ISC MITSUBISHI LANCER 2006 Service Manual
[x] Cancel search | Manufacturer: MITSUBISHI, Model Year: 2006, Model line: LANCER, Model: MITSUBISHI LANCER 2006Pages: 800, PDF Size: 45.03 MB
Page 197 of 800
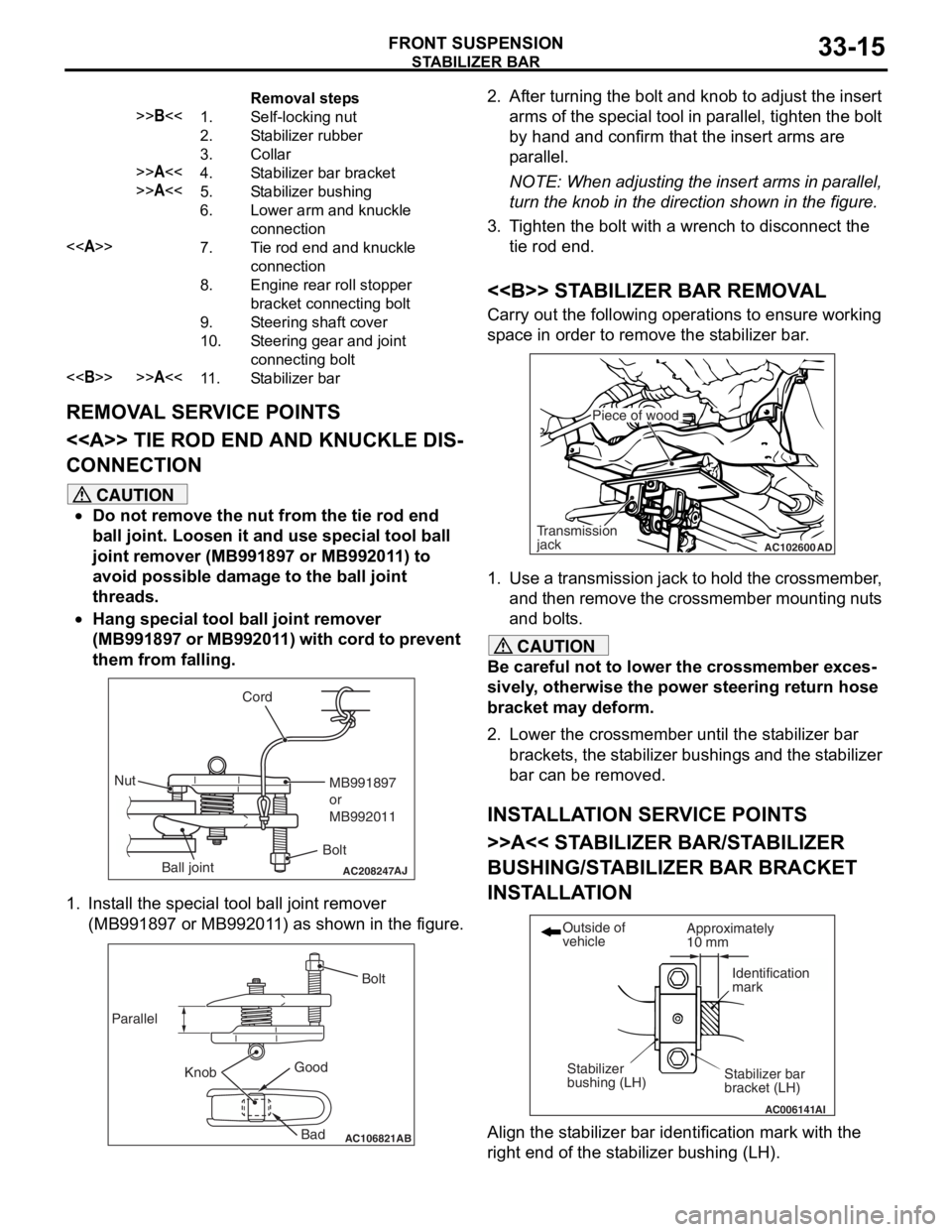
Removal steps
>>B<<1.Self-locking nut
2.Stabilizer rubber
3.Collar
>>A<<4.Stabilizer bar bracket
>>A<<5.Stabilizer bushing
6.Lower arm and knuckle
connection
<>7.Tie rod end and knuckle
connection
8.Engine rear roll stopper
bracket connecting bolt
9.Steering shaft cover
10.Steering gear and joint
connecting bolt
<>>>A<<11 .Stabilizer bar
STABILIZER BA R
FRONT SU SPENSION33-15
REMOVA L SER V ICE POINTS
<> TIE ROD END AND KNUCKLE DIS-
CONNECTION
CAUTION
•Do not remove the nut from the tie rod end
ball joint. Loosen it and use special tool ball
joint remover (MB991897 or MB992011) to
avoid possible damage to the ball joint
threads.
•
AC208247AJ
Cord
BoltMB991897
or
MB992011
Nut
Ball joint
Hang special tool ball joint remover
(MB991897 or MB992011) with cord to prevent
them from falling.
1. Install the special tool ball joint remover (MB991897 or MB992011) as shown in the figure.
AC106821
Knob
Parallel
Bolt
Good Bad
AB
2. After turning the bolt and knob to adjust the insert arms of the special tool in parallel, tighten the bolt
by hand and confirm that the insert arms are
parallel.
NOTE: When adjusting the insert arms in parallel,
turn the knob in the direction shown in the figure.
3. Tighten the bolt with a wrench to disconnect the tie rod end.
<> STABILIZER BAR REMOVAL
Carry out the following operations to ensure working
space in order to remove the stabilizer bar.
AC102600 AD
Piece of wood
Transmission
jack
1. Use a transmission jack to hold the crossmember,
and then remove the crossmember mounting nuts
and bolts.
CAUTION
Be careful not to lower the crossmember exces-
sively, otherwise the power steering return hose
bracket may deform.
2. Lower the crossmember until the stabilizer bar
brackets, the stabilizer bush ings and the stabilizer
bar can be removed.
INSTALLATION SERVICE POINTS
>>A<< STABILIZER BAR/STABILIZER
BUSHING/STABILIZ ER BAR BRACKET
INSTALLATION
AC006141 AI
Stabilizer bar
bracket (LH)
Outside of
vehicle
Stabilizer
bushing (LH) Approximately
10 mm
Identification
mark
Align the stabilizer bar iden
tification mark with the
right end of the stabilizer bushing (LH).
Page 204 of 800
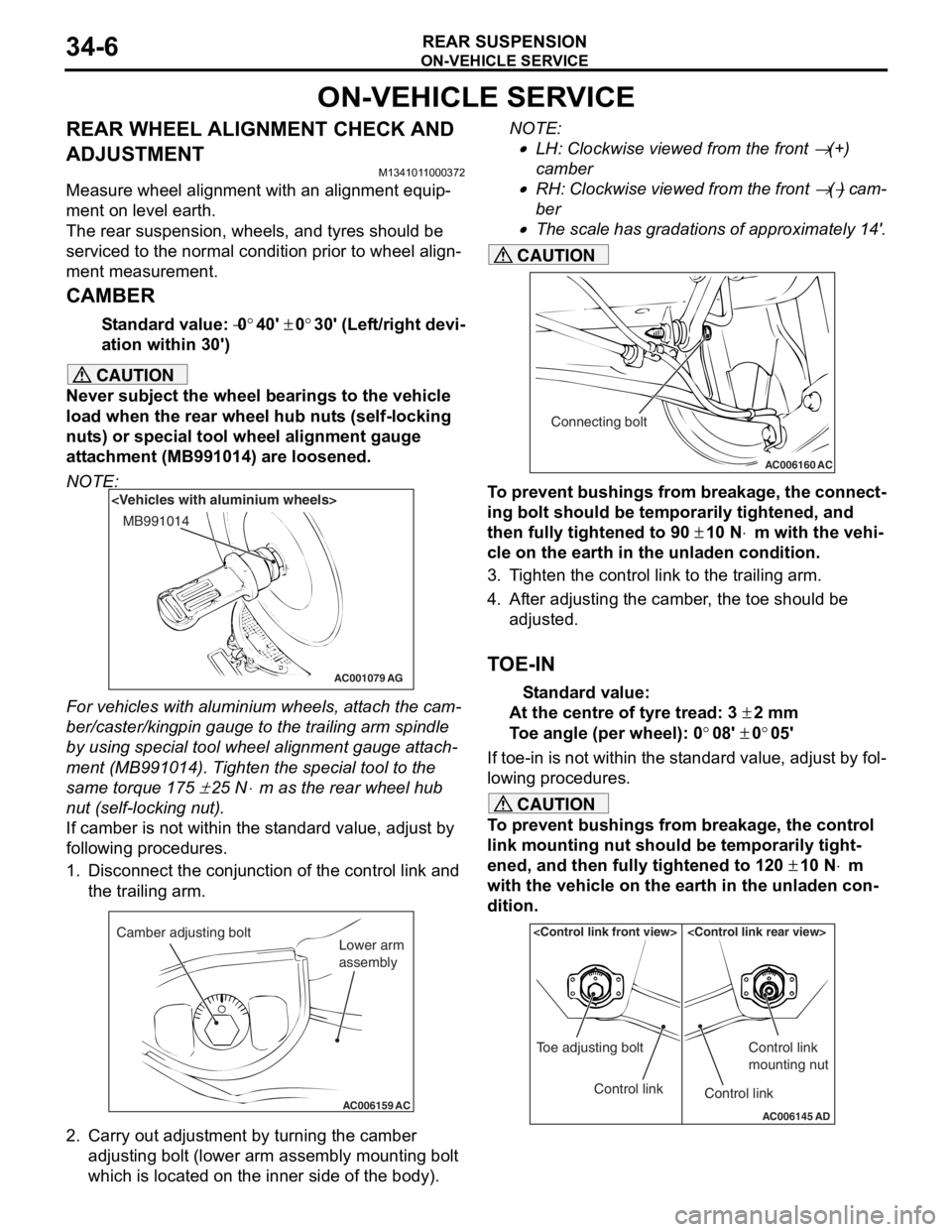
ON-VEHICLE SERVICE
REAR SUSPENSION34-6
ON-VEHICLE SERVICE
REAR WHEEL ALIGNMENT CHECK AND
ADJUSTMENT
M1341011000372
Measure wheel alignment with an alignment equip-
ment on level earth.
The rear suspension, wheels, and tyres should be
serviced to the normal condition prior to wheel align
-
ment measurement.
CAMBER
Standard value: −0°40' ± 0°30' (Left/right devi-
ation within 30')
CAUTION
Never subject the wheel bearings to the vehicle
load when the rear wheel hub nuts (self-locking
nuts) or special tool wheel alignment gauge
attachment (MB991014) are loosened.
NOTE:
AC001079
MB991014
AG
For vehicles with aluminium wheels, attach the cam-
ber/caster/kingpin gauge to the trailing arm spindle
by using special tool wheel alignment gauge attach
-
ment (MB991014). Tighten the special tool to the
same torque 175
± 25 N⋅m as the rear wheel hub
nut (self-locking nut).
If camber is not within the standard value, adjust by
following procedures.
1. Disconnect the conjunction of the control link and the trailing arm.
AC006159 AC
Camber adjusting bolt
Lower arm
assembly
2. Carry out adjustment by turning the camber
adjusting bolt (lower arm assembly mounting bolt
which is located on the inner side of the body).
NOTE: .
•LH: Clockwise viewed from the front → (+)
camber
•RH: Clockwise viewed from the front → (−) cam-
ber
•
AC006160 AC
Connecting bolt
The scale has gradations of approximately 14'.
CAUTION
To prevent bushings from breakage, the connect-
ing bolt should be temporarily tightened, and
then fully tightened to 90
± 10 N⋅m with the vehi-
cle on the earth in the unladen condition.
3. Tighten the control link to the trailing arm.
4. After adjusting the camber, the toe should be
adjusted.
TOE-IN
Standard value:
At the centre of tyre tread: 3 ± 2 mm
Toe angle (per wheel): 0°08' ± 0°05'
If toe-in is not within the standard value, adjust by fol-
lowing procedures.
CAUTION
To prevent bushings from breakage, the control
link mounting nut should be temporarily tight
-
ened, and then fully tightened to 120 ± 10 N⋅m
with the vehicle on the earth in the unladen con
-
dition.
AC006145 AD
Control link
Toe adjusting boltControl link
Control link
mounting nut
Page 207 of 800
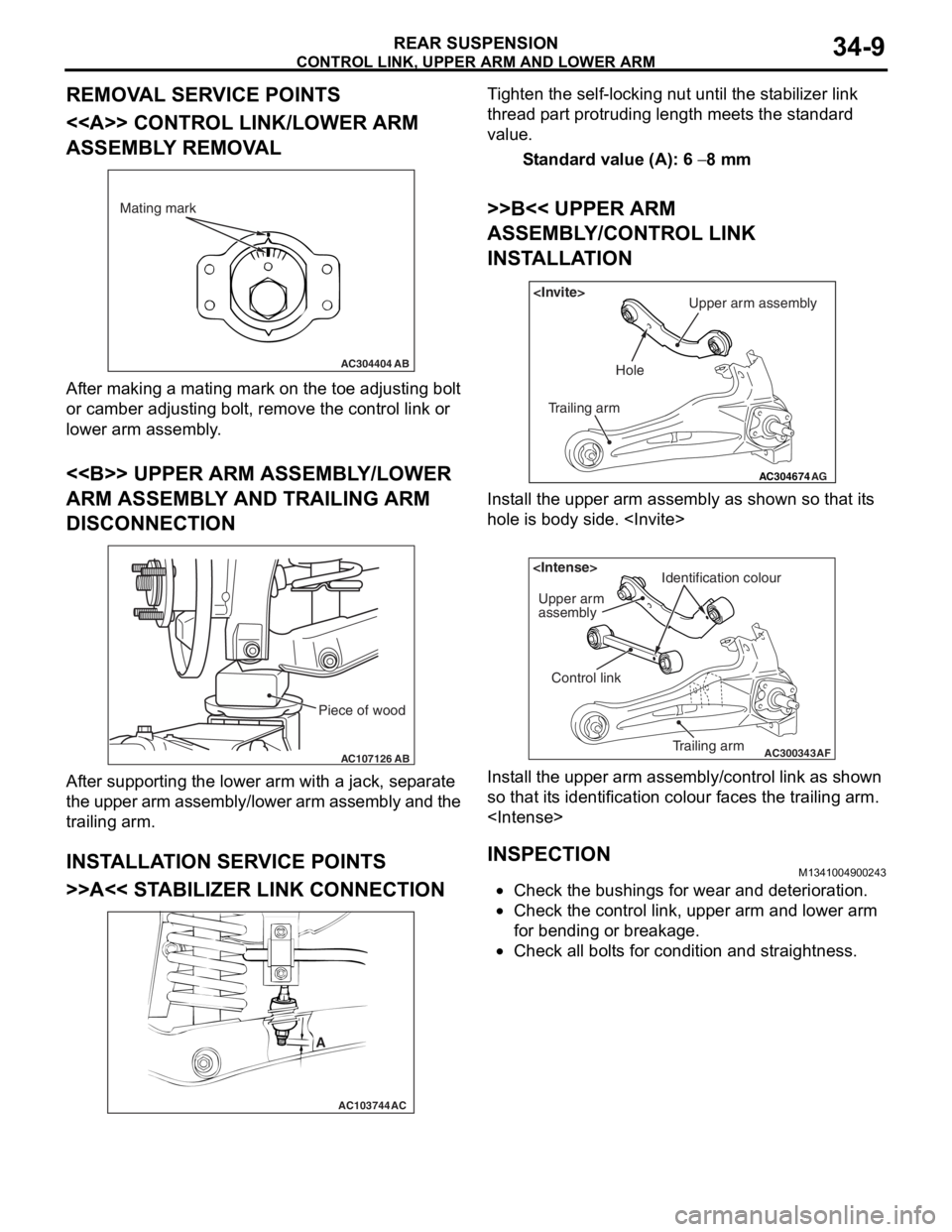
Page 211 of 800
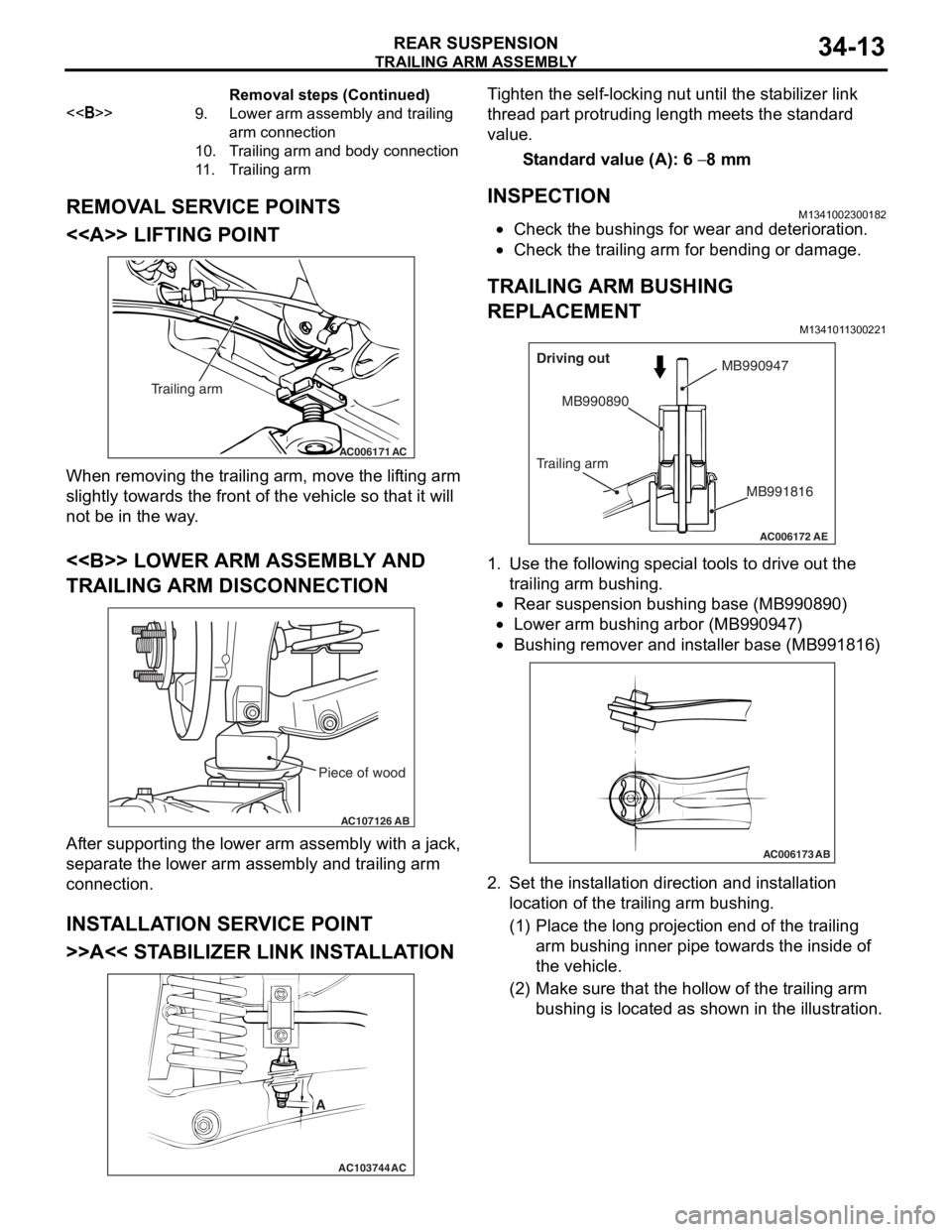
Page 215 of 800
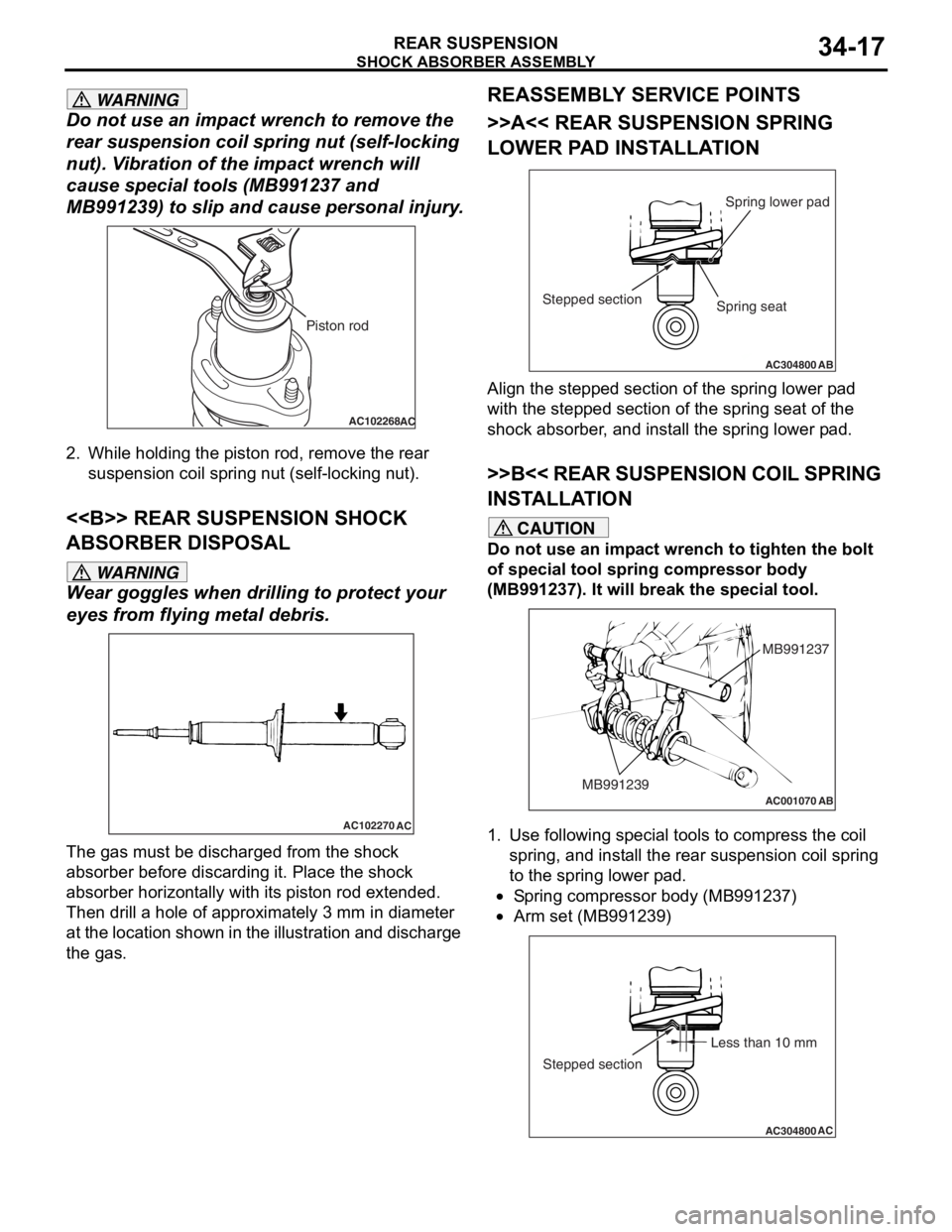
SHOCK ABSORBER ASSEMBLY
REAR SUSPENSION34-17
WARNING
Do not use an impact wrench to remove the
rear suspension coil spring nut (self-locking
nut). Vibration of the impact wrench will
cause special t ools (MB991237 and
MB991239) to slip and cause personal injury.
AC102268AC
Piston rod
2. While holding the piston rod, remove the rear
suspension coil spring nut (self-locking nut).
<> REAR SUSPENSION SHOCK
ABSORBER DISPOSAL
WARNING
Wear goggles when dril ling to protect your
eyes from flying metal debris.
AC102270
AC
The gas must be discharged from the shock
absorber before discarding it. Place the shock
absorber horizontally with its piston rod extended.
Then drill a hole of approximately 3 mm in diameter
at the location shown in the illustration and discharge
the gas.
REASSEMBLY SERVICE POINTS
>>A<< REAR SUSPENSION SPRING
LOWER PAD INSTALLATION
AC304800AB
Spring lower pad
Stepped section
Spring seat
Align the stepped section of the spring lower pad
with the stepped section of the spring seat of the
shock absorber, and install the spring lower pad.
>>B<< REAR SUSPENSION COIL SPRING
INSTALLATION
CAUTION
Do not use an impact wrench to tighten the bolt
of special tool spring compressor body
(MB991237). It will break the special tool.
AC001070
MB991237
MB991239
AB
1. Use following special tools to compress the coil spring, and install the rear suspension coil spring
to the spring lower pad.
•Spring compressor body (MB991237)
•
AC304800AC
Less than 10 mm
Stepped section
Arm set (MB991239)
Page 222 of 800
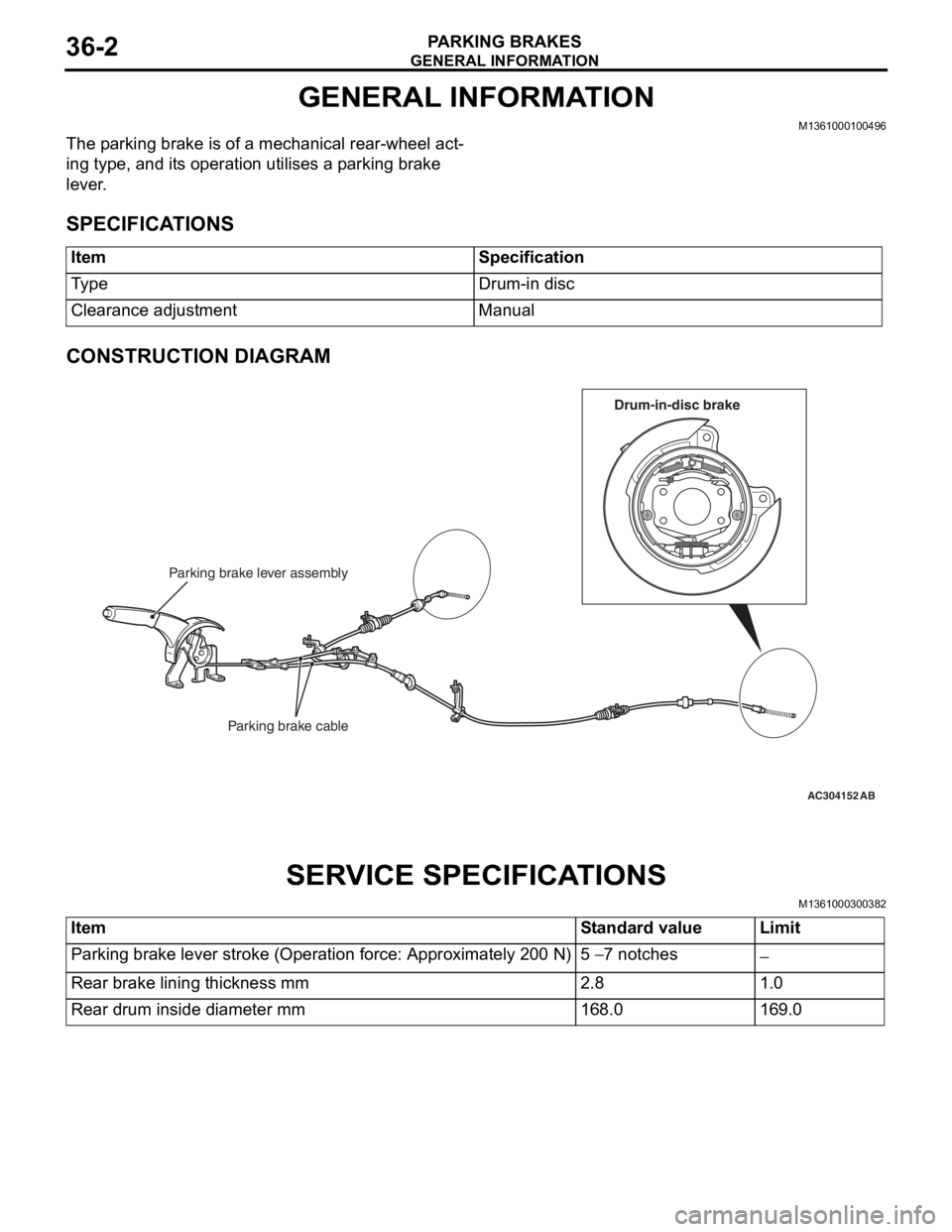
GENERAL INFORMATION
PARKING BRAKES36-2
GENERAL INFORMATION
M1361000100496
The parking brake is of a mechanical rear-wheel act-
ing type, and its operation utilises a parking brake
lever.
SPECIFICATIONS
ItemSpecification
Ty p eDrum-in disc
Clearance adjustmentManual
CONSTRUCTION DIAGRAM
AC211553
AC104333
AC304152
Parking brake lever assembly
Parking brake cable
AB
Drum-in-disc brake
SERV ICE SPECI F ICA T IONS
M13610003 0038 2
ItemStandard valueLimit
Parking brake lever stroke (Operation force: Approximately 200 N)5 − 7 notches−
Rear brake lining thickness mm2.81.0
Rear drum inside diameter mm168.0169.0
Page 223 of 800
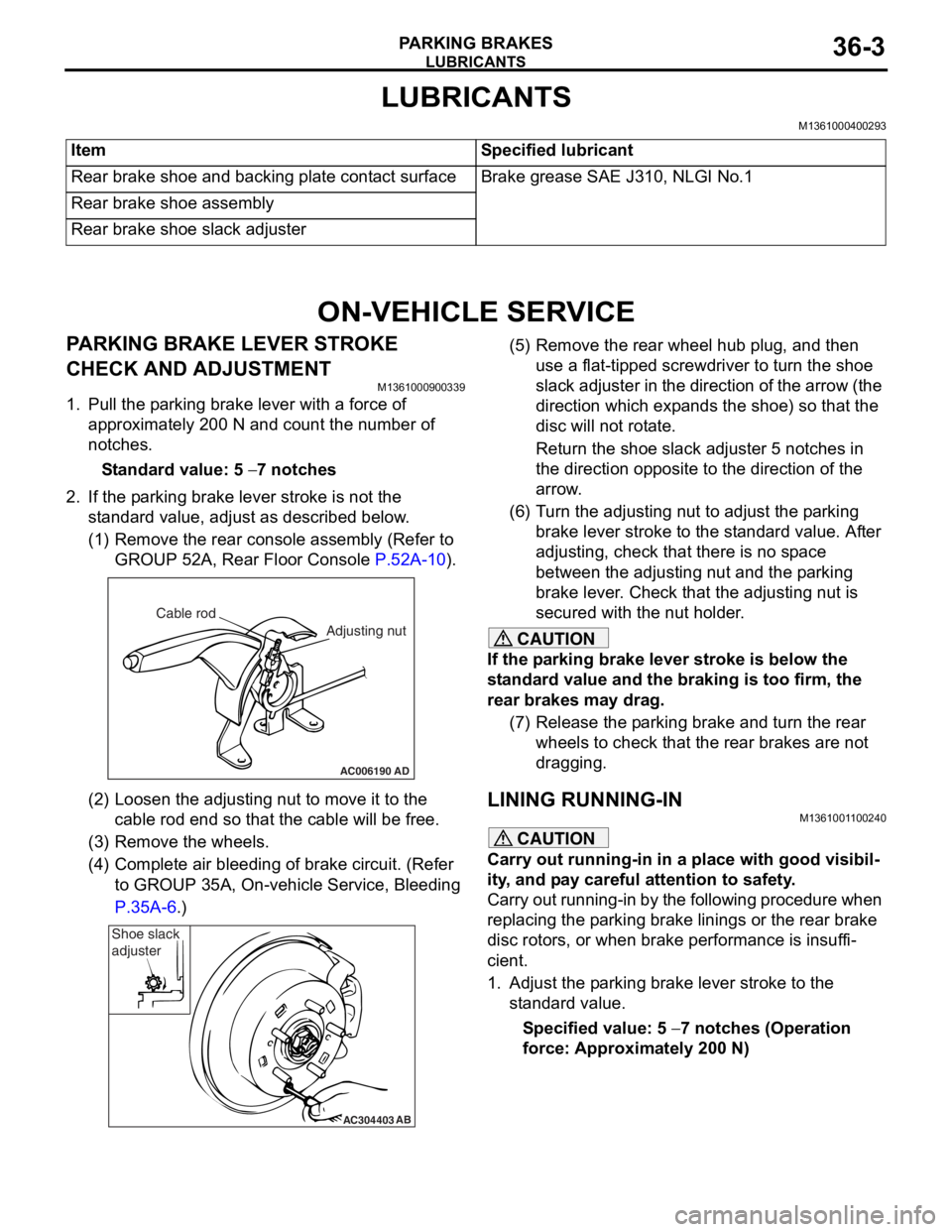
LUBRICANTS
PARKING BRAKES36-3
LUBRICANTS
M1361000400293
ItemSpecified lubricant
Rear brake shoe and backing plate contact surfaceBrake grease SAE J310, NLGI No.1
Rear brake shoe assembly
Rear brake shoe slack adjuster
ON-VEHIC LE SER VI CE
PARKING BRAKE LE VER STROKE
CHECK AND ADJUSTMENT
M13610009 0033 9
1.Pull the p a rkin g brake le ver wit h a force of
ap proxima t ely 200 N an d co unt the number of
no tche s.
St andard va lue: 5 − 7 notches
2.If the p a rking b r ake leve r stro ke is no t the
st a ndard valu e, adjust as de scribed below .
(1)R emove the rear console a sse mbly (Refer to
GROUP 5 2 A, Rear Floor Console
P.52A-10).
AC006190
Cable rod
Adjusting nut
AD
(2)Loosen th e adjusting nu t to move it to th e
cab l e rod end so tha t the cable will be fre e .
(3)R emove the wheels.
(4)C omplete a i r bleedin g of b r ake circuit. (Re f er
to GROUP 35A, On-ve h icle Service, Blee ding
P.35A-6.)
AC304403AB
Shoe slack
adjuster
(5
) R emove the rear whee l hub plug , and then
use a flat-tipped screwdriver to turn the shoe
slack ad juster in the direction of the arrow (the
dire ctio n which exp a nds the shoe) so that the
disc will no t rot a te.
Return the sh oe slack adjust e r 5 not ches in
the d
i rection opposite t o the d i rection of the
arrow
.
(6) T urn th e adjusting nut to adjust the p a rking
brake le ver stroke to the st anda rd value. Af ter
adjusting, check that there is n o sp ace
between the a d justing nut an d the p a rking
brake le ver . Che ck that th e adjusting nut is
secured with the nut ho lder .
CAUTION
If the parking brake lever stroke is below the
standard value and the braking is too firm, the
rear brakes may drag.
(7) Release the parking brake and turn the rear wheels to check that t he rear brakes are not
dragging.
LINING RUNNING-INM1361001100240
CAUTION
Carry out running-in in a place with good visibil-
ity, and pay careful attention to safety.
Carry out running-in by the following procedure when
replacing the parking brake linings or the rear brake
disc rotors, or when brake performance is insuffi
-
cient.
1. Adjust the parking brake lever stroke to the standard value.
Specified value: 5 − 7 notches (Operation
force: Approximately 200 N)
Page 227 of 800
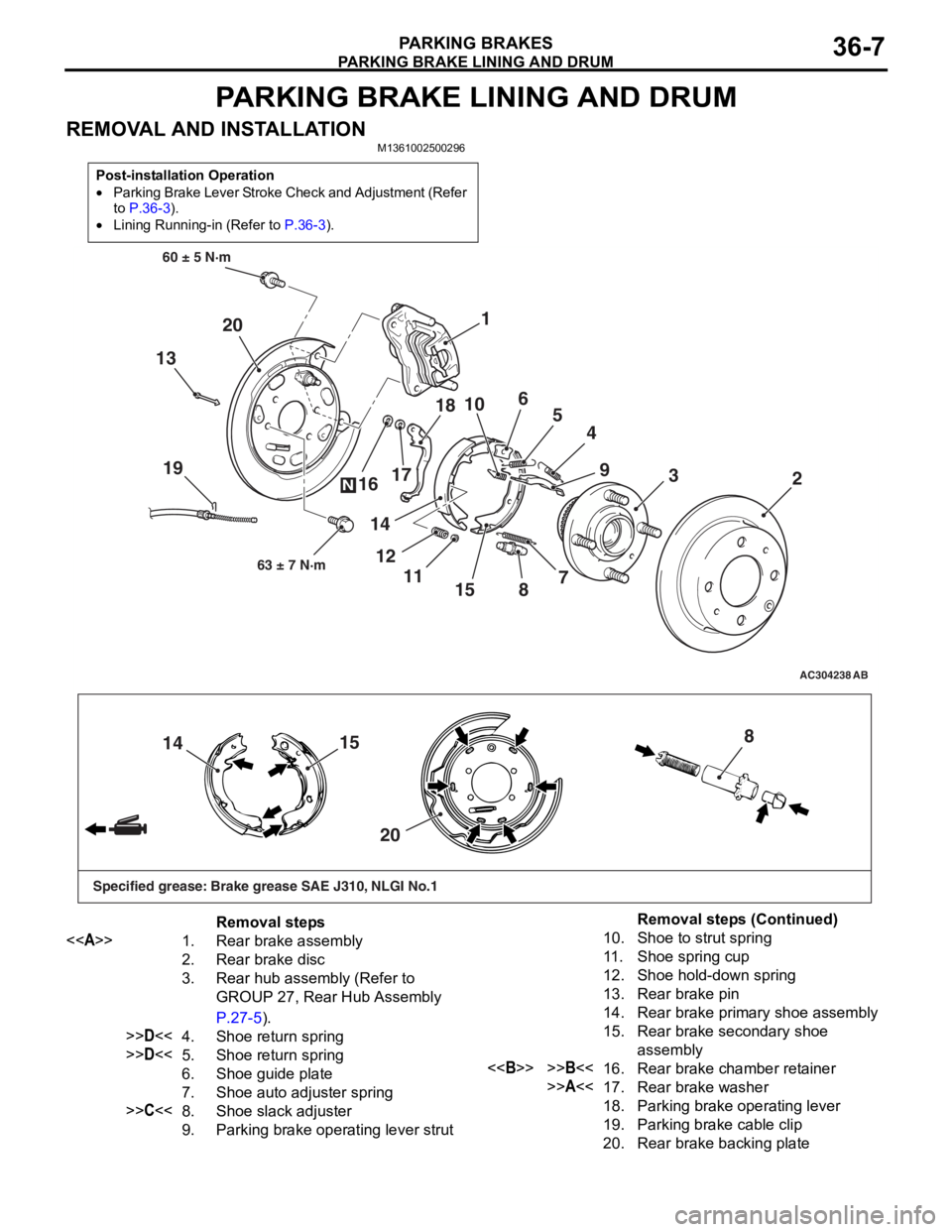
PARKING BRAKE LINING AND DRUM
PARKING BRAKES36-7
PARKING BRAKE LINING AND DRUM
REMOVAL AND INSTALLATIONM1361002500296
Post-installation Operation
•Parking Brake Lever Stroke Check and Adjustment (Refer
to
P.36-3).
•Lining Running-in (Refer to P.36-3).
AC304238
19
60 ± 5 N·m63 ± 7 N·m
AB
13 4
15 5
3
8 9
7 2
1
6
10
11
12 17
18
14
16
20
N
15
14
20 8
Specified grease: Brake grease SAE J310, NLGI No.1
Removal steps
<> 1. Rear brake assembly
2. Rear brake disc
3.Rear hub assembly (Refer to
GROUP 27, Rear Hub Assembly
P.27-5).
>>D<<4.Shoe return spring
>>D<<5. Shoe return spring
6. Shoe guide plate
7. Shoe auto adjuster spring
>>C<<8. Shoe slack adjuster
9. Parking brake operating lever strut
10. Shoe to strut spring
11 . Shoe spring cup
12. Shoe hold-down spring
13. Rear brake pin
14. Rear brake primary shoe assembly
15. Rear brake secondary shoe
assembly
<>>>B<<16. Rear brake chamber retainer
>>A<<17. Rear brake washer
18. Parking brake operating lever
19. Parking brake cable clip
20. Rear brake backing plate
Removal steps (Continued)
Page 233 of 800
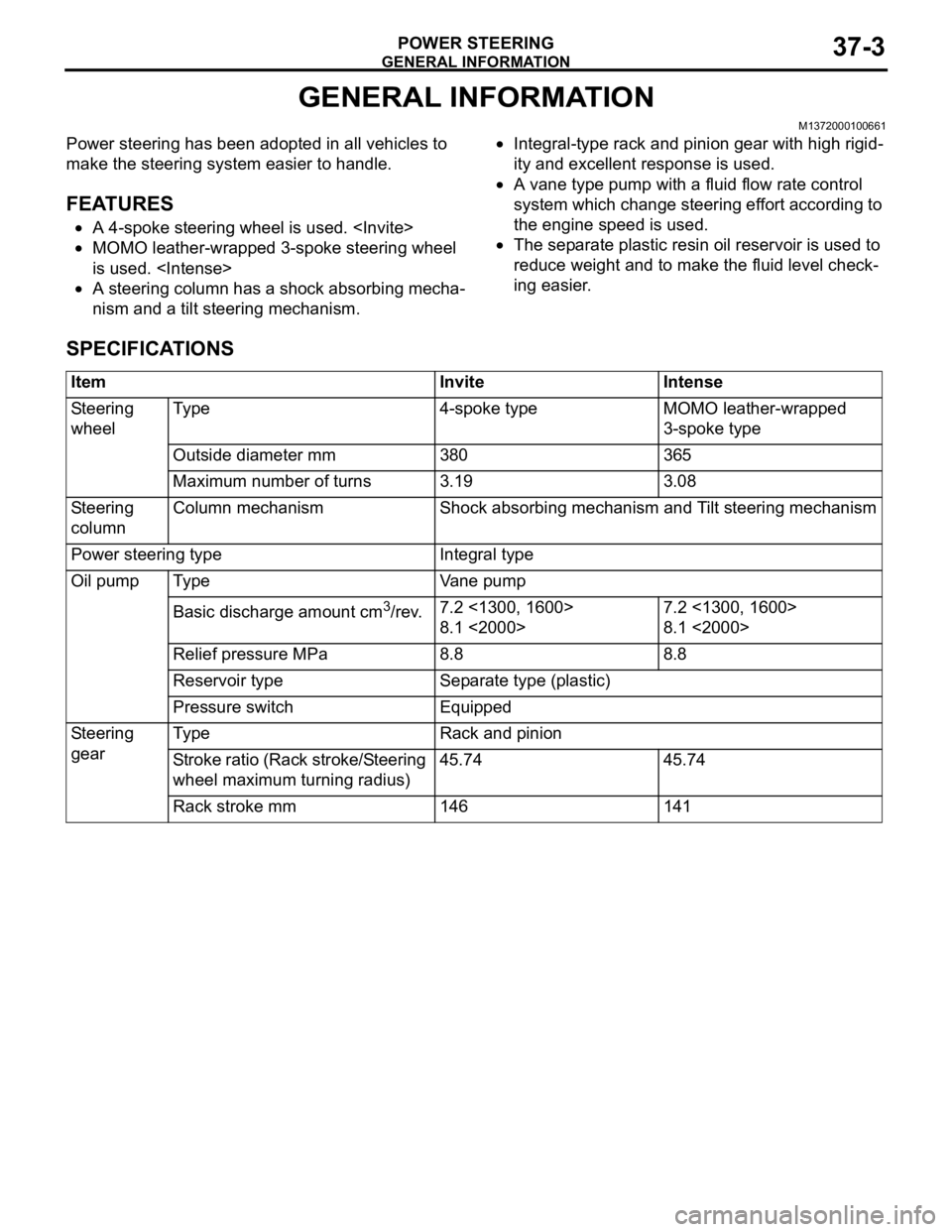
GENERAL INFORMATION
POWER STEERING37-3
GENERAL INFORMATION
M1372000100661
Power steering has been adopted in all vehicles to
make the steering system easier to handle.
FEATURES
•A 4-spoke steering wheel is used.
•MOMO leather-wrapped 3-spoke steering wheel
is used.
•A steering column has a shock absorbing mecha-
nism and a tilt steering mechanism.
•Integral-type rack and pinion gear with high rigid-
ity and excellent response is used.
•A vane type pump with a fluid flow rate control
system which change steering effort according to
the engine speed is used.
•The separate plastic resin oil reservoir is used to
reduce weight and to make the fluid level check
-
ing easier.
SPECIFICATIONS
ItemInviteIntense
Steering
wheelTy p e4-spoke typeMOMO leather-wrapped
3-spoke type
Outside diameter mm380365
Maximum number of turns3.193.08
Steering
columnColumn mechanismShock absorbing mechanism and Tilt steering mechanism
Power steering typeIntegral type
Oil pumpTy p eVane pump
Basic discharge amount cm3/rev.7.2 <1300, 1600>
8.1 <2000>
7.2 <1300, 1600>
8.1 <2000>
Relief pressure MPa8.88.8
Reservoir typeSeparate type (plastic)
Pressure switchEquipped
Steering
gearTy p eRack and pinion
Stroke ratio (Rack stroke/Steering
wheel maximum turning radius)45.7445.74
Rack stroke mm146141
Page 238 of 800
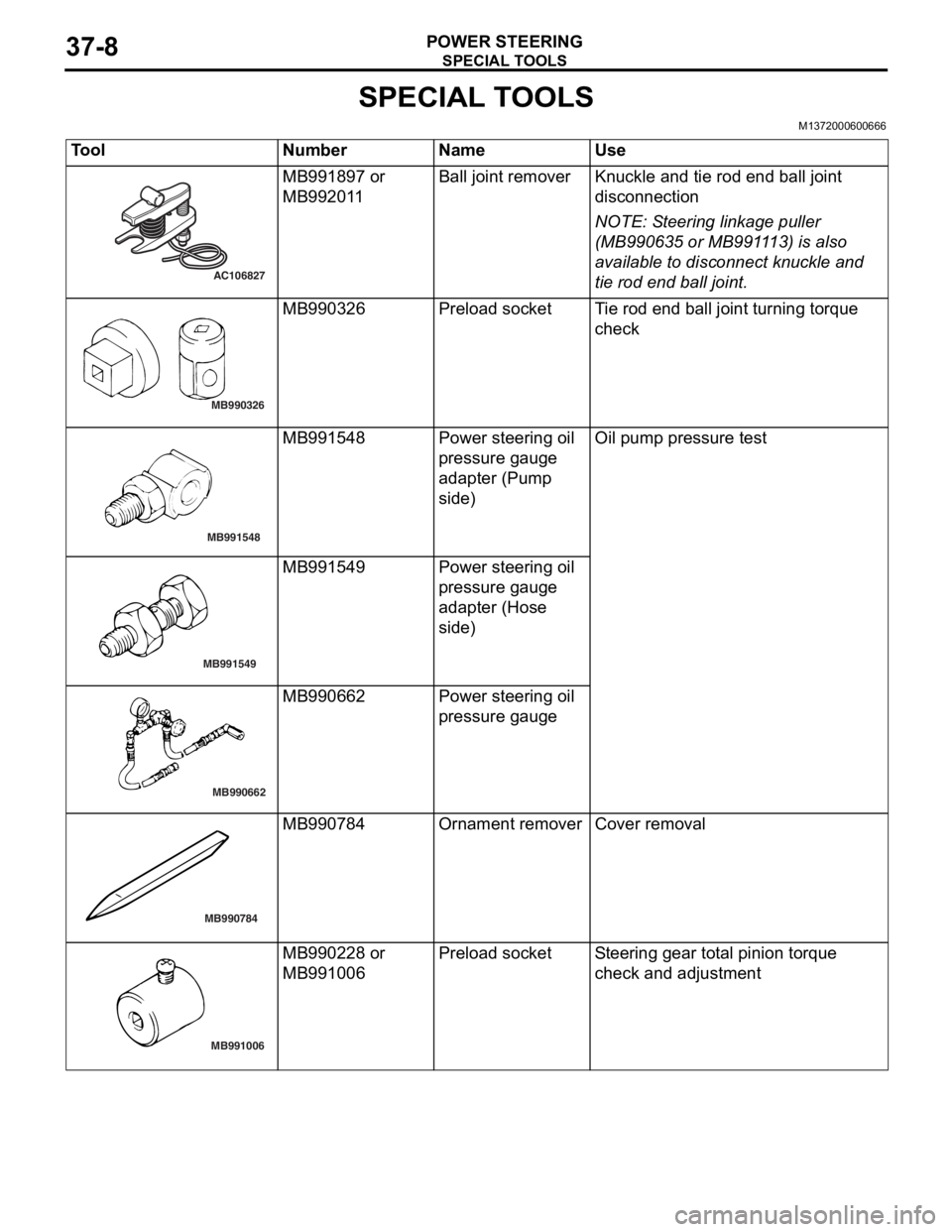
SPECIAL TOOLS
POWER STEERING37-8
SPECIAL TOOLS
M1372000600666
ToolNumberNameUse
AC106827
MB991897 or
MB9920
1 1Ball j o in t remo verKnuckle and tie rod e nd ball joint
discon
nection
NOTE: St eering linkage pu lle r
(MB990 635 o r MB991 1 13) is also
ava
ilab
l e to disconn ect knuckle and
tie ro
d end ball joint.
MB990326
MB9903 26Prel oad socketTi e rod end b a ll join t turning torq ue
che
c k
MB991548
MB9915 48Powe r stee ring oil
pressure g
auge
adapte
r (Pump
sid
e )Oil pump pre ssu re test
MB991549
MB991549Powe r stee ring oil
pressure g
auge
adapte
r (Hose
sid
e )
MB990662
MB9906 62Powe r stee ring oil
pressure g
auge
MB990784
MB990784Ornament removerCover removal
MB991006
MB9902 28 or
MB9910
06Prel oad socketSt e e ring gear to t a l pinion torque
che
ck and ad justmen t