service indicator MAZDA 6 2002 Workshop Manual Suplement
[x] Cancel search | Manufacturer: MAZDA, Model Year: 2002, Model line: 6, Model: MAZDA 6 2002Pages: 909, PDF Size: 17.16 MB
Page 8 of 909
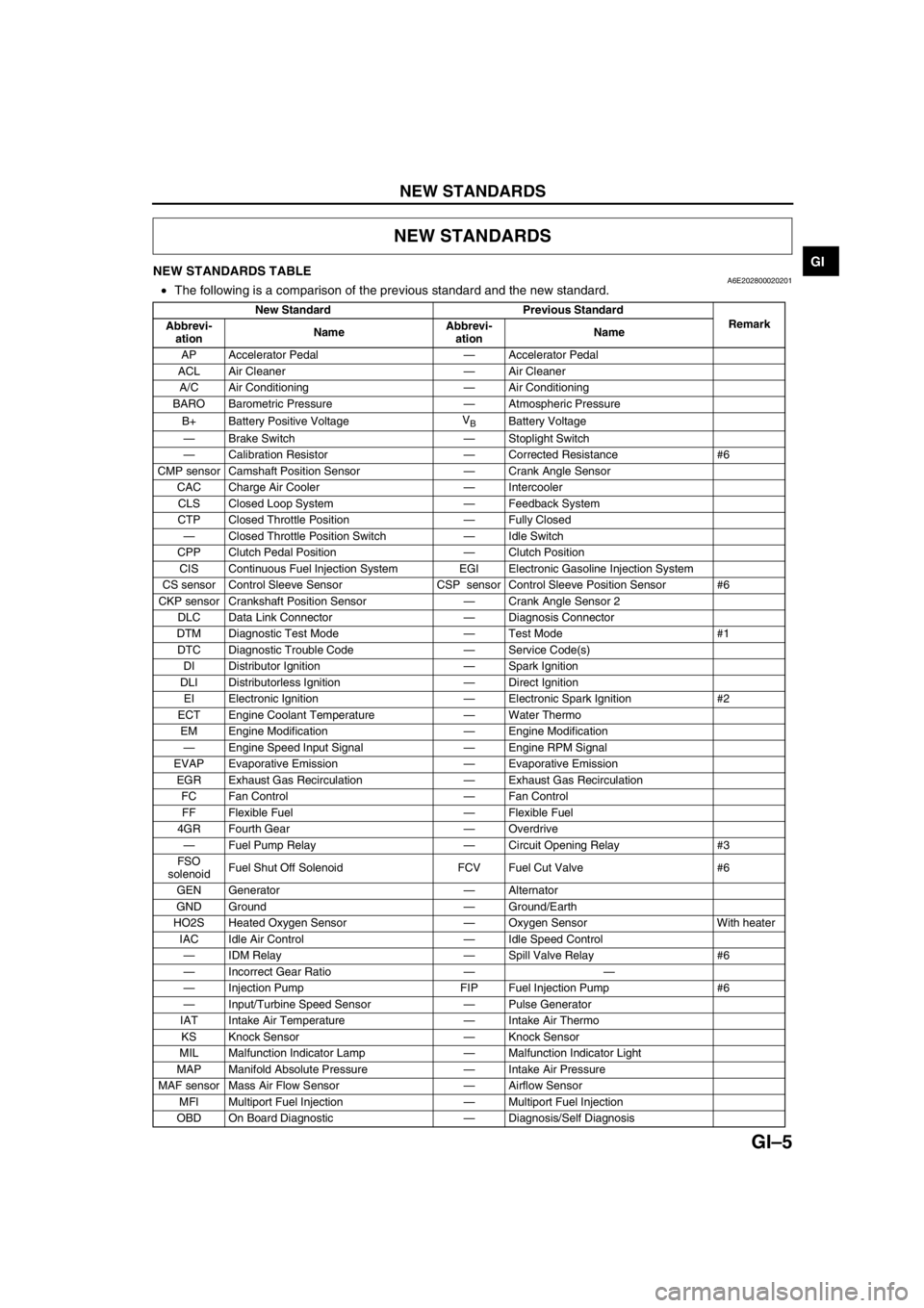
NEW STANDARDS
GI–5
GINEW STANDARDS TABLEA6E202800020201•The following is a comparison of the previous standard and the new standard.
NEW STANDARDS
New Standard Previous Standard
Remark
Abbrevi-
ationNameAbbrevi-
ationName
AP Accelerator Pedal—Accelerator Pedal
ACL Air Cleaner—Air Cleaner
A/C Air Conditioning—Air Conditioning
BARO Barometric Pressure—Atmospheric Pressure
B+ Battery Positive VoltageV
BBattery Voltage
—Brake Switch—Stoplight Switch
—Calibration Resistor—Corrected Resistance #6
CMP sensor Camshaft Position Sensor—Crank Angle Sensor
CAC Charge Air Cooler—Intercooler
CLS Closed Loop System—Feedback System
CTP Closed Throttle Position—Fully Closed
—Closed Throttle Position Switch—Idle Switch
CPP Clutch Pedal Position—Clutch Position
CIS Continuous Fuel Injection System EGI Electronic Gasoline Injection System
CS sensor Control Sleeve Sensor CSP sensor Control Sleeve Position Sensor #6
CKP sensor Crankshaft Position Sensor—Crank Angle Sensor 2
DLC Data Link Connector—Diagnosis Connector
DTM Diagnostic Test Mode—Test Mode #1
DTC Diagnostic Trouble Code—Service Code(s)
DI Distributor Ignition—Spark Ignition
DLI Distributorless Ignition—Direct Ignition
EI Electronic Ignition—Electronic Spark Ignition #2
ECT Engine Coolant Temperature—Water Thermo
EM Engine Modification—Engine Modification
—Engine Speed Input Signal—Engine RPM Signal
EVAP Evaporative Emission—Evaporative Emission
EGR Exhaust Gas Recirculation—Exhaust Gas Recirculation
FC Fan Control—Fan Control
FF Flexible Fuel—Flexible Fuel
4GR Fourth Gear—Overdrive
—Fuel Pump Relay—Circuit Opening Relay #3
FSO
solenoidFuel Shut Off Solenoid FCV Fuel Cut Valve #6
GEN Generator—Alternator
GND Ground—Ground/Earth
HO2S Heated Oxygen Sensor—Oxygen Sensor With heater
IAC Idle Air Control—Idle Speed Control
—IDM Relay—Spill Valve Relay #6
—Incorrect Gear Ratio——
—Injection Pump FIP Fuel Injection Pump #6
—Input/Turbine Speed Sensor—Pulse Generator
IAT Intake Air Temperature—Intake Air Thermo
KS Knock Sensor—Knock Sensor
MIL Malfunction Indicator Lamp—Malfunction Indicator Light
MAP Manifold Absolute Pressure—Intake Air Pressure
MAF sensor Mass Air Flow Sensor—Airflow Sensor
MFI Multiport Fuel Injection—Multiport Fuel Injection
OBD On Board Diagnostic—Diagnosis/Self Diagnosis
Page 603 of 909
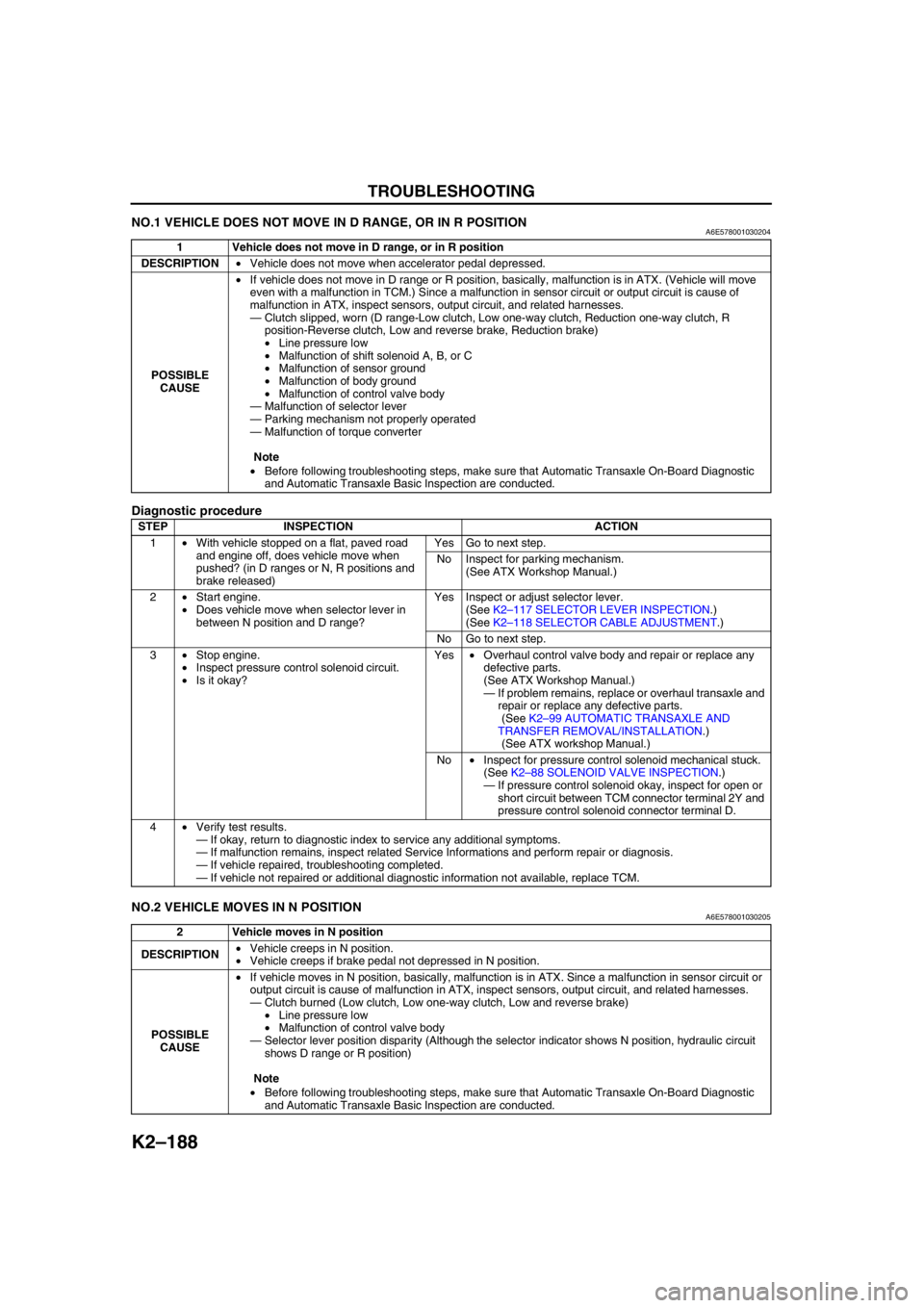
K2–188
TROUBLESHOOTING
NO.1 VEHICLE DOES NOT MOVE IN D RANGE, OR IN R POSITIONA6E578001030204
Diagnostic procedure
End Of SieNO.2 VEHICLE MOVES IN N POSITIONA6E578001030205
1 Vehicle does not move in D range, or in R position
DESCRIPTION•Vehicle does not move when accelerator pedal depressed.
POSSIBLE
CAUSE•If vehicle does not move in D range or R position, basically, malfunction is in ATX. (Vehicle will move
even with a malfunction in TCM.) Since a malfunction in sensor circuit or output circuit is cause of
malfunction in ATX, inspect sensors, output circuit, and related harnesses.
—Clutch slipped, worn (D range-Low clutch, Low one-way clutch, Reduction one-way clutch, R
position-Reverse clutch, Low and reverse brake, Reduction brake)
•Line pressure low
•Malfunction of shift solenoid A, B, or C
•Malfunction of sensor ground
•Malfunction of body ground
•Malfunction of control valve body
—Malfunction of selector lever
—Parking mechanism not properly operated
—Malfunction of torque converter
Note
•Before following troubleshooting steps, make sure that Automatic Transaxle On-Board Diagnostic
and Automatic Transaxle Basic Inspection are conducted.
STEP INSPECTION ACTION
1•With vehicle stopped on a flat, paved road
and engine off, does vehicle move when
pushed? (in D ranges or N, R positions and
brake released)Yes Go to next step.
No Inspect for parking mechanism.
(See ATX Workshop Manual.)
2•Start engine.
•Does vehicle move when selector lever in
between N position and D range?Yes Inspect or adjust selector lever.
(See K2–117 SELECTOR LEVER INSPECTION.)
(See K2–118 SELECTOR CABLE ADJUSTMENT.)
No Go to next step.
3•Stop engine.
•Inspect pressure control solenoid circuit.
•Is it okay?Yes•Overhaul control valve body and repair or replace any
defective parts.
(See ATX Workshop Manual.)
—If problem remains, replace or overhaul transaxle and
repair or replace any defective parts.
(See K2–99 AUTOMATIC TRANSAXLE AND
TRANSFER REMOVAL/INSTALLATION.)
(See ATX workshop Manual.)
No•Inspect for pressure control solenoid mechanical stuck.
(See K2–88 SOLENOID VALVE INSPECTION.)
—If pressure control solenoid okay, inspect for open or
short circuit between TCM connector terminal 2Y and
pressure control solenoid connector terminal D.
4•Verify test results.
—If okay, return to diagnostic index to service any additional symptoms.
—If malfunction remains, inspect related Service Informations and perform repair or diagnosis.
—If vehicle repaired, troubleshooting completed.
—If vehicle not repaired or additional diagnostic information not available, replace TCM.
2 Vehicle moves in N position
DESCRIPTION•Vehicle creeps in N position.
•Vehicle creeps if brake pedal not depressed in N position.
POSSIBLE
CAUSE•If vehicle moves in N position, basically, malfunction is in ATX. Since a malfunction in sensor circuit or
output circuit is cause of malfunction in ATX, inspect sensors, output circuit, and related harnesses.
—Clutch burned (Low clutch, Low one-way clutch, Low and reverse brake)
•Line pressure low
•Malfunction of control valve body
—Selector lever position disparity (Although the selector indicator shows N position, hydraulic circuit
shows D range or R position)
Note
•Before following troubleshooting steps, make sure that Automatic Transaxle On-Board Diagnostic
and Automatic Transaxle Basic Inspection are conducted.
Page 605 of 909
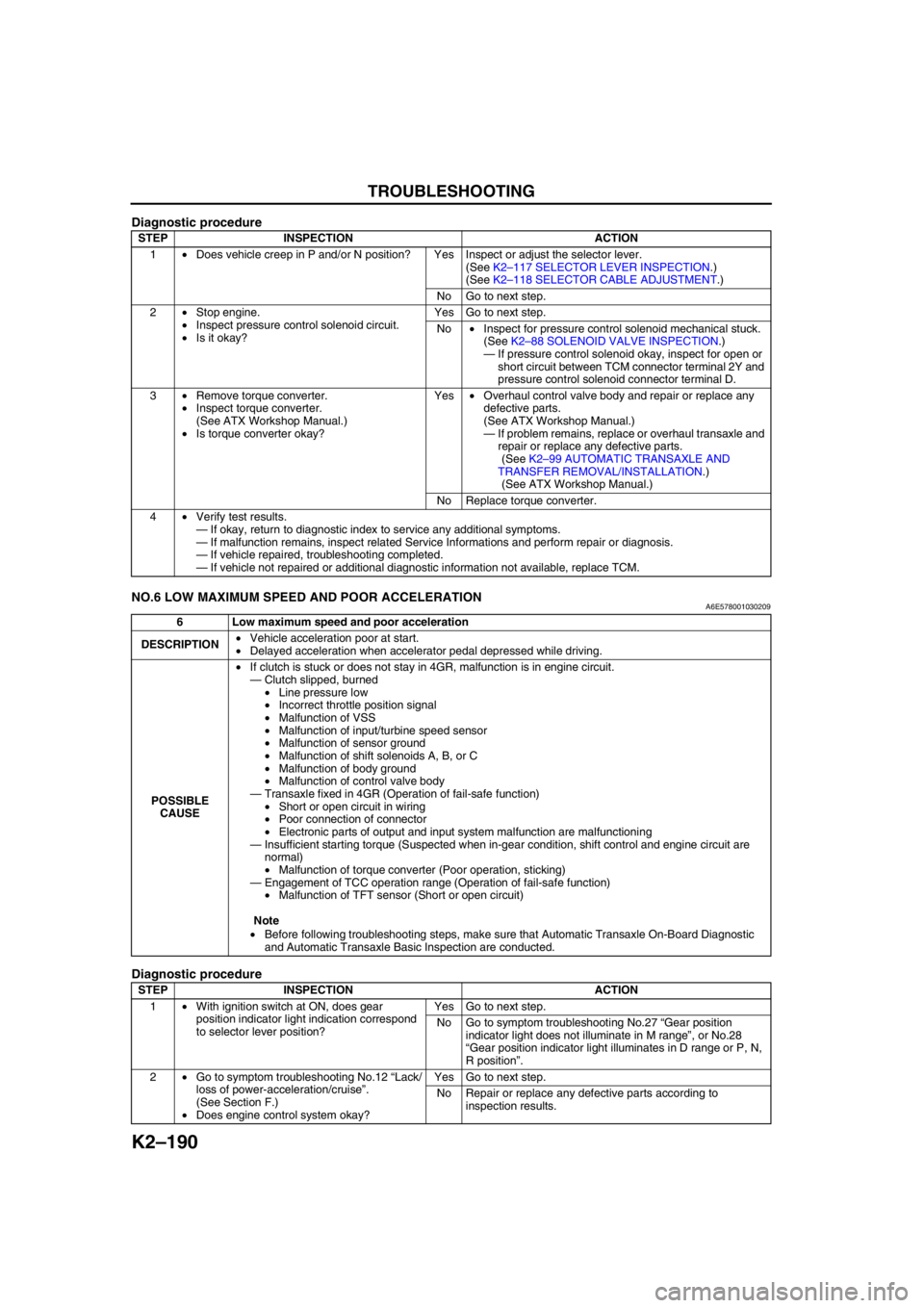
K2–190
TROUBLESHOOTING
Diagnostic procedure
End Of SieNO.6 LOW MAXIMUM SPEED AND POOR ACCELERATIONA6E578001030209
Diagnostic procedure
STEP INSPECTION ACTION
1•Does vehicle creep in P and/or N position? Yes Inspect or adjust the selector lever.
(See K2–117 SELECTOR LEVER INSPECTION.)
(See K2–118 SELECTOR CABLE ADJUSTMENT.)
No Go to next step.
2•Stop engine.
•Inspect pressure control solenoid circuit.
•Is it okay?Yes Go to next step.
No•Inspect for pressure control solenoid mechanical stuck.
(See K2–88 SOLENOID VALVE INSPECTION.)
—If pressure control solenoid okay, inspect for open or
short circuit between TCM connector terminal 2Y and
pressure control solenoid connector terminal D.
3•Remove torque converter.
•Inspect torque converter.
(See ATX Workshop Manual.)
•Is torque converter okay?Yes•Overhaul control valve body and repair or replace any
defective parts.
(See ATX Workshop Manual.)
—If problem remains, replace or overhaul transaxle and
repair or replace any defective parts.
(See K2–99 AUTOMATIC TRANSAXLE AND
TRANSFER REMOVAL/INSTALLATION.)
(See ATX Workshop Manual.)
No Replace torque converter.
4•Verify test results.
—If okay, return to diagnostic index to service any additional symptoms.
—If malfunction remains, inspect related Service Informations and perform repair or diagnosis.
—If vehicle repaired, troubleshooting completed.
—If vehicle not repaired or additional diagnostic information not available, replace TCM.
6 Low maximum speed and poor acceleration
DESCRIPTION•Vehicle acceleration poor at start.
•Delayed acceleration when accelerator pedal depressed while driving.
POSSIBLE
CAUSE•If clutch is stuck or does not stay in 4GR, malfunction is in engine circuit.
—Clutch slipped, burned
•Line pressure low
•Incorrect throttle position signal
•Malfunction of VSS
•Malfunction of input/turbine speed sensor
•Malfunction of sensor ground
•Malfunction of shift solenoids A, B, or C
•Malfunction of body ground
•Malfunction of control valve body
—Transaxle fixed in 4GR (Operation of fail-safe function)
•Short or open circuit in wiring
•Poor connection of connector
•Electronic parts of output and input system malfunction are malfunctioning
—Insufficient starting torque (Suspected when in-gear condition, shift control and engine circuit are
normal)
•Malfunction of torque converter (Poor operation, sticking)
—Engagement of TCC operation range (Operation of fail-safe function)
•Malfunction of TFT sensor (Short or open circuit)
Note
•Before following troubleshooting steps, make sure that Automatic Transaxle On-Board Diagnostic
and Automatic Transaxle Basic Inspection are conducted.
STEP INSPECTION ACTION
1•With ignition switch at ON, does gear
position indicator light indication correspond
to selector lever position?Yes Go to next step.
No Go to symptom troubleshooting No.27 “Gear position
indicator light does not illuminate in M range”, or No.28
“Gear position indicator light illuminates in D range or P, N,
R position”.
2•Go to symptom troubleshooting No.12 “Lack/
loss of power-acceleration/cruise”.
(See Section F.)
•Does engine control system okay?Yes Go to next step.
No Repair or replace any defective parts according to
inspection results.
Page 609 of 909
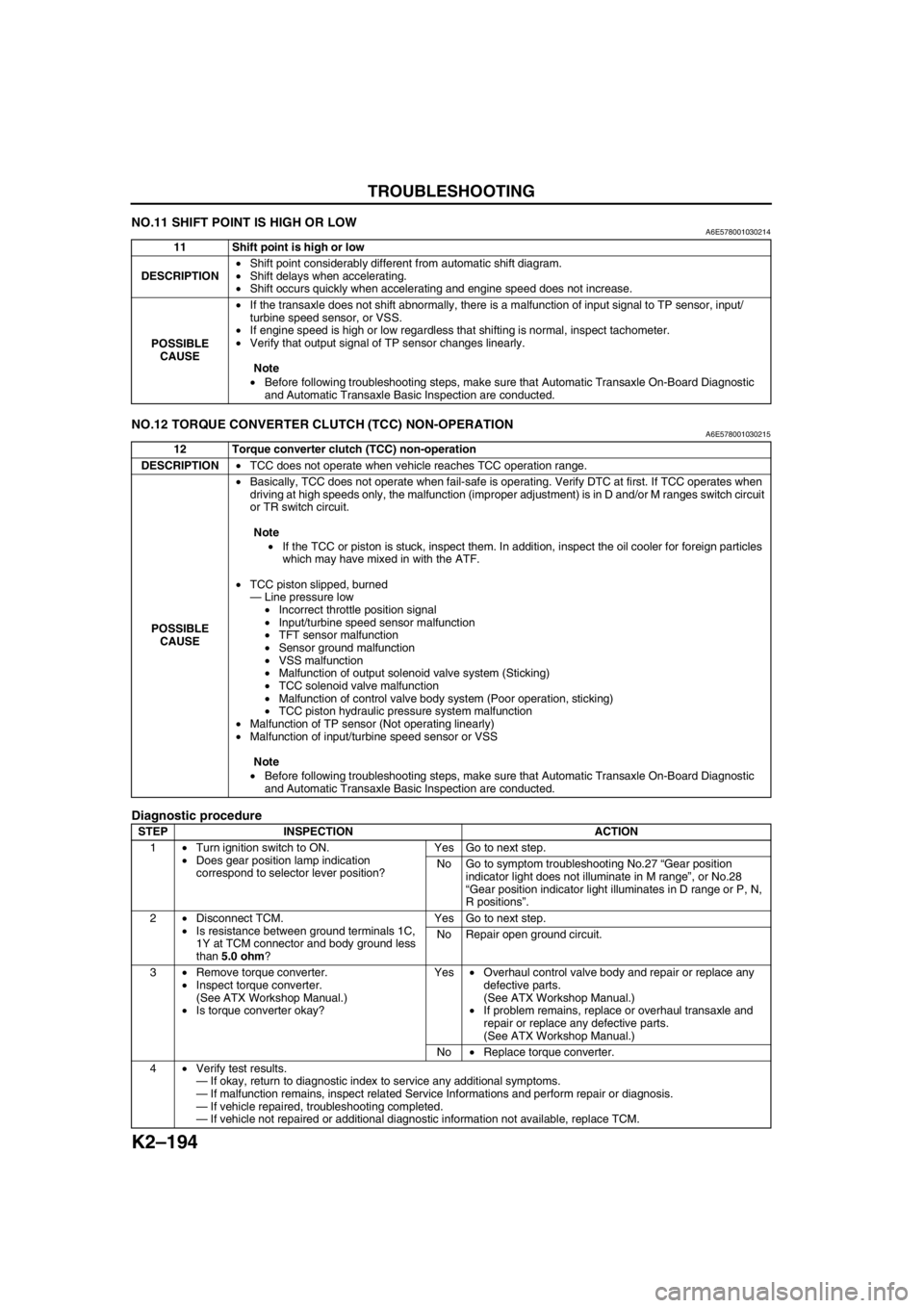
K2–194
TROUBLESHOOTING
NO.11 SHIFT POINT IS HIGH OR LOWA6E578001030214
End Of SieNO.12 TORQUE CONVERTER CLUTCH (TCC) NON-OPERATIONA6E578001030215
Diagnostic procedure
11 Shift point is high or low
DESCRIPTION•Shift point considerably different from automatic shift diagram.
•Shift delays when accelerating.
•Shift occurs quickly when accelerating and engine speed does not increase.
POSSIBLE
CAUSE•If the transaxle does not shift abnormally, there is a malfunction of input signal to TP sensor, input/
turbine speed sensor, or VSS.
•If engine speed is high or low regardless that shifting is normal, inspect tachometer.
•Verify that output signal of TP sensor changes linearly.
Note
•Before following troubleshooting steps, make sure that Automatic Transaxle On-Board Diagnostic
and Automatic Transaxle Basic Inspection are conducted.
12 Torque converter clutch (TCC) non-operation
DESCRIPTION•TCC does not operate when vehicle reaches TCC operation range.
POSSIBLE
CAUSE•Basically, TCC does not operate when fail-safe is operating. Verify DTC at first. If TCC operates when
driving at high speeds only, the malfunction (improper adjustment) is in D and/or M ranges switch circuit
or TR switch circuit.
Note
•If the TCC or piston is stuck, inspect them. In addition, inspect the oil cooler for foreign particles
which may have mixed in with the ATF.
•TCC piston slipped, burned
—Line pressure low
•Incorrect throttle position signal
•Input/turbine speed sensor malfunction
•TFT sensor malfunction
•Sensor ground malfunction
•VSS malfunction
•Malfunction of output solenoid valve system (Sticking)
•TCC solenoid valve malfunction
•Malfunction of control valve body system (Poor operation, sticking)
•TCC piston hydraulic pressure system malfunction
•Malfunction of TP sensor (Not operating linearly)
•Malfunction of input/turbine speed sensor or VSS
Note
•Before following troubleshooting steps, make sure that Automatic Transaxle On-Board Diagnostic
and Automatic Transaxle Basic Inspection are conducted.
STEP INSPECTION ACTION
1•Turn ignition switch to ON.
•Does gear position lamp indication
correspond to selector lever position?Yes Go to next step.
No Go to symptom troubleshooting No.27 “Gear position
indicator light does not illuminate in M range”, or No.28
“Gear position indicator light illuminates in D range or P, N,
R positions”.
2•Disconnect TCM.
•Is resistance between ground terminals 1C,
1Y at TCM connector and body ground less
than 5.0 ohm?Yes Go to next step.
No Repair open ground circuit.
3•Remove torque converter.
•Inspect torque converter.
(See ATX Workshop Manual.)
•Is torque converter okay?Yes•Overhaul control valve body and repair or replace any
defective parts.
(See ATX Workshop Manual.)
•If problem remains, replace or overhaul transaxle and
repair or replace any defective parts.
(See ATX Workshop Manual.)
No•Replace torque converter.
4•Verify test results.
—If okay, return to diagnostic index to service any additional symptoms.
—If malfunction remains, inspect related Service Informations and perform repair or diagnosis.
—If vehicle repaired, troubleshooting completed.
—If vehicle not repaired or additional diagnostic information not available, replace TCM.
Page 615 of 909
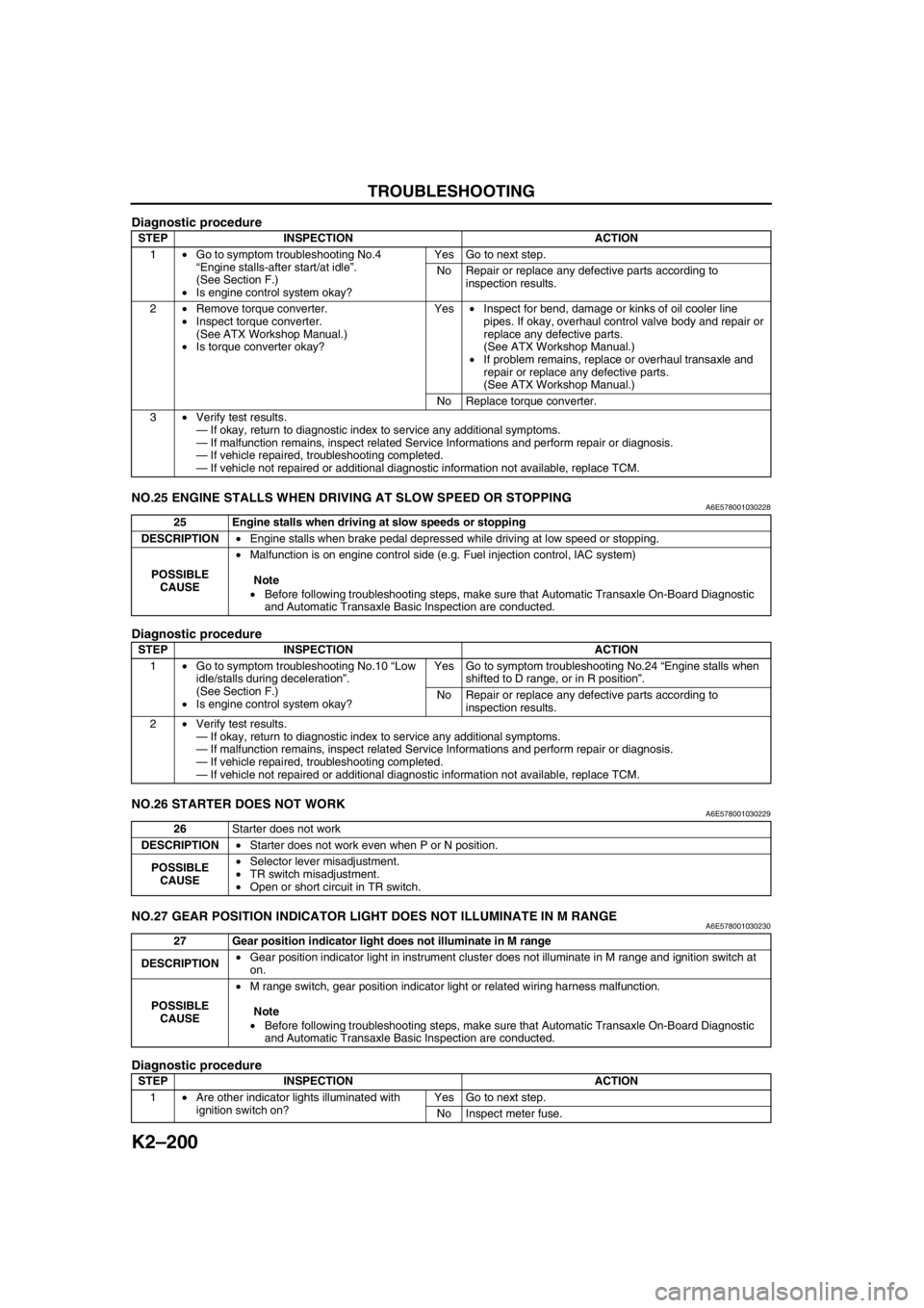
K2–200
TROUBLESHOOTING
Diagnostic procedure
End Of SieNO.25 ENGINE STALLS WHEN DRIVING AT SLOW SPEED OR STOPPINGA6E578001030228
Diagnostic procedure
End Of SieNO.26 STARTER DOES NOT WORKA6E578001030229
End Of SieNO.27 GEAR POSITION INDICATOR LIGHT DOES NOT ILLUMINATE IN M RANGEA6E578001030230
Diagnostic procedure
STEP INSPECTION ACTION
1•Go to symptom troubleshooting No.4
“Engine stalls-after start/at idle”.
(See Section F.)
•Is engine control system okay?Yes Go to next step.
No Repair or replace any defective parts according to
inspection results.
2•Remove torque converter.
•Inspect torque converter.
(See ATX Workshop Manual.)
•Is torque converter okay?Yes•Inspect for bend, damage or kinks of oil cooler line
pipes. If okay, overhaul control valve body and repair or
replace any defective parts.
(See ATX Workshop Manual.)
•If problem remains, replace or overhaul transaxle and
repair or replace any defective parts.
(See ATX Workshop Manual.)
No Replace torque converter.
3•Verify test results.
—If okay, return to diagnostic index to service any additional symptoms.
—If malfunction remains, inspect related Service Informations and perform repair or diagnosis.
—If vehicle repaired, troubleshooting completed.
—If vehicle not repaired or additional diagnostic information not available, replace TCM.
25 Engine stalls when driving at slow speeds or stopping
DESCRIPTION•Engine stalls when brake pedal depressed while driving at low speed or stopping.
POSSIBLE
CAUSE•Malfunction is on engine control side (e.g. Fuel injection control, IAC system)
Note
•Before following troubleshooting steps, make sure that Automatic Transaxle On-Board Diagnostic
and Automatic Transaxle Basic Inspection are conducted.
STEP INSPECTION ACTION
1•Go to symptom troubleshooting No.10 “Low
idle/stalls during deceleration”.
(See Section F.)
•Is engine control system okay?Yes Go to symptom troubleshooting No.24 “Engine stalls when
shifted to D range, or in R position”.
No Repair or replace any defective parts according to
inspection results.
2•Verify test results.
—If okay, return to diagnostic index to service any additional symptoms.
—If malfunction remains, inspect related Service Informations and perform repair or diagnosis.
—If vehicle repaired, troubleshooting completed.
—If vehicle not repaired or additional diagnostic information not available, replace TCM.
26Starter does not work
DESCRIPTION•Starter does not work even when P or N position.
POSSIBLE
CAUSE•Selector lever misadjustment.
•TR switch misadjustment.
•Open or short circuit in TR switch.
27 Gear position indicator light does not illuminate in M range
DESCRIPTION•Gear position indicator light in instrument cluster does not illuminate in M range and ignition switch at
on.
POSSIBLE
CAUSE•M range switch, gear position indicator light or related wiring harness malfunction.
Note
•Before following troubleshooting steps, make sure that Automatic Transaxle On-Board Diagnostic
and Automatic Transaxle Basic Inspection are conducted.
STEP INSPECTION ACTION
1•Are other indicator lights illuminated with
ignition switch on? Yes Go to next step.
No Inspect meter fuse.
Page 616 of 909
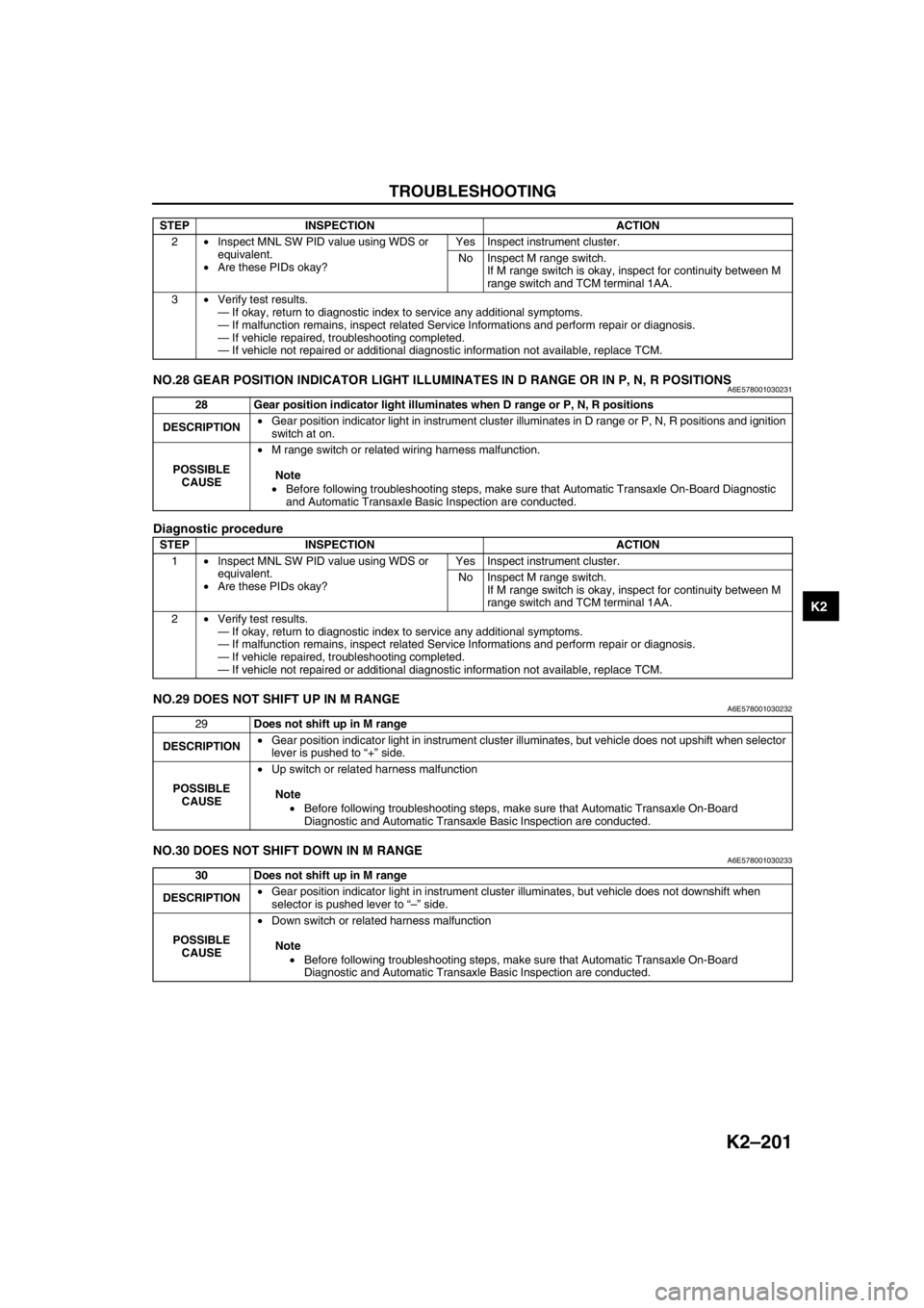
TROUBLESHOOTING
K2–201
K2
End Of SieNO.28 GEAR POSITION INDICATOR LIGHT ILLUMINATES IN D RANGE OR IN P, N, R POSITIONSA6E578001030231
Diagnostic procedure
End Of SieNO.29 DOES NOT SHIFT UP IN M RANGEA6E578001030232
End Of SieNO.30 DOES NOT SHIFT DOWN IN M RANGEA6E578001030233
End Of Sie
2•Inspect MNL SW PID value using WDS or
equivalent.
•Are these PIDs okay?Yes Inspect instrument cluster.
No Inspect M range switch.
If M range switch is okay, inspect for continuity between M
range switch and TCM terminal 1AA.
3•Verify test results.
—If okay, return to diagnostic index to service any additional symptoms.
—If malfunction remains, inspect related Service Informations and perform repair or diagnosis.
—If vehicle repaired, troubleshooting completed.
—If vehicle not repaired or additional diagnostic information not available, replace TCM. STEP INSPECTION ACTION
28 Gear position indicator light illuminates when D range or P, N, R positions
DESCRIPTION•Gear position indicator light in instrument cluster illuminates in D range or P, N, R positions and ignition
switch at on.
POSSIBLE
CAUSE•M range switch or related wiring harness malfunction.
Note
•Before following troubleshooting steps, make sure that Automatic Transaxle On-Board Diagnostic
and Automatic Transaxle Basic Inspection are conducted.
STEP INSPECTION ACTION
1•Inspect MNL SW PID value using WDS or
equivalent.
•Are these PIDs okay?Yes Inspect instrument cluster.
No Inspect M range switch.
If M range switch is okay, inspect for continuity between M
range switch and TCM terminal 1AA.
2•Verify test results.
—If okay, return to diagnostic index to service any additional symptoms.
—If malfunction remains, inspect related Service Informations and perform repair or diagnosis.
—If vehicle repaired, troubleshooting completed.
—If vehicle not repaired or additional diagnostic information not available, replace TCM.
29Does not shift up in M range
DESCRIPTION•Gear position indicator light in instrument cluster illuminates, but vehicle does not upshift when selector
lever is pushed to “+” side.
POSSIBLE
CAUSE•Up switch or related harness malfunction
Note
•Before following troubleshooting steps, make sure that Automatic Transaxle On-Board
Diagnostic and Automatic Transaxle Basic Inspection are conducted.
30 Does not shift up in M range
DESCRIPTION•Gear position indicator light in instrument cluster illuminates, but vehicle does not downshift when
selector is pushed lever to “–” side.
POSSIBLE
CAUSE•Down switch or related harness malfunction
Note
•Before following troubleshooting steps, make sure that Automatic Transaxle On-Board
Diagnostic and Automatic Transaxle Basic Inspection are conducted.
Page 812 of 909
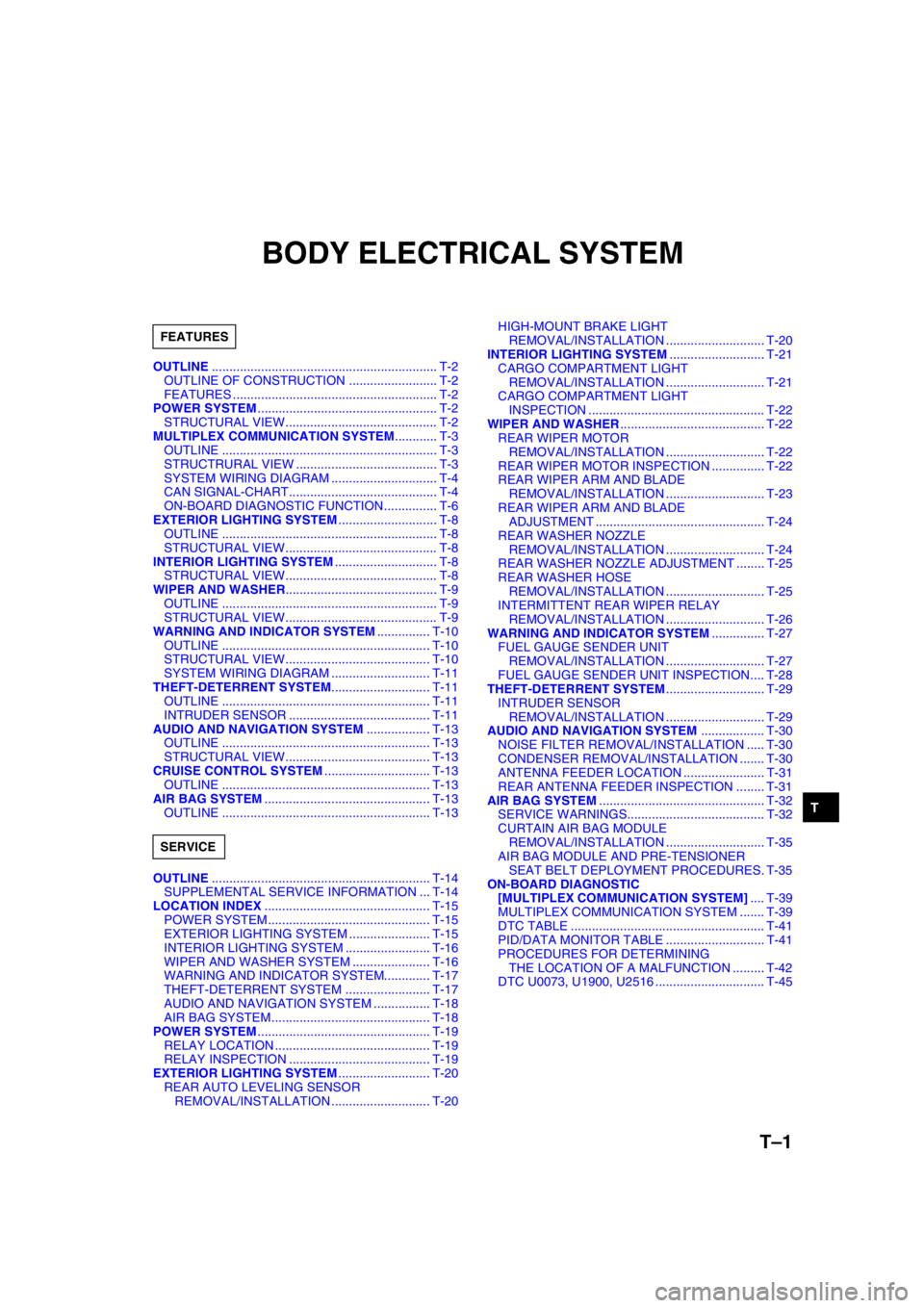
T–1
T
TBODY ELECTRICAL SYSTEM
OUTLINE................................................................ T-2
OUTLINE OF CONSTRUCTION ......................... T-2
FEATURES .......................................................... T-2
POWER SYSTEM................................................... T-2
STRUCTURAL VIEW........................................... T-2
MULTIPLEX COMMUNICATION SYSTEM............ T-3
OUTLINE ............................................................. T-3
STRUCTRURAL VIEW ........................................ T-3
SYSTEM WIRING DIAGRAM .............................. T-4
CAN SIGNAL-CHART.......................................... T-4
ON-BOARD DIAGNOSTIC FUNCTION............... T-6
EXTERIOR LIGHTING SYSTEM............................ T-8
OUTLINE ............................................................. T-8
STRUCTURAL VIEW........................................... T-8
INTERIOR LIGHTING SYSTEM............................. T-8
STRUCTURAL VIEW........................................... T-8
WIPER AND WASHER........................................... T-9
OUTLINE ............................................................. T-9
STRUCTURAL VIEW........................................... T-9
WARNING AND INDICATOR SYSTEM............... T-10
OUTLINE ........................................................... T-10
STRUCTURAL VIEW......................................... T-10
SYSTEM WIRING DIAGRAM ............................ T-11
THEFT-DETERRENT SYSTEM............................ T-11
OUTLINE ........................................................... T-11
INTRUDER SENSOR ........................................ T-11
AUDIO AND NAVIGATION SYSTEM.................. T-13
OUTLINE ........................................................... T-13
STRUCTURAL VIEW......................................... T-13
CRUISE CONTROL SYSTEM.............................. T-13
OUTLINE ........................................................... T-13
AIR BAG SYSTEM............................................... T-13
OUTLINE ........................................................... T-13
OUTLINE.............................................................. T-14
SUPPLEMENTAL SERVICE INFORMATION ... T-14
LOCATION INDEX............................................... T-15
POWER SYSTEM.............................................. T-15
EXTERIOR LIGHTING SYSTEM ....................... T-15
INTERIOR LIGHTING SYSTEM ........................ T-16
WIPER AND WASHER SYSTEM ...................... T-16
WARNING AND INDICATOR SYSTEM............. T-17
THEFT-DETERRENT SYSTEM ........................ T-17
AUDIO AND NAVIGATION SYSTEM ................ T-18
AIR BAG SYSTEM............................................. T-18
POWER SYSTEM................................................. T-19
RELAY LOCATION ............................................ T-19
RELAY INSPECTION ........................................ T-19
EXTERIOR LIGHTING SYSTEM.......................... T-20
REAR AUTO LEVELING SENSOR
REMOVAL/INSTALLATION ............................ T-20HIGH-MOUNT BRAKE LIGHT
REMOVAL/INSTALLATION ............................ T-20
INTERIOR LIGHTING SYSTEM........................... T-21
CARGO COMPARTMENT LIGHT
REMOVAL/INSTALLATION ............................ T-21
CARGO COMPARTMENT LIGHT
INSPECTION .................................................. T-22
WIPER AND WASHER......................................... T-22
REAR WIPER MOTOR
REMOVAL/INSTALLATION ............................ T-22
REAR WIPER MOTOR INSPECTION ............... T-22
REAR WIPER ARM AND BLADE
REMOVAL/INSTALLATION ............................ T-23
REAR WIPER ARM AND BLADE
ADJUSTMENT ................................................ T-24
REAR WASHER NOZZLE
REMOVAL/INSTALLATION ............................ T-24
REAR WASHER NOZZLE ADJUSTMENT ........ T-25
REAR WASHER HOSE
REMOVAL/INSTALLATION ............................ T-25
INTERMITTENT REAR WIPER RELAY
REMOVAL/INSTALLATION ............................ T-26
WARNING AND INDICATOR SYSTEM............... T-27
FUEL GAUGE SENDER UNIT
REMOVAL/INSTALLATION ............................ T-27
FUEL GAUGE SENDER UNIT INSPECTION.... T-28
THEFT-DETERRENT SYSTEM............................ T-29
INTRUDER SENSOR
REMOVAL/INSTALLATION ............................ T-29
AUDIO AND NAVIGATION SYSTEM.................. T-30
NOISE FILTER REMOVAL/INSTALLATION ..... T-30
CONDENSER REMOVAL/INSTALLATION ....... T-30
ANTENNA FEEDER LOCATION ....................... T-31
REAR ANTENNA FEEDER INSPECTION ........ T-31
AIR BAG SYSTEM............................................... T-32
SERVICE WARNINGS....................................... T-32
CURTAIN AIR BAG MODULE
REMOVAL/INSTALLATION ............................ T-35
AIR BAG MODULE AND PRE-TENSIONER
SEAT BELT DEPLOYMENT PROCEDURES. T-35
ON-BOARD DIAGNOSTIC
[MULTIPLEX COMMUNICATION SYSTEM].... T-39
MULTIPLEX COMMUNICATION SYSTEM ....... T-39
DTC TABLE ....................................................... T-41
PID/DATA MONITOR TABLE ............................ T-41
PROCEDURES FOR DETERMINING
THE LOCATION OF A MALFUNCTION ......... T-42
DTC U0073, U1900, U2516 ............................... T-45 FEATURES
SERVICE
Page 838 of 909
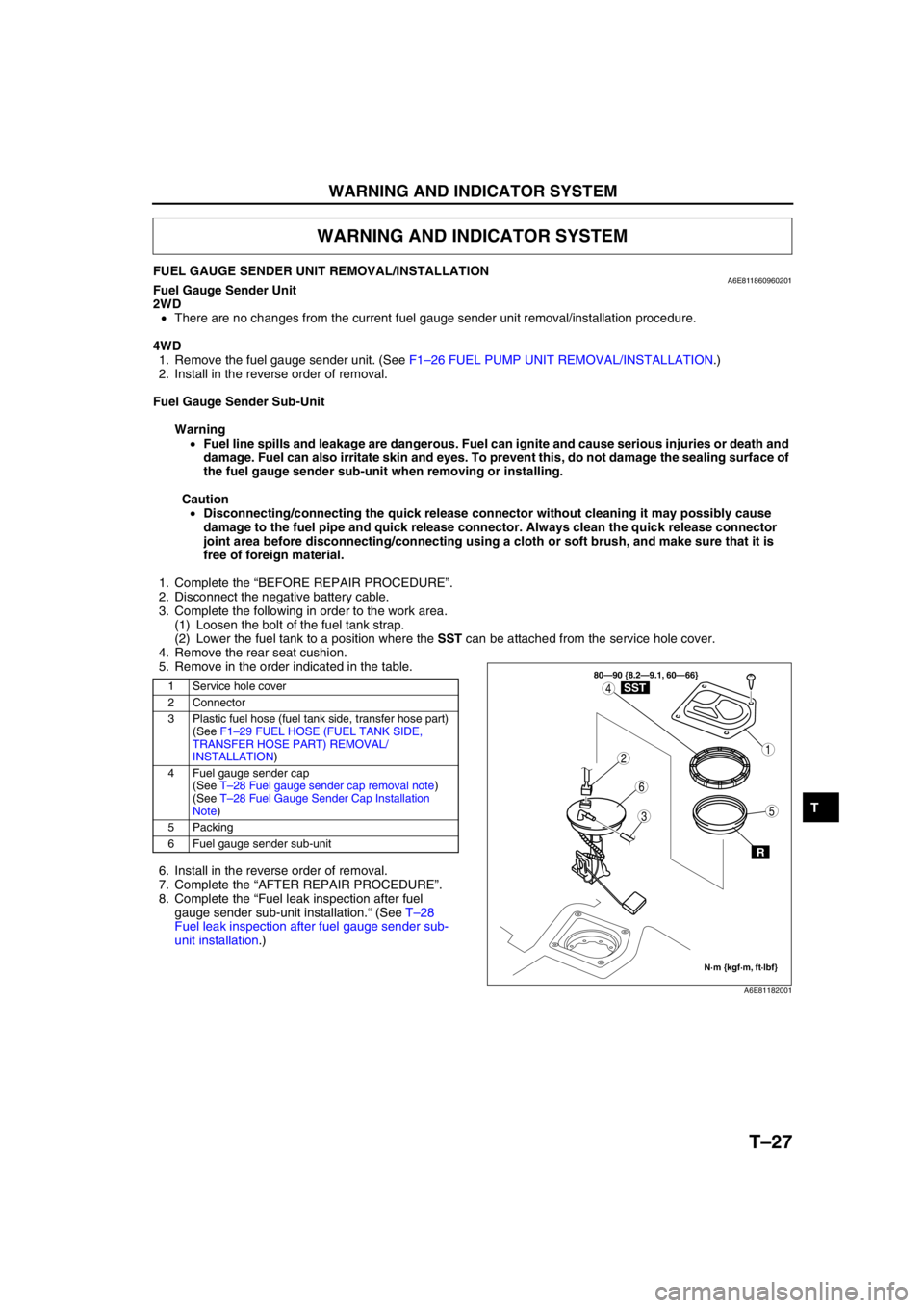
WARNING AND INDICATOR SYSTEM
T–27
T
FUEL GAUGE SENDER UNIT REMOVAL/INSTALLATIONA6E811860960201Fuel Gauge Sender Unit
2WD
•There are no changes from the current fuel gauge sender unit removal/installation procedure.
4WD
1. Remove the fuel gauge sender unit. (See F1–26 FUEL PUMP UNIT REMOVAL/INSTALLATION.)
2. Install in the reverse order of removal.
Fuel Gauge Sender Sub-Unit
Warning
•Fuel line spills and leakage are dangerous. Fuel can ignite and cause serious injuries or death and
damage. Fuel can also irritate skin and eyes. To prevent this, do not damage the sealing surface of
the fuel gauge sender sub-unit when removing or installing.
Caution
•Disconnecting/connecting the quick release connector without cleaning it may possibly cause
damage to the fuel pipe and quick release connector. Always clean the quick release connector
joint area before disconnecting/connecting using a cloth or soft brush, and make sure that it is
free of foreign material.
1. Complete the “BEFORE REPAIR PROCEDURE”.
2. Disconnect the negative battery cable.
3. Complete the following in order to the work area.
(1) Loosen the bolt of the fuel tank strap.
(2) Lower the fuel tank to a position where the SST can be attached from the service hole cover.
4. Remove the rear seat cushion.
5. Remove in the order indicated in the table.
6. Install in the reverse order of removal.
7. Complete the “AFTER REPAIR PROCEDURE”.
8. Complete the “Fuel leak inspection after fuel
gauge sender sub-unit installation.“ (See T–28
Fuel leak inspection after fuel gauge sender sub-
unit installation.)
WARNING AND INDICATOR SYSTEM
1 Service hole cover
2 Connector
3 Plastic fuel hose (fuel tank side, transfer hose part)
(See F1–29 FUEL HOSE (FUEL TANK SIDE,
TRANSFER HOSE PART) REMOVAL/
INSTALLATION)
4 Fuel gauge sender cap
(See T–28 Fuel gauge sender cap removal note)
(See T–28 Fuel Gauge Sender Cap Installation
Note)
5 Packing
6 Fuel gauge sender sub-unit
3
1
4
5
6
2
80—90 {8.2—9.1, 60—66}
N·m {kgf·m, ft·lbf}
R
SST
A6E81182001