speed sensor RENAULT SCENIC 2000 J64 / 1.G Technical Note 3426A Workshop Manual
[x] Cancel search | Manufacturer: RENAULT, Model Year: 2000, Model line: SCENIC, Model: RENAULT SCENIC 2000 J64 / 1.GPages: 118, PDF Size: 1.5 MB
Page 2 of 118
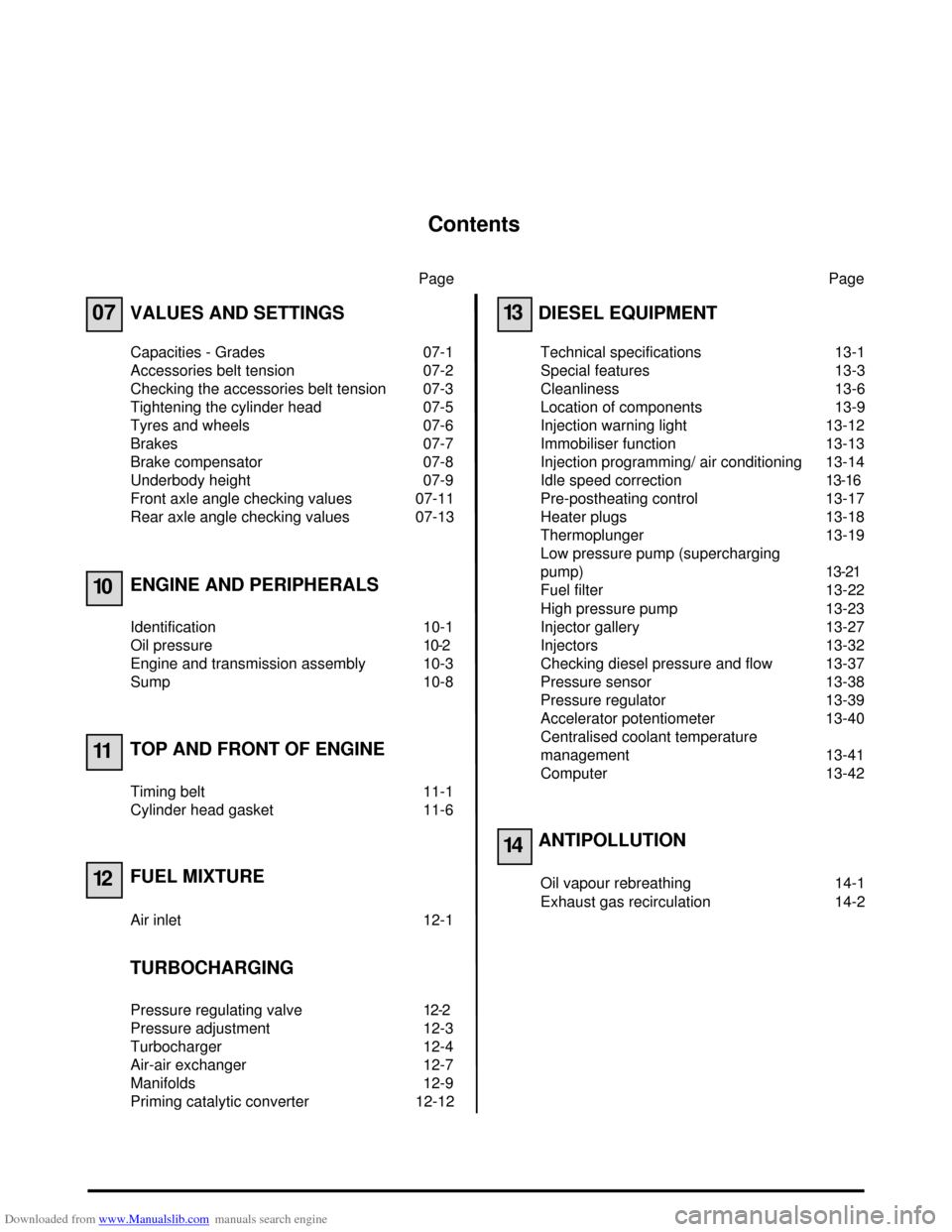
Downloaded from www.Manualslib.com manuals search engine Contents
Page
07
10
11
12
VALUES AND SETTINGS
Capacities - Grades 07-1
Accessories belt tension 07-2
Checking the accessories belt tension 07-3
Tightening the cylinder head 07-5
Tyres and wheels 07-6
Brakes 07-7
Brake compensator 07-8
Underbody height 07-9
Front axle angle checking values 07-11
Rear axle angle checking values 07-13
ENGINE AND PERIPHERALS
Identification 10-1
Oil pressure 10-2
Engine and transmission assembly 10-3
Sump 10-8
TOP AND FRONT OF ENGINE
Timing belt 11-1
Cylinder head gasket 11-6
FUEL MIXTURE
Air inlet 12-1
TURBOCHARGING
Pressure regulating valve 12-2
Pressure adjustment 12-3
Turbocharger 12-4
Air-air exchanger 12-7
Manifolds 12-9
Priming catalytic converter 12-12Page
13
14
DIESEL EQUIPMENT
Technical specifications 13-1
Special features 13-3
Cleanliness 13-6
Location of components 13-9
Injection warning light 13-12
Immobiliser function 13-13
Injection programming/ air conditioning 13-14
Idle speed correction13-16
Pre-postheating control 13-17
Heater plugs 13-18
Thermoplunger 13-19
Low pressure pump (supercharging
pump)13-21
Fuel filter 13-22
High pressure pump 13-23
Injector gallery 13-27
Injectors 13-32
Checking diesel pressure and flow 13-37
Pressure sensor 13-38
Pressure regulator 13-39
Accelerator potentiometer 13-40
Centralised coolant temperature
management 13-41
Computer 13-42
ANTIPOLLUTION
Oil vapour rebreathing 14-1
Exhaust gas recirculation 14-2
Page 44 of 118
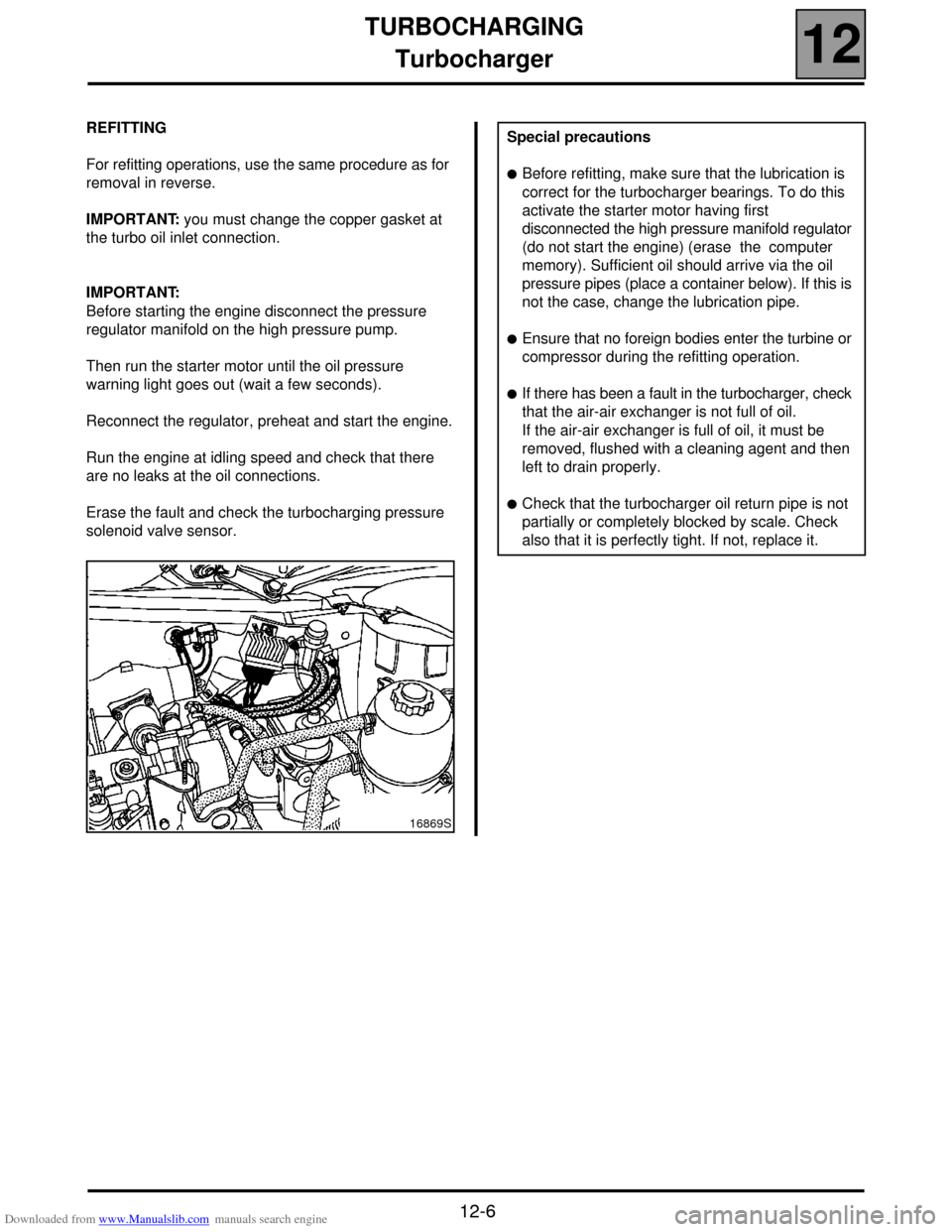
Downloaded from www.Manualslib.com manuals search engine TURBOCHARGING
Turbocharger
12
12-6
REFITTING
For refitting operations, use the same procedure as for
removal in reverse.
IMPORTANT: you must change the copper gasket at
the turbo oil inlet connection.
IMPORTANT:
Before starting the engine disconnect the pressure
regulator manifold on the high pressure pump.
Then run the starter motor until the oil pressure
warning light goes out (wait a few seconds).
Reconnect the regulator, preheat and start the engine.
Run the engine at idling speed and check that there
are no leaks at the oil connections.
Erase the fault and check the turbocharging pressure
solenoid valve sensor.
16869S
Special precautions
!Before refitting, make sure that the lubrication is
correct for the turbocharger bearings. To do this
activate the starter motor having first
disconnected the high pressure manifold regulator
(do not start the engine) (erase the computer
memory). Sufficient oil should arrive via the oil
pressure pipes (place a container below). If this is
not the case, change the lubrication pipe.
!Ensure that no foreign bodies enter the turbine or
compressor during the refitting operation.
!If there has been a fault in the turbocharger, check
that the air-air exchanger is not full of oil.
If the air-air exchanger is full of oil, it must be
removed, flushed with a cleaning agent and then
left to drain properly.
!Check that the turbocharger oil return pipe is not
partially or completely blocked by scale. Check
also that it is perfectly tight. If not, replace it.
Page 52 of 118
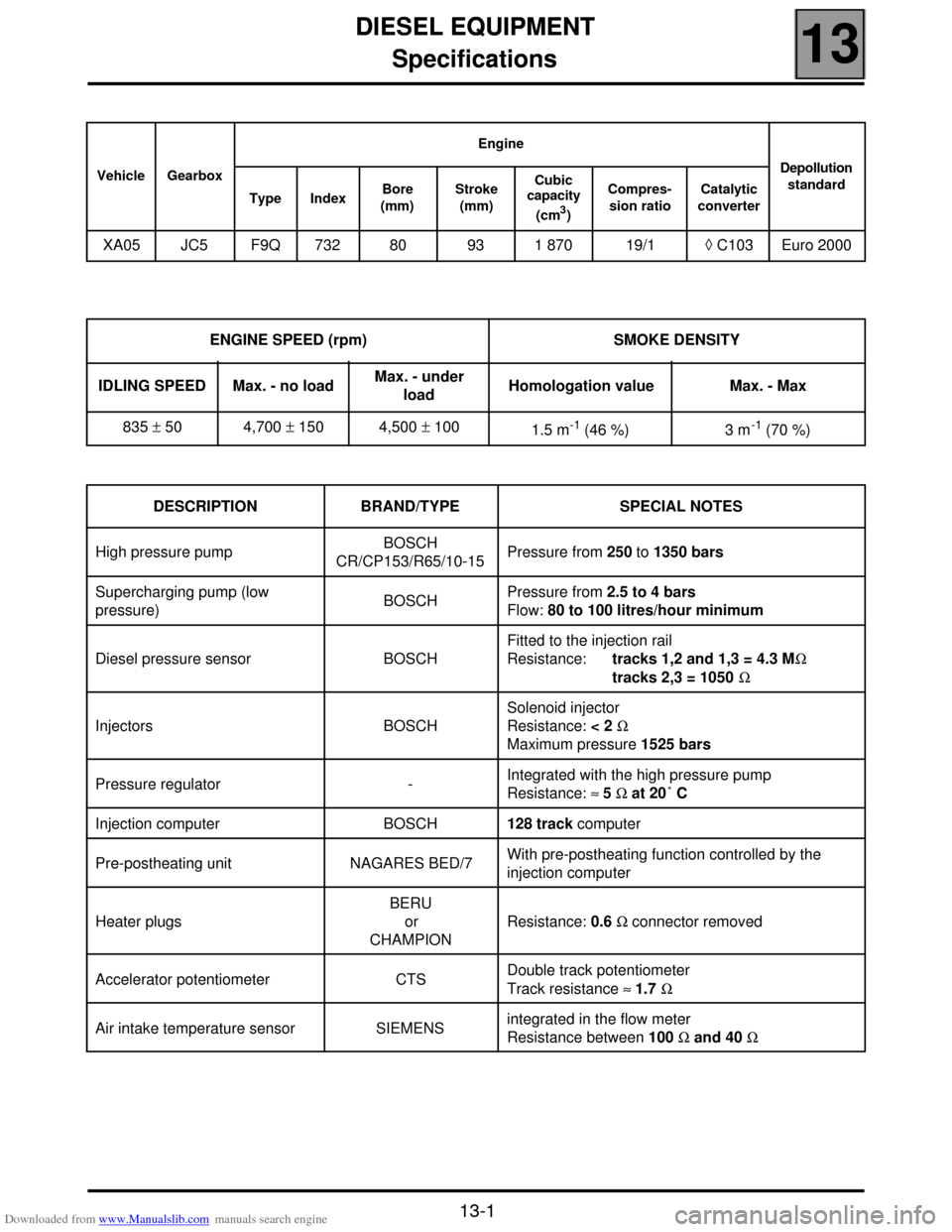
Downloaded from www.Manualslib.com manuals search engine DIESEL EQUIPMENT
Specifications
13
113
DIESEL EQUIPMENT
Specifications
Vehicle GearboxEngine
Depollution
standard
Type IndexBore
(mm) Stroke
(mm) Cubic
capacity
(cm
3)Compres-
sion ratioCatalytic
converter
XA05 JC5 F9Q 732 80 93 1 870 19/1◊ C103 Euro 2000
ENGINE SPEED (rpm) SMOKE DENSITY
IDLING SPEED Max. - no loadMax. - under
loadHomologation value Max. - Max
835 ± 50 4,700 ± 150 4,500 ± 100
1.5 m
-1 (46 %) 3 m-1 (70 %)
DESCRIPTION BRAND/TYPE SPECIAL NOTES
High pressure pumpBOSCH
CR/CP153/R65/10-15Pressure from 250 to 1350 bars
Supercharging pump (low
pressure)BOSCHPressure from 2.5 to 4 bars
Flow: 80 to 100 litres/hour minimum
Diesel pressure sensor BOSCHFitted to the injection rail
Resistance: tracks 1,2 and 1,3 = 4.3 MΩ
tracks 2,3 = 1050 Ω
Injectors BOSCHSolenoid injector
Resistance: < 2 Ω
Maximum pressure 1525 bars
Pressure regulator - Integrated with the high pressure pump
Resistance: ≈ 5 Ω at 20˚ C
Injection computer BOSCH128 track computer
Pre-postheating unit NAGARES BED/7With pre-postheating function controlled by the
injection computer
Heater plugsBERU
or
CHAMPIONResistance: 0.6 Ω connector removed
Accelerator potentiometer CTSDouble track potentiometer
Track resistance ≈ 1.7 Ω
Air intake temperature sensor SIEMENSintegrated in the flow meter
Resistance between 100 Ω and 40 Ω
13-1
Page 53 of 118
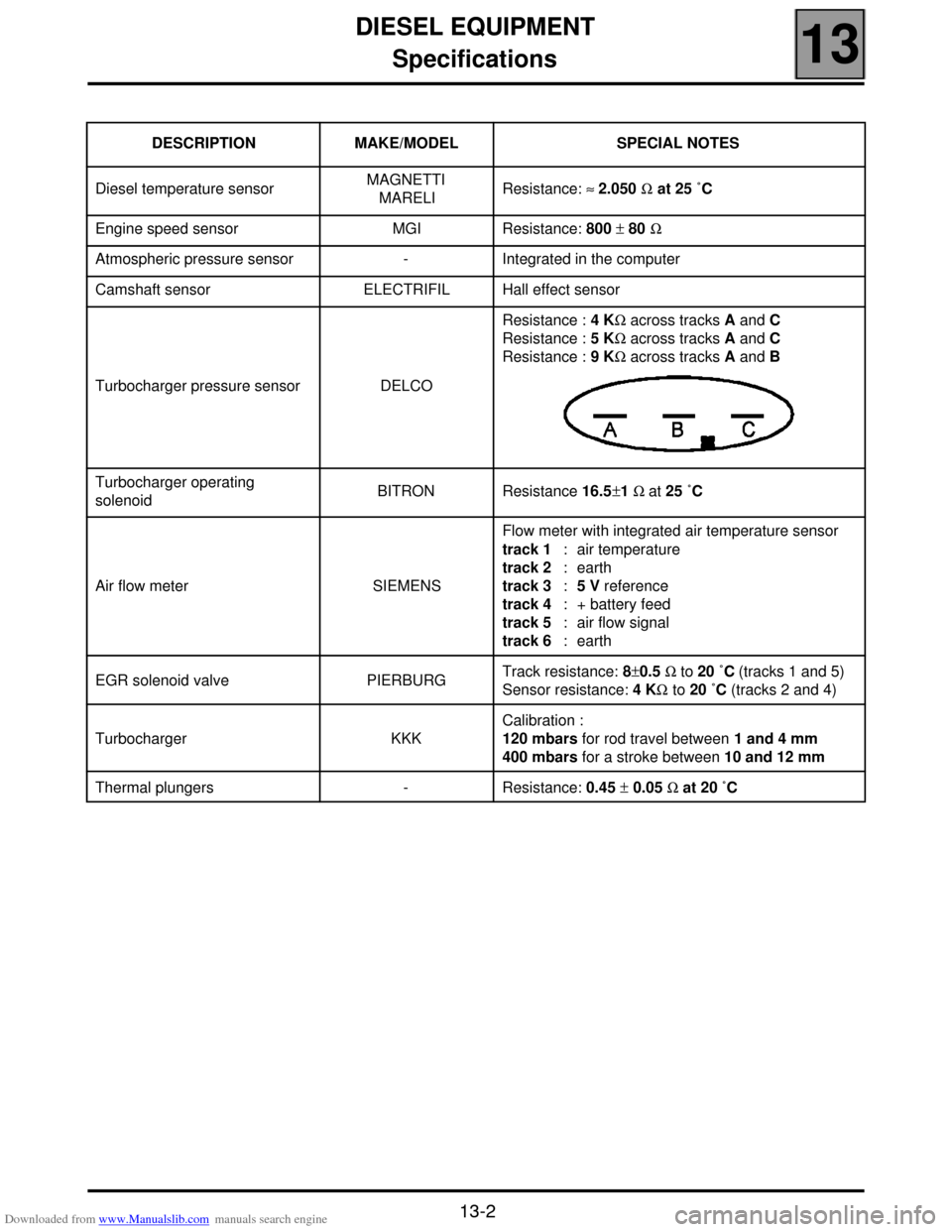
Downloaded from www.Manualslib.com manuals search engine DIESEL EQUIPMENT
Specifications
13
13-2
DESCRIPTION MAKE/MODEL SPECIAL NOTES
Diesel temperature sensorMAGNETTI
MARELIResistance: ≈ 2.050 Ω at 25 ˚C
Engine speed sensor MGI Resistance: 800 ± 80 Ω
Atmospheric pressure sensor - Integrated in the computer
Camshaft sensor ELECTRIFIL Hall effect sensor
Turbocharger pressure sensor DELCOResistance : 4 KΩ across tracks A and C
Resistance : 5 KΩ across tracks A and C
Resistance : 9 KΩ across tracks A and B
Turbocharger operating
solenoidBITRON Resistance 16.5±1 Ω at 25 ˚C
Air flow meter SIEMENSFlow meter with integrated air temperature sensor
track 1 : air temperature
track 2 : earth
track 3 : 5 V reference
track 4 : + battery feed
track 5 : air flow signal
track 6 : earth
EGR solenoid valve PIERBURGTrack resistance: 8±0.5 Ω to 20 ˚C (tracks 1 and 5)
Sensor resistance: 4 KΩ to 20 ˚C (tracks 2 and 4)
Turbocharger KKKCalibration :
120 mbars for rod travel between 1 and 4 mm
400 mbars for a stroke between 10 and 12 mm
Thermal plungers - Resistance: 0.45 ± 0.05 Ω at 20 ˚C
Page 55 of 118
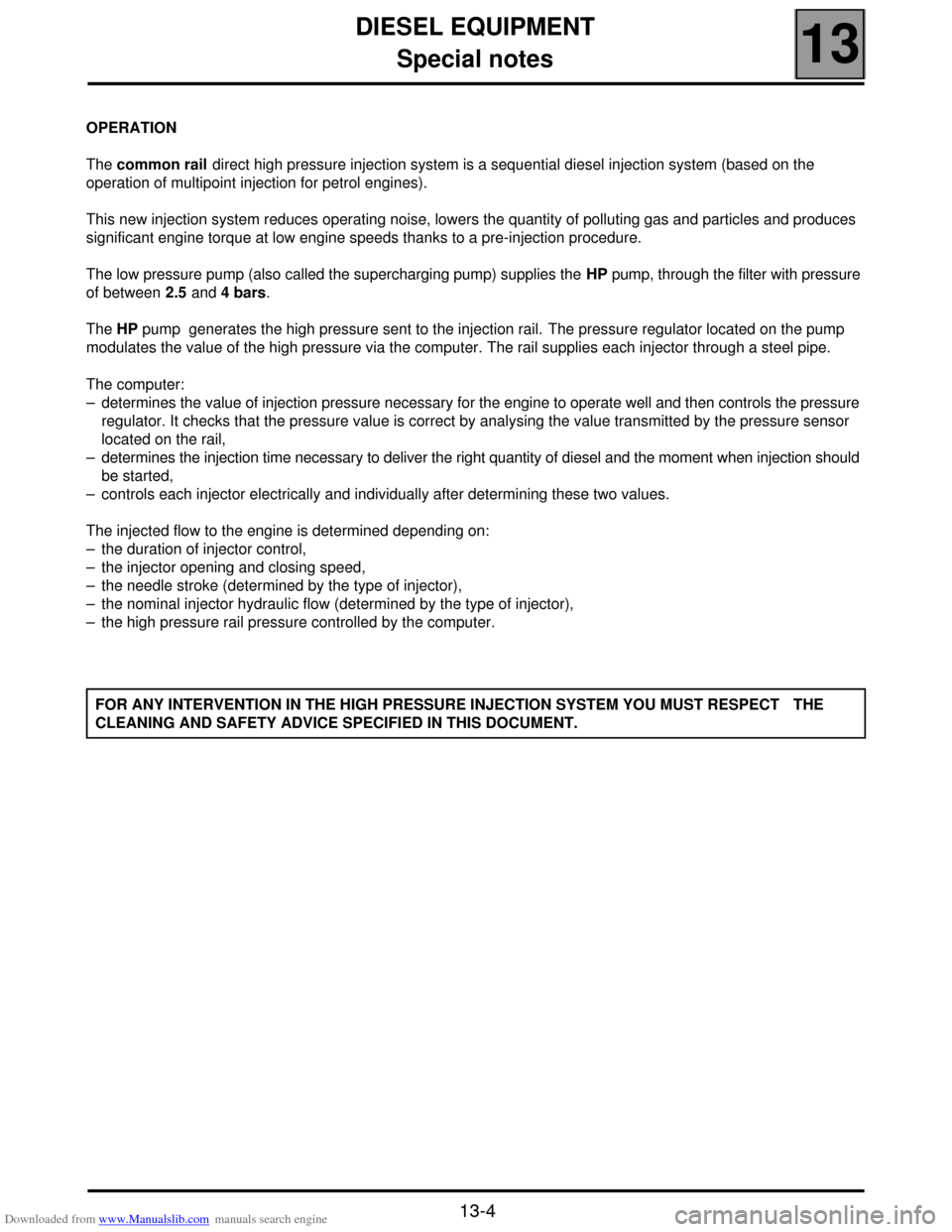
Downloaded from www.Manualslib.com manuals search engine DIESEL EQUIPMENT
Special notes
13
13-4
OPERATION
The common rail direct high pressure injection system is a sequential diesel injection system (based on the
operation of multipoint injection for petrol engines).
This new injection system reduces operating noise, lowers the quantity of polluting gas and particles and produces
significant engine torque at low engine speeds thanks to a pre-injection procedure.
The low pressure pump (also called the supercharging pump) supplies the HP pump, through the filter with pressure
of between 2.5 and 4 bars.
The HP pump generates the high pressure sent to the injection rail. The pressure regulator located on the pump
modulates the value of the high pressure via the computer. The rail supplies each injector through a steel pipe.
The computer:
– determines the value of injection pressure necessary for the engine to operate well and then controls the pressure
regulator. It checks that the pressure value is correct by analysing the value transmitted by the pressure sensor
located on the rail,
– determines the injection time necessary to deliver the right quantity of diesel and the moment when injection should
be started,
– controls each injector electrically and individually after determining these two values.
The injected flow to the engine is determined depending on:
– the duration of injector control,
– the injector opening and closing speed,
– the needle stroke (determined by the type of injector),
– the nominal injector hydraulic flow (determined by the type of injector),
– the high pressure rail pressure controlled by the computer.
FOR ANY INTERVENTION IN THE HIGH PRESSURE INJECTION SYSTEM YOU MUST RESPECT THE
CLEANING AND SAFETY ADVICE SPECIFIED IN THIS DOCUMENT.
Page 56 of 118
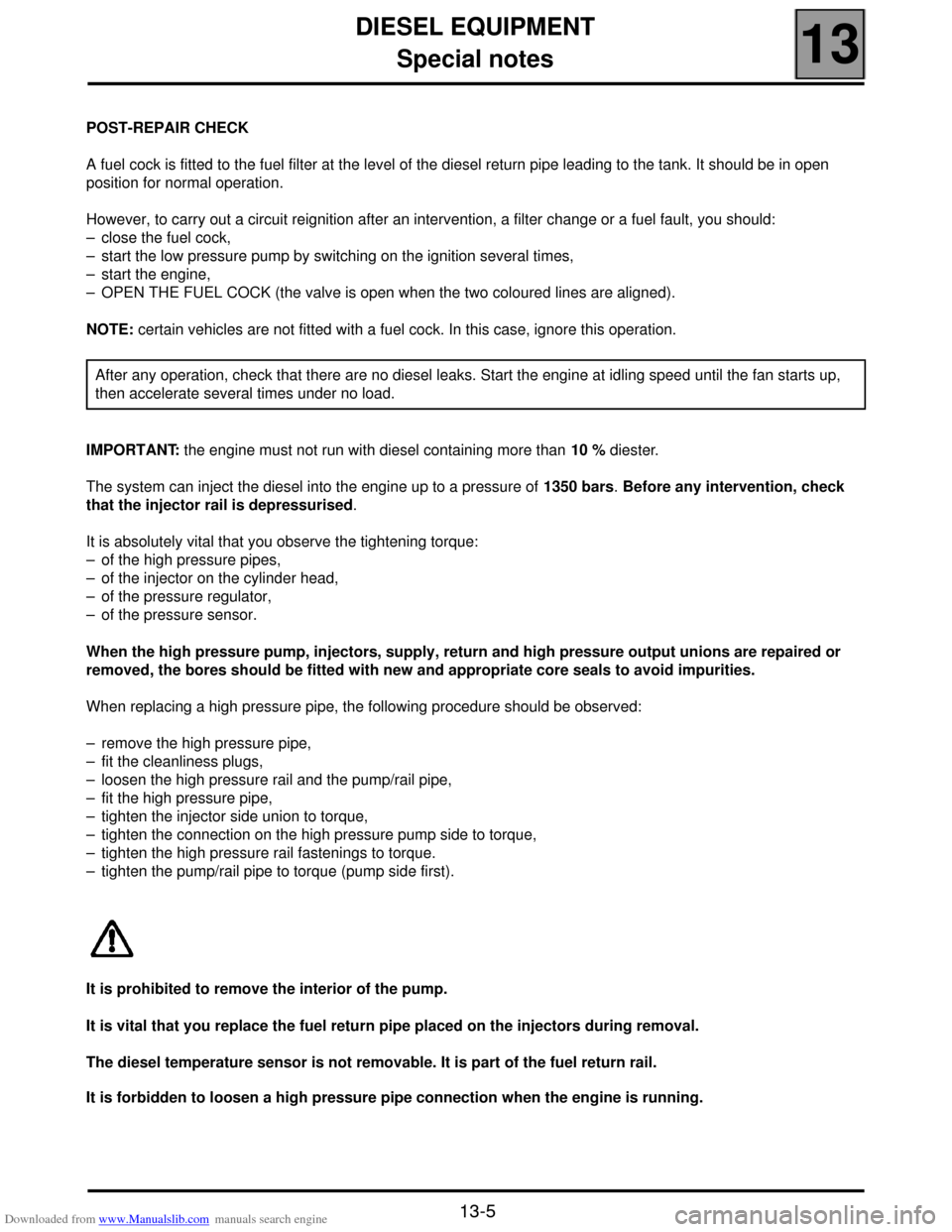
Downloaded from www.Manualslib.com manuals search engine DIESEL EQUIPMENT
Special notes
13
13-5
POST-REPAIR CHECK
A fuel cock is fitted to the fuel filter at the level of the diesel return pipe leading to the tank. It should be in open
position for normal operation.
However, to carry out a circuit reignition after an intervention, a filter change or a fuel fault, you should:
– close the fuel cock,
– start the low pressure pump by switching on the ignition several times,
– start the engine,
– OPEN THE FUEL COCK (the valve is open when the two coloured lines are aligned).
NOTE: certain vehicles are not fitted with a fuel cock. In this case, ignore this operation.
IMPORTANT: the engine must not run with diesel containing more than 10 % diester.
The system can inject the diesel into the engine up to a pressure of 1350 bars. Before any intervention, check
that the injector rail is depressurised.
It is absolutely vital that you observe the tightening torque:
– of the high pressure pipes,
– of the injector on the cylinder head,
– of the pressure regulator,
– of the pressure sensor.
When the high pressure pump, injectors, supply, return and high pressure output unions are repaired or
removed, the bores should be fitted with new and appropriate core seals to avoid impurities.
When replacing a high pressure pipe, the following procedure should be observed:
– remove the high pressure pipe,
– fit the cleanliness plugs,
– loosen the high pressure rail and the pump/rail pipe,
– fit the high pressure pipe,
– tighten the injector side union to torque,
– tighten the connection on the high pressure pump side to torque,
– tighten the high pressure rail fastenings to torque.
– tighten the pump/rail pipe to torque (pump side first).
It is prohibited to remove the interior of the pump.
It is vital that you replace the fuel return pipe placed on the injectors during removal.
The diesel temperature sensor is not removable. It is part of the fuel return rail.
It is forbidden to loosen a high pressure pipe connection when the engine is running.After any operation, check that there are no diesel leaks. Start the engine at idling speed until the fan starts up,
then accelerate several times under no load.
Page 60 of 118
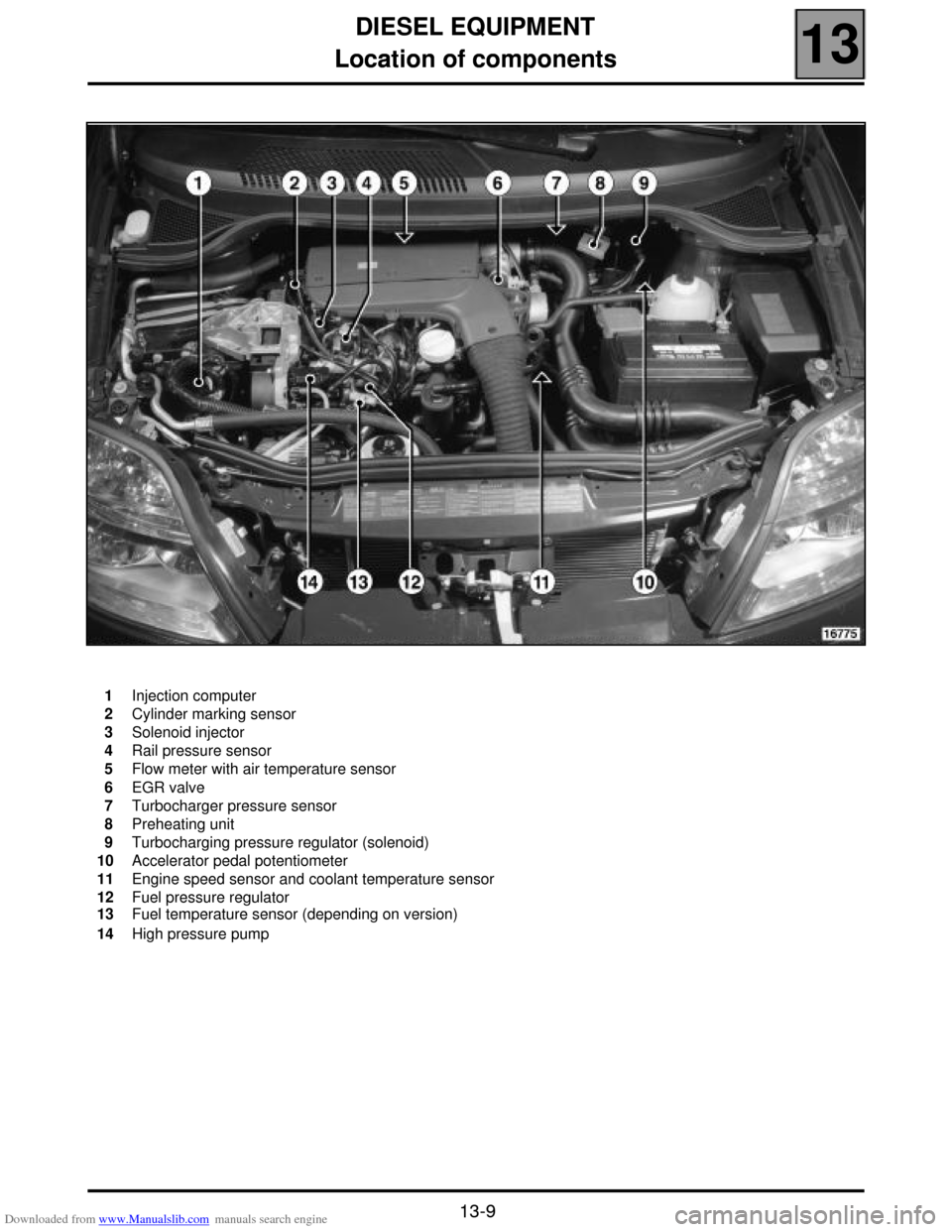
Downloaded from www.Manualslib.com manuals search engine DIESEL EQUIPMENT
Location of components
13
13-9
Location of components
1
2
3
4
5
6
7
8
9
10
11
12
13
14Injection computer
Cylinder marking sensor
Solenoid injector
Rail pressure sensor
Flow meter with air temperature sensor
EGR valve
Turbocharger pressure sensor
Preheating unit
Turbocharging pressure regulator (solenoid)
Accelerator pedal potentiometer
Engine speed sensor and coolant temperature sensor
Fuel pressure regulator
Fuel temperature sensor (depending on version)
High pressure pump
Page 63 of 118
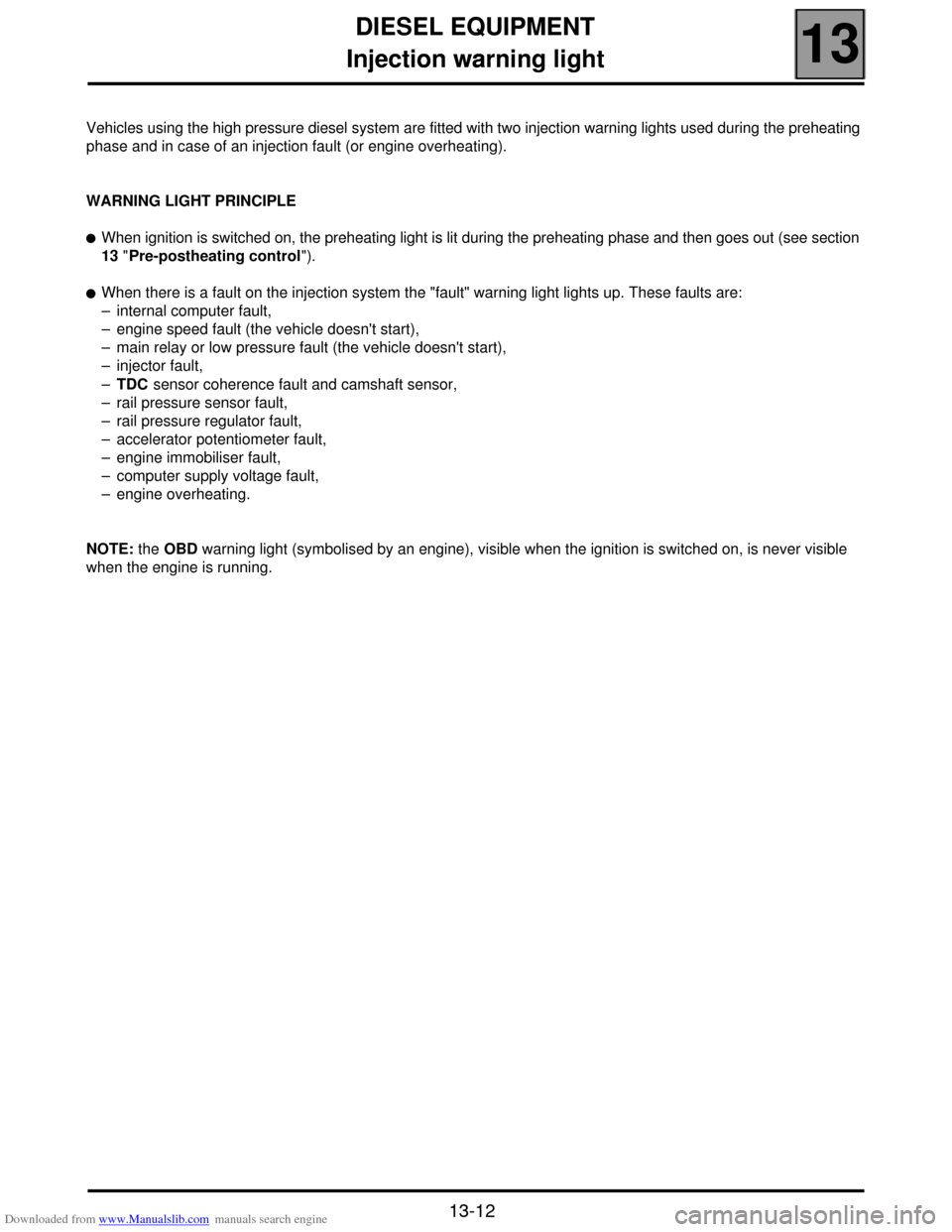
Downloaded from www.Manualslib.com manuals search engine DIESEL EQUIPMENT
Injection warning light
13
13-12
Injection warning light
Vehicles using the high pressure diesel system are fitted with two injection warning lights used during the preheating
phase and in case of an injection fault (or engine overheating).
WARNING LIGHT PRINCIPLE
!When ignition is switched on, the preheating light is lit during the preheating phase and then goes out (see section
13 "Pre-postheating control").
!When there is a fault on the injection system the "fault" warning light lights up. These faults are:
– internal computer fault,
– engine speed fault (the vehicle doesn't start),
– main relay or low pressure fault (the vehicle doesn't start),
– injector fault,
–TDC sensor coherence fault and camshaft sensor,
– rail pressure sensor fault,
– rail pressure regulator fault,
– accelerator potentiometer fault,
– engine immobiliser fault,
– computer supply voltage fault,
– engine overheating.
NOTE: the OBD warning light (symbolised by an engine), visible when the ignition is switched on, is never visible
when the engine is running.
Page 89 of 118
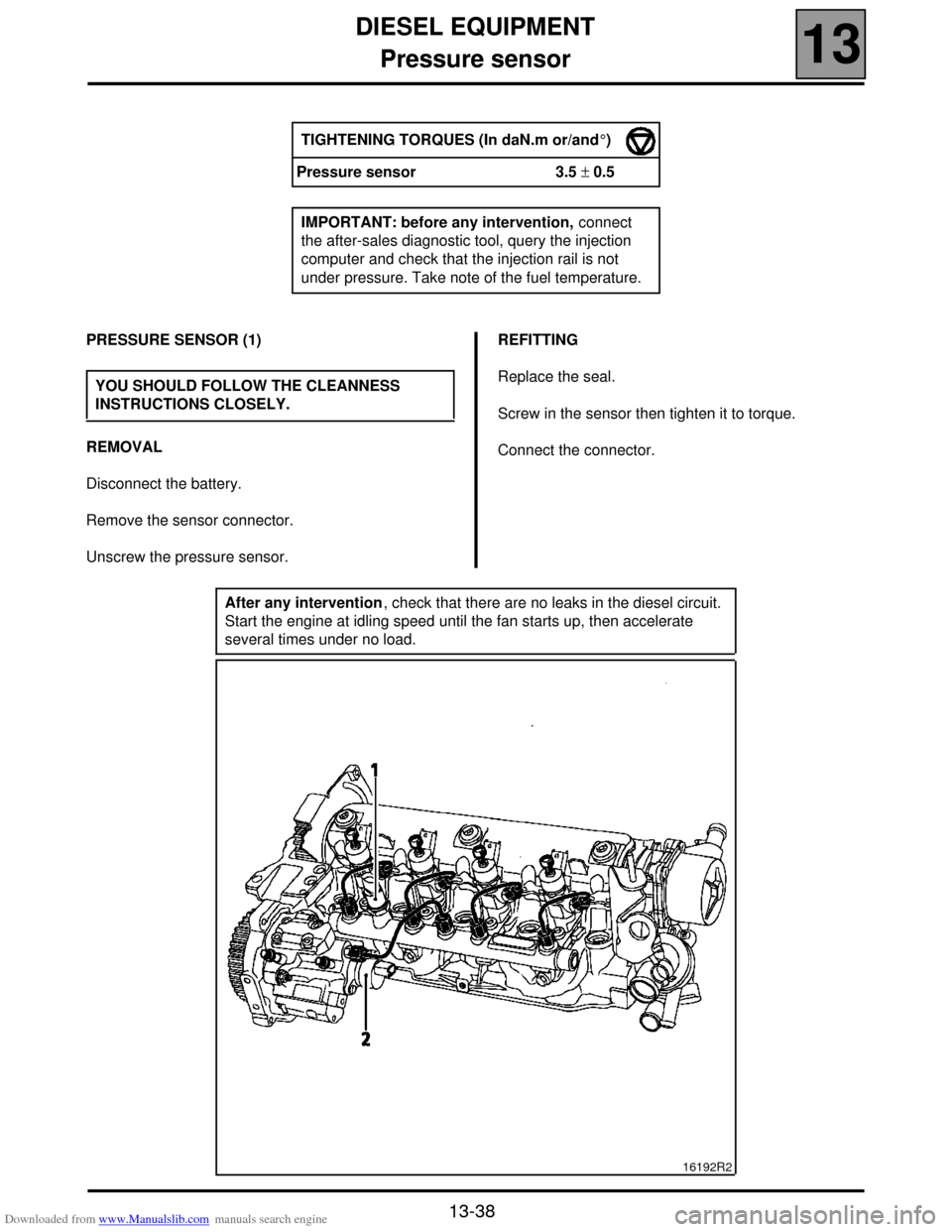
Downloaded from www.Manualslib.com manuals search engine DIESEL EQUIPMENT
Pressure sensor
13
13-38
Pressure sensor
TIGHTENING TORQUES (In daN.m or/and°)
Pressure sensor 3.5 ± 0.5
IMPORTANT: before any intervention, connect
the after-sales diagnostic tool, query the injection
computer and check that the injection rail is not
under pressure. Take note of the fuel temperature.
PRESSURE SENSOR (1)
REMOVAL
Disconnect the battery.
Remove the sensor connector.
Unscrew the pressure sensor.REFITTING
Replace the seal.
Screw in the sensor then tighten it to torque.
Connect the connector. YOU SHOULD FOLLOW THE CLEANNESS
INSTRUCTIONS CLOSELY.
After any intervention, check that there are no leaks in the diesel circuit.
Start the engine at idling speed until the fan starts up, then accelerate
several times under no load.
16192R2
Page 90 of 118
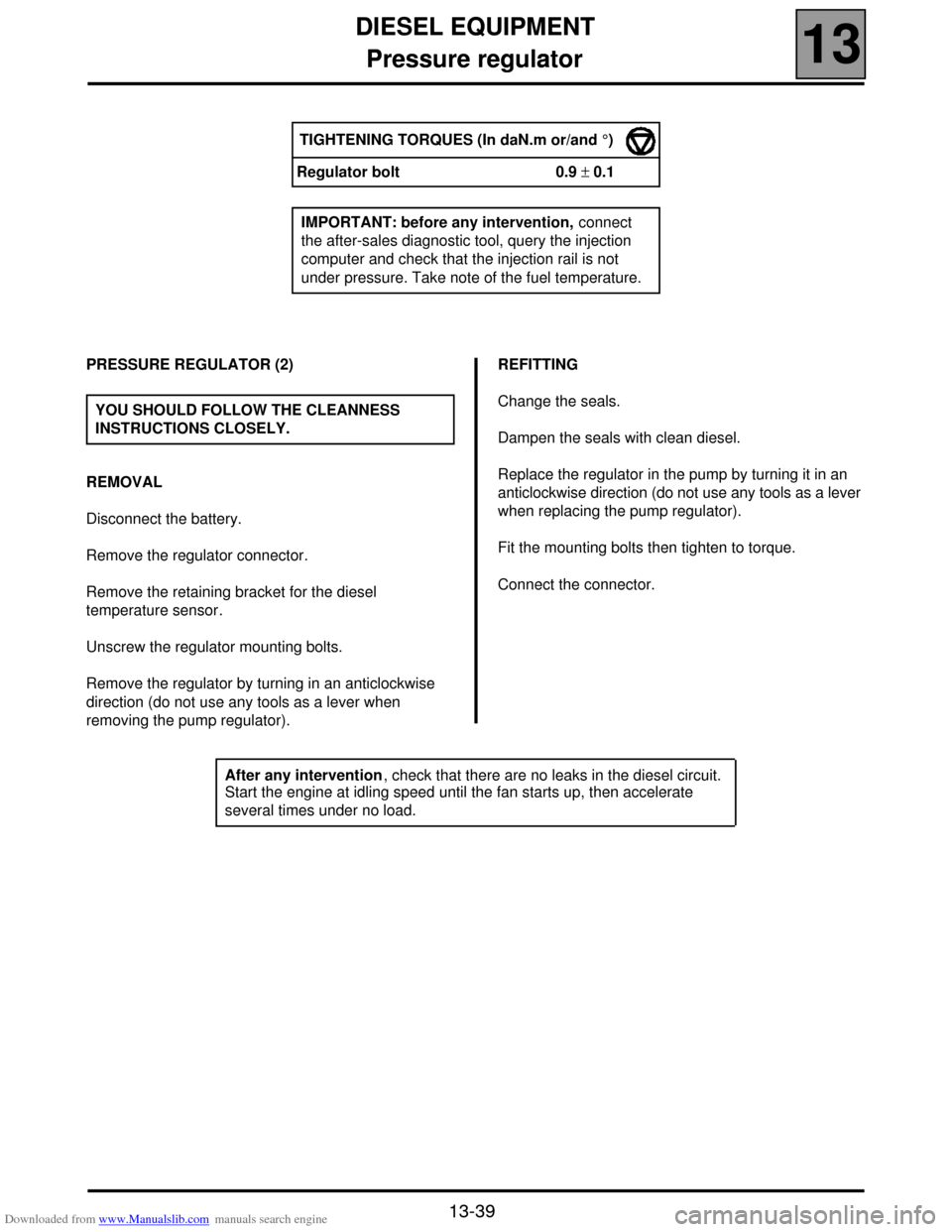
Downloaded from www.Manualslib.com manuals search engine DIESEL EQUIPMENT
Pressure regulator
13
13-39
Pressure regulator
TIGHTENING TORQUES (In daN.m or/and °)
Regulator bolt 0.9 ± 0.1
IMPORTANT: before any intervention, connect
the after-sales diagnostic tool, query the injection
computer and check that the injection rail is not
under pressure. Take note of the fuel temperature.
PRESSURE REGULATOR (2)
REMOVAL
Disconnect the battery.
Remove the regulator connector.
Remove the retaining bracket for the diesel
temperature sensor.
Unscrew the regulator mounting bolts.
Remove the regulator by turning in an anticlockwise
direction (do not use any tools as a lever when
removing the pump regulator).REFITTING
Change the seals.
Dampen the seals with clean diesel.
Replace the regulator in the pump by turning it in an
anticlockwise direction (do not use any tools as a lever
when replacing the pump regulator).
Fit the mounting bolts then tighten to torque.
Connect the connector. YOU SHOULD FOLLOW THE CLEANNESS
INSTRUCTIONS CLOSELY.
After any intervention, check that there are no leaks in the diesel circuit.
Start the engine at idling speed until the fan starts up, then accelerate
several times under no load.