torque MAZDA 6 2002 Workshop Manual Suplement
[x] Cancel search | Manufacturer: MAZDA, Model Year: 2002, Model line: 6, Model: MAZDA 6 2002Pages: 909, PDF Size: 17.16 MB
Page 704 of 909
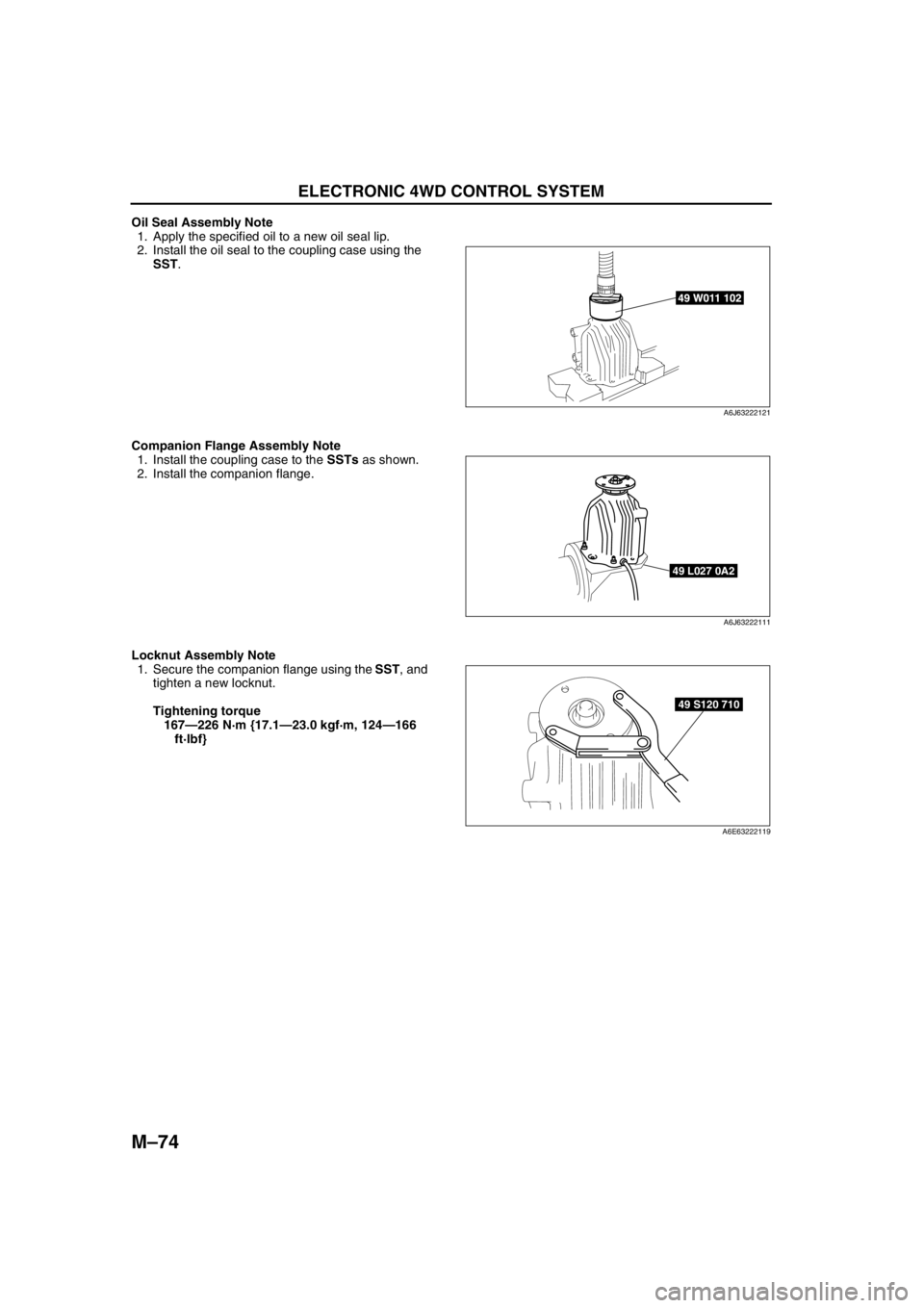
M–74
ELECTRONIC 4WD CONTROL SYSTEM
Oil Seal Assembly Note
1. Apply the specified oil to a new oil seal lip.
2. Install the oil seal to the coupling case using the
SST.
Companion Flange Assembly Note
1. Install the coupling case to the SSTs as shown.
2. Install the companion flange.
Locknut Assembly Note
1. Secure the companion flange using the SST, and
tighten a new locknut.
Tightening torque
167—226 N·m {17.1—23.0 kgf·m, 124—166
ft·lbf}
End Of Sie
49 W011 102
A6J63222121
49 L027 0A2
A6J63222111
49 S120 710
A6E63222119
Page 710 of 909
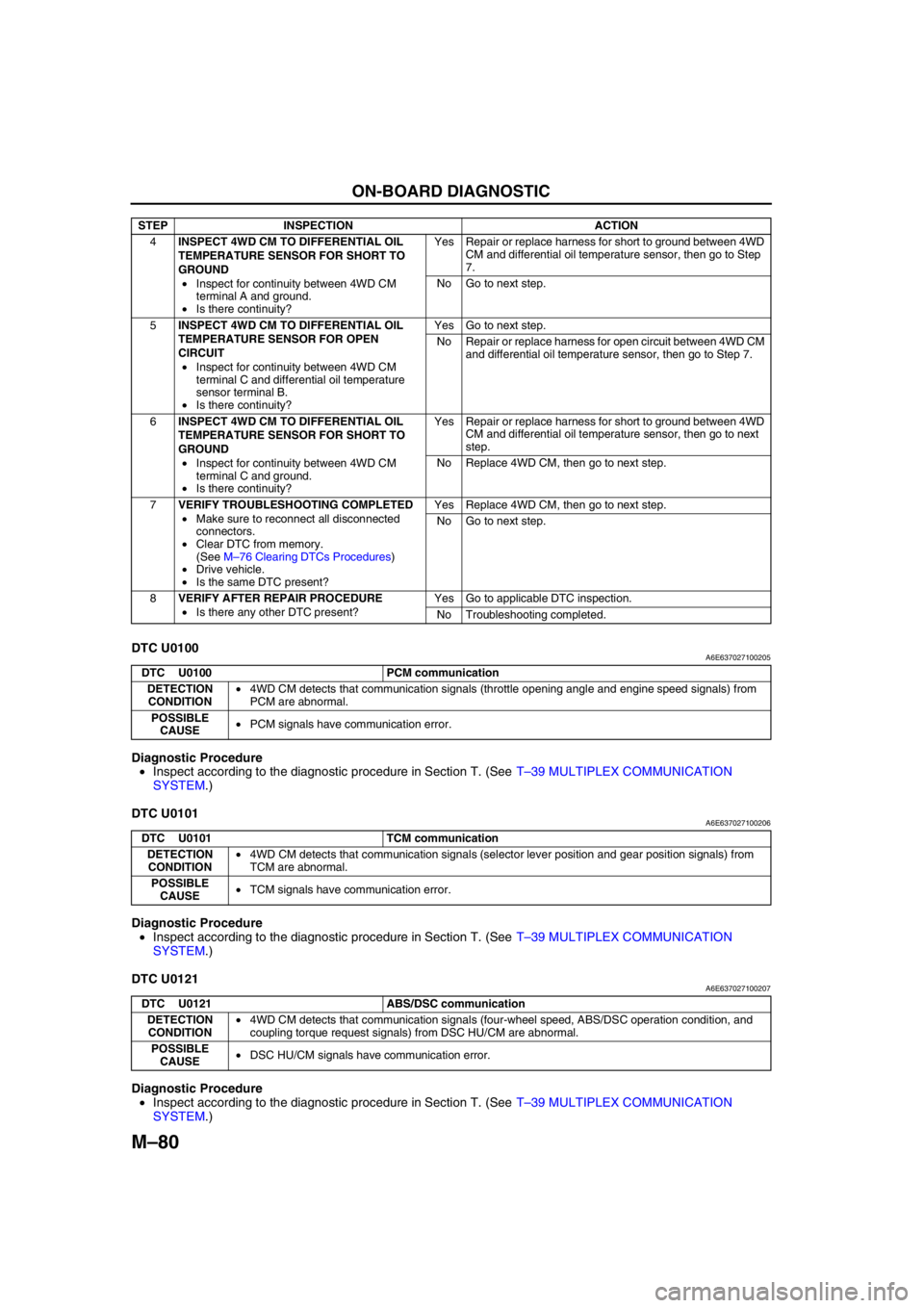
M–80
ON-BOARD DIAGNOSTIC
End Of Sie
DTC U0100A6E637027100205
Diagnostic Procedure
•Inspect according to the diagnostic procedure in Section T. (See T–39 MULTIPLEX COMMUNICATION
SYSTEM.)
End Of Sie
DTC U0101A6E637027100206
Diagnostic Procedure
•Inspect according to the diagnostic procedure in Section T. (See T–39 MULTIPLEX COMMUNICATION
SYSTEM.)
End Of Sie
DTC U0121A6E637027100207
Diagnostic Procedure
•Inspect according to the diagnostic procedure in Section T. (See T–39 MULTIPLEX COMMUNICATION
SYSTEM.)
End Of Sie
4INSPECT 4WD CM TO DIFFERENTIAL OIL
TEMPERATURE SENSOR FOR SHORT TO
GROUND
•Inspect for continuity between 4WD CM
terminal A and ground.
•Is there continuity?Yes Repair or replace harness for short to ground between 4WD
CM and differential oil temperature sensor, then go to Step
7.
No Go to next step.
5INSPECT 4WD CM TO DIFFERENTIAL OIL
TEMPERATURE SENSOR FOR OPEN
CIRCUIT
•Inspect for continuity between 4WD CM
terminal C and differential oil temperature
sensor terminal B.
•Is there continuity?Yes Go to next step.
No Repair or replace harness for open circuit between 4WD CM
and differential oil temperature sensor, then go to Step 7.
6INSPECT 4WD CM TO DIFFERENTIAL OIL
TEMPERATURE SENSOR FOR SHORT TO
GROUND
•Inspect for continuity between 4WD CM
terminal C and ground.
•Is there continuity?Yes Repair or replace harness for short to ground between 4WD
CM and differential oil temperature sensor, then go to next
step.
No Replace 4WD CM, then go to next step.
7VERIFY TROUBLESHOOTING COMPLETED
•Make sure to reconnect all disconnected
connectors.
•Clear DTC from memory.
(See M–76 Clearing DTCs Procedures)
•Drive vehicle.
•Is the same DTC present?Yes Replace 4WD CM, then go to next step.
No Go to next step.
8VERIFY AFTER REPAIR PROCEDURE
•Is there any other DTC present?Yes Go to applicable DTC inspection.
No Troubleshooting completed. STEP INSPECTION ACTION
DTC U0100 PCM communication
DETECTION
CONDITION•4WD CM detects that communication signals (throttle opening angle and engine speed signals) from
PCM are abnormal.
POSSIBLE
CAUSE•PCM signals have communication error.
DTC U0101 TCM communication
DETECTION
CONDITION•4WD CM detects that communication signals (selector lever position and gear position signals) from
TCM are abnormal.
POSSIBLE
CAUSE•TCM signals have communication error.
DTC U0121 ABS/DSC communication
DETECTION
CONDITION•4WD CM detects that communication signals (four-wheel speed, ABS/DSC operation condition, and
coupling torque request signals) from DSC HU/CM are abnormal.
POSSIBLE
CAUSE•DSC HU/CM signals have communication error.
Page 721 of 909
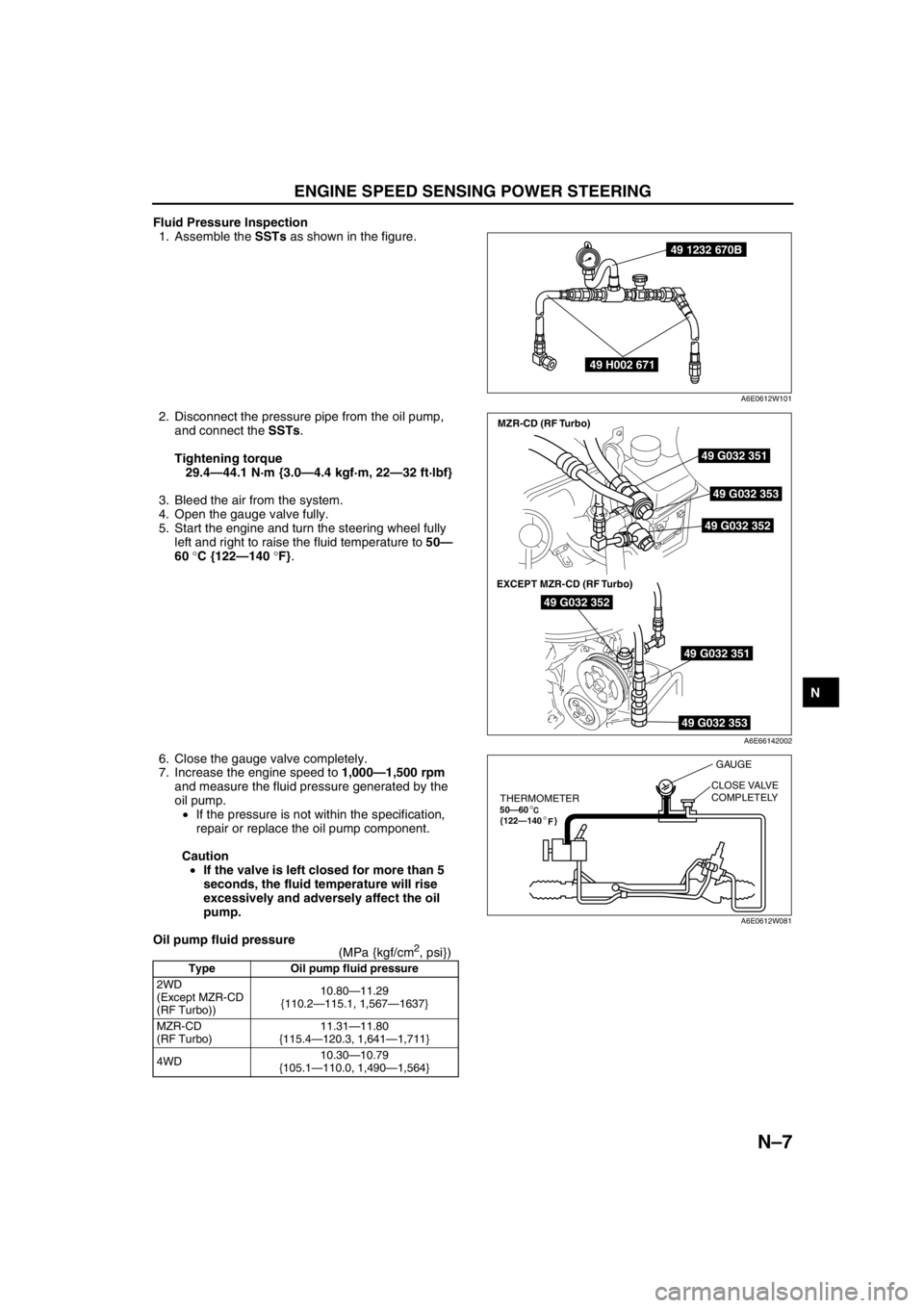
ENGINE SPEED SENSING POWER STEERING
N–7
N
Fluid Pressure Inspection
1. Assemble the SSTs as shown in the figure.
2. Disconnect the pressure pipe from the oil pump,
and connect the SSTs.
Tightening torque
29.4—44.1 N·m {3.0—4.4 kgf·m, 22—32 ft·lbf}
3. Bleed the air from the system.
4. Open the gauge valve fully.
5. Start the engine and turn the steering wheel fully
left and right to raise the fluid temperature to 50—
60 °C {122—140 °F}.
6. Close the gauge valve completely.
7. Increase the engine speed to 1,000—1,500 rpm
and measure the fluid pressure generated by the
oil pump.
•If the pressure is not within the specification,
repair or replace the oil pump component.
Caution
•If the valve is left closed for more than 5
seconds, the fluid temperature will rise
excessively and adversely affect the oil
pump.
Oil pump fluid pressure
(MPa {kgf/cm
2, psi})
Type Oil pump fluid pressure
2WD
(Except MZR-CD
(RF Turbo))10.80—11.29
{110.2—115.1, 1,567—1637}
MZR-CD
(RF Turbo)11.31—11.80
{115.4—120.3, 1,641—1,711}
4WD10.30—10.79
{105.1—110.0, 1,490—1,564}
49 1232 670B
49 H002 671
A6E0612W101
49 G032 351
49 G032 353
49 G032 352
49 G032 352
49 G032 351
49 G032 353
MZR-CD (RF Turbo)
EXCEPT MZR-CD (RF Turbo)
A6E66142002
THERMOMETER50—60
{122—140 }°
°F
GAUGE
CLOSE VALVE
COMPLETELY
A6E0612W081
Page 722 of 909
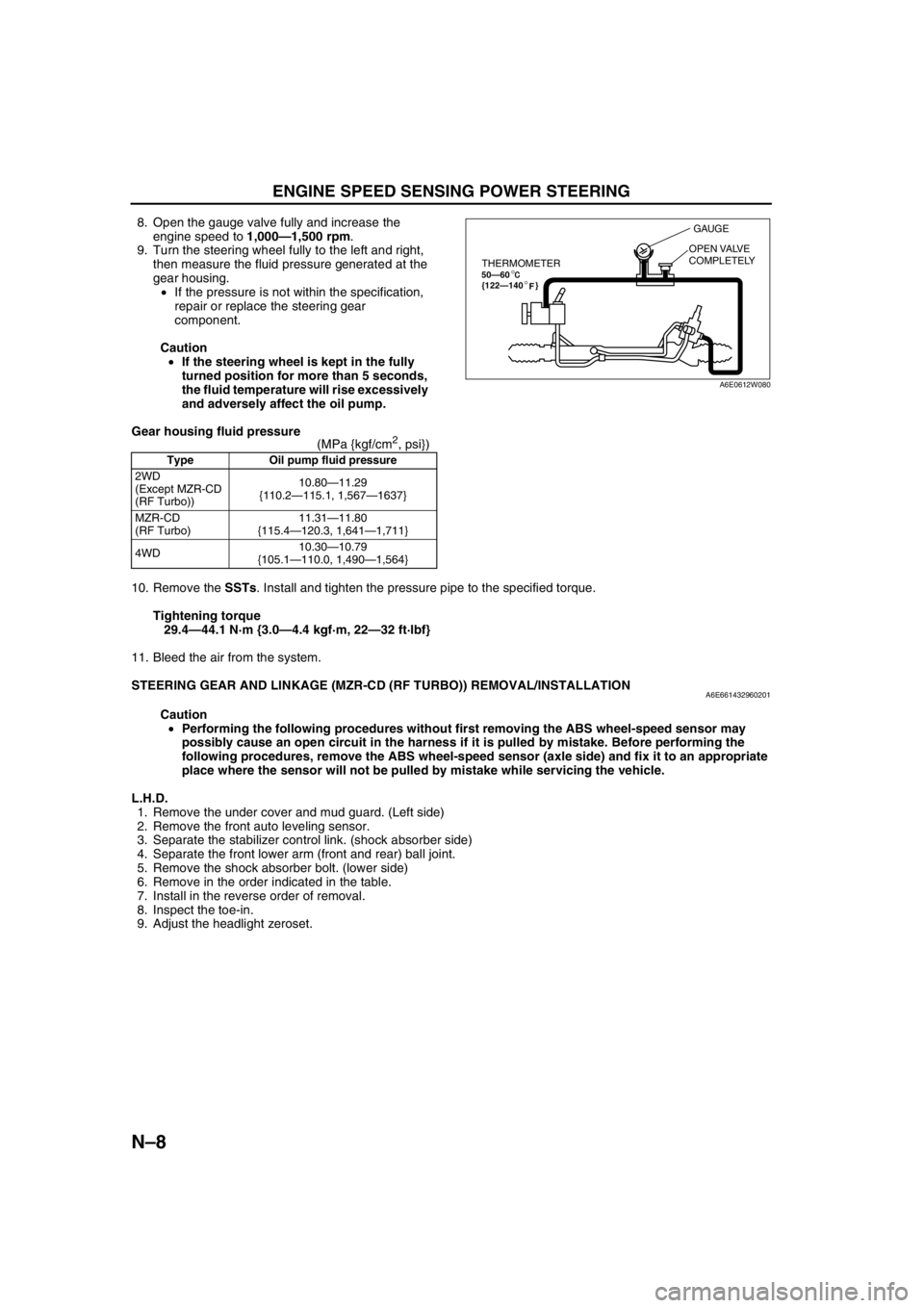
N–8
ENGINE SPEED SENSING POWER STEERING
8. Open the gauge valve fully and increase the
engine speed to 1,000—1,500 rpm.
9. Turn the steering wheel fully to the left and right,
then measure the fluid pressure generated at the
gear housing.
•If the pressure is not within the specification,
repair or replace the steering gear
component.
Caution
•If the steering wheel is kept in the fully
turned position for more than 5 seconds,
the fluid temperature will rise excessively
and adversely affect the oil pump.
Gear housing fluid pressure
(MPa {kgf/cm
2, psi})
10. Remove the SSTs. Install and tighten the pressure pipe to the specified torque.
Tightening torque
29.4—44.1 N·m {3.0—4.4 kgf·m, 22—32 ft·lbf}
11. Bleed the air from the system.
End Of Sie
STEERING GEAR AND LINKAGE (MZR-CD (RF TURBO)) REMOVAL/INSTALLATIONA6E661432960201
Caution
•Performing the following procedures without first removing the ABS wheel-speed sensor may
possibly cause an open circuit in the harness if it is pulled by mistake. Before performing the
following procedures, remove the ABS wheel-speed sensor (axle side) and fix it to an appropriate
place where the sensor will not be pulled by mistake while servicing the vehicle.
L.H.D.
1. Remove the under cover and mud guard. (Left side)
2. Remove the front auto leveling sensor.
3. Separate the stabilizer control link. (shock absorber side)
4. Separate the front lower arm (front and rear) ball joint.
5. Remove the shock absorber bolt. (lower side)
6. Remove in the order indicated in the table.
7. Install in the reverse order of removal.
8. Inspect the toe-in.
9. Adjust the headlight zeroset.
Type Oil pump fluid pressure
2WD
(Except MZR-CD
(RF Turbo))10.80—11.29
{110.2—115.1, 1,567—1637}
MZR-CD
(RF Turbo)11.31—11.80
{115.4—120.3, 1,641—1,711}
4WD10.30—10.79
{105.1—110.0, 1,490—1,564}
THERMOMETER50—60
{122—140 }°
°F
GAUGE
OPEN VALVE
COMPLETELY
A6E0612W080
Page 725 of 909
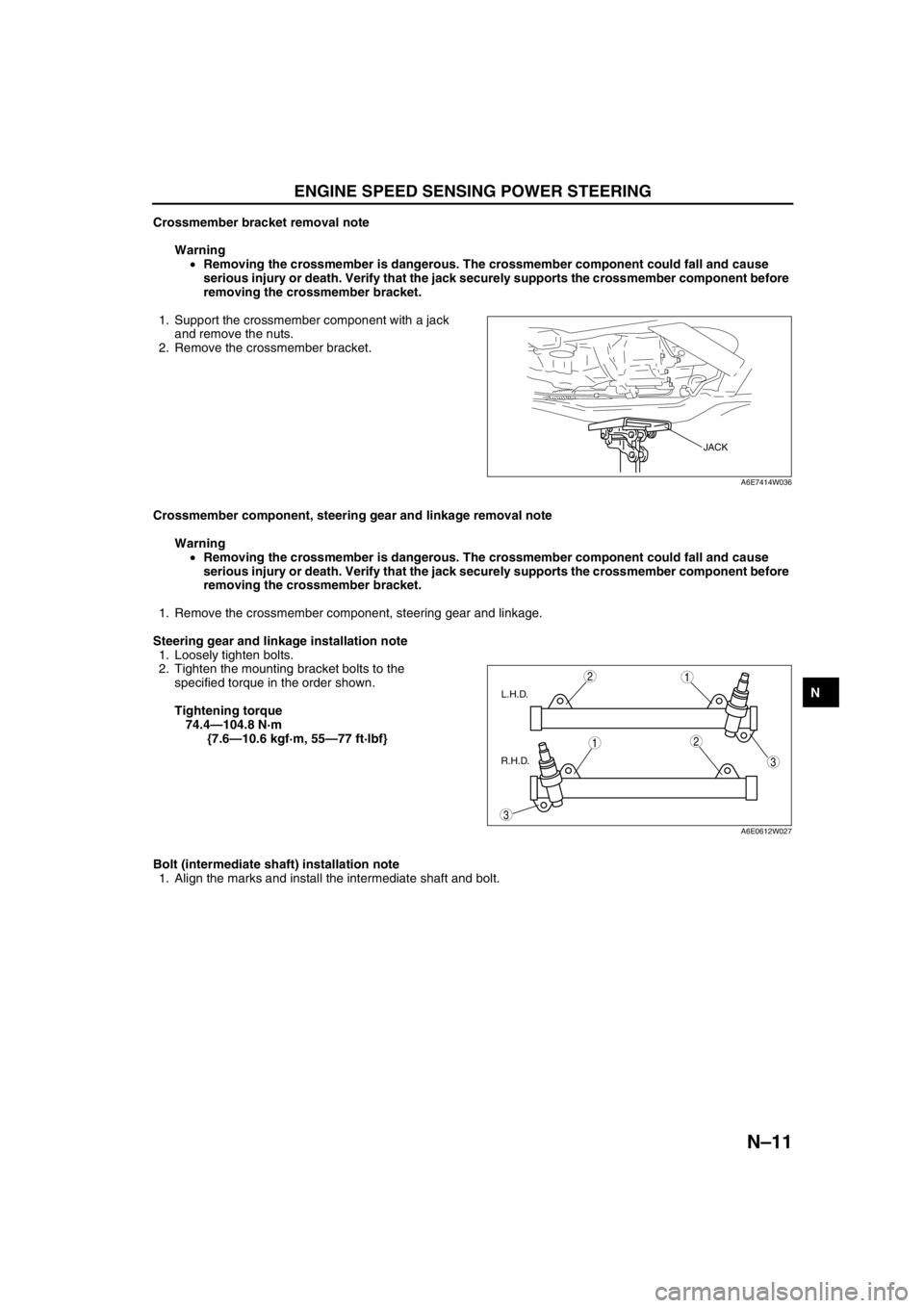
ENGINE SPEED SENSING POWER STEERING
N–11
N
Crossmember bracket removal note
Warning
•Removing the crossmember is dangerous. The crossmember component could fall and cause
serious injury or death. Verify that the jack securely supports the crossmember component before
removing the crossmember bracket.
1. Support the crossmember component with a jack
and remove the nuts.
2. Remove the crossmember bracket.
Crossmember component, steering gear and linkage removal note
Warning
•Removing the crossmember is dangerous. The crossmember component could fall and cause
serious injury or death. Verify that the jack securely supports the crossmember component before
removing the crossmember bracket.
1. Remove the crossmember component, steering gear and linkage.
Steering gear and linkage installation note
1. Loosely tighten bolts.
2. Tighten the mounting bracket bolts to the
specified torque in the order shown.
Tightening torque
74.4—104.8 N·m
{7.6—10.6 kgf·m, 55—77 ft·lbf}
Bolt (intermediate shaft) installation note
1. Align the marks and install the intermediate shaft and bolt.
JACK
A6E7414W036
3
3
1
1
2
2
L.H.D.
R.H.D.
A6E0612W027
Page 739 of 909
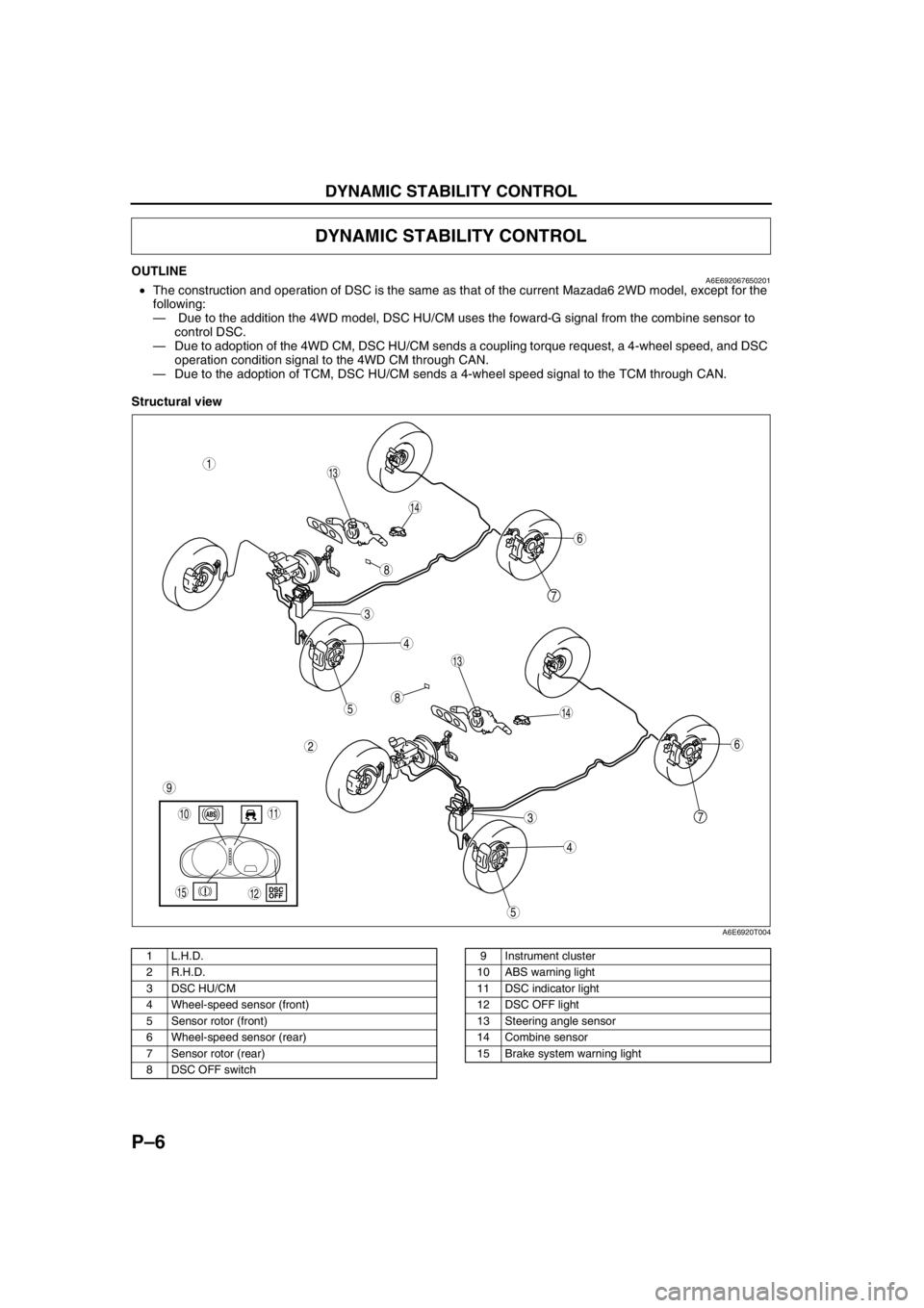
P–6
DYNAMIC STABILITY CONTROL
OUTLINEA6E692067650201•The construction and operation of DSC is the same as that of the current Mazada6 2WD model, except for the
following:
— Due to the addition the 4WD model, DSC HU/CM uses the foward-G signal from the combine sensor to
control DSC.
—Due to adoption of the 4WD CM, DSC HU/CM sends a coupling torque request, a 4-wheel speed, and DSC
operation condition signal to the 4WD CM through CAN.
—Due to the adoption of TCM, DSC HU/CM sends a 4-wheel speed signal to the TCM through CAN.
Structural view
.
DYNAMIC STABILITY CONTROL
7
5
4
3
1
2
14
13
6
13
12
5
4
3
7
6
1011
9
14
8
8
15
A6E6920T004
1 L.H.D.
2 R.H.D.
3 DSC HU/CM
4 Wheel-speed sensor (front)
5 Sensor rotor (front)
6 Wheel-speed sensor (rear)
7 Sensor rotor (rear)
8 DSC OFF switch9 Instrument cluster
10 ABS warning light
11 DSC indicator light
12 DSC OFF light
13 Steering angle sensor
14 Combine sensor
15 Brake system warning light
Page 741 of 909
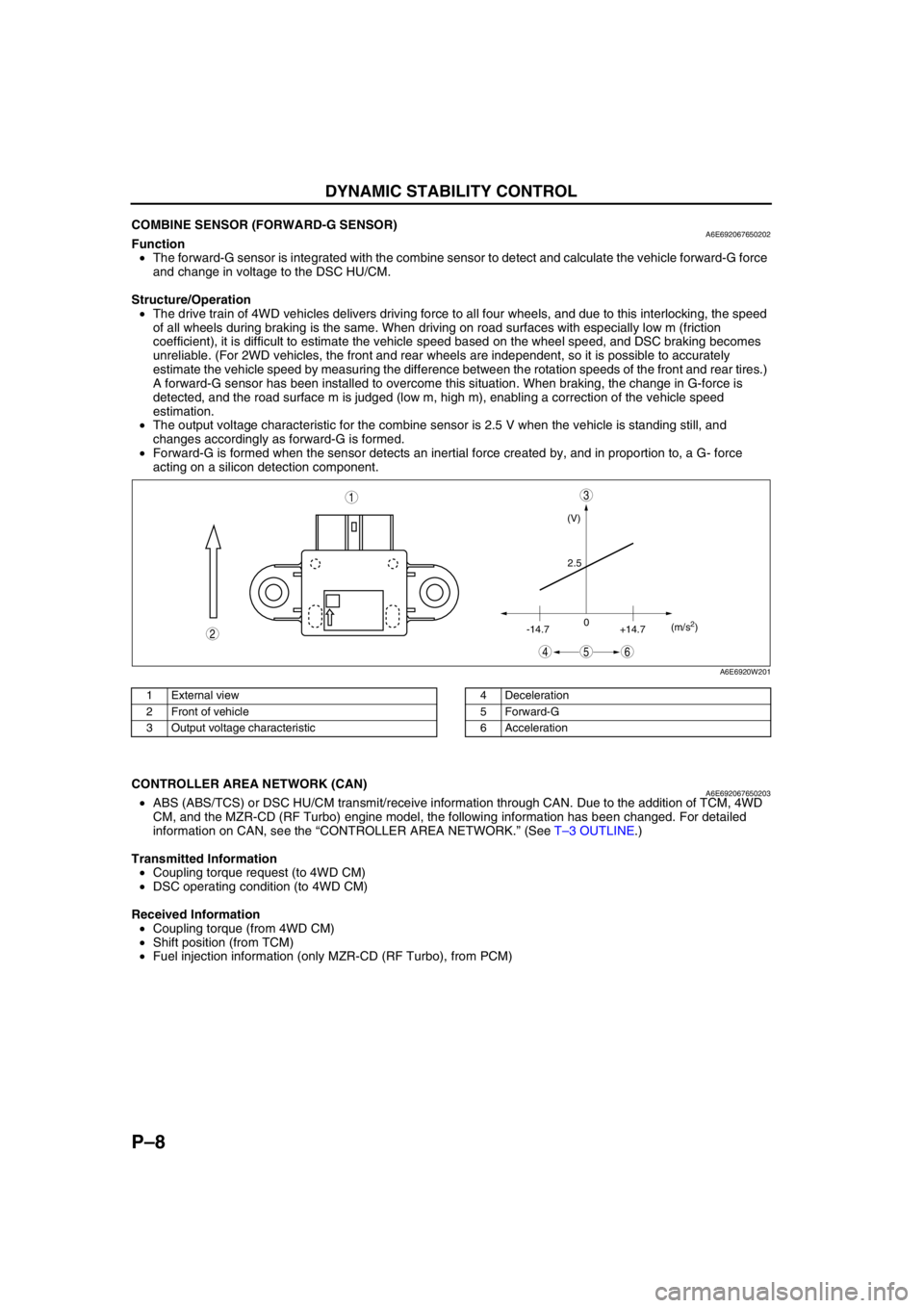
P–8
DYNAMIC STABILITY CONTROL
End Of SieCOMBINE SENSOR (FORWARD-G SENSOR)A6E692067650202Function
•The forward-G sensor is integrated with the combine sensor to detect and calculate the vehicle forward-G force
and change in voltage to the DSC HU/CM.
Structure/Operation
•The drive train of 4WD vehicles delivers driving force to all four wheels, and due to this interlocking, the speed
of all wheels during braking is the same. When driving on road surfaces with especially low m (friction
coefficient), it is difficult to estimate the vehicle speed based on the wheel speed, and DSC braking becomes
unreliable. (For 2WD vehicles, the front and rear wheels are independent, so it is possible to accurately
estimate the vehicle speed by measuring the difference between the rotation speeds of the front and rear tires.)
A forward-G sensor has been installed to overcome this situation. When braking, the change in G-force is
detected, and the road surface m is judged (low m, high m), enabling a correction of the vehicle speed
estimation.
•The output voltage characteristic for the combine sensor is 2.5 V when the vehicle is standing still, and
changes accordingly as forward-G is formed.
•Forward-G is formed when the sensor detects an inertial force created by, and in proportion to, a G- force
acting on a silicon detection component.
.
End Of Sie
CONTROLLER AREA NETWORK (CAN)A6E692067650203•ABS (ABS/TCS) or DSC HU/CM transmit/receive information through CAN. Due to the addition of TCM, 4WD
CM, and the MZR-CD (RF Turbo) engine model, the following information has been changed. For detailed
information on CAN, see the “CONTROLLER AREA NETWORK.” (See T–3 OUTLINE.)
Transmitted Information
•Coupling torque request (to 4WD CM)
•DSC operating condition (to 4WD CM)
Received Information
•Coupling torque (from 4WD CM)
•Shift position (from TCM)
•Fuel injection information (only MZR-CD (RF Turbo), from PCM)
End Of Sie
(V)
2.5
-14.70
+14.7(m/s
2)
45
3
6
2
1
A6E6920W201
1 External view
2 Front of vehicle
3 Output voltage characteristic4 Deceleration
5 Forward-G
6 Acceleration
Page 743 of 909
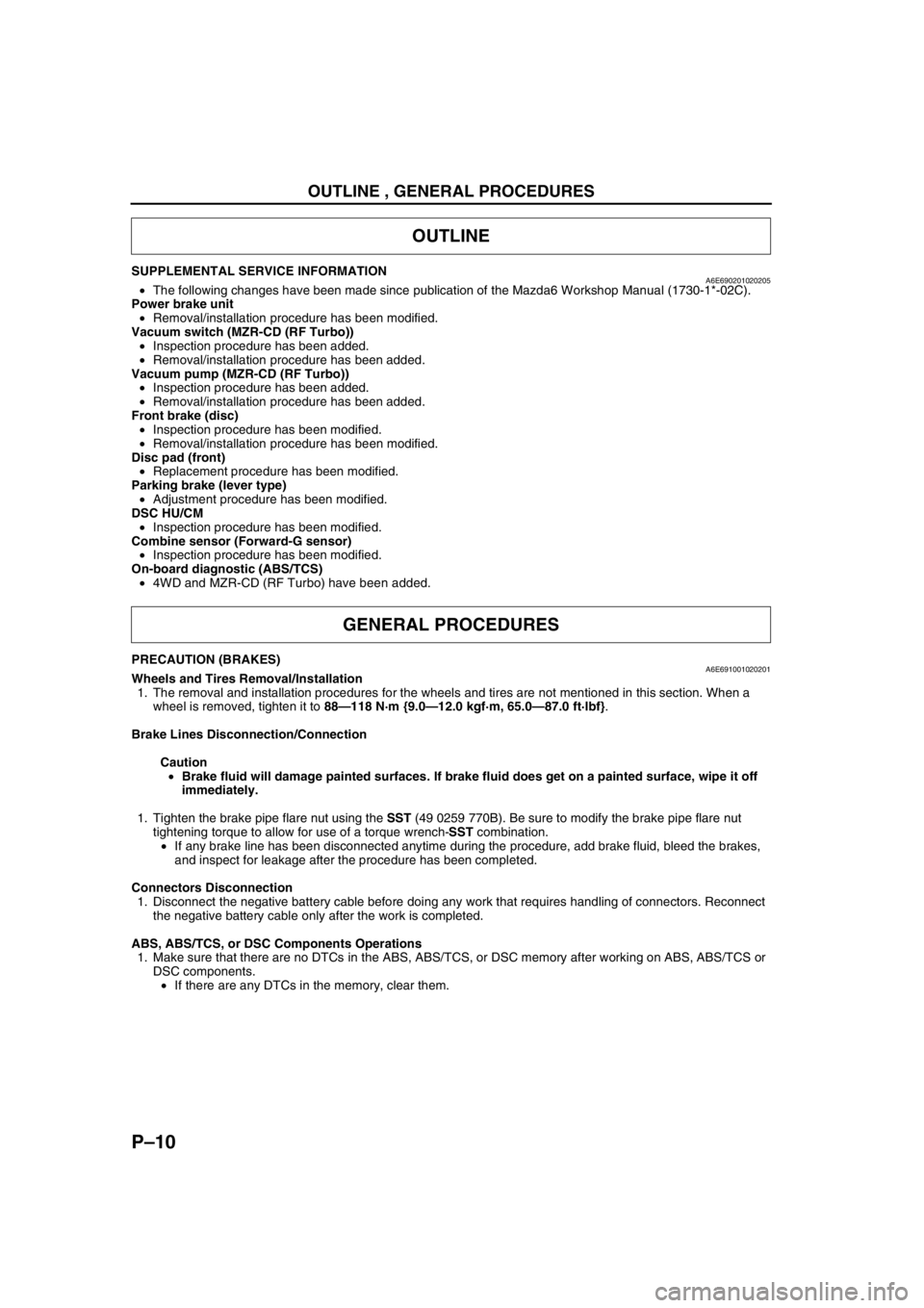
P–10
OUTLINE , GENERAL PROCEDURES
SUPPLEMENTAL SERVICE INFORMATIONA6E690201020205•The following changes have been made since publication of the Mazda6 Workshop Manual (1730-1*-02C).
Power brake unit
•Removal/installation procedure has been modified.
Vacuum switch (MZR-CD (RF Turbo))
•Inspection procedure has been added.
•Removal/installation procedure has been added.
Vacuum pump (MZR-CD (RF Turbo))
•Inspection procedure has been added.
•Removal/installation procedure has been added.
Front brake (disc)
•Inspection procedure has been modified.
•Removal/installation procedure has been modified.
Disc pad (front)
•Replacement procedure has been modified.
Parking brake (lever type)
•Adjustment procedure has been modified.
DSC HU/CM
•Inspection procedure has been modified.
Combine sensor (Forward-G sensor)
•Inspection procedure has been modified.
On-board diagnostic (ABS/TCS)
•4WD and MZR-CD (RF Turbo) have been added.
End Of Sie
PRECAUTION (BRAKES)A6E691001020201Wheels and Tires Removal/Installation
1. The removal and installation procedures for the wheels and tires are not mentioned in this section. When a
wheel is removed, tighten it to 88—118 N·m {9.0—12.0 kgf·m, 65.0—87.0 ft·lbf}.
Brake Lines Disconnection/Connection
Caution
•Brake fluid will damage painted surfaces. If brake fluid does get on a painted surface, wipe it off
immediately.
1. Tighten the brake pipe flare nut using the SST (49 0259 770B). Be sure to modify the brake pipe flare nut
tightening torque to allow for use of a torque wrench-SST combination.
•If any brake line has been disconnected anytime during the procedure, add brake fluid, bleed the brakes,
and inspect for leakage after the procedure has been completed.
Connectors Disconnection
1. Disconnect the negative battery cable before doing any work that requires handling of connectors. Reconnect
the negative battery cable only after the work is completed.
ABS, ABS/TCS, or DSC Components Operations
1. Make sure that there are no DTCs in the ABS, ABS/TCS, or DSC memory after working on ABS, ABS/TCS or
DSC components.
•If there are any DTCs in the memory, clear them.
End Of Sie
OUTLINE
GENERAL PROCEDURES
Page 758 of 909
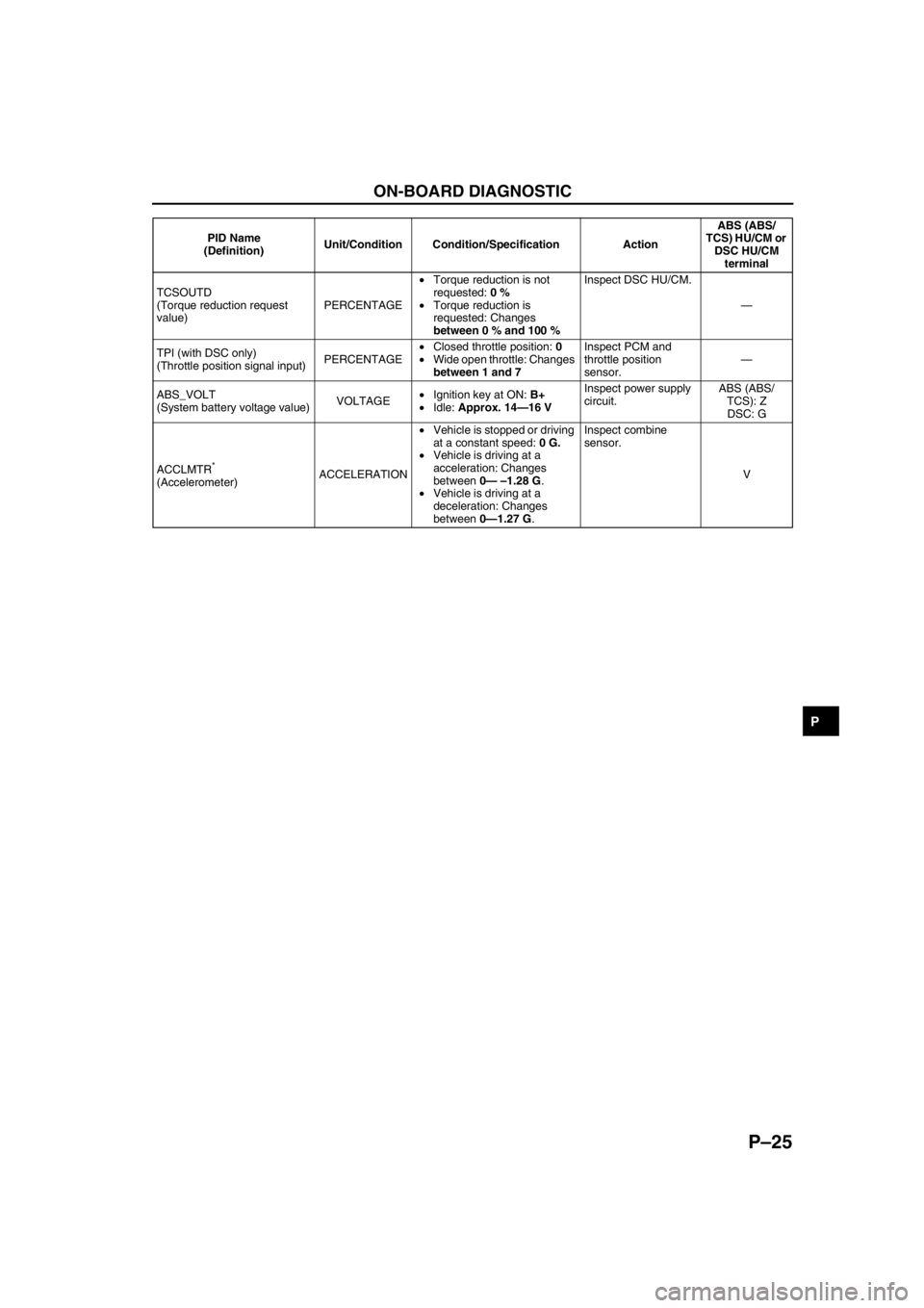
ON-BOARD DIAGNOSTIC
P–25
P
End Of Sie
TCSOUTD
(Torque reduction request
value)PERCENTAGE•Torque reduction is not
requested: 0 %
•Torque reduction is
requested: Changes
between 0 % and 100 %Inspect DSC HU/CM.
—
TPI (with DSC only)
(Throttle position signal input)PERCENTAGE•Closed throttle position: 0
•Wide open throttle: Changes
between 1 and 7Inspect PCM and
throttle position
sensor.—
ABS_VOLT
(System battery voltage value)VOLTAGE•Ignition key at ON: B+
•Idle: Approx. 14—16 VInspect power supply
circuit.ABS (ABS/
TCS): Z
DSC: G
ACCLMTR
*
(Accelerometer)ACCELERATION•Vehicle is stopped or driving
at a constant speed: 0 G.
•Vehicle is driving at a
acceleration: Changes
between 0— –1.28 G.
•Vehicle is driving at a
deceleration: Changes
between 0—1.27 G.Inspect combine
sensor.
V PID Name
(Definition)Unit/Condition Condition/Specification ActionABS (ABS/
TCS) HU/CM or
DSC HU/CM
terminal
Page 759 of 909
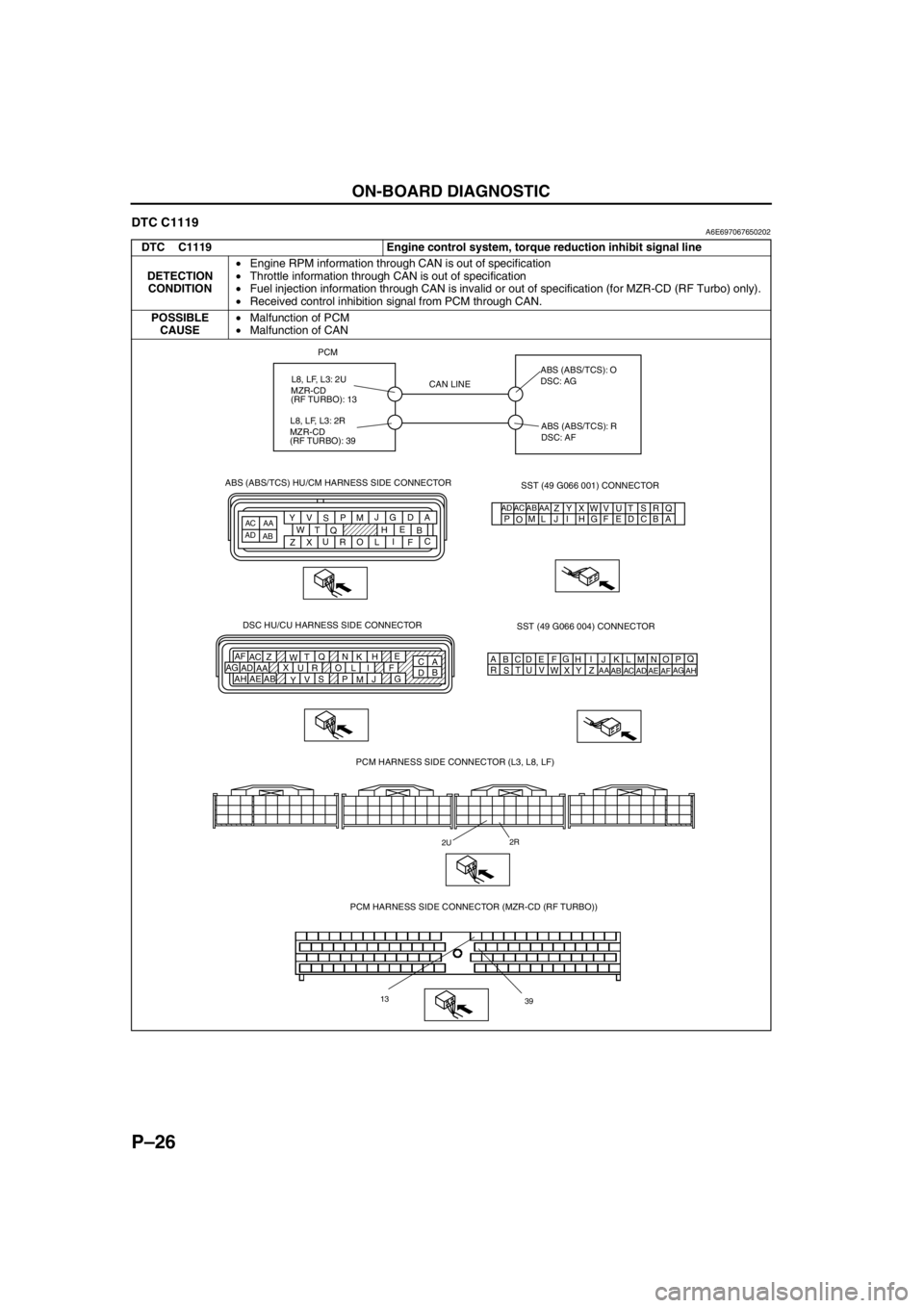
P–26
ON-BOARD DIAGNOSTIC
DTC C1119A6E697067650202
DTC C1119 Engine control system, torque reduction inhibit signal line
DETECTION
CONDITION•Engine RPM information through CAN is out of specification
•Throttle information through CAN is out of specification
•Fuel injection information through CAN is invalid or out of specification (for MZR-CD (RF Turbo) only).
•Received control inhibition signal from PCM through CAN.
POSSIBLE
CAUSE•Malfunction of PCM
•Malfunction of CAN
PCM
PCM HARNESS SIDE CONNECTOR (L3, L8, LF)
2U2R
CAN LINEABS (ABS/TCS): O
DSC: AG
ABS (ABS/TCS): R
DSC: AF
AQ
B
CDE
FG
HI
J DSC HU/CU HARNESS SIDE CONNECTOR
A
C E
H
K N Q
T
W Z AC AF
F I L O R U X
AA AD AG
G
J
M P S
V
Y AB
AE AHB
DKN
T
WZ
AC
AFLO
RU
XAA
ADAGMP
SV
YAB
AEAH
SST (49 G066 001) CONNECTOR
AD AC AB AAA Q
B R
C S
D T
E U
F V
G W
H X
I Y
J L M
O PZ ABS (ABS/TCS) HU/CM HARNESS SIDE CONNECTOR
ADAC
ABAA
A
B
C D
E
F G
H
I J
L M
O P
Q
R S
T
U V
W
X Y
Z
SST (49 G066 004) CONNECTOR
PCM HARNESS SIDE CONNECTOR (MZR-CD (RF TURBO))
13
39
L8, LF, L3: 2U
MZR-CD
(RF TURBO): 13
L8, LF, L3: 2R
MZR-CD
(RF TURBO): 39