sensor MITSUBISHI LANCER EVOLUTION IX 2005 Service Manual
[x] Cancel search | Manufacturer: MITSUBISHI, Model Year: 2005, Model line: LANCER EVOLUTION IX, Model: MITSUBISHI LANCER EVOLUTION IX 2005Pages: 364, PDF Size: 14.38 MB
Page 113 of 364
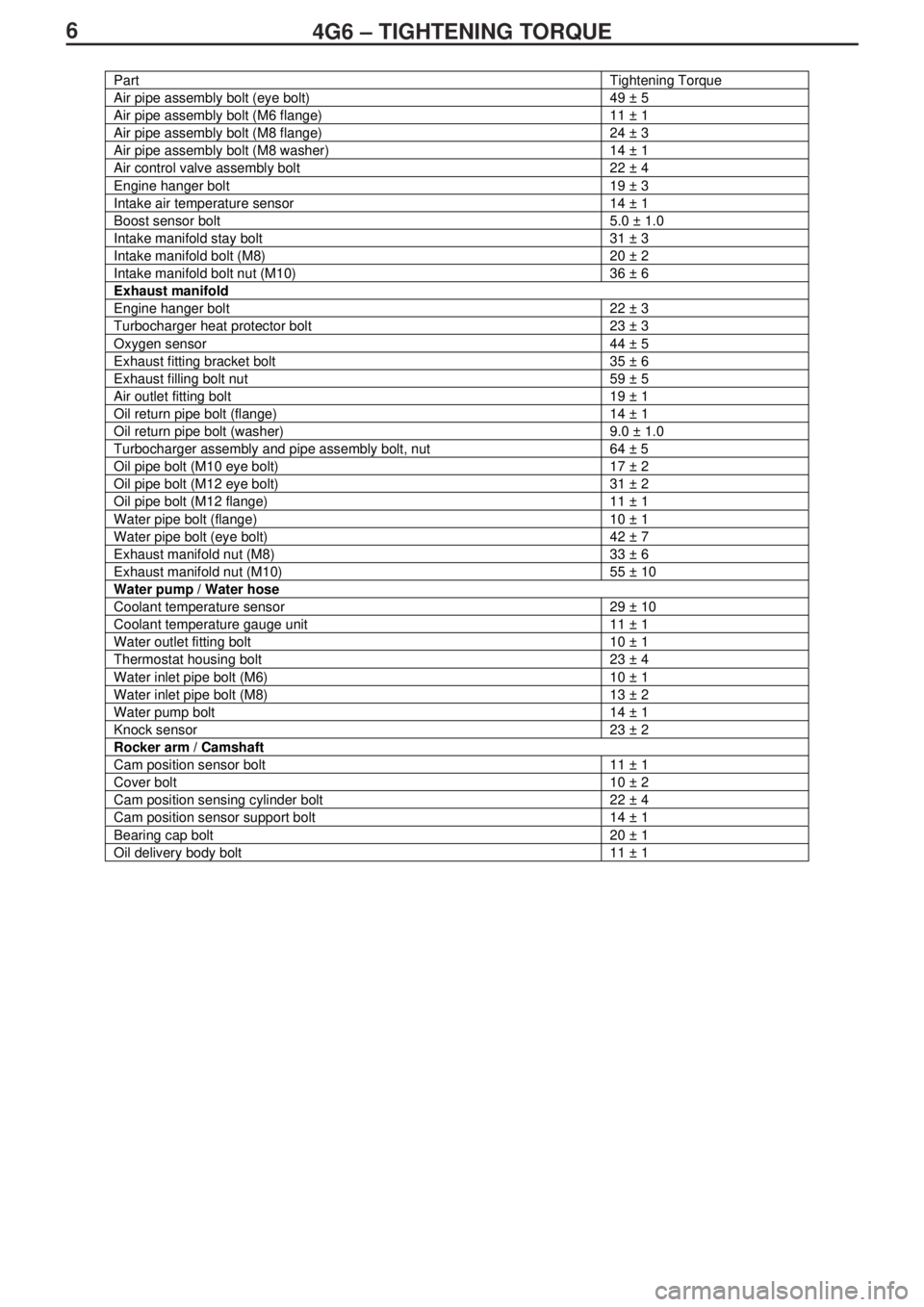
64G6 – TIGHTENING TORQUE
PartTightening Torque
Air pipe assembly bolt (eye bolt) 49 ± 5
Air pipe assembly bolt (M6 flange) 11 ± 1
Air pipe assembly bolt (M8 flange) 24 ± 3
Air pipe assembly bolt (M8 washer) 14 ± 1
Air control valve assembly bolt 22 ± 4
Engine hanger bolt 19 ± 3
Intake air temperature sensor 14 ± 1
Boost sensor bolt 5.0 ± 1.0
Intake manifold stay bolt 31 ± 3
Intake manifold bolt (M8) 20 ± 2
Intake manifold bolt nut (M10) 36 ± 6
Exhaust manifold
Engine hanger bolt 22 ± 3
Turbocharger heat protector bolt 23 ± 3
Oxygen sensor 44 ± 5
Exhaust fitting bracket bolt 35 ± 6
Exhaust filling bolt nut 59 ± 5
Air outlet fitting bolt 19 ± 1
Oil return pipe bolt (flange) 14 ± 1
Oil return pipe bolt (washer) 9.0 ± 1.0
Turbocharger assembly and pipe assembly bolt, nut 64 ± 5
Oil pipe bolt (M10 eye bolt) 17 ± 2
Oil pipe bolt (M12 eye bolt) 31 ± 2
Oil pipe bolt (M12 flange) 11 ± 1
Water pipe bolt (flange) 10 ± 1
Water pipe bolt (eye bolt) 42 ± 7
Exhaust manifold nut (M8) 33 ± 6
Exhaust manifold nut (M10) 55 ± 10
Water pump / Water hose
Coolant temperature sensor 29 ± 10
Coolant temperature gauge unit 11 ± 1
Water outlet fitting bolt 10 ± 1
Thermostat housing bolt 23 ± 4
Water inlet pipe bolt (M6) 10 ± 1
Water inlet pipe bolt (M8) 13 ± 2
Water pump bolt 14 ± 1
Knock sensor 23 ± 2
Rocker arm / Camshaft
Cam position sensor bolt 11 ± 1
Cover bolt 10 ± 2
Cam position sensing cylinder bolt 22 ± 4
Cam position sensor support bolt 14 ± 1
Bearing cap bolt 20 ± 1
Oil delivery body bolt 11 ± 1
Page 114 of 364
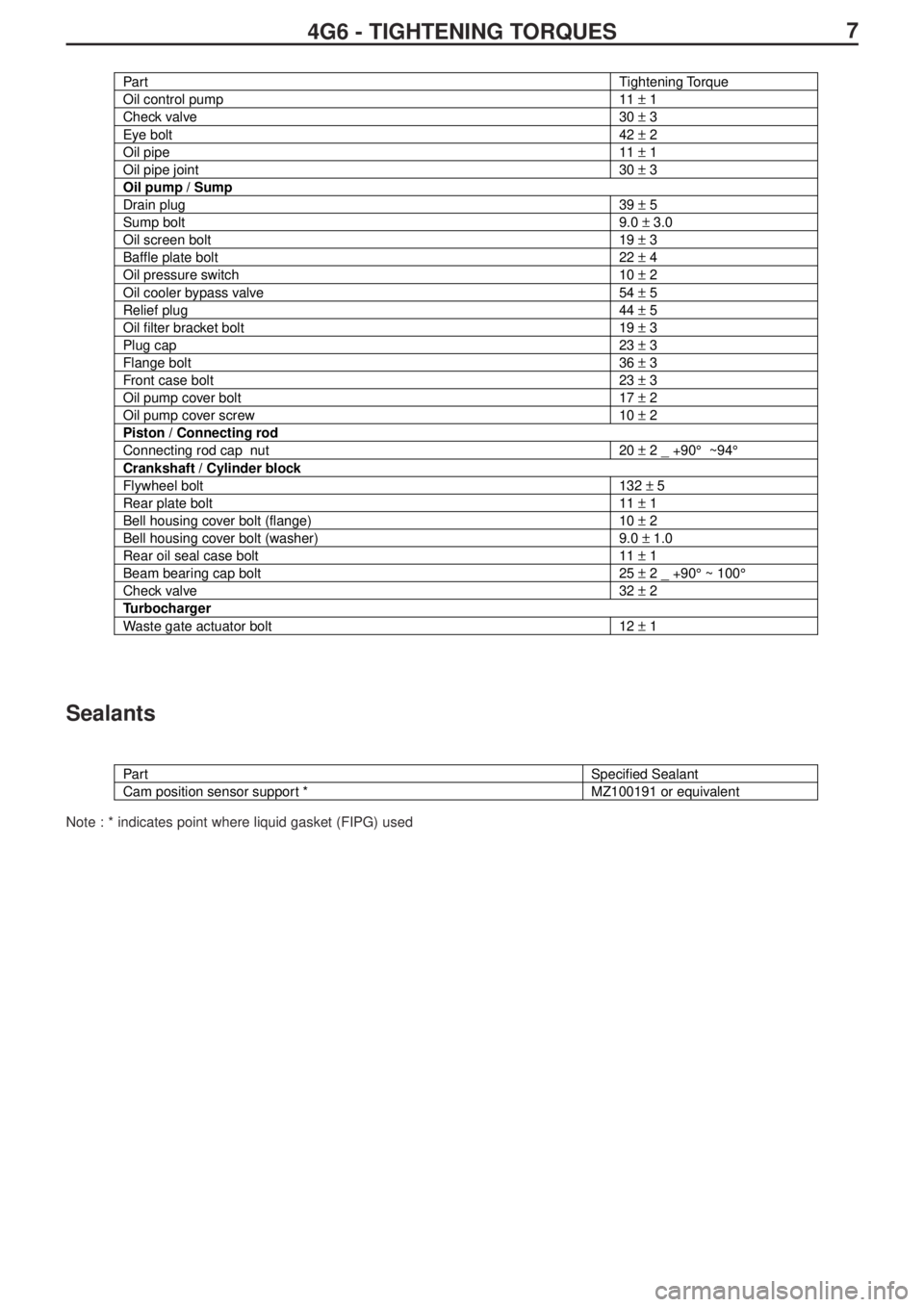
74G6 - TIGHTENING TORQUES
Par tTightening Torque
Oil control pump11 ± 1
Check valve30 ± 3
Eye bolt42 ± 2
Oil pipe11 ± 1
Oil pipe joint30 ± 3
Oil pump / Sump
Drain plug39 ± 5
Sump bolt9.0 ± 3.0
Oil screen bolt19 ± 3
Baffle plate bolt22 ± 4
Oil pressure switch10 ± 2
Oil cooler bypass valve54 ± 5
Relief plug44 ± 5
Oil filter bracket bolt19 ± 3
Plug cap23 ± 3
Flange bolt36 ± 3
Front case bolt23 ± 3
Oil pump cover bolt17 ± 2
Oil pump cover screw10 ± 2
Piston / Connecting rod
Connecting rod cap nut20 ± 2 _ +90° ~94°
Crankshaft / Cylinder block
Flywheel bolt132 ± 5
Rear plate bolt11 ± 1
Bell housing cover bolt (flange)10 ± 2
Bell housing cover bolt (washer)9.0 ± 1.0
Rear oil seal case bolt11 ± 1
Beam bearing cap bolt25 ± 2 _ +90° ~ 100°
Check valve32 ± 2
Turbocharger
Waste gate actuator bolt12 ± 1
Sealants
Par tSpecified Sealant
Cam position sensor support *MZ100191 or equivalent
Note : * indicates point where liquid gasket (FIPG) used
Page 118 of 364
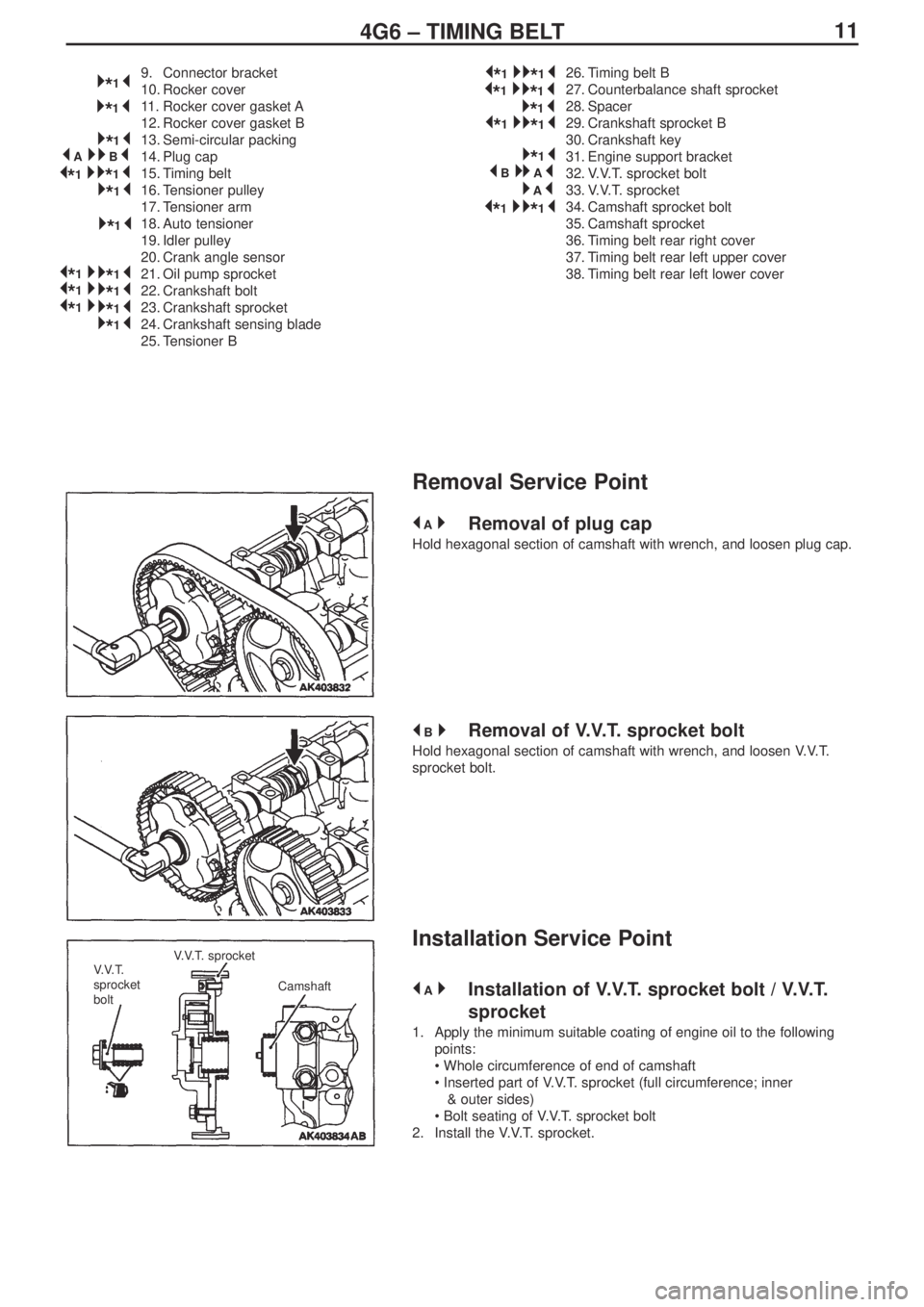
114G6 – TIMING BELT
9. Connector bracket
10. Rocker cover
11.Rocker cover gasket A
12. Rocker cover gasket B
13. Semi-circular packing
14. Plug cap
15. Timing belt
16. Tensioner pulley
17. Tensioner arm
18. Auto tensioner
19. Idler pulley
20. Crank angle sensor
21. Oil pump sprocket
22. Crankshaft bolt
23. Crankshaft sprocket
24. Crankshaft sensing blade
25. Tensioner B26. Timing belt B
27. Counterbalance shaft sprocket
28. Spacer
29. Crankshaft sprocket B
30. Crankshaft key
31. Engine support bracket
32. V.V.T. sprocket bolt
33. V.V.T. sprocket
34. Camshaft sprocket bolt
35. Camshaft sprocket
36. Timing belt rear right cover
37. Timing belt rear left upper cover
38. Timing belt rear left lower cover
Removal Service Point
Removal of plug cap
Hold hexagonal section of camshaft with wrench, and loosen plug cap.
Removal of V.V.T. sprocket bolt
Hold hexagonal section of camshaft with wrench, and loosen V.V.T.
sprocket bolt.
Installation Service Point
Installation of V.V.T. sprocket bolt / V.V.T.
sprocket
1. Apply the minimum suitable coating of engine oil to the following
points:
• Whole circumference of end of camshaft
• Inserted part of V.V.T. sprocket (full circumference; inner
& outer sides)
• Bolt seating of V.V.T. sprocket bolt
2. Install the V.V.T. sprocket.
V. V. T.
sprocket
boltV.V.T. sprocket
Camshaft
* A
* B
B*
A*
A*
* * 1
* * 1
* * 1
* * 1
* * 1
* * 1
* * 1
* * 1
* 1*
* 1*
* 1*
* 1*
* 1*
* 1*
* 1*
* 1*
* 1*
* 1*
* 1*
* 1*
* 1*
* 1*
* 1*
* 1*
* A
* B
* A
Page 122 of 364
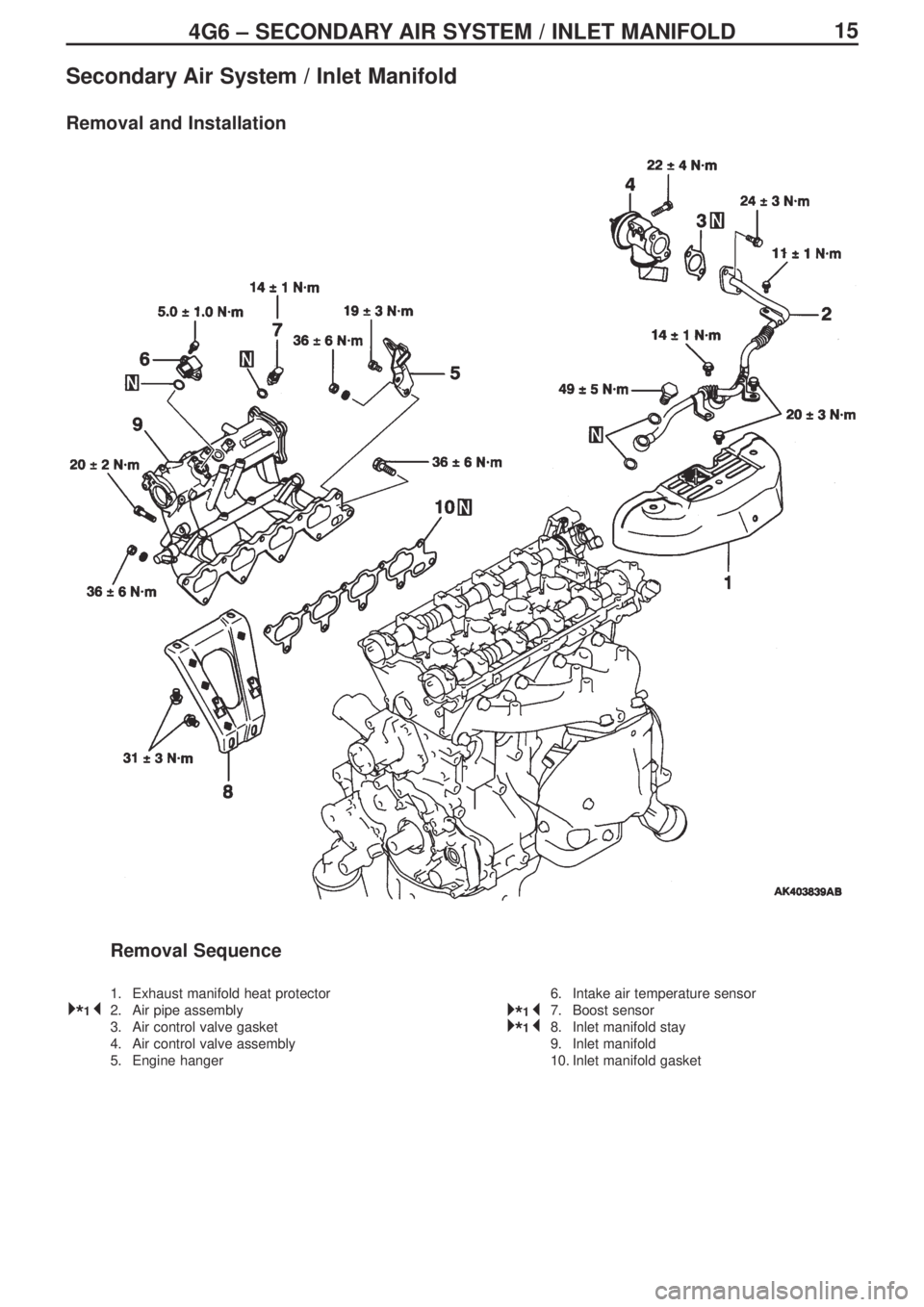
154G6 – SECONDARY AIR SYSTEM / INLET MANIFOLD
Secondary Air System / Inlet Manifold
Removal and Installation
Removal Sequence
1. Exhaust manifold heat protector
2. Air pipe assembly
3. Air control valve gasket
4. Air control valve assembly
5. Engine hanger6. Intake air temperature sensor
7. Boost sensor
8. Inlet manifold stay
9. Inlet manifold
10. Inlet manifold gasket
* 1*
* 1*
* 1*
Page 123 of 364

164G6 – EXHAUST MANIFOLD
Exhaust Manifold
Removal and Installation
Removal Sequence
1. Engine hanger
2. Turbocharger heat protector
3. Oxygen sensor
4. Exhaust fitting bracket
5. Exhaust fitting
6. Exhaust fitting gasket
7. Air outlet fitting
8. Air outlet fitting gasket
9. Oil return pipe10. Oil return pipe gasket
11.Oil return pipe gasket
12. Turbocharger assembly & pipe assembly
13. Turbocharger gasket
14. Oil pump
15. Water pipe B
16. Water pipe A
17. Turbocharger assembly
18. Exhaust manifold
19. Exhaust manifold gasket
* 1*
* 1 *
* 1*
Page 124 of 364
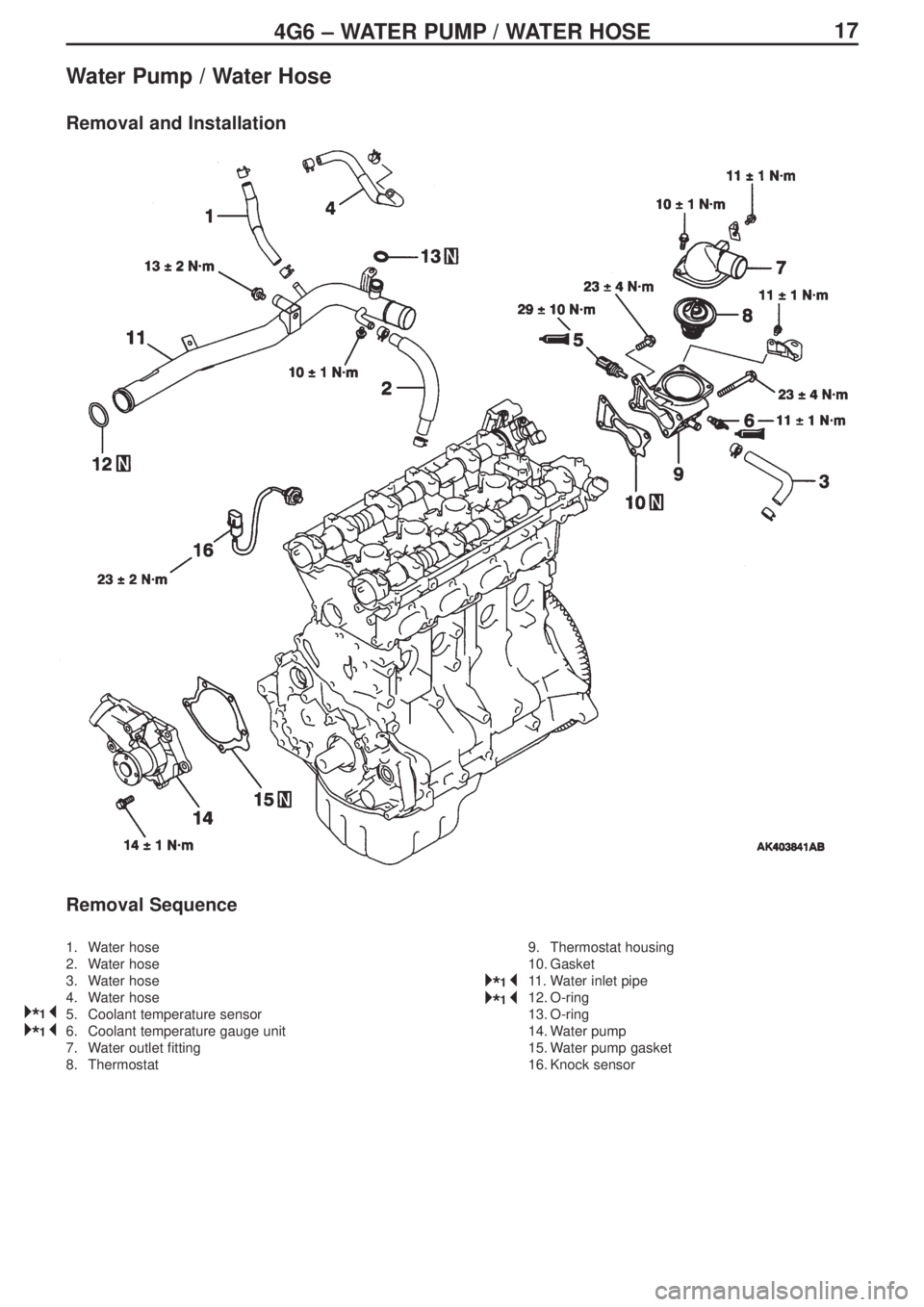
174G6 – WATER PUMP / WATER HOSE
Water Pump / Water Hose
Removal and Installation
Removal Sequence
1. Water hose
2. Water hose
3. Water hose
4. Water hose
5. Coolant temperature sensor
6. Coolant temperature gauge unit
7. Water outlet fitting
8. Thermostat9. Thermostat housing
10. Gasket
11.Water inlet pipe
12. O-ring
13. O-ring
14. Water pump
15. Water pump gasket
16. Knock sensor
* 1*
* 1*
* 1*
* 1*
Page 125 of 364
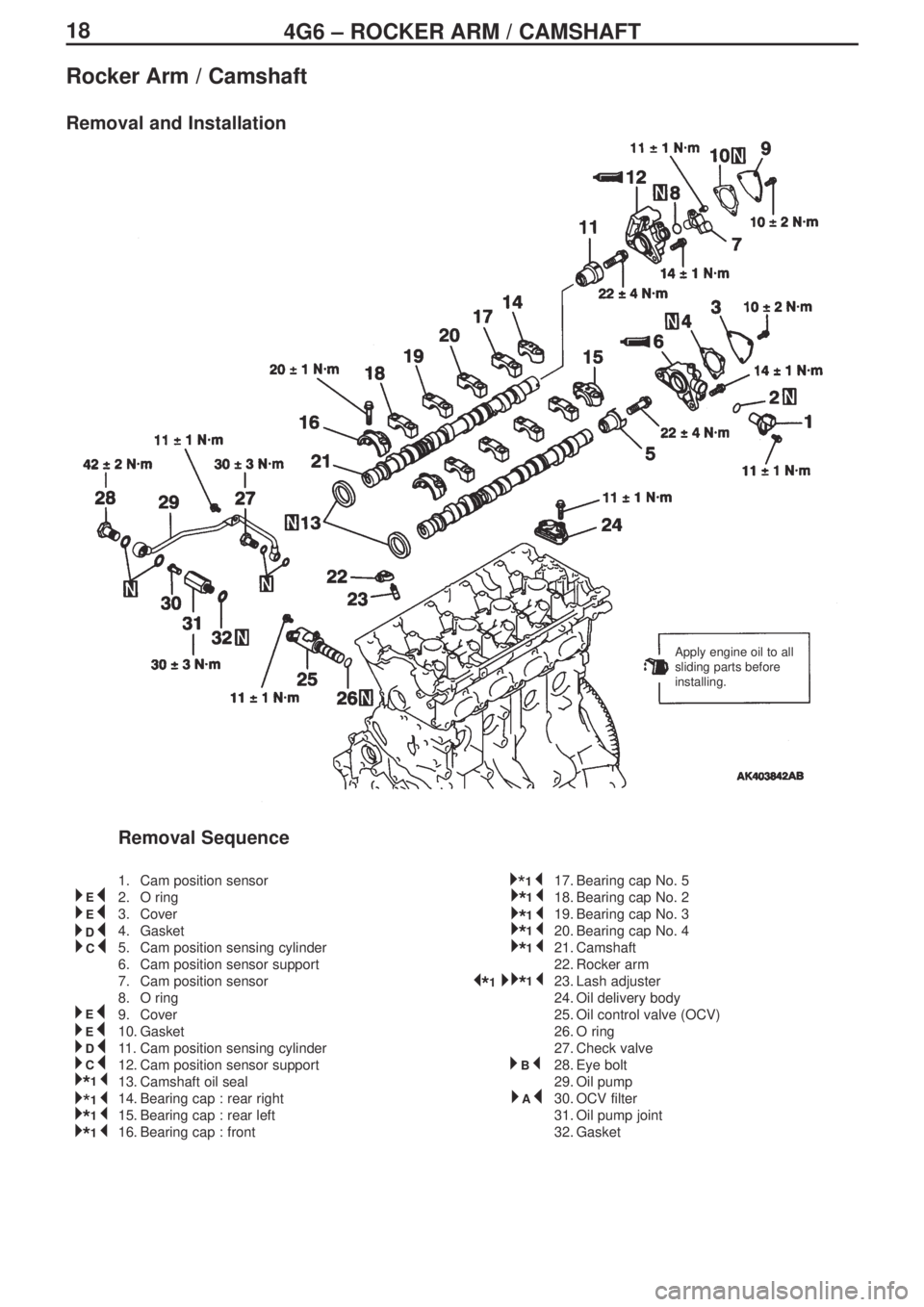
184G6 – ROCKER ARM / CAMSHAFT
Rocker Arm / Camshaft
Removal and Installation
Removal Sequence
1. Cam position sensor
2. O ring
3. Cover
4. Gasket
5. Cam position sensing cylinder
6. Cam position sensor support
7. Cam position sensor
8. O ring
9. Cover
10. Gasket
11.Cam position sensing cylinder
12. Cam position sensor support
13. Camshaft oil seal
14. Bearing cap : rear right
15. Bearing cap : rear left
16. Bearing cap : front17. Bearing cap No. 5
18. Bearing cap No. 2
19. Bearing cap No. 3
20. Bearing cap No. 4
21. Camshaft
22. Rocker arm
23. Lash adjuster
24. Oil delivery body
25. Oil control valve (OCV)
26. O ring
27. Check valve
28. Eye bolt
29. Oil pump
30. OCV filter
31. Oil pump joint
32. Gasket
Apply engine oil to all
sliding parts before
installing.
E *
E
*
D
*
D
*
C
*
C
*
E
*
E
*
* 1*
*1*
* 1*
* 1*
*1*
* 1*
* 1*
* 1*
* 1*
* 1* * * 1
B*
A *
Page 126 of 364
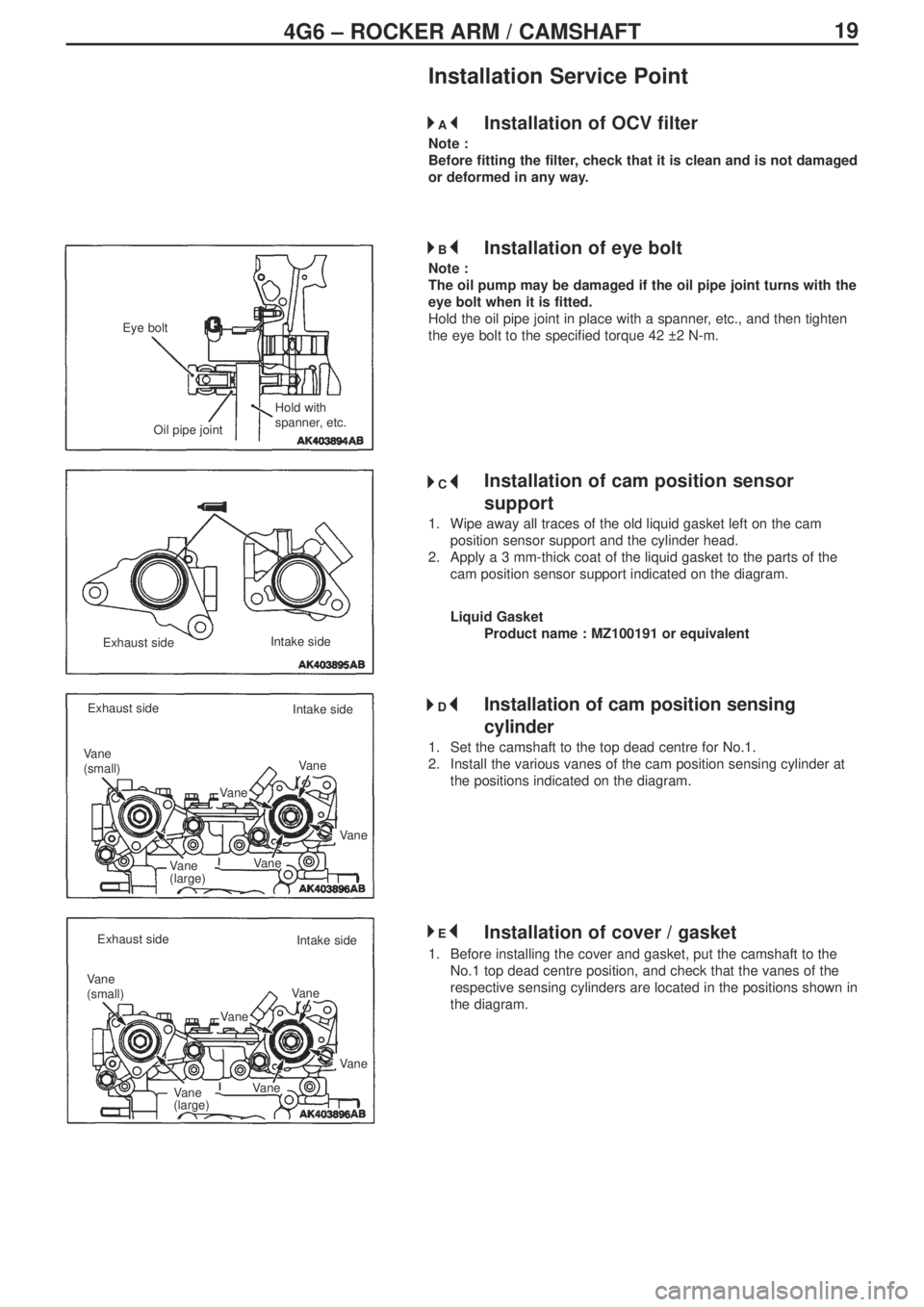
194G6 – ROCKER ARM / CAMSHAFT
Installation Service Point
Installation of OCV filter
Note :
Before fitting the filter, check that it is clean and is not damaged
or deformed in any way.
Installation of eye bolt
Note :
The oil pump may be damaged if the oil pipe joint turns with the
eye bolt when it is fitted.
Hold the oil pipe joint in place with a spanner, etc., and then tighten
the eye bolt to the specified torque 42 ±2 N-m.
Installation of cam position sensor
support
1. Wipe away all traces of the old liquid gasket left on the cam
position sensor support and the cylinder head.
2. Apply a 3 mm-thick coat of the liquid gasket to the parts of the
cam position sensor support indicated on the diagram.
Liquid Gasket
Product name : MZ100191 or equivalent
Installation of cam position sensing
cylinder
1. Set the camshaft to the top dead centre for No.1.
2. Install the various vanes of the cam position sensing cylinder at
the positions indicated on the diagram.
Installation of cover / gasket
1. Before installing the cover and gasket, put the camshaft to the
No.1 top dead centre position, and check that the vanes of the
respective sensing cylinders are located in the positions shown in
the diagram.
Eye bolt
Hold with
spanner, etc.
Oil pipe joint
Exhaust sideIntake side
Exhaust side
Exhaust sideIntake side
Intake sideVane
Vane
Vane
Vane VaneVane
Vane Vane
Vane
(large) Vane
(large) Vane
(small)
Vane
(small)
A*
B *
C
*
D
*
E
*
Page 138 of 364
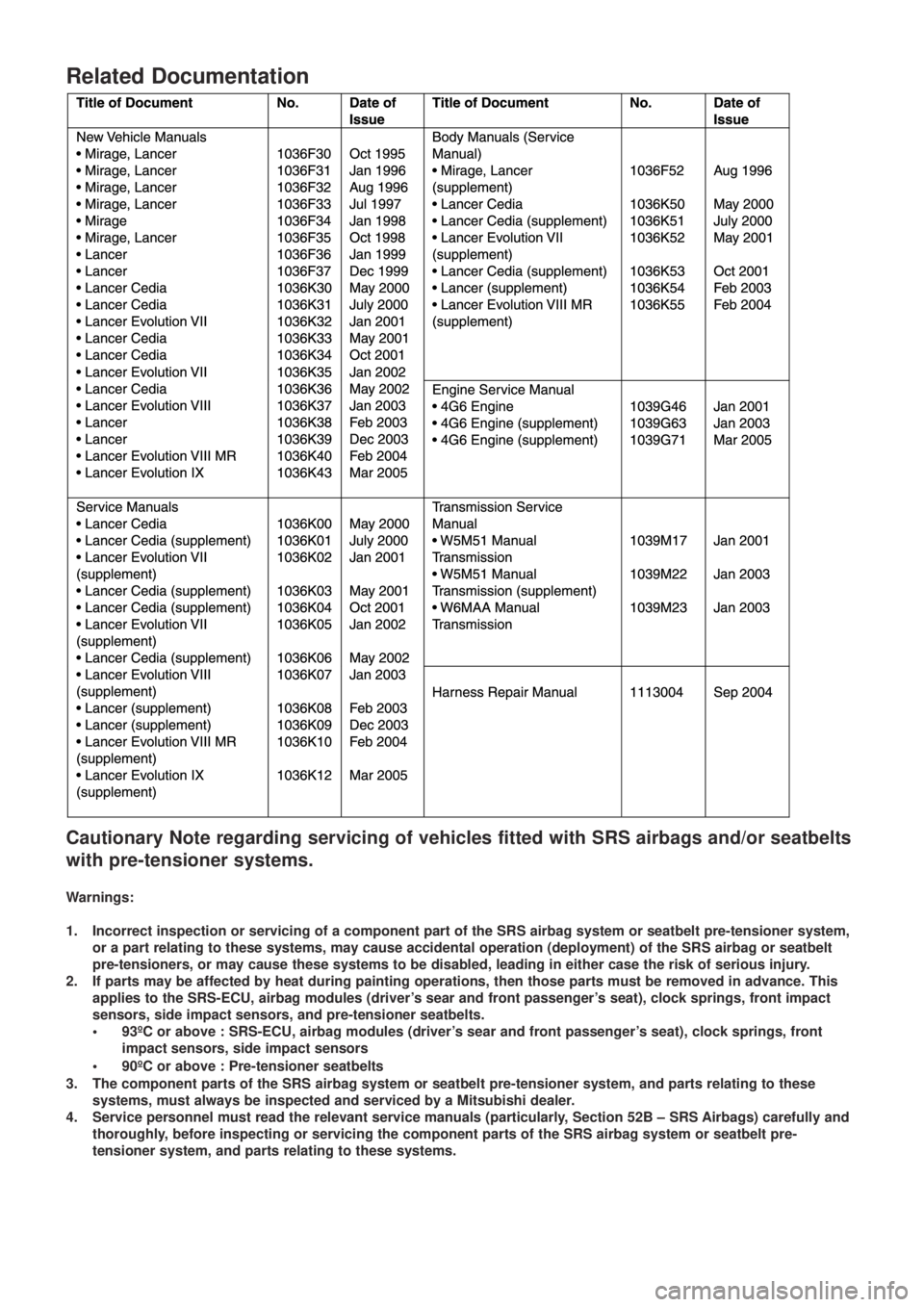
Related Documentation
Cautionary Note regarding servicing of vehicles fitted with SRS airbags and/or seatbelts
with pre-tensioner systems.
Warnings:
1. Incorrect inspection or servicing of a component part of the SRS airbag system or seatbelt pre-tensioner system,
or a part relating to these systems, may cause accidental operation (deployment) of the SRS airbag or seatbelt
pre-tensioners, or may cause these systems to be disabled, leading in either case the risk of serious injury.
2. If parts may be affected by heat during painting operations, then those parts must be removed in advance. This
applies to the SRS-ECU, airbag modules (driver’s sear and front passenger’s seat), clock springs, front impact
sensors, side impact sensors, and pre-tensioner seatbelts.
• 93ºC or above : SRS-ECU, airbag modules (driver’s sear and front passenger’s seat), clock springs, front
impact sensors, side impact sensors
•90ºC or above : Pre-tensioner seatbelts
3. The component parts of the SRS airbag system or seatbelt pre-tensioner system, and parts relating to these
systems, must always be inspected and serviced by a Mitsubishi dealer.
4. Service personnel must read the relevant service manuals (particularly, Section 52B – SRS Airbags) carefully and
thoroughly, before inspecting or servicing the component parts of the SRS airbag system or seatbelt pre-
tensioner system, and parts relating to these systems.
Page 142 of 364
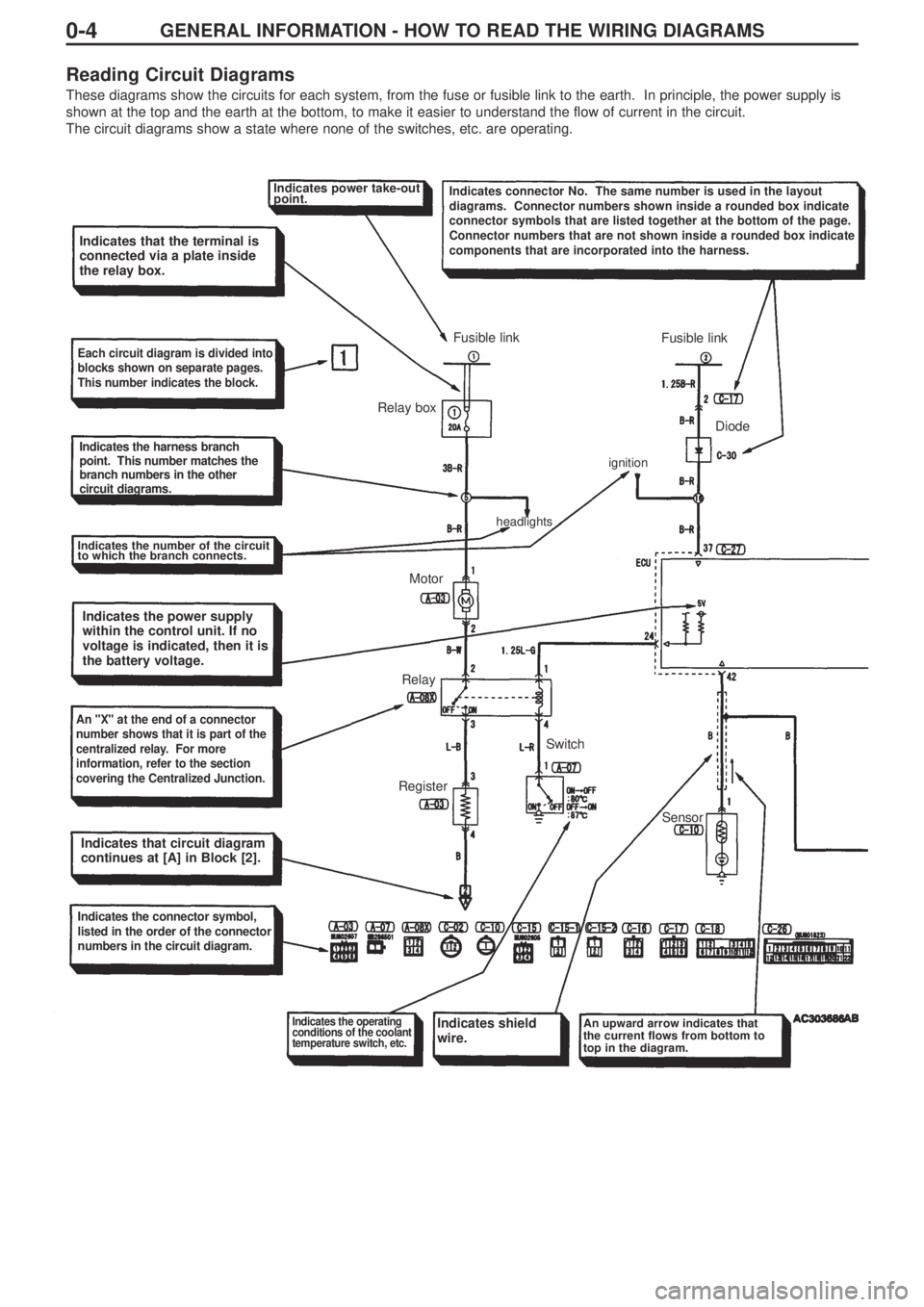
GENERAL INFORMATION - HOW TO READ THE WIRING DIAGRAMS0-4
Reading Circuit Diagrams
These diagrams show the circuits for each system, from the fuse or fusible link to the earth. In principle, the power supply is
shown at the top and the earth at the bottom, to make it easier to understand the flow of current in the circuit.
The circuit diagrams show a state where none of the switches, etc. are operating.
Indicates power take-out
point.Indicates connector No. The same number is used in the layout
diagrams. Connector numbers shown inside a rounded box indicate
connector symbols that are listed together at the bottom of the page.
Connector numbers that are not shown inside a rounded box indicate
components that are incorporated into the harness.
Indicates that the terminal is
connected via a plate inside
the relay box.
Each circuit diagram is divided into
blocks shown on separate pages.
This number indicates the block.
Indicates the harness branch
point. This number matches the
branch numbers in the other
circuit diagrams.
Indicates the number of the circuit
to which the branch connects.
Indicates the power supply
within the control unit. If no
voltage is indicated, then it is
the battery voltage.
An "X" at the end of a connector
number shows that it is part of the
centralized relay. For more
information, refer to the section
covering the Centralized Junction.
Indicates that circuit diagram
continues at [A] in Block [2].
Indicates the connector symbol,
listed in the order of the connector
numbers in the circuit diagram.
Indicates the operating
conditions of the coolant
temperature switch, etc.Indicates shield
wire.An upward arrow indicates that
the current flows from bottom to
top in the diagram.
RegisterRelayMotor Relay boxFusible link
Fusible link
Diode
Sensor Switch
headlightsignition