check engine RENAULT SCENIC 2014 J95 / 3.G Petrol Injection - Sagem3000 Owner's Manual
[x] Cancel search | Manufacturer: RENAULT, Model Year: 2014, Model line: SCENIC, Model: RENAULT SCENIC 2014 J95 / 3.GPages: 181
Page 46 of 181
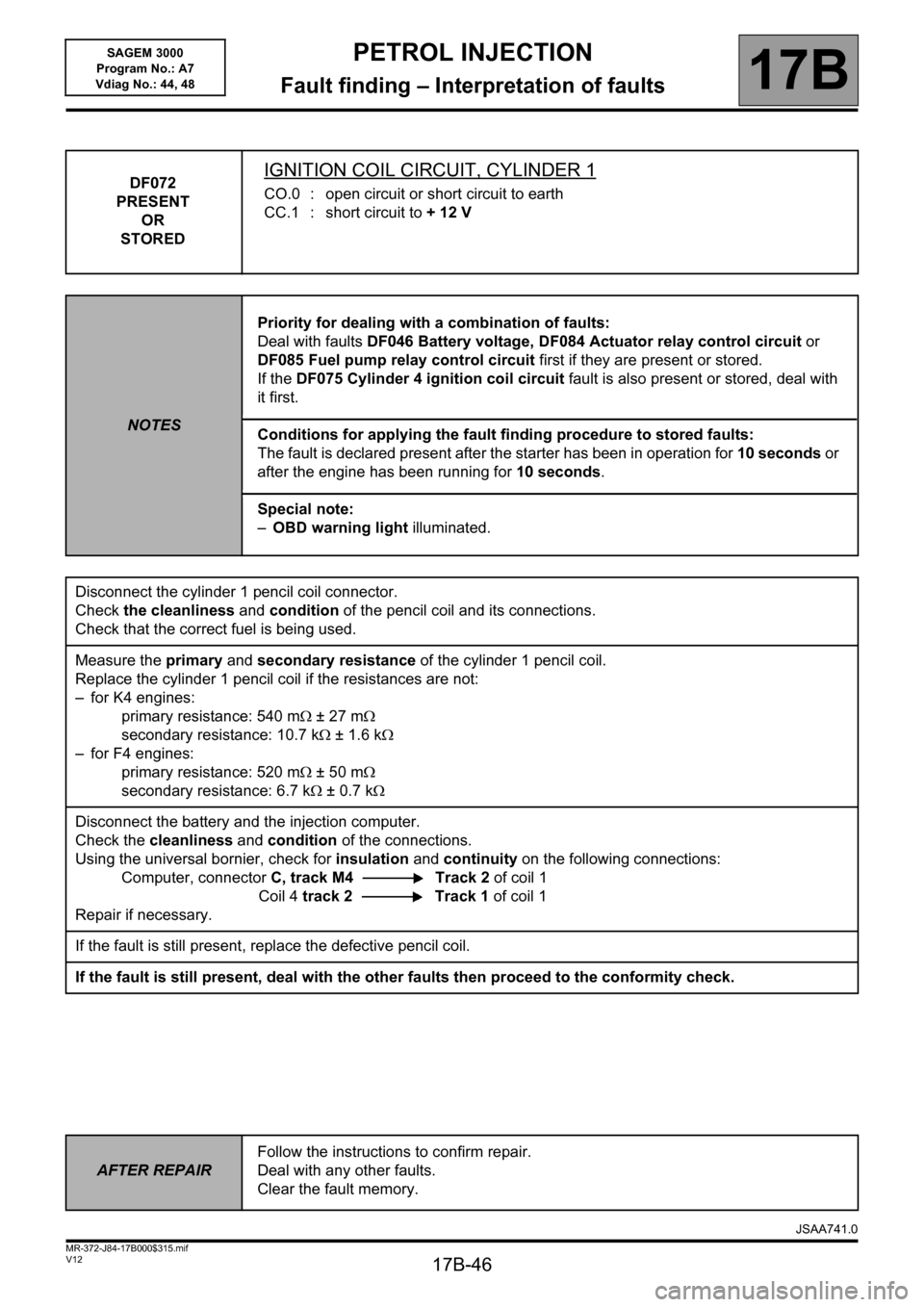
PETROL INJECTION
Fault finding – Interpretation of faults17B
17B-46V12 MR-372-J84-17B000$315.mif
SAGEM 3000
Program No.: A7
Vdiag No.: 44, 48
DF072
PRESENT
OR
STOREDIGNITION COIL CIRCUIT, CYLINDER 1
CO.0 : open circuit or short circuit to earth
CC.1 : short circuit to + 12 V
NOTESPriority for dealing with a combination of faults:
Deal with faults DF046 Battery voltage, DF084 Actuator relay control circuit or
DF085 Fuel pump relay control circuit first if they are present or stored.
If the DF075 Cylinder 4 ignition coil circuit fault is also present or stored, deal with
it first.
Conditions for applying the fault finding procedure to stored faults:
The fault is declared present after the starter has been in operation for 10 seconds or
after the engine has been running for 10 seconds.
Special note:
–OBD warning light illuminated.
Disconnect the cylinder 1 pencil coil connector.
Check the cleanliness and condition of the pencil coil and its connections.
Check that the correct fuel is being used.
Measure the primary and secondary resistance of the cylinder 1 pencil coil.
Replace the cylinder 1 pencil coil if the resistances are not:
– for K4 engines:
primary resistance: 540 m ± 27 m
secondary resistance: 10.7 k ± 1.6 k
– for F4 engines:
primary resistance: 520 m ± 50 m
secondary resistance: 6.7 k ± 0.7 k
Disconnect the battery and the injection computer.
Check the cleanliness and condition of the connections.
Using the universal bornier, check for insulation and continuity on the following connections:
Computer, connector C, track M4 Track 2 of coil 1
Coil 4 track 2 Track 1 of coil 1
Repair if necessary.
If the fault is still present, replace the defective pencil coil.
If the fault is still present, deal with the other faults then proceed to the conformity check.
AFTER REPAIRFollow the instructions to confirm repair.
Deal with any other faults.
Clear the fault memory.
JSAA741.0
Page 47 of 181
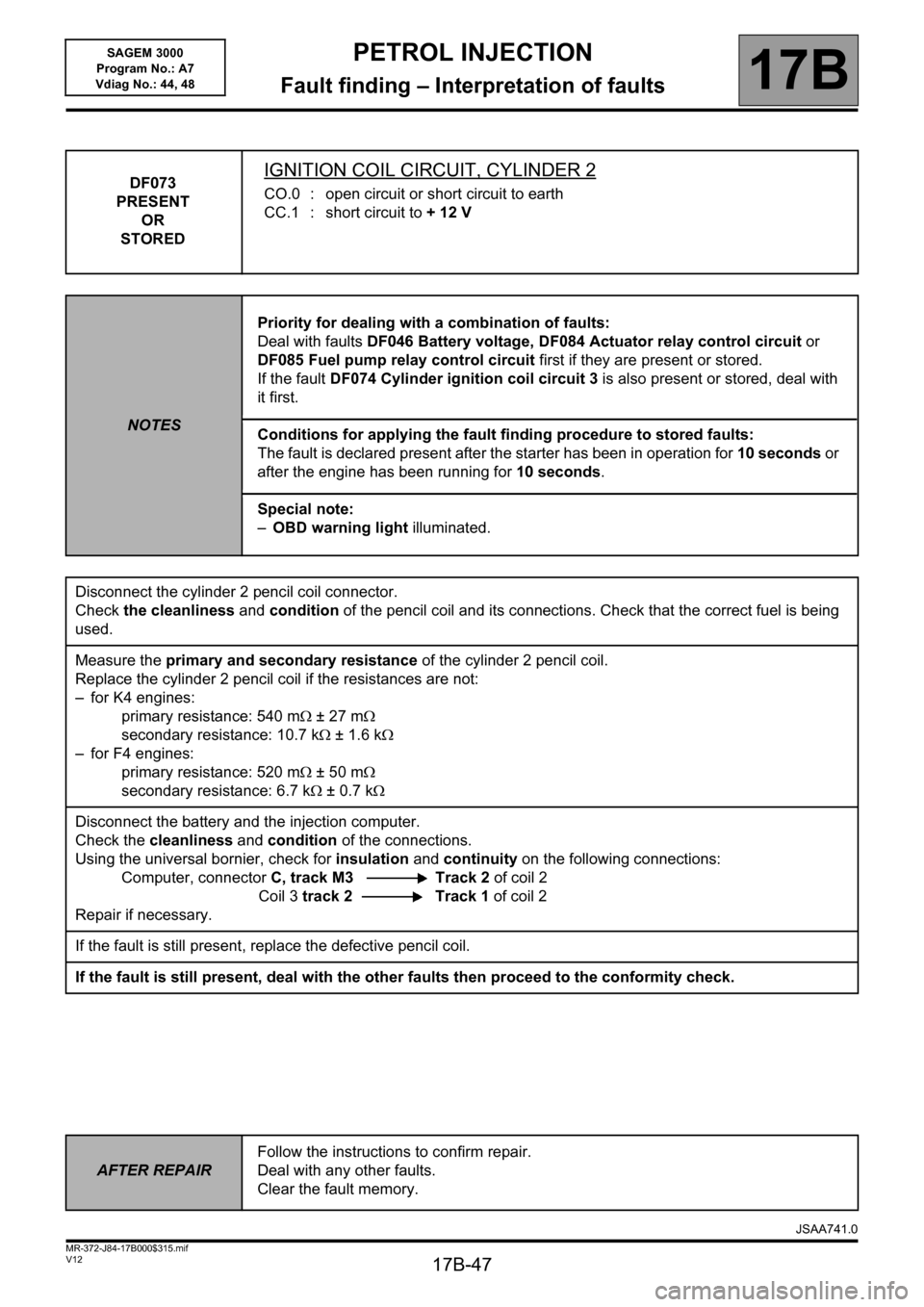
PETROL INJECTION
Fault finding – Interpretation of faults17B
17B-47V12 MR-372-J84-17B000$315.mif
SAGEM 3000
Program No.: A7
Vdiag No.: 44, 48
DF073
PRESENT
OR
STOREDIGNITION COIL CIRCUIT, CYLINDER 2
CO.0 : open circuit or short circuit to earth
CC.1 : short circuit to + 12 V
NOTESPriority for dealing with a combination of faults:
Deal with faults DF046 Battery voltage, DF084 Actuator relay control circuit or
DF085 Fuel pump relay control circuit first if they are present or stored.
If the fault DF074 Cylinder ignition coil circuit 3 is also present or stored, deal with
it first.
Conditions for applying the fault finding procedure to stored faults:
The fault is declared present after the starter has been in operation for 10 seconds or
after the engine has been running for 10 seconds.
Special note:
–OBD warning light illuminated.
Disconnect the cylinder 2 pencil coil connector.
Check the cleanliness and condition of the pencil coil and its connections. Check that the correct fuel is being
used.
Measure the primary and secondary resistance of the cylinder 2 pencil coil.
Replace the cylinder 2 pencil coil if the resistances are not:
– for K4 engines:
primary resistance: 540 m ± 27 m
secondary resistance: 10.7 k ± 1.6 k
– for F4 engines:
primary resistance: 520 m ± 50 m
secondary resistance: 6.7 k ± 0.7 k
Disconnect the battery and the injection computer.
Check the cleanliness and condition of the connections.
Using the universal bornier, check for insulation and continuity on the following connections:
Computer, connector C, track M3 Track 2 of coil 2
Coil 3 track 2 Track 1 of coil 2
Repair if necessary.
If the fault is still present, replace the defective pencil coil.
If the fault is still present, deal with the other faults then proceed to the conformity check.
AFTER REPAIRFollow the instructions to confirm repair.
Deal with any other faults.
Clear the fault memory.
JSAA741.0
Page 48 of 181
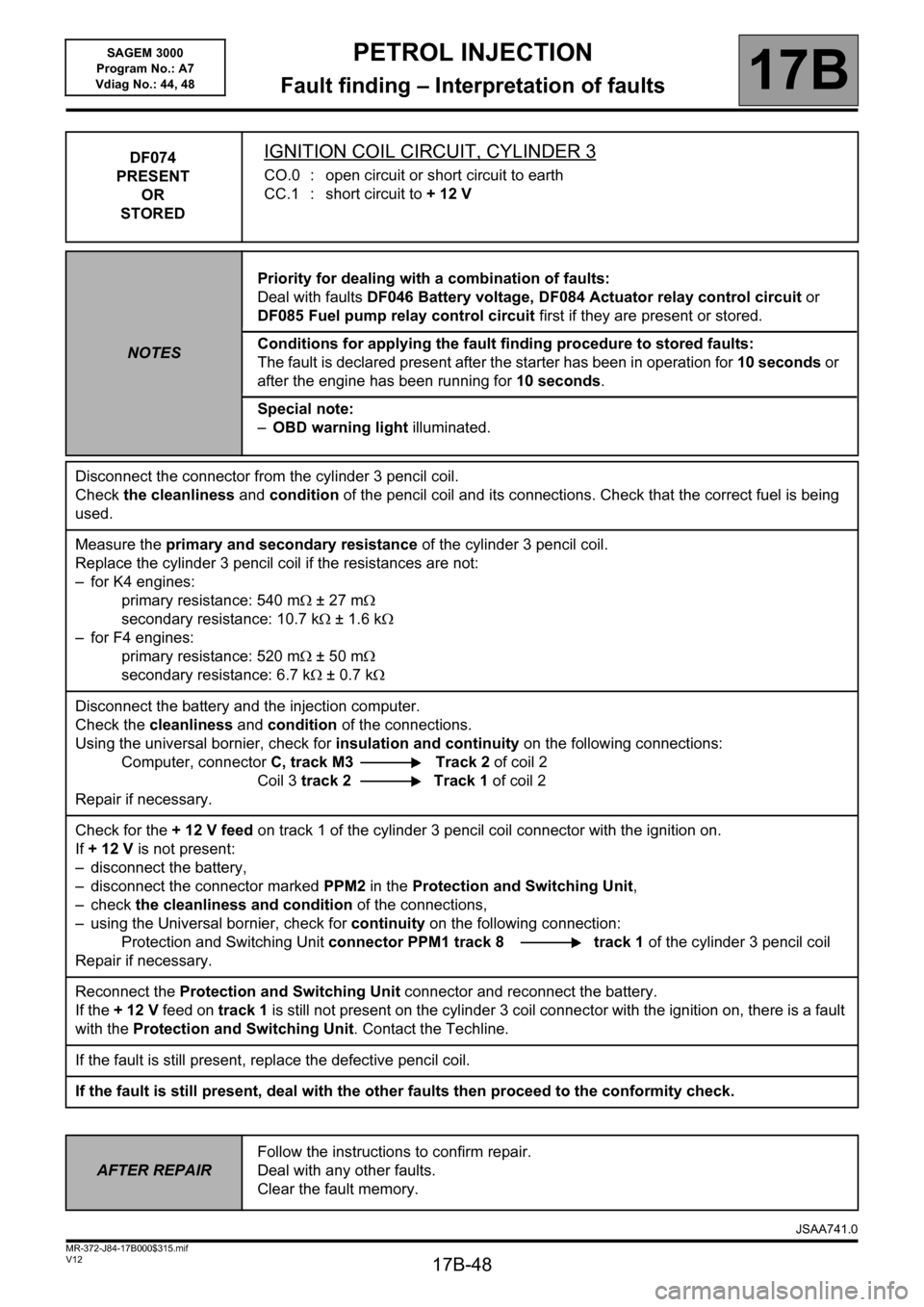
PETROL INJECTION
Fault finding – Interpretation of faults17B
17B-48V12 MR-372-J84-17B000$315.mif
SAGEM 3000
Program No.: A7
Vdiag No.: 44, 48
DF074
PRESENT
OR
STOREDIGNITION COIL CIRCUIT, CYLINDER 3
CO.0 : open circuit or short circuit to earth
CC.1 : short circuit to + 12 V
NOTESPriority for dealing with a combination of faults:
Deal with faults DF046 Battery voltage, DF084 Actuator relay control circuit or
DF085 Fuel pump relay control circuit first if they are present or stored.
Conditions for applying the fault finding procedure to stored faults:
The fault is declared present after the starter has been in operation for 10 seconds or
after the engine has been running for 10 seconds.
Special note:
–OBD warning light illuminated.
Disconnect the connector from the cylinder 3 pencil coil.
Check the cleanliness and condition of the pencil coil and its connections. Check that the correct fuel is being
used.
Measure the primary and secondary resistance of the cylinder 3 pencil coil.
Replace the cylinder 3 pencil coil if the resistances are not:
– for K4 engines:
primary resistance: 540 m ± 27 m
secondary resistance: 10.7 k ± 1.6 k
– for F4 engines:
primary resistance: 520 m ± 50 m
secondary resistance: 6.7 k ± 0.7 k
Disconnect the battery and the injection computer.
Check the cleanliness and condition of the connections.
Using the universal bornier, check for insulation and continuity on the following connections:
Computer, connector C, track M3 Track 2 of coil 2
Coil 3 track 2 Track 1 of coil 2
Repair if necessary.
Check for the + 12 V feed on track 1 of the cylinder 3 pencil coil connector with the ignition on.
If +12V is not present:
– disconnect the battery,
– disconnect the connector marked PPM2 in the Protection and Switching Unit,
–check the cleanliness and condition of the connections,
– using the Universal bornier, check for continuity on the following connection:
Protection and Switching Unit connector PPM1 track 8 track 1 of the cylinder 3 pencil coil
Repair if necessary.
Reconnect the Protection and Switching Unit connector and reconnect the battery.
If the + 12 V feed on track 1 is still not present on the cylinder 3 coil connector with the ignition on, there is a fault
with the Protection and Switching Unit. Contact the Techline.
If the fault is still present, replace the defective pencil coil.
If the fault is still present, deal with the other faults then proceed to the conformity check.
AFTER REPAIRFollow the instructions to confirm repair.
Deal with any other faults.
Clear the fault memory.
JSAA741.0
Page 49 of 181
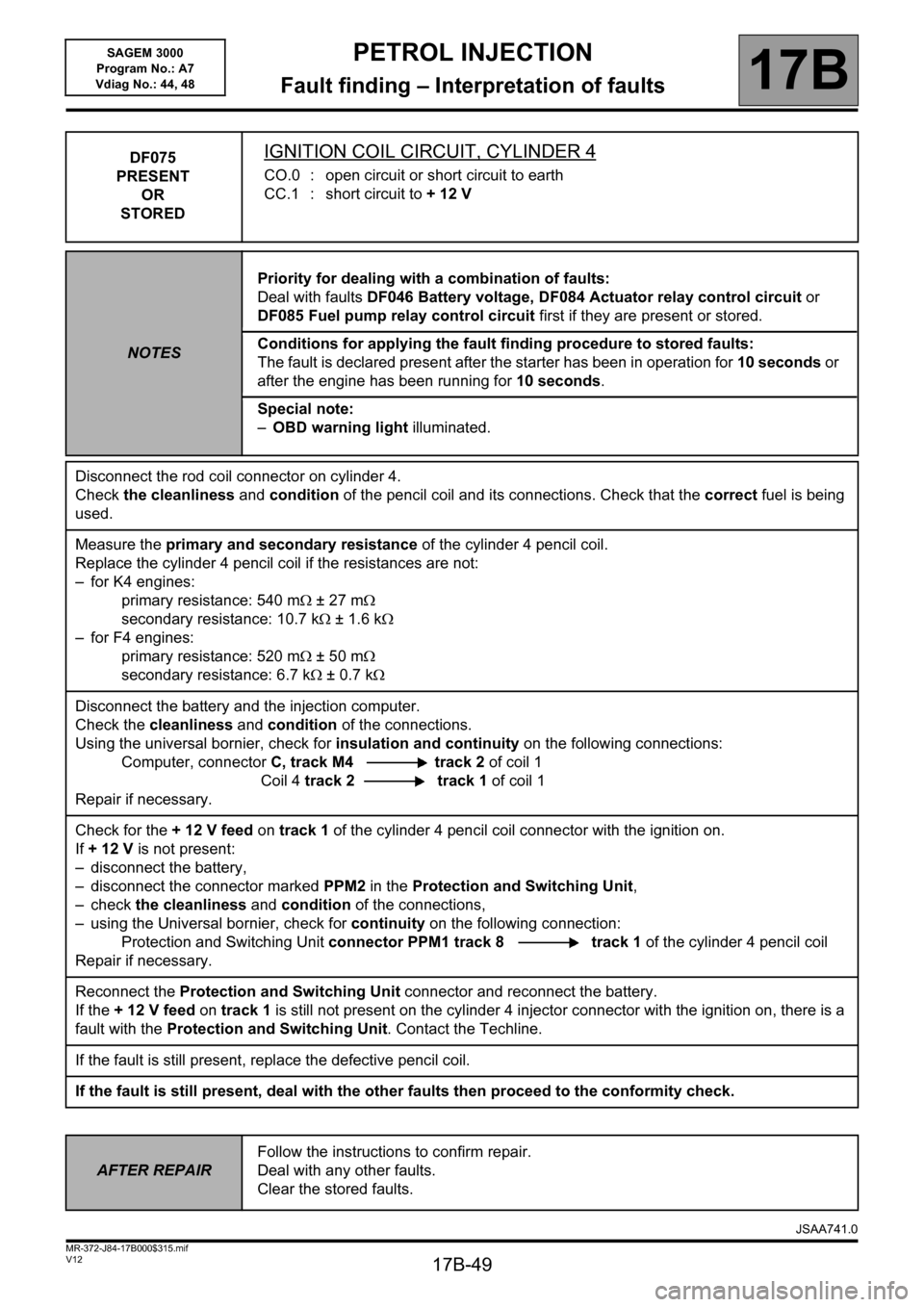
PETROL INJECTION
Fault finding – Interpretation of faults17B
17B-49V12 MR-372-J84-17B000$315.mif
SAGEM 3000
Program No.: A7
Vdiag No.: 44, 48
DF075
PRESENT
OR
STOREDIGNITION COIL CIRCUIT, CYLINDER 4
CO.0 : open circuit or short circuit to earth
CC.1 : short circuit to + 12 V
NOTESPriority for dealing with a combination of faults:
Deal with faults DF046 Battery voltage, DF084 Actuator relay control circuit or
DF085 Fuel pump relay control circuit first if they are present or stored.
Conditions for applying the fault finding procedure to stored faults:
The fault is declared present after the starter has been in operation for 10 seconds or
after the engine has been running for 10 seconds.
Special note:
–OBD warning light illuminated.
Disconnect the rod coil connector on cylinder 4.
Check the cleanliness and condition of the pencil coil and its connections. Check that the correct fuel is being
used.
Measure the primary and secondary resistance of the cylinder 4 pencil coil.
Replace the cylinder 4 pencil coil if the resistances are not:
– for K4 engines:
primary resistance: 540 m ± 27 m
secondary resistance: 10.7 k ± 1.6 k
– for F4 engines:
primary resistance: 520 m ± 50 m
secondary resistance: 6.7 k ± 0.7 k
Disconnect the battery and the injection computer.
Check the cleanliness and condition of the connections.
Using the universal bornier, check for insulation and continuity on the following connections:
Computer, connector C, track M4 track 2 of coil 1
Coil 4 track 2 track 1 of coil 1
Repair if necessary.
Check for the + 12 V feed on track 1 of the cylinder 4 pencil coil connector with the ignition on.
If +12V is not present:
– disconnect the battery,
– disconnect the connector marked PPM2 in the Protection and Switching Unit,
–check the cleanliness and condition of the connections,
– using the Universal bornier, check for continuity on the following connection:
Protection and Switching Unit connector PPM1 track 8 track 1 of the cylinder 4 pencil coil
Repair if necessary.
Reconnect the Protection and Switching Unit connector and reconnect the battery.
If the + 12 V feed on track 1 is still not present on the cylinder 4 injector connector with the ignition on, there is a
fault with the Protection and Switching Unit. Contact the Techline.
If the fault is still present, replace the defective pencil coil.
If the fault is still present, deal with the other faults then proceed to the conformity check.
AFTER REPAIRFollow the instructions to confirm repair.
Deal with any other faults.
Clear the stored faults.
JSAA741.0
Page 50 of 181
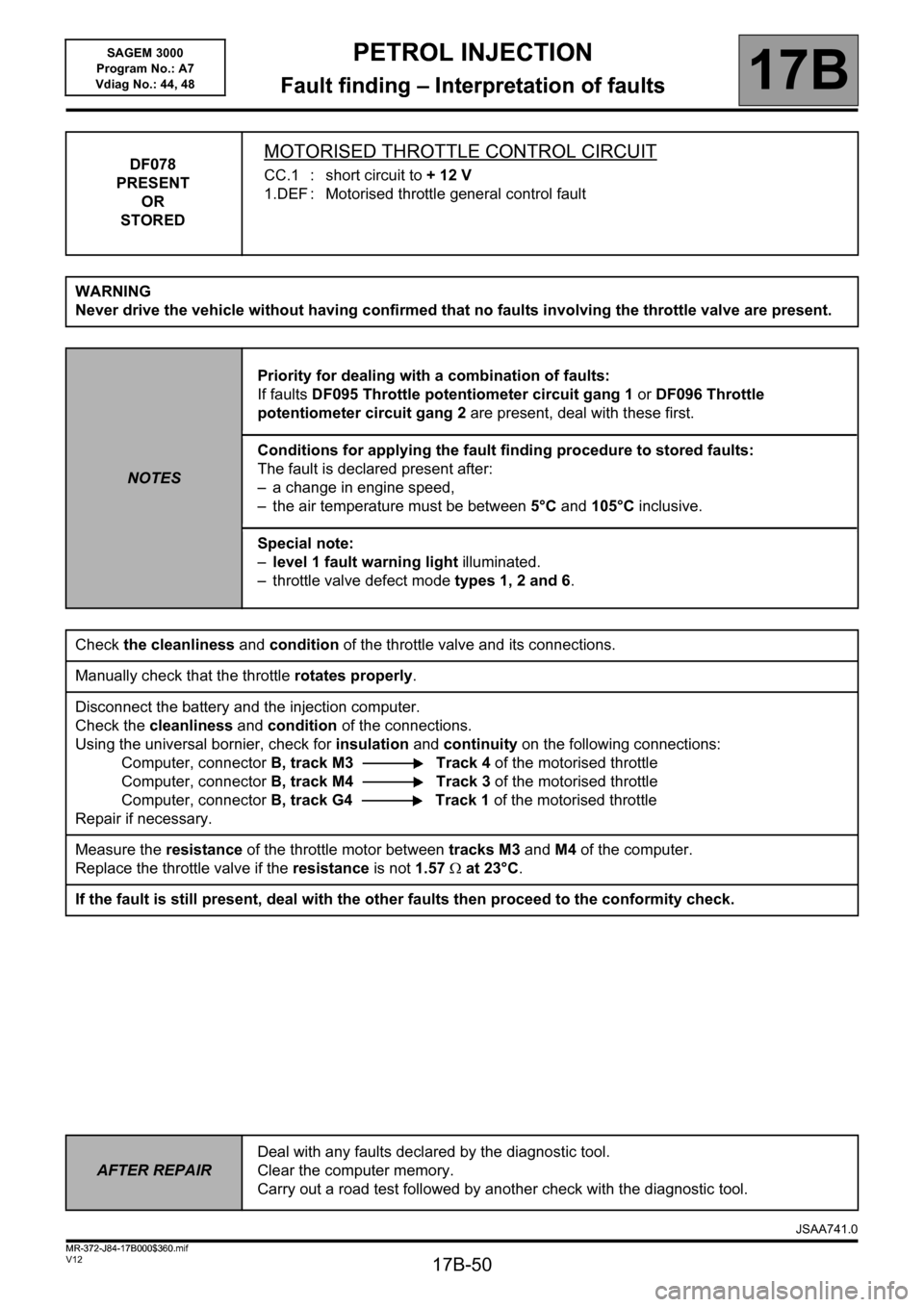
PETROL INJECTION
Fault finding – Interpretation of faults17B
17B-50V12 MR-372-J84-17B000$360.mif
SAGEM 3000
Program No.: A7
Vdiag No.: 44, 48PETROL INJECTION
Fault finding – Interpretation of faults
DF078
PRESENT
OR
STOREDMOTORISED THROTTLE CONTROL CIRCUIT
CC.1 : short circuit to + 12 V
1.DEF : Motorised throttle general control fault
WARNING
Never drive the vehicle without having confirmed that no faults involving the throttle valve are present.
NOTESPriority for dealing with a combination of faults:
If faults DF095 Throttle potentiometer circuit gang 1 or DF096 Throttle
potentiometer circuit gang 2 are present, deal with these first.
Conditions for applying the fault finding procedure to stored faults:
The fault is declared present after:
– a change in engine speed,
– the air temperature must be between 5°C and 105°C inclusive.
Special note:
–level 1 fault warning light illuminated.
– throttle valve defect mode types 1, 2 and 6.
Check the cleanliness and condition of the throttle valve and its connections.
Manually check that the throttle rotates properly.
Disconnect the battery and the injection computer.
Check the cleanliness and condition of the connections.
Using the universal bornier, check for insulation and continuity on the following connections:
Computer, connector B, track M3 Track 4 of the motorised throttle
Computer, connector B, track M4 Track 3 of the motorised throttle
Computer, connector B, track G4 Track 1 of the motorised throttle
Repair if necessary.
Measure the resistance of the throttle motor between tracks M3 and M4 of the computer.
Replace the throttle valve if the resistance is not 1.57 at 23°C.
If the fault is still present, deal with the other faults then proceed to the conformity check.
AFTER REPAIRDeal with any faults declared by the diagnostic tool.
Clear the computer memory.
Carry out a road test followed by another check with the diagnostic tool.
JSAA741.0
MR-372-J84-17B000$360.mif
Page 51 of 181
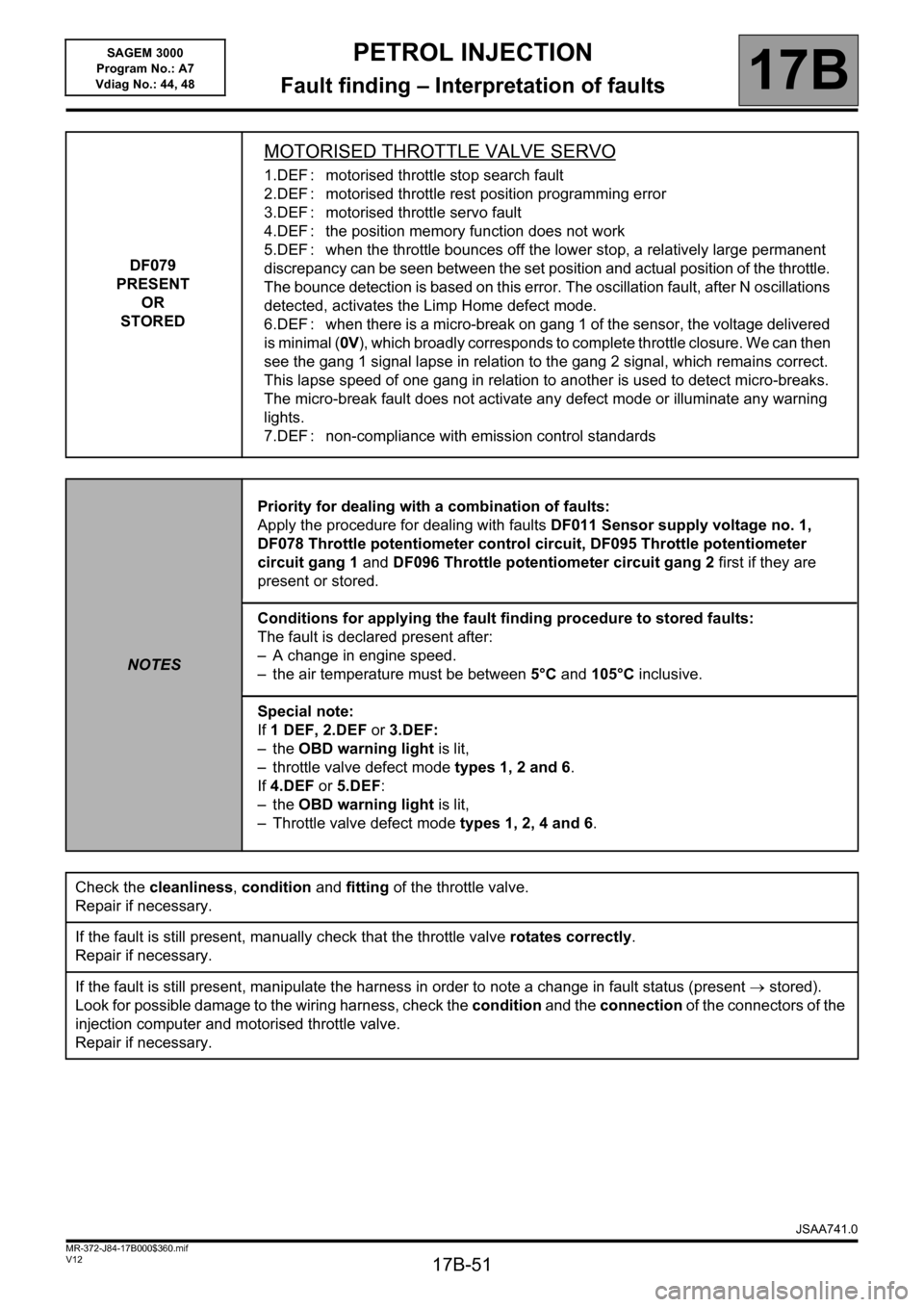
PETROL INJECTION
Fault finding – Interpretation of faults17B
17B-51V12 MR-372-J84-17B000$360.mif
SAGEM 3000
Program No.: A7
Vdiag No.: 44, 48
DF079
PRESENT
OR
STORED
MOTORISED THROTTLE VALVE SERVO
1.DEF : motorised throttle stop search fault
2.DEF : motorised throttle rest position programming error
3.DEF : motorised throttle servo fault
4.DEF : the position memory function does not work
5.DEF : when the throttle bounces off the lower stop, a relatively large permanent
discrepancy can be seen between the set position and actual position of the throttle.
The bounce detection is based on this error. The oscillation fault, after N oscillations
detected, activates the Limp Home defect mode.
6.DEF : when there is a micro-break on gang 1 of the sensor, the voltage delivered
is minimal (0V), which broadly corresponds to complete throttle closure. We can then
see the gang 1 signal lapse in relation to the gang 2 signal, which remains correct.
This lapse speed of one gang in relation to another is used to detect micro-breaks.
The micro-break fault does not activate any defect mode or illuminate any warning
lights.
7.DEF : non-compliance with emission control standards
NOTESPriority for dealing with a combination of faults:
Apply the procedure for dealing with faults DF011 Sensor supply voltage no. 1,
DF078 Throttle potentiometer control circuit, DF095 Throttle potentiometer
circuit gang 1 and DF096 Throttle potentiometer circuit gang 2 first if they are
present or stored.
Conditions for applying the fault finding procedure to stored faults:
The fault is declared present after:
– A change in engine speed.
– the air temperature must be between 5°C and 105°C inclusive.
Special note:
If 1 DEF, 2.DEF or 3.DEF:
– the OBD warning light is lit,
– throttle valve defect mode types 1, 2 and 6.
If 4.DEF or 5.DEF:
– the OBD warning light is lit,
– Throttle valve defect mode types 1, 2, 4 and 6.
Check the cleanliness, condition and fitting of the throttle valve.
Repair if necessary.
If the fault is still present, manually check that the throttle valve rotates correctly.
Repair if necessary.
If the fault is still present, manipulate the harness in order to note a change in fault status (present stored).
Look for possible damage to the wiring harness, check the condition and the connection of the connectors of the
injection computer and motorised throttle valve.
Repair if necessary.
JSAA741.0
Page 55 of 181
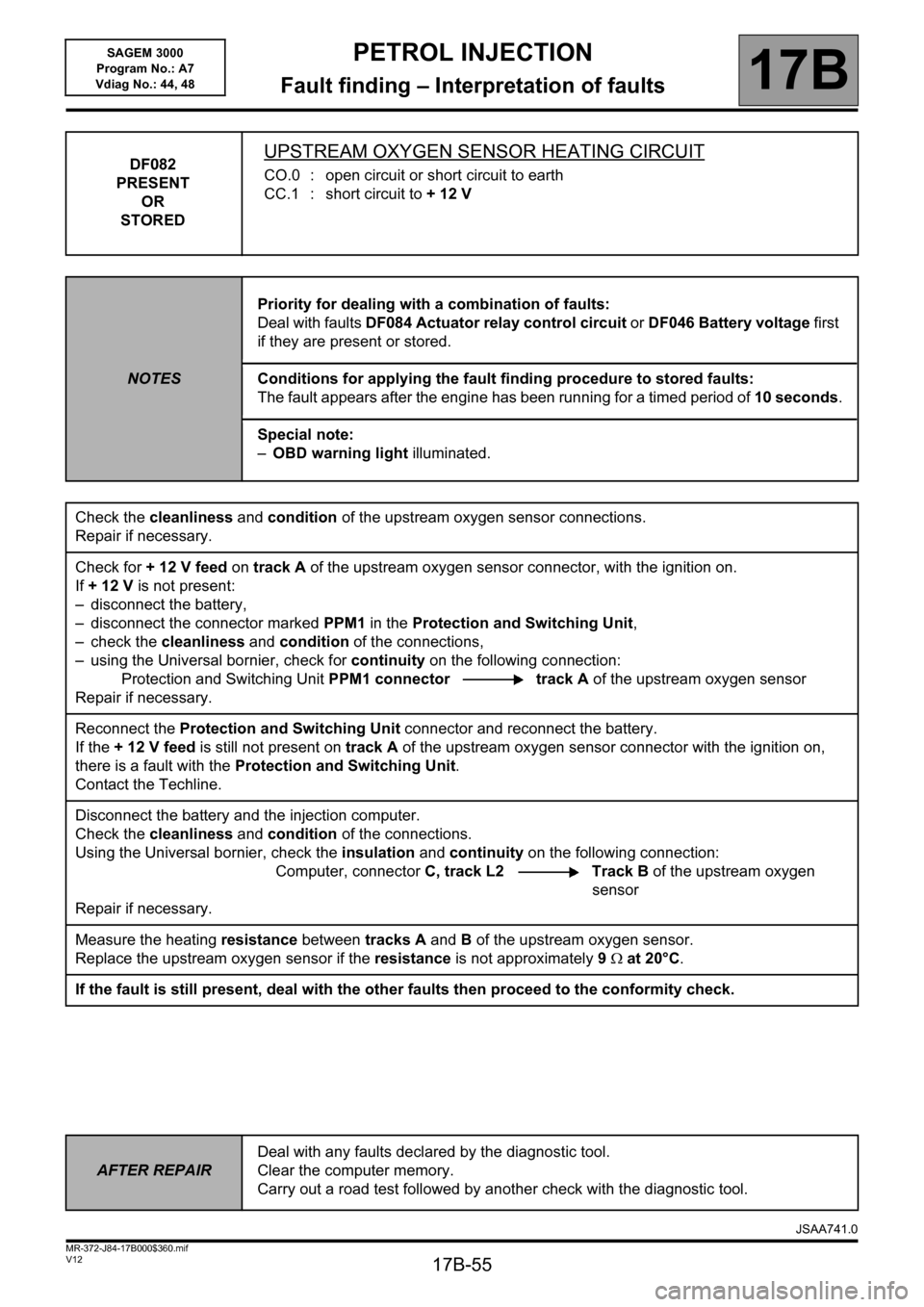
PETROL INJECTION
Fault finding – Interpretation of faults17B
17B-55V12 MR-372-J84-17B000$360.mif
SAGEM 3000
Program No.: A7
Vdiag No.: 44, 48
DF082
PRESENT
OR
STOREDUPSTREAM OXYGEN SENSOR HEATING CIRCUIT
CO.0 : open circuit or short circuit to earth
CC.1 : short circuit to + 12 V
NOTESPriority for dealing with a combination of faults:
Deal with faults DF084 Actuator relay control circuit or DF046 Battery voltage first
if they are present or stored.
Conditions for applying the fault finding procedure to stored faults:
The fault appears after the engine has been running for a timed period of 10 seconds.
Special note:
–OBD warning light illuminated.
Check the cleanliness and condition of the upstream oxygen sensor connections.
Repair if necessary.
Check for + 12 V feed on track A of the upstream oxygen sensor connector, with the ignition on.
If +12V is not present:
– disconnect the battery,
– disconnect the connector marked PPM1 in the Protection and Switching Unit,
– check the cleanliness and condition of the connections,
– using the Universal bornier, check for continuity on the following connection:
Protection and Switching Unit PPM1 connector track A of the upstream oxygen sensor
Repair if necessary.
Reconnect the Protection and Switching Unit connector and reconnect the battery.
If the + 12 V feed is still not present on track A of the upstream oxygen sensor connector with the ignition on,
there is a fault with the Protection and Switching Unit.
Contact the Techline.
Disconnect the battery and the injection computer.
Check the cleanliness and condition of the connections.
Using the Universal bornier, check the insulation and continuity on the following connection:
Computer, connector C, track L2 Track B of the upstream oxygen
sensor
Repair if necessary.
Measure the heating resistance between tracks A and B of the upstream oxygen sensor.
Replace the upstream oxygen sensor if the resistance is not approximately 9 at 20°C.
If the fault is still present, deal with the other faults then proceed to the conformity check.
AFTER REPAIRDeal with any faults declared by the diagnostic tool.
Clear the computer memory.
Carry out a road test followed by another check with the diagnostic tool.
JSAA741.0
Page 56 of 181
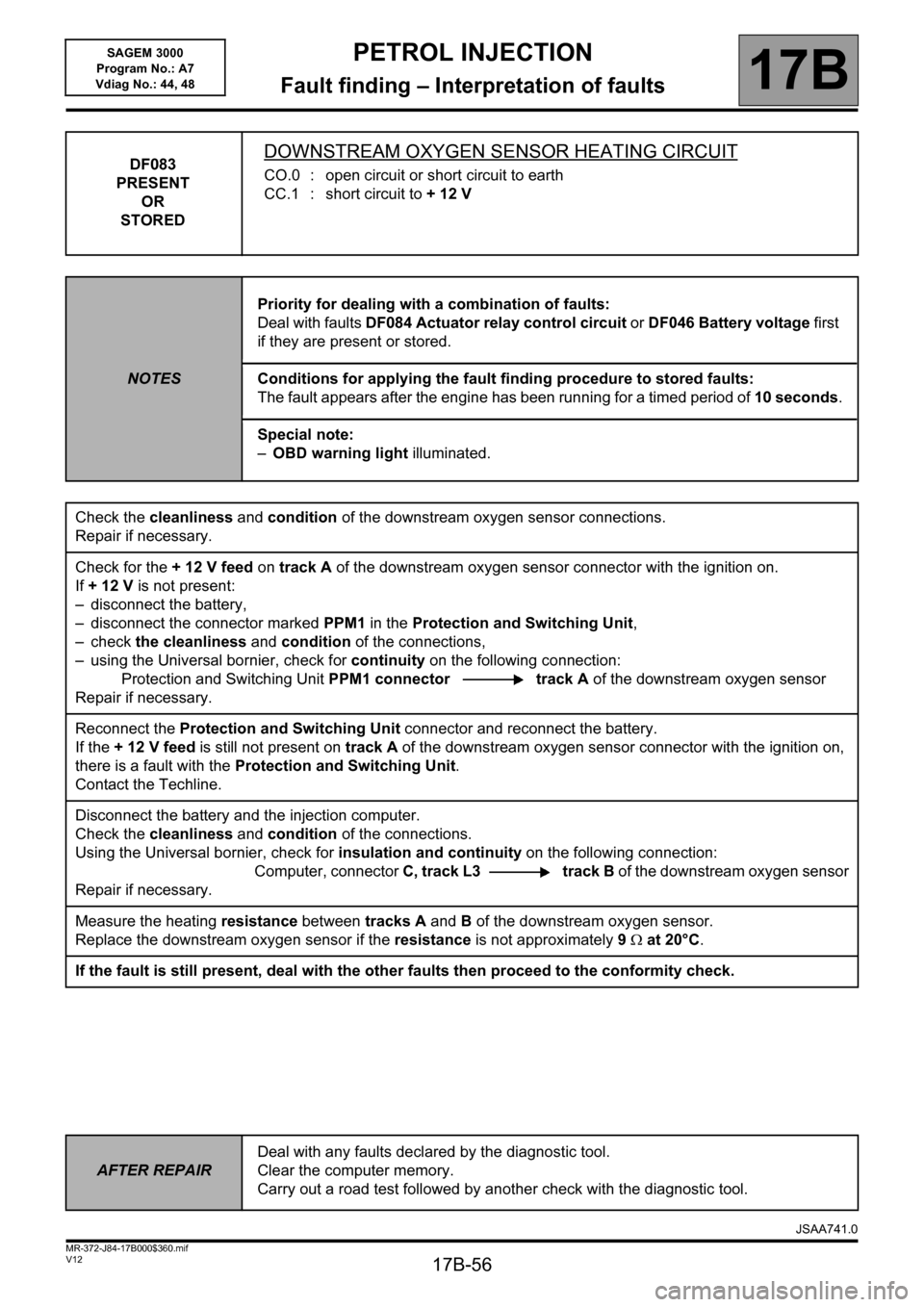
PETROL INJECTION
Fault finding – Interpretation of faults17B
17B-56V12 MR-372-J84-17B000$360.mif
SAGEM 3000
Program No.: A7
Vdiag No.: 44, 48
DF083
PRESENT
OR
STOREDDOWNSTREAM OXYGEN SENSOR HEATING CIRCUIT
CO.0 : open circuit or short circuit to earth
CC.1 : short circuit to + 12 V
NOTESPriority for dealing with a combination of faults:
Deal with faults DF084 Actuator relay control circuit or DF046 Battery voltage first
if they are present or stored.
Conditions for applying the fault finding procedure to stored faults:
The fault appears after the engine has been running for a timed period of 10 seconds.
Special note:
–OBD warning light illuminated.
Check the cleanliness and condition of the downstream oxygen sensor connections.
Repair if necessary.
Check for the + 12 V feed on track A of the downstream oxygen sensor connector with the ignition on.
If +12V is not present:
– disconnect the battery,
– disconnect the connector marked PPM1 in the Protection and Switching Unit,
–check the cleanliness and condition of the connections,
– using the Universal bornier, check for continuity on the following connection:
Protection and Switching Unit PPM1 connector track A of the downstream oxygen sensor
Repair if necessary.
Reconnect the Protection and Switching Unit connector and reconnect the battery.
If the + 12 V feed is still not present on track A of the downstream oxygen sensor connector with the ignition on,
there is a fault with the Protection and Switching Unit.
Contact the Techline.
Disconnect the battery and the injection computer.
Check the cleanliness and condition of the connections.
Using the Universal bornier, check for insulation and continuity on the following connection:
Computer, connector C, track L3 track B of the downstream oxygen sensor
Repair if necessary.
Measure the heating resistance between tracks A and B of the downstream oxygen sensor.
Replace the downstream oxygen sensor if the resistance is not approximately 9 at 20°C.
If the fault is still present, deal with the other faults then proceed to the conformity check.
AFTER REPAIRDeal with any faults declared by the diagnostic tool.
Clear the computer memory.
Carry out a road test followed by another check with the diagnostic tool.
JSAA741.0
Page 59 of 181

PETROL INJECTION
Fault finding – Interpretation of faults17B
17B-59V12 MR-372-J84-17B000$360.mif
SAGEM 3000
Program No.: A7
Vdiag No.: 44, 48
DF086
PRESENT
OR
STOREDCOOLANT PUMP RELAY CONTROL CIRCUIT
CO : open circuit
CO.0 : short circuit to earth
CC.1 : short circuit to + 12 V
NOTESConditions for applying the fault finding procedure to stored faults:
The fault is declared present with the engine running.
IMPORTANT
Check that when the coolant pump is active, the coolant circulates in reverse order to
the usual circulation.
Check the cleanliness, condition and fitting of the coolant pump.
Top up the coolant if necessary.
If the fault is still present, manipulate the harness to see if the status changes.
Look for any harness damage, and check the condition and connection points of the injection computer and the
coolant pump connectors.
Repair if necessary.
If the fault is still present, check for +12V on track 2 of the coolant pump.
If the +12V is not present on track 2 of the coolant pump, check the following connection for insulation,
continuity and the absence of interference resistance:
Coolant pump track 2 track 1, connector PPM1, of the Protection and Switching Unit
Repair if necessary.
If the fault is still present, check the insulation, continuity and the absence of interference resistance on the
following connections:
Computer, connector C, track L4 track 1 of the coolant pump
Repair if necessary.
If the fault is still present, check that the resistance between tracks 1 and 2 of the coolant pump is neither zero
nor infinite.
Replace the coolant pump if necessary.
If the fault is still present, deal with the other faults then proceed to the conformity check.
AFTER REPAIRFollow the instructions to confirm repair.
Deal with any other faults.
Clear the stored faults.
JSAA741.0
Page 60 of 181
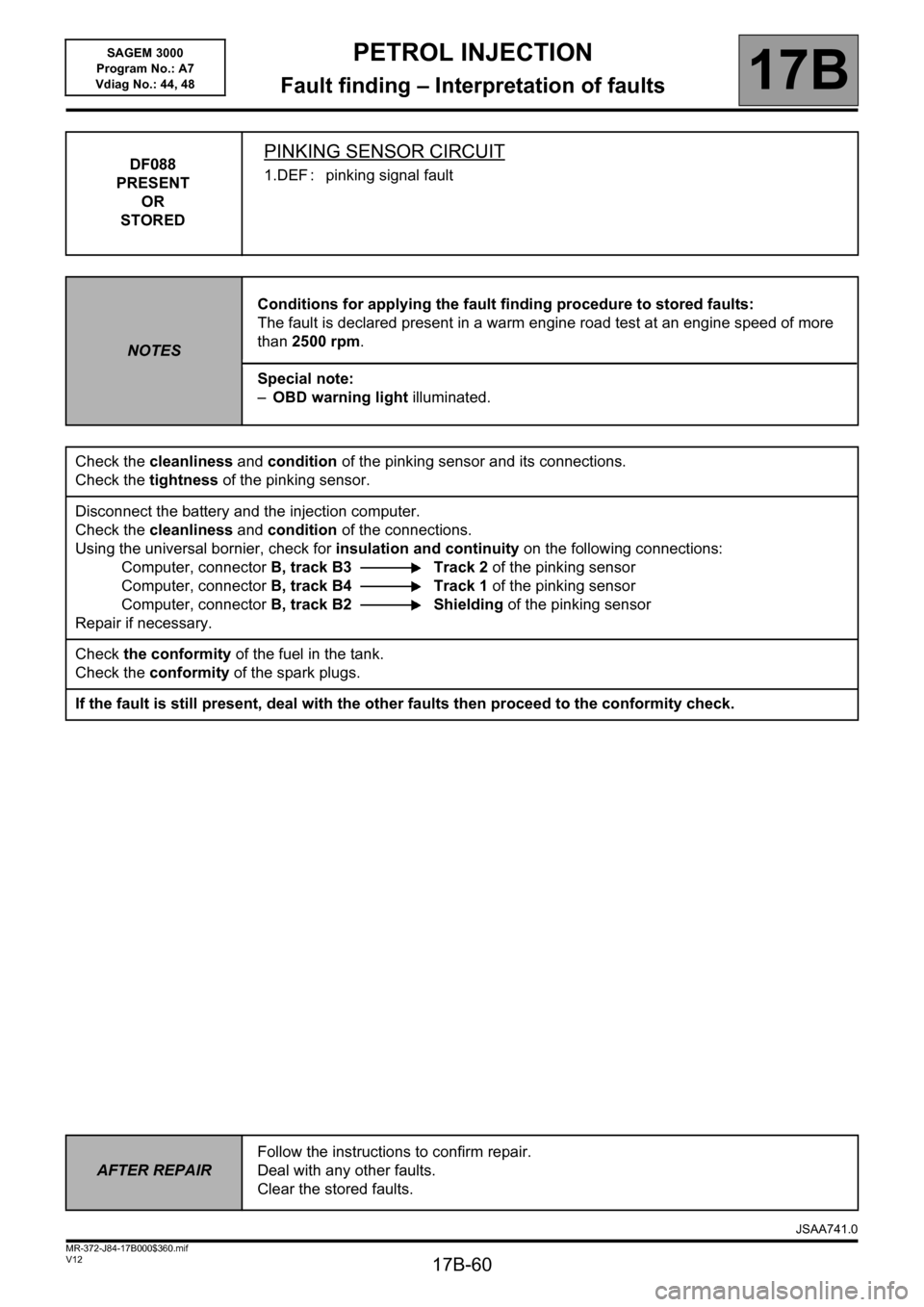
PETROL INJECTION
Fault finding – Interpretation of faults17B
17B-60V12 MR-372-J84-17B000$360.mif
SAGEM 3000
Program No.: A7
Vdiag No.: 44, 48
DF088
PRESENT
OR
STOREDPINKING SENSOR CIRCUIT
1.DEF : pinking signal fault
NOTESConditions for applying the fault finding procedure to stored faults:
The fault is declared present in a warm engine road test at an engine speed of more
than 2500 rpm.
Special note:
–OBD warning light illuminated.
Check the cleanliness and condition of the pinking sensor and its connections.
Check the tightness of the pinking sensor.
Disconnect the battery and the injection computer.
Check the cleanliness and condition of the connections.
Using the universal bornier, check for insulation and continuity on the following connections:
Computer, connector B, track B3 Track 2 of the pinking sensor
Computer, connector B, track B4 Track 1 of the pinking sensor
Computer, connectorB, track B2 Shielding of the pinking sensor
Repair if necessary.
Check the conformity of the fuel in the tank.
Check the conformity of the spark plugs.
If the fault is still present, deal with the other faults then proceed to the conformity check.
AFTER REPAIRFollow the instructions to confirm repair.
Deal with any other faults.
Clear the stored faults.
JSAA741.0