sensor MITSUBISHI LANCER EVOLUTION IX 2005 Owner's Guide
[x] Cancel search | Manufacturer: MITSUBISHI, Model Year: 2005, Model line: LANCER EVOLUTION IX, Model: MITSUBISHI LANCER EVOLUTION IX 2005Pages: 364, PDF Size: 14.38 MB
Page 73 of 364
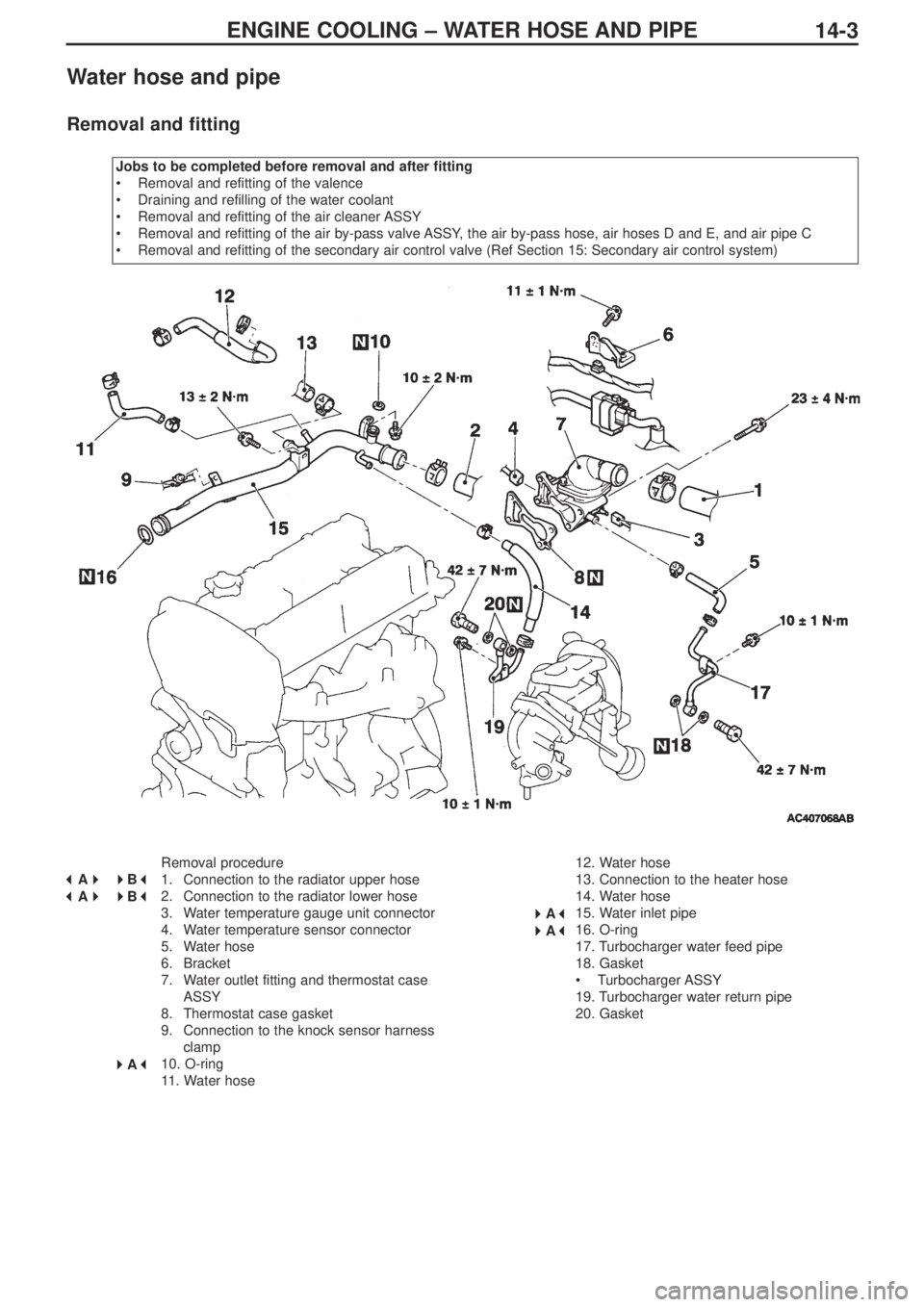
ENGINE COOLING – WATER HOSE AND PIPE
14-3
Water hose and pipe
Removal and fitting
Jobs to be completed before removal and after fitting
•Removal and refitting of the valence
•Draining and refilling of the water coolant
•Removal and refitting of the air cleaner ASSY
•Removal and refitting of the air by-pass valve ASSY, the air by-pass hose, air hoses D and E, and air pipe C
•Removal and refitting of the secondary air control valve (Ref Section 15: Secondary air control system)
Removal procedure
1. Connection to the radiator upper hose
2. Connection to the radiator lower hose
3. Water temperature gauge unit connector
4. Water temperature sensor connector
5. Water hose
6. Bracket
7. Water outlet fitting and thermostat case
ASSY
8. Thermostat case gasket
9. Connection to the knock sensor harness
clamp
10. O-ring
11. Water hose12. Water hose
13. Connection to the heater hose
14. Water hose
15. Water inlet pipe
16. O-ring
17. Turbocharger water feed pipe
18. Gasket
•Turbocharger ASSY
19. Turbocharger water return pipe
20. Gasket
A
B
A
B
A
A
A
Page 75 of 364
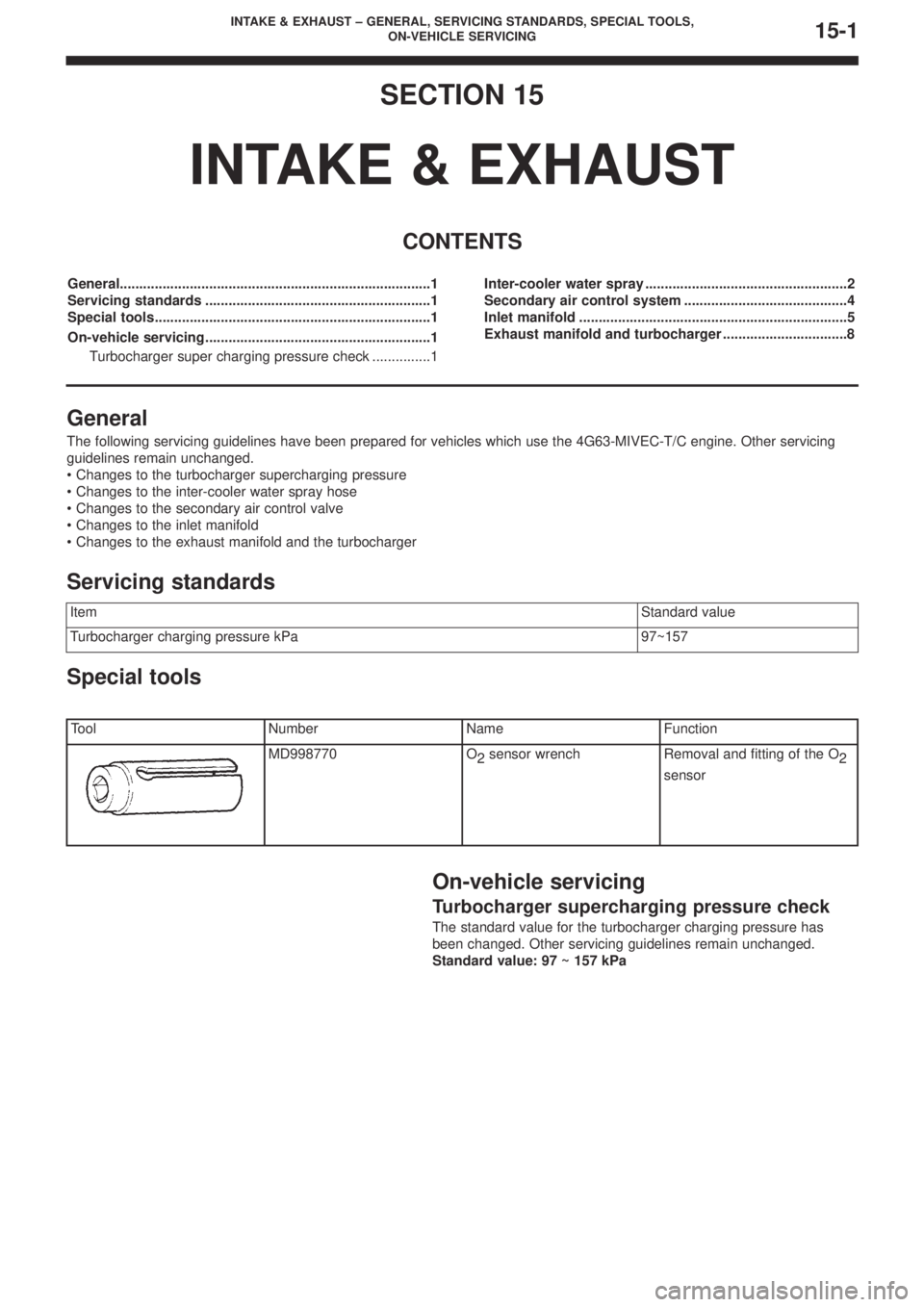
INTAKE & EXHAUST – GENERAL, SERVICING STANDARDS, SPECIAL TOOLS,
ON-VEHICLE SERVICING15-1
SECTION 15
INTAKE & EXHAUST
CONTENTS
General................................................................................1
Servicing standards ..........................................................1
Special tools.......................................................................1
On-vehicle servicing..........................................................1
Turbocharger super charging pressure check ...............1Inter-cooler water spray ....................................................2
Secondary air control system ..........................................4
Inlet manifold .....................................................................5
Exhaust manifold and turbocharger ................................8
General
The following servicing guidelines have been prepared for vehicles which use the 4G63-MIVEC-T/C engine. Other servicing
guidelines remain unchanged.
• Changes to the turbocharger supercharging pressure
• Changes to the inter-cooler water spray hose
• Changes to the secondary air control valve
• Changes to the inlet manifold
• Changes to the exhaust manifold and the turbocharger
Special tools
On-vehicle servicing
Turbocharger supercharging pressure check
The standard value for the turbocharger charging pressure has
been changed. Other servicing guidelines remain unchanged.
Standard value: 97 ~ 157 kPa
ItemStandard value
Turbocharger charging pressure kPa97~157
Servicing standards
ToolNumberNameFunction
MD998770O
2sensor wrenchRemoval and fitting of the O
2
sensor
Page 80 of 364
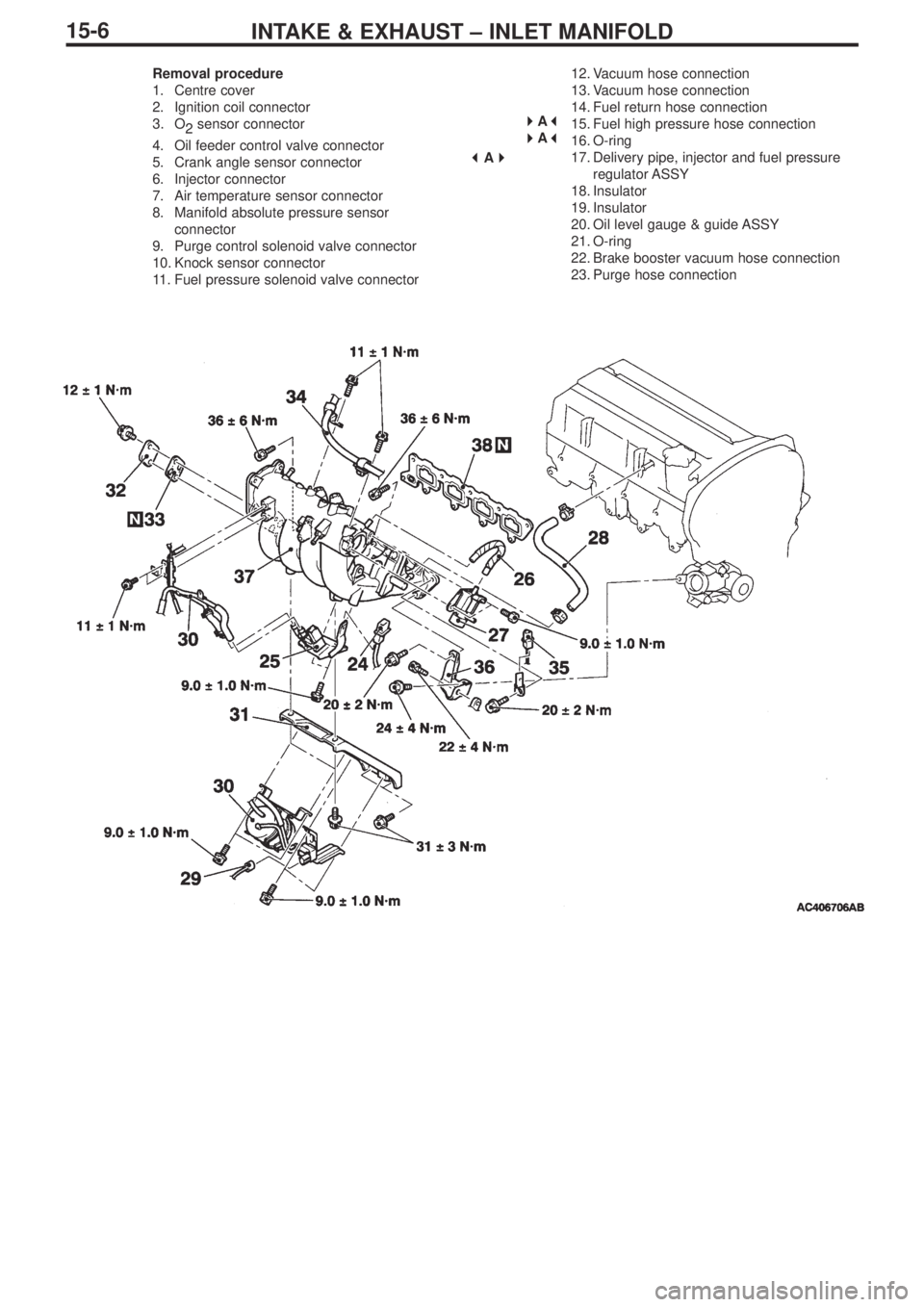
INTAKE & EXHAUST – INLET MANIFOLD15-6
Removal procedure
1. Centre cover
2. Ignition coil connector
3. O
2sensor connector
4. Oil feeder control valve connector
5. Crank angle sensor connector
6. Injector connector
7. Air temperature sensor connector
8. Manifold absolute pressure sensor
connector
9. Purge control solenoid valve connector
10. Knock sensor connector
11.Fuel pressure solenoid valve connector12. Vacuum hose connection
13. Vacuum hose connection
14. Fuel return hose connection
15. Fuel high pressure hose connection
16. O-ring
17. Delivery pipe, injector and fuel pressure
regulator ASSY
18. Insulator
19. Insulator
20. Oil level gauge & guide ASSY
21. O-ring
22. Brake booster vacuum hose connection
23. Purge hose connection
A
A
A
Page 81 of 364
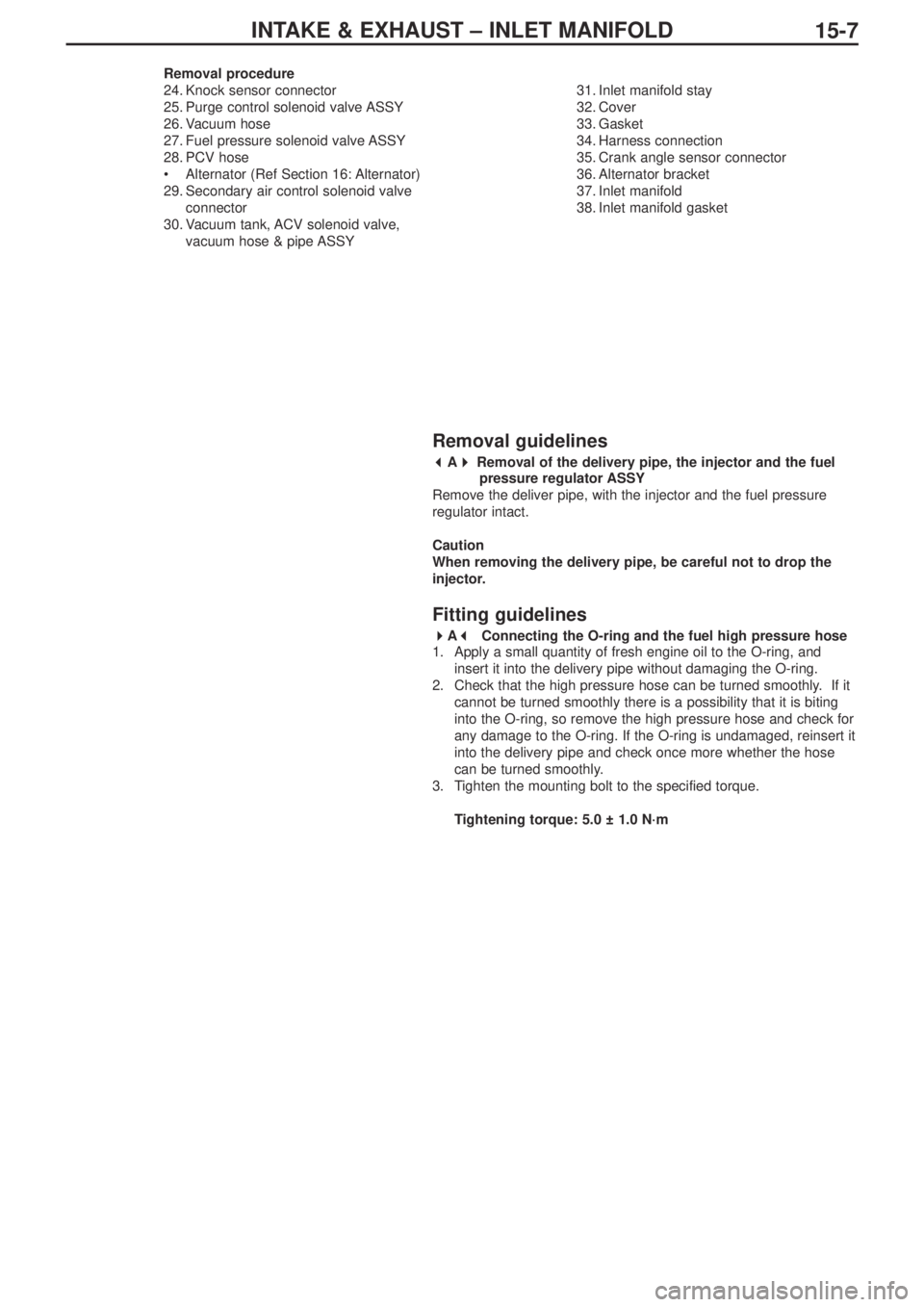
INTAKE & EXHAUST – INLET MANIFOLD
15-7
Removal procedure
24. Knock sensor connector
25. Purge control solenoid valve ASSY
26. Vacuum hose
27. Fuel pressure solenoid valve ASSY
28. PCV hose
•Alternator (Ref Section 16: Alternator)
29. Secondary air control solenoid valve
connector
30. Vacuum tank, ACV solenoid valve,
vacuum hose & pipe ASSY31. Inlet manifold stay
32. Cover
33. Gasket
34. Harness connection
35. Crank angle sensor connector
36. Alternator bracket
37. Inlet manifold
38. Inlet manifold gasket
Removal guidelines
A
Removal of the delivery pipe, the injector and the fuel
pressure regulator ASSY
Remove the deliver pipe, with the injector and the fuel pressure
regulator intact.
Caution
When removing the delivery pipe, be careful not to drop the
injector.
Fitting guidelines
A
Connecting the O-ring and the fuel high pressure hose
1. Apply a small quantity of fresh engine oil to the O-ring, and
insert it into the delivery pipe without damaging the O-ring.
2. Check that the high pressure hose can be turned smoothly. If it
cannot be turned smoothly there is a possibility that it is biting
into the O-ring, so remove the high pressure hose and check for
any damage to the O-ring. If the O-ring is undamaged, reinsert it
into the delivery pipe and check once more whether the hose
can be turned smoothly.
3. Tighten the mounting bolt to the specified torque.
Tightening torque: 5.0 ± 1.0 N·m
Page 83 of 364
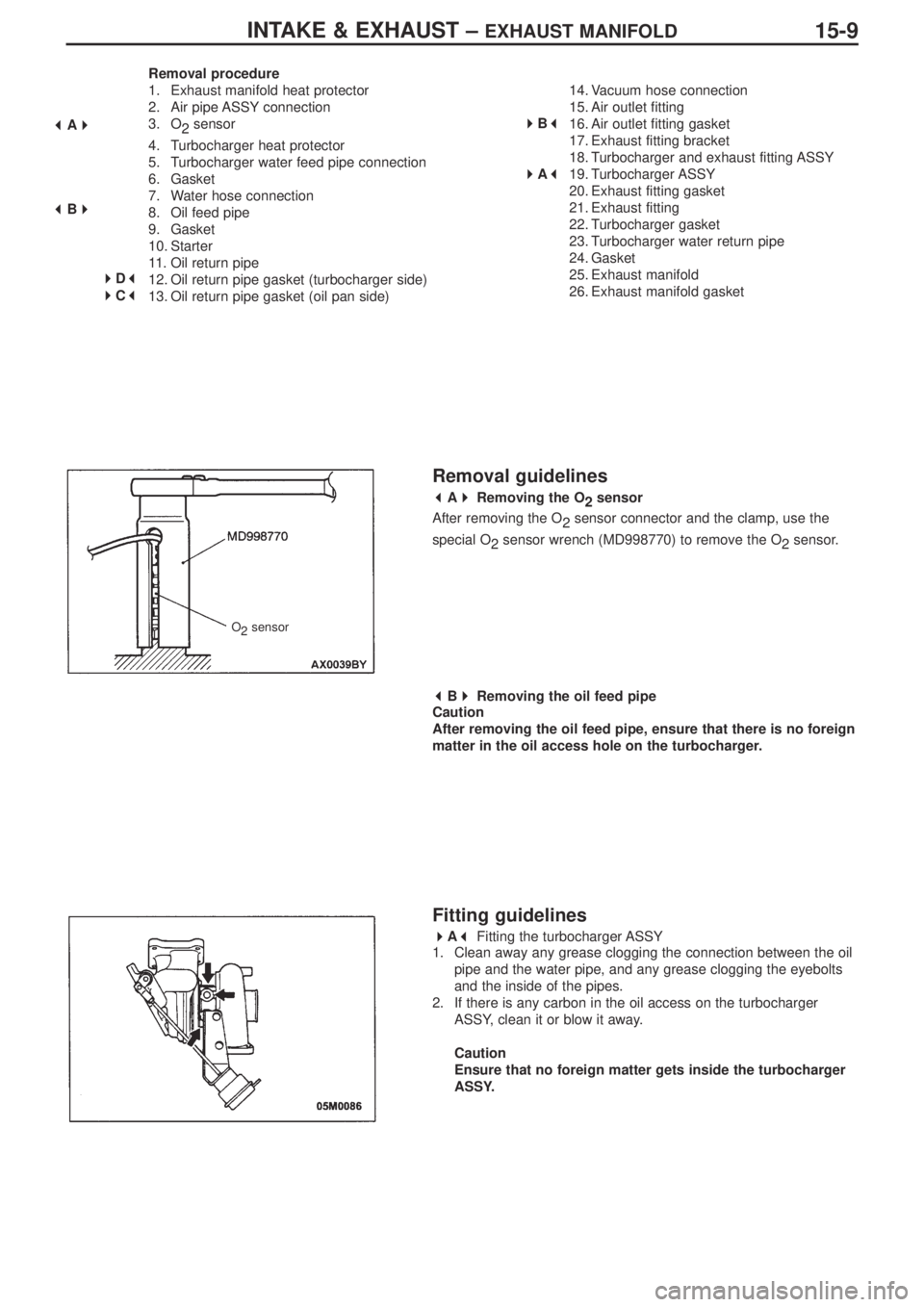
INTAKE & EXHAUST – EXHAUST MANIFOLD15-9
Removal procedure
1. Exhaust manifold heat protector
2. Air pipe ASSY connection
3. O
2sensor
4. Turbocharger heat protector
5. Turbocharger water feed pipe connection
6. Gasket
7. Water hose connection
8. Oil feed pipe
9. Gasket
10. Starter
11.Oil return pipe
12. Oil return pipe gasket (turbocharger side)
13. Oil return pipe gasket (oil pan side)14. Vacuum hose connection
15. Air outlet fitting
16. Air outlet fitting gasket
17. Exhaust fitting bracket
18. Turbocharger and exhaust fitting ASSY
19. Turbocharger ASSY
20. Exhaust fitting gasket
21. Exhaust fitting
22. Turbocharger gasket
23. Turbocharger water return pipe
24. Gasket
25. Exhaust manifold
26. Exhaust manifold gasket
Removal guidelines
A
Removing the O
2sensor
After removing the O
2sensor connector and the clamp, use the
special O
2 sensor wrench (MD998770) to remove the O
2sensor.
B
Removing the oil feed pipe
Caution
After removing the oil feed pipe, ensure that there is no foreign
matter in the oil access hole on the turbocharger.
Fitting guidelines
A
Fitting the turbocharger ASSY
1. Clean away any grease clogging the connection between the oil
pipe and the water pipe, and any grease clogging the eyebolts
and the inside of the pipes.
2. If there is any carbon in the oil access on the turbocharger
ASSY, clean it or blow it away.
Caution
Ensure that no foreign matter gets inside the turbocharger
ASSY.
A
B
D
C
B
A
O
2sensor
Page 85 of 364
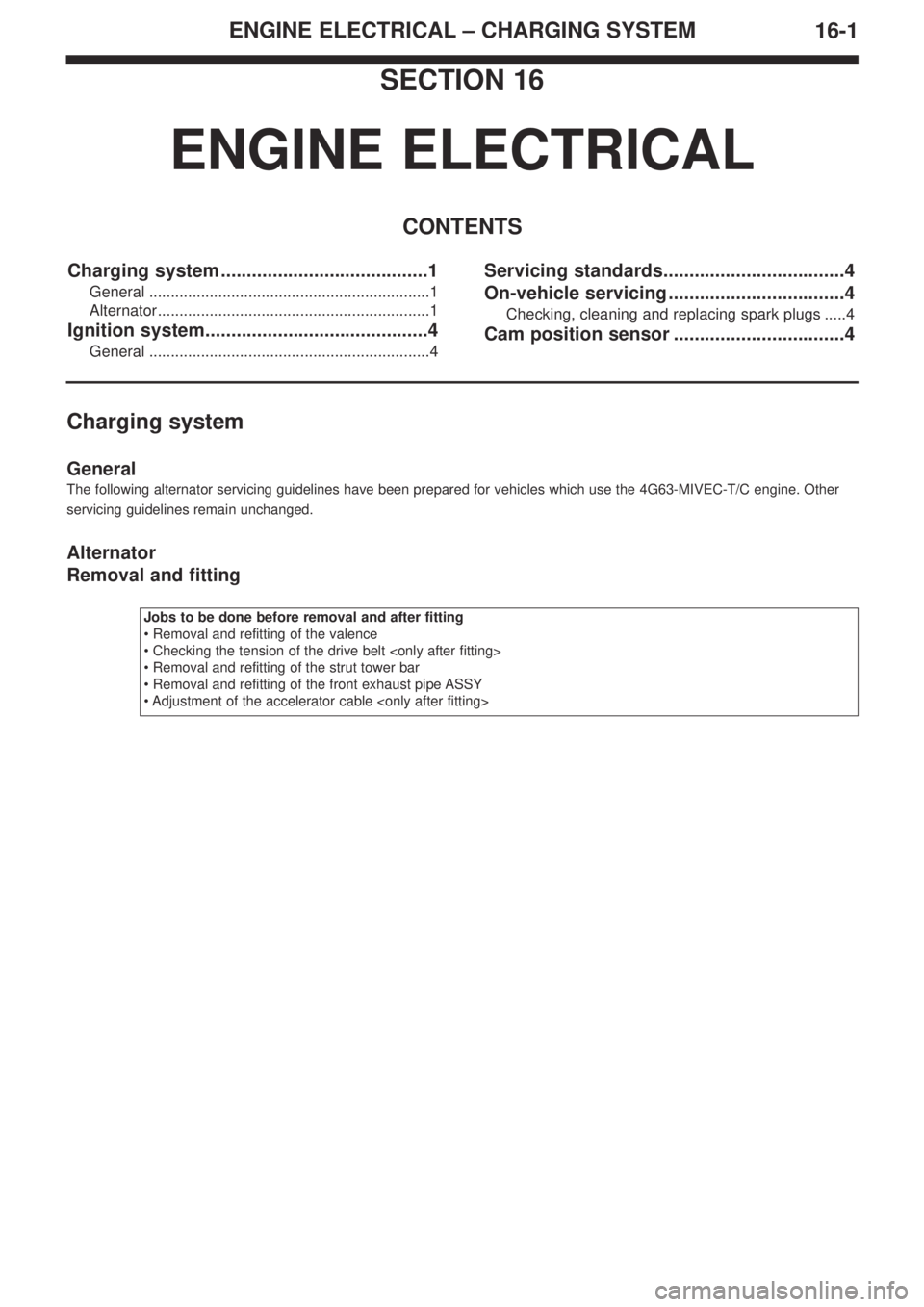
ENGINE ELECTRICAL – CHARGING SYSTEM
16-1
SECTION 16
ENGINE ELECTRICAL
CONTENTS
Charging system ........................................1
General .................................................................1
Alternator...............................................................1
Ignition system...........................................4
General .................................................................4
Servicing standards...................................4
On-vehicle servicing ..................................4
Checking, cleaning and replacing spark plugs .....4
Cam position sensor .................................4
Charging system
General
The following alternator servicing guidelines have been prepared for vehicles which use the 4G63-MIVEC-T/C engine. Other
servicing guidelines remain unchanged.
Alternator
Removal and fitting
Jobs to be done before removal and after fitting
• Removal and refitting of the valence
• Checking the tension of the drive belt
• Removal and refitting of the strut tower bar
• Removal and refitting of the front exhaust pipe ASSY
• Adjustment of the accelerator cable
Page 86 of 364
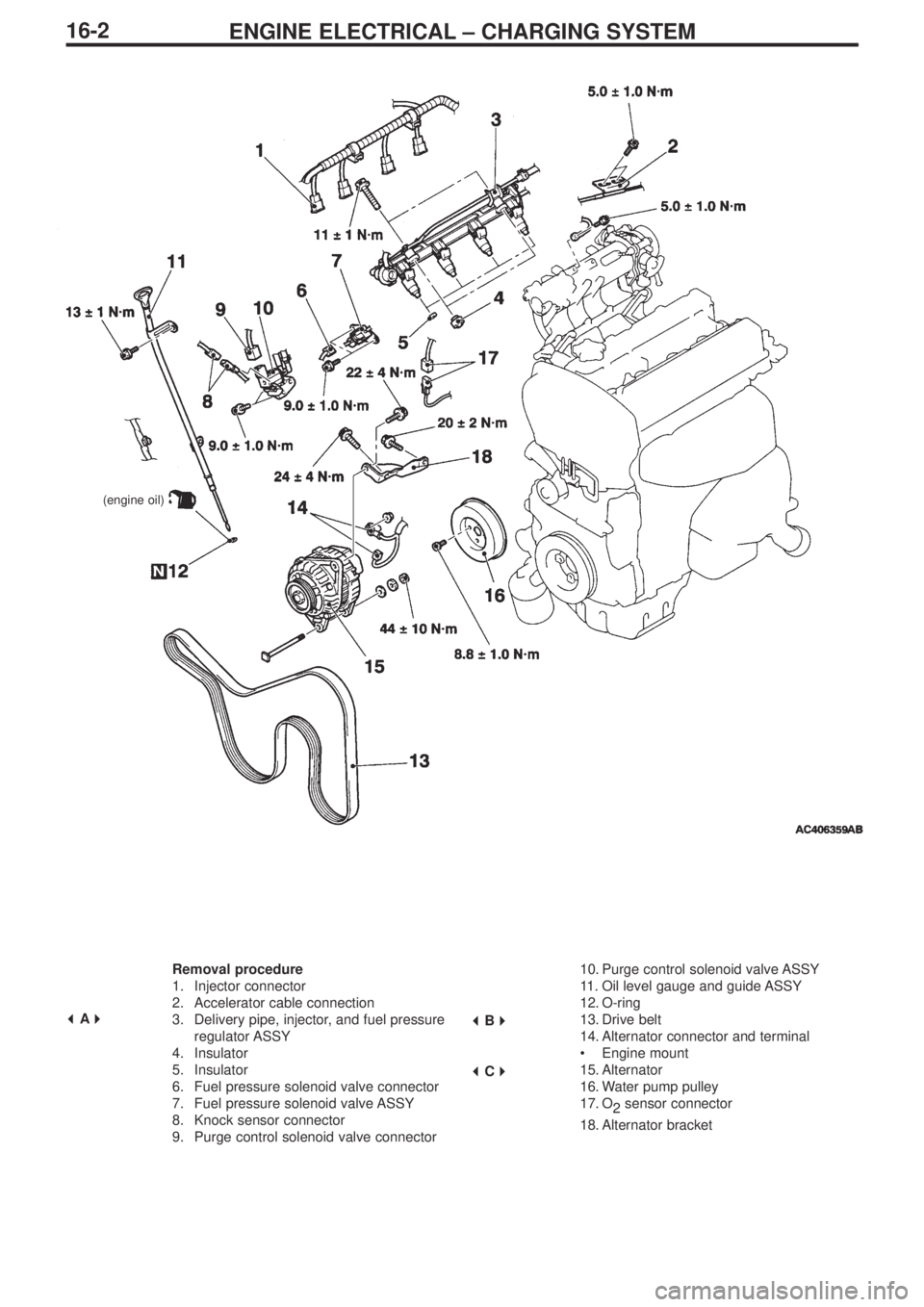
ENGINE ELECTRICAL – CHARGING SYSTEM16-2
Removal procedure
1. Injector connector
2. Accelerator cable connection
3. Delivery pipe, injector, and fuel pressure
regulator ASSY
4. Insulator
5. Insulator
6. Fuel pressure solenoid valve connector
7. Fuel pressure solenoid valve ASSY
8. Knock sensor connector
9. Purge control solenoid valve connector10. Purge control solenoid valve ASSY
11.Oil level gauge and guide ASSY
12. O-ring
13. Drive belt
14. Alternator connector and terminal
• Engine mount
15. Alternator
16. Water pump pulley
17. O
2sensor connector
18. Alternator bracket
(engine oil)
A
B
C
Page 88 of 364
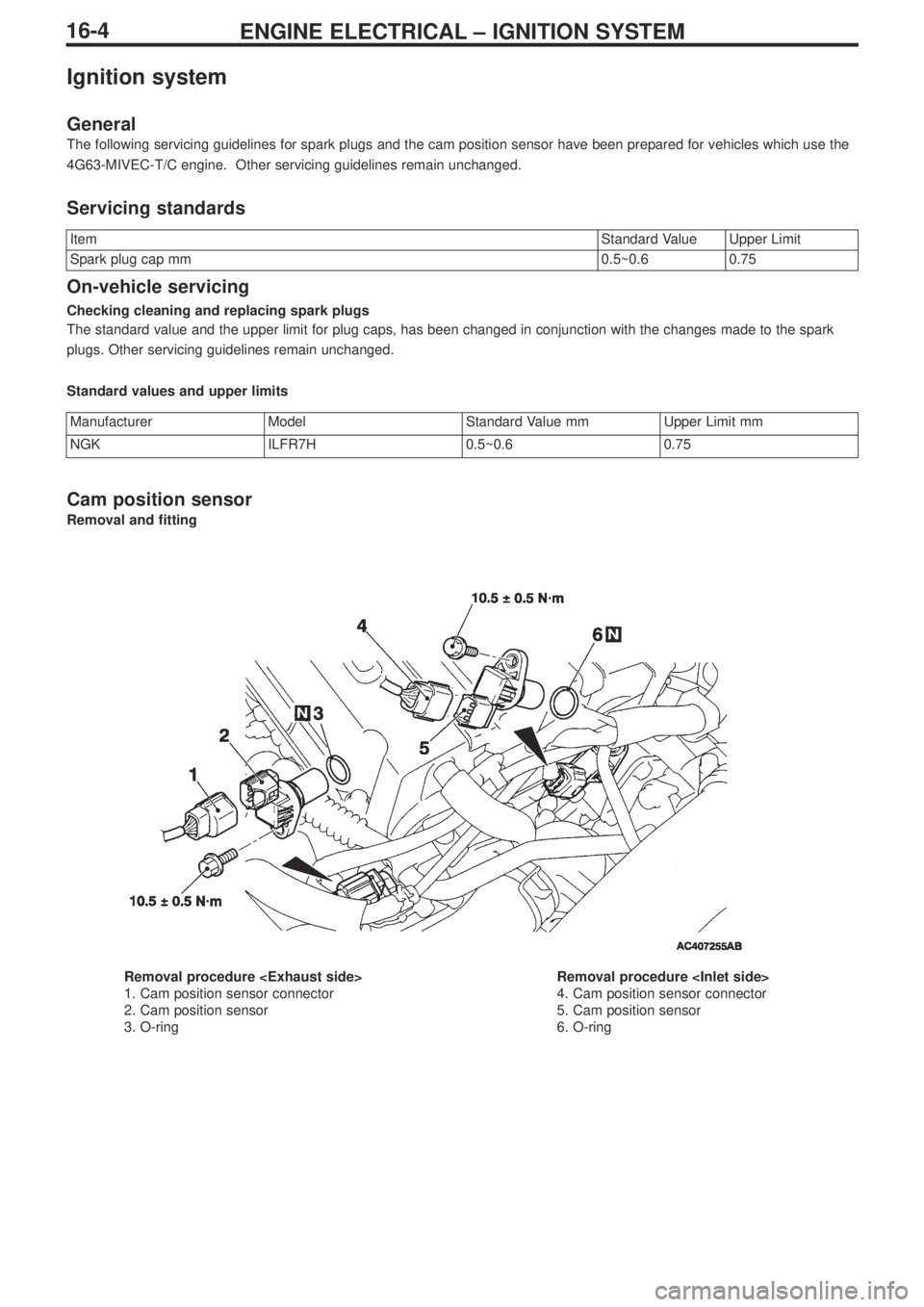
ENGINE ELECTRICAL – IGNITION SYSTEM16-4
Ignition system
General
The following servicing guidelines for spark plugs and the cam position sensor have been prepared for vehicles which use the
4G63-MIVEC-T/C engine. Other servicing guidelines remain unchanged.
Servicing standards
On-vehicle servicing
Checking cleaning and replacing spark plugs
The standard value and the upper limit for plug caps, has been changed in conjunction with the changes made to the spark
plugs. Other servicing guidelines remain unchanged.
Standard values and upper limits
Cam position sensor
Removal and fitting
Removal procedure
1. Cam position sensor connector
2. Cam position sensor
3. O-ringRemoval procedure
4. Cam position sensor connector
5. Cam position sensor
6. O-ring
ItemStandard ValueUpper Limit
Spark plug cap mm0.5~0.60.75
ManufacturerModelStandard Value mmUpper Limit mm
NGKILFR7H0.5~0.60.75
Page 111 of 364
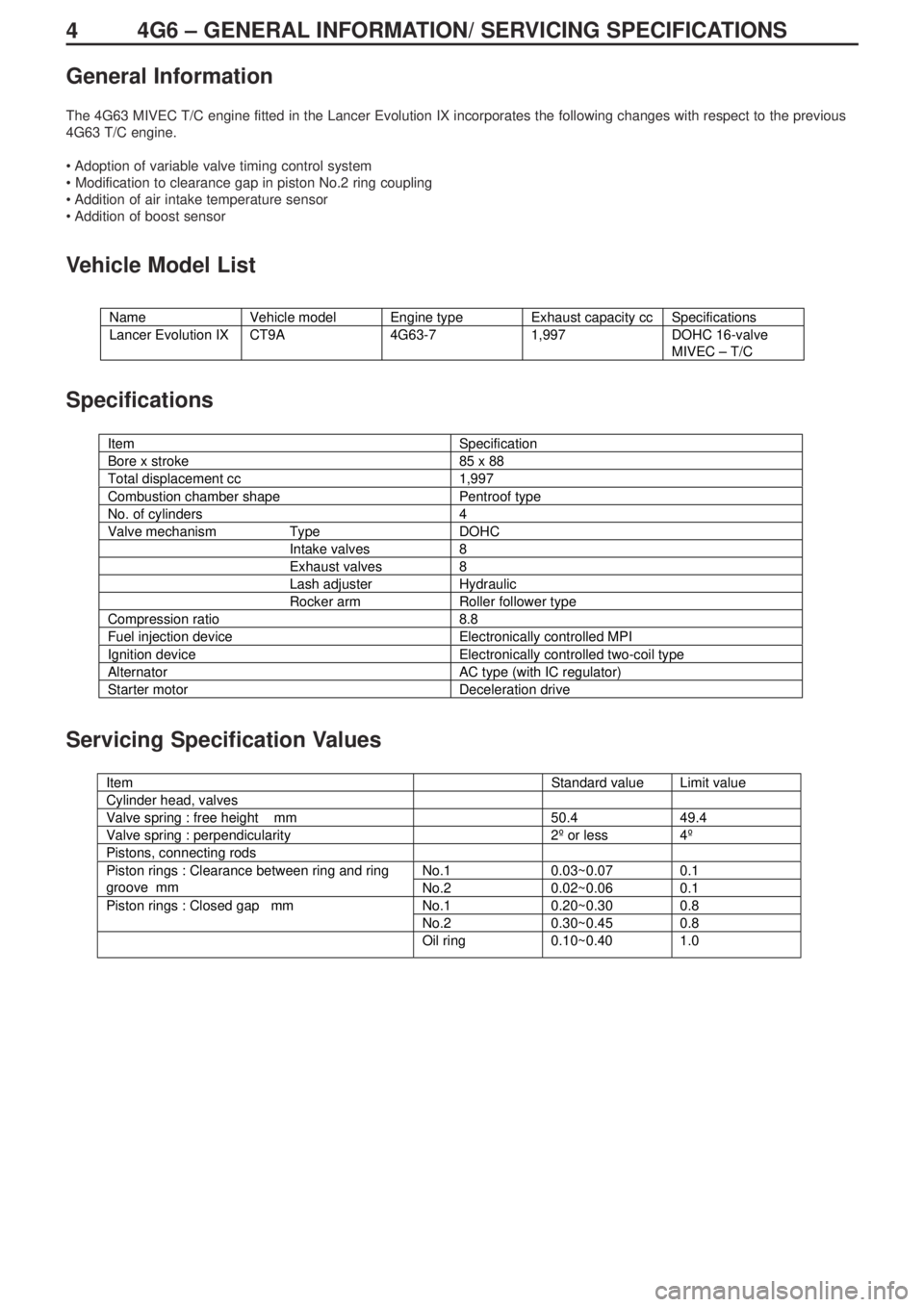
44G6 – GENERAL INFORMATION/ SERVICING SPECIFICATIONS
General Information
The 4G63 MIVEC T/C engine fitted in the Lancer Evolution IX incorporates the following changes with respect to the previous
4G63 T/C engine.
• Adoption of variable valve timing control system
• Modification to clearance gap in piston No.2 ring coupling
• Addition of air intake temperature sensor
• Addition of boost sensor
Vehicle Model List
Specifications
Servicing Specification Values
Name Vehicle model Engine type Exhaust capacity cc Specifications
Lancer Evolution IX CT9A 4G63-7 1,997 DOHC 16-valve
MIVEC – T/C
Item Specification
Bore x stroke 85 x 88
Total displacement cc 1,997
Combustion chamber shape Pentroof type
No. of cylinders 4
Valve mechanism Type DOHC
Intake valves 8
Exhaust valves 8
Lash adjuster Hydraulic
Rocker arm Roller follower type
Compression ratio 8.8
Fuel injection device Electronically controlled MPI
Ignition device Electronically controlled two-coil type
Alternator AC type (with IC regulator)
Starter motor Deceleration drive
g
Item Standard value Limit value
Cylinder head, valves
Valve spring : free height mm 50.4 49.4
Valve spring : perpendicularity 2º or less 4º
Pistons, connecting rods
No.1 0.03~0.07 0.1Piston rings : Clearance between ring and ring
groove mm
No.2 0.02~0.06 0.1
No.1 0.20~0.30 0.8Piston rings : Closed gap mm
No.2 0.30~0.45 0.8
Oil ring 0.10~0.40 1.0
Page 112 of 364
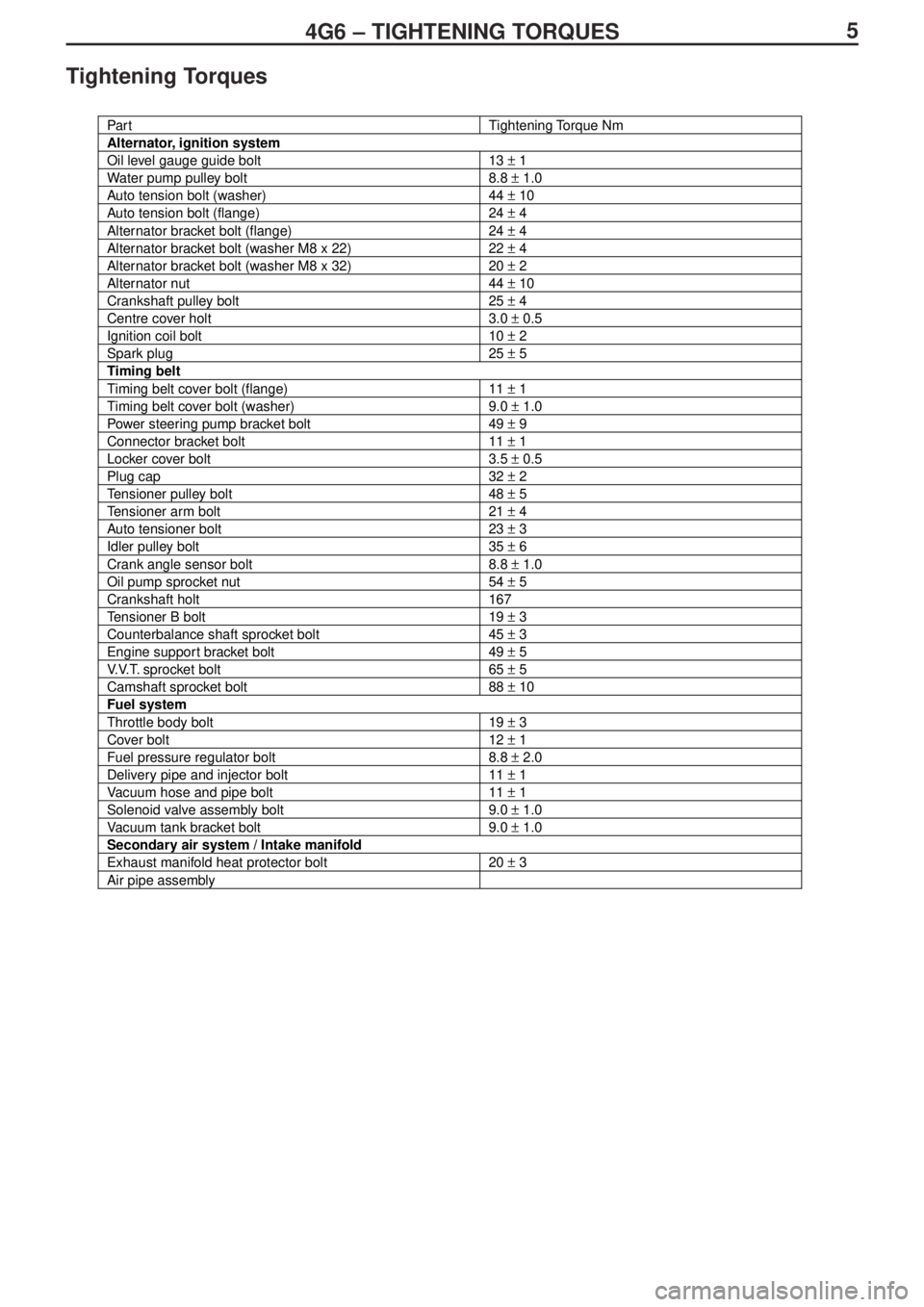
54G6 – TIGHTENING TORQUES
Tightening Torques
Par tTightening Torque Nm
Alternator, ignition system
Oil level gauge guide bolt13 ± 1
Water pump pulley bolt8.8 ± 1.0
Auto tension bolt (washer)44 ± 10
Auto tension bolt (flange)24 ± 4
Alternator bracket bolt (flange)24 ± 4
Alternator bracket bolt (washer M8 x 22)22 ± 4
Alternator bracket bolt (washer M8 x 32)20 ± 2
Alternator nut44 ± 10
Crankshaft pulley bolt25 ± 4
Centre cover holt3.0 ± 0.5
Ignition coil bolt10 ± 2
Spark plug25 ± 5
Timing belt
Timing belt cover bolt (flange)11 ± 1
Timing belt cover bolt (washer)9.0 ± 1.0
Power steering pump bracket bolt49 ± 9
Connector bracket bolt11 ± 1
Locker cover bolt3.5 ± 0.5
Plug cap32 ± 2
Tensioner pulley bolt48 ± 5
Tensioner arm bolt21 ± 4
Auto tensioner bolt23 ± 3
Idler pulley bolt35 ± 6
Crank angle sensor bolt8.8 ± 1.0
Oil pump sprocket nut54 ± 5
Crankshaft holt167
Tensioner B bolt19 ± 3
Counterbalance shaft sprocket bolt45 ± 3
Engine support bracket bolt49 ± 5
V.V.T. sprocket bolt65 ± 5
Camshaft sprocket bolt88 ± 10
Fuel system
Throttle body bolt19 ± 3
Cover bolt12 ± 1
Fuel pressure regulator bolt8.8 ± 2.0
Delivery pipe and injector bolt11 ± 1
Vacuum hose and pipe bolt11 ± 1
Solenoid valve assembly bolt9.0 ± 1.0
Vacuum tank bracket bolt9.0 ± 1.0
Secondary air system / Intake manifold
Exhaust manifold heat protector bolt20 ± 3
Air pipe assembly