engine OPEL FRONTERA 1998 Workshop Manual
[x] Cancel search | Manufacturer: OPEL, Model Year: 1998, Model line: FRONTERA, Model: OPEL FRONTERA 1998Pages: 6000, PDF Size: 97 MB
Page 1877 of 6000
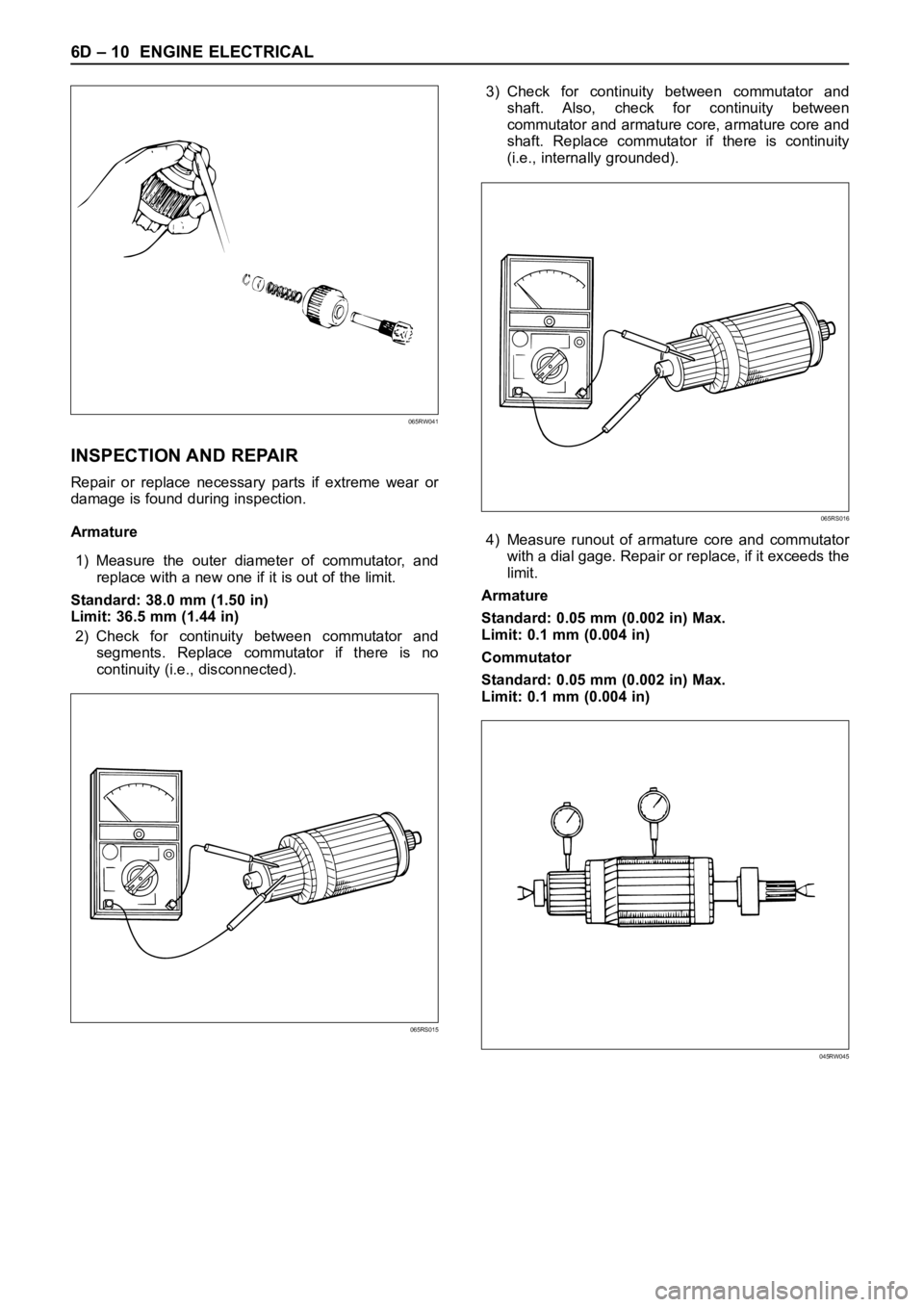
6D – 10 ENGINE ELECTRICAL
INSPECTION AND REPAIR
Repair or replace necessary parts if extreme wear or
damage is found during inspection.
Armature
1) Measure the outer diameter of commutator, and
replace with a new one if it is out of the limit.
Standard: 38.0 mm (1.50 in)
Limit: 36.5 mm (1.44 in)
2) Check for continuity between commutator and
segments. Replace commutator if there is no
continuity (i.e., disconnected).3) Check for continuity between commutator and
shaft. Also, check for continuity between
commutator and armature core, armature core and
shaft. Replace commutator if there is continuity
(i.e., internally grounded).
4) Measure runout of armature core and commutator
with a dial gage. Repair or replace, if it exceeds the
limit.
Armature
Standard: 0.05 mm (0.002 in) Max.
Limit: 0.1 mm (0.004 in)
Commutator
Standard: 0.05 mm (0.002 in) Max.
Limit: 0.1 mm (0.004 in)
065RW041
065RS015
065RS016
045RW045
Page 1878 of 6000
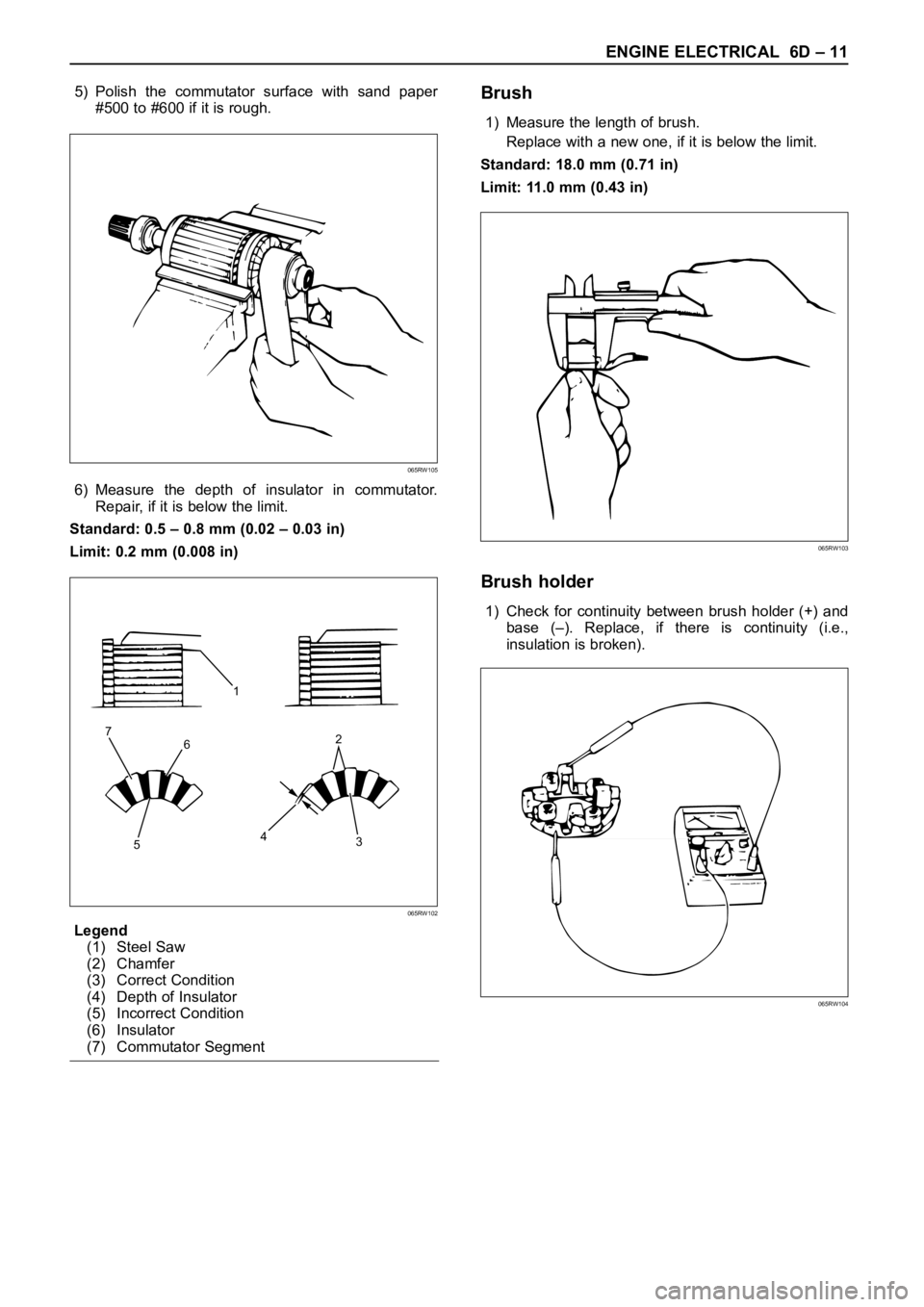
ENGINE ELECTRICAL 6D – 11
5) Polish the commutator surface with sand paper
#500 to #600 if it is rough.
6) Measure the depth of insulator in commutator.
Repair, if it is below the limit.
Standard: 0.5 – 0.8 mm (0.02 – 0.03 in)
Limit: 0.2 mm (0.008 in)
Legend
(1) Steel Saw
(2) Chamfer
(3) Correct Condition
(4) Depth of Insulator
(5) Incorrect Condition
(6) Insulator
(7) Commutator SegmentBrush
1) Measure the length of brush.
Replace with a new one, if it is below the limit.
Standard: 18.0 mm (0.71 in)
Limit: 11.0 mm (0.43 in)
Brush holder
1) Check for continuity between brush holder (+) and
base (–). Replace, if there is continuity (i.e.,
insulation is broken).
065RW105
1
6
53 42 7
065RW102
065RW103
065RW104
Page 1879 of 6000
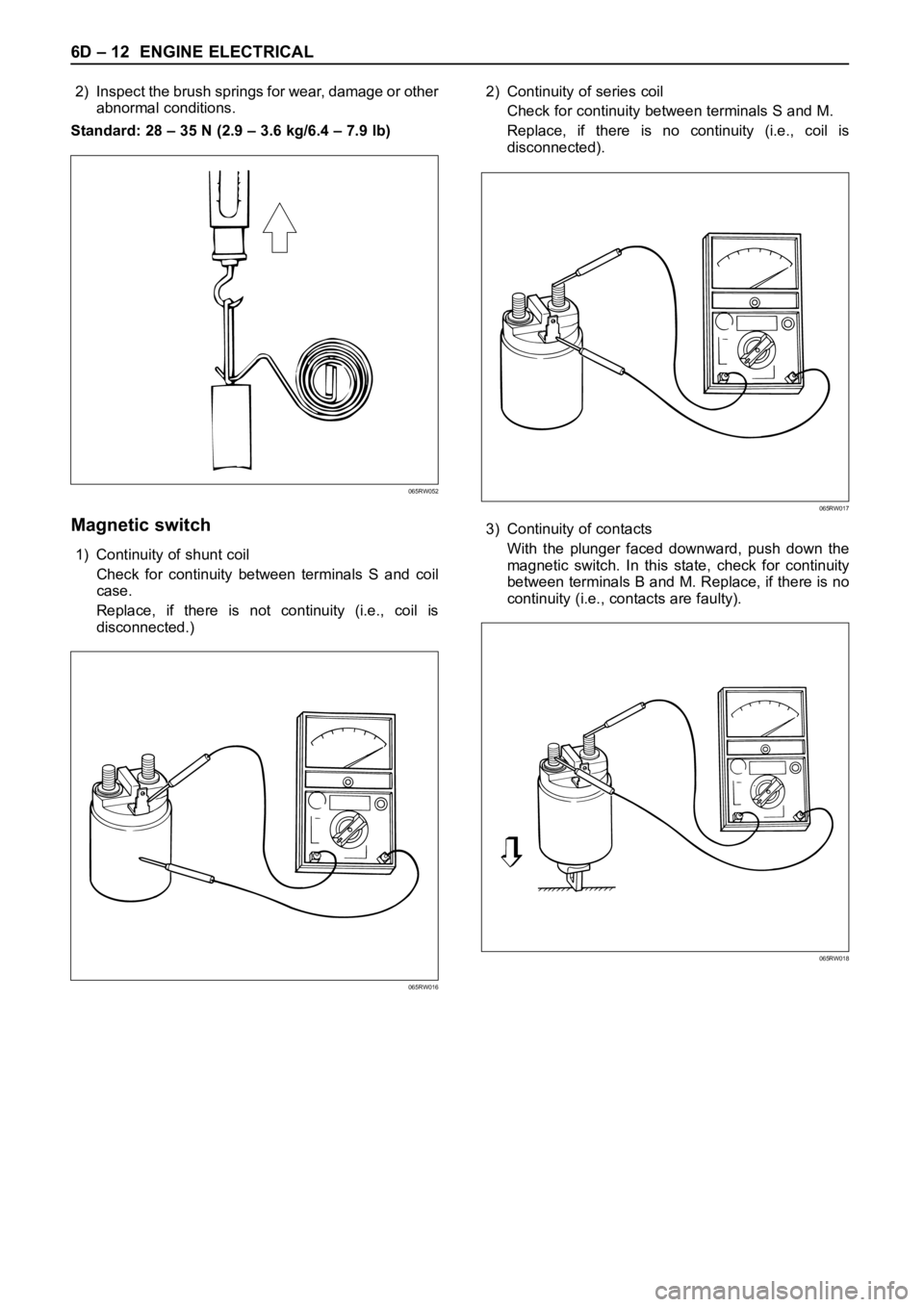
6D – 12 ENGINE ELECTRICAL
2) Inspect the brush springs for wear, damage or other
abnormal conditions.
Standard: 28 – 35 N (2.9 – 3.6 kg/6.4 – 7.9 lb)
Magnetic switch
1) Continuity of shunt coil
Check for continuity between terminals S and coil
case.
Replace, if there is not continuity (i.e., coil is
disconnected.)2) Continuity of series coil
Check for continuity between terminals S and M.
Replace, if there is no continuity (i.e., coil is
disconnected).
3) Continuity of contacts
With the plunger faced downward, push down the
magnetic switch. In this state, check for continuity
between terminals B and M. Replace, if there is no
continuity (i.e., contacts are faulty).
065RW052
065RW017
065RW018
065RW016
Page 1880 of 6000
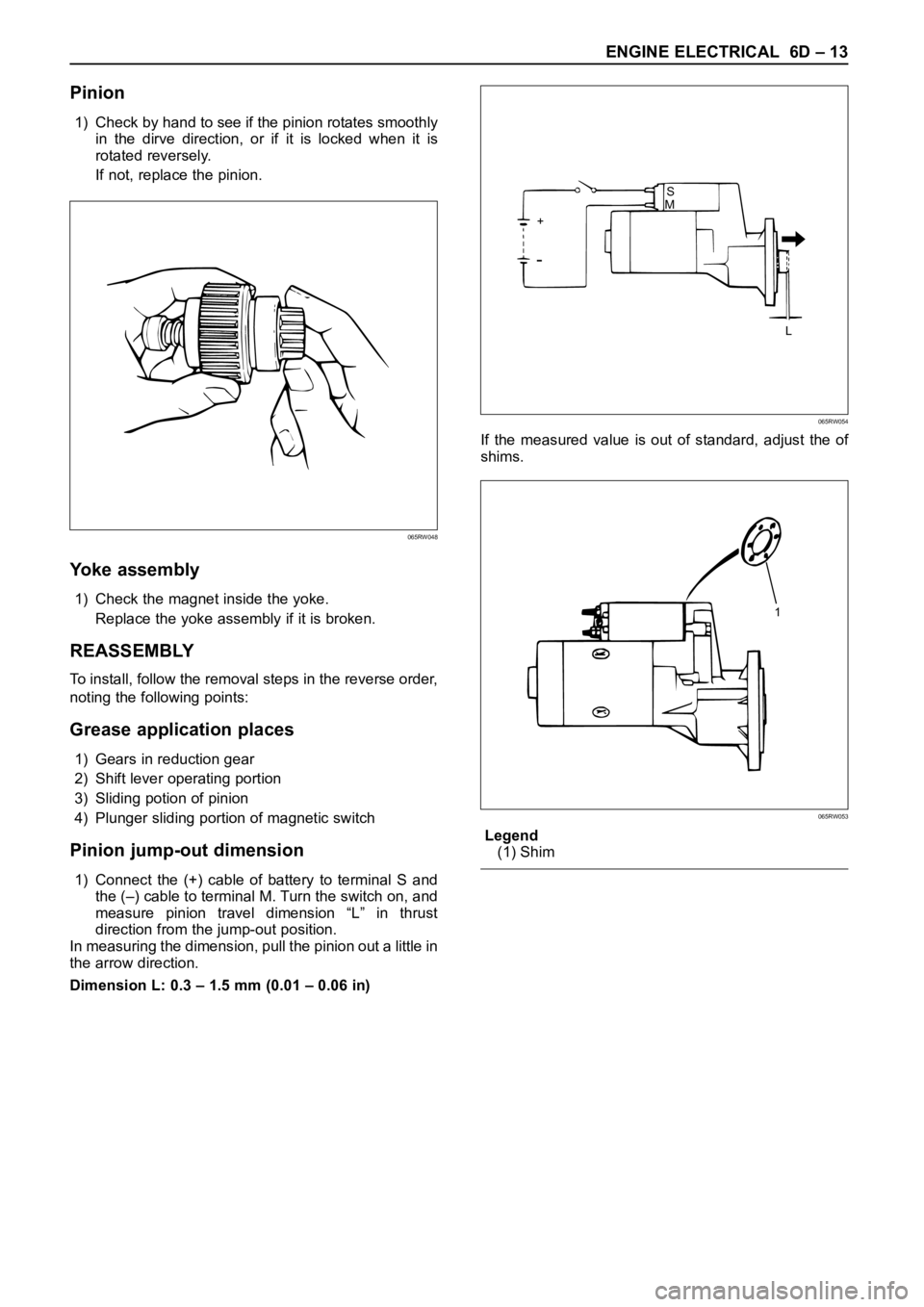
ENGINE ELECTRICAL 6D – 13
Pinion
1) Check by hand to see if the pinion rotates smoothly
in the dirve direction, or if it is locked when it is
rotated reversely.
If not, replace the pinion.
Yoke assembly
1) Check the magnet inside the yoke.
Replace the yoke assembly if it is broken.
REASSEMBLY
To install, follow the removal steps in the reverse order,
noting the following points:
Grease application places
1) Gears in reduction gear
2) Shift lever operating portion
3) Sliding potion of pinion
4) Plunger sliding portion of magnetic switch
Pinion jump-out dimension
1) Connect the (+) cable of battery to terminal S and
the (–) cable to terminal M. Turn the switch on, and
measure pinion travel dimension “L” in thrust
direction from the jump-out position.
In measuring the dimension, pull the pinion out a little in
the arrow direction.
Dimension L: 0.3 – 1.5 mm (0.01 – 0.06 in)If the measured value is out of standard, adjust the of
shims.
Legend
(1) Shim
065RW048
S
+
L M
065RW054
1
065RW053
Page 1881 of 6000
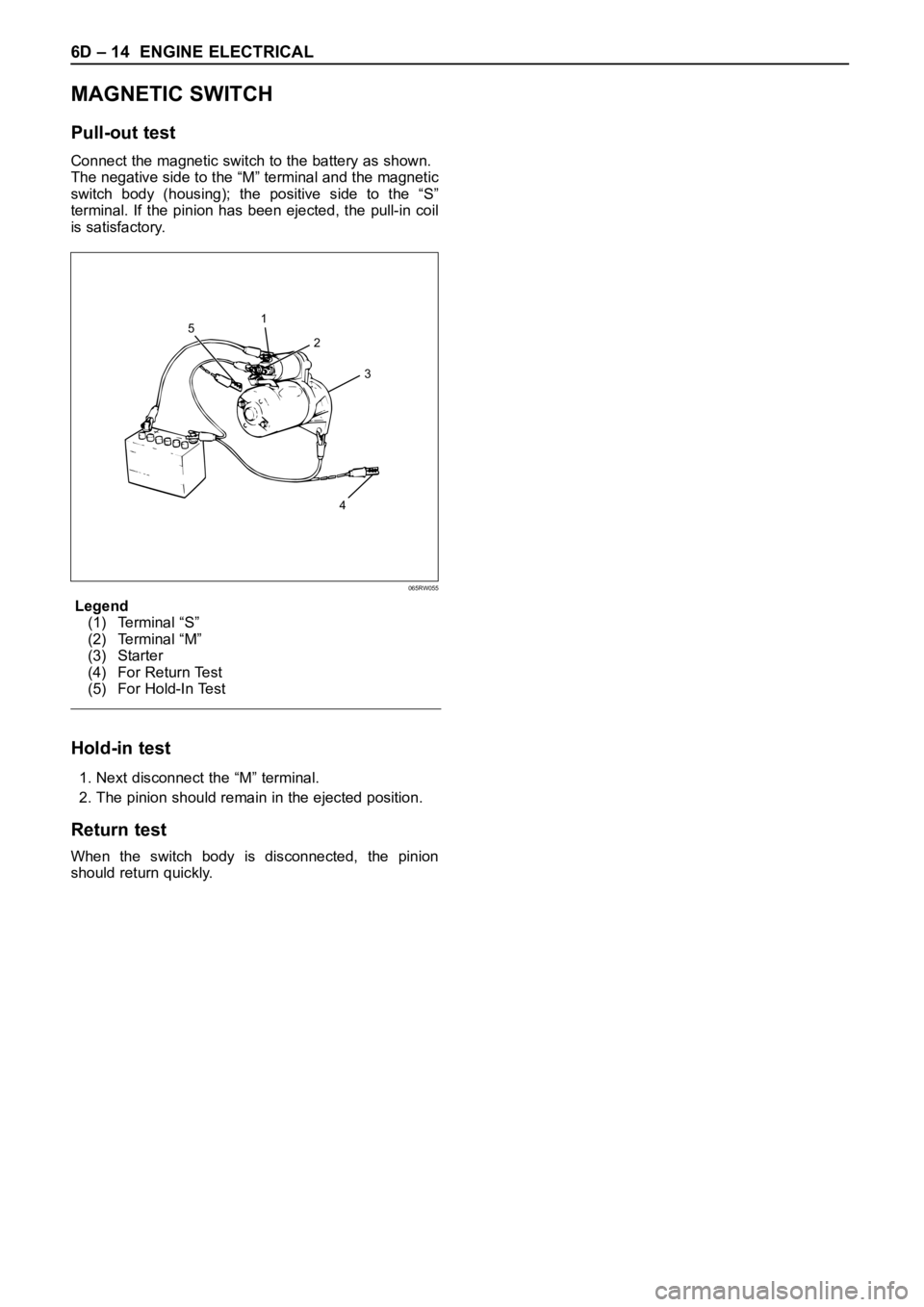
6D – 14 ENGINE ELECTRICAL
MAGNETIC SWITCH
Pull-out test
Connect the magnetic switch to the battery as shown.
The negative side to the “M” terminal and the magnetic
switch body (housing); the positive side to the “S”
terminal. If the pinion has been ejected, the pull-in coil
is satisfactory.
Legend
(1) Terminal “S”
(2) Terminal “M”
(3) Starter
(4) For Return Test
(5) For Hold-In Test
Hold-in test
1. Next disconnect the “M” terminal.
2. The pinion should remain in the ejected position.
Return test
When the switch body is disconnected, the pinion
should return quickly.
2 1
5
3
4
065RW055
Page 1882 of 6000
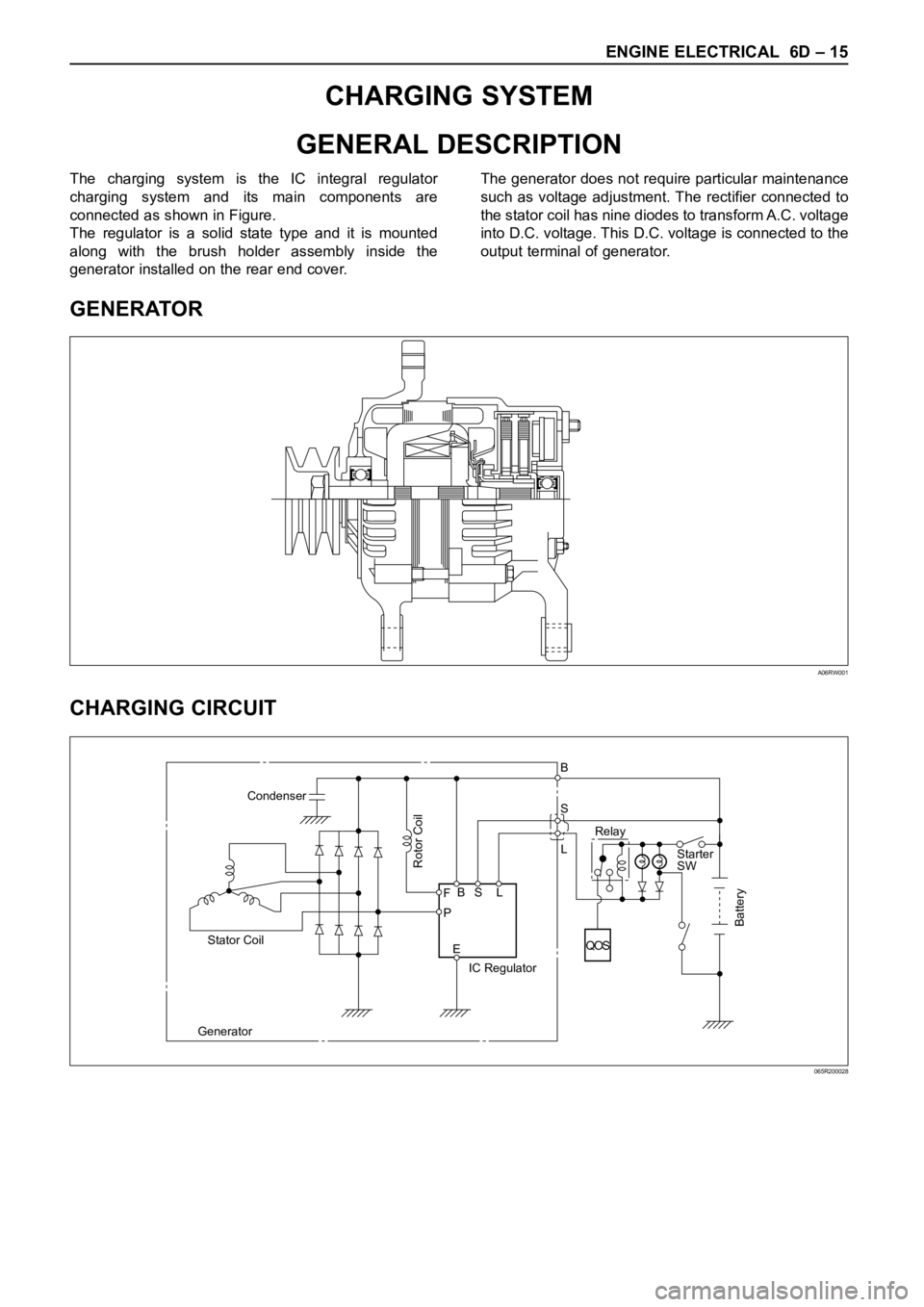
ENGINE ELECTRICAL 6D – 15
CHARGING SYSTEM
GENERAL DESCRIPTION
GENERATOR
CHARGING CIRCUIT
The charging system is the IC integral regulator
charging system and its main components are
connected as shown in Figure.
The regulator is a solid state type and it is mounted
along with the brush holder assembly inside the
generator installed on the rear end cover.The generator does not require particular maintenance
such as voltage adjustment. The rectifier connected to
the stator coil has nine diodes to transform A.C. voltage
into D.C. voltage. This D.C. voltage is connected to the
output terminal of generator.
A06RW001
Condenser
GeneratorStator Coil
IC RegulatorStarter
SW
Rotor Coil
Battery
P F
EBS LRelay B
S
L
QOS
065R200028
Page 1883 of 6000
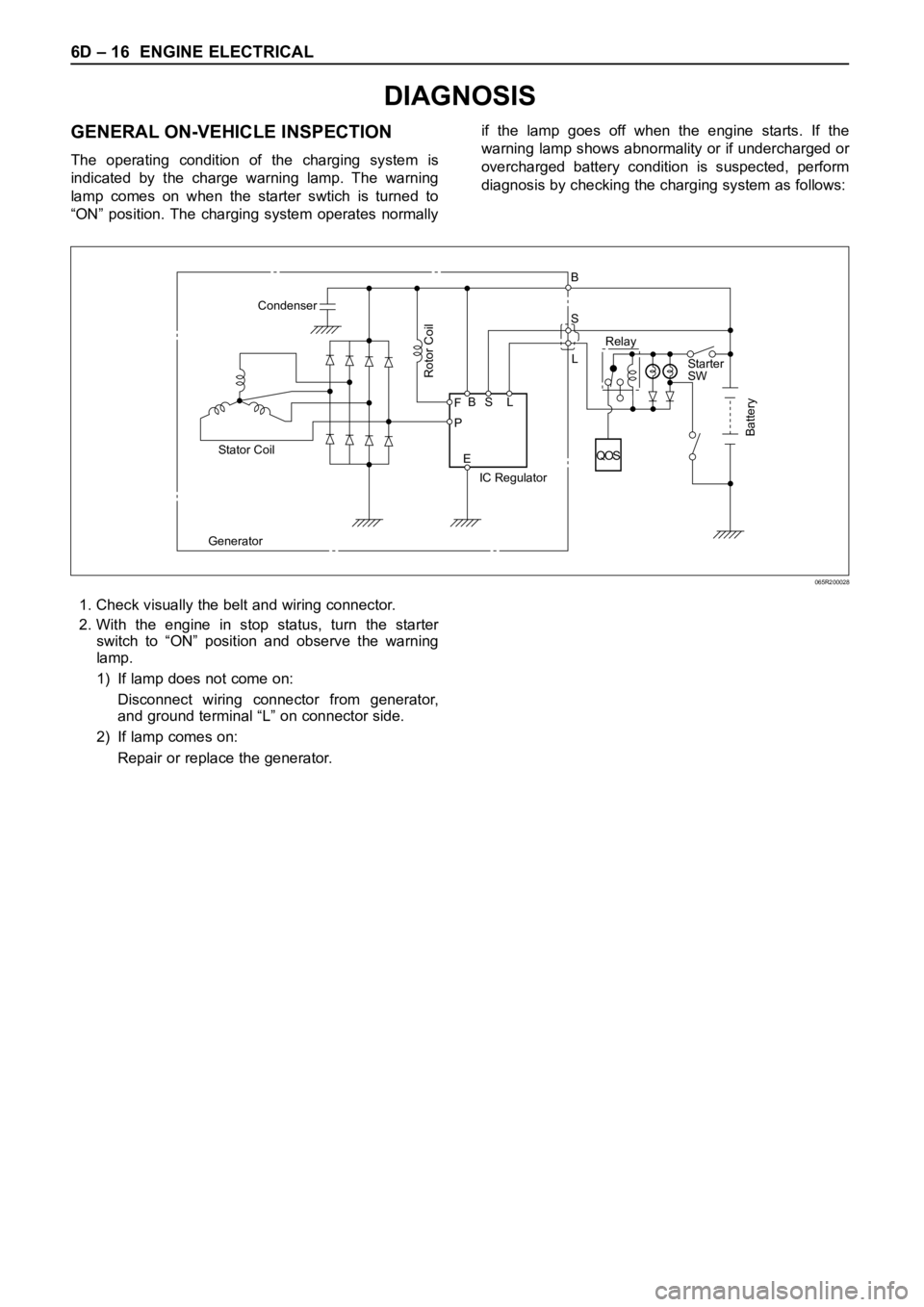
6D – 16 ENGINE ELECTRICAL
DIAGNOSIS
GENERAL ON-VEHICLE INSPECTION
The operating condition of the charging system is
indicated by the charge warning lamp. The warning
lamp comes on when the starter swtich is turned to
“ON” position. The charging system operates normallyif the lamp goes off when the engine starts. If the
warning lamp shows abnormality or if undercharged or
overcharged battery condition is suspected, perform
diagnosis by checking the charging system as follows:
Condenser
GeneratorStator Coil
IC RegulatorStarter
SW
Rotor Coil
Battery
P F
EBS LRelay B
S
L
QOS
065R200028
1. Check visually the belt and wiring connector.
2. With the engine in stop status, turn the starter
switch to “ON” position and observe the warning
lamp.
1) If lamp does not come on:
Disconnect wiring connector from generator,
and ground terminal “L” on connector side.
2) If lamp comes on:
Repair or replace the generator.
Page 1884 of 6000
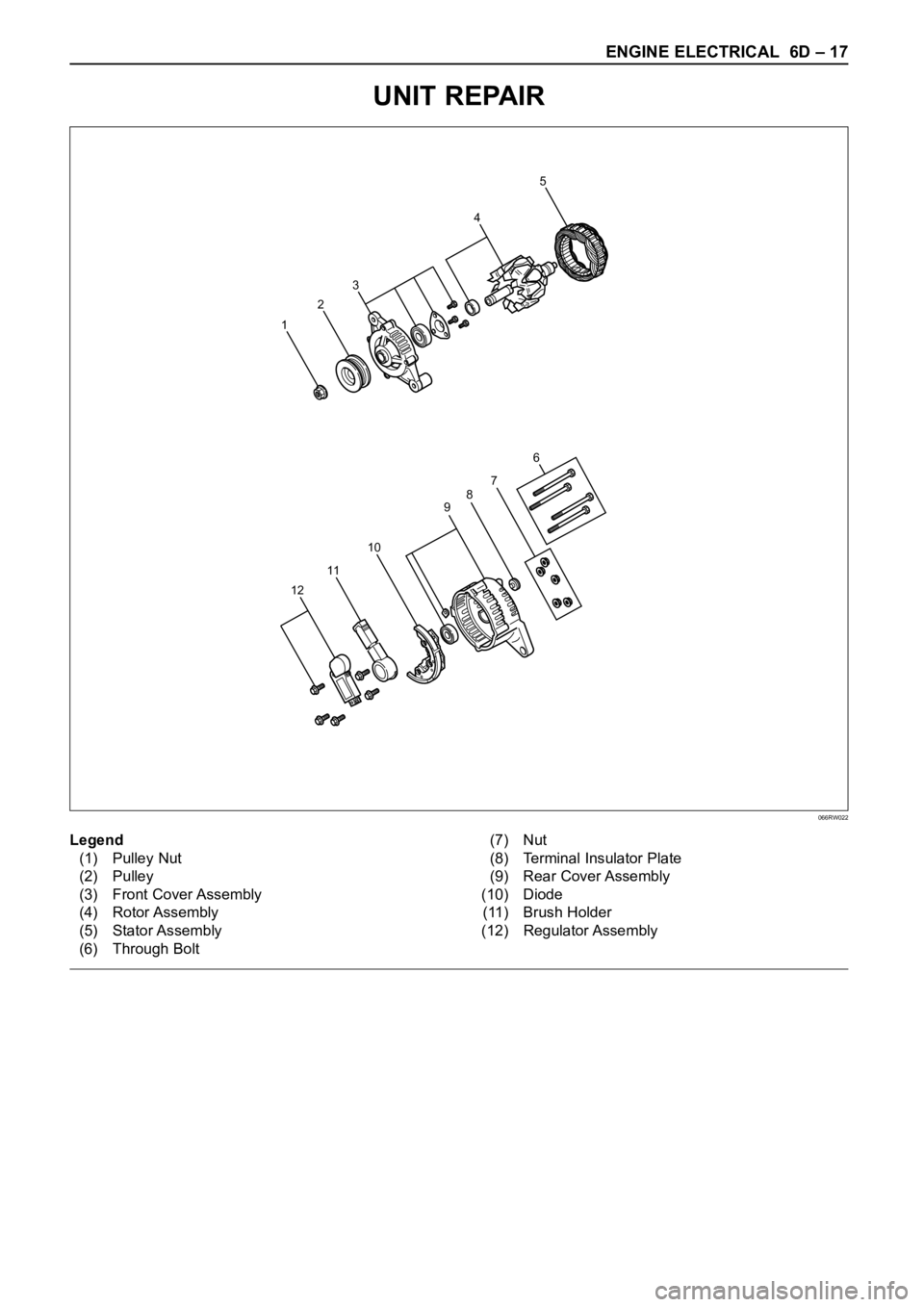
ENGINE ELECTRICAL 6D – 17
UNIT REPAIR
5
4
3
2
1
7
6
109
8
11
12
066RW022
Legend
(1) Pulley Nut
(2) Pulley
(3) Front Cover Assembly
(4) Rotor Assembly
(5) Stator Assembly
(6) Through Bolt(7) Nut
(8) Terminal Insulator Plate
(9) Rear Cover Assembly
(10) Diode
(11) Brush Holder
(12) Regulator Assembly
Page 1885 of 6000
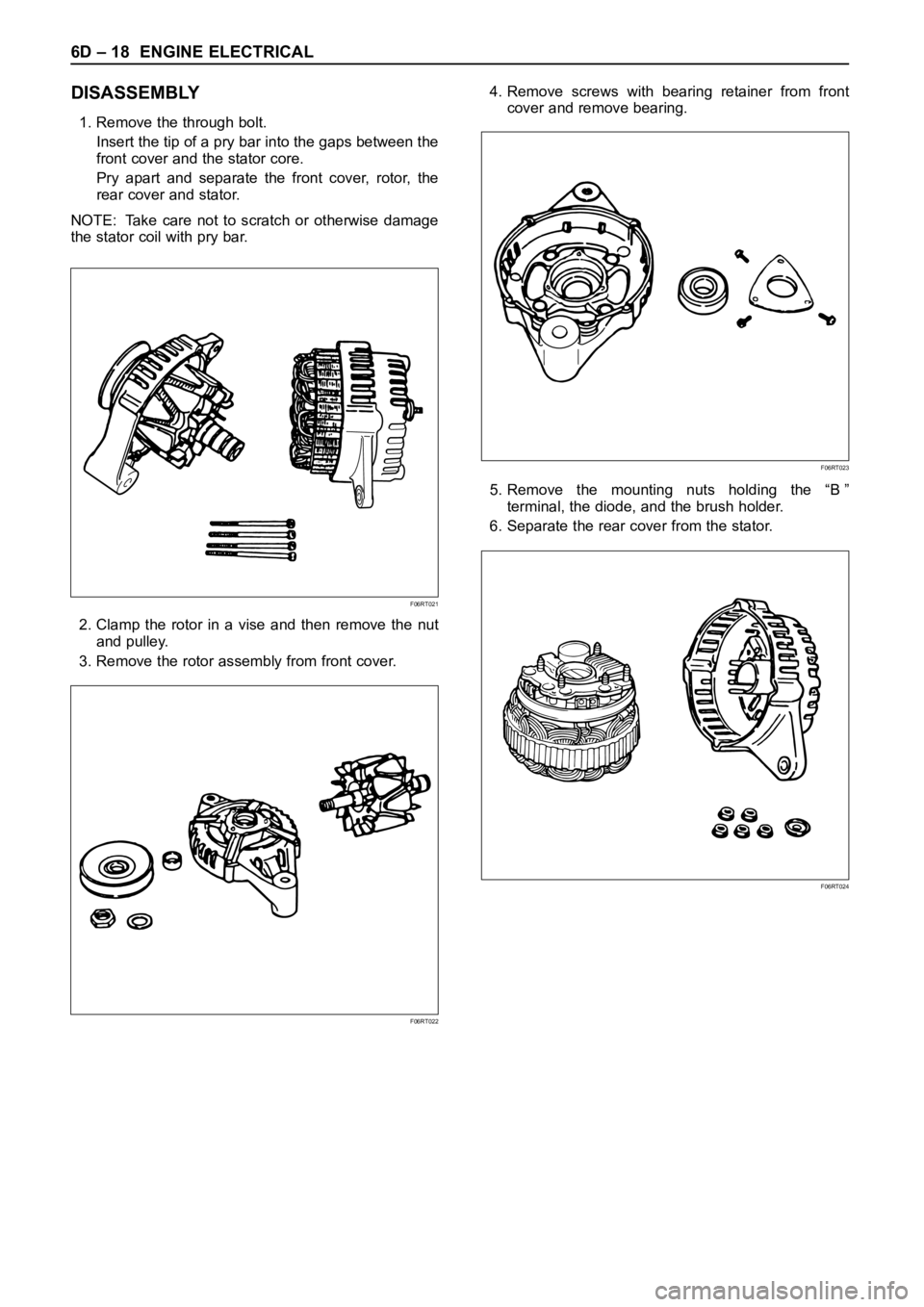
6D – 18 ENGINE ELECTRICAL
DISASSEMBLY
1. Remove the through bolt.
Insert the tip of a pry bar into the gaps between the
front cover and the stator core.
Pry apart and separate the front cover, rotor, the
rear cover and stator.
NOTE: Take care not to scratch or otherwise damage
the stator coil with pry bar.
2. Clamp the rotor in a vise and then remove the nut
and pulley.
3. Remove the rotor assembly from front cover.4. Remove screws with bearing retainer from front
cover and remove bearing.
5. Remove the mounting nuts holding the “B ”
terminal, the diode, and the brush holder.
6. Separate the rear cover from the stator.
F06RT021
F06RT022
F06RT023
F06RT024
Page 1886 of 6000
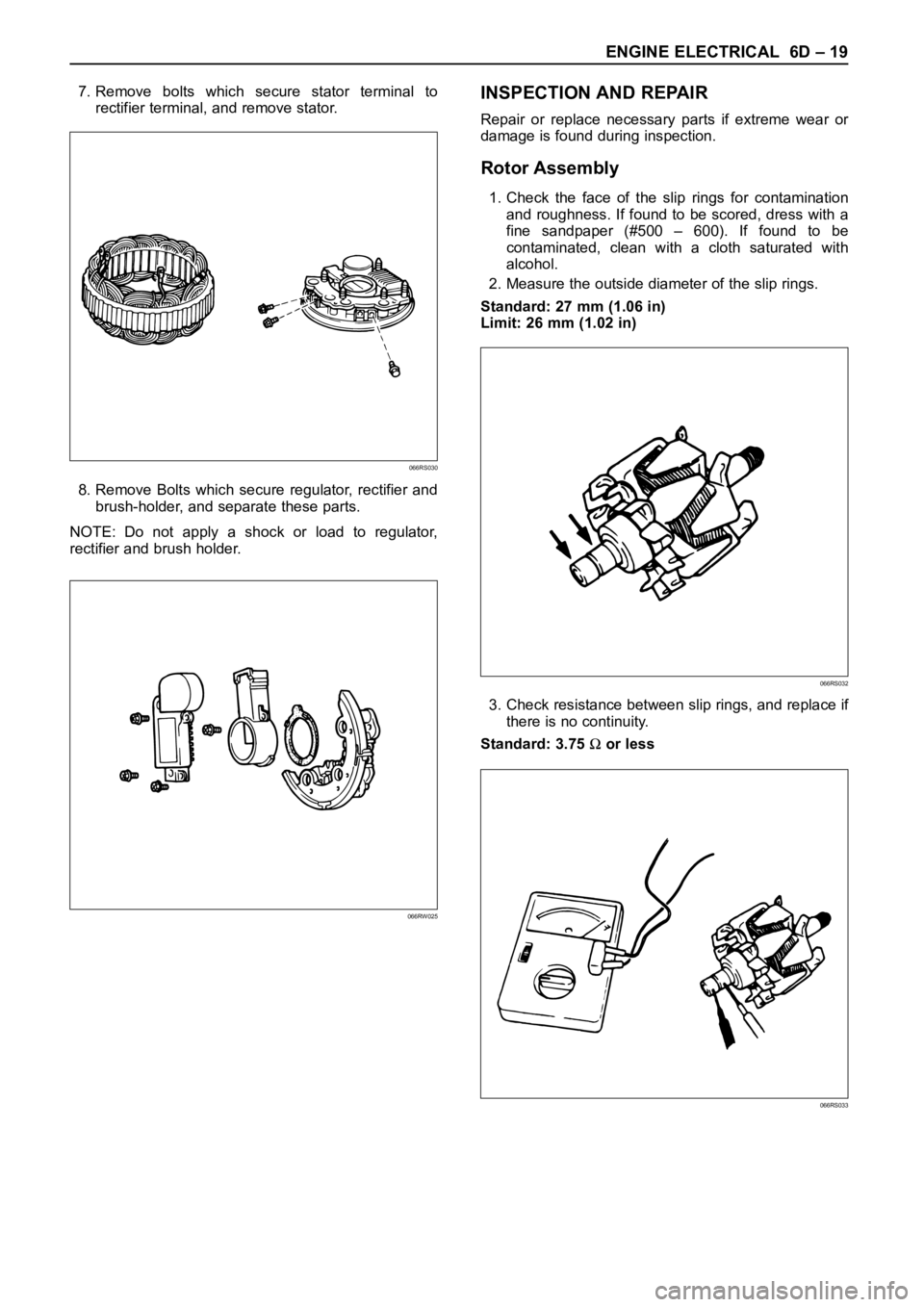
ENGINE ELECTRICAL 6D – 19
7. Remove bolts which secure stator terminal to
rectifier terminal, and remove stator.
8. Remove Bolts which secure regulator, rectifier and
brush-holder, and separate these parts.
NOTE: Do not apply a shock or load to regulator,
rectifier and brush holder.INSPECTION AND REPAIR
Repair or replace necessary parts if extreme wear or
damage is found during inspection.
Rotor Assembly
1. Check the face of the slip rings for contamination
and roughness. If found to be scored, dress with a
fine sandpaper (#500 – 600). If found to be
contaminated, clean with a cloth saturated with
alcohol.
2. Measure the outside diameter of the slip rings.
Standard: 27 mm (1.06 in)
Limit: 26 mm (1.02 in)
3. Check resistance between slip rings, and replace if
there is no continuity.
Standard: 3.75
or less
066RS030
066RW025
066RS032
066RS033