engine MAZDA 6 2002 Workshop Manual Suplement
[x] Cancel search | Manufacturer: MAZDA, Model Year: 2002, Model line: 6, Model: MAZDA 6 2002Pages: 909, PDF Size: 17.16 MB
Page 230 of 909
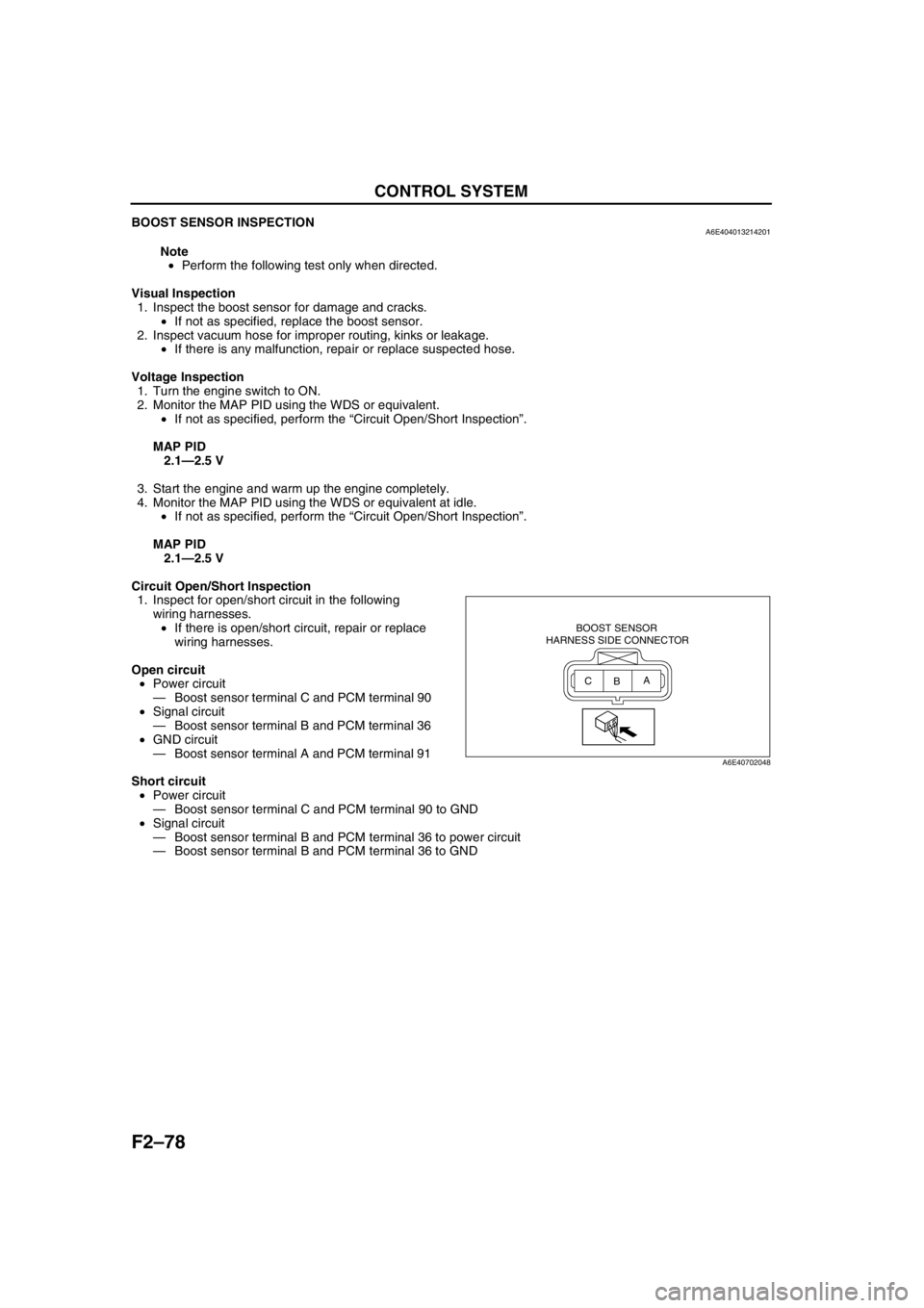
F2–78
CONTROL SYSTEM
BOOST SENSOR INSPECTIONA6E404013214201
Note
•Perform the following test only when directed.
Visual Inspection
1. Inspect the boost sensor for damage and cracks.
•If not as specified, replace the boost sensor.
2. Inspect vacuum hose for improper routing, kinks or leakage.
•If there is any malfunction, repair or replace suspected hose.
Voltage Inspection
1. Turn the engine switch to ON.
2. Monitor the MAP PID using the WDS or equivalent.
•If not as specified, perform the “Circuit Open/Short Inspection”.
MAP PID
2.1—2.5 V
3. Start the engine and warm up the engine completely.
4. Monitor the MAP PID using the WDS or equivalent at idle.
•If not as specified, perform the “Circuit Open/Short Inspection”.
MAP PID
2.1—2.5 V
Circuit Open/Short Inspection
1. Inspect for open/short circuit in the following
wiring harnesses.
•If there is open/short circuit, repair or replace
wiring harnesses.
Open circuit
•Power circuit
—Boost sensor terminal C and PCM terminal 90
•Signal circuit
—Boost sensor terminal B and PCM terminal 36
•GND circuit
—Boost sensor terminal A and PCM terminal 91
Short circuit
•Power circuit
—Boost sensor terminal C and PCM terminal 90 to GND
•Signal circuit
—Boost sensor terminal B and PCM terminal 36 to power circuit
—Boost sensor terminal B and PCM terminal 36 to GND
End Of Sie
BOOST SENSOR
HARNESS SIDE CONNECTOR
A
B C
A6E40702048
Page 231 of 909
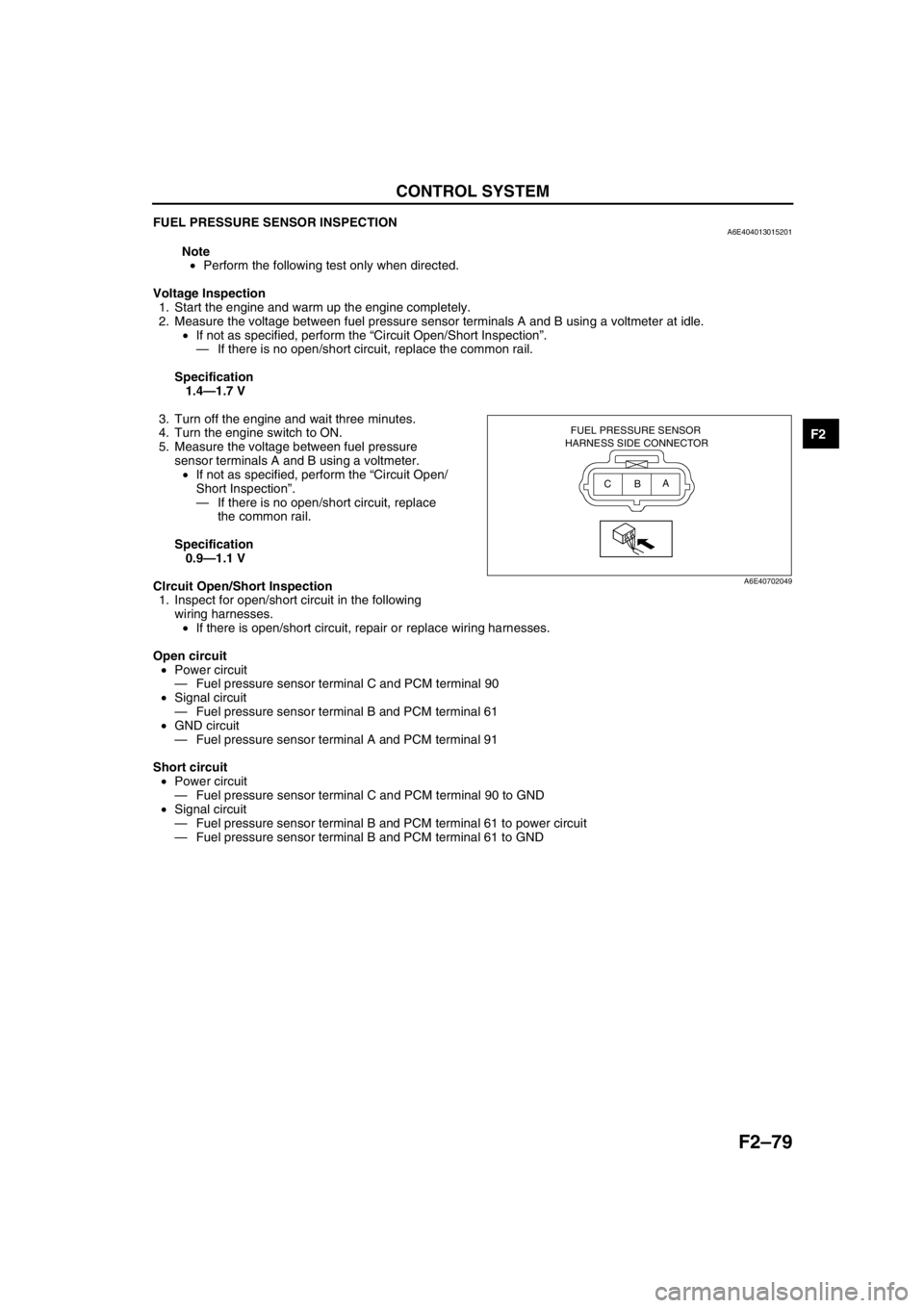
CONTROL SYSTEM
F2–79
F2
FUEL PRESSURE SENSOR INSPECTIONA6E404013015201
Note
•Perform the following test only when directed.
Voltage Inspection
1. Start the engine and warm up the engine completely.
2. Measure the voltage between fuel pressure sensor terminals A and B using a voltmeter at idle.
•If not as specified, perform the “Circuit Open/Short Inspection”.
—If there is no open/short circuit, replace the common rail.
Specification
1.4—1.7 V
3. Turn off the engine and wait three minutes.
4. Turn the engine switch to ON.
5. Measure the voltage between fuel pressure
sensor terminals A and B using a voltmeter.
•If not as specified, perform the “Circuit Open/
Short Inspection”.
—If there is no open/short circuit, replace
the common rail.
Specification
0.9—1.1 V
CIrcuit Open/Short Inspection
1. Inspect for open/short circuit in the following
wiring harnesses.
•If there is open/short circuit, repair or replace wiring harnesses.
Open circuit
•Power circuit
—Fuel pressure sensor terminal C and PCM terminal 90
•Signal circuit
—Fuel pressure sensor terminal B and PCM terminal 61
•GND circuit
—Fuel pressure sensor terminal A and PCM terminal 91
Short circuit
•Power circuit
—Fuel pressure sensor terminal C and PCM terminal 90 to GND
•Signal circuit
—Fuel pressure sensor terminal B and PCM terminal 61 to power circuit
—Fuel pressure sensor terminal B and PCM terminal 61 to GND
End Of Sie
FUEL PRESSURE SENSOR
HARNESS SIDE CONNECTOR
A
B C
A6E40702049
Page 232 of 909
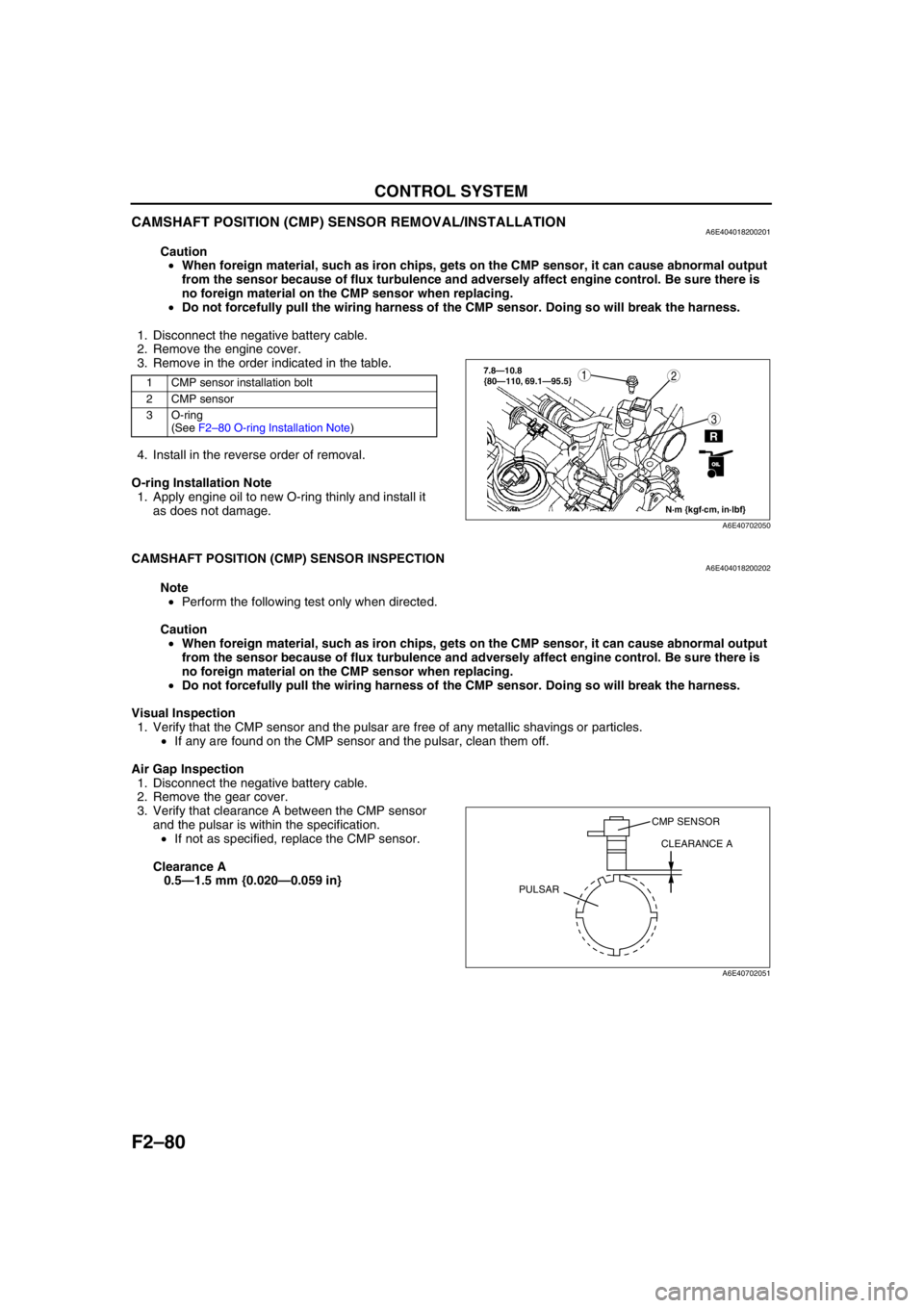
F2–80
CONTROL SYSTEM
CAMSHAFT POSITION (CMP) SENSOR REMOVAL/INSTALLATIONA6E404018200201
Caution
•When foreign material, such as iron chips, gets on the CMP sensor, it can cause abnormal output
from the sensor because of flux turbulence and adversely affect engine control. Be sure there is
no foreign material on the CMP sensor when replacing.
•Do not forcefully pull the wiring harness of the CMP sensor. Doing so will break the harness.
1. Disconnect the negative battery cable.
2. Remove the engine cover.
3. Remove in the order indicated in the table.
4. Install in the reverse order of removal.
O-ring Installation Note
1. Apply engine oil to new O-ring thinly and install it
as does not damage.
End Of Sie
CAMSHAFT POSITION (CMP) SENSOR INSPECTIONA6E404018200202
Note
•Perform the following test only when directed.
Caution
•When foreign material, such as iron chips, gets on the CMP sensor, it can cause abnormal output
from the sensor because of flux turbulence and adversely affect engine control. Be sure there is
no foreign material on the CMP sensor when replacing.
•Do not forcefully pull the wiring harness of the CMP sensor. Doing so will break the harness.
Visual Inspection
1. Verify that the CMP sensor and the pulsar are free of any metallic shavings or particles.
•If any are found on the CMP sensor and the pulsar, clean them off.
Air Gap Inspection
1. Disconnect the negative battery cable.
2. Remove the gear cover.
3. Verify that clearance A between the CMP sensor
and the pulsar is within the specification.
•If not as specified, replace the CMP sensor.
Clearance A
0.5—1.5 mm {0.020—0.059 in}
1 CMP sensor installation bolt
2 CMP sensor
3 O-ring
(See F2–80 O-ring Installation Note)
N·m {kgf·cm, in·lbf}
3
127.8—10.8
{80—110, 69.1—95.5}
R
OILOIL
A6E40702050
CMP SENSOR
CLEARANCE A
PULSAR
A6E40702051
Page 233 of 909
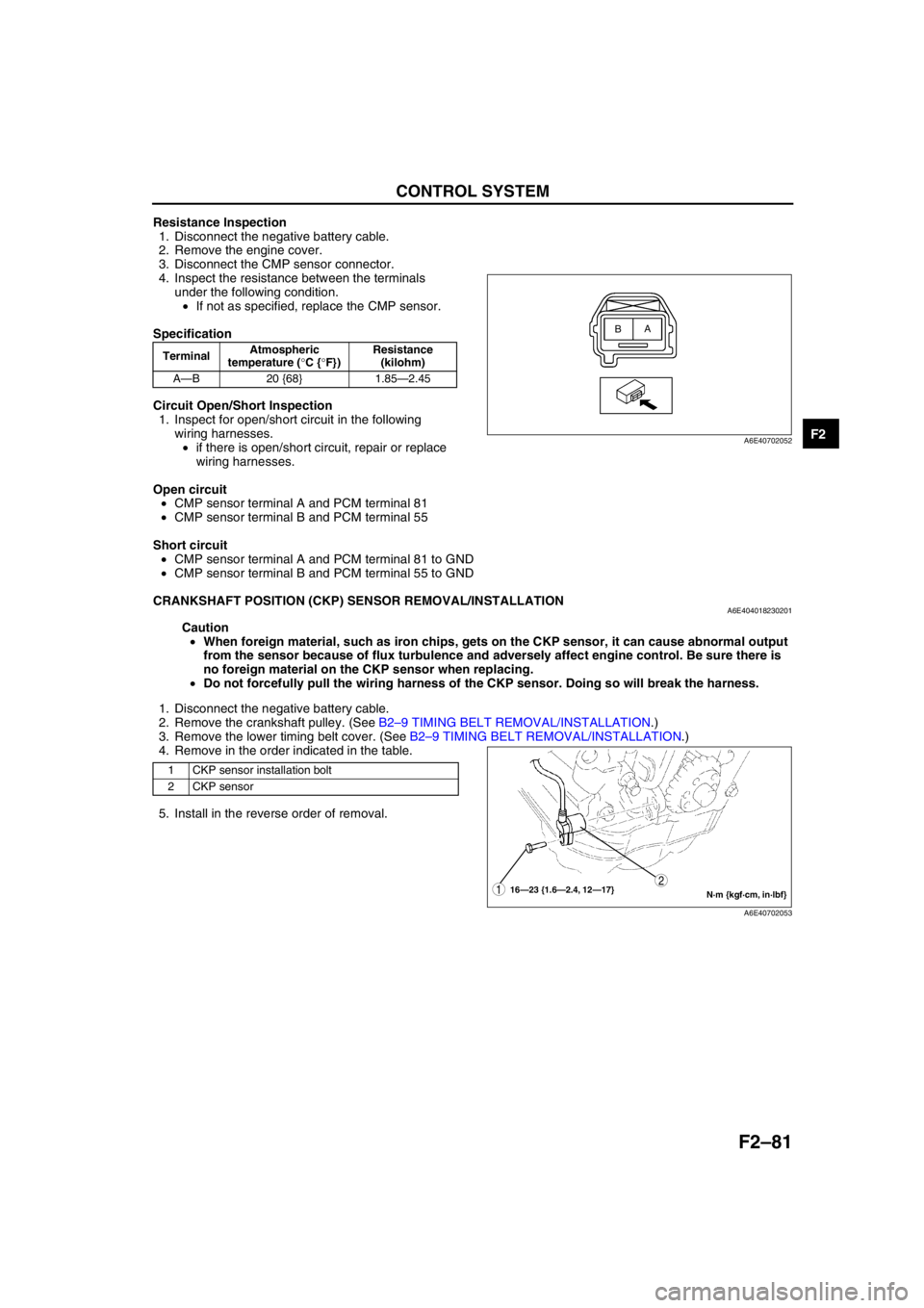
CONTROL SYSTEM
F2–81
F2
Resistance Inspection
1. Disconnect the negative battery cable.
2. Remove the engine cover.
3. Disconnect the CMP sensor connector.
4. Inspect the resistance between the terminals
under the following condition.
•If not as specified, replace the CMP sensor.
Specification
Circuit Open/Short Inspection
1. Inspect for open/short circuit in the following
wiring harnesses.
•if there is open/short circuit, repair or replace
wiring harnesses.
Open circuit
•CMP sensor terminal A and PCM terminal 81
•CMP sensor terminal B and PCM terminal 55
Short circuit
•CMP sensor terminal A and PCM terminal 81 to GND
•CMP sensor terminal B and PCM terminal 55 to GND
End Of Sie
CRANKSHAFT POSITION (CKP) SENSOR REMOVAL/INSTALLATIONA6E404018230201
Caution
•When foreign material, such as iron chips, gets on the CKP sensor, it can cause abnormal output
from the sensor because of flux turbulence and adversely affect engine control. Be sure there is
no foreign material on the CKP sensor when replacing.
•Do not forcefully pull the wiring harness of the CKP sensor. Doing so will break the harness.
1. Disconnect the negative battery cable.
2. Remove the crankshaft pulley. (See B2–9 TIMING BELT REMOVAL/INSTALLATION.)
3. Remove the lower timing belt cover. (See B2–9 TIMING BELT REMOVAL/INSTALLATION.)
4. Remove in the order indicated in the table.
5. Install in the reverse order of removal.
End Of Sie
TerminalAtmospheric
temperature (°C {°F})Resistance
(kilohm)
A—B 20 {68} 1.85—2.45
A
B
A6E40702052
1 CKP sensor installation bolt
2 CKP sensor
N·m {kgf·cm, in·lbf} 16—23 {1.6—2.4, 12—17}12
A6E40702053
Page 234 of 909
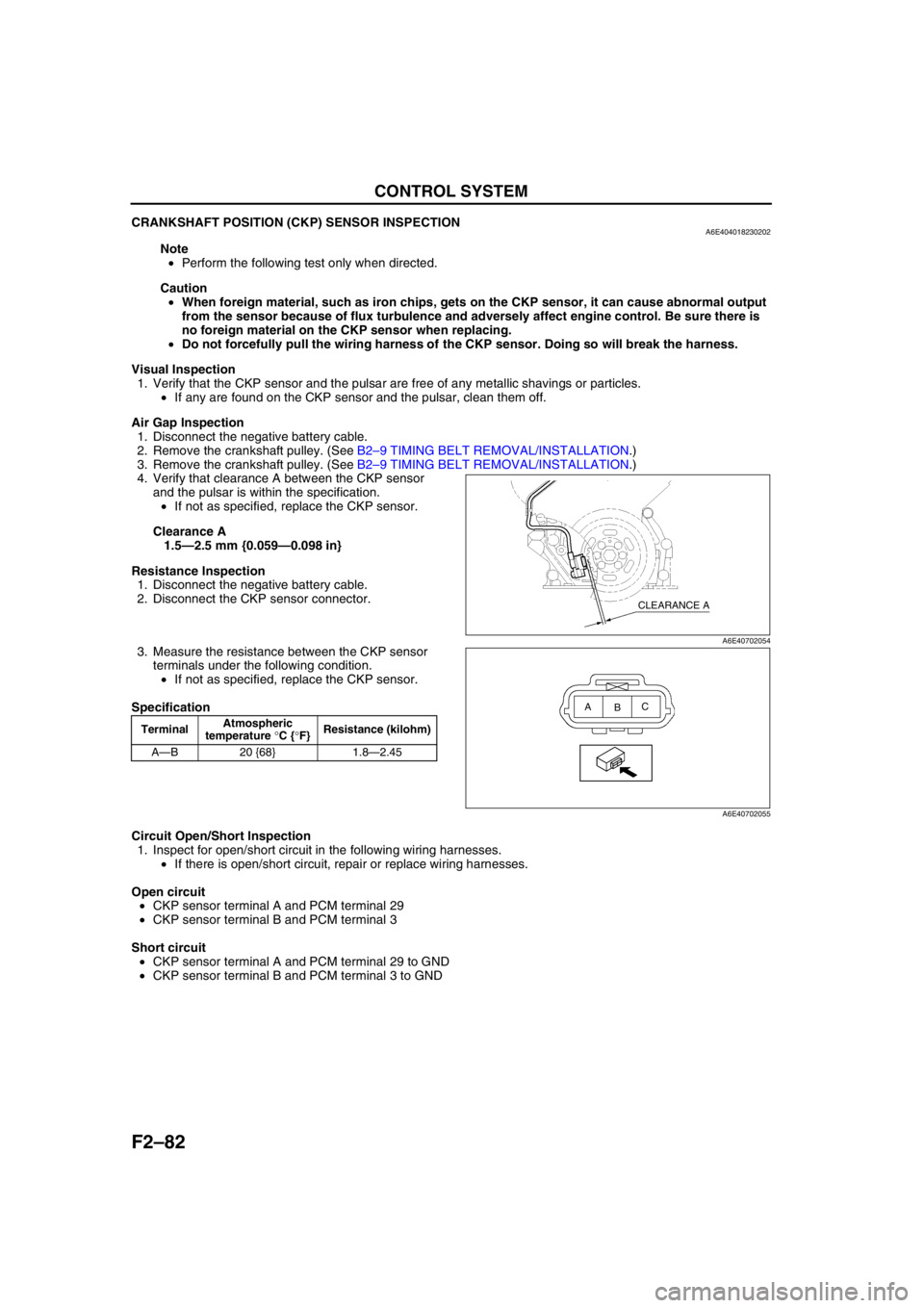
F2–82
CONTROL SYSTEM
CRANKSHAFT POSITION (CKP) SENSOR INSPECTIONA6E404018230202
Note
•Perform the following test only when directed.
Caution
•When foreign material, such as iron chips, gets on the CKP sensor, it can cause abnormal output
from the sensor because of flux turbulence and adversely affect engine control. Be sure there is
no foreign material on the CKP sensor when replacing.
•Do not forcefully pull the wiring harness of the CKP sensor. Doing so will break the harness.
Visual Inspection
1. Verify that the CKP sensor and the pulsar are free of any metallic shavings or particles.
•If any are found on the CKP sensor and the pulsar, clean them off.
Air Gap Inspection
1. Disconnect the negative battery cable.
2. Remove the crankshaft pulley. (See B2–9 TIMING BELT REMOVAL/INSTALLATION.)
3. Remove the crankshaft pulley. (See B2–9 TIMING BELT REMOVAL/INSTALLATION.)
4. Verify that clearance A between the CKP sensor
and the pulsar is within the specification.
•If not as specified, replace the CKP sensor.
Clearance A
1.5—2.5 mm {0.059—0.098 in}
Resistance Inspection
1. Disconnect the negative battery cable.
2. Disconnect the CKP sensor connector.
3. Measure the resistance between the CKP sensor
terminals under the following condition.
•If not as specified, replace the CKP sensor.
Specification
Circuit Open/Short Inspection
1. Inspect for open/short circuit in the following wiring harnesses.
•If there is open/short circuit, repair or replace wiring harnesses.
Open circuit
•CKP sensor terminal A and PCM terminal 29
•CKP sensor terminal B and PCM terminal 3
Short circuit
•CKP sensor terminal A and PCM terminal 29 to GND
•CKP sensor terminal B and PCM terminal 3 to GND
End Of Sie
TerminalAtmospheric
temperature °C {°F}Resistance (kilohm)
A—B 20 {68} 1.8—2.45
CLEARANCE A
A6E40702054
A
BC
A6E40702055
Page 237 of 909
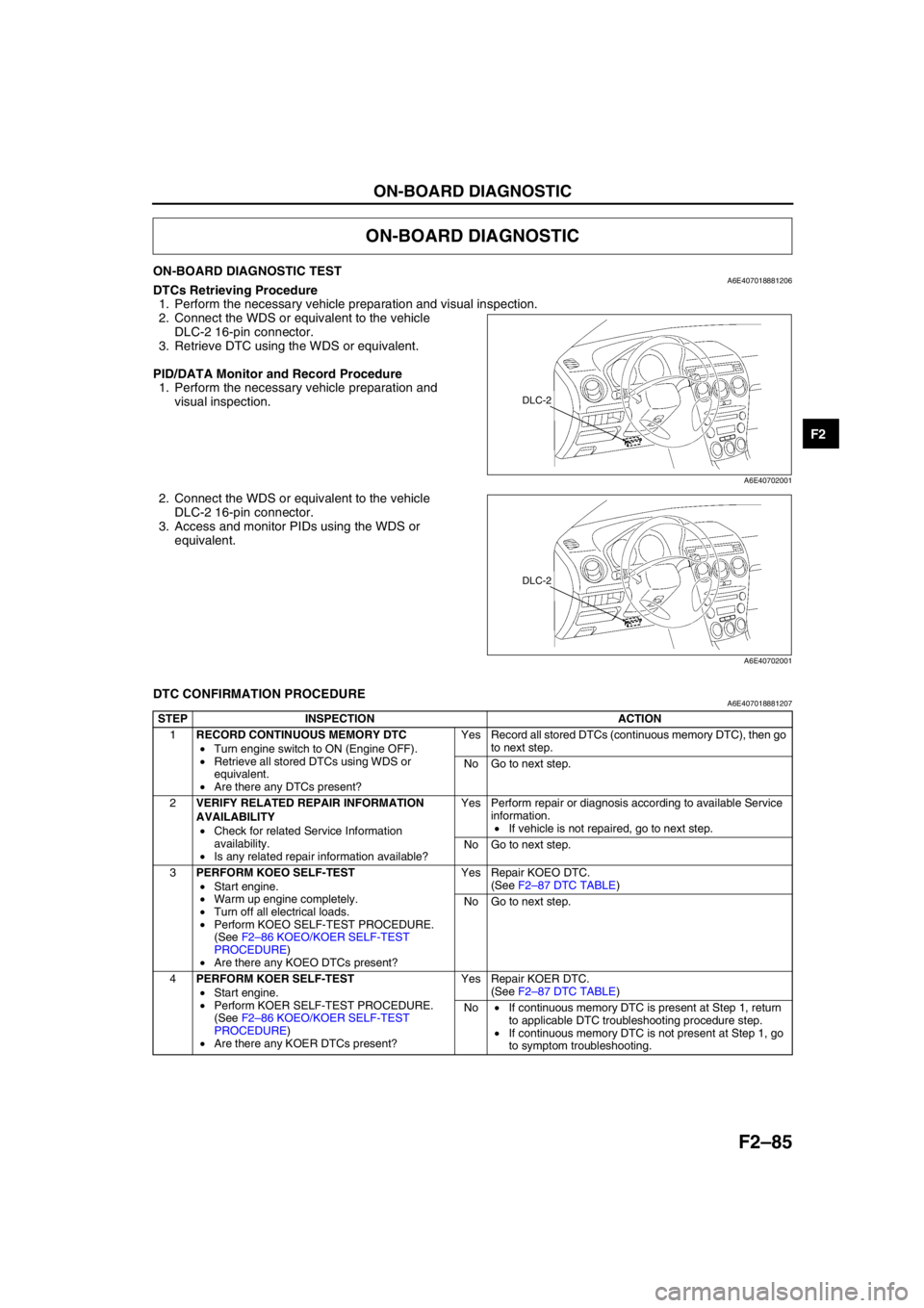
ON-BOARD DIAGNOSTIC
F2–85
F2
ON-BOARD DIAGNOSTIC TESTA6E407018881206DTCs Retrieving Procedure
1. Perform the necessary vehicle preparation and visual inspection.
2. Connect the WDS or equivalent to the vehicle
DLC-2 16-pin connector.
3. Retrieve DTC using the WDS or equivalent.
PID/DATA Monitor and Record Procedure
1. Perform the necessary vehicle preparation and
visual inspection.
2. Connect the WDS or equivalent to the vehicle
DLC-2 16-pin connector.
3. Access and monitor PIDs using the WDS or
equivalent.
End Of Sie
DTC CONFIRMATION PROCEDUREA6E407018881207
End Of Sie
ON-BOARD DIAGNOSTIC
DLC-2
A6E40702001
DLC-2
A6E40702001
STEP INSPECTION ACTION
1RECORD CONTINUOUS MEMORY DTC
•Turn engine switch to ON (Engine OFF).
•Retrieve all stored DTCs using WDS or
equivalent.
•Are there any DTCs present?Yes Record all stored DTCs (continuous memory DTC), then go
to next step.
No Go to next step.
2VERIFY RELATED REPAIR INFORMATION
AVAILABILITY
•Check for related Service Information
availability.
•Is any related repair information available?Yes Perform repair or diagnosis according to available Service
information.
•If vehicle is not repaired, go to next step.
No Go to next step.
3PERFORM KOEO SELF-TEST
•Start engine.
•Warm up engine completely.
•Turn off all electrical loads.
•Perform KOEO SELF-TEST PROCEDURE.
(See F2–86 KOEO/KOER SELF-TEST
PROCEDURE)
•Are there any KOEO DTCs present?Yes Repair KOEO DTC.
(See F2–87 DTC TABLE)
No Go to next step.
4PERFORM KOER SELF-TEST
•Start engine.
•Perform KOER SELF-TEST PROCEDURE.
(See F2–86 KOEO/KOER SELF-TEST
PROCEDURE)
•Are there any KOER DTCs present?Yes Repair KOER DTC.
(See F2–87 DTC TABLE)
No•If continuous memory DTC is present at Step 1, return
to applicable DTC troubleshooting procedure step.
•If continuous memory DTC is not present at Step 1, go
to symptom troubleshooting.
Page 238 of 909
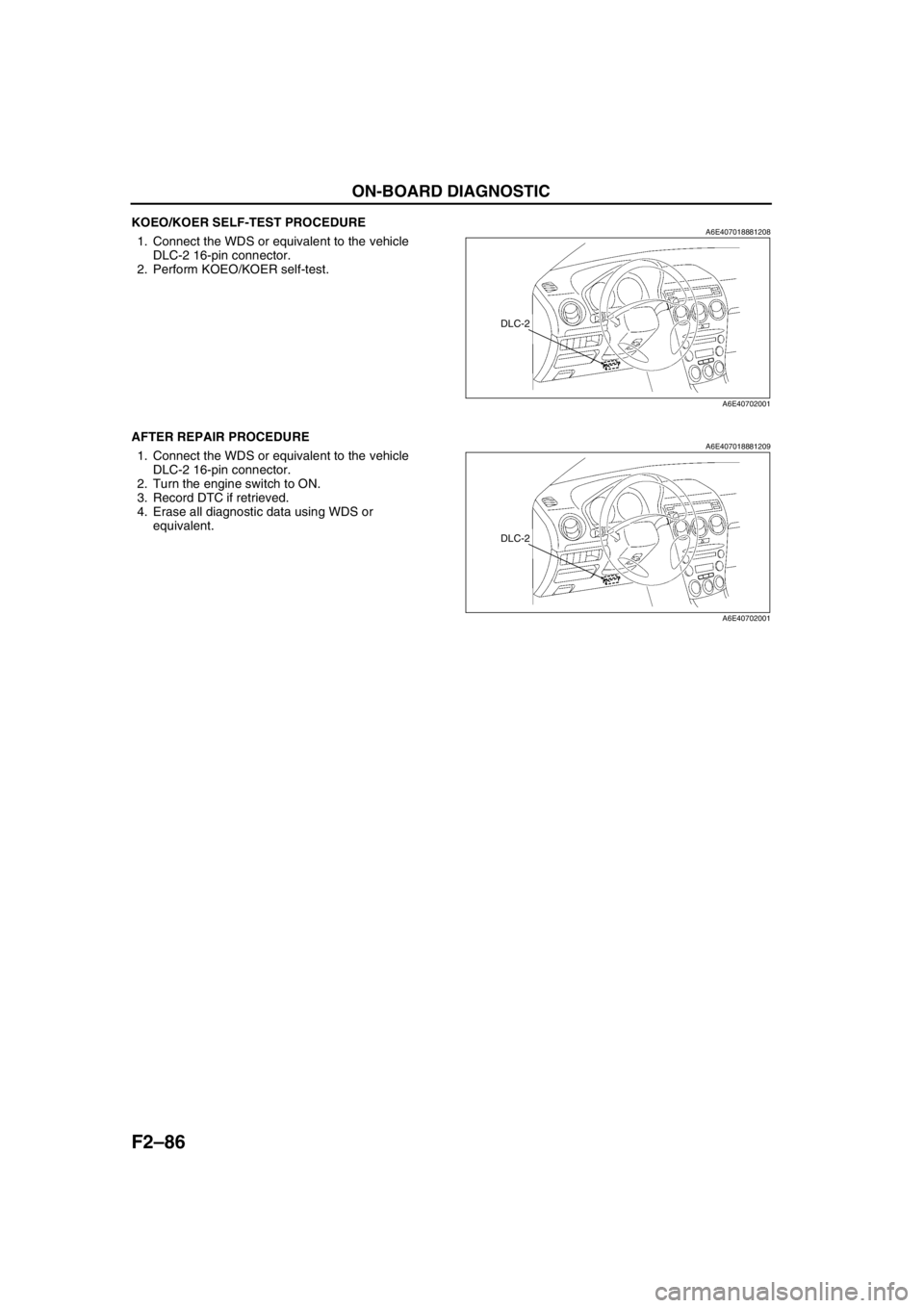
F2–86
ON-BOARD DIAGNOSTIC
KOEO/KOER SELF-TEST PROCEDUREA6E4070188812081. Connect the WDS or equivalent to the vehicle
DLC-2 16-pin connector.
2. Perform KOEO/KOER self-test.
End Of Sie
AFTER REPAIR PROCEDUREA6E4070188812091. Connect the WDS or equivalent to the vehicle
DLC-2 16-pin connector.
2. Turn the engine switch to ON.
3. Record DTC if retrieved.
4. Erase all diagnostic data using WDS or
equivalent.
DLC-2
A6E40702001
DLC-2
A6E40702001
Page 239 of 909
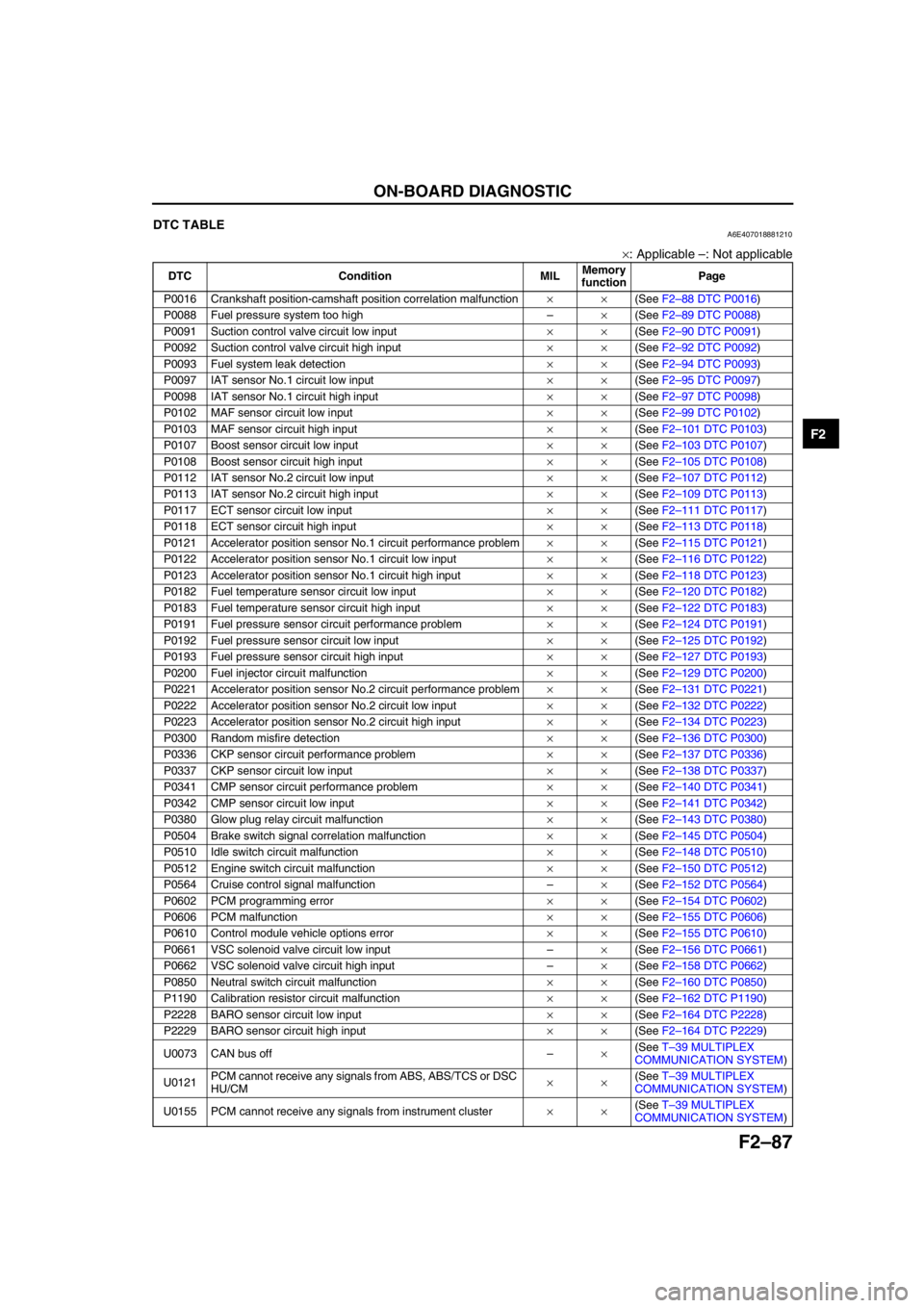
ON-BOARD DIAGNOSTIC
F2–87
F2
End Of SieDTC TABLEA6E407018881210
×: Applicable –: Not applicable
DTC Condition MILMemory
functionPage
P0016 Crankshaft position-camshaft position correlation malfunction××(See F2–88 DTC P0016)
P0088 Fuel pressure system too high–×(See F2–89 DTC P0088)
P0091 Suction control valve circuit low input××(See F2–90 DTC P0091)
P0092 Suction control valve circuit high input××(See F2–92 DTC P0092)
P0093 Fuel system leak detection××(See F2–94 DTC P0093)
P0097 IAT sensor No.1 circuit low input××(See F2–95 DTC P0097)
P0098 IAT sensor No.1 circuit high input××(See F2–97 DTC P0098)
P0102 MAF sensor circuit low input××(See F2–99 DTC P0102)
P0103 MAF sensor circuit high input××(See F2–101 DTC P0103)
P0107 Boost sensor circuit low input××(See F2–103 DTC P0107)
P0108 Boost sensor circuit high input××(See F2–105 DTC P0108)
P0112 IAT sensor No.2 circuit low input××(See F2–107 DTC P0112)
P0113 IAT sensor No.2 circuit high input××(See F2–109 DTC P0113)
P0117 ECT sensor circuit low input××(See F2–111 DTC P0117)
P0118 ECT sensor circuit high input××(See F2–113 DTC P0118)
P0121 Accelerator position sensor No.1 circuit performance problem××(See F2–115 DTC P0121)
P0122 Accelerator position sensor No.1 circuit low input××(See F2–116 DTC P0122)
P0123 Accelerator position sensor No.1 circuit high input××(See F2–118 DTC P0123)
P0182 Fuel temperature sensor circuit low input××(See F2–120 DTC P0182)
P0183 Fuel temperature sensor circuit high input××(See F2–122 DTC P0183)
P0191 Fuel pressure sensor circuit performance problem××(See F2–124 DTC P0191)
P0192 Fuel pressure sensor circuit low input××(See F2–125 DTC P0192)
P0193 Fuel pressure sensor circuit high input××(See F2–127 DTC P0193)
P0200 Fuel injector circuit malfunction××(See F2–129 DTC P0200)
P0221 Accelerator position sensor No.2 circuit performance problem××(See F2–131 DTC P0221)
P0222 Accelerator position sensor No.2 circuit low input××(See F2–132 DTC P0222)
P0223 Accelerator position sensor No.2 circuit high input××(See F2–134 DTC P0223)
P0300 Random misfire detection××(See F2–136 DTC P0300)
P0336 CKP sensor circuit performance problem××(See F2–137 DTC P0336)
P0337 CKP sensor circuit low input××(See F2–138 DTC P0337)
P0341 CMP sensor circuit performance problem××(See F2–140 DTC P0341)
P0342 CMP sensor circuit low input××(See F2–141 DTC P0342)
P0380 Glow plug relay circuit malfunction××(See F2–143 DTC P0380)
P0504 Brake switch signal correlation malfunction××(See F2–145 DTC P0504)
P0510 Idle switch circuit malfunction××(See F2–148 DTC P0510)
P0512 Engine switch circuit malfunction××(See F2–150 DTC P0512)
P0564 Cruise control signal malfunction–×(See F2–152 DTC P0564)
P0602 PCM programming error××(See F2–154 DTC P0602)
P0606 PCM malfunction××(See F2–155 DTC P0606)
P0610 Control module vehicle options error××(See F2–155 DTC P0610)
P0661 VSC solenoid valve circuit low input–×(See F2–156 DTC P0661)
P0662 VSC solenoid valve circuit high input–×(See F2–158 DTC P0662)
P0850 Neutral switch circuit malfunction××(See F2–160 DTC P0850)
P1190 Calibration resistor circuit malfunction××(See F2–162 DTC P1190)
P2228 BARO sensor circuit low input××(See F2–164 DTC P2228)
P2229 BARO sensor circuit high input××(See F2–164 DTC P2229)
U0073 CAN bus off–×(See T–39 MULTIPLEX
COMMUNICATION SYSTEM)
U0121PCM cannot receive any signals from ABS, ABS/TCS or DSC
HU/CM××(See T–39 MULTIPLEX
COMMUNICATION SYSTEM)
U0155 PCM cannot receive any signals from instrument cluster××(See T–39 MULTIPLEX
COMMUNICATION SYSTEM)
Page 240 of 909
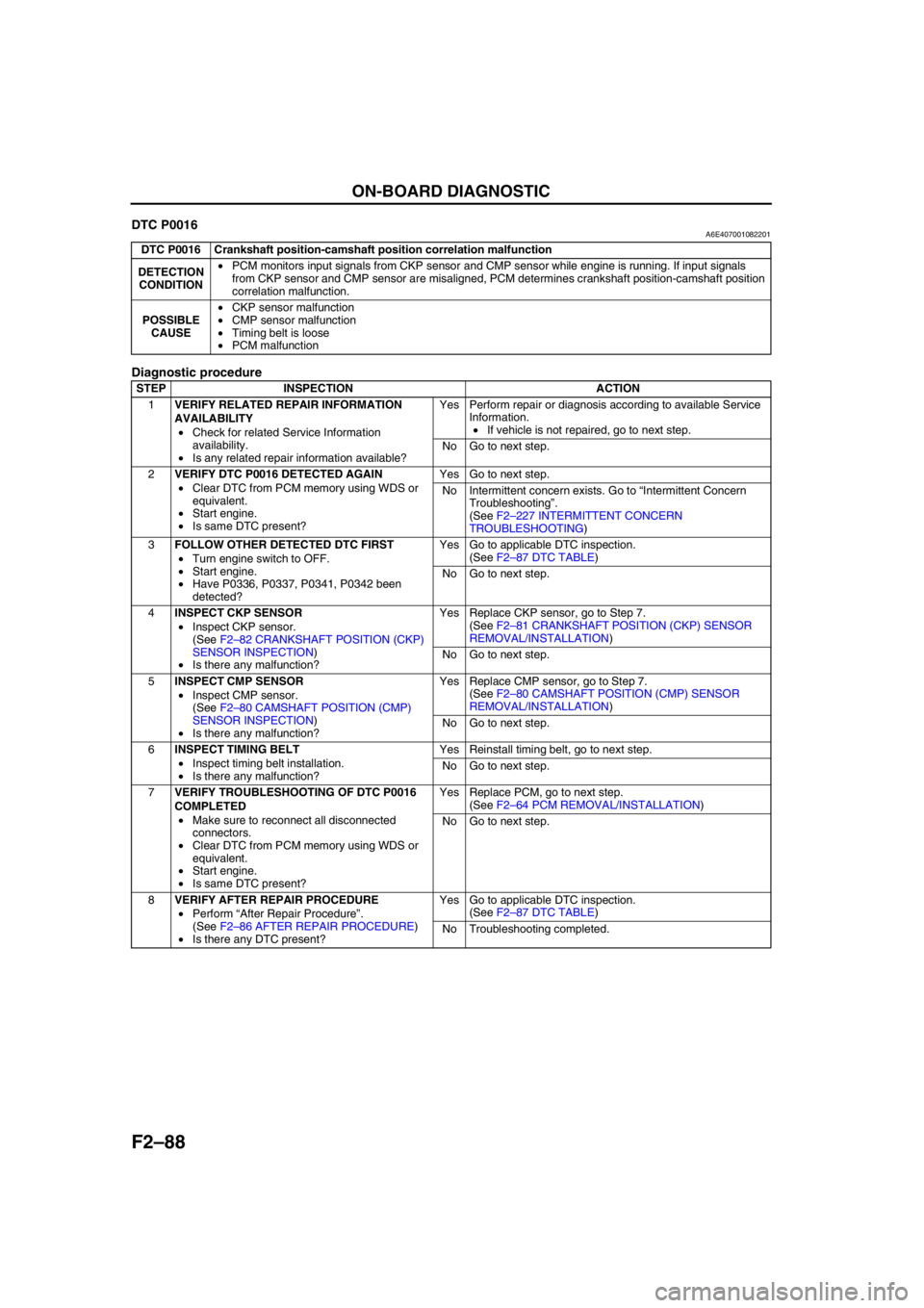
F2–88
ON-BOARD DIAGNOSTIC
End Of SieDTC P0016A6E407001082201
Diagnostic procedure
End Of Sie
DTC P0016 Crankshaft position-camshaft position correlation malfunction
DETECTION
CONDITION•PCM monitors input signals from CKP sensor and CMP sensor while engine is running. If input signals
from CKP sensor and CMP sensor are misaligned, PCM determines crankshaft position-camshaft position
correlation malfunction.
POSSIBLE
CAUSE•CKP sensor malfunction
•CMP sensor malfunction
•Timing belt is loose
•PCM malfunction
STEP INSPECTION ACTION
1VERIFY RELATED REPAIR INFORMATION
AVAILABILITY
•Check for related Service Information
availability.
•Is any related repair information available?Yes Perform repair or diagnosis according to available Service
Information.
•If vehicle is not repaired, go to next step.
No Go to next step.
2VERIFY DTC P0016 DETECTED AGAIN
•Clear DTC from PCM memory using WDS or
equivalent.
•Start engine.
•Is same DTC present?Yes Go to next step.
No Intermittent concern exists. Go to “Intermittent Concern
Troubleshooting”.
(See F2–227 INTERMITTENT CONCERN
TROUBLESHOOTING)
3FOLLOW OTHER DETECTED DTC FIRST
•Turn engine switch to OFF.
•Start engine.
•Have P0336, P0337, P0341, P0342 been
detected?Yes Go to applicable DTC inspection.
(See F2–87 DTC TABLE)
No Go to next step.
4INSPECT CKP SENSOR
•Inspect CKP sensor.
(See F2–82 CRANKSHAFT POSITION (CKP)
SENSOR INSPECTION)
•Is there any malfunction?Yes Replace CKP sensor, go to Step 7.
(See F2–81 CRANKSHAFT POSITION (CKP) SENSOR
REMOVAL/INSTALLATION)
No Go to next step.
5INSPECT CMP SENSOR
•Inspect CMP sensor.
(See F2–80 CAMSHAFT POSITION (CMP)
SENSOR INSPECTION)
•Is there any malfunction?Yes Replace CMP sensor, go to Step 7.
(See F2–80 CAMSHAFT POSITION (CMP) SENSOR
REMOVAL/INSTALLATION)
No Go to next step.
6INSPECT TIMING BELT
•Inspect timing belt installation.
•Is there any malfunction?Yes Reinstall timing belt, go to next step.
No Go to next step.
7VERIFY TROUBLESHOOTING OF DTC P0016
COMPLETED
•Make sure to reconnect all disconnected
connectors.
•Clear DTC from PCM memory using WDS or
equivalent.
•Start engine.
•Is same DTC present?Yes Replace PCM, go to next step.
(See F2–64 PCM REMOVAL/INSTALLATION)
No Go to next step.
8VERIFY AFTER REPAIR PROCEDURE
•Perform “After Repair Procedure”.
(See F2–86 AFTER REPAIR PROCEDURE)
•Is there any DTC present?Yes Go to applicable DTC inspection.
(See F2–87 DTC TABLE)
No Troubleshooting completed.
Page 241 of 909
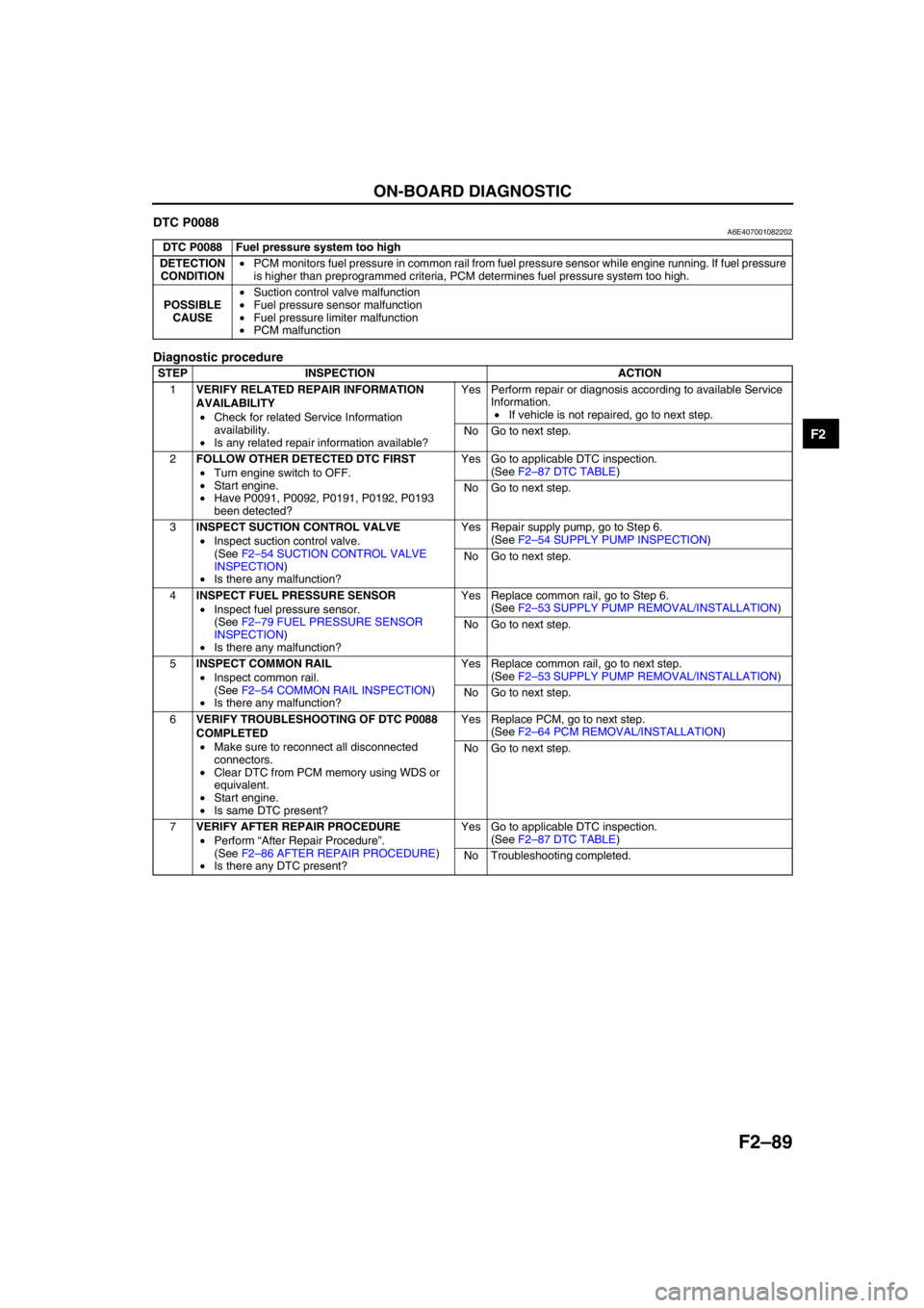
ON-BOARD DIAGNOSTIC
F2–89
F2
DTC P0088A6E407001082202
Diagnostic procedure
End Of Sie
DTC P0088 Fuel pressure system too high
DETECTION
CONDITION•PCM monitors fuel pressure in common rail from fuel pressure sensor while engine running. If fuel pressure
is higher than preprogrammed criteria, PCM determines fuel pressure system too high.
POSSIBLE
CAUSE•Suction control valve malfunction
•Fuel pressure sensor malfunction
•Fuel pressure limiter malfunction
•PCM malfunction
STEP INSPECTION ACTION
1VERIFY RELATED REPAIR INFORMATION
AVAILABILITY
•Check for related Service Information
availability.
•Is any related repair information available?Yes Perform repair or diagnosis according to available Service
Information.
•If vehicle is not repaired, go to next step.
No Go to next step.
2FOLLOW OTHER DETECTED DTC FIRST
•Turn engine switch to OFF.
•Start engine.
•Have P0091, P0092, P0191, P0192, P0193
been detected?Yes Go to applicable DTC inspection.
(See F2–87 DTC TABLE)
No Go to next step.
3INSPECT SUCTION CONTROL VALVE
•Inspect suction control valve.
(See F2–54 SUCTION CONTROL VALVE
INSPECTION)
•Is there any malfunction?Yes Repair supply pump, go to Step 6.
(See F2–54 SUPPLY PUMP INSPECTION)
No Go to next step.
4INSPECT FUEL PRESSURE SENSOR
•Inspect fuel pressure sensor.
(See F2–79 FUEL PRESSURE SENSOR
INSPECTION)
•Is there any malfunction?Yes Replace common rail, go to Step 6.
(See F2–53 SUPPLY PUMP REMOVAL/INSTALLATION)
No Go to next step.
5INSPECT COMMON RAIL
•Inspect common rail.
(See F2–54 COMMON RAIL INSPECTION)
•Is there any malfunction?Yes Replace common rail, go to next step.
(See F2–53 SUPPLY PUMP REMOVAL/INSTALLATION)
No Go to next step.
6VERIFY TROUBLESHOOTING OF DTC P0088
COMPLETED
•Make sure to reconnect all disconnected
connectors.
•Clear DTC from PCM memory using WDS or
equivalent.
•Start engine.
•Is same DTC present?Yes Replace PCM, go to next step.
(See F2–64 PCM REMOVAL/INSTALLATION)
No Go to next step.
7VERIFY AFTER REPAIR PROCEDURE
•Perform “After Repair Procedure”.
(See F2–86 AFTER REPAIR PROCEDURE)
•Is there any DTC present?Yes Go to applicable DTC inspection.
(See F2–87 DTC TABLE)
No Troubleshooting completed.