check engine LAND ROVER DISCOVERY 2002 Workshop Manual
[x] Cancel search | Manufacturer: LAND ROVER, Model Year: 2002, Model line: DISCOVERY, Model: LAND ROVER DISCOVERY 2002Pages: 1672, PDF Size: 46.1 MB
Page 7 of 1672
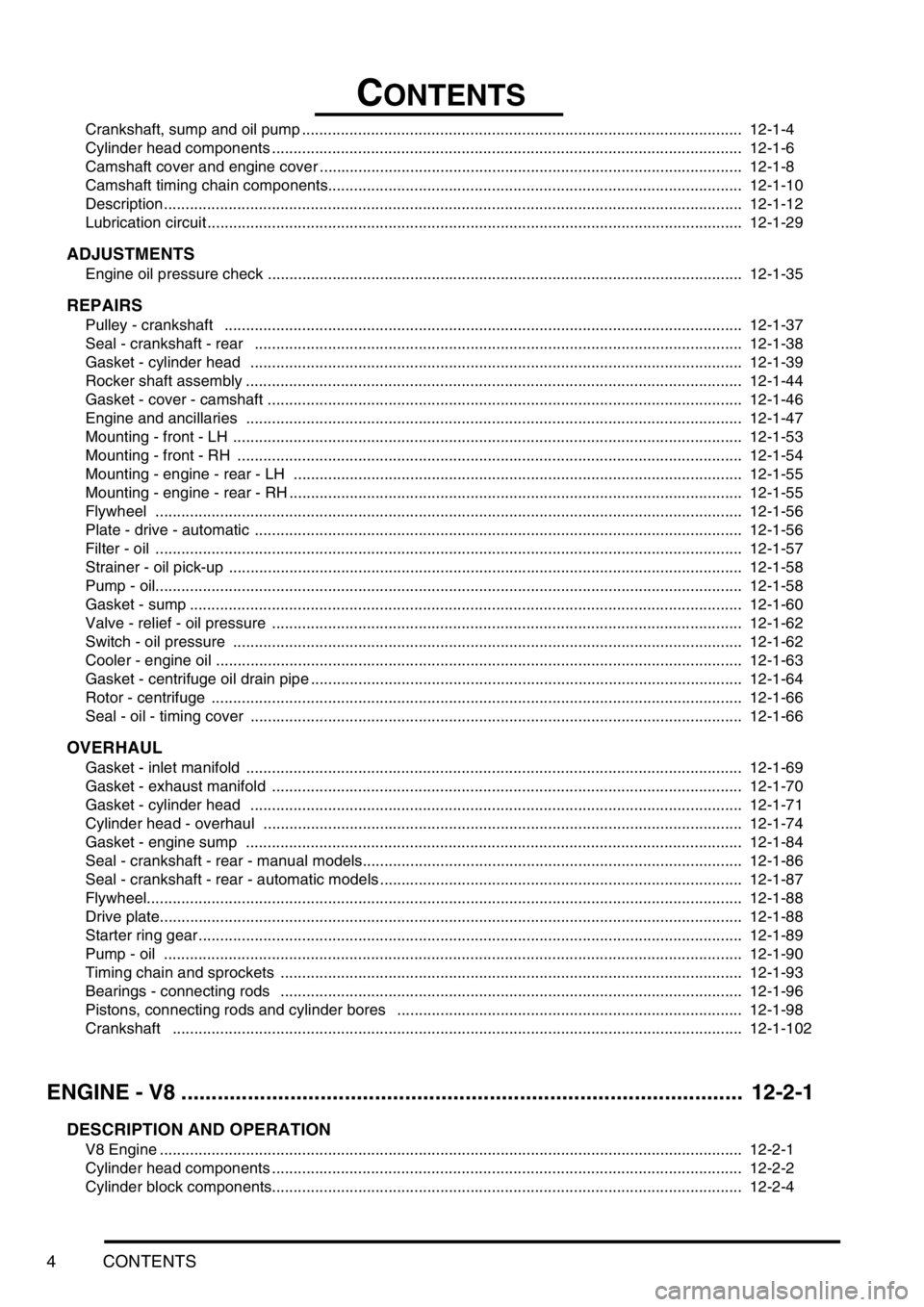
CONTENTS
4CONTENTS
Crankshaft, sump and oil pump ...................................................................................................... 12-1-4
Cylinder head components ............................................................................................................. 12-1-6
Camshaft cover and engine cover .................................................................................................. 12-1-8
Camshaft timing chain components................................................................................................ 12-1-10
Description ...................................................................................................................................... 12-1-12
Lubrication circuit ............................................................................................................................ 12-1-29
ADJUSTMENTS
Engine oil pressure check .............................................................................................................. 12-1-35
REPAIRS
Pulley - crankshaft ........................................................................................................................ 12-1-37
Seal - crankshaft - rear ................................................................................................................. 12-1-38
Gasket - cylinder head .................................................................................................................. 12-1-39
Rocker shaft assembly ................................................................................................................... 12-1-44
Gasket - cover - camshaft .............................................................................................................. 12-1-46
Engine and ancillaries ................................................................................................................... 12-1-47
Mounting - front - LH ...................................................................................................................... 12-1-53
Mounting - front - RH ..................................................................................................................... 12-1-54
Mounting - engine - rear - LH ........................................................................................................ 12-1-55
Mounting - engine - rear - RH ......................................................................................................... 12-1-55
Flywheel ........................................................................................................................................ 12-1-56
Plate - drive - automatic ................................................................................................................. 12-1-56
Filter - oil ........................................................................................................................................ 12-1-57
Strainer - oil pick-up ....................................................................................................................... 12-1-58
Pump - oil........................................................................................................................................ 12-1-58
Gasket - sump ................................................................................................................................ 12-1-60
Valve - relief - oil pressure ............................................................................................................. 12-1-62
Switch - oil pressure ...................................................................................................................... 12-1-62
Cooler - engine oil .......................................................................................................................... 12-1-63
Gasket - centrifuge oil drain pipe .................................................................................................... 12-1-64
Rotor - centrifuge ........................................................................................................................... 12-1-66
Seal - oil - timing cover .................................................................................................................. 12-1-66
OVERHAUL
Gasket - inlet manifold ................................................................................................................... 12-1-69
Gasket - exhaust manifold ............................................................................................................. 12-1-70
Gasket - cylinder head .................................................................................................................. 12-1-71
Cylinder head - overhaul ............................................................................................................... 12-1-74
Gasket - engine sump ................................................................................................................... 12-1-84
Seal - crankshaft - rear - manual models........................................................................................ 12-1-86
Seal - crankshaft - rear - automatic models .................................................................................... 12-1-87
Flywheel.......................................................................................................................................... 12-1-88
Drive plate....................................................................................................................................... 12-1-88
Starter ring gear .............................................................................................................................. 12-1-89
Pump - oil ...................................................................................................................................... 12-1-90
Timing chain and sprockets ........................................................................................................... 12-1-93
Bearings - connecting rods ........................................................................................................... 12-1-96
Pistons, connecting rods and cylinder bores ................................................................................ 12-1-98
Crankshaft .................................................................................................................................... 12-1-102
ENGINE - V8 ............................................................................................. 12-2-1
DESCRIPTION AND OPERATION
V8 Engine ....................................................................................................................................... 12-2-1
Cylinder head components ............................................................................................................. 12-2-2
Cylinder block components............................................................................................................. 12-2-4
Page 8 of 1672
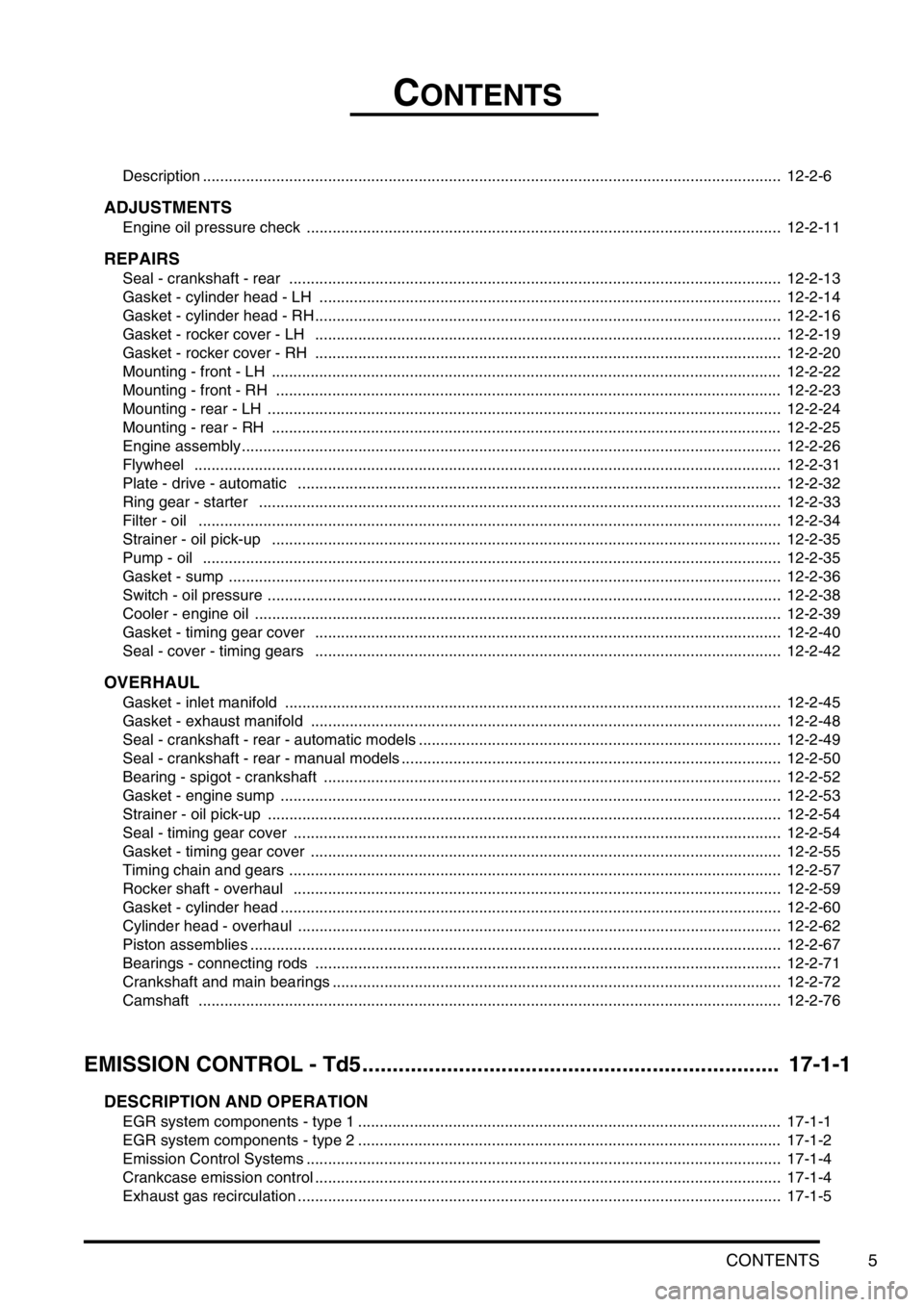
CONTENTS
CONTENTS 5
Description ...................................................................................................................................... 12-2-6
ADJUSTMENTS
Engine oil pressure check .............................................................................................................. 12-2-11
REPAIRS
Seal - crankshaft - rear .................................................................................................................. 12-2-13
Gasket - cylinder head - LH ........................................................................................................... 12-2-14
Gasket - cylinder head - RH ............................................................................................................ 12-2-16
Gasket - rocker cover - LH ............................................................................................................ 12-2-19
Gasket - rocker cover - RH ............................................................................................................ 12-2-20
Mounting - front - LH ...................................................................................................................... 12-2-22
Mounting - front - RH ..................................................................................................................... 12-2-23
Mounting - rear - LH ....................................................................................................................... 12-2-24
Mounting - rear - RH ...................................................................................................................... 12-2-25
Engine assembly............................................................................................................................. 12-2-26
Flywheel ........................................................................................................................................ 12-2-31
Plate - drive - automatic ................................................................................................................ 12-2-32
Ring gear - starter ......................................................................................................................... 12-2-33
Filter - oil ....................................................................................................................................... 12-2-34
Strainer - oil pick-up ...................................................................................................................... 12-2-35
Pump - oil ...................................................................................................................................... 12-2-35
Gasket - sump ................................................................................................................................ 12-2-36
Switch - oil pressure ....................................................................................................................... 12-2-38
Cooler - engine oil .......................................................................................................................... 12-2-39
Gasket - timing gear cover ............................................................................................................ 12-2-40
Seal - cover - timing gears ............................................................................................................ 12-2-42
OVERHAUL
Gasket - inlet manifold ................................................................................................................... 12-2-45
Gasket - exhaust manifold ............................................................................................................. 12-2-48
Seal - crankshaft - rear - automatic models .................................................................................... 12-2-49
Seal - crankshaft - rear - manual models ........................................................................................ 12-2-50
Bearing - spigot - crankshaft .......................................................................................................... 12-2-52
Gasket - engine sump .................................................................................................................... 12-2-53
Strainer - oil pick-up ....................................................................................................................... 12-2-54
Seal - timing gear cover ................................................................................................................. 12-2-54
Gasket - timing gear cover ............................................................................................................. 12-2-55
Timing chain and gears .................................................................................................................. 12-2-57
Rocker shaft - overhaul ................................................................................................................. 12-2-59
Gasket - cylinder head .................................................................................................................... 12-2-60
Cylinder head - overhaul ................................................................................................................ 12-2-62
Piston assemblies ........................................................................................................................... 12-2-67
Bearings - connecting rods ............................................................................................................ 12-2-71
Crankshaft and main bearings ........................................................................................................ 12-2-72
Camshaft ....................................................................................................................................... 12-2-76
EMISSION CONTROL - Td5..................................................................... 17-1-1
DESCRIPTION AND OPERATION
EGR system components - type 1 .................................................................................................. 17-1-1
EGR system components - type 2 .................................................................................................. 17-1-2
Emission Control Systems .............................................................................................................. 17-1-4
Crankcase emission control ............................................................................................................ 17-1-4
Exhaust gas recirculation ................................................................................................................ 17-1-5
Page 38 of 1672

GENERAL INFORMATION
03-3
Environmental Precautions
General
This section provides general information which can
help to reduce the environmental impacts from the
activities carried out in workshops.
Emissions to air
Many of the activities that are carried out in
workshops emit gases and fumes which contribute to
global warming, depletion of the ozone layer and/or
the formation of photochemical smog at ground
level. By considering how the workshop activities are
carried out, these gases and fumes can be
minimised, thus reducing the impact on the
environment.
Exhaust fumes
Running car engines is an essential part of workshop
activities and exhaust fumes need to be ventilated to
atmosphere. However, the amount of time engines
are running and the position of the vehicle should be
carefully considered at all times, to reduce the
release of poisonous gases and minimise the
inconvenience to people living nearby.
Solvents
Some of the cleaning agents used are solvent based
and will evaporate to atmosphere if used carelessly,
or if cans are left unsealed. All solvent containers
should be firmly closed when not needed and
solvent should be used sparingly. Suitable
alternative materials may be available to replace
some of the commonly used solvents. Similarly,
many paints are solvent based and the spray should
be minimised to reduce solvent emissions.
Refrigerant
It is illegal to release any refrigerants into the
atmosphere. Discharge and replacement of these
materials from air conditioning units should only be
carried out using the correct equipment.
Checklist
Always adhere to the following.
Engines:
ldon't leave engines running unnecessarily;
lminimise testing times and check where the
exhaust fumes are being blown.
Materials:
lkeep lids on containers of solvents;
lonly use the minimum quantity;
lconsider alternative materials;
lminimise over-spray when painting. Gases:
luse the correct equipment for collecting
refrigerants;
ldon't burn rubbish on site.
Discharges to water
Most sites will have two systems for discharging
water: storm drains and foul drains. Storm drains
should only receive clean water, foul drains will take
dirty water.
The foul drain will accept many of the normal waste
waters such as washing water, detergents and
domestic type wastes, but oil, petrol, solvent, acids,
hydraulic oil, antifreeze and other such substances
should never be poured down the drain. If in any
doubt speak to the Water Company first.
Every precaution must be taken to prevent spillage of
oil, fuel, solvents etc. reaching the drains. All
handling of such materials must take place well away
from the drains and preferably in an area with a kerb
or wall around it, to prevent discharge into the drain.
If a spillage occurs it should be soaked up
immediately. Having a spill kit available will make
this easier.
Additional precautions
Check whether the surface water drains are
connected to an oil water separator, this could
reduce the pollution if an incident was to occur. Oil
water separators do need regular maintenance to
ensure effectiveness.
Checklist
Always adhere to the following.
Disposal:
lnever pour anything down a drain without first
checking that it is environmentally safe to do so,
and that it does not contravene any local
regulations or bye-laws;
l have oil traps emptied regularly.
Spillage prevention:
lstore liquids in a walled area;
lmake sure that taps on liquid containers are
secure and cannot be accidentally turned on;
lprotect bulk storage tanks from vandalism by
locking the valves;
ltransfer liquids from one container to another in
an area away from open drains;
lensure lids are replaced securely on containers;
lhave spill kits available near to points of storage
and handling of liquids.
Page 39 of 1672
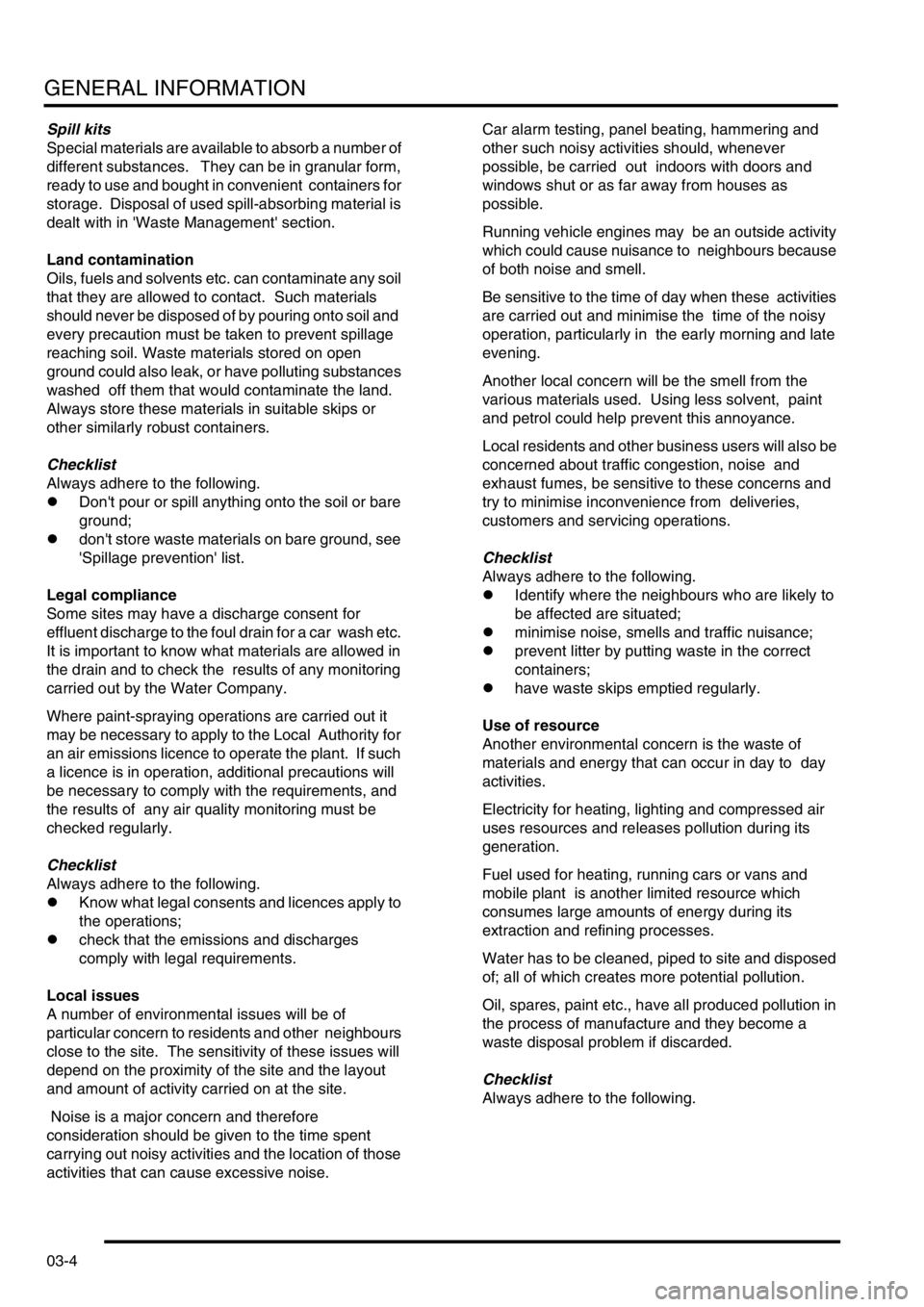
GENERAL INFORMATION
03-4
Spill kits
Special materials are available to absorb a number of
different substances. They can be in granular form,
ready to use and bought in convenient containers for
storage. Disposal of used spill-absorbing material is
dealt with in 'Waste Management' section.
Land contamination
Oils, fuels and solvents etc. can contaminate any soil
that they are allowed to contact. Such materials
should never be disposed of by pouring onto soil and
every precaution must be taken to prevent spillage
reaching soil. Waste materials stored on open
ground could also leak, or have polluting substances
washed off them that would contaminate the land.
Always store these materials in suitable skips or
other similarly robust containers.
Checklist
Always adhere to the following.
lDon't pour or spill anything onto the soil or bare
ground;
ldon't store waste materials on bare ground, see
'Spillage prevention' list.
Legal compliance
Some sites may have a discharge consent for
effluent discharge to the foul drain for a car wash etc.
It is important to know what materials are allowed in
the drain and to check the results of any monitoring
carried out by the Water Company.
Where paint-spraying operations are carried out it
may be necessary to apply to the Local Authority for
an air emissions licence to operate the plant. If such
a licence is in operation, additional precautions will
be necessary to comply with the requirements, and
the results of any air quality monitoring must be
checked regularly.
Checklist
Always adhere to the following.
lKnow what legal consents and licences apply to
the operations;
lcheck that the emissions and discharges
comply with legal requirements.
Local issues
A number of environmental issues will be of
particular concern to residents and other neighbours
close to the site. The sensitivity of these issues will
depend on the proximity of the site and the layout
and amount of activity carried on at the site.
Noise is a major concern and therefore
consideration should be given to the time spent
carrying out noisy activities and the location of those
activities that can cause excessive noise. Car alarm testing, panel beating, hammering and
other such noisy activities should, whenever
possible, be carried out indoors with doors and
windows shut or as far away from houses as
possible.
Running vehicle engines may be an outside activity
which could cause nuisance to neighbours because
of both noise and smell.
Be sensitive to the time of day when these activities
are carried out and minimise the time of the noisy
operation, particularly in the early morning and late
evening.
Another local concern will be the smell from the
various materials used. Using less solvent, paint
and petrol could help prevent this annoyance.
Local residents and other business users will also be
concerned about traffic congestion, noise and
exhaust fumes, be sensitive to these concerns and
try to minimise inconvenience from deliveries,
customers and servicing operations.
Checklist
Always adhere to the following.
lIdentify where the neighbours who are likely to
be affected are situated;
lminimise noise, smells and traffic nuisance;
lprevent litter by putting waste in the correct
containers;
lhave waste skips emptied regularly.
Use of resource
Another environmental concern is the waste of
materials and energy that can occur in day to day
activities.
Electricity for heating, lighting and compressed air
uses resources and releases pollution during its
generation.
Fuel used for heating, running cars or vans and
mobile plant is another limited resource which
consumes large amounts of energy during its
extraction and refining processes.
Water has to be cleaned, piped to site and disposed
of; all of which creates more potential pollution.
Oil, spares, paint etc., have all produced pollution in
the process of manufacture and they become a
waste disposal problem if discarded.
Checklist
Always adhere to the following.
Page 40 of 1672
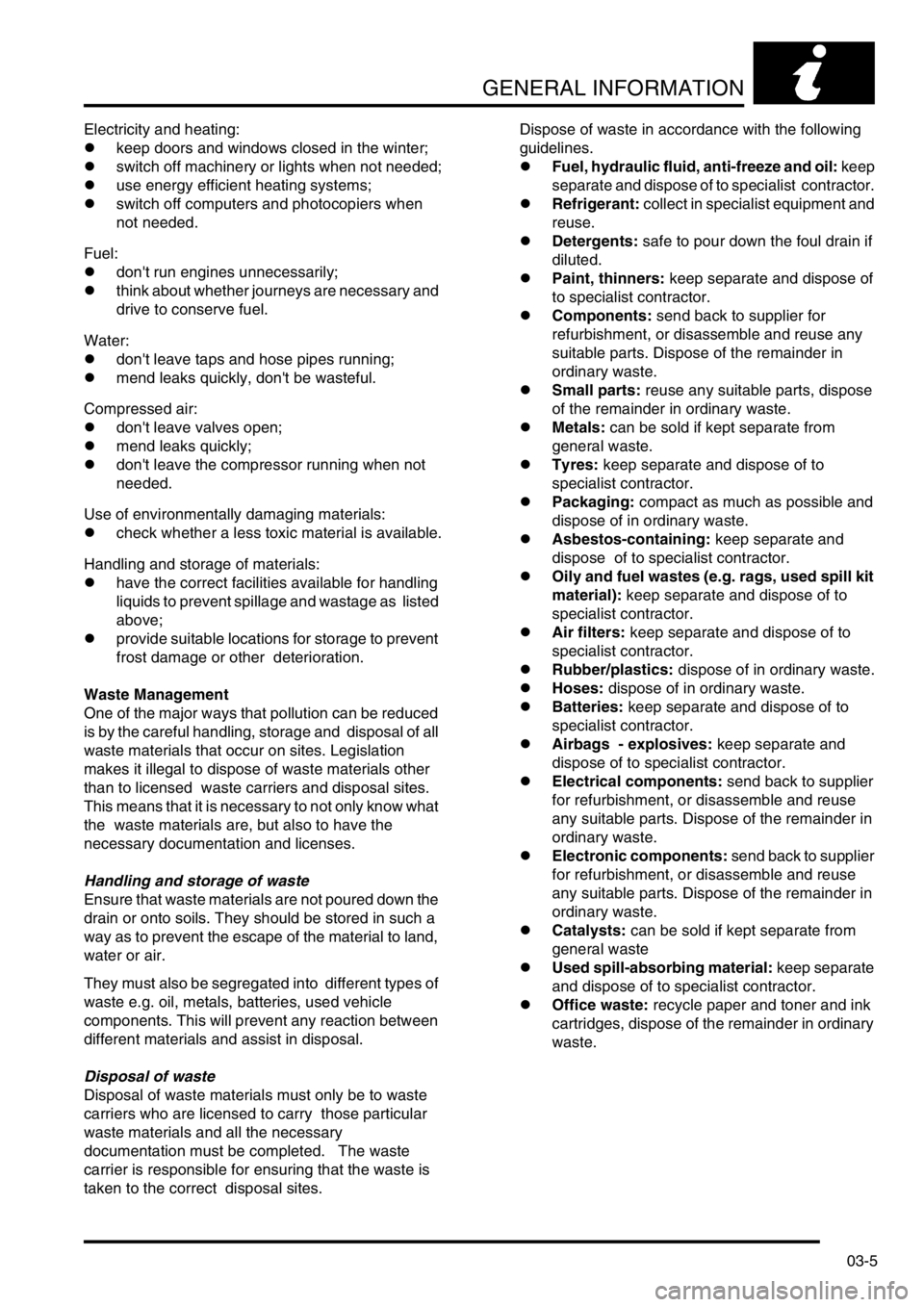
GENERAL INFORMATION
03-5
Electricity and heating:
lkeep doors and windows closed in the winter;
lswitch off machinery or lights when not needed;
luse energy efficient heating systems;
lswitch off computers and photocopiers when
not needed.
Fuel:
ldon't run engines unnecessarily;
lthink about whether journeys are necessary and
drive to conserve fuel.
Water:
ldon't leave taps and hose pipes running;
lmend leaks quickly, don't be wasteful.
Compressed air:
ldon't leave valves open;
lmend leaks quickly;
ldon't leave the compressor running when not
needed.
Use of environmentally damaging materials:
lcheck whether a less toxic material is available.
Handling and storage of materials:
lhave the correct facilities available for handling
liquids to prevent spillage and wastage as listed
above;
lprovide suitable locations for storage to prevent
frost damage or other deterioration.
Waste Management
One of the major ways that pollution can be reduced
is by the careful handling, storage and disposal of all
waste materials that occur on sites. Legislation
makes it illegal to dispose of waste materials other
than to licensed waste carriers and disposal sites.
This means that it is necessary to not only know what
the waste materials are, but also to have the
necessary documentation and licenses.
Handling and storage of waste
Ensure that waste materials are not poured down the
drain or onto soils. They should be stored in such a
way as to prevent the escape of the material to land,
water or air.
They must also be segregated into different types of
waste e.g. oil, metals, batteries, used vehicle
components. This will prevent any reaction between
different materials and assist in disposal.
Disposal of waste
Disposal of waste materials must only be to waste
carriers who are licensed to carry those particular
waste materials and all the necessary
documentation must be completed. The waste
carrier is responsible for ensuring that the waste is
taken to the correct disposal sites.Dispose of waste in accordance with the following
guidelines.
lFuel, hydraulic fluid, anti-freeze and oil: keep
separate and dispose of to specialist contractor.
lRefrigerant: collect in specialist equipment and
reuse.
lDetergents: safe to pour down the foul drain if
diluted.
lPaint, thinners: keep separate and dispose of
to specialist contractor.
lComponents: send back to supplier for
refurbishment, or disassemble and reuse any
suitable parts. Dispose of the remainder in
ordinary waste.
lSmall parts: reuse any suitable parts, dispose
of the remainder in ordinary waste.
lMetals: can be sold if kept separate from
general waste.
lTyres: keep separate and dispose of to
specialist contractor.
lPackaging: compact as much as possible and
dispose of in ordinary waste.
lAsbestos-containing: keep separate and
dispose of to specialist contractor.
lOily and fuel wastes (e.g. rags, used spill kit
material): keep separate and dispose of to
specialist contractor.
lAir filters: keep separate and dispose of to
specialist contractor.
lRubber/plastics: dispose of in ordinary waste.
lHoses: dispose of in ordinary waste.
lBatteries: keep separate and dispose of to
specialist contractor.
lAirbags - explosives: keep separate and
dispose of to specialist contractor.
lElectrical components: send back to supplier
for refurbishment, or disassemble and reuse
any suitable parts. Dispose of the remainder in
ordinary waste.
lElectronic components: send back to supplier
for refurbishment, or disassemble and reuse
any suitable parts. Dispose of the remainder in
ordinary waste.
lCatalysts: can be sold if kept separate from
general waste
lUsed spill-absorbing material: keep separate
and dispose of to specialist contractor.
lOffice waste: recycle paper and toner and ink
cartridges, dispose of the remainder in ordinary
waste.
Page 50 of 1672
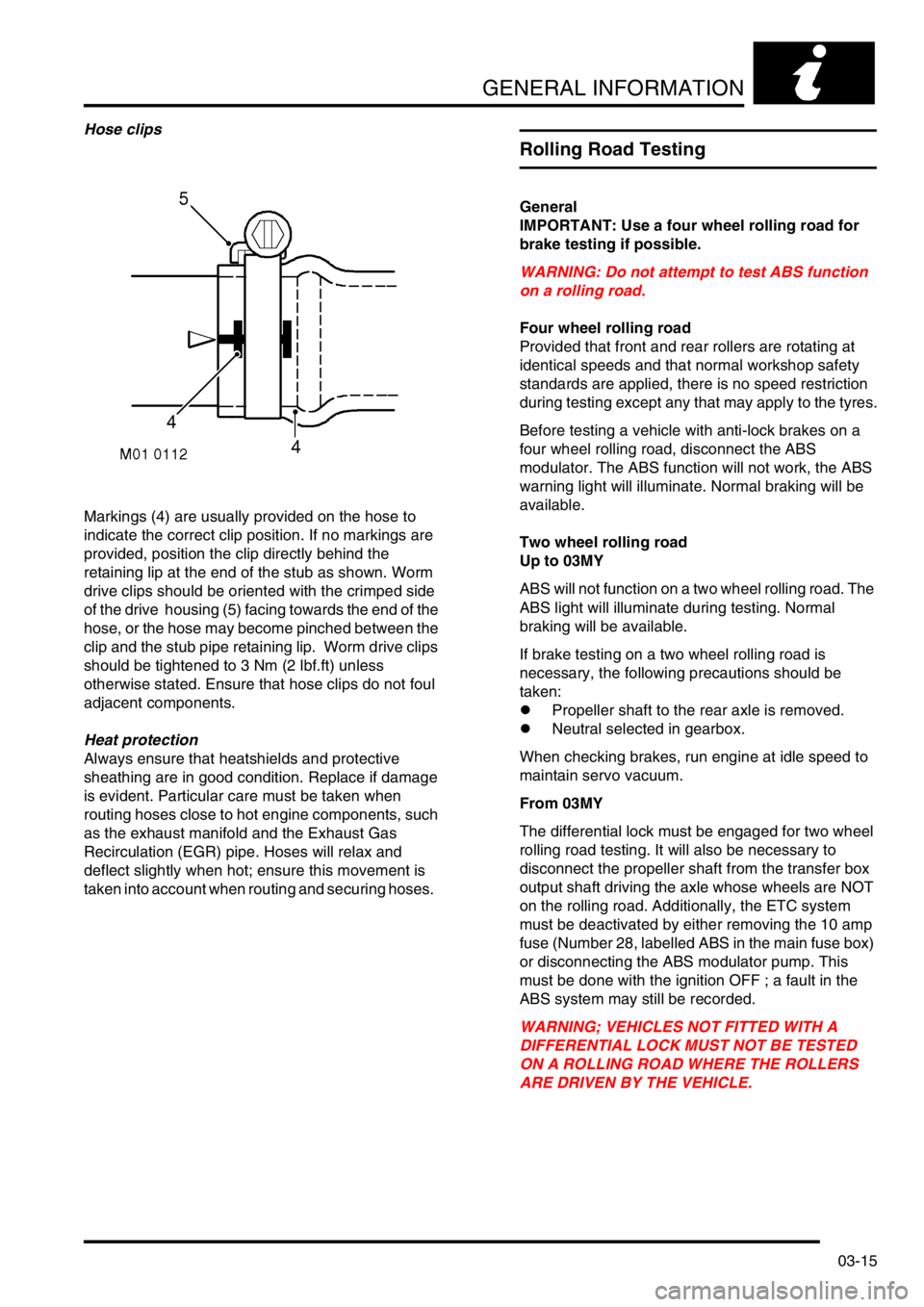
GENERAL INFORMATION
03-15
Hose clips
Markings (4) are usually provided on the hose to
indicate the correct clip position. If no markings are
provided, position the clip directly behind the
retaining lip at the end of the stub as shown. Worm
drive clips should be oriented with the crimped side
of the drive housing (5) facing towards the end of the
hose, or the hose may become pinched between the
clip and the stub pipe retaining lip. Worm drive clips
should be tightened to 3 Nm (2 lbf.ft) unless
otherwise stated. Ensure that hose clips do not foul
adjacent components.
Heat protection
Always ensure that heatshields and protective
sheathing are in good condition. Replace if damage
is evident. Particular care must be taken when
routing hoses close to hot engine components, such
as the exhaust manifold and the Exhaust Gas
Recirculation (EGR) pipe. Hoses will relax and
deflect slightly when hot; ensure this movement is
taken into account when routing and securing hoses.
Rolling Road Testing
General
IMPORTANT: Use a four wheel rolling road for
brake testing if possible.
WARNING: Do not attempt to test ABS function
on a rolling road.
Four wheel rolling road
Provided that front and rear rollers are rotating at
identical speeds and that normal workshop safety
standards are applied, there is no speed restriction
during testing except any that may apply to the tyres.
Before testing a vehicle with anti-lock brakes on a
four wheel rolling road, disconnect the ABS
modulator. The ABS function will not work, the ABS
warning light will illuminate. Normal braking will be
available.
Two wheel rolling road
Up to 03MY
ABS will not function on a two wheel rolling road. The
ABS light will illuminate during testing. Normal
braking will be available.
If brake testing on a two wheel rolling road is
necessary, the following precautions should be
taken:
lPropeller shaft to the rear axle is removed.
lNeutral selected in gearbox.
When checking brakes, run engine at idle speed to
maintain servo vacuum.
From 03MY
The differential lock must be engaged for two wheel
rolling road testing. It will also be necessary to
disconnect the propeller shaft from the transfer box
output shaft driving the axle whose wheels are NOT
on the rolling road. Additionally, the ETC system
must be deactivated by either removing the 10 amp
fuse (Number 28, labelled ABS in the main fuse box)
or disconnecting the ABS modulator pump. This
must be done with the ignition OFF ; a fault in the
ABS system may still be recorded.
WARNING; VEHICLES NOT FITTED WITH A
DIFFERENTIAL LOCK MUST NOT BE TESTED
ON A ROLLING ROAD WHERE THE ROLLERS
ARE DRIVEN BY THE VEHICLE.
Page 52 of 1672
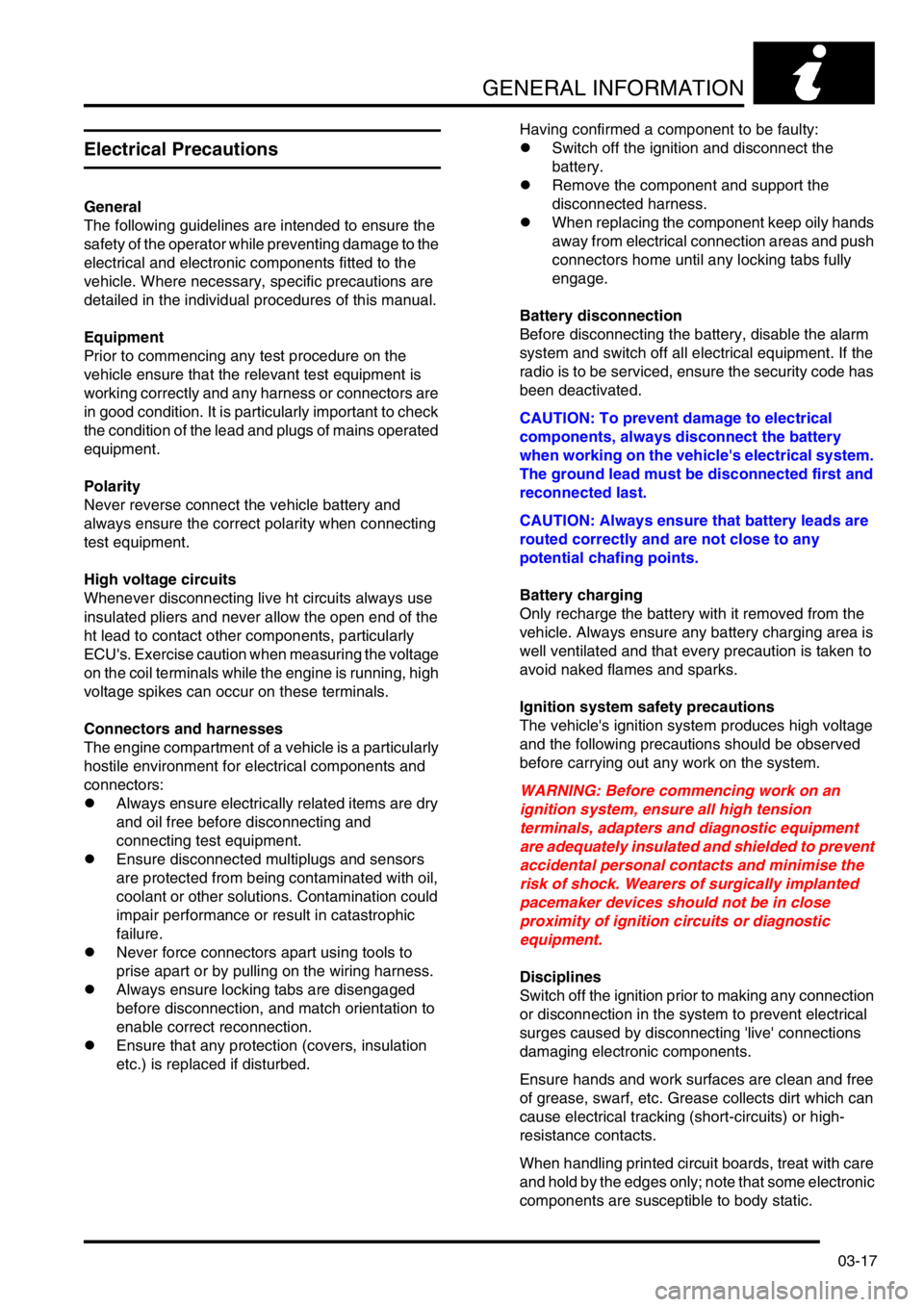
GENERAL INFORMATION
03-17
Electrical Precautions
General
The following guidelines are intended to ensure the
safety of the operator while preventing damage to the
electrical and electronic components fitted to the
vehicle. Where necessary, specific precautions are
detailed in the individual procedures of this manual.
Equipment
Prior to commencing any test procedure on the
vehicle ensure that the relevant test equipment is
working correctly and any harness or connectors are
in good condition. It is particularly important to check
the condition of the lead and plugs of mains operated
equipment.
Polarity
Never reverse connect the vehicle battery and
always ensure the correct polarity when connecting
test equipment.
High voltage circuits
Whenever disconnecting live ht circuits always use
insulated pliers and never allow the open end of the
ht lead to contact other components, particularly
ECU's. Exercise caution when measuring the voltage
on the coil terminals while the engine is running, high
voltage spikes can occur on these terminals.
Connectors and harnesses
The engine compartment of a vehicle is a particularly
hostile environment for electrical components and
connectors:
lAlways ensure electrically related items are dry
and oil free before disconnecting and
connecting test equipment.
lEnsure disconnected multiplugs and sensors
are protected from being contaminated with oil,
coolant or other solutions. Contamination could
impair performance or result in catastrophic
failure.
lNever force connectors apart using tools to
prise apart or by pulling on the wiring harness.
lAlways ensure locking tabs are disengaged
before disconnection, and match orientation to
enable correct reconnection.
lEnsure that any protection (covers, insulation
etc.) is replaced if disturbed.Having confirmed a component to be faulty:
lSwitch off the ignition and disconnect the
battery.
lRemove the component and support the
disconnected harness.
lWhen replacing the component keep oily hands
away from electrical connection areas and push
connectors home until any locking tabs fully
engage.
Battery disconnection
Before disconnecting the battery, disable the alarm
system and switch off all electrical equipment. If the
radio is to be serviced, ensure the security code has
been deactivated.
CAUTION: To prevent damage to electrical
components, always disconnect the battery
when working on the vehicle's electrical system.
The ground lead must be disconnected first and
reconnected last.
CAUTION: Always ensure that battery leads are
routed correctly and are not close to any
potential chafing points.
Battery charging
Only recharge the battery with it removed from the
vehicle. Always ensure any battery charging area is
well ventilated and that every precaution is taken to
avoid naked flames and sparks.
Ignition system safety precautions
The vehicle's ignition system produces high voltage
and the following precautions should be observed
before carrying out any work on the system.
WARNING: Before commencing work on an
ignition system, ensure all high tension
terminals, adapters and diagnostic equipment
are adequately insulated and shielded to prevent
accidental personal contacts and minimise the
risk of shock. Wearers of surgically implanted
pacemaker devices should not be in close
proximity of ignition circuits or diagnostic
equipment.
Disciplines
Switch off the ignition prior to making any connection
or disconnection in the system to prevent electrical
surges caused by disconnecting 'live' connections
damaging electronic components.
Ensure hands and work surfaces are clean and free
of grease, swarf, etc. Grease collects dirt which can
cause electrical tracking (short-circuits) or high-
resistance contacts.
When handling printed circuit boards, treat with care
and hold by the edges only; note that some electronic
components are susceptible to body static.
Page 53 of 1672
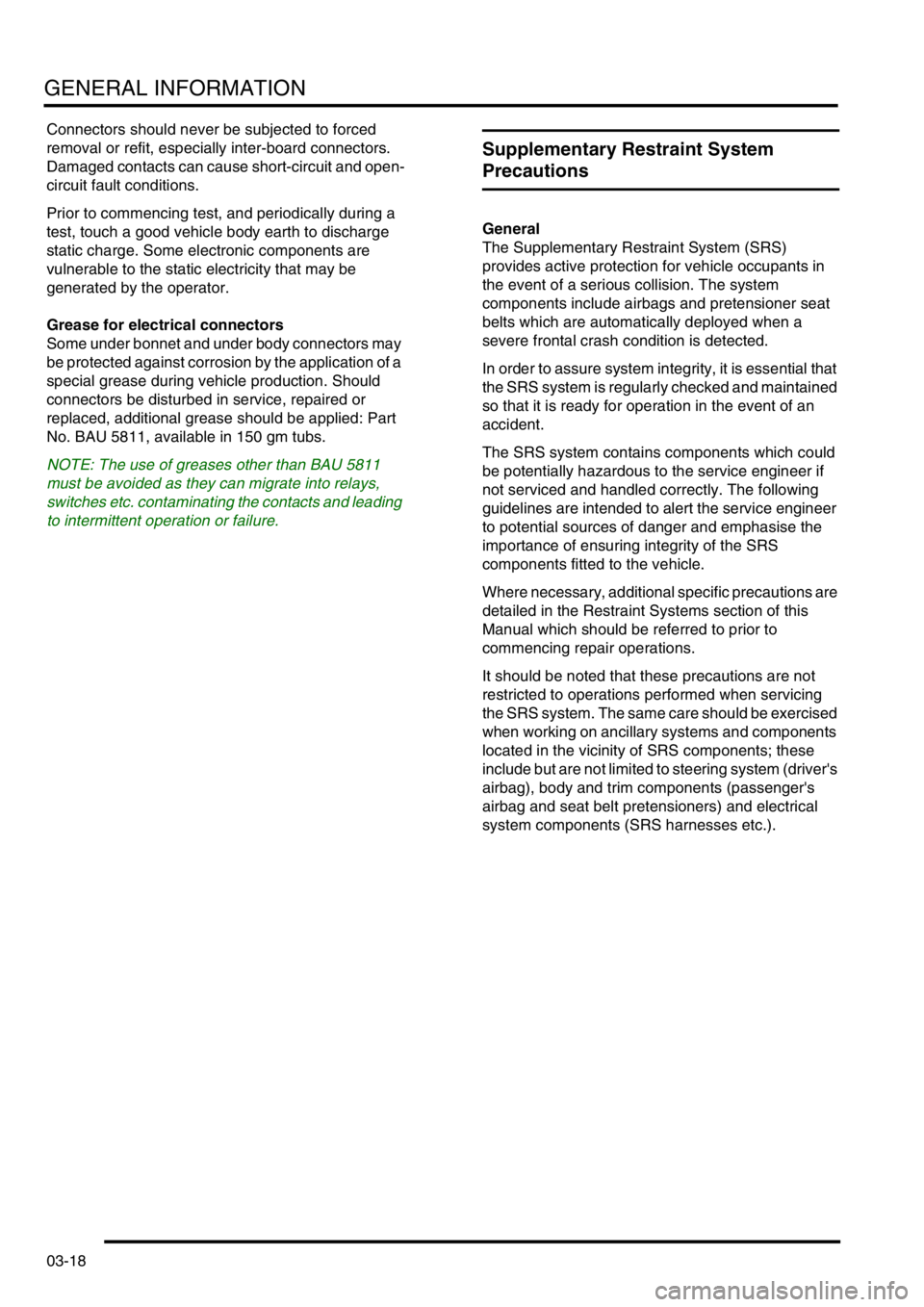
GENERAL INFORMATION
03-18
Connectors should never be subjected to forced
removal or refit, especially inter-board connectors.
Damaged contacts can cause short-circuit and open-
circuit fault conditions.
Prior to commencing test, and periodically during a
test, touch a good vehicle body earth to discharge
static charge. Some electronic components are
vulnerable to the static electricity that may be
generated by the operator.
Grease for electrical connectors
Some under bonnet and under body connectors may
be protected against corrosion by the application of a
special grease during vehicle production. Should
connectors be disturbed in service, repaired or
replaced, additional grease should be applied: Part
No. BAU 5811, available in 150 gm tubs.
NOTE: The use of greases other than BAU 5811
must be avoided as they can migrate into relays,
switches etc. contaminating the contacts and leading
to intermittent operation or failure.
Supplementary Restraint System
Precautions
General
The Supplementary Restraint System (SRS)
provides active protection for vehicle occupants in
the event of a serious collision. The system
components include airbags and pretensioner seat
belts which are automatically deployed when a
severe frontal crash condition is detected.
In order to assure system integrity, it is essential that
the SRS system is regularly checked and maintained
so that it is ready for operation in the event of an
accident.
The SRS system contains components which could
be potentially hazardous to the service engineer if
not serviced and handled correctly. The following
guidelines are intended to alert the service engineer
to potential sources of danger and emphasise the
importance of ensuring integrity of the SRS
components fitted to the vehicle.
Where necessary, additional specific precautions are
detailed in the Restraint Systems section of this
Manual which should be referred to prior to
commencing repair operations.
It should be noted that these precautions are not
restricted to operations performed when servicing
the SRS system. The same care should be exercised
when working on ancillary systems and components
located in the vicinity of SRS components; these
include but are not limited to steering system (driver's
airbag), body and trim components (passenger's
airbag and seat belt pretensioners) and electrical
system components (SRS harnesses etc.).
Page 59 of 1672
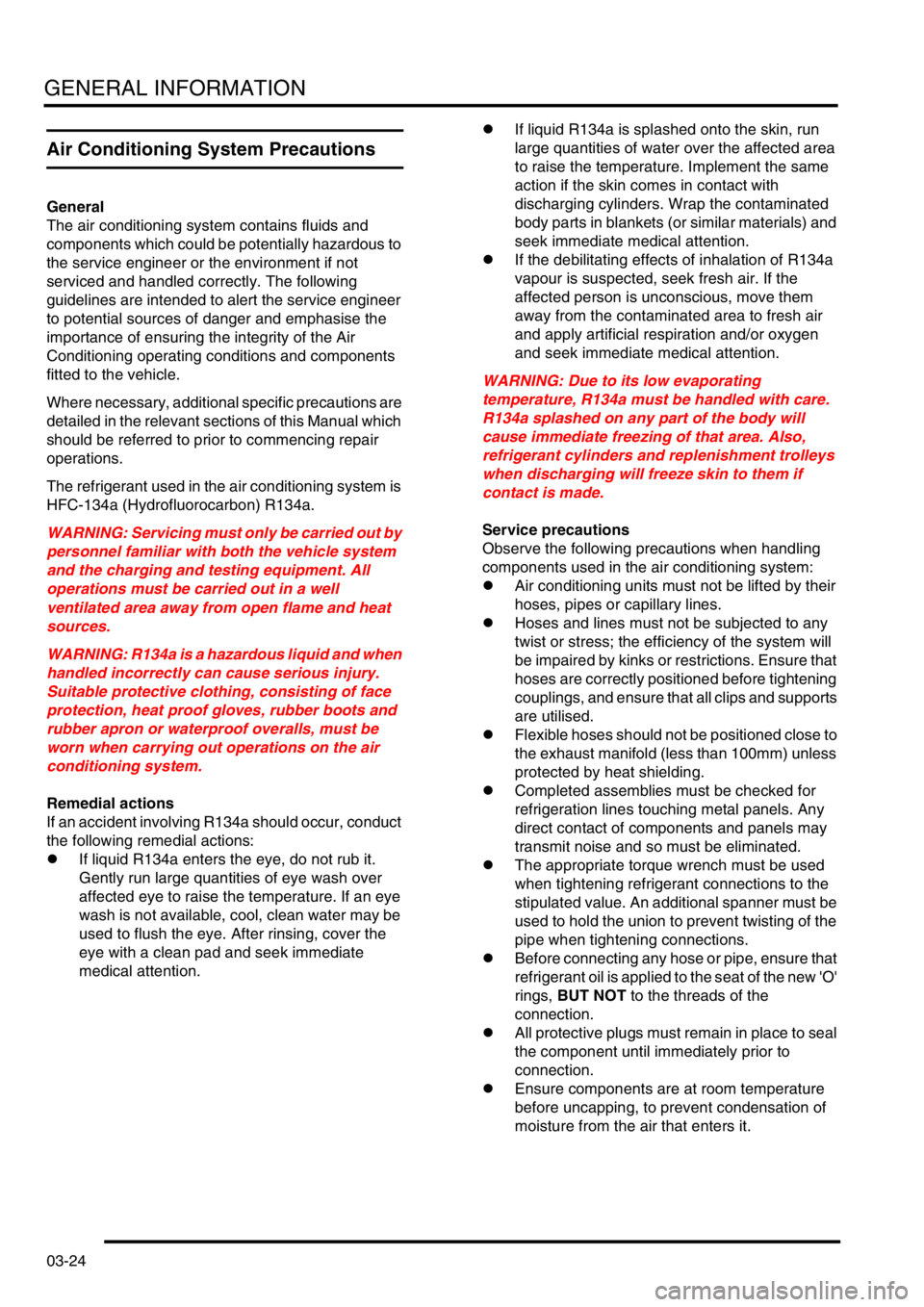
GENERAL INFORMATION
03-24
Air Conditioning System Precautions
General
The air conditioning system contains fluids and
components which could be potentially hazardous to
the service engineer or the environment if not
serviced and handled correctly. The following
guidelines are intended to alert the service engineer
to potential sources of danger and emphasise the
importance of ensuring the integrity of the Air
Conditioning operating conditions and components
fitted to the vehicle.
Where necessary, additional specific precautions are
detailed in the relevant sections of this Manual which
should be referred to prior to commencing repair
operations.
The refrigerant used in the air conditioning system is
HFC-134a (Hydrofluorocarbon) R134a.
WARNING: Servicing must only be carried out by
personnel familiar with both the vehicle system
and the charging and testing equipment. All
operations must be carried out in a well
ventilated area away from open flame and heat
sources.
WARNING: R134a is a hazardous liquid and when
handled incorrectly can cause serious injury.
Suitable protective clothing, consisting of face
protection, heat proof gloves, rubber boots and
rubber apron or waterproof overalls, must be
worn when carrying out operations on the air
conditioning system.
Remedial actions
If an accident involving R134a should occur, conduct
the following remedial actions:
lIf liquid R134a enters the eye, do not rub it.
Gently run large quantities of eye wash over
affected eye to raise the temperature. If an eye
wash is not available, cool, clean water may be
used to flush the eye. After rinsing, cover the
eye with a clean pad and seek immediate
medical attention.lIf liquid R134a is splashed onto the skin, run
large quantities of water over the affected area
to raise the temperature. Implement the same
action if the skin comes in contact with
discharging cylinders. Wrap the contaminated
body parts in blankets (or similar materials) and
seek immediate medical attention.
lIf the debilitating effects of inhalation of R134a
vapour is suspected, seek fresh air. If the
affected person is unconscious, move them
away from the contaminated area to fresh air
and apply artificial respiration and/or oxygen
and seek immediate medical attention.
WARNING: Due to its low evaporating
temperature, R134a must be handled with care.
R134a splashed on any part of the body will
cause immediate freezing of that area. Also,
refrigerant cylinders and replenishment trolleys
when discharging will freeze skin to them if
contact is made.
Service precautions
Observe the following precautions when handling
components used in the air conditioning system:
lAir conditioning units must not be lifted by their
hoses, pipes or capillary lines.
lHoses and lines must not be subjected to any
twist or stress; the efficiency of the system will
be impaired by kinks or restrictions. Ensure that
hoses are correctly positioned before tightening
couplings, and ensure that all clips and supports
are utilised.
lFlexible hoses should not be positioned close to
the exhaust manifold (less than 100mm) unless
protected by heat shielding.
lCompleted assemblies must be checked for
refrigeration lines touching metal panels. Any
direct contact of components and panels may
transmit noise and so must be eliminated.
lThe appropriate torque wrench must be used
when tightening refrigerant connections to the
stipulated value. An additional spanner must be
used to hold the union to prevent twisting of the
pipe when tightening connections.
lBefore connecting any hose or pipe, ensure that
refrigerant oil is applied to the seat of the new 'O'
rings, BUT NOT to the threads of the
connection.
lAll protective plugs must remain in place to seal
the component until immediately prior to
connection.
lEnsure components are at room temperature
before uncapping, to prevent condensation of
moisture from the air that enters it.
Page 62 of 1672
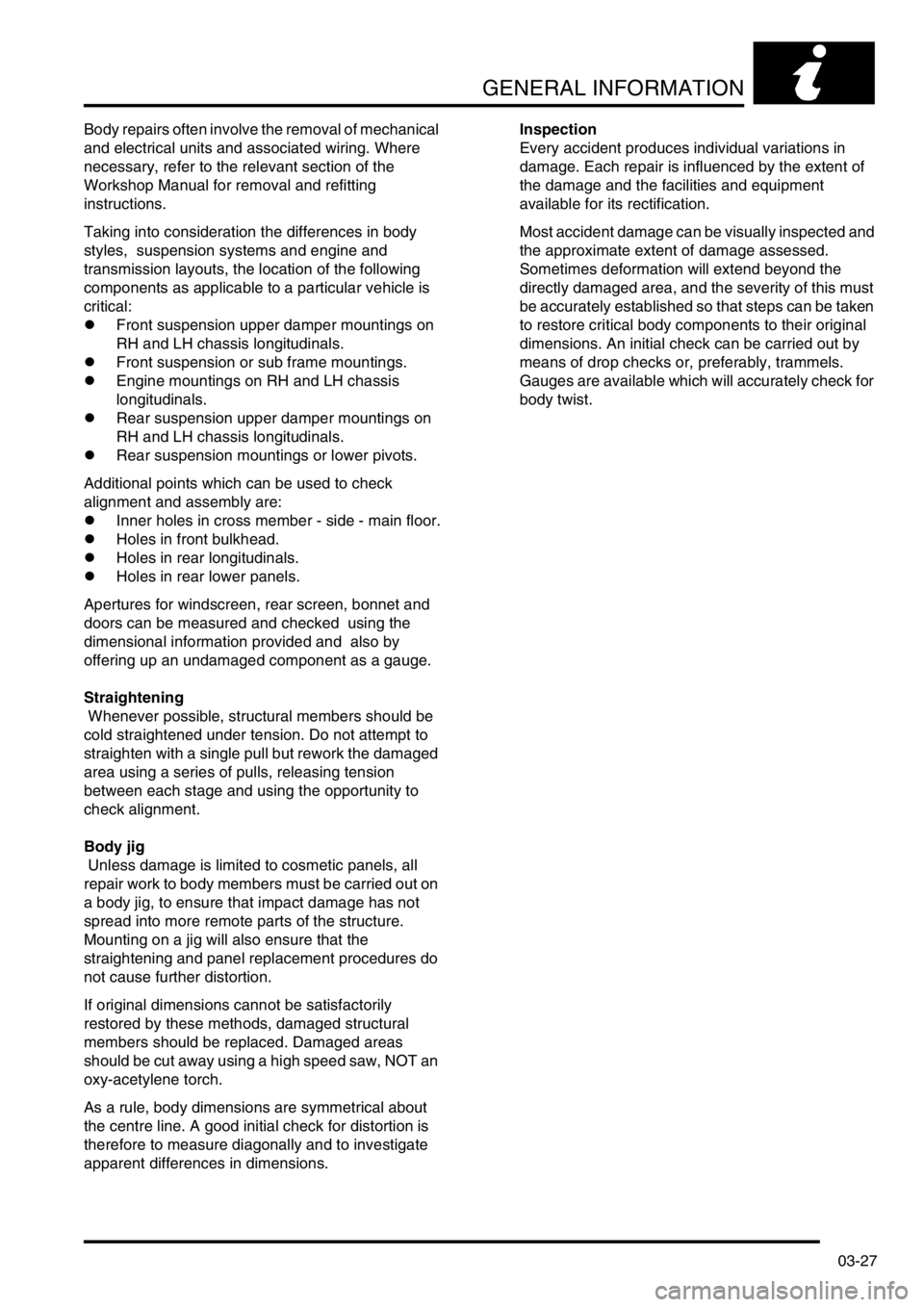
GENERAL INFORMATION
03-27
Body repairs often involve the removal of mechanical
and electrical units and associated wiring. Where
necessary, refer to the relevant section of the
Workshop Manual for removal and refitting
instructions.
Taking into consideration the differences in body
styles, suspension systems and engine and
transmission layouts, the location of the following
components as applicable to a particular vehicle is
critical:
lFront suspension upper damper mountings on
RH and LH chassis longitudinals.
lFront suspension or sub frame mountings.
lEngine mountings on RH and LH chassis
longitudinals.
lRear suspension upper damper mountings on
RH and LH chassis longitudinals.
lRear suspension mountings or lower pivots.
Additional points which can be used to check
alignment and assembly are:
lInner holes in cross member - side - main floor.
lHoles in front bulkhead.
lHoles in rear longitudinals.
lHoles in rear lower panels.
Apertures for windscreen, rear screen, bonnet and
doors can be measured and checked using the
dimensional information provided and also by
offering up an undamaged component as a gauge.
Straightening
Whenever possible, structural members should be
cold straightened under tension. Do not attempt to
straighten with a single pull but rework the damaged
area using a series of pulls, releasing tension
between each stage and using the opportunity to
check alignment.
Body jig
Unless damage is limited to cosmetic panels, all
repair work to body members must be carried out on
a body jig, to ensure that impact damage has not
spread into more remote parts of the structure.
Mounting on a jig will also ensure that the
straightening and panel replacement procedures do
not cause further distortion.
If original dimensions cannot be satisfactorily
restored by these methods, damaged structural
members should be replaced. Damaged areas
should be cut away using a high speed saw, NOT an
oxy-acetylene torch.
As a rule, body dimensions are symmetrical about
the centre line. A good initial check for distortion is
therefore to measure diagonally and to investigate
apparent differences in dimensions.Inspection
Every accident produces individual variations in
damage. Each repair is influenced by the extent of
the damage and the facilities and equipment
available for its rectification.
Most accident damage can be visually inspected and
the approximate extent of damage assessed.
Sometimes deformation will extend beyond the
directly damaged area, and the severity of this must
be accurately established so that steps can be taken
to restore critical body components to their original
dimensions. An initial check can be carried out by
means of drop checks or, preferably, trammels.
Gauges are available which will accurately check for
body twist.