check engine MITSUBISHI LANCER EVOLUTION IX 2005 Service Manual
[x] Cancel search | Manufacturer: MITSUBISHI, Model Year: 2005, Model line: LANCER EVOLUTION IX, Model: MITSUBISHI LANCER EVOLUTION IX 2005Pages: 364, PDF Size: 14.38 MB
Page 65 of 364
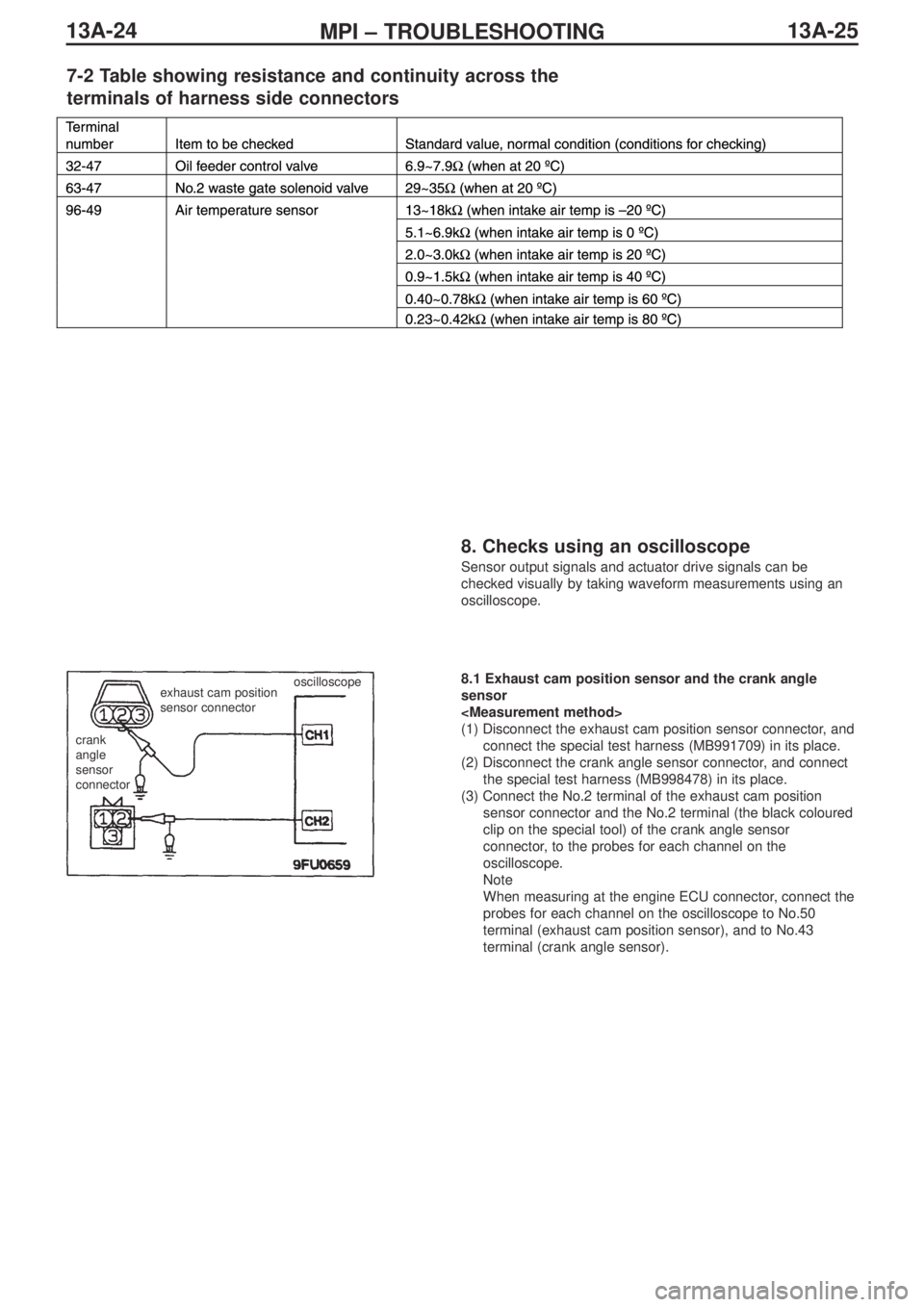
13A-25MPI – TROUBLESHOOTING 13A-24
7-2 Table showing resistance and continuity across the
terminals of harness side connectors
8. Checks using an oscilloscope
Sensor output signals and actuator drive signals can be
checked visually by taking waveform measurements using an
oscilloscope.
crank
angle
sensor
connectorexhaust cam position
sensor connector
oscilloscope8.1 Exhaust cam position sensor and the crank angle
sensor
(1) Disconnect the exhaust cam position sensor connector, and
connect the special test harness (MB991709) in its place.
(2) Disconnect the crank angle sensor connector, and connect
the special test harness (MB998478) in its place.
(3) Connect the No.2 terminal of the exhaust cam position
sensor connector and the No.2 terminal (the black coloured
clip on the special tool) of the crank angle sensor
connector, to the probes for each channel on the
oscilloscope.
Note
When measuring at the engine ECU connector, connect the
probes for each channel on the oscilloscope to No.50
terminal (exhaust cam position sensor), and to No.43
terminal (crank angle sensor).
Page 66 of 364
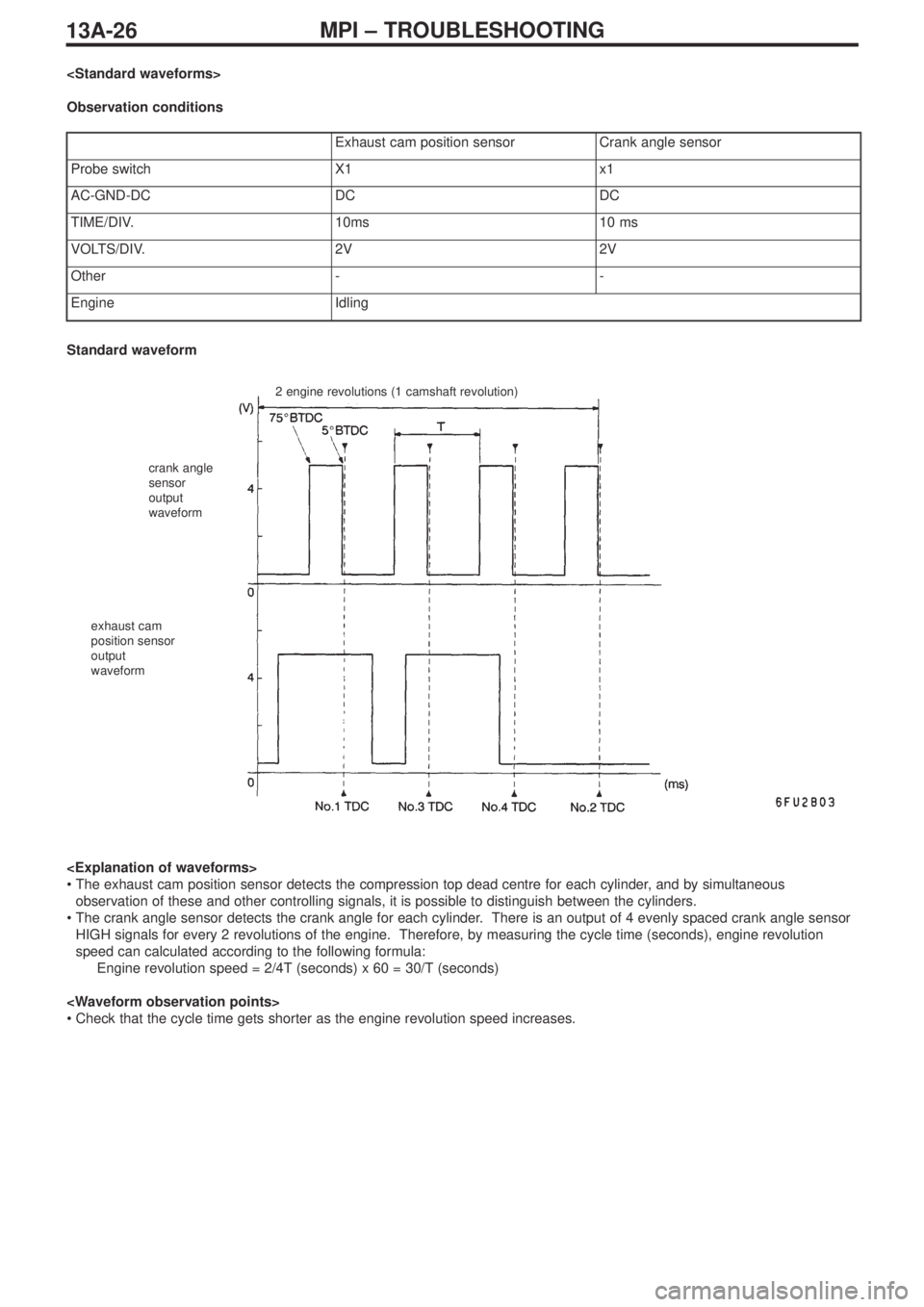
13A-26MPI – TROUBLESHOOTING
Observation conditions
Exhaust cam position sensorCrank angle sensor
Probe switchX1x1
AC-GND-DCDCDC
TIME/DIV.10ms10 ms
VOLTS/DIV.2V2V
Other--
EngineIdling
2 engine revolutions (1 camshaft revolution)
crank angle
sensor
output
waveform
exhaust cam
position sensor
output
waveform
Standard waveform
•The exhaust cam position sensor detects the compression top dead centre for each cylinder, and by simultaneous
observation of these and other controlling signals, it is possible to distinguish between the cylinders.
•The crank angle sensor detects the crank angle for each cylinder. There is an output of 4 evenly spaced crank angle sensor
HIGH signals for every 2 revolutions of the engine. Therefore, by measuring the cycle time (seconds), engine revolution
speed can calculated according to the following formula:
Engine revolution speed = 2/4T (seconds) x 60 = 30/T (seconds)
•Check that the cycle time gets shorter as the engine revolution speed increases.
Page 67 of 364
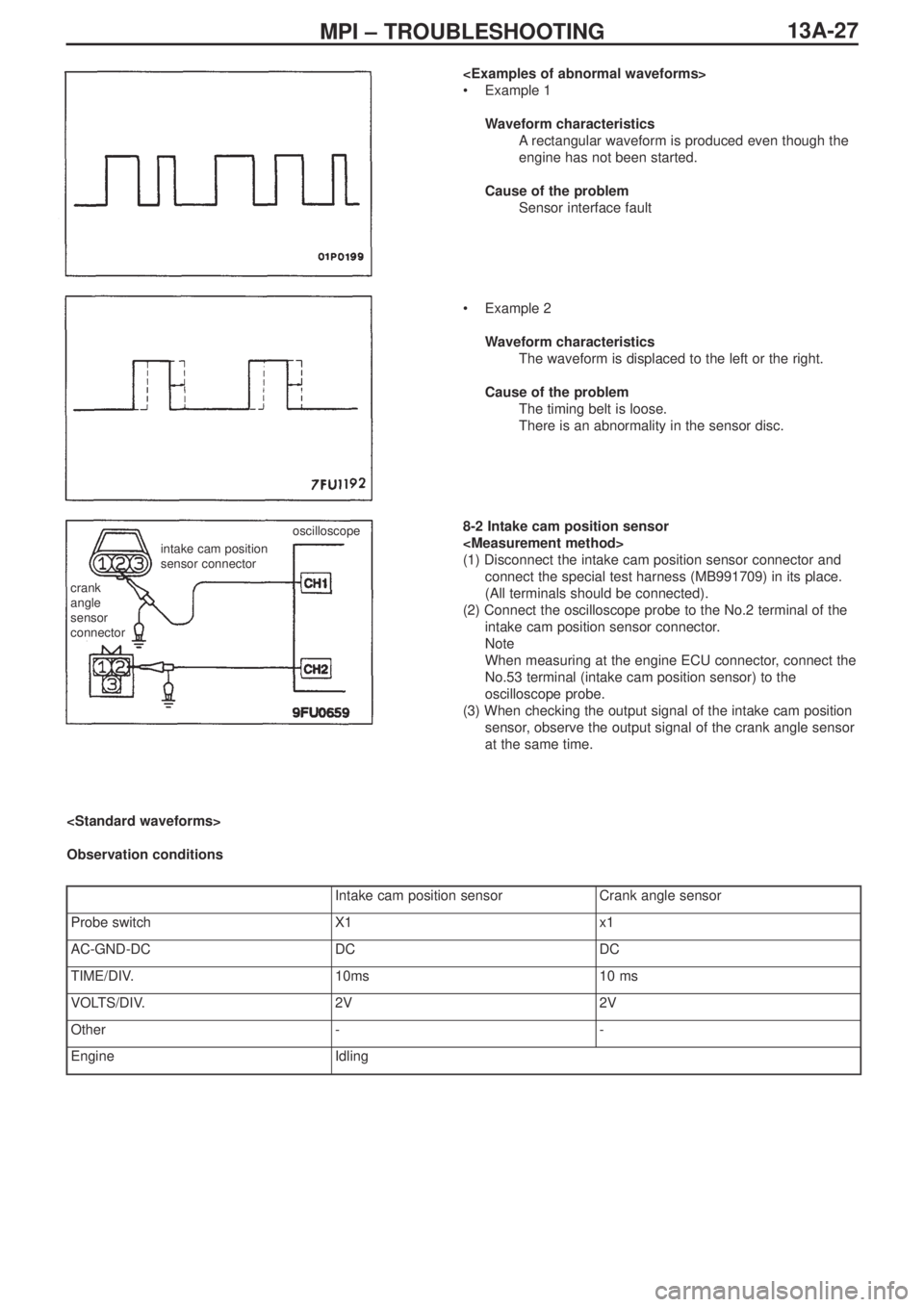
13A-27MPI – TROUBLESHOOTING
•Example 1
Waveform characteristics
Arectangular waveform is produced even though the
engine has not been started.
Cause of the problem
Sensor interface fault
•Example 2
Waveform characteristics
The waveform is displaced to the left or the right.
Cause of the problem
The timing belt is loose.
There is an abnormality in the sensor disc.
8-2 Intake cam position sensor
(1) Disconnect the intake cam position sensor connector and
connect the special test harness (MB991709) in its place.
(All terminals should be connected).
(2) Connect the oscilloscope probe to the No.2 terminal of the
intake cam position sensor connector.
Note
When measuring at the engine ECU connector, connect the
No.53 terminal (intake cam position sensor) to the
oscilloscope probe.
(3) When checking the output signal of the intake cam position
sensor, observe the output signal of the crank angle sensor
at the same time.
crank
angle
sensor
connector
intake cam position
sensor connectoroscilloscope
Observation conditions
Intake cam position sensorCrank angle sensor
Probe switchX1x1
AC-GND-DCDCDC
TIME/DIV.10ms10 ms
VOLTS/DIV.2V2V
Other--
EngineIdling
Page 68 of 364
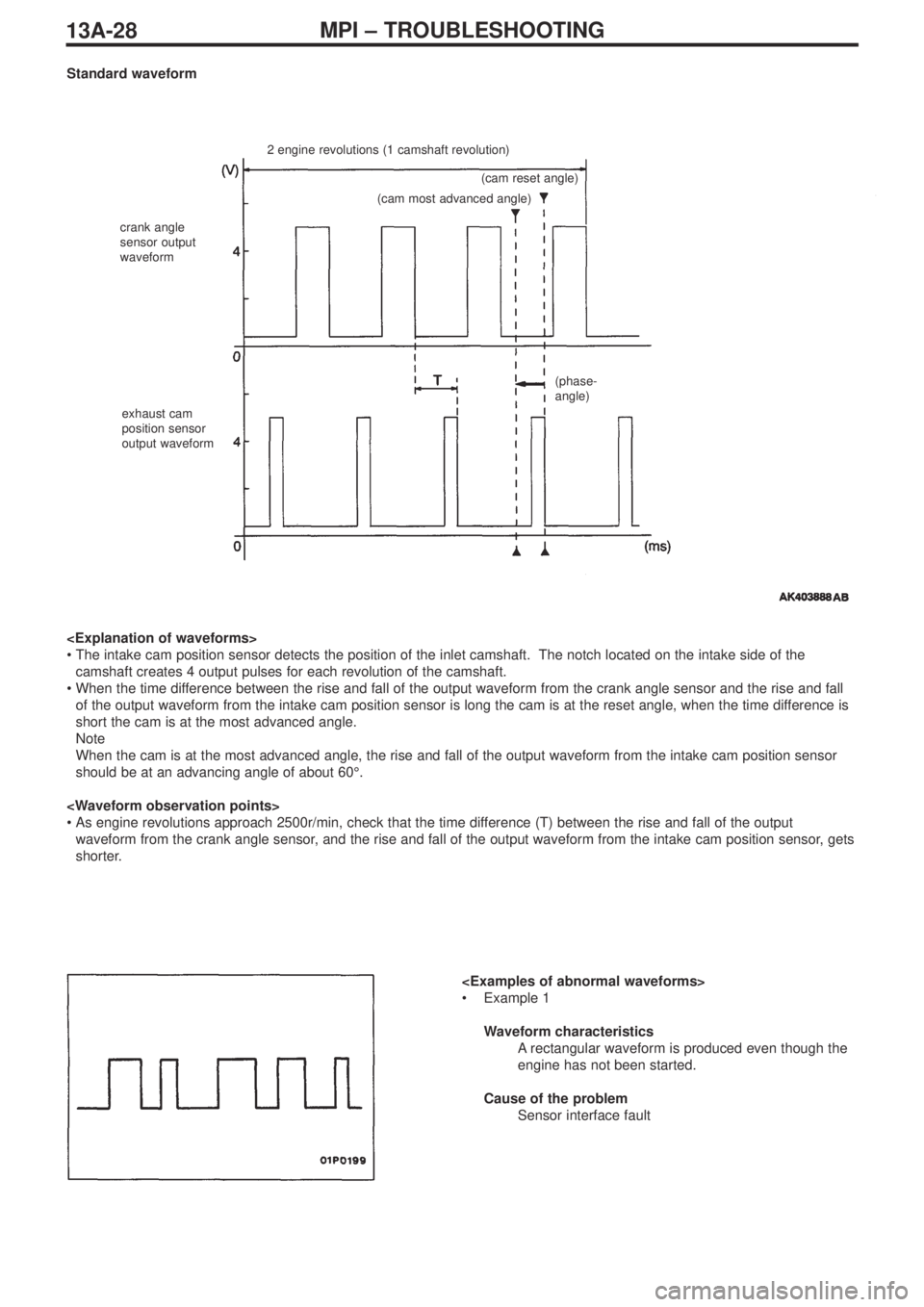
13A-28MPI – TROUBLESHOOTING
Standard waveform
2 engine revolutions (1 camshaft revolution)
crank angle
sensor output
waveform
exhaust cam
position sensor
output waveform(cam reset angle)
(cam most advanced angle)
(phase-
angle)
•The intake cam position sensor detects the position of the inlet camshaft. The notch located on the intake side of the
camshaft creates 4 output pulses for each revolution of the camshaft.
•When the time difference between the rise and fall of the output waveform from the crank angle sensor and the rise and fall
of the output waveform from the intake cam position sensor is long the cam is at the reset angle, when the time difference is
short the cam is at the most advanced angle.
Note
When the cam is at the most advanced angle, the rise and fall of the output waveform from the intake cam position sensor
should be at an advancing angle of about 60°.
•As engine revolutions approach 2500r/min, check that the time difference (T) between the rise and fall of the output
waveform from the crank angle sensor, and the rise and fall of the output waveform from the intake cam position sensor, gets
shorter.
•Example 1
Waveform characteristics
Arectangular waveform is produced even though the
engine has not been started.
Cause of the problem
Sensor interface fault
Page 75 of 364
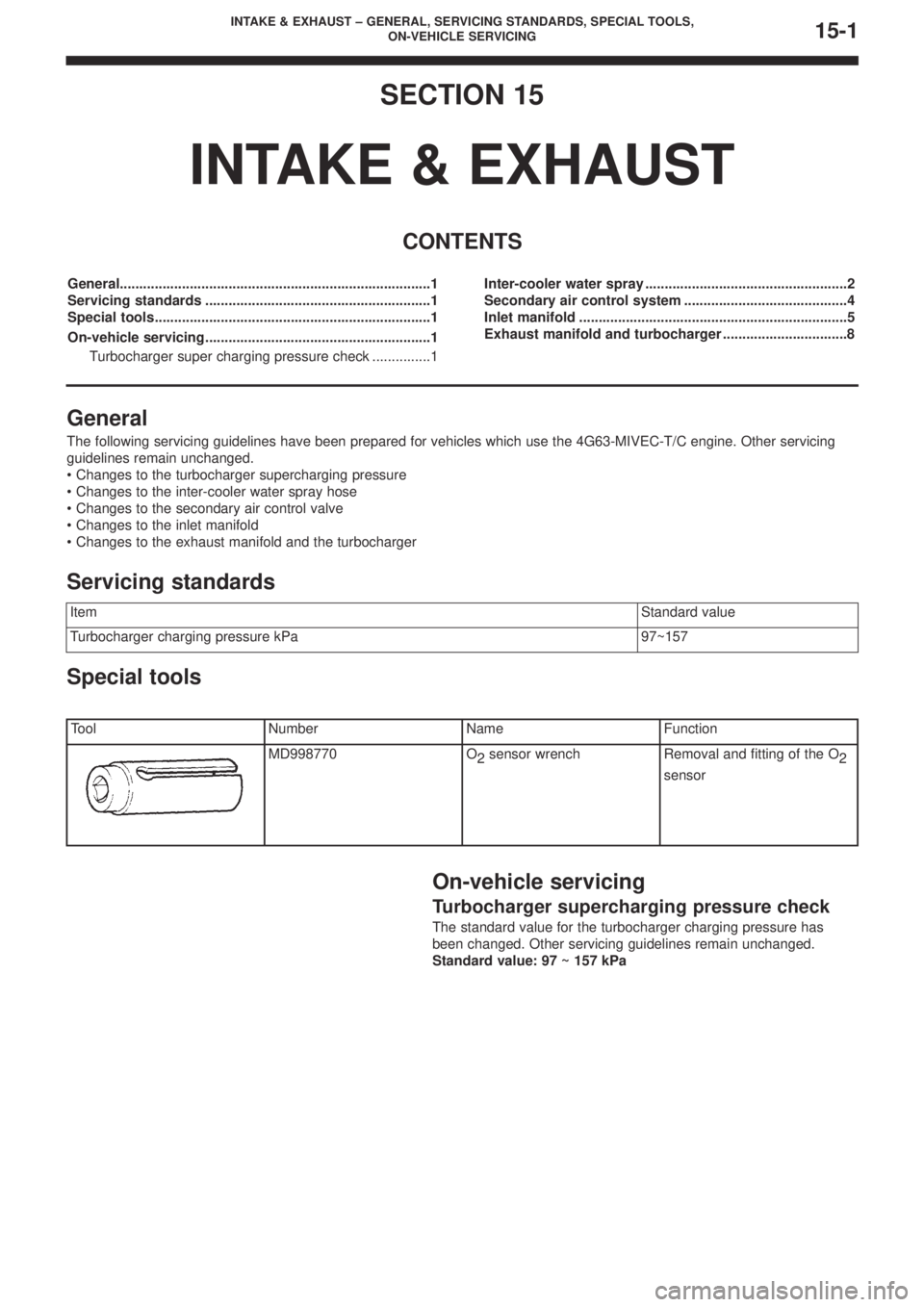
INTAKE & EXHAUST – GENERAL, SERVICING STANDARDS, SPECIAL TOOLS,
ON-VEHICLE SERVICING15-1
SECTION 15
INTAKE & EXHAUST
CONTENTS
General................................................................................1
Servicing standards ..........................................................1
Special tools.......................................................................1
On-vehicle servicing..........................................................1
Turbocharger super charging pressure check ...............1Inter-cooler water spray ....................................................2
Secondary air control system ..........................................4
Inlet manifold .....................................................................5
Exhaust manifold and turbocharger ................................8
General
The following servicing guidelines have been prepared for vehicles which use the 4G63-MIVEC-T/C engine. Other servicing
guidelines remain unchanged.
• Changes to the turbocharger supercharging pressure
• Changes to the inter-cooler water spray hose
• Changes to the secondary air control valve
• Changes to the inlet manifold
• Changes to the exhaust manifold and the turbocharger
Special tools
On-vehicle servicing
Turbocharger supercharging pressure check
The standard value for the turbocharger charging pressure has
been changed. Other servicing guidelines remain unchanged.
Standard value: 97 ~ 157 kPa
ItemStandard value
Turbocharger charging pressure kPa97~157
Servicing standards
ToolNumberNameFunction
MD998770O
2sensor wrenchRemoval and fitting of the O
2
sensor
Page 81 of 364
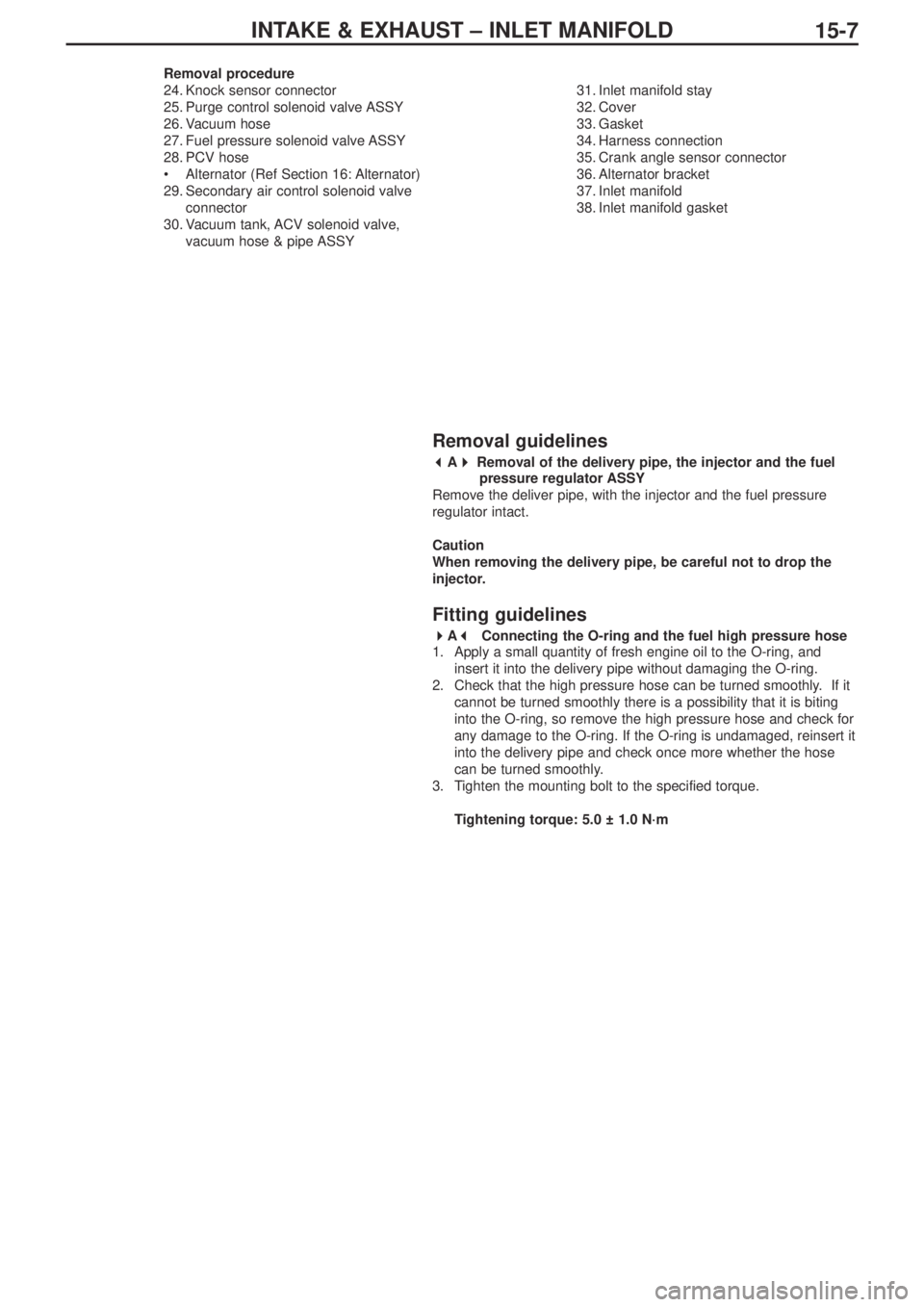
INTAKE & EXHAUST – INLET MANIFOLD
15-7
Removal procedure
24. Knock sensor connector
25. Purge control solenoid valve ASSY
26. Vacuum hose
27. Fuel pressure solenoid valve ASSY
28. PCV hose
•Alternator (Ref Section 16: Alternator)
29. Secondary air control solenoid valve
connector
30. Vacuum tank, ACV solenoid valve,
vacuum hose & pipe ASSY31. Inlet manifold stay
32. Cover
33. Gasket
34. Harness connection
35. Crank angle sensor connector
36. Alternator bracket
37. Inlet manifold
38. Inlet manifold gasket
Removal guidelines
A
Removal of the delivery pipe, the injector and the fuel
pressure regulator ASSY
Remove the deliver pipe, with the injector and the fuel pressure
regulator intact.
Caution
When removing the delivery pipe, be careful not to drop the
injector.
Fitting guidelines
A
Connecting the O-ring and the fuel high pressure hose
1. Apply a small quantity of fresh engine oil to the O-ring, and
insert it into the delivery pipe without damaging the O-ring.
2. Check that the high pressure hose can be turned smoothly. If it
cannot be turned smoothly there is a possibility that it is biting
into the O-ring, so remove the high pressure hose and check for
any damage to the O-ring. If the O-ring is undamaged, reinsert it
into the delivery pipe and check once more whether the hose
can be turned smoothly.
3. Tighten the mounting bolt to the specified torque.
Tightening torque: 5.0 ± 1.0 N·m
Page 85 of 364
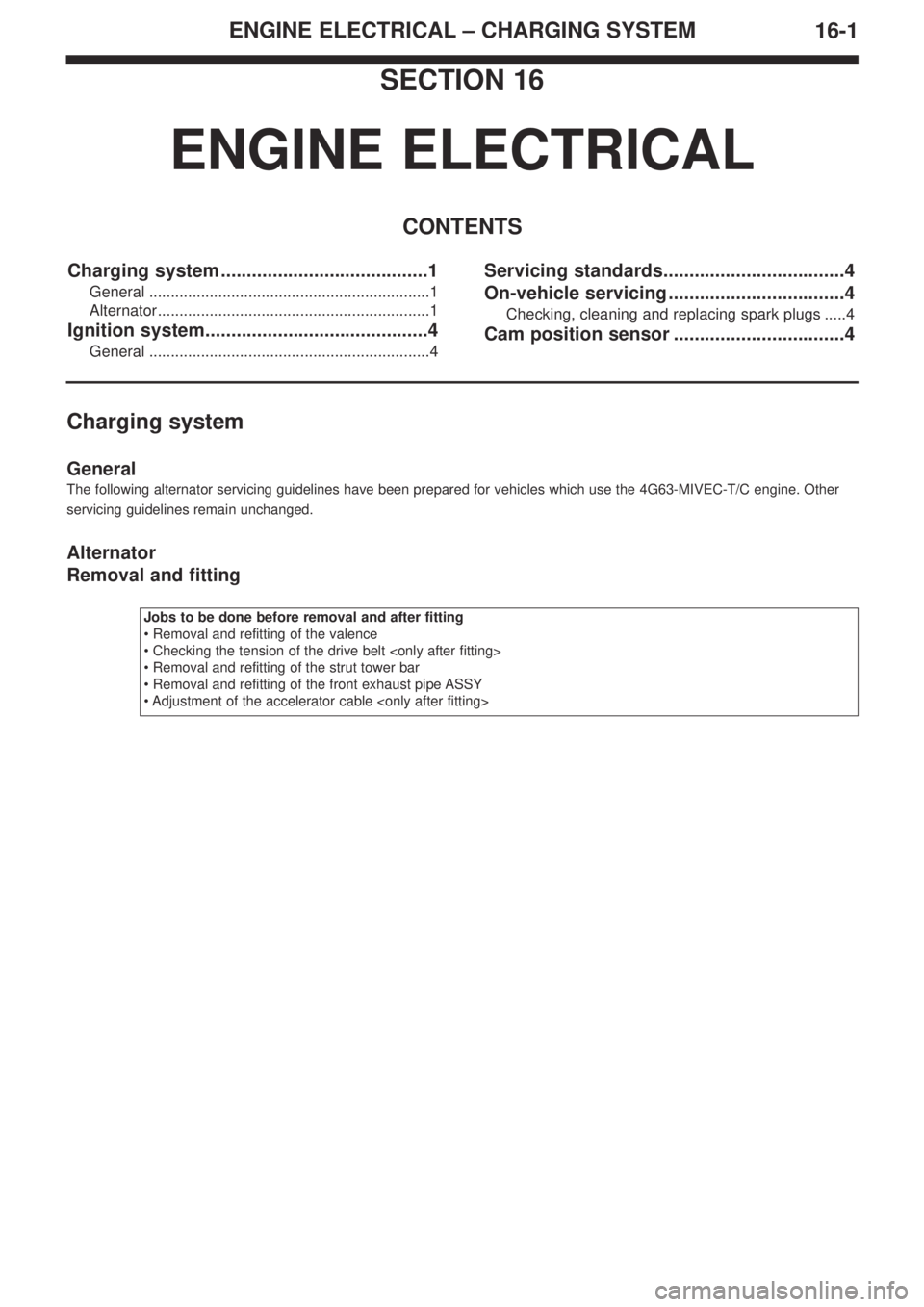
ENGINE ELECTRICAL – CHARGING SYSTEM
16-1
SECTION 16
ENGINE ELECTRICAL
CONTENTS
Charging system ........................................1
General .................................................................1
Alternator...............................................................1
Ignition system...........................................4
General .................................................................4
Servicing standards...................................4
On-vehicle servicing ..................................4
Checking, cleaning and replacing spark plugs .....4
Cam position sensor .................................4
Charging system
General
The following alternator servicing guidelines have been prepared for vehicles which use the 4G63-MIVEC-T/C engine. Other
servicing guidelines remain unchanged.
Alternator
Removal and fitting
Jobs to be done before removal and after fitting
• Removal and refitting of the valence
• Checking the tension of the drive belt
• Removal and refitting of the strut tower bar
• Removal and refitting of the front exhaust pipe ASSY
• Adjustment of the accelerator cable
Page 88 of 364
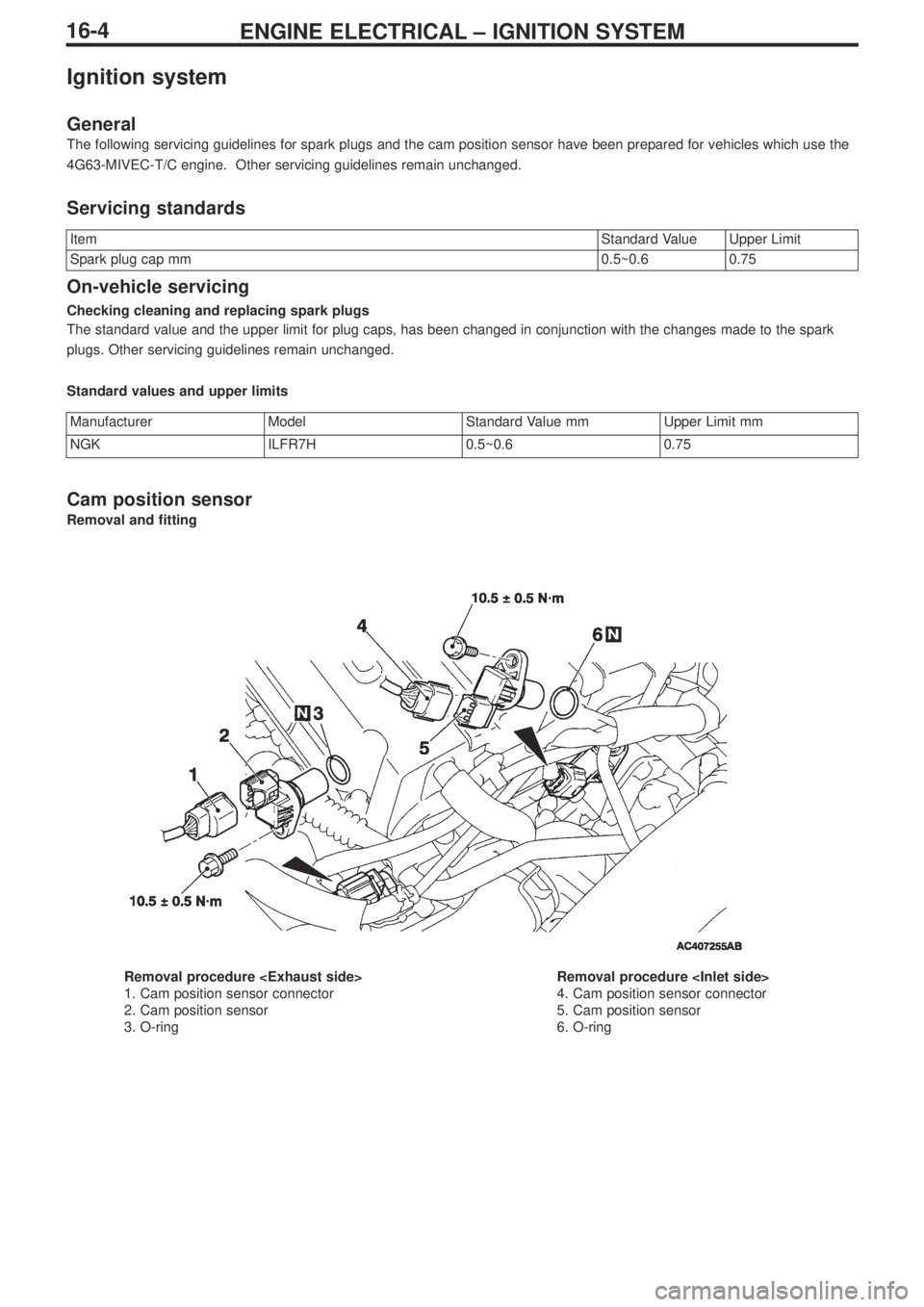
ENGINE ELECTRICAL – IGNITION SYSTEM16-4
Ignition system
General
The following servicing guidelines for spark plugs and the cam position sensor have been prepared for vehicles which use the
4G63-MIVEC-T/C engine. Other servicing guidelines remain unchanged.
Servicing standards
On-vehicle servicing
Checking cleaning and replacing spark plugs
The standard value and the upper limit for plug caps, has been changed in conjunction with the changes made to the spark
plugs. Other servicing guidelines remain unchanged.
Standard values and upper limits
Cam position sensor
Removal and fitting
Removal procedure
1. Cam position sensor connector
2. Cam position sensor
3. O-ringRemoval procedure
4. Cam position sensor connector
5. Cam position sensor
6. O-ring
ItemStandard ValueUpper Limit
Spark plug cap mm0.5~0.60.75
ManufacturerModelStandard Value mmUpper Limit mm
NGKILFR7H0.5~0.60.75
Page 109 of 364
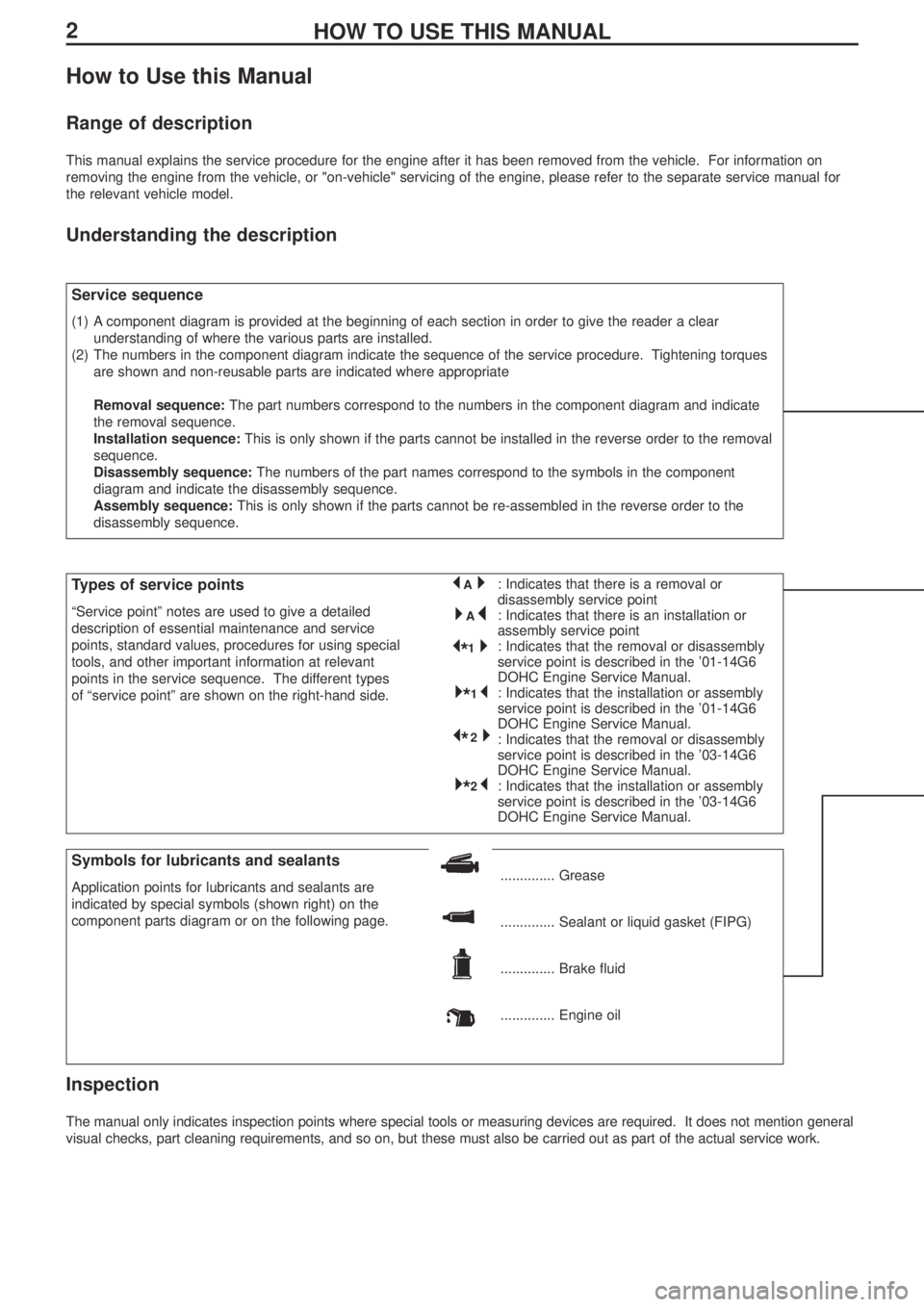
2HOW TO USE THIS MANUAL
How to Use this Manual
Range of description
This manual explains the service procedure for the engine after it has been removed from the vehicle. For information on
removing the engine from the vehicle, or "on-vehicle" servicing of the engine, please refer to the separate service manual for
the relevant vehicle model.
Understanding the description
Inspection
The manual only indicates inspection points where special tools or measuring devices are required. It does not mention general
visual checks, part cleaning requirements, and so on, but these must also be carried out as part of the actual service work.
Service sequence
(1) A component diagram is provided at the beginning of each section in order to give the reader a clear
understanding of where the various parts are installed.
(2) The numbers in the component diagram indicate the sequence of the service procedure. Tightening torques
are shown and non-reusable parts are indicated where appropriate
Removal sequence:The part numbers correspond to the numbers in the component diagram and indicate
the removal sequence.
Installation sequence:This is only shown if the parts cannot be installed in the reverse order to the removal
sequence.
Disassembly sequence: The numbers of the part names correspond to the symbols in the component
diagram and indicate the disassembly sequence.
Assembly sequence:This is only shown if the parts cannot be re-assembled in the reverse order to the
disassembly sequence.
Symbols for lubricants and sealants
Application points for lubricants and sealants are
indicated by special symbols (shown right) on the
component parts diagram or on the following page............... Grease
.............. Sealant or liquid gasket (FIPG)
.............. Brake fluid
.............. Engine oil
Types of service points
“Service point” notes are used to give a detailed
description of essential maintenance and service
points, standard values, procedures for using special
tools, and other important information at relevant
points in the service sequence. The different types
of “service point” are shown on the right-hand side.: Indicates that there is a removal or
disassembly service point
: Indicates that there is an installation or
assembly service point
: Indicates that the removal or disassembly
service point is described in the ’01-14G6
DOHC Engine Service Manual.
: Indicates that the installation or assembly
service point is described in the ’01-14G6
DOHC Engine Service Manual.
: Indicates that the removal or disassembly
service point is described in the ’03-14G6
DOHC Engine Service Manual.
: Indicates that the installation or assembly
service point is described in the ’03-14G6
DOHC Engine Service Manual.
* * 1
* * 2
*
1*
* 2*
A *
* A
Page 125 of 364
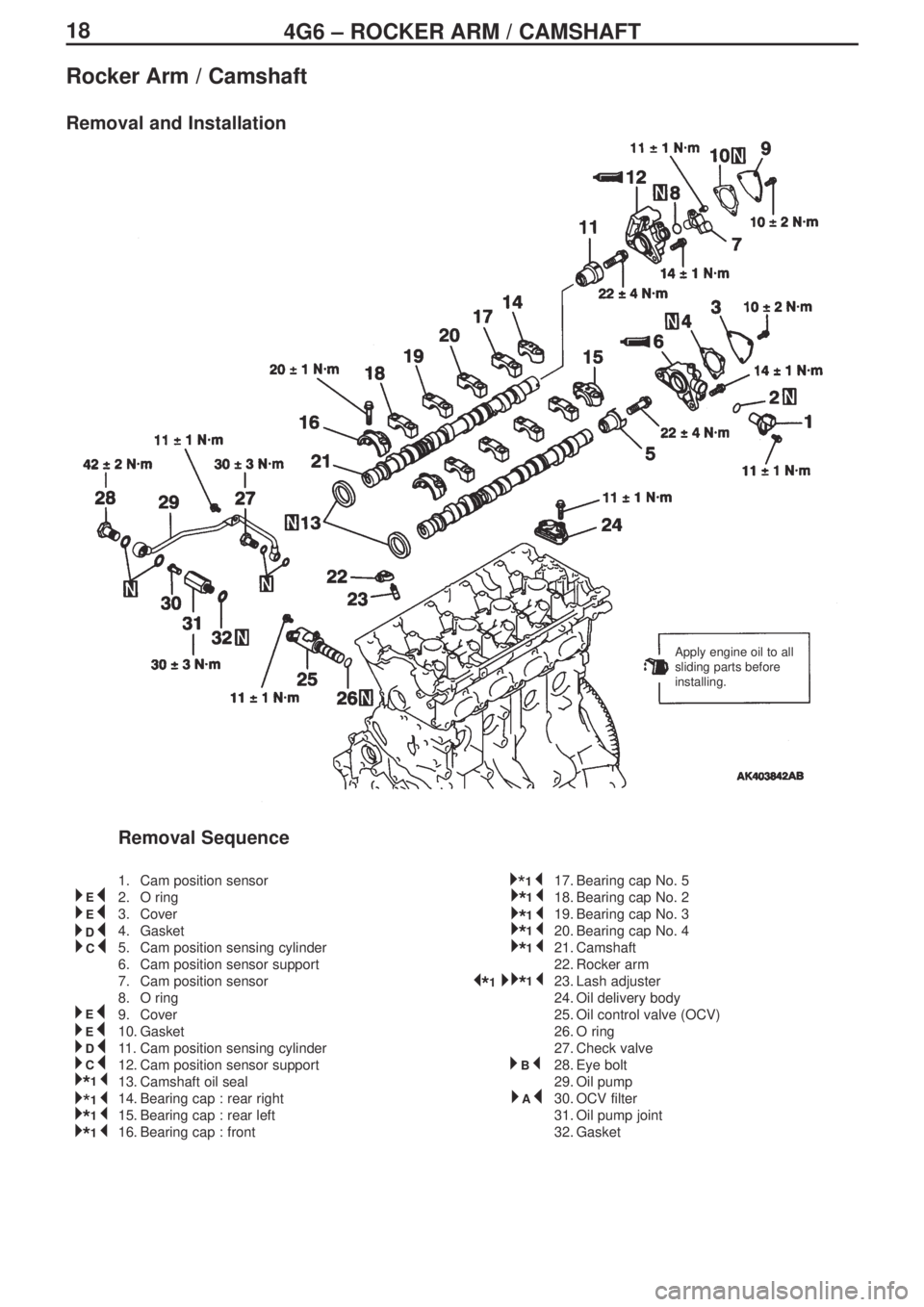
184G6 – ROCKER ARM / CAMSHAFT
Rocker Arm / Camshaft
Removal and Installation
Removal Sequence
1. Cam position sensor
2. O ring
3. Cover
4. Gasket
5. Cam position sensing cylinder
6. Cam position sensor support
7. Cam position sensor
8. O ring
9. Cover
10. Gasket
11.Cam position sensing cylinder
12. Cam position sensor support
13. Camshaft oil seal
14. Bearing cap : rear right
15. Bearing cap : rear left
16. Bearing cap : front17. Bearing cap No. 5
18. Bearing cap No. 2
19. Bearing cap No. 3
20. Bearing cap No. 4
21. Camshaft
22. Rocker arm
23. Lash adjuster
24. Oil delivery body
25. Oil control valve (OCV)
26. O ring
27. Check valve
28. Eye bolt
29. Oil pump
30. OCV filter
31. Oil pump joint
32. Gasket
Apply engine oil to all
sliding parts before
installing.
E *
E
*
D
*
D
*
C
*
C
*
E
*
E
*
* 1*
*1*
* 1*
* 1*
*1*
* 1*
* 1*
* 1*
* 1*
* 1* * * 1
B*
A *