clock MITSUBISHI LANCER EVOLUTION IV 1998 Workshop Manual
[x] Cancel search | Manufacturer: MITSUBISHI, Model Year: 1998, Model line: LANCER EVOLUTION IV, Model: MITSUBISHI LANCER EVOLUTION IV 1998Pages: 396, PDF Size: 7.1 MB
Page 11 of 396
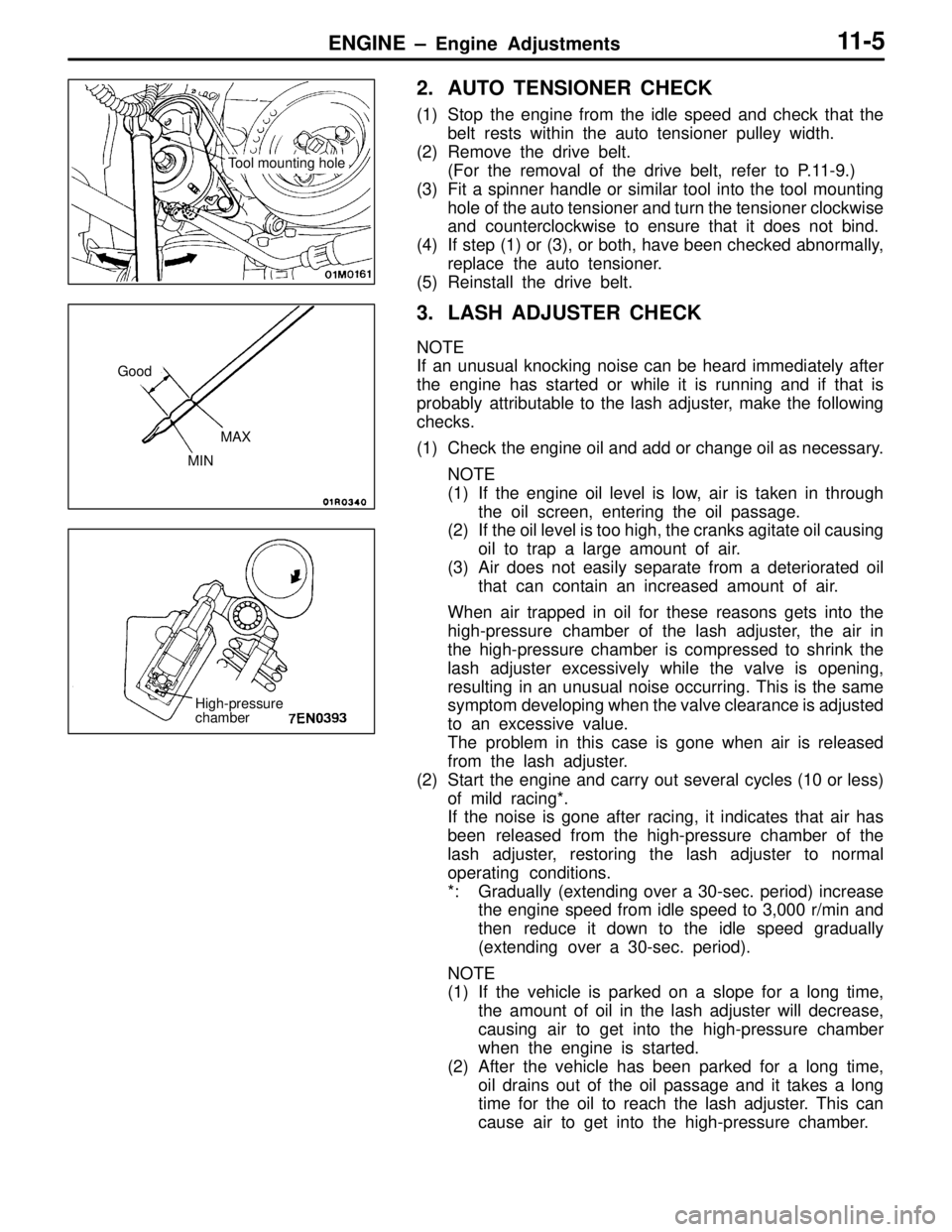
ENGINE – Engine Adjustments11-5
2. AUTO TENSIONER CHECK
(1) Stop the engine from the idle speed and check that the
belt rests within the auto tensioner pulley width.
(2) Remove the drive belt.
(For the removal of the drive belt, refer to P.11-9.)
(3) Fit a spinner handle or similar tool into the tool mounting
hole of the auto tensioner and turn the tensioner clockwise
and counterclockwise to ensure that it does not bind.
(4) If step (1) or (3), or both, have been checked abnormally,
replace the auto tensioner.
(5) Reinstall the drive belt.
3. LASH ADJUSTER CHECK
NOTE
If an unusual knocking noise can be heard immediately after
the engine has started or while it is running and if that is
probably attributable to the lash adjuster, make the following
checks.
(1) Check the engine oil and add or change oil as necessary.
NOTE
(1) If the engine oil level is low, air is taken in through
the oil screen, entering the oil passage.
(2) If the oil level is too high, the cranks agitate oil causing
oil to trap a large amount of air.
(3) Air does not easily separate from a deteriorated oil
that can contain an increased amount of air.
When air trapped in oil for these reasons gets into the
high-pressure chamber of the lash adjuster, the air in
the high-pressure chamber is compressed to shrink the
lash adjuster excessively while the valve is opening,
resulting in an unusual noise occurring. This is the same
symptom developing when the valve clearance is adjusted
to an excessive value.
The problem in this case is gone when air is released
from the lash adjuster.
(2) Start the engine and carry out several cycles (10 or less)
of mild racing*.
If the noise is gone after racing, it indicates that air has
been released from the high-pressure chamber of the
lash adjuster, restoring the lash adjuster to normal
operating conditions.
*: Gradually (extending over a 30-sec. period) increase
the engine speed from idle speed to 3,000 r/min and
then reduce it down to the idle speed gradually
(extending over a 30-sec. period).
NOTE
(1) If the vehicle is parked on a slope for a long time,
the amount of oil in the lash adjuster will decrease,
causing air to get into the high-pressure chamber
when the engine is started.
(2) After the vehicle has been parked for a long time,
oil drains out of the oil passage and it takes a long
time for the oil to reach the lash adjuster. This can
cause air to get into the high-pressure chamber.
Tool mounting hole
Good
MAX
MIN
High-pressure
chamber
Page 12 of 396

ENGINE – Engine Adjustments11-6
(3) If the noise is not eliminated by racing, follow these steps
to check the lash adjuster.
a. Stop the engine.
b. Bring no. 1 cylinder to TDC on the compression stroke.
c. Push the rocker arms indicated by arrow A on the
left to see if they go down.
d. Slowly turn the crankshaft clockwise 360.
e. Perform the same step as step c for rocker arms
indicated by arrow B.
f. Push the part of the rocker arm which contacts the
top of the lash adjuster. If the rocker arm can be
easily moved down to the bottom, the lash adjuster
is defective, requiring replacement.
When the lash adjuster is replaced, be sure first to
bleed the lash adjuster of air before installation. Then,
perform steps a through e to ensure that no abnormal
symptoms are noted.
NOTE
(1) The leak-down test is an effective means to
accurately determine if the lash adjuster is
operational or not.
(2) For the leak-down test and bleeding procedures,
refer to ENGINE WORKSHOP MANUAL.
If the rocker arm is felt binding and cannot be
pushed downward as you push it, the lash adjuster
is operational. Check for other possible causes
for the noise.
(4) Lash adjuster replacement
Caution
From the cylinder from which the lash adjuster is
to be removed, turn the crankshaft to lower the piston,
as the valve contacts the piston when pushed down.
A rocker arm cannot be removed if it is lifted by the
cam. If this is the case, turn the crankshaft so that
the arm is not lifted.
a. Using the special tool, push the valve downward to
remove the roller rocker arm.
b. Remove the lash adjuster from the cylinder head.
c. Mount a brandnew lash adjuster which has been bled
of air in the cylinder head.
d. Using the special tool, lower the valve and install
the roller rocker arm.
NOTE
To mount the roller rocker arm, first place the pivot
side of the rocker arm on the lash adjuster, then push
down the valve; next, place the slipper side of the
rocker arm on the valve system side.Timing belt side
ABABAA B B
MD998782
MD998782
Page 34 of 396
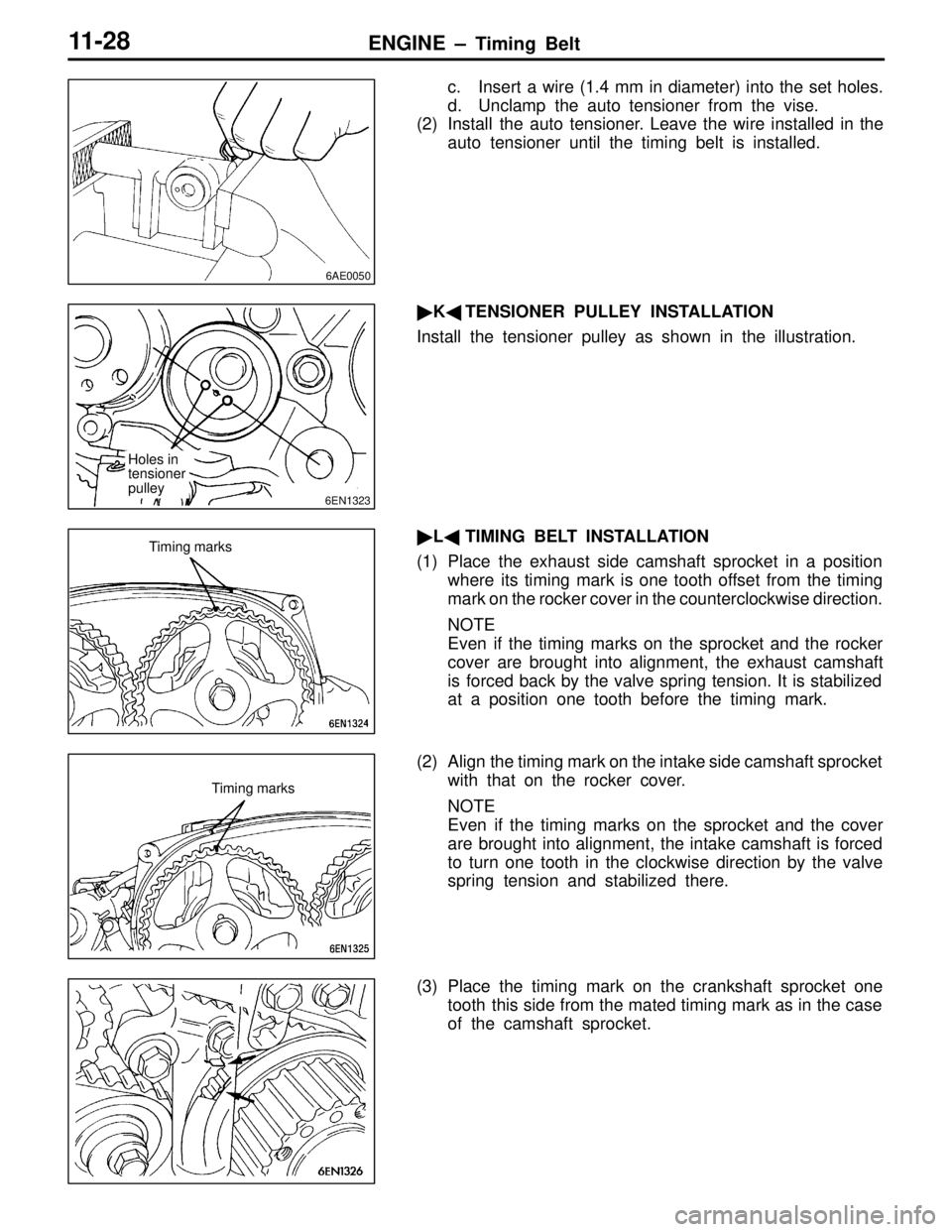
ENGINE – Timing Belt11-28
c. Insert a wire (1.4 mm in diameter) into the set holes.
d. Unclamp the auto tensioner from the vise.
(2) Install the auto tensioner. Leave the wire installed in the
auto tensioner until the timing belt is installed.
K TENSIONER PULLEY INSTALLATION
Install the tensioner pulley as shown in the illustration.
L TIMING BELT INSTALLATION
(1) Place the exhaust side camshaft sprocket in a position where its timing mark is one tooth offset from the timing
mark on the rocker cover in the counterclockwise direction.
NOTE
Even if the timing marks on the sprocket and the rocker
cover are brought into alignment, the exhaust camshaft
is forced back by the valve spring tension. It is stabilized
at a position one tooth before the timing mark.
(2) Align the timing mark on the intake side camshaft sprocket with that on the rocker cover.
NOTE
Even if the timing marks on the sprocket and the cover
are brought into alignment, the intake camshaft is forced
to turn one tooth in the clockwise direction by the valve
spring tension and stabilized there.
(3) Place the timing mark on the crankshaft sprocket one tooth this side from the mated timing mark as in the case
of the camshaft sprocket.
6AE0050
6EN1323
Holes in
tensioner
pulley
Timing marks
Timing marks
Page 35 of 396
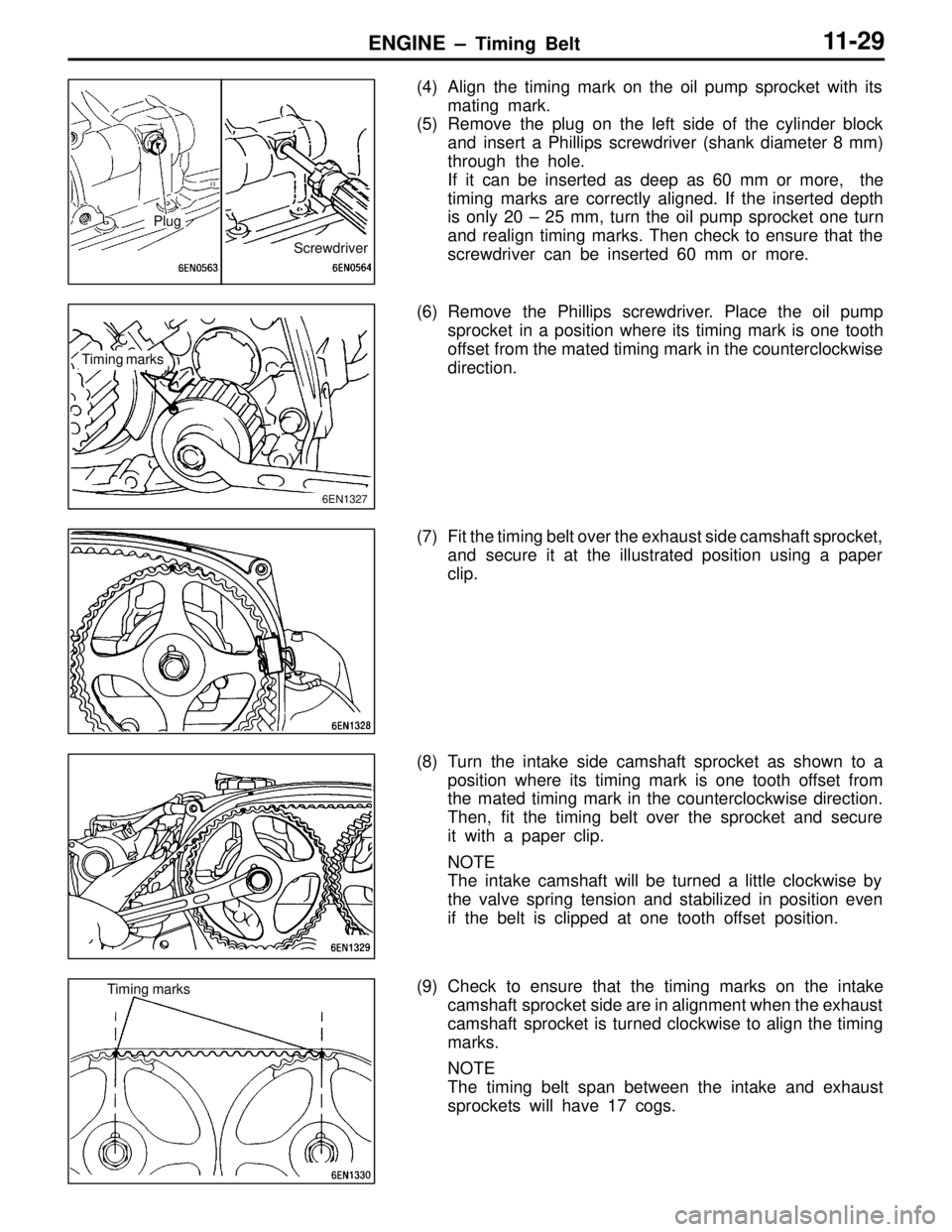
ENGINE – T iming Belt 11-29
(4) Align the timing mark on the oil pump sprocket with its
mating mark.
(5) Remove the plug on the left side of the cylinder block
and insert a Phillips screwdriver (shank diameter 8 mm)
through the hole.
If it can be inserted as deep as 60 mm or more, the
timing marks are correctly aligned. If the inserted depth
is only 20 – 25 mm, turn the oil pump sprocket one turn
and realign timing marks. Then check to ensure that the
screwdriver can be inserted 60 mm or more.
(6) Remove the Phillips screwdriver. Place the oil pump sprocket in a position where its timing mark is one tooth
offset from the mated timing mark in the counterclockwise
direction.
(7) Fit the timing belt over the exhaust side camshaft sprocket, and secure it at the illustrated position using a paper
clip.
(8) Turn the intake side camshaft sprocket as shown to a position where its timing mark is one tooth offset from
the mated timing mark in the counterclockwise direction.
Then, fit the timing belt over the sprocket and secure
it with a paper clip.
NOTE
The intake camshaft will be turned a little clockwise by
the valve spring tension and stabilized in position even
if the belt is clipped at one tooth offset position.
(9) Check to ensure that the timing marks on the intake camshaft sprocket side are in alignment when the exhaust
camshaft sprocket is turned clockwise to align the timing
marks.
NOTE
The timing belt span between the intake and exhaust
sprockets will have 17 cogs.
Screwdriver
Plug
Timing marks
6EN1327
Timing marks
Page 36 of 396
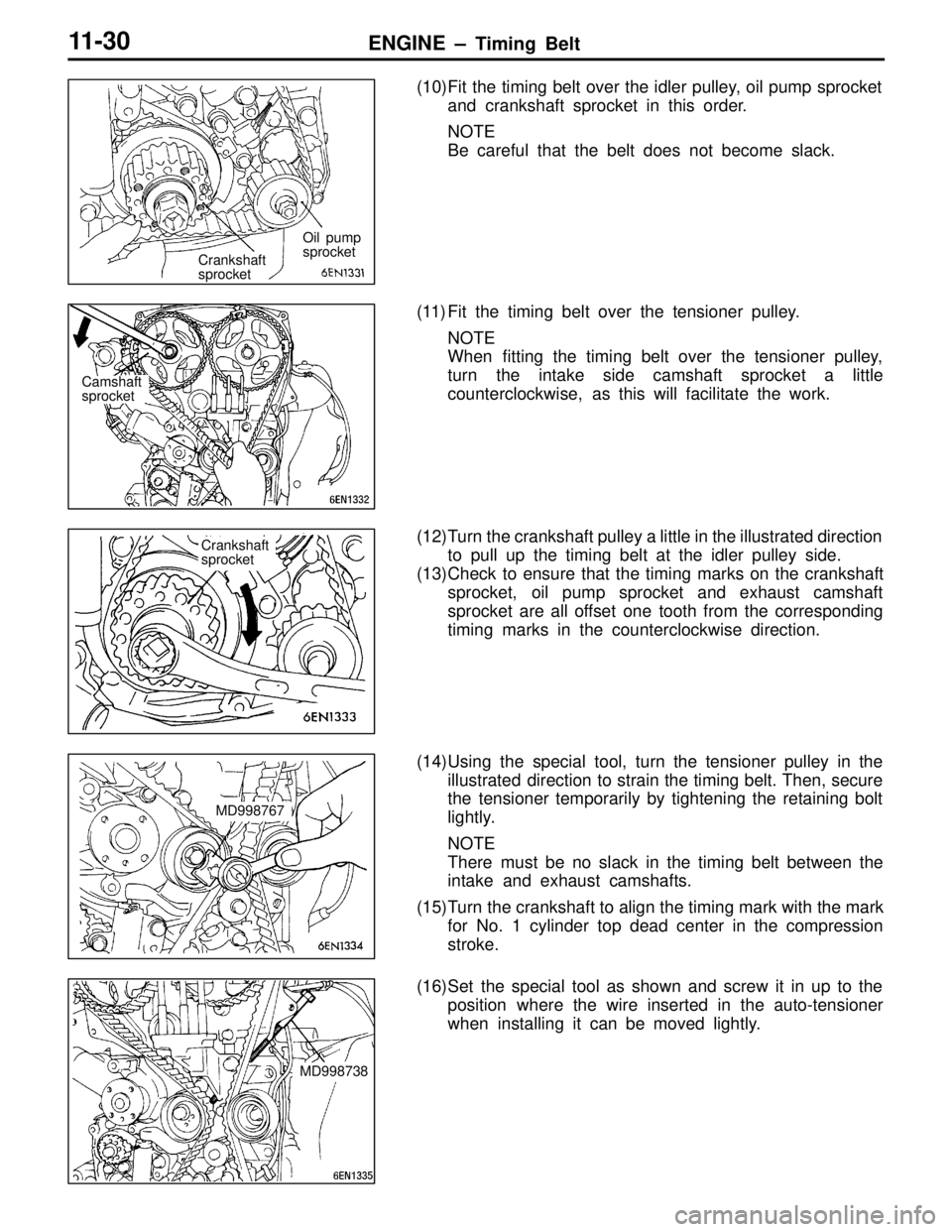
ENGINE – Timing Belt11-30
(10)Fit the timing belt over the idler pulley, oil pump sprocket
and crankshaft sprocket in this order.
NOTE
Be careful that the belt does not become slack.
(11) Fit the timing belt over the tensioner pulley. NOTE
When fitting the timing belt over the tensioner pulley,
turn the intake side camshaft sprocket a little
counterclockwise, as this will facilitate the work.
(12)Turn the crankshaft pulley a little in the illustrated direction to pull up the timing belt at the idler pulley side.
(13)Check to ensure that the timing marks on the crankshaft sprocket, oil pump sprocket and exhaust camshaft
sprocket are all offset one tooth from the corresponding
timing marks in the counterclockwise direction.
(14)Using the special tool, turn the tensioner pulley in the illustrated direction to strain the timing belt. Then, secure
the tensioner temporarily by tightening the retaining bolt
lightly.
NOTE
There must be no slack in the timing belt between the
intake and exhaust camshafts.
(15)Turn the crankshaft to align the timing mark with the mark for No. 1 cylinder top dead center in the compression
stroke.
(16)Set the special tool as shown and screw it in up to the position where the wire inserted in the auto-tensioner
when installing it can be moved lightly.
Crankshaft
sprocket Oil pump
sprocket
Camshaft
sprocket
Crankshaft
sprocket
MD998767
MD998738
Page 37 of 396
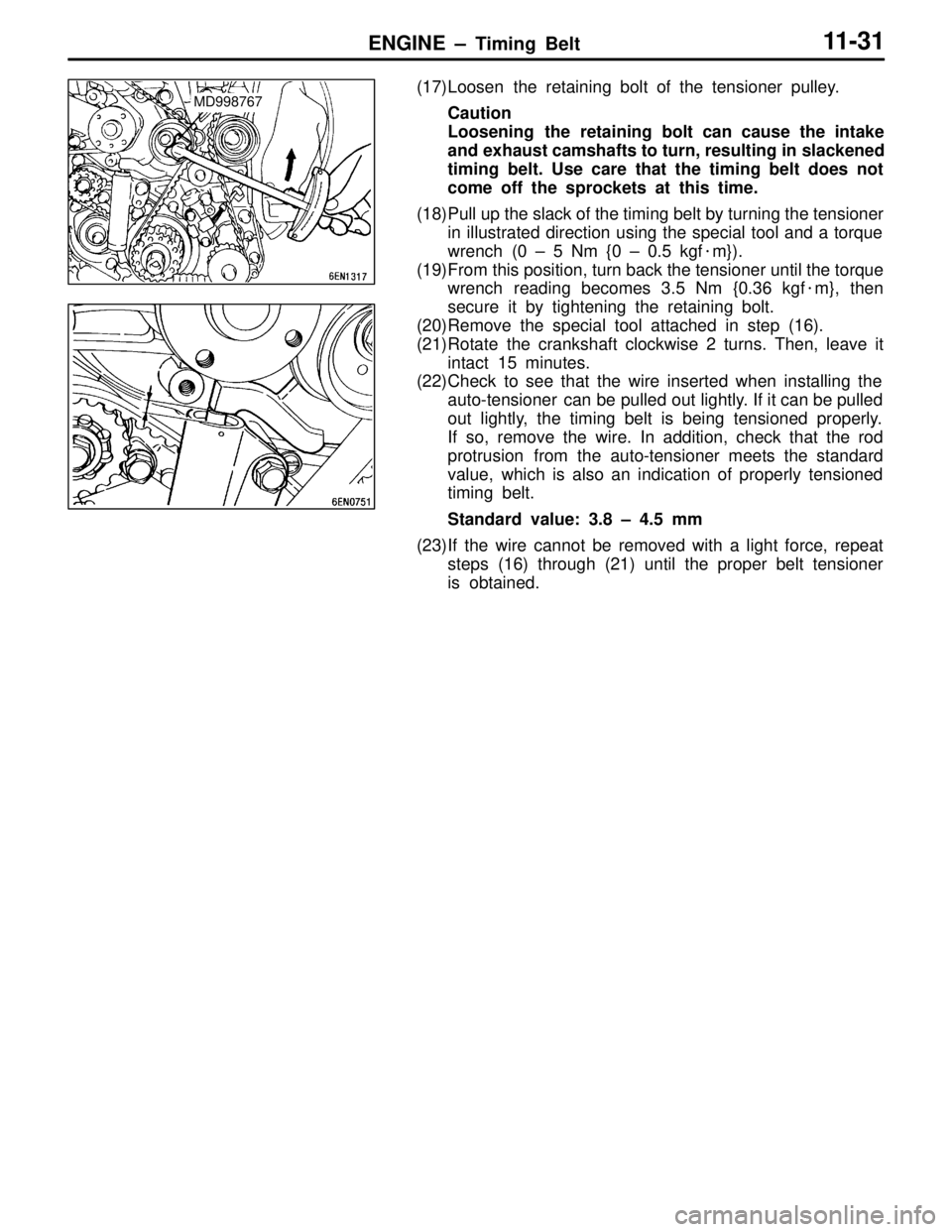
ENGINE – T iming Belt 11-31
(17)Loosen the retaining bolt of the tensioner pulley.
Caution
Loosening the retaining bolt can cause the intake
and exhaust camshafts to turn, resulting in slackened
timing belt. Use care that the timing belt does not
come off the sprockets at this time.
(18)Pull up the slack of the timing belt by turning the tensioner in illustrated direction using the special tool and a torque
wrench (0 – 5 Nm {0 – 0.5 kgf m}).
(19)From this position, turn back the tensioner until the torque wrench reading becomes 3.5 Nm {0.36 kgf m}, then
secure it by tightening the retaining bolt.
(20)Remove the special tool attached in step (16).
(21)Rotate the crankshaft clockwise 2 turns. Then, leave it intact 15 minutes.
(22)Check to see that the wire inserted when installing the
auto-tensioner can be pulled out lightly. If it can be pulled
out lightly, the timing belt is being tensioned properly.
If so, remove the wire. In addition, check that the rod
protrusion from the auto-tensioner meets the standard
value, which is also an indication of properly tensioned
timing belt.
Standard value: 3.8 – 4.5 mm
(23)If the wire cannot be removed with a light force, repeat steps (16) through (21) until the proper belt tensioner
is obtained.MD998767
Page 213 of 396
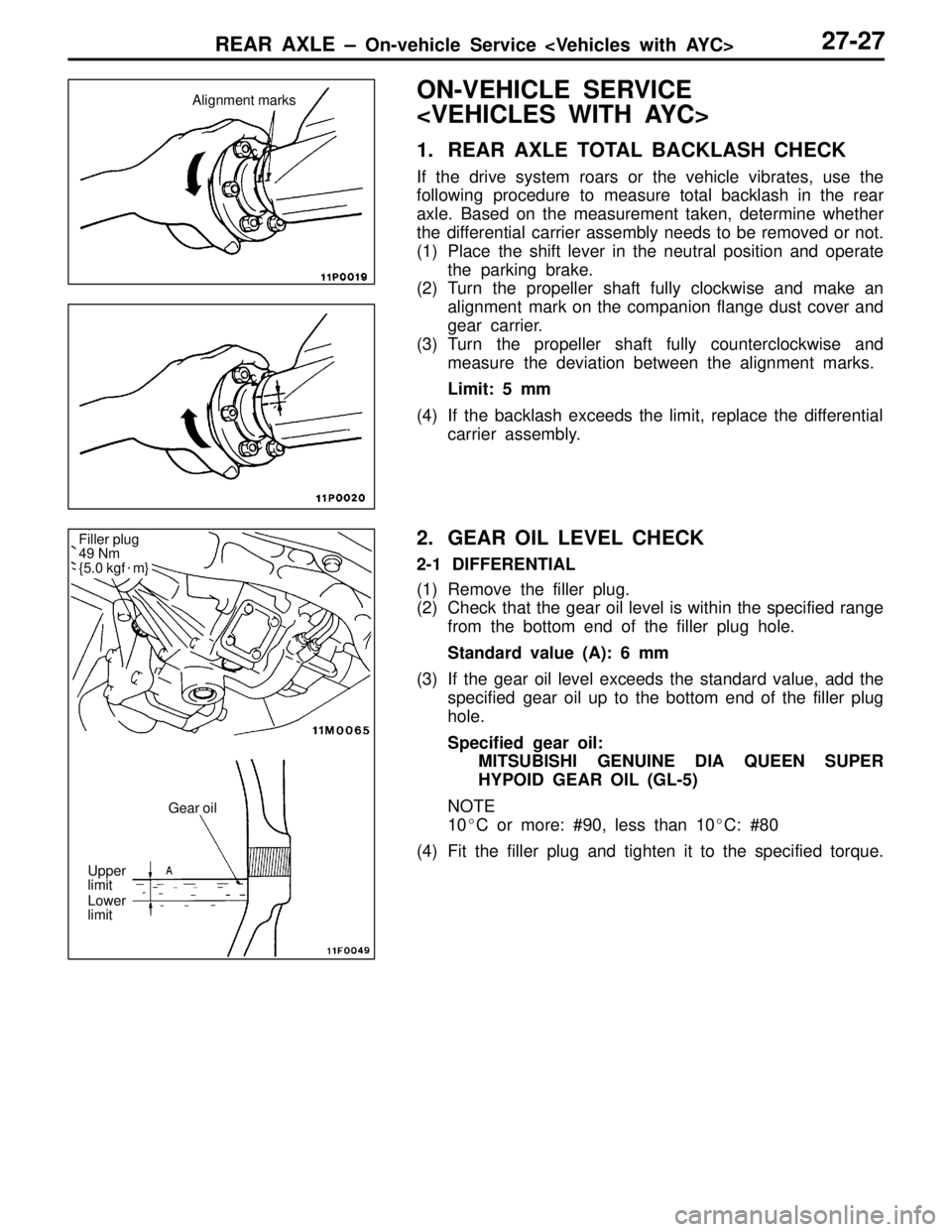
REAR AXLE – On-vehicle Service
ON-VEHICLE SERVICE
1. REAR AXLE TOTAL BACKLASH CHECK
If the drive system roars or the vehicle vibrates, use the
following procedure to measure total backlash in the rear
axle. Based on the measurement taken, determine whether
the differential carrier assembly needs to be removed or not.
(1) Place the shift lever in the neutral position and operate
the parking brake.
(2) Turn the propeller shaft fully clockwise and make an
alignment mark on the companion flange dust cover and
gear carrier.
(3) Turn the propeller shaft fully counterclockwise and
measure the deviation between the alignment marks.
Limit: 5 mm
(4) If the backlash exceeds the limit, replace the differential
carrier assembly.
2. GEAR OIL LEVEL CHECK
2-1 DIFFERENTIAL
(1) Remove the filler plug.
(2) Check that the gear oil level is within the specified range
from the bottom end of the filler plug hole.
Standard value (A): 6 mm
(3) If the gear oil level exceeds the standard value, add the
specified gear oil up to the bottom end of the filler plug
hole.
Specified gear oil:
MITSUBISHI GENUINE DIA QUEEN SUPER
HYPOID GEAR OIL (GL-5)
NOTE
10C or more: #90, less than 10C: #80
(4) Fit the filler plug and tighten it to the specified torque.
Alignment marks
Filler plug
49 Nm
{5.0 kgfm}
Gear oil
Upper
limit
Lower
limit
Page 215 of 396
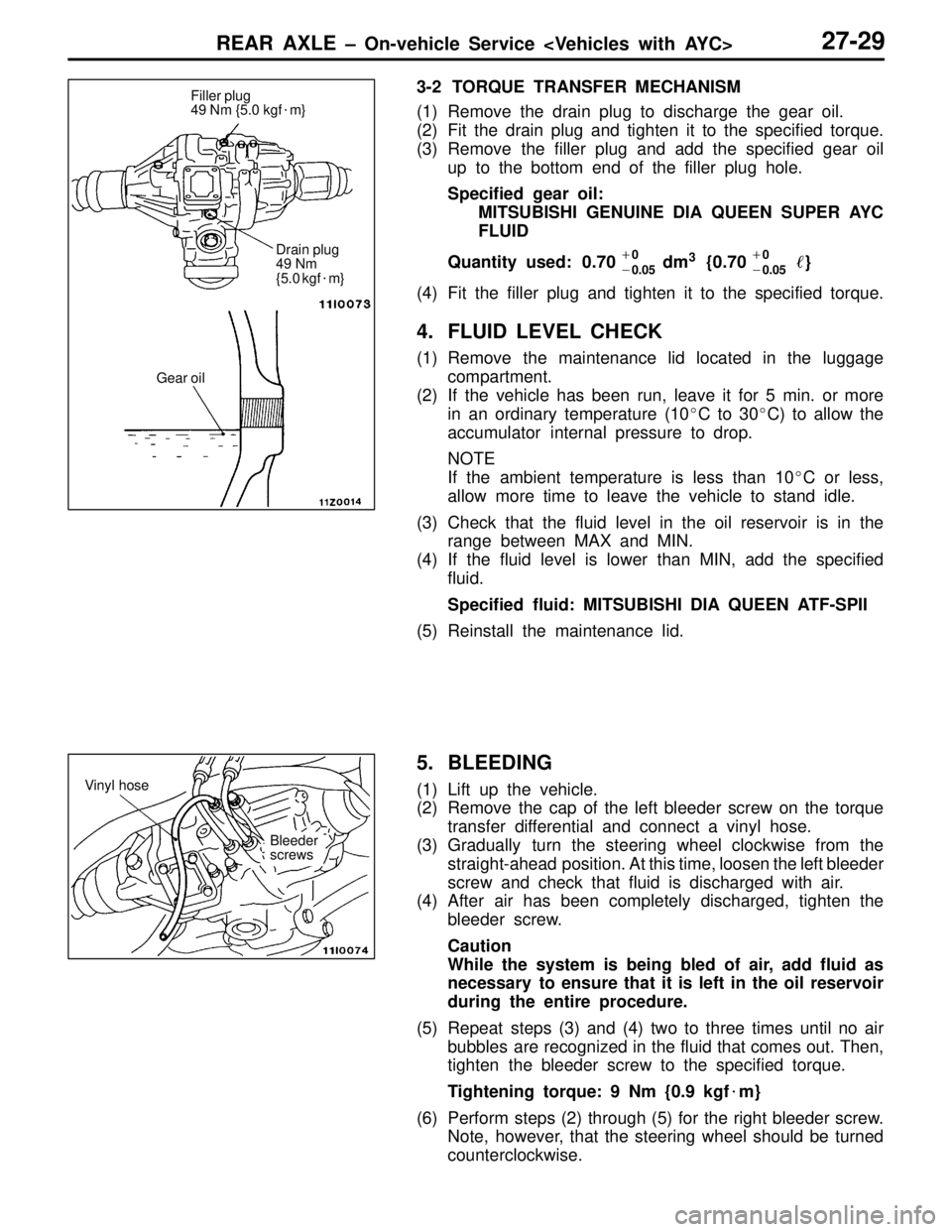
REAR AXLE – On-vehicle Service
3-2 TORQUE TRANSFER MECHANISM
(1) Remove the drain plug to discharge the gear oil.
(2) Fit the drain plug and tighten it to the specified torque.
(3) Remove the filler plug and add the specified gear oil
up to the bottom end of the filler plug hole.
Specified gear oil:
MITSUBISHI GENUINE DIA QUEEN SUPER AYC
FLUID
Quantity used: 0.70
0
0.05dm3{0.700
0.05}
(4) Fit the filler plug and tighten it to the specified torque.
4. FLUID LEVEL CHECK
(1) Remove the maintenance lid located in the luggage
compartment.
(2) If the vehicle has been run, leave it for 5 min. or more
in an ordinary temperature (10C to 30C) to allow the
accumulator internal pressure to drop.
NOTE
If the ambient temperature is less than 10C or less,
allow more time to leave the vehicle to stand idle.
(3) Check that the fluid level in the oil reservoir is in the
range between MAX and MIN.
(4) If the fluid level is lower than MIN, add the specified
fluid.
Specified fluid: MITSUBISHI DIA QUEEN ATF-SPII
(5) Reinstall the maintenance lid.
5. BLEEDING
(1) Lift up the vehicle.
(2) Remove the cap of the left bleeder screw on the torque
transfer differential and connect a vinyl hose.
(3) Gradually turn the steering wheel clockwise from the
straight-ahead position. At this time, loosen the left bleeder
screw and check that fluid is discharged with air.
(4) After air has been completely discharged, tighten the
bleeder screw.
Caution
While the system is being bled of air, add fluid as
necessary to ensure that it is left in the oil reservoir
during the entire procedure.
(5) Repeat steps (3) and (4) two to three times until no air
bubbles are recognized in the fluid that comes out. Then,
tighten the bleeder screw to the specified torque.
Tightening torque: 9 Nm {0.9 kgfm}
(6) Perform steps (2) through (5) for the right bleeder screw.
Note, however, that the steering wheel should be turned
counterclockwise.
Filler plug
49 Nm {5.0 kgfm}
Gear oil
Drain plug
49 Nm
{5.0 kgfm}
Bleeder
screws Vinyl hose
Page 254 of 396
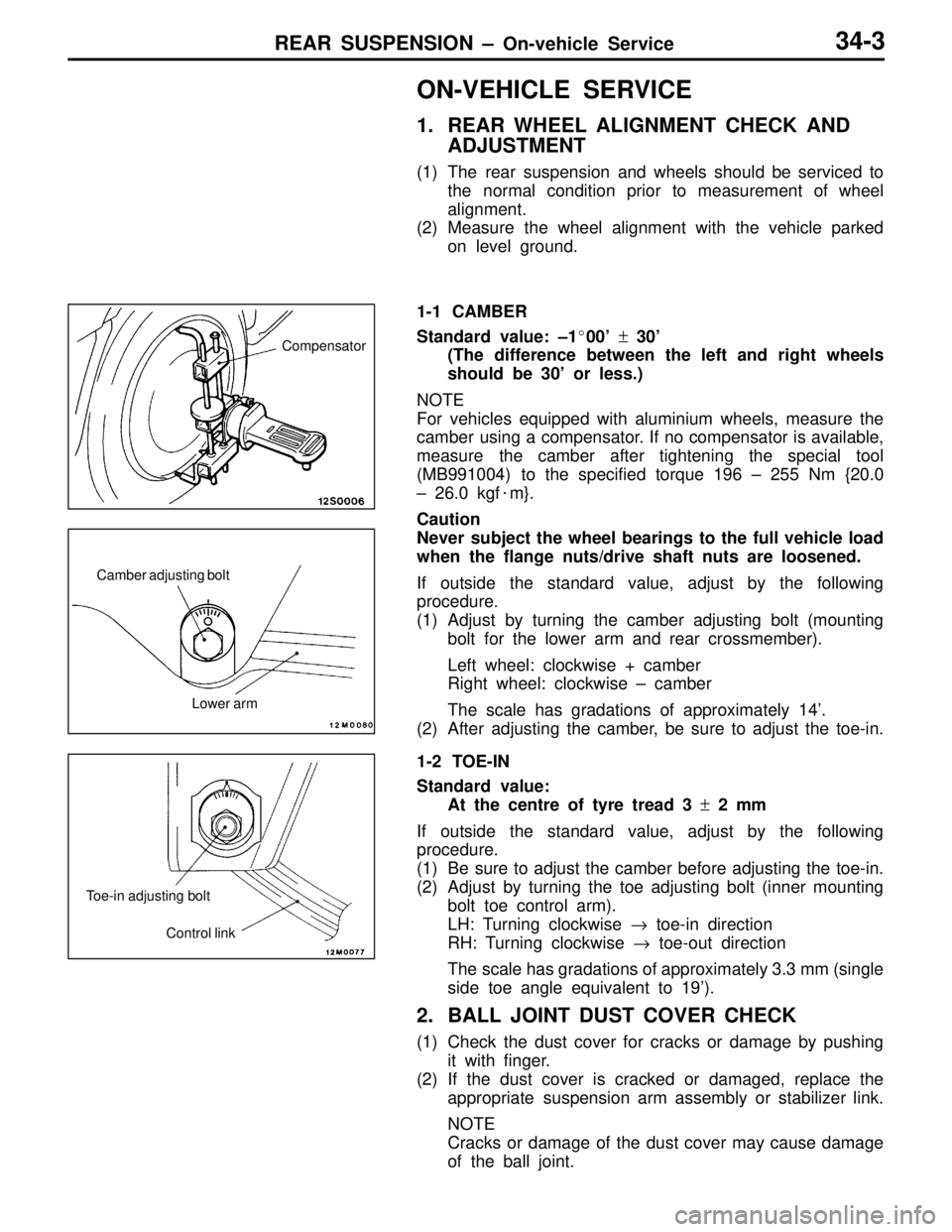
REAR SUSPENSION – On-vehicle Service34-3
ON-VEHICLE SERVICE
1. REAR WHEEL ALIGNMENT CHECK AND
ADJUSTMENT
(1) The rear suspension and wheels should be serviced to
the normal condition prior to measurement of wheel
alignment.
(2) Measure the wheel alignment with the vehicle parked
on level ground.
1-1 CAMBER
Standard value: –100’ ± 30’
(The difference between the left and right wheels
should be 30’ or less.)
NOTE
For vehicles equipped with aluminium wheels, measure the
camber using a compensator. If no compensator is available,
measure the camber after tightening the special tool
(MB991004) to the specified torque 196 – 255 Nm {20.0
– 26.0 kgfm}.
Caution
Never subject the wheel bearings to the full vehicle load
when the flange nuts/drive shaft nuts are loosened.
If outside the standard value, adjust by the following
procedure.
(1) Adjust by turning the camber adjusting bolt (mounting
bolt for the lower arm and rear crossmember).
Left wheel: clockwise + camber
Right wheel: clockwise – camber
The scale has gradations of approximately 14’.
(2) After adjusting the camber, be sure to adjust the toe-in.
1-2 TOE-IN
Standard value:
At the centre of tyre tread 3 ± 2 mm
If outside the standard value, adjust by the following
procedure.
(1) Be sure to adjust the camber before adjusting the toe-in.
(2) Adjust by turning the toe adjusting bolt (inner mounting
bolt toe control arm).
LH: Turning clockwise → toe-in direction
RH: Turning clockwise → toe-out direction
The scale has gradations of approximately 3.3 mm (single
side toe angle equivalent to 19’).
2. BALL JOINT DUST COVER CHECK
(1) Check the dust cover for cracks or damage by pushing
it with finger.
(2) If the dust cover is cracked or damaged, replace the
appropriate suspension arm assembly or stabilizer link.
NOTE
Cracks or damage of the dust cover may cause damage
of the ball joint.
Compensator
Camber adjusting bolt
Lower arm
Toe-in adjusting bolt
Control link
Page 345 of 396
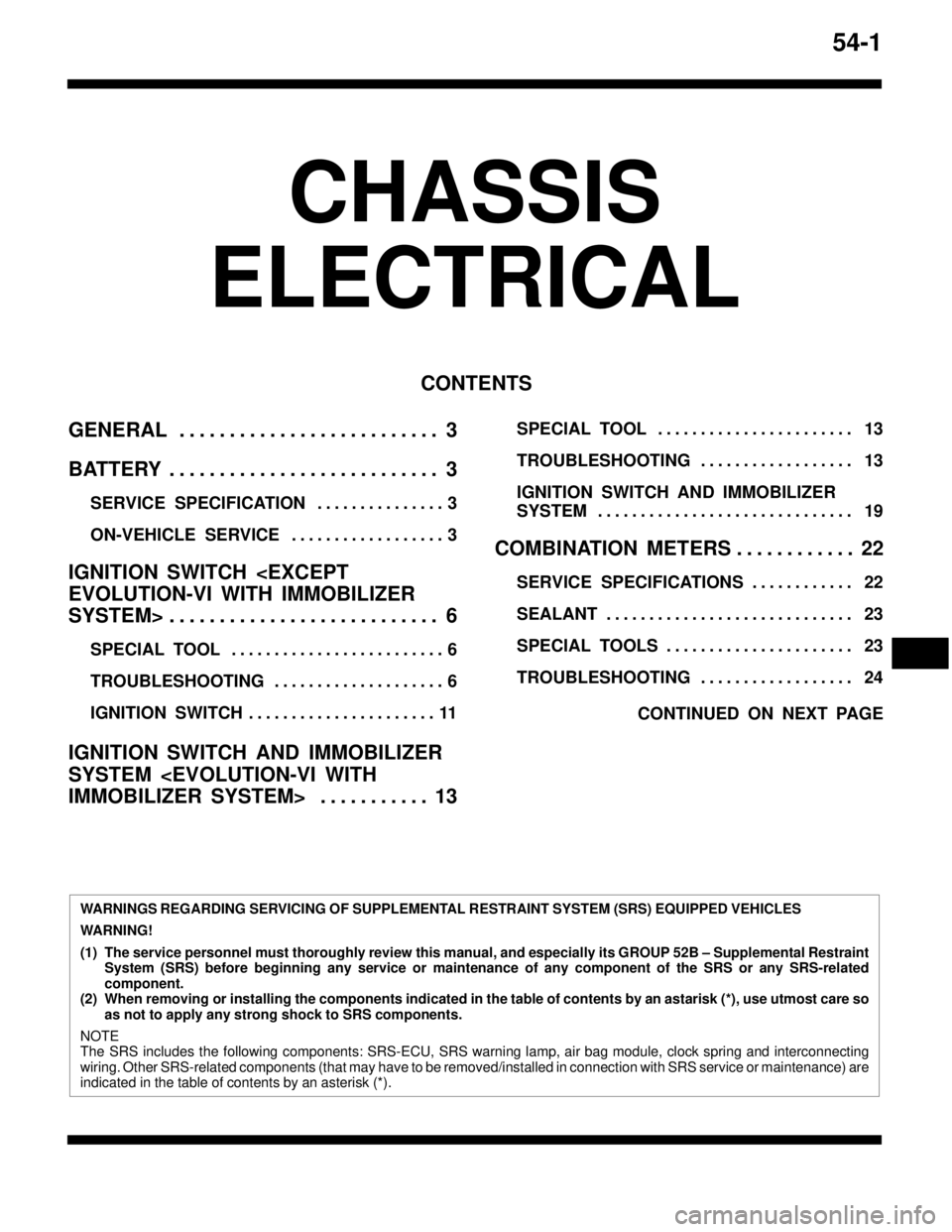
54-1
CHASSIS
ELECTRICAL
CONTENTS
GENERAL 3. . . . . . . . . . . . . . . . . . . . . . . . . .
BATTERY 3. . . . . . . . . . . . . . . . . . . . . . . . . . .
SERVICE SPECIFICATION 3. . . . . . . . . . . . . . .
ON-VEHICLE SERVICE 3. . . . . . . . . . . . . . . . . .
IGNITION SWITCH
SYSTEM> 6. . . . . . . . . . . . . . . . . . . . . . . . . . .
SPECIAL TOOL 6. . . . . . . . . . . . . . . . . . . . . . . . .
TROUBLESHOOTING 6. . . . . . . . . . . . . . . . . . . .
IGNITION SWITCH 11. . . . . . . . . . . . . . . . . . . . . .
IGNITION SWITCH AND IMMOBILIZER
SYSTEM
SPECIAL TOOL 13. . . . . . . . . . . . . . . . . . . . . . .
TROUBLESHOOTING 13. . . . . . . . . . . . . . . . . .
IGNITION SWITCH AND IMMOBILIZER
SYSTEM 19. . . . . . . . . . . . . . . . . . . . . . . . . . . . . .
COMBINATION METERS 22. . . . . . . . . . . .
SERVICE SPECIFICATIONS 22. . . . . . . . . . . .
SEALANT 23. . . . . . . . . . . . . . . . . . . . . . . . . . . . .
SPECIAL TOOLS 23. . . . . . . . . . . . . . . . . . . . . .
TROUBLESHOOTING 24. . . . . . . . . . . . . . . . . .
CONTINUED ON NEXT PAGE
WARNINGS REGARDING SERVICING OF SUPPLEMENTAL RESTRAINT SYSTEM (SRS) EQUIPPED VEHICLES
WARNING!
(1) The service personnel must thoroughly review this manual, and especially its GROUP 52B – Supplemental Restraint
System (SRS) before beginning any service or maintenance of any component of the SRS or any SRS-related
component.
(2) When removing or installing the components indicated in the table of contents by an astarisk (*), use utmost care so
as not to apply any strong shock to SRS components.
NOTE
The SRS includes the following components: SRS-ECU, SRS warning lamp, air bag module, clock spring and interconnecting
wiring. Other SRS-related components (that may have to be removed/installed in connection with SRS service or maintenance) are
indicated in the table of contents by an asterisk (*).