display RENAULT SCENIC 2009 J84 / 2.G Engine And Peripherals EDC16 Manual PDF
[x] Cancel search | Manufacturer: RENAULT, Model Year: 2009, Model line: SCENIC, Model: RENAULT SCENIC 2009 J84 / 2.GPages: 273
Page 218 of 273
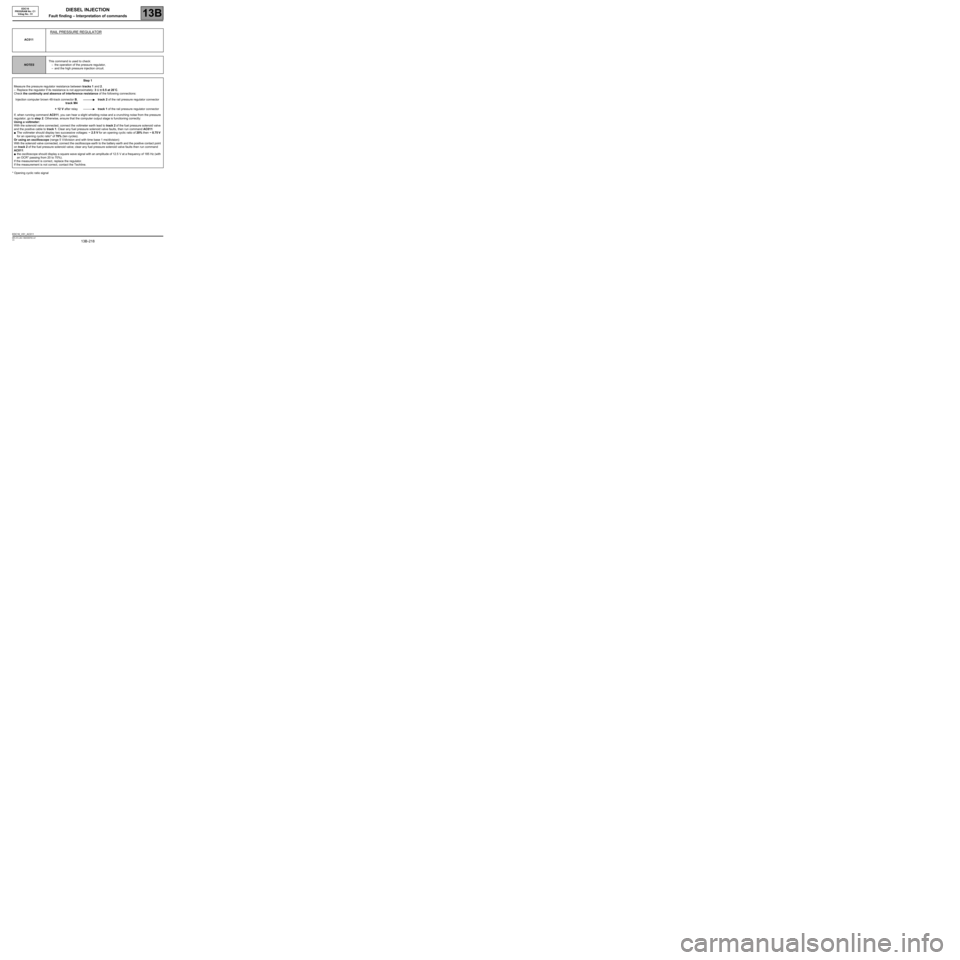
DIESEL INJECTION
Fault finding – Interpretation of commands13B
13B -218V3 MR-372-J84-13B250$765.mif
EDC16
PROGRAM No: C1
Vdiag No.: 51
* Opening cyclic ratio signalAC011
RAIL PRESSURE REGULATOR
NOTESThis command is used to check:
–the operation of the pressure regulator,
–and the high pressure injection circuit.
Step 1
Measure the pressure regulator resistance between tracks 1 and 2.
–Replace the regulator if its resistance is not approximately: 3 Ω ± 0.5 at 20˚C.
Check the continuity and absence of interference resistance of the following connections:
Injection computer brown 48-track connector B,
track M4track 2 of the rail pressure regulator connector
+ 12 V after relaytrack 1 of the rail pressure regulator connector
If, when running command AC011, you can hear a slight whistling noise and a crunching noise from the pressure
regulator, go to step 2. Otherwise, ensure that the computer output stage is functioning correctly:
Using a voltmeter:
With the solenoid valve connected, connect the voltmeter earth lead to track 2 of the fuel pressure solenoid valve
and the positive cable to track 1. Clear any fuel pressure solenoid valve faults, then run command AC011:
●The voltmeter should display two successive voltages: ~ 2.5 V for an opening cyclic ratio of 20% then ~ 8.75 V
for an opening cyclic ratio* of 70% (ten cycles).
Or using an oscilloscope (range 5 V/division and with time base 1 ms/division):
With the solenoid valve connected, connect the oscilloscope earth to the battery earth and the positive contact point
on track 2 of the fuel pressure solenoid valve; clear any fuel pressure solenoid valve faults then run command
AC011:
●the oscilloscope should display a square wave signal with an amplitude of 12.5 V at a frequency of 185 Hz (with
an OCR* passing from 20 to 70%).
If the measurement is correct, replace the regulator.
If the measurement is not correct, contact the Techline.
EDC16_V51_AC011
Page 220 of 273
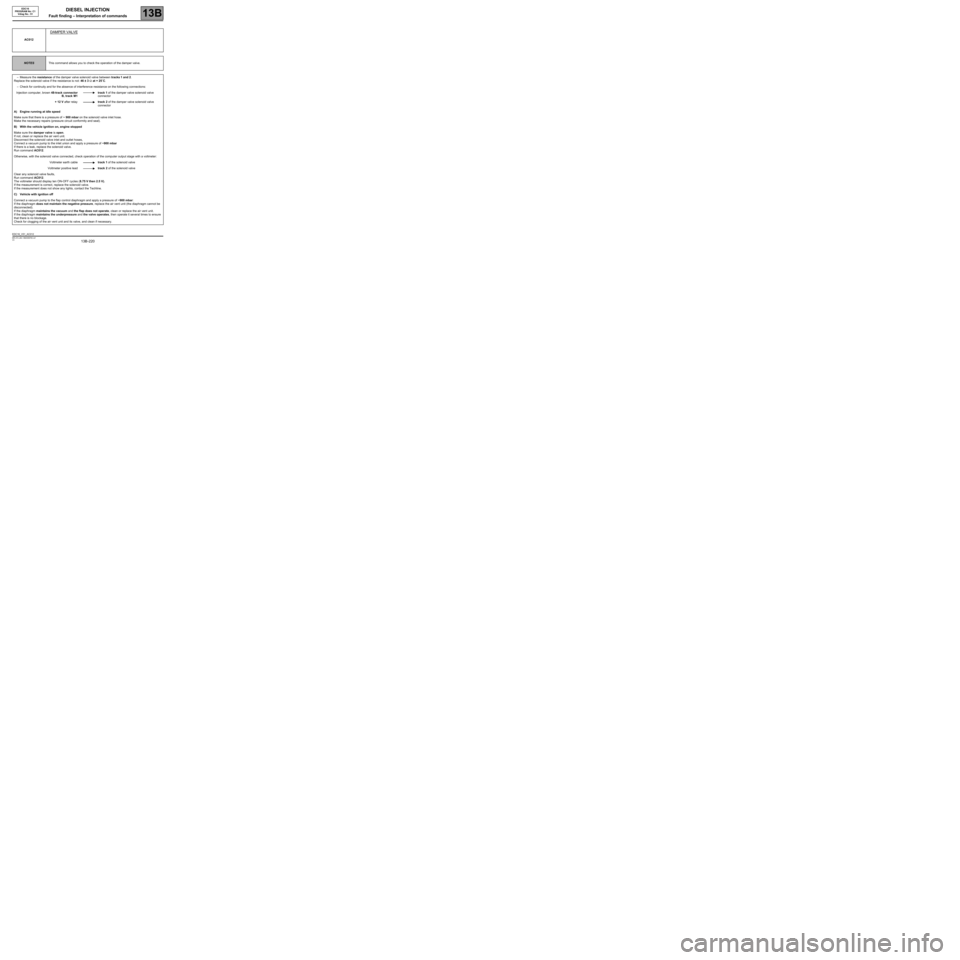
DIESEL INJECTION
Fault finding – Interpretation of commands13B
13B -220V3 MR-372-J84-13B250$765.mif
EDC16
PROGRAM No: C1
Vdiag No.: 51
AC012
DAMPER VALVE
NOTESThis command allows you to check the operation of the damper valve.
–Measure the resistance of the damper valve solenoid valve between tracks 1 and 2.
Replace the solenoid valve if the resistance is not: 46 ± 3 Ω at + 25˚C.
–Check for continuity and for the absence of interference resistance on the following connections:
Injection computer, brown 48-track connector
B, track M1track 1 of the damper valve solenoid valve
connector
+ 12 V after relaytrack 2 of the damper valve solenoid valve
connector
A) Engine running at idle speed
Make sure that there is a pressure of ~ 900 mbar on the solenoid valve inlet hose.
Make the necessary repairs (pressure circuit conformity and seal).
B) With the vehicle ignition on, engine stopped
Make sure the damper valve is open.
If not, clean or replace the air vent unit.
Disconnect the solenoid valve inlet and outlet hoses,
Connect a vacuum pump to the inlet union and apply a pressure of ~900 mbar
If there is a leak, replace the solenoid valve.
Run command AC012.
Otherwise, with the solenoid valve connected, check operation of the computer output stage with a voltmeter:
Voltmeter earth cabletrack 1 of the solenoid valve
Voltmeter positive leadtrack 2 of the solenoid valve
Clear any solenoid valve faults,
Run command AC012.
The voltmeter should display ten ON-OFF cycles (8.75 V then 2.5 V).
If the measurement is correct, replace the solenoid valve.
If the measurement does not show any lights, contact the Techline.
C) Vehicle with ignition off
Connect a vacuum pump to the flap control diaphragm and apply a pressure of ~900 mbar:
If the diaphragm does not maintain the negative pressure, replace the air vent unit (the diaphragm cannot be
disconnected).
If the diaphragm maintains the vacuum and the flap does not operate, clean or replace the air vent unit.
If the diaphragm maintains the underpressure and the valve operates, then operate it several times to ensure
that there is no blockage.
Check for clogging of the air vent unit and its valve, and clean if necessary.
EDC16_V51_AC012
Page 224 of 273
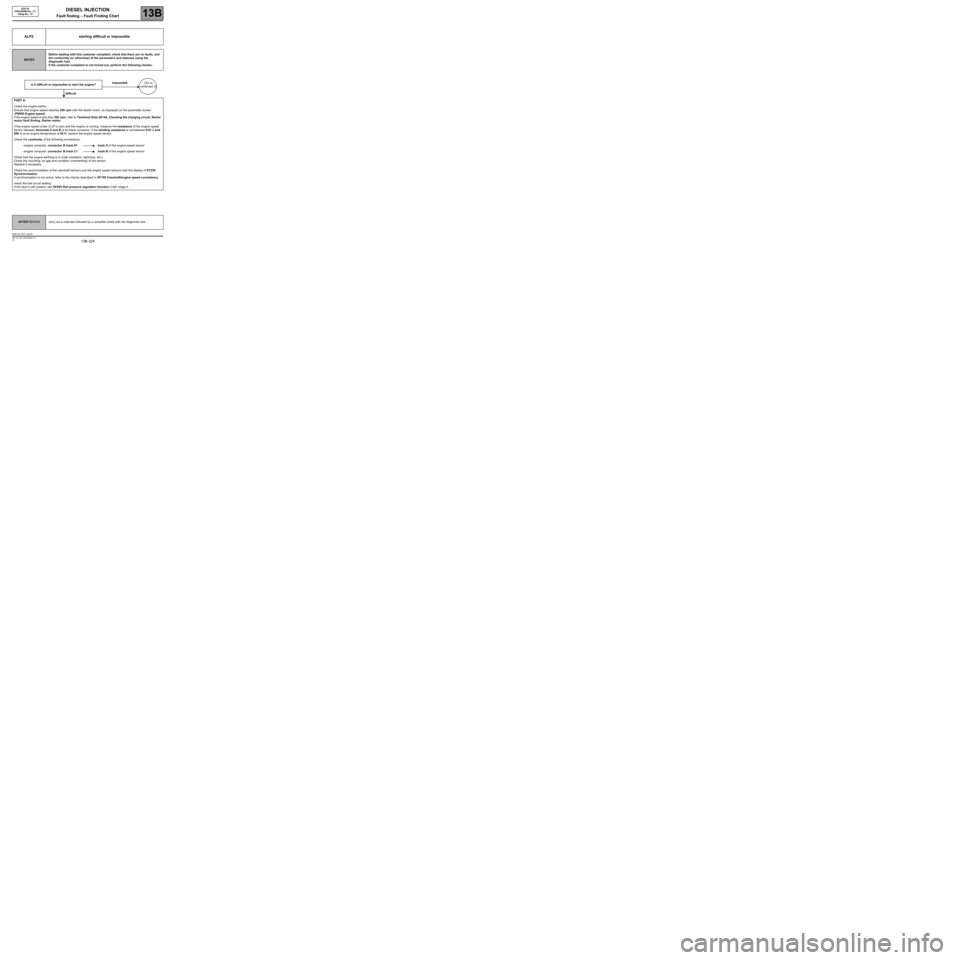
DIESEL INJECTION
Fault finding – Fault Finding Chart13B
13B -224V3 MR-372-J84-13B250$855.mif
EDC16
PROGRAM No.: C1
Vdiag No.: 51
ALP2 starting difficult or impossible
NOTESBefore dealing with this customer complaint, check that there are no faults, and
the conformity (or otherwise) of the parameters and statuses using the
diagnostic tool.
If the customer complaint is not ironed out, perform the following checks:
Is it difficult or impossible to start the engine?impossible(Go to
continued 2)
difficult
PART A:
Check the engine earths.
Ensure that engine speed reaches 250 rpm with the starter motor, as displayed on the parameter screen
(PR055 Engine speed).
If the engine speed is less than 250 rpm, refer to Technical Note 6014A, Checking the charging circuit, Starter
motor fault finding, Starter motor.
If the engine speed under CLIP is zero and the engine is running, measure the resistance of the engine speed
sensor between terminals A and B of its black connector. If the winding resistance is not between 510 Ω and
850 Ω at an engine temperature of 20˚C, replace the engine speed sensor.
Check the continuity of the following connections:
–engine computer, connector B track D1 track A of the engine speed sensor
–engine computer, connector B track C1 track B of the engine speed sensor
Check that the engine earthing is in order (oxidation, tightness, etc.).
Check the mounting, air gap and condition (overheating) of the sensor.
Replace if necessary.
Check the synchronisation of the camshaft sensors and the engine speed sensors with the display of ET238
Synchronisation.
If synchronisation is not active, refer to the checks described in DF195 Camshaft/engine speed consistency.
check the fuel circuit sealing.
If the fault is still present, see DF053 Rail pressure regulation function 2.def, stage 4.
AFTER REPAIRcarry out a road test followed by a complete check with the diagnostic tool.
EDC16_V51_ALP2
Page 246 of 273
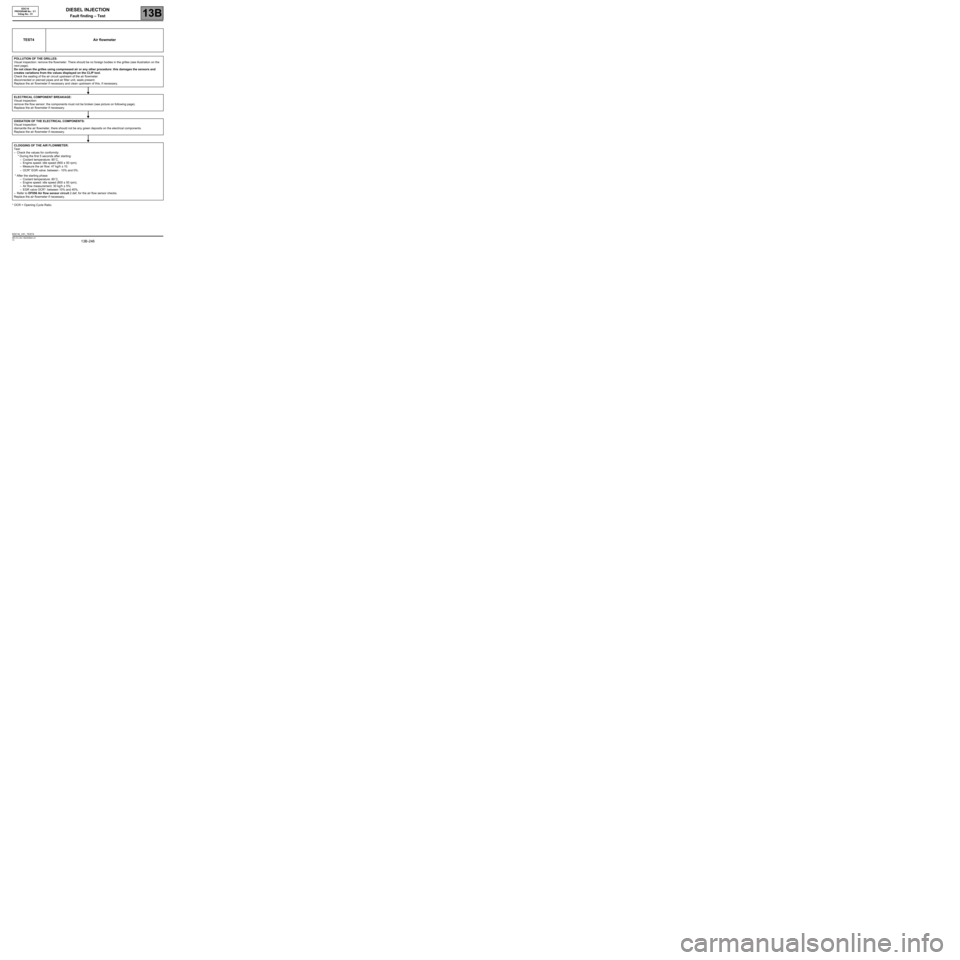
DIESEL INJECTION
Fault finding – Test13B
13B -246V3 MR-372-J84-13B250$900.mif
EDC16
PROGRAM No.: C1
Vdiag No.: 51
* OCR = Opening Cycle Ratio.
TEST4 Air flowmeter
POLLUTION OF THE GRILLES:
Visual inspection: remove the flowmeter. There should be no foreign bodies in the grilles (see illustration on the
next page).
Do not clean the grilles using compressed air or any other procedure: this damages the sensors and
creates variations from the values displayed on the CLIP tool.
Check the sealing of the air circuit upstream of the air flowmeter:
disconnected or pierced pipes and air filter unit, seals present.
Replace the air flowmeter if necessary and clean upstream of this, if necessary.
ELECTRICAL COMPONENT BREAKAGE:
Visual inspection:
remove the flow sensor: the components must not be broken (see picture on following page).
Replace the air flowmeter if necessary.
OXIDATION OF THE ELECTRICAL COMPONENTS:
Visual inspection:
dismantle the air flowmeter, there should not be any green deposits on the electrical components.
Replace the air flowmeter if necessary.
CLOGGING OF THE AIR FLOWMETER:
Test:
–Check the values for conformity:
* During the first 5 seconds after starting:
–Coolant temperature: 80˚C,
–Engine speed: idle speed (800 ± 50 rpm);
–Measure the air flow: 47 kg/h ± 10.
–OCR* EGR valve: between - 10% and 0%.
* After the starting phase:
–Coolant temperature: 80˚C,
–Engine speed: idle speed (800 ± 50 rpm);
–Air flow measurement: 30 kg/h ± 5%;
–EGR valve OCR*: between 10% and 40%.
–Refer to DF056 Air flow sensor circuit 2.def, for the air flow sensor checks.
Replace the air flowmeter if necessary.
EDC16_V51_TEST4
Page 248 of 273
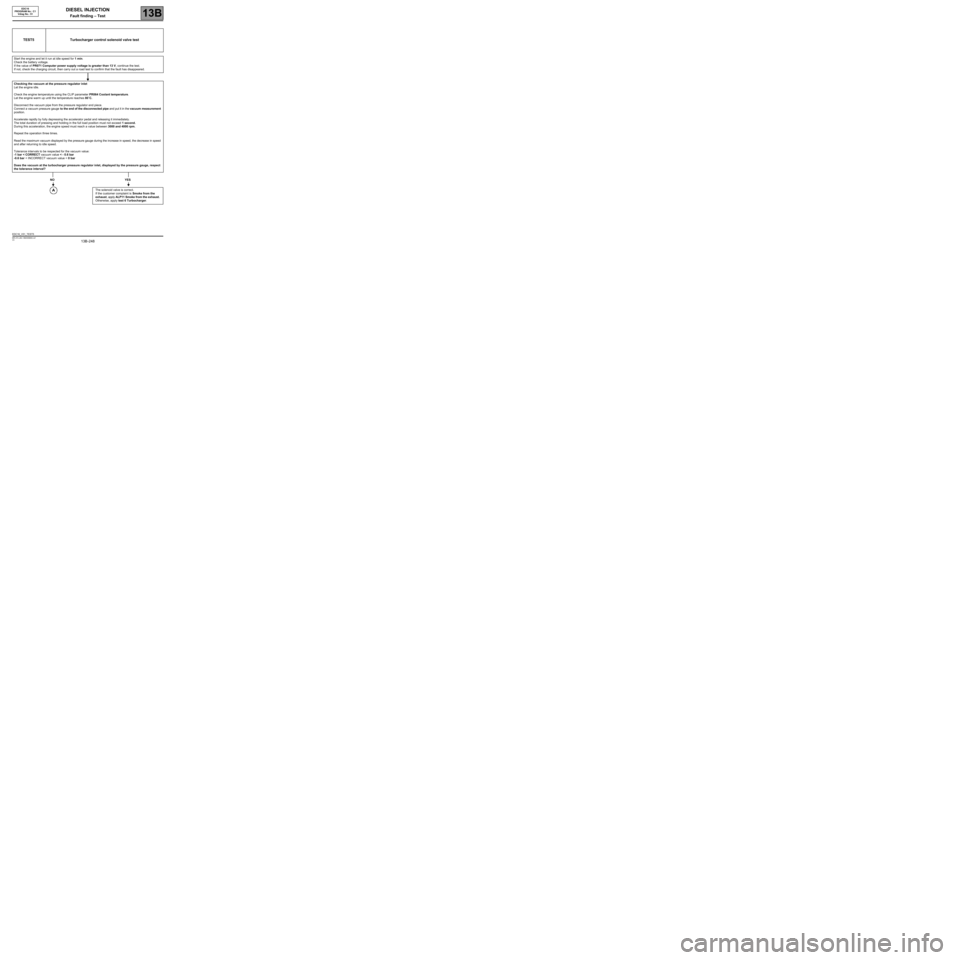
DIESEL INJECTION
Fault finding – Test13B
13B -248V3 MR-372-J84-13B250$900.mif
EDC16
PROGRAM No.: C1
Vdiag No.: 51
TEST5 Turbocharger control solenoid valve test
Start the engine and let it run at idle speed for 1 min.
Check the battery voltage.
If the value of PR071 Computer power supply voltage is greater than 13 V, continue the test.
If not, check the charging circuit, then carry out a road test to confirm that the fault has disappeared.
Checking the vacuum at the pressure regulator inlet
Let the engine idle.
Check the engine temperature using the CLIP parameter PR064 Coolant temperature.
Let the engine warm up until the temperature reaches 80˚C.
Disconnect the vacuum pipe from the pressure regulator end piece.
Connect a vacuum pressure gauge to the end of the disconnected pipe and put it in the vacuum measurement
position.
Accelerate rapidly by fully depressing the accelerator pedal and releasing it immediately.
The total duration of pressing and holding in the full load position must not exceed 1 second.
During this acceleration, the engine speed must reach a value between 3000 and 4000 rpm.
Repeat the operation three times.
Read the maximum vacuum displayed by the pressure gauge during the increase in speed, the decrease in speed
and after returning to idle speed.
Tolerance intervals to be respected for the vacuum value:
-1 bar < CORRECT vacuum value < - 0.6 bar
-0.6 bar < INCORRECT vacuum value < 0 bar
Does the vacuum at the turbocharger pressure regulator inlet, displayed by the pressure gauge, respect
the tolerance interval?
NO YES
The solenoid valve is correct.
If the customer complaint is Smoke from the
exhaust, apply ALP11 Smoke from the exhaust.
Otherwise, apply test 6 Turbocharger.
1
EDC16_V51_TEST5
Page 249 of 273
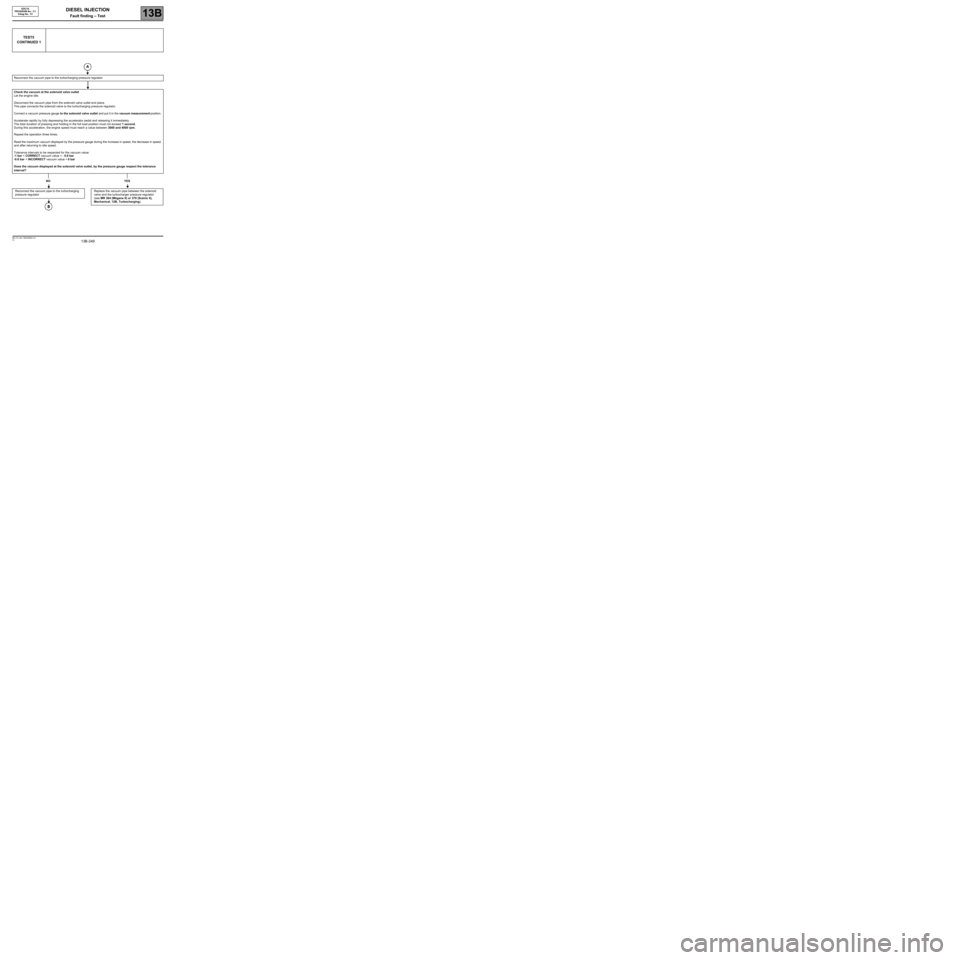
DIESEL INJECTION
Fault finding – Test13B
13B -249V3 MR-372-J84-13B250$900.mif
EDC16
PROGRAM No.: C1
Vdiag No.: 51
TEST5
CONTINUED 1
Reconnect the vacuum pipe to the turbocharging pressure regulator
Check the vacuum at the solenoid valve outlet
Let the engine idle.
Disconnect the vacuum pipe from the solenoid valve outlet end piece.
This pipe connects the solenoid valve to the turbocharging pressure regulator.
Connect a vacuum pressure gauge to the solenoid valve outlet and put it in the vacuum measurement position.
Accelerate rapidly by fully depressing the accelerator pedal and releasing it immediately.
The total duration of pressing and holding in the full load position must not exceed 1 second.
During this acceleration, the engine speed must reach a value between 3000 and 4000 rpm.
Repeat the operation three times.
Read the maximum vacuum displayed by the pressure gauge during the increase in speed, the decrease in speed
and after returning to idle speed.
Tolerance intervals to be respected for the vacuum value:
-1 bar < CORRECT vacuum value < - 0.6 bar
-0.6 bar < INCORRECT vacuum value < 0 bar
Does the vacuum displayed at the solenoid valve outlet, by the pressure gauge respect the tolerance
interval?
NO YES
Reconnect the vacuum pipe to the turbocharging
pressure regulator Replace the vacuum pipe between the solenoid
valve and the turbocharger pressure regulator
(see MR 364 (Mégane II) or 370 (Scénic II),
Mechanical, 12B, Turbocharging).
1
Page 251 of 273
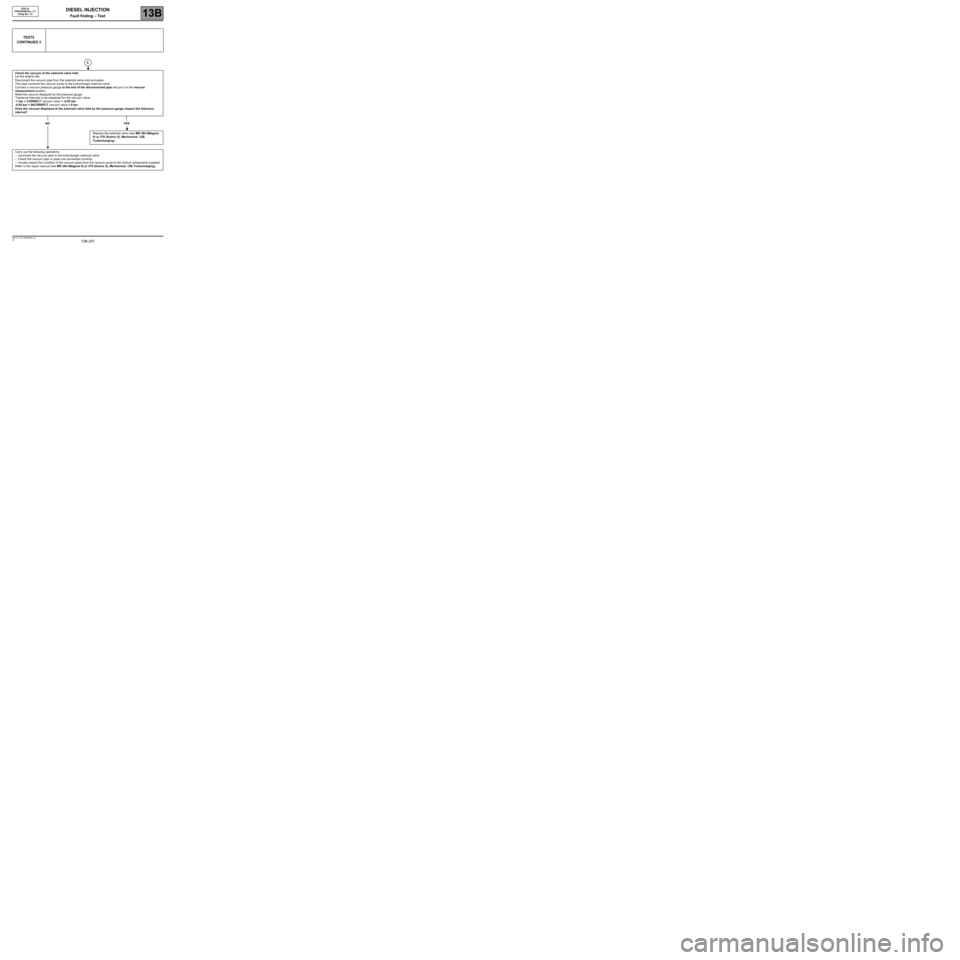
DIESEL INJECTION
Fault finding – Test13B
13B -251V3 MR-372-J84-13B250$900.mif
EDC16
PROGRAM No.: C1
Vdiag No.: 51
TEST5
CONTINUED 3
Check the vacuum at the solenoid valve inlet
Let the engine idle.
Disconnect the vacuum pipe from the solenoid valve inlet end piece.
This pipe connects the vacuum pump to the turbocharger solenoid valve.
Connect a vacuum pressure gauge to the end of the disconnected pipe and put it in the vacuum
measurement position.
Read the vacuum displayed by the pressure gauge.
Tolerance intervals to be respected for the vacuum value:
-1 bar < CORRECT vacuum value < -0.85 bar
-0.85 bar < INCORRECT vacuum value < 0 bar
Does the vacuum displayed at the solenoid valve inlet by the pressure gauge respect the tolerance
interval?
NO YES
Replace the solenoid valve (see MR 364 (Mégane
II) or 370 (Scénic II), Mechanical, 12B,
Turbocharging).
Carry out the following operations.
–reconnect the vacuum pipe to the turbocharger solenoid valve.
–Check the vacuum pipe or pipes are connected correctly.
–visually inspect the condition of the vacuum pipes from the vacuum pump to the various components supplied.
Refer to the repair manual (see MR 364 (Mégane II) or 370 (Scénic II), Mechanical, 12B Turbocharging).
C
1
Page 257 of 273
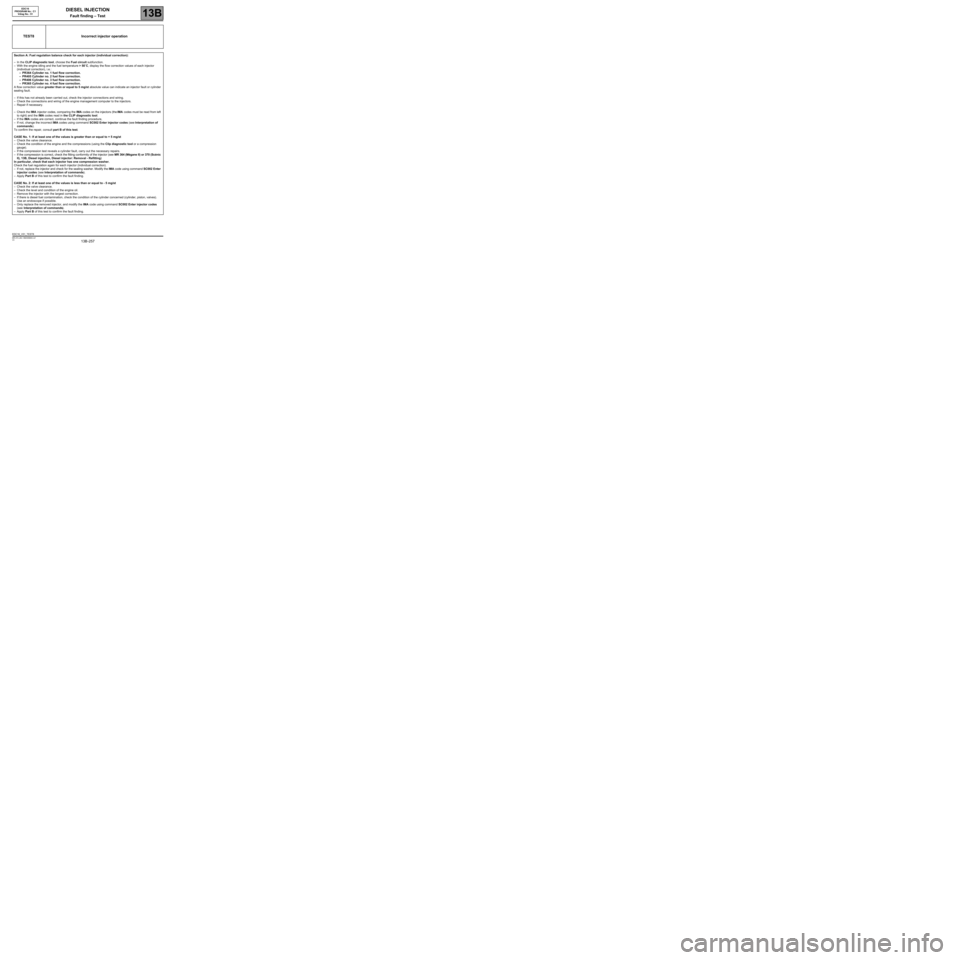
DIESEL INJECTION
Fault finding – Test13B
13B -257V3 MR-372-J84-13B250$900.mif
EDC16
PROGRAM No.: C1
Vdiag No.: 51
TEST8 Incorrect injector operation
Section A: Fuel regulation balance check for each injector (individual correction):
–In the CLIP diagnostic tool, choose the Fuel circuit subfunction.
–With the engine idling and the fuel temperature > 50˚C, display the flow correction values of each injector
(individual correction), i.e.:
–PR364 Cylinder no. 1 fuel flow correction.
–PR405 Cylinder no. 2 fuel flow correction.
–PR406 Cylinder no. 3 fuel flow correction.
–PR365 Cylinder no. 4 fuel flow correction.
A flow correction value greater than or equal to 5 mg/st absolute value can indicate an injector fault or cylinder
sealing fault.
–If this has not already been carried out, check the injector connections and wiring.
–Check the connections and wiring of the engine management computer to the injectors.
–Repair if necessary.
–Check the IMA injector codes, comparing the IMA codes on the injectors (the IMA codes must be read from left
to right) and the IMA codes read in the CLIP diagnostic tool.
–If the IMA codes are correct, continue the fault finding procedure,
–If not, change the incorrect IMA codes using command SC002 Enter injector codes (see Interpretation of
commands).
To confirm the repair, consult part B of this test.
CASE No. 1: If at least one of the values is greater than or equal to + 5 mg/st
–Check the valve clearance.
–Check the condition of the engine and the compressions (using the Clip diagnostic tool or a compression
gauge).
–If the compression test reveals a cylinder fault, carry out the necessary repairs.
–If the compression is correct, check the fitting conformity of the injector (see MR 364 (Mégane II) or 370 (Scénic
II), 13B, Diesel injection, Diesel injector: Removal - Refitting)
In particular, check that each injector has one compression washer.
Check the fuel regulation again for each injector (individual correction).
–If not, replace the injector and check for the sealing washer. Modify the IMA code using command SC002 Enter
injector codes (see Interpretation of commands).
–Apply Part B of this test to confirm the fault finding.
CASE No. 2: If at least one of the values is less than or equal to - 5 mg/st
–Check the valve clearance.
–Check the level and condition of the engine oil.
–Remove the injector with the largest correction.
–If there is diesel fuel contamination, check the condition of the cylinder concerned (cylinder, piston, valves).
Use an endoscope if possible.
–Only replace the removed injector, and modify the IMA code using command SC002 Enter injector codes
(see Interpretation of commands).
–Apply Part B of this test to confirm the fault finding.
EDC16_V51_TEST8
Page 262 of 273
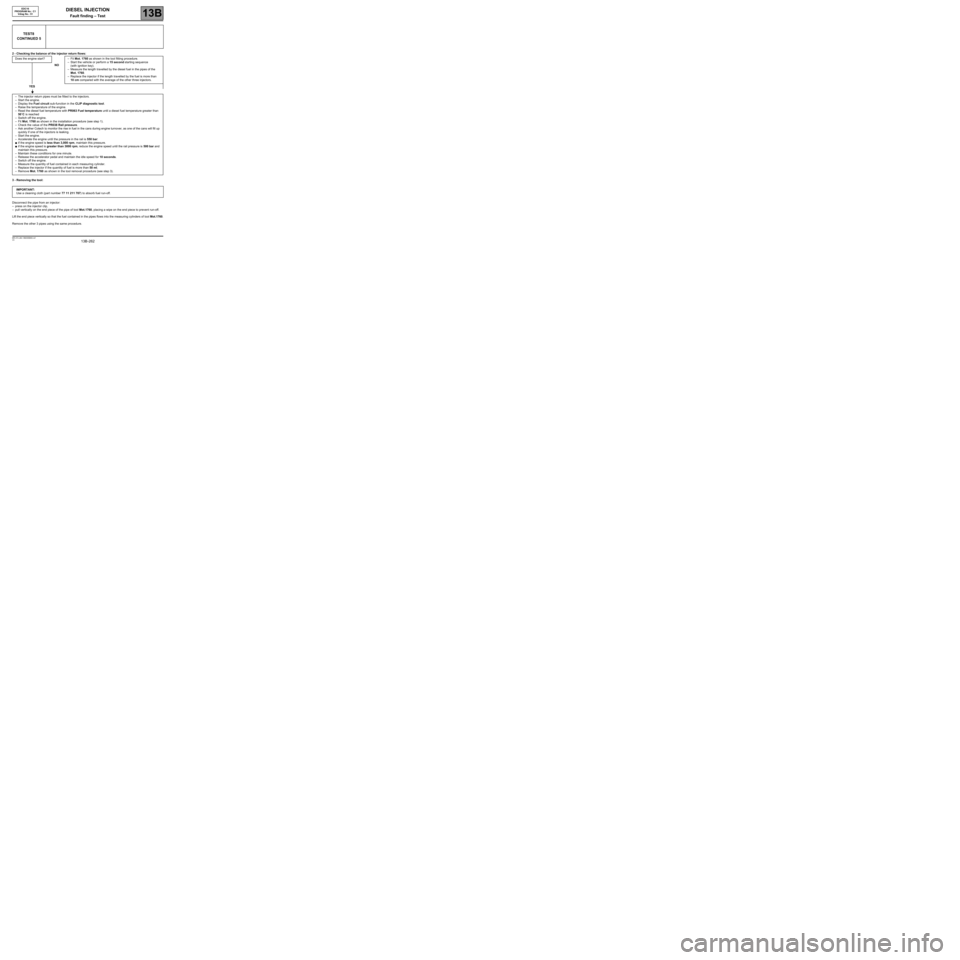
DIESEL INJECTION
Fault finding – Test13B
13B -262V3 MR-372-J84-13B250$900.mif
EDC16
PROGRAM No.: C1
Vdiag No.: 51
2 - Checking the balance of the injector return flows:
3 - Removing the tool:
Disconnect the pipe from an injector:
–press on the injector clip,
–pull vertically on the end piece of the pipe of tool Mot.1760, placing a wipe on the end piece to prevent run-off.
Lift the end piece vertically so that the fuel contained in the pipes flows into the measuring cylinders of tool Mot.1760.
Remove the other 3 pipes using the same procedure.
TEST8
CONTINUED 5
Does the engine start? – Fit Mot. 1760 as shown in the tool fitting procedure.
–Start the vehicle or perform a 15 second starting sequence
(with ignition key).
–Measure the length travelled by the diesel fuel in the pipes of the
Mot. 1760.
–Replace the injector if the length travelled by the fuel is more than
10 cm compared with the average of the other three injectors. NO
YES
–The injector return pipes must be fitted to the injectors.
–Start the engine.
–Display the Fuel circuit sub-function in the CLIP diagnostic tool.
–Raise the temperature of the engine.
–Read the diesel fuel temperature with PR063 Fuel temperature until a diesel fuel temperature greater than
50˚C is reached
–Switch off the engine.
–Fit Mot. 1760 as shown in the installation procedure (see step 1).
–Check the value of the PR038 Rail pressure.
–Ask another Cotech to monitor the rise in fuel in the cans during engine turnover, as one of the cans will fill up
quickly if one of the injectors is leaking.
–Start the engine.
–Accelerate the engine until the pressure in the rail is 550 bar:
●if the engine speed is less than 3,000 rpm, maintain this pressure.
●if the engine speed is greater than 3000 rpm, reduce the engine speed until the rail pressure is 500 bar and
maintain this pressure.
–Maintain these conditions for one minute.
–Release the accelerator pedal and maintain the idle speed for 10 seconds.
–Switch off the engine.
–Measure the quantity of fuel contained in each measuring cylinder.
–Replace the injector if the quantity of fuel is more than 50 ml.
–Remove Mot. 1760 as shown in the tool removal procedure (see step 3).
IMPORTANT:
Use a cleaning cloth (part number 77 11 211 707) to absorb fuel run-off.
Page 269 of 273
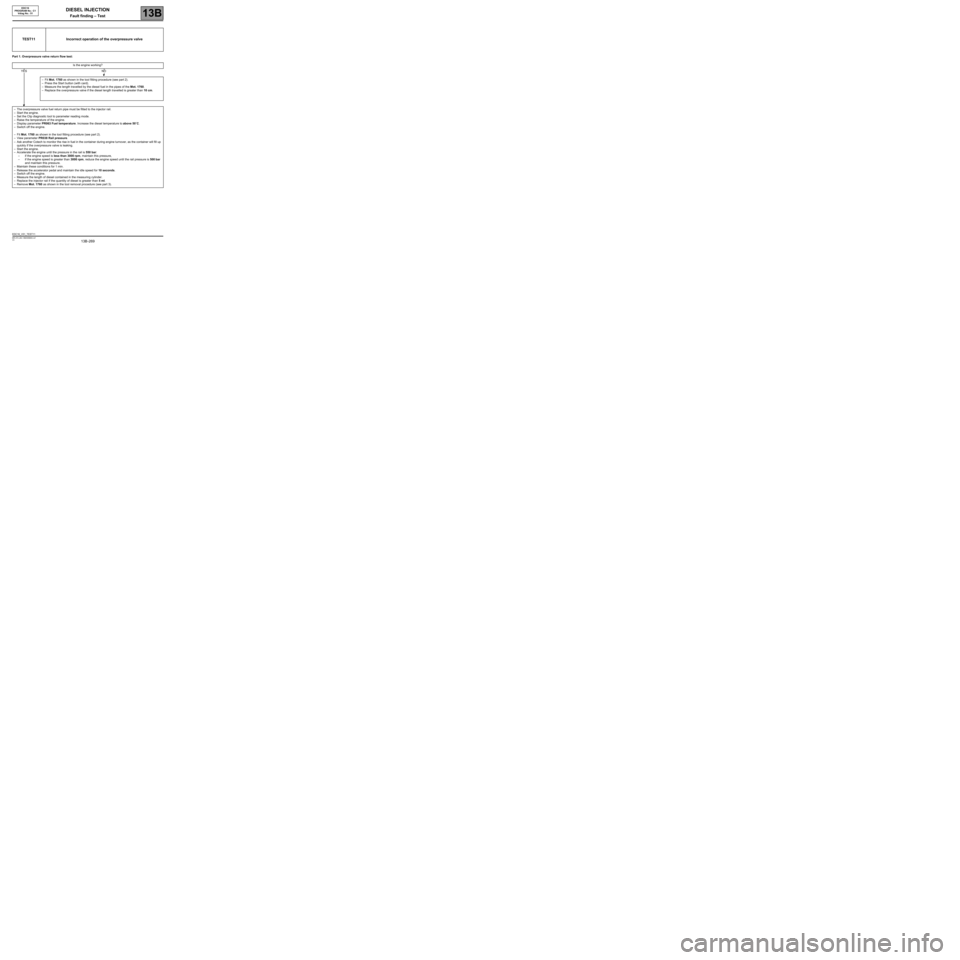
DIESEL INJECTION
Fault finding – Test13B
13B -269V3 MR-372-J84-13B250$900.mif
EDC16
PROGRAM No.: C1
Vdiag No.: 51
Part 1. Overpressure valve return flow test:
TEST11 Incorrect operation of the overpressure valve
Is the engine working?
–Fit Mot. 1760 as shown in the tool fitting procedure (see part 2).
–Press the Start button (with card).
–Measure the length travelled by the diesel fuel in the pipes of the Mot. 1760.
–Replace the overpressure valve if the diesel length travelled is greater than 10 cm.
–The overpressure valve fuel return pipe must be fitted to the injector rail.
–Start the engine.
–Set the Clip diagnostic tool to parameter reading mode.
–Raise the temperature of the engine.
–Display parameter PR063 Fuel temperature. Increase the diesel temperature to above 50˚C.
–Switch off the engine.
–Fit Mot. 1760 as shown in the tool fitting procedure (see part 2).
–View parameter PR038 Rail pressure.
–Ask another Cotech to monitor the rise in fuel in the container during engine turnover, as the container will fill up
quickly if the overpressure valve is leaking.
–Start the engine.
–Accelerate the engine until the pressure in the rail is 550 bar:
–if the engine speed is less than 3000 rpm, maintain this pressure,
–if the engine speed is greater than 3000 rpm, reduce the engine speed until the rail pressure is 500 bar
and maintain this pressure.
–Maintain these conditions for 1 min.
–Release the accelerator pedal and maintain the idle speed for 10 seconds.
–Switch off the engine.
–Measure the length of diesel contained in the measuring cylinder.
–Replace the injector rail if the quantity of diesel is greater than 5 ml.
–Remove Mot. 1760 as shown in the tool removal procedure (see part 3).
YESNO
EDC16_V51_TEST11