fuel filter RENAULT SCENIC 2011 J95 / 3.G Engine And Peripherals Siemens Injection Owner's Manual
[x] Cancel search | Manufacturer: RENAULT, Model Year: 2011, Model line: SCENIC, Model: RENAULT SCENIC 2011 J95 / 3.GPages: 329, PDF Size: 1.71 MB
Page 187 of 329
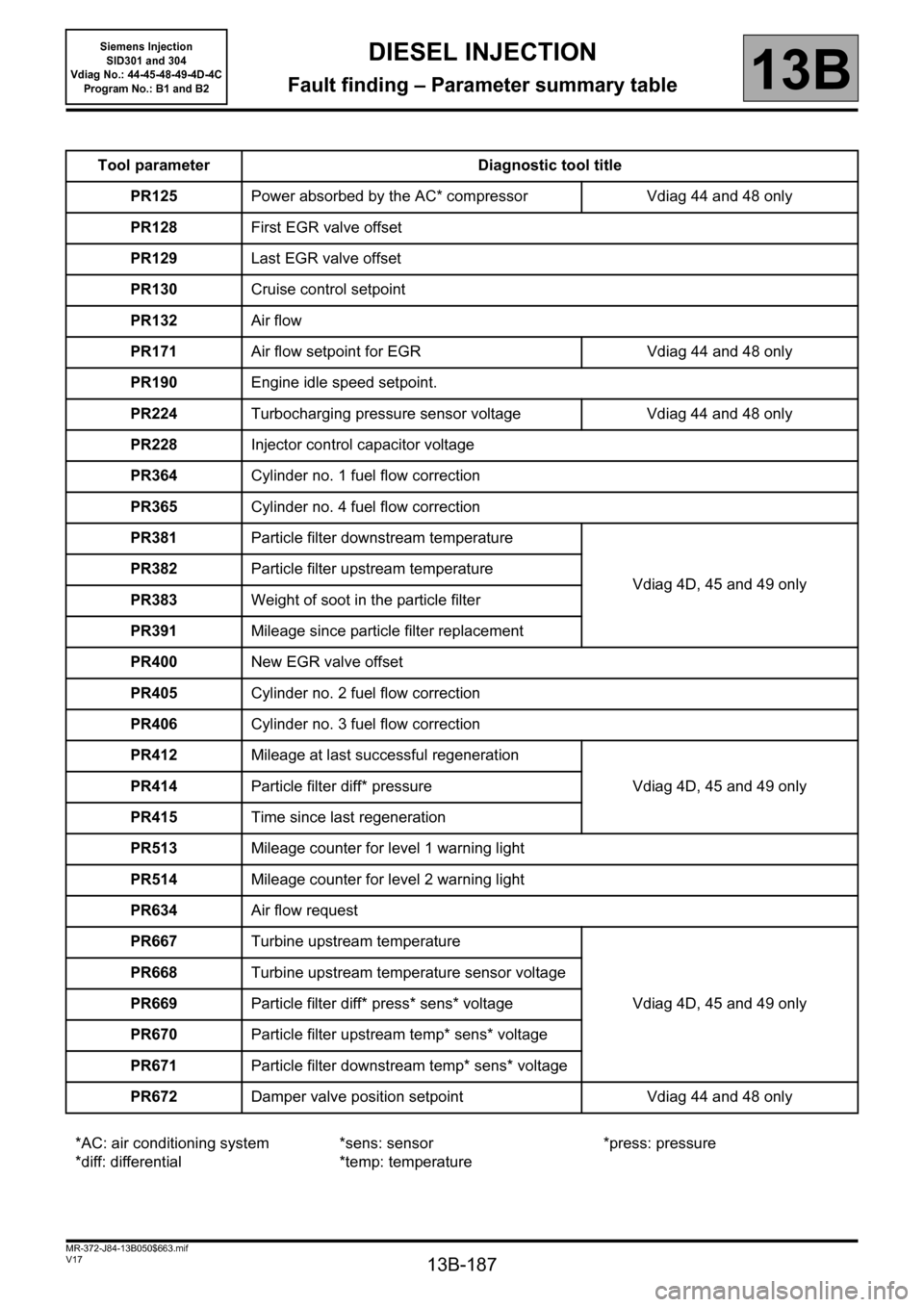
13B-187
MR-372-J84-13B050$663.mif
V17
Siemens Injection
SID301 and 304
Vdiag No.: 44-45-48-49-4D-4C
Program No.: B1 and B2DIESEL INJECTION
Fault finding – Parameter summary table13B
Tool parameter Diagnostic tool title
PR125Power absorbed by the AC* compressor Vdiag 44 and 48 only
PR128First EGR valve offset
PR129Last EGR valve offset
PR130Cruise control setpoint
PR132Air flow
PR171Air flow setpoint for EGR Vdiag 44 and 48 only
PR190Engine idle speed setpoint.
PR224Turbocharging pressure sensor voltage Vdiag 44 and 48 only
PR228Injector control capacitor voltage
PR364Cylinder no. 1 fuel flow correction
PR365Cylinder no. 4 fuel flow correction
PR381Particle filter downstream temperature
Vdiag 4D, 45 and 49 only PR382Particle filter upstream temperature
PR383Weight of soot in the particle filter
PR391Mileage since particle filter replacement
PR400New EGR valve offset
PR405Cylinder no. 2 fuel flow correction
PR406Cylinder no. 3 fuel flow correction
PR412Mileage at last successful regeneration
Vdiag 4D, 45 and 49 only PR414Particle filter diff* pressure
PR415Time since last regeneration
PR513Mileage counter for level 1 warning light
PR514Mileage counter for level 2 warning light
PR634Air flow request
PR667Turbine upstream temperature
Vdiag 4D, 45 and 49 only PR668Turbine upstream temperature sensor voltage
PR669Particle filter diff* press* sens* voltage
PR670Particle filter upstream temp* sens* voltage
PR671Particle filter downstream temp* sens* voltage
PR672Damper valve position setpoint Vdiag 44 and 48 only
*AC: air conditioning system
*diff: differential*sens: sensor
*temp: temperature*press: pressure
Page 188 of 329
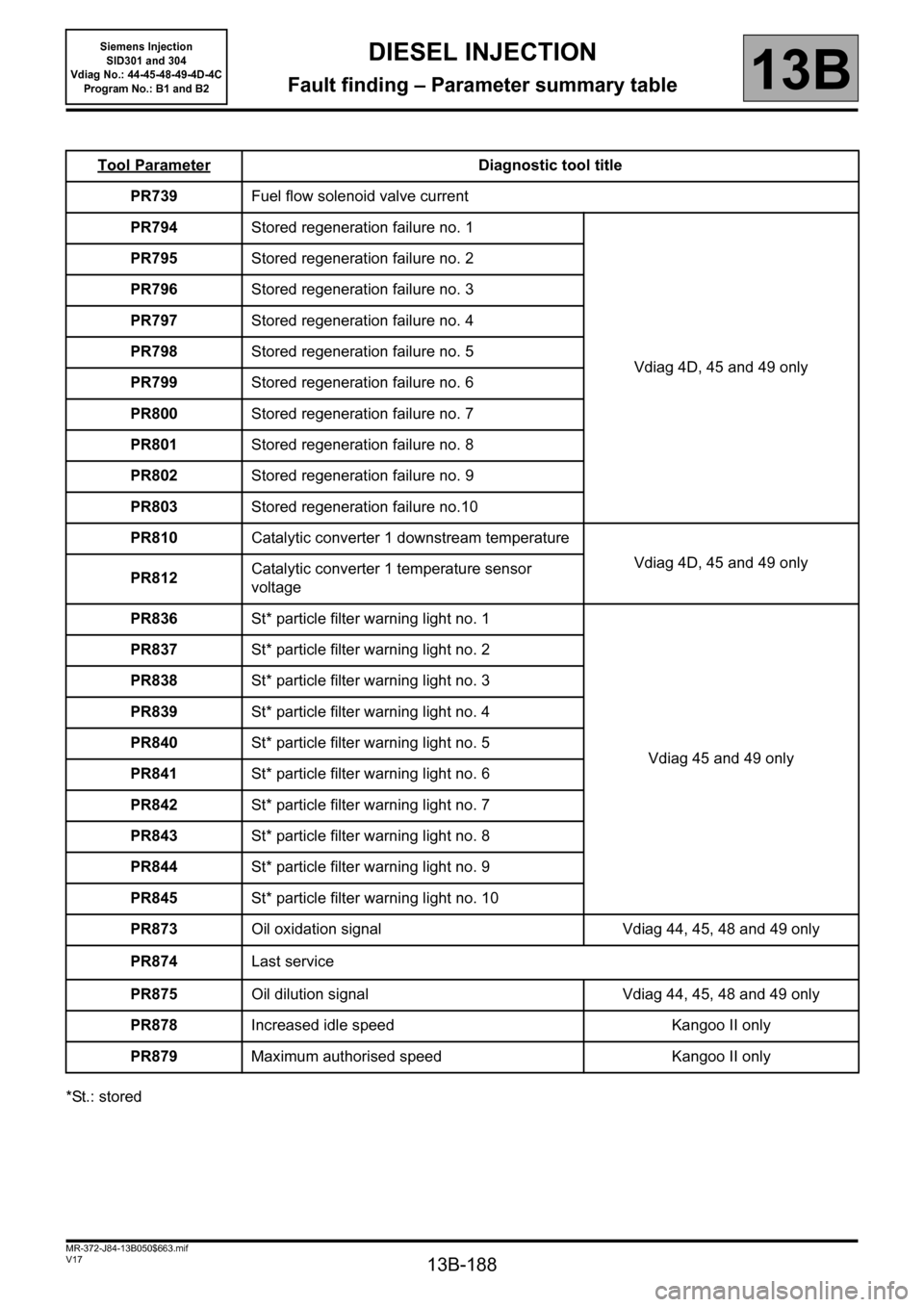
13B-188
MR-372-J84-13B050$663.mif
V17
Siemens Injection
SID301 and 304
Vdiag No.: 44-45-48-49-4D-4C
Program No.: B1 and B2DIESEL INJECTION
Fault finding – Parameter summary table13B
*St.: storedTool Parameter
Diagnostic tool title
PR739Fuel flow solenoid valve current
PR794Stored regeneration failure no. 1
Vdiag 4D, 45 and 49 only PR795Stored regeneration failure no. 2
PR796Stored regeneration failure no. 3
PR797Stored regeneration failure no. 4
PR798Stored regeneration failure no. 5
PR799Stored regeneration failure no. 6
PR800Stored regeneration failure no. 7
PR801Stored regeneration failure no. 8
PR802Stored regeneration failure no. 9
PR803Stored regeneration failure no.10
PR810Catalytic converter 1 downstream temperature
Vdiag 4D, 45 and 49 only
PR812Catalytic converter 1 temperature sensor
voltage
PR836St* particle filter warning light no. 1
Vdiag 45 and 49 only PR837St* particle filter warning light no. 2
PR838St* particle filter warning light no. 3
PR839St* particle filter warning light no. 4
PR840St* particle filter warning light no. 5
PR841St* particle filter warning light no. 6
PR842St* particle filter warning light no. 7
PR843St* particle filter warning light no. 8
PR844St* particle filter warning light no. 9
PR845St* particle filter warning light no. 10
PR873Oil oxidation signal Vdiag 44, 45, 48 and 49 only
PR874Last service
PR875Oil dilution signal Vdiag 44, 45, 48 and 49 only
PR878Increased idle speed Kangoo II only
PR879Maximum authorised speed Kangoo II only
Page 258 of 329
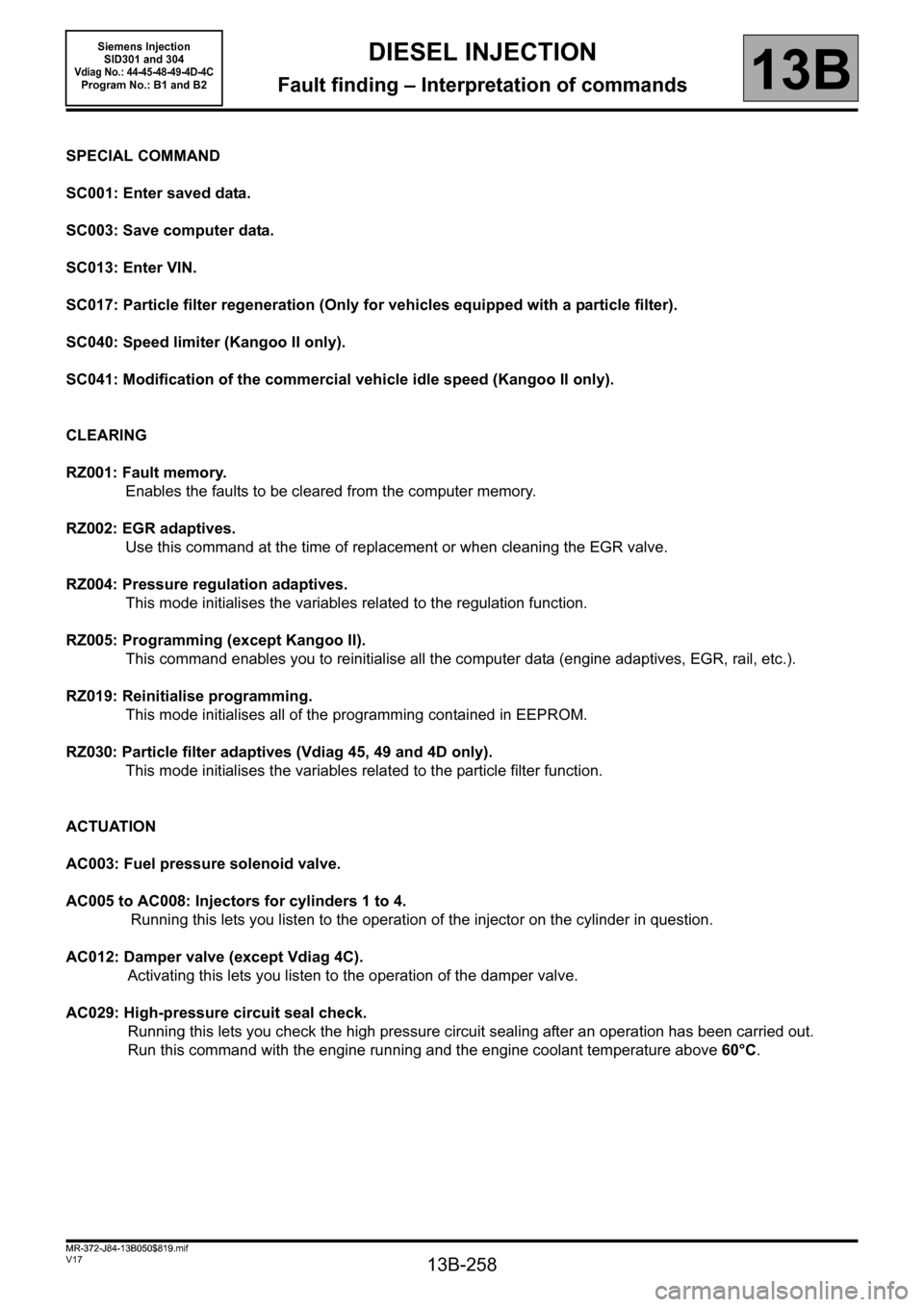
13B-258
MR-372-J84-13B050$819.mif
V17
13B
DIESEL INJECTION
Fault finding – Interpretation of commands
SPECIAL COMMAND
SC001: Enter saved data.
SC003: Save computer data.
SC013: Enter VIN.
SC017: Particle filter regeneration (Only for vehicles equipped with a particle filter).
SC040: Speed limiter (Kangoo II only).
SC041: Modification of the commercial vehicle idle speed (Kangoo II only).
CLEARING
RZ001: Fault memory.
Enables the faults to be cleared from the computer memory.
RZ002: EGR adaptives.
Use this command at the time of replacement or when cleaning the EGR valve.
RZ004: Pressure regulation adaptives.
This mode initialises the variables related to the regulation function.
RZ005: Programming (except Kangoo II).
This command enables you to reinitialise all the computer data (engine adaptives, EGR, rail, etc.).
RZ019: Reinitialise programming.
This mode initialises all of the programming contained in EEPROM.
RZ030: Particle filter adaptives (Vdiag 45, 49 and 4D only).
This mode initialises the variables related to the particle filter function.
ACTUATION
AC003: Fuel pressure solenoid valve.
AC005 to AC008: Injectors for cylinders 1 to 4.
Running this lets you listen to the operation of the injector on the cylinder in question.
AC012: Damper valve (except Vdiag 4C).
Activating this lets you listen to the operation of the damper valve.
AC029: High-pressure circuit seal check.
Running this lets you check the high pressure circuit sealing after an operation has been carried out.
Run this command with the engine running and the engine coolant temperature above 60°C.
MR-372-J84-13B050$819.mif
Siemens Injection
SID301 and 304
Vdiag No.: 44-45-48-49-4D-4CProgram No.: B1 and B2
Page 259 of 329
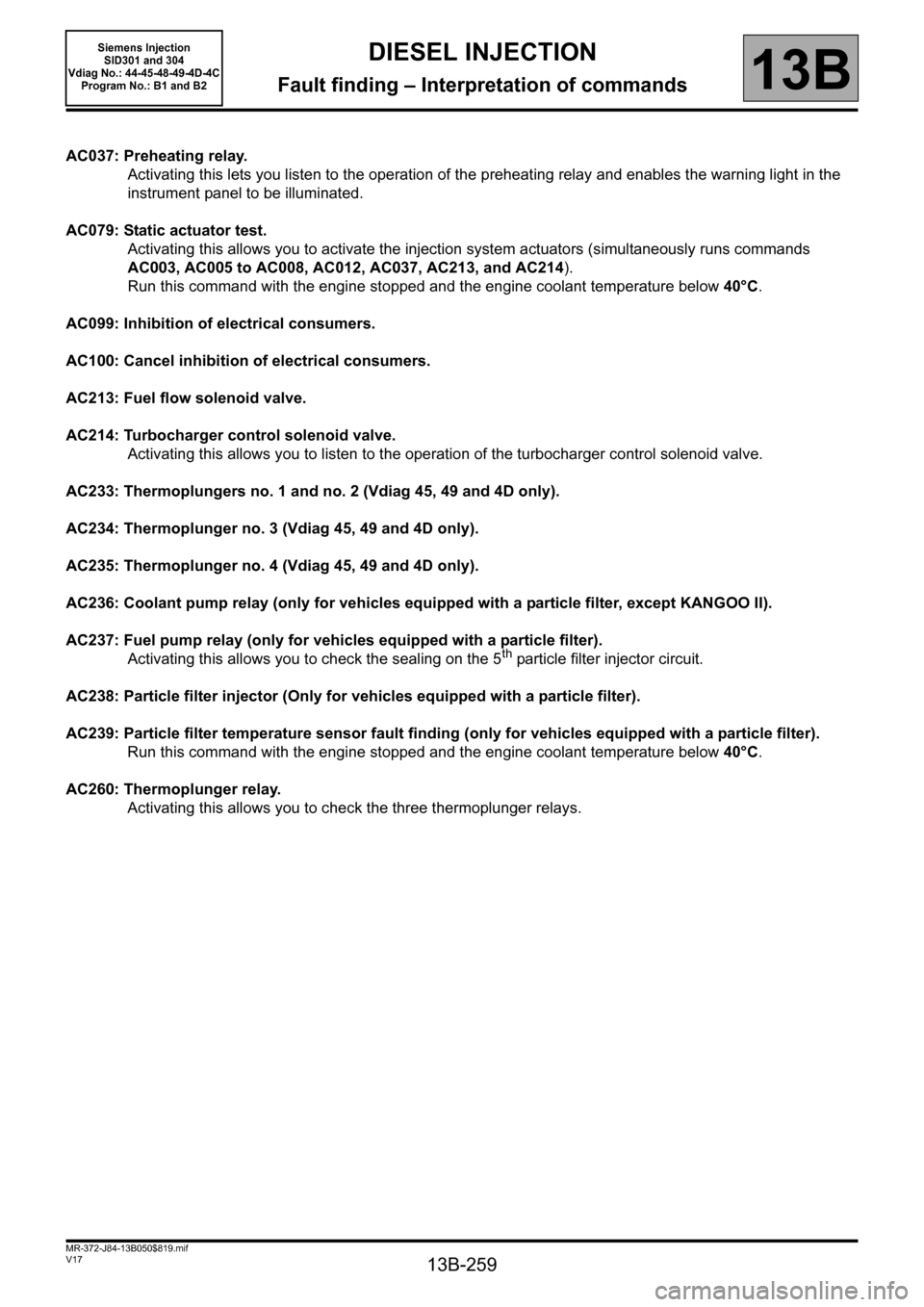
13B-259
MR-372-J84-13B050$819.mif
V17
DIESEL INJECTION
Fault finding – Interpretation of commands
Siemens Injection
SID301 and 304
Vdiag No.: 44-45-48-49-4D-4C
Program No.: B1 and B2
13B
AC037: Preheating relay.
Activating this lets you listen to the operation of the preheating relay and enables the warning light in the
instrument panel to be illuminated.
AC079: Static actuator test.
Activating this allows you to activate the injection system actuators (simultaneously runs commands
AC003, AC005 to AC008, AC012, AC037, AC213, and AC214).
Run this command with the engine stopped and the engine coolant temperature below 40°C.
AC099: Inhibition of electrical consumers.
AC100: Cancel inhibition of electrical consumers.
AC213: Fuel flow solenoid valve.
AC214: Turbocharger control solenoid valve.
Activating this allows you to listen to the operation of the turbocharger control solenoid valve.
AC233: Thermoplungers no. 1 and no. 2 (Vdiag 45, 49 and 4D only).
AC234: Thermoplunger no. 3 (Vdiag 45, 49 and 4D only).
AC235: Thermoplunger no. 4 (Vdiag 45, 49 and 4D only).
AC236: Coolant pump relay (only for vehicles equipped with a particle filter, except KANGOO II).
AC237: Fuel pump relay (only for vehicles equipped with a particle filter).
Activating this allows you to check the sealing on the 5
th particle filter injector circuit.
AC238: Particle filter injector (Only for vehicles equipped with a particle filter).
AC239: Particle filter temperature sensor fault finding (only for vehicles equipped with a particle filter).
Run this command with the engine stopped and the engine coolant temperature below 40°C.
AC260: Thermoplunger relay.
Activating this allows you to check the three thermoplunger relays.
Page 262 of 329
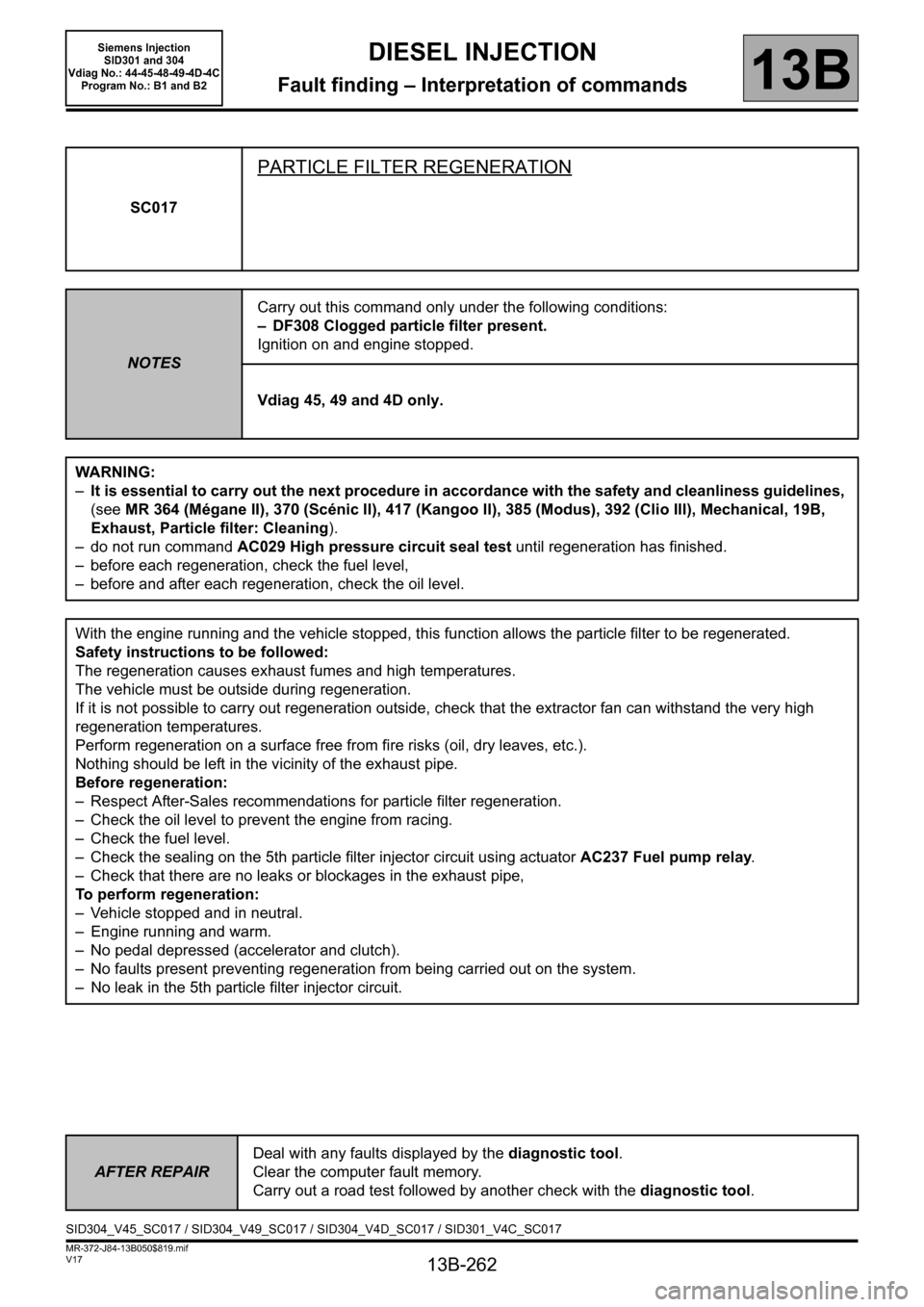
13B-262
MR-372-J84-13B050$819.mif
V17
DIESEL INJECTION
Fault finding – Interpretation of commands
Siemens Injection
SID301 and 304
Vdiag No.: 44-45-48-49-4D-4C
Program No.: B1 and B2
13B
SC017
PARTICLE FILTER REGENERATION
NOTESCarry out this command only under the following conditions:
– DF308 Clogged particle filter present.
Ignition on and engine stopped.
Vdiag 45, 49 and 4D only.
WARNING:
–It is essential to carry out the next procedure in accordance with the safety and cleanliness guidelines,
(see MR 364 (Mégane II), 370 (Scénic II), 417 (Kangoo II), 385 (Modus), 392 (Clio III), Mechanical, 19B,
Exhaust, Particle filter: Cleaning).
– do not run command AC029 High pressure circuit seal test until regeneration has finished.
– before each regeneration, check the fuel level,
– before and after each regeneration, check the oil level.
With the engine running and the vehicle stopped, this function allows the particle filter to be regenerated.
Safety instructions to be followed:
The regeneration causes exhaust fumes and high temperatures.
The vehicle must be outside during regeneration.
If it is not possible to carry out regeneration outside, check that the extractor fan can withstand the very high
regeneration temperatures.
Perform regeneration on a surface free from fire risks (oil, dry leaves, etc.).
Nothing should be left in the vicinity of the exhaust pipe.
Before regeneration:
– Respect After-Sales recommendations for particle filter regeneration.
– Check the oil level to prevent the engine from racing.
– Check the fuel level.
– Check the sealing on the 5th particle filter injector circuit using actuator AC237 Fuel pump relay.
– Check that there are no leaks or blockages in the exhaust pipe,
To perform regeneration:
– Vehicle stopped and in neutral.
– Engine running and warm.
– No pedal depressed (accelerator and clutch).
– No faults present preventing regeneration from being carried out on the system.
– No leak in the 5th particle filter injector circuit.
AFTER REPAIRDeal with any faults displayed by the diagnostic tool.
Clear the computer fault memory.
Carry out a road test followed by another check with the diagnostic tool.
SID304_V45_SC017 / SID304_V49_SC017 / SID304_V4D_SC017 / SID301_V4C_SC017
Page 278 of 329
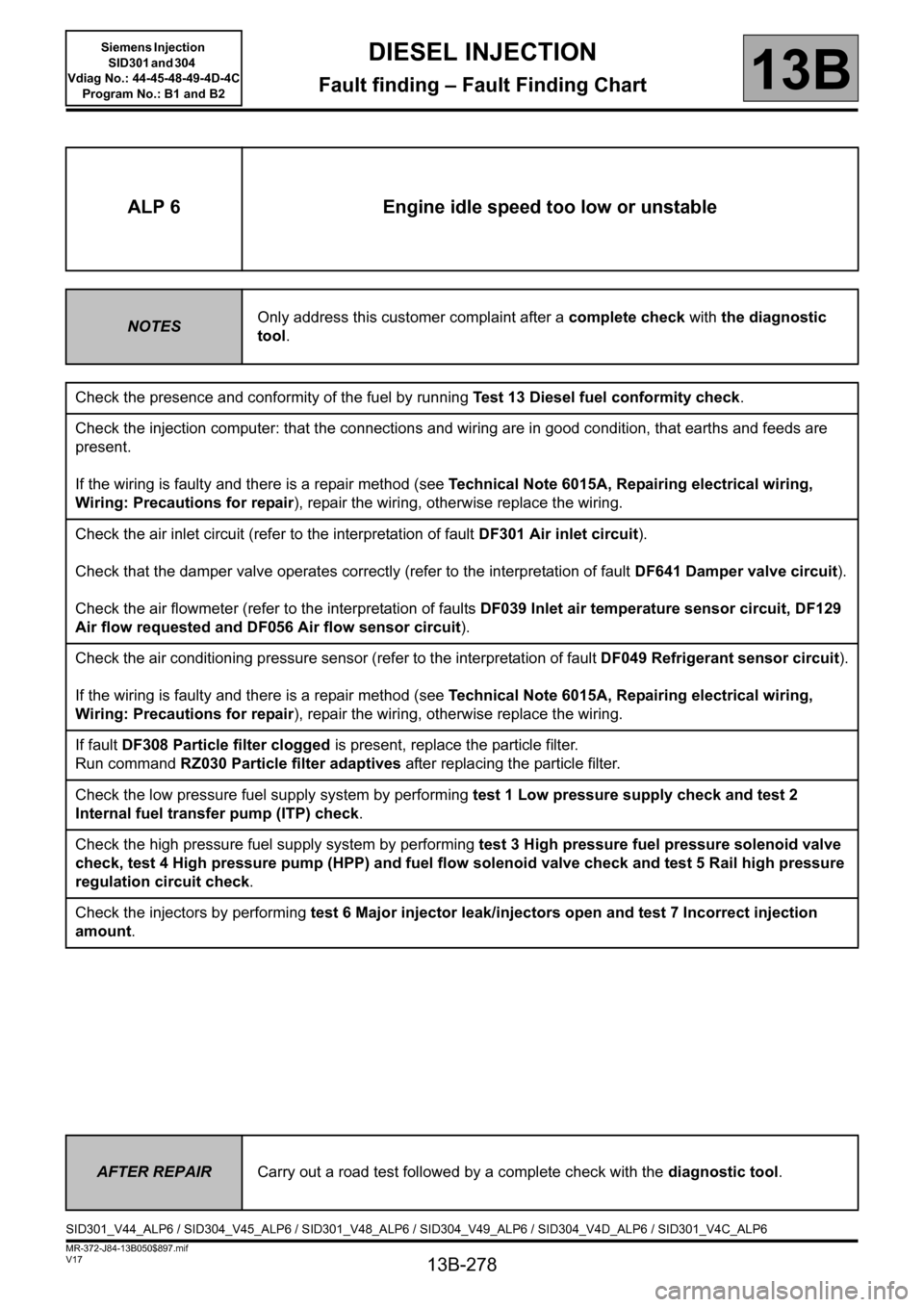
13B-278
MR-372-J84-13B050$897.mif
V17
DIESEL INJECTION
Fault finding – Fault Finding Chart
Siemens Injection
SID301 and 304
Vdiag No.: 44-45-48-49-4D-4C
Program No.: B1 and B2
13B
ALP 6 Engine idle speed too low or unstable
NOTESOnly address this customer complaint after a complete check with the diagnostic
tool.
Check the presence and conformity of the fuel by running Test 13 Diesel fuel conformity check.
Check the injection computer: that the connections and wiring are in good condition, that earths and feeds are
present.
If the wiring is faulty and there is a repair method (see Technical Note 6015A, Repairing electrical wiring,
Wiring: Precautions for repair), repair the wiring, otherwise replace the wiring.
Check the air inlet circuit (refer to the interpretation of fault DF301 Air inlet circuit).
Check that the damper valve operates correctly (refer to the interpretation of fault DF641 Damper valve circuit).
Check the air flowmeter (refer to the interpretation of faults DF039 Inlet air temperature sensor circuit, DF129
Air flow requested and DF056 Air flow sensor circuit).
Check the air conditioning pressure sensor (refer to the interpretation of fault DF049 Refrigerant sensor circuit).
If the wiring is faulty and there is a repair method (see Technical Note 6015A, Repairing electrical wiring,
Wiring: Precautions for repair), repair the wiring, otherwise replace the wiring.
If fault DF308 Particle filter clogged is present, replace the particle filter.
Run command RZ030 Particle filter adaptives after replacing the particle filter.
Check the low pressure fuel supply system by performing test 1 Low pressure supply check and test 2
Internal fuel transfer pump (ITP) check.
Check the high pressure fuel supply system by performing test 3 High pressure fuel pressure solenoid valve
check, test 4 High pressure pump (HPP) and fuel flow solenoid valve check and test 5 Rail high pressure
regulation circuit check.
Check the injectors by performing test 6 Major injector leak/injectors open and test 7 Incorrect injection
amount.
AFTER REPAIRCarry out a road test followed by a complete check with the diagnostic tool.
SID301_V44_ALP6 / SID304_V45_ALP6 / SID301_V48_ALP6 / SID304_V49_ALP6 / SID304_V4D_ALP6 / SID301_V4C_ALP6
Page 284 of 329
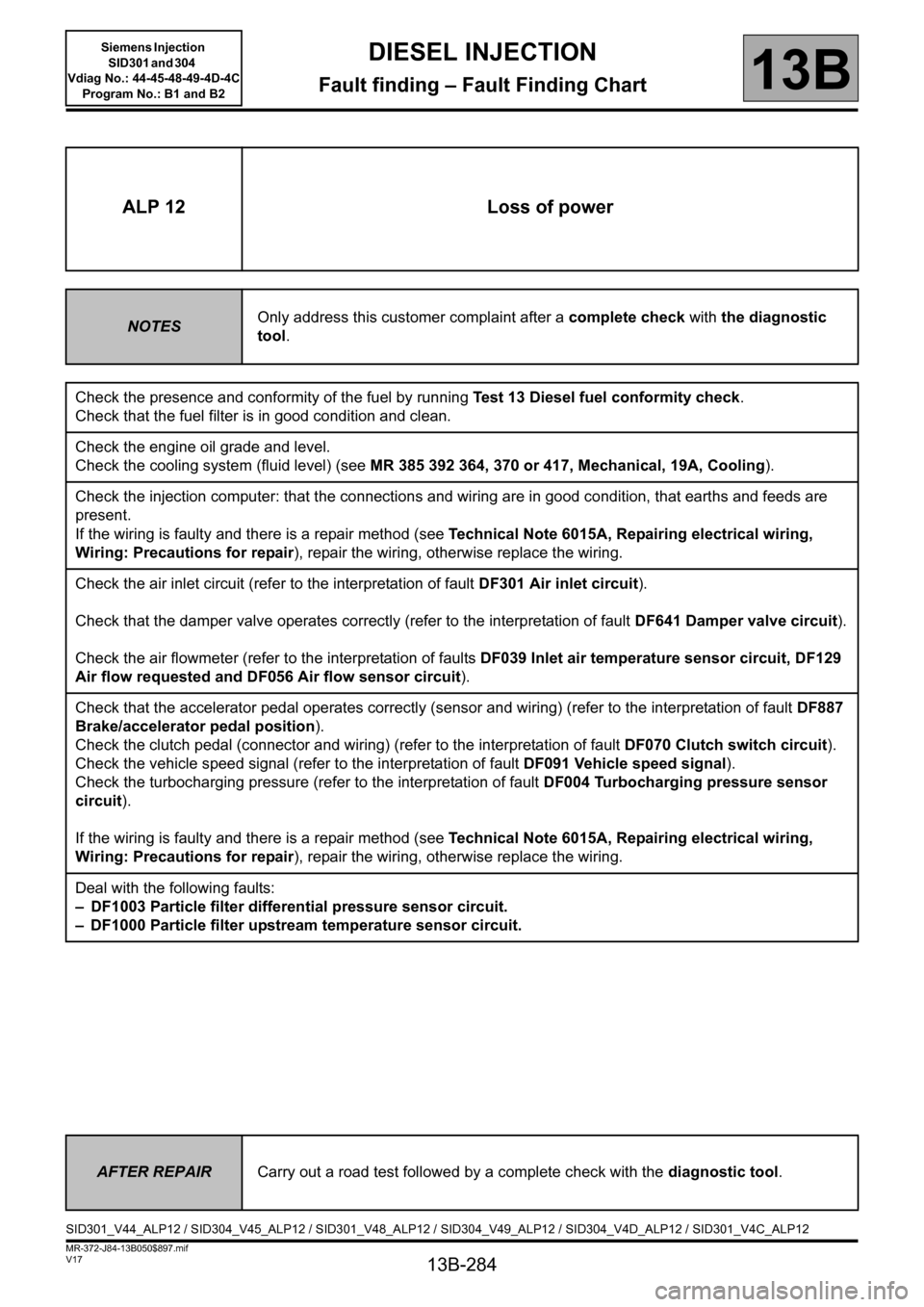
13B-284
MR-372-J84-13B050$897.mif
V17
DIESEL INJECTION
Fault finding – Fault Finding Chart
Siemens Injection
SID301 and 304
Vdiag No.: 44-45-48-49-4D-4C
Program No.: B1 and B2
13B
ALP 12 Loss of power
NOTESOnly address this customer complaint after a complete check with the diagnostic
tool.
Check the presence and conformity of the fuel by running Test 13 Diesel fuel conformity check.
Check that the fuel filter is in good condition and clean.
Check the engine oil grade and level.
Check the cooling system (fluid level) (see MR 385 392 364, 370 or 417, Mechanical, 19A, Cooling).
Check the injection computer: that the connections and wiring are in good condition, that earths and feeds are
present.
If the wiring is faulty and there is a repair method (see Technical Note 6015A, Repairing electrical wiring,
Wiring: Precautions for repair), repair the wiring, otherwise replace the wiring.
Check the air inlet circuit (refer to the interpretation of fault DF301 Air inlet circuit).
Check that the damper valve operates correctly (refer to the interpretation of fault DF641 Damper valve circuit).
Check the air flowmeter (refer to the interpretation of faults DF039 Inlet air temperature sensor circuit, DF129
Air flow requested and DF056 Air flow sensor circuit).
Check that the accelerator pedal operates correctly (sensor and wiring) (refer to the interpretation of fault DF887
Brake/accelerator pedal position).
Check the clutch pedal (connector and wiring) (refer to the interpretation of fault DF070 Clutch switch circuit).
Check the vehicle speed signal (refer to the interpretation of fault DF091 Vehicle speed signal).
Check the turbocharging pressure (refer to the interpretation of fault DF004 Turbocharging pressure sensor
circuit).
If the wiring is faulty and there is a repair method (see Technical Note 6015A, Repairing electrical wiring,
Wiring: Precautions for repair), repair the wiring, otherwise replace the wiring.
Deal with the following faults:
– DF1003 Particle filter differential pressure sensor circuit.
– DF1000 Particle filter upstream temperature sensor circuit.
AFTER REPAIRCarry out a road test followed by a complete check with the diagnostic tool.
SID301_V44_ALP12 / SID304_V45_ALP12 / SID301_V48_ALP12 / SID304_V49_ALP12 / SID304_V4D_ALP12 / SID301_V4C_ALP12
Page 293 of 329
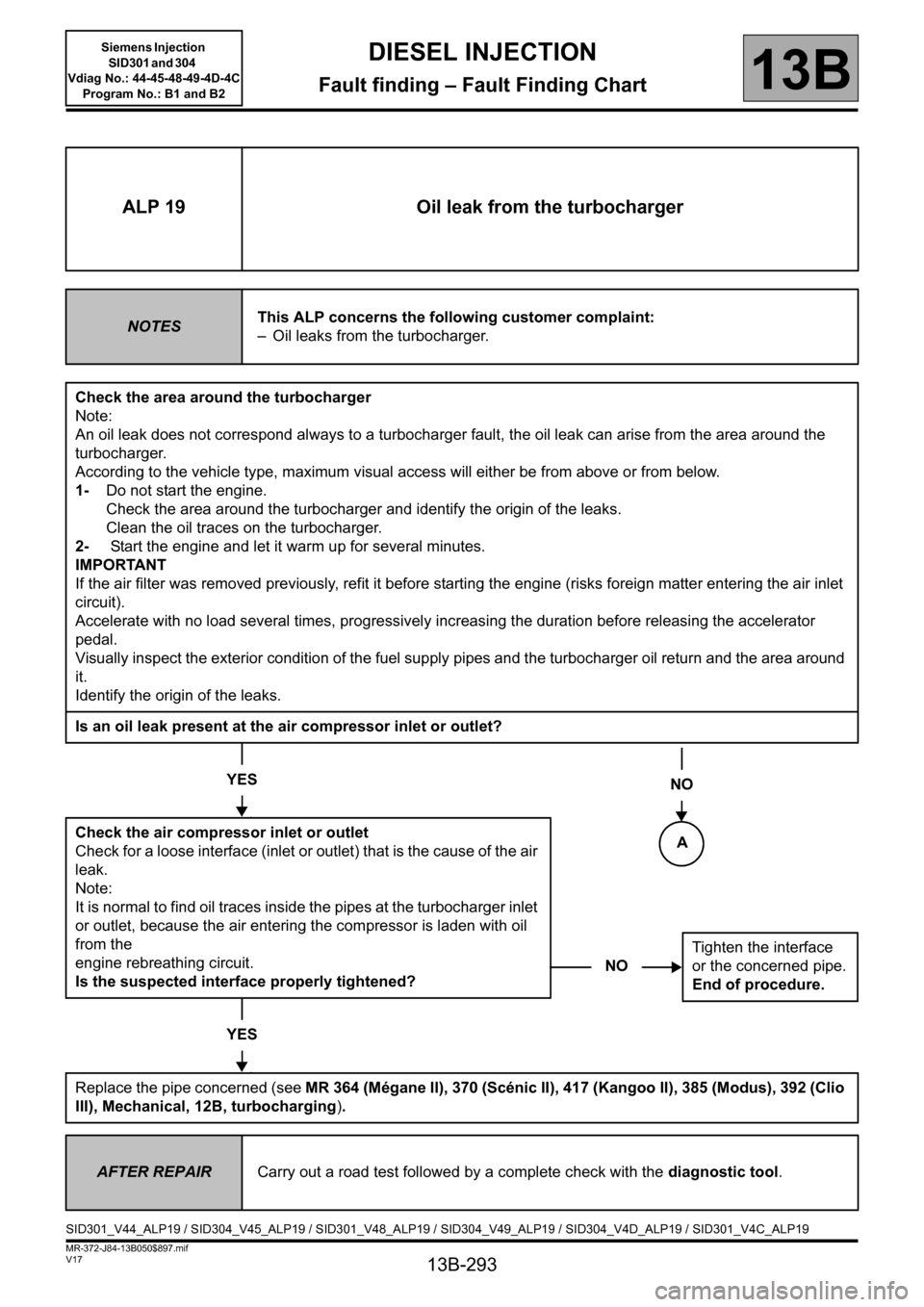
13B-293
MR-372-J84-13B050$897.mif
V17
Siemens Injection
SID301 and 304
Vdiag No.: 44-45-48-49-4D-4C
Program No.: B1 and B2DIESEL INJECTION
Fault finding – Fault Finding Chart13B
NOTighten the interface
or the concerned pipe.
End of procedure.
ALP 19 Oil leak from the turbocharger
NOTESThis ALP concerns the following customer complaint:
– Oil leaks from the turbocharger.
Check the area around the turbocharger
Note:
An oil leak does not correspond always to a turbocharger fault, the oil leak can arise from the area around the
turbocharger.
According to the vehicle type, maximum visual access will either be from above or from below.
1-Do not start the engine.
Check the area around the turbocharger and identify the origin of the leaks.
Clean the oil traces on the turbocharger.
2- Start the engine and let it warm up for several minutes.
IMPORTANT
If the air filter was removed previously, refit it before starting the engine (risks foreign matter entering the air inlet
circuit).
Accelerate with no load several times, progressively increasing the duration before releasing the accelerator
pedal.
Visually inspect the exterior condition of the fuel supply pipes and the turbocharger oil return and the area around
it.
Identify the origin of the leaks.
Is an oil leak present at the air compressor inlet or outlet?
YES
Check the air compressor inlet or outlet
Check for a loose interface (inlet or outlet) that is the cause of the air
leak.
Note:
It is normal to find oil traces inside the pipes at the turbocharger inlet
or outlet, because the air entering the compressor is laden with oil
from the
engine rebreathing circuit.
Is the suspected interface properly tightened?
YES
Replace the pipe concerned (see MR 364 (Mégane II), 370 (Scénic II), 417 (Kangoo II), 385 (Modus), 392 (Clio
III), Mechanical, 12B, turbocharging).
NO
AFTER REPAIRCarry out a road test followed by a complete check with the diagnostic tool.
SID301_V44_ALP19 / SID304_V45_ALP19 / SID301_V48_ALP19 / SID304_V49_ALP19 / SID304_V4D_ALP19 / SID301_V4C_ALP19
A
Page 296 of 329
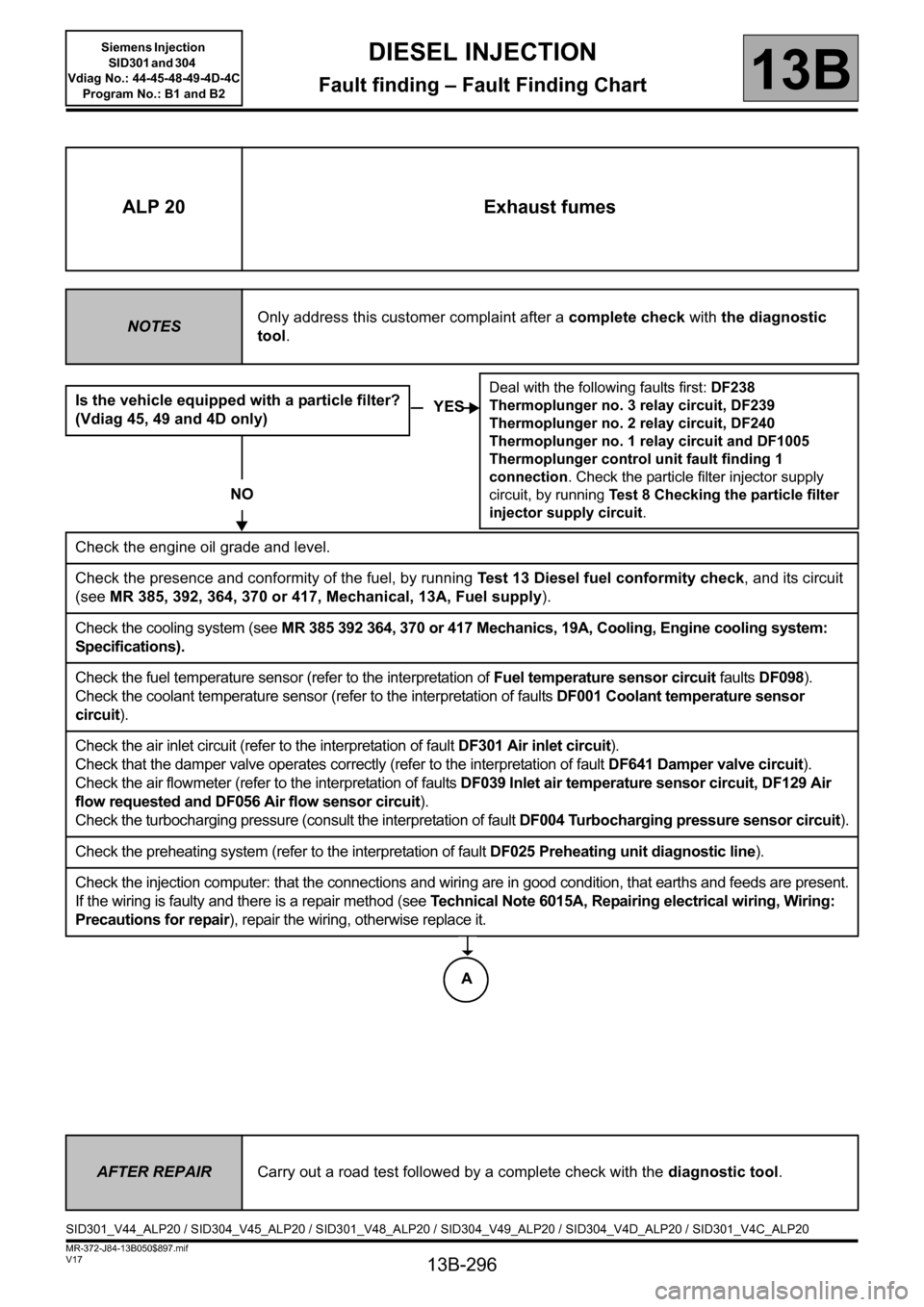
13B-296
MR-372-J84-13B050$897.mif
V17
Siemens Injection
SID301 and 304
Vdiag No.: 44-45-48-49-4D-4C
Program No.: B1 and B2DIESEL INJECTION
Fault finding – Fault Finding Chart13B
ALP 20 Exhaust fumes
NOTESOnly address this customer complaint after a complete check with the diagnostic
tool.
Is the vehicle equipped with a particle filter?
(Vdiag 45, 49 and 4D only)
NO
Check the engine oil grade and level.
Check the presence and conformity of the fuel, by running Test 13 Diesel fuel conformity check, and its circuit
(see MR 385, 392, 364, 370 or 417, Mechanical, 13A, Fuel supply).
Check the cooling system (see MR 385 392 364, 370 or 417 Mechanics, 19A, Cooling, Engine cooling system:
Specifications).
Check the fuel temperature sensor (refer to the interpretation of Fuel temperature sensor circuit faults DF098).
Check the coolant temperature sensor (refer to the interpretation of faults DF001 Coolant temperature sensor
circuit).
Check the air inlet circuit (refer to the interpretation of fault DF301 Air inlet circuit).
Check that the damper valve operates correctly (refer to the interpretation of fault DF641 Damper valve circuit).
Check the air flowmeter (refer to the interpretation of faults DF039 Inlet air temperature sensor circuit, DF129 Air
flow requested and DF056 Air flow sensor circuit).
Check the turbocharging pressure (consult the interpretation of fault DF004 Turbocharging pressure sensor circuit).
Check the preheating system (refer to the interpretation of fault DF025 Preheating unit diagnostic line).
Check the injection computer: that the connections and wiring are in good condition, that earths and feeds are present.
If the wiring is faulty and there is a repair method (see Technical Note 6015A, Repairing electrical wiring, Wiring:
Precautions for repair), repair the wiring, otherwise replace it.
YES
Deal with the following faults first: DF238
Thermoplunger no. 3 relay circuit, DF239
Thermoplunger no. 2 relay circuit, DF240
Thermoplunger no. 1 relay circuit and DF1005
Thermoplunger control unit fault finding 1
connection. Check the particle filter injector supply
circuit, by running Test 8 Checking the particle filter
injector supply circuit.
AFTER REPAIRCarry out a road test followed by a complete check with the diagnostic tool.
SID301_V44_ALP20 / SID304_V45_ALP20 / SID301_V48_ALP20 / SID304_V49_ALP20 / SID304_V4D_ALP20 / SID301_V4C_ALP20
A
Page 297 of 329
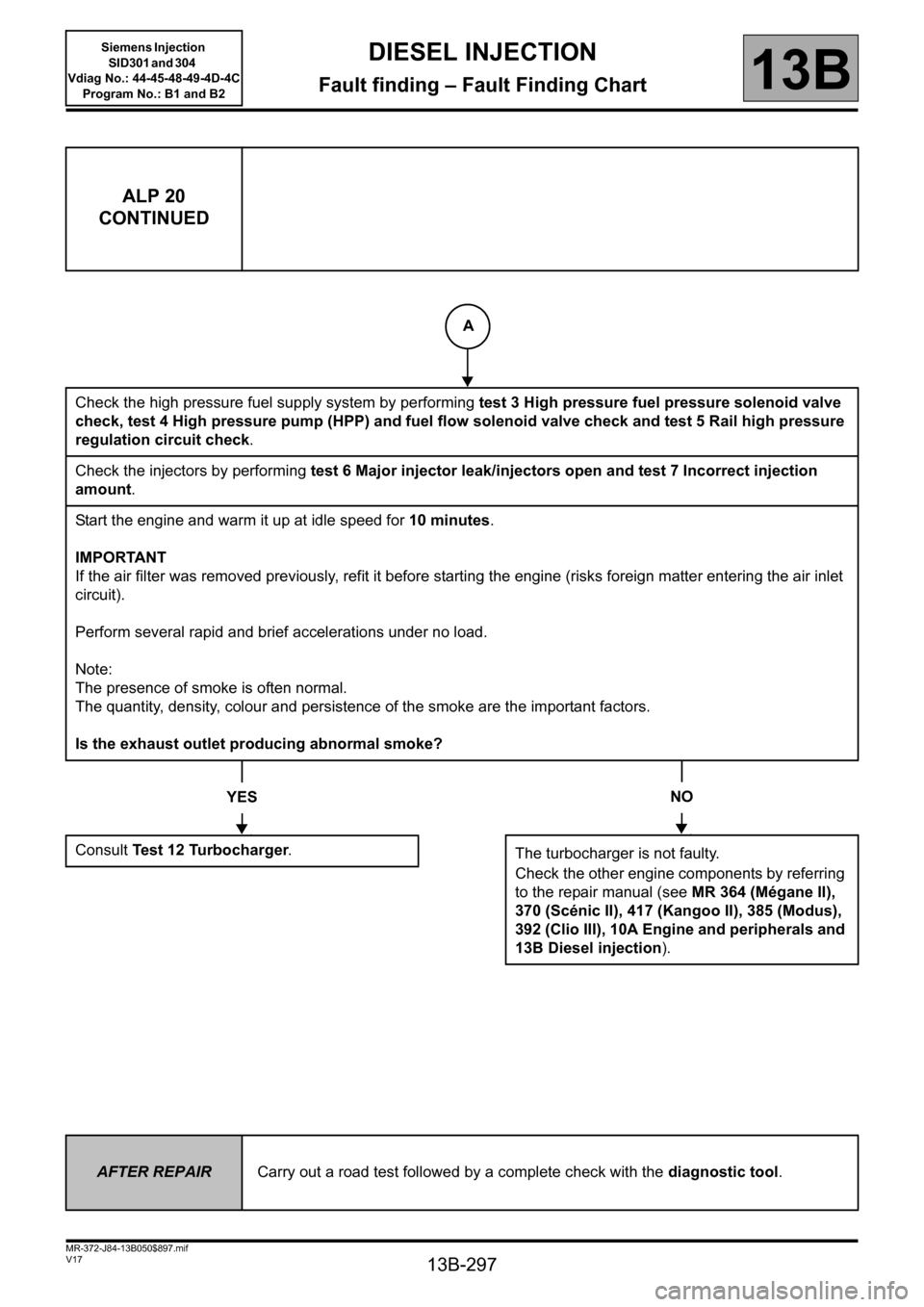
13B-297
MR-372-J84-13B050$897.mif
V17
Siemens Injection
SID301 and 304
Vdiag No.: 44-45-48-49-4D-4C
Program No.: B1 and B2DIESEL INJECTION
Fault finding – Fault Finding Chart13B
ALP 20
CONTINUED
Check the high pressure fuel supply system by performing test 3 High pressure fuel pressure solenoid valve
check, test 4 High pressure pump (HPP) and fuel flow solenoid valve check and test 5 Rail high pressure
regulation circuit check.
Check the injectors by performing test 6 Major injector leak/injectors open and test 7 Incorrect injection
amount.
Start the engine and warm it up at idle speed for 10 minutes.
IMPORTANT
If the air filter was removed previously, refit it before starting the engine (risks foreign matter entering the air inlet
circuit).
Perform several rapid and brief accelerations under no load.
Note:
The presence of smoke is often normal.
The quantity, density, colour and persistence of the smoke are the important factors.
Is the exhaust outlet producing abnormal smoke?
YES
Consult Te s t 1 2 Tu r b o c h a r g e r.
NO
The turbocharger is not faulty.
Check the other engine components by referring
to the repair manual (see MR 364 (Mégane II),
370 (Scénic II), 417 (Kangoo II), 385 (Modus),
392 (Clio III), 10A Engine and peripherals and
13B Diesel injection).
AFTER REPAIRCarry out a road test followed by a complete check with the diagnostic tool.
A