stop start MITSUBISHI MONTERO 1998 User Guide
[x] Cancel search | Manufacturer: MITSUBISHI, Model Year: 1998, Model line: MONTERO, Model: MITSUBISHI MONTERO 1998Pages: 1501, PDF Size: 25.81 MB
Page 371 of 1501
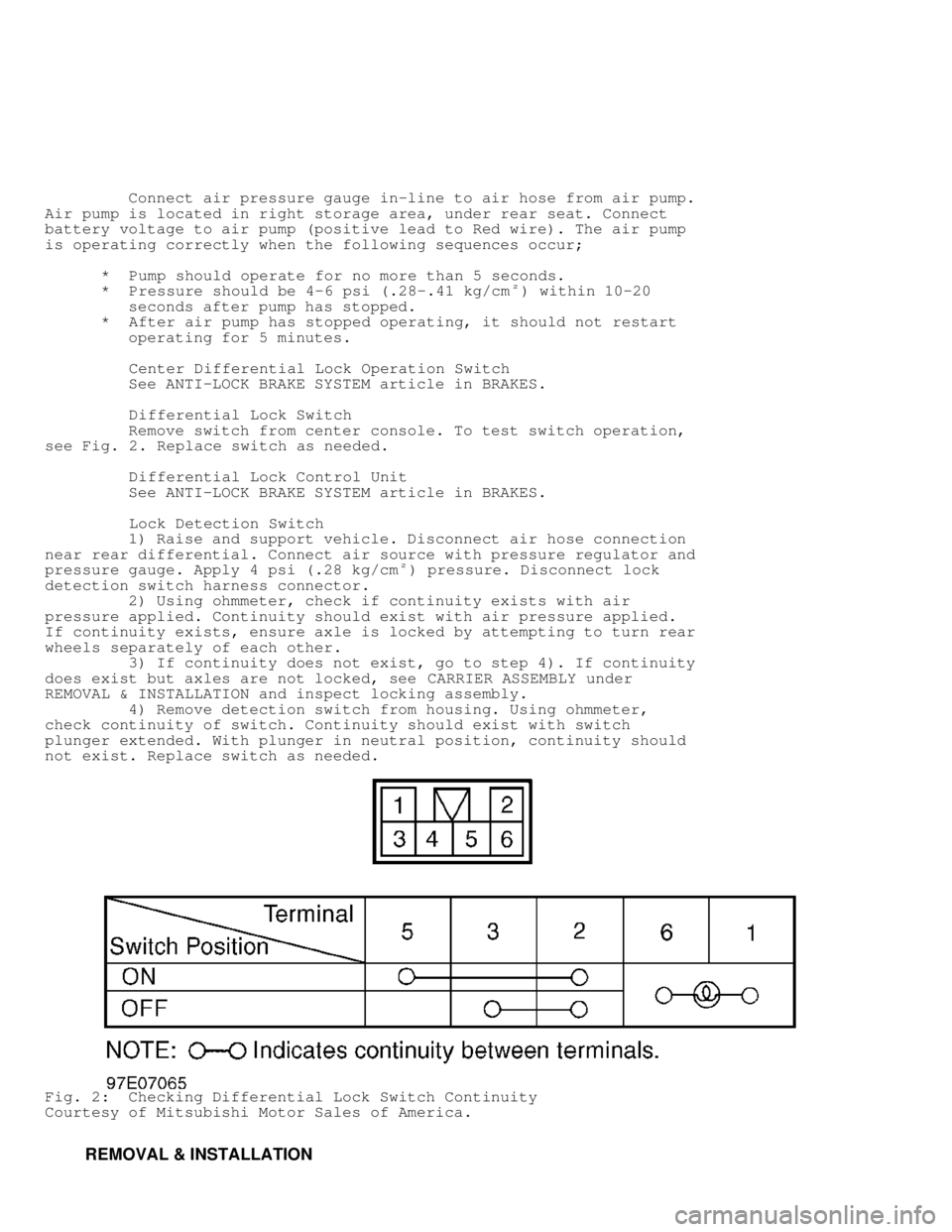
Connect air pressure gauge in-line to air hose from air pump.
Air pump is located in right storage area, under rear seat. Connect
battery voltage to air pump (positive lead to Red wire). The air pump
is operating correctly when the following sequences occur;
* Pump should operate for no more than 5 seconds.
* Pressure should be 4-6 psi (.28-.41 kg/cm
) within 10-20
seconds after pump has stopped.
* After air pump has stopped operating, it should not restart
operating for 5 minutes.
Center Differential Lock Operation Switch
See ANTI-LOCK BRAKE SYSTEM article in BRAKES.
Differential Lock Switch
Remove switch from center console. To test switch operation,
see Fig. 2 . Replace switch as needed.
Differential Lock Control Unit
See ANTI-LOCK BRAKE SYSTEM article in BRAKES.
Lock Detection Switch
1) Raise and support vehicle. Disconnect air hose connection
near rear differential. Connect air source with pressure regulator and
pressure gauge. Apply 4 psi (.28 kg/cm
) pressure. Disconnect lock
detection switch harness connector.
2) Using ohmmeter, check if continuity exists with air
pressure applied. Continuity should exist with air pressure applied.
If continuity exists, ensure axle is locked by attempting to turn rear
wheels separately of each other.
3) If continuity does not exist, go to step 4). If continuity\
does exist but axles are not locked, see CARRIER ASSEMBLY under
REMOVAL & INSTALLATION and inspect locking assembly.
4) Remove detection switch from housing. Using ohmmeter,
check continuity of switch. Continuity should exist with switch
plunger extended. With plunger in neutral position, continuity should
not exist. Replace switch as needed.
Fig. 2: Checking Differential Lock Switch Continuity
Courtesy of Mitsubishi Motor Sales of America.
REMOVAL & INSTALLATION
Page 390 of 1501
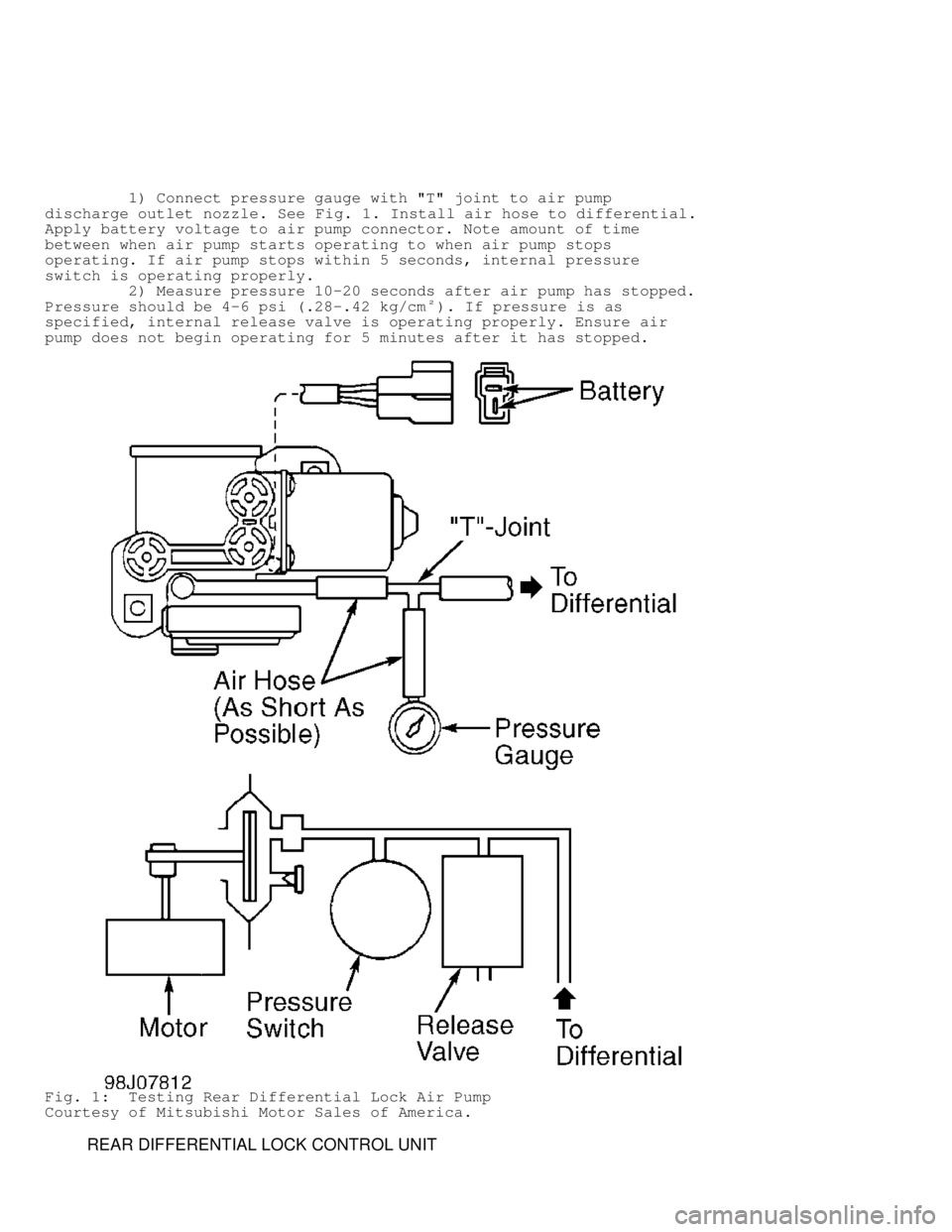
1) Connect pressure gauge with "T" joint to air pump
discharge outlet nozzle. See Fig. 1. Install air hose to differential.
Apply battery voltage to air pump connector. Note amount of time
between when air pump starts operating to when air pump stops
operating. If air pump stops within 5 seconds, internal pressure
switch is operating properly.
2) Measure pressure 10-20 seconds after air pump has stopped.
Pressure should be 4-6 psi (.28-.42 kg/cm
). If pressure is as
specified, internal release valve is operating properly. Ensure air
pump does not begin operating for 5 minutes after it has stopped.
Fig. 1: Testing Rear Differential Lock Air Pump
Courtesy of Mitsubishi Motor Sales of America.
REAR DIFFERENTIAL LOCK CONTROL UNIT
Page 587 of 1501
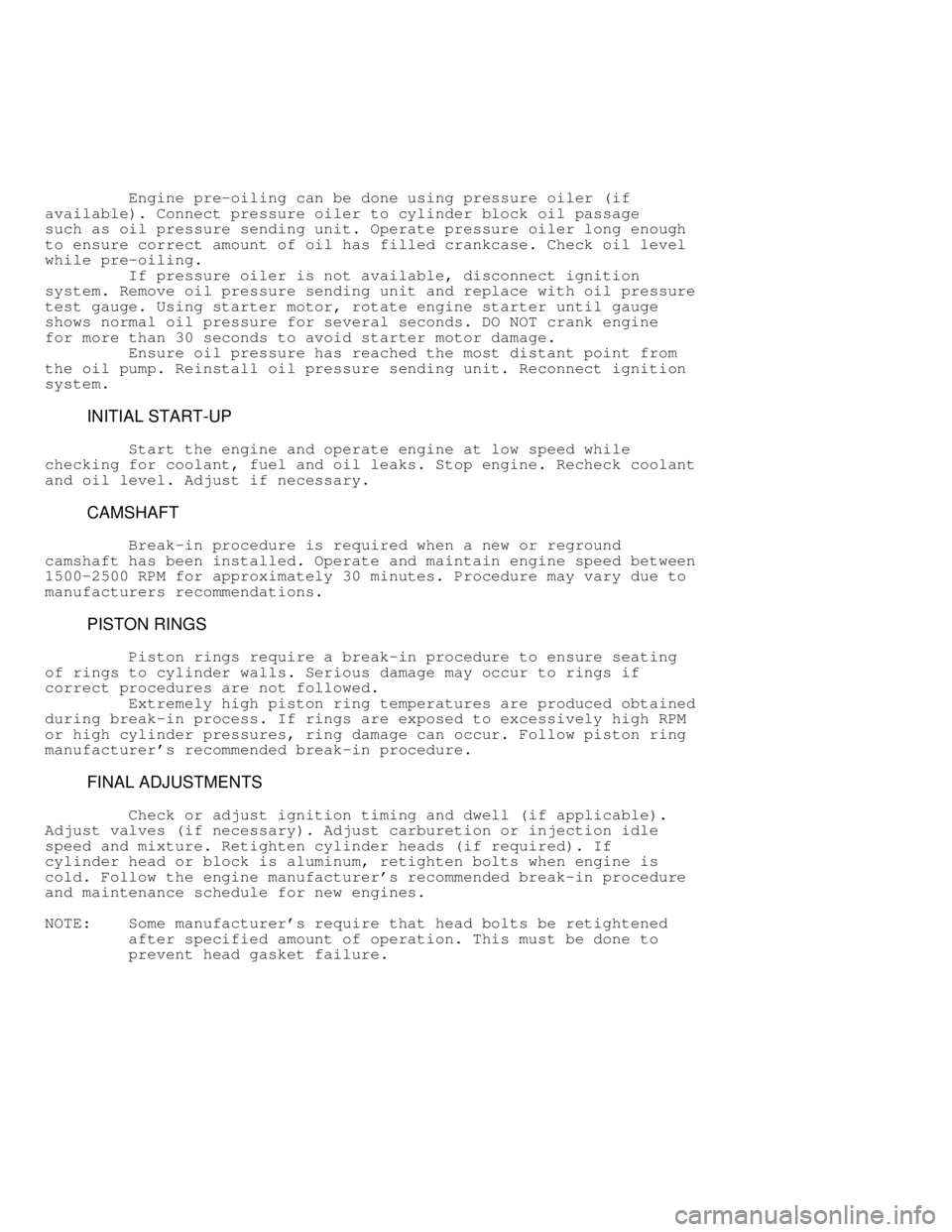
Engine pre-oiling can be done using pressure oiler (if
available). Connect pressure oiler to cylinder block oil passage
such as oil pressure sending unit. Operate pressure oiler long enough
to ensure correct amount of oil has filled crankcase. Check oil level
while pre-oiling.
If pressure oiler is not available, disconnect ignition
system. Remove oil pressure sending unit and replace with oil pressure
test gauge. Using starter motor, rotate engine starter until gauge
shows normal oil pressure for several seconds. DO NOT crank engine
for more than 30 seconds to avoid starter motor damage.
Ensure oil pressure has reached the most distant point from
the oil pump. Reinstall oil pressure sending unit. Reconnect ignition
system.
INITIAL START-UP
Start the engine and operate engine at low speed while
checking for coolant, fuel and oil leaks. Stop engine. Recheck coolant
and oil level. Adjust if necessary.
CAMSHAFT
Break-in procedure is required when a new or reground
camshaft has been installed. Operate and maintain engine speed between
1500-2500 RPM for approximately 30 minutes. Procedure may vary due to
manufacturers recommendations.
PISTON RINGS
Piston rings require a break-in procedure to ensure seating
of rings to cylinder walls. Serious damage may occur to rings if
correct procedures are not followed.
Extremely high piston ring temperatures are produced obtained
during break-in process. If rings are exposed to excessively high RPM
or high cylinder pressures, ring damage can occur. Follow piston ring
manufacturer's recommended break-in procedure.
FINAL ADJUSTMENTS
Check or adjust ignition timing and dwell (if applicable).
Adjust valves (if necessary). Adjust carburetion or injection idle
speed and mixture. Retighten cylinder heads (if required). If
cylinder head or block is aluminum, retighten bolts when engine is
cold. Follow the engine manufacturer's recommended break-in procedure
and maintenance schedule for new engines.
NOTE: Some manufacturer's require that head bolts be retightened
after specified amount of operation. This must be done to
prevent head gasket failure.
Page 703 of 1501
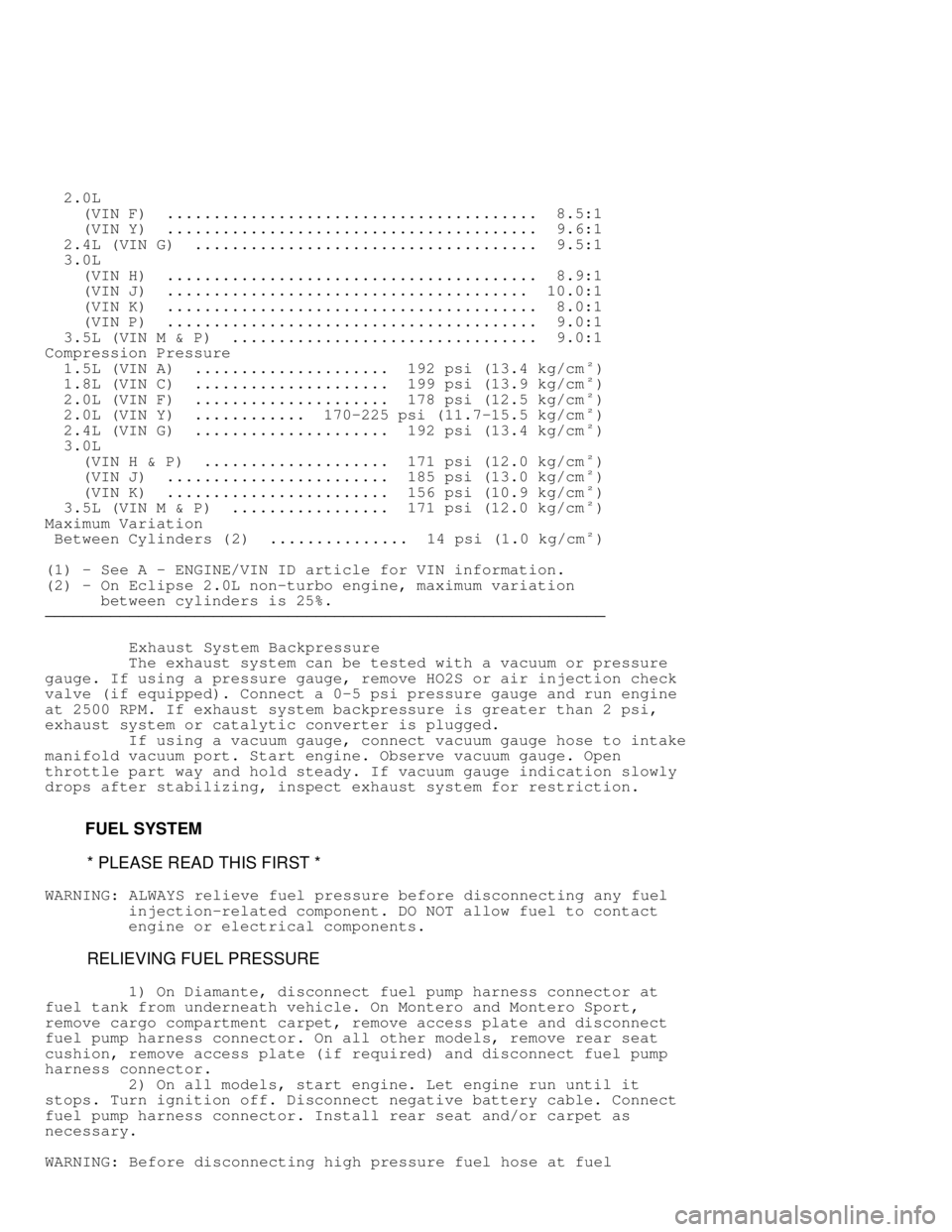
2.0L
(VIN F) ........................................ 8.5:1
(VIN Y) ........................................ 9.6:1
2.4L (VIN G) ..................................... 9.5:1
3.0L
(VIN H) ........................................ 8.9:1
(VIN J) ....................................... 10.0:1
(VIN K) ........................................ 8.0:1
(VIN P) ........................................ 9.0:1
3.5L (VIN M & P) ................................. 9.0:1
Compression Pressure
1.5L (VIN A) ..................... 192 psi (13.4 kg/cm
)
1.8L (VIN C) ..................... 199 psi (13.9 kg/cm)
2.0L (VIN F) ..................... 178 psi (12.5 kg/cm)
2.0L (VIN Y) ............ 170-225 psi (11.7-15.5 kg/cm)
2.4L (VIN G) ..................... 192 psi (13.4 kg/cm)
3.0L
(VIN H & P) .................... 171 psi (12.0 kg/cm
)
(VIN J) ........................ 185 psi (13.0 kg/cm)
(VIN K) ........................ 156 psi (10.9 kg/cm)
3.5L (VIN M & P) ................. 171 psi (12.0 kg/cm)
Maximum Variation
Between Cylinders ( 2) ............... 14 psi (1.0 kg/cm
)
( 1) - See A - ENGINE/VIN ID article for VIN information.
( 2) - On Eclipse 2.0L non-turbo engine, maximum variation
between cylinders is 25%.
\
\
\
\
\
\
Exhaust System Backpressure
The exhaust system can be tested with a vacuum or pressure
gauge. If using a pressure gauge, remove HO2S or air injection check
valve (if equipped). Connect a 0-5 psi pressure gauge and run engine
at 2500 RPM. If exhaust system backpressure is greater than 2 psi,
exhaust system or catalytic converter is plugged.
If using a vacuum gauge, connect vacuum gauge hose to intake
manifold vacuum port. Start engine. Observe vacuum gauge. Open
throttle part way and hold steady. If vacuum gauge indication slowly
drops after stabilizing, inspect exhaust system for restriction.
FUEL SYSTEM
* PLEASE READ THIS FIRST *
WARNING: ALWAYS relieve fuel pressure before disconnecting any fuel
injection-related component. DO NOT allow fuel to contact
engine or electrical components.
RELIEVING FUEL PRESSURE
1) On Diamante, disconnect fuel pump harness connector at
fuel tank from underneath vehicle. On Montero and Montero Sport,
remove cargo compartment carpet, remove access plate and disconnect
fuel pump harness connector. On all other models, remove rear seat
cushion, remove access plate (if required) and disconnect fuel pump
harness connector.
2) On all models, start engine. Let engine run until it
stops. Turn ignition off. Disconnect negative battery cable. Connect
fuel pump harness connector. Install rear seat and/or carpet as
necessary.
WARNING: Before disconnecting high pressure fuel hose at fuel
Page 705 of 1501
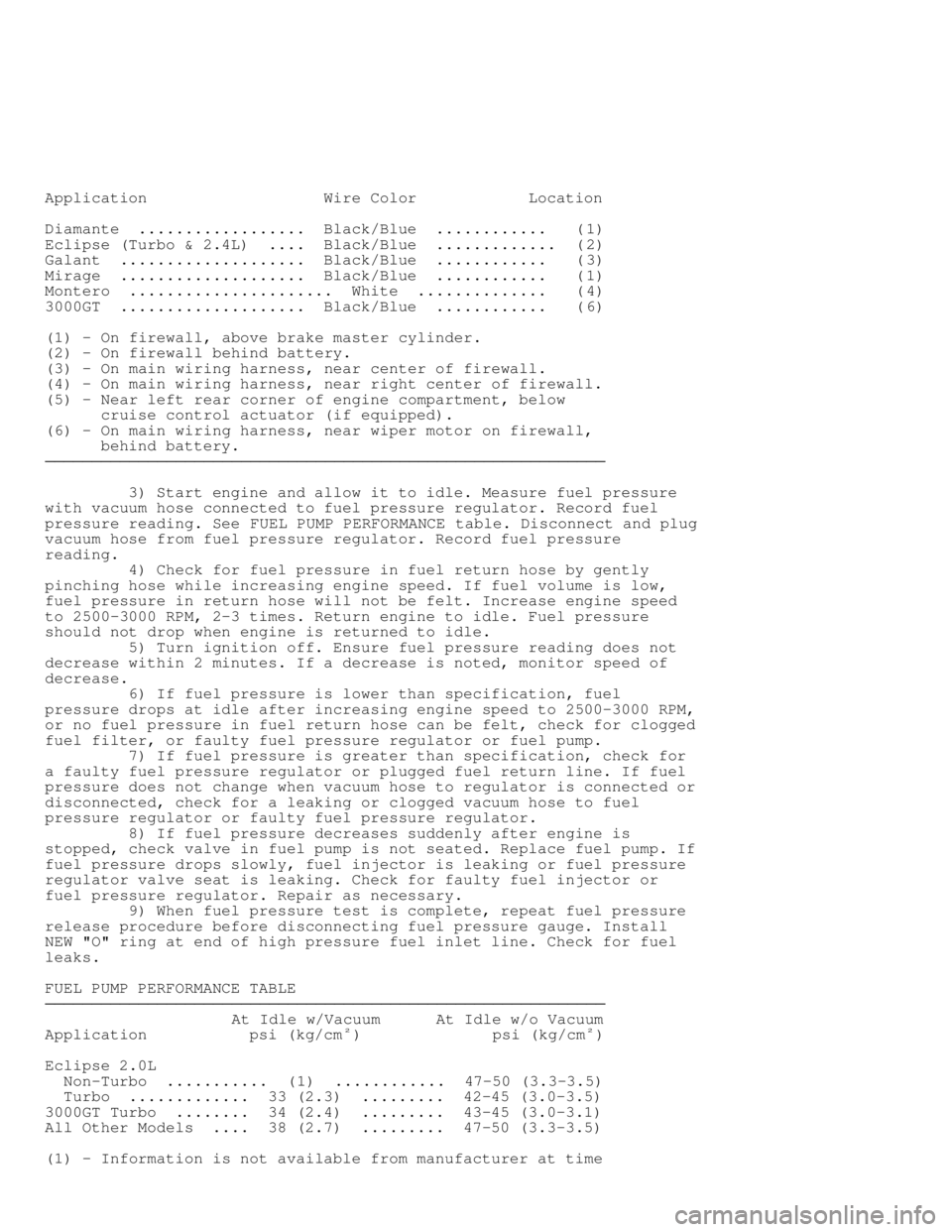
Application Wire Color Location
Diamante .................. Black/Blue ............ (1)
Eclipse (Turbo & 2.4L) .... Black/Blue ............. ( 2)
Galant .................... Black/Blue ............ ( 3)
Mirage .................... Black/Blue ............ ( 1)
Montero ...................... White .............. ( 4)
3000GT .................... Black/Blue ............ ( 6)
( 1) - On firewall, above brake master cylinder.
( 2) - On firewall behind battery.
( 3) - On main wiring harness, near center of firewall.
( 4) - On main wiring harness, near right center of firewall.
( 5) - Near left rear corner of engine compartment, below
cruise control actuator (if equipped).
( 6) - On main wiring harness, near wiper motor on firewall,
behind battery.
\
\
\
\
\
\
3) Start engine and allow it to idle. Measure fuel pressure
with vacuum hose connected to fuel pressure regulator. Record fuel
pressure reading. See FUEL PUMP PERFORMANCE table. Disconnect and plug
vacuum hose from fuel pressure regulator. Record fuel pressure
reading.
4) Check for fuel pressure in fuel return hose by gently
pinching hose while increasing engine speed. If fuel volume is low,
fuel pressure in return hose will not be felt. Increase engine speed
to 2500-3000 RPM, 2-3 times. Return engine to idle. Fuel pressure
should not drop when engine is returned to idle.
5) Turn ignition off. Ensure fuel pressure reading does not
decrease within 2 minutes. If a decrease is noted, monitor speed of
decrease.
6) If fuel pressure is lower than specification, fuel
pressure drops at idle after increasing engine speed to 2500-3000 RPM,
or no fuel pressure in fuel return hose can be felt, check for clogged
fuel filter, or faulty fuel pressure regulator or fuel pump.
7) If fuel pressure is greater than specification, check for
a faulty fuel pressure regulator or plugged fuel return line. If fuel
pressure does not change when vacuum hose to regulator is connected or
disconnected, check for a leaking or clogged vacuum hose to fuel
pressure regulator or faulty fuel pressure regulator.
8) If fuel pressure decreases suddenly after engine is
stopped, check valve in fuel pump is not seated. Replace fuel pump. If
fuel pressure drops slowly, fuel injector is leaking or fuel pressure
regulator valve seat is leaking. Check for faulty fuel injector or
fuel pressure regulator. Repair as necessary.
9) When fuel pressure test is complete, repeat fuel pressure
release procedure before disconnecting fuel pressure gauge. Install
NEW "O" ring at end of high pressure fuel inlet line. Check for fuel
leaks.
FUEL PUMP PERFORMANCE TABLE
\
\
\
\
\
\
At Idle w/Vacuum At Idle w/o Vacuum
Application psi (kg/cm) psi (kg/cm)
Eclipse 2.0L
Non-Turbo ........... ( 1) ............ 47-50 (3.3-3.5)
Turbo ............. 33 (2.3) ......... 42-45 (3.0-3.5)
3000GT Turbo ........ 34 (2.4) ......... 43-45 (3.0-3.1)
All Other Models .... 38 (2.7) ......... 47-50 (3.3-3.5)
( 1) - Information is not available from manufacturer at time
Page 815 of 1501
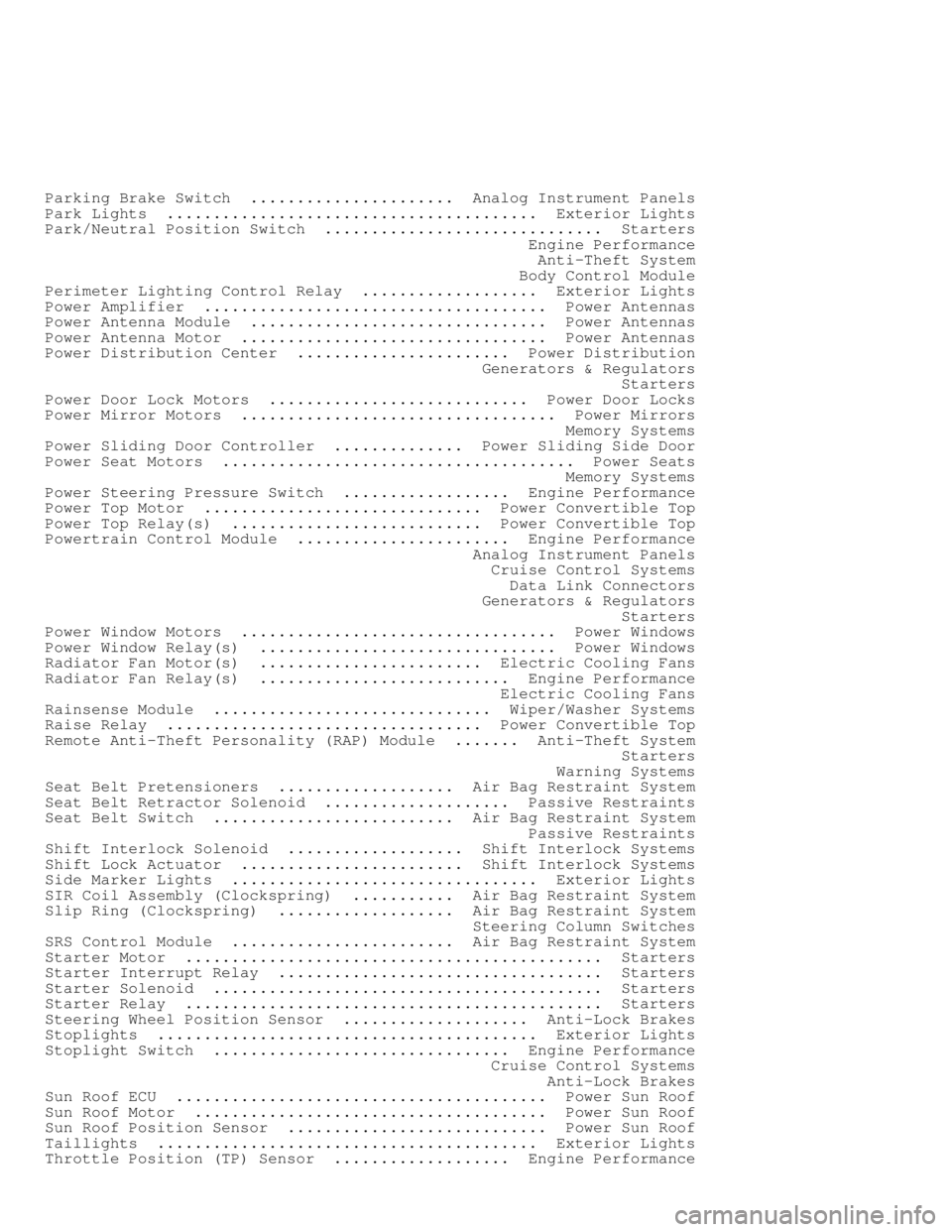
Parking Brake Switch ...................... Analog Instrument Panels
Park Lights ........................................ Exterior Lights
Park/Neutral Position Switch .............................. Starters
Engine Performance
Anti-Theft System
Body Control Module
Perimeter Lighting Control Relay ................... Exterior Lights
Power Amplifier ..................................... Power Antennas
Power Antenna Module ................................ Power Antennas
Power Antenna Motor ................................. Power Antennas
Power Distribution Center ....................... Power Distribution
Generators & Regulators
Starters
Power Door Lock Motors ............................ Power Door Locks
Power Mirror Motors .................................. Power Mirrors
Memory Systems
Power Sliding Door Controller .............. Power Sliding Side Door
Power Seat Motors ...................................... Power Seats
Memory Systems
Power Steering Pressure Switch .................. Engine Performance
Power Top Motor .............................. Power Convertible Top
Power Top Relay(s) ........................... Power Convertible Top\
Powertrain Control Module ....................... Engine Performance
Analog Instrument Panels
Cruise Control Systems
Data Link Connectors
Generators & Regulators
Starters
Power Window Motors .................................. Power Windows
Power Window Relay(s) ................................ Power Windows\
Radiator Fan Motor(s) ........................ Electric Cooling Fans\
Radiator Fan Relay(s) ........................... Engine Performance\
Electric Cooling Fans
Rainsense Module .............................. Wiper/Washer Systems
Raise Relay .................................. Power Convertible Top
Remote Anti-Theft Personality (RAP) Module ....... Anti-Theft System\
Starters
Warning Systems
Seat Belt Pretensioners ................... Air Bag Restraint System
Seat Belt Retractor Solenoid .................... Passive Restraints
Seat Belt Switch .......................... Air Bag Restraint System
Passive Restraints
Shift Interlock Solenoid ................... Shift Interlock Systems
Shift Lock Actuator ........................ Shift Interlock Systems
Side Marker Lights ................................. Exterior Lights
SIR Coil Assembly (Clockspring) ........... Air Bag Restraint System\
Slip Ring (Clockspring) ................... Air Bag Restraint System\
Steering Column Switches
SRS Control Module ........................ Air Bag Restraint System
Starter Motor ............................................. Starters
Starter Interrupt Relay ................................... Starters
Starter Solenoid .......................................... Starters
Starter Relay ............................................. Starters
Steering Wheel Position Sensor .................... Anti-Lock Brakes
Stoplights ......................................... Exterior Lights
Stoplight Switch ................................ Engine Performance
Cruise Control Systems
Anti-Lock Brakes
Sun Roof ECU ........................................ Power Sun Roof
Sun Roof Motor ...................................... Power Sun Roof
Sun Roof Position Sensor ............................ Power Sun Roof
Taillights ......................................... Exterior Lights
Throttle Position (TP) Sensor ................... Engine Performance\
Page 996 of 1501
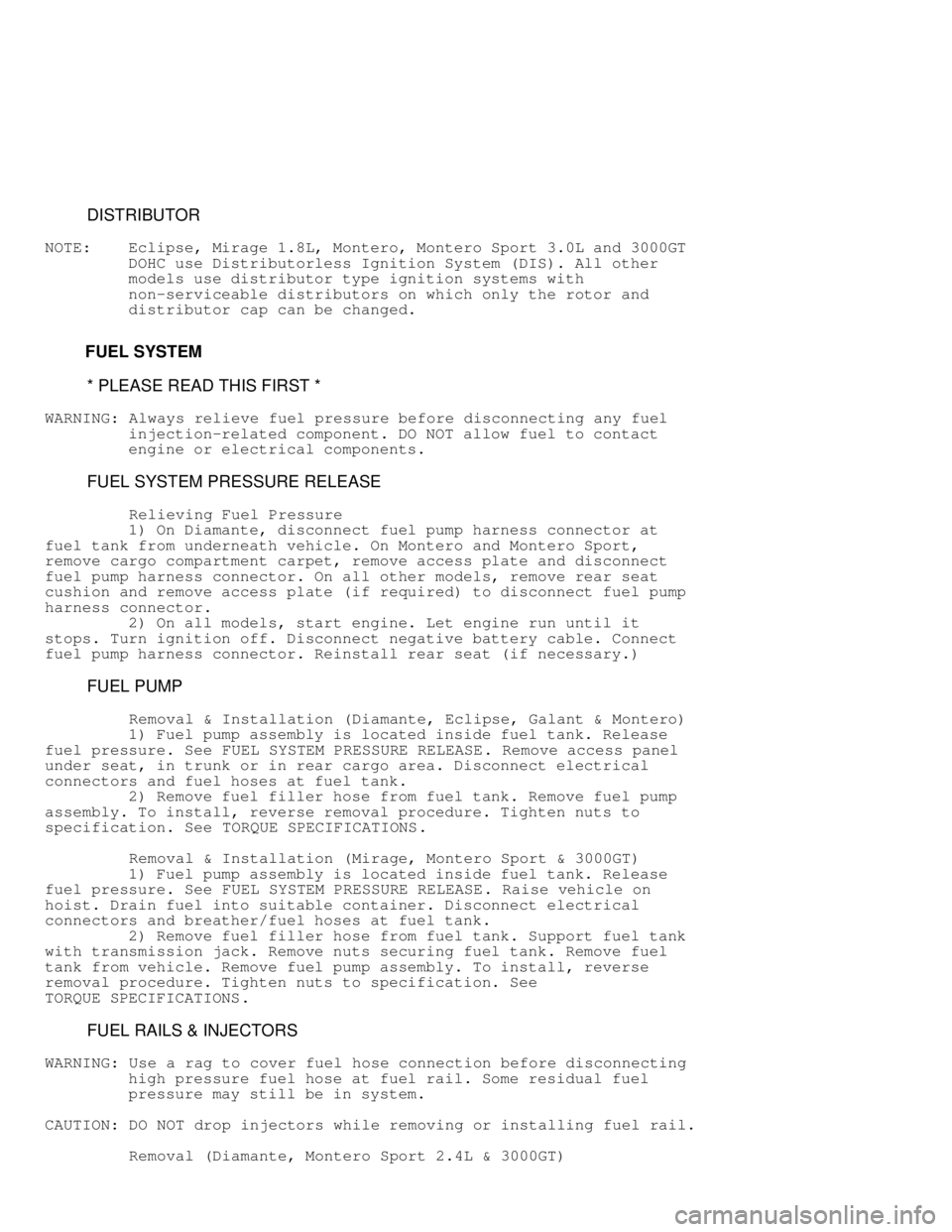
DISTRIBUTOR
NOTE: Eclipse, Mirage 1.8L, Montero, Montero Sport 3.0L and 3000GT
DOHC use Distributorless Ignition System (DIS). All other
models use distributor type ignition systems with
non-serviceable distributors on which only the rotor and
distributor cap can be changed.
FUEL SYSTEM
* PLEASE READ THIS FIRST *
WARNING: Always relieve fuel pressure before disconnecting any fuel
injection-related component. DO NOT allow fuel to contact
engine or electrical components.
FUEL SYSTEM PRESSURE RELEASE
Relieving Fuel Pressure
1) On Diamante, disconnect fuel pump harness connector at
fuel tank from underneath vehicle. On Montero and Montero Sport,
remove cargo compartment carpet, remove access plate and disconnect
fuel pump harness connector. On all other models, remove rear seat
cushion and remove access plate (if required) to disconnect fuel pump
harness connector.
2) On all models, start engine. Let engine run until it
stops. Turn ignition off. Disconnect negative battery cable. Connect
fuel pump harness connector. Reinstall rear seat (if necessary.)
FUEL PUMP
Removal & Installation (Diamante, Eclipse, Galant & Montero)
1) Fuel pump assembly is located inside fuel tank. Release
fuel pressure. See FUEL SYSTEM PRESSURE RELEASE . Remove access panel
under seat, in trunk or in rear cargo area. Disconnect electrical
connectors and fuel hoses at fuel tank.
2) Remove fuel filler hose from fuel tank. Remove fuel pump
assembly. To install, reverse removal procedure. Tighten nuts to
specification. See TORQUE SPECIFICATIONS .
Removal & Installation (Mirage, Montero Sport & 3000GT)
1) Fuel pump assembly is located inside fuel tank. Release
fuel pressure. See FUEL SYSTEM PRESSURE RELEASE . Raise vehicle on
hoist. Drain fuel into suitable container. Disconnect electrical
connectors and breather/fuel hoses at fuel tank.
2) Remove fuel filler hose from fuel tank. Support fuel tank
with transmission jack. Remove nuts securing fuel tank. Remove fuel
tank from vehicle. Remove fuel pump assembly. To install, reverse
removal procedure. Tighten nuts to specification. See
TORQUE SPECIFICATIONS .
FUEL RAILS & INJECTORS
WARNING: Use a rag to cover fuel hose connection before disconnecting
high pressure fuel hose at fuel rail. Some residual fuel
pressure may still be in system.
CAUTION: DO NOT drop injectors while removing or installing fuel rail.
Removal (Diamante, Montero Sport 2.4L & 3000GT)
Page 1003 of 1501
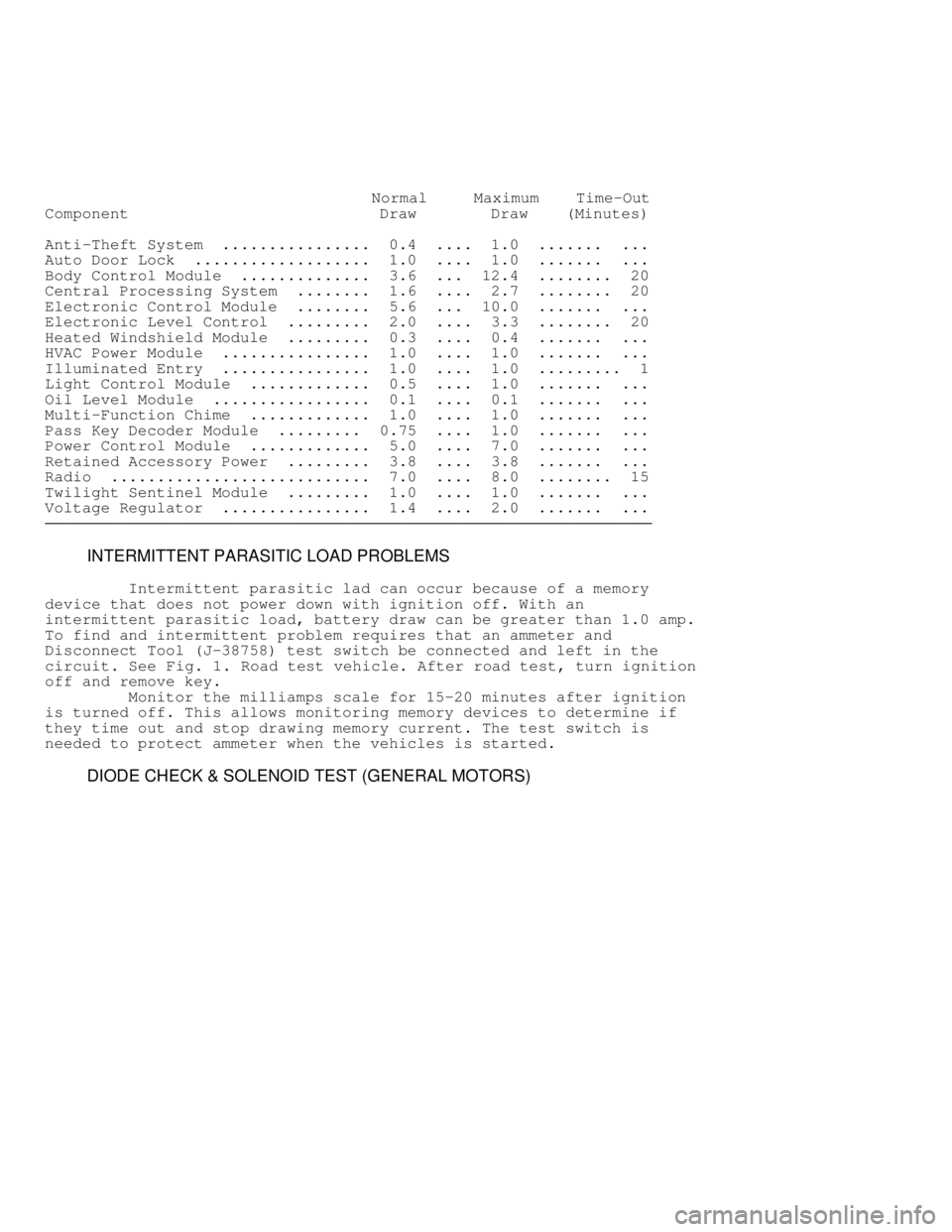
Normal Maximum Time-Out
Component Draw Draw (Minutes)
Anti-Theft System ................ 0.4 .... 1.0 ....... ...
Auto Door Lock ................... 1.0 .... 1.0 ....... ...
Body Control Module .............. 3.6 ... 12.4 ........ 20
Central Processing System ........ 1.6 .... 2.7 ........ 20
Electronic Control Module ........ 5.6 ... 10.0 ....... ...
Electronic Level Control ......... 2.0 .... 3.3 ........ 20
Heated Windshield Module ......... 0.3 .... 0.4 ....... ...
HVAC Power Module ................ 1.0 .... 1.0 ....... ...
Illuminated Entry ................ 1.0 .... 1.0 ......... 1
Light Control Module ............. 0.5 .... 1.0 ....... ...
Oil Level Module ................. 0.1 .... 0.1 ....... ...
Multi-Function Chime ............. 1.0 .... 1.0 ....... ...
Pass Key Decoder Module ......... 0.75 .... 1.0 ....... ...
Power Control Module ............. 5.0 .... 7.0 ....... ...
Retained Accessory Power ......... 3.8 .... 3.8 ....... ...
Radio ............................ 7.0 .... 8.0 ........ 15
Twilight Sentinel Module ......... 1.0 .... 1.0 ....... ...
Voltage Regulator ................ 1.4 .... 2.0 ....... ...
\
\
\
\
\
\
\
INTERMITTENT PARASITIC LOAD PROBLEMS
Intermittent parasitic lad can occur because of a memory
device that does not power down with ignition off. With an
intermittent parasitic load, battery draw can be greater than 1.0 amp.
To find and intermittent problem requires that an ammeter and
Disconnect Tool (J-38758) test switch be connected and left in the
circuit. See Fig. 1. Road test vehicle. After road test, turn ignition
off and remove key.
Monitor the milliamps scale for 15-20 minutes after ignition
is turned off. This allows monitoring memory devices to determine if
they time out and stop drawing memory current. The test switch is
needed to protect ammeter when the vehicles is started.
DIODE CHECK & SOLENOID TEST (GENERAL MOTORS)
Page 1081 of 1501
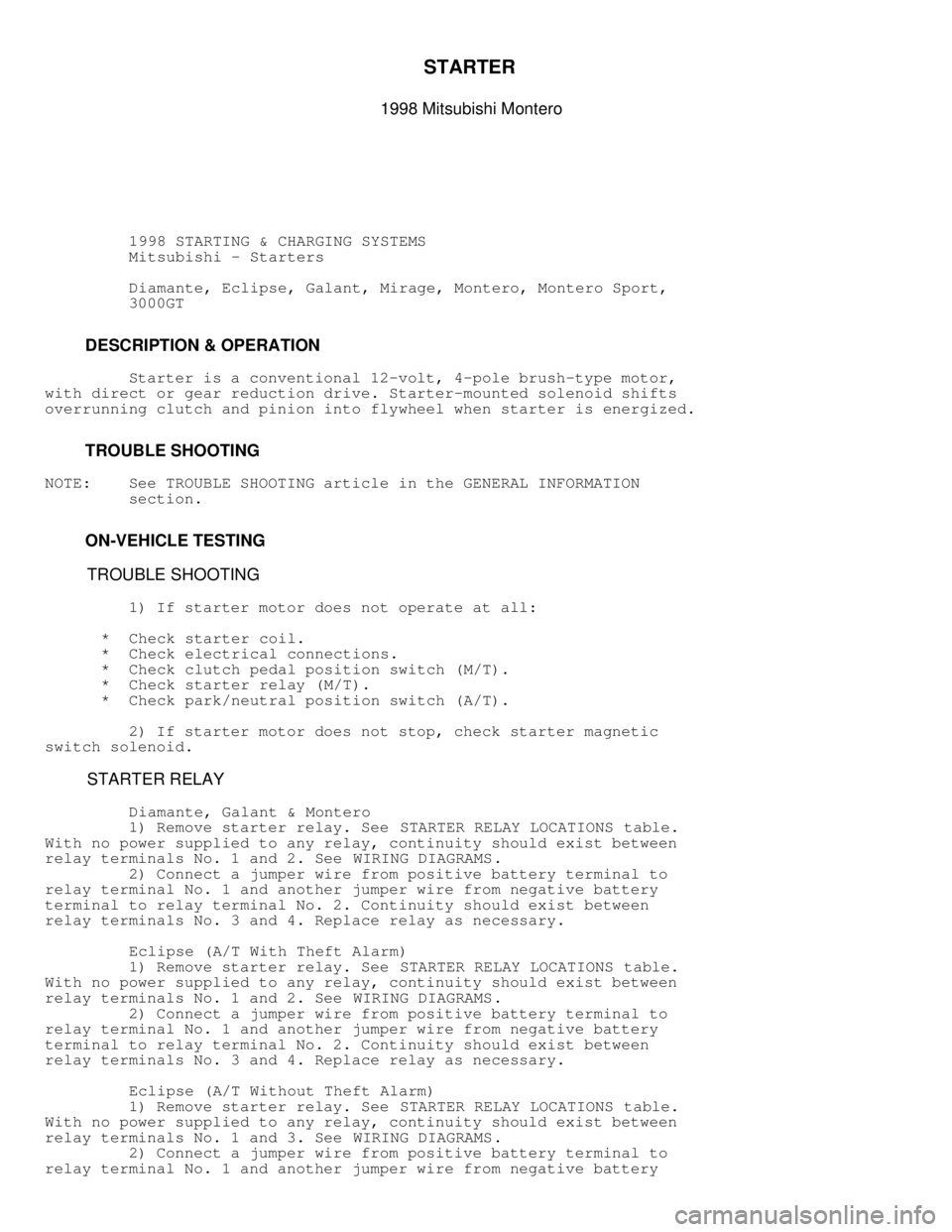
STARTER
1998 Mitsubishi Montero
1998 STARTING & CHARGING SYSTEMS
Mitsubishi - Starters
Diamante, Eclipse, Galant, Mirage, Montero, Montero Sport,
3000GT
DESCRIPTION & OPERATION
Starter is a conventional 12-volt, 4-pole brush-type motor,
with direct or gear reduction drive. Starter-mounted solenoid shifts
overrunning clutch and pinion into flywheel when starter is energized.
TROUBLE SHOOTING
NOTE: See TROUBLE SHOOTING article in the GENERAL INFORMATION
section.
ON-VEHICLE TESTING
TROUBLE SHOOTING
1) If starter motor does not operate at all:
* Check starter coil.
* Check electrical connections.
* Check clutch pedal position switch (M/T).
* Check starter relay (M/T).
* Check park/neutral position switch (A/T).
2) If starter motor does not stop, check starter magnetic
switch solenoid.
STARTER RELAY
Diamante, Galant & Montero
1) Remove starter relay. See STARTER RELAY LOCATIONS table.
With no power supplied to any relay, continuity should exist between
relay terminals No. 1 and 2. See WIRING DIAGRAMS.
2) Connect a jumper wire from positive battery terminal to
relay terminal No. 1 and another jumper wire from negative battery
terminal to relay terminal No. 2. Continuity should exist between
relay terminals No. 3 and 4. Replace relay as necessary.
Eclipse (A/T With Theft Alarm)
1) Remove starter relay. See STARTER RELAY LOCATIONS table.
With no power supplied to any relay, continuity should exist between
relay terminals No. 1 and 2. See WIRING DIAGRAMS.
2) Connect a jumper wire from positive battery terminal to
relay terminal No. 1 and another jumper wire from negative battery
terminal to relay terminal No. 2. Continuity should exist between
relay terminals No. 3 and 4. Replace relay as necessary.
Eclipse (A/T Without Theft Alarm)
1) Remove starter relay. See STARTER RELAY LOCATIONS table.
With no power supplied to any relay, continuity should exist between
relay terminals No. 1 and 3. See WIRING DIAGRAMS.
2) Connect a jumper wire from positive battery terminal to
relay terminal No. 1 and another jumper wire from negative battery
Page 1085 of 1501
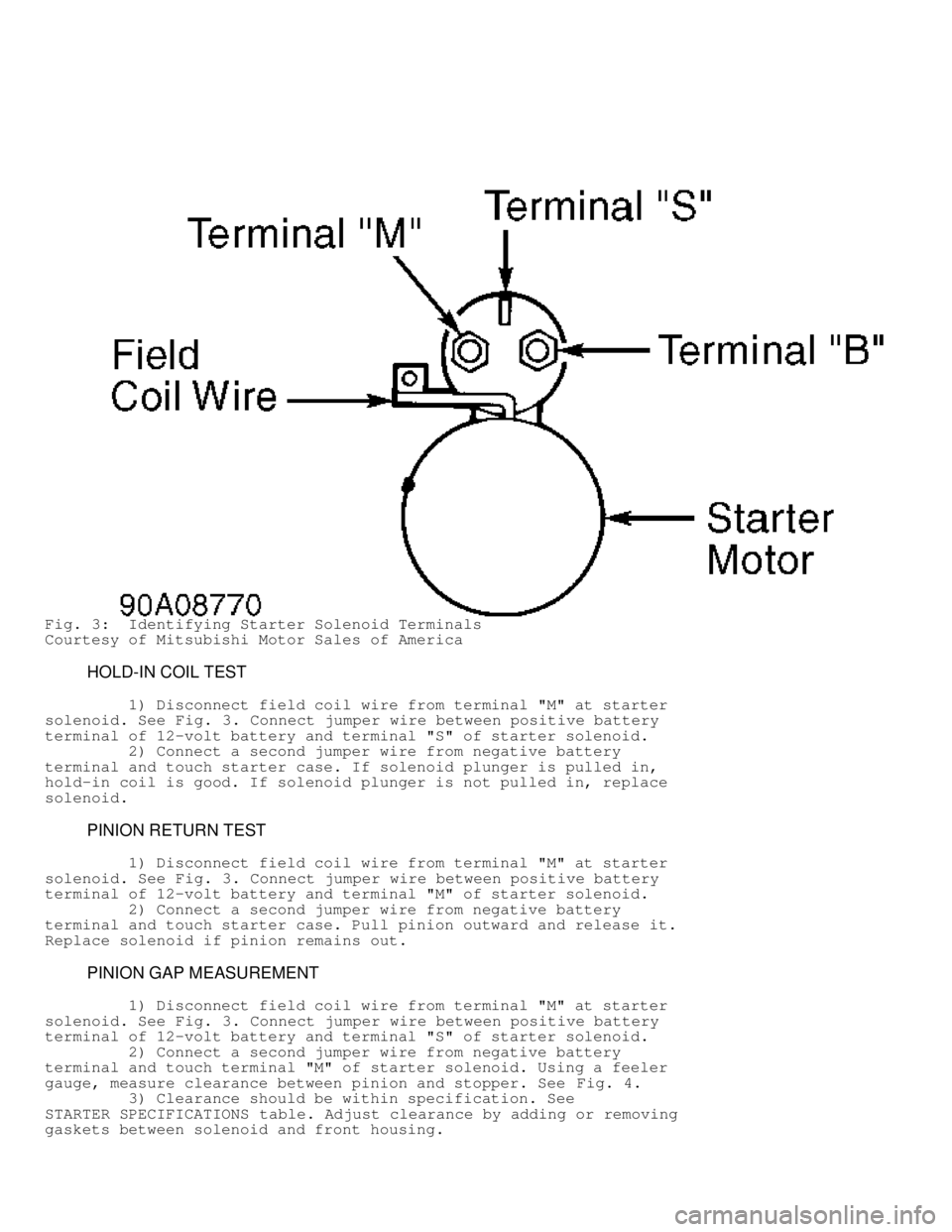
Fig. 3: Identifying Starter Solenoid Terminals
Courtesy of Mitsubishi Motor Sales of America
HOLD-IN COIL TEST
1) Disconnect field coil wire from terminal "M" at starter
solenoid. See Fig. 3. Connect jumper wire between positive battery
terminal of 12-volt battery and terminal "S" of starter solenoid.
2) Connect a second jumper wire from negative battery
terminal and touch starter case. If solenoid plunger is pulled in,
hold-in coil is good. If solenoid plunger is not pulled in, replace
solenoid.
PINION RETURN TEST
1) Disconnect field coil wire from terminal "M" at starter
solenoid. See Fig. 3. Connect jumper wire between positive battery
terminal of 12-volt battery and terminal "M" of starter solenoid.
2) Connect a second jumper wire from negative battery
terminal and touch starter case. Pull pinion outward and release it.
Replace solenoid if pinion remains out.
PINION GAP MEASUREMENT
1) Disconnect field coil wire from terminal "M" at starter
solenoid. See Fig. 3. Connect jumper wire between positive battery
terminal of 12-volt battery and terminal "S" of starter solenoid.
2) Connect a second jumper wire from negative battery
terminal and touch terminal "M" of starter solenoid. Using a feeler
gauge, measure clearance between pinion and stopper. See Fig. 4.
3) Clearance should be within specification. See
STARTER SPECIFICATIONS table. Adjust clearance by adding or removing
gaskets between solenoid and front housing.