engine RENAULT SCENIC 2011 J95 / 3.G Engine And Peripherals Workshop Manual
[x] Cancel search | Manufacturer: RENAULT, Model Year: 2011, Model line: SCENIC, Model: RENAULT SCENIC 2011 J95 / 3.GPages: 198, PDF Size: 0.85 MB
Page 1 of 198
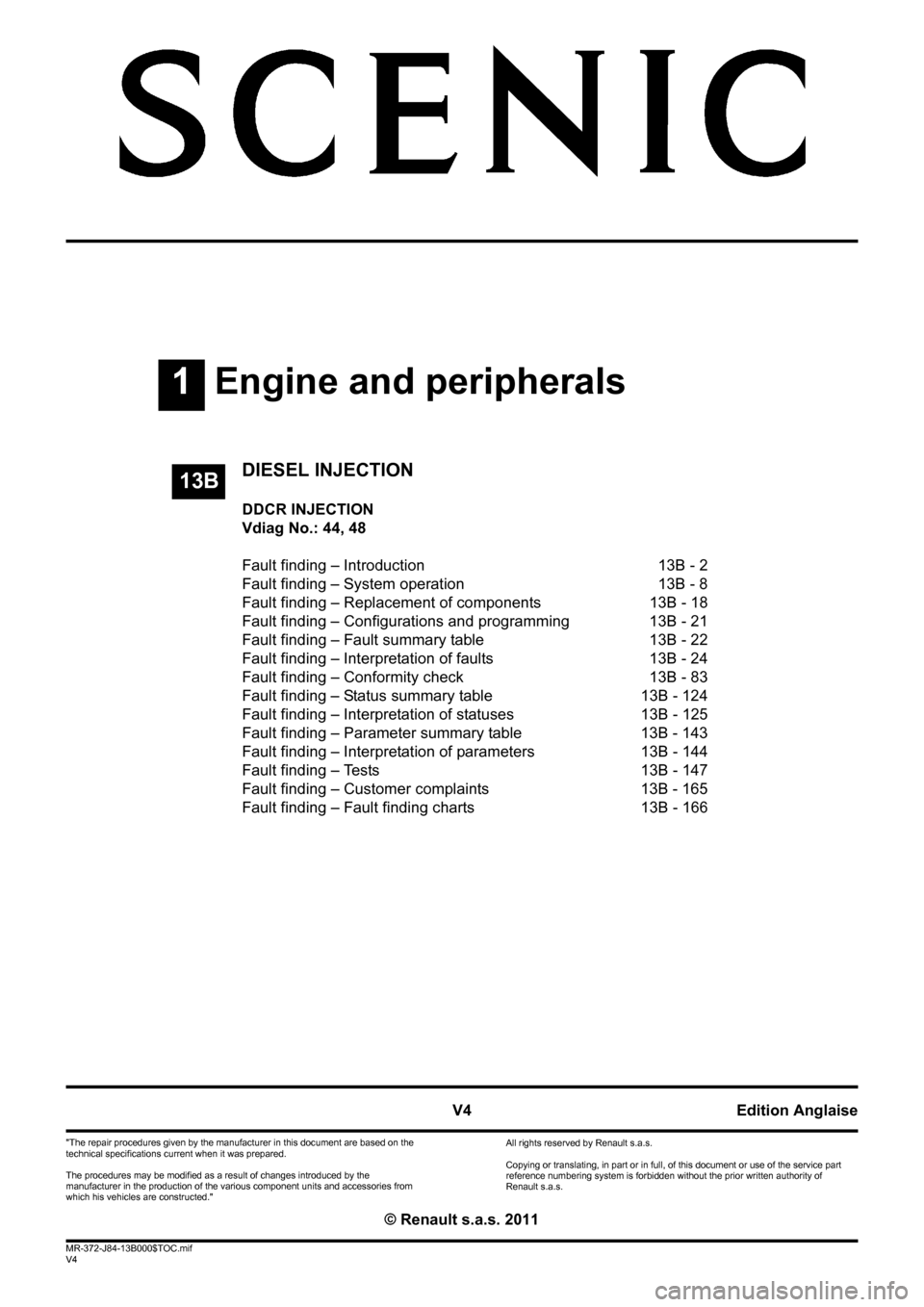
1Engine and peripherals
V4 MR-372-J84-13B000$TOC.mif
V4
13B
"The repair procedures given by the manufacturer in this document are based on the
technical specifications current when it was prepared.
The procedures may be modified as a result of changes introduced by the
manufacturer in the production of the various component units and accessories from
which his vehicles are constructed."
V4
All rights reserved by Renault s.a.s.
Edition Anglaise
Copying or translating, in part or in full, of this document or use of the service part
reference numbering system is forbidden without the prior written authority of
Renault s.a.s.
© Renault s.a.s. 2011
DIESEL INJECTION
DDCR INJECTION
Vdiag No.: 44, 48
Fault finding – Introduction 13B - 2
Fault finding – System operation 13B - 8
Fault finding – Replacement of components 13B - 18
Fault finding – Configurations and programming 13B - 21
Fault finding – Fault summary table 13B - 22
Fault finding – Interpretation of faults 13B - 24
Fault finding – Conformity check 13B - 83
Fault finding – Status summary table 13B - 124
Fault finding – Interpretation of statuses 13B - 125
Fault finding – Parameter summary table 13B - 143
Fault finding – Interpretation of parameters 13B - 144
Fault finding – Tests 13B - 147
Fault finding – Customer complaints 13B - 165
Fault finding – Fault finding charts 13B - 166
Page 2 of 198
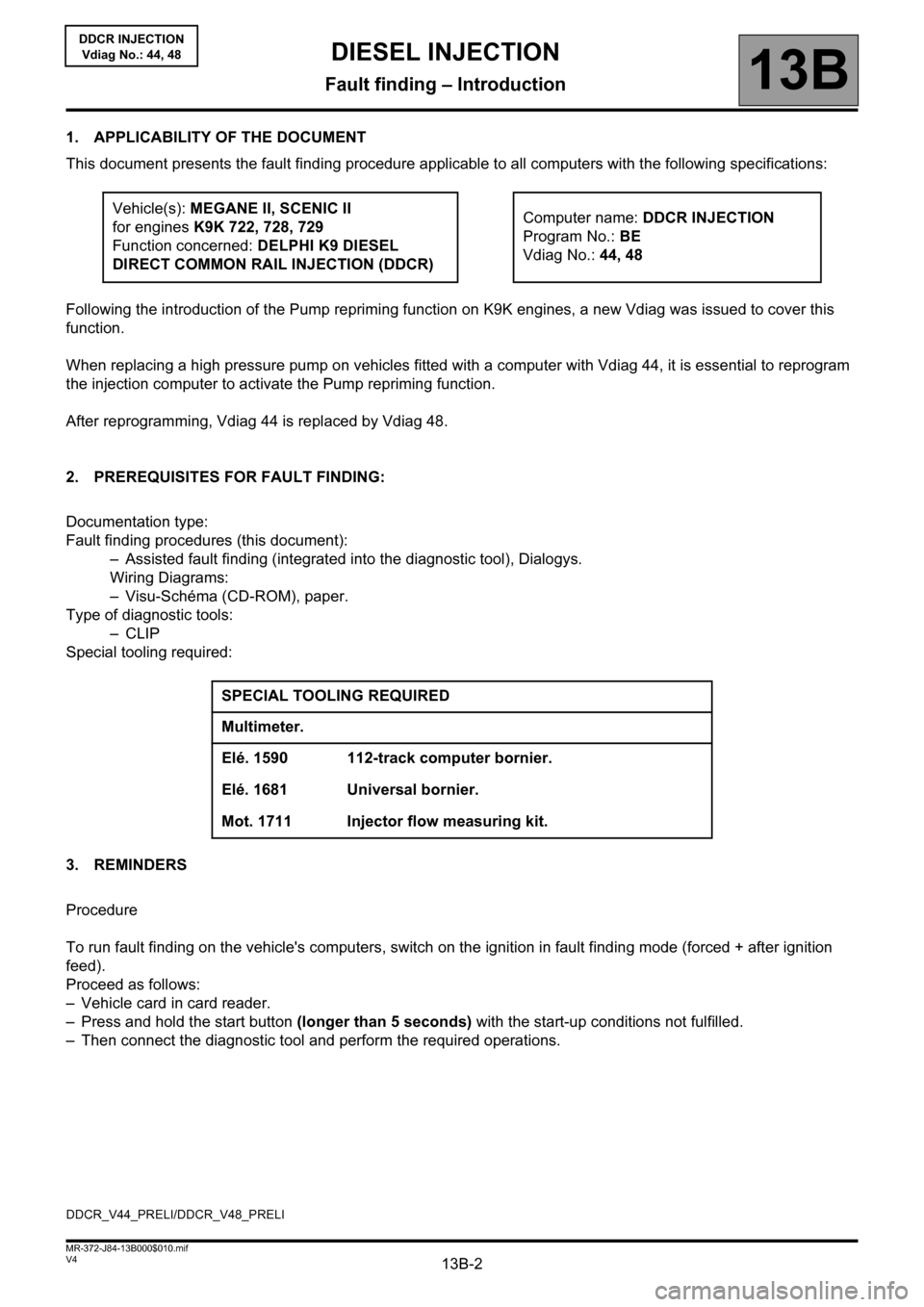
13B-2V4 MR-372-J84-13B000$010.mif
13B
DDCR INJECTION
Vdiag No.: 44, 48
1. APPLICABILITY OF THE DOCUMENT
This document presents the fault finding procedure applicable to all computers with the following specifications:
Following the introduction of the Pump repriming function on K9K engines, a new Vdiag was issued to cover this
function.
When replacing a high pressure pump on vehicles fitted with a computer with Vdiag 44, it is essential to reprogram
the injection computer to activate the Pump repriming function.
After reprogramming, Vdiag 44 is replaced by Vdiag 48.
2. PREREQUISITES FOR FAULT FINDING:
Documentation type:
Fault finding procedures (this document):
– Assisted fault finding (integrated into the diagnostic tool), Dialogys.
Wiring Diagrams:
– Visu-Schéma (CD-ROM), paper.
Type of diagnostic tools:
–CLIP
Special tooling required:
3. REMINDERS
Procedure
To run fault finding on the vehicle's computers, switch on the ignition in fault finding mode (forced + after ignition
feed).
Proceed as follows:
– Vehicle card in card reader.
– Press and hold the start button (longer than 5 seconds) with the start-up conditions not fulfilled.
– Then connect the diagnostic tool and perform the required operations.Vehicle(s): MEGANE II, SCENIC II
for engines K9K 722, 728, 729
Function concerned: DELPHI K9 DIESEL
DIRECT COMMON RAIL INJECTION (DDCR)Computer name: DDCR INJECTION
Program No.: BE
Vdiag No.: 44, 48
SPECIAL TOOLING REQUIRED
Multimeter.
Elé. 1590 112-track computer bornier.
Elé. 1681 Universal bornier.
Mot. 1711 Injector flow measuring kit.
DDCR_V44_PRELI/DDCR_V48_PRELI
DIESEL INJECTION
Fault finding – Introduction
Page 6 of 198
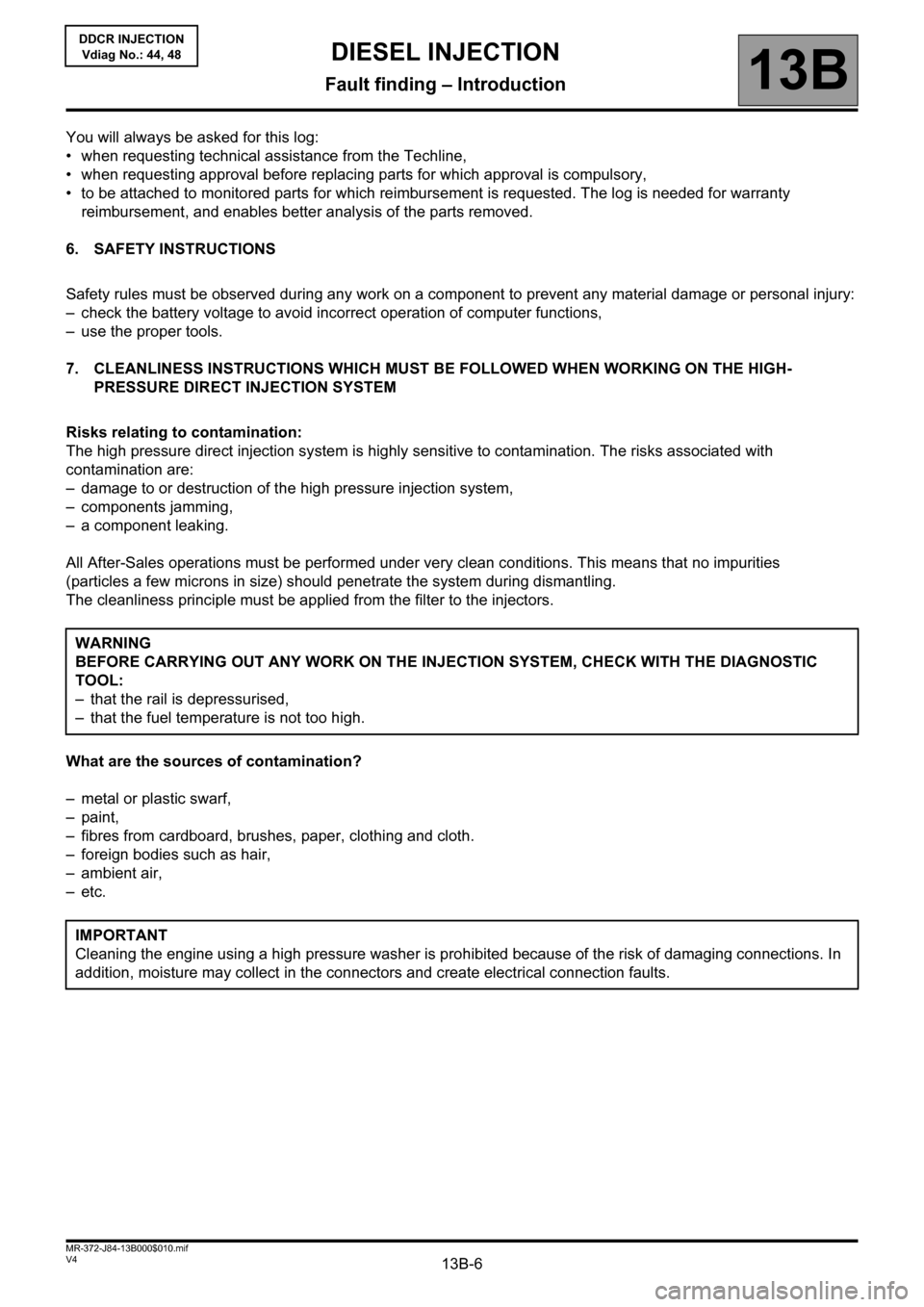
13B-6V4 MR-372-J84-13B000$010.mif
DIESEL INJECTION
Fault finding – Introduction13B
DDCR INJECTION
Vdiag No.: 44, 48
You will always be asked for this log:
• when requesting technical assistance from the Techline,
• when requesting approval before replacing parts for which approval is compulsory,
• to be attached to monitored parts for which reimbursement is requested. The log is needed for warranty
reimbursement, and enables better analysis of the parts removed.
6. SAFETY INSTRUCTIONS
Safety rules must be observed during any work on a component to prevent any material damage or personal injury:
– check the battery voltage to avoid incorrect operation of computer functions,
– use the proper tools.
7. CLEANLINESS INSTRUCTIONS WHICH MUST BE FOLLOWED WHEN WORKING ON THE HIGH-
PRESSURE DIRECT INJECTION SYSTEM
Risks relating to contamination:
The high pressure direct injection system is highly sensitive to contamination. The risks associated with
contamination are:
– damage to or destruction of the high pressure injection system,
– components jamming,
– a component leaking.
All After-Sales operations must be performed under very clean conditions. This means that no impurities
(particles a few microns in size) should penetrate the system during dismantling.
The cleanliness principle must be applied from the filter to the injectors.
What are the sources of contamination?
– metal or plastic swarf,
– paint,
– fibres from cardboard, brushes, paper, clothing and cloth.
– foreign bodies such as hair,
– ambient air,
–etc.WARNING
BEFORE CARRYING OUT ANY WORK ON THE INJECTION SYSTEM, CHECK WITH THE DIAGNOSTIC
TOOL:
– that the rail is depressurised,
– that the fuel temperature is not too high.
IMPORTANT
Cleaning the engine using a high pressure washer is prohibited because of the risk of damaging connections. In
addition, moisture may collect in the connectors and create electrical connection faults.
Page 8 of 198
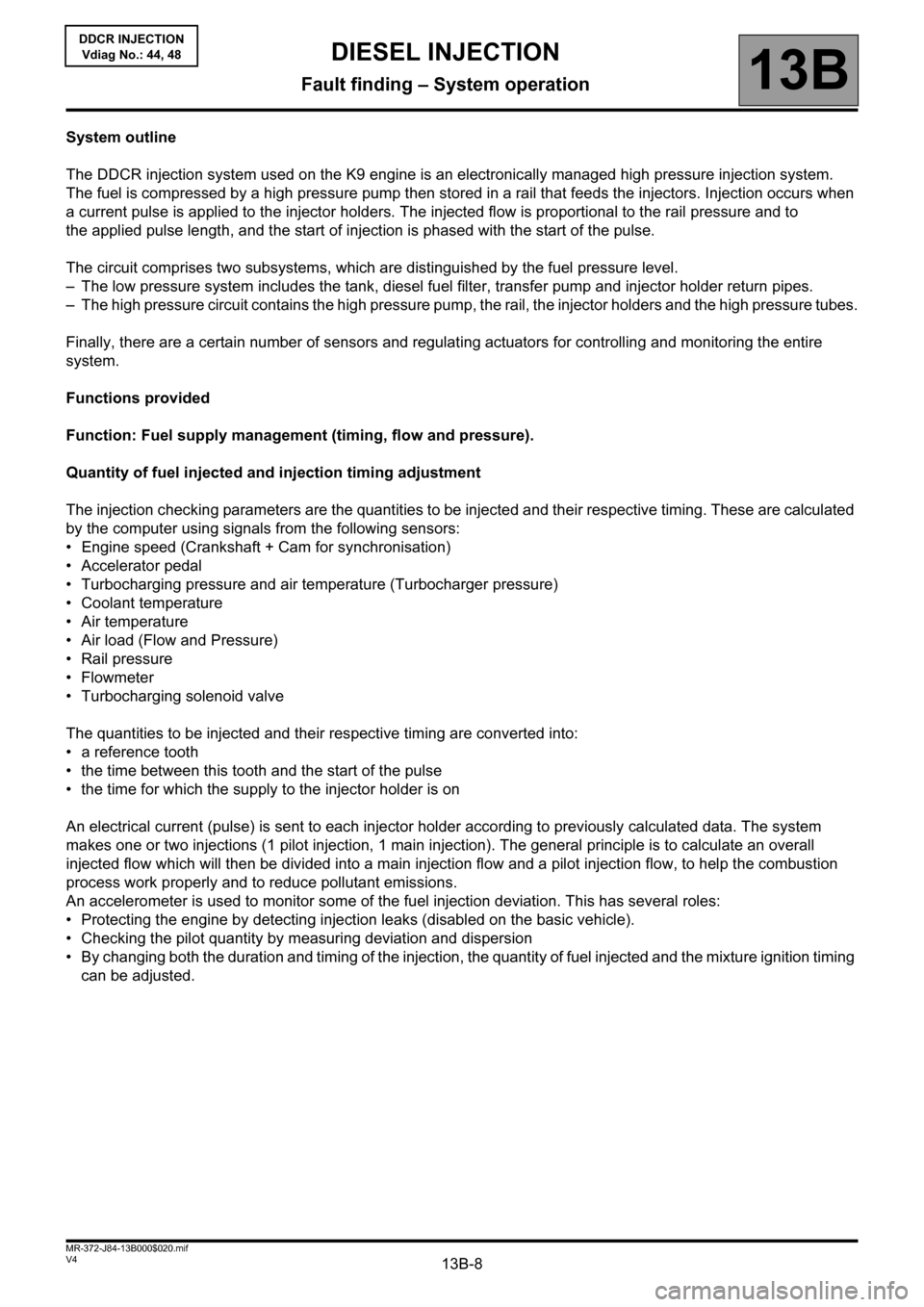
13B-8V4 MR-372-J84-13B000$020.mif
13B
DDCR INJECTION
Vdiag No.: 44, 48
System outline
The DDCR injection system used on the K9 engine is an electronically managed high pressure injection system.
The fuel is compressed by a high pressure pump then stored in a rail that feeds the injectors. Injection occurs when
a current pulse is applied to the injector holders. The injected flow is proportional to the rail pressure and to
the applied pulse length, and the start of injection is phased with the start of the pulse.
The circuit comprises two subsystems, which are distinguished by the fuel pressure level.
– The low pressure system includes the tank, diesel fuel filter, transfer pump and injector holder return pipes.
– The high pressure circuit contains the high pressure pump, the rail, the injector holders and the high pressure tubes.
Finally, there are a certain number of sensors and regulating actuators for controlling and monitoring the entire
system.
Functions provided
Function: Fuel supply management (timing, flow and pressure).
Quantity of fuel injected and injection timing adjustment
The injection checking parameters are the quantities to be injected and their respective timing. These are calculated
by the computer using signals from the following sensors:
• Engine speed (Crankshaft + Cam for synchronisation)
• Accelerator pedal
• Turbocharging pressure and air temperature (Turbocharger pressure)
• Coolant temperature
• Air temperature
• Air load (Flow and Pressure)
• Rail pressure
• Flowmeter
• Turbocharging solenoid valve
The quantities to be injected and their respective timing are converted into:
• a reference tooth
• the time between this tooth and the start of the pulse
• the time for which the supply to the injector holder is on
An electrical current (pulse) is sent to each injector holder according to previously calculated data. The system
makes one or two injections (1 pilot injection, 1 main injection). The general principle is to calculate an overall
injected flow which will then be divided into a main injection flow and a pilot injection flow, to help the combustion
process work properly and to reduce pollutant emissions.
An accelerometer is used to monitor some of the fuel injection deviation. This has several roles:
• Protecting the engine by detecting injection leaks (disabled on the basic vehicle).
• Checking the pilot quantity by measuring deviation and dispersion
• By changing both the duration and timing of the injection, the quantity of fuel injected and the mixture ignition timing
can be adjusted.
DIESEL INJECTION
Fault finding – System operation
Page 9 of 198
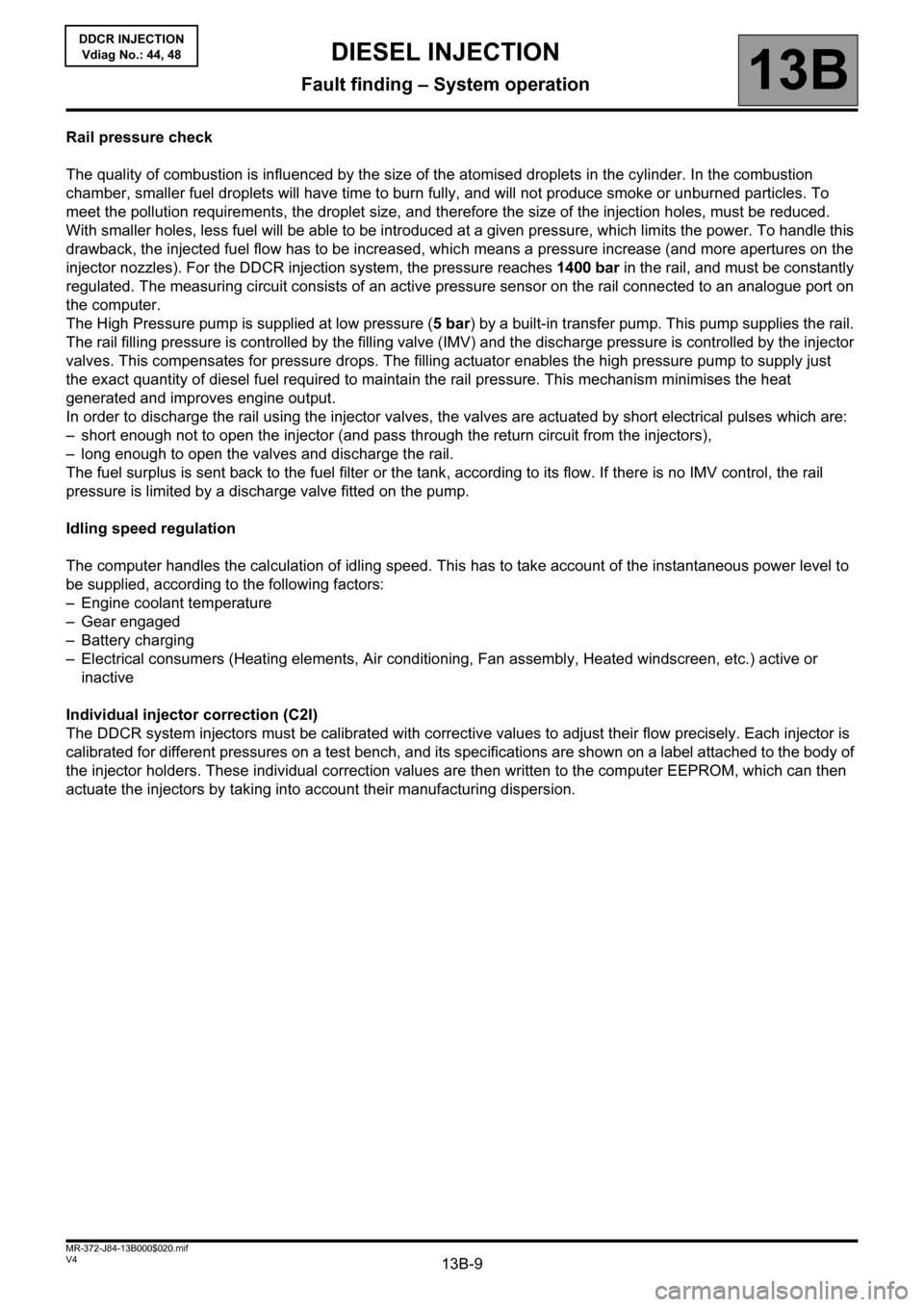
13B-9V4 MR-372-J84-13B000$020.mif
DIESEL INJECTION
Fault finding – System operation13B
DDCR INJECTION
Vdiag No.: 44, 48
Rail pressure check
The quality of combustion is influenced by the size of the atomised droplets in the cylinder. In the combustion
chamber, smaller fuel droplets will have time to burn fully, and will not produce smoke or unburned particles. To
meet the pollution requirements, the droplet size, and therefore the size of the injection holes, must be reduced.
With smaller holes, less fuel will be able to be introduced at a given pressure, which limits the power. To handle this
drawback, the injected fuel flow has to be increased, which means a pressure increase (and more apertures on the
injector nozzles). For the DDCR injection system, the pressure reaches 1400 bar in the rail, and must be constantly
regulated. The measuring circuit consists of an active pressure sensor on the rail connected to an analogue port on
the computer.
The High Pressure pump is supplied at low pressure (5bar) by a built-in transfer pump. This pump supplies the rail.
The rail filling pressure is controlled by the filling valve (IMV) and the discharge pressure is controlled by the injector
valves. This compensates for pressure drops. The filling actuator enables the high pressure pump to supply just
the exact quantity of diesel fuel required to maintain the rail pressure. This mechanism minimises the heat
generated and improves engine output.
In order to discharge the rail using the injector valves, the valves are actuated by short electrical pulses which are:
– short enough not to open the injector (and pass through the return circuit from the injectors),
– long enough to open the valves and discharge the rail.
The fuel surplus is sent back to the fuel filter or the tank, according to its flow. If there is no IMV control, the rail
pressure is limited by a discharge valve fitted on the pump.
Idling speed regulation
The computer handles the calculation of idling speed. This has to take account of the instantaneous power level to
be supplied, according to the following factors:
– Engine coolant temperature
– Gear engaged
– Battery charging
– Electrical consumers (Heating elements, Air conditioning, Fan assembly, Heated windscreen, etc.) active or
inactive
Individual injector correction (C2I)
The DDCR system injectors must be calibrated with corrective values to adjust their flow precisely. Each injector is
calibrated for different pressures on a test bench, and its specifications are shown on a label attached to the body of
the injector holders. These individual correction values are then written to the computer EEPROM, which can then
actuate the injectors by taking into account their manufacturing dispersion.
Page 10 of 198
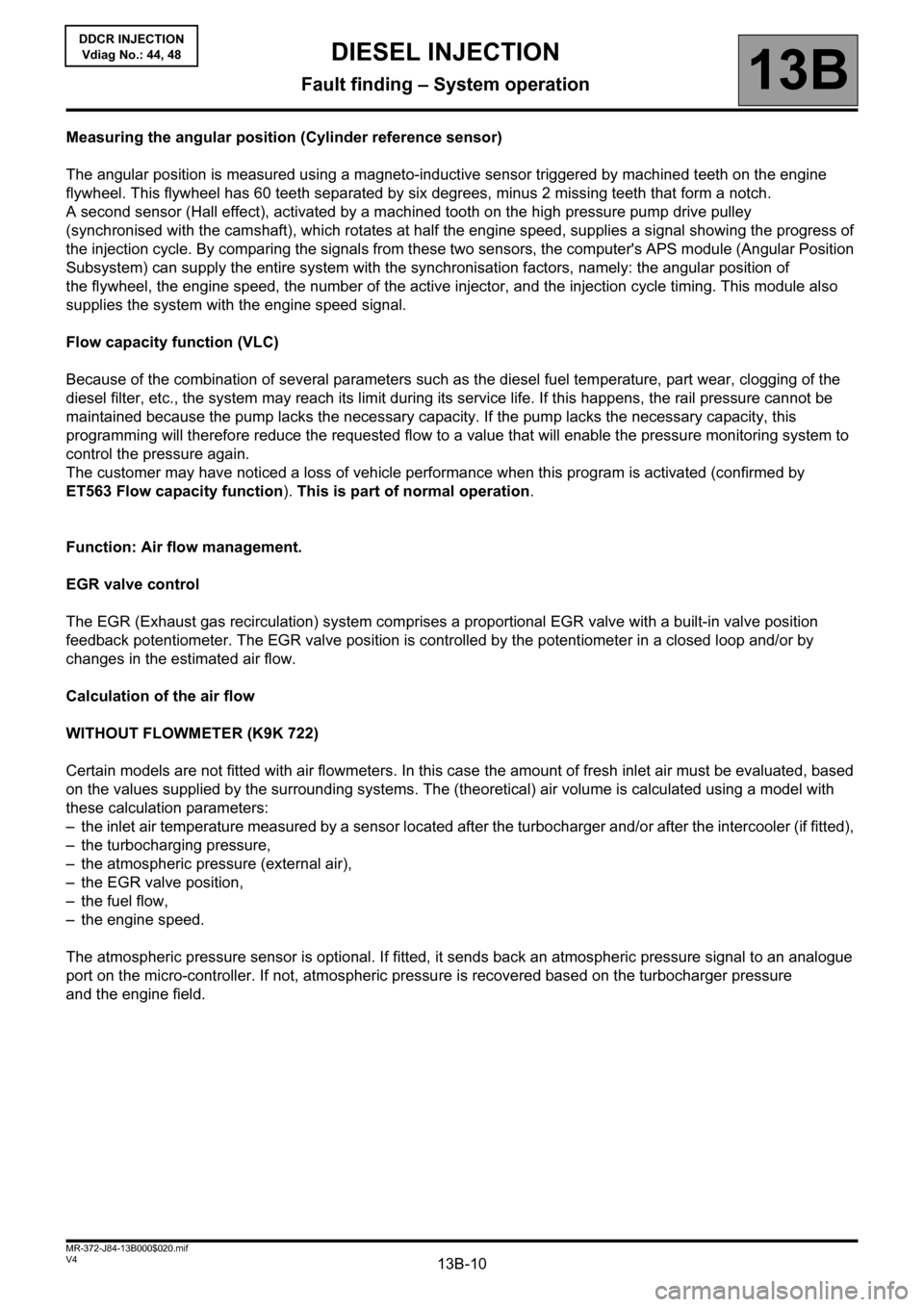
13B-10V4 MR-372-J84-13B000$020.mif
DIESEL INJECTION
Fault finding – System operation13B
DDCR INJECTION
Vdiag No.: 44, 48
Measuring the angular position (Cylinder reference sensor)
The angular position is measured using a magneto-inductive sensor triggered by machined teeth on the engine
flywheel. This flywheel has 60 teeth separated by six degrees, minus 2 missing teeth that form a notch.
A second sensor (Hall effect), activated by a machined tooth on the high pressure pump drive pulley
(synchronised with the camshaft), which rotates at half the engine speed, supplies a signal showing the progress of
the injection cycle. By comparing the signals from these two sensors, the computer's APS module (Angular Position
Subsystem) can supply the entire system with the synchronisation factors, namely: the angular position of
the flywheel, the engine speed, the number of the active injector, and the injection cycle timing. This module also
supplies the system with the engine speed signal.
Flow capacity function (VLC)
Because of the combination of several parameters such as the diesel fuel temperature, part wear, clogging of the
diesel filter, etc., the system may reach its limit during its service life. If this happens, the rail pressure cannot be
maintained because the pump lacks the necessary capacity. If the pump lacks the necessary capacity, this
programming will therefore reduce the requested flow to a value that will enable the pressure monitoring system to
control the pressure again.
The customer may have noticed a loss of vehicle performance when this program is activated (confirmed by
ET563 Flow capacity function). This is part of normal operation.
Function: Air flow management.
EGR valve control
The EGR (Exhaust gas recirculation) system comprises a proportional EGR valve with a built-in valve position
feedback potentiometer. The EGR valve position is controlled by the potentiometer in a closed loop and/or by
changes in the estimated air flow.
Calculation of the air flow
WITHOUT FLOWMETER (K9K 722)
Certain models are not fitted with air flowmeters. In this case the amount of fresh inlet air must be evaluated, based
on the values supplied by the surrounding systems. The (theoretical) air volume is calculated using a model with
these calculation parameters:
– the inlet air temperature measured by a sensor located after the turbocharger and/or after the intercooler (if fitted),
– the turbocharging pressure,
– the atmospheric pressure (external air),
– the EGR valve position,
– the fuel flow,
– the engine speed.
The atmospheric pressure sensor is optional. If fitted, it sends back an atmospheric pressure signal to an analogue
port on the micro-controller. If not, atmospheric pressure is recovered based on the turbocharger pressure
and the engine field.
Page 11 of 198
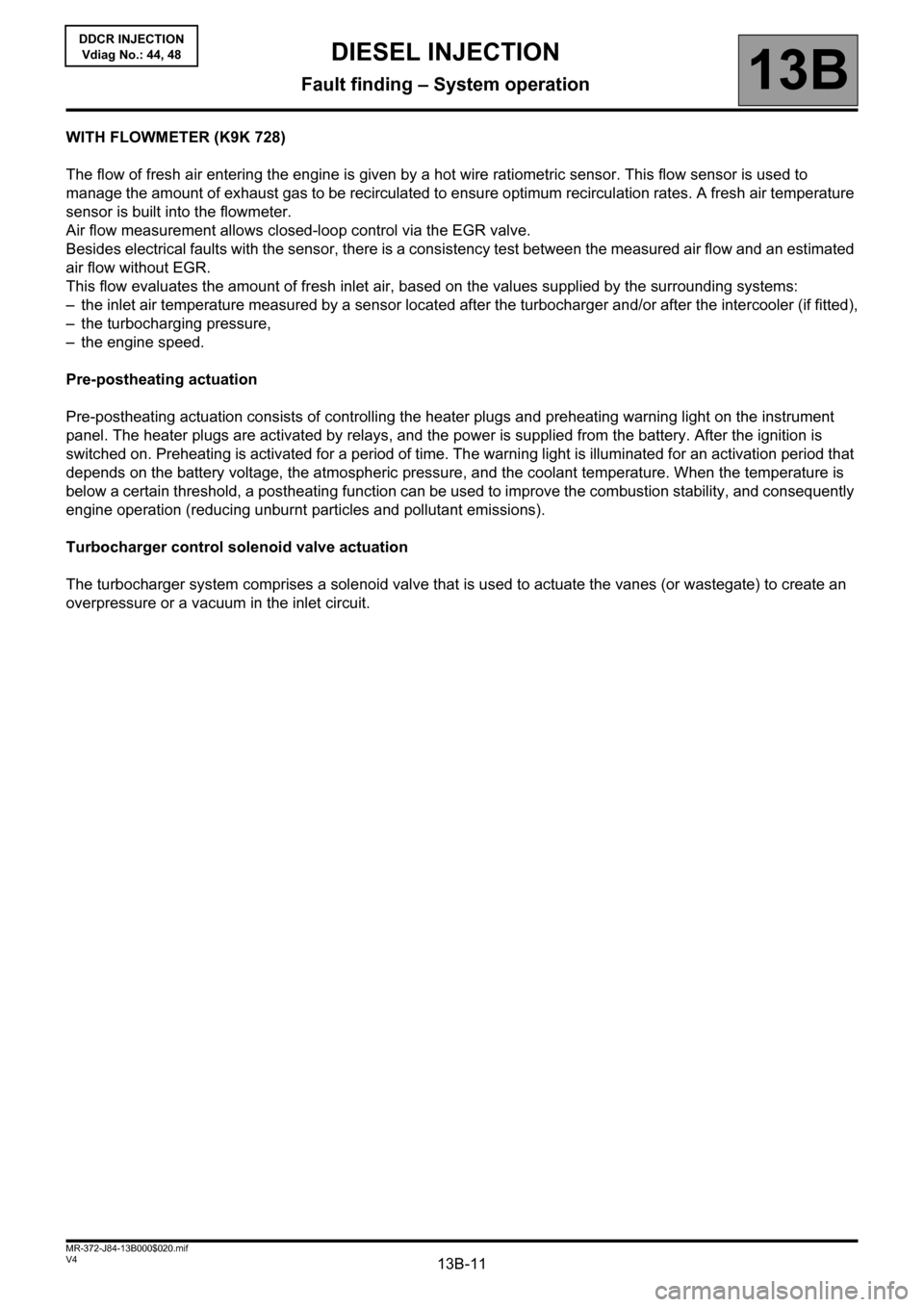
13B-11V4 MR-372-J84-13B000$020.mif
DIESEL INJECTION
Fault finding – System operation13B
DDCR INJECTION
Vdiag No.: 44, 48
WITH FLOWMETER (K9K 728)
The flow of fresh air entering the engine is given by a hot wire ratiometric sensor. This flow sensor is used to
manage the amount of exhaust gas to be recirculated to ensure optimum recirculation rates. A fresh air temperature
sensor is built into the flowmeter.
Air flow measurement allows closed-loop control via the EGR valve.
Besides electrical faults with the sensor, there is a consistency test between the measured air flow and an estimated
air flow without EGR.
This flow evaluates the amount of fresh inlet air, based on the values supplied by the surrounding systems:
– the inlet air temperature measured by a sensor located after the turbocharger and/or after the intercooler (if fitted),
– the turbocharging pressure,
– the engine speed.
Pre-postheating actuation
Pre-postheating actuation consists of controlling the heater plugs and preheating warning light on the instrument
panel. The heater plugs are activated by relays, and the power is supplied from the battery. After the ignition is
switched on. Preheating is activated for a period of time. The warning light is illuminated for an activation period that
depends on the battery voltage, the atmospheric pressure, and the coolant temperature. When the temperature is
below a certain threshold, a postheating function can be used to improve the combustion stability, and consequently
engine operation (reducing unburnt particles and pollutant emissions).
Turbocharger control solenoid valve actuation
The turbocharger system comprises a solenoid valve that is used to actuate the vanes (or wastegate) to create an
overpressure or a vacuum in the inlet circuit.
Page 12 of 198
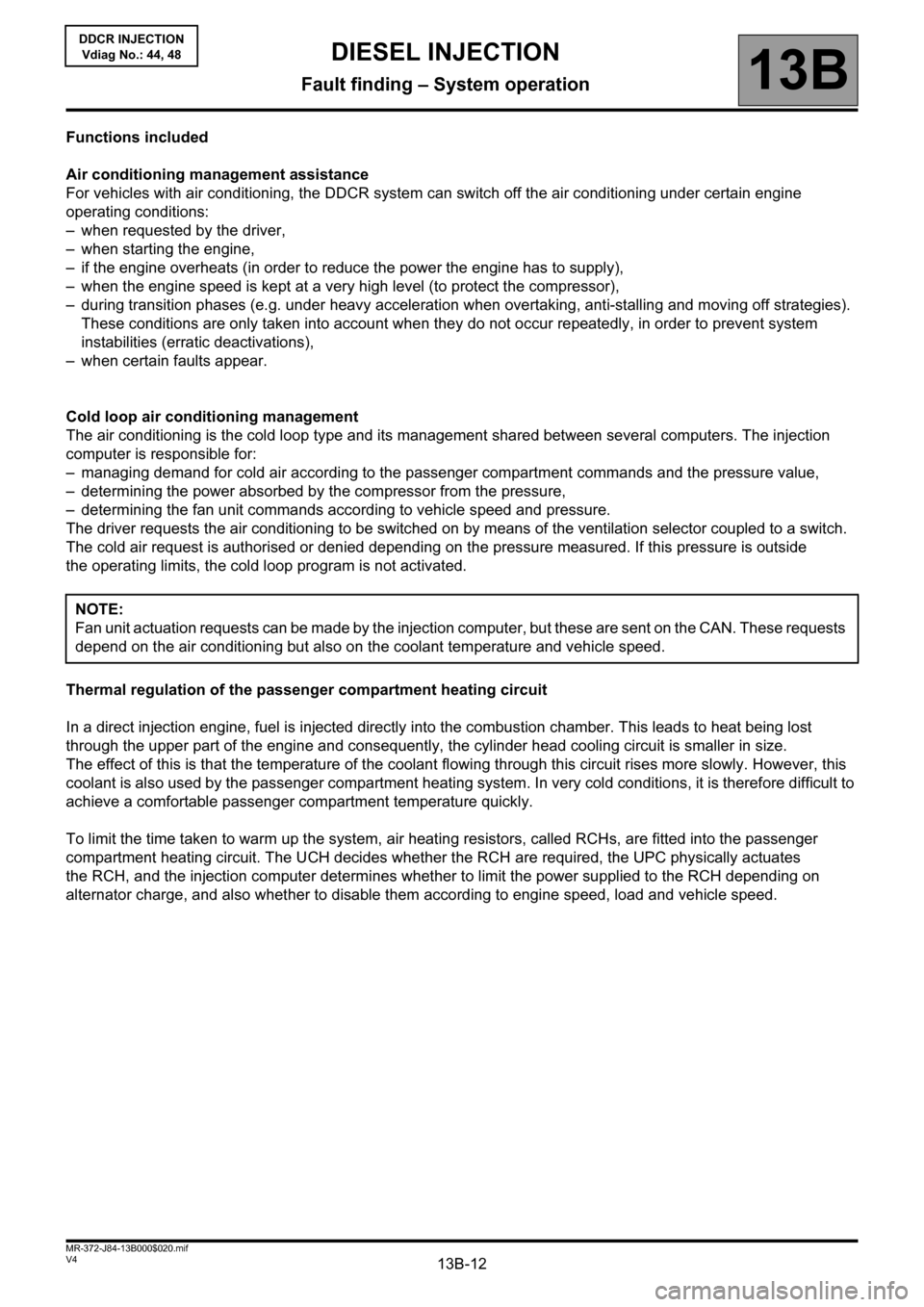
13B-12V4 MR-372-J84-13B000$020.mif
DIESEL INJECTION
Fault finding – System operation13B
DDCR INJECTION
Vdiag No.: 44, 48
Functions included
Air conditioning management assistance
For vehicles with air conditioning, the DDCR system can switch off the air conditioning under certain engine
operating conditions:
– when requested by the driver,
– when starting the engine,
– if the engine overheats (in order to reduce the power the engine has to supply),
– when the engine speed is kept at a very high level (to protect the compressor),
– during transition phases (e.g. under heavy acceleration when overtaking, anti-stalling and moving off strategies).
These conditions are only taken into account when they do not occur repeatedly, in order to prevent system
instabilities (erratic deactivations),
– when certain faults appear.
Cold loop air conditioning management
The air conditioning is the cold loop type and its management shared between several computers. The injection
computer is responsible for:
– managing demand for cold air according to the passenger compartment commands and the pressure value,
– determining the power absorbed by the compressor from the pressure,
– determining the fan unit commands according to vehicle speed and pressure.
The driver requests the air conditioning to be switched on by means of the ventilation selector coupled to a switch.
The cold air request is authorised or denied depending on the pressure measured. If this pressure is outside
the operating limits, the cold loop program is not activated.
Thermal regulation of the passenger compartment heating circuit
In a direct injection engine, fuel is injected directly into the combustion chamber. This leads to heat being lost
through the upper part of the engine and consequently, the cylinder head cooling circuit is smaller in size.
The effect of this is that the temperature of the coolant flowing through this circuit rises more slowly. However, this
coolant is also used by the passenger compartment heating system. In very cold conditions, it is therefore difficult to
achieve a comfortable passenger compartment temperature quickly.
To limit the time taken to warm up the system, air heating resistors, called RCHs, are fitted into the passenger
compartment heating circuit. The UCH decides whether the RCH are required, the UPC physically actuates
the RCH, and the injection computer determines whether to limit the power supplied to the RCH depending on
alternator charge, and also whether to disable them according to engine speed, load and vehicle speed. NOTE:
Fan unit actuation requests can be made by the injection computer, but these are sent on the CAN. These requests
depend on the air conditioning but also on the coolant temperature and vehicle speed.
Page 13 of 198
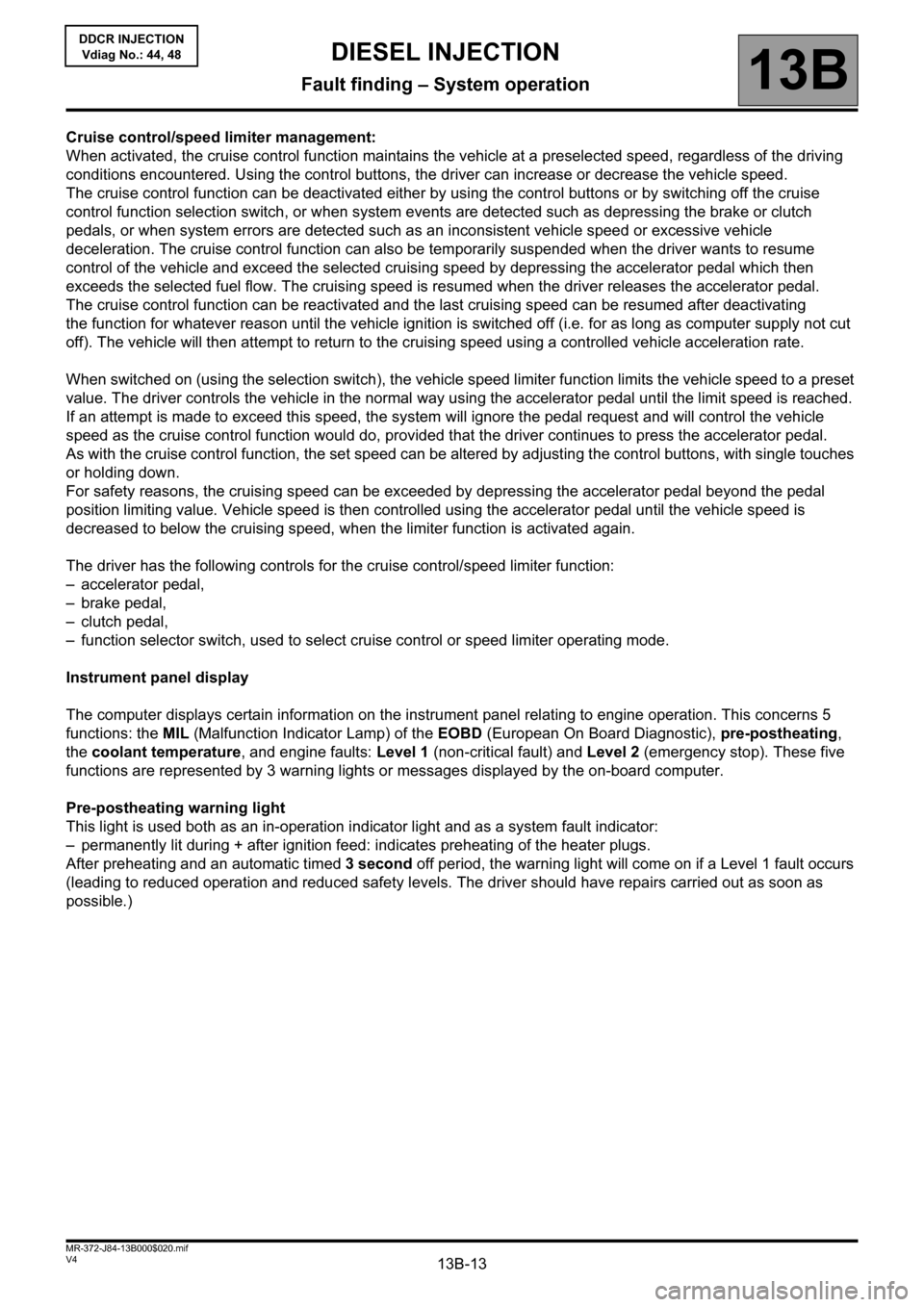
13B-13V4 MR-372-J84-13B000$020.mif
DIESEL INJECTION
Fault finding – System operation13B
DDCR INJECTION
Vdiag No.: 44, 48
Cruise control/speed limiter management:
When activated, the cruise control function maintains the vehicle at a preselected speed, regardless of the driving
conditions encountered. Using the control buttons, the driver can increase or decrease the vehicle speed.
The cruise control function can be deactivated either by using the control buttons or by switching off the cruise
control function selection switch, or when system events are detected such as depressing the brake or clutch
pedals, or when system errors are detected such as an inconsistent vehicle speed or excessive vehicle
deceleration. The cruise control function can also be temporarily suspended when the driver wants to resume
control of the vehicle and exceed the selected cruising speed by depressing the accelerator pedal which then
exceeds the selected fuel flow. The cruising speed is resumed when the driver releases the accelerator pedal.
The cruise control function can be reactivated and the last cruising speed can be resumed after deactivating
the function for whatever reason until the vehicle ignition is switched off (i.e. for as long as computer supply not cut
off). The vehicle will then attempt to return to the cruising speed using a controlled vehicle acceleration rate.
When switched on (using the selection switch), the vehicle speed limiter function limits the vehicle speed to a preset
value. The driver controls the vehicle in the normal way using the accelerator pedal until the limit speed is reached.
If an attempt is made to exceed this speed, the system will ignore the pedal request and will control the vehicle
speed as the cruise control function would do, provided that the driver continues to press the accelerator pedal.
As with the cruise control function, the set speed can be altered by adjusting the control buttons, with single touches
or holding down.
For safety reasons, the cruising speed can be exceeded by depressing the accelerator pedal beyond the pedal
position limiting value. Vehicle speed is then controlled using the accelerator pedal until the vehicle speed is
decreased to below the cruising speed, when the limiter function is activated again.
The driver has the following controls for the cruise control/speed limiter function:
– accelerator pedal,
– brake pedal,
– clutch pedal,
– function selector switch, used to select cruise control or speed limiter operating mode.
Instrument panel display
The computer displays certain information on the instrument panel relating to engine operation. This concerns 5
functions: the MIL (Malfunction Indicator Lamp) of the EOBD (European On Board Diagnostic), pre-postheating,
the coolant temperature, and engine faults: Level 1 (non-critical fault) and Level 2 (emergency stop). These five
functions are represented by 3 warning lights or messages displayed by the on-board computer.
Pre-postheating warning light
This light is used both as an in-operation indicator light and as a system fault indicator:
– permanently lit during + after ignition feed: indicates preheating of the heater plugs.
After preheating and an automatic timed 3 second off period, the warning light will come on if a Level 1 fault occurs
(leading to reduced operation and reduced safety levels. The driver should have repairs carried out as soon as
possible.)
Page 14 of 198
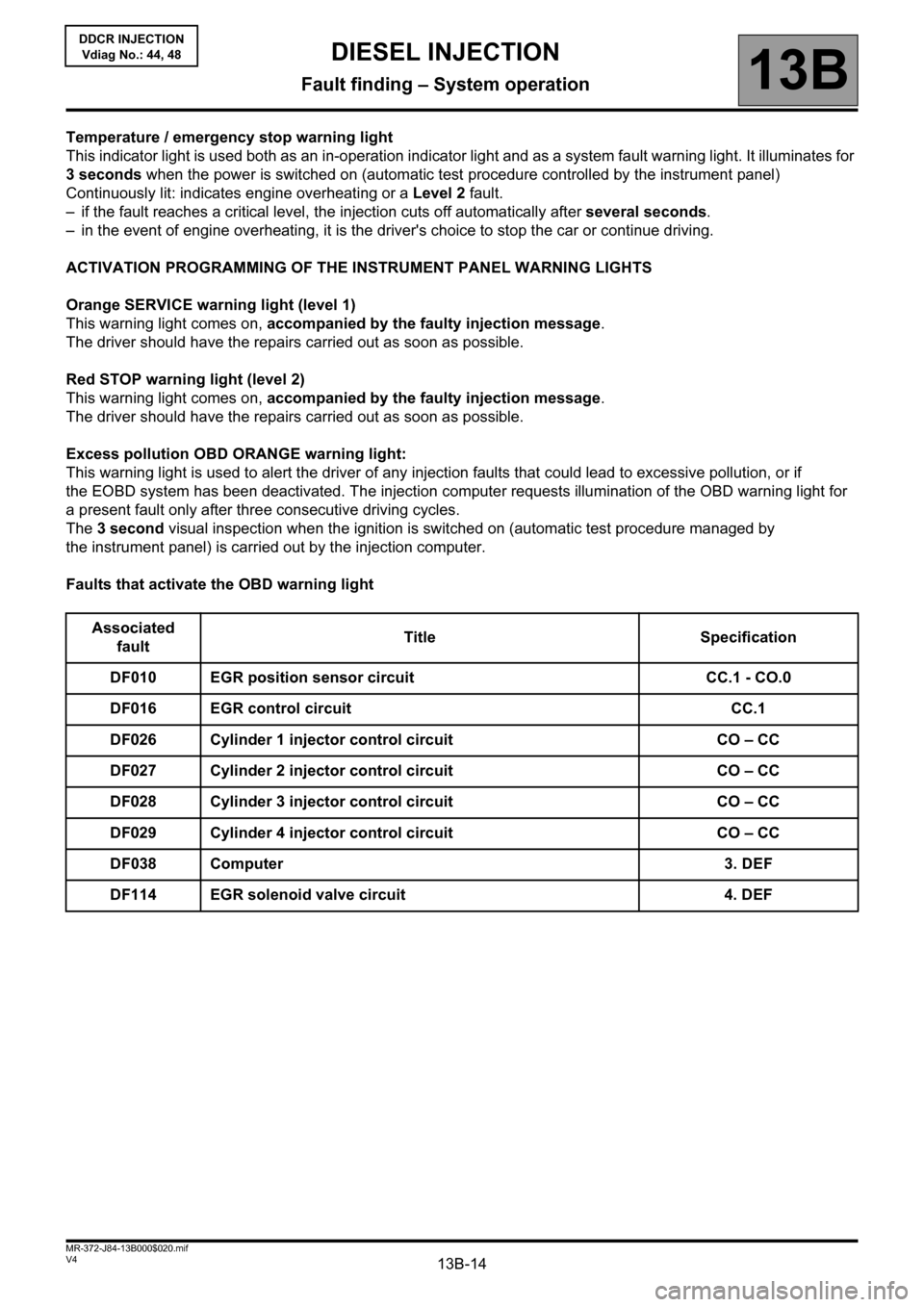
13B-14V4 MR-372-J84-13B000$020.mif
DIESEL INJECTION
Fault finding – System operation13B
DDCR INJECTION
Vdiag No.: 44, 48
Temperature / emergency stop warning light
This indicator light is used both as an in-operation indicator light and as a system fault warning light. It illuminates for
3 seconds when the power is switched on (automatic test procedure controlled by the instrument panel)
Continuously lit: indicates engine overheating or a Level 2 fault.
– if the fault reaches a critical level, the injection cuts off automatically after several seconds.
– in the event of engine overheating, it is the driver's choice to stop the car or continue driving.
ACTIVATION PROGRAMMING OF THE INSTRUMENT PANEL WARNING LIGHTS
Orange SERVICE warning light (level 1)
This warning light comes on, accompanied by the faulty injection message.
The driver should have the repairs carried out as soon as possible.
Red STOP warning light (level 2)
This warning light comes on, accompanied by the faulty injection message.
The driver should have the repairs carried out as soon as possible.
Excess pollution OBD ORANGE warning light:
This warning light is used to alert the driver of any injection faults that could lead to excessive pollution, or if
the EOBD system has been deactivated. The injection computer requests illumination of the OBD warning light for
a present fault only after three consecutive driving cycles.
The 3 second visual inspection when the ignition is switched on (automatic test procedure managed by
the instrument panel) is carried out by the injection computer.
Faults that activate the OBD warning light
Associated
faultTitle Specification
DF010 EGR position sensor circuit CC.1 - CO.0
DF016 EGR control circuit CC.1
DF026 Cylinder 1 injector control circuit CO – CC
DF027 Cylinder 2 injector control circuit CO – CC
DF028 Cylinder 3 injector control circuit CO – CC
DF029 Cylinder 4 injector control circuit CO – CC
DF038 Computer 3. DEF
DF114 EGR solenoid valve circuit 4. DEF