dashboard NISSAN PULSAR 1987 Workshop Manual
[x] Cancel search | Manufacturer: NISSAN, Model Year: 1987, Model line: PULSAR, Model: NISSAN PULSAR 1987Pages: 238, PDF Size: 28.91 MB
Page 4 of 238
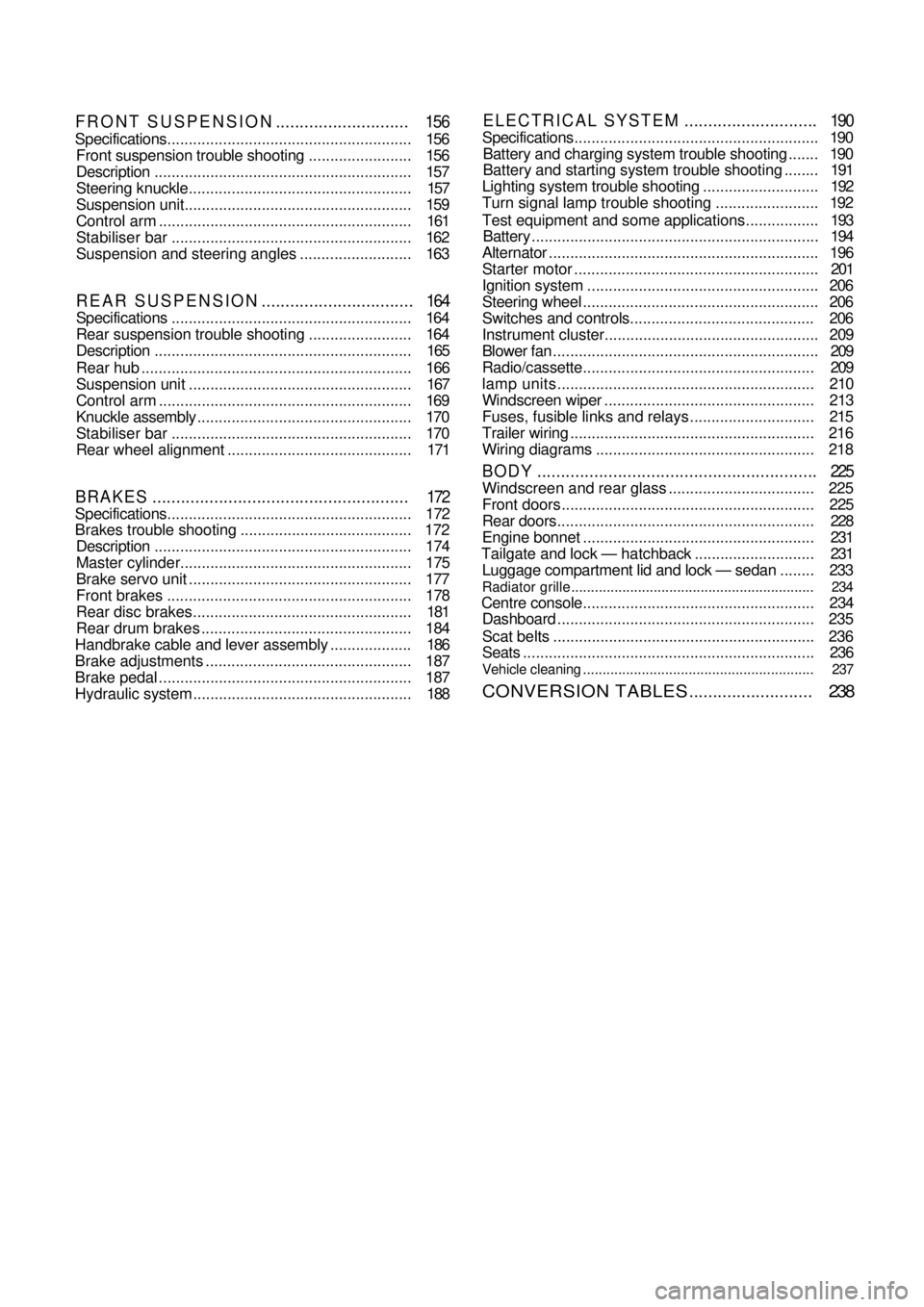
FRONT SUSPENSION............................ 156
Specifications......................................................... 156
Front suspension tr ouble shooting ........................ 156
Description ............................................................ 157
Steering knuckle.................................................... 157
Suspension unit..................................................... 159
Control arm ........................................................... 161
Stabiliser bar ........................................................ 162
Suspension and steering angles .......................... 163
REAR SUSPENSION................................ 164
Specifications ........................................................ 164
Rear suspension tr ouble shooting ........................ 164
Description ............................................................ 165
Rear hub ............................................................... 166
Suspension unit .................................................... 167
Control arm ........................................................... 169
Knuckle assembly.................................................. 170
Stabiliser bar ........................................................ 170
Rear wheel alignment ........................................... 171
BRAKES...................................................... 172
Specifications......................................................... 172
Brakes trouble shooting ........................................ 172
Description ............................................................ 174
Master cyli nder...................................................... 175
Brake servo unit .................................................... 177
Front brakes ......................................................... 178
Rear disc brakes................................................... 181
Rear drum brakes ................................................. 184
Handbrake cable and le ver assembly ................... 186
Brake adjustments ................................................ 187
Brake pedal ........................................................... 187
Hydraulic system................................................... 188
ELECTRICAL SYSTEM............................ 190
Specifications......................................................... 190
Battery and charging system trouble shooting ....... 190
Battery and starting system trouble shooting ........ 191
Lighting system trouble shooting ........................... 192
Turn signal lamp trouble shooting ........................ 192
Test equipment and so me applications................. 193
Battery ................................................................... 194
Alternator ............................................................... 196
Starter motor ......................................................... 201
Ignition system ...................................................... 206
Steering wheel ....................................................... 206
Switches and controls........................................... 206
Instrument cluster.................................................. 209
Blower fan .............................................................. 209
Radio/cassette...................................................... 209
lamp units ............................................................ 210
Windscreen wiper ................................................. 213
Fuses, fusible links and relays ............................. 215
Trailer wiring ......................................................... 216
Wiring diagrams ................................................... 218
BODY........................................................... 225
Windscreen and re ar glass .................................. 225
Front doors ........................................................... 225
Rear doors............................................................ 228
Engine bonnet...................................................... 231
Tailgate and lock — hatchback ............................ 231
Luggage compartment lid and lock — sedan ........ 233
Radiator grille.............................................................. 234
Centre console...................................................... 234 Dashboard ............................................................ 235
Scat belts ............................................................. 236
Seats .................................................................... 236
Vehicle cleaning ........................................................... 237
CONVERSION TABLES.......................... 238
Page 33 of 238
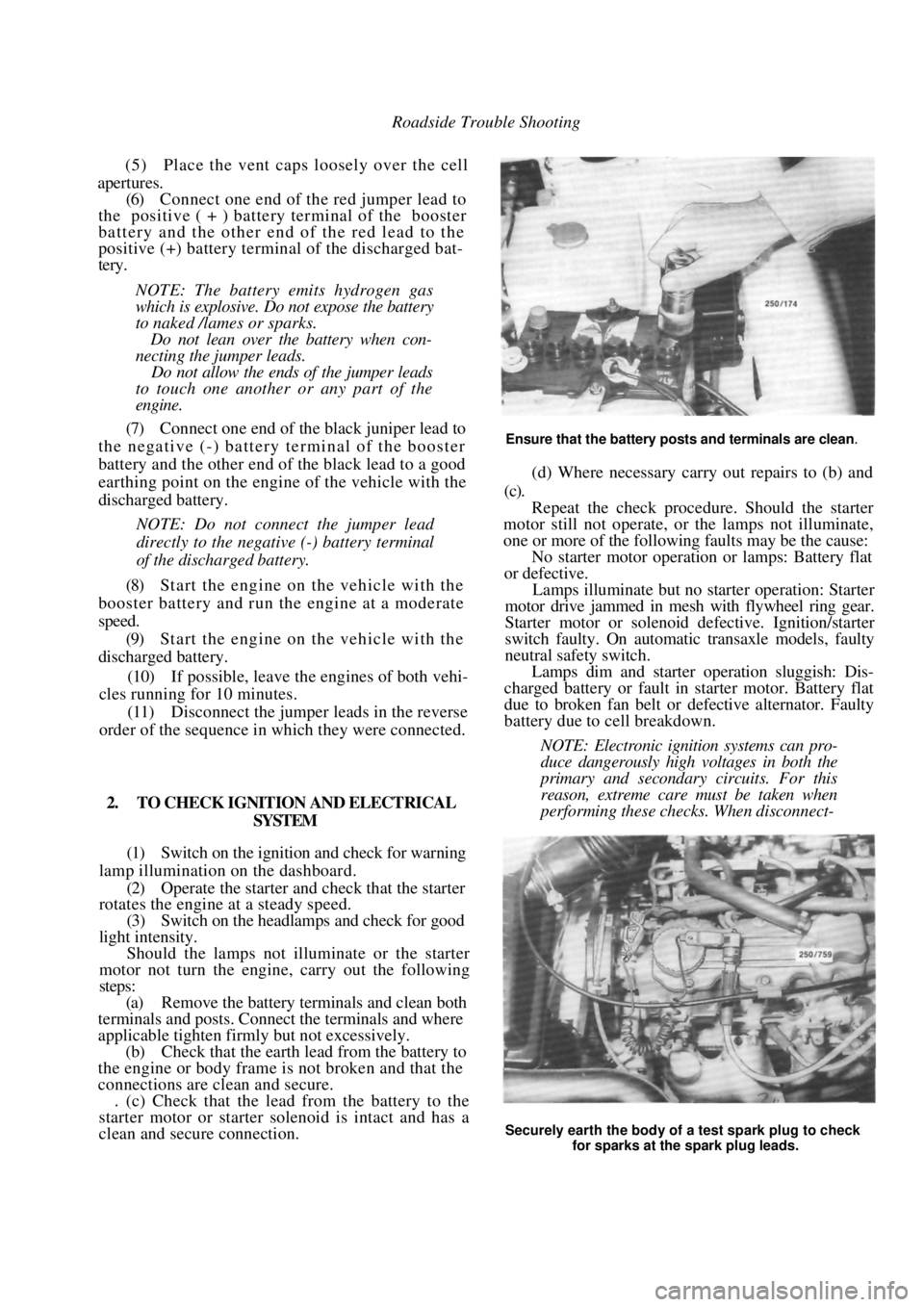
Roadside Trouble Shooting
(5) Place the vent caps loosely over the cell
apertures.
(6) Connect one end of the red jumper lead to
the positive ( + ) battery terminal of the booster
battery and the other end of the red lead to the
positive (+) battery terminal of the discharged bat-
tery.
NOTE: The battery emits hydrogen gas
which is explosive. Do not expose the battery
to naked /lames or sparks.
Do not lean over the battery when con-
necting the jumper leads.
Do not allow the ends of the jumper leads
to touch one another or any part of the
engine.
(7) Connect one end of the black juniper lead to
the negative (-) battery terminal of the booster
battery and the other end of the black lead to a good
earthing point on the engine of the vehicle with the
discharged battery.
NOTE: Do not connect the jumper lead
directly to the negative (-) battery terminal
of the discharged battery.
(8) Start the engine on the vehicle with the
booster battery and run the engine at a moderate
speed. (9) Start the engine on the vehicle with the
discharged battery.
(10) If possible, leave the engines of both vehi-
cles running for 10 minutes.
(11) Disconnect the jumper leads in the reverse
order of the sequence in which they were connected.
2. TO CHECK IGNITION AND ELECTRICAL SYSTEM
(1) Switch on the ignition and check for warning
lamp illumination on the dashboard. (2) Operate the starter and check that the starter
rotates the engine at a steady speed.
(3) Switch on the headlamps and check for good
light intensity. Should the lamps not illum inate or the starter
motor not turn the engine, carry out the following
steps:
(a) Remove the battery terminals and clean both
terminals and posts. Connect the terminals and where
applicable tighten firmly but not excessively.
(b) Check that the earth lead from the battery to
the engine or body frame is not broken and that the
connections are clean and secure. . (c) Check that the lead from the battery to the
starter motor or starter solenoid is intact and has a
clean and secure connection.
Ensure that the battery posts and terminals are clean.
(d) Where necessary carry out repairs to (b) and
(c).
Repeat the check procedur e. Should the starter
motor still not operate, or the lamps not illuminate,
one or more of the following faults may be the cause:
No starter motor operation or lamps: Battery flat
or defective.
Lamps illuminate but no starter operation: Starter
motor drive jammed in mesh with flywheel ring gear.
Starter motor or solenoid defective. Ignition/starter
switch faulty. On automatic transaxle models, faulty
neutral safety switch.
Lamps dim and starter operation sluggish: Dis-
charged battery or fault in starter motor. Battery flat
due to broken fan belt or de fective alternator. Faulty
battery due to cell breakdown.
NOTE: Electronic ignition systems can pro-
duce dangerously high voltages in both the
primary and secondary circuits. For this
reason, extreme care must be taken when
performing these checks. When disconnect-
Securely earth the body of a test spark plug to check
for sparks at the spark plug leads.
Page 78 of 238
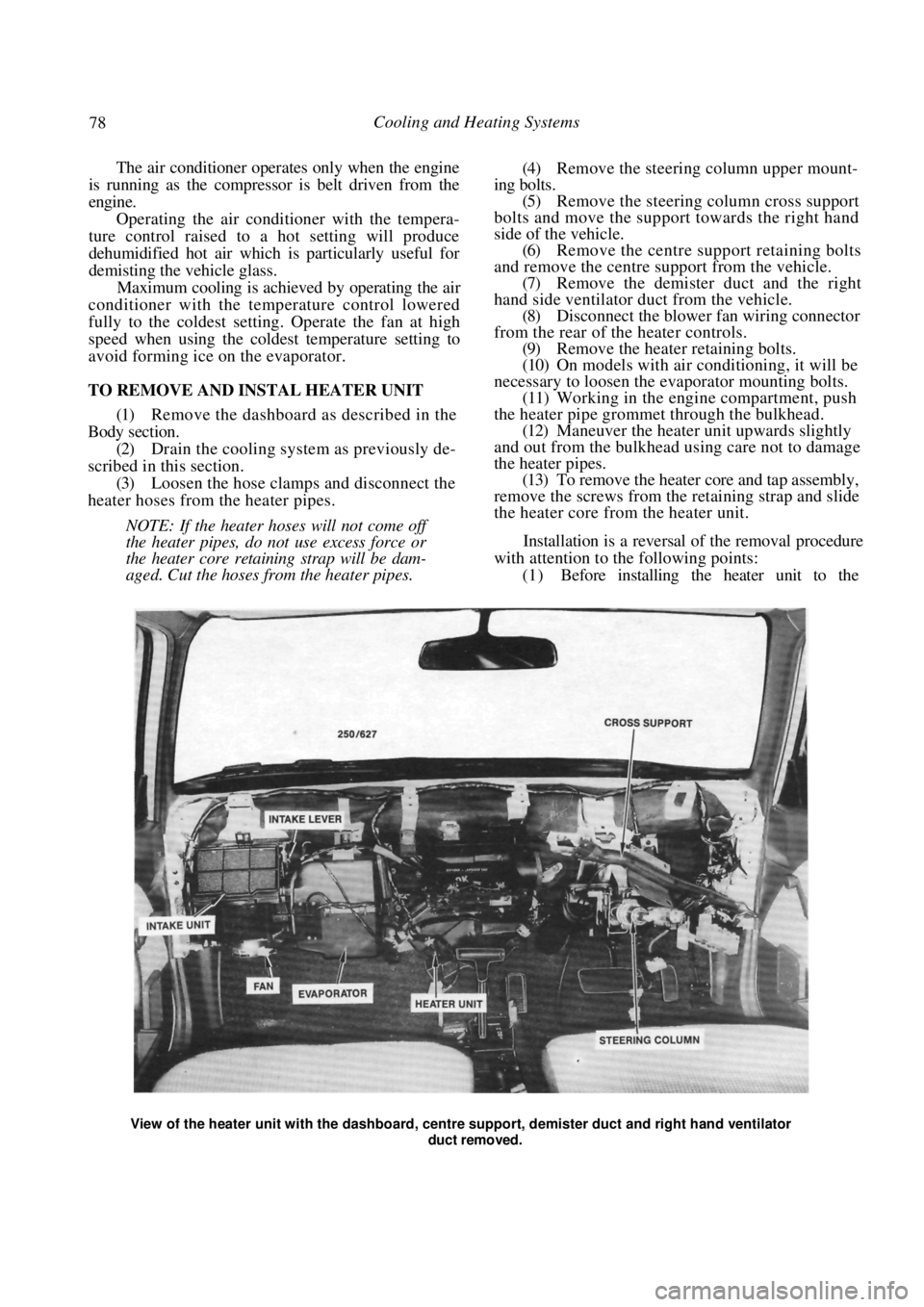
78 Cooling and Heating Systems
The air conditioner operates only when the engine
is running as the compressor is belt driven from the
engine.
Operating the air conditioner with the tempera-
ture control raised to a hot setting will produce
dehumidified hot air which is particularly useful for
demisting the vehicle glass.
Maximum cooling is achieved by operating the air
conditioner with the temperature control lowered
fully to the coldest setting . Operate the fan at high
speed when using the coldest temperature setting to
avoid forming ice on the evaporator.
TO REMOVE AND INSTAL HEATER UNIT
(1) Remove the dashboard as described in the
Body section. (2) Drain the cooling system as previously de-
scribed in this section. (3) Loosen the hose clamps and disconnect the
heater hoses from the heater pipes.
NOTE: If the heater hos es will not come off
the heater pipes, do not use excess force or
the heater core retaining strap will be dam-
aged. Cut the hoses from the heater pipes.
(4) Remove the steering column upper mount-
ing bolts. (5) Remove the steering column cross support
bolts and move the support towards the right hand
side of the vehicle. (6) Remove the centre support retaining bolts
and remove the centre support from the vehicle.
(7) Remove the demister duct and the right
hand side ventilator duct from the vehicle. (8) Disconnect the blower fan wiring connector
from the rear of the heater controls. (9) Remove the heater retaining bolts.
(10) On models with air conditioning, it will be
necessary to loosen the evaporator mounting bolts. (11) Working in the engine compartment, push
the heater pipe grommet through the bulkhead. (12) Maneuver the heater unit upwards slightly
and out from the bulkhead using care not to damage
the heater pipes. (13) To remove the heater core and tap assembly,
remove the screws from the retaining strap and slide
the heater core from the heater unit.
Installation is a reversal of the removal procedure
with attention to the following points:
(1 ) Before installing the heater unit to the
View of the heater unit with the dashboard, centr e support, demister duct and right hand ventilator
duct removed.
Page 79 of 238
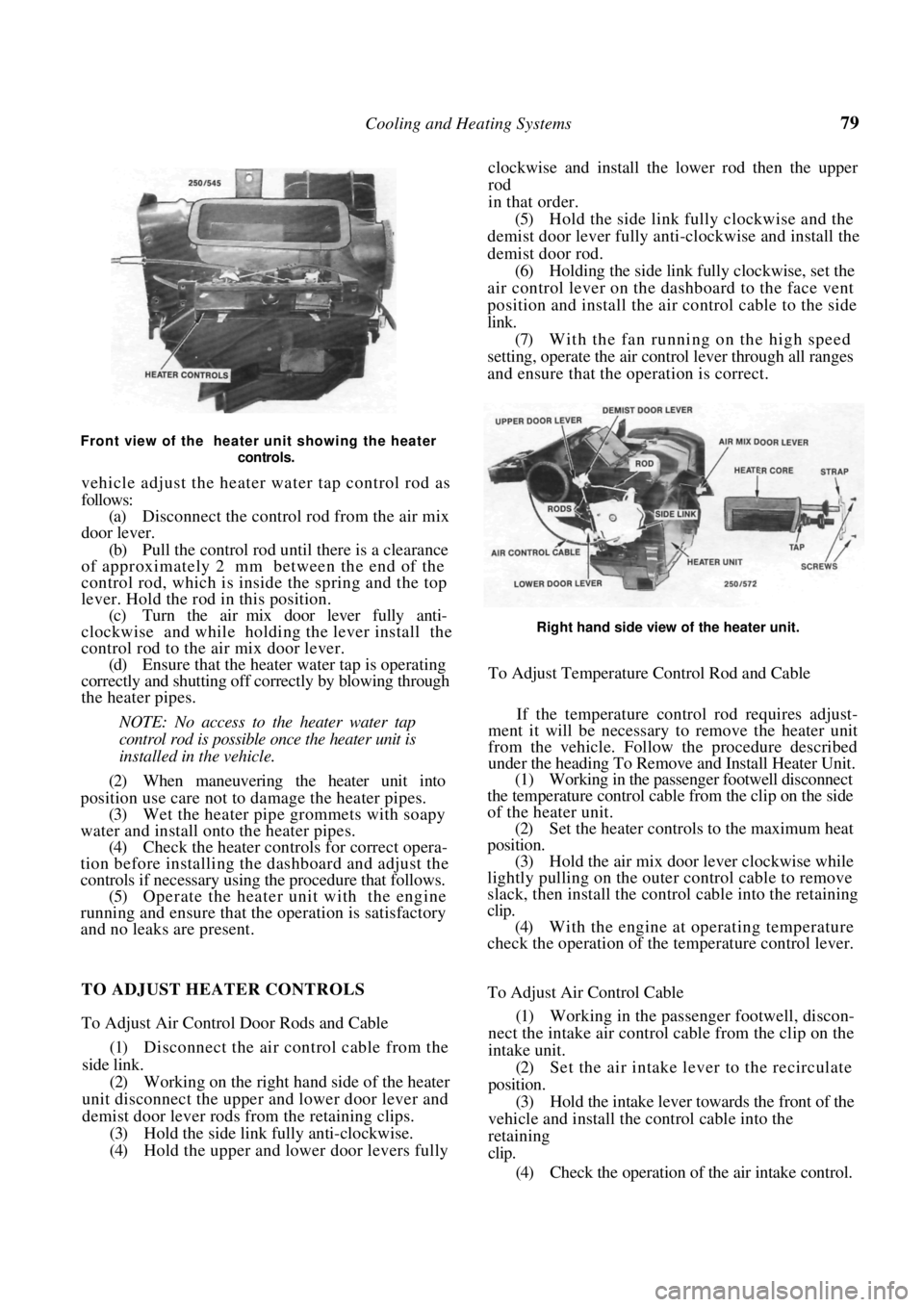
Cooling and Heating Systems 79
Front view of the heater unit showing the heater controls.
vehicle adjust the heater water tap control rod as
follows:
(a) Disconnect the control rod from the air mix
door lever.
(b) Pull the control rod un til there is a clearance
of approximately 2 mm between the end of the
control rod, which is inside the spring and the top
lever. Hold the rod in this position.
(c) Turn the air mix door lever fully anti-
clockwise and while holding the lever install the
control rod to the air mix door lever. (d) Ensure that the heater water tap is operating
correctly and shutting off correctly by blowing through
the heater pipes.
NOTE: No access to the heater water tap
control rod is possible once the heater unit is
installed in the vehicle.
(2) When maneuvering the heater unit into
position use care not to damage the heater pipes. (3) Wet the heater pipe grommets with soapy
water and install onto the heater pipes. (4) Check the heater controls for correct opera-
tion before installing the dashboard and adjust the
controls if necessary using the procedure that follows. (5) Operate the heater unit with the engine
running and ensure that the operation is satisfactory
and no leaks are present. clockwise and install the lower rod then the upper
rod
in that order.
(5)
Hold the side link fully clockwise and the
demist door lever fully anti-clockwise and install the
demist door rod. (6) Holding the side link fully clockwise, set the
air control lever on the dashboard to the face vent
position and install the air control cable to the side
link. (7) With the fan running on the high speed
setting, operate the air cont rol lever through all ranges
and ensure that the operation is correct.
Right hand side view of the heater unit.
To Adjust Temperature Control Rod and Cable
If the temperature control rod requires adjust-
ment it will be necessary to remove the heater unit
from the vehicle. Follow the procedure described
under the heading To Remove and Install Heater Unit.
(1) Working in the passenger footwell disconnect
the temperature control cable from the clip on the side
of the heater unit. (2) Set the heater controls to the maximum heat
position. (3) Hold the air mix door lever clockwise while
lightly pulling on the outer control cable to remove
slack, then install the control cable into the retaining
clip.
(4) With the engine at operating temperature
check the operation of the temperature control lever.
TO ADJUST HEATER CONTROLS
To Adjust Air Control Door Rods and Cable
(1) Disconnect the air control cable from the
side link. (2) Working on the right hand side of the heater
unit disconnect the upper and lower door lever and
demist door lever rods from the retaining clips.
(3) Hold the side link fully anti-clockwise.
(4) Hold the upper and lower door levers fully To Adjust Air Control Cable
(1)
Working in the passeng er footwell, discon-
nect the intake air control cable from the clip on the
intake unit. (2) Set the air intake lever to the recirculate
position. (3) Hold the intake lever to wards the front of the
vehicle and install the control cable into the
retaining
clip.
(4) Check the operation of the air intake control.
Page 122 of 238
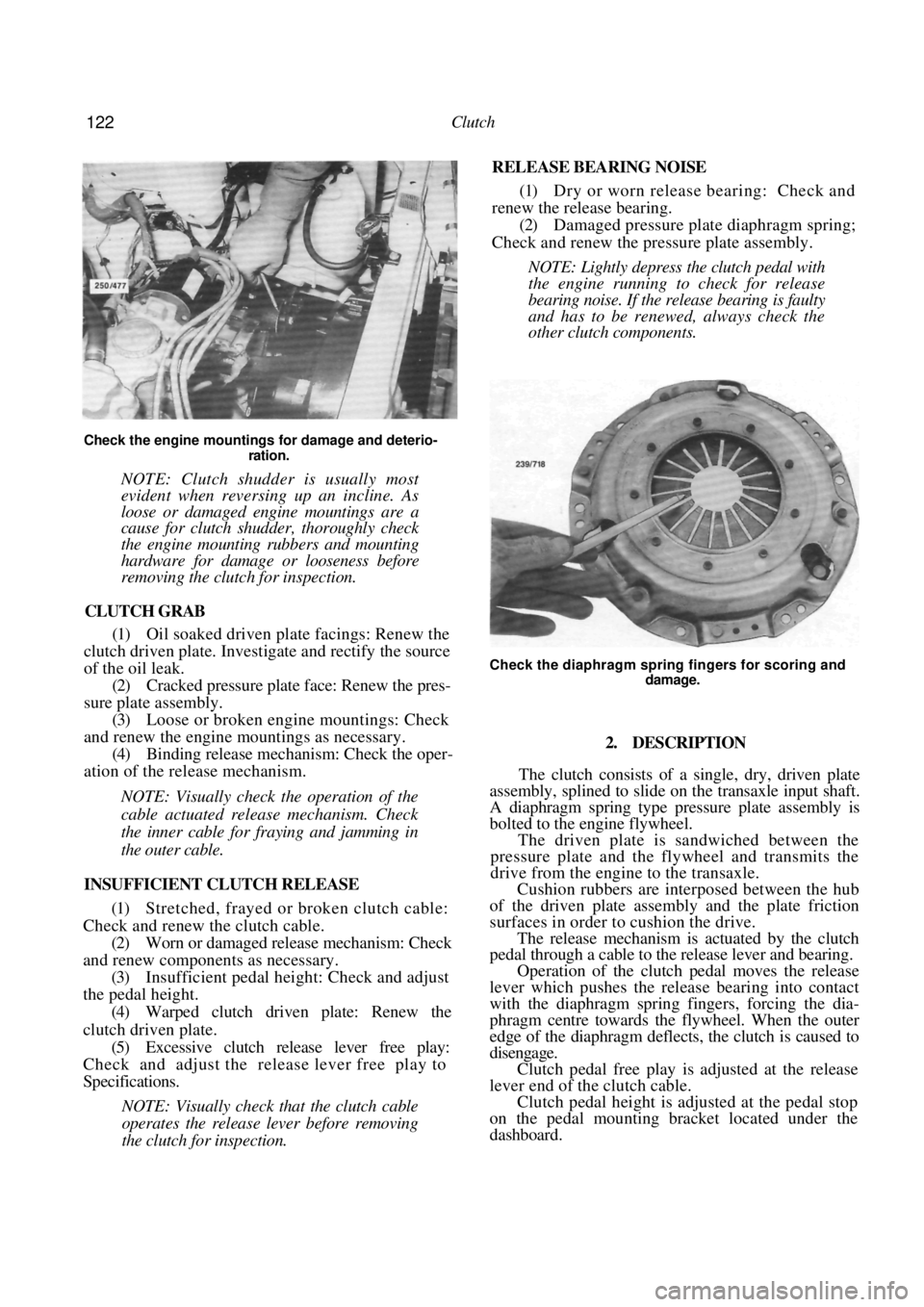
122 Clutch
Check the engine mountings for damage and deterio- ration.
NOTE: Clutch shudder is usually most
evident when reversing up an incline. As
loose or damaged engine mountings are a
cause for clutch shudder, thoroughly check
the engine mounting rubbers and mounting
hardware for damage or looseness before
removing the clutch for inspection.
CLUTCH GRAB
(1) Oil soaked driven plate facings: Renew the
clutch driven plate. Invest igate and rectify the source
of the oil leak.
(2) Cracked pressure plate face: Renew the pres-
sure plate assembly. (3) Loose or broken engine mountings: Check
and renew the engine mountings as necessary.
(4) Binding release mechanism: Check the oper-
ation of the release mechanism.
NOTE: Visually check the operation of the
cable actuated release mechanism. Check
the inner cable for fraying and jamming in
the outer cable.
INSUFFICIENT CLUTCH RELEASE
(1) Stretched, frayed or broken clutch cable:
Check and renew the clutch cable. (2) Worn or damaged release mechanism: Check
and renew components as necessary. (3) Insufficient pedal height: Check and adjust
the pedal height.
(4) Warped clutch driven plate: Renew the
clutch driven plate. (5) Excessive clutch release lever free play:
Check and adjust the release lever free play to
Specifications.
NOTE: Visually check that the clutch cable
operates the release lever before removing
the clutch for inspection.
RELEASE BEARING NOISE
(1) Dry or worn release bearing: Check and
renew the release bearing.
(2) Damaged pressure plate diaphragm spring;
Check and renew the pressure plate assembly.
NOTE: Lightly depress the clutch pedal with
the engine running to check for release
bearing noise. If the release bearing is faulty
and has to be renewed, always check the
other clutch components.
Check the diaphragm spring fingers for scoring and damage.
2. DESCRIPTION
The clutch consists of a single, dry, driven plate
assembly, splined to slide on the transaxle input shaft.
A diaphragm spring type pr essure plate assembly is
bolted to the engine flywheel.
The driven plate is sandwiched between the
pressure plate and the flywheel and transmits the
drive from the engine to the transaxle.
Cushion rubbers are interposed between the hub
of the driven plate assembly and the plate friction
surfaces in order to cushion the drive.
The release mechanism is actuated by the clutch
pedal through a cable to the release lever and bearing.
Operation of the clutch pedal moves the release
lever which pushes the release bearing into contact
with the diaphragm spring fingers, forcing the dia-
phragm centre towards the flywheel. When the outer
edge of the diaphragm deflects, the clutch is caused to
disengage.
Clutch pedal free play is adjusted at the release
lever end of the clutch cable.
Clutch pedal height is adjusted at the pedal stop
on the pedal mounting bracket located under the
dashboard.
Page 148 of 238
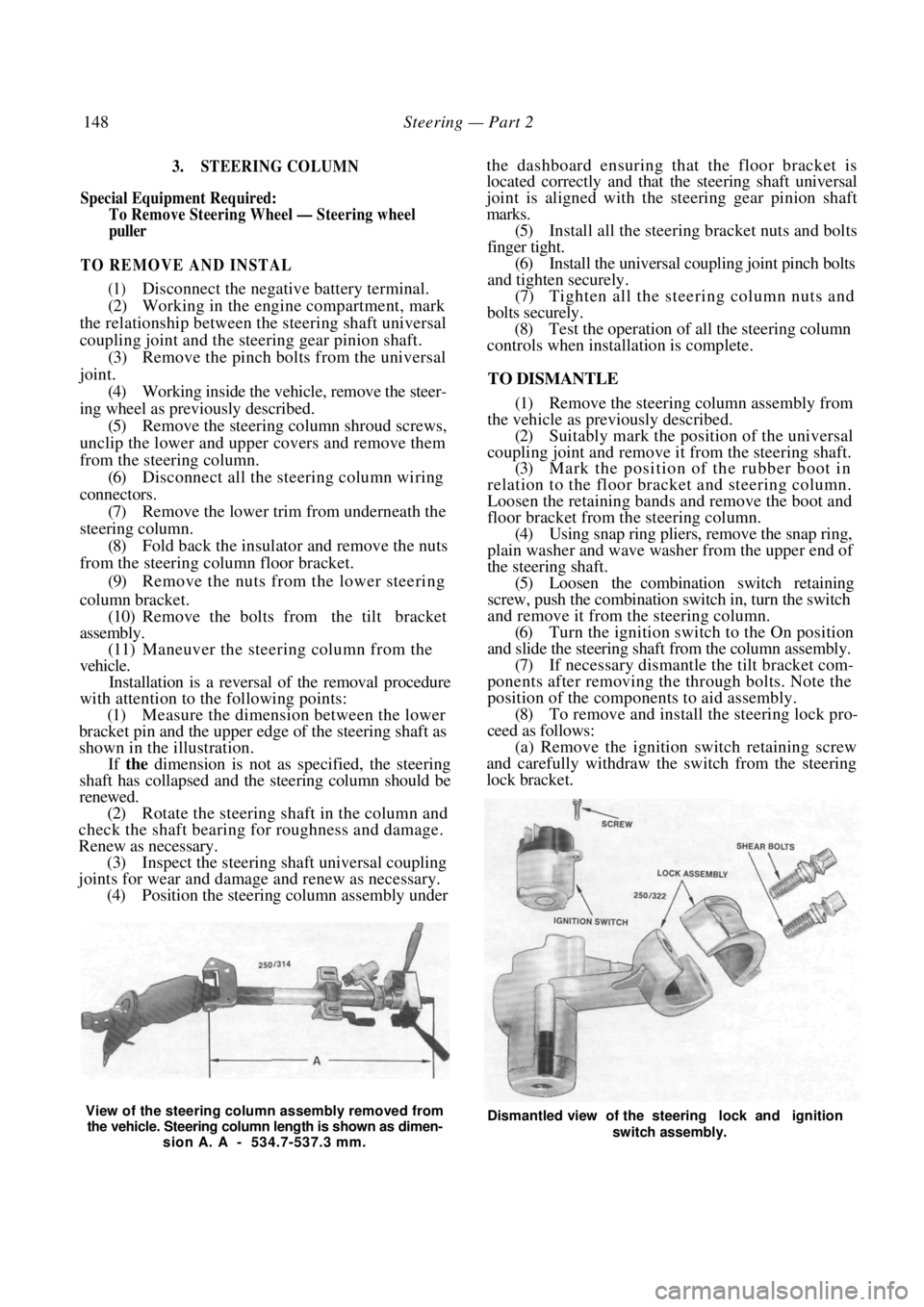
148 Steering — Part 2
3. STEERING COLUMN
Special Equipment Required:
To Remove Steering Wheel — Steering wheel
puller
TO REMOVE AND INSTAL
(1) Disconnect the negative battery terminal.
(2) Working in the engine compartment, mark
the relationship between the steering shaft universal
coupling joint and the steering gear pinion shaft. (3) Remove the pinch bolts from the universal
joint. (4) Working inside the vehi cle, remove the steer-
ing wheel as previously described. (5) Remove the steering column shroud screws,
unclip the lower and upper covers and remove them
from the steering column. (6) Disconnect all the steering column wiring
connectors. (7) Remove the lower trim from underneath the
steering column.
(8) Fold back the insulator and remove the nuts
from the steering colu mn floor bracket.
(9) Remove the nuts from the lower steering
column bracket. (10) Remove the bolts from the tilt bracket
assembly. (11) Maneuver the steering column from the
vehicle.
Installation is a reversal of the removal procedure
with attention to the following points:
(1) Measure the dimension between the lower
bracket pin and the upper edge of the steering shaft as
shown in the illustration.
If the dimension is not as specified, the steering
shaft has collapsed and the steering column should be
renewed.
(2) Rotate the steering shaft in the column and
check the shaft bearing for roughness and damage.
Renew as necessary. (3) Inspect the steering shaft universal coupling
joints for wear and damage and renew as necessary. (4) Position the steering column assembly under
the dashboard ensuring that the floor bracket is
located correctly and that the steering shaft universal
joint is aligned with the steering gear pinion shaft
marks.
(5) Install all the steering bracket nuts and bolts
finger tight. (6) Install the universal coupling joint pinch bolts
and tighten securely.
(7) Tighten all the stee ring column nuts and
bolts securely. (8) Test the operation of all the steering column
controls when installation is complete.
TO DISMANTLE
(1) Remove the steering column assembly from
the vehicle as previously described. (2) Suitably mark the position of the universal
coupling joint and remove it from the steering shaft. (3) Mark the position of the rubber boot in
relation to the floor bracket and steering column.
Loosen the retaining bands and remove the boot and
floor bracket from th e steering column.
(4) Using snap ring pliers, remove the snap ring,
plain washer and wave washer from the upper end of
the steering shaft. (5) Loosen the combination switch retaining
screw, push the combination switch in, turn the switch
and remove it from the steering column. (6) Turn the ignition switch to the On position
and slide the steering shaft from the column assembly. (7) If necessary dismantle the tilt bracket com-
ponents after removing the through bolts. Note the
position of the components to aid assembly. (8) To remove and install the steering lock pro-
ceed as follows: (a) Remove the ignition switch retaining screw
and carefully withdraw the switch from the steering
lock bracket.
View of the steering column assembly removed from
the vehicle. Steering column length is shown as dimen- sion A. A - 534.7-537.3 mm. Dismantled view of the steering lock and ignition
switch assembly.
Page 193 of 238
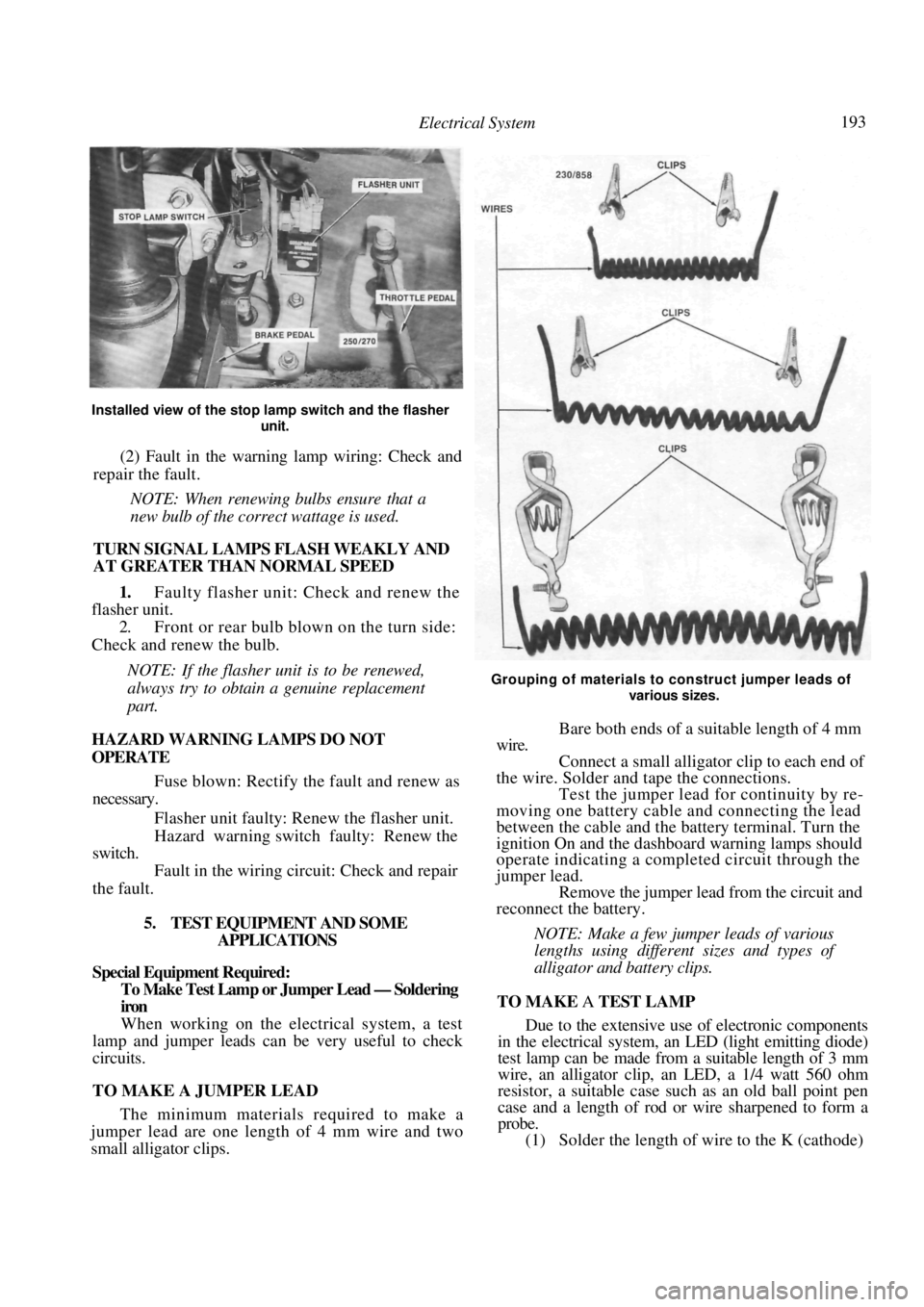
Electrical System 193
Installed view of the stop lamp switch and the flasher
unit.
(2) Fault in the warning lamp wiring: Check and
repair the fault.
NOTE: When renewing bulbs ensure that a
new bulb of the correct wattage is used.
TURN SIGNAL LAMPS FLASH WEAKLY AND
AT GREATER THAN NORMAL SPEED
1. Faulty flasher unit: Check and renew the
flasher unit.
2. Front or rear bulb blown on the turn side:
Check and renew the bulb.
NOTE: If the flasher unit is to be renewed,
always try to obtain a genuine replacement
part.
HAZARD WARNING LAMPS DO NOT
OPERATE
Fuse blown: Rectify the fault and renew as
necessary.
Flasher unit faulty: Re new the flasher unit.
Hazard warning switch faulty: Renew the
switch.
Fault in the wiring circuit: Check and repair
the fault.
5. TEST EQUIPMENT AND SOME APPLICATIONS
Special Equipment Required:
To Make Test Lamp or Jumper Lead — Soldering
iron
When working on the electrical system, a test
lamp and jumper leads can be very useful to check
circuits.
TO MAKE A JUMPER LEAD
The minimum materials required to make a
jumper lead are one length of 4 mm wire and two
small alligator clips.
Grouping of materials to construct jumper leads of
various sizes.
Bare both ends of a suitable length of 4 mm
wire. Connect a small alligato r clip to each end of
the wire. Solder and tape the connections. Test the jumper lead for continuity by re-
moving one battery cable and connecting the lead
between the cable and the battery terminal. Turn the
ignition On and the dashboard warning lamps should
operate indicating a completed circuit through the
jumper lead. Remove the jumper lead from the circuit and
reconnect the battery.
NOTE: Make a few jumper leads of various
lengths using different sizes and types of
alligator and battery clips.
TO MAKE A TEST LAMP
Due to the extensive use of electronic components
in the electrical system, an LED (light emitting diode)
test lamp can be made from a suitable length of 3 mm
wire, an alligator clip, an LED, a 1/4 watt 560 ohm
resistor, a suitable case such as an old ball point pen
case and a length of rod or wire sharpened to form a
probe.
(1) Solder the length of wire to the K (cathode)
Page 215 of 238
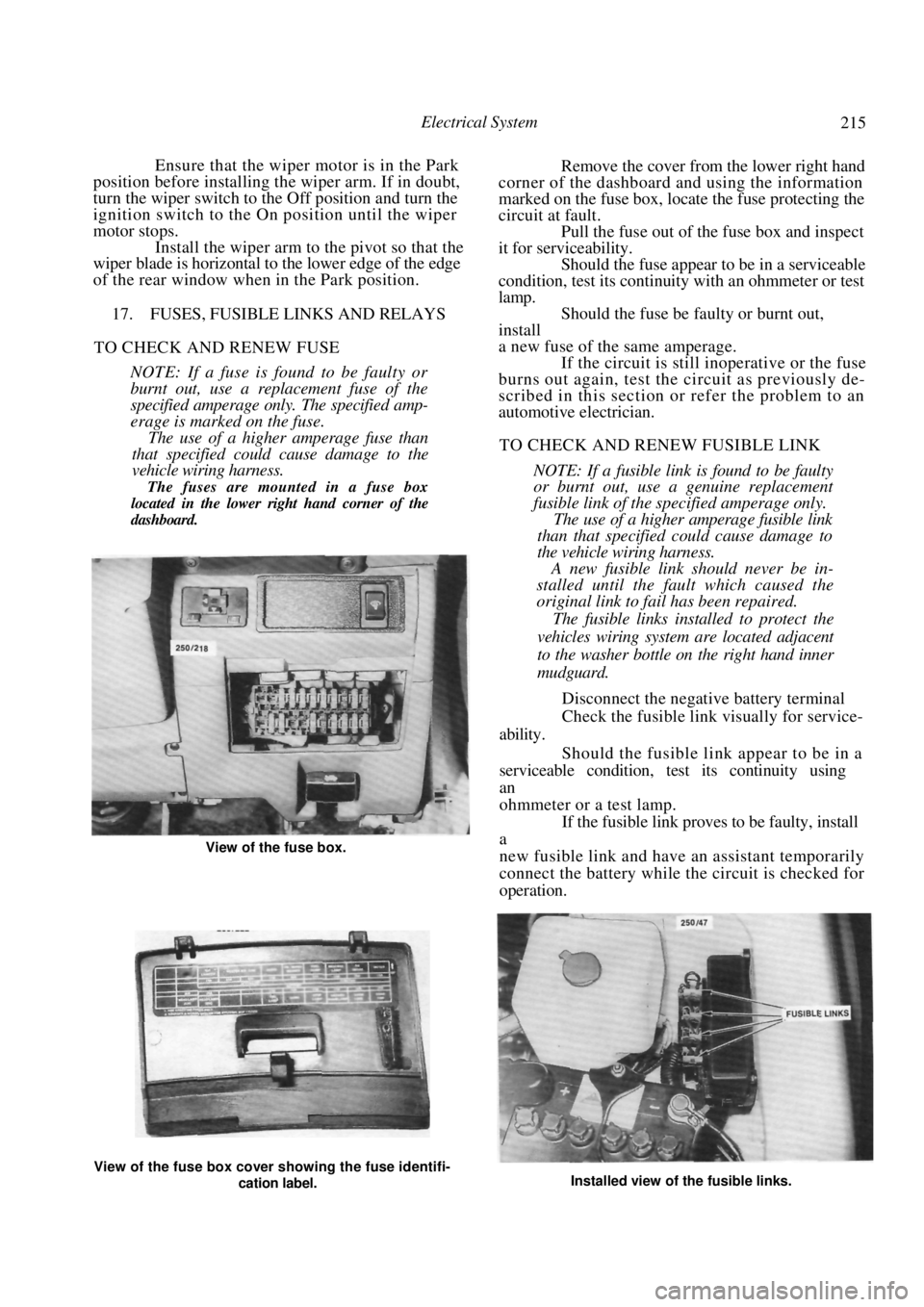
Electrical System 215
Ensure that the wiper motor is in the Park
position before installing the wiper arm. If in doubt,
turn the wiper switch to the Off position and turn the
ignition switch to the On position until the wiper
motor stops.
Install the wiper arm to the pivot so that the
wiper blade is horizontal to the lower edge of the edge
of the rear window when in the Park position.
17. FUSES, FUSIBLE LINKS AND RELAYS
TO CHECK AND RENEW FUSE
NOTE: If a fuse is found to be faulty or
burnt out, use a replacement fuse of the
specified amperage only. The specified amp-
erage is marked on the fuse.
The use of a higher amperage fuse than
that specified could cause damage to the
vehicle wiring harness.
The fuses are mounted in a fuse box
located in the lower right hand corner of the
dashboard.
Remove the cover from the lower right hand
corner of the dashboard and using the information
marked on the fuse box, locate the fuse protecting the
circuit at fault. Pull the fuse out of the fuse box and inspect
it for serviceability.
Should the fuse appear to be in a serviceable
condition, test its continuity with an ohmmeter or test
lamp. Should the fuse be faulty or burnt out,
install
a new fuse of the same amperage. If the circuit is still inoperative or the fuse
burns out again, test the circuit as previously de-
scribed in this section or refer the problem to an
automotive electrician.
TO CHECK AND RENEW FUSIBLE LINK
NOTE: If a fusible link is found to be faulty
or burnt out, use a genuine replacement
fusible link of the specified amperage only.
The use of a higher amperage fusible link
than that specified could cause damage to
the vehicle wiring harness.
A new fusible link should never be in-
stalled until the fault which caused the
original link to fail has been repaired.
The fusible links installed to protect the
vehicles wiring system are located adjacent
to the washer bottle on the right hand inner
mudguard.
Disconnect the negative battery terminal
Check the fusible link visually for service-
ability.
Should the fusible link appear to be in a
serviceable condition, test its continuity using
an
ohmmeter or a test lamp. If the fusible link proves to be faulty, install
a
new fusible link and have an assistant temporarily
connect the battery while the circuit is checked for
operation.
View of the fuse box cover showing the fuse identifi-
cation label. Installed view of the fusible links.
View of the fuse box.
Page 216 of 238
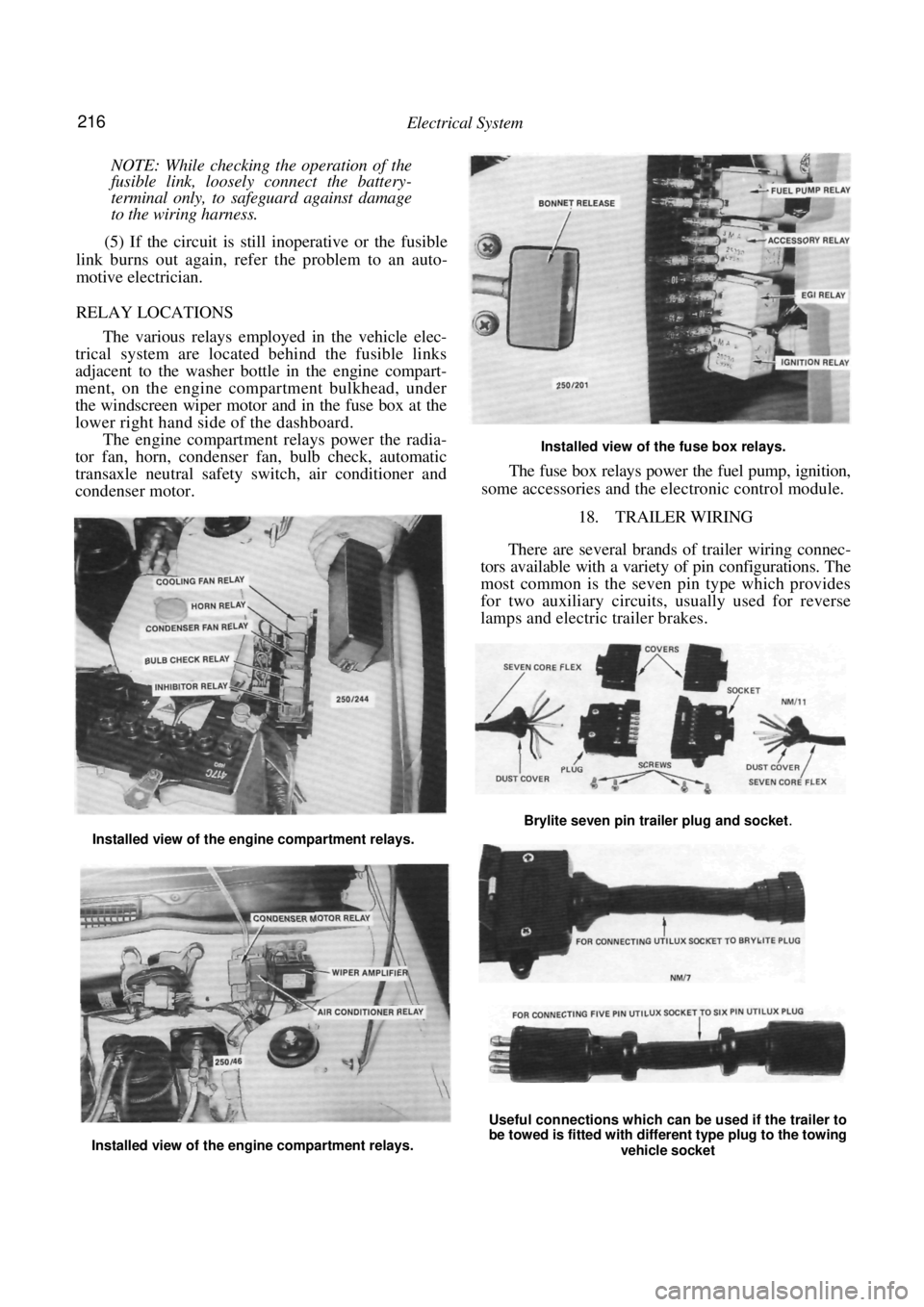
216 Electrical System
NOTE: While checking the operation of the
fusible link, loosely connect the battery-
terminal only, to safeguard against damage
to the wiring harness.
(5) If the circuit is still inoperative or the fusible
link burns out again, refer the problem to an auto-
motive electrician.
RELAY LOCATIONS
The various relays employed in the vehicle elec-
trical system are located behind the fusible links
adjacent to the washer bottle in the engine compart-
ment, on the engine compartment bulkhead, under
the windscreen wiper motor and in the fuse box at the
lower right hand side of the dashboard.
The engine compartment relays power the radia-
tor fan, horn, condenser fan, bulb check, automatic
transaxle neutral safety switch, air conditioner and
condenser motor.
Installed view of the fuse box relays.
The fuse box relays power the fuel pump, ignition,
some accessories and the el ectronic control module.
18. TRAILER WIRING
There are several brands of trailer wiring connec-
tors available with a variet y of pin configurations. The
most common is the seven pin type which provides
for two auxiliary circuits, usually used for reverse
lamps and electric trailer brakes.
Installed view of the engine compartment relays.
Installed view of the engine compartment relays.
Useful connections which can be used if the trailer to
be towed is fitted with different type plug to the towing
vehicle socket
Brylite seven pin trailer plug and socket.
Page 217 of 238
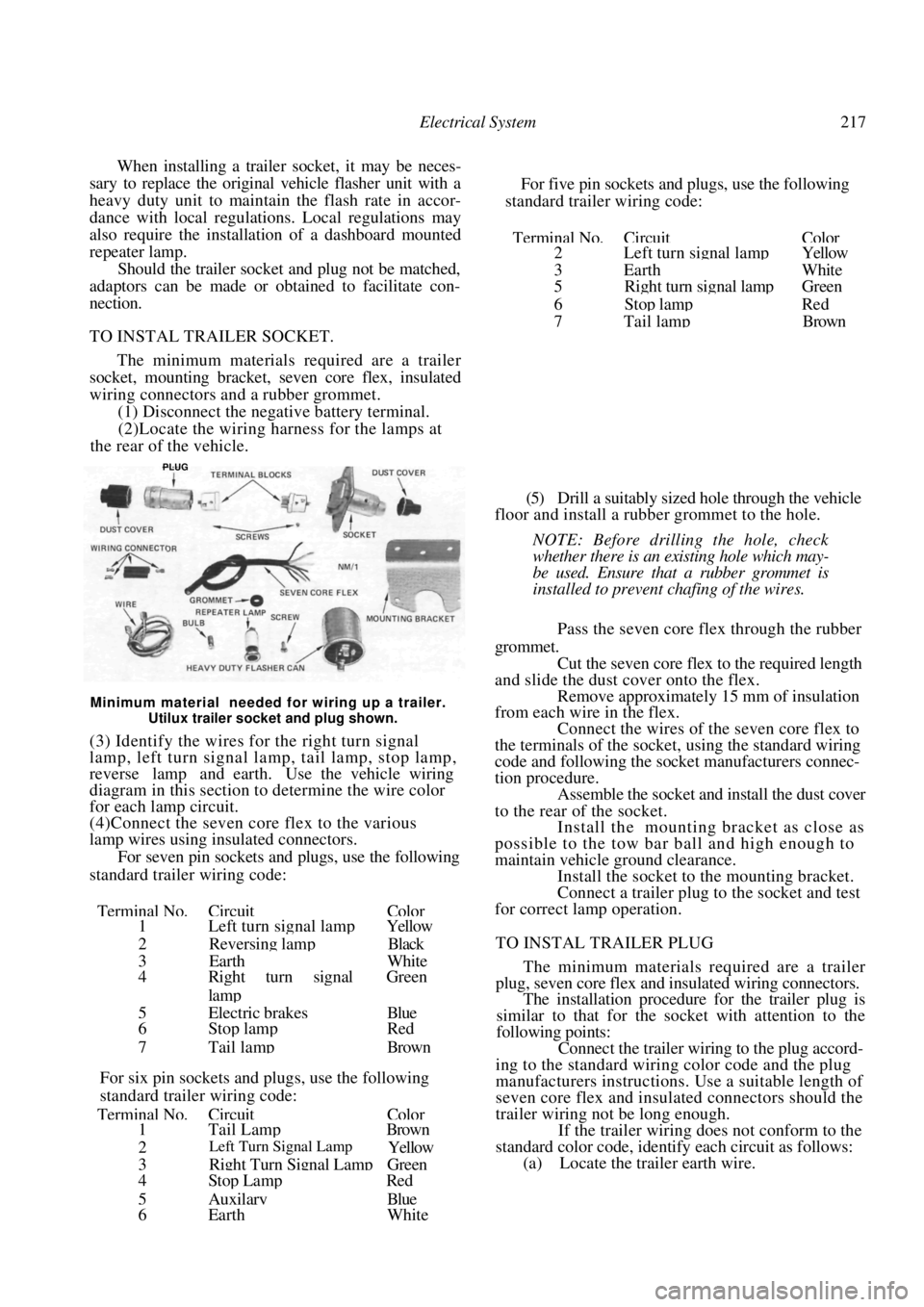
Electrical System 217
When installing a trailer socket, it may be neces-
sary to replace the original vehicle flasher unit with a
heavy duty unit to maintain the flash rate in accor-
dance with local regulations. Local regulations may
also require the installation of a dashboard mounted
repeater lamp.
Should the trailer socket and plug not be matched,
adaptors can be made or obtained to facilitate con-
nection.
TO INSTAL TRAILER SOCKET.
The minimum materials required are a trailer
socket, mounting bracket, seven core flex, insulated
wiring connectors and a rubber grommet.
(1) Disconnect the negative battery terminal.
(2)Locate the wiring harness for the lamps at
the rear of the vehicle.
For five pin sockets and plugs, use the following
standard trailer wiring code:
Terminal No.CircuitColor2 Left turn signal lampYellow
3Earth White
5 Ri
ght turn signal lampGreen
6Stop lamp Red
7 Tail lam
p Brown
Minimum material needed for wiring up a trailer.
Utilux trailer socket and plug shown.
(3) Identify the wires for the right turn signal
lamp, left turn signal lamp, tail lamp, stop lamp,
reverse lamp and earth. Use the vehicle wiring
diagram in this section to determine the wire color
for each lamp circuit.
(4)Connect the seven core flex to the various
lamp wires using insulated connectors.
For seven pin sockets and plugs, use the following
standard trailer wiring code:
Terminal No.CircuitColor1 Left turn signal lamp Yellow
2 Reversing lamp Black
3EarthWhite
4 Right turn signal Green
lamp
5Electric brakesBlue
6 Stop lampRed
7
Tail lampBrown
For six pin sockets and pl ugs, use the following
standard trailer wiring code:
Terminal No.CircuitColor1 Tail LampBrown
2 Left Turn Signal Lamp Yellow
3Right Turn Signal LampGreen
4 Stop LampRed
5AuxilaryBlue
6 Earth White
(5) Drill a suitably si
zed hole through the vehicle
floor and install a rubber grommet to the hole.
NOTE: Before drilling the hole, check
whether there is an existing hole which may-
be used. Ensure that a rubber grommet is
installed to prevent chafing of the wires.
Pass the seven core flex through the rubber
grommet. Cut the seven core flex to the required length
and slide the dust cover onto the flex. Remove approximately 15 mm of insulation
from each wire in the flex.
Connect the wires of the seven core flex to
the terminals of the socket, using the standard wiring
code and following the socket manufacturers connec-
tion procedure. Assemble the socket and install the dust cover
to the rear of the socket. Install the mounting bracket as close as
possible to the tow bar ball and high enough to
maintain vehicle ground clearance. Install the socket to the mounting bracket.
Connect a trailer plug to the socket and test
for correct lamp operation.
TO INSTAL TRAILER PLUG
The minimum materials required are a trailer
plug, seven core flex and insulated wiring connectors.
The installation procedure for the trailer plug is
similar to that for the socket with attention to the
following points:
Connect the trailer wiring to the plug accord-
ing to the standard wiring color code and the plug
manufacturers instructions. Use a suitable length of
seven core flex and insulated connectors should the
trailer wiring not be long enough.
If the trailer wiring does not conform to the
standard color code, identify each circuit as follows: (a) Locate the trailer earth wire.
PLUG