ignition MITSUBISHI LANCER 2006 User Guide
[x] Cancel search | Manufacturer: MITSUBISHI, Model Year: 2006, Model line: LANCER, Model: MITSUBISHI LANCER 2006Pages: 800, PDF Size: 45.03 MB
Page 93 of 800
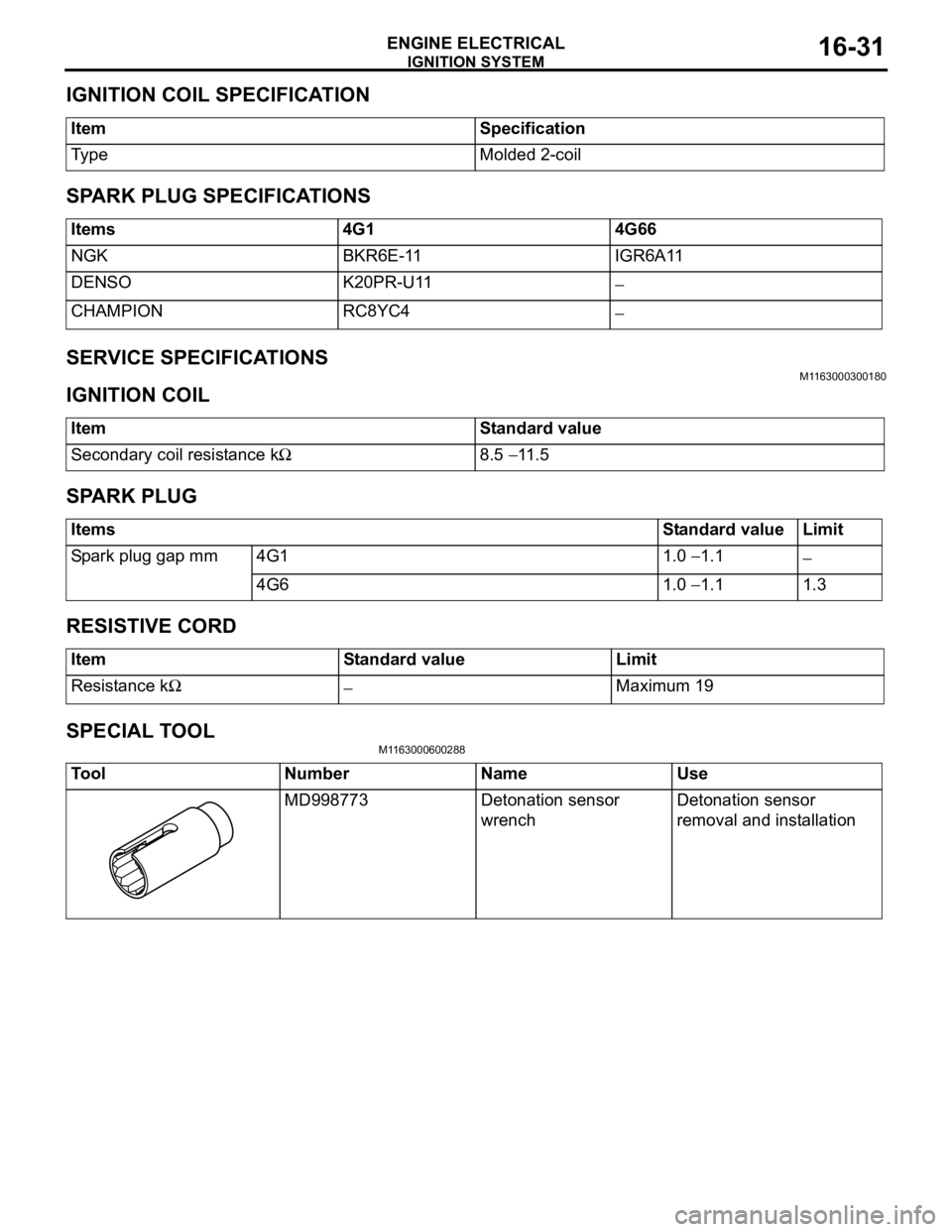
IGNITION SYSTEM
ENGINE ELECTRICAL16-31
IGNITION COIL SPECIFICATION
ItemSpecification
Ty p eMolded 2-coil
SPARK PLUG SPECIFICATIONS
Items4G14G66
NGKBKR6E-11IGR6A11
DENSOK20PR-U11−
CHAMPIONRC8YC4−
SERVICE SPECIFICATIONSM1163000300180
IGNITION COIL
ItemStandard value
Secondary coil resistance kΩ8.5 − 11.5
SPARK PLUG
ItemsStandard valueLimit
Spark plug gap mm4G11.0 − 1.1−
4G61.0 − 1.11.3
RESISTIVE CORD
ItemStandard valueLimit
Resistance kΩ−Maximum 19
SPECIAL TOOL
M1163000600288
ToolNumberNameUse
MD998773Detonation sensor
wrenchDetonation sensor
removal and installation
Page 94 of 800
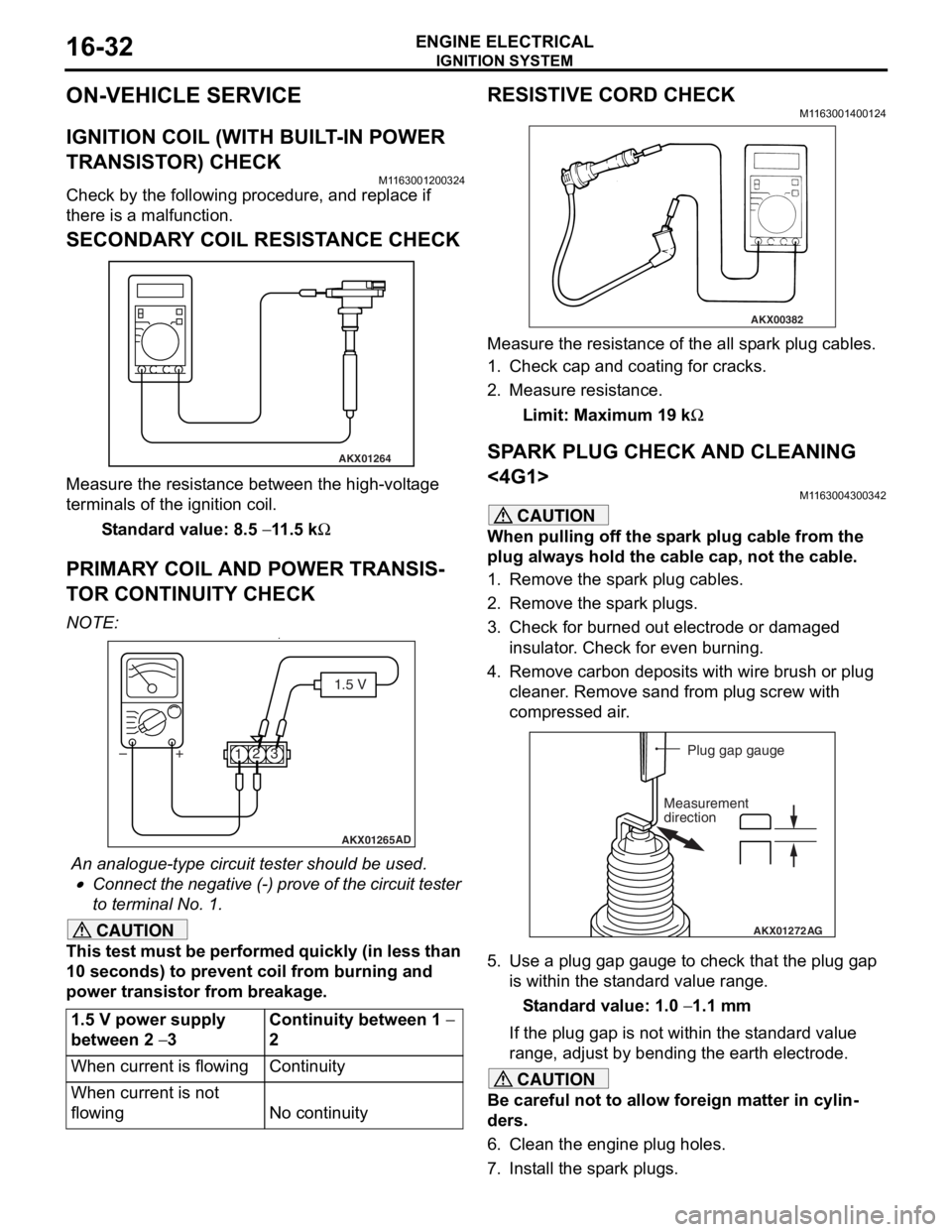
IGNITION SYSTEM
ENGINE ELECTRICAL16-32
ON-VEHICLE SERVICE
IGNITION COIL (WITH BUILT-IN POWER
TRANSISTOR) CHECK
M1163001200324
Check by the following procedure, and replace if
there is a malfunction.
SECONDARY COIL RESISTANCE CHECK
AKX01264
Measure the resist ance bet we en the high- volt ag e
terminals of th
e ign i tio n coil.
St andard va lue: 8.5 − 11 .5 kΩ
PRIM AR Y COIL AND POWER TRANSIS-
TO R CONTINUITY CHECK
NO TE: .•
AKX01265 AD
1.5 V
1 23
+
–
An analogue-t y pe circuit t e ster shou ld be use d .
•Connect the n egative (-) pro v e of the circuit t e ster
to t
e rminal No. 1.
CAUTION
This test must be performed quickly (in less than
10 seconds) to prevent coil from burning and
power transistor from breakage.
1.5 V power supply
between 2
− 3
Continuity between 1 −
2
When current is flowingContinuity
When current is not
flowing
No continuity
RESISTIVE CORD CHECK
M1163001400124
AKX00382
Measure the resistance of the all spark plug cables.
1. Check cap and coating for cracks.
2. Measure resistance.
Limit: Maximum 19 kΩ
SPARK PLUG CHECK AND CLEANING
<4G1>
M1163004300342
CAUTION
When pulling off the spark plug cable from the
plug always hold the cable cap, not the cable.
1. Remove the spark plug cables.
2. Remove the spark plugs.
3. Check for burned out electrode or damaged insulator. Check for even burning.
4. Remove carbon deposits with wire brush or plug cleaner. Remove sand from plug screw with
compressed air.
AKX01272 AG
Plug gap gauge
Measurement
direction
5. Use a plug gap gauge to check that the plug gap is within the standard value range.
Standard value: 1.0 − 1.1 mm
If the plug gap is not within the standard value
range, adjust by bending the earth electrode.
CAUTION
Be careful not to allow foreign matter in cylin-
ders.
6. Clean the engine plug holes.
7. Install the spark plugs.
Page 95 of 800
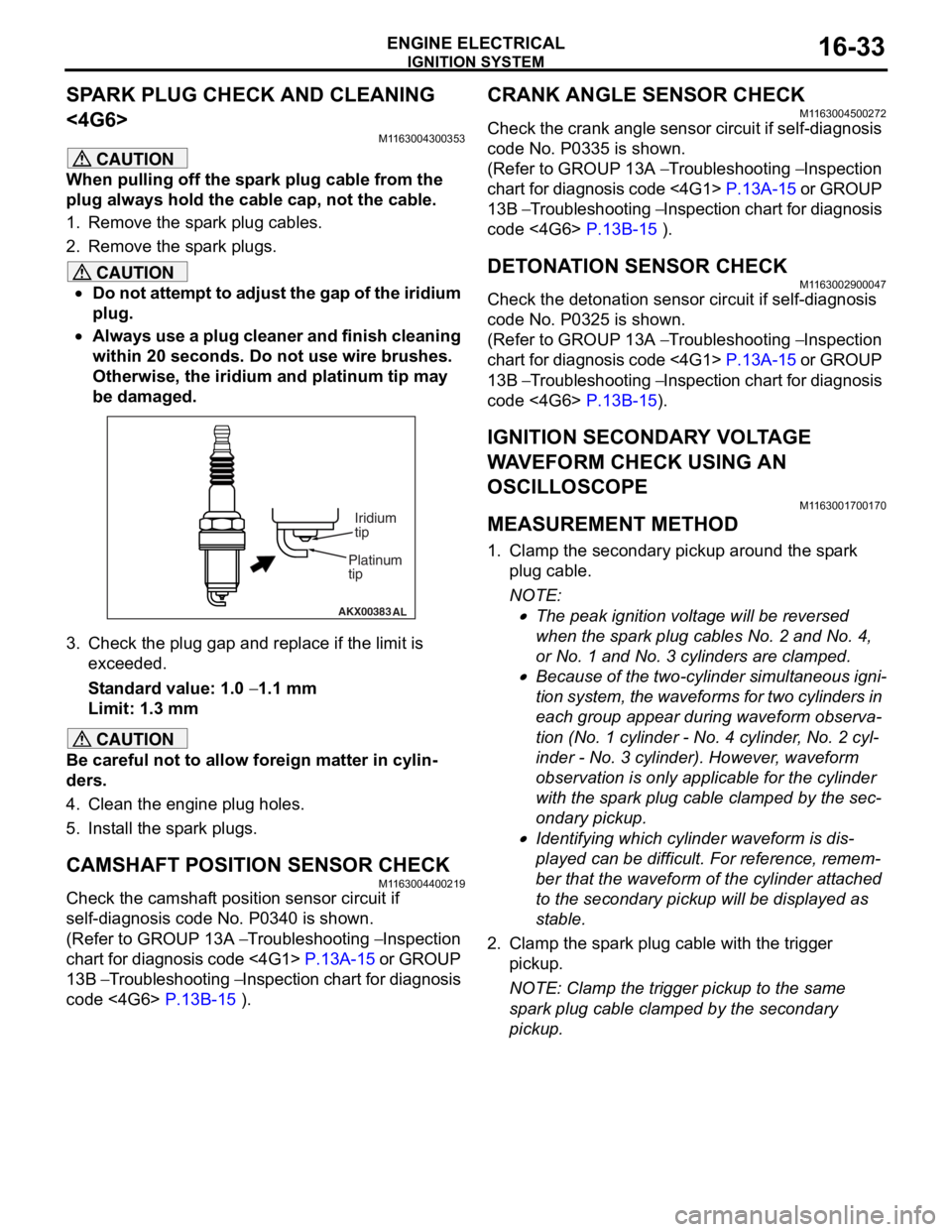
IGNITION SYSTEM
ENGINE ELECTRICAL16-33
SPARK PLUG CHECK AND CLEANING
<4G6>
M1163004300353
CAUTION
When pulling off the spark plug cable from the
plug always hold the cable cap, not the cable.
1. Remove the spark plug cables.
2. Remove the spark plugs.
CAUTION
•Do not attempt to adjust the gap of the iridium
plug.
•
AKX00383 AL
Platinum
tipIridium
tip
Always use a plug cleaner and finish cleaning
within 20 seconds. Do not use wire brushes.
Otherwise, the iridium and platinum tip may
be damaged.
3. Check the plug gap and re
place if the limit is
exceeded.
Standard value: 1.0 − 1.1 mm
Limit: 1.3 mm
CAUTION
Be careful not to allow foreign matter in cylin-
ders.
4. Clean the engine plug holes.
5. Install the spark plugs.
CAMSHAFT POSITION SENSOR CHECK
M1163004400219
Check the camshaft position sensor circuit if
self-diagnosis code No. P0340 is shown.
(Refer to GROUP 13A − Troubleshooting − Inspection
chart for diagnosis code <4G1>
P.13A-15 or GROUP
13B − Troubleshooting − Inspection chart for diagnosis
code <4G6>
P.13B-15 ).
CRANK ANGLE SENSOR CHECK
M1163004500272
Check the crank angle sensor circuit if self-diagnosis
code No. P0335 is shown.
(Refer to GROUP 13A − Troubleshooting − Inspection
chart for diagnosis code <4G1>
P.13A-15 or GROUP
13B − Troubleshooting − Inspection chart for diagnosis
code <4G6>
P.13B-15 ).
DETONATION SENSOR CHECKM1163002900047
Check the detonation sensor circuit if self-diagnosis
code No. P0325 is shown.
(Refer to GROUP 13A − Troubleshooting − Inspection
chart for diagnosis code <4G1>
P.13A-15 or GROUP
13B − Troubleshooting − Inspection chart for diagnosis
code <4G6>
P.13B-15).
IGNITION SECONDARY VOLTAGE
WAVEFORM CHECK USING AN
OSCILLOSCOPE
M1163001700170
MEASUREMENT METHOD
1. Clamp the secondary pickup around the spark
plug cable.
NOTE: .
•The peak ignition voltage will be reversed
when the spark plug cables No. 2 and No. 4,
or No. 1 and No. 3 cylinders are clamped.
•Because of the two-cylinder simultaneous igni-
tion system, the waveforms for two cylinders in
each group appear during waveform observa
-
tion (No. 1 cylinder - No. 4 cylinder, No. 2 cyl-
inder - No. 3 cylinder). However, waveform
observation is only applicable for the cylinder
with the spark plug cable clamped by the sec
-
ondary pickup.
•Identifying which cylinder waveform is dis-
played can be difficult. For reference, remem-
ber that the waveform of the cylinder attached
to the secondary pickup will be displayed as
stable.
2. Clamp the spark plug cable with the trigger pickup.
NOTE: Clamp the trigger pickup to the same
spark plug cable clamped by the secondary
pickup.
Page 96 of 800
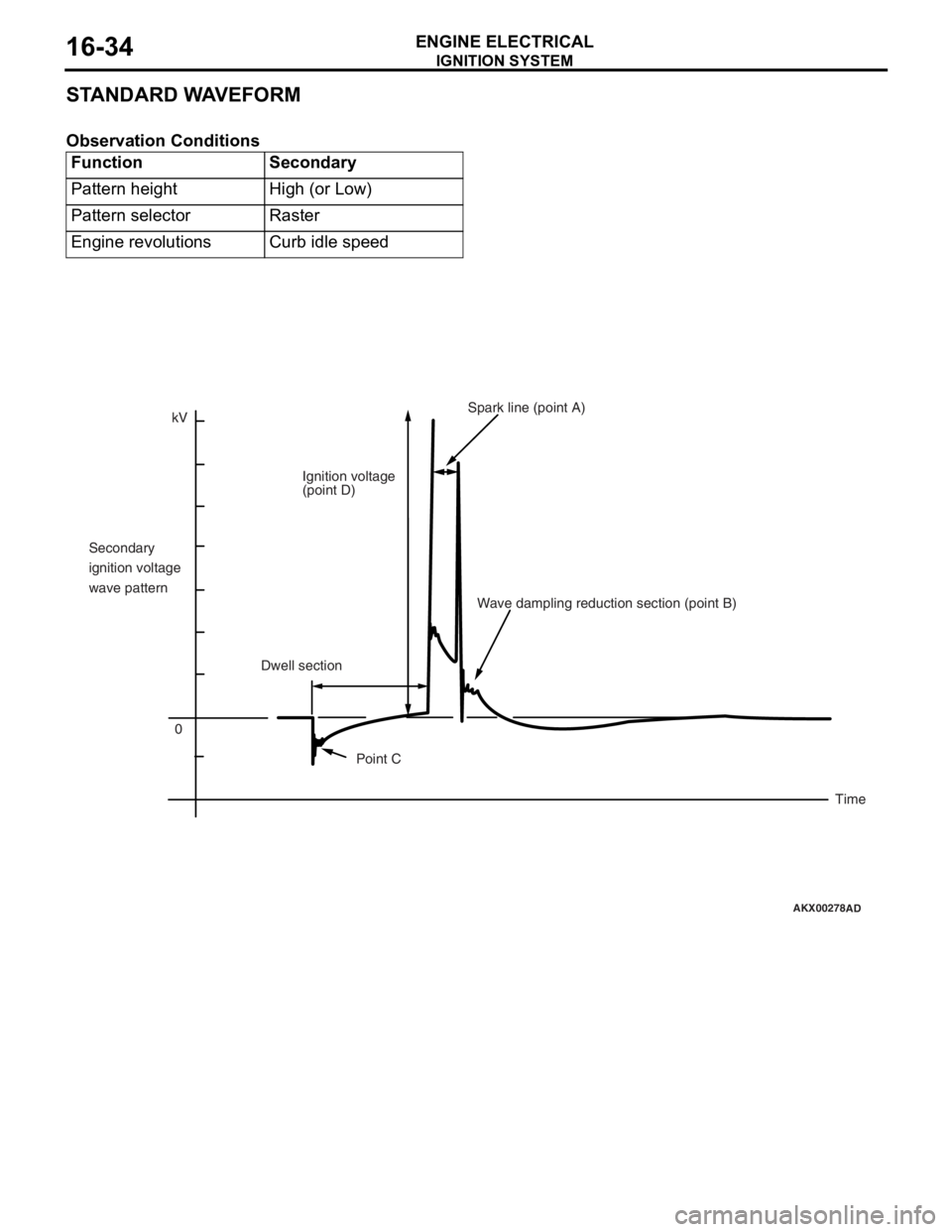
IGNITION SYSTEM
ENGINE ELECTRICAL16-34
STANDARD WAVEFORM
Observation Conditions
FunctionSecondary
Pattern heightHigh (or Low)
Pattern selectorRaster
Engine revolutionsCurb idle speed
AKX00278
kV0
Secondary
ignition voltage
wave pattern
Ignition voltage
(point D)
Spark line (point A)
Dwell section Wave dampling reduction section (point B)
Point C Time
AD
Page 97 of 800
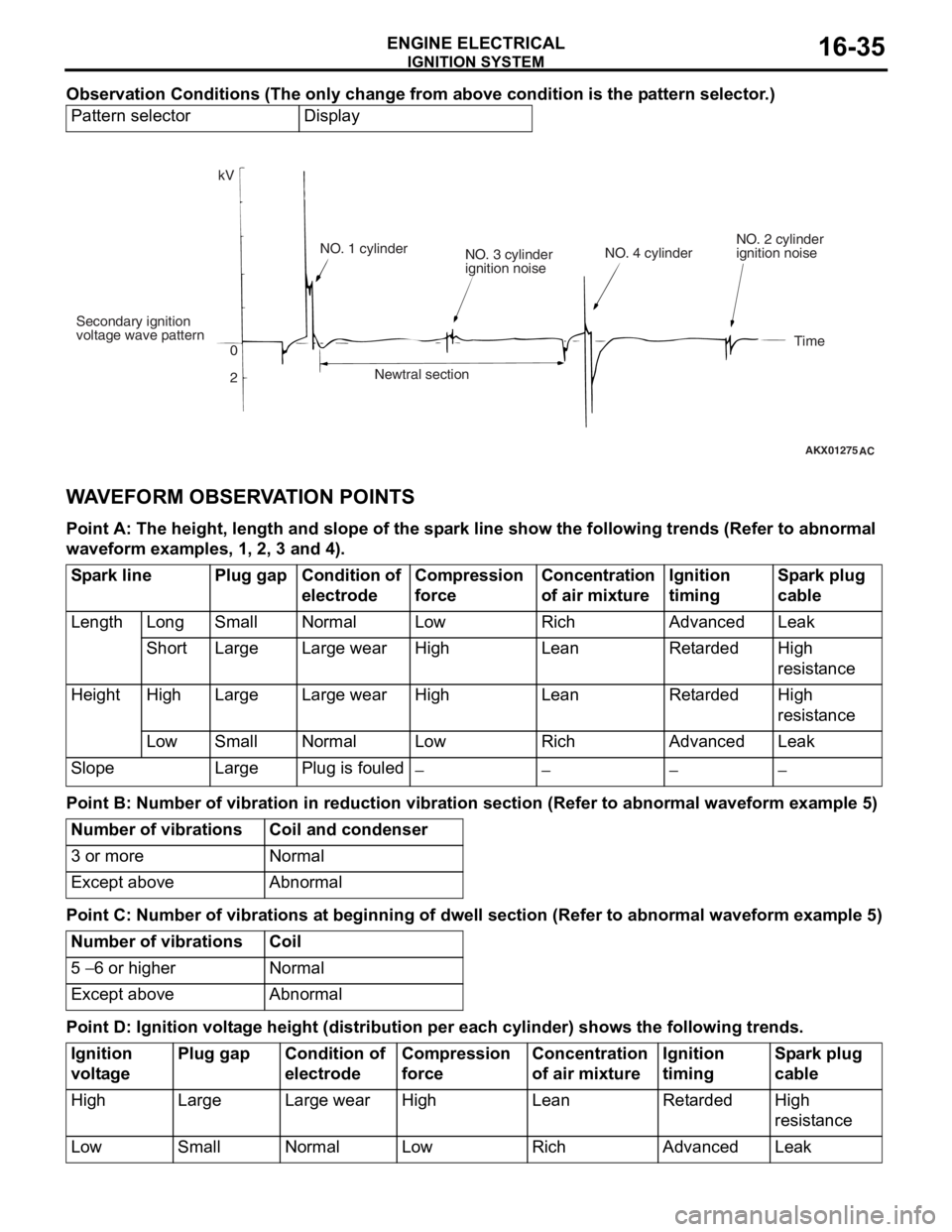
IGNITION SYSTEM
ENGINE ELECTRICAL16-35
Observation Conditions (The only change from above condition is the pattern selector.)
Pattern selectorDisplay
AKX01275
kV
Secondary ignition
voltage wave pattern 0
2NO. 1 cylinder
NO. 3 cylinder
ignition noise
Newtral section NO. 4 cylinder
NO. 2 cylinder
ignition noise
Time
AC
WA VEFORM OBSER V A T ION POINTS
Point A: The he ight, len g th and s l ope of th e sp a r k line sho w the following trends (Re f er to abnorma l
wave
form exam ples, 1 , 2, 3 a nd 4).
Spark linePlug gapCondition of
electrodeCompression
force Concentration
of air mixtureIgnition
timingSpark plug
cable
LengthLongSmallNormalLowRichAdvancedLeak
ShortLargeLarge wearHigh LeanRetardedHigh
resistance
HeightHighLargeLarge wearHighLeanRetardedHigh
resistance
LowSmallNormalLow RichAdvancedLeak
SlopeLargePlug is fouled−−−−
Point B: Number of v i bra t ion in red uction vi bra t ion sec tion (Refer to a bnormal wavefo r m examp l e 5)
Number of vibrationsCoil and condenser
3 or moreNormal
Except aboveAbnormal
Point C: Number of v i bra t ions a t beginnin g of dwell se ction (Refer to a bnormal wave form exam ple 5)
Number of vibrationsCoil
5 − 6 or higherNormal
Except aboveAbnormal
Point D: Ignition volt a g e height (distribution per each cylinder) s hows the follo wing tren ds.
Ignition
voltagePlug gapCondition of
electrodeCompression
forceConcentration
of air mixtureIgnition
timingSpark plug
cable
HighLargeLarge wearHighLeanRetardedHigh
resistance
LowSmallNormalLowRichAdvancedLeak
Page 98 of 800
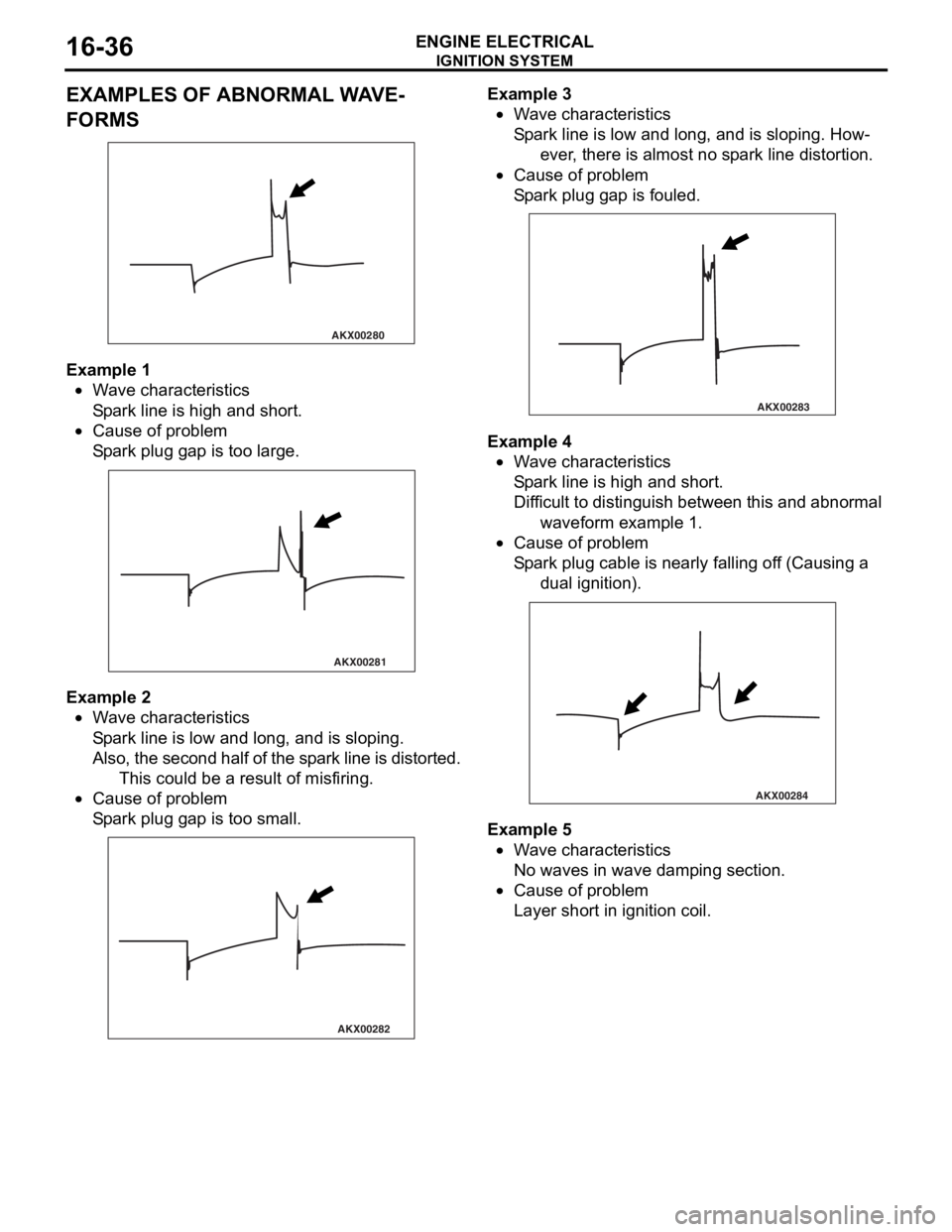
IGNITION SYSTEM
ENGINE ELECTRICAL16-36
EXAMPLES OF ABNORMAL WAVE-
FORMS
AKX00280
Example 1
•Wa ve ch aracte rist ics
Sp a r k line is high an d sh ort.
•Cause of pr oblem
Sp a r k plug ga p is too large.
AKX00281
Example 2
•Wa ve ch aracte rist ics
Sp a r k line is low and long, a nd is sloping.
Also, the secon d half of the sp ark line is distorted.
This cou l d be a result o f misfiring.
•Cause of pr oblem
Sp a r k plug ga p is too small.
AKX00282
Example 3
•Wa ve ch aracte rist ics
Sp a r k line is low and long, a nd is sloping. How-
ever, there is a l mo st no sp ark lin e distortion.
•Cause of pr oblem
Sp a r k plug ga p is fouled.
AKX00283
Example 4
•Wa ve ch aracte rist ics
Sp a r k line is high an d sh ort.
Diff icu l t to distingu ish be twe en this an d a bnormal
wa vefor m examp l e 1.
•Cause of pr oblem
Sp a r k plug cable is nearly fallin g of f (Ca u sing a
dual ignition ).
AKX00284
Example 5
•Wa ve ch aracte rist ics
No waves in wave damp i ng section.
•Cause of pr oblem
Layer short in ign i tio n coil.
Page 99 of 800

IGNITION SYSTEM
ENGINE ELECTRICAL16-37
IGNITION COIL RELAY CHECK
M1163006500018
AC301727
2 1
3
4
AC304311AB
Battery
Ignition coil relay
Battery
voltageTerminal No.to
be connected
to testerContinuity test
results
Not applied1 − 4Open circuit
Connect
terminal No.2
and battery (+)
terminal.
Connect
terminal No.3
and battery (
−)
terminal.
1 − 4Less than 2
ohms
Page 100 of 800
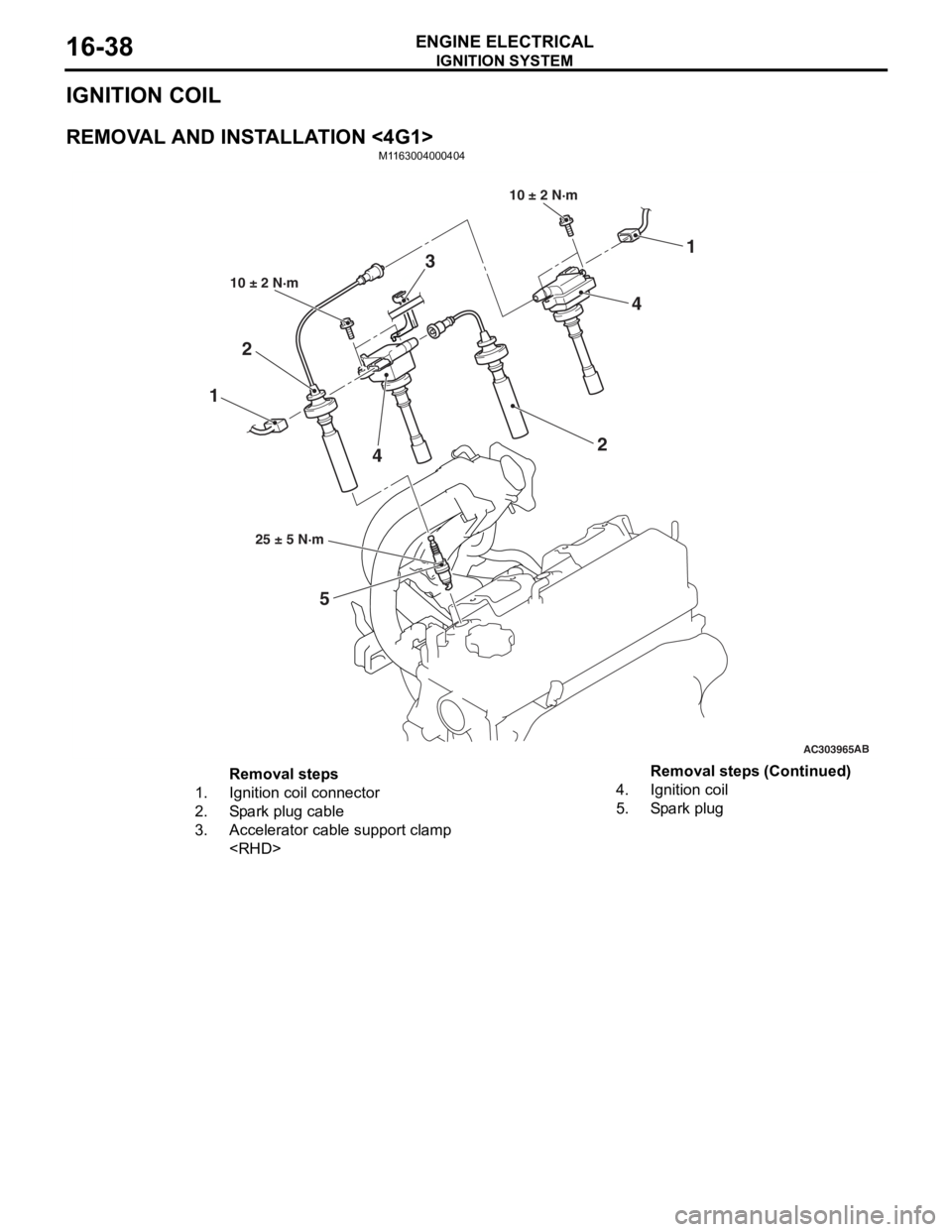
IGNITION SYSTEM
ENGINE ELECTRICAL16-38
IGNITION COIL
REMOVAL AND INSTALLATION <4G1>
M1163004000404
AC303965AB
11
5
2
2
10 ± 2 N·m
10 ± 2 N·m
25 ± 5 N·m
3
4
4
Removal steps
1.Ignition coil connector
2.Spark plug cable
3.Accelerator cable support clamp
4.Ignition coil
5.Spark plug
Removal steps (Continued)
Page 101 of 800
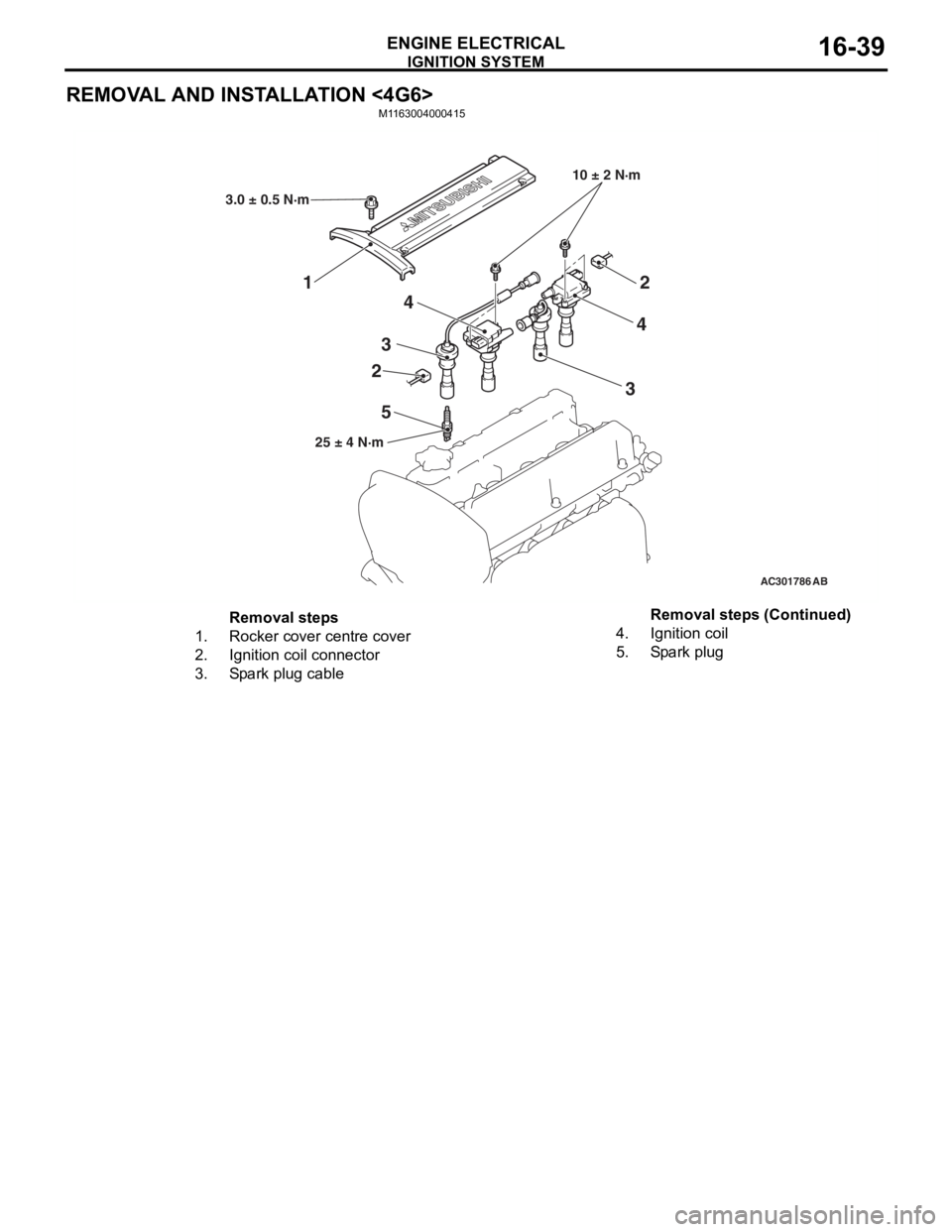
IGNITION SYSTEM
ENGINE ELECTRICAL16-39
REMOVAL AND INSTALLATION <4G6>
M1163004000415
AC301786
10 ± 2 N·m
25 ± 4 N·m
5 4
2 2
3
3
4
AB
1
3.0 ± 0.5 N·m
Removal steps
1.Rocker cover centre cover
2.Ignition coil connector
3.Spark plug cable
4.Ignition coil
5.Spark plug
Removal steps (Continued)
Page 102 of 800
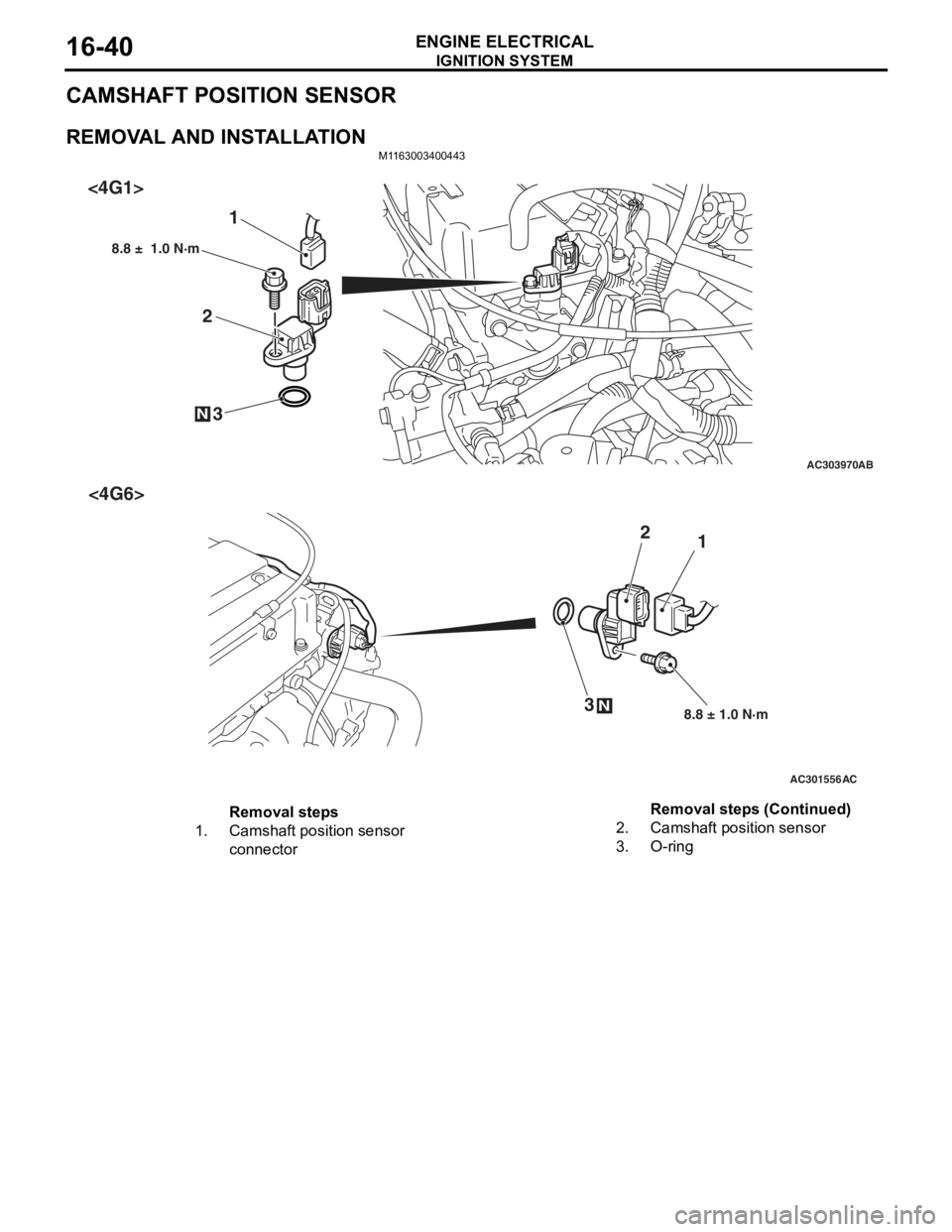
IGNITION SYSTEM
ENGINE ELECTRICAL16-40
CAMSHAFT POSITION SENSOR
REMOVAL AND INSTALLATION
M1163003400443
AC303970AB
23
8.8 ± 1.0 N·m
N
1
<4G1>
AC301556
N
1
2
3
8.8 ± 1.0 N·m
AC
<4G6>
Removal steps
1.Camshaft position sensor
connector2.Camshaft position sensor
3.O-ring
Removal steps (Continued)