washer RENAULT SCENIC 2012 J95 / 3.G Engine And Peripherals EDC16CP33 Workshop Manual
[x] Cancel search | Manufacturer: RENAULT, Model Year: 2012, Model line: SCENIC, Model: RENAULT SCENIC 2012 J95 / 3.GPages: 510, PDF Size: 2.98 MB
Page 8 of 510
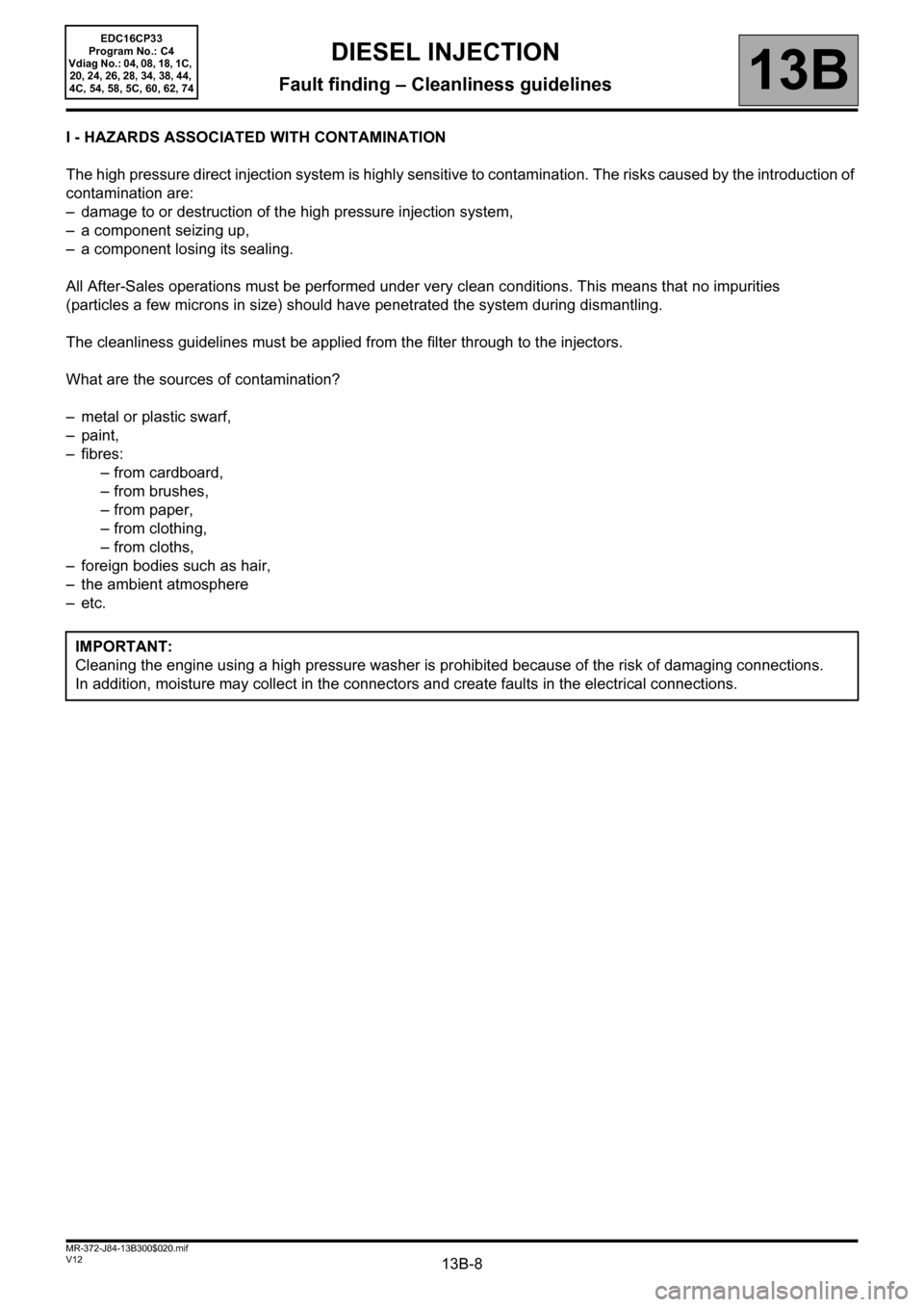
13B-8V12 MR-372-J84-13B300$020.mif
13B
EDC16CP33
Program No.: C4
Vdiag No.: 04, 08, 18, 1C,
20, 24, 26, 28, 34, 38, 44,
4C, 54, 58, 5C, 60, 62, 74
I - HAZARDS ASSOCIATED WITH CONTAMINATION
The high pressure direct injection system is highly sensitive to contamination. The risks caused by the introduction of
contamination are:
– damage to or destruction of the high pressure injection system,
– a component seizing up,
– a component losing its sealing.
All After-Sales operations must be performed under very clean conditions. This means that no impurities
(particles a few microns in size) should have penetrated the system during dismantling.
The cleanliness guidelines must be applied from the filter through to the injectors.
What are the sources of contamination?
– metal or plastic swarf,
– paint,
–fibres:
– from cardboard,
– from brushes,
– from paper,
– from clothing,
– from cloths,
– foreign bodies such as hair,
– the ambient atmosphere
–etc.
IMPORTANT:
Cleaning the engine using a high pressure washer is prohibited because of the risk of damaging connections.
In addition, moisture may collect in the connectors and create faults in the electrical connections.
DIESEL INJECTION
Fault finding – Cleanliness guidelines
Page 477 of 510
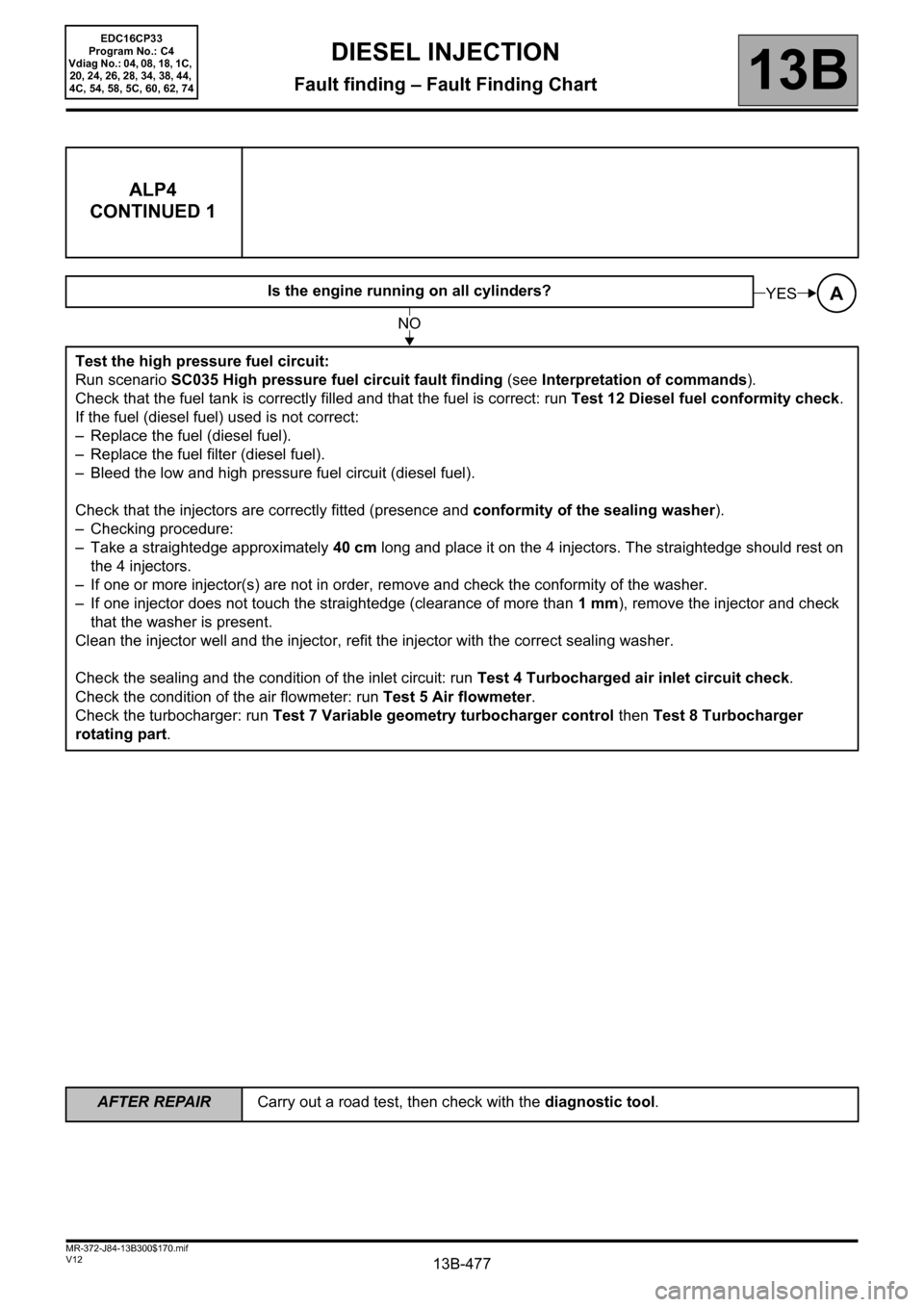
13B-477
AFTER REPAIRCarry out a road test, then check with the diagnostic tool.
V12 MR-372-J84-13B300$170.mif
DIESEL INJECTION
Fault finding – Fault Finding Chart13B
ALP4
CONTINUED 1
Is the engine running on all cylinders?
Test the high pressure fuel circuit:
Run scenario SC035 High pressure fuel circuit fault finding (see Interpretation of commands).
Check that the fuel tank is correctly filled and that the fuel is correct: run Test 12 Diesel fuel conformity check.
If the fuel (diesel fuel) used is not correct:
– Replace the fuel (diesel fuel).
– Replace the fuel filter (diesel fuel).
– Bleed the low and high pressure fuel circuit (diesel fuel).
Check that the injectors are correctly fitted (presence and conformity of the sealing washer).
– Checking procedure:
– Take a straightedge approximately 40 cm long and place it on the 4 injectors. The straightedge should rest on
the 4 injectors.
– If one or more injector(s) are not in order, remove and check the conformity of the washer.
– If one injector does not touch the straightedge (clearance of more than 1mm), remove the injector and check
that the washer is present.
Clean the injector well and the injector, refit the injector with the correct sealing washer.
Check the sealing and the condition of the inlet circuit: run Test 4 Turbocharged air inlet circuit check.
Check the condition of the air flowmeter: run Test 5 Air flowmeter.
Check the turbocharger: run Test 7 Variable geometry turbocharger control then Test 8 Turbocharger
rotating part.AYES
NO
EDC16CP33
Program No.: C4
Vdiag No.: 04, 08, 18, 1C,
20, 24, 26, 28, 34, 38, 44,
4C, 54, 58, 5C, 60, 62, 74
Page 506 of 510
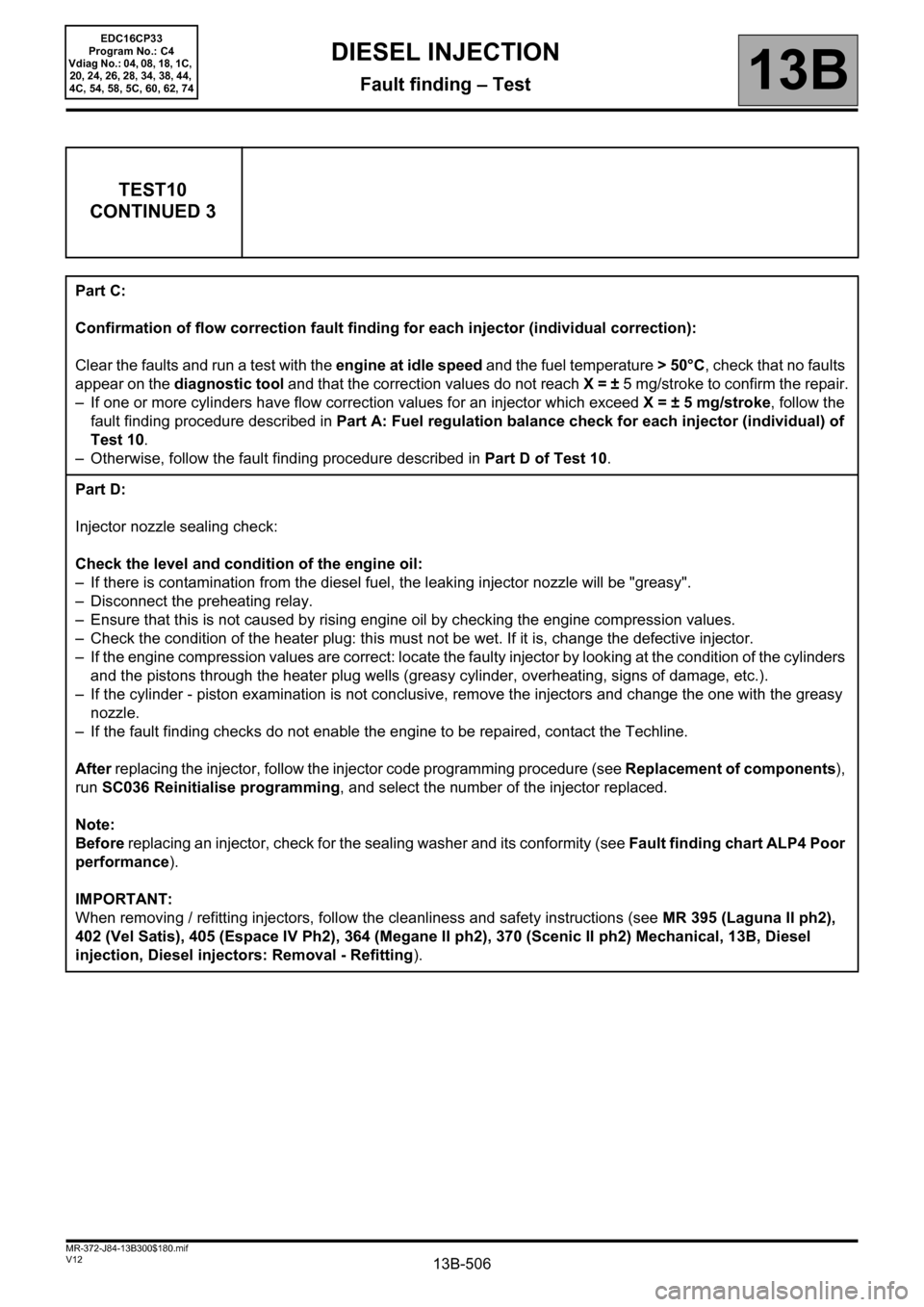
13B-506V12 MR-372-J84-13B300$180.mif
DIESEL INJECTION
Fault finding – Test13B
TEST10
CONTINUED 3
Part C:
Confirmation of flow correction fault finding for each injector (individual correction):
Clear the faults and run a test with the engine at idle speed and the fuel temperature > 50°C, check that no faults
appear on the diagnostic tool and that the correction values do not reach X = ± 5 mg/stroke to confirm the repair.
– If one or more cylinders have flow correction values for an injector which exceed X = ± 5 mg/stroke, follow the
fault finding procedure described in Part A: Fuel regulation balance check for each injector (individual) of
Test 10.
– Otherwise, follow the fault finding procedure described in Part D of Test 10.
Part D:
Injector nozzle sealing check:
Check the level and condition of the engine oil:
– If there is contamination from the diesel fuel, the leaking injector nozzle will be "greasy".
– Disconnect the preheating relay.
– Ensure that this is not caused by rising engine oil by checking the engine compression values.
– Check the condition of the heater plug: this must not be wet. If it is, change the defective injector.
– If the engine compression values are correct: locate the faulty injector by looking at the condition of the cylinders
and the pistons through the heater plug wells (greasy cylinder, overheating, signs of damage, etc.).
– If the cylinder - piston examination is not conclusive, remove the injectors and change the one with the greasy
nozzle.
– If the fault finding checks do not enable the engine to be repaired, contact the Techline.
After replacing the injector, follow the injector code programming procedure (see Replacement of components),
run SC036 Reinitialise programming, and select the number of the injector replaced.
Note:
Before replacing an injector, check for the sealing washer and its conformity (see Fault finding chart ALP4 Poor
performance).
IMPORTANT:
When removing / refitting injectors, follow the cleanliness and safety instructions (see MR 395 (Laguna II ph2),
402 (Vel Satis), 405 (Espace IV Ph2), 364 (Megane II ph2), 370 (Scenic II ph2) Mechanical, 13B, Diesel
injection, Diesel injectors: Removal - Refitting).
EDC16CP33
Program No.: C4
Vdiag No.: 04, 08, 18, 1C,
20, 24, 26, 28, 34, 38, 44,
4C, 54, 58, 5C, 60, 62, 74