Df 129 RENAULT SCENIC 2011 J95 / 3.G Engine And Peripherals Siemens Injection User Guide
[x] Cancel search | Manufacturer: RENAULT, Model Year: 2011, Model line: SCENIC, Model: RENAULT SCENIC 2011 J95 / 3.GPages: 329, PDF Size: 1.71 MB
Page 222 of 329
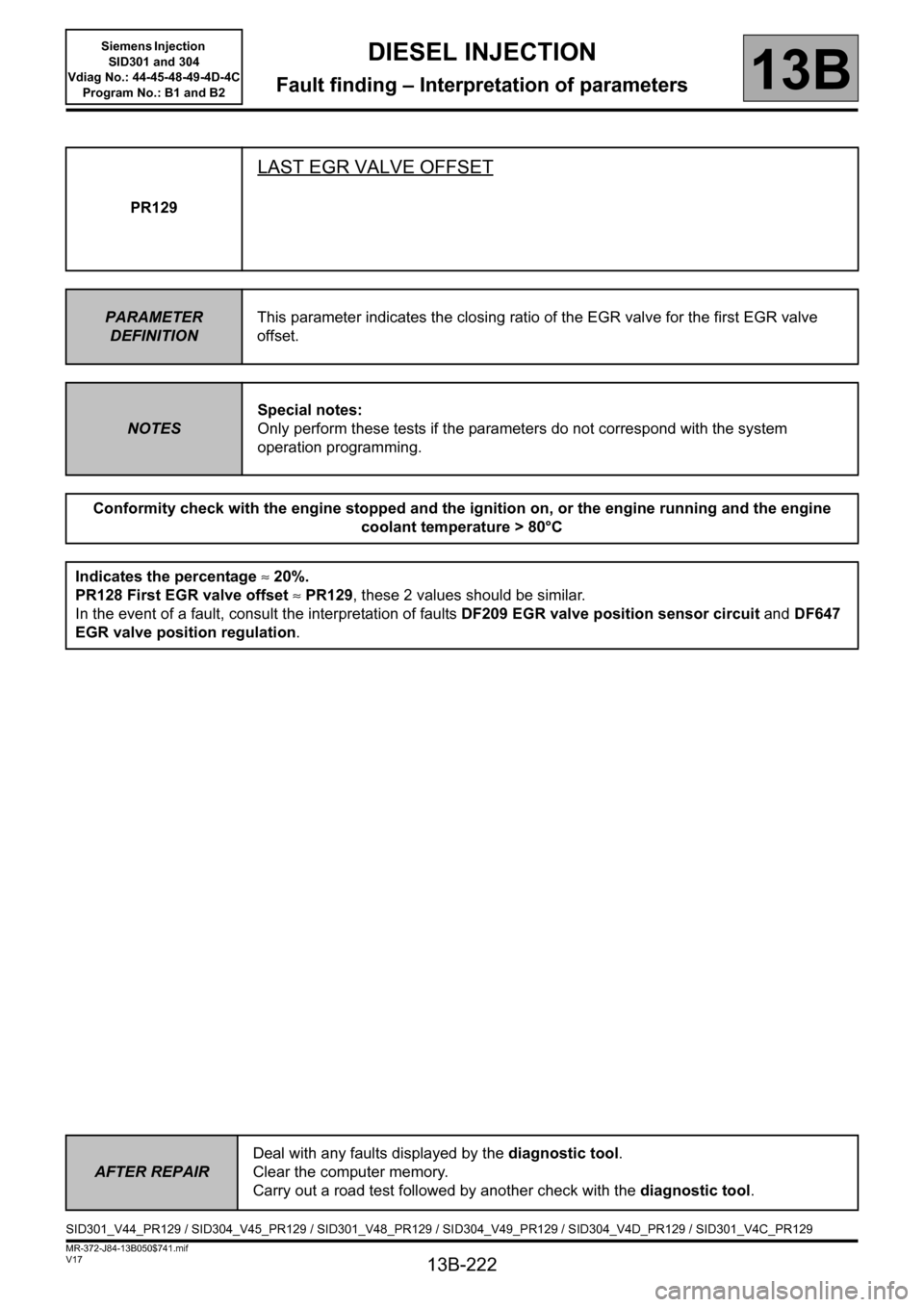
13B-222
MR-372-J84-13B050$741.mif
V17
DIESEL INJECTION
Fault finding – Interpretation of parameters
Siemens Injection
SID301 and 304
Vdiag No.: 44-45-48-49-4D-4C
Program No.: B1 and B2
13B
PR129
LAST EGR VALVE OFFSET
PARAMETER
DEFINITIONThis parameter indicates the closing ratio of the EGR valve for the first EGR valve
offset.
NOTESSpecial notes:
Only perform these tests if the parameters do not correspond with the system
operation programming.
Conformity check with the engine stopped and the ignition on, or the engine running and the engine
coolant temperature > 80°C
Indicates the percentage ≈ 20%.
PR128 First EGR valve offset ≈ PR129, these 2 values should be similar.
In the event of a fault, consult the interpretation of faults DF209 EGR valve position sensor circuit and DF647
EGR valve position regulation.
AFTER REPAIRDeal with any faults displayed by the diagnostic tool.
Clear the computer memory.
Carry out a road test followed by another check with the diagnostic tool.
SID301_V44_PR129 / SID304_V45_PR129 / SID301_V48_PR129 / SID304_V49_PR129 / SID304_V4D_PR129 / SID301_V4C_PR129
Page 278 of 329
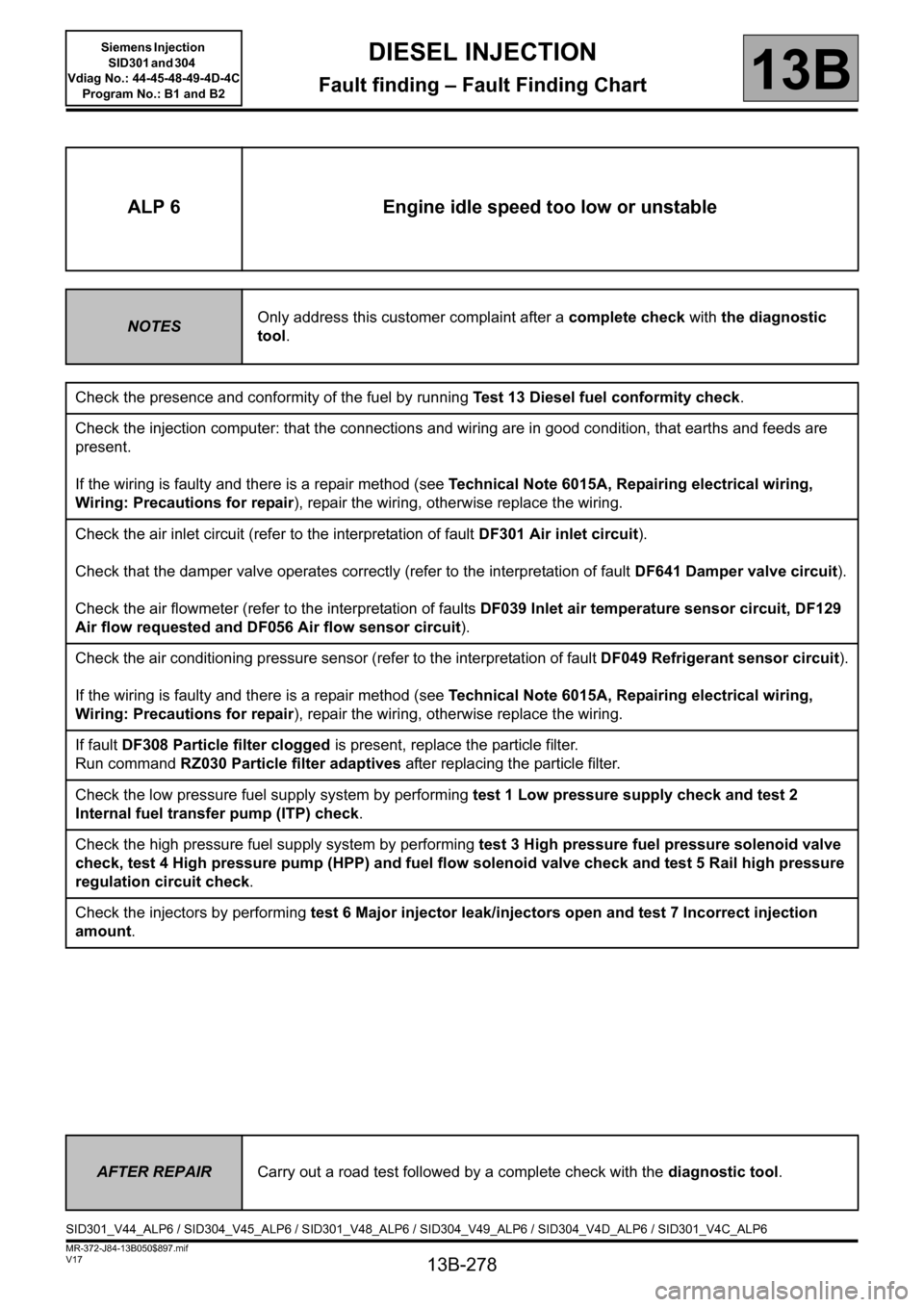
13B-278
MR-372-J84-13B050$897.mif
V17
DIESEL INJECTION
Fault finding – Fault Finding Chart
Siemens Injection
SID301 and 304
Vdiag No.: 44-45-48-49-4D-4C
Program No.: B1 and B2
13B
ALP 6 Engine idle speed too low or unstable
NOTESOnly address this customer complaint after a complete check with the diagnostic
tool.
Check the presence and conformity of the fuel by running Test 13 Diesel fuel conformity check.
Check the injection computer: that the connections and wiring are in good condition, that earths and feeds are
present.
If the wiring is faulty and there is a repair method (see Technical Note 6015A, Repairing electrical wiring,
Wiring: Precautions for repair), repair the wiring, otherwise replace the wiring.
Check the air inlet circuit (refer to the interpretation of fault DF301 Air inlet circuit).
Check that the damper valve operates correctly (refer to the interpretation of fault DF641 Damper valve circuit).
Check the air flowmeter (refer to the interpretation of faults DF039 Inlet air temperature sensor circuit, DF129
Air flow requested and DF056 Air flow sensor circuit).
Check the air conditioning pressure sensor (refer to the interpretation of fault DF049 Refrigerant sensor circuit).
If the wiring is faulty and there is a repair method (see Technical Note 6015A, Repairing electrical wiring,
Wiring: Precautions for repair), repair the wiring, otherwise replace the wiring.
If fault DF308 Particle filter clogged is present, replace the particle filter.
Run command RZ030 Particle filter adaptives after replacing the particle filter.
Check the low pressure fuel supply system by performing test 1 Low pressure supply check and test 2
Internal fuel transfer pump (ITP) check.
Check the high pressure fuel supply system by performing test 3 High pressure fuel pressure solenoid valve
check, test 4 High pressure pump (HPP) and fuel flow solenoid valve check and test 5 Rail high pressure
regulation circuit check.
Check the injectors by performing test 6 Major injector leak/injectors open and test 7 Incorrect injection
amount.
AFTER REPAIRCarry out a road test followed by a complete check with the diagnostic tool.
SID301_V44_ALP6 / SID304_V45_ALP6 / SID301_V48_ALP6 / SID304_V49_ALP6 / SID304_V4D_ALP6 / SID301_V4C_ALP6
Page 279 of 329
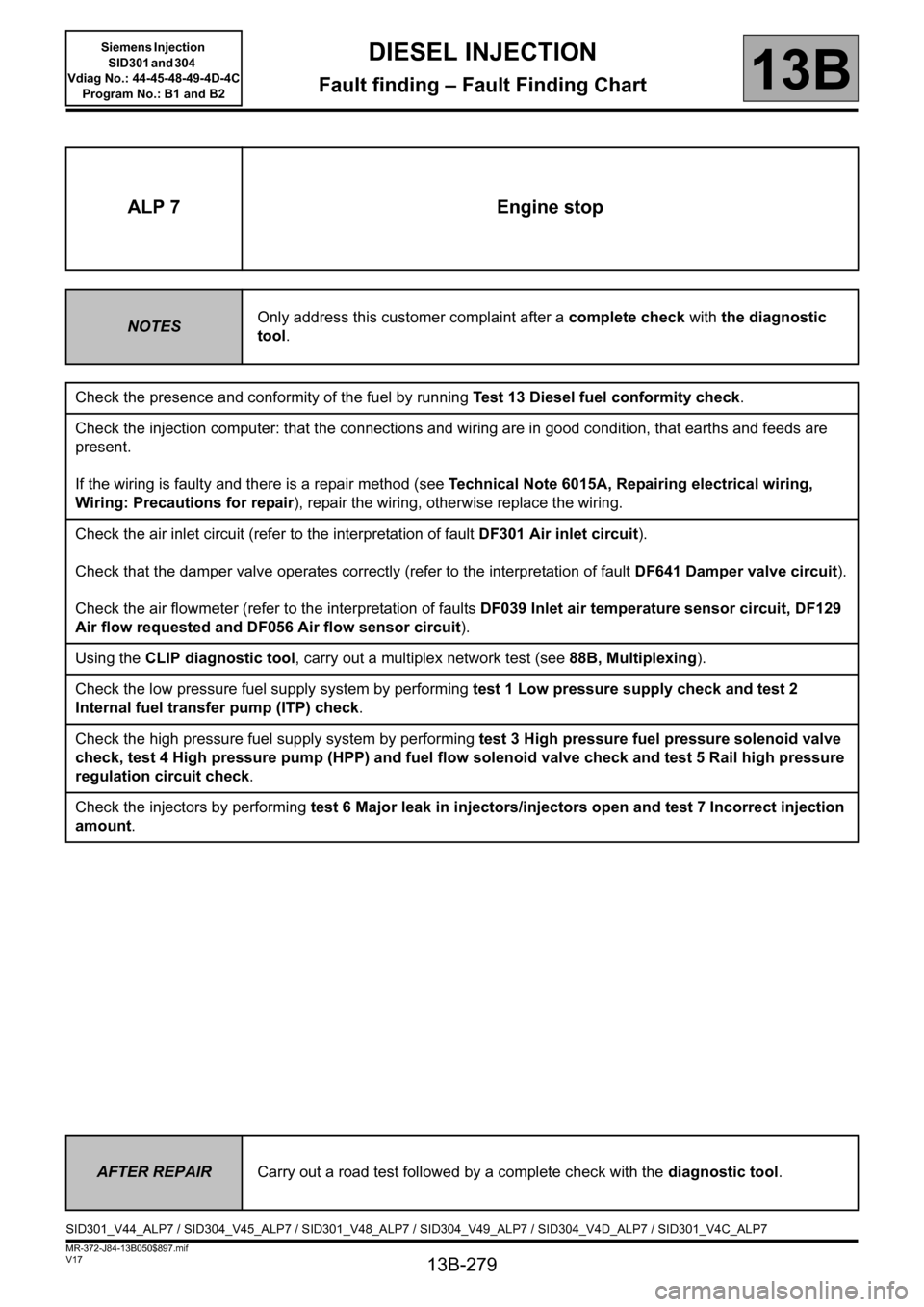
13B-279
MR-372-J84-13B050$897.mif
V17
DIESEL INJECTION
Fault finding – Fault Finding Chart
Siemens Injection
SID301 and 304
Vdiag No.: 44-45-48-49-4D-4C
Program No.: B1 and B2
13B
ALP 7 Engine stop
NOTESOnly address this customer complaint after a complete check with the diagnostic
tool.
Check the presence and conformity of the fuel by running Test 13 Diesel fuel conformity check.
Check the injection computer: that the connections and wiring are in good condition, that earths and feeds are
present.
If the wiring is faulty and there is a repair method (see Technical Note 6015A, Repairing electrical wiring,
Wiring: Precautions for repair), repair the wiring, otherwise replace the wiring.
Check the air inlet circuit (refer to the interpretation of fault DF301 Air inlet circuit).
Check that the damper valve operates correctly (refer to the interpretation of fault DF641 Damper valve circuit).
Check the air flowmeter (refer to the interpretation of faults DF039 Inlet air temperature sensor circuit, DF129
Air flow requested and DF056 Air flow sensor circuit).
Using the CLIP diagnostic tool, carry out a multiplex network test (see 88B, Multiplexing).
Check the low pressure fuel supply system by performing test 1 Low pressure supply check and test 2
Internal fuel transfer pump (ITP) check.
Check the high pressure fuel supply system by performing test 3 High pressure fuel pressure solenoid valve
check, test 4 High pressure pump (HPP) and fuel flow solenoid valve check and test 5 Rail high pressure
regulation circuit check.
Check the injectors by performing test 6 Major leak in injectors/injectors open and test 7 Incorrect injection
amount.
AFTER REPAIRCarry out a road test followed by a complete check with the diagnostic tool.
SID301_V44_ALP7 / SID304_V45_ALP7 / SID301_V48_ALP7 / SID304_V49_ALP7 / SID304_V4D_ALP7 / SID301_V4C_ALP7
Page 280 of 329
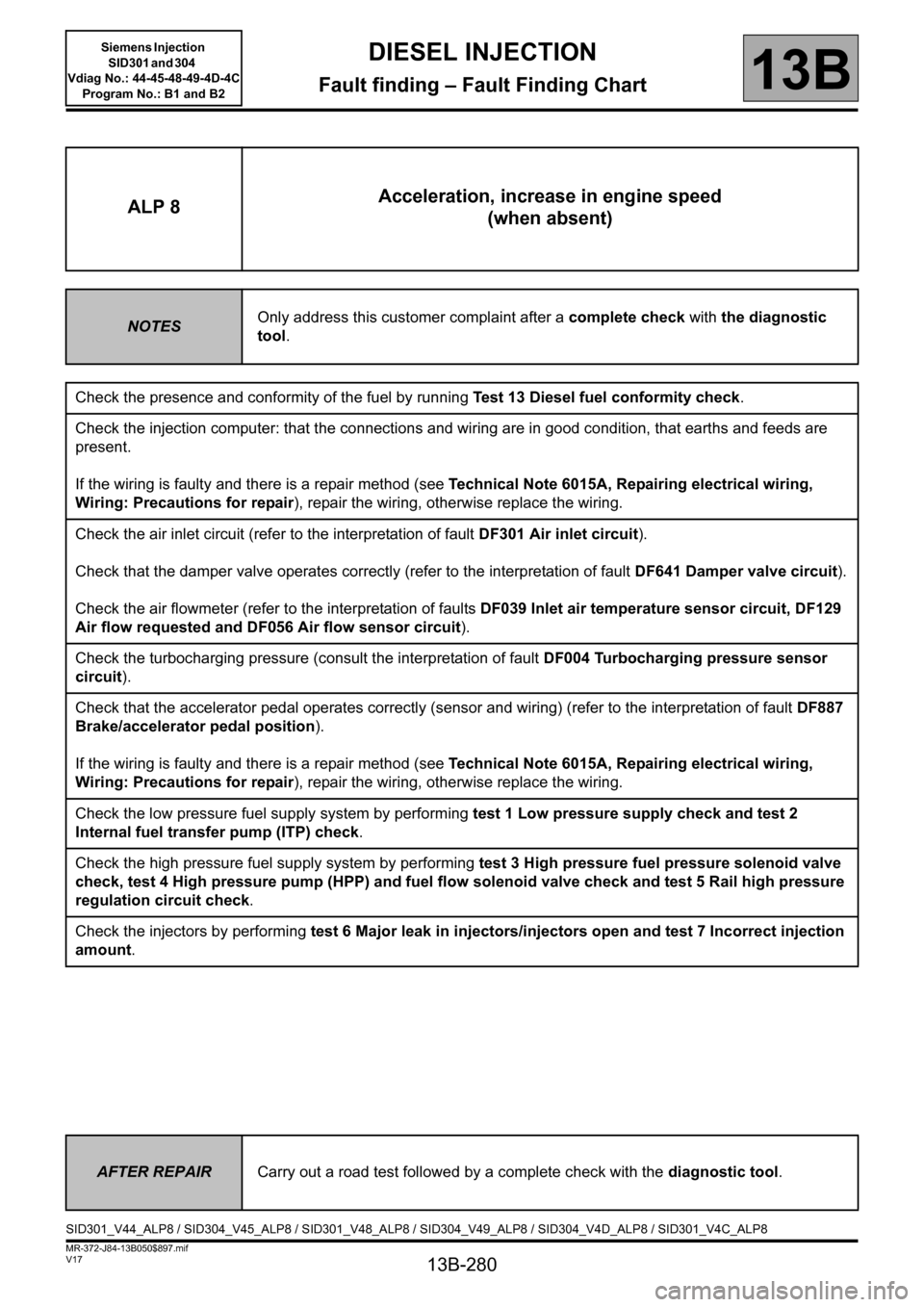
13B-280
MR-372-J84-13B050$897.mif
V17
DIESEL INJECTION
Fault finding – Fault Finding Chart
Siemens Injection
SID301 and 304
Vdiag No.: 44-45-48-49-4D-4C
Program No.: B1 and B2
13B
ALP 8Acceleration, increase in engine speed
(when absent)
NOTESOnly address this customer complaint after a complete check with the diagnostic
tool.
Check the presence and conformity of the fuel by running Test 13 Diesel fuel conformity check.
Check the injection computer: that the connections and wiring are in good condition, that earths and feeds are
present.
If the wiring is faulty and there is a repair method (see Technical Note 6015A, Repairing electrical wiring,
Wiring: Precautions for repair), repair the wiring, otherwise replace the wiring.
Check the air inlet circuit (refer to the interpretation of fault DF301 Air inlet circuit).
Check that the damper valve operates correctly (refer to the interpretation of fault DF641 Damper valve circuit).
Check the air flowmeter (refer to the interpretation of faults DF039 Inlet air temperature sensor circuit, DF129
Air flow requested and DF056 Air flow sensor circuit).
Check the turbocharging pressure (consult the interpretation of fault DF004 Turbocharging pressure sensor
circuit).
Check that the accelerator pedal operates correctly (sensor and wiring) (refer to the interpretation of fault DF887
Brake/accelerator pedal position).
If the wiring is faulty and there is a repair method (see Technical Note 6015A, Repairing electrical wiring,
Wiring: Precautions for repair), repair the wiring, otherwise replace the wiring.
Check the low pressure fuel supply system by performing test 1 Low pressure supply check and test 2
Internal fuel transfer pump (ITP) check.
Check the high pressure fuel supply system by performing test 3 High pressure fuel pressure solenoid valve
check, test 4 High pressure pump (HPP) and fuel flow solenoid valve check and test 5 Rail high pressure
regulation circuit check.
Check the injectors by performing test 6 Major leak in injectors/injectors open and test 7 Incorrect injection
amount.
AFTER REPAIRCarry out a road test followed by a complete check with the diagnostic tool.
SID301_V44_ALP8 / SID304_V45_ALP8 / SID301_V48_ALP8 / SID304_V49_ALP8 / SID304_V4D_ALP8 / SID301_V4C_ALP8
Page 281 of 329
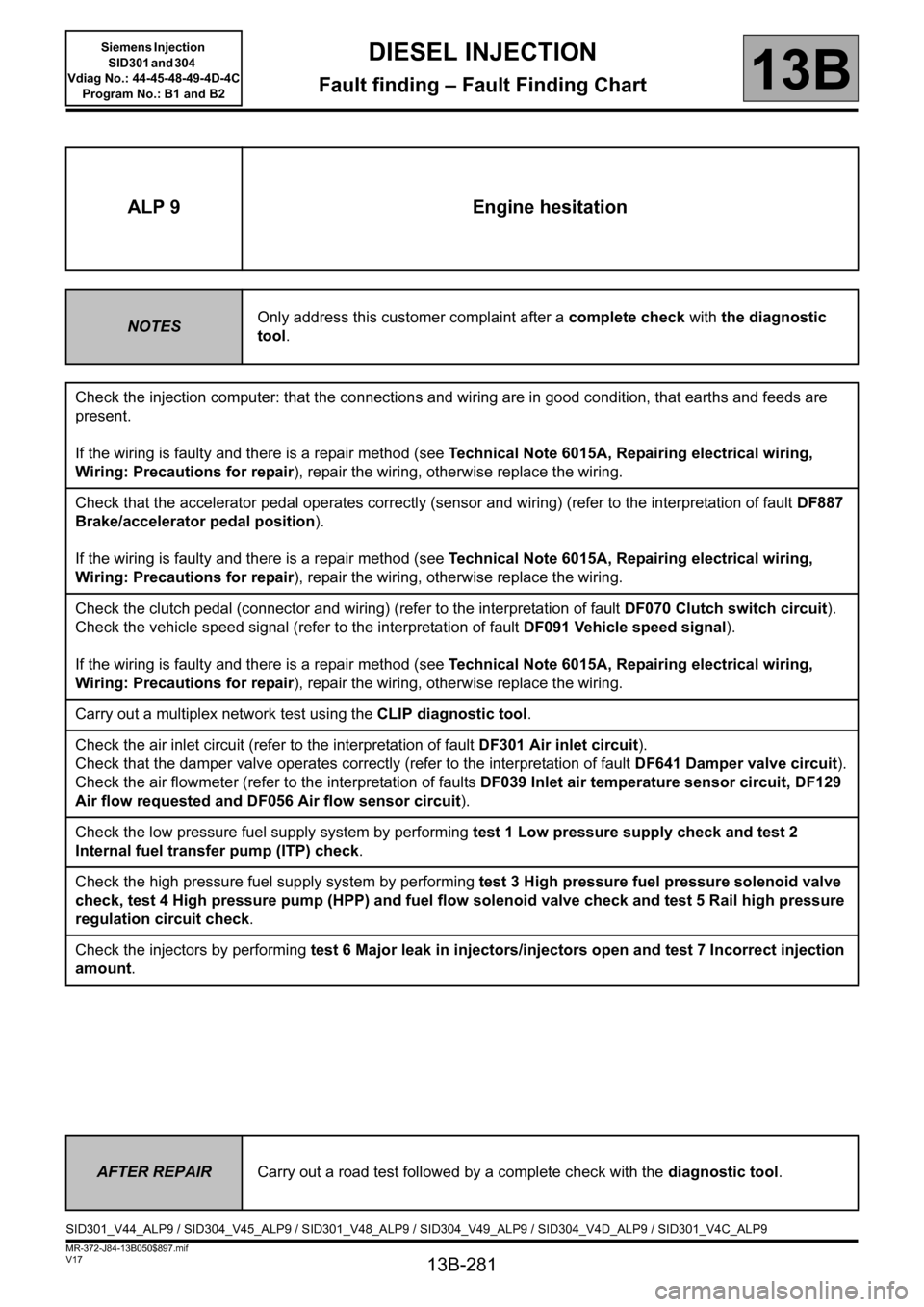
13B-281
MR-372-J84-13B050$897.mif
V17
DIESEL INJECTION
Fault finding – Fault Finding Chart
Siemens Injection
SID301 and 304
Vdiag No.: 44-45-48-49-4D-4C
Program No.: B1 and B2
13B
ALP 9 Engine hesitation
NOTESOnly address this customer complaint after a complete check with the diagnostic
tool.
Check the injection computer: that the connections and wiring are in good condition, that earths and feeds are
present.
If the wiring is faulty and there is a repair method (see Technical Note 6015A, Repairing electrical wiring,
Wiring: Precautions for repair), repair the wiring, otherwise replace the wiring.
Check that the accelerator pedal operates correctly (sensor and wiring) (refer to the interpretation of fault DF887
Brake/accelerator pedal position).
If the wiring is faulty and there is a repair method (see Technical Note 6015A, Repairing electrical wiring,
Wiring: Precautions for repair), repair the wiring, otherwise replace the wiring.
Check the clutch pedal (connector and wiring) (refer to the interpretation of fault DF070 Clutch switch circuit).
Check the vehicle speed signal (refer to the interpretation of fault DF091 Vehicle speed signal).
If the wiring is faulty and there is a repair method (see Technical Note 6015A, Repairing electrical wiring,
Wiring: Precautions for repair), repair the wiring, otherwise replace the wiring.
Carry out a multiplex network test using the CLIP diagnostic tool.
Check the air inlet circuit (refer to the interpretation of fault DF301 Air inlet circuit).
Check that the damper valve operates correctly (refer to the interpretation of fault DF641 Damper valve circuit).
Check the air flowmeter (refer to the interpretation of faults DF039 Inlet air temperature sensor circuit, DF129
Air flow requested and DF056 Air flow sensor circuit).
Check the low pressure fuel supply system by performing test 1 Low pressure supply check and test 2
Internal fuel transfer pump (ITP) check.
Check the high pressure fuel supply system by performing test 3 High pressure fuel pressure solenoid valve
check, test 4 High pressure pump (HPP) and fuel flow solenoid valve check and test 5 Rail high pressure
regulation circuit check.
Check the injectors by performing test 6 Major leak in injectors/injectors open and test 7 Incorrect injection
amount.
AFTER REPAIRCarry out a road test followed by a complete check with the diagnostic tool.
SID301_V44_ALP9 / SID304_V45_ALP9 / SID301_V48_ALP9 / SID304_V49_ALP9 / SID304_V4D_ALP9 / SID301_V4C_ALP9
Page 284 of 329
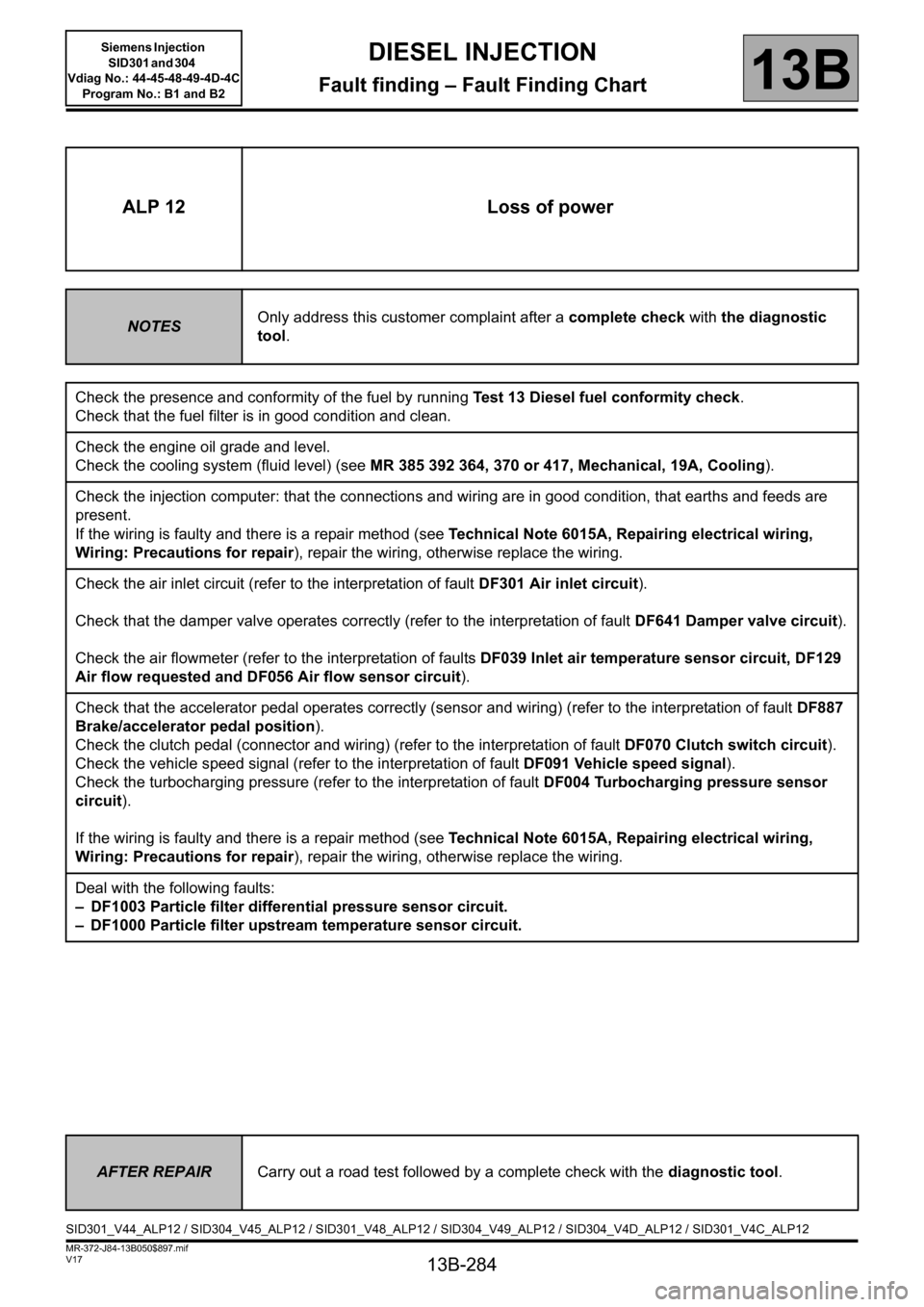
13B-284
MR-372-J84-13B050$897.mif
V17
DIESEL INJECTION
Fault finding – Fault Finding Chart
Siemens Injection
SID301 and 304
Vdiag No.: 44-45-48-49-4D-4C
Program No.: B1 and B2
13B
ALP 12 Loss of power
NOTESOnly address this customer complaint after a complete check with the diagnostic
tool.
Check the presence and conformity of the fuel by running Test 13 Diesel fuel conformity check.
Check that the fuel filter is in good condition and clean.
Check the engine oil grade and level.
Check the cooling system (fluid level) (see MR 385 392 364, 370 or 417, Mechanical, 19A, Cooling).
Check the injection computer: that the connections and wiring are in good condition, that earths and feeds are
present.
If the wiring is faulty and there is a repair method (see Technical Note 6015A, Repairing electrical wiring,
Wiring: Precautions for repair), repair the wiring, otherwise replace the wiring.
Check the air inlet circuit (refer to the interpretation of fault DF301 Air inlet circuit).
Check that the damper valve operates correctly (refer to the interpretation of fault DF641 Damper valve circuit).
Check the air flowmeter (refer to the interpretation of faults DF039 Inlet air temperature sensor circuit, DF129
Air flow requested and DF056 Air flow sensor circuit).
Check that the accelerator pedal operates correctly (sensor and wiring) (refer to the interpretation of fault DF887
Brake/accelerator pedal position).
Check the clutch pedal (connector and wiring) (refer to the interpretation of fault DF070 Clutch switch circuit).
Check the vehicle speed signal (refer to the interpretation of fault DF091 Vehicle speed signal).
Check the turbocharging pressure (refer to the interpretation of fault DF004 Turbocharging pressure sensor
circuit).
If the wiring is faulty and there is a repair method (see Technical Note 6015A, Repairing electrical wiring,
Wiring: Precautions for repair), repair the wiring, otherwise replace the wiring.
Deal with the following faults:
– DF1003 Particle filter differential pressure sensor circuit.
– DF1000 Particle filter upstream temperature sensor circuit.
AFTER REPAIRCarry out a road test followed by a complete check with the diagnostic tool.
SID301_V44_ALP12 / SID304_V45_ALP12 / SID301_V48_ALP12 / SID304_V49_ALP12 / SID304_V4D_ALP12 / SID301_V4C_ALP12
Page 288 of 329
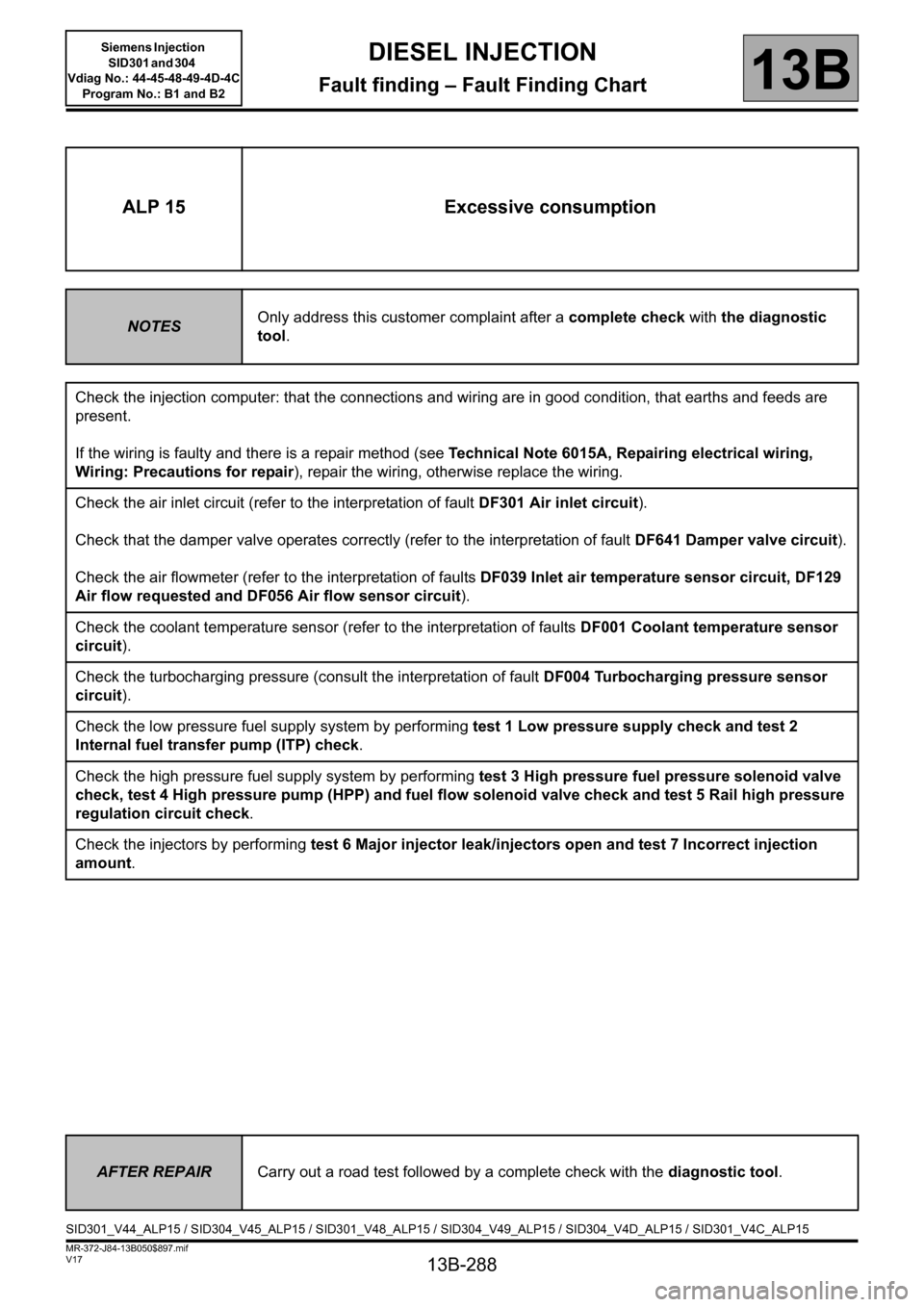
13B-288
MR-372-J84-13B050$897.mif
V17
DIESEL INJECTION
Fault finding – Fault Finding Chart
Siemens Injection
SID301 and 304
Vdiag No.: 44-45-48-49-4D-4C
Program No.: B1 and B2
13B
ALP 15 Excessive consumption
NOTESOnly address this customer complaint after a complete check with the diagnostic
tool.
Check the injection computer: that the connections and wiring are in good condition, that earths and feeds are
present.
If the wiring is faulty and there is a repair method (see Technical Note 6015A, Repairing electrical wiring,
Wiring: Precautions for repair), repair the wiring, otherwise replace the wiring.
Check the air inlet circuit (refer to the interpretation of fault DF301 Air inlet circuit).
Check that the damper valve operates correctly (refer to the interpretation of fault DF641 Damper valve circuit).
Check the air flowmeter (refer to the interpretation of faults DF039 Inlet air temperature sensor circuit, DF129
Air flow requested and DF056 Air flow sensor circuit).
Check the coolant temperature sensor (refer to the interpretation of faults DF001 Coolant temperature sensor
circuit).
Check the turbocharging pressure (consult the interpretation of fault DF004 Turbocharging pressure sensor
circuit).
Check the low pressure fuel supply system by performing test 1 Low pressure supply check and test 2
Internal fuel transfer pump (ITP) check.
Check the high pressure fuel supply system by performing test 3 High pressure fuel pressure solenoid valve
check, test 4 High pressure pump (HPP) and fuel flow solenoid valve check and test 5 Rail high pressure
regulation circuit check.
Check the injectors by performing test 6 Major injector leak/injectors open and test 7 Incorrect injection
amount.
AFTER REPAIRCarry out a road test followed by a complete check with the diagnostic tool.
SID301_V44_ALP15 / SID304_V45_ALP15 / SID301_V48_ALP15 / SID304_V49_ALP15 / SID304_V4D_ALP15 / SID301_V4C_ALP15
Page 290 of 329
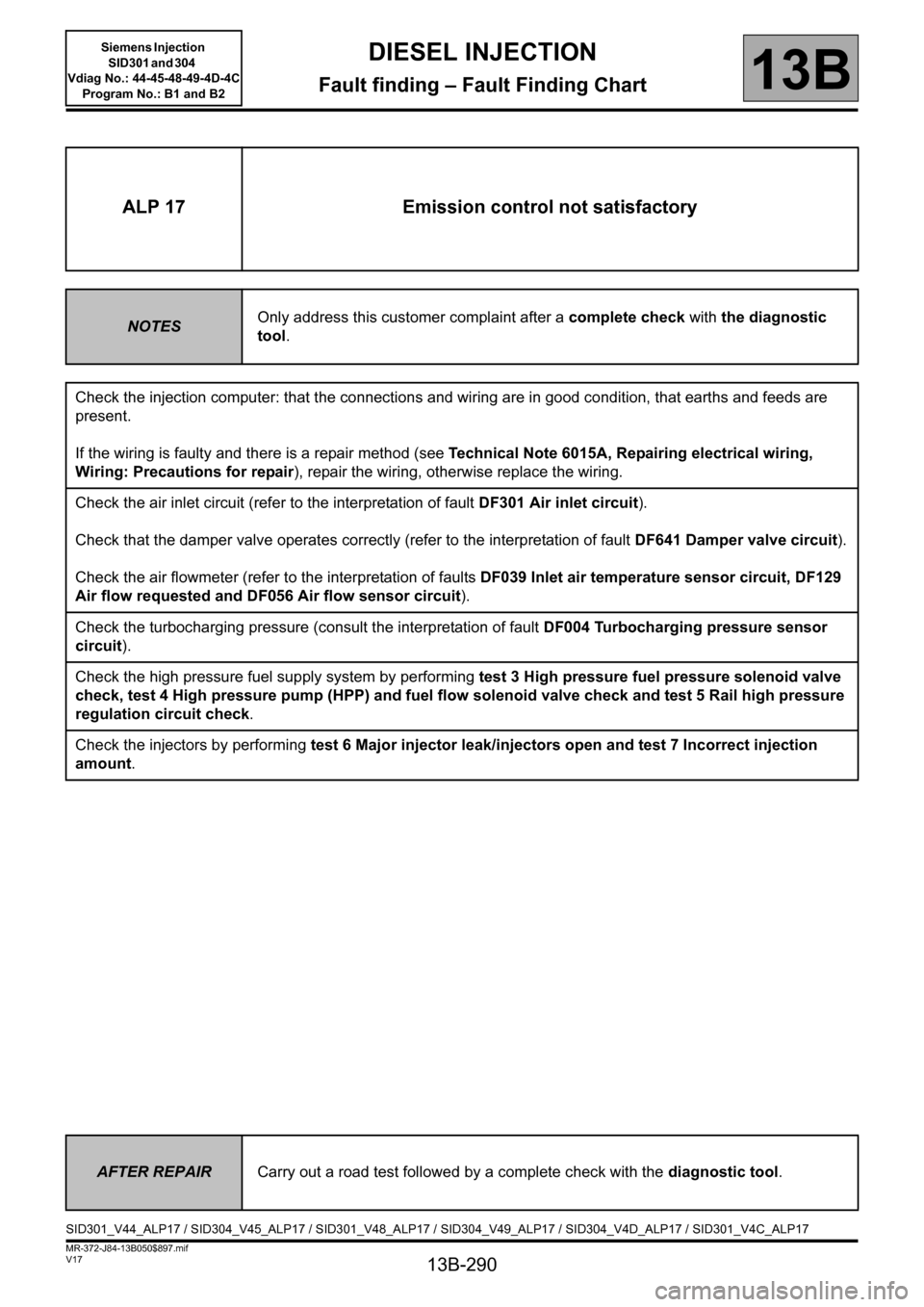
13B-290
MR-372-J84-13B050$897.mif
V17
DIESEL INJECTION
Fault finding – Fault Finding Chart
Siemens Injection
SID301 and 304
Vdiag No.: 44-45-48-49-4D-4C
Program No.: B1 and B2
13B
ALP 17 Emission control not satisfactory
NOTESOnly address this customer complaint after a complete check with the diagnostic
tool.
Check the injection computer: that the connections and wiring are in good condition, that earths and feeds are
present.
If the wiring is faulty and there is a repair method (see Technical Note 6015A, Repairing electrical wiring,
Wiring: Precautions for repair), repair the wiring, otherwise replace the wiring.
Check the air inlet circuit (refer to the interpretation of fault DF301 Air inlet circuit).
Check that the damper valve operates correctly (refer to the interpretation of fault DF641 Damper valve circuit).
Check the air flowmeter (refer to the interpretation of faults DF039 Inlet air temperature sensor circuit, DF129
Air flow requested and DF056 Air flow sensor circuit).
Check the turbocharging pressure (consult the interpretation of fault DF004 Turbocharging pressure sensor
circuit).
Check the high pressure fuel supply system by performing test 3 High pressure fuel pressure solenoid valve
check, test 4 High pressure pump (HPP) and fuel flow solenoid valve check and test 5 Rail high pressure
regulation circuit check.
Check the injectors by performing test 6 Major injector leak/injectors open and test 7 Incorrect injection
amount.
AFTER REPAIRCarry out a road test followed by a complete check with the diagnostic tool.
SID301_V44_ALP17 / SID304_V45_ALP17 / SID301_V48_ALP17 / SID304_V49_ALP17 / SID304_V4D_ALP17 / SID301_V4C_ALP17
Page 296 of 329
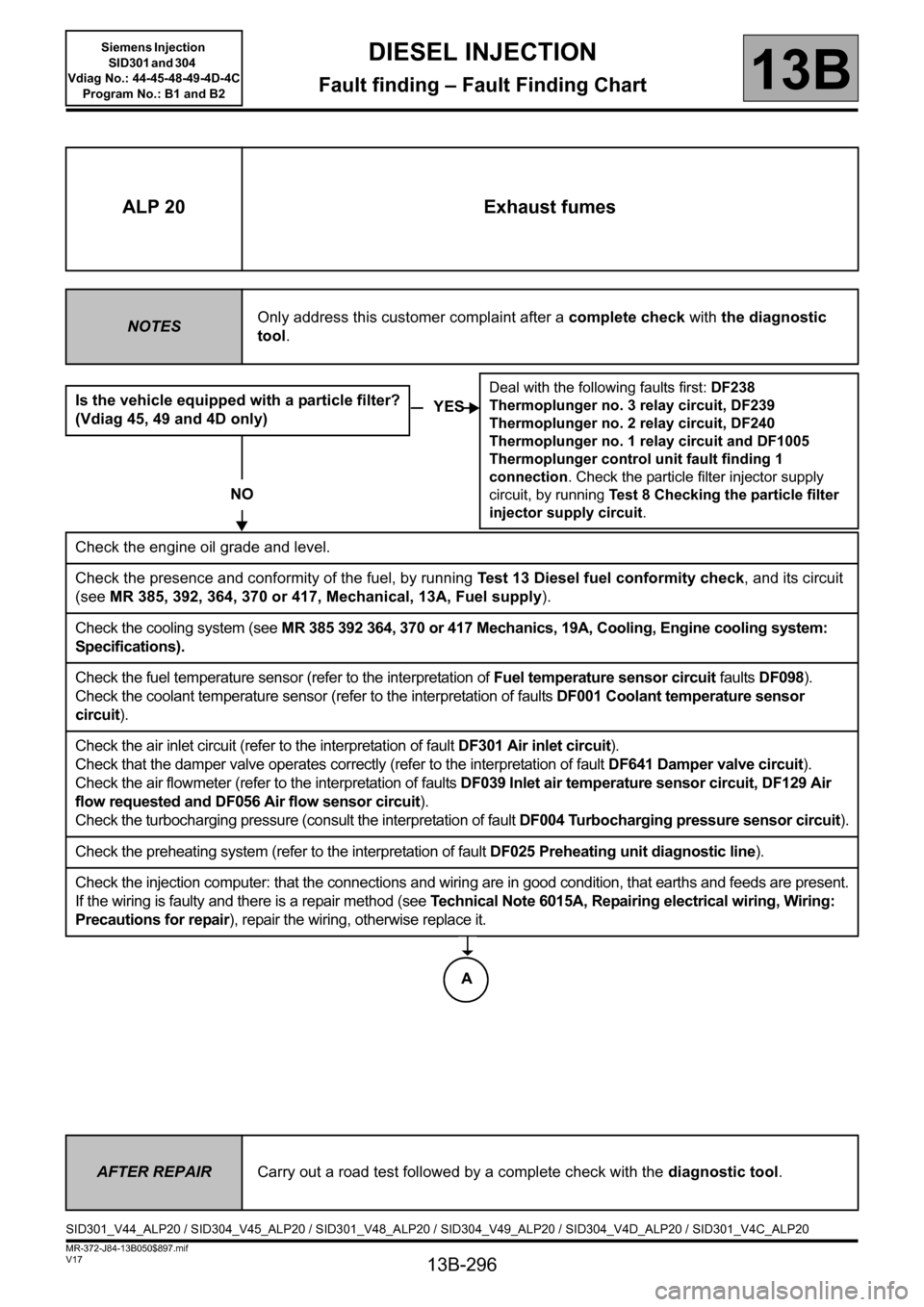
13B-296
MR-372-J84-13B050$897.mif
V17
Siemens Injection
SID301 and 304
Vdiag No.: 44-45-48-49-4D-4C
Program No.: B1 and B2DIESEL INJECTION
Fault finding – Fault Finding Chart13B
ALP 20 Exhaust fumes
NOTESOnly address this customer complaint after a complete check with the diagnostic
tool.
Is the vehicle equipped with a particle filter?
(Vdiag 45, 49 and 4D only)
NO
Check the engine oil grade and level.
Check the presence and conformity of the fuel, by running Test 13 Diesel fuel conformity check, and its circuit
(see MR 385, 392, 364, 370 or 417, Mechanical, 13A, Fuel supply).
Check the cooling system (see MR 385 392 364, 370 or 417 Mechanics, 19A, Cooling, Engine cooling system:
Specifications).
Check the fuel temperature sensor (refer to the interpretation of Fuel temperature sensor circuit faults DF098).
Check the coolant temperature sensor (refer to the interpretation of faults DF001 Coolant temperature sensor
circuit).
Check the air inlet circuit (refer to the interpretation of fault DF301 Air inlet circuit).
Check that the damper valve operates correctly (refer to the interpretation of fault DF641 Damper valve circuit).
Check the air flowmeter (refer to the interpretation of faults DF039 Inlet air temperature sensor circuit, DF129 Air
flow requested and DF056 Air flow sensor circuit).
Check the turbocharging pressure (consult the interpretation of fault DF004 Turbocharging pressure sensor circuit).
Check the preheating system (refer to the interpretation of fault DF025 Preheating unit diagnostic line).
Check the injection computer: that the connections and wiring are in good condition, that earths and feeds are present.
If the wiring is faulty and there is a repair method (see Technical Note 6015A, Repairing electrical wiring, Wiring:
Precautions for repair), repair the wiring, otherwise replace it.
YES
Deal with the following faults first: DF238
Thermoplunger no. 3 relay circuit, DF239
Thermoplunger no. 2 relay circuit, DF240
Thermoplunger no. 1 relay circuit and DF1005
Thermoplunger control unit fault finding 1
connection. Check the particle filter injector supply
circuit, by running Test 8 Checking the particle filter
injector supply circuit.
AFTER REPAIRCarry out a road test followed by a complete check with the diagnostic tool.
SID301_V44_ALP20 / SID304_V45_ALP20 / SID301_V48_ALP20 / SID304_V49_ALP20 / SID304_V4D_ALP20 / SID301_V4C_ALP20
A
Page 299 of 329
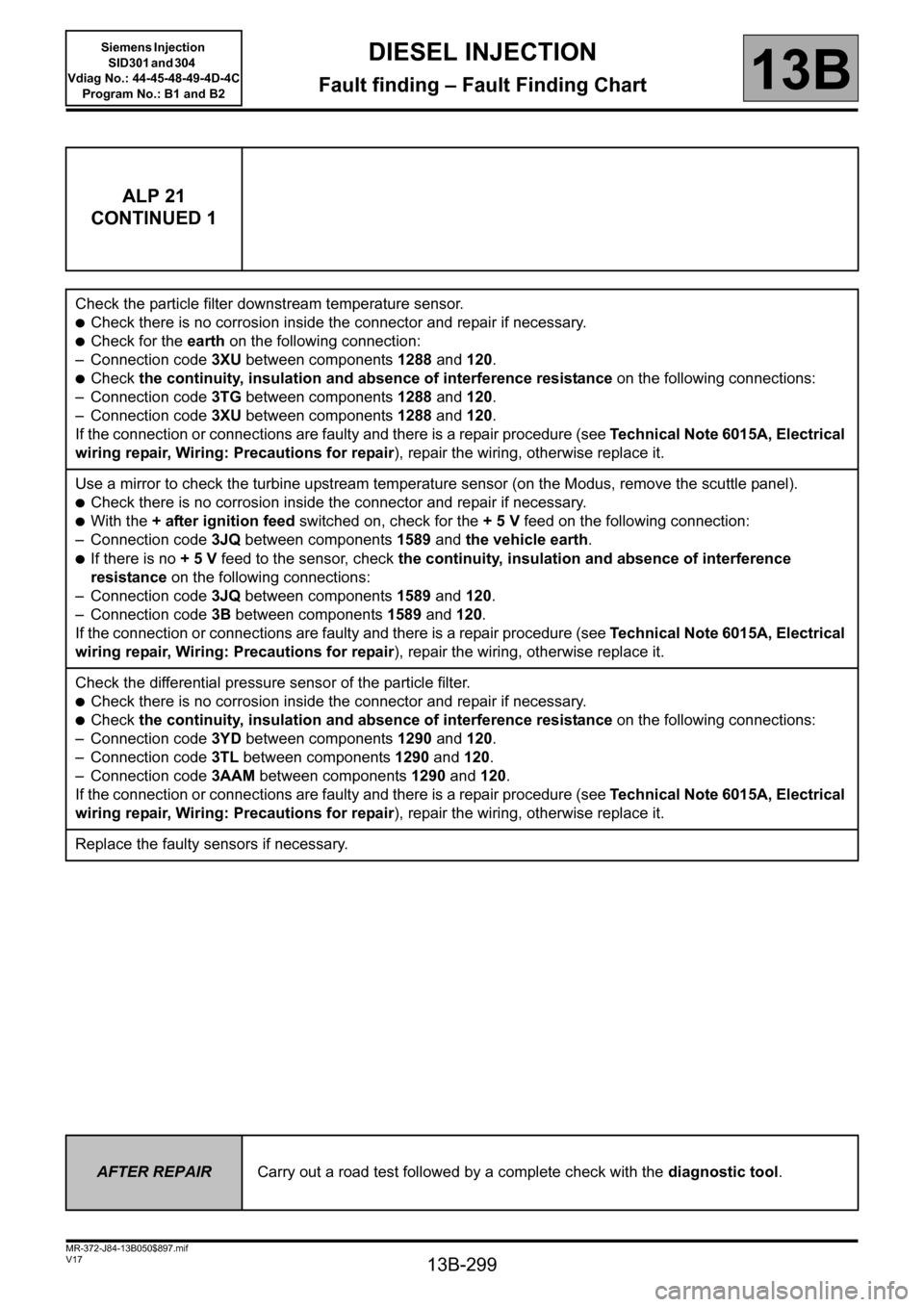
13B-299
MR-372-J84-13B050$897.mif
V17
DIESEL INJECTION
Fault finding – Fault Finding Chart
Siemens Injection
SID301 and 304
Vdiag No.: 44-45-48-49-4D-4C
Program No.: B1 and B2
13B
ALP 21
CONTINUED 1
Check the particle filter downstream temperature sensor.
●Check there is no corrosion inside the connector and repair if necessary.
●Check for the earth on the following connection:
– Connection code 3XU between components 1288 and 120.
●Check the continuity, insulation and absence of interference resistance on the following connections:
– Connection code 3TG between components 1288 and 120.
– Connection code 3XU between components 1288 and 120.
If the connection or connections are faulty and there is a repair procedure (see Technical Note 6015A, Electrical
wiring repair, Wiring: Precautions for repair), repair the wiring, otherwise replace it.
Use a mirror to check the turbine upstream temperature sensor (on the Modus, remove the scuttle panel).
●Check there is no corrosion inside the connector and repair if necessary.
●With the + after ignition feed switched on, check for the + 5 V feed on the following connection:
– Connection code 3JQ between components 1589 and the vehicle earth.
●If there is no + 5 V feed to the sensor, check the continuity, insulation and absence of interference
resistance on the following connections:
– Connection code 3JQ between components 1589 and 120.
– Connection code 3B between components 1589 and 120.
If the connection or connections are faulty and there is a repair procedure (see Technical Note 6015A, Electrical
wiring repair, Wiring: Precautions for repair), repair the wiring, otherwise replace it.
Check the differential pressure sensor of the particle filter.
●Check there is no corrosion inside the connector and repair if necessary.
●Check the continuity, insulation and absence of interference resistance on the following connections:
– Connection code 3YD between components 1290 and 120.
– Connection code 3TL between components 1290 and 120.
– Connection code 3AAM between components 1290 and 120.
If the connection or connections are faulty and there is a repair procedure (see Technical Note 6015A, Electrical
wiring repair, Wiring: Precautions for repair), repair the wiring, otherwise replace it.
Replace the faulty sensors if necessary.
AFTER REPAIRCarry out a road test followed by a complete check with the diagnostic tool.