check engine MITSUBISHI MONTERO 1998 Service Manual
[x] Cancel search | Manufacturer: MITSUBISHI, Model Year: 1998, Model line: MONTERO, Model: MITSUBISHI MONTERO 1998Pages: 1501, PDF Size: 25.81 MB
Page 747 of 1501
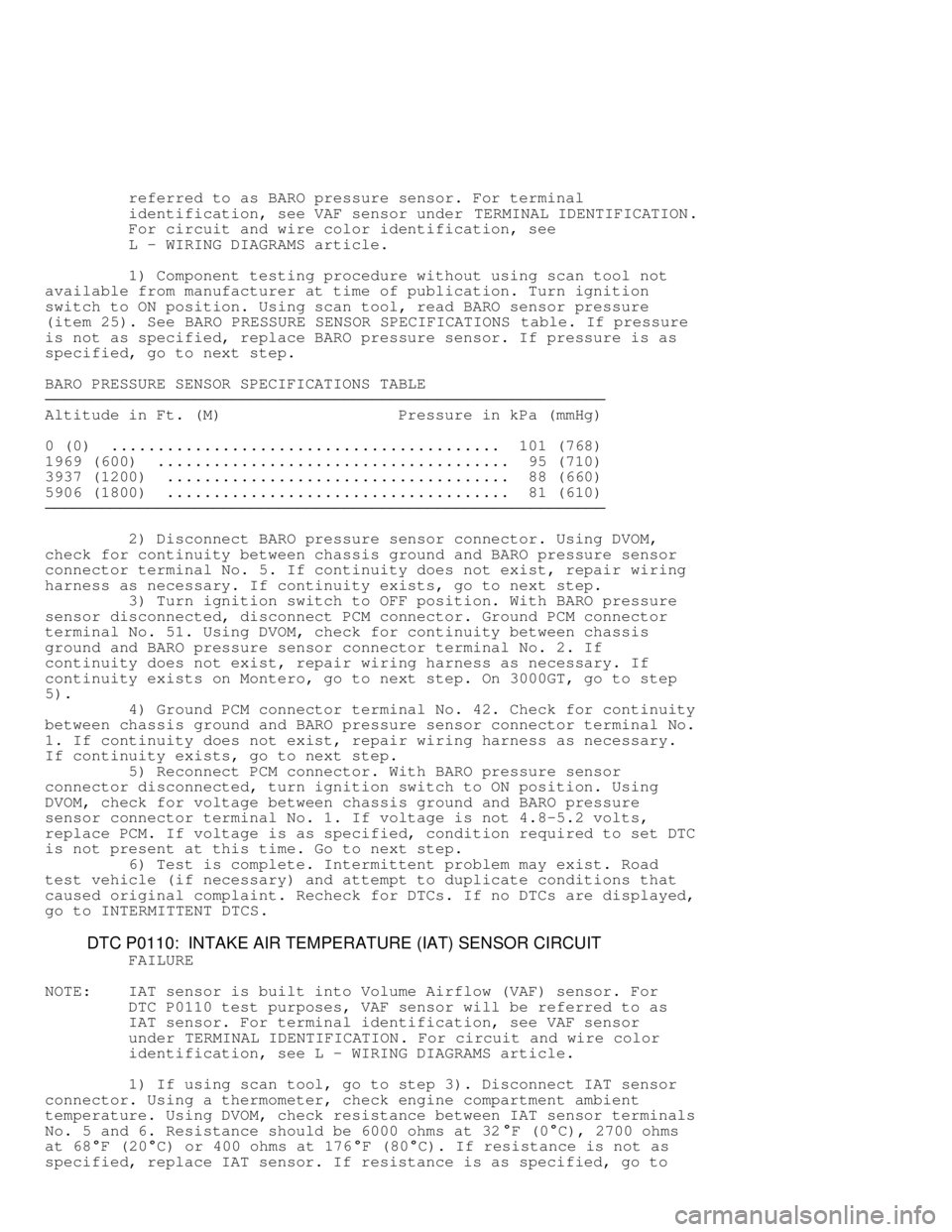
referred to as BARO pressure sensor. For terminal
identification, see VAF sensor under TERMINAL IDENTIFICATION.
For circuit and wire color identification, see
L - WIRING DIAGRAMS article.
1) Component testing procedure without using scan tool not
available from manufacturer at time of publication. Turn ignition
switch to ON position. Using scan tool, read BARO sensor pressure
(item 25). See BARO PRESSURE SENSOR SPECIFICATIONS table. If pressure
is not as specified, replace BARO pressure sensor. If pressure is as
specified, go to next step.
BARO PRESSURE SENSOR SPECIFICATIONS TABLE
\
\
\
\
\
\
Altitude in Ft. (M) Pressure in kPa (mmHg)
0 (0) .......................................... 101 (768)
1969 (600) ...................................... 95 (710)
3937 (1200) ..................................... 88 (660)
5906 (1800) ..................................... 81 (610)
\
\
\
\
\
\
2) Disconnect BARO pressure sensor connector. Using DVOM,
check for continuity between chassis ground and BARO pressure sensor
connector terminal No. 5. If continuity does not exist, repair wiring
harness as necessary. If continuity exists, go to next step.
3) Turn ignition switch to OFF position. With BARO pressure
sensor disconnected, disconnect PCM connector. Ground PCM connector
terminal No. 51. Using DVOM, check for continuity between chassis
ground and BARO pressure sensor connector terminal No. 2. If
continuity does not exist, repair wiring harness as necessary. If
continuity exists on Montero, go to next step. On 3000GT, go to step
5).
4) Ground PCM connector terminal No. 42. Check for continuity
between chassis ground and BARO pressure sensor connector terminal No.
1. If continuity does not exist, repair wiring harness as necessary.
If continuity exists, go to next step.
5) Reconnect PCM connector. With BARO pressure sensor
connector disconnected, turn ignition switch to ON position. Using
DVOM, check for voltage between chassis ground and BARO pressure
sensor connector terminal No. 1. If voltage is not 4.8-5.2 volts,
replace PCM. If voltage is as specified, condition required to set DTC
is not present at this time. Go to next step.
6) Test is complete. Intermittent problem may exist. Road
test vehicle (if necessary) and attempt to duplicate conditions that
caused original complaint. Recheck for DTCs. If no DTCs are displayed,
go to INTERMITTENT DTCS .
DTC P0110: INTAKE AIR TEMPERATURE (IAT) SENSOR CIRCUIT
FAILURE
NOTE: IAT sensor is built into Volume Airflow (VAF) sensor. For
DTC P0110 test purposes, VAF sensor will be referred to as
IAT sensor. For terminal identification, see VAF sensor
under TERMINAL IDENTIFICATION . For circuit and wire color
identification, see L - WIRING DIAGRAMS article.
1) If using scan tool, go to step 3). Disconnect IAT sensor
connector. Using a thermometer, check engine compartment ambient
temperature. Using DVOM, check resistance between IAT sensor terminals
No. 5 and 6. Resistance should be 6000 ohms at 32
F (0C), 2700 ohms
at 68F (20C) or 400 ohms at 176F (80C). If resistance is not as
specified, replace IAT sensor. If resistance is as specified, go to
Page 748 of 1501
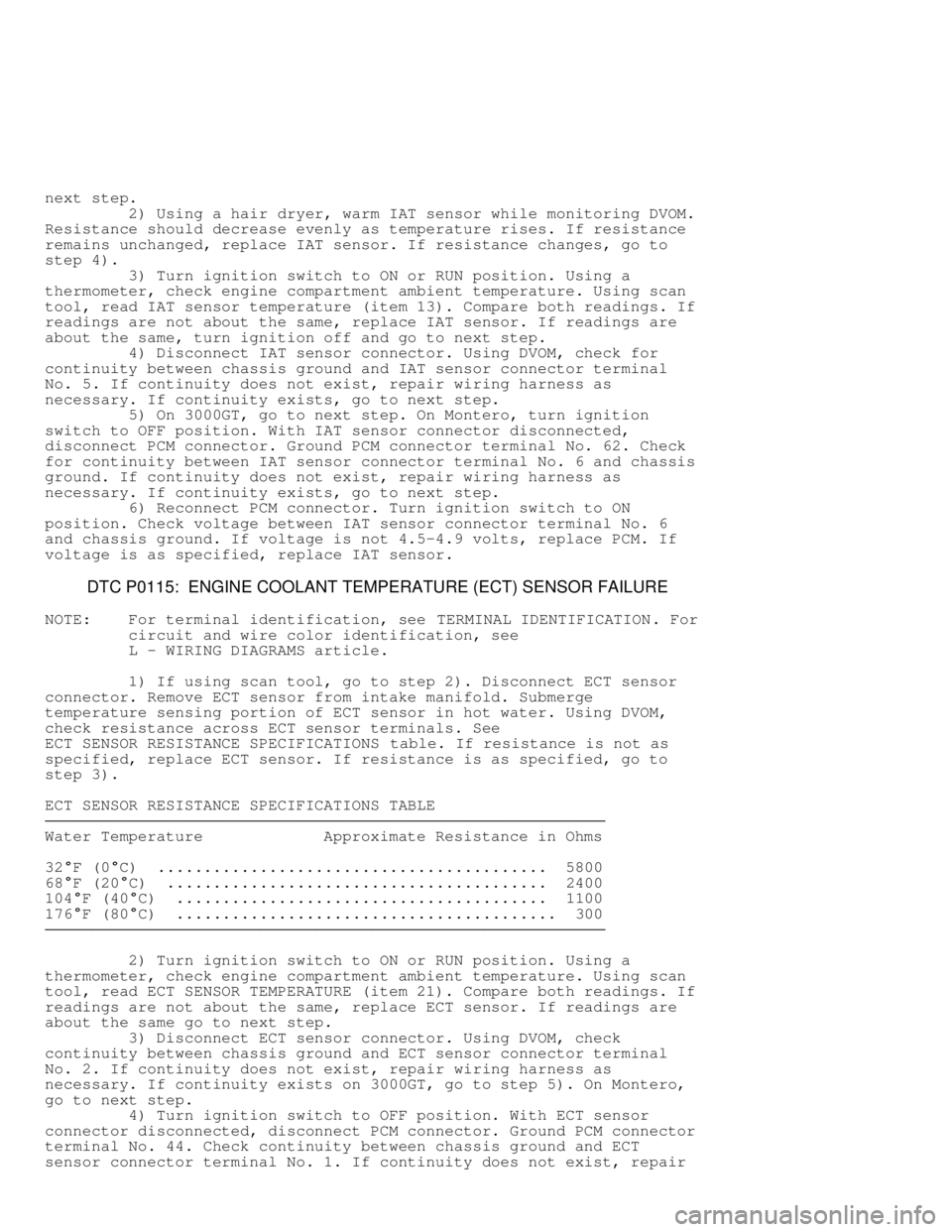
next step.
2) Using a hair dryer, warm IAT sensor while monitoring DVOM.
Resistance should decrease evenly as temperature rises. If resistance
remains unchanged, replace IAT sensor. If resistance changes, go to
step 4).
3) Turn ignition switch to ON or RUN position. Using a
thermometer, check engine compartment ambient temperature. Using scan
tool, read IAT sensor temperature (item 13). Compare both readings. If\
readings are not about the same, replace IAT sensor. If readings are
about the same, turn ignition off and go to next step.
4) Disconnect IAT sensor connector. Using DVOM, check for
continuity between chassis ground and IAT sensor connector terminal
No. 5. If continuity does not exist, repair wiring harness as
necessary. If continuity exists, go to next step.
5) On 3000GT, go to next step. On Montero, turn ignition
switch to OFF position. With IAT sensor connector disconnected,
disconnect PCM connector. Ground PCM connector terminal No. 62. Check
for continuity between IAT sensor connector terminal No. 6 and chassis
ground. If continuity does not exist, repair wiring harness as
necessary. If continuity exists, go to next step.
6) Reconnect PCM connector. Turn ignition switch to ON
position. Check voltage between IAT sensor connector terminal No. 6
and chassis ground. If voltage is not 4.5-4.9 volts, replace PCM. If
voltage is as specified, replace IAT sensor.
DTC P0115: ENGINE COOLANT TEMPERATURE (ECT) SENSOR FAILURE
NOTE: For terminal identification, see TERMINAL IDENTIFICATION. For
circuit and wire color identification, see
L - WIRING DIAGRAMS article.
1) If using scan tool, go to step 2). Disconnect ECT sensor
connector. Remove ECT sensor from intake manifold. Submerge
temperature sensing portion of ECT sensor in hot water. Using DVOM,
check resistance across ECT sensor terminals. See
ECT SENSOR RESISTANCE SPECIFICATIONS table. If resistance is not as
specified, replace ECT sensor. If resistance is as specified, go to
step 3).
ECT SENSOR RESISTANCE SPECIFICATIONS TABLE
\
\
\
\
\
\
Water Temperature Approximate Resistance in Ohms
32
F (0C) .......................................... 5800
68F (20C) ......................................... 2400
104F (40C) ........................................ 1100
176F (80C) ......................................... 300 \
\
\
\
\
\
2) Turn ignition switch to ON or RUN position. Using a
thermometer, check engine compartment ambient temperature. Using scan
tool, read ECT SENSOR TEMPERATURE (item 21). Compare both readings. If\
readings are not about the same, replace ECT sensor. If readings are
about the same go to next step.
3) Disconnect ECT sensor connector. Using DVOM, check
continuity between chassis ground and ECT sensor connector terminal
No. 2. If continuity does not exist, repair wiring harness as
necessary. If continuity exists on 3000GT, go to step 5). On Montero,
go to next step.
4) Turn ignition switch to OFF position. With ECT sensor
connector disconnected, disconnect PCM connector. Ground PCM connector
terminal No. 44. Check continuity between chassis ground and ECT
sensor connector terminal No. 1. If continuity does not exist, repair
Page 750 of 1501
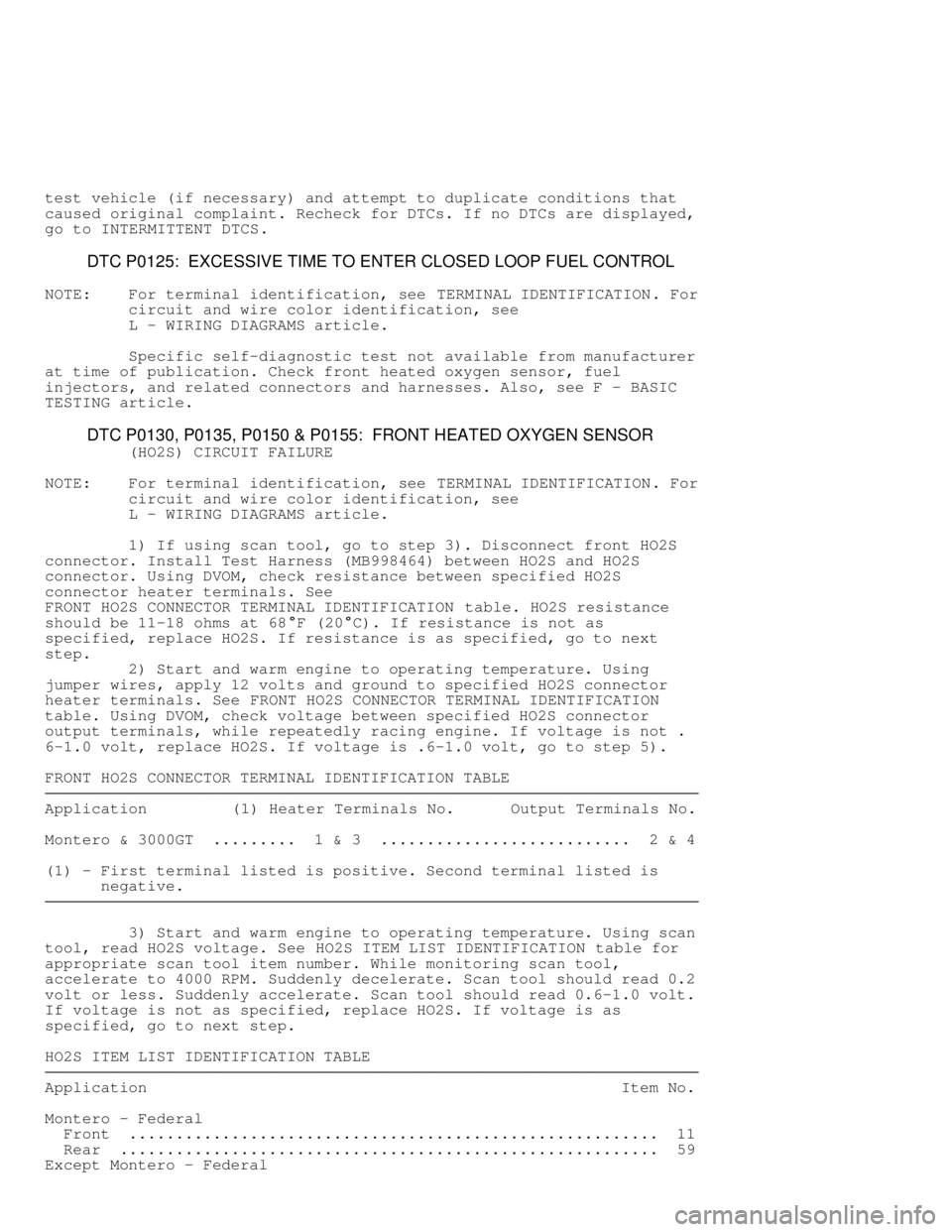
test vehicle (if necessary) and attempt to duplicate conditions that
caused original complaint. Recheck for DTCs. If no DTCs are displayed,
go to INTERMITTENT DTCS .
DTC P0125: EXCESSIVE TIME TO ENTER CLOSED LOOP FUEL CONTROL
NOTE: For terminal identification, see TERMINAL IDENTIFICATION. For
circuit and wire color identification, see
L - WIRING DIAGRAMS article.
Specific self-diagnostic test not available from manufacturer
at time of publication. Check front heated oxygen sensor, fuel
injectors, and related connectors and harnesses. Also, see F - BASIC
TESTING article.
DTC P0130, P0135, P0150 & P0155: FRONT HEATED OXYGEN SENSOR
(HO2S) CIRCUIT FAILURE
NOTE: For terminal identification, see TERMINAL IDENTIFICATION. For
circuit and wire color identification, see
L - WIRING DIAGRAMS article.
1) If using scan tool, go to step 3). Disconnect front HO2S
connector. Install Test Harness (MB998464) between HO2S and HO2S
connector. Using DVOM, check resistance between specified HO2S
connector heater terminals. See
FRONT HO2S CONNECTOR TERMINAL IDENTIFICATION table. HO2S resistance
should be 11-18 ohms at 68
F (20C). If resistance is not as
specified, replace HO2S. If resistance is as specified, go to next
step.
2) Start and warm engine to operating temperature. Using
jumper wires, apply 12 volts and ground to specified HO2S connector
heater terminals. See FRONT HO2S CONNECTOR TERMINAL IDENTIFICATION
table. Using DVOM, check voltage between specified HO2S connector
output terminals, while repeatedly racing engine. If voltage is not .
6-1.0 volt, replace HO2S. If voltage is .6-1.0 volt, go to step 5).
FRONT HO2S CONNECTOR TERMINAL IDENTIFICATION TABLE
\
\
\
\
\
\
\
Application (1) Heater Terminals No. Output Terminals No.
Montero & 3000GT ......... 1 & 3 ........................... 2 & 4
( 1) - First terminal listed is positive. Second terminal listed is
negative.
\
\
\
\
\
\
\
3) Start and warm engine to operating temperature. Using scan
tool, read HO2S voltage. See HO2S ITEM LIST IDENTIFICATION table for
appropriate scan tool item number. While monitoring scan tool,
accelerate to 4000 RPM. Suddenly decelerate. Scan tool should read 0.2
volt or less. Suddenly accelerate. Scan tool should read 0.6-1.0 volt.
If voltage is not as specified, replace HO2S. If voltage is as
specified, go to next step.
HO2S ITEM LIST IDENTIFICATION TABLE
\
\
\
\
\
\
\
Application Item No.
Montero - Federal
Front ......................................................... 11
Rear .......................................................... 59
Except Montero - Federal
Page 752 of 1501
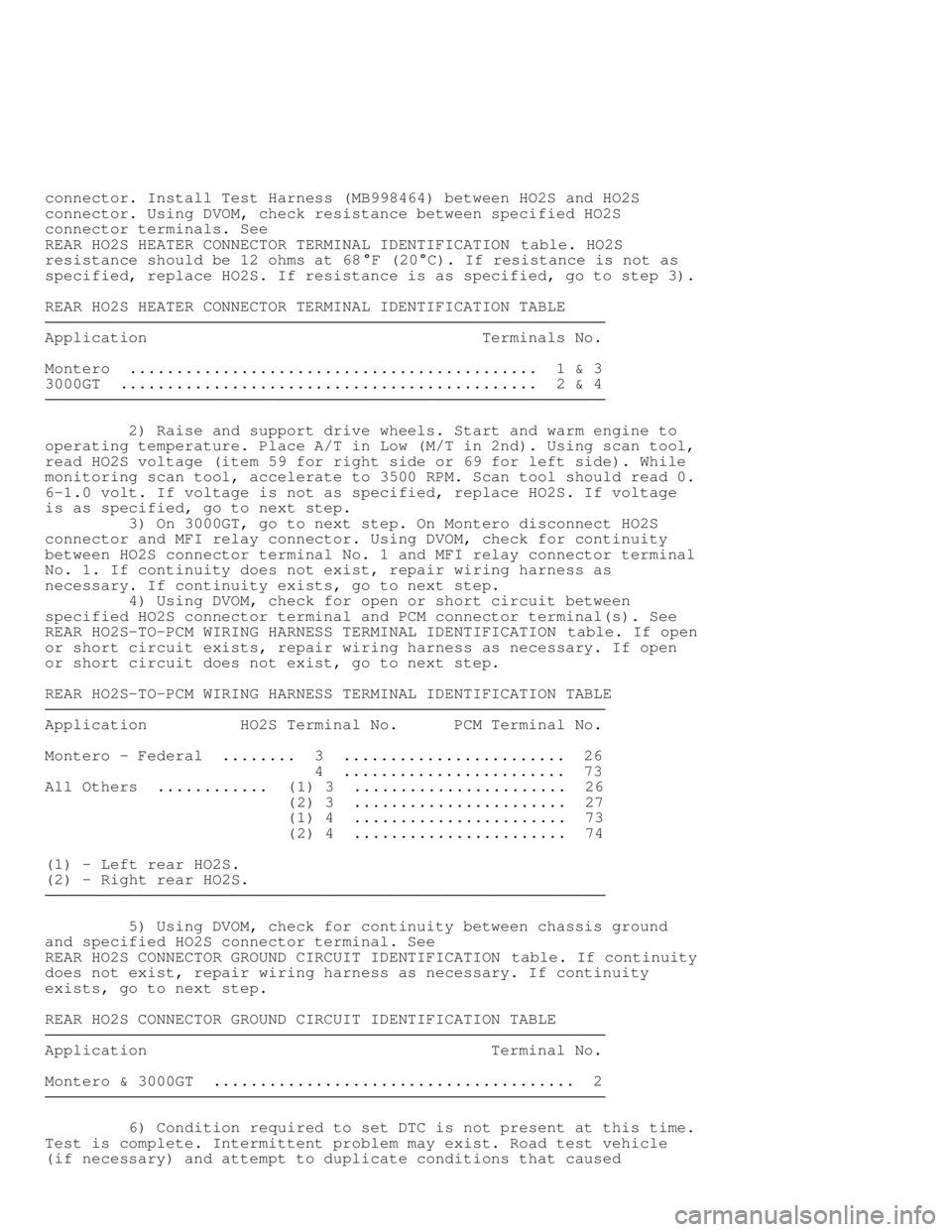
connector. Install Test Harness (MB998464) between HO2S and HO2S
connector. Using DVOM, check resistance between specified HO2S
connector terminals. See
REAR HO2S HEATER CONNECTOR TERMINAL IDENTIFICATION table. HO2S
resistance should be 12 ohms at 68
F (20C). If resistance is not as
specified, replace HO2S. If resistance is as specified, go to step 3).
REAR HO2S HEATER CONNECTOR TERMINAL IDENTIFICATION TABLE
\
\
\
\
\
\
Application Terminals No.
Montero ............................................ 1 & 3
3000GT ............................................. 2 & 4
\
\
\
\
\
\
2) Raise and support drive wheels. Start and warm engine to
operating temperature. Place A/T in Low (M/T in 2nd). Using scan tool,\
read HO2S voltage (item 59 for right side or 69 for left side). While
monitoring scan tool, accelerate to 3500 RPM. Scan tool should read 0.
6-1.0 volt. If voltage is not as specified, replace HO2S. If voltage
is as specified, go to next step.
3) On 3000GT, go to next step. On Montero disconnect HO2S
connector and MFI relay connector. Using DVOM, check for continuity
between HO2S connector terminal No. 1 and MFI relay connector terminal
No. 1. If continuity does not exist, repair wiring harness as
necessary. If continuity exists, go to next step.
4) Using DVOM, check for open or short circuit between
specified HO2S connector terminal and PCM connector terminal(s). See
REAR HO2S-TO-PCM WIRING HARNESS TERMINAL IDENTIFICATION table. If open
or short circuit exists, repair wiring harness as necessary. If open
or short circuit does not exist, go to next step.
REAR HO2S-TO-PCM WIRING HARNESS TERMINAL IDENTIFICATION TABLE
\
\
\
\
\
\
Application HO2S Terminal No. PCM Terminal No.
Montero - Federal ........ 3 ........................ 26
4 ........................ 73
All Others ............ ( 1) 3 ....................... 26
( 2) 3 ....................... 27
( 1) 4 ....................... 73
( 2) 4 ....................... 74
( 1) - Left rear HO2S.
( 2) - Right rear HO2S.
\
\
\
\
\
\
5) Using DVOM, check for continuity between chassis ground
and specified HO2S connector terminal. See
REAR HO2S CONNECTOR GROUND CIRCUIT IDENTIFICATION table. If continuity
does not exist, repair wiring harness as necessary. If continuity
exists, go to next step.
REAR HO2S CONNECTOR GROUND CIRCUIT IDENTIFICATION TABLE
\
\
\
\
\
\
Application Terminal No.
Montero & 3000GT ....................................... 2
\
\
\
\
\
\
6) Condition required to set DTC is not present at this time.
Test is complete. Intermittent problem may exist. Road test vehicle
(if necessary) and attempt to duplicate conditions that caused
Page 753 of 1501
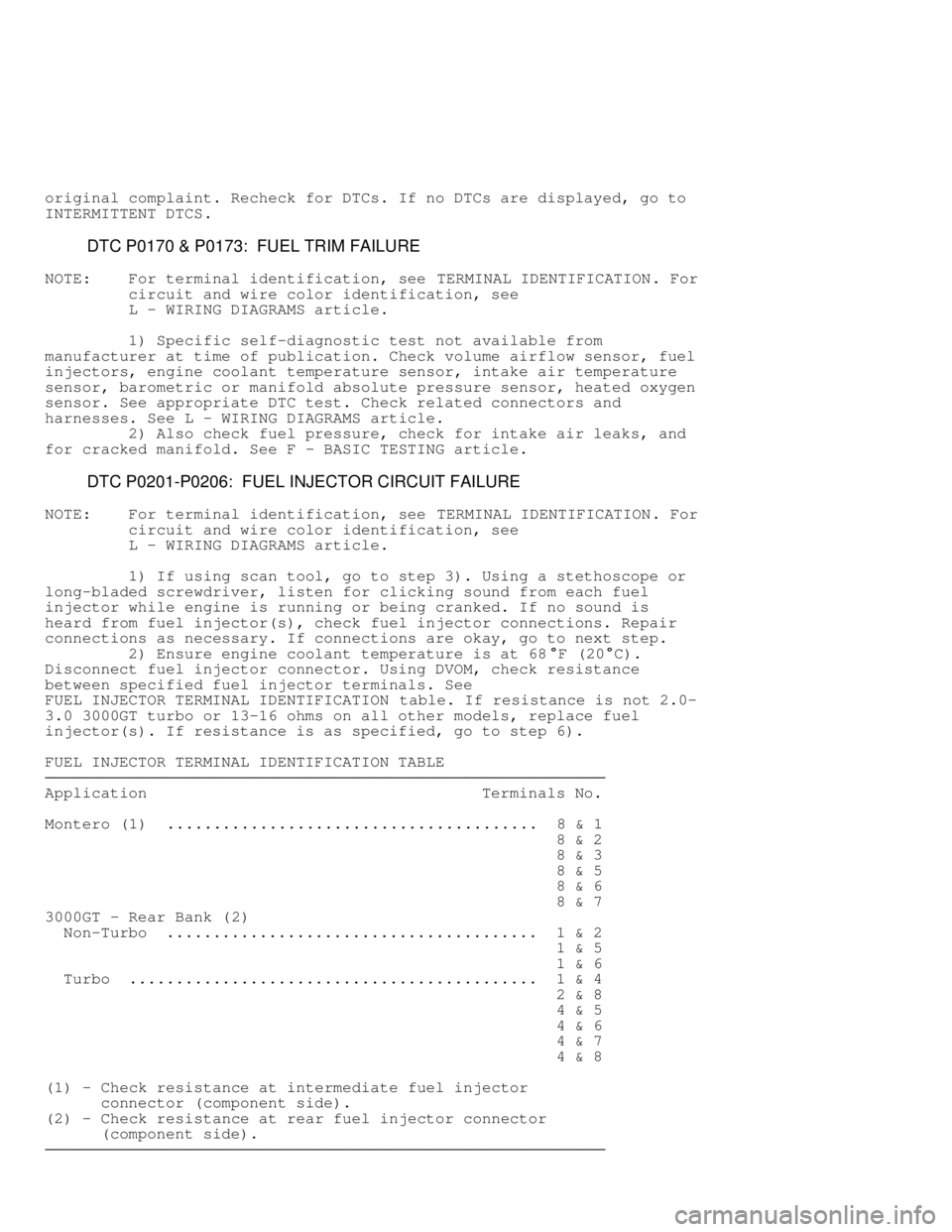
original complaint. Recheck for DTCs. If no DTCs are displayed, go to
INTERMITTENT DTCS.
DTC P0170 & P0173: FUEL TRIM FAILURE
NOTE: For terminal identification, see TERMINAL IDENTIFICATION. For
circuit and wire color identification, see
L - WIRING DIAGRAMS article.
1) Specific self-diagnostic test not available from
manufacturer at time of publication. Check volume airflow sensor, fuel
injectors, engine coolant temperature sensor, intake air temperature
sensor, barometric or manifold absolute pressure sensor, heated oxygen
sensor. See appropriate DTC test. Check related connectors and
harnesses. See L - WIRING DIAGRAMS article.
2) Also check fuel pressure, check for intake air leaks, and
for cracked manifold. See F - BASIC TESTING article.
DTC P0201-P0206: FUEL INJECTOR CIRCUIT FAILURE
NOTE: For terminal identification, see TERMINAL IDENTIFICATION. For
circuit and wire color identification, see
L - WIRING DIAGRAMS article.
1) If using scan tool, go to step 3). Using a stethoscope or
long-bladed screwdriver, listen for clicking sound from each fuel
injector while engine is running or being cranked. If no sound is
heard from fuel injector(s), check fuel injector connections. Repair
connections as necessary. If connections are okay, go to next step.
2) Ensure engine coolant temperature is at 68
F (20C).
Disconnect fuel injector connector. Using DVOM, check resistance
between specified fuel injector terminals. See
FUEL INJECTOR TERMINAL IDENTIFICATION table. If resistance is not 2.0-
3.0 3000GT turbo or 13-16 ohms on all other models, replace fuel
injector(s). If resistance is as specified, go to step 6).
FUEL INJECTOR TERMINAL IDENTIFICATION TABLE
\
\
\
\
\
\
Application Terminals No.
Montero ( 1) ........................................ 8 & 1
8 & 2
8 & 3
8 & 5
8 & 6
8 & 7
3000GT - Rear Bank ( 2)
Non-Turbo ........................................ 1 & 2
1 & 5
1 & 6
Turbo ............................................ 1 & 4
2 & 8
4 & 5
4 & 6
4 & 7
4 & 8
( 1) - Check resistance at intermediate fuel injector
connector (component side).
( 2) - Check resistance at rear fuel injector connector
(component side).
\
\
\
\
\
\
Page 756 of 1501
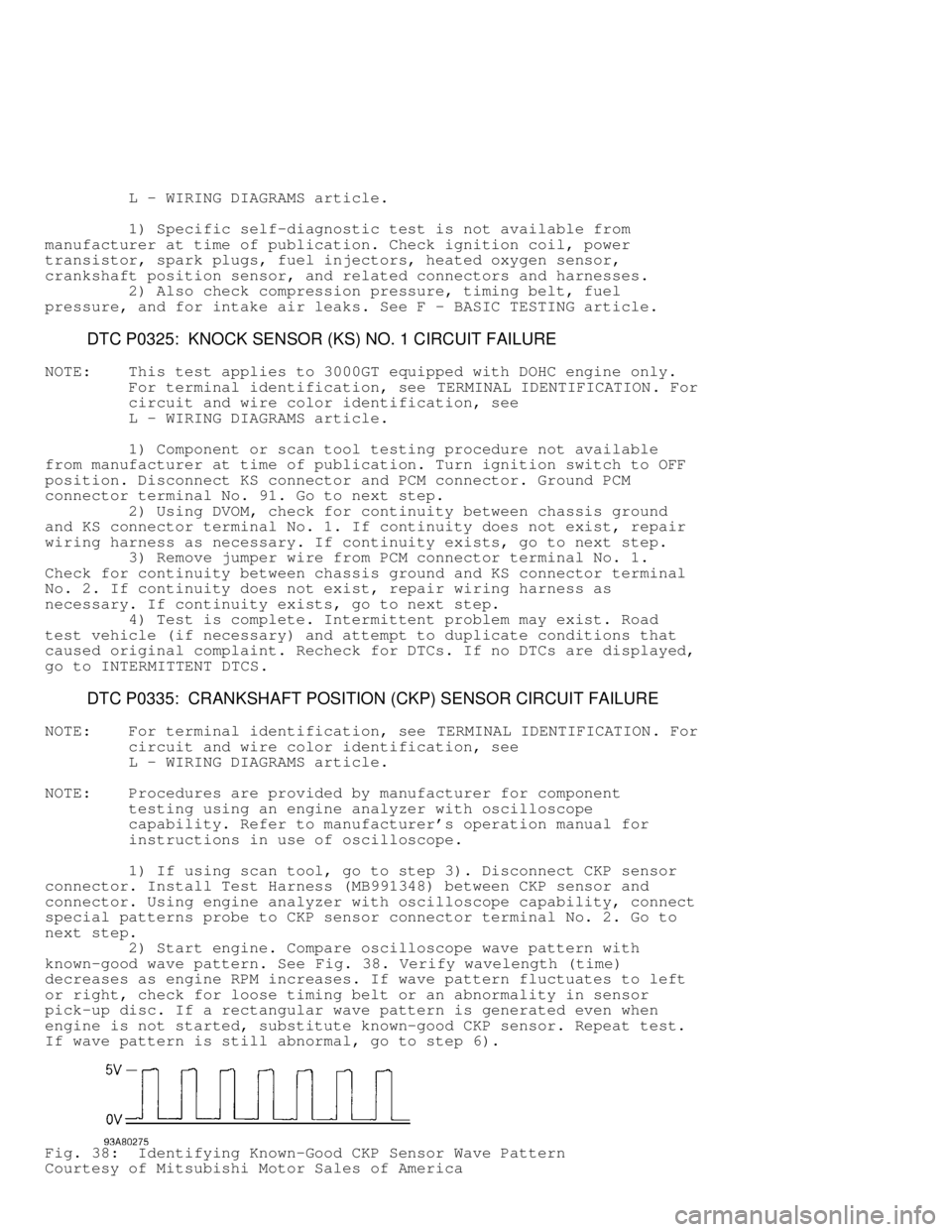
L - WIRING DIAGRAMS article.
1) Specific self-diagnostic test is not available from
manufacturer at time of publication. Check ignition coil, power
transistor, spark plugs, fuel injectors, heated oxygen sensor,
crankshaft position sensor, and related connectors and harnesses.
2) Also check compression pressure, timing belt, fuel
pressure, and for intake air leaks. See F - BASIC TESTING article.
DTC P0325: KNOCK SENSOR (KS) NO. 1 CIRCUIT FAILURE
NOTE: This test applies to 3000GT equipped with DOHC engine only.
For terminal identification, see TERMINAL IDENTIFICATION. For
circuit and wire color identification, see
L - WIRING DIAGRAMS article.
1) Component or scan tool testing procedure not available
from manufacturer at time of publication. Turn ignition switch to OFF
position. Disconnect KS connector and PCM connector. Ground PCM
connector terminal No. 91. Go to next step.
2) Using DVOM, check for continuity between chassis ground
and KS connector terminal No. 1. If continuity does not exist, repair
wiring harness as necessary. If continuity exists, go to next step.
3) Remove jumper wire from PCM connector terminal No. 1.
Check for continuity between chassis ground and KS connector terminal
No. 2. If continuity does not exist, repair wiring harness as
necessary. If continuity exists, go to next step.
4) Test is complete. Intermittent problem may exist. Road
test vehicle (if necessary) and attempt to duplicate conditions that
caused original complaint. Recheck for DTCs. If no DTCs are displayed,
go to INTERMITTENT DTCS .
DTC P0335: CRANKSHAFT POSITION (CKP) SENSOR CIRCUIT FAILURE
NOTE: For terminal identification, see TERMINAL IDENTIFICATION. For
circuit and wire color identification, see
L - WIRING DIAGRAMS article.
NOTE: Procedures are provided by manufacturer for component
testing using an engine analyzer with oscilloscope
capability. Refer to manufacturer's operation manual for
instructions in use of oscilloscope.
1) If using scan tool, go to step 3). Disconnect CKP sensor
connector. Install Test Harness (MB991348) between CKP sensor and
connector. Using engine analyzer with oscilloscope capability, connect
special patterns probe to CKP sensor connector terminal No. 2. Go to
next step.
2) Start engine. Compare oscilloscope wave pattern with
known-good wave pattern. See Fig. 38. Verify wavelength (time)
decreases as engine RPM increases. If wave pattern fluctuates to left
or right, check for loose timing belt or an abnormality in sensor
pick-up disc. If a rectangular wave pattern is generated even when
engine is not started, substitute known-good CKP sensor. Repeat test.
If wave pattern is still abnormal, go to step 6).
Fig. 38: Identifying Known-Good CKP Sensor Wave Pattern
Courtesy of Mitsubishi Motor Sales of America
Page 757 of 1501
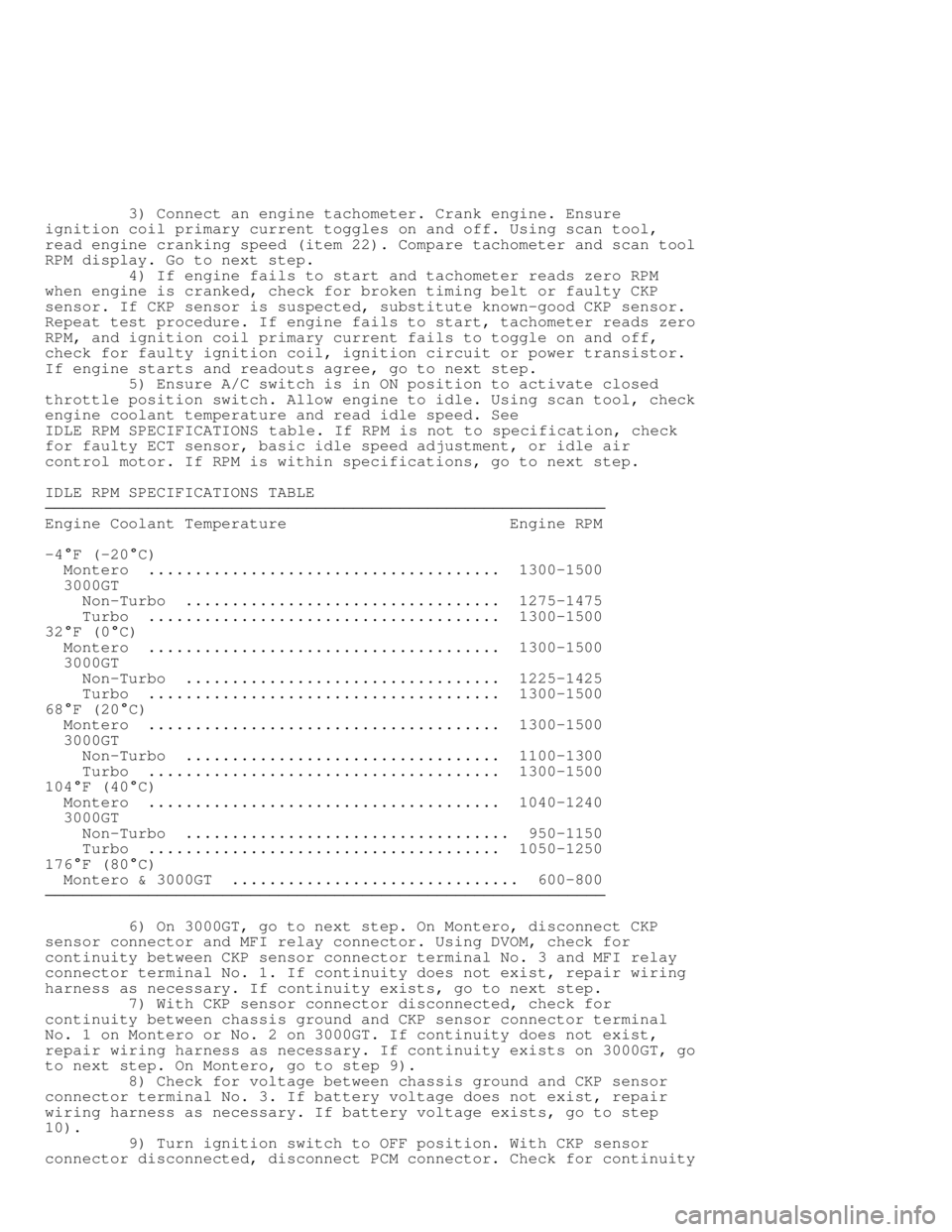
3) Connect an engine tachometer. Crank engine. Ensure
ignition coil primary current toggles on and off. Using scan tool,
read engine cranking speed (item 22). Compare tachometer and scan tool\
RPM display. Go to next step.
4) If engine fails to start and tachometer reads zero RPM
when engine is cranked, check for broken timing belt or faulty CKP
sensor. If CKP sensor is suspected, substitute known-good CKP sensor.
Repeat test procedure. If engine fails to start, tachometer reads zero
RPM, and ignition coil primary current fails to toggle on and off,
check for faulty ignition coil, ignition circuit or power transistor.
If engine starts and readouts agree, go to next step.
5) Ensure A/C switch is in ON position to activate closed
throttle position switch. Allow engine to idle. Using scan tool, check
engine coolant temperature and read idle speed. See
IDLE RPM SPECIFICATIONS table. If RPM is not to specification, check
for faulty ECT sensor, basic idle speed adjustment, or idle air
control motor. If RPM is within specifications, go to next step.
IDLE RPM SPECIFICATIONS TABLE
\
\
\
\
\
\
Engine Coolant Temperature Engine RPM
-4
F (-20C)
Montero ...................................... 1300-1500
3000GT
Non-Turbo .................................. 1275-1475
Turbo ...................................... 1300-1500
32
F (0C)
Montero ...................................... 1300-1500
3000GT
Non-Turbo .................................. 1225-1425
Turbo ...................................... 1300-1500
68
F (20C)
Montero ...................................... 1300-1500
3000GT
Non-Turbo .................................. 1100-1300
Turbo ...................................... 1300-1500
104
F (40C)
Montero ...................................... 1040-1240
3000GT
Non-Turbo ................................... 950-1150
Turbo ...................................... 1050-1250
176
F (80C)
Montero & 3000GT ............................... 600-800
\
\
\
\
\
\
6) On 3000GT, go to next step. On Montero, disconnect CKP
sensor connector and MFI relay connector. Using DVOM, check for
continuity between CKP sensor connector terminal No. 3 and MFI relay
connector terminal No. 1. If continuity does not exist, repair wiring
harness as necessary. If continuity exists, go to next step.
7) With CKP sensor connector disconnected, check for
continuity between chassis ground and CKP sensor connector terminal
No. 1 on Montero or No. 2 on 3000GT. If continuity does not exist,
repair wiring harness as necessary. If continuity exists on 3000GT, go
to next step. On Montero, go to step 9).
8) Check for voltage between chassis ground and CKP sensor
connector terminal No. 3. If battery voltage does not exist, repair
wiring harness as necessary. If battery voltage exists, go to step
10).
9) Turn ignition switch to OFF position. With CKP sensor
connector disconnected, disconnect PCM connector. Check for continuity
Page 758 of 1501
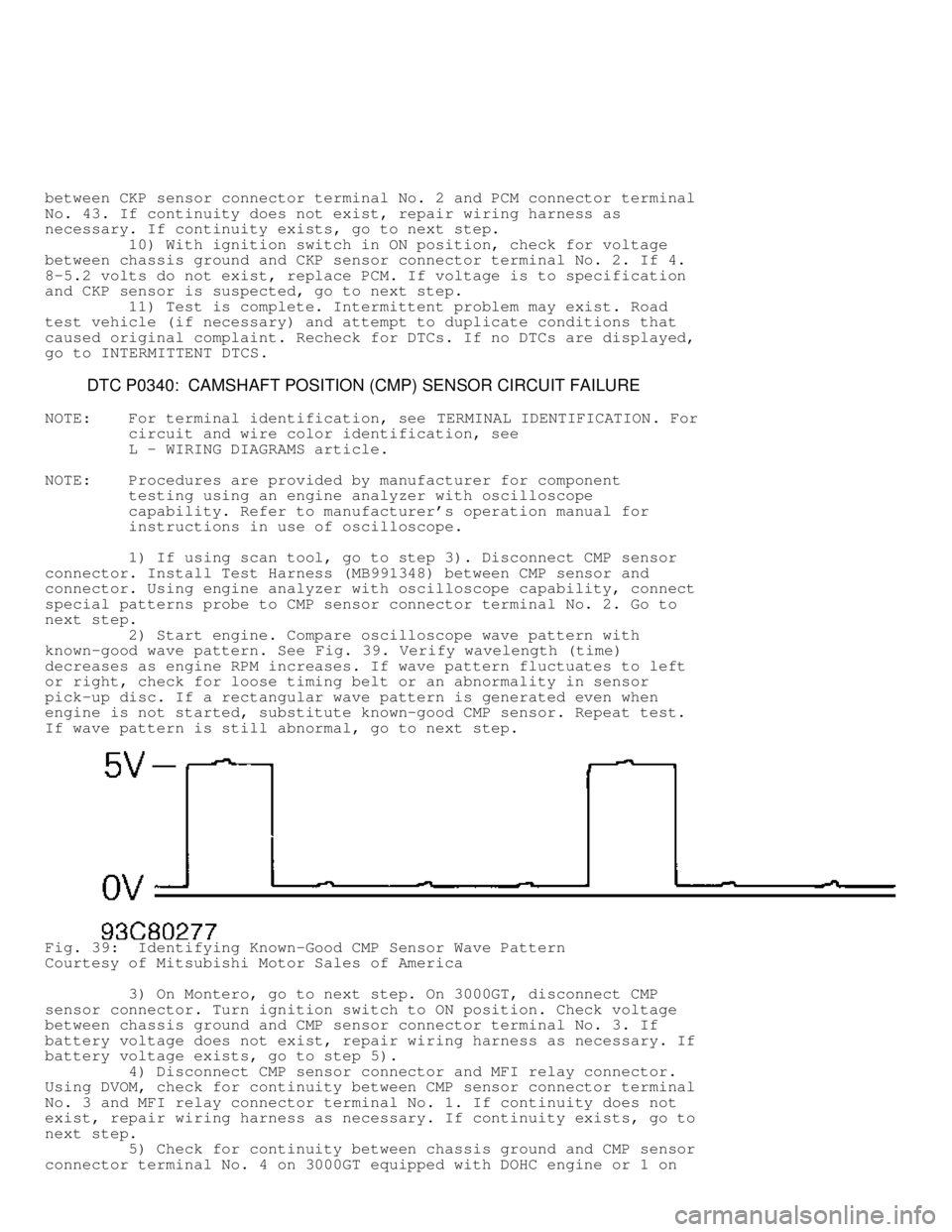
between CKP sensor connector terminal No. 2 and PCM connector terminal
No. 43. If continuity does not exist, repair wiring harness as
necessary. If continuity exists, go to next step.
10) With ignition switch in ON position, check for voltage
between chassis ground and CKP sensor connector terminal No. 2. If 4.
8-5.2 volts do not exist, replace PCM. If voltage is to specification
and CKP sensor is suspected, go to next step.
11) Test is complete. Intermittent problem may exist. Road
test vehicle (if necessary) and attempt to duplicate conditions that
caused original complaint. Recheck for DTCs. If no DTCs are displayed,
go to INTERMITTENT DTCS .
DTC P0340: CAMSHAFT POSITION (CMP) SENSOR CIRCUIT FAILURE
NOTE: For terminal identification, see TERMINAL IDENTIFICATION. For
circuit and wire color identification, see
L - WIRING DIAGRAMS article.
NOTE: Procedures are provided by manufacturer for component
testing using an engine analyzer with oscilloscope
capability. Refer to manufacturer's operation manual for
instructions in use of oscilloscope.
1) If using scan tool, go to step 3). Disconnect CMP sensor
connector. Install Test Harness (MB991348) between CMP sensor and
connector. Using engine analyzer with oscilloscope capability, connect
special patterns probe to CMP sensor connector terminal No. 2. Go to
next step.
2) Start engine. Compare oscilloscope wave pattern with
known-good wave pattern. See Fig. 39. Verify wavelength (time)
decreases as engine RPM increases. If wave pattern fluctuates to left
or right, check for loose timing belt or an abnormality in sensor
pick-up disc. If a rectangular wave pattern is generated even when
engine is not started, substitute known-good CMP sensor. Repeat test.
If wave pattern is still abnormal, go to next step.
Fig. 39: Identifying Known-Good CMP Sensor Wave Pattern
Courtesy of Mitsubishi Motor Sales of America
3) On Montero, go to next step. On 3000GT, disconnect CMP
sensor connector. Turn ignition switch to ON position. Check voltage
between chassis ground and CMP sensor connector terminal No. 3. If
battery voltage does not exist, repair wiring harness as necessary. If
battery voltage exists, go to step 5).
4) Disconnect CMP sensor connector and MFI relay connector.
Using DVOM, check for continuity between CMP sensor connector terminal
No. 3 and MFI relay connector terminal No. 1. If continuity does not
exist, repair wiring harness as necessary. If continuity exists, go to
next step.
5) Check for continuity between chassis ground and CMP sensor
connector terminal No. 4 on 3000GT equipped with DOHC engine or 1 on
Page 760 of 1501
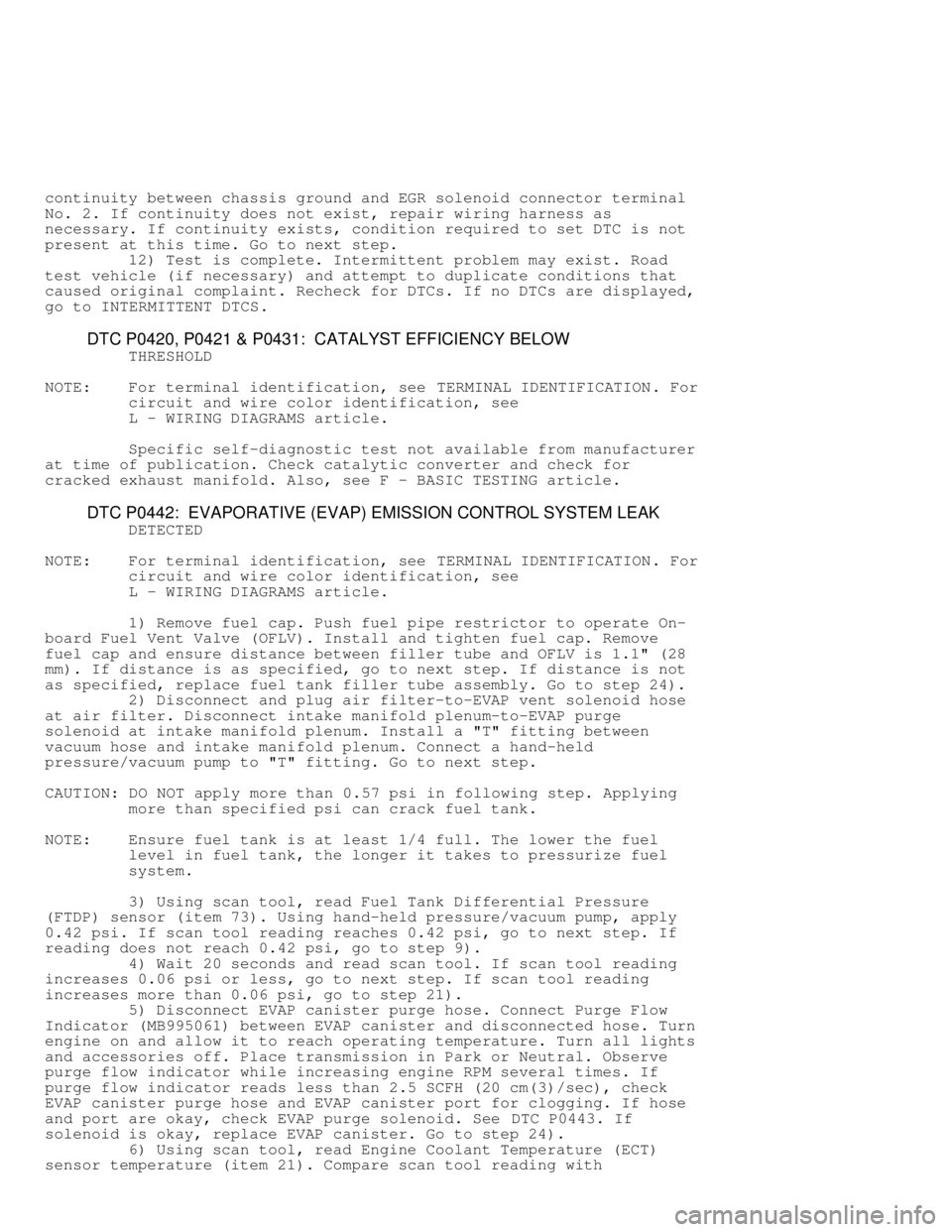
continuity between chassis ground and EGR solenoid connector terminal
No. 2. If continuity does not exist, repair wiring harness as
necessary. If continuity exists, condition required to set DTC is not
present at this time. Go to next step.
12) Test is complete. Intermittent problem may exist. Road
test vehicle (if necessary) and attempt to duplicate conditions that
caused original complaint. Recheck for DTCs. If no DTCs are displayed,
go to INTERMITTENT DTCS .
DTC P0420, P0421 & P0431: CATALYST EFFICIENCY BELOW
THRESHOLD
NOTE: For terminal identification, see TERMINAL IDENTIFICATION. For
circuit and wire color identification, see
L - WIRING DIAGRAMS article.
Specific self-diagnostic test not available from manufacturer
at time of publication. Check catalytic converter and check for
cracked exhaust manifold. Also, see F - BASIC TESTING article.
DTC P0442: EVAPORATIVE (EVAP) EMISSION CONTROL SYSTEM LEAK
DETECTED
NOTE: For terminal identification, see TERMINAL IDENTIFICATION. For
circuit and wire color identification, see
L - WIRING DIAGRAMS article.
1) Remove fuel cap. Push fuel pipe restrictor to operate On-
board Fuel Vent Valve (OFLV). Install and tighten fuel cap. Remove
fuel cap and ensure distance between filler tube and OFLV is 1.1" (28
mm). If distance is as specified, go to next step. If distance is not
as specified, replace fuel tank filler tube assembly. Go to step 24).
2) Disconnect and plug air filter-to-EVAP vent solenoid hose
at air filter. Disconnect intake manifold plenum-to-EVAP purge
solenoid at intake manifold plenum. Install a "T" fitting between
vacuum hose and intake manifold plenum. Connect a hand-held
pressure/vacuum pump to "T" fitting. Go to next step.
CAUTION: DO NOT apply more than 0.57 psi in following step. Applying
more than specified psi can crack fuel tank.
NOTE: Ensure fuel tank is at least 1/4 full. The lower the fuel
level in fuel tank, the longer it takes to pressurize fuel
system.
3) Using scan tool, read Fuel Tank Differential Pressure
(FTDP) sensor (item 73). Using hand-held pressure/vacuum pump, apply\
0.42 psi. If scan tool reading reaches 0.42 psi, go to next step. If
reading does not reach 0.42 psi, go to step 9).
4) Wait 20 seconds and read scan tool. If scan tool reading
increases 0.06 psi or less, go to next step. If scan tool reading
increases more than 0.06 psi, go to step 21).
5) Disconnect EVAP canister purge hose. Connect Purge Flow
Indicator (MB995061) between EVAP canister and disconnected hose. Turn\
engine on and allow it to reach operating temperature. Turn all lights
and accessories off. Place transmission in Park or Neutral. Observe
purge flow indicator while increasing engine RPM several times. If
purge flow indicator reads less than 2.5 SCFH (20 cm(3)/sec), check
EVAP canister purge hose and EVAP canister port for clogging. If hose
and port are okay, check EVAP purge solenoid. See DTC P0443. If
solenoid is okay, replace EVAP canister. Go to step 24).
6) Using scan tool, read Engine Coolant Temperature (ECT)
sensor temperature (item 21). Compare scan tool reading with
Page 761 of 1501
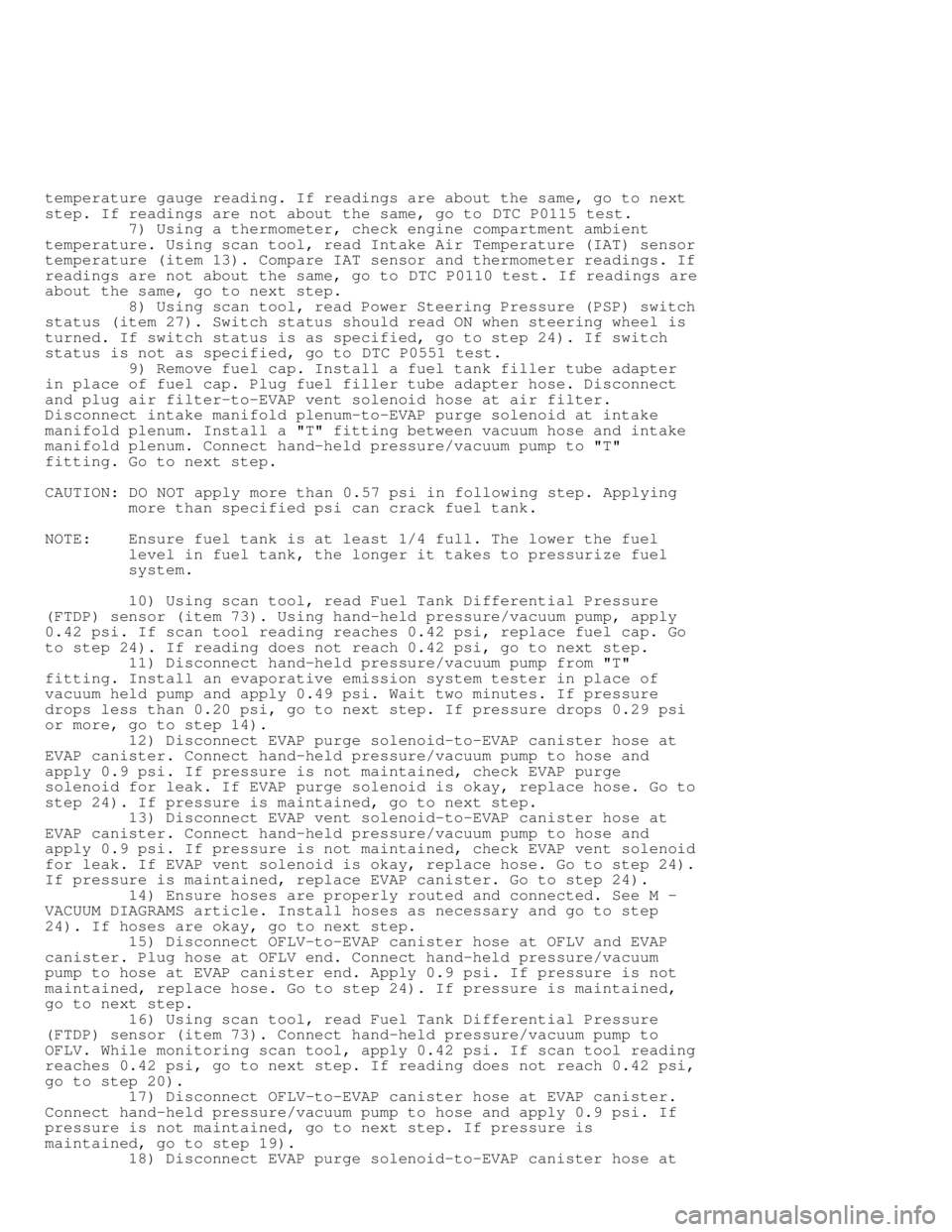
temperature gauge reading. If readings are about the same, go to next
step. If readings are not about the same, go to DTC P0115 test.
7) Using a thermometer, check engine compartment ambient
temperature. Using scan tool, read Intake Air Temperature (IAT) sensor\
temperature (item 13). Compare IAT sensor and thermometer readings. If\
readings are not about the same, go to DTC P0110 test. If readings are
about the same, go to next step.
8) Using scan tool, read Power Steering Pressure (PSP) switc\
h
status (item 27). Switch status should read ON when steering wheel is
turned. If switch status is as specified, go to step 24). If switch
status is not as specified, go to DTC P0551 test.
9) Remove fuel cap. Install a fuel tank filler tube adapter
in place of fuel cap. Plug fuel filler tube adapter hose. Disconnect
and plug air filter-to-EVAP vent solenoid hose at air filter.
Disconnect intake manifold plenum-to-EVAP purge solenoid at intake
manifold plenum. Install a "T" fitting between vacuum hose and intake
manifold plenum. Connect hand-held pressure/vacuum pump to "T"
fitting. Go to next step.
CAUTION: DO NOT apply more than 0.57 psi in following step. Applying
more than specified psi can crack fuel tank.
NOTE: Ensure fuel tank is at least 1/4 full. The lower the fuel
level in fuel tank, the longer it takes to pressurize fuel
system.
10) Using scan tool, read Fuel Tank Differential Pressure
(FTDP) sensor (item 73). Using hand-held pressure/vacuum pump, apply\
0.42 psi. If scan tool reading reaches 0.42 psi, replace fuel cap. Go
to step 24). If reading does not reach 0.42 psi, go to next step.
11) Disconnect hand-held pressure/vacuum pump from "T"
fitting. Install an evaporative emission system tester in place of
vacuum held pump and apply 0.49 psi. Wait two minutes. If pressure
drops less than 0.20 psi, go to next step. If pressure drops 0.29 psi
or more, go to step 14).
12) Disconnect EVAP purge solenoid-to-EVAP canister hose at
EVAP canister. Connect hand-held pressure/vacuum pump to hose and
apply 0.9 psi. If pressure is not maintained, check EVAP purge
solenoid for leak. If EVAP purge solenoid is okay, replace hose. Go to
step 24). If pressure is maintained, go to next step.
13) Disconnect EVAP vent solenoid-to-EVAP canister hose at
EVAP canister. Connect hand-held pressure/vacuum pump to hose and
apply 0.9 psi. If pressure is not maintained, check EVAP vent solenoid
for leak. If EVAP vent solenoid is okay, replace hose. Go to step 24).
If pressure is maintained, replace EVAP canister. Go to step 24).
14) Ensure hoses are properly routed and connected. See M -
VACUUM DIAGRAMS article. Install hoses as necessary and go to step
24). If hoses are okay, go to next step.
15) Disconnect OFLV-to-EVAP canister hose at OFLV and EVAP
canister. Plug hose at OFLV end. Connect hand-held pressure/vacuum
pump to hose at EVAP canister end. Apply 0.9 psi. If pressure is not
maintained, replace hose. Go to step 24). If pressure is maintained,
go to next step.
16) Using scan tool, read Fuel Tank Differential Pressure
(FTDP) sensor (item 73). Connect hand-held pressure/vacuum pump to
OFLV. While monitoring scan tool, apply 0.42 psi. If scan tool reading
reaches 0.42 psi, go to next step. If reading does not reach 0.42 psi,
go to step 20).
17) Disconnect OFLV-to-EVAP canister hose at EVAP canister.
Connect hand-held pressure/vacuum pump to hose and apply 0.9 psi. If
pressure is not maintained, go to next step. If pressure is
maintained, go to step 19).
18) Disconnect EVAP purge solenoid-to-EVAP canister hose at