engine MAZDA 6 2002 Workshop Manual Suplement
[x] Cancel search | Manufacturer: MAZDA, Model Year: 2002, Model line: 6, Model: MAZDA 6 2002Pages: 909, PDF Size: 17.16 MB
Page 181 of 909
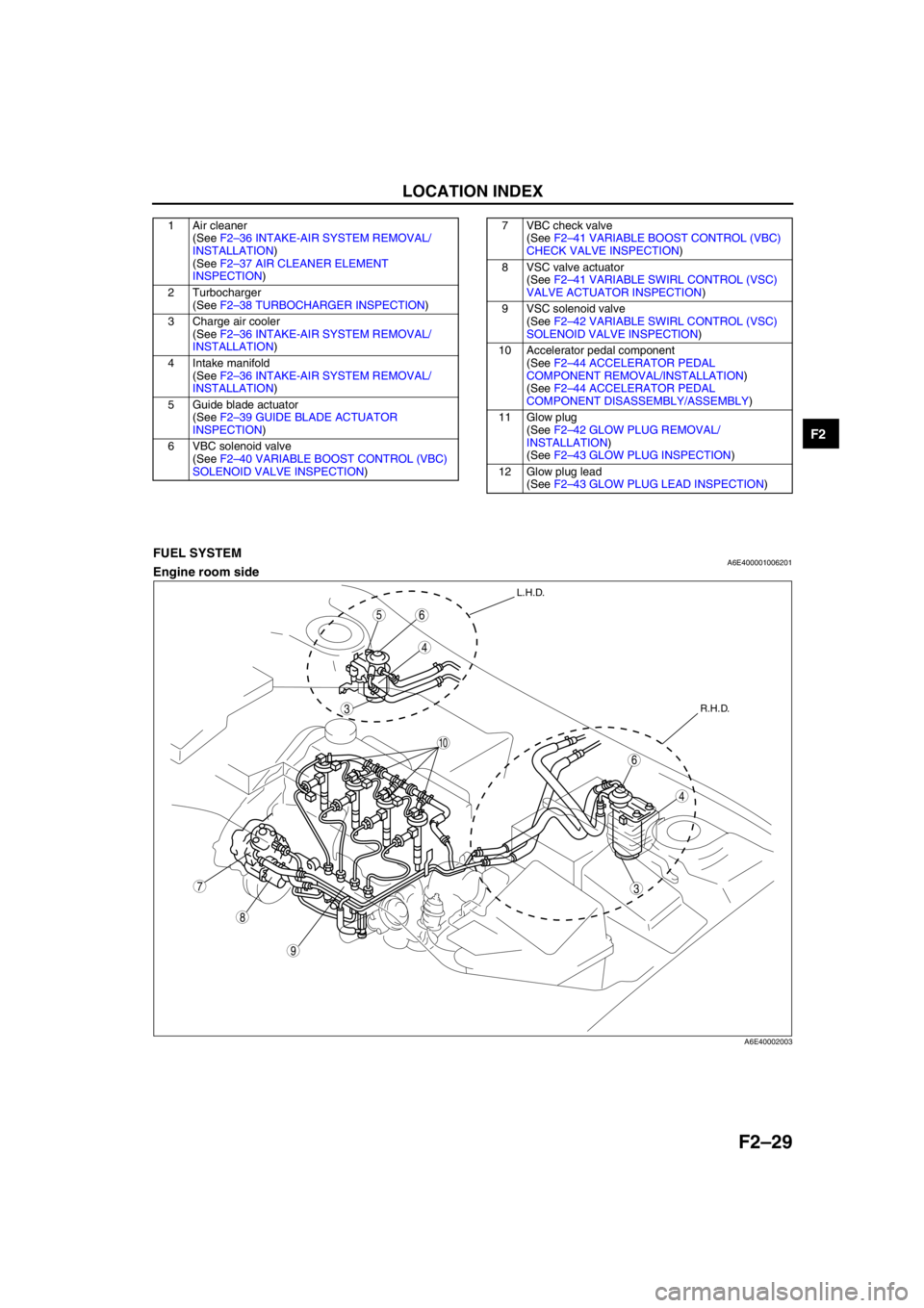
LOCATION INDEX
F2–29
F2
End Of Sie
FUEL SYSTEMA6E400001006201Engine room side
1 Air cleaner
(See F2–36 INTAKE-AIR SYSTEM REMOVAL/
INSTALLATION)
(See F2–37 AIR CLEANER ELEMENT
INSPECTION)
2 Turbocharger
(See F2–38 TURBOCHARGER INSPECTION)
3 Charge air cooler
(See F2–36 INTAKE-AIR SYSTEM REMOVAL/
INSTALLATION)
4 Intake manifold
(See F2–36 INTAKE-AIR SYSTEM REMOVAL/
INSTALLATION)
5 Guide blade actuator
(See F2–39 GUIDE BLADE ACTUATOR
INSPECTION)
6 VBC solenoid valve
(See F2–40 VARIABLE BOOST CONTROL (VBC)
SOLENOID VALVE INSPECTION)7 VBC check valve
(See F2–41 VARIABLE BOOST CONTROL (VBC)
CHECK VALVE INSPECTION)
8 VSC valve actuator
(See F2–41 VARIABLE SWIRL CONTROL (VSC)
VALVE ACTUATOR INSPECTION)
9 VSC solenoid valve
(See F2–42 VARIABLE SWIRL CONTROL (VSC)
SOLENOID VALVE INSPECTION)
10 Accelerator pedal component
(See F2–44 ACCELERATOR PEDAL
COMPONENT REMOVAL/INSTALLATION)
(See F2–44 ACCELERATOR PEDAL
COMPONENT DISASSEMBLY/ASSEMBLY)
11 Glow plug
(See F2–42 GLOW PLUG REMOVAL/
INSTALLATION)
(See F2–43 GLOW PLUG INSPECTION)
12 Glow plug lead
(See F2–43 GLOW PLUG LEAD INSPECTION)
9
8
7
5
4
3
6
10
6
4
3
L.H.D.
R.H.D.
A6E40002003
Page 185 of 909
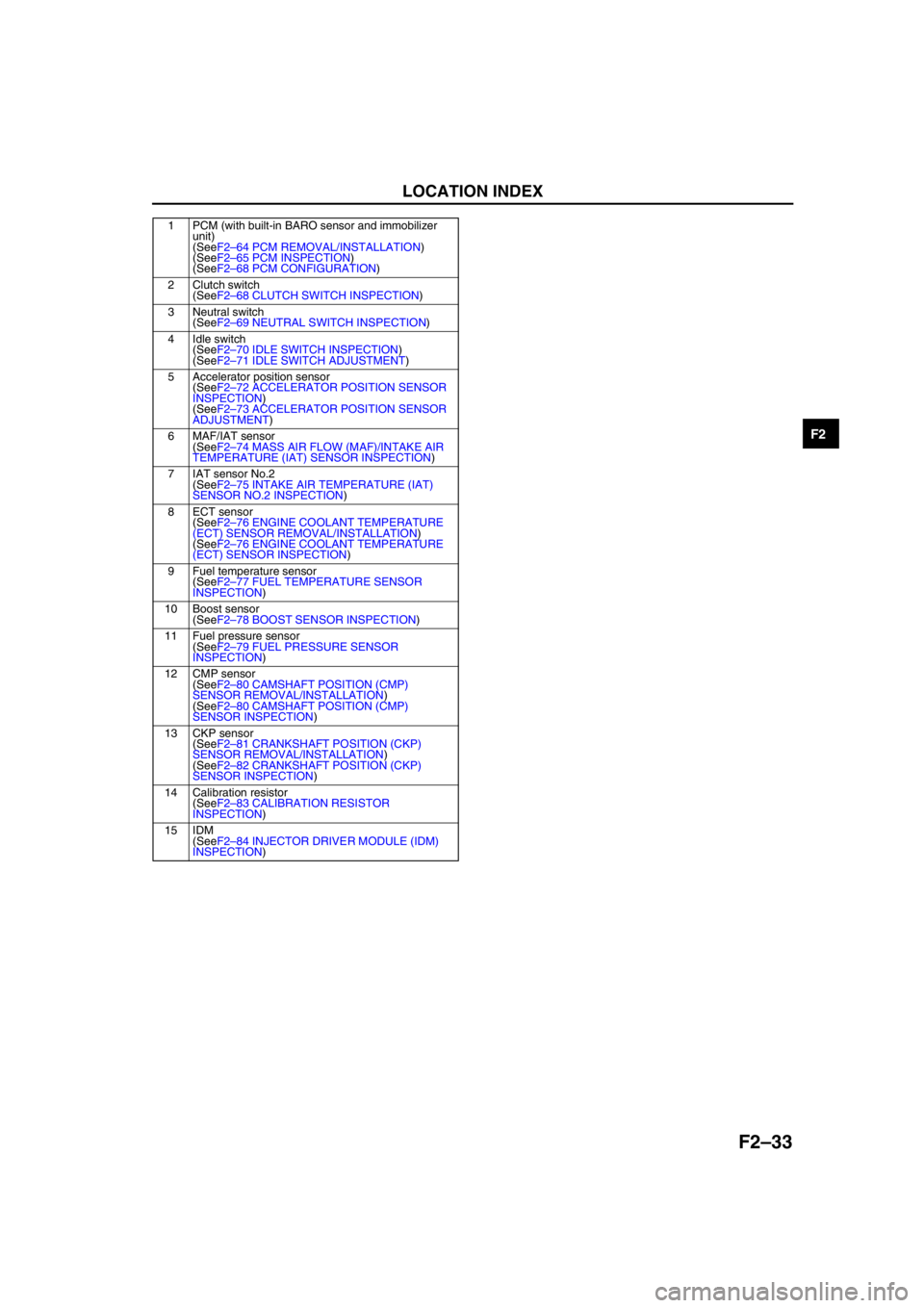
LOCATION INDEX
F2–33
F2
End Of Sie
1 PCM (with built-in BARO sensor and immobilizer
unit)
(SeeF2–64 PCM REMOVAL/INSTALLATION)
(SeeF2–65 PCM INSPECTION)
(SeeF2–68 PCM CONFIGURATION)
2 Clutch switch
(SeeF2–68 CLUTCH SWITCH INSPECTION)
3 Neutral switch
(SeeF2–69 NEUTRAL SWITCH INSPECTION)
4 Idle switch
(SeeF2–70 IDLE SWITCH INSPECTION)
(SeeF2–71 IDLE SWITCH ADJUSTMENT)
5 Accelerator position sensor
(SeeF2–72 ACCELERATOR POSITION SENSOR
INSPECTION)
(SeeF2–73 ACCELERATOR POSITION SENSOR
ADJUSTMENT)
6 MAF/IAT sensor
(SeeF2–74 MASS AIR FLOW (MAF)/INTAKE AIR
TEMPERATURE (IAT) SENSOR INSPECTION)
7 IAT sensor No.2
(SeeF2–75 INTAKE AIR TEMPERATURE (IAT)
SENSOR NO.2 INSPECTION)
8ECT sensor
(SeeF2–76 ENGINE COOLANT TEMPERATURE
(ECT) SENSOR REMOVAL/INSTALLATION)
(SeeF2–76 ENGINE COOLANT TEMPERATURE
(ECT) SENSOR INSPECTION)
9 Fuel temperature sensor
(SeeF2–77 FUEL TEMPERATURE SENSOR
INSPECTION)
10 Boost sensor
(SeeF2–78 BOOST SENSOR INSPECTION)
11 Fuel pressure sensor
(SeeF2–79 FUEL PRESSURE SENSOR
INSPECTION)
12 CMP sensor
(SeeF2–80 CAMSHAFT POSITION (CMP)
SENSOR REMOVAL/INSTALLATION)
(SeeF2–80 CAMSHAFT POSITION (CMP)
SENSOR INSPECTION)
13 CKP sensor
(SeeF2–81 CRANKSHAFT POSITION (CKP)
SENSOR REMOVAL/INSTALLATION)
(SeeF2–82 CRANKSHAFT POSITION (CKP)
SENSOR INSPECTION)
14 Calibration resistor
(SeeF2–83 CALIBRATION RESISTOR
INSPECTION)
15 IDM
(SeeF2–84 INJECTOR DRIVER MODULE (IDM)
INSPECTION)
Page 186 of 909
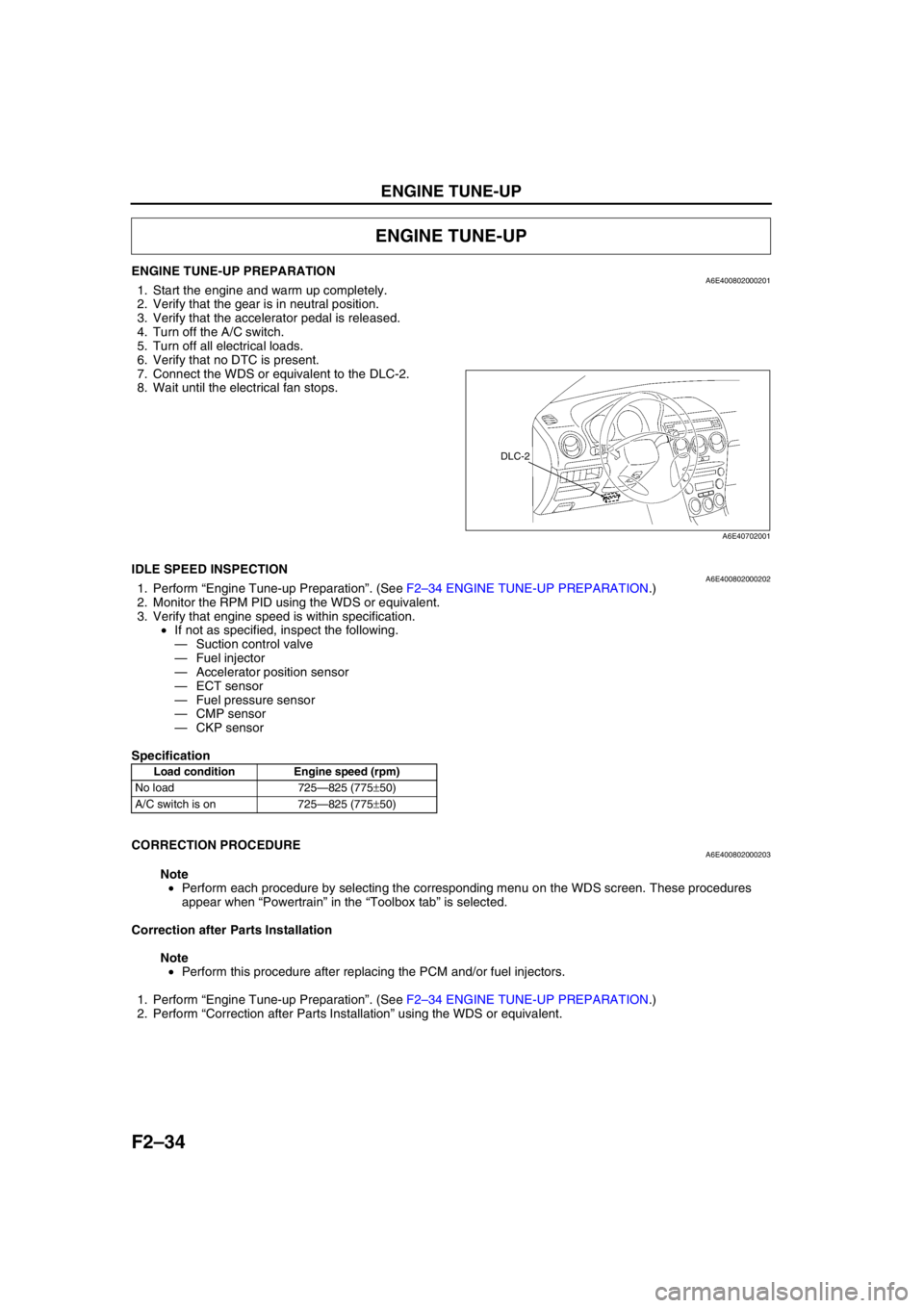
F2–34
ENGINE TUNE-UP
ENGINE TUNE-UP PREPARATIONA6E4008020002011. Start the engine and warm up completely.
2. Verify that the gear is in neutral position.
3. Verify that the accelerator pedal is released.
4. Turn off the A/C switch.
5. Turn off all electrical loads.
6. Verify that no DTC is present.
7. Connect the WDS or equivalent to the DLC-2.
8. Wait until the electrical fan stops.
End Of Sie
IDLE SPEED INSPECTIONA6E4008020002021. Perform “Engine Tune-up Preparation”. (See F2–34 ENGINE TUNE-UP PREPARATION.)
2. Monitor the RPM PID using the WDS or equivalent.
3. Verify that engine speed is within specification.
•If not as specified, inspect the following.
—Suction control valve
—Fuel injector
—Accelerator position sensor
—ECT sensor
—Fuel pressure sensor
—CMP sensor
—CKP sensor
Specification
End Of Sie
CORRECTION PROCEDUREA6E400802000203
Note
•Perform each procedure by selecting the corresponding menu on the WDS screen. These procedures
appear when “Powertrain” in the “Toolbox tab” is selected.
Correction after Parts Installation
Note
•Perform this procedure after replacing the PCM and/or fuel injectors.
1. Perform “Engine Tune-up Preparation”. (See F2–34 ENGINE TUNE-UP PREPARATION.)
2. Perform “Correction after Parts Installation” using the WDS or equivalent.
ENGINE TUNE-UP
DLC-2
A6E40702001
Load condition Engine speed (rpm)
No load 725—825 (775±50)
A/C switch is on 725—825 (775±50)
Page 187 of 909
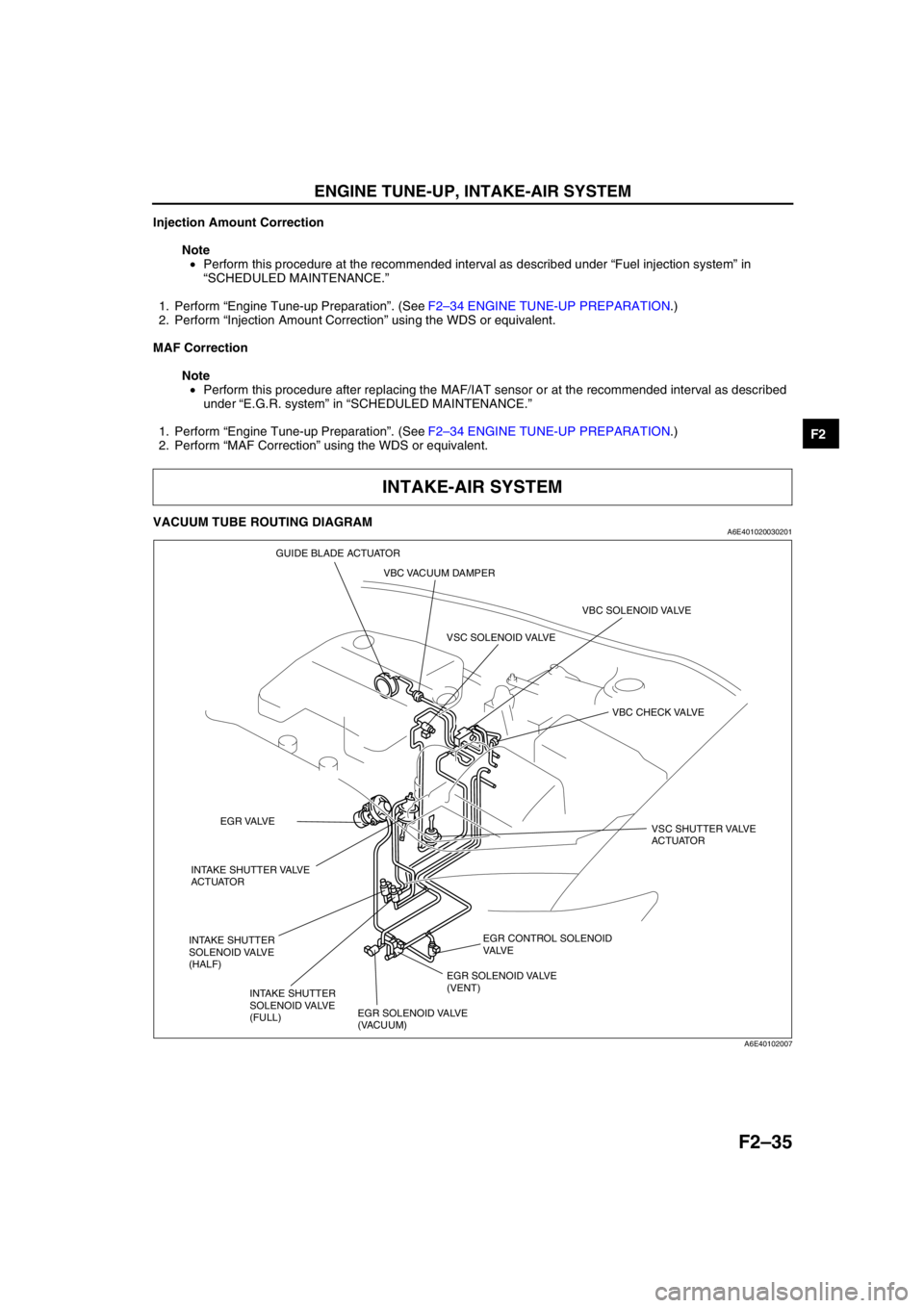
ENGINE TUNE-UP, INTAKE-AIR SYSTEM
F2–35
F2
Injection Amount Correction
Note
•Perform this procedure at the recommended interval as described under “Fuel injection system” in
“SCHEDULED MAINTENANCE.”
1. Perform “Engine Tune-up Preparation”. (See F2–34 ENGINE TUNE-UP PREPARATION.)
2. Perform “Injection Amount Correction” using the WDS or equivalent.
MAF Correction
Note
•Perform this procedure after replacing the MAF/IAT sensor or at the recommended interval as described
under “E.G.R. system” in “SCHEDULED MAINTENANCE.”
1. Perform “Engine Tune-up Preparation”. (See F2–34 ENGINE TUNE-UP PREPARATION.)
2. Perform “MAF Correction” using the WDS or equivalent.
End Of Sie
VACUUM TUBE ROUTING DIAGRAMA6E401020030201
End Of Sie
INTAKE-AIR SYSTEM
EGR CONTROL SOLENOID
VA LV E
VBC SOLENOID VALVE
VBC CHECK VALVE
EGR SOLENOID VALVE
(VACUUM)EGR SOLENOID VALVE
(VENT) VSC SOLENOID VALVE
VSC SHUTTER VALVE
ACTUATOR
INTAKE SHUTTER VALVE
ACTUATOREGR VALVE
INTAKE SHUTTER
SOLENOID VALVE
(HALF)
INTAKE SHUTTER
SOLENOID VALVE
(FULL)VBC VACUUM DAMPER GUIDE BLADE ACTUATOR
A6E40102007
Page 188 of 909
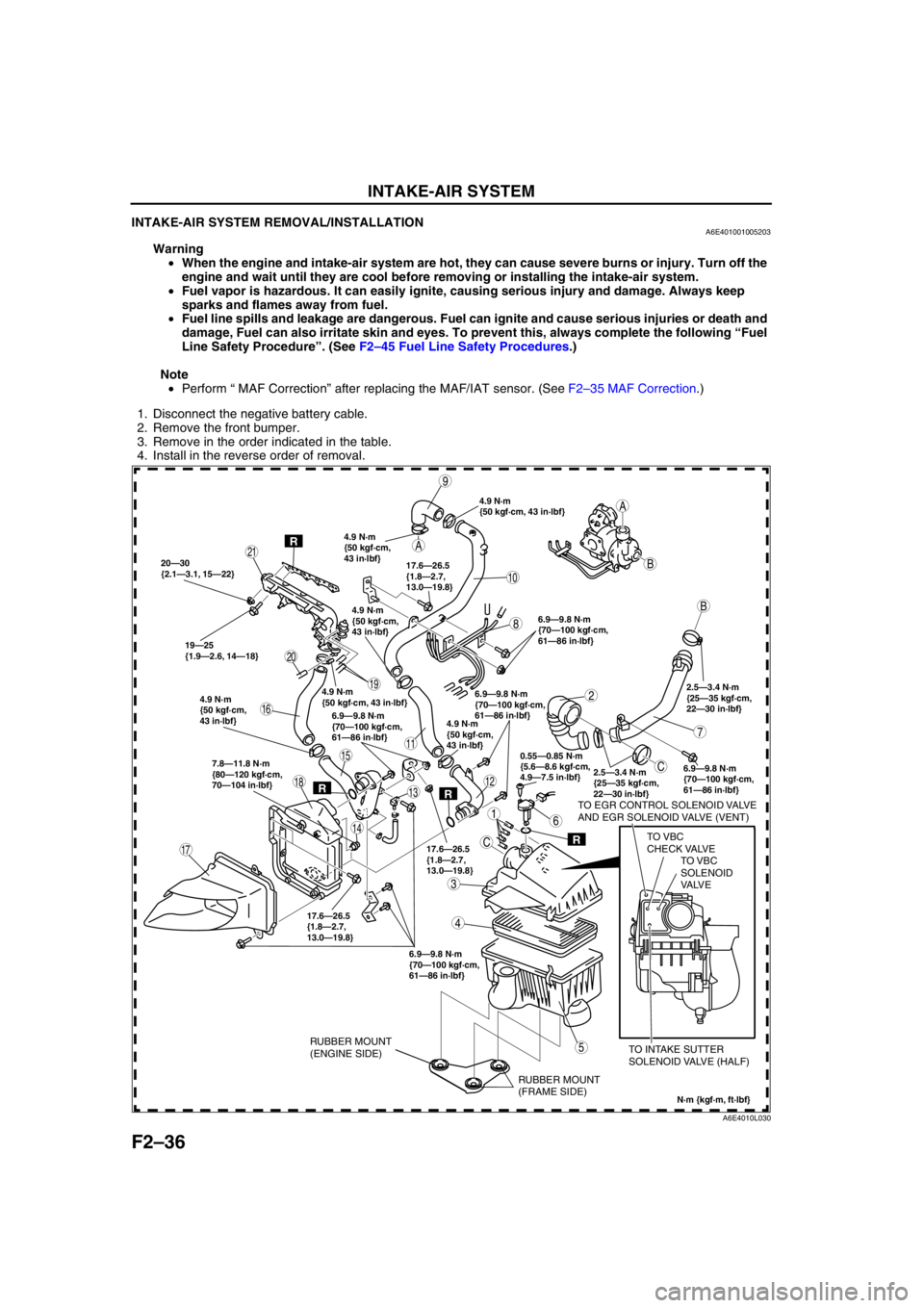
F2–36
INTAKE-AIR SYSTEM
INTAKE-AIR SYSTEM REMOVAL/INSTALLATIONA6E401001005203
Warning
•When the engine and intake-air system are hot, they can cause severe burns or injury. Turn off the
engine and wait until they are cool before removing or installing the intake-air system.
•Fuel vapor is hazardous. It can easily ignite, causing serious injury and damage. Always keep
sparks and flames away from fuel.
•Fuel line spills and leakage are dangerous. Fuel can ignite and cause serious injuries or death and
damage, Fuel can also irritate skin and eyes. To prevent this, always complete the following “Fuel
Line Safety Procedure”. (See F2–45 Fuel Line Safety Procedures.)
Note
•Perform “ MAF Correction” after replacing the MAF/IAT sensor. (See F2–35 MAF Correction.)
1. Disconnect the negative battery cable.
2. Remove the front bumper.
3. Remove in the order indicated in the table.
4. Install in the reverse order of removal.
.
A
A
C
C
B
B
20—30
{2.1—3.1, 15—22}
19—25
{1.9—2.6, 14—18}6.9—9.8 N·m
{70—100 kgf·cm,
61—86 in·lbf}
2.5—3.4 N·m
{25—35 kgf·cm,
22—30 in·lbf}
6.9—9.8 N·m
{70—100 kgf·cm,
61—86 in·lbf} 7.8—11.8 N·m
{80—120 kgf·cm,
70—104 in·lbf}
6.9—9.8 N·m
{70—100 kgf·cm,
61—86 in·lbf} 17.6—26.5
{1.8—2.7,
13.0—19.8}6.9—9.8 N·m
{70—100 kgf·cm,
61—86 in·lbf}
6.9—9.8 N·m
{70—100 kgf·cm,
61—86 in·lbf}
2.5—3.4 N·m
{25—35 kgf·cm,
22—30 in·lbf}
TO EGR CONTROL SOLENOID VALVE
AND EGR SOLENOID VALVE (VENT)
TO VBC
CHECK VALVE
TO INTAKE SUTTER
SOLENOID VALVE (HALF)
9
10
19
17
11
20
21
1
2
3
5
4
7
6
8
12
14
13
15
16
18
0.55—0.85 N·m
{5.6—8.6 kgf·cm,
4.9—7.5 in·lbf}
N·m {kgf·m, ft·lbf}
R
RR
R
17.6—26.5
{1.8—2.7,
13.0—19.8}17.6—26.5
{1.8—2.7,
13.0—19.8}
4.9 N·m
{50 kgf·cm, 43 in·lbf}
4.9 N·m
{50 kgf·cm,
43 in·lbf}
4.9 N·m
{50 kgf·cm, 43 in·lbf}4.9 N·m
{50 kgf·cm,
43 in·lbf}
4.9 N·m
{50 kgf·cm,
43 in·lbf}
4.9 N·m
{50 kgf·cm,
43 in·lbf}
RUBBER MOUNT
(FRAME SIDE) RUBBER MOUNT
(ENGINE SIDE)
TO VBC
SOLENOID
VA LV E
A6E4010L030
Page 189 of 909
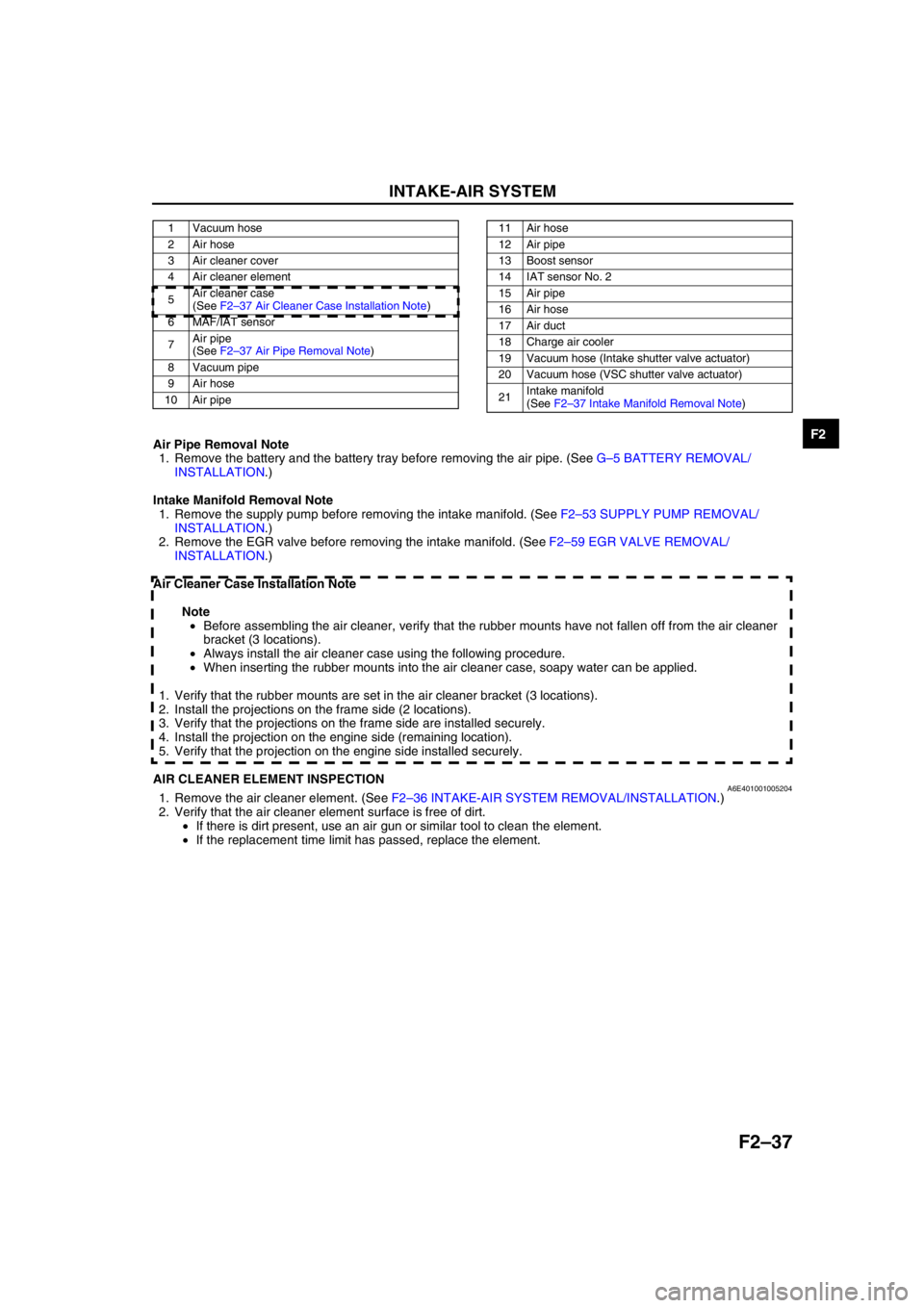
INTAKE-AIR SYSTEM
F2–37
F2Air Pipe Removal Note
1. Remove the battery and the battery tray before removing the air pipe. (See G–5 BATTERY REMOVAL/
INSTALLATION.)
Intake Manifold Removal Note
1. Remove the supply pump before removing the intake manifold. (See F2–53 SUPPLY PUMP REMOVAL/
INSTALLATION.)
2. Remove the EGR valve before removing the intake manifold. (See F2–59 EGR VALVE REMOVAL/
INSTALLATION.)
Air Cleaner Case Installation Note
Note
•Before assembling the air cleaner, verify that the rubber mounts have not fallen off from the air cleaner
bracket (3 locations).
•Always install the air cleaner case using the following procedure.
•When inserting the rubber mounts into the air cleaner case, soapy water can be applied.
1. Verify that the rubber mounts are set in the air cleaner bracket (3 locations).
2. Install the projections on the frame side (2 locations).
3. Verify that the projections on the frame side are installed securely.
4. Install the projection on the engine side (remaining location).
5. Verify that the projection on the engine side installed securely.
End Of Sie
AIR CLEANER ELEMENT INSPECTIONA6E4010010052041. Remove the air cleaner element. (See F2–36 INTAKE-AIR SYSTEM REMOVAL/INSTALLATION.)
2. Verify that the air cleaner element surface is free of dirt.
•If there is dirt present, use an air gun or similar tool to clean the element.
•If the replacement time limit has passed, replace the element.
End Of Sie
1 Vacuum hose
2 Air hose
3 Air cleaner cover
4 Air cleaner element
5Air cleaner case
(See F2–37 Air Cleaner Case Installation Note)
6 MAF/IAT sensor
7Air pipe
(See F2–37 Air Pipe Removal Note)
8 Vacuum pipe
9 Air hose
10 Air pipe11 Air hose
12 Air pipe
13 Boost sensor
14 IAT sensor No. 2
15 Air pipe
16 Air hose
17 Air duct
18 Charge air cooler
19 Vacuum hose (Intake shutter valve actuator)
20 Vacuum hose (VSC shutter valve actuator)
21Intake manifold
(See F2–37 Intake Manifold Removal Note)
Page 190 of 909
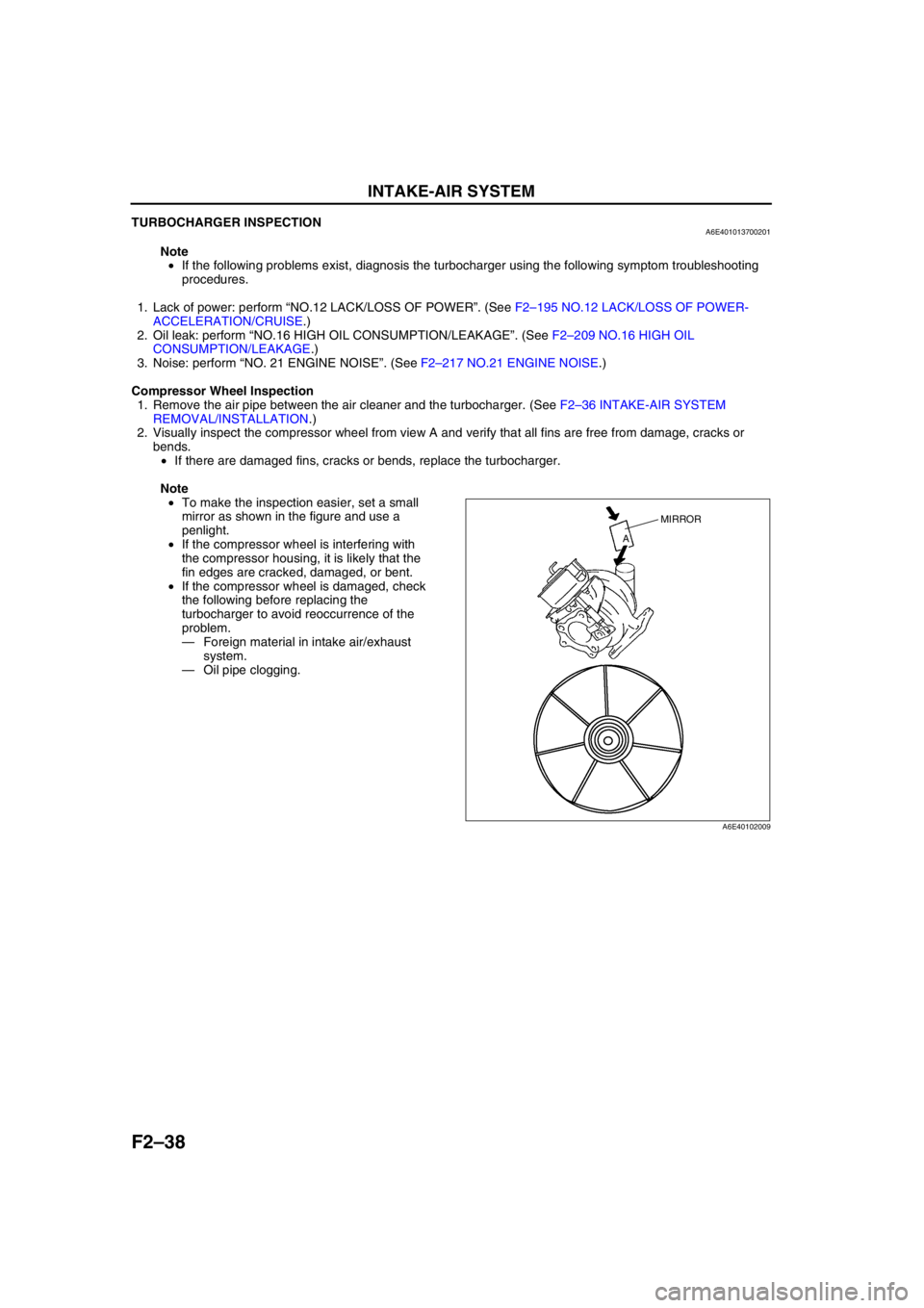
F2–38
INTAKE-AIR SYSTEM
TURBOCHARGER INSPECTIONA6E401013700201
Note
•If the following problems exist, diagnosis the turbocharger using the following symptom troubleshooting
procedures.
1. Lack of power: perform “NO.12 LACK/LOSS OF POWER”. (See F2–195 NO.12 LACK/LOSS OF POWER-
ACCELERATION/CRUISE.)
2. Oil leak: perform “NO.16 HIGH OIL CONSUMPTION/LEAKAGE”. (See F2–209 NO.16 HIGH OIL
CONSUMPTION/LEAKAGE.)
3. Noise: perform “NO. 21 ENGINE NOISE”. (See F2–217 NO.21 ENGINE NOISE.)
Compressor Wheel Inspection
1. Remove the air pipe between the air cleaner and the turbocharger. (See F2–36 INTAKE-AIR SYSTEM
REMOVAL/INSTALLATION.)
2. Visually inspect the compressor wheel from view A and verify that all fins are free from damage, cracks or
bends.
•If there are damaged fins, cracks or bends, replace the turbocharger.
Note
•To make the inspection easier, set a small
mirror as shown in the figure and use a
penlight.
•If the compressor wheel is interfering with
the compressor housing, it is likely that the
fin edges are cracked, damaged, or bent.
•If the compressor wheel is damaged, check
the following before replacing the
turbocharger to avoid reoccurrence of the
problem.
—Foreign material in intake air/exhaust
system.
—Oil pipe clogging.
MIRROR
A
A6E40102009
Page 192 of 909
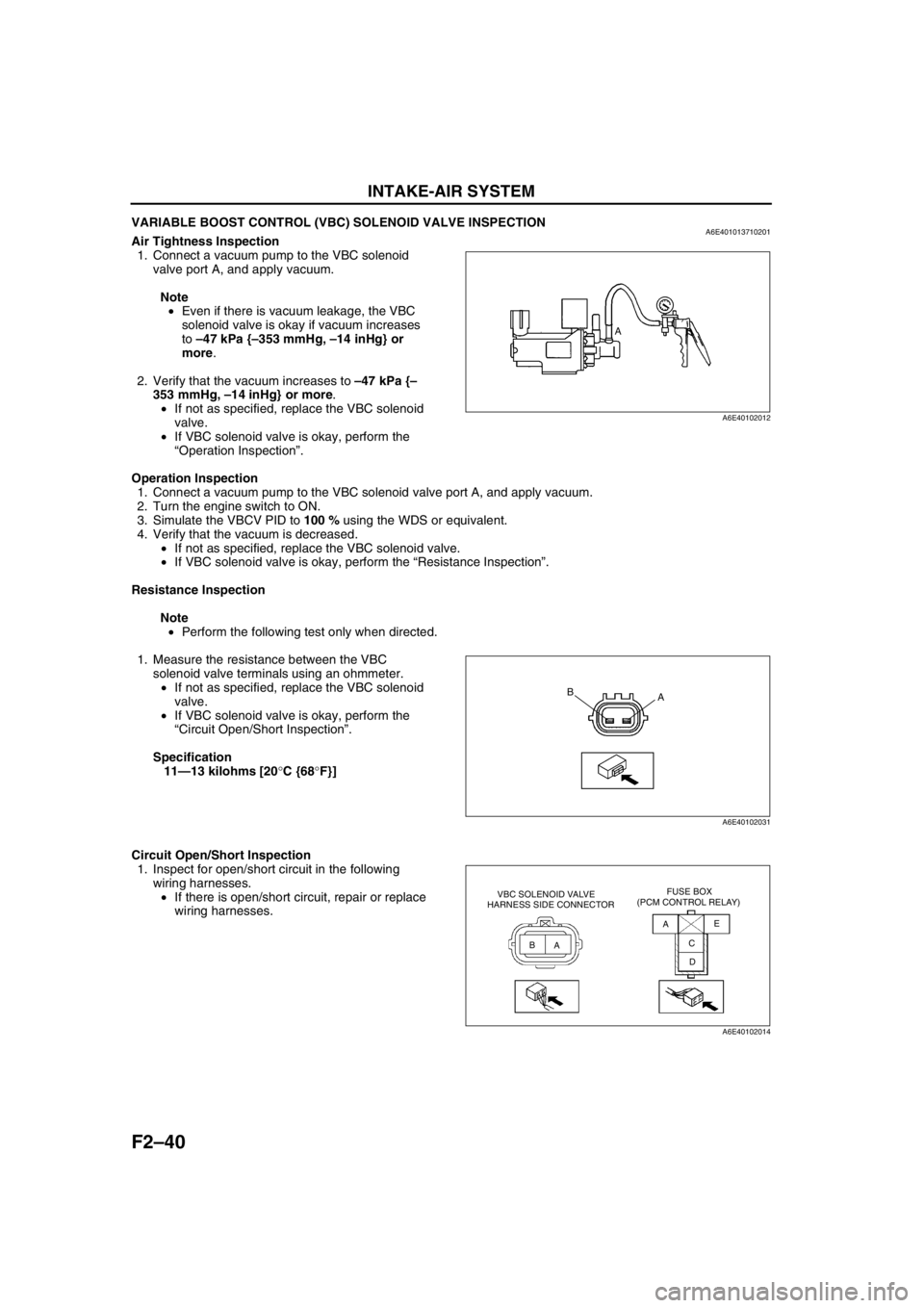
F2–40
INTAKE-AIR SYSTEM
VARIABLE BOOST CONTROL (VBC) SOLENOID VALVE INSPECTIONA6E401013710201Air Tightness Inspection
1. Connect a vacuum pump to the VBC solenoid
valve port A, and apply vacuum.
Note
•Even if there is vacuum leakage, the VBC
solenoid valve is okay if vacuum increases
to –47 kPa {–353 mmHg, –14 inHg} or
more.
2. Verify that the vacuum increases to –47 kPa {–
353 mmHg, –14 inHg} or more.
•If not as specified, replace the VBC solenoid
valve.
•If VBC solenoid valve is okay, perform the
“Operation Inspection”.
Operation Inspection
1. Connect a vacuum pump to the VBC solenoid valve port A, and apply vacuum.
2. Turn the engine switch to ON.
3. Simulate the VBCV PID to 100 % using the WDS or equivalent.
4. Verify that the vacuum is decreased.
•If not as specified, replace the VBC solenoid valve.
•If VBC solenoid valve is okay, perform the “Resistance Inspection”.
Resistance Inspection
Note
•Perform the following test only when directed.
1. Measure the resistance between the VBC
solenoid valve terminals using an ohmmeter.
•If not as specified, replace the VBC solenoid
valve.
•If VBC solenoid valve is okay, perform the
“Circuit Open/Short Inspection”.
Specification
11—13 kilohms [20°C {68°F}]
Circuit Open/Short Inspection
1. Inspect for open/short circuit in the following
wiring harnesses.
•If there is open/short circuit, repair or replace
wiring harnesses.
A
A6E40102012
A B
A6E40102031
AA
BC
DE VBC SOLENOID VALVE
HARNESS SIDE CONNECTORFUSE BOX
(PCM CONTROL RELAY)
A6E40102014
Page 197 of 909
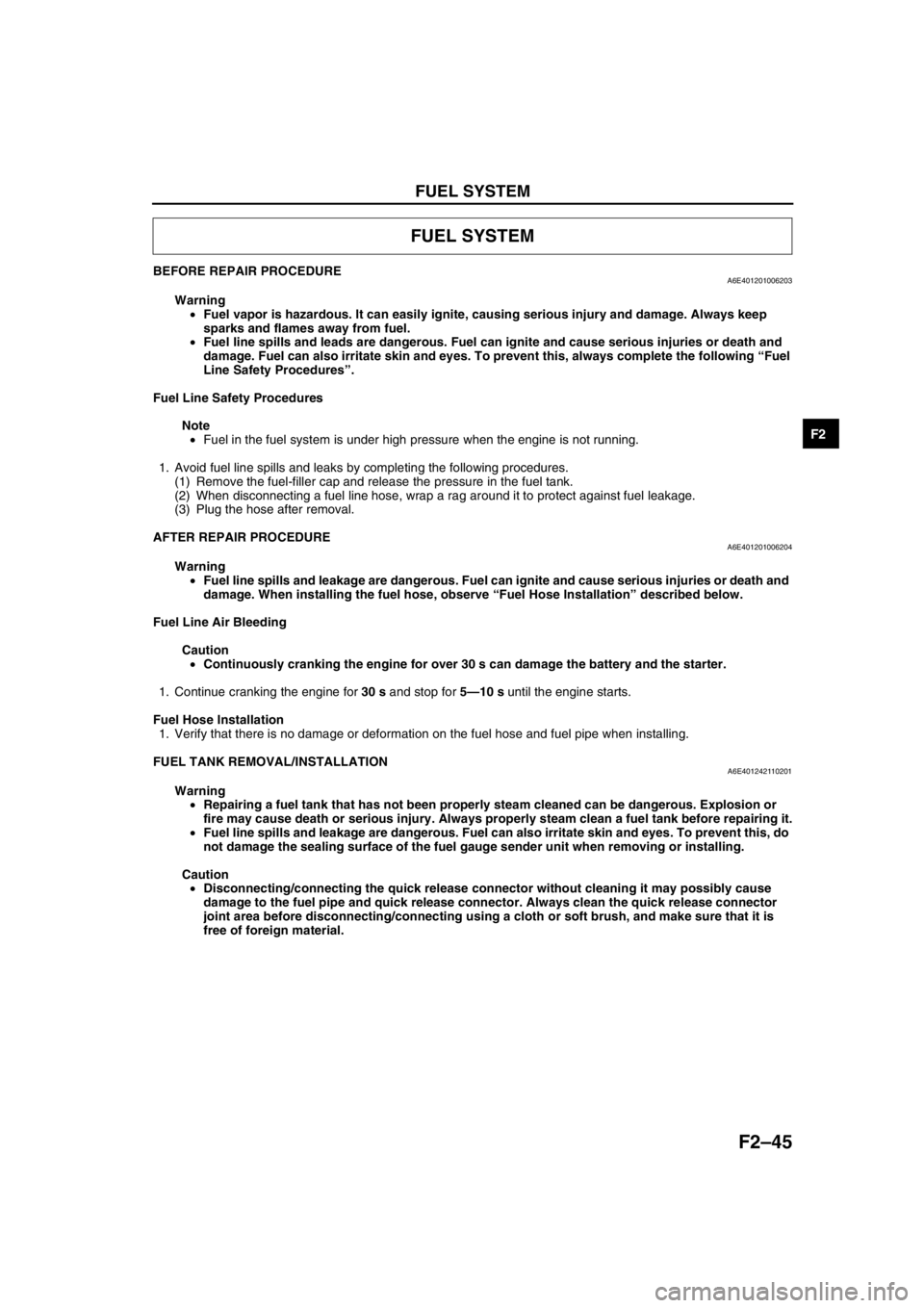
FUEL SYSTEM
F2–45
F2
BEFORE REPAIR PROCEDUREA6E401201006203
Warning
•Fuel vapor is hazardous. It can easily ignite, causing serious injury and damage. Always keep
sparks and flames away from fuel.
•Fuel line spills and leads are dangerous. Fuel can ignite and cause serious injuries or death and
damage. Fuel can also irritate skin and eyes. To prevent this, always complete the following “Fuel
Line Safety Procedures”.
Fuel Line Safety Procedures
Note
•Fuel in the fuel system is under high pressure when the engine is not running.
1. Avoid fuel line spills and leaks by completing the following procedures.
(1) Remove the fuel-filler cap and release the pressure in the fuel tank.
(2) When disconnecting a fuel line hose, wrap a rag around it to protect against fuel leakage.
(3) Plug the hose after removal.
End Of Sie
AFTER REPAIR PROCEDUREA6E401201006204
Warning
•Fuel line spills and leakage are dangerous. Fuel can ignite and cause serious injuries or death and
damage. When installing the fuel hose, observe “Fuel Hose Installation” described below.
Fuel Line Air Bleeding
Caution
•Continuously cranking the engine for over 30 s can damage the battery and the starter.
1. Continue cranking the engine for 30 s and stop for 5—10 s until the engine starts.
Fuel Hose Installation
1. Verify that there is no damage or deformation on the fuel hose and fuel pipe when installing.
End Of Sie
FUEL TANK REMOVAL/INSTALLATIONA6E401242110201
Warning
•Repairing a fuel tank that has not been properly steam cleaned can be dangerous. Explosion or
fire may cause death or serious injury. Always properly steam clean a fuel tank before repairing it.
•Fuel line spills and leakage are dangerous. Fuel can also irritate skin and eyes. To prevent this, do
not damage the sealing surface of the fuel gauge sender unit when removing or installing.
Caution
•Disconnecting/connecting the quick release connector without cleaning it may possibly cause
damage to the fuel pipe and quick release connector. Always clean the quick release connector
joint area before disconnecting/connecting using a cloth or soft brush, and make sure that it is
free of foreign material.
FUEL SYSTEM
Page 201 of 909
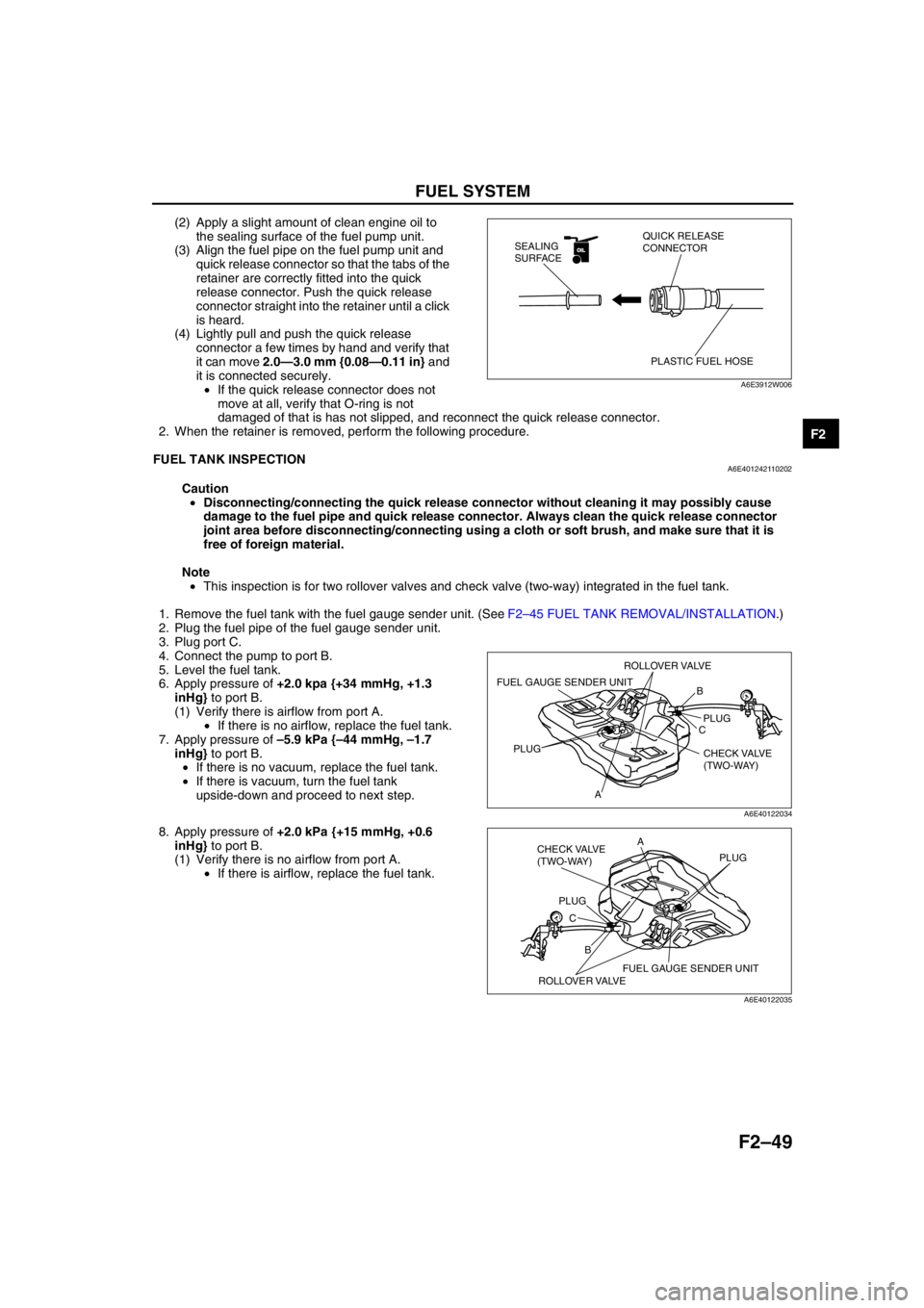
FUEL SYSTEM
F2–49
F2
(2) Apply a slight amount of clean engine oil to
the sealing surface of the fuel pump unit.
(3) Align the fuel pipe on the fuel pump unit and
quick release connector so that the tabs of the
retainer are correctly fitted into the quick
release connector. Push the quick release
connector straight into the retainer until a click
is heard.
(4) Lightly pull and push the quick release
connector a few times by hand and verify that
it can move 2.0—3.0 mm {0.08—0.11 in} and
it is connected securely.
•If the quick release connector does not
move at all, verify that O-ring is not
damaged of that is has not slipped, and reconnect the quick release connector.
2. When the retainer is removed, perform the following procedure.
End Of Sie
FUEL TANK INSPECTIONA6E401242110202
Caution
•Disconnecting/connecting the quick release connector without cleaning it may possibly cause
damage to the fuel pipe and quick release connector. Always clean the quick release connector
joint area before disconnecting/connecting using a cloth or soft brush, and make sure that it is
free of foreign material.
Note
•This inspection is for two rollover valves and check valve (two-way) integrated in the fuel tank.
1. Remove the fuel tank with the fuel gauge sender unit. (See F2–45 FUEL TANK REMOVAL/INSTALLATION.)
2. Plug the fuel pipe of the fuel gauge sender unit.
3. Plug port C.
4. Connect the pump to port B.
5. Level the fuel tank.
6. Apply pressure of +2.0 kpa {+34 mmHg, +1.3
inHg} to port B.
(1) Verify there is airflow from port A.
•If there is no airflow, replace the fuel tank.
7. Apply pressure of –5.9 kPa {–44 mmHg, –1.7
inHg} to port B.
•If there is no vacuum, replace the fuel tank.
•If there is vacuum, turn the fuel tank
upside-down and proceed to next step.
8. Apply pressure of +2.0 kPa {+15 mmHg, +0.6
inHg} to port B.
(1) Verify there is no airflow from port A.
•If there is airflow, replace the fuel tank.
End Of Sie
OILOIL
PLASTIC FUEL HOSE QUICK RELEASE
CONNECTOR SEALING
SURFACE
A6E3912W006
B
C
APLUG
PLUG
CHECK VALVE
(TWO-WAY)
FUEL GAUGE SENDER UNIT
ROLLOVER VALVE
A6E40122034
B CA
PLUGPLUG
CHECK VALVE
(TWO-WAY)
FUEL GAUGE SENDER UNIT
ROLLOVER VALVE
A6E40122035