ABS RENAULT SCENIC 2011 J95 / 3.G Engine And Peripherals EDC16 Injection Repair Manual
[x] Cancel search | Manufacturer: RENAULT, Model Year: 2011, Model line: SCENIC, Model: RENAULT SCENIC 2011 J95 / 3.GPages: 236, PDF Size: 1.32 MB
Page 187 of 236
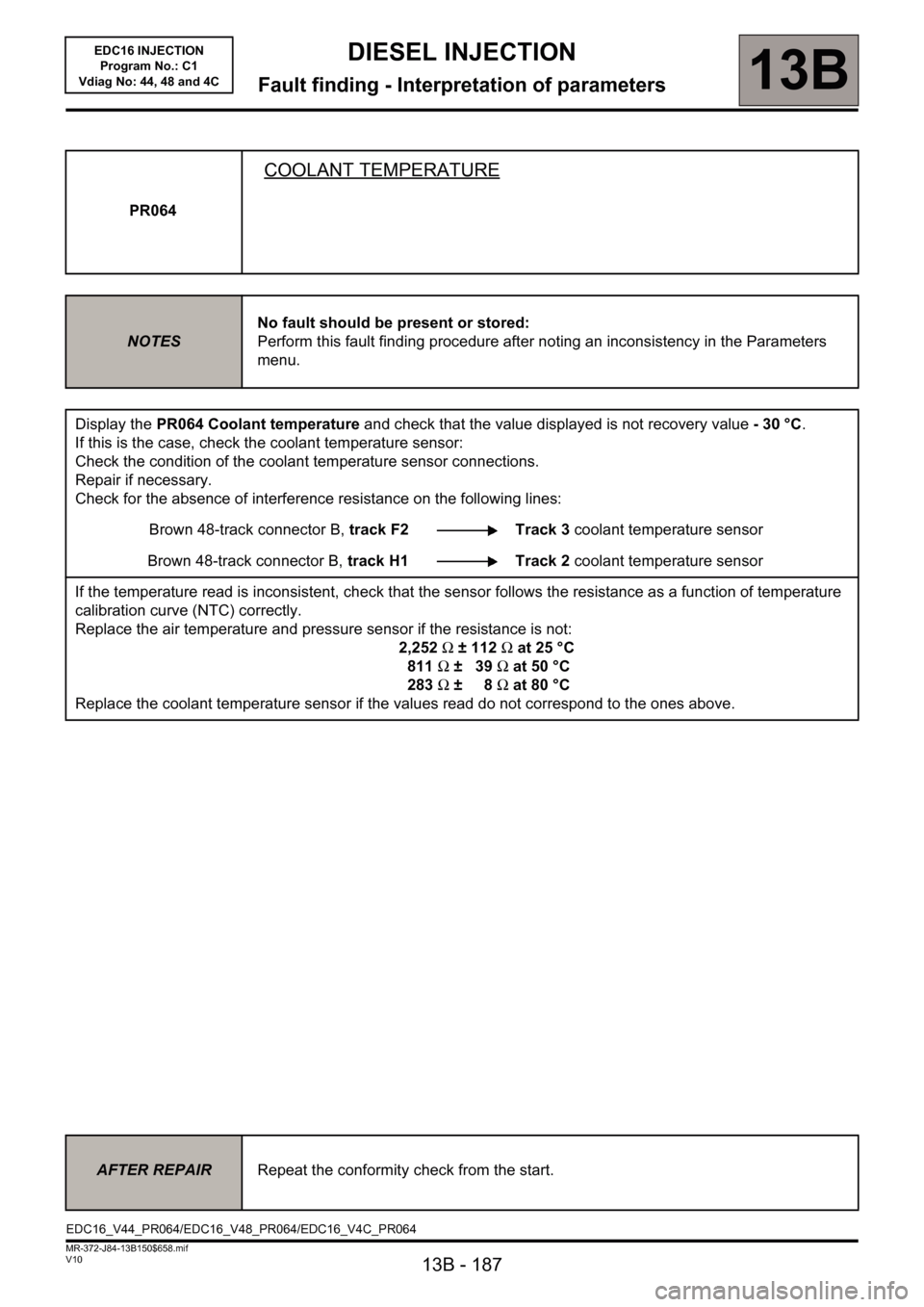
13B - 187
DIESEL INJECTION
Fault finding - Interpretation of parameters13B
V10 MR-372-J84-13B150$658.mif
EDC16 INJECTION
Program No.: C1
Vdiag No: 44, 48 and 4C
PR064
COOLANT TEMPERATURE
NOTESNo fault should be present or stored:
Perform this fault finding procedure after noting an inconsistency in the Parameters
menu.
Display the PR064 Coolant temperature and check that the value displayed is not recovery value -30°C.
If this is the case, check the coolant temperature sensor:
Check the condition of the coolant temperature sensor connections.
Repair if necessary.
Check for the absence of interference resistance on the following lines:
Brown 48-track connector B, track F2 Track 3 coolant temperature sensor
Brown 48-track connector B, track H1 Track 2 coolant temperature sensor
If the temperature read is inconsistent, check that the sensor follows the resistance as a function of temperature
calibration curve (NTC) correctly.
Replace the air temperature and pressure sensor if the resistance is not:
2,252Ω ± 112Ω at 25 °C
811Ω ±39Ω at 50 °C
283Ω ±8Ω at 80 °C
Replace the coolant temperature sensor if the values read do not correspond to the ones above.
AFTER REPAIRRepeat the conformity check from the start.
EDC16_V44_PR064/EDC16_V48_PR064/EDC16_V4C_PR064
Page 194 of 236
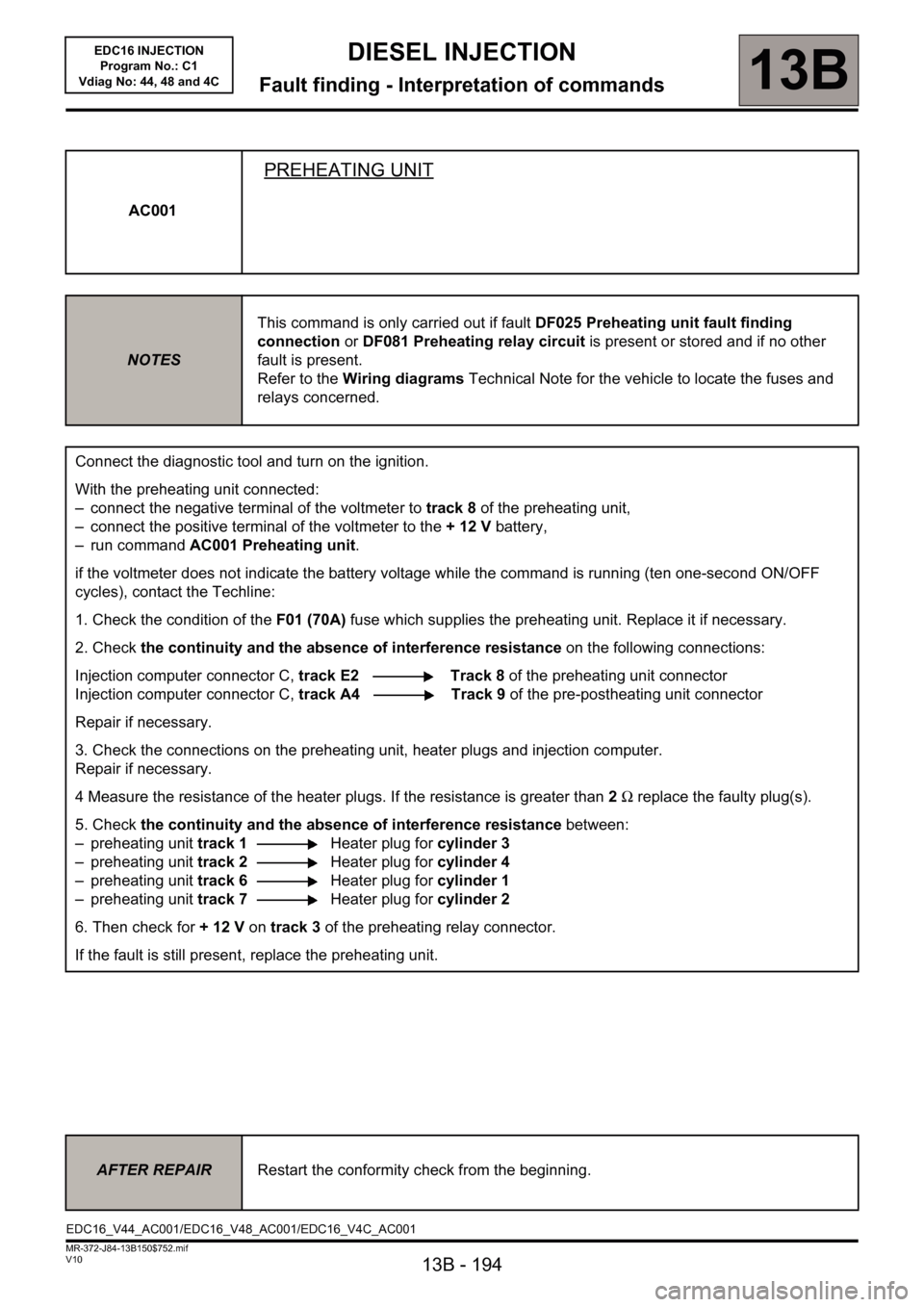
13B - 194
DIESEL INJECTION
Fault finding - Interpretation of commands13B
V10 MR-372-J84-13B150$752.mif
EDC16 INJECTION
Program No.: C1
Vdiag No: 44, 48 and 4C
AC001
PREHEATING UNIT
NOTESThis command is only carried out if fault DF025 Preheating unit fault finding
connection or DF081 Preheating relay circuit is present or stored and if no other
fault is present.
Refer to the Wiring diagrams Technical Note for the vehicle to locate the fuses and
relays concerned.
Connect the diagnostic tool and turn on the ignition.
With the preheating unit connected:
– connect the negative terminal of the voltmeter to track 8 of the preheating unit,
– connect the positive terminal of the voltmeter to the + 12 V battery,
– run command AC001 Preheating unit.
if the voltmeter does not indicate the battery voltage while the command is running (ten one-second ON/OFF
cycles), contact the Techline:
1. Check the condition of theF01 (70A) fuse which supplies the preheating unit. Replace it if necessary.
2. Check the continuity and the absence of interference resistance on the following connections:
Injection computer connector C, track E2 Track 8 of the preheating unit connector
Injection computer connector C, track A4 Track 9 of the pre-postheating unit connector
Repair if necessary.
3. Check the connections on the preheating unit, heater plugs and injection computer.
Repair if necessary.
4 Measure the resistance of the heater plugs. If the resistance is greater than 2Ω replace the faulty plug(s).
5. Check the continuity and the absence of interference resistance between:
– preheating unit track 1Heater plug for cylinder 3
– preheating unit track 2Heater plug for cylinder 4
– preheating unit track 6Heater plug for cylinder 1
– preheating unit track 7Heater plug for cylinder 2
6. Then check for +12V on track 3 of the preheating relay connector.
If the fault is still present, replace the preheating unit.
AFTER REPAIRRestart the conformity check from the beginning.
EDC16_V44_AC001/EDC16_V48_AC001/EDC16_V4C_AC001
Page 195 of 236
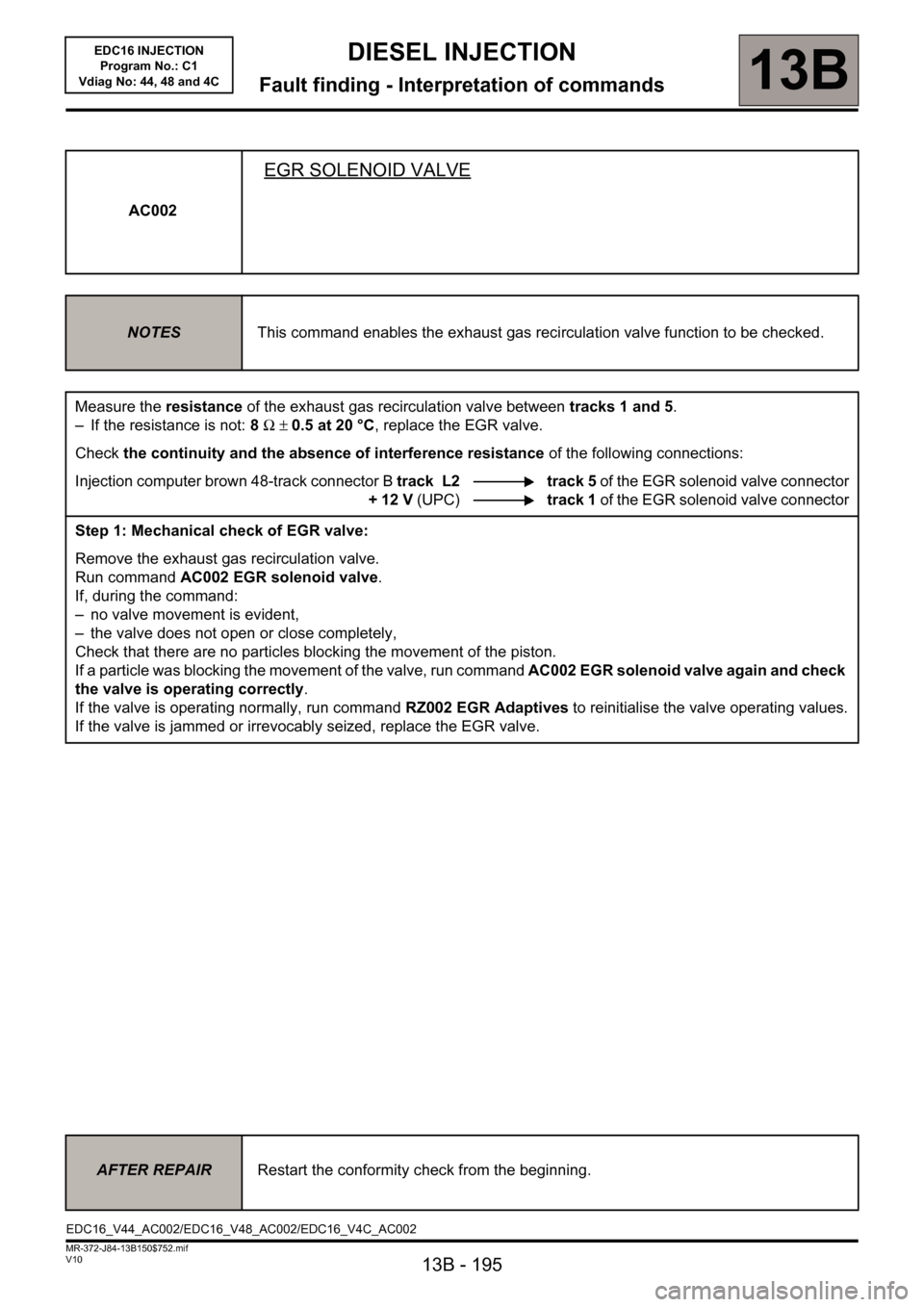
13B - 195
DIESEL INJECTION
Fault finding - Interpretation of commands13B
V10 MR-372-J84-13B150$752.mif
EDC16 INJECTION
Program No.: C1
Vdiag No: 44, 48 and 4C
AC002
EGR SOLENOID VALVE
NOTESThis command enables the exhaust gas recirculation valve function to be checked.
Measure the resistance of the exhaust gas recirculation valve between tracks 1 and 5.
– If the resistance is not: 8 Ω ± 0.5 at 20 °C, replace the EGR valve.
Check the continuity and the absence of interference resistance of the following connections:
Injection computer brown 48-track connector B track L2 track 5 of the EGR solenoid valve connector
+ 12 V (UPC)track 1 of the EGR solenoid valve connector
Step 1: Mechanical check of EGR valve:
Remove the exhaust gas recirculation valve.
Run command AC002 EGR solenoid valve.
If, during the command:
– no valve movement is evident,
– the valve does not open or close completely,
Check that there are no particles blocking the movement of the piston.
If a particle was blocking the movement of the valve, run command AC002 EGR solenoid valve again and check
the valve is operating correctly.
If the valve is operating normally, run command RZ002 EGR Adaptives to reinitialise the valve operating values.
If the valve is jammed or irrevocably seized, replace the EGR valve.
AFTER REPAIRRestart the conformity check from the beginning.
EDC16_V44_AC002/EDC16_V48_AC002/EDC16_V4C_AC002
Page 197 of 236
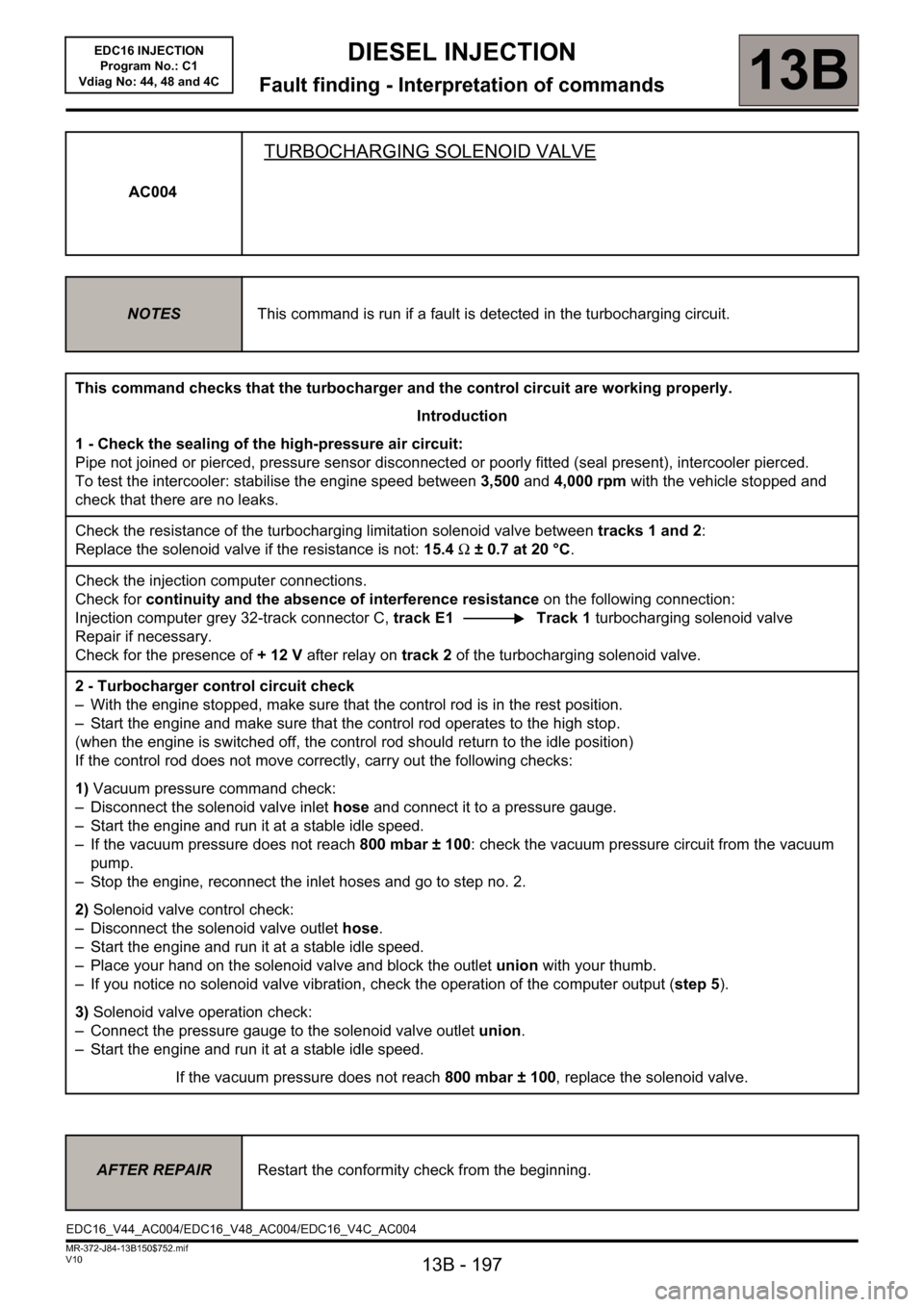
13B - 197
DIESEL INJECTION
Fault finding - Interpretation of commands13B
V10 MR-372-J84-13B150$752.mif
EDC16 INJECTION
Program No.: C1
Vdiag No: 44, 48 and 4C
AC004
TURBOCHARGING SOLENOID VALVE
NOTESThis command is run if a fault is detected in the turbocharging circuit.
This command checks that the turbocharger and the control circuit are working properly.
Introduction
1 - Check the sealing of the high-pressure air circuit:
Pipe not joined or pierced, pressure sensor disconnected or poorly fitted (seal present), intercooler pierced.
To test the intercooler: stabilise the engine speed between 3,500 and 4,000 rpm with the vehicle stopped and
check that there are no leaks.
Check the resistance of the turbocharging limitation solenoid valve between tracks 1 and 2:
Replace the solenoid valve if the resistance is not: 15.4 Ω ± 0.7 at 20 °C.
Check the injection computer connections.
Check for continuity and the absence of interference resistance on the following connection:
Injection computer grey 32-track connector C, track E1 Track 1 turbocharging solenoid valve
Repair if necessary.
Check for the presence of +12V after relay on track 2 of the turbocharging solenoid valve.
2 - Turbocharger control circuit check
– With the engine stopped, make sure that the control rod is in the rest position.
– Start the engine and make sure that the control rod operates to the high stop.
(when the engine is switched off, the control rod should return to the idle position)
If the control rod does not move correctly, carry out the following checks:
1) Vacuum pressure command check:
– Disconnect the solenoid valve inlet hose and connect it to a pressure gauge.
– Start the engine and run it at a stable idle speed.
– If the vacuum pressure does not reach 800 mbar ± 100: check the vacuum pressure circuit from the vacuum
pump.
– Stop the engine, reconnect the inlet hoses and go to step no. 2.
2) Solenoid valve control check:
– Disconnect the solenoid valve outlet hose.
– Start the engine and run it at a stable idle speed.
– Place your hand on the solenoid valve and block the outlet union with your thumb.
– If you notice no solenoid valve vibration, check the operation of the computer output (step 5).
3) Solenoid valve operation check:
– Connect the pressure gauge to the solenoid valve outlet union.
– Start the engine and run it at a stable idle speed.
If the vacuum pressure does not reach 800 mbar ± 100, replace the solenoid valve.
AFTER REPAIRRestart the conformity check from the beginning.
EDC16_V44_AC004/EDC16_V48_AC004/EDC16_V4C_AC004
Page 199 of 236
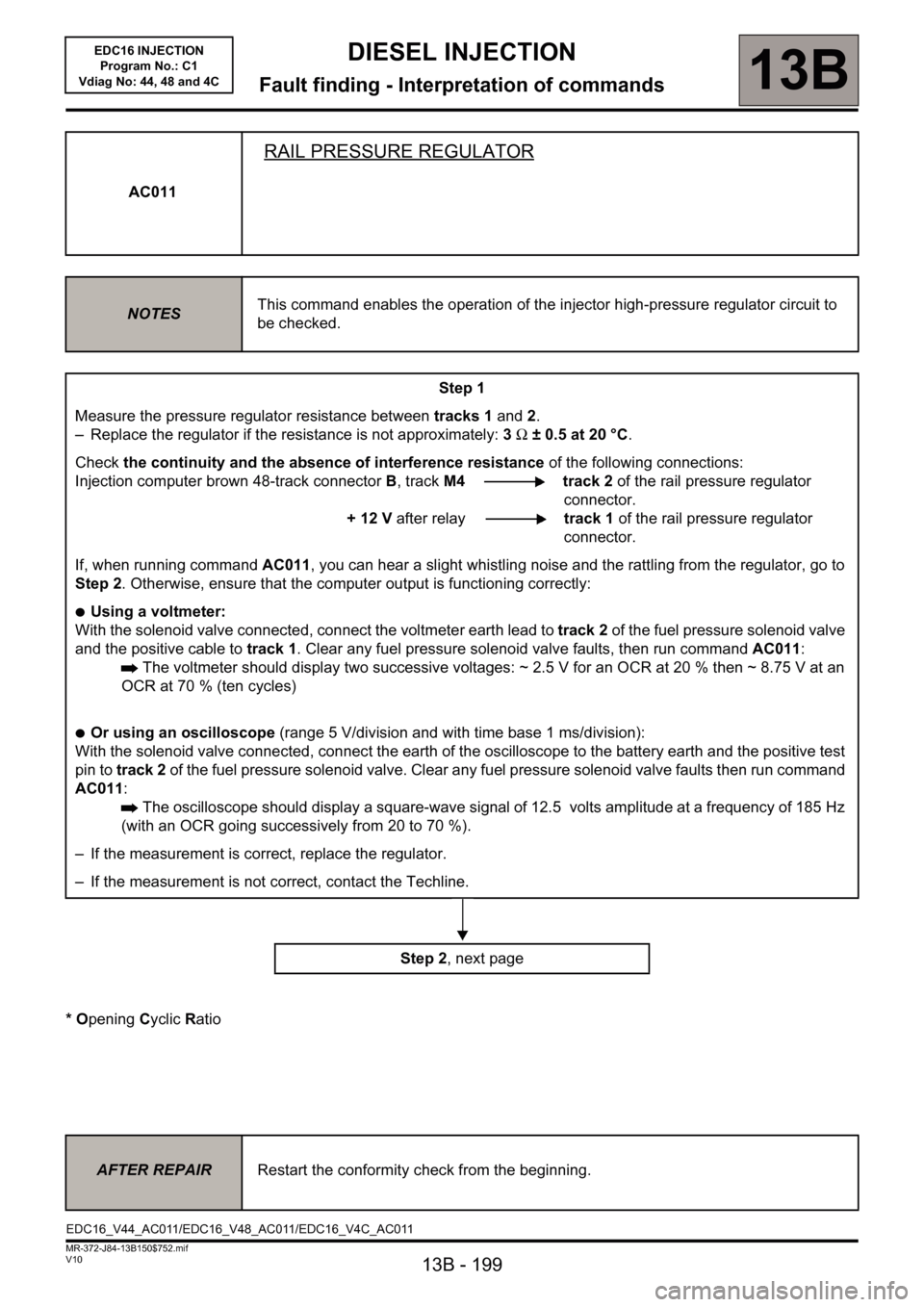
13B - 199
DIESEL INJECTION
Fault finding - Interpretation of commands13B
V10 MR-372-J84-13B150$752.mif
EDC16 INJECTION
Program No.: C1
Vdiag No: 44, 48 and 4C
* Opening Cyclic Ratio AC011
RAIL PRESSURE REGULATOR
NOTESThis command enables the operation of the injector high-pressure regulator circuit to
be checked.
Step 1
Measure the pressure regulator resistance between tracks 1 and 2.
– Replace the regulator if the resistance is not approximately: 3Ω ± 0.5 at 20 °C.
Check the continuity and the absence of interference resistance of the following connections:
Injection computer brown 48-track connectorB, trackM4 track 2 of the rail pressure regulator
connector.
+ 12 V after relaytrack 1 of the rail pressure regulator
connector.
If, when running command AC011, you can hear a slight whistling noise and the rattling from the regulator, go to
Step 2. Otherwise, ensure that the computer output is functioning correctly:
●Using a voltmeter:
With the solenoid valve connected, connect the voltmeter earth lead to track 2 of the fuel pressure solenoid valve
and the positive cable to track 1. Clear any fuel pressure solenoid valve faults, then run command AC011:
The voltmeter should display two successive voltages: ~ 2.5 V for an OCR at 20 % then ~ 8.75 V at an
OCR at 70 % (ten cycles)
●Or using an oscilloscope (range 5 V/division and with time base 1 ms/division):
With the solenoid valve connected, connect the earth of the oscilloscope to the battery earth and the positive test
pin to track 2 of the fuel pressure solenoid valve. Clear any fuel pressure solenoid valve faults then run command
AC011:
The oscilloscope should display a square-wave signal of 12.5 volts amplitude at a frequency of 185 Hz
(with an OCR going successively from 20 to 70 %).
– If the measurement is correct, replace the regulator.
– If the measurement is not correct, contact the Techline.
Step 2, next page
AFTER REPAIRRestart the conformity check from the beginning.
EDC16_V44_AC011/EDC16_V48_AC011/EDC16_V4C_AC011
Page 201 of 236
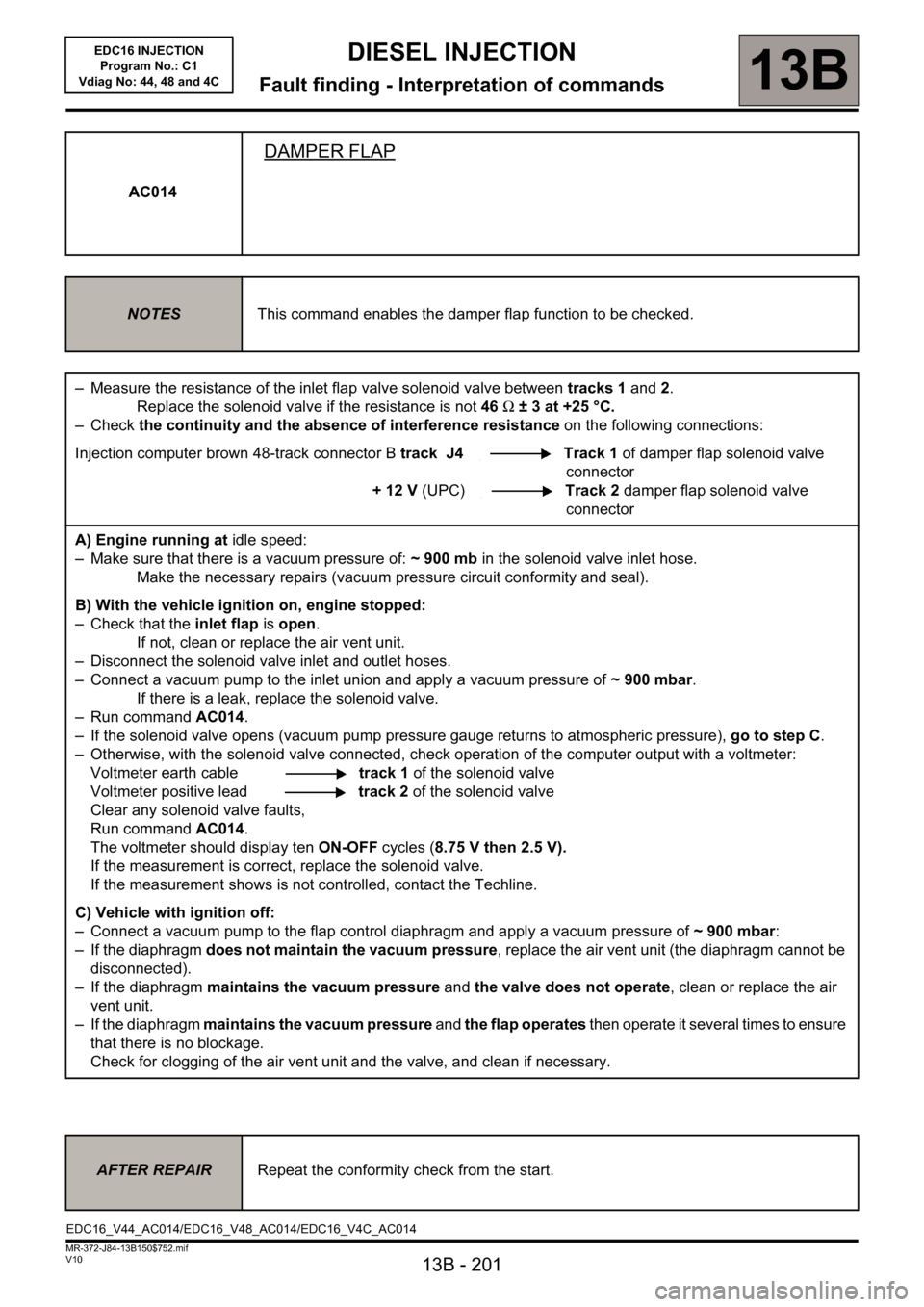
13B - 201
DIESEL INJECTION
Fault finding - Interpretation of commands13B
V10 MR-372-J84-13B150$752.mif
EDC16 INJECTION
Program No.: C1
Vdiag No: 44, 48 and 4C
AC014
DAMPER FLAP
NOTESThis command enables the damper flap function to be checked.
– Measure the resistance of the inlet flap valve solenoid valve between tracks 1 and 2.
Replace the solenoid valve if the resistance is not 46 Ω ± 3 at +25 °C.
–Check the continuity and the absence of interference resistance on the following connections:
Injection computer brown 48-track connector B track J4 Track 1 of damper flap solenoid valve
connector
+ 12 V (UPC)Track 2 damper flap solenoid valve
connector
A) Engine running at idle speed:
– Make sure that there is a vacuum pressure of: ~ 900 mb in the solenoid valve inlet hose.
Make the necessary repairs (vacuum pressure circuit conformity and seal).
B) With the vehicle ignition on, engine stopped:
– Check that the inlet flap is open.
If not, clean or replace the air vent unit.
– Disconnect the solenoid valve inlet and outlet hoses.
– Connect a vacuum pump to the inlet union and apply a vacuum pressure of ~ 900 mbar.
If there is a leak, replace the solenoid valve.
– Run command AC014.
– If the solenoid valve opens (vacuum pump pressure gauge returns to atmospheric pressure), go to step C.
– Otherwise, with the solenoid valve connected, check operation of the computer output with a voltmeter:
Voltmeter earth cabletrack 1 of the solenoid valve
Voltmeter positive leadtrack 2 of the solenoid valve
Clear any solenoid valve faults,
Run command AC014.
The voltmeter should display ten ON-OFF cycles (8.75 V then 2.5 V).
If the measurement is correct, replace the solenoid valve.
If the measurement shows is not controlled, contact the Techline.
C) Vehicle with ignition off:
– Connect a vacuum pump to the flap control diaphragm and apply a vacuum pressure of ~ 900 mbar:
– If the diaphragm does not maintain the vacuum pressure, replace the air vent unit (the diaphragm cannot be
disconnected).
– If the diaphragm maintains the vacuum pressure and the valve does not operate, clean or replace the air
vent unit.
– If the diaphragm maintains the vacuum pressure and the flap operates then operate it several times to ensure
that there is no blockage.
Check for clogging of the air vent unit and the valve, and clean if necessary.
AFTER REPAIRRepeat the conformity check from the start.
EDC16_V44_AC014/EDC16_V48_AC014/EDC16_V4C_AC014
Page 203 of 236
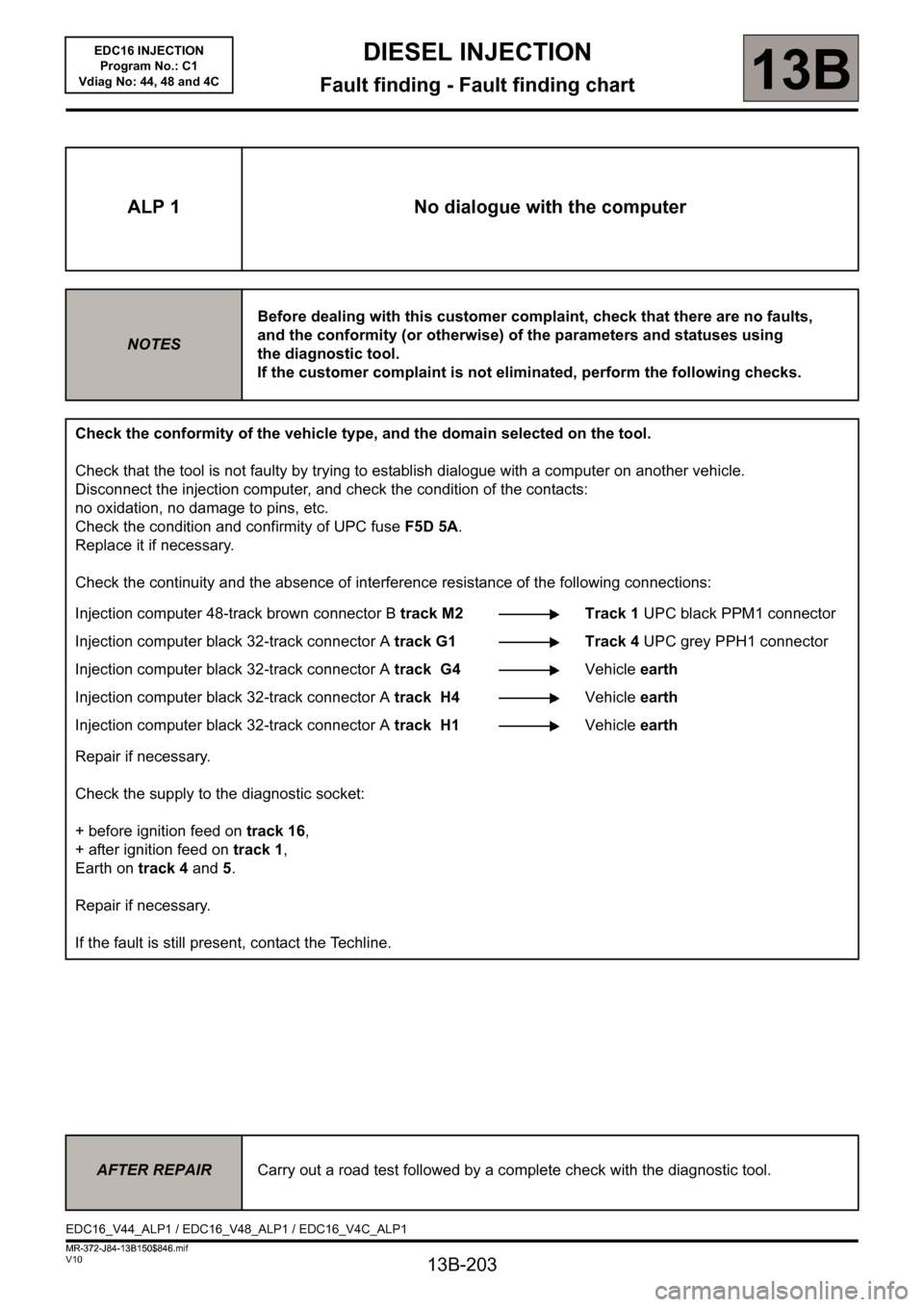
13B-203
MR-372-J84-13B150$846.mif
V10
13B
EDC16 INJECTION
Program No.: C1
Vdiag No: 44, 48 and 4CDIESEL INJECTION
Fault finding - Fault finding chart
ALP 1 No dialogue with the computer
NOTESBefore dealing with this customer complaint, check that there are no faults,
and the conformity (or otherwise) of the parameters and statuses using
the diagnostic tool.
If the customer complaint is not eliminated, perform the following checks.
Check the conformity of the vehicle type, and the domain selected on the tool.
Check that the tool is not faulty by trying to establish dialogue with a computer on another vehicle.
Disconnect the injection computer, and check the condition of the contacts:
no oxidation, no damage to pins, etc.
Check the condition and confirmity of UPC fuse F5D 5A.
Replace it if necessary.
Check the continuity and the absence of interference resistance of the following connections:
Injection computer 48-track brown connector B track M2
Injection computer black 32-track connector A track G1
Injection computer black 32-track connector A track G4
Injection computer black 32-track connector A track H4
Injection computer black 32-track connector A track H1Track 1 UPC black PPM1 connector
Track 4 UPC grey PPH1 connector
Vehicle earth
Vehicle earth
Vehicle earth
Repair if necessary.
Check the supply to the diagnostic socket:
+ before ignition feed on track 16,
+ after ignition feed on track 1,
Earth on track 4 and 5.
Repair if necessary.
If the fault is still present, contact the Techline.
AFTER REPAIRCarry out a road test followed by a complete check with the diagnostic tool.
EDC16_V44_ALP1 / EDC16_V48_ALP1 / EDC16_V4C_ALP1
MR-372-J84-13B150$846.mif
Page 204 of 236
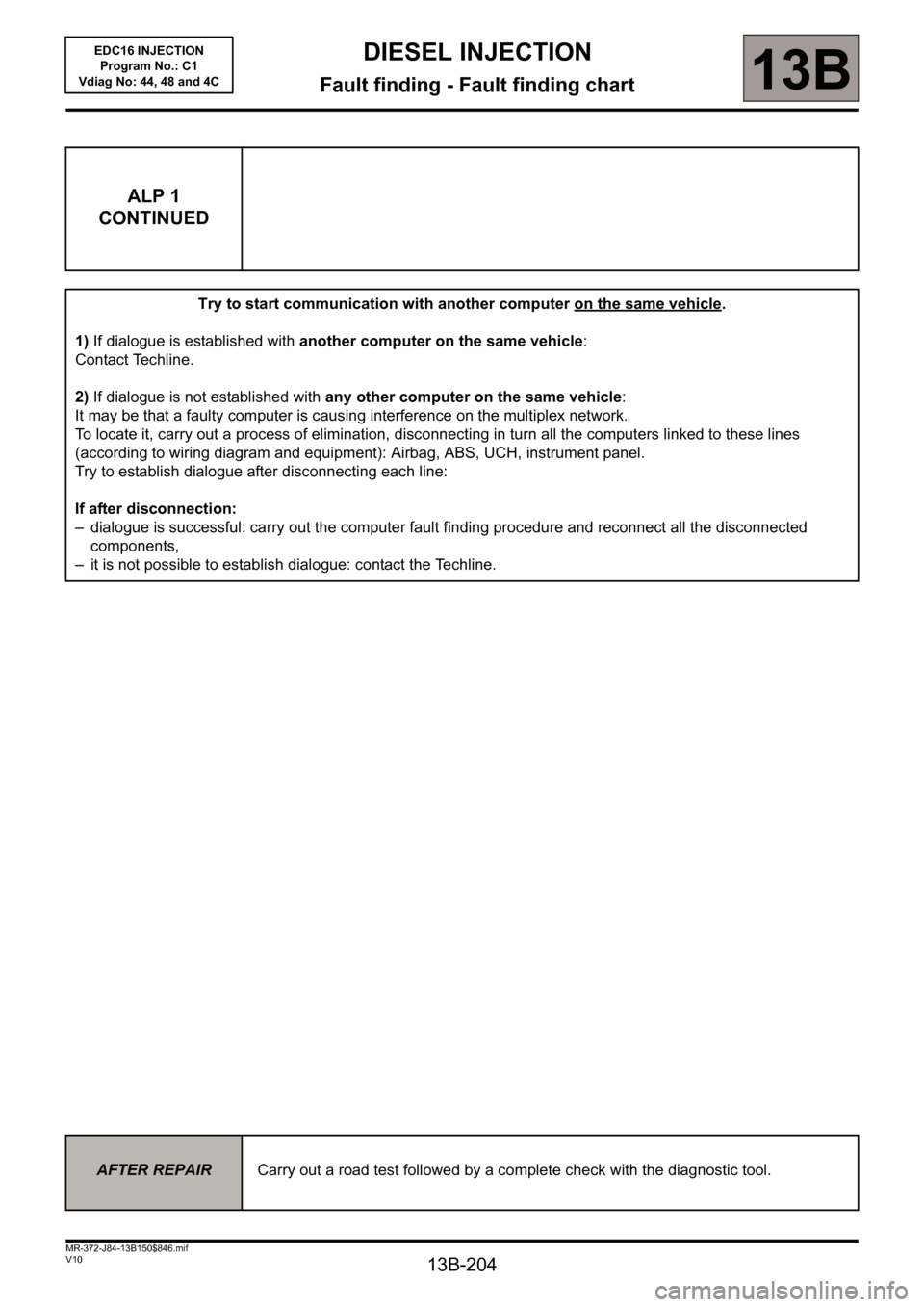
13B-204
MR-372-J84-13B150$846.mif
V10
DIESEL INJECTION
Fault finding - Fault finding chart13B
ALP 1
CONTINUED
Try to start communication with another computer on the same vehicle.
1)If dialogue is established with another computer on the same vehicle:
Contact Techline.
2)If dialogue is not established with any other computer on the same vehicle:
It may be that a faulty computer is causing interference on the multiplex network.
To locate it, carry out a process of elimination, disconnecting in turn all the computers linked to these lines
(according to wiring diagram and equipment): Airbag, ABS, UCH, instrument panel.
Try to establish dialogue after disconnecting each line:
If after disconnection:
– dialogue is successful: carry out the computer fault finding procedure and reconnect all the disconnected
components,
– it is not possible to establish dialogue: contact the Techline.
AFTER REPAIRCarry out a road test followed by a complete check with the diagnostic tool.
EDC16 INJECTION
Program No.: C1
Vdiag No: 44, 48 and 4C
Page 226 of 236
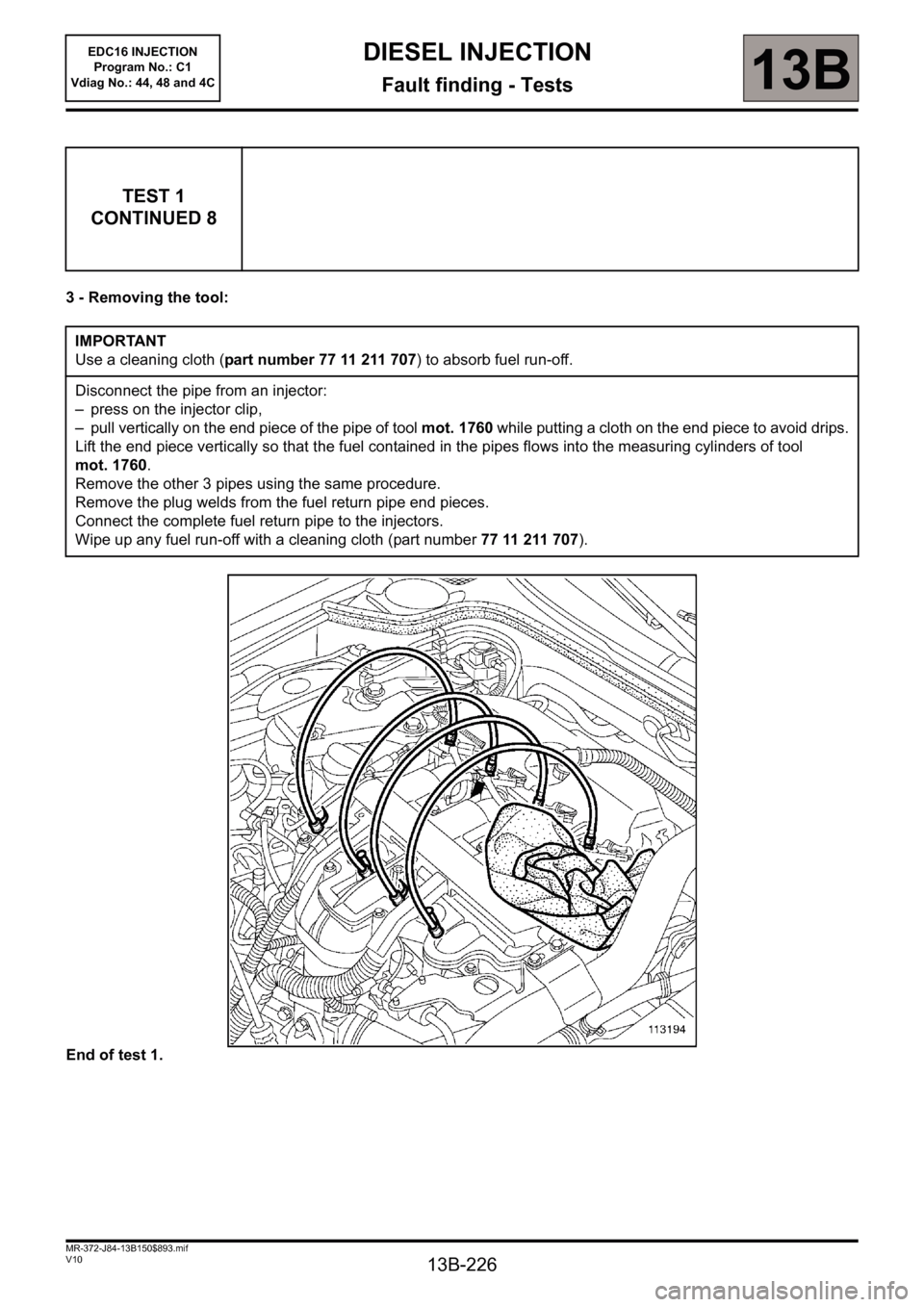
13B-226
MR-372-J84-13B150$893.mif
V10
DIESEL INJECTION
Fault finding - Tests
EDC16 INJECTION
Program No.: C1
Vdiag No.: 44, 48 and 4C
13B
3 - Removing the tool:
End of test 1.
TEST 1
CONTINUED 8
IMPORTANT
Use a cleaning cloth (part number 77 11 211 707) to absorb fuel run-off.
Disconnect the pipe from an injector:
– press on the injector clip,
– pull vertically on the end piece of the pipe of tool mot. 1760 while putting a cloth on the end piece to avoid drips.
Lift the end piece vertically so that the fuel contained in the pipes flows into the measuring cylinders of tool
mot. 1760.
Remove the other 3 pipes using the same procedure.
Remove the plug welds from the fuel return pipe end pieces.
Connect the complete fuel return pipe to the injectors.
Wipe up any fuel run-off with a cleaning cloth (part number 77 11 211 707).
Page 235 of 236
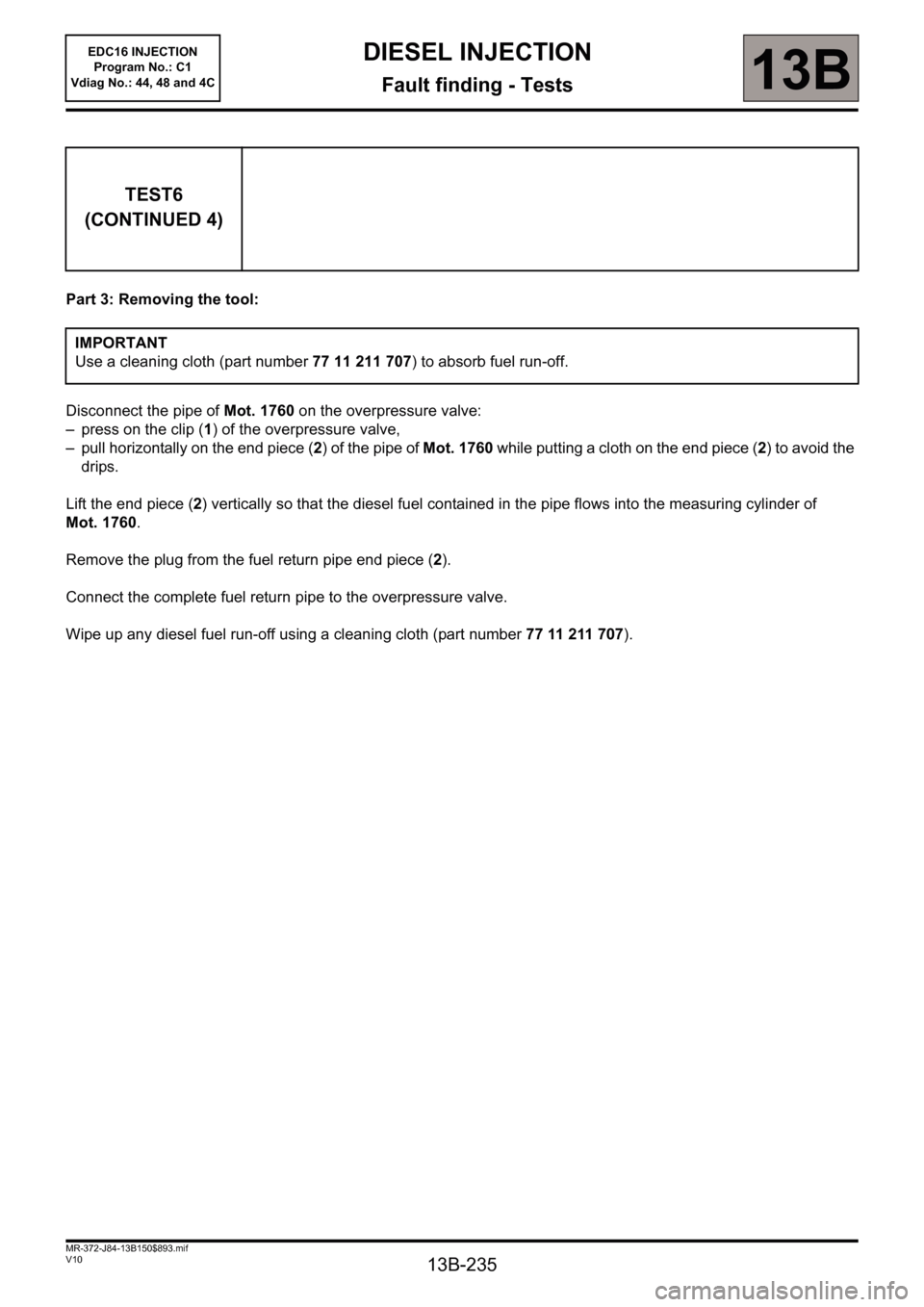
13B-235
MR-372-J84-13B150$893.mif
V10
13B
EDC16 INJECTION
Program No.: C1
Vdiag No.: 44, 48 and 4CDIESEL INJECTION
Fault finding - Tests
Part 3: Removing the tool:
Disconnect the pipe of Mot. 1760 on the overpressure valve:
– press on the clip (1) of the overpressure valve,
– pull horizontally on the end piece (2) of the pipe of Mot. 1760 while putting a cloth on the end piece (2) to avoid the
drips.
Lift the end piece (2) vertically so that the diesel fuel contained in the pipe flows into the measuring cylinder of
Mot. 1760.
Remove the plug from the fuel return pipe end piece (2).
Connect the complete fuel return pipe to the overpressure valve.
Wipe up any diesel fuel run-off using a cleaning cloth (part number 77 11 211 707).
TEST6
(CONTINUED 4)
IMPORTANT
Use a cleaning cloth (part number 77 11 211 707) to absorb fuel run-off.