosh in the fuel tank is detected (excess fuel vapour will be generated, invalidating the result)
Page 411 of 1672
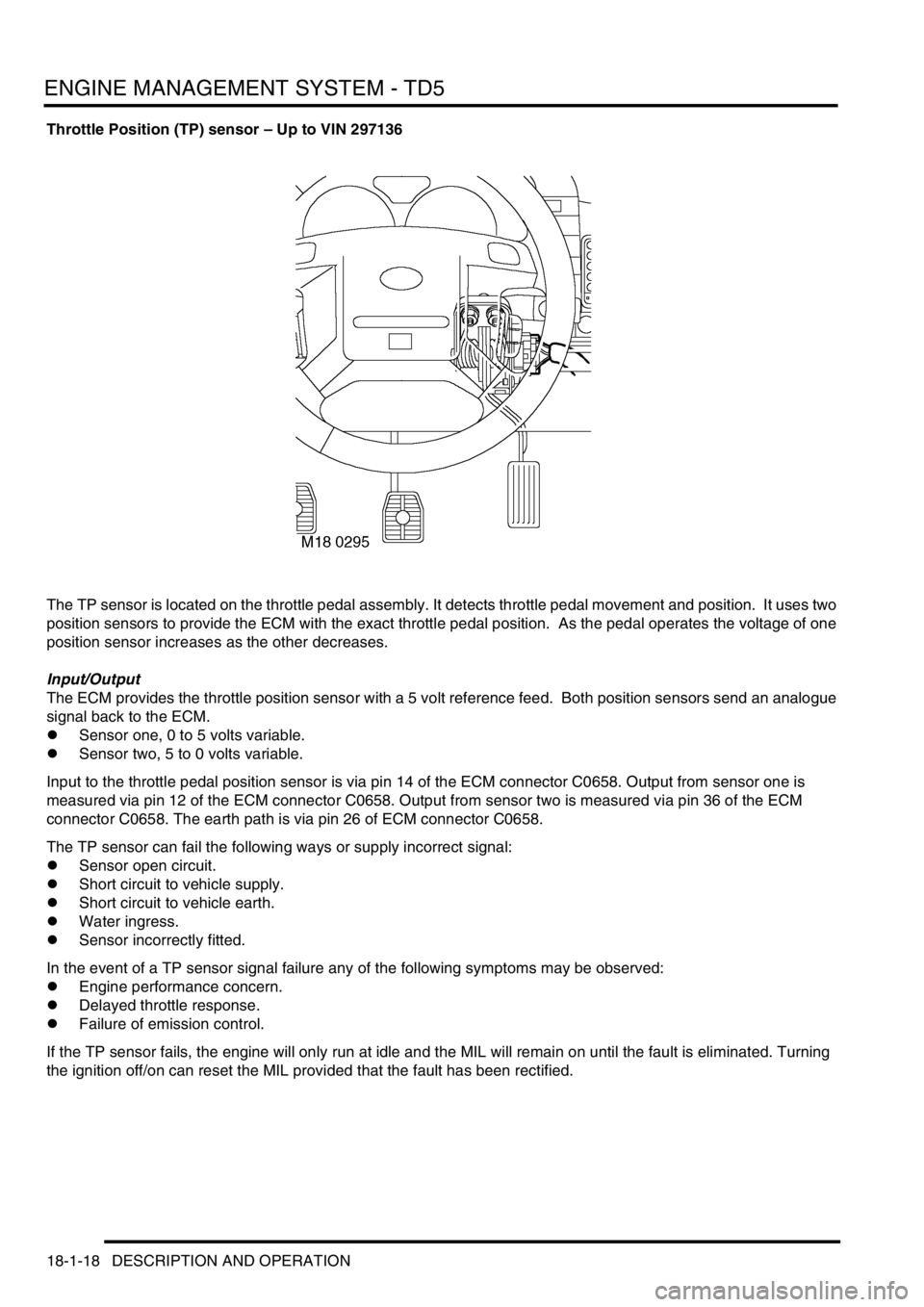
ENGINE MANAGEMENT SYSTEM - TD5
18-1-18 DESCRIPTION AND OPERATION
Throttle Position (TP) sensor – Up to VIN 297136
The TP sensor is located on the throttle pedal assembly. It detects throttle pedal movement and position. It uses two
position sensors to provide the ECM with the exact throttle pedal position. As the pedal operates the voltage of one
position sensor increases as the other decreases.
Input/Output
The ECM provides the throttle position sensor with a 5 volt reference feed. Both position sensors send an analogue
signal back to the ECM.
lSensor one, 0 to 5 volts variable.
lSensor two, 5 to 0 volts variable.
Input to the throttle pedal position sensor is via pin 14 of the ECM connector C0658. Output from sensor one is
measured via pin 12 of the ECM connector C0658. Output from sensor two is measured via pin 36 of the ECM
connector C0658. The earth path is via pin 26 of ECM connector C0658.
The TP sensor can fail the following ways or supply incorrect signal:
lSensor open circuit.
lShort circuit to vehicle supply.
lShort circuit to vehicle earth.
lWater ingress.
lSensor incorrectly fitted.
In the event of a TP sensor signal failure any of the following symptoms may be observed:
lEngine performance concern.
lDelayed throttle response.
lFailure of emission control.
If the TP sensor fails, the engine will only run at idle and the MIL will remain on until the fault is eliminated. Turning
the ignition off/on can reset the MIL provided that the fault has been rectified.
Page 412 of 1672
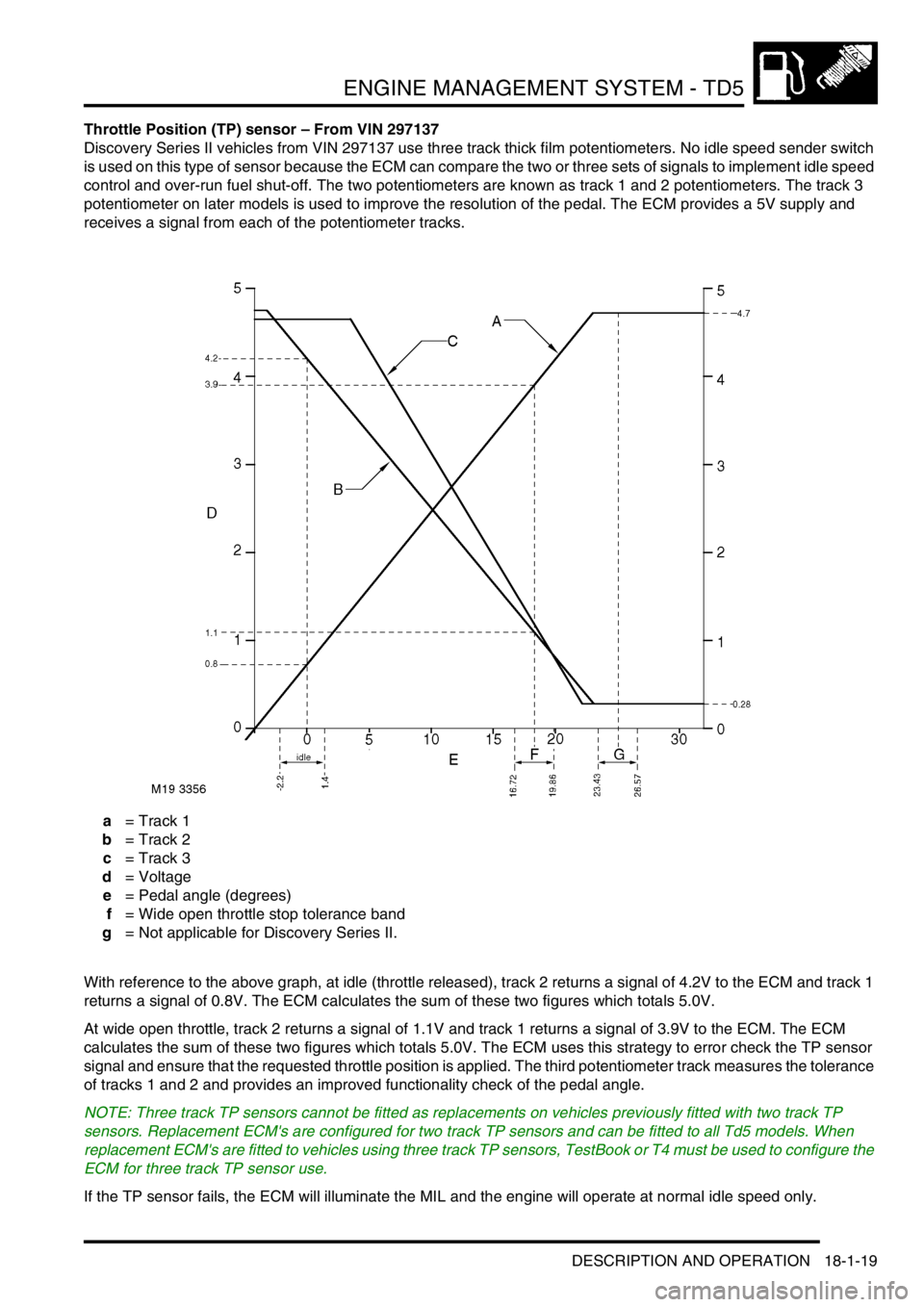
ENGINE MANAGEMENT SYSTEM - TD5
DESCRIPTION AND OPERATION 18-1-19
Throttle Position (TP) sensor – From VIN 297137
Discovery Series II vehicles from VIN 297137 use three track thick film potentiometers. No idle speed sender switch
is used on this type of sensor because the ECM can compare the two or three sets of signals to implement idle speed
control and over-run fuel shut-off. The two potentiometers are known as track 1 and 2 potentiometers. The track 3
potentiometer on later models is used to improve the resolution of the pedal. The ECM provides a 5V supply and
receives a signal from each of the potentiometer tracks.
a = Track 1
b = Track 2
c = Track 3
d = Voltage
e = Pedal angle (degrees)
f = Wide open throttle stop tolerance band
g = Not applicable for Discovery Series II.
With reference to the above graph, at idle (throttle released), track 2 returns a signal of 4.2V to the ECM and track 1
returns a signal of 0.8V. The ECM calculates the sum of these two figures which totals 5.0V.
At wide open throttle, track 2 returns a signal of 1.1V and track 1 returns a signal of 3.9V to the ECM. The ECM
calculates the sum of these two figures which totals 5.0V. The ECM uses this strategy to error check the TP sensor
signal and ensure that the requested throttle position is applied. The third potentiometer track measures the tolerance
of tracks 1 and 2 and provides an improved functionality check of the pedal angle.
NOTE: Three track TP sensors cannot be fitted as replacements on vehicles previously fitted with two track TP
sensors. Replacement ECM's are configured for two track TP sensors and can be fitted to all Td5 models. When
replacement ECM's are fitted to vehicles using three track TP sensors, TestBook or T4 must be used to configure the
ECM for three track TP sensor use.
If the TP sensor fails, the ECM will illuminate the MIL and the engine will operate at normal idle speed only.
Page 413 of 1672
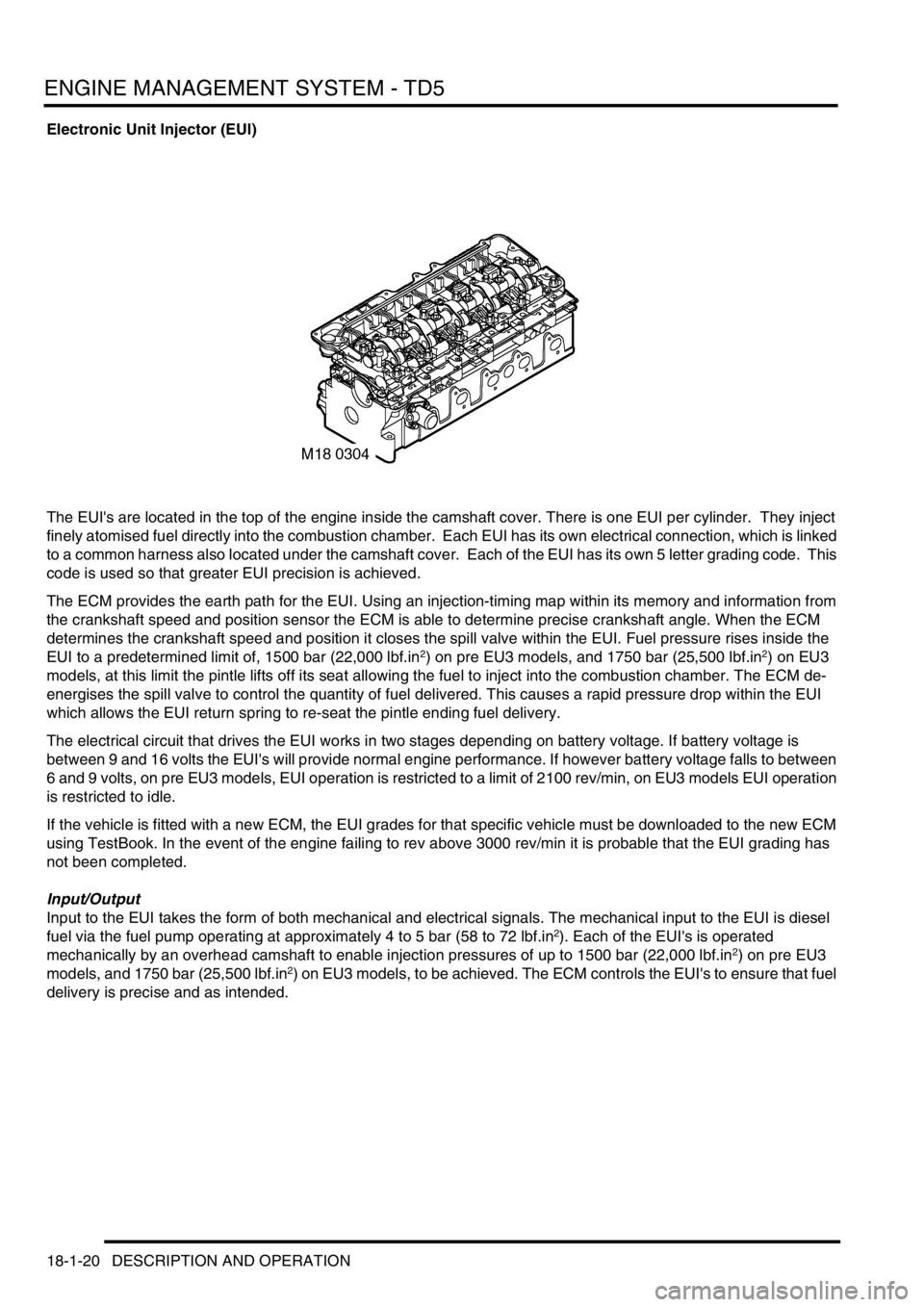
ENGINE MANAGEMENT SYSTEM - TD5
18-1-20 DESCRIPTION AND OPERATION
Electronic Unit Injector (EUI)
The EUI's are located in the top of the engine inside the camshaft cover. There is one EUI per cylinder. They inject
finely atomised fuel directly into the combustion chamber. Each EUI has its own electrical connection, which is linked
to a common harness also located under the camshaft cover. Each of the EUI has its own 5 letter grading code. This
code is used so that greater EUI precision is achieved.
The ECM provides the earth path for the EUI. Using an injection-timing map within its memory and information from
the crankshaft speed and position sensor the ECM is able to determine precise crankshaft angle. When the ECM
determines the crankshaft speed and position it closes the spill valve within the EUI. Fuel pressure rises inside the
EUI to a predetermined limit of, 1500 bar (22,000 lbf.in
2) on pre EU3 models, and 1750 bar (25,500 lbf.in2) on EU3
models, at this limit the pintle lifts off its seat allowing the fuel to inject into the combustion chamber. The ECM de-
energises the spill valve to control the quantity of fuel delivered. This causes a rapid pressure drop within the EUI
which allows the EUI return spring to re-seat the pintle ending fuel delivery.
The electrical circuit that drives the EUI works in two stages depending on battery voltage. If battery voltage is
between 9 and 16 volts the EUI's will provide normal engine performance. If however battery voltage falls to between
6 and 9 volts, on pre EU3 models, EUI operation is restricted to a limit of 2100 rev/min, on EU3 models EUI operation
is restricted to idle.
If the vehicle is fitted with a new ECM, the EUI grades for that specific vehicle must be downloaded to the new ECM
using TestBook. In the event of the engine failing to rev above 3000 rev/min it is probable that the EUI grading has
not been completed.
Input/Output
Input to the EUI takes the form of both mechanical and electrical signals. The mechanical input to the EUI is diesel
fuel via the fuel pump operating at approximately 4 to 5 bar (58 to 72 lbf.in
2). Each of the EUI's is operated
mechanically by an overhead camshaft to enable injection pressures of up to 1500 bar (22,000 lbf.in2) on pre EU3
models, and 1750 bar (25,500 lbf.in2) on EU3 models, to be achieved. The ECM controls the EUI's to ensure that fuel
delivery is precise and as intended.
Page 426 of 1672
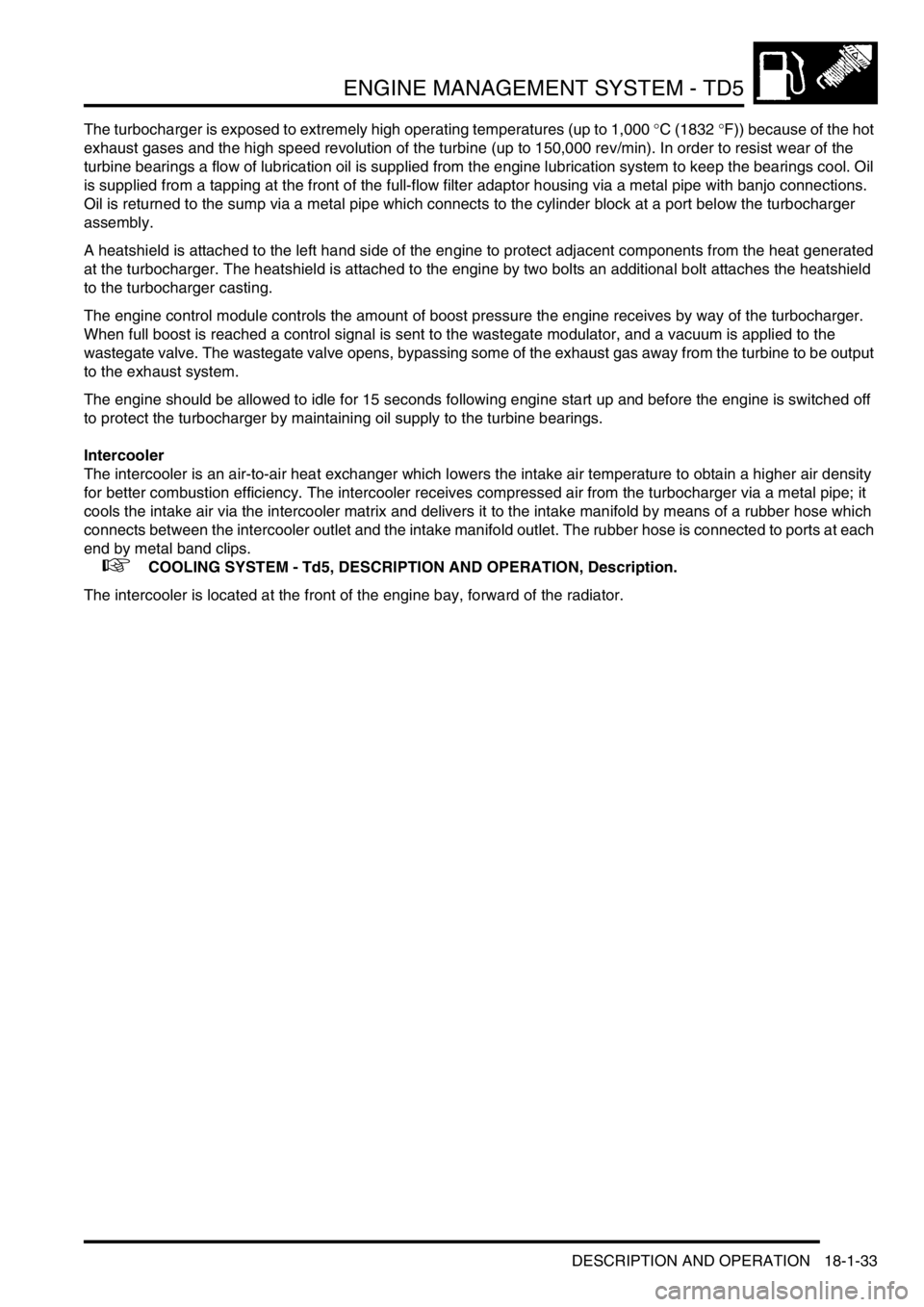
ENGINE MANAGEMENT SYSTEM - TD5
DESCRIPTION AND OPERATION 18-1-33
The turbocharger is exposed to extremely high operating temperatures (up to 1,000 °C (1832 °F)) because of the hot
exhaust gases and the high speed revolution of the turbine (up to 150,000 rev/min). In order to resist wear of the
turbine bearings a flow of lubrication oil is supplied from the engine lubrication system to keep the bearings cool. Oil
is supplied from a tapping at the front of the full-flow filter adaptor housing via a metal pipe with banjo connections.
Oil is returned to the sump via a metal pipe which connects to the cylinder block at a port below the turbocharger
assembly.
A heatshield is attached to the left hand side of the engine to protect adjacent components from the heat generated
at the turbocharger. The heatshield is attached to the engine by two bolts an additional bolt attaches the heatshield
to the turbocharger casting.
The engine control module controls the amount of boost pressure the engine receives by way of the turbocharger.
When full boost is reached a control signal is sent to the wastegate modulator, and a vacuum is applied to the
wastegate valve. The wastegate valve opens, bypassing some of the exhaust gas away from the turbine to be output
to the exhaust system.
The engine should be allowed to idle for 15 seconds following engine start up and before the engine is switched off
to protect the turbocharger by maintaining oil supply to the turbine bearings.
Intercooler
The intercooler is an air-to-air heat exchanger which lowers the intake air temperature to obtain a higher air density
for better combustion efficiency. The intercooler receives compressed air from the turbocharger via a metal pipe; it
cools the intake air via the intercooler matrix and delivers it to the intake manifold by means of a rubber hose which
connects between the intercooler outlet and the intake manifold outlet. The rubber hose is connected to ports at each
end by metal band clips.
+ COOLING SYSTEM - Td5, DESCRIPTION AND OPERATION, Description.
The intercooler is located at the front of the engine bay, forward of the radiator.