stop start MITSUBISHI MONTERO 1998 Service Manual
[x] Cancel search | Manufacturer: MITSUBISHI, Model Year: 1998, Model line: MONTERO, Model: MITSUBISHI MONTERO 1998Pages: 1501, PDF Size: 25.81 MB
Page 219 of 1501
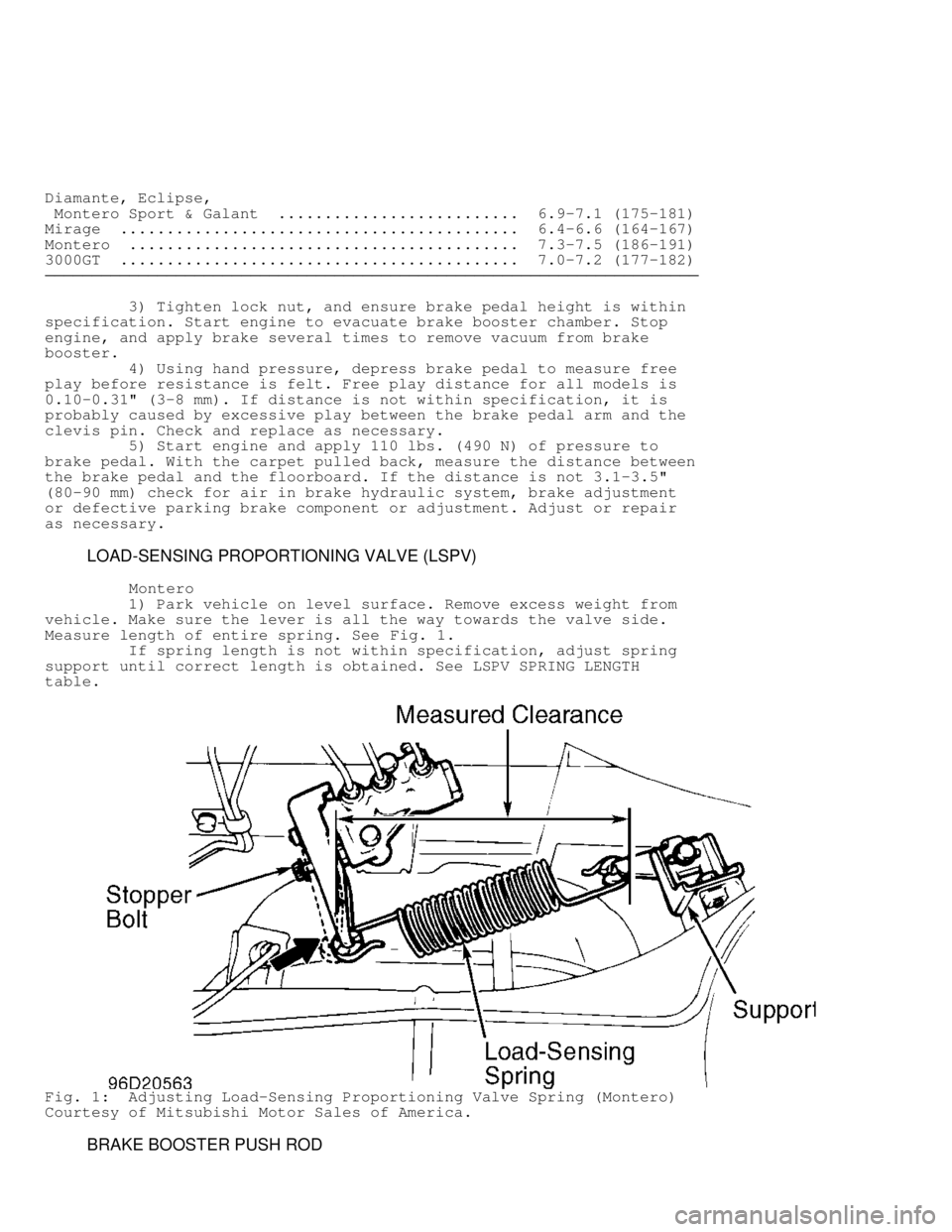
Diamante, Eclipse,
Montero Sport & Galant .......................... 6.9-7.1 (175-181)\
Mirage ........................................... 6.4-6.6 (164-167)\
Montero .......................................... 7.3-7.5 (186-191)\
3000GT ........................................... 7.0-7.2 (177-182)\
\
\
\
\
\
\
\
3) Tighten lock nut, and ensure brake pedal height is within
specification. Start engine to evacuate brake booster chamber. Stop
engine, and apply brake several times to remove vacuum from brake
booster.
4) Using hand pressure, depress brake pedal to measure free
play before resistance is felt. Free play distance for all models is
0.10-0.31" (3-8 mm). If distance is not within specification, it is
probably caused by excessive play between the brake pedal arm and the
clevis pin. Check and replace as necessary.
5) Start engine and apply 110 lbs. (490 N) of pressure to
brake pedal. With the carpet pulled back, measure the distance between
the brake pedal and the floorboard. If the distance is not 3.1-3.5"
(80-90 mm) check for air in brake hydraulic system, brake adjustment
or defective parking brake component or adjustment. Adjust or repair
as necessary.
LOAD-SENSING PROPORTIONING VALVE (LSPV)
Montero
1) Park vehicle on level surface. Remove excess weight from
vehicle. Make sure the lever is all the way towards the valve side.
Measure length of entire spring. See Fig. 1.
If spring length is not within specification, adjust spring
support until correct length is obtained. See LSPV SPRING LENGTH
table.
Fig. 1: Adjusting Load-Sensing Proportioning Valve Spring (Montero)
Courtesy of Mitsubishi Motor Sales of America.
BRAKE BOOSTER PUSH ROD
Page 224 of 1501
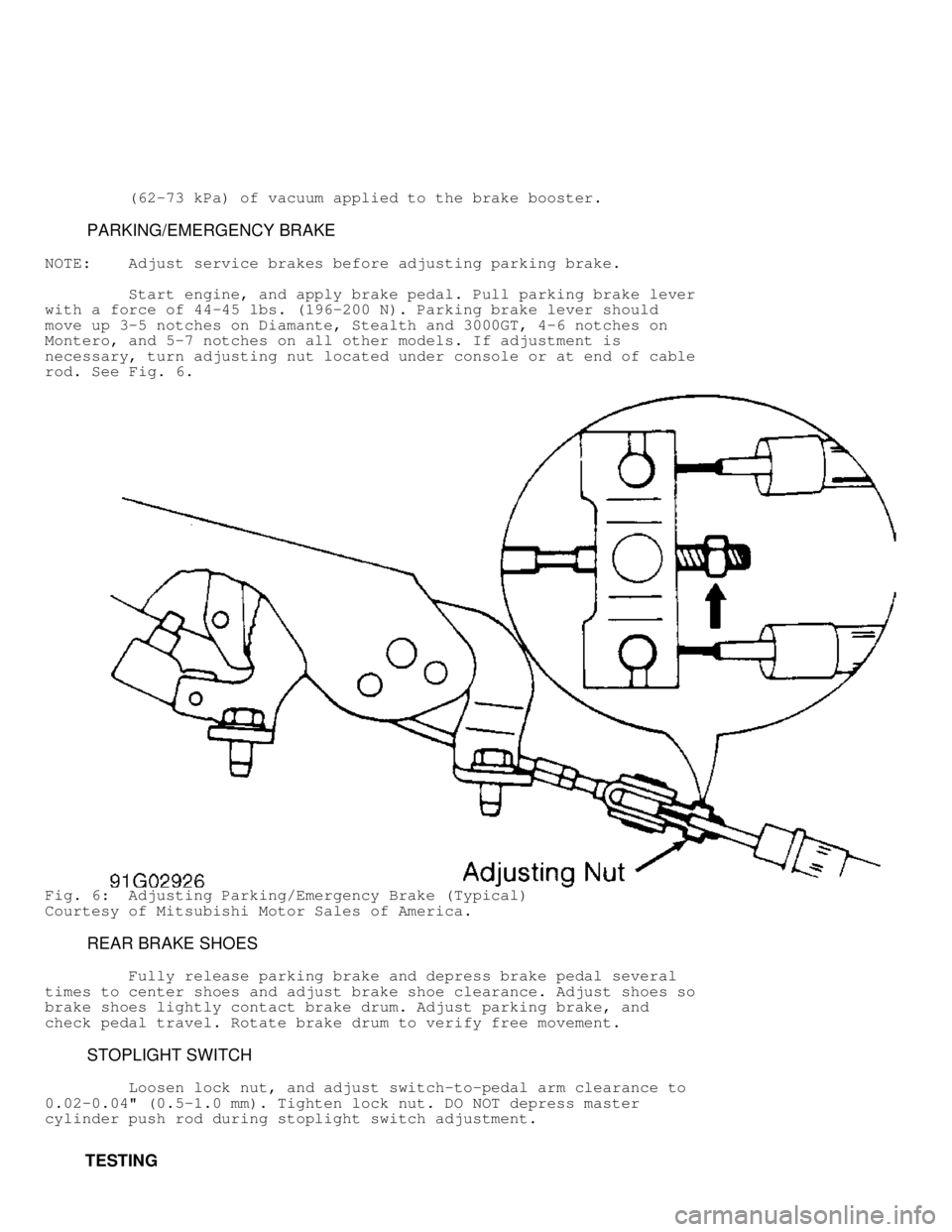
(62-73 kPa) of vacuum applied to the brake booster.
PARKING/EMERGENCY BRAKE
NOTE: Adjust service brakes before adjusting parking brake.
Start engine, and apply brake pedal. Pull parking brake lever
with a force of 44-45 lbs. (196-200 N). Parking brake lever should
move up 3-5 notches on Diamante, Stealth and 3000GT, 4-6 notches on
Montero, and 5-7 notches on all other models. If adjustment is
necessary, turn adjusting nut located under console or at end of cable
rod. See Fig. 6.
Fig. 6: Adjusting Parking/Emergency Brake (Typical)
Courtesy of Mitsubishi Motor Sales of America.
REAR BRAKE SHOES
Fully release parking brake and depress brake pedal several
times to center shoes and adjust brake shoe clearance. Adjust shoes so
brake shoes lightly contact brake drum. Adjust parking brake, and
check pedal travel. Rotate brake drum to verify free movement.
STOPLIGHT SWITCH
Loosen lock nut, and adjust switch-to-pedal arm clearance to
0.02-0.04" (0.5-1.0 mm). Tighten lock nut. DO NOT depress master
cylinder push rod during stoplight switch adjustment.
TESTING
Page 225 of 1501
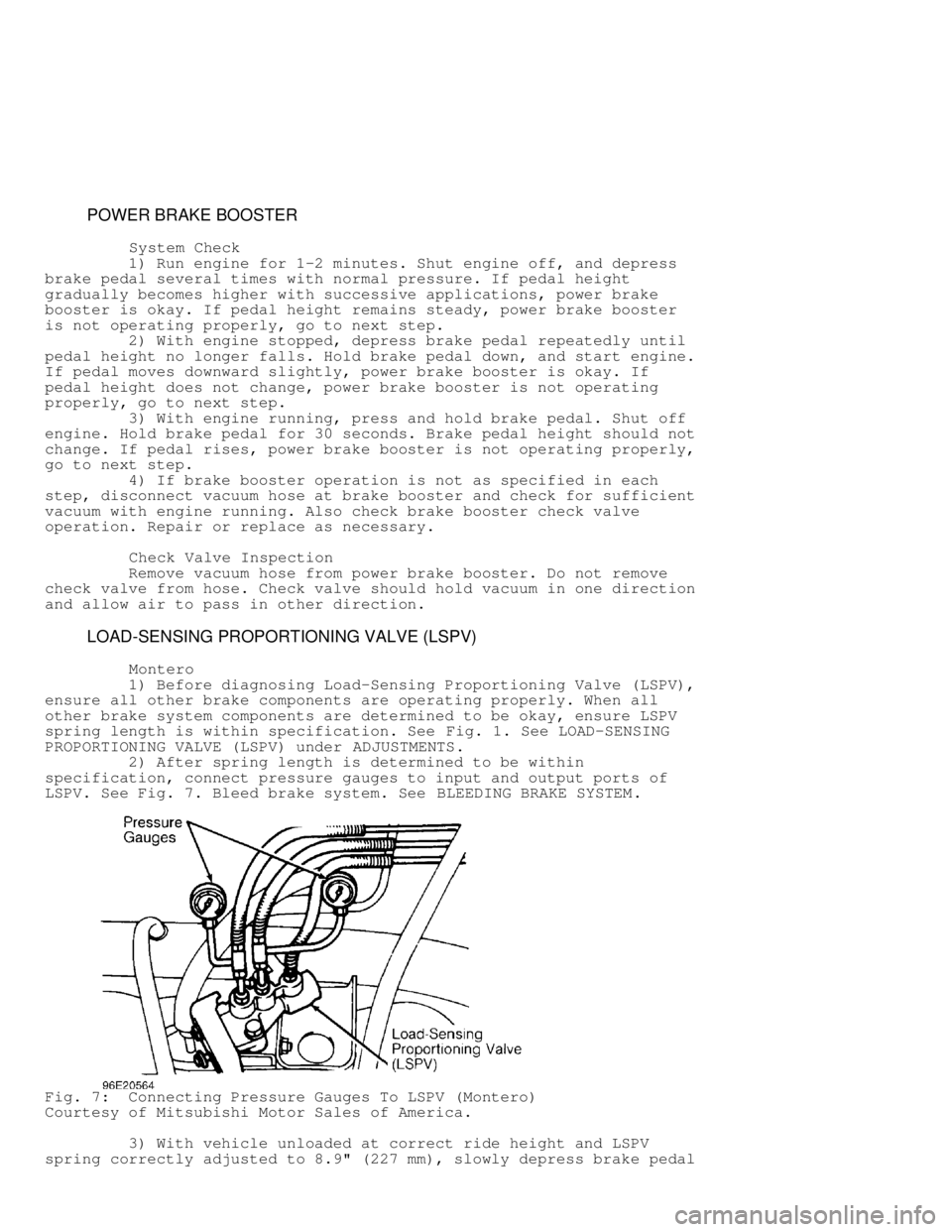
POWER BRAKE BOOSTER
System Check
1) Run engine for 1-2 minutes. Shut engine off, and depress
brake pedal several times with normal pressure. If pedal height
gradually becomes higher with successive applications, power brake
booster is okay. If pedal height remains steady, power brake booster
is not operating properly, go to next step.
2) With engine stopped, depress brake pedal repeatedly until
pedal height no longer falls. Hold brake pedal down, and start engine.
If pedal moves downward slightly, power brake booster is okay. If
pedal height does not change, power brake booster is not operating
properly, go to next step.
3) With engine running, press and hold brake pedal. Shut off
engine. Hold brake pedal for 30 seconds. Brake pedal height should not
change. If pedal rises, power brake booster is not operating properly,
go to next step.
4) If brake booster operation is not as specified in each
step, disconnect vacuum hose at brake booster and check for sufficient
vacuum with engine running. Also check brake booster check valve
operation. Repair or replace as necessary.
Check Valve Inspection
Remove vacuum hose from power brake booster. Do not remove
check valve from hose. Check valve should hold vacuum in one direction
and allow air to pass in other direction.
LOAD-SENSING PROPORTIONING VALVE (LSPV)
Montero
1) Before diagnosing Load-Sensing Proportioning Valve (LSPV)\
,
ensure all other brake components are operating properly. When all
other brake system components are determined to be okay, ensure LSPV
spring length is within specification. See Fig. 1. See LOAD-SENSING
PROPORTIONING VALVE (LSPV) under ADJUSTMENTS.
2) After spring length is determined to be within
specification, connect pressure gauges to input and output ports of
LSPV. See Fig. 7. Bleed brake system. See BLEEDING BRAKE SYSTEM.
Fig. 7: Connecting Pressure Gauges To LSPV (Montero)
Courtesy of Mitsubishi Motor Sales of America.
3) With vehicle unloaded at correct ride height and LSPV
spring correctly adjusted to 8.9" (227 mm), slowly depress brake pedal\
Page 260 of 1501
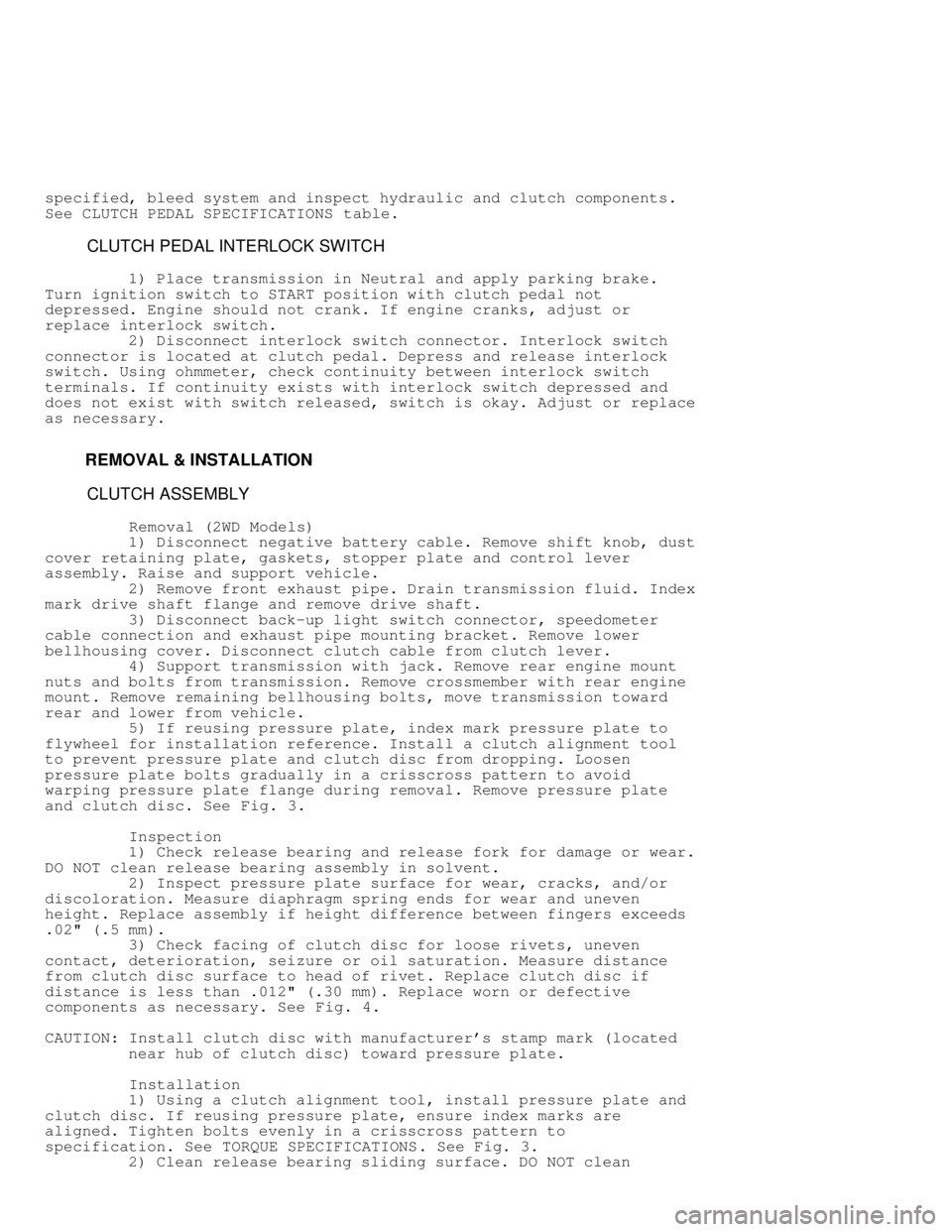
specified, bleed system and inspect hydraulic and clutch components.
See CLUTCH PEDAL SPECIFICATIONS table.
CLUTCH PEDAL INTERLOCK SWITCH
1) Place transmission in Neutral and apply parking brake.
Turn ignition switch to START position with clutch pedal not
depressed. Engine should not crank. If engine cranks, adjust or
replace interlock switch.
2) Disconnect interlock switch connector. Interlock switch
connector is located at clutch pedal. Depress and release interlock
switch. Using ohmmeter, check continuity between interlock switch
terminals. If continuity exists with interlock switch depressed and
does not exist with switch released, switch is okay. Adjust or replace
as necessary.
REMOVAL & INSTALLATION
CLUTCH ASSEMBLY
Removal (2WD Models)
1) Disconnect negative battery cable. Remove shift knob, dust
cover retaining plate, gaskets, stopper plate and control lever
assembly. Raise and support vehicle.
2) Remove front exhaust pipe. Drain transmission fluid. Index
mark drive shaft flange and remove drive shaft.
3) Disconnect back-up light switch connector, speedometer
cable connection and exhaust pipe mounting bracket. Remove lower
bellhousing cover. Disconnect clutch cable from clutch lever.
4) Support transmission with jack. Remove rear engine mount
nuts and bolts from transmission. Remove crossmember with rear engine
mount. Remove remaining bellhousing bolts, move transmission toward
rear and lower from vehicle.
5) If reusing pressure plate, index mark pressure plate to
flywheel for installation reference. Install a clutch alignment tool
to prevent pressure plate and clutch disc from dropping. Loosen
pressure plate bolts gradually in a crisscross pattern to avoid
warping pressure plate flange during removal. Remove pressure plate
and clutch disc. See Fig. 3.
Inspection
1) Check release bearing and release fork for damage or wear.
DO NOT clean release bearing assembly in solvent.
2) Inspect pressure plate surface for wear, cracks, and/or
discoloration. Measure diaphragm spring ends for wear and uneven
height. Replace assembly if height difference between fingers exceeds
.02" (.5 mm).
3) Check facing of clutch disc for loose rivets, uneven
contact, deterioration, seizure or oil saturation. Measure distance
from clutch disc surface to head of rivet. Replace clutch disc if
distance is less than .012" (.30 mm). Replace worn or defective
components as necessary. See Fig. 4.
CAUTION: Install clutch disc with manufacturer's stamp mark (located
near hub of clutch disc) toward pressure plate.
Installation
1) Using a clutch alignment tool, install pressure plate and
clutch disc. If reusing pressure plate, ensure index marks are
aligned. Tighten bolts evenly in a crisscross pattern to
specification. See TORQUE SPECIFICATIONS . See Fig. 3.
2) Clean release bearing sliding surface. DO NOT clean
Page 261 of 1501
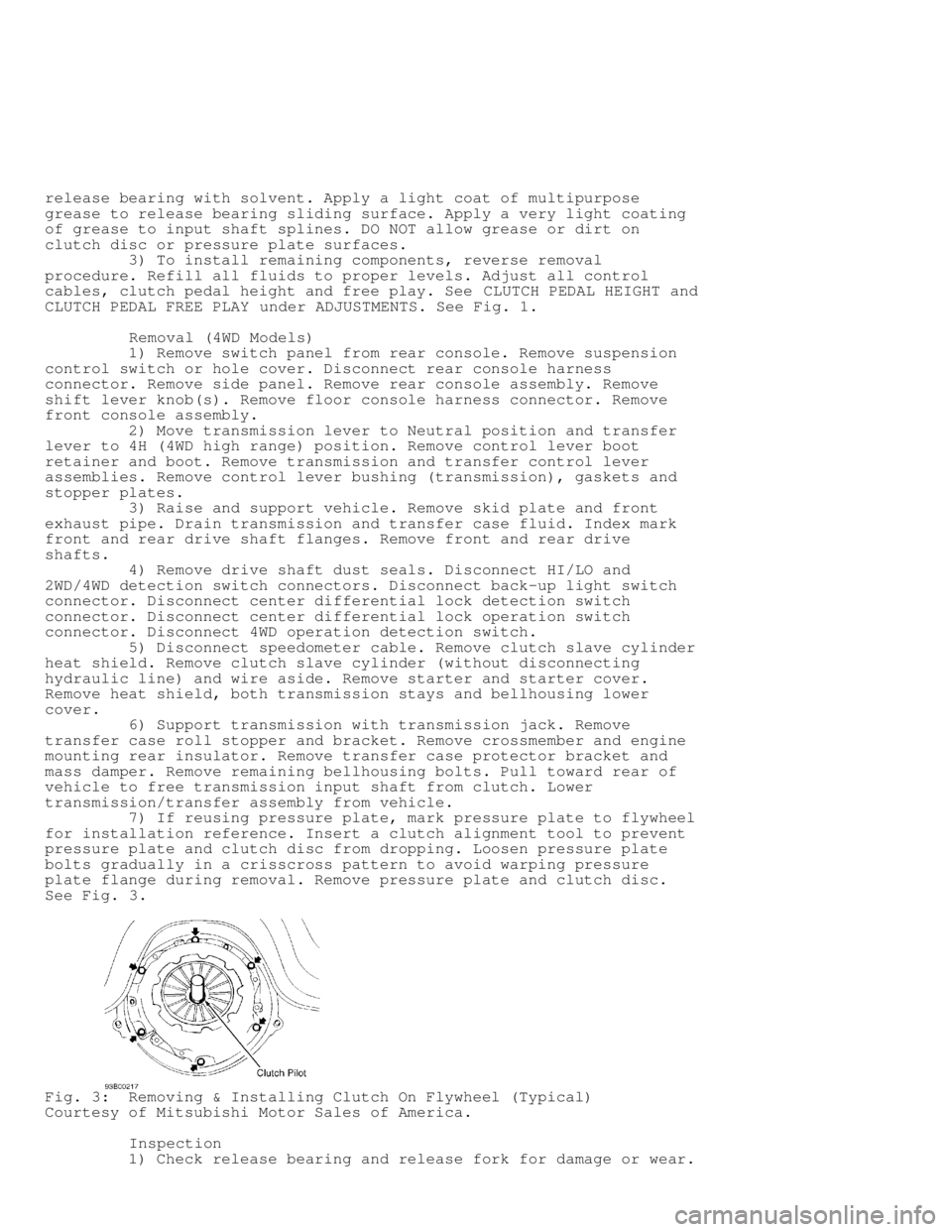
release bearing with solvent. Apply a light coat of multipurpose
grease to release bearing sliding surface. Apply a very light coating
of grease to input shaft splines. DO NOT allow grease or dirt on
clutch disc or pressure plate surfaces.
3) To install remaining components, reverse removal
procedure. Refill all fluids to proper levels. Adjust all control
cables, clutch pedal height and free play. See CLUTCH PEDAL HEIGHT and
CLUTCH PEDAL FREE PLAY under ADJUSTMENTS. See Fig. 1.
Removal (4WD Models)
1) Remove switch panel from rear console. Remove suspension
control switch or hole cover. Disconnect rear console harness
connector. Remove side panel. Remove rear console assembly. Remove
shift lever knob(s). Remove floor console harness connector. Remove
front console assembly.
2) Move transmission lever to Neutral position and transfer
lever to 4H (4WD high range) position. Remove control lever boot
retainer and boot. Remove transmission and transfer control lever
assemblies. Remove control lever bushing (transmission), gaskets and
stopper plates.
3) Raise and support vehicle. Remove skid plate and front
exhaust pipe. Drain transmission and transfer case fluid. Index mark
front and rear drive shaft flanges. Remove front and rear drive
shafts.
4) Remove drive shaft dust seals. Disconnect HI/LO and
2WD/4WD detection switch connectors. Disconnect back-up light switch
connector. Disconnect center differential lock detection switch
connector. Disconnect center differential lock operation switch
connector. Disconnect 4WD operation detection switch.
5) Disconnect speedometer cable. Remove clutch slave cylinder
heat shield. Remove clutch slave cylinder (without disconnecting
hydraulic line) and wire aside. Remove starter and starter cover.
Remove heat shield, both transmission stays and bellhousing lower
cover.
6) Support transmission with transmission jack. Remove
transfer case roll stopper and bracket. Remove crossmember and engine
mounting rear insulator. Remove transfer case protector bracket and
mass damper. Remove remaining bellhousing bolts. Pull toward rear of
vehicle to free transmission input shaft from clutch. Lower
transmission/transfer assembly from vehicle.
7) If reusing pressure plate, mark pressure plate to flywheel
for installation reference. Insert a clutch alignment tool to prevent
pressure plate and clutch disc from dropping. Loosen pressure plate
bolts gradually in a crisscross pattern to avoid warping pressure
plate flange during removal. Remove pressure plate and clutch disc.
See Fig. 3 .
Fig. 3: Removing & Installing Clutch On Flywheel (Typical)
Courtesy of Mitsubishi Motor Sales of America.
Inspection
1) Check release bearing and release fork for damage or wear.
Page 267 of 1501

Clutch Pedal Mounting Nut .................................. 21 (29)\
Flywheel Bolt
Montero .................................................. 54 (74)\
Montero Sport ........................................... 98 (132)\
Fulcrum Ball ............................................... 26 (35)\
Hydraulic Line Flare Nut ................................... 11 (15)\
Push Rod Jam Nut ........................................... 10 (13)\
Release Cylinder Mounting Bolt ............................. 27 (36)\
Starter Mounting Bolt ...................................... 23 (31)\
Transfer Case Roll Stopper Bolt ............................ 33 (44)\
Transmission Crossmember Mounting Bolt ..................... 47 (64)\
Transmission Support Bolt
Front (Crossmember) ...................................... 29 (39\
)
Rear ..................................................... 26 (35)\
\
\
\
\
\
\
\
Page 268 of 1501
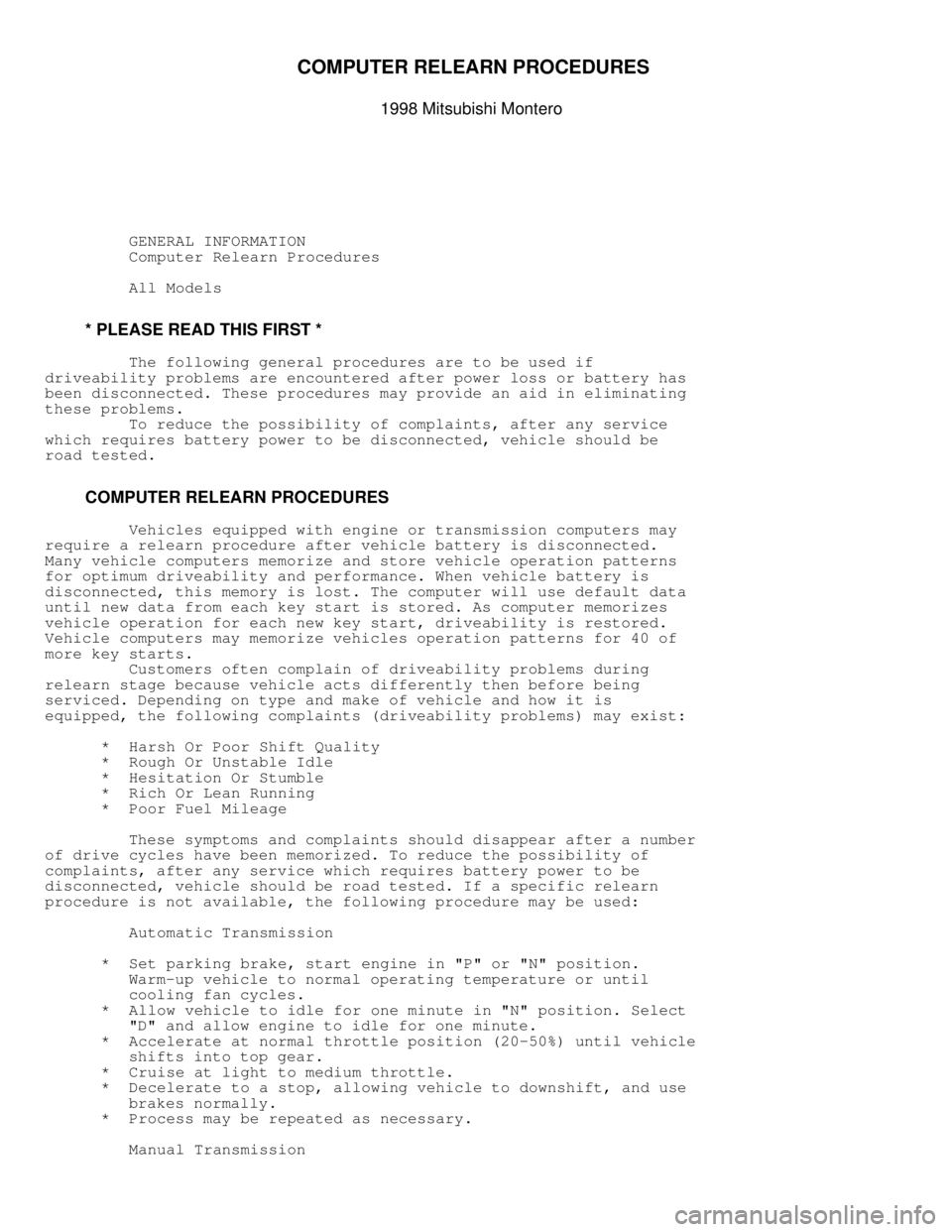
COMPUTER RELEARN PROCEDURES
1998 Mitsubishi Montero
GENERAL INFORMATION
Computer Relearn Procedures
All Models
* PLEASE READ THIS FIRST *
The following general procedures are to be used if
driveability problems are encountered after power loss or battery has
been disconnected. These procedures may provide an aid in eliminating
these problems.
To reduce the possibility of complaints, after any service
which requires battery power to be disconnected, vehicle should be
road tested.
COMPUTER RELEARN PROCEDURES
Vehicles equipped with engine or transmission computers may
require a relearn procedure after vehicle battery is disconnected.
Many vehicle computers memorize and store vehicle operation patterns
for optimum driveability and performance. When vehicle battery is
disconnected, this memory is lost. The computer will use default data
until new data from each key start is stored. As computer memorizes
vehicle operation for each new key start, driveability is restored.
Vehicle computers may memorize vehicles operation patterns for 40 of
more key starts.
Customers often complain of driveability problems during
relearn stage because vehicle acts differently then before being
serviced. Depending on type and make of vehicle and how it is
equipped, the following complaints (driveability problems) may exist:
* Harsh Or Poor Shift Quality
* Rough Or Unstable Idle
* Hesitation Or Stumble
* Rich Or Lean Running
* Poor Fuel Mileage
These symptoms and complaints should disappear after a number
of drive cycles have been memorized. To reduce the possibility of
complaints, after any service which requires battery power to be
disconnected, vehicle should be road tested. If a specific relearn
procedure is not available, the following procedure may be used:
Automatic Transmission
* Set parking brake, start engine in "P" or "N" position.
Warm-up vehicle to normal operating temperature or until
cooling fan cycles.
* Allow vehicle to idle for one minute in "N" position. Select
"D" and allow engine to idle for one minute.
* Accelerate at normal throttle position (20-50%) until vehicle
shifts into top gear.
* Cruise at light to medium throttle.
* Decelerate to a stop, allowing vehicle to downshift, and use
brakes normally.
* Process may be repeated as necessary.
Manual Transmission
Page 319 of 1501
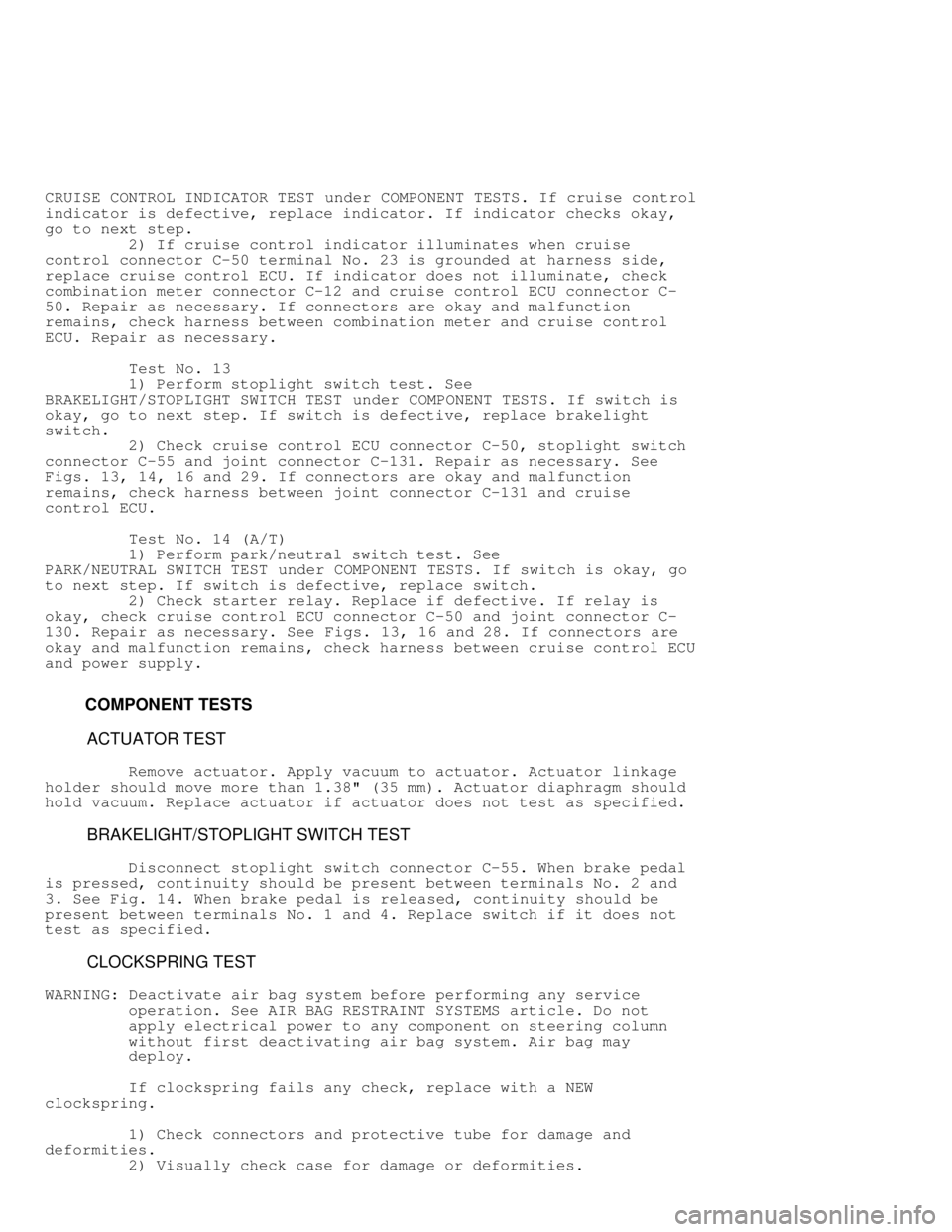
CRUISE CONTROL INDICATOR TEST under COMPONENT TESTS. If cruise control
indicator is defective, replace indicator. If indicator checks okay,
go to next step.
2) If cruise control indicator illuminates when cruise
control connector C-50 terminal No. 23 is grounded at harness side,
replace cruise control ECU. If indicator does not illuminate, check
combination meter connector C-12 and cruise control ECU connector C-
50. Repair as necessary. If connectors are okay and malfunction
remains, check harness between combination meter and cruise control
ECU. Repair as necessary.
Test No. 13
1) Perform stoplight switch test. See
BRAKELIGHT/STOPLIGHT SWITCH TEST under COMPONENT TESTS. If switch is
okay, go to next step. If switch is defective, replace brakelight
switch.
2) Check cruise control ECU connector C-50, stoplight switch
connector C-55 and joint connector C-131. Repair as necessary. See
Figs. 13 , 14, 16 and 29. If connectors are okay and malfunction
remains, check harness between joint connector C-131 and cruise
control ECU.
Test No. 14 (A/T)
1) Perform park/neutral switch test. See
PARK/NEUTRAL SWITCH TEST under COMPONENT TESTS. If switch is okay, go
to next step. If switch is defective, replace switch.
2) Check starter relay. Replace if defective. If relay is
okay, check cruise control ECU connector C-50 and joint connector C-
130. Repair as necessary. See Figs. 13, 16 and 28. If connectors are
okay and malfunction remains, check harness between cruise control ECU
and power supply.
COMPONENT TESTS
ACTUATOR TEST
Remove actuator. Apply vacuum to actuator. Actuator linkage
holder should move more than 1.38" (35 mm). Actuator diaphragm should
hold vacuum. Replace actuator if actuator does not test as specified.
BRAKELIGHT/STOPLIGHT SWITCH TEST
Disconnect stoplight switch connector C-55. When brake pedal
is pressed, continuity should be present between terminals No. 2 and
3. See Fig. 14. When brake pedal is released, continuity should be
present between terminals No. 1 and 4. Replace switch if it does not
test as specified.
CLOCKSPRING TEST
WARNING: Deactivate air bag system before performing any service
operation. See AIR BAG RESTRAINT SYSTEMS article. Do not
apply electrical power to any component on steering column
without first deactivating air bag system. Air bag may
deploy.
If clockspring fails any check, replace with a NEW
clockspring.
1) Check connectors and protective tube for damage and
deformities.
2) Visually check case for damage or deformities.
Page 338 of 1501
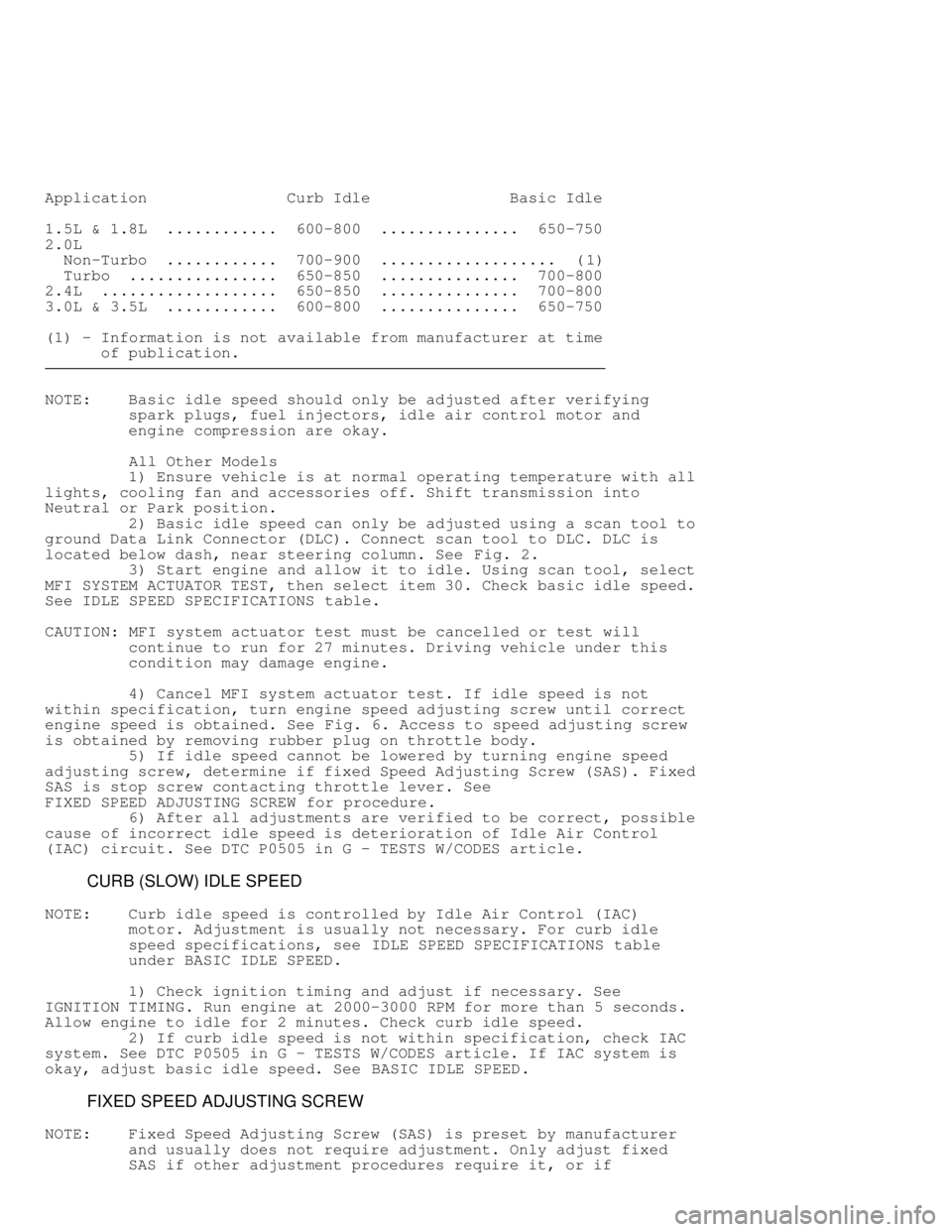
Application Curb Idle Basic Idle
1.5L & 1.8L ............ 600-800 ............... 650-750
2.0L
Non-Turbo ............ 700-900 ................... (1)
Turbo ................ 650-850 ............... 700-800
2.4L ................... 650-850 ............... 700-800
3.0L & 3.5L ............ 600-800 ............... 650-750
( 1) - Information is not available from manufacturer at time
of publication.
\
\
\
\
\
\
NOTE: Basic idle speed should only be adjusted after verifying
spark plugs, fuel injectors, idle air control motor and
engine compression are okay.
All Other Models
1) Ensure vehicle is at normal operating temperature with all
lights, cooling fan and accessories off. Shift transmission into
Neutral or Park position.
2) Basic idle speed can only be adjusted using a scan tool to
ground Data Link Connector (DLC). Connect scan tool to DLC. DLC is
located below dash, near steering column. See Fig. 2.
3) Start engine and allow it to idle. Using scan tool, select
MFI SYSTEM ACTUATOR TEST, then select item 30. Check basic idle speed.
See IDLE SPEED SPECIFICATIONS table.
CAUTION: MFI system actuator test must be cancelled or test will
continue to run for 27 minutes. Driving vehicle under this
condition may damage engine.
4) Cancel MFI system actuator test. If idle speed is not
within specification, turn engine speed adjusting screw until correct
engine speed is obtained. See Fig. 6. Access to speed adjusting screw
is obtained by removing rubber plug on throttle body.
5) If idle speed cannot be lowered by turning engine speed
adjusting screw, determine if fixed Speed Adjusting Screw (SAS). Fixed\
SAS is stop screw contacting throttle lever. See
FIXED SPEED ADJUSTING SCREW for procedure.
6) After all adjustments are verified to be correct, possible
cause of incorrect idle speed is deterioration of Idle Air Control
(IAC) circuit. See DTC P0505 in G - TESTS W/CODES article.
CURB (SLOW) IDLE SPEED
NOTE: Curb idle speed is controlled by Idle Air Control (IAC)
motor. Adjustment is usually not necessary. For curb idle
speed specifications, see IDLE SPEED SPECIFICATIONS table
under BASIC IDLE SPEED.
1) Check ignition timing and adjust if necessary. See
IGNITION TIMING . Run engine at 2000-3000 RPM for more than 5 seconds.
Allow engine to idle for 2 minutes. Check curb idle speed.
2) If curb idle speed is not within specification, check IAC
system. See DTC P0505 in G - TESTS W/CODES article. If IAC system is
okay, adjust basic idle speed. See BASIC IDLE SPEED.
FIXED SPEED ADJUSTING SCREW
NOTE: Fixed Speed Adjusting Screw (SAS) is preset by manufacturer
and usually does not require adjustment. Only adjust fixed
SAS if other adjustment procedures require it, or if
Page 349 of 1501
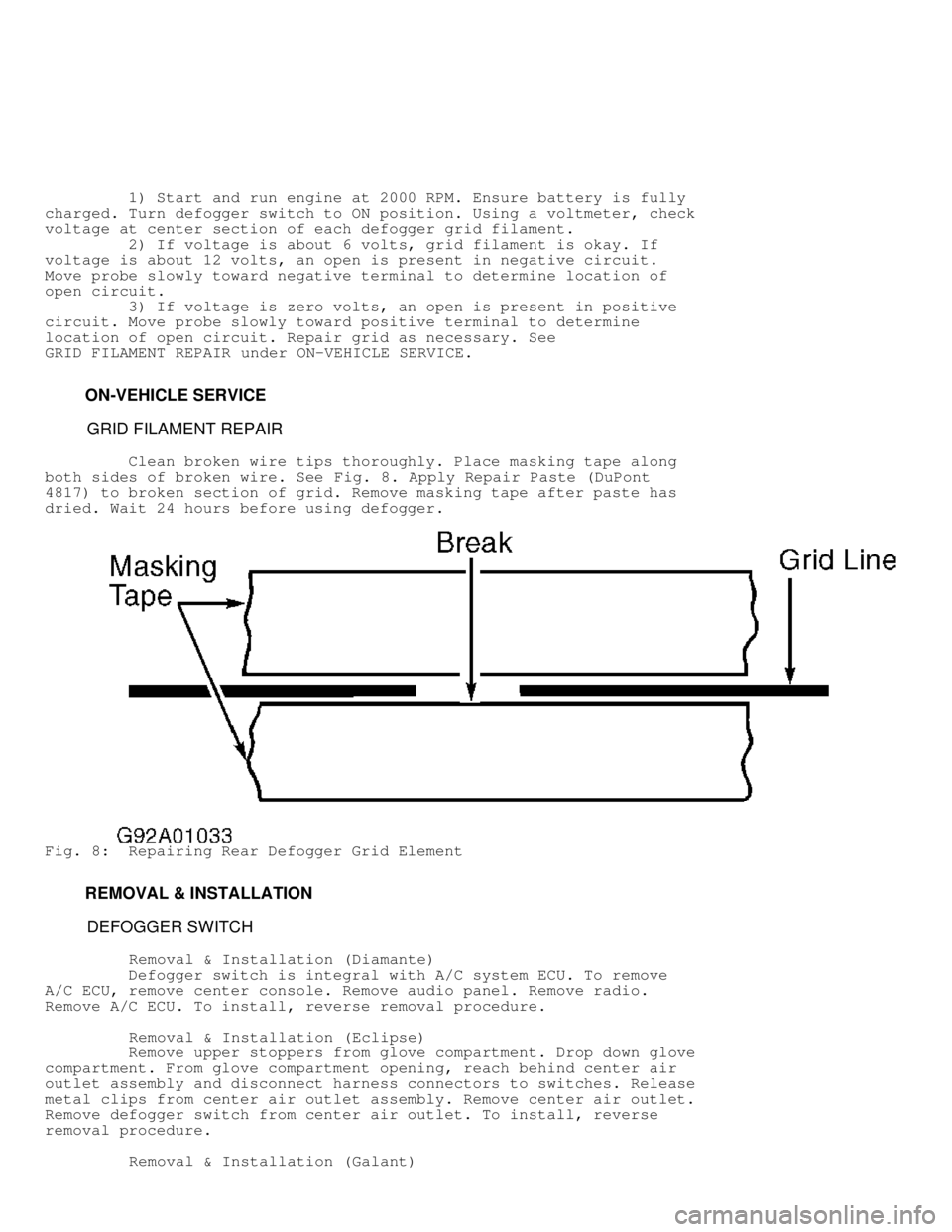
1) Start and run engine at 2000 RPM. Ensure battery is fully
charged. Turn defogger switch to ON position. Using a voltmeter, check
voltage at center section of each defogger grid filament.
2) If voltage is about 6 volts, grid filament is okay. If
voltage is about 12 volts, an open is present in negative circuit.
Move probe slowly toward negative terminal to determine location of
open circuit.
3) If voltage is zero volts, an open is present in positive
circuit. Move probe slowly toward positive terminal to determine
location of open circuit. Repair grid as necessary. See
GRID FILAMENT REPAIR under ON-VEHICLE SERVICE.
ON-VEHICLE SERVICE
GRID FILAMENT REPAIR
Clean broken wire tips thoroughly. Place masking tape along
both sides of broken wire. See Fig. 8. Apply Repair Paste (DuPont
4817) to broken section of grid. Remove masking tape after paste has
dried. Wait 24 hours before using defogger.
Fig. 8: Repairing Rear Defogger Grid Element
REMOVAL & INSTALLATION
DEFOGGER SWITCH
Removal & Installation (Diamante)
Defogger switch is integral with A/C system ECU. To remove
A/C ECU, remove center console. Remove audio panel. Remove radio.
Remove A/C ECU. To install, reverse removal procedure.
Removal & Installation (Eclipse)
Remove upper stoppers from glove compartment. Drop down glove
compartment. From glove compartment opening, reach behind center air
outlet assembly and disconnect harness connectors to switches. Release
metal clips from center air outlet assembly. Remove center air outlet.
Remove defogger switch from center air outlet. To install, reverse
removal procedure.
Removal & Installation (Galant)