sensor RENAULT SCENIC 2011 J95 / 3.G Engine And Peripherals Siemens Injection Workshop Manual
[x] Cancel search | Manufacturer: RENAULT, Model Year: 2011, Model line: SCENIC, Model: RENAULT SCENIC 2011 J95 / 3.GPages: 329, PDF Size: 1.71 MB
Page 290 of 329
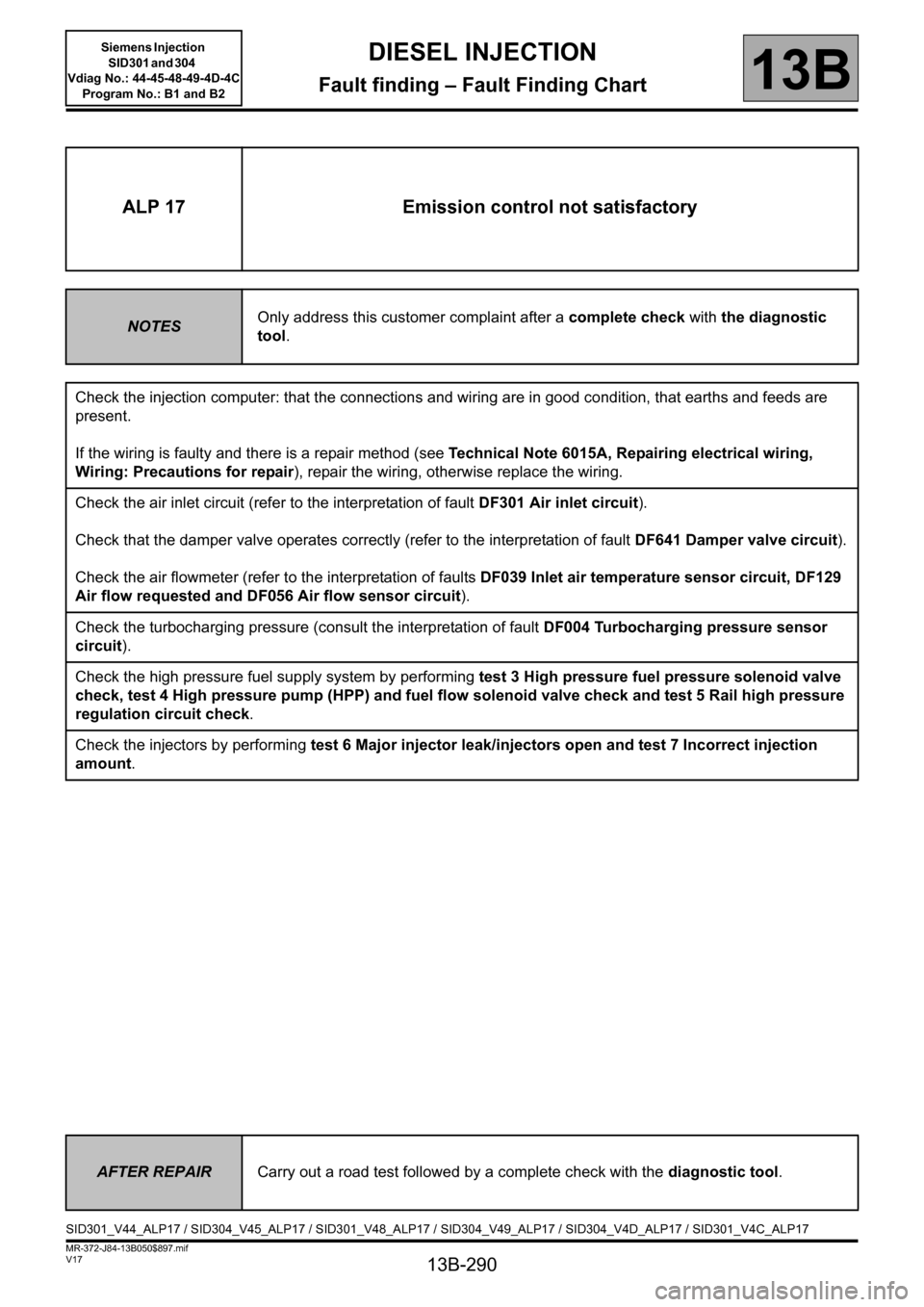
13B-290
MR-372-J84-13B050$897.mif
V17
DIESEL INJECTION
Fault finding – Fault Finding Chart
Siemens Injection
SID301 and 304
Vdiag No.: 44-45-48-49-4D-4C
Program No.: B1 and B2
13B
ALP 17 Emission control not satisfactory
NOTESOnly address this customer complaint after a complete check with the diagnostic
tool.
Check the injection computer: that the connections and wiring are in good condition, that earths and feeds are
present.
If the wiring is faulty and there is a repair method (see Technical Note 6015A, Repairing electrical wiring,
Wiring: Precautions for repair), repair the wiring, otherwise replace the wiring.
Check the air inlet circuit (refer to the interpretation of fault DF301 Air inlet circuit).
Check that the damper valve operates correctly (refer to the interpretation of fault DF641 Damper valve circuit).
Check the air flowmeter (refer to the interpretation of faults DF039 Inlet air temperature sensor circuit, DF129
Air flow requested and DF056 Air flow sensor circuit).
Check the turbocharging pressure (consult the interpretation of fault DF004 Turbocharging pressure sensor
circuit).
Check the high pressure fuel supply system by performing test 3 High pressure fuel pressure solenoid valve
check, test 4 High pressure pump (HPP) and fuel flow solenoid valve check and test 5 Rail high pressure
regulation circuit check.
Check the injectors by performing test 6 Major injector leak/injectors open and test 7 Incorrect injection
amount.
AFTER REPAIRCarry out a road test followed by a complete check with the diagnostic tool.
SID301_V44_ALP17 / SID304_V45_ALP17 / SID301_V48_ALP17 / SID304_V49_ALP17 / SID304_V4D_ALP17 / SID301_V4C_ALP17
Page 296 of 329
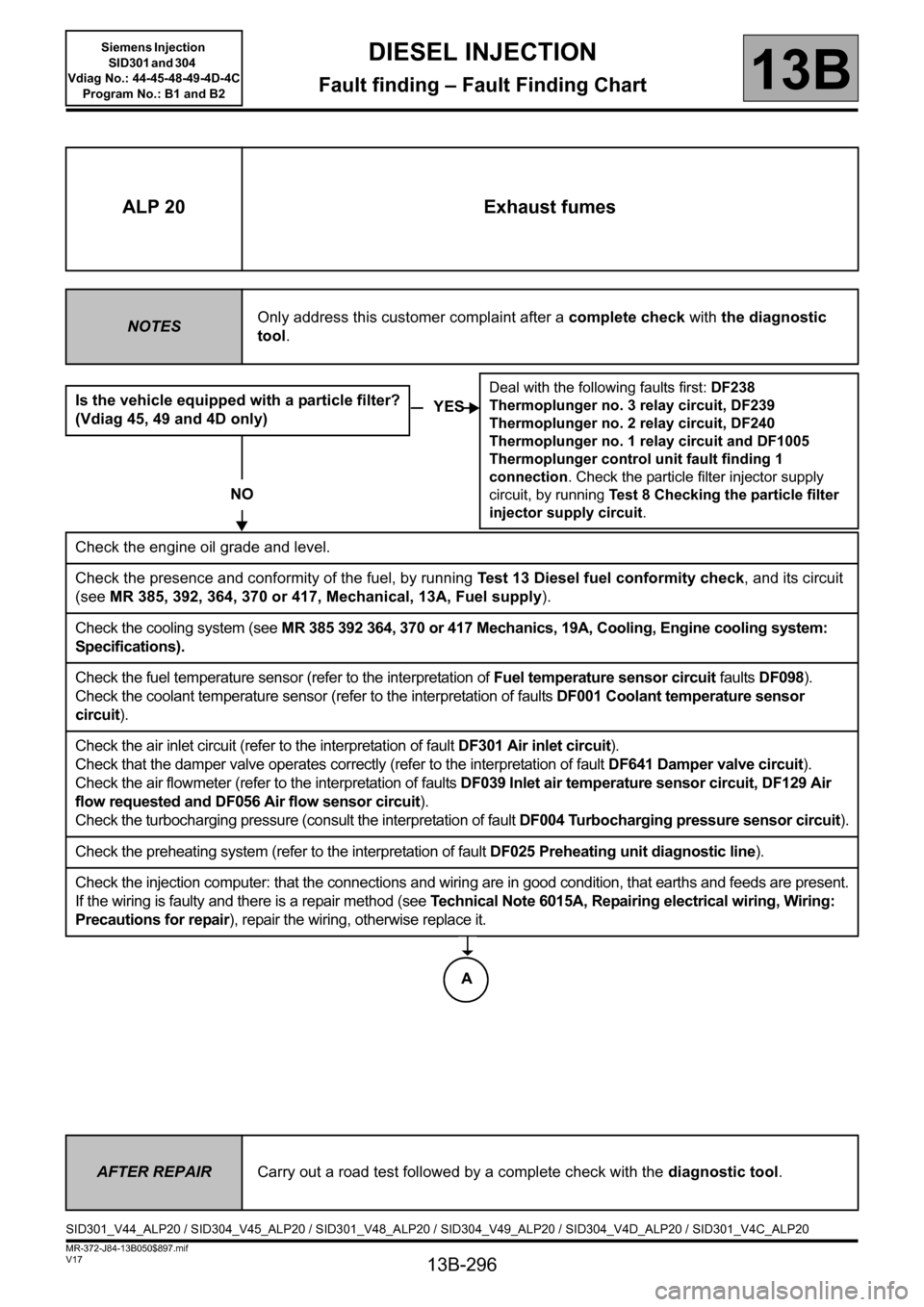
13B-296
MR-372-J84-13B050$897.mif
V17
Siemens Injection
SID301 and 304
Vdiag No.: 44-45-48-49-4D-4C
Program No.: B1 and B2DIESEL INJECTION
Fault finding – Fault Finding Chart13B
ALP 20 Exhaust fumes
NOTESOnly address this customer complaint after a complete check with the diagnostic
tool.
Is the vehicle equipped with a particle filter?
(Vdiag 45, 49 and 4D only)
NO
Check the engine oil grade and level.
Check the presence and conformity of the fuel, by running Test 13 Diesel fuel conformity check, and its circuit
(see MR 385, 392, 364, 370 or 417, Mechanical, 13A, Fuel supply).
Check the cooling system (see MR 385 392 364, 370 or 417 Mechanics, 19A, Cooling, Engine cooling system:
Specifications).
Check the fuel temperature sensor (refer to the interpretation of Fuel temperature sensor circuit faults DF098).
Check the coolant temperature sensor (refer to the interpretation of faults DF001 Coolant temperature sensor
circuit).
Check the air inlet circuit (refer to the interpretation of fault DF301 Air inlet circuit).
Check that the damper valve operates correctly (refer to the interpretation of fault DF641 Damper valve circuit).
Check the air flowmeter (refer to the interpretation of faults DF039 Inlet air temperature sensor circuit, DF129 Air
flow requested and DF056 Air flow sensor circuit).
Check the turbocharging pressure (consult the interpretation of fault DF004 Turbocharging pressure sensor circuit).
Check the preheating system (refer to the interpretation of fault DF025 Preheating unit diagnostic line).
Check the injection computer: that the connections and wiring are in good condition, that earths and feeds are present.
If the wiring is faulty and there is a repair method (see Technical Note 6015A, Repairing electrical wiring, Wiring:
Precautions for repair), repair the wiring, otherwise replace it.
YES
Deal with the following faults first: DF238
Thermoplunger no. 3 relay circuit, DF239
Thermoplunger no. 2 relay circuit, DF240
Thermoplunger no. 1 relay circuit and DF1005
Thermoplunger control unit fault finding 1
connection. Check the particle filter injector supply
circuit, by running Test 8 Checking the particle filter
injector supply circuit.
AFTER REPAIRCarry out a road test followed by a complete check with the diagnostic tool.
SID301_V44_ALP20 / SID304_V45_ALP20 / SID301_V48_ALP20 / SID304_V49_ALP20 / SID304_V4D_ALP20 / SID301_V4C_ALP20
A
Page 298 of 329
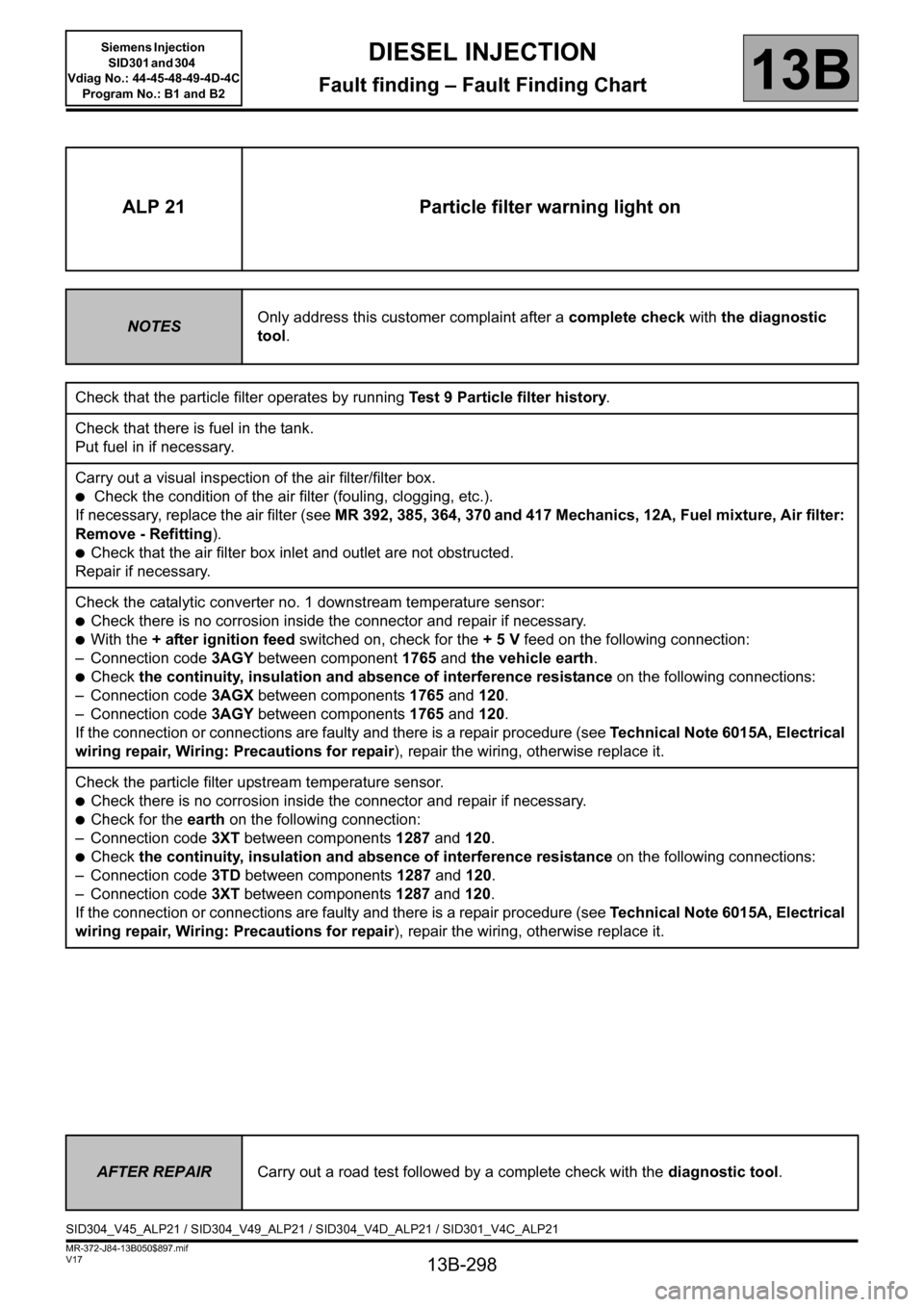
13B-298
MR-372-J84-13B050$897.mif
V17
DIESEL INJECTION
Fault finding – Fault Finding Chart
Siemens Injection
SID301 and 304
Vdiag No.: 44-45-48-49-4D-4C
Program No.: B1 and B2
13B
ALP 21 Particle filter warning light on
NOTESOnly address this customer complaint after a complete check with the diagnostic
tool.
Check that the particle filter operates by running Test 9 Particle filter history.
Check that there is fuel in the tank.
Put fuel in if necessary.
Carry out a visual inspection of the air filter/filter box.
● Check the condition of the air filter (fouling, clogging, etc.).
If necessary, replace the air filter (see MR 392, 385, 364, 370 and 417 Mechanics, 12A, Fuel mixture, Air filter:
Remove - Refitting).
●Check that the air filter box inlet and outlet are not obstructed.
Repair if necessary.
Check the catalytic converter no. 1 downstream temperature sensor:
●Check there is no corrosion inside the connector and repair if necessary.
●With the + after ignition feed switched on, check for the + 5 V feed on the following connection:
– Connection code 3AGY between component 1765 and the vehicle earth.
●Check the continuity, insulation and absence of interference resistance on the following connections:
– Connection code 3AGX between components 1765 and 120.
– Connection code 3AGY between components 1765 and 120.
If the connection or connections are faulty and there is a repair procedure (see Technical Note 6015A, Electrical
wiring repair, Wiring: Precautions for repair), repair the wiring, otherwise replace it.
Check the particle filter upstream temperature sensor.
●Check there is no corrosion inside the connector and repair if necessary.
●Check for the earth on the following connection:
– Connection code 3XT between components 1287 and 120.
●Check the continuity, insulation and absence of interference resistance on the following connections:
– Connection code 3TD between components 1287 and 120.
– Connection code 3XT between components 1287 and 120.
If the connection or connections are faulty and there is a repair procedure (see Technical Note 6015A, Electrical
wiring repair, Wiring: Precautions for repair), repair the wiring, otherwise replace it.
AFTER REPAIRCarry out a road test followed by a complete check with the diagnostic tool.
SID304_V45_ALP21 / SID304_V49_ALP21 / SID304_V4D_ALP21 / SID301_V4C_ALP21
Page 299 of 329
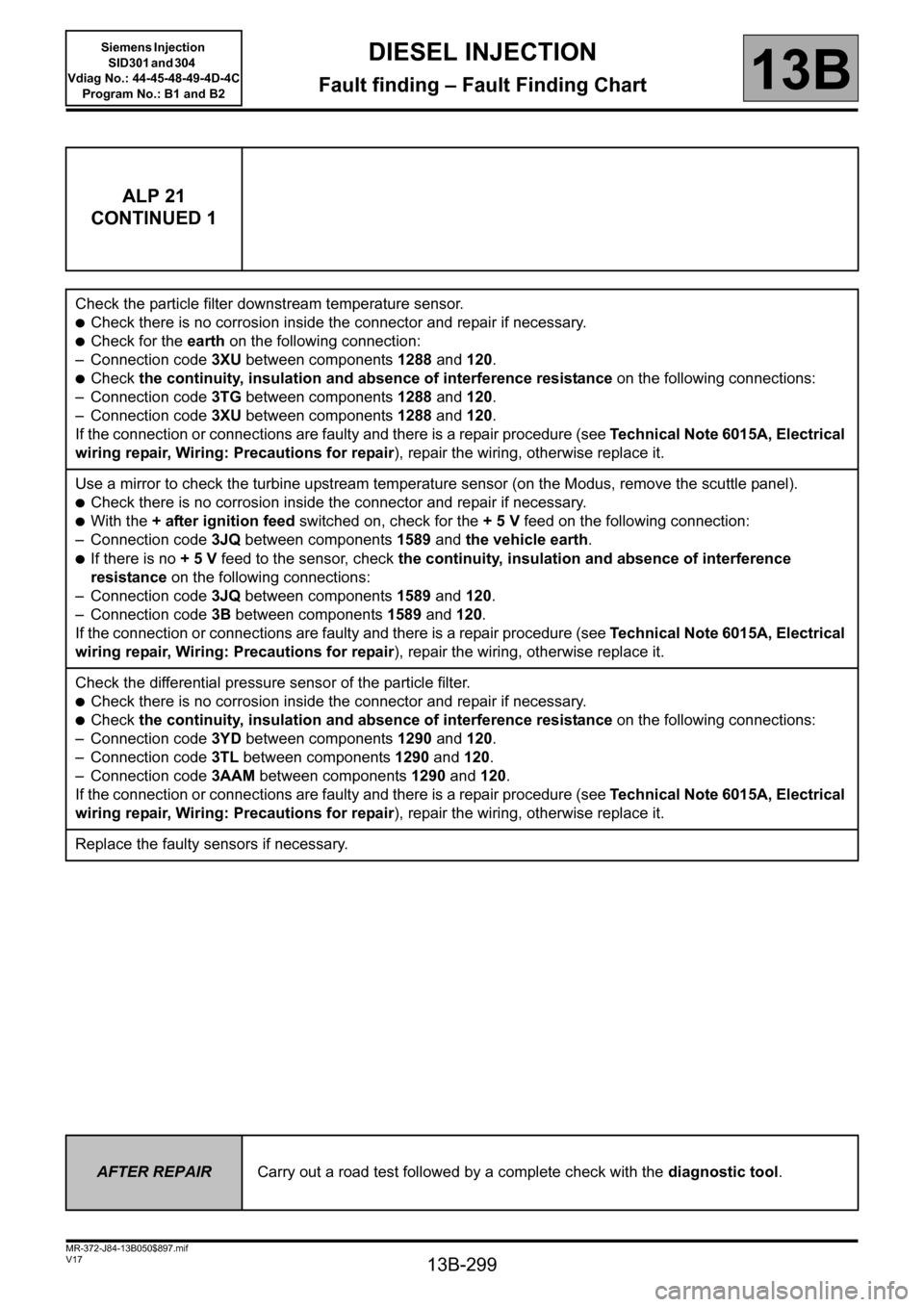
13B-299
MR-372-J84-13B050$897.mif
V17
DIESEL INJECTION
Fault finding – Fault Finding Chart
Siemens Injection
SID301 and 304
Vdiag No.: 44-45-48-49-4D-4C
Program No.: B1 and B2
13B
ALP 21
CONTINUED 1
Check the particle filter downstream temperature sensor.
●Check there is no corrosion inside the connector and repair if necessary.
●Check for the earth on the following connection:
– Connection code 3XU between components 1288 and 120.
●Check the continuity, insulation and absence of interference resistance on the following connections:
– Connection code 3TG between components 1288 and 120.
– Connection code 3XU between components 1288 and 120.
If the connection or connections are faulty and there is a repair procedure (see Technical Note 6015A, Electrical
wiring repair, Wiring: Precautions for repair), repair the wiring, otherwise replace it.
Use a mirror to check the turbine upstream temperature sensor (on the Modus, remove the scuttle panel).
●Check there is no corrosion inside the connector and repair if necessary.
●With the + after ignition feed switched on, check for the + 5 V feed on the following connection:
– Connection code 3JQ between components 1589 and the vehicle earth.
●If there is no + 5 V feed to the sensor, check the continuity, insulation and absence of interference
resistance on the following connections:
– Connection code 3JQ between components 1589 and 120.
– Connection code 3B between components 1589 and 120.
If the connection or connections are faulty and there is a repair procedure (see Technical Note 6015A, Electrical
wiring repair, Wiring: Precautions for repair), repair the wiring, otherwise replace it.
Check the differential pressure sensor of the particle filter.
●Check there is no corrosion inside the connector and repair if necessary.
●Check the continuity, insulation and absence of interference resistance on the following connections:
– Connection code 3YD between components 1290 and 120.
– Connection code 3TL between components 1290 and 120.
– Connection code 3AAM between components 1290 and 120.
If the connection or connections are faulty and there is a repair procedure (see Technical Note 6015A, Electrical
wiring repair, Wiring: Precautions for repair), repair the wiring, otherwise replace it.
Replace the faulty sensors if necessary.
AFTER REPAIRCarry out a road test followed by a complete check with the diagnostic tool.
Page 310 of 329
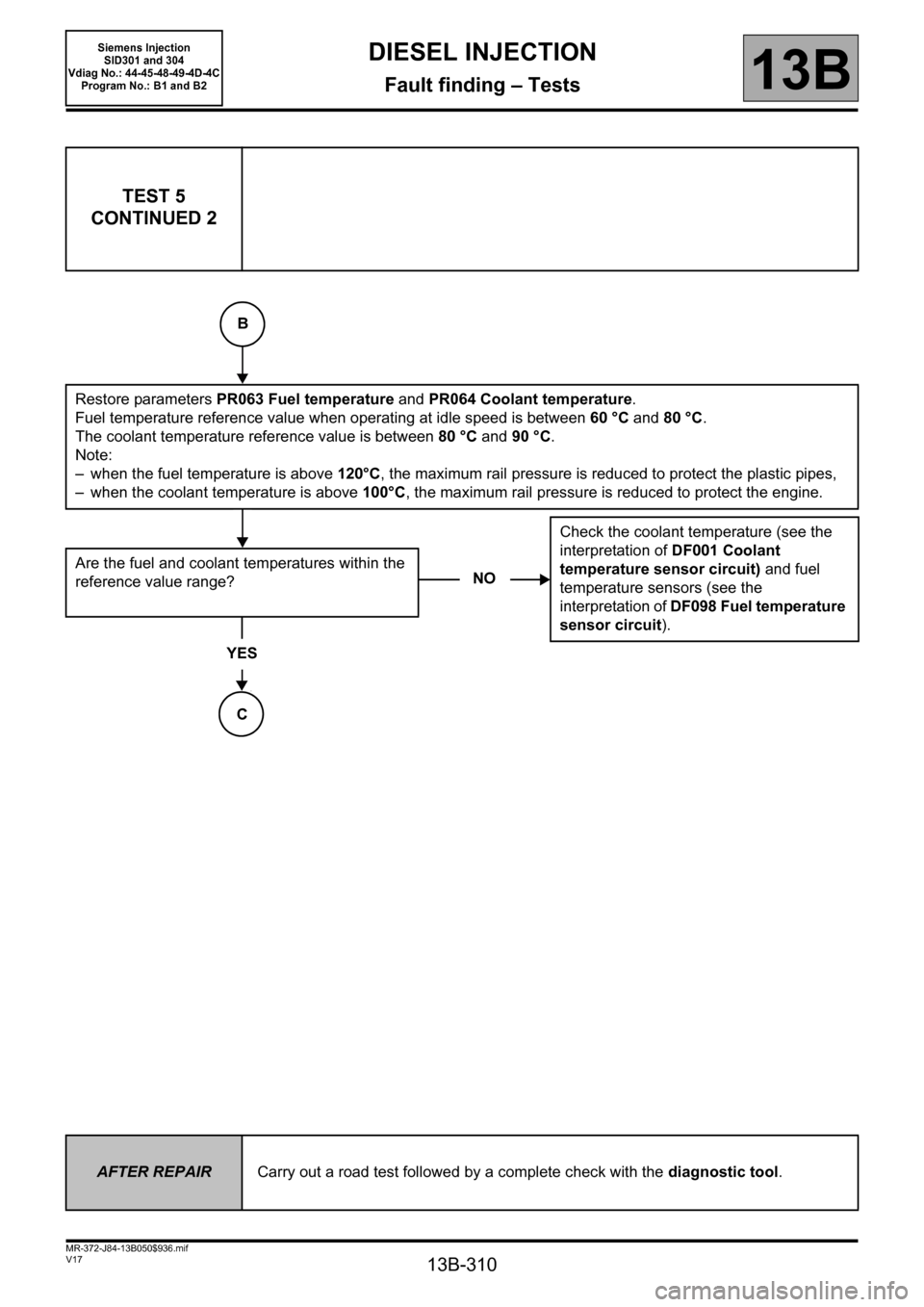
13B-310
MR-372-J84-13B050$936.mif
V17
DIESEL INJECTION
Fault finding – Tests13B
Siemens Injection
SID301 and 304
Vdiag No.: 44-45-48-49-4D-4C
Program No.: B1 and B2
TEST 5
CONTINUED 2
Restore parameters PR063 Fuel temperature and PR064 Coolant temperature.
Fuel temperature reference value when operating at idle speed is between 60 °C and 80 °C.
The coolant temperature reference value is between 80 °C and 90 °C.
Note:
– when the fuel temperature is above 120°C, the maximum rail pressure is reduced to protect the plastic pipes,
– when the coolant temperature is above 100°C, the maximum rail pressure is reduced to protect the engine.
Are the fuel and coolant temperatures within the
reference value range?
YES
NOCheck the coolant temperature (see the
interpretation of DF001 Coolant
temperature sensor circuit) and fuel
temperature sensors (see the
interpretation of DF098 Fuel temperature
sensor circuit).
AFTER REPAIRCarry out a road test followed by a complete check with the diagnostic tool.
B
C
Page 311 of 329
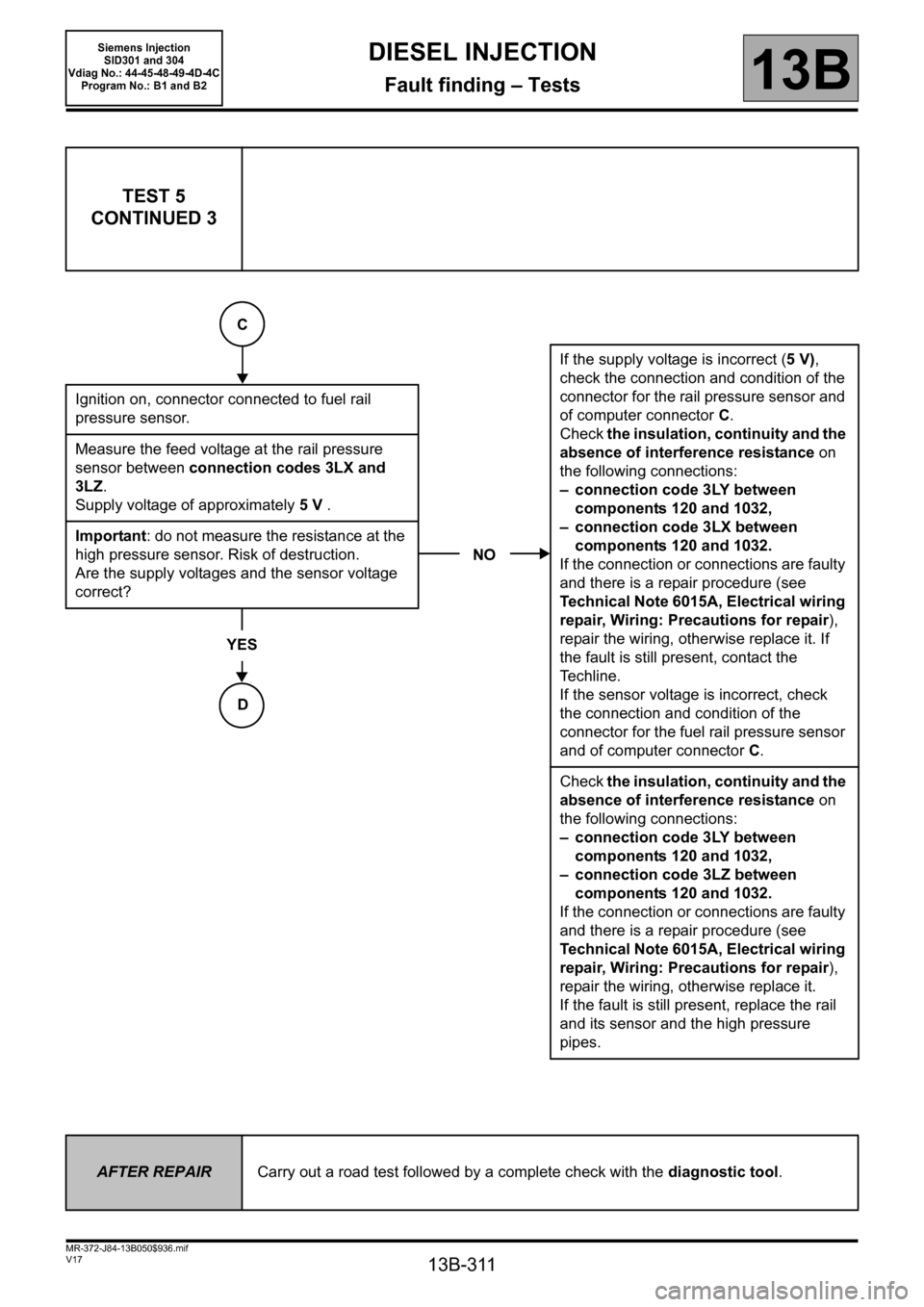
13B-311
MR-372-J84-13B050$936.mif
V17
DIESEL INJECTION
Fault finding – Tests13B
Siemens Injection
SID301 and 304
Vdiag No.: 44-45-48-49-4D-4C
Program No.: B1 and B2
TEST 5
CONTINUED 3
Ignition on, connector connected to fuel rail
pressure sensor.
Measure the feed voltage at the rail pressure
sensor between connection codes 3LX and
3LZ.
Supply voltage of approximately 5V .
Important: do not measure the resistance at the
high pressure sensor. Risk of destruction.
Are the supply voltages and the sensor voltage
correct?
YES
NOIf the supply voltage is incorrect (5 V),
check the connection and condition of the
connector for the rail pressure sensor and
of computer connector C.
Check the insulation, continuity and the
absence of interference resistance on
the following connections:
– connection code 3LY between
components 120 and 1032,
– connection code 3LX between
components 120 and 1032.
If the connection or connections are faulty
and there is a repair procedure (see
Technical Note 6015A, Electrical wiring
repair, Wiring: Precautions for repair),
repair the wiring, otherwise replace it. If
the fault is still present, contact the
Techline.
If the sensor voltage is incorrect, check
the connection and condition of the
connector for the fuel rail pressure sensor
and of computer connector C.
Check the insulation, continuity and the
absence of interference resistance on
the following connections:
– connection code 3LY between
components 120 and 1032,
– connection code 3LZ between
components 120 and 1032.
If the connection or connections are faulty
and there is a repair procedure (see
Technical Note 6015A, Electrical wiring
repair, Wiring: Precautions for repair),
repair the wiring, otherwise replace it.
If the fault is still present, replace the rail
and its sensor and the high pressure
pipes.
AFTER REPAIRCarry out a road test followed by a complete check with the diagnostic tool.
C
D
Page 312 of 329
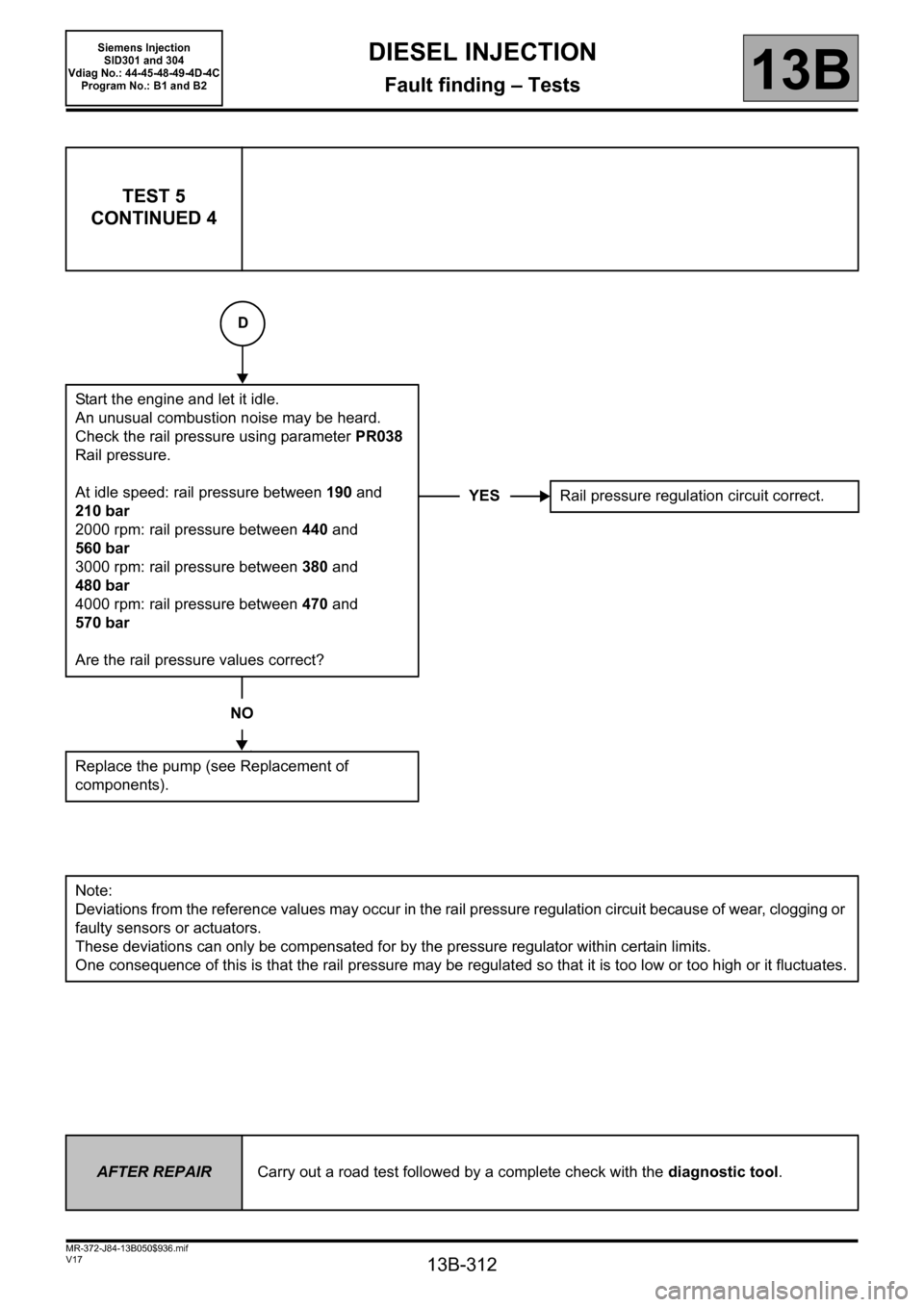
13B-312
MR-372-J84-13B050$936.mif
V17
DIESEL INJECTION
Fault finding – Tests13B
Siemens Injection
SID301 and 304
Vdiag No.: 44-45-48-49-4D-4C
Program No.: B1 and B2
TEST 5
CONTINUED 4
Start the engine and let it idle.
An unusual combustion noise may be heard.
Check the rail pressure using parameter PR038
Rail pressure.
At idle speed: rail pressure between 190 and
210 bar
2000 rpm: rail pressure between 440 and
560 bar
3000 rpm: rail pressure between 380 and
480 bar
4000 rpm: rail pressure between 470 and
570 bar
Are the rail pressure values correct?
NO
Replace the pump (see Replacement of
components).
Note:
Deviations from the reference values may occur in the rail pressure regulation circuit because of wear, clogging or
faulty sensors or actuators.
These deviations can only be compensated for by the pressure regulator within certain limits.
One consequence of this is that the rail pressure may be regulated so that it is too low or too high or it fluctuates.
YESRail pressure regulation circuit correct.
AFTER REPAIRCarry out a road test followed by a complete check with the diagnostic tool.
D
Page 320 of 329
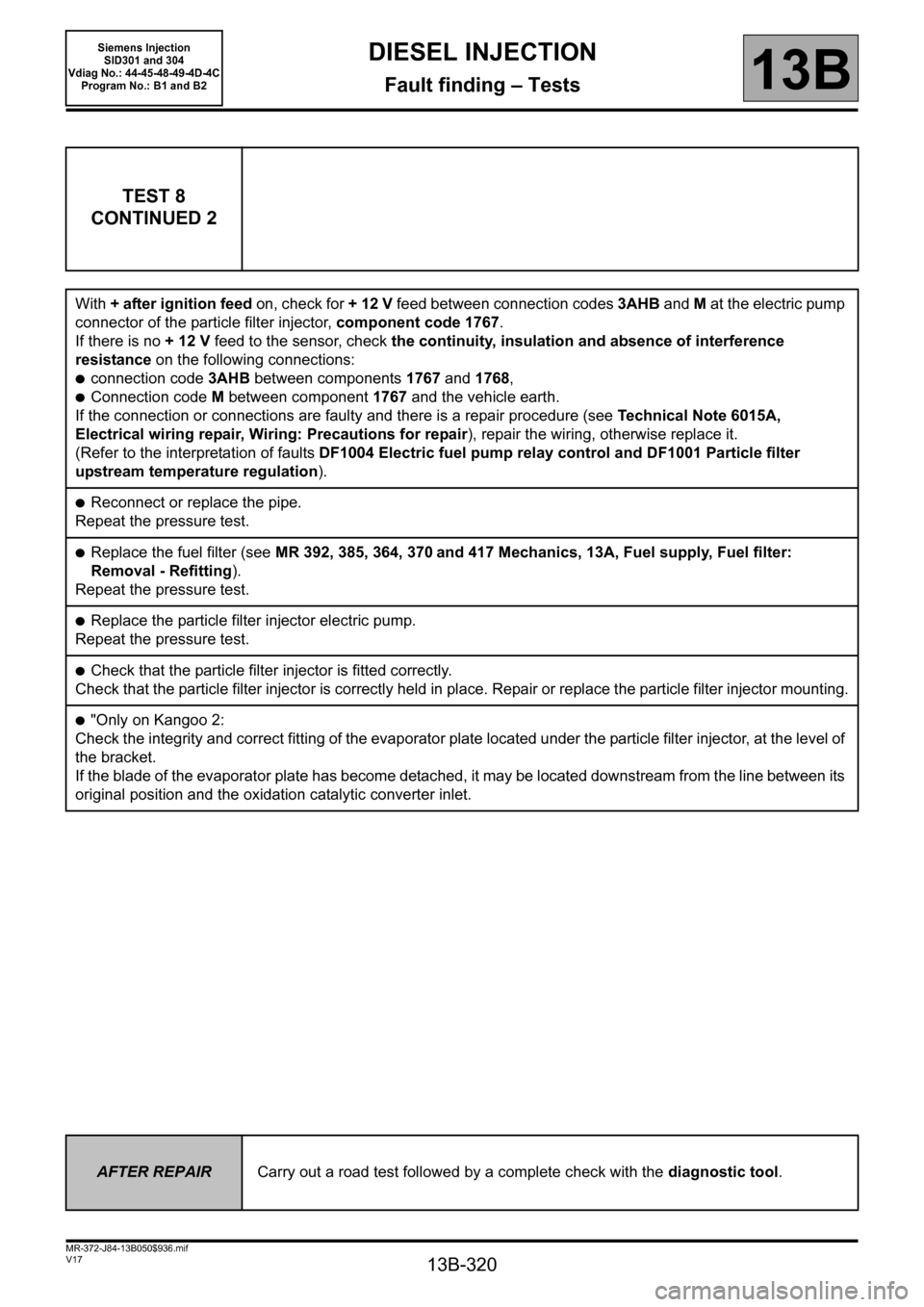
13B-320
MR-372-J84-13B050$936.mif
V17
DIESEL INJECTION
Fault finding – Tests
Siemens Injection
SID301 and 304
Vdiag No.: 44-45-48-49-4D-4C
Program No.: B1 and B2
13B
TEST 8
CONTINUED 2
With + after ignition feed on, check for + 12 V feed between connection codes 3AHB and M at the electric pump
connector of the particle filter injector, component code 1767.
If there is no + 12 V feed to the sensor, check the continuity, insulation and absence of interference
resistance on the following connections:
●connection code 3AHB between components 1767 and 1768,
●Connection code M between component 1767 and the vehicle earth.
If the connection or connections are faulty and there is a repair procedure (see Technical Note 6015A,
Electrical wiring repair, Wiring: Precautions for repair), repair the wiring, otherwise replace it.
(Refer to the interpretation of faults DF1004 Electric fuel pump relay control and DF1001 Particle filter
upstream temperature regulation).
●Reconnect or replace the pipe.
Repeat the pressure test.
●Replace the fuel filter (see MR 392, 385, 364, 370 and 417 Mechanics, 13A, Fuel supply, Fuel filter:
Removal - Refitting).
Repeat the pressure test.
●Replace the particle filter injector electric pump.
Repeat the pressure test.
●Check that the particle filter injector is fitted correctly.
Check that the particle filter injector is correctly held in place. Repair or replace the particle filter injector mounting.
●"Only on Kangoo 2:
Check the integrity and correct fitting of the evaporator plate located under the particle filter injector, at the level of
the bracket.
If the blade of the evaporator plate has become detached, it may be located downstream from the line between its
original position and the oxidation catalytic converter inlet.
AFTER REPAIRCarry out a road test followed by a complete check with the diagnostic tool.
Page 326 of 329
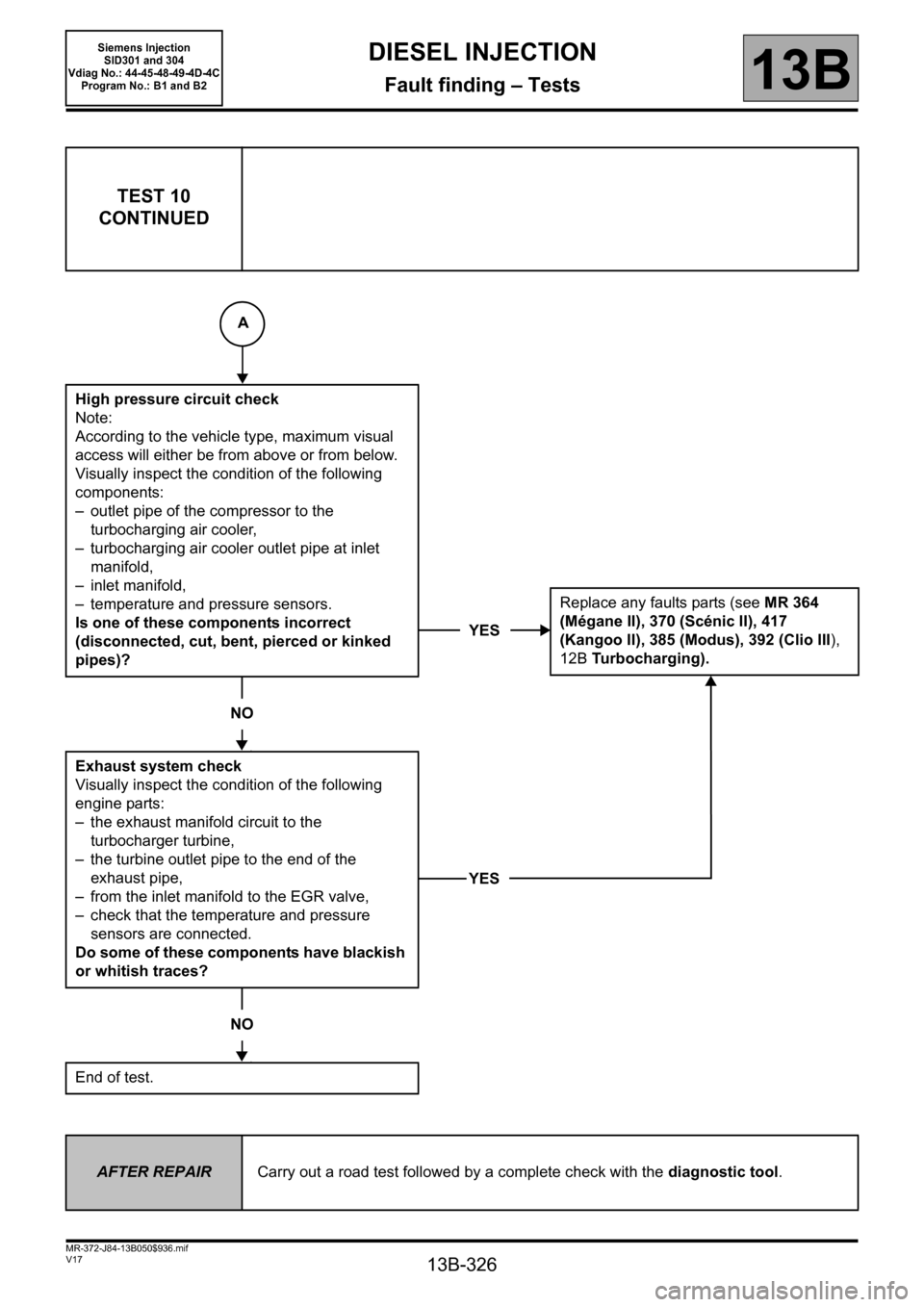
13B-326
MR-372-J84-13B050$936.mif
V17
DIESEL INJECTION
Fault finding – Tests13B
Siemens Injection
SID301 and 304
Vdiag No.: 44-45-48-49-4D-4C
Program No.: B1 and B2
TEST 10
CONTINUED
High pressure circuit check
Note:
According to the vehicle type, maximum visual
access will either be from above or from below.
Visually inspect the condition of the following
components:
– outlet pipe of the compressor to the
turbocharging air cooler,
– turbocharging air cooler outlet pipe at inlet
manifold,
– inlet manifold,
– temperature and pressure sensors.
Is one of these components incorrect
(disconnected, cut, bent, pierced or kinked
pipes)?
NO
Exhaust system check
Visually inspect the condition of the following
engine parts:
– the exhaust manifold circuit to the
turbocharger turbine,
– the turbine outlet pipe to the end of the
exhaust pipe,
– from the inlet manifold to the EGR valve,
– check that the temperature and pressure
sensors are connected.
Do some of these components have blackish
or whitish traces?
NO
End of test.
YESReplace any faults parts (see MR 364
(Mégane II), 370 (Scénic II), 417
(Kangoo II), 385 (Modus), 392 (Clio III),
12B Turbocharging).
YES
AFTER REPAIRCarry out a road test followed by a complete check with the diagnostic tool.
A