check engine MITSUBISHI MONTERO 1998 Service Manual
[x] Cancel search | Manufacturer: MITSUBISHI, Model Year: 1998, Model line: MONTERO, Model: MITSUBISHI MONTERO 1998Pages: 1501, PDF Size: 25.81 MB
Page 838 of 1501
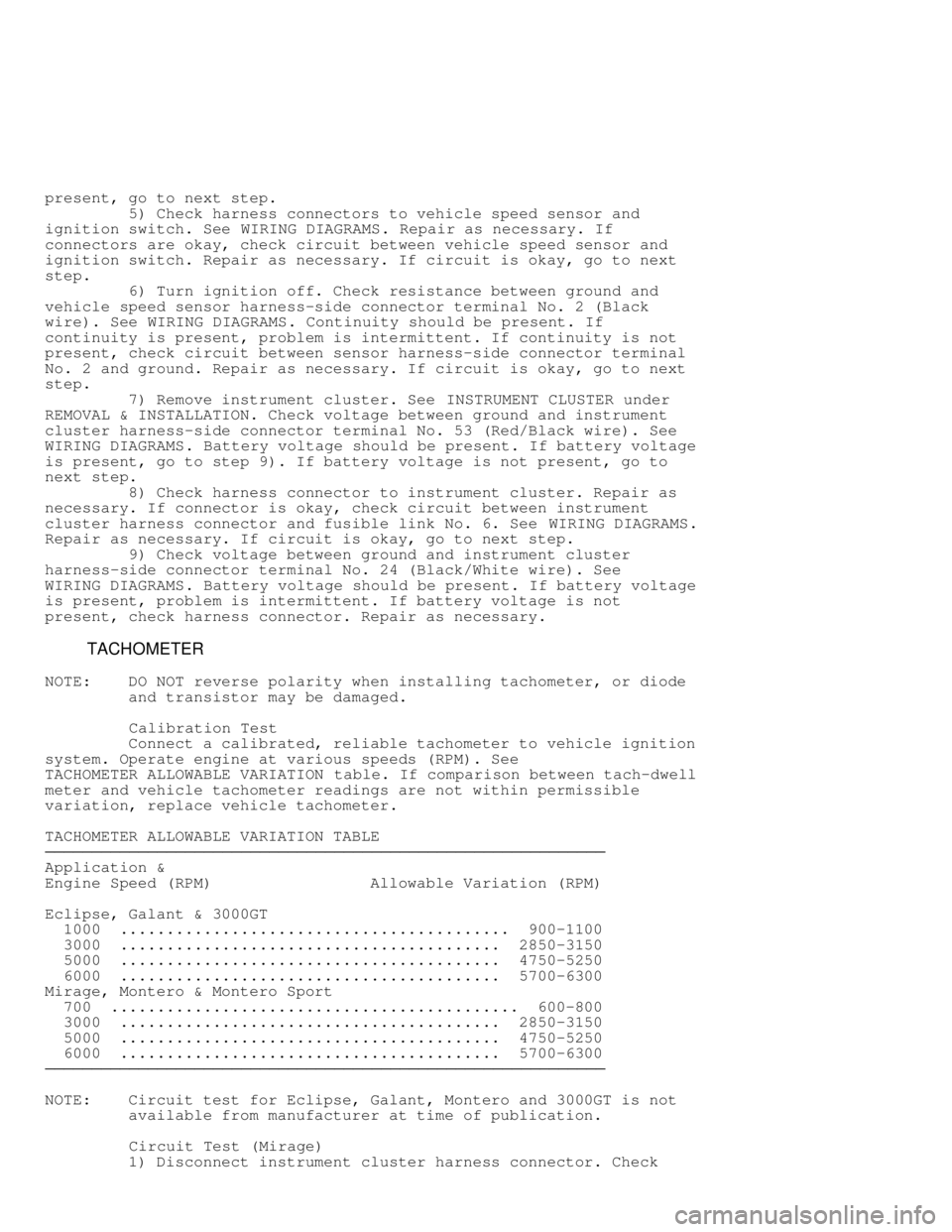
present, go to next step.
5) Check harness connectors to vehicle speed sensor and
ignition switch. See WIRING DIAGRAMS. Repair as necessary. If
connectors are okay, check circuit between vehicle speed sensor and
ignition switch. Repair as necessary. If circuit is okay, go to next
step.
6) Turn ignition off. Check resistance between ground and
vehicle speed sensor harness-side connector terminal No. 2 (Black
wire). See WIRING DIAGRAMS . Continuity should be present. If
continuity is present, problem is intermittent. If continuity is not
present, check circuit between sensor harness-side connector terminal
No. 2 and ground. Repair as necessary. If circuit is okay, go to next
step.
7) Remove instrument cluster. See INSTRUMENT CLUSTER under
REMOVAL & INSTALLATION. Check voltage between ground and instrument
cluster harness-side connector terminal No. 53 (Red/Black wire). See
WIRING DIAGRAMS . Battery voltage should be present. If battery voltage
is present, go to step 9). If battery voltage is not present, go to
next step.
8) Check harness connector to instrument cluster. Repair as
necessary. If connector is okay, check circuit between instrument
cluster harness connector and fusible link No. 6. See WIRING DIAGRAMS.
Repair as necessary. If circuit is okay, go to next step.
9) Check voltage between ground and instrument cluster
harness-side connector terminal No. 24 (Black/White wire). See
WIRING DIAGRAMS . Battery voltage should be present. If battery voltage
is present, problem is intermittent. If battery voltage is not
present, check harness connector. Repair as necessary.
TACHOMETER
NOTE: DO NOT reverse polarity when installing tachometer, or diode
and transistor may be damaged.
Calibration Test
Connect a calibrated, reliable tachometer to vehicle ignition
system. Operate engine at various speeds (RPM). See
TACHOMETER ALLOWABLE VARIATION table. If comparison between tach-dwell
meter and vehicle tachometer readings are not within permissible
variation, replace vehicle tachometer.
TACHOMETER ALLOWABLE VARIATION TABLE
\
\
\
\
\
\
Application &
Engine Speed (RPM) Allowable Variation (RPM)
Eclipse, Galant & 3000GT
1000 .......................................... 900-1100
3000 ......................................... 2850-3150
5000 ......................................... 4750-5250
6000 ......................................... 5700-6300
Mirage, Montero & Montero Sport
700 ............................................ 600-800
3000 ......................................... 2850-3150
5000 ......................................... 4750-5250
6000 ......................................... 5700-6300
\
\
\
\
\
\
NOTE: Circuit test for Eclipse, Galant, Montero and 3000GT is not
available from manufacturer at time of publication.
Circuit Test (Mirage)
1) Disconnect instrument cluster harness connector. Check
Page 839 of 1501
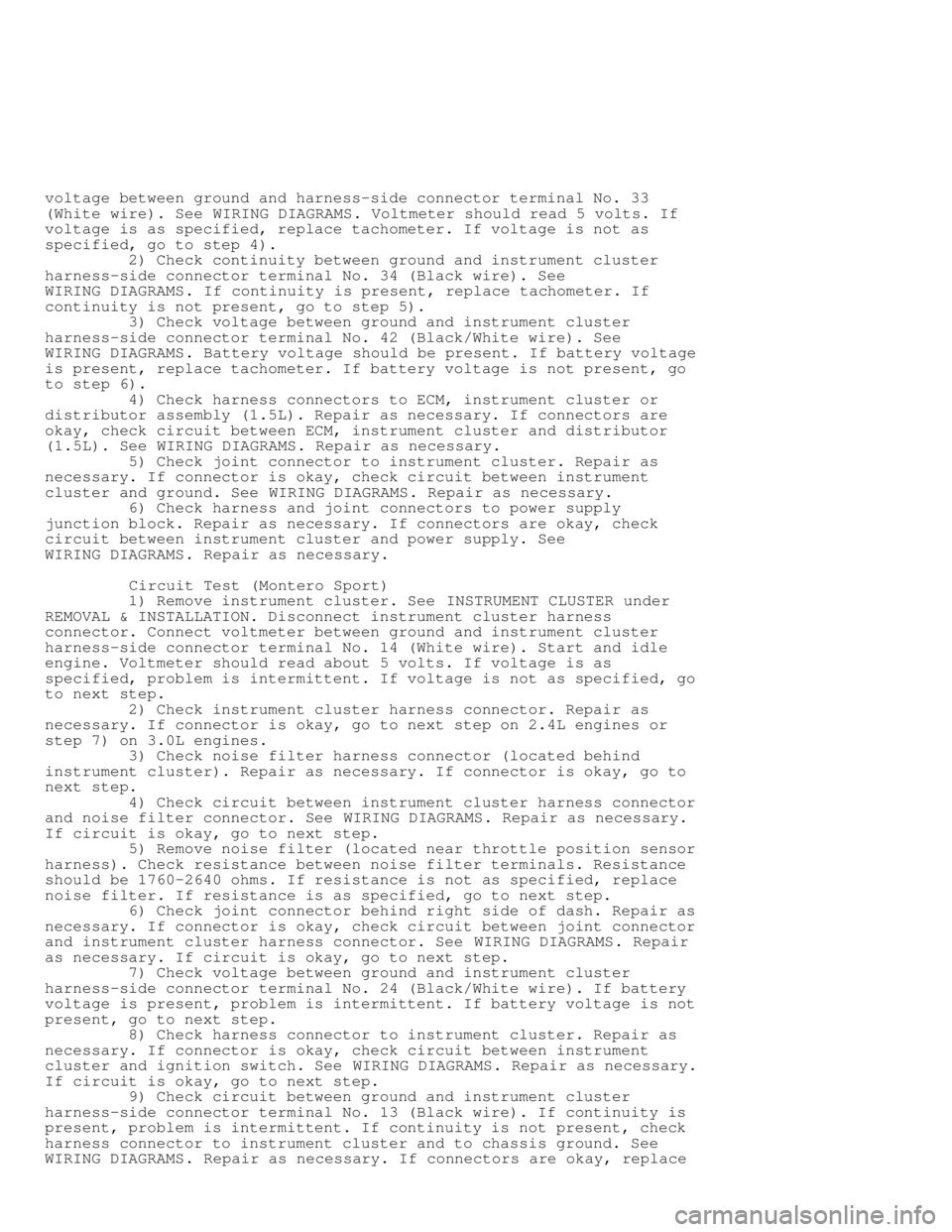
voltage between ground and harness-side connector terminal No. 33
(White wire). See WIRING DIAGRAMS. Voltmeter should read 5 volts. If
voltage is as specified, replace tachometer. If voltage is not as
specified, go to step 4).
2) Check continuity between ground and instrument cluster
harness-side connector terminal No. 34 (Black wire). See
WIRING DIAGRAMS . If continuity is present, replace tachometer. If
continuity is not present, go to step 5).
3) Check voltage between ground and instrument cluster
harness-side connector terminal No. 42 (Black/White wire). See
WIRING DIAGRAMS . Battery voltage should be present. If battery voltage
is present, replace tachometer. If battery voltage is not present, go
to step 6).
4) Check harness connectors to ECM, instrument cluster or
distributor assembly (1.5L). Repair as necessary. If connectors are
okay, check circuit between ECM, instrument cluster and distributor
(1.5L). See WIRING DIAGRAMS . Repair as necessary.
5) Check joint connector to instrument cluster. Repair as
necessary. If connector is okay, check circuit between instrument
cluster and ground. See WIRING DIAGRAMS. Repair as necessary.
6) Check harness and joint connectors to power supply
junction block. Repair as necessary. If connectors are okay, check
circuit between instrument cluster and power supply. See
WIRING DIAGRAMS . Repair as necessary.
Circuit Test (Montero Sport)
1) Remove instrument cluster. See INSTRUMENT CLUSTER under
REMOVAL & INSTALLATION. Disconnect instrument cluster harness
connector. Connect voltmeter between ground and instrument cluster
harness-side connector terminal No. 14 (White wire). Start and idle
engine. Voltmeter should read about 5 volts. If voltage is as
specified, problem is intermittent. If voltage is not as specified, go
to next step.
2) Check instrument cluster harness connector. Repair as
necessary. If connector is okay, go to next step on 2.4L engines or
step 7) on 3.0L engines.
3) Check noise filter harness connector (located behind
instrument cluster). Repair as necessary. If connector is okay, go to
next step.
4) Check circuit between instrument cluster harness connector
and noise filter connector. See WIRING DIAGRAMS. Repair as necessary.
If circuit is okay, go to next step.
5) Remove noise filter (located near throttle position sensor\
harness). Check resistance between noise filter terminals. Resistance
should be 1760-2640 ohms. If resistance is not as specified, replace
noise filter. If resistance is as specified, go to next step.
6) Check joint connector behind right side of dash. Repair as
necessary. If connector is okay, check circuit between joint connector
and instrument cluster harness connector. See WIRING DIAGRAMS. Repair
as necessary. If circuit is okay, go to next step.
7) Check voltage between ground and instrument cluster
harness-side connector terminal No. 24 (Black/White wire). If battery
voltage is present, problem is intermittent. If battery voltage is not
present, go to next step.
8) Check harness connector to instrument cluster. Repair as
necessary. If connector is okay, check circuit between instrument
cluster and ignition switch. See WIRING DIAGRAMS. Repair as necessary.
If circuit is okay, go to next step.
9) Check circuit between ground and instrument cluster
harness-side connector terminal No. 13 (Black wire). If continuity is
present, problem is intermittent. If continuity is not present, check
harness connector to instrument cluster and to chassis ground. See
WIRING DIAGRAMS . Repair as necessary. If connectors are okay, replace
Page 840 of 1501
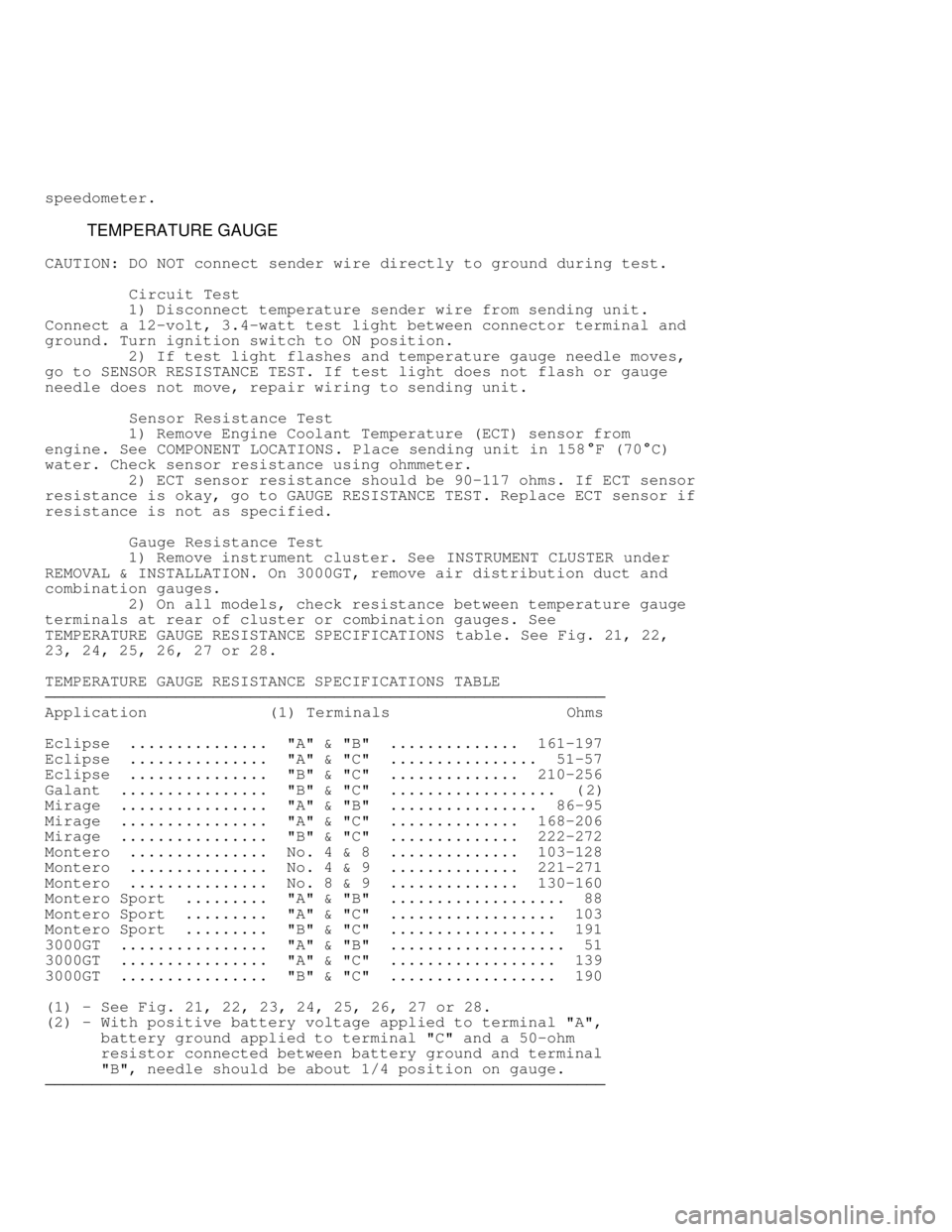
speedometer.
TEMPERATURE GAUGE
CAUTION: DO NOT connect sender wire directly to ground during test.
Circuit Test
1) Disconnect temperature sender wire from sending unit.
Connect a 12-volt, 3.4-watt test light between connector terminal and
ground. Turn ignition switch to ON position.
2) If test light flashes and temperature gauge needle moves,
go to SENSOR RESISTANCE TEST. If test light does not flash or gauge
needle does not move, repair wiring to sending unit.
Sensor Resistance Test
1) Remove Engine Coolant Temperature (ECT) sensor from
engine. See COMPONENT LOCATIONS . Place sending unit in 158
F (70C)
water. Check sensor resistance using ohmmeter.
2) ECT sensor resistance should be 90-117 ohms. If ECT sensor
resistance is okay, go to GAUGE RESISTANCE TEST. Replace ECT sensor if
resistance is not as specified.
Gauge Resistance Test
1) Remove instrument cluster. See INSTRUMENT CLUSTER under
REMOVAL & INSTALLATION. On 3000GT, remove air distribution duct and
combination gauges.
2) On all models, check resistance between temperature gauge
terminals at rear of cluster or combination gauges. See
TEMPERATURE GAUGE RESISTANCE SPECIFICATIONS table. See Fig. 21, 22,
23, 24, 25, 26, 27 or 28.
TEMPERATURE GAUGE RESISTANCE SPECIFICATIONS TABLE
\
\
\
\
\
\
Application ( 1) Terminals Ohms
Eclipse ............... "A" & "B" .............. 161-197
Eclipse ............... "A" & "C" ................ 51-57
Eclipse ............... "B" & "C" .............. 210-256
Galant ................ "B" & "C" .................. ( 2)
Mirage ................ "A" & "B" ................ 86-95
Mirage ................ "A" & "C" .............. 168-206
Mirage ................ "B" & "C" .............. 222-272
Montero ............... No. 4 & 8 .............. 103-128
Montero ............... No. 4 & 9 .............. 221-271
Montero ............... No. 8 & 9 .............. 130-160
Montero Sport ......... "A" & "B" ................... 88
Montero Sport ......... "A" & "C" .................. 103
Montero Sport ......... "B" & "C" .................. 191
3000GT ................ "A" & "B" ................... 51
3000GT ................ "A" & "C" .................. 139
3000GT ................ "B" & "C" .................. 190
( 1) - See Fig. 21, 22, 23, 24, 25, 26, 27 or 28.
( 2) - With positive battery voltage applied to terminal "A",
battery ground applied to terminal "C" and a 50-ohm
resistor connected between battery ground and terminal
"B", needle should be about 1/4 position on gauge.
\
\
\
\
\
\
Page 848 of 1501
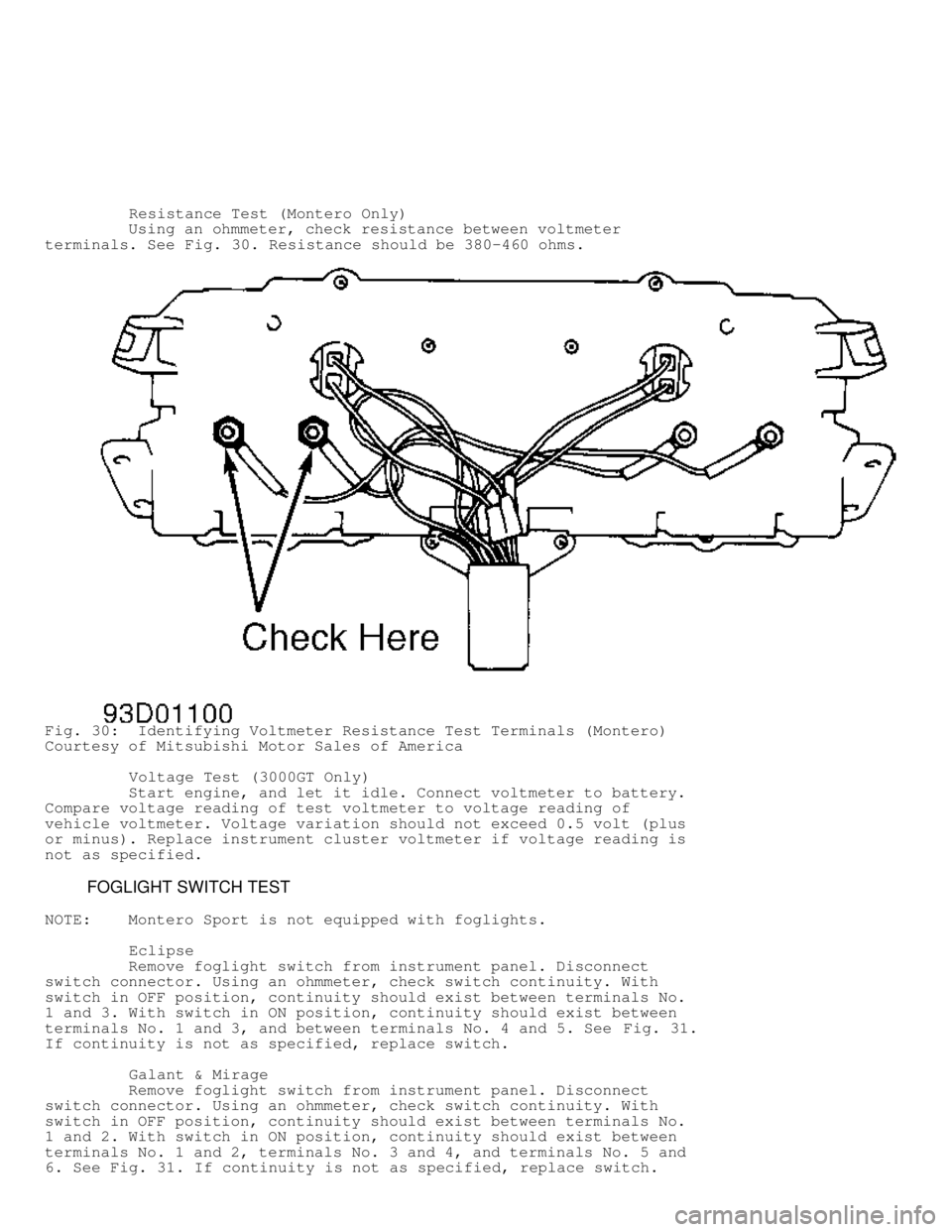
Resistance Test (Montero Only)
Using an ohmmeter, check resistance between voltmeter
terminals. See Fig. 30. Resistance should be 380-460 ohms.
Fig. 30: Identifying Voltmeter Resistance Test Terminals (Montero)
Courtesy of Mitsubishi Motor Sales of America
Voltage Test (3000GT Only)
Start engine, and let it idle. Connect voltmeter to battery.
Compare voltage reading of test voltmeter to voltage reading of
vehicle voltmeter. Voltage variation should not exceed 0.5 volt (plus
or minus). Replace instrument cluster voltmeter if voltage reading is
not as specified.
FOGLIGHT SWITCH TEST
NOTE: Montero Sport is not equipped with foglights.
Eclipse
Remove foglight switch from instrument panel. Disconnect
switch connector. Using an ohmmeter, check switch continuity. With
switch in OFF position, continuity should exist between terminals No.
1 and 3. With switch in ON position, continuity should exist between
terminals No. 1 and 3, and between terminals No. 4 and 5. See Fig. 31.
If continuity is not as specified, replace switch.
Galant & Mirage
Remove foglight switch from instrument panel. Disconnect
switch connector. Using an ohmmeter, check switch continuity. With
switch in OFF position, continuity should exist between terminals No.
1 and 2. With switch in ON position, continuity should exist between
terminals No. 1 and 2, terminals No. 3 and 4, and terminals No. 5 and
6. See Fig. 31. If continuity is not as specified, replace switch.
Page 850 of 1501
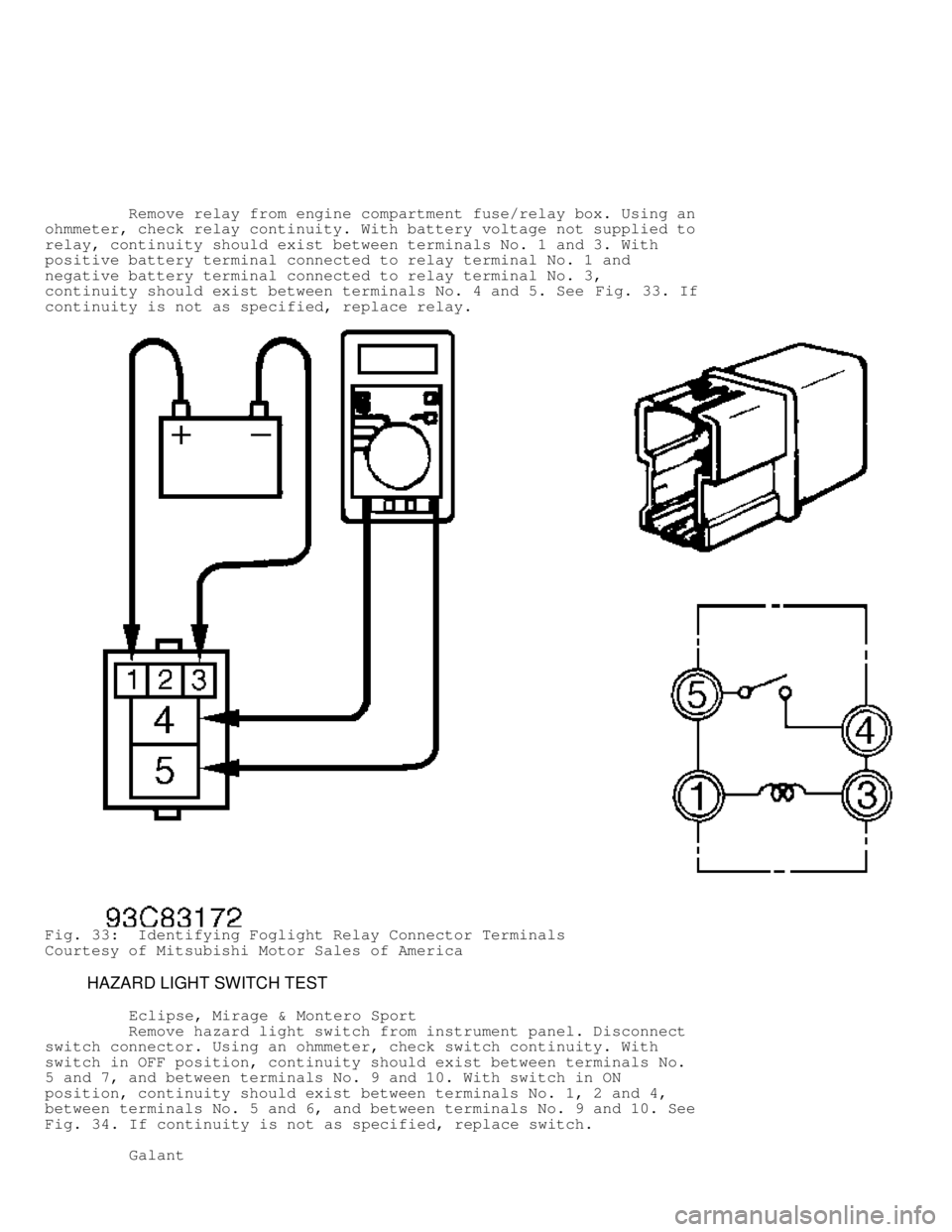
Remove relay from engine compartment fuse/relay box. Using an
ohmmeter, check relay continuity. With battery voltage not supplied to
relay, continuity should exist between terminals No. 1 and 3. With
positive battery terminal connected to relay terminal No. 1 and
negative battery terminal connected to relay terminal No. 3,
continuity should exist between terminals No. 4 and 5. See Fig. 33. If
continuity is not as specified, replace relay.
Fig. 33: Identifying Foglight Relay Connector Terminals
Courtesy of Mitsubishi Motor Sales of America
HAZARD LIGHT SWITCH TEST
Eclipse, Mirage & Montero Sport
Remove hazard light switch from instrument panel. Disconnect
switch connector. Using an ohmmeter, check switch continuity. With
switch in OFF position, continuity should exist between terminals No.
5 and 7, and between terminals No. 9 and 10. With switch in ON
position, continuity should exist between terminals No. 1, 2 and 4,
between terminals No. 5 and 6, and between terminals No. 9 and 10. See
Fig. 34 . If continuity is not as specified, replace switch.
Galant
Page 874 of 1501
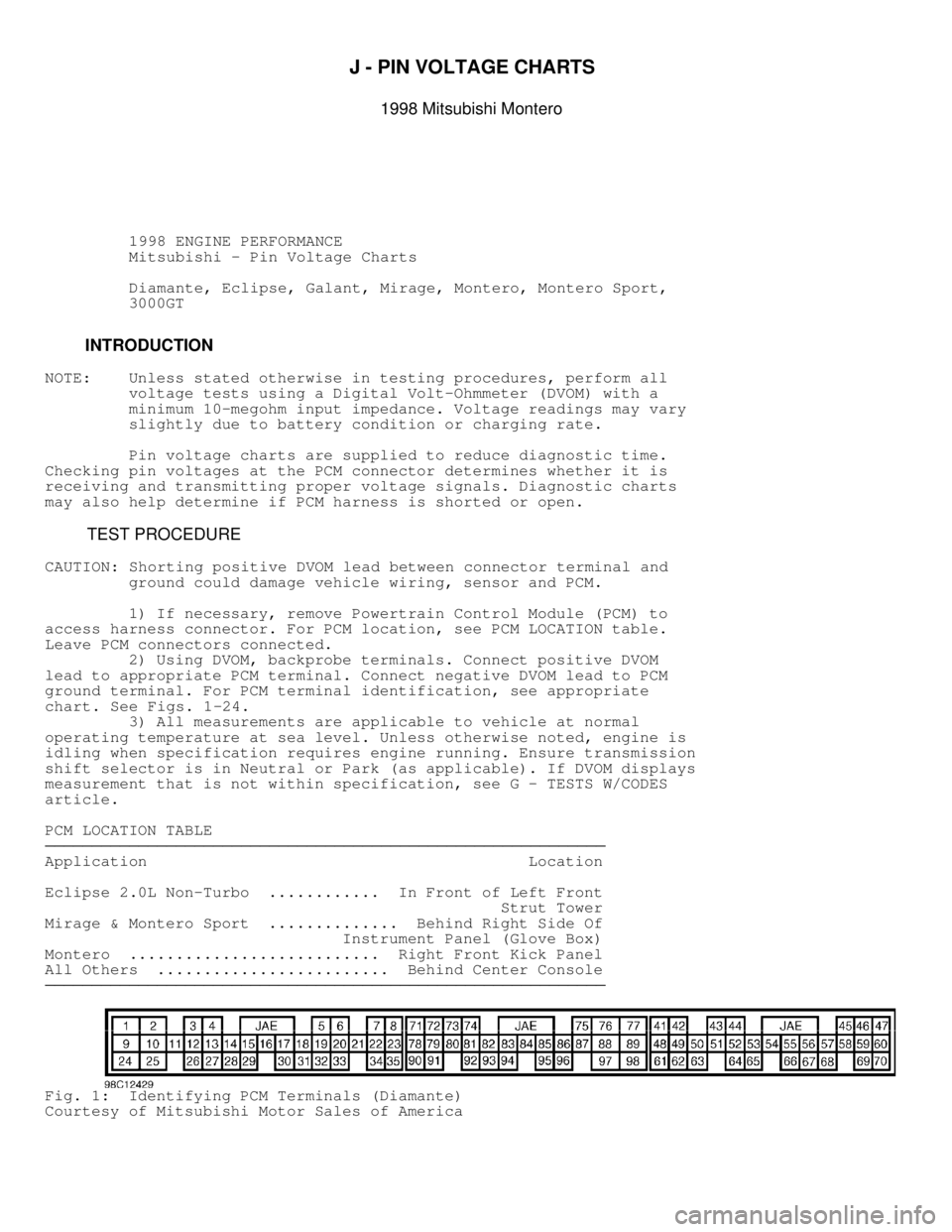
J - PIN VOLTAGE CHARTS
1998 Mitsubishi Montero
1998 ENGINE PERFORMANCE
Mitsubishi - Pin Voltage Charts
Diamante, Eclipse, Galant, Mirage, Montero, Montero Sport,
3000GT
INTRODUCTION
NOTE: Unless stated otherwise in testing procedures, perform all
voltage tests using a Digital Volt-Ohmmeter (DVOM) with a
minimum 10-megohm input impedance. Voltage readings may vary
slightly due to battery condition or charging rate.
Pin voltage charts are supplied to reduce diagnostic time.
Checking pin voltages at the PCM connector determines whether it is
receiving and transmitting proper voltage signals. Diagnostic charts
may also help determine if PCM harness is shorted or open.
TEST PROCEDURE
CAUTION: Shorting positive DVOM lead between connector terminal and
ground could damage vehicle wiring, sensor and PCM.
1) If necessary, remove Powertrain Control Module (PCM) to
access harness connector. For PCM location, see PCM LOCATION table.
Leave PCM connectors connected.
2) Using DVOM, backprobe terminals. Connect positive DVOM
lead to appropriate PCM terminal. Connect negative DVOM lead to PCM
ground terminal. For PCM terminal identification, see appropriate
chart. See Figs. 1-24.
3) All measurements are applicable to vehicle at normal
operating temperature at sea level. Unless otherwise noted, engine is
idling when specification requires engine running. Ensure transmission
shift selector is in Neutral or Park (as applicable). If DVOM displays\
measurement that is not within specification, see G - TESTS W/CODES
article.
PCM LOCATION TABLE
\
\
\
\
\
\
Application Location
Eclipse 2.0L Non-Turbo ............ In Front of Left Front
Strut Tower
Mirage & Montero Sport .............. Behind Right Side Of
Instrument Panel (Glove Box)
Montero ........................... Right Front Kick Panel
All Others ......................... Behind Center Console
\
\
\
\
\
\
Fig. 1: Identifying PCM Terminals (Diamante)
Courtesy of Mitsubishi Motor Sales of America
Page 895 of 1501
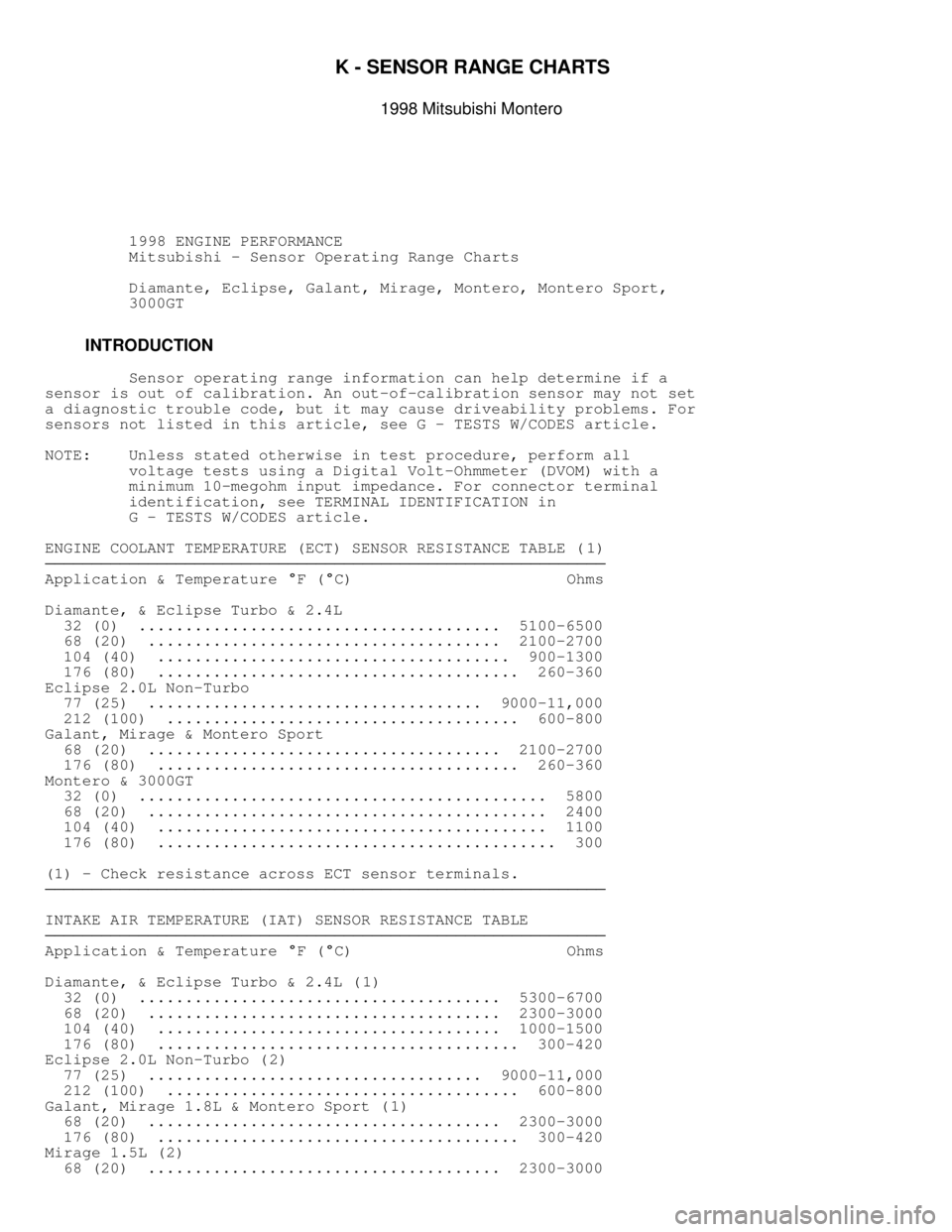
K - SENSOR RANGE CHARTS
1998 Mitsubishi Montero
1998 ENGINE PERFORMANCE
Mitsubishi - Sensor Operating Range Charts
Diamante, Eclipse, Galant, Mirage, Montero, Montero Sport,
3000GT
INTRODUCTION
Sensor operating range information can help determine if a
sensor is out of calibration. An out-of-calibration sensor may not set
a diagnostic trouble code, but it may cause driveability problems. For
sensors not listed in this article, see G - TESTS W/CODES article.
NOTE: Unless stated otherwise in test procedure, perform all
voltage tests using a Digital Volt-Ohmmeter (DVOM) with a
minimum 10-megohm input impedance. For connector terminal
identification, see TERMINAL IDENTIFICATION in
G - TESTS W/CODES article.
ENGINE COOLANT TEMPERATURE (ECT) SENSOR RESISTANCE TABLE ( 1)
\
\
\
\
\
\
Application & Temperature F (C) Ohms
Diamante, & Eclipse Turbo & 2.4L
32 (0) ....................................... 5100-6500
68 (20) ...................................... 2100-2700
104 (40) ...................................... 900-1300
176 (80) ....................................... 260-360
Eclipse 2.0L Non-Turbo
77 (25) .................................... 9000-11,000
212 (100) ...................................... 600-800
Galant, Mirage & Montero Sport
68 (20) ...................................... 2100-2700
176 (80) ....................................... 260-360
Montero & 3000GT
32 (0) ............................................ 5800
68 (20) ........................................... 2400
104 (40) .......................................... 1100
176 (80) ........................................... 300
( 1) - Check resistance across ECT sensor terminals.
\
\
\
\
\
\
INTAKE AIR TEMPERATURE (IAT) SENSOR RESISTANCE TABLE \
\
\
\
\
\
Application & Temperature F (C) Ohms
Diamante, & Eclipse Turbo & 2.4L ( 1)
32 (0) ....................................... 5300-6700
68 (20) ...................................... 2300-3000
104 (40) ..................................... 1000-1500
176 (80) ....................................... 300-420
Eclipse 2.0L Non-Turbo ( 2)
77 (25) .................................... 9000-11,000
212 (100) ...................................... 600-800
Galant, Mirage 1.8L & Montero Sport ( 1)
68 (20) ...................................... 2300-3000
176 (80) ....................................... 300-420
Mirage 1.5L ( 2)
68 (20) ...................................... 2300-3000
Page 961 of 1501
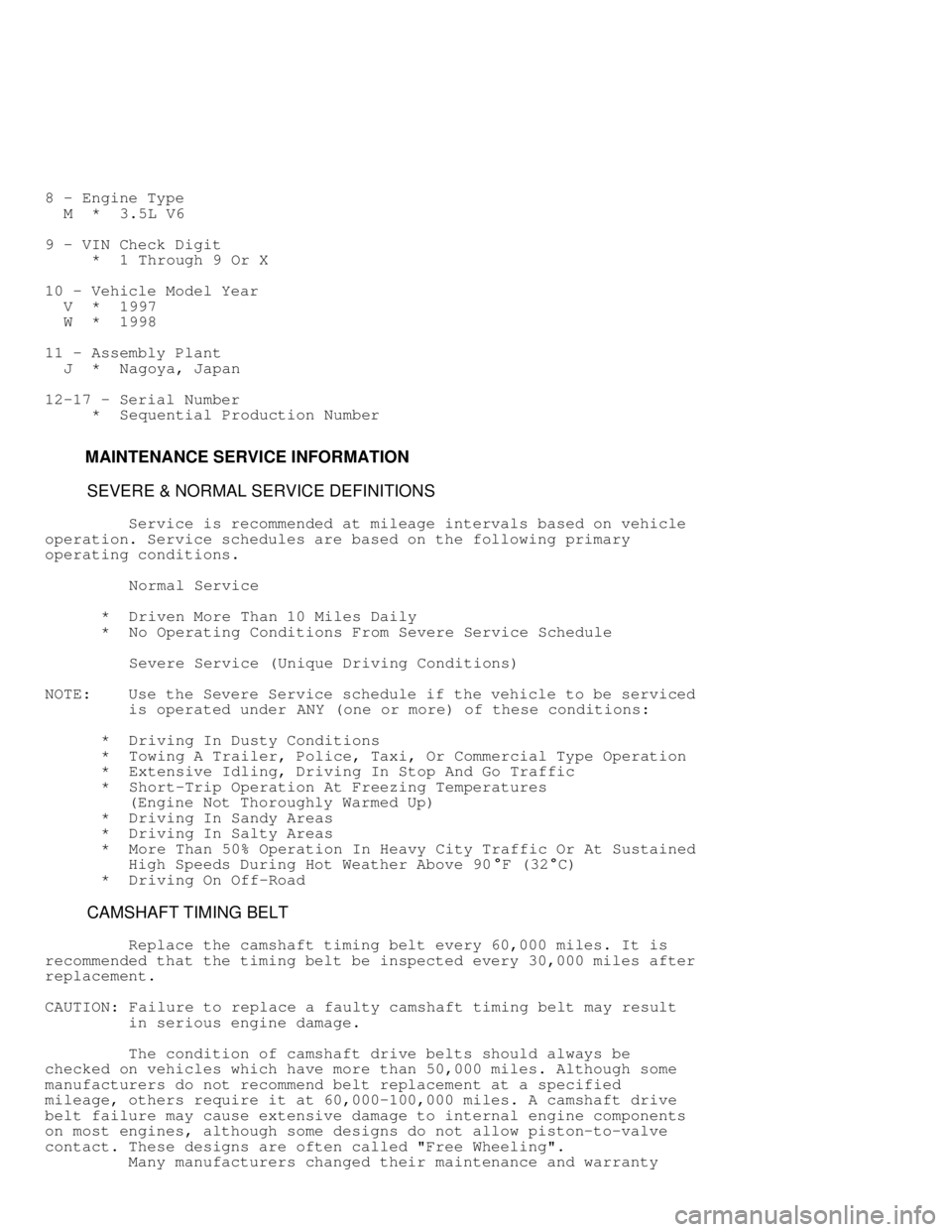
8 - Engine Type
M * 3.5L V6
9 - VIN Check Digit
* 1 Through 9 Or X
10 - Vehicle Model Year
V * 1997
W * 1998
11 - Assembly Plant
J * Nagoya, Japan
12-17 - Serial Number
* Sequential Production Number
MAINTENANCE SERVICE INFORMATION
SEVERE & NORMAL SERVICE DEFINITIONS
Service is recommended at mileage intervals based on vehicle
operation. Service schedules are based on the following primary
operating conditions.
Normal Service
* Driven More Than 10 Miles Daily
* No Operating Conditions From Severe Service Schedule
Severe Service (Unique Driving Conditions)
NOTE: Use the Severe Service schedule if the vehicle to be serviced
is operated under ANY (one or more) of these conditions:
* Driving In Dusty Conditions
* Towing A Trailer, Police, Taxi, Or Commercial Type Operation
* Extensive Idling, Driving In Stop And Go Traffic
* Short-Trip Operation At Freezing Temperatures
(Engine Not Thoroughly Warmed Up)
* Driving In Sandy Areas
* Driving In Salty Areas
* More Than 50% Operation In Heavy City Traffic Or At Sustained
High Speeds During Hot Weather Above 90
\bF (32\bC)
* Driving On Off-Road
CAMSHAFT TIMING BELT
Replace the camshaft timing belt every 60,000 miles. It is
recommended that the timing belt be inspected every 30,000 miles after
replacement.
CAUTION: Failure to replace a faulty camshaft timing belt may result
in serious engine damage.
The condition of camshaft drive belts should always be
checked on vehicles which have more than 50,000 miles. Although some
manufacturers do not recommend belt replacement at a specified
mileage, others require it at 60,000-100,000 miles. A camshaft drive
belt failure may cause extensive damage to internal engine components
on most engines, although some designs do not allow piston-to-valve
contact. These designs are often called "Free Wheeling".
Many manufacturers changed their maintenance and warranty
Page 967 of 1501
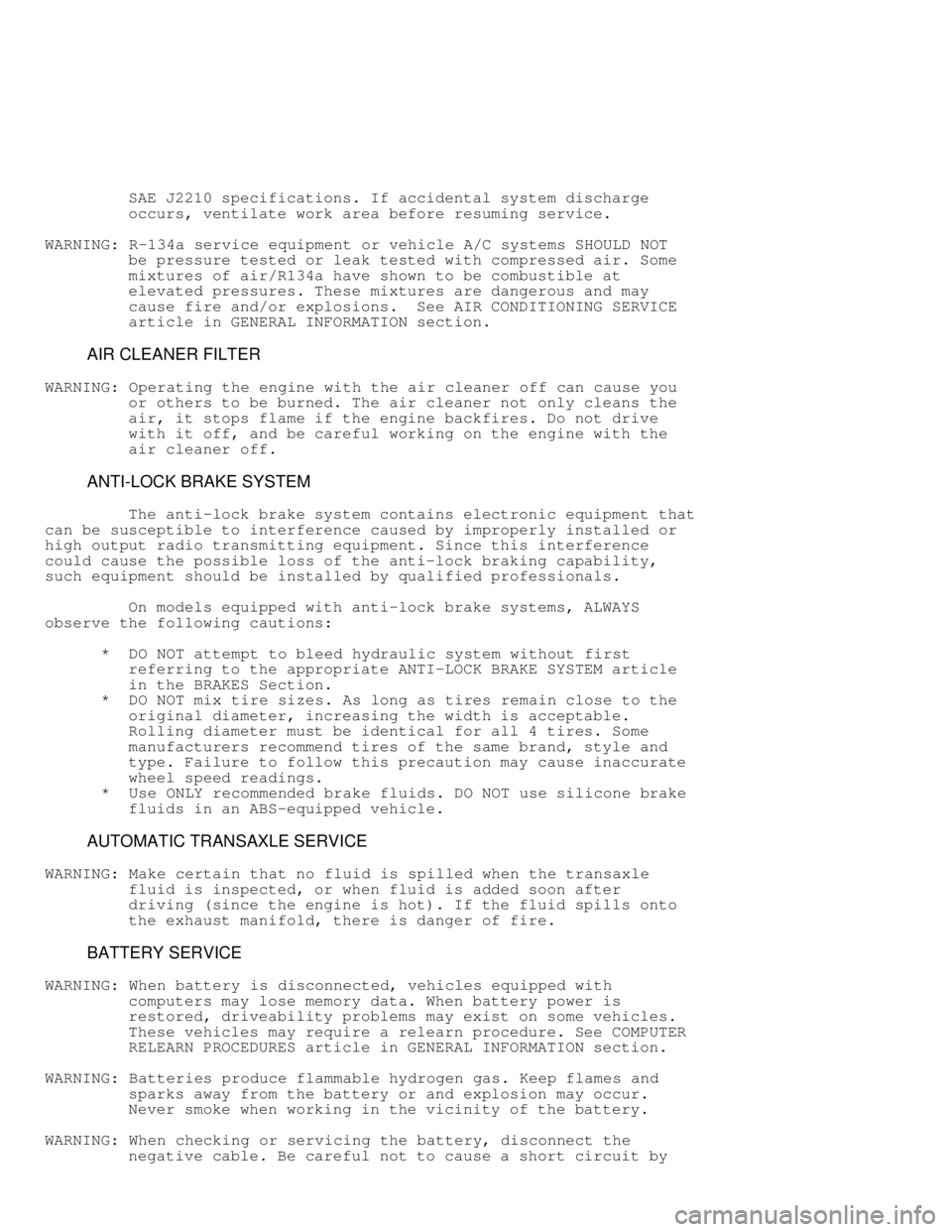
SAE J2210 specifications. If accidental system discharge
occurs, ventilate work area before resuming service.
WARNING: R-134a service equipment or vehicle A/C systems SHOULD NOT
be pressure tested or leak tested with compressed air. Some
mixtures of air/R134a have shown to be combustible at
elevated pressures. These mixtures are dangerous and may
cause fire and/or explosions. See AIR CONDITIONING SERVICE
article in GENERAL INFORMATION section.
AIR CLEANER FILTER
WARNING: Operating the engine with the air cleaner off can cause you
or others to be burned. The air cleaner not only cleans the
air, it stops flame if the engine backfires. Do not drive
with it off, and be careful working on the engine with the
air cleaner off.
ANTI-LOCK BRAKE SYSTEM
The anti-lock brake system contains electronic equipment that
can be susceptible to interference caused by improperly installed or
high output radio transmitting equipment. Since this interference
could cause the possible loss of the anti-lock braking capability,
such equipment should be installed by qualified professionals.
On models equipped with anti-lock brake systems, ALWAYS
observe the following cautions:
* DO NOT attempt to bleed hydraulic system without first
referring to the appropriate ANTI-LOCK BRAKE SYSTEM article
in the BRAKES Section.
* DO NOT mix tire sizes. As long as tires remain close to the
original diameter, increasing the width is acceptable.
Rolling diameter must be identical for all 4 tires. Some
manufacturers recommend tires of the same brand, style and
type. Failure to follow this precaution may cause inaccurate
wheel speed readings.
* Use ONLY recommended brake fluids. DO NOT use silicone brake
fluids in an ABS-equipped vehicle.
AUTOMATIC TRANSAXLE SERVICE
WARNING: Make certain that no fluid is spilled when the transaxle
fluid is inspected, or when fluid is added soon after
driving (since the engine is hot). If the fluid spills onto
the exhaust manifold, there is danger of fire.
BATTERY SERVICE
WARNING: When battery is disconnected, vehicles equipped with
computers may lose memory data. When battery power is
restored, driveability problems may exist on some vehicles.
These vehicles may require a relearn procedure. See COMPUTER
RELEARN PROCEDURES article in GENERAL INFORMATION section.
WARNING: Batteries produce flammable hydrogen gas. Keep flames and
sparks away from the battery or and explosion may occur.
Never smoke when working in the vicinity of the battery.
WARNING: When checking or servicing the battery, disconnect the
negative cable. Be careful not to cause a short circuit by
Page 998 of 1501
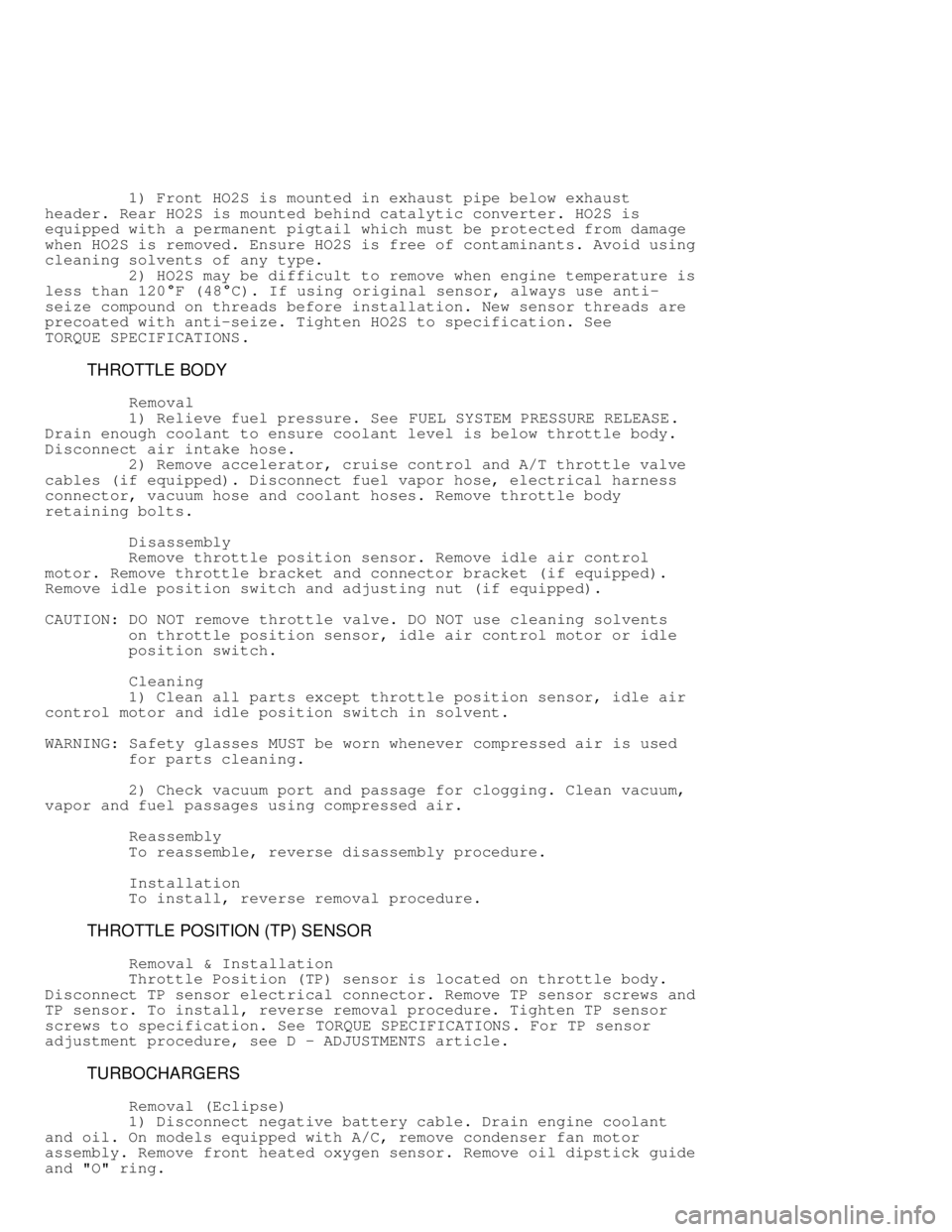
1) Front HO2S is mounted in exhaust pipe below exhaust
header. Rear HO2S is mounted behind catalytic converter. HO2S is
equipped with a permanent pigtail which must be protected from damage
when HO2S is removed. Ensure HO2S is free of contaminants. Avoid using
cleaning solvents of any type.
2) HO2S may be difficult to remove when engine temperature is
less than 120
F (48 C). If using original sensor, always use anti-
seize compound on threads before installation. New sensor threads are
precoated with anti-seize. Tighten HO2S to specification. See
TORQUE SPECIFICATIONS .
THROTTLE BODY
Removal
1) Relieve fuel pressure. See FUEL SYSTEM PRESSURE RELEASE.
Drain enough coolant to ensure coolant level is below throttle body.
Disconnect air intake hose.
2) Remove accelerator, cruise control and A/T throttle valve
cables (if equipped). Disconnect fuel vapor hose, electrical harness
connector, vacuum hose and coolant hoses. Remove throttle body
retaining bolts.
Disassembly
Remove throttle position sensor. Remove idle air control
motor. Remove throttle bracket and connector bracket (if equipped).
Remove idle position switch and adjusting nut (if equipped).
CAUTION: DO NOT remove throttle valve. DO NOT use cleaning solvents
on throttle position sensor, idle air control motor or idle
position switch.
Cleaning
1) Clean all parts except throttle position sensor, idle air
control motor and idle position switch in solvent.
WARNING: Safety glasses MUST be worn whenever compressed air is used
for parts cleaning.
2) Check vacuum port and passage for clogging. Clean vacuum,
vapor and fuel passages using compressed air.
Reassembly
To reassemble, reverse disassembly procedure.
Installation
To install, reverse removal procedure.
THROTTLE POSITION (TP) SENSOR
Removal & Installation
Throttle Position (TP) sensor is located on throttle body.
Disconnect TP sensor electrical connector. Remove TP sensor screws and
TP sensor. To install, reverse removal procedure. Tighten TP sensor
screws to specification. See TORQUE SPECIFICATIONS. For TP sensor
adjustment procedure, see D - ADJUSTMENTS article.
TURBOCHARGERS
Removal (Eclipse)
1) Disconnect negative battery cable. Drain engine coolant
and oil. On models equipped with A/C, remove condenser fan motor
assembly. Remove front heated oxygen sensor. Remove oil dipstick guide
and "O" ring.