check engine light MITSUBISHI MONTERO 1998 Service Manual
[x] Cancel search | Manufacturer: MITSUBISHI, Model Year: 1998, Model line: MONTERO, Model: MITSUBISHI MONTERO 1998Pages: 1501, PDF Size: 25.81 MB
Page 86 of 1501
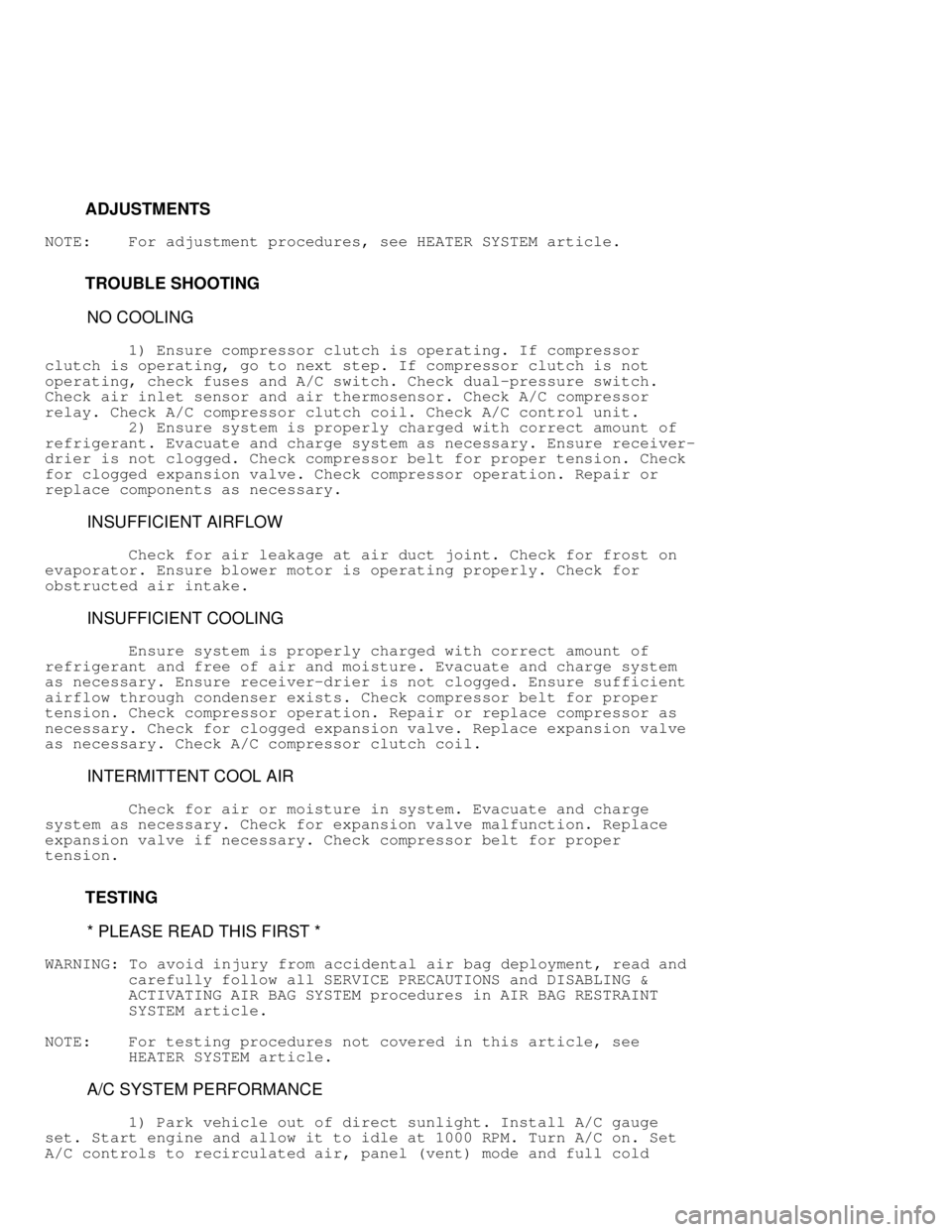
ADJUSTMENTS
NOTE: For adjustment procedures, see HEATER SYSTEM article.
TROUBLE SHOOTING
NO COOLING
1) Ensure compressor clutch is operating. If compressor
clutch is operating, go to next step. If compressor clutch is not
operating, check fuses and A/C switch. Check dual-pressure switch.
Check air inlet sensor and air thermosensor. Check A/C compressor
relay. Check A/C compressor clutch coil. Check A/C control unit.
2) Ensure system is properly charged with correct amount of
refrigerant. Evacuate and charge system as necessary. Ensure receiver-
drier is not clogged. Check compressor belt for proper tension. Check
for clogged expansion valve. Check compressor operation. Repair or
replace components as necessary.
INSUFFICIENT AIRFLOW
Check for air leakage at air duct joint. Check for frost on
evaporator. Ensure blower motor is operating properly. Check for
obstructed air intake.
INSUFFICIENT COOLING
Ensure system is properly charged with correct amount of
refrigerant and free of air and moisture. Evacuate and charge system
as necessary. Ensure receiver-drier is not clogged. Ensure sufficient
airflow through condenser exists. Check compressor belt for proper
tension. Check compressor operation. Repair or replace compressor as
necessary. Check for clogged expansion valve. Replace expansion valve
as necessary. Check A/C compressor clutch coil.
INTERMITTENT COOL AIR
Check for air or moisture in system. Evacuate and charge
system as necessary. Check for expansion valve malfunction. Replace
expansion valve if necessary. Check compressor belt for proper
tension.
TESTING
* PLEASE READ THIS FIRST *
WARNING: To avoid injury from accidental air bag deployment, read and
carefully follow all SERVICE PRECAUTIONS and DISABLING &
ACTIVATING AIR BAG SYSTEM procedures in AIR BAG RESTRAINT
SYSTEM article.
NOTE: For testing procedures not covered in this article, see
HEATER SYSTEM article.
A/C SYSTEM PERFORMANCE
1) Park vehicle out of direct sunlight. Install A/C gauge
set. Start engine and allow it to idle at 1000 RPM. Turn A/C on. Set
A/C controls to recirculated air, panel (vent) mode and full cold
Page 119 of 1501
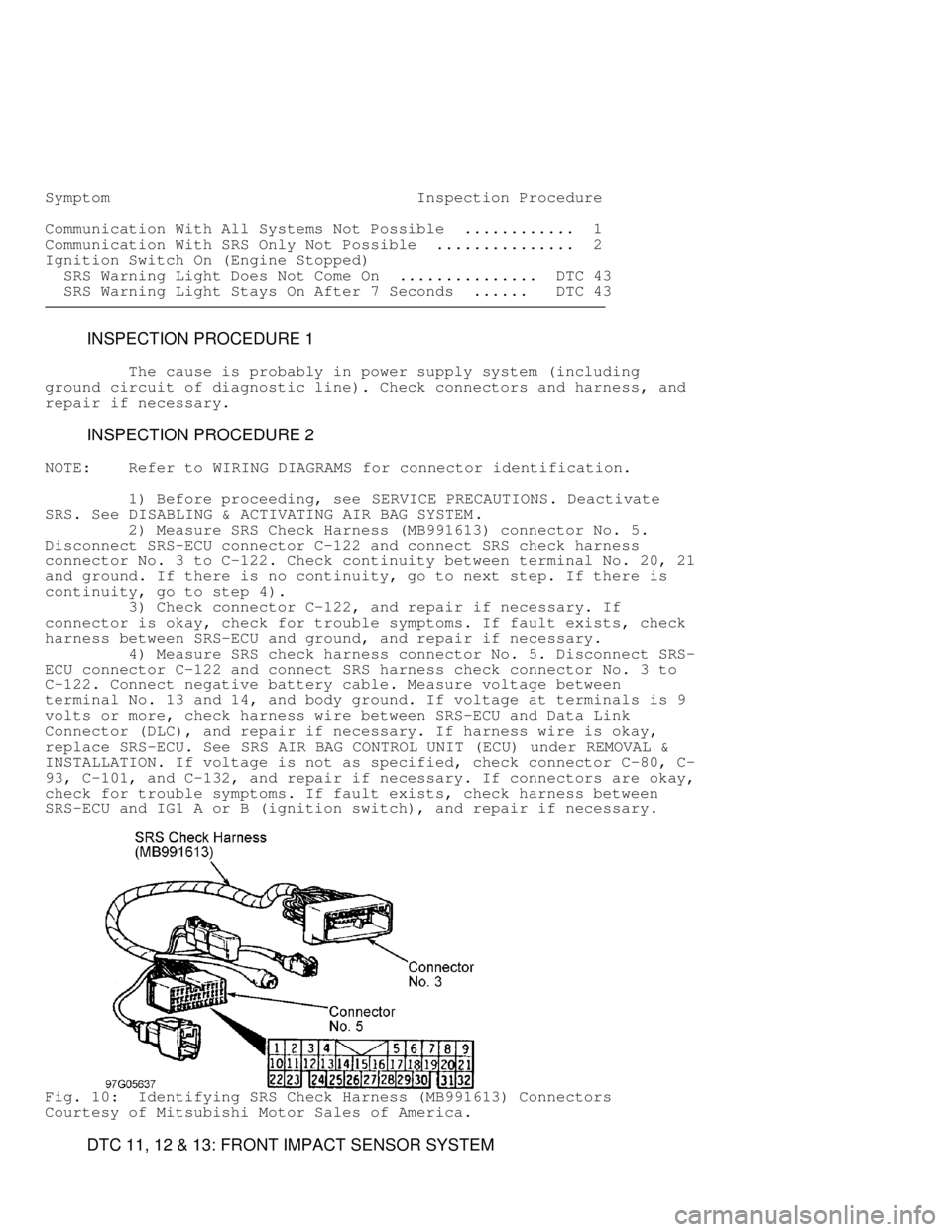
Symptom Inspection Procedure
Communication With All Systems Not Possible ............ 1
Communication With SRS Only Not Possible ............... 2
Ignition Switch On (Engine Stopped)
SRS Warning Light Does Not Come On ............... DTC 43
SRS Warning Light Stays On After 7 Seconds ...... DTC 43
\
\
\
\
\
\
INSPECTION PROCEDURE 1
The cause is probably in power supply system (including
ground circuit of diagnostic line). Check connectors and harness, and
repair if necessary.
INSPECTION PROCEDURE 2
NOTE: Refer to WIRING DIAGRAMS for connector identification.
1) Before proceeding, see SERVICE PRECAUTIONS. Deactivate
SRS. See DISABLING & ACTIVATING AIR BAG SYSTEM .
2) Measure SRS Check Harness (MB991613) connector No. 5.
Disconnect SRS-ECU connector C-122 and connect SRS check harness
connector No. 3 to C-122. Check continuity between terminal No. 20, 21
and ground. If there is no continuity, go to next step. If there is
continuity, go to step 4).
3) Check connector C-122, and repair if necessary. If
connector is okay, check for trouble symptoms. If fault exists, check
harness between SRS-ECU and ground, and repair if necessary.
4) Measure SRS check harness connector No. 5. Disconnect SRS-
ECU connector C-122 and connect SRS harness check connector No. 3 to
C-122. Connect negative battery cable. Measure voltage between
terminal No. 13 and 14, and body ground. If voltage at terminals is 9
volts or more, check harness wire between SRS-ECU and Data Link
Connector (DLC), and repair if necessary. If harness wire is okay,
replace SRS-ECU. See SRS AIR BAG CONTROL UNIT (ECU) under REMOVAL &
INSTALLATION. If voltage is not as specified, check connector C-80, C-
93, C-101, and C-132, and repair if necessary. If connectors are okay,
check for trouble symptoms. If fault exists, check harness between
SRS-ECU and IG1 A or B (ignition switch), and repair if necessary.
Fig. 10: Identifying SRS Check Harness (MB991613) Connectors
Courtesy of Mitsubishi Motor Sales of America.
DTC 11, 12 & 13: FRONT IMPACT SENSOR SYSTEM
Page 128 of 1501
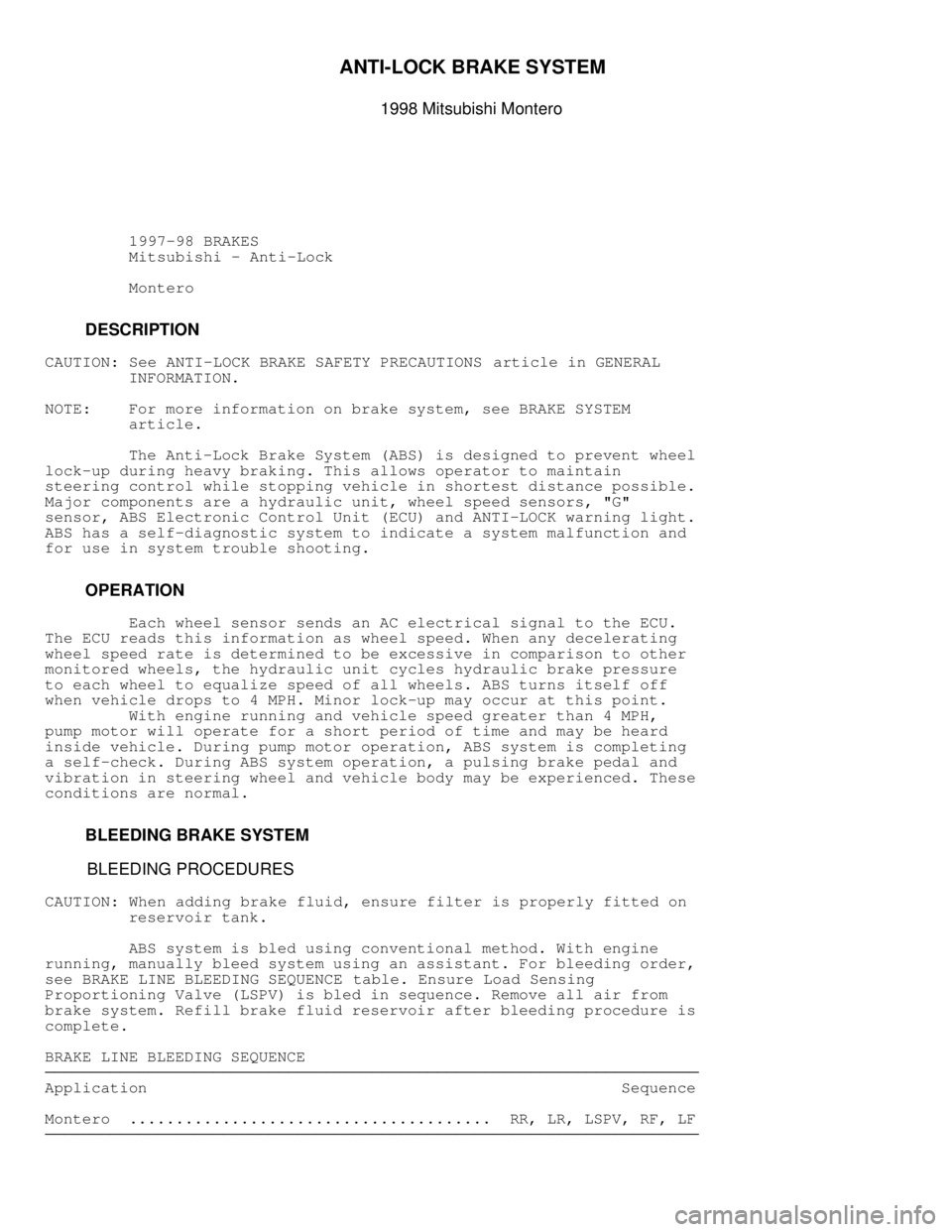
ANTI-LOCK BRAKE SYSTEM
1998 Mitsubishi Montero
1997-98 BRAKES
Mitsubishi - Anti-Lock
Montero
DESCRIPTION
CAUTION: See ANTI-LOCK BRAKE SAFETY PRECAUTIONS article in GENERAL
INFORMATION.
NOTE: For more information on brake system, see BRAKE SYSTEM
article.
The Anti-Lock Brake System (ABS) is designed to prevent wheel\
lock-up during heavy braking. This allows operator to maintain
steering control while stopping vehicle in shortest distance possible.
Major components are a hydraulic unit, wheel speed sensors, "G"
sensor, ABS Electronic Control Unit (ECU) and ANTI-LOCK warning light.\
ABS has a self-diagnostic system to indicate a system malfunction and
for use in system trouble shooting.
OPERATION
Each wheel sensor sends an AC electrical signal to the ECU.
The ECU reads this information as wheel speed. When any decelerating
wheel speed rate is determined to be excessive in comparison to other
monitored wheels, the hydraulic unit cycles hydraulic brake pressure
to each wheel to equalize speed of all wheels. ABS turns itself off
when vehicle drops to 4 MPH. Minor lock-up may occur at this point.
With engine running and vehicle speed greater than 4 MPH,
pump motor will operate for a short period of time and may be heard
inside vehicle. During pump motor operation, ABS system is completing
a self-check. During ABS system operation, a pulsing brake pedal and
vibration in steering wheel and vehicle body may be experienced. These
conditions are normal.
BLEEDING BRAKE SYSTEM
BLEEDING PROCEDURES
CAUTION: When adding brake fluid, ensure filter is properly fitted on
reservoir tank.
ABS system is bled using conventional method. With engine
running, manually bleed system using an assistant. For bleeding order,
see BRAKE LINE BLEEDING SEQUENCE table. Ensure Load Sensing
Proportioning Valve (LSPV) is bled in sequence. Remove all air from
brake system. Refill brake fluid reservoir after bleeding procedure is
complete.
BRAKE LINE BLEEDING SEQUENCE
\
\
\
\
\
\
\
Application Sequence
Montero ....................................... RR, LR, LSPV, RF, LF
\
\
\
\
\
\
\
Page 130 of 1501
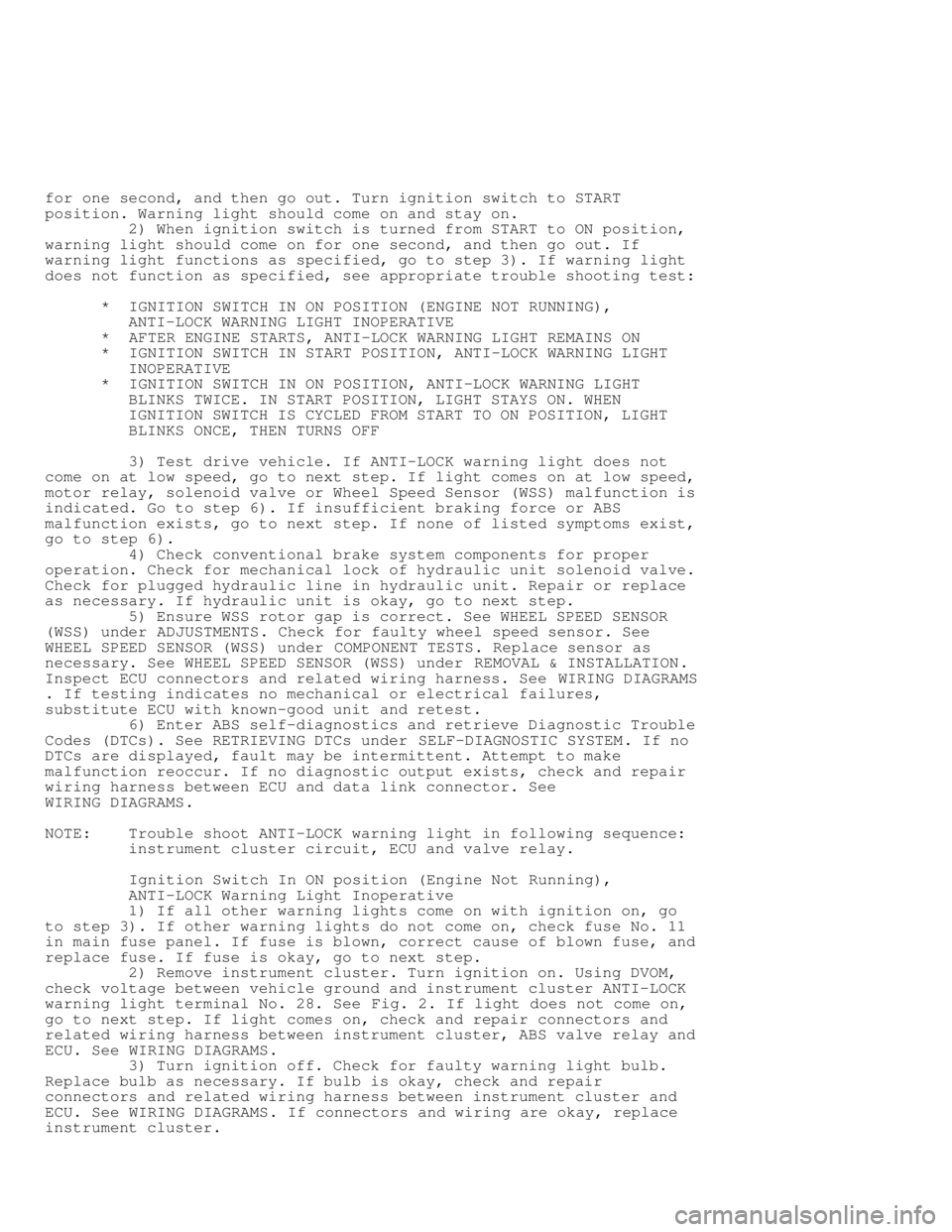
for one second, and then go out. Turn ignition switch to START
position. Warning light should come on and stay on.
2) When ignition switch is turned from START to ON position,
warning light should come on for one second, and then go out. If
warning light functions as specified, go to step 3). If warning light
does not function as specified, see appropriate trouble shooting test:
* IGNITION SWITCH IN ON POSITION (ENGINE NOT RUNNING),
ANTI-LOCK WARNING LIGHT INOPERATIVE
* AFTER ENGINE STARTS, ANTI-LOCK WARNING LIGHT REMAINS ON
* IGNITION SWITCH IN START POSITION, ANTI-LOCK WARNING LIGHT
INOPERATIVE
* IGNITION SWITCH IN ON POSITION, ANTI-LOCK WARNING LIGHT
BLINKS TWICE. IN START POSITION, LIGHT STAYS ON. WHEN
IGNITION SWITCH IS CYCLED FROM START TO ON POSITION, LIGHT
BLINKS ONCE, THEN TURNS OFF
3) Test drive vehicle. If ANTI-LOCK warning light does not
come on at low speed, go to next step. If light comes on at low speed,
motor relay, solenoid valve or Wheel Speed Sensor (WSS) malfunction is\
indicated. Go to step 6). If insufficient braking force or ABS
malfunction exists, go to next step. If none of listed symptoms exist,
go to step 6).
4) Check conventional brake system components for proper
operation. Check for mechanical lock of hydraulic unit solenoid valve.
Check for plugged hydraulic line in hydraulic unit. Repair or replace
as necessary. If hydraulic unit is okay, go to next step.
5) Ensure WSS rotor gap is correct. See WHEEL SPEED SENSOR
(WSS) under ADJUSTMENTS. Check for faulty wheel speed sensor. See
WHEEL SPEED SENSOR (WSS) under COMPONENT TESTS. Replace sensor as
necessary. See WHEEL SPEED SENSOR (WSS) under REMOVAL & INSTALLATION.
Inspect ECU connectors and related wiring harness. See WIRING DIAGRAMS
. If testing indicates no mechanical or electrical failures,
substitute ECU with known-good unit and retest.
6) Enter ABS self-diagnostics and retrieve Diagnostic Trouble
Codes (DTCs). See RETRIEVING DTCs under SELF-DIAGNOSTIC SYSTEM. If no
DTCs are displayed, fault may be intermittent. Attempt to make
malfunction reoccur. If no diagnostic output exists, check and repair
wiring harness between ECU and data link connector. See
WIRING DIAGRAMS .
NOTE: Trouble shoot ANTI-LOCK warning light in following sequence:
instrument cluster circuit, ECU and valve relay.
Ignition Switch In ON position (Engine Not Running),
ANTI-LOCK Warning Light Inoperative
1) If all other warning lights come on with ignition on, go
to step 3). If other warning lights do not come on, check fuse No. 11
in main fuse panel. If fuse is blown, correct cause of blown fuse, and
replace fuse. If fuse is okay, go to next step.
2) Remove instrument cluster. Turn ignition on. Using DVOM,
check voltage between vehicle ground and instrument cluster ANTI-LOCK
warning light terminal No. 28. See Fig. 2. If light does not come on,
go to next step. If light comes on, check and repair connectors and
related wiring harness between instrument cluster, ABS valve relay and
ECU. See WIRING DIAGRAMS .
3) Turn ignition off. Check for faulty warning light bulb.
Replace bulb as necessary. If bulb is okay, check and repair
connectors and related wiring harness between instrument cluster and
ECU. See WIRING DIAGRAMS . If connectors and wiring are okay, replace
instrument cluster.
Page 131 of 1501
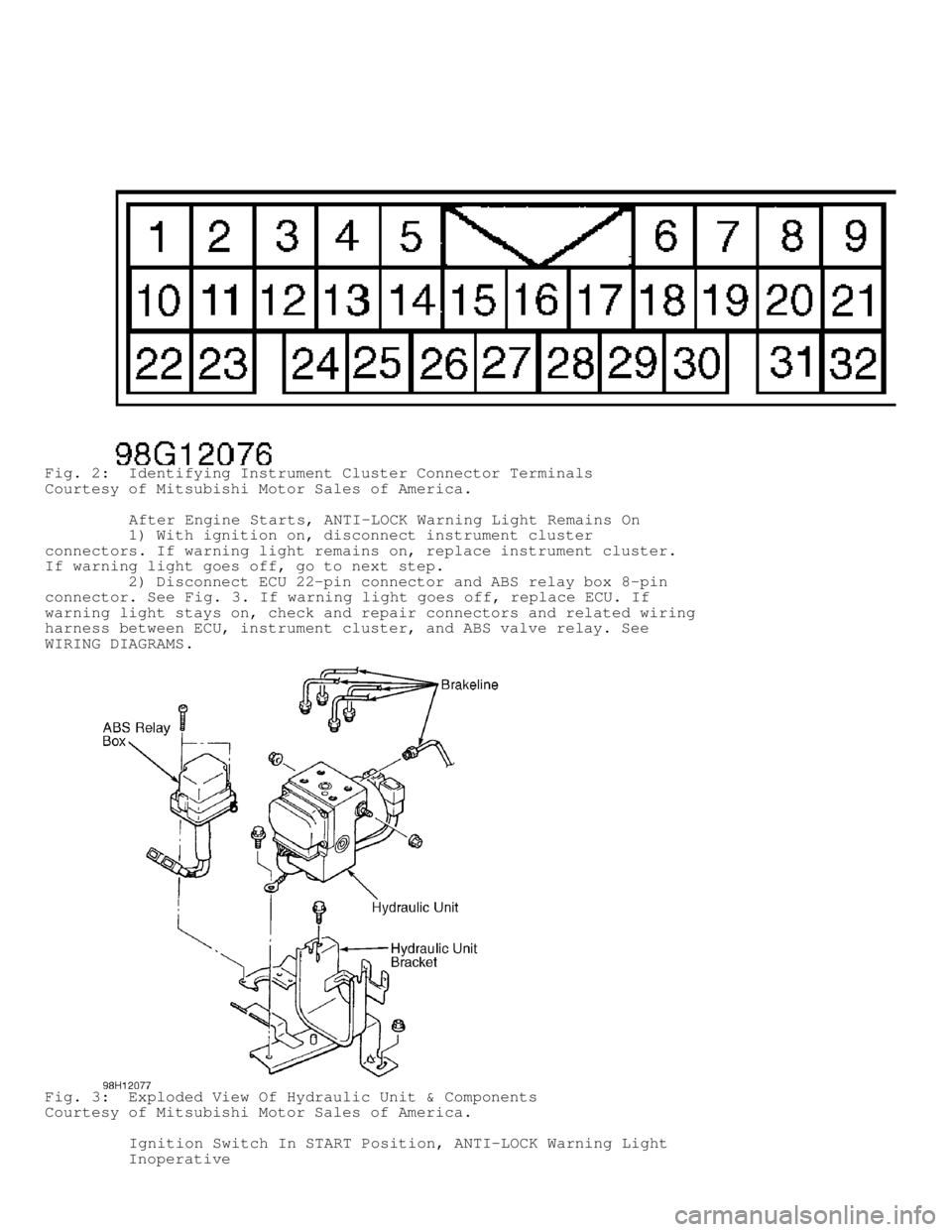
Fig. 2: Identifying Instrument Cluster Connector Terminals
Courtesy of Mitsubishi Motor Sales of America.
After Engine Starts, ANTI-LOCK Warning Light Remains On
1) With ignition on, disconnect instrument cluster
connectors. If warning light remains on, replace instrument cluster.
If warning light goes off, go to next step.
2) Disconnect ECU 22-pin connector and ABS relay box 8-pin
connector. See Fig. 3. If warning light goes off, replace ECU. If
warning light stays on, check and repair connectors and related wiring
harness between ECU, instrument cluster, and ABS valve relay. See
WIRING DIAGRAMS .
Fig. 3: Exploded View Of Hydraulic Unit & Components
Courtesy of Mitsubishi Motor Sales of America.
Ignition Switch In START Position, ANTI-LOCK Warning Light
Inoperative
Page 138 of 1501
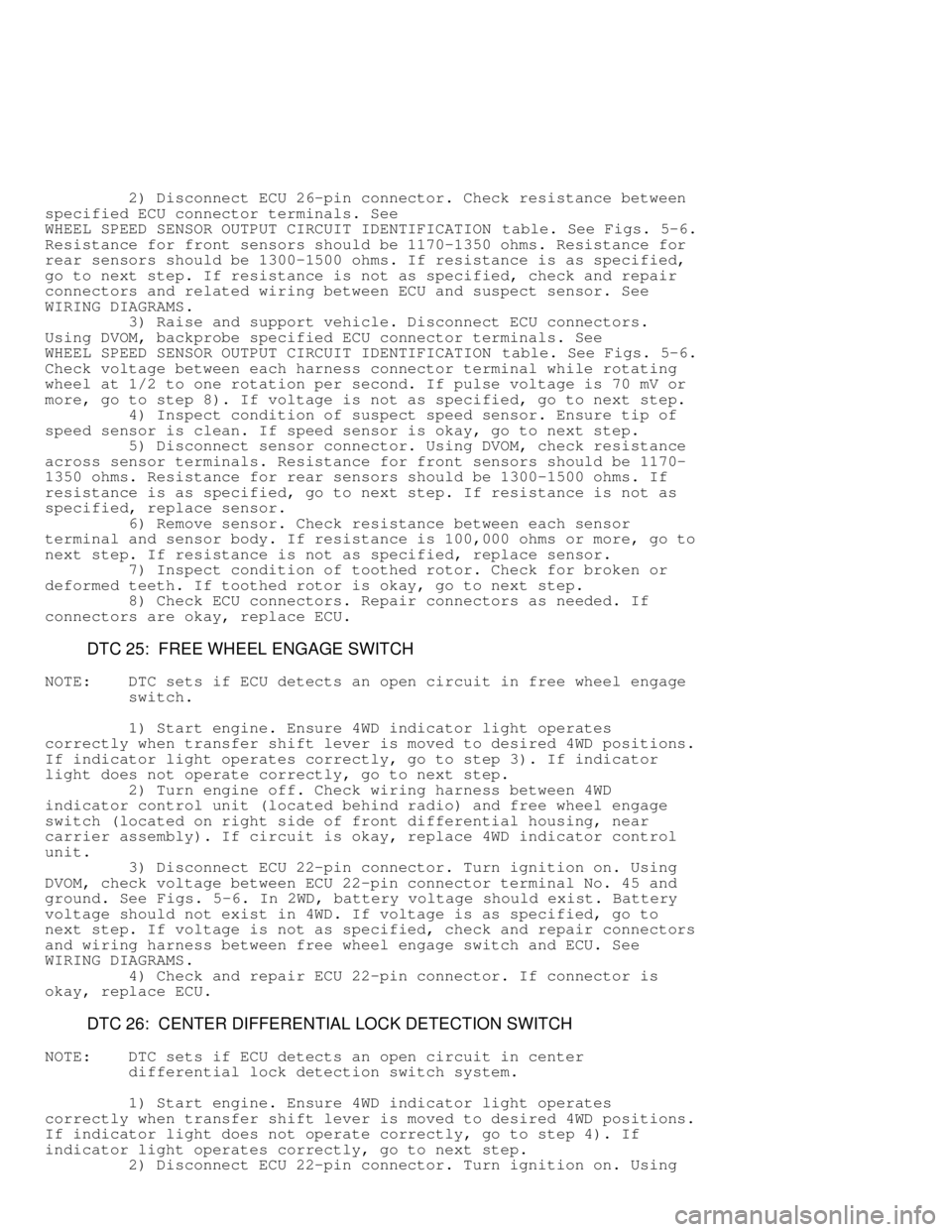
2) Disconnect ECU 26-pin connector. Check resistance between
specified ECU connector terminals. See
WHEEL SPEED SENSOR OUTPUT CIRCUIT IDENTIFICATION table. See Figs. 5-6.
Resistance for front sensors should be 1170-1350 ohms. Resistance for
rear sensors should be 1300-1500 ohms. If resistance is as specified,
go to next step. If resistance is not as specified, check and repair
connectors and related wiring between ECU and suspect sensor. See
WIRING DIAGRAMS .
3) Raise and support vehicle. Disconnect ECU connectors.
Using DVOM, backprobe specified ECU connector terminals. See
WHEEL SPEED SENSOR OUTPUT CIRCUIT IDENTIFICATION table. See Figs. 5-6.
Check voltage between each harness connector terminal while rotating
wheel at 1/2 to one rotation per second. If pulse voltage is 70 mV or
more, go to step 8). If voltage is not as specified, go to next step.
4) Inspect condition of suspect speed sensor. Ensure tip of
speed sensor is clean. If speed sensor is okay, go to next step.
5) Disconnect sensor connector. Using DVOM, check resistance
across sensor terminals. Resistance for front sensors should be 1170-
1350 ohms. Resistance for rear sensors should be 1300-1500 ohms. If
resistance is as specified, go to next step. If resistance is not as
specified, replace sensor.
6) Remove sensor. Check resistance between each sensor
terminal and sensor body. If resistance is 100,000 ohms or more, go to
next step. If resistance is not as specified, replace sensor.
7) Inspect condition of toothed rotor. Check for broken or
deformed teeth. If toothed rotor is okay, go to next step.
8) Check ECU connectors. Repair connectors as needed. If
connectors are okay, replace ECU.
DTC 25: FREE WHEEL ENGAGE SWITCH
NOTE: DTC sets if ECU detects an open circuit in free wheel engage
switch.
1) Start engine. Ensure 4WD indicator light operates
correctly when transfer shift lever is moved to desired 4WD positions.
If indicator light operates correctly, go to step 3). If indicator
light does not operate correctly, go to next step.
2) Turn engine off. Check wiring harness between 4WD
indicator control unit (located behind radio) and free wheel engage
switch (located on right side of front differential housing, near
carrier assembly). If circuit is okay, replace 4WD indicator control
unit.
3) Disconnect ECU 22-pin connector. Turn ignition on. Using
DVOM, check voltage between ECU 22-pin connector terminal No. 45 and
ground. See Figs. 5-6. In 2WD, battery voltage should exist. Battery
voltage should not exist in 4WD. If voltage is as specified, go to
next step. If voltage is not as specified, check and repair connectors
and wiring harness between free wheel engage switch and ECU. See
WIRING DIAGRAMS .
4) Check and repair ECU 22-pin connector. If connector is
okay, replace ECU.
DTC 26: CENTER DIFFERENTIAL LOCK DETECTION SWITCH
NOTE: DTC sets if ECU detects an open circuit in center
differential lock detection switch system.
1) Start engine. Ensure 4WD indicator light operates
correctly when transfer shift lever is moved to desired 4WD positions.
If indicator light does not operate correctly, go to step 4). If
indicator light operates correctly, go to next step.
2) Disconnect ECU 22-pin connector. Turn ignition on. Using
Page 140 of 1501
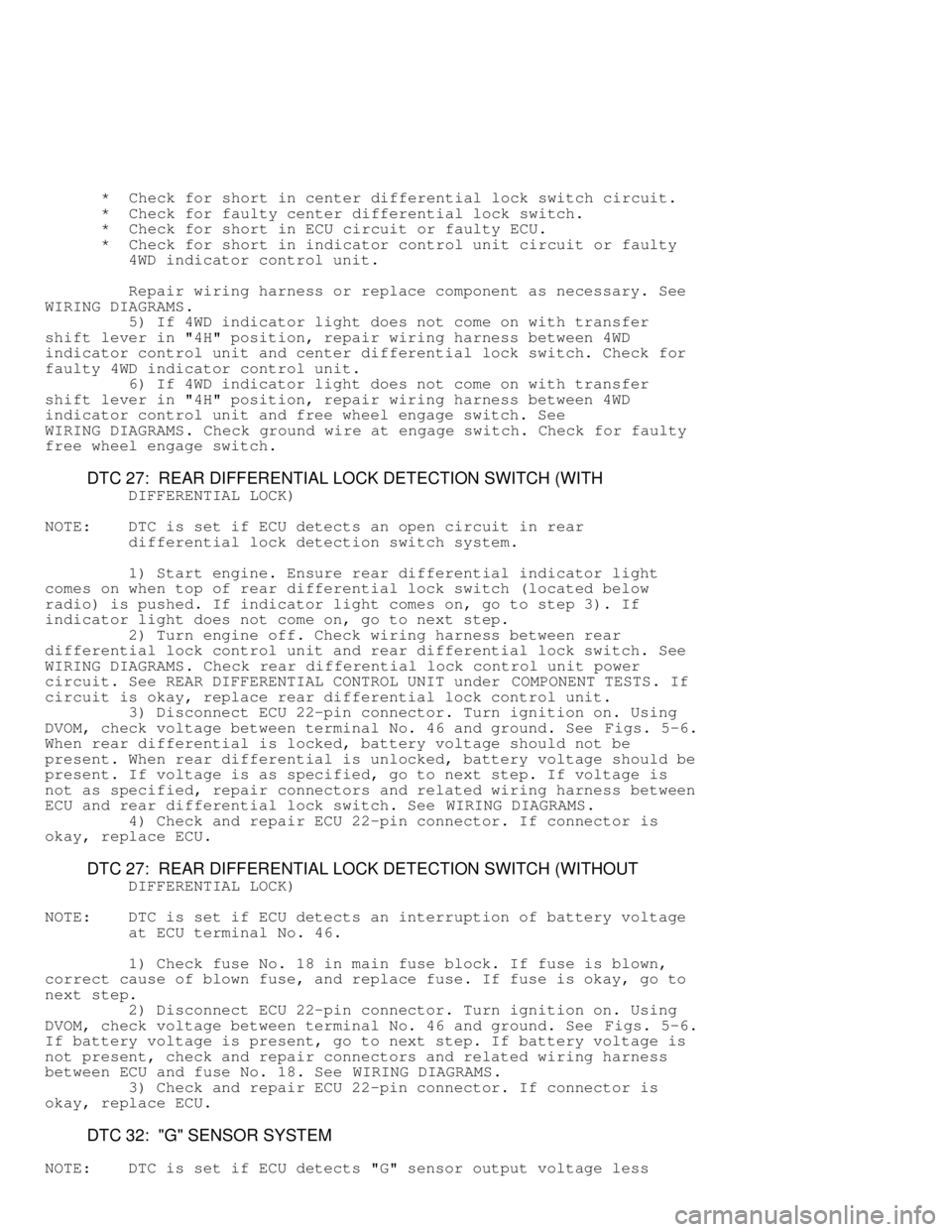
* Check for short in center differential lock switch circuit.
* Check for faulty center differential lock switch.
* Check for short in ECU circuit or faulty ECU.
* Check for short in indicator control unit circuit or faulty
4WD indicator control unit.
Repair wiring harness or replace component as necessary. See
WIRING DIAGRAMS .
5) If 4WD indicator light does not come on with transfer
shift lever in "4H" position, repair wiring harness between 4WD
indicator control unit and center differential lock switch. Check for
faulty 4WD indicator control unit.
6) If 4WD indicator light does not come on with transfer
shift lever in "4H" position, repair wiring harness between 4WD
indicator control unit and free wheel engage switch. See
WIRING DIAGRAMS . Check ground wire at engage switch. Check for faulty
free wheel engage switch.
DTC 27: REAR DIFFERENTIAL LOCK DETECTION SWITCH (WITH
DIFFERENTIAL LOCK)
NOTE: DTC is set if ECU detects an open circuit in rear
differential lock detection switch system.
1) Start engine. Ensure rear differential indicator light
comes on when top of rear differential lock switch (located below
radio) is pushed. If indicator light comes on, go to step 3). If
indicator light does not come on, go to next step.
2) Turn engine off. Check wiring harness between rear
differential lock control unit and rear differential lock switch. See
WIRING DIAGRAMS . Check rear differential lock control unit power
circuit. See REAR DIFFERENTIAL CONTROL UNIT under COMPONENT TESTS. If
circuit is okay, replace rear differential lock control unit.
3) Disconnect ECU 22-pin connector. Turn ignition on. Using
DVOM, check voltage between terminal No. 46 and ground. See Figs. 5-6.
When rear differential is locked, battery voltage should not be
present. When rear differential is unlocked, battery voltage should be
present. If voltage is as specified, go to next step. If voltage is
not as specified, repair connectors and related wiring harness between
ECU and rear differential lock switch. See WIRING DIAGRAMS.
4) Check and repair ECU 22-pin connector. If connector is
okay, replace ECU.
DTC 27: REAR DIFFERENTIAL LOCK DETECTION SWITCH (WITHOUT
DIFFERENTIAL LOCK)
NOTE: DTC is set if ECU detects an interruption of battery voltage
at ECU terminal No. 46.
1) Check fuse No. 18 in main fuse block. If fuse is blown,
correct cause of blown fuse, and replace fuse. If fuse is okay, go to
next step.
2) Disconnect ECU 22-pin connector. Turn ignition on. Using
DVOM, check voltage between terminal No. 46 and ground. See Figs. 5-6.
If battery voltage is present, go to next step. If battery voltage is
not present, check and repair connectors and related wiring harness
between ECU and fuse No. 18. See WIRING DIAGRAMS.
3) Check and repair ECU 22-pin connector. If connector is
okay, replace ECU.
DTC 32: "G" SENSOR SYSTEM
NOTE: DTC is set if ECU detects "G" sensor output voltage less
Page 156 of 1501
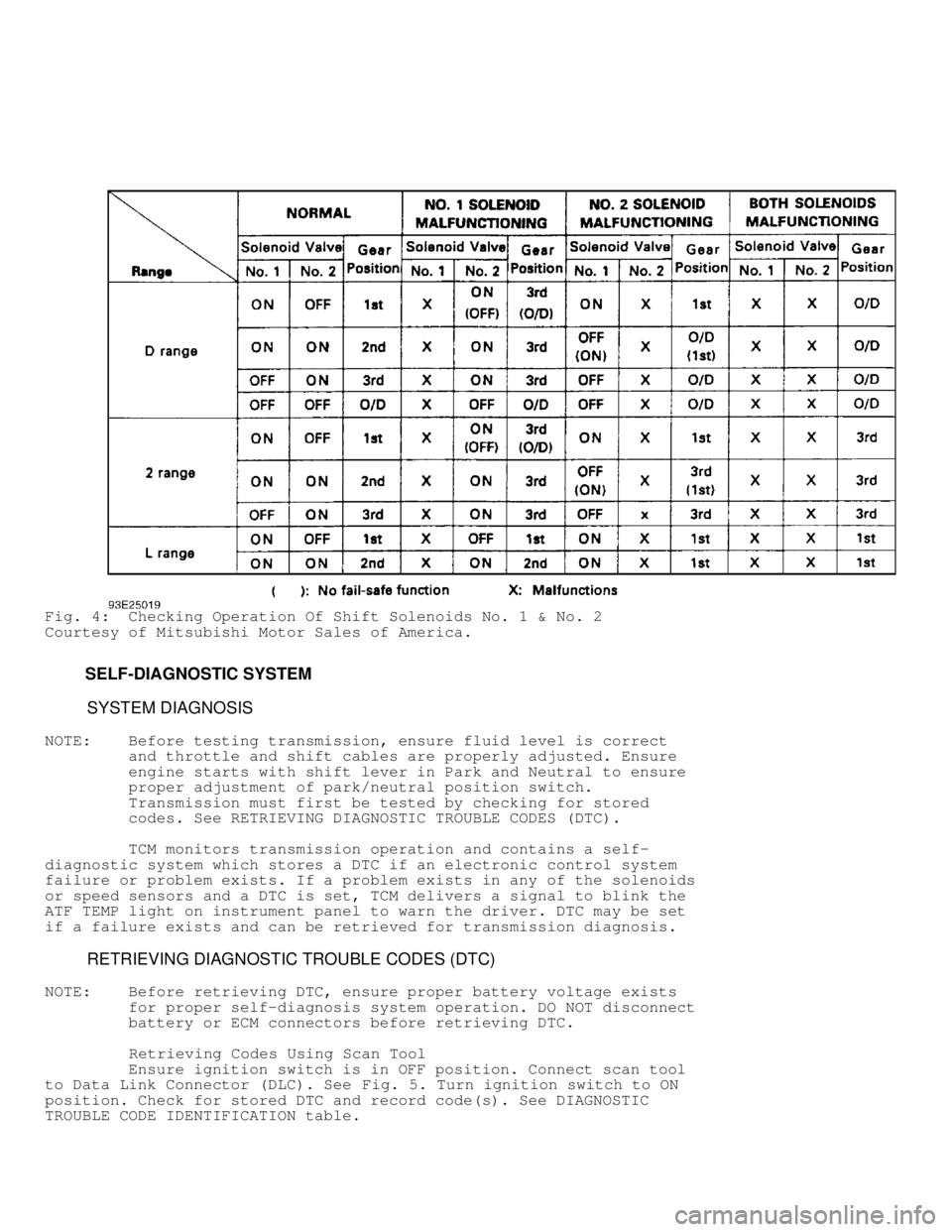
Fig. 4: Checking Operation Of Shift Solenoids No. 1 & No. 2
Courtesy of Mitsubishi Motor Sales of America.
SELF-DIAGNOSTIC SYSTEM
SYSTEM DIAGNOSIS
NOTE: Before testing transmission, ensure fluid level is correct
and throttle and shift cables are properly adjusted. Ensure
engine starts with shift lever in Park and Neutral to ensure
proper adjustment of park/neutral position switch.
Transmission must first be tested by checking for stored
codes. See RETRIEVING DIAGNOSTIC TROUBLE CODES (DTC).
TCM monitors transmission operation and contains a self-
diagnostic system which stores a DTC if an electronic control system
failure or problem exists. If a problem exists in any of the solenoids
or speed sensors and a DTC is set, TCM delivers a signal to blink the
ATF TEMP light on instrument panel to warn the driver. DTC may be set
if a failure exists and can be retrieved for transmission diagnosis.
RETRIEVING DIAGNOSTIC TROUBLE CODES (DTC)
NOTE: Before retrieving DTC, ensure proper battery voltage exists
for proper self-diagnosis system operation. DO NOT disconnect
battery or ECM connectors before retrieving DTC.
Retrieving Codes Using Scan Tool
Ensure ignition switch is in OFF position. Connect scan tool
to Data Link Connector (DLC). See Fig. 5. Turn ignition switch to ON
position. Check for stored DTC and record code(s). See DIAGNOSTIC
TROUBLE CODE IDENTIFICATION table.
Page 164 of 1501
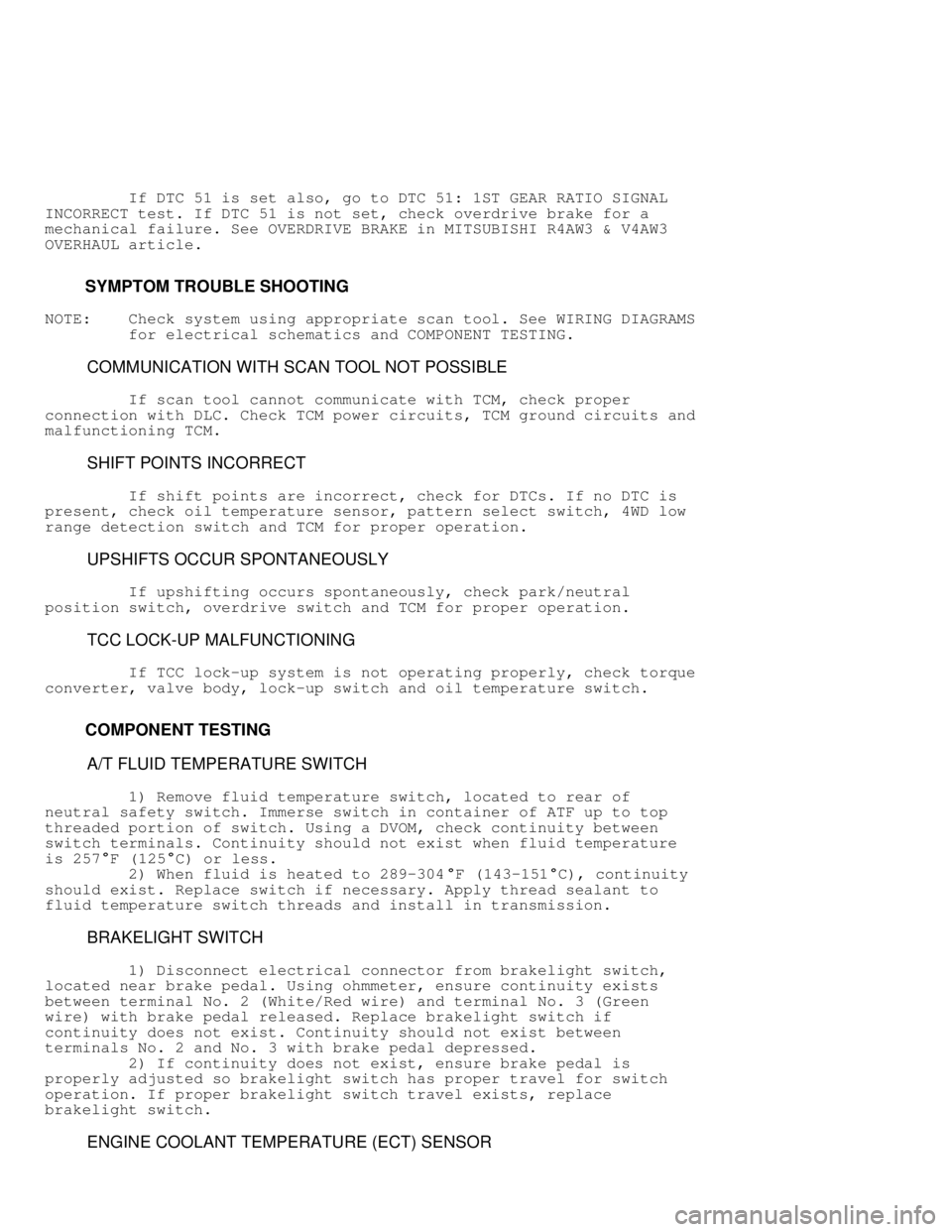
If DTC 51 is set also, go to DTC 51: 1ST GEAR RATIO SIGNAL
INCORRECT test. If DTC 51 is not set, check overdrive brake for a
mechanical failure. See OVERDRIVE BRAKE in MITSUBISHI R4AW3 & V4AW3
OVERHAUL article.
SYMPTOM TROUBLE SHOOTING
NOTE: Check system using appropriate scan tool. See WIRING DIAGRAMS
for electrical schematics and COMPONENT TESTING.
COMMUNICATION WITH SCAN TOOL NOT POSSIBLE
If scan tool cannot communicate with TCM, check proper
connection with DLC. Check TCM power circuits, TCM ground circuits and
malfunctioning TCM.
SHIFT POINTS INCORRECT
If shift points are incorrect, check for DTCs. If no DTC is
present, check oil temperature sensor, pattern select switch, 4WD low
range detection switch and TCM for proper operation.
UPSHIFTS OCCUR SPONTANEOUSLY
If upshifting occurs spontaneously, check park/neutral
position switch, overdrive switch and TCM for proper operation.
TCC LOCK-UP MALFUNCTIONING
If TCC lock-up system is not operating properly, check torque
converter, valve body, lock-up switch and oil temperature switch.
COMPONENT TESTING
A/T FLUID TEMPERATURE SWITCH
1) Remove fluid temperature switch, located to rear of
neutral safety switch. Immerse switch in container of ATF up to top
threaded portion of switch. Using a DVOM, check continuity between
switch terminals. Continuity should not exist when fluid temperature
is 257
F (125C) or less.
2) When fluid is heated to 289-304F (143-151C), continuity
should exist. Replace switch if necessary. Apply thread sealant to
fluid temperature switch threads and install in transmission.
BRAKELIGHT SWITCH
1) Disconnect electrical connector from brakelight switch,
located near brake pedal. Using ohmmeter, ensure continuity exists
between terminal No. 2 (White/Red wire) and terminal No. 3 (Green
wire) with brake pedal released. Replace brakelight switch if
continuity does not exist. Continuity should not exist between
terminals No. 2 and No. 3 with brake pedal depressed.
2) If continuity does not exist, ensure brake pedal is
properly adjusted so brakelight switch has proper travel for switch
operation. If proper brakelight switch travel exists, replace
brakelight switch.
ENGINE COOLANT TEMPERATURE (ECT) SENSOR
Page 168 of 1501
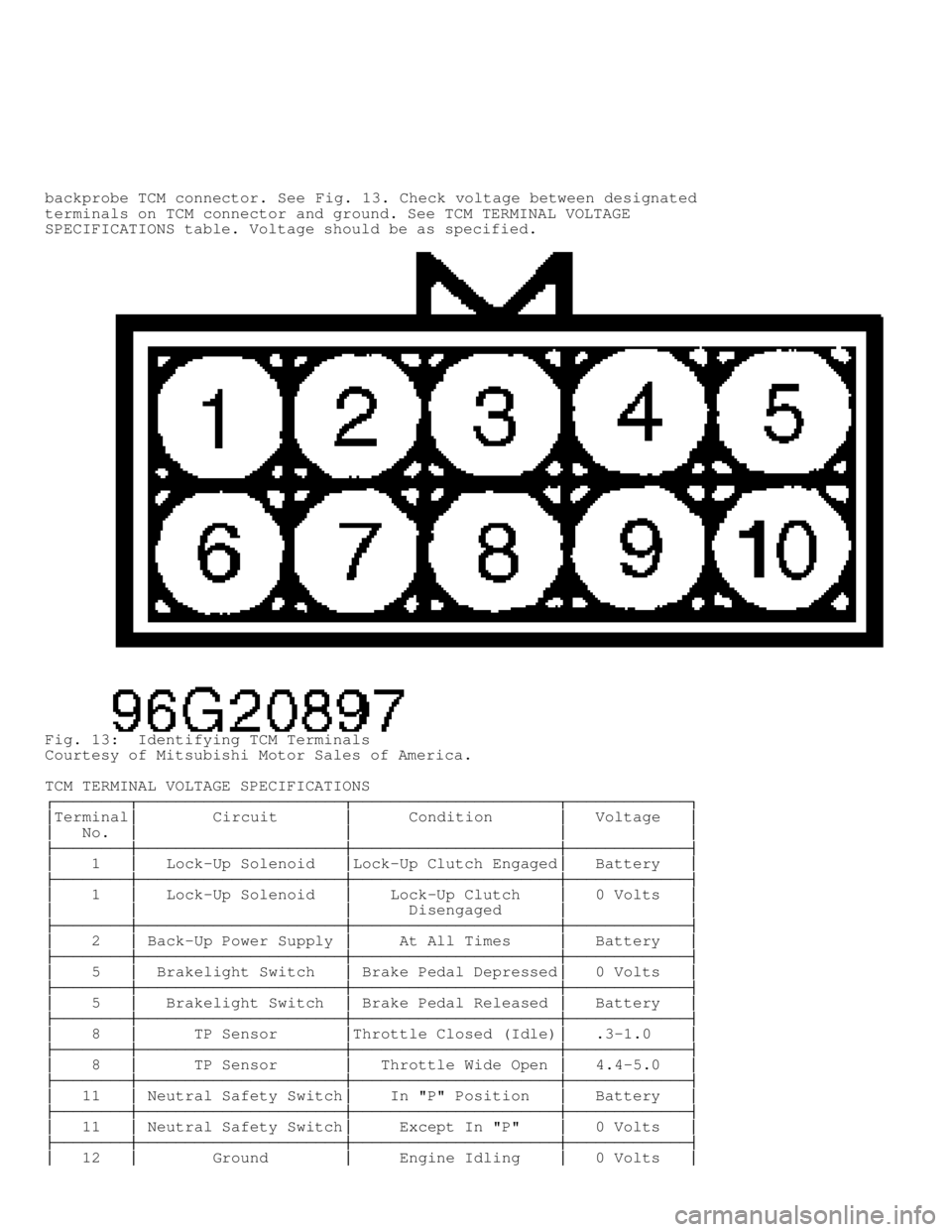
backprobe TCM connector. See Fig. 13. Check voltage between designated
terminals on TCM connector and ground. See TCM TERMINAL VOLTAGE
SPECIFICATIONS table. Voltage should be as specified.
Fig. 13: Identifying TCM Terminals
Courtesy of Mitsubishi Motor Sales of America.
TCM TERMINAL VOLTAGE SPECIFICATIONS
\
\
\
\
\
\
\
Terminal Circuit Condition Voltage
No.
\b
\
\
\
\
\
\
\
1 Lock-Up Solenoid Lock-Up Clutch Engaged Battery
\b
\
\
\
\
\
\
\
1 Lock-Up Solenoid Lock-Up Clutch 0 Volts
Disengaged
\b
\
\
\
\
\
\
\
2 Back-Up Power Supply At All Times Battery
\b
\
\
\
\
\
\
\
5 Brakelight Switch Brake Pedal Depressed 0 Volts
\b
\
\
\
\
\
\
\
5 Brakelight Switch Brake Pedal Released Battery
\b
\
\
\
\
\
\
\
8 TP Sensor Throttle Closed (Idle) .3-1.0
\b
\
\
\
\
\
\
\
8 TP Sensor Throttle Wide Open 4.4-5.0
\b
\
\
\
\
\
\
\
11 Neutral Safety Switch In "P" Position Battery
\b
\
\
\
\
\
\
\
11 Neutral Safety Switch Except In "P" 0 Volts
\b
\
\
\
\
\
\
\
12 Ground Engine Idling 0 Volts