engine RENAULT TWINGO 2009 2.G Electrical Equipment - Petrol Injection Repair Manual
[x] Cancel search | Manufacturer: RENAULT, Model Year: 2009, Model line: TWINGO, Model: RENAULT TWINGO 2009 2.GPages: 348
Page 76 of 348
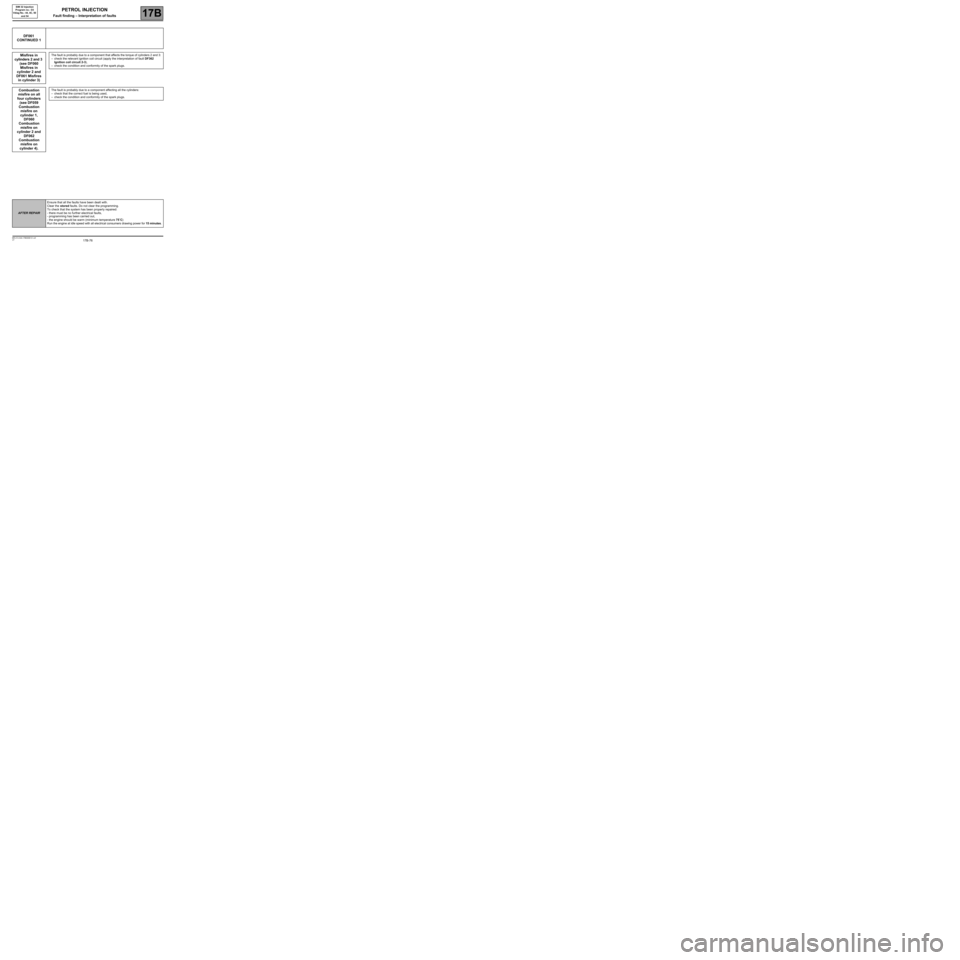
17B-76V7 MR-413-X44-17B000$131.mif
PETROL INJECTION
Fault finding – Interpretation of faults17B
SIM 32 Injection
Program no.: D3
Vdiag No.: 44, 4C, 50
and 54
DF061
CONTINUED 1
Misfires in
cylinders 2 and 3
(see DF060
Misfires in
cylinder 2 and
DF061 Misfires
in cylinder 3)
The fault is probably due to a component that affects the torque of cylinders 2 and 3:
–check the relevant ignition coil circuit (apply the interpretation of fault DF362
Ignition coil circuit 2-3),
–check the condition and conformity of the spark plugs.
Combustion
misfire on all
four cylinders
(see DF059
Combustion
misfire on
cylinder 1,
DF060
Combustion
misfire on
cylinder 2 and
DF062
Combustion
misfire on
cylinder 4).The fault is probably due to a component affecting all the cylinders:
–check that the correct fuel is being used,
–check the condition and conformity of the spark plugs.
AFTER REPAIREnsure that all the faults have been dealt with.
Clear the stored faults. Do not clear the programming.
To check that the system has been properly repaired:
- there must be no further electrical faults,
- programming has been carried out,
- the engine should be warm (minimum temperature 75˚C)
Run the engine at idle speed with all electrical consumers drawing power for 15 minutes.
Page 77 of 348
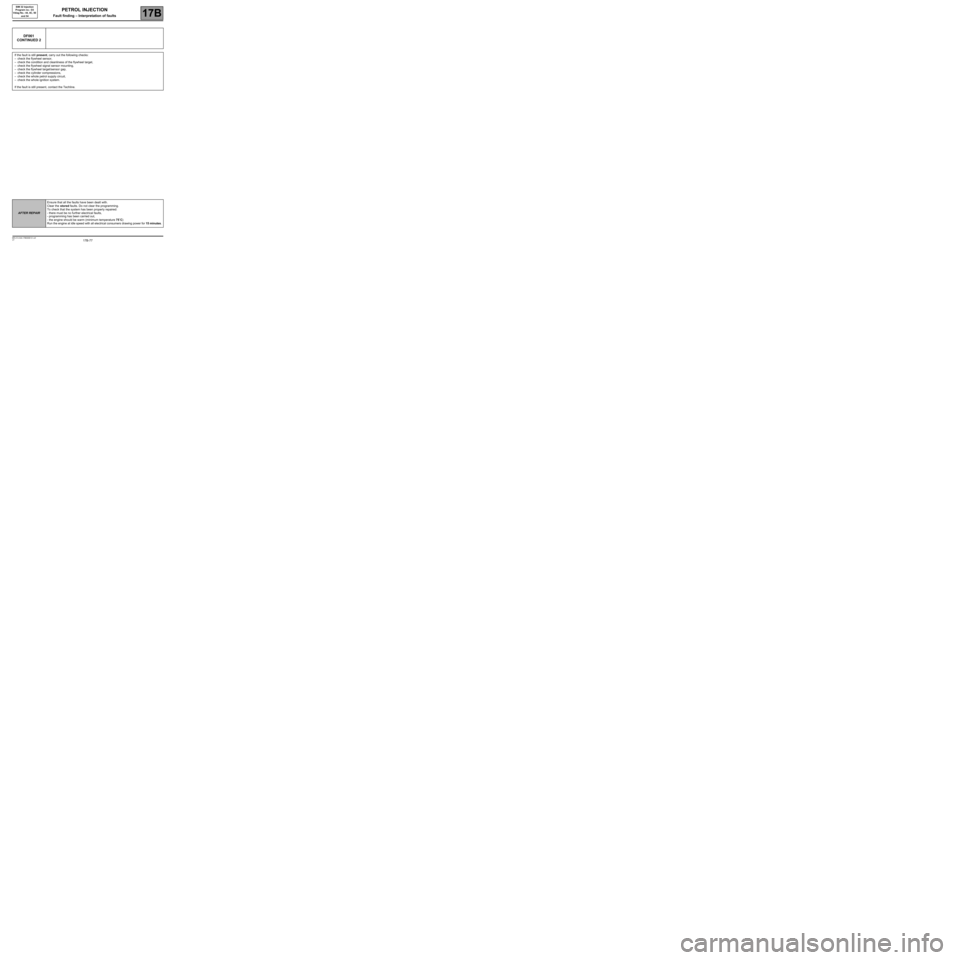
17B-77V7 MR-413-X44-17B000$131.mif
PETROL INJECTION
Fault finding – Interpretation of faults17B
SIM 32 Injection
Program no.: D3
Vdiag No.: 44, 4C, 50
and 54
DF061
CONTINUED 2
If the fault is still present, carry out the following checks:
–check the flywheel sensor,
–check the condition and cleanliness of the flywheel target,
–check the flywheel signal sensor mounting,
–check the flywheel target/sensor gap,
–check the cylinder compressions,
–check the whole petrol supply circuit,
–check the whole ignition system.
If the fault is still present, contact the Techline.
AFTER REPAIREnsure that all the faults have been dealt with.
Clear the stored faults. Do not clear the programming.
To check that the system has been properly repaired:
- there must be no further electrical faults,
- programming has been carried out,
- the engine should be warm (minimum temperature 75˚C)
Run the engine at idle speed with all electrical consumers drawing power for 15 minutes.
Page 78 of 348
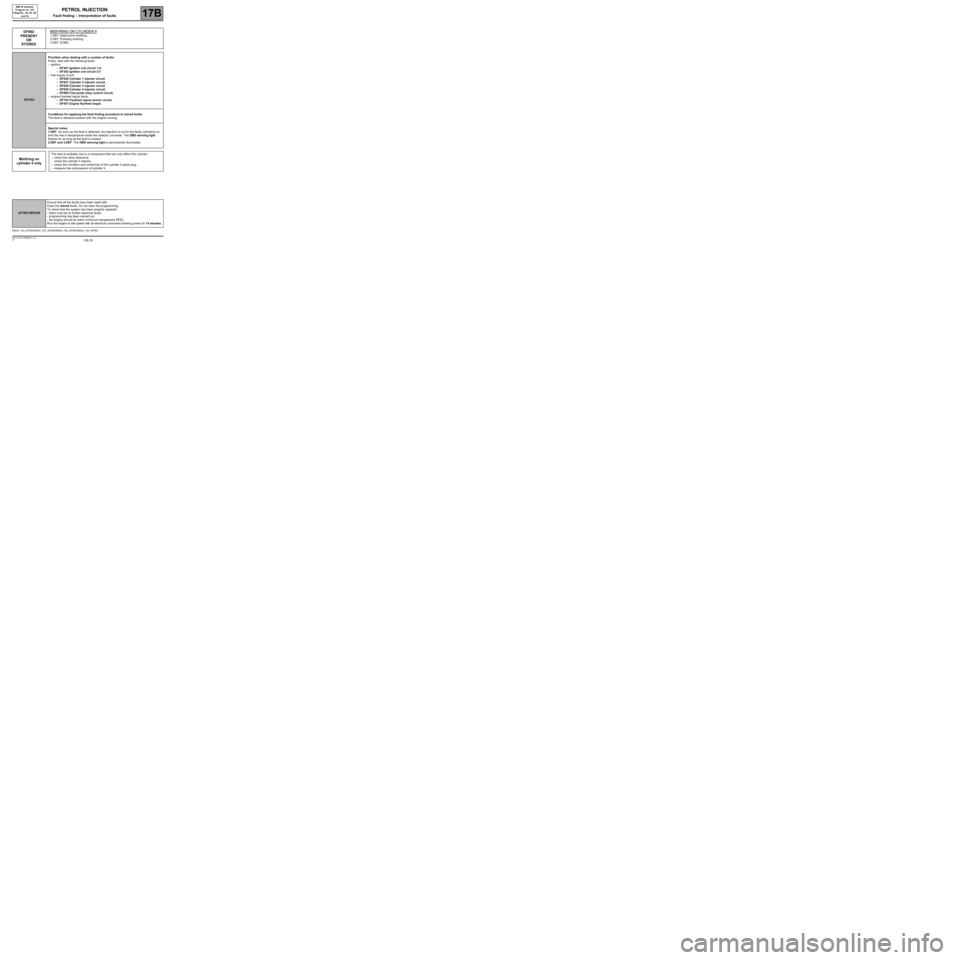
17B-78V7 MR-413-X44-17B000$131.mif
PETROL INJECTION
Fault finding – Interpretation of faults17B
SIM 32 Injection
Program no.: D3
Vdiag No.: 44, 4C, 50
and 54
DF062
PRESENT
OR
STOREDMISFIRING ON CYLINDER 4
1.DEF: Destructive misfiring
2.DEF: Polluting misfiring
3.DEF: EOBD
NOTESPriorities when dealing with a number of faults:
Firstly, deal with the following faults:
–ignition:
–DF361 Ignition coil circuit 1-4,
–DF362 Ignition coil circuit 2-3
–fuel supply circuit:
–DF026 Cylinder 1 injector circuit
–DF027 Cylinder 2 injector circuit,
–DF028 Cylinder 3 injector circuit
–DF029 Cylinder 4 injector circuit,
–DF085 Fuel pump relay control circuit,
–engine flywheel signal faults:
–DF154 Flywheel signal sensor circuit,
–DF457 Engine flywheel target.
Conditions for applying the fault finding procedure to stored faults:
The fault is declared present with the engine running.
Special notes:
1.DEF: As soon as the fault is detected, the injection is cut for the faulty cylinder(s) to
limit the rise in temperature inside the catalytic converter. The OBD warning light
flashes for as long as the fault is present.
2.DEF and 3.DEF: The OBD warning light is permanently illuminated.
Misfiring on
cylinder 4 only
The fault is probably due to a component that can only affect this cylinder:
–check the valve clearance,
–check the cylinder 4 injector,
–check the condition and conformity of the cylinder 4 spark plug,
–measure the compression of cylinder 4.
SIM32_V44_DF062/SIM32_V4C_DF062/SIM32_V50_DF062/SIM32_V54_DF062
AFTER REPAIREnsure that all the faults have been dealt with.
Clear the stored faults. Do not clear the programming.
To check that the system has been properly repaired:
- there must be no further electrical faults,
- programming has been carried out,
- the engine should be warm (minimum temperature 75˚C)
Run the engine at idle speed with all electrical consumers drawing power for 15 minutes.
Page 79 of 348
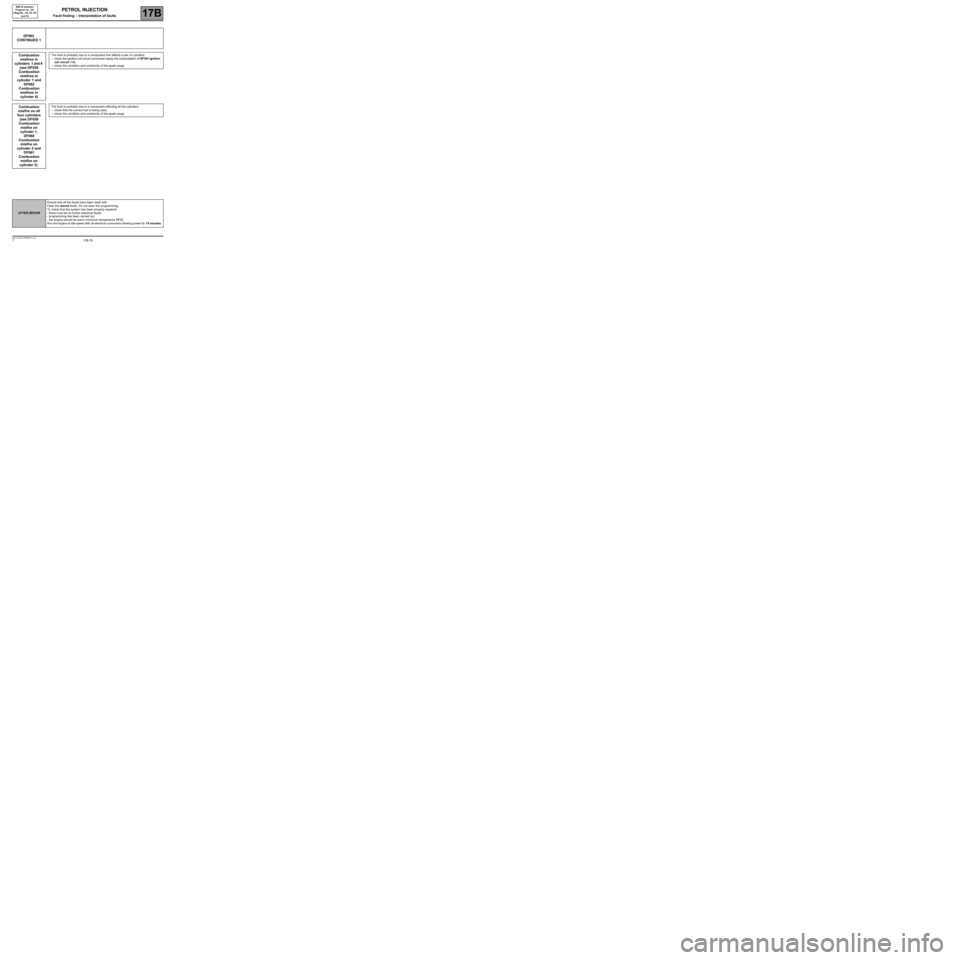
17B-79V7 MR-413-X44-17B000$131.mif
PETROL INJECTION
Fault finding – Interpretation of faults17B
SIM 32 Injection
Program no.: D3
Vdiag No.: 44, 4C, 50
and 54
DF062
CONTINUED 1
Combustion
misfires in
cylinders 1 and 4
(see DF059
Combustion
misfires in
cylinder 1 and
DF062
Combustion
misfires in
cylinder 4)
The fault is probably due to a component that affects a pair of cylinders:
–check the ignition coil circuit concerned (apply the interpretation of DF361 Ignition
coil circuit 1-4),
–check the condition and conformity of the spark plugs.
Combustion
misfire on all
four cylinders
(see DF059
Combustion
misfire on
cylinder 1,
DF060
Combustion
misfire on
cylinder 2 and
DF061
Combustion
misfire on
cylinder 3).The fault is probably due to a component affecting all the cylinders:
–check that the correct fuel is being used,
–check the condition and conformity of the spark plugs.
AFTER REPAIREnsure that all the faults have been dealt with.
Clear the stored faults. Do not clear the programming.
To check that the system has been properly repaired:
- there must be no further electrical faults,
- programming has been carried out,
- the engine should be warm (minimum temperature 75˚C)
Run the engine at idle speed with all electrical consumers drawing power for 15 minutes.
Page 80 of 348
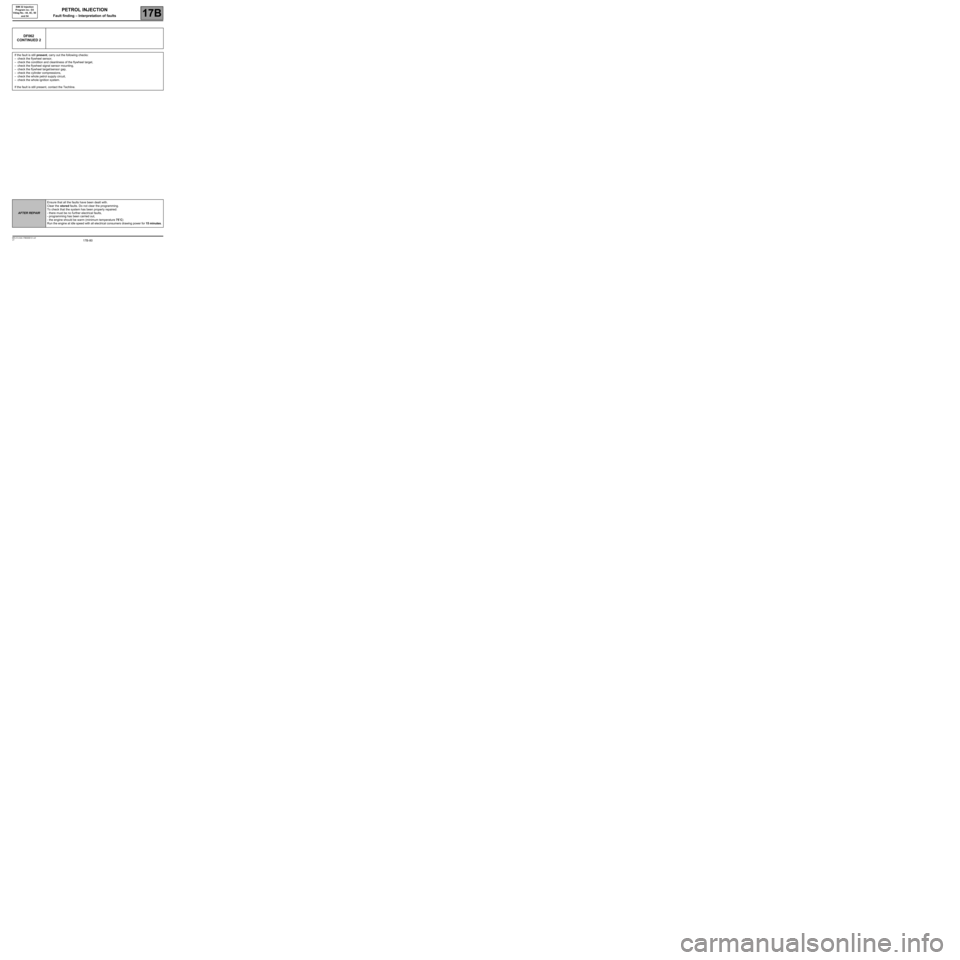
17B-80V7 MR-413-X44-17B000$131.mif
PETROL INJECTION
Fault finding – Interpretation of faults17B
SIM 32 Injection
Program no.: D3
Vdiag No.: 44, 4C, 50
and 54
DF062
CONTINUED 2
If the fault is still present, carry out the following checks:
–check the flywheel sensor,
–check the condition and cleanliness of the flywheel target,
–check the flywheel signal sensor mounting,
–check the flywheel target/sensor gap,
–check the cylinder compressions,
–check the whole petrol supply circuit,
–check the whole ignition system.
If the fault is still present, contact the Techline.
AFTER REPAIREnsure that all the faults have been dealt with.
Clear the stored faults. Do not clear the programming.
To check that the system has been properly repaired:
- there must be no further electrical faults,
- programming has been carried out,
- the engine should be warm (minimum temperature 75˚C)
Run the engine at idle speed with all electrical consumers drawing power for 15 minutes.
Page 81 of 348
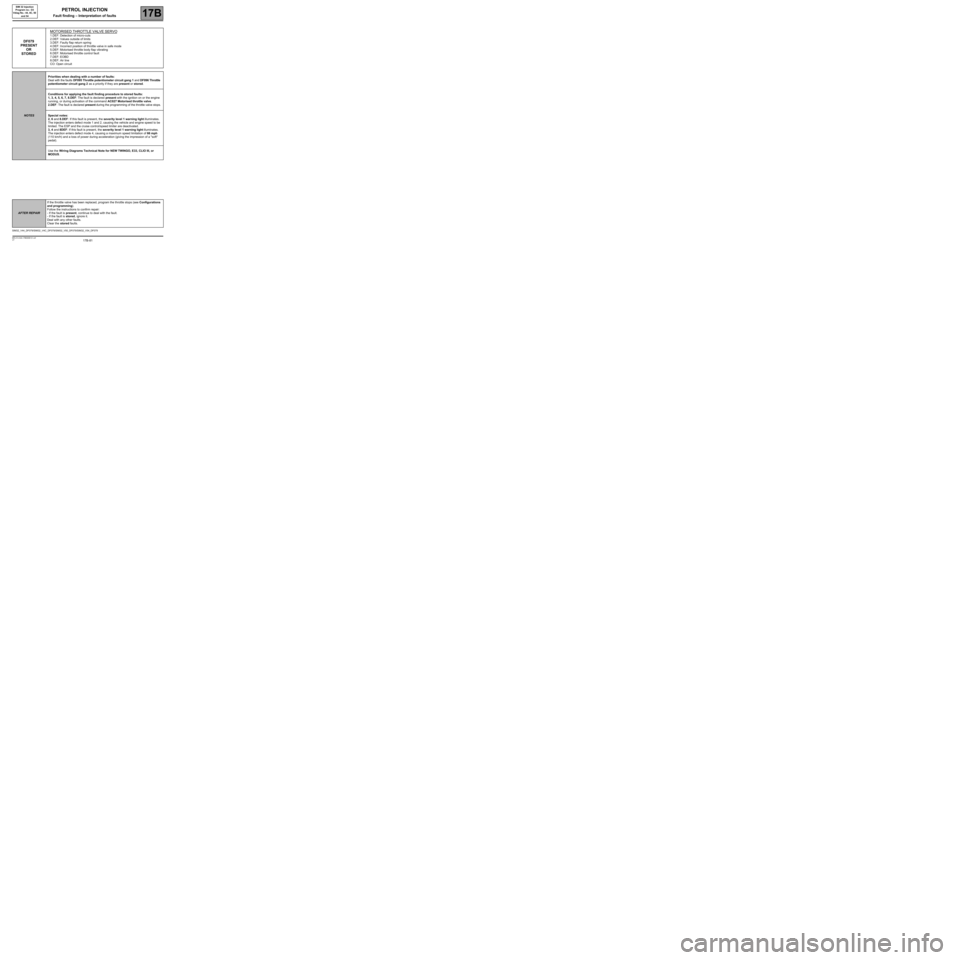
17B-81V7 MR-413-X44-17B000$131.mif
PETROL INJECTION
Fault finding – Interpretation of faults17B
SIM 32 Injection
Program no.: D3
Vdiag No.: 44, 4C, 50
and 54
DF079
PRESENT
OR
STOREDMOTORISED THROTTLE VALVE SERVO
1.DEF: Detection of micro-cuts
2.DEF: Values outside of limits
3.DEF: Faulty flap return spring
4.DEF: Incorrect position of throttle valve in safe mode
5.DEF: Motorised throttle body flap vibrating
6.DEF: Motorised throttle control fault
7.DEF: EOBD
8.DEF: Air line
CO: Open circuit
NOTESPriorities when dealing with a number of faults:
Deal with the faults DF095 Throttle potentiometer circuit gang 1 and DF096 Throttle
potentiometer circuit gang 2 as a priority if they are present or stored.
Conditions for applying the fault finding procedure to stored faults:
1, 3, 4, 5, 6, 7, 8.DEF: The fault is declared present with the ignition on or the engine
running, or during activation of the command AC027 Motorised throttle valve.
2.DEF: The fault is declared present during the programming of the throttle valve stops.
Special notes:
2, 6 and 8.DEF: If this fault is present, the severity level 1 warning light illuminates.
The injection enters defect mode 1 and 2, causing the vehicle and engine speed to be
limited. The ESP and the cruise control/speed limiter are deactivated.
3, 4 and 8DEF: If this fault is present, the severity level 1 warning light illuminates.
The injection enters defect mode 4, causing a maximum speed limitation of 66 mph
(110 km/h) and a loss of power during acceleration (giving the impression of a "soft"
pedal).
Use the Wiring Diagrams Technical Note for NEW TWINGO, E33, CLIO III, or
MODUS.
SIM32_V44_DF079/SIM32_V4C_DF079/SIM32_V50_DF079/SIM32_V54_DF079
AFTER REPAIRIf the throttle valve has been replaced, program the throttle stops (see Configurations
and programming).
Follow the instructions to confirm repair:
- If the fault is present, continue to deal with the fault.
- If the fault is stored, ignore it.
Deal with any other faults.
Clear the stored faults.
Page 83 of 348

17B-83V7 MR-413-X44-17B000$131.mif
PETROL INJECTION
Fault finding – Interpretation of faults17B
SIM 32 Injection
Program no.: D3
Vdiag No.: 44, 4C, 50
and 54
DF079
CONTINUED 2
Look for possible damage to the wiring harness.
Check the condition of the engine management computer connector (component code 120).
If the connector is faulty and there is a repair procedure (see Technical Note 6015A, Repairing electrical wiring,
Wiring: Precautions for repair), repair the connector, otherwise replace the wiring.
If the fault is still present, disconnect the battery and the injection computer.
Check the insulation, continuity and absence of interference resistance on the following connections:
●3AJB between the components 120 and 1076, and 3AJC between the components 120 and 1076,
●3MP between the components 120 and 1076,
●3MN between the components 120 and 1076,
●3MQ between the components 120 and 1076,
●3MO between the components 120 and 1076.
●3LR between the components 120 and 921,
●3LS between the components 120 and 921,
●3LT between the components 120 and 921,
●3LU between the components 120 and 921,
●3LW between the components 120 and 921,
●3LV between the components 120 and 921.
If the connection or connections are faulty and there is a repair procedure (see Technical Note 6015A, Electrical
wiring repair, Wiring: Precautions for repair), repair the wiring, otherwise replace it.
If the fault is still present, contact the Techline.
AFTER REPAIRIf the throttle valve has been replaced, program the throttle stops (see Configurations
and programming).
Follow the instructions to confirm repair:
- If the fault is present, continue to deal with the fault.
- If the fault is stored, ignore it.
Deal with any other faults.
Clear the stored faults.
Page 84 of 348
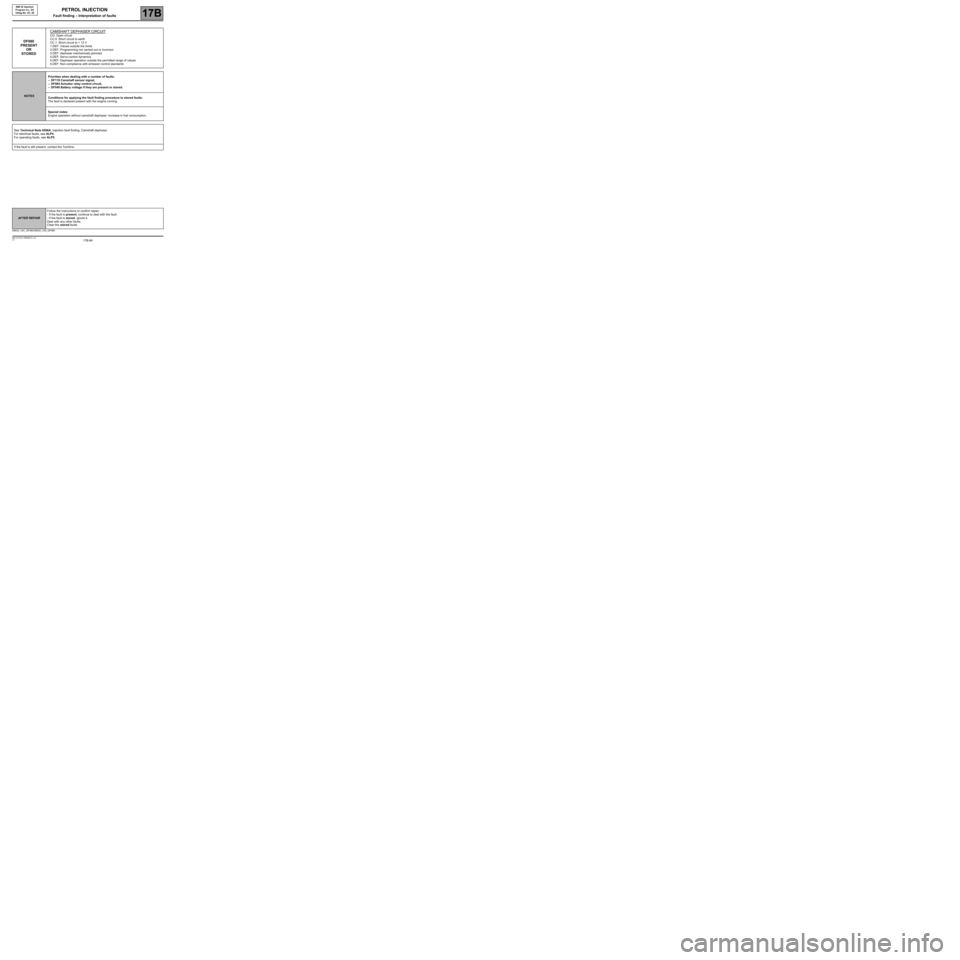
17B-84V7 MR-413-X44-17B000$131.mif
PETROL INJECTION
Fault finding – Interpretation of faults17B
SIM 32 Injection
Program no.: D3
Vdiag No: 4C, 50
DF080
PRESENT
OR
STOREDCAMSHAFT DEPHASER CIRCUIT
CO: Open circuit
CC.0: Short circuit to earth
CC.1: Short circuit to + 12 V
1.DEF: Values outside the limits
2.DEF: Programming not carried out or incorrect
3.DEF: dephaser mechanically jammed.
4.DEF: Servo-control dynamics
5.DEF: Dephaser operation outside the permitted range of values
6.DEF: Non-compliance with emission control standards
NOTESPriorities when dealing with a number of faults:
–DF119 Camshaft sensor signal,
–DF084 Actuator relay control circuit,
–DF046 Battery voltage if they are present or stored.
Conditions for applying the fault finding procedure to stored faults:
The fault is declared present with the engine running.
Special notes:
Engine operation without camshaft dephaser: increase in fuel consumption.
See Technical Note 6506A, Injection fault finding, Camshaft dephaser.
For electrical faults, see ALP4.
For operating faults, see ALP5.
If the fault is still present, contact the Techline.
SIM32_V4C_DF080/SIM32_V50_DF080
AFTER REPAIRFollow the instructions to confirm repair:
- If the fault is present, continue to deal with the fault.
- If the fault is stored, ignore it.
Deal with any other faults.
Clear the stored faults.
Page 85 of 348
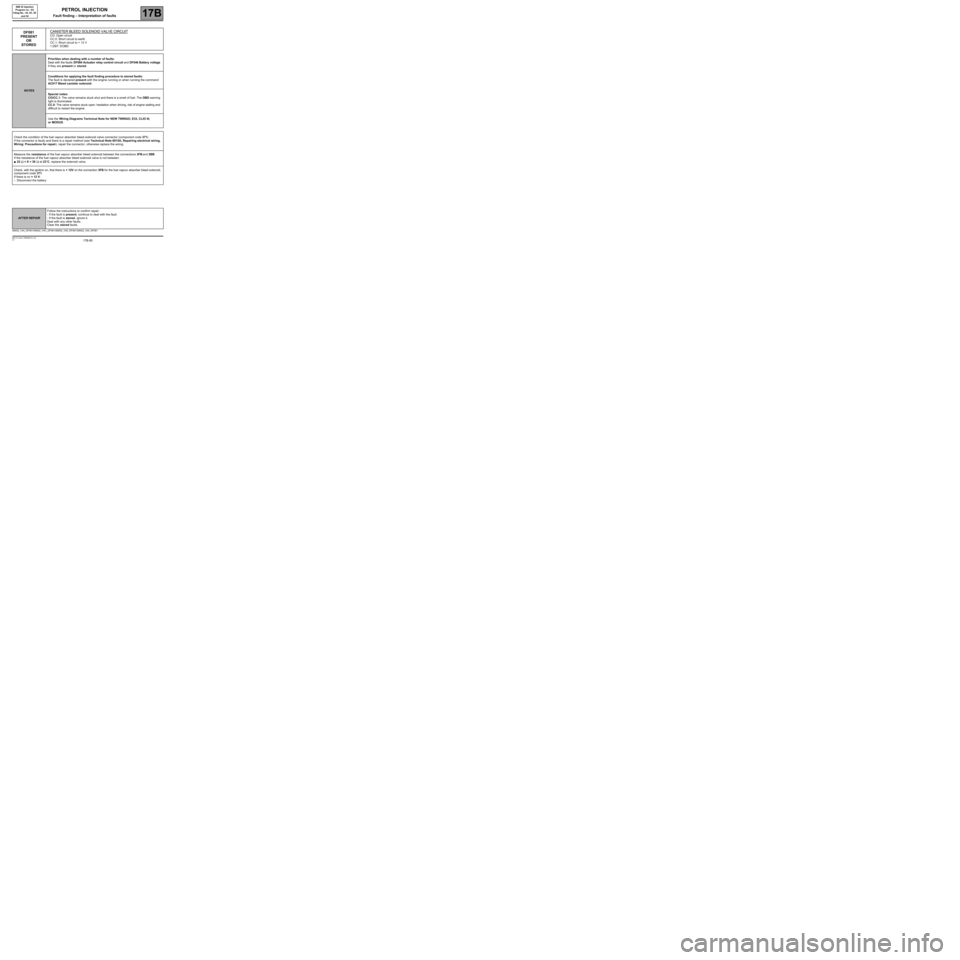
17B-85V7 MR-413-X44-17B000$131.mif
PETROL INJECTION
Fault finding – Interpretation of faults17B
SIM 32 Injection
Program no.: D3
Vdiag No.: 44, 4C, 50
and 54
DF081
PRESENT
OR
STOREDCANISTER BLEED SOLENOID VALVE CIRCUITCO: Open circuit
CC.0: Short circuit to earth
CC.1: Short circuit to + 12 V
1.DEF: EOBD
NOTESPriorities when dealing with a number of faults:
Deal with the faults DF084 Actuator relay control circuit and DF046 Battery voltage
if they are present or stored.
Conditions for applying the fault finding procedure to stored faults:
The fault is declared present with the engine running or when running the command
AC017 Bleed canister solenoid.
Special notes:
CO/CC.1: The valve remains stuck shut and there is a smell of fuel. The OBD warning
light is illuminated.
CC.0: The valve remains stuck open: hesitation when driving, risk of engine stalling and
difficult to restart the engine.
Use the Wiring Diagrams Technical Note for NEW TWINGO, E33, CLIO III,
or MODUS.
Check the condition of the fuel vapour absorber bleed solenoid valve connector (component code 371).
If the connector is faulty and there is a repair method (see Technical Note 6015A, Repairing electrical wiring,
Wiring: Precautions for repair), repair the connector, otherwise replace the wiring.
Measure the resistance of the fuel vapour absorber bleed solenoid between the connections 3FB and 3BB:
If the resistance of the fuel vapour absorber bleed solenoid valve is not between:
●22 Ω < X < 30 Ω at 23˚C, replace the solenoid valve.
Check, with the ignition on, that there is + 12V on the connection 3FB for the fuel vapour absorber bleed solenoid,
component code 371.
If there is no + 12 V:
–Disconnect the battery
SIM32_V44_DF081/SIM32_V4C_DF081/SIM32_V50_DF081/SIM32_V54_DF081
AFTER REPAIRFollow the instructions to confirm repair:
- If the fault is present, continue to deal with the fault.
- If the fault is stored, ignore it.
Deal with any other faults.
Clear the stored faults.
Page 86 of 348
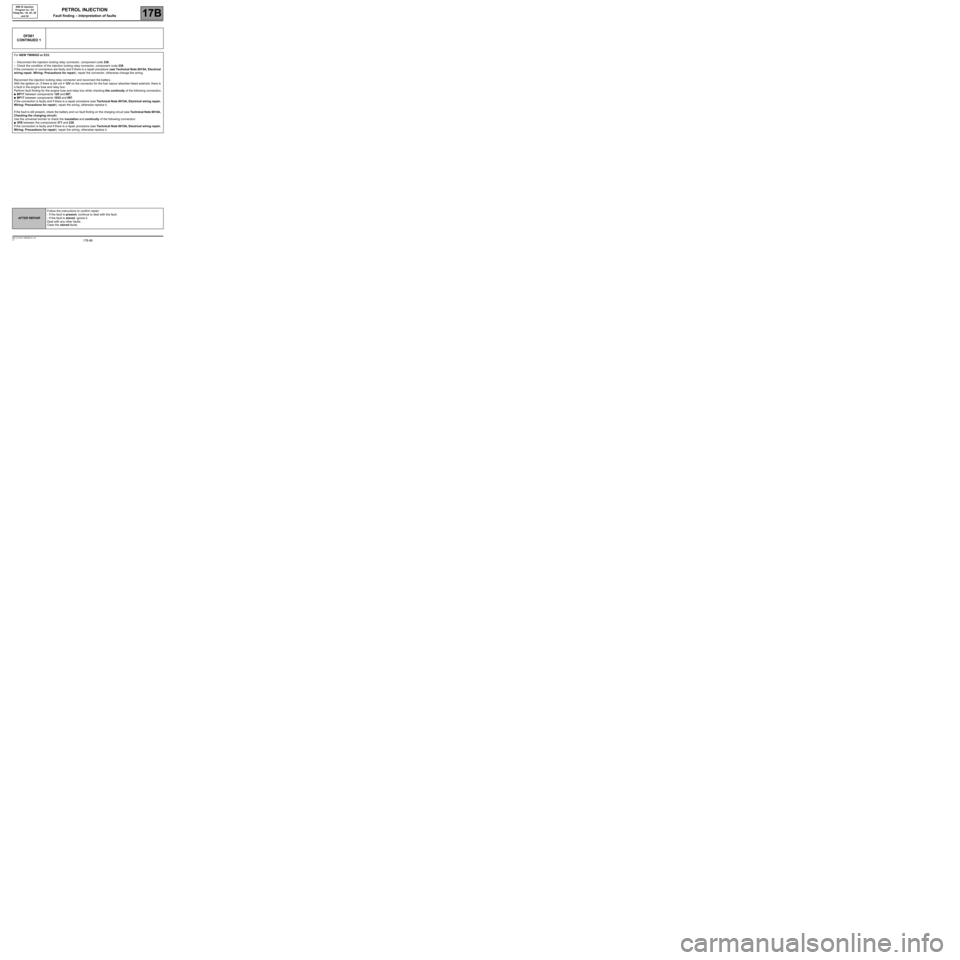
17B-86V7 MR-413-X44-17B000$131.mif
PETROL INJECTION
Fault finding – Interpretation of faults17B
SIM 32 Injection
Program no.: D3
Vdiag No.: 44, 4C, 50
and 54
DF081
CONTINUED 1
For NEW TWINGO or E33:
–Disconnect the injection locking relay connector, component code 238,
–Check the condition of the injection locking relay connector, component code 238.
If the connector or connectors are faulty and if there is a repair procedure (see Technical Note 6015A, Electrical
wiring repair, Wiring: Precautions for repair), repair the connector, otherwise change the wiring.
Reconnect the injection locking relay connector and reconnect the battery.
With the ignition on, if there is still not + 12V on the connector for the fuel vapour absorber bleed solenoid, there is
a fault in the engine fuse and relay box.
Perform fault finding for the engine fuse and relay box while checking the continuity of the following connection:
●BP17 between components 120 and 597,
●BP17 between components 1033 and 597.
If the connection is faulty and if there is a repair procedure (see Technical Note 6015A, Electrical wiring repair,
Wiring: Precautions for repair), repair the wiring, otherwise replace it.
If the fault is still present, check the battery and run fault finding on the charging circuit (see Technical Note 6014A,
Checking the charging circuit).
Use the universal bornier to check the insulation and continuity of the following connection:
●3FB between the components 371 and 238.
If the connection is faulty and if there is a repair procedure (see Technical Note 6015A, Electrical wiring repair,
Wiring: Precautions for repair), repair the wiring, otherwise replace it.
AFTER REPAIRFollow the instructions to confirm repair:
- If the fault is present, continue to deal with the fault.
- If the fault is stored, ignore it.
Deal with any other faults.
Clear the stored faults.