towing RENAULT TWINGO 2009 2.G Engine And Peripherals Manual Online
[x] Cancel search | Manufacturer: RENAULT, Model Year: 2009, Model line: TWINGO, Model: RENAULT TWINGO 2009 2.GPages: 652
Page 446 of 652
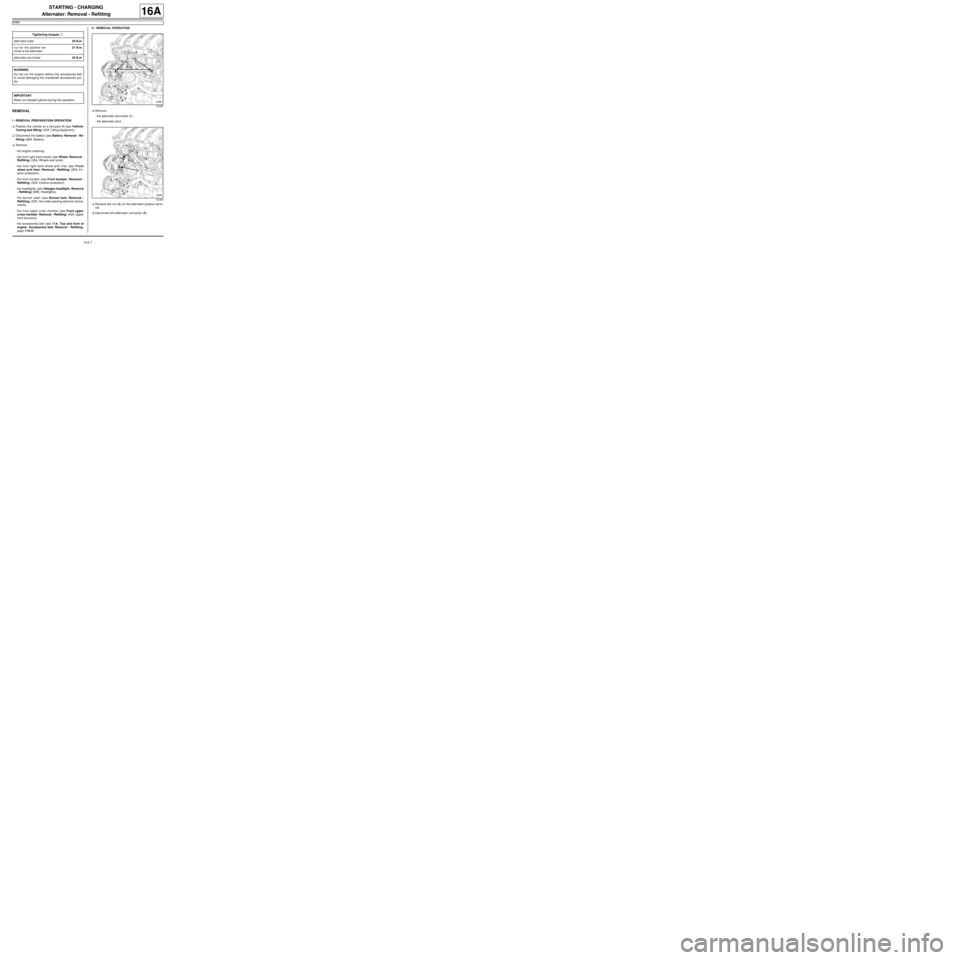
16A-7
STARTING - CHARGING
Alternator: Removal - Refitting
K4M
16A
REMOVAL
I - REMOVAL PREPARATION OPERATION
aPosition the vehicle on a two-post lift (see Vehicle:
Towing and lifting) (02A, Lifting equipment).
aDisconnect the battery (see Battery: Removal - Re-
fitting) (80A, Battery).
aRemove:
-the engine undertray,
-the front right-hand wheel (see Wheel: Removal -
Refitting) (35A, Wheels and tyres),
-the front right-hand wheel arch liner (see Front
wheel arch liner: Removal - Refitting) (55A, Ex-
terior protection),
-the front bumper (see Front bumper: Removal -
Refitting) (55A, Exterior protection),
-the headlights (see Halogen headlight: Removal
- Refitting) (80B, Headlights),
-the bonnet catch (see Bonnet lock: Removal -
Refitting) (52A, Non-side opening element mecha-
nisms),
-the front upper cross member (see Front upper
cross member: Removal - Refitting) (42A, Upper
front structure),
-the accessories belt (see 11A, Top and front of
engine, Accessories belt: Removal - Refitting,
page 11A-3) .II - REMOVAL OPERATION
aRemove:
-the alternator strut bolts (1) ,
-the alternator strut.
aRemove the nut (2) on the alternator positive termi-
nal.
aDisconnect the alternator connector (3) . Tightening torquesm
alter nator bolts25 N.m
nut for the positive ter-
minal of the alternator21 N.m
alter nator strut bolts25 N.m
WARNING
Do not r un the engine without the accessories belt
to avoid damaging the crankshaft accessories pul-
ley.
IMPORTANT
Wear cut-resistant gloves during the operation.
132363
132365
Page 488 of 652
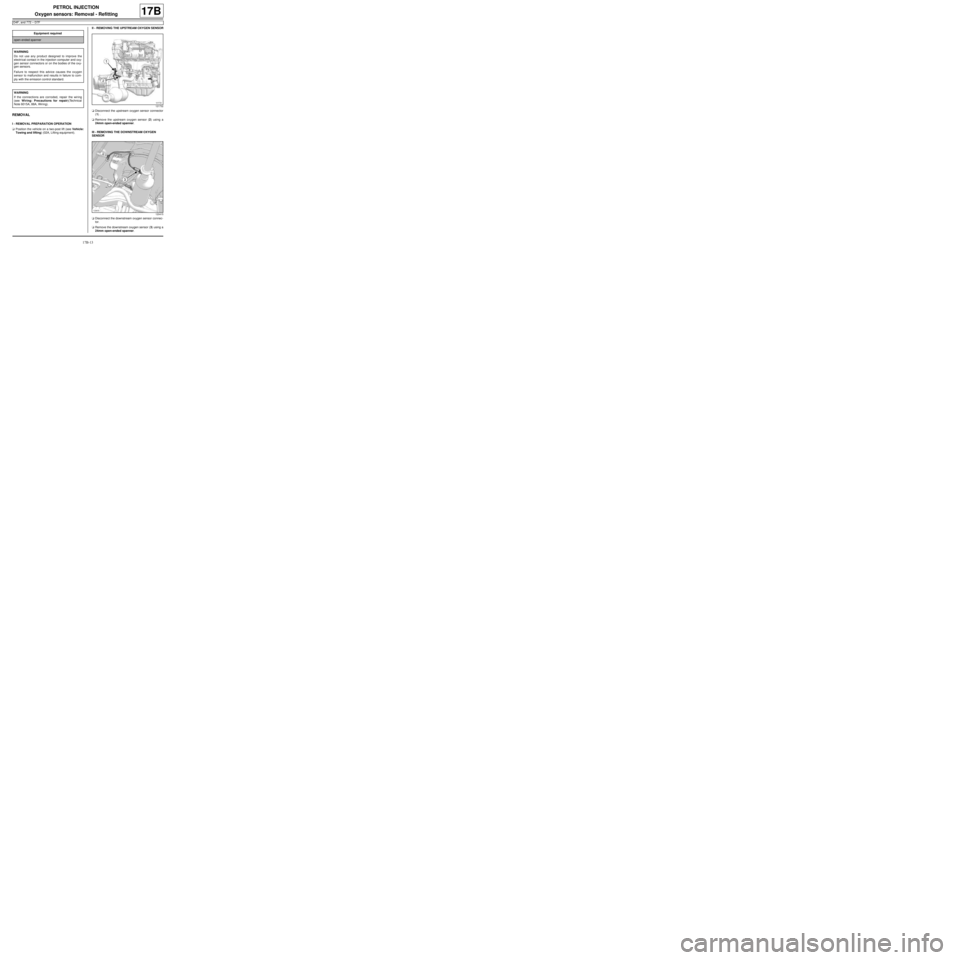
17B-13
PETROL INJECTION
Oxygen sensors: Removal - Refitting
D4F, and 772 – D7F
17B
REMOVAL
I - REMOVAL PREPARATION OPERATION
aPosition the vehicle on a two-post lift (see Vehicle:
Towing and lifting) (02A, Lifting equipment).II - REMOVING THE UPSTREAM OXYGEN SENSOR
aDisconnect the upstream oxygen sensor connector
(1) .
aRemove the upstream oxygen sensor (2) using a
24mm open-ended spanner.
III - REMOVING THE DOWNSTREAM OXYGEN
SENSOR
aDisconnect the downstream oxygen sensor connec-
tor.
aRemove the downstream oxygen sensor (3) using a
24mm open-ended spanner. Equipment required
open-ended spanner
WARNING
Do not use any product designed to improve the
electr ical contact in the injection computer and oxy-
gen sensor connectors or on the bodies of the oxy-
gen sensors.
Failure to respect this advice causes the oxygen
sensor to malfunction and results in failure to com-
ply with the emission control standard.
WARNING
If the connections are corroded, repair the wiring
(see Wiring: Precautions for repair)(Technical
Note 6015A, 88A, Wiring).
121732
120415
Page 490 of 652
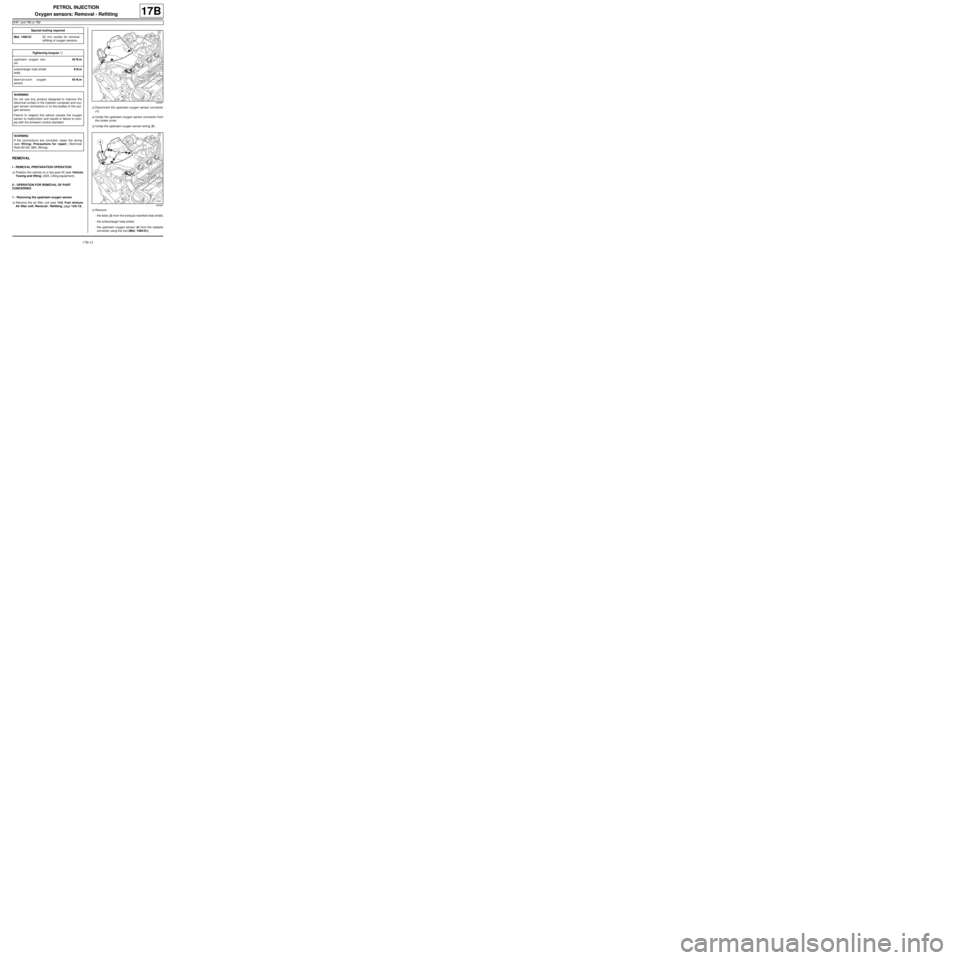
17B-15
PETROL INJECTION
Oxygen sensors: Removal - Refitting
D4F, and 780 or 782
17B
REMOVAL
I - REMOVAL PREPARATION OPERATION
aPosition the vehicle on a two-post lift (see Vehicle:
Towing and lifting) (02A, Lifting equipment).
II - OPERATION FOR REMOVAL OF PART
CONCERNED
1 - Removing the upstream oxygen sensor
aRemove the air filter unit (see 12A, Fuel mixture,
Air filter unit: Removal - Refitting, page 12A-13) .aDisconnect the upstream oxygen sensor connector
(1) .
aUnclip the upstream oxygen sensor connector from
the rocker cover.
aUnclip the upstream oxygen sensor wiring (2) .
aRemove:
-the bolts (3) from the exhaust manifold heat shield,
-the turbocharger heat shield,
-the upstream oxygen sensor (4) from the catalytic
converter using the tool (Mot. 1495-01). Special tooling required
Mot. 1495-0122 mm socket for removal -
refitting of oxygen sensors.
Tightening torquesm
upstream oxygen sen-
sor45 N.m
turbocharger heat shield
bolts8 N.m
downstream oxygen
sensor45 N.m
WARNING
Do not use any product designed to improve the
electr ical contact in the injection computer and oxy-
gen sensor connectors or on the bodies of the oxy-
gen sensors.
Failure to respect this advice causes the oxygen
sensor to malfunction and results in failure to com-
ply with the emission control standard.
WARNING
If the connections are corroded, repair the wiring
(see Wiring: Precautions for repair) (Technical
Note 6015A, 88A, Wiring).
120957
120957
Page 492 of 652
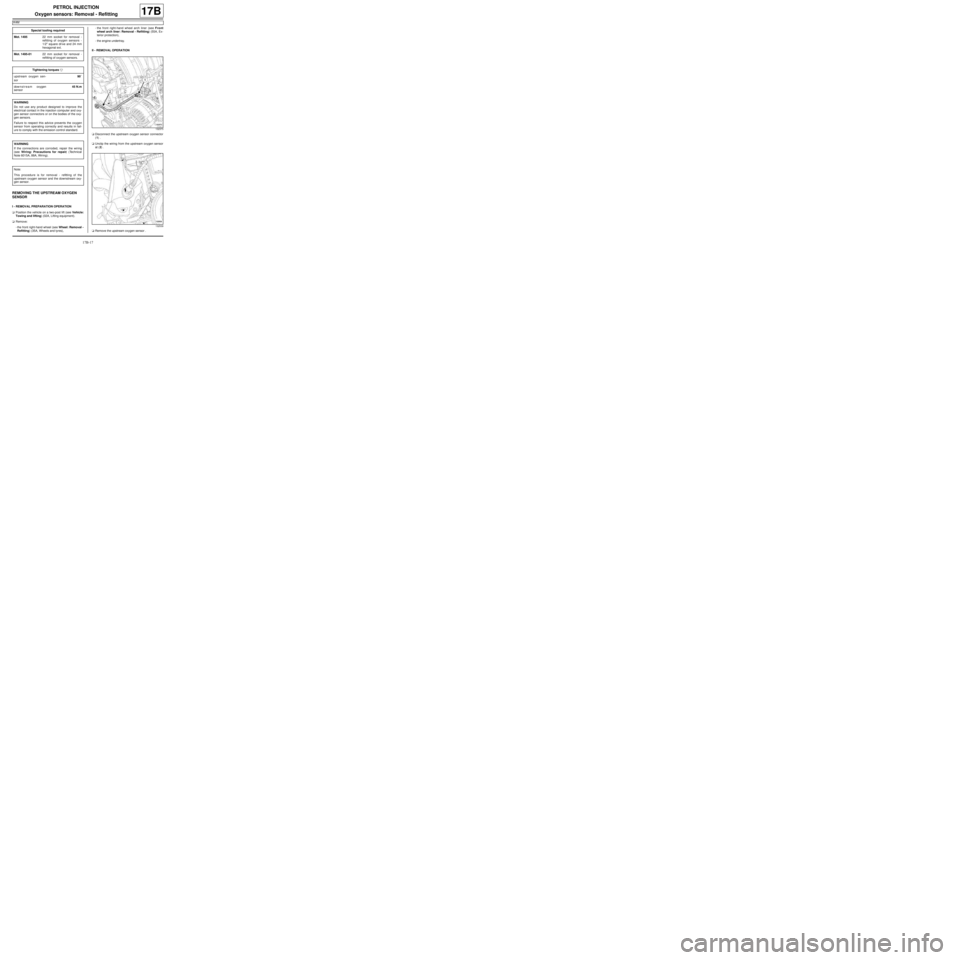
17B-17
PETROL INJECTION
Oxygen sensors: Removal - Refitting
K4M
17B
REMOVING THE UPSTREAM OXYGEN
SENSOR
I - REMOVAL PREPARATION OPERATION
aPosition the vehicle on a two-post lift (see Vehicle:
Towing and lifting) (02A, Lifting equipment).
aRemove:
-the front right-hand wheel (see Wheel: Removal -
Refitting) (35A, Wheels and tyres),-the front right-hand wheel arch liner (see Front
wheel arch liner: Removal - Refitting) (55A, Ex-
terior protection),
-the engine undertray.
II - REMOVAL OPERATION
aDisconnect the upstream oxygen sensor connector
(1) .
aUnclip the wiring from the upstream oxygen sensor
at (2) .
aRemove the upstream oxygen sensor . Special tooling required
Mot. 149522 mm socket for removal -
refitting of oxygen sensors -
1/2" square dr ive and 24 mm
hexagonal ext.
Mot. 1495-0122 mm socket for removal -
refitting of oxygen sensors.
Tightening torquesm
upstream oxygen sen-
sor90˚
downstream oxygen
sensor45 N.m
WARNING
Do not use any product designed to improve the
electr ical contact in the injection computer and oxy-
gen sensor connectors or on the bodies of the oxy-
gen sensors.
Failure to respect this advice prevents the oxygen
sensor from operating correctly and results in fail-
ure to comply with the emission control standard.
WARNING
If the connections are corroded, repair the wiring
(see Wiring: Precautions for repair) (Technical
Note 6015A, 88A, Wiring).
Note:
This procedure is for removal - refitting of the
upstream oxygen sensor and the downstream oxy-
gen sensor.
132373
132539
Page 501 of 652
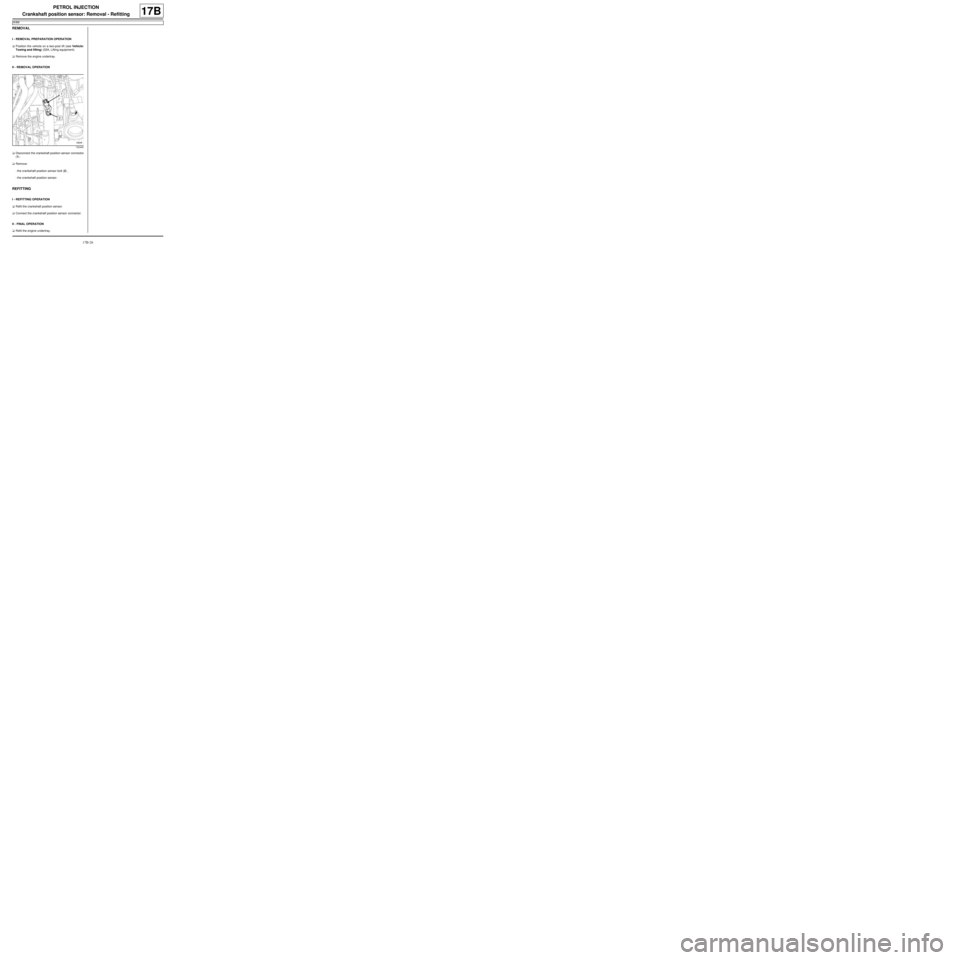
17B-26
PETROL INJECTION
Crankshaft position sensor: Removal - Refitting
K4M
17B
REMOVAL
I - REMOVAL PREPARATION OPERATION
aPosition the vehicle on a two-post lift (see Vehicle:
Towing and lifting) (02A, Lifting equipment).
aRemove the engine undertray.
II - REMOVAL OPERATION
aDisconnect the crankshaft position sensor connector
(1) .
aRemove:
-the crankshaft position sensor bolt (2) ,
-the crankshaft position sensor.
REFITTING
I - REFITTING OPERATION
aRefit the crankshaft position sensor.
aConnect the crankshaft position sensor connector.
II - FINAL OPERATION
aRefit the engine undertray.
132445
Page 519 of 652
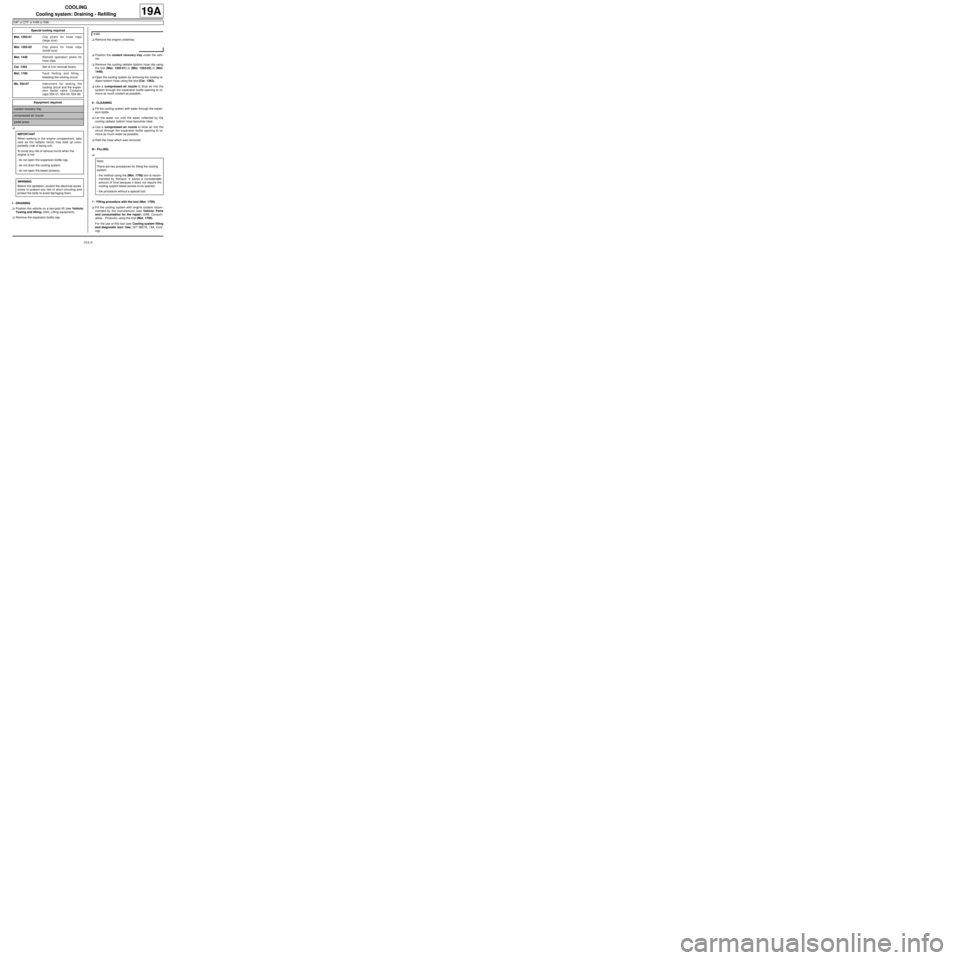
19A-9
COOLING
Cooling system: Draining - Refilling
D4F or D7F or K4M or K9K
19A
a
I - DRAINING
aPosition the vehicle on a two-post lift (see Vehicle:
Towing and lifting) (02A, Lifting equipment).
aRemove the expansion bottle cap.aRemove the engine undertray.
aPosition the coolant recovery tray under the vehi-
cle.
aRemove the cooling radiator bottom hose clip using
the tool (Mot. 1202-01) or (Mot. 1202-02) or (Mot.
1448).
aOpen the cooling system by removing the cooling ra-
diator bottom hose using the tool (Car. 1363).
aUse a compressed air nozzle to blow air into the
system through the expansion bottle opening to re-
move as much coolant as possible.
II - CLEANING
aFill the cooling system with water through the expan-
sion bottle.
aLet the water run until the water collected by the
cooling radiator bottom hose becomes clear.
aUse a compressed air nozzle to blow air into the
circuit through the expansion bottle opening to re-
move as much water as possible.
aRefit the hose which was removed.
III - FILLING
a
1 - Filling procedure with the tool (Mot. 1700)
aFill the cooling system with engine coolant recom-
mended by the manufacturer (see Vehicle: Parts
and consumables for the repair) (04B, Consum-
ables - Products) using the tool (Mot. 1700).
For the use of this tool (see Cooling system filling
and diagnostic tool: Use) (NT 3857A, 19A, Cool-
ing). Special tooling required
Mot. 1202-01Clip pliers for hose clips
(large size).
Mot. 1202-02Clip pliers for hose clips
(small size)
Mot. 1448Remote operation pliers for
hose clips .
Car. 1363Set of tr im removal levers.
Mot. 1700Fault finding and filling -
bleeding the cooling circuit.
Ms. 554-07Instr ument for testing the
cooling circuit and the expan-
sion bottle valve. Contains
caps 554-01, 554-04, 554-06
Equipment required
coolant recovery tray
compressed air nozzle
pedal press
IMPORTANT
When working in the engine compartment, take
care as the radiator fan(s) may start up unex-
pectedly (risk of being cut).
To avoid any risk of serious burns when the
engine is hot:
-do not open the expansion bottle cap,
-do not dr ain the cooling system,
-do not open the bleed screw(s).
WARNING
Before the operation, protect the electrical acces-
sories to prevent any risk of short circuiting and
protect the belts to avoid damaging them.
K4M
Note:
There are two procedures for filling the cooling
system:
-the method using the (Mot. 1700) tool is recom-
mended by Renault. It saves a considerable
amount of time because it does not require the
cooling system bleed screws to be opened,
-the procedure without a special tool.
Page 522 of 652
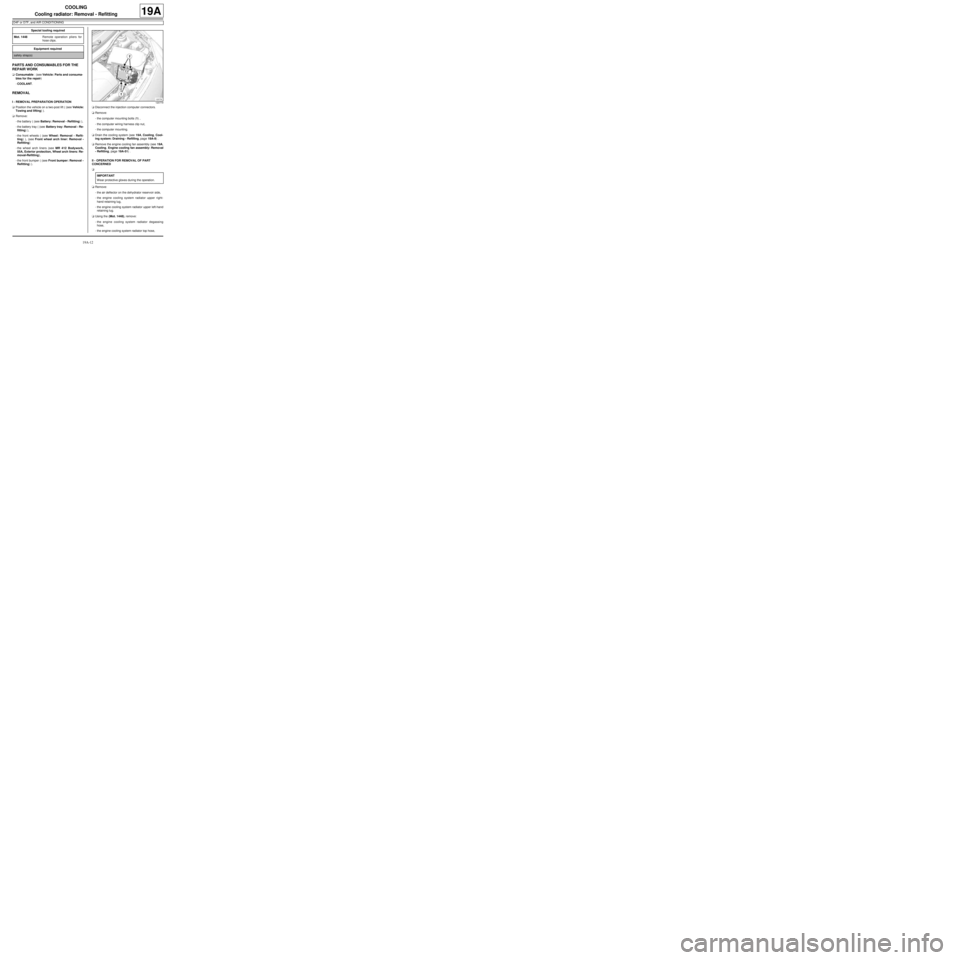
19A-12
COOLING
Cooling radiator: Removal - Refitting
D4F or D7F, and AIR CONDITIONING
19A
PARTS AND CONSUMABLES FOR THE
REPAIR WORK
aConsumable : (see Vehicle: Parts and consuma-
bles for the repair)
-COOLANT.
REMOVAL
I - REMOVAL PREPARATION OPERATION
aPosition the vehicle on a two-post lift ( (see Vehicle:
Towing and lifting) ).
aRemove:
-the battery ( (see Battery: Removal - Refitting) ),
-the battery tray ( (see Battery tray: Removal - Re-
fitting) ),
-the front wheels ( (see Wheel: Removal - Refit-
ting) ), (see Front wheel arch liner: Removal -
Refitting)
-the wheel arch liners (see MR 412 Bodywork,
55A, Exterior protection, Wheel arch liners: Re-
moval-Refitting),
-the front bumper ( (see Front bumper: Removal -
Refitting) ).aDisconnect the injection computer connectors.
aRemove:
-the computer mounting bolts (1) ,
-the computer wiring harness clip nut,
-the computer mounting.
aDrain the cooling system (see 19A, Cooling, Cool-
ing system: Draining - Refilling, page 19A-9) .
aRemove the engine cooling fan assembly (see 19A,
Cooling, Engine cooling fan assembly: Removal
- Refitting, page 19A-51) .
II - OPERATION FOR REMOVAL OF PART
CONCERNED
a
aRemove:
-the air deflector on the dehydrator reservoir side,
-the engine cooling system radiator upper right-
hand retaining lug,
-the engine cooling system radiator upper left-hand
retaining lug.
aUsing the (Mot. 1448), remove:
-the engine cooling system radiator degassing
hose,
-the engine cooling system radiator top hose, Special tooling required
Mot. 1448Remote operation pliers for
hose clips .
Equipment required
safety strap(s)
120779
IMPORTANT
Wear protective gloves during the operation.
Page 524 of 652
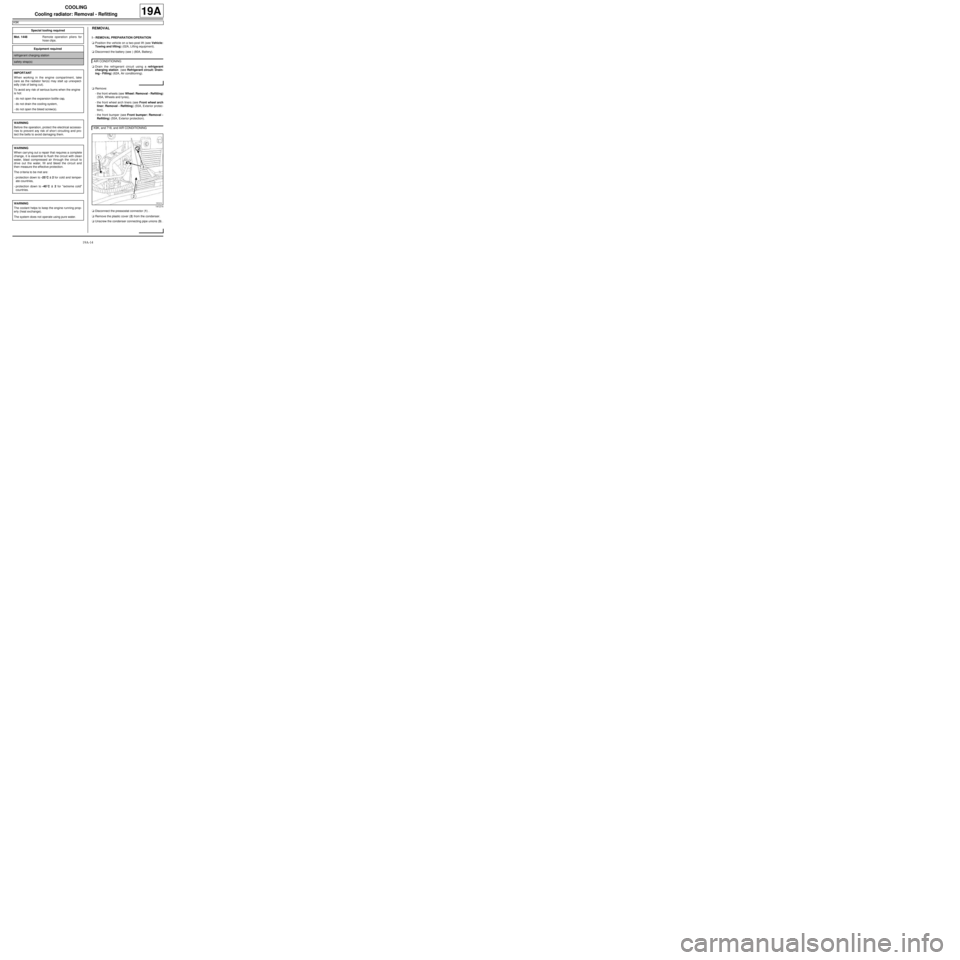
19A-14
COOLING
Cooling radiator: Removal - Refitting
K9K
19A
REMOVAL
I - REMOVAL PREPARATION OPERATION
aPosition the vehicle on a two-post lift (see Vehicle:
Towing and lifting) (02A, Lifting equipment).
aDisconnect the battery (see ) (80A, Battery).
aDrain the refrigerant circuit using a refrigerant
charging station (see Refrigerant circuit: Drain-
ing - Filling) (62A, Air conditioning).
aRemove:
-the front wheels (see Wheel: Removal - Refitting)
(35A, Wheels and tyres),
-the front wheel arch liners (see Front wheel arch
liner: Removal - Refitting) (55A, Exterior protec-
tion),
-the front bumper (see Front bumper: Removal -
Refitting) (55A, Exterior protection).
aDisconnect the pressostat connector (1) .
aRemove the plastic cover (2) from the condenser.
aUnscrew the condenser connecting pipe unions (3) . Special tooling required
Mot. 1448Remote operation pliers for
hose clips .
Equipment required
refrigerant charging station
safety strap(s)
IMPORTANT
When working in the engine compartment, take
care as the radiator fan(s) may start up unexpect-
edly (risk of being cut).
To avoid any risk of serious burns when the engine
is hot:
-do not open the expansion bottle cap,
-do not drain the cooling system,
-do not open the bleed screw(s).
WARNING
Before the operation, protect the electrical accesso-
ries to prevent any risk of shor t circuiting and pro-
tect the belts to avoid damaging them.
WARNING
When carr ying out a repair that requires a complete
change, it is essential to flush the circuit with clean
water, blast compressed air through the circuit to
drive out the water, fill and bleed the circuit and
then measure the effective protection.
The cr iteria to be met are:
-protection down to -25˚C ±± ± ±
2 for cold and temper-
ate countries,
-protection down to -40˚C ±± ± ±
2 for "extreme cold"
countries.
WARNING
The coolant helps to keep the engine running prop-
erly (heat exchange).
The system does not operate using pure water.AIR CONDITIONING
K9K, and 718, and AIR CONDITIONING
141214
Page 528 of 652
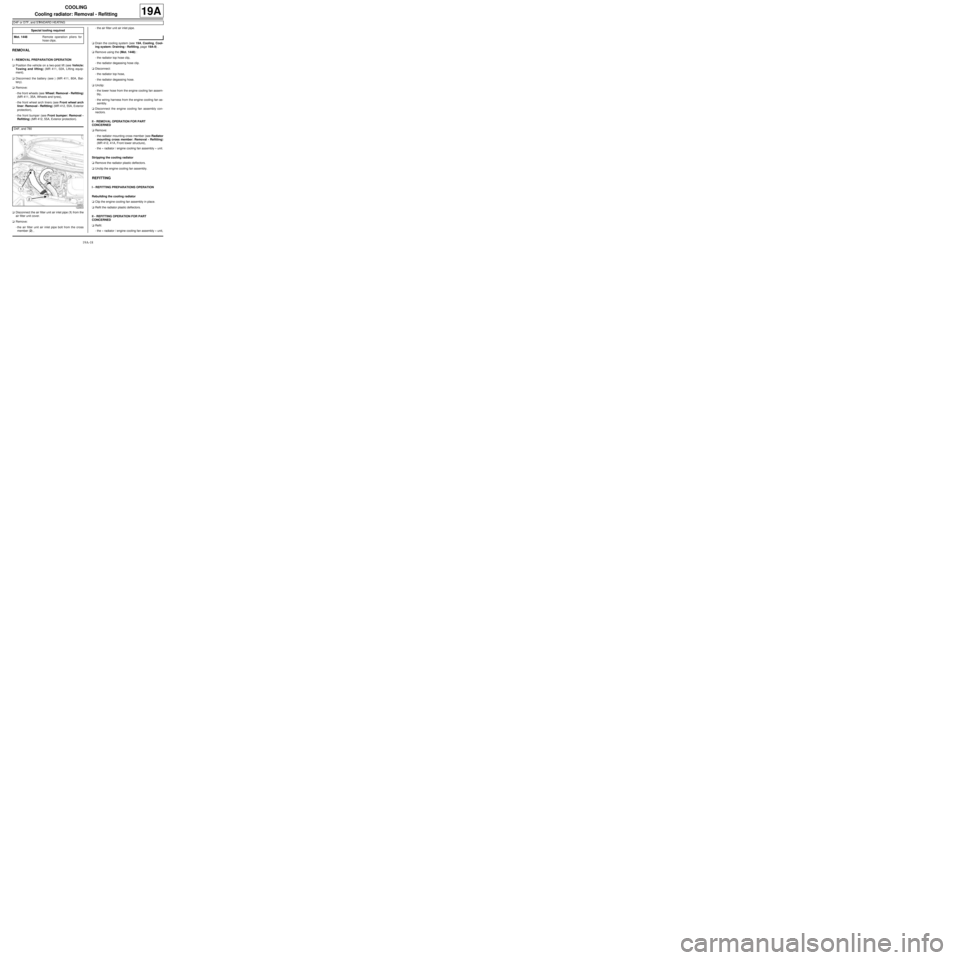
19A-18
COOLING
Cooling radiator: Removal - Refitting
D4F or D7F, and STANDARD HEATING
19A
REMOVAL
I - REMOVAL PREPARATION OPERATION
aPosition the vehicle on a two-post lift (see Vehicle:
Towing and lifting) (MR 411, 02A, Lifting equip-
ment).
aDisconnect the battery (see ) (MR 411, 80A, Bat-
tery).
aRemove:
-the front wheels (see Wheel: Removal - Refitting)
(MR 411, 35A, Wheels and tyres),
-the front wheel arch liners (see Front wheel arch
liner: Removal - Refitting) (MR 412, 55A, Exterior
protection),
-the front bumper (see Front bumper: Removal -
Refitting) (MR 412, 55A, Exterior protection).
aDisconnect the air filter unit air inlet pipe (1) from the
air filter unit cover.
aRemove:
-the air filter unit air inlet pipe bolt from the cross
member (2) ,-the air filter unit air inlet pipe.
aDrain the cooling system (see 19A, Cooling, Cool-
ing system: Draining - Refilling, page 19A-9) .
aRemove using the (Mot. 1448) :
-the radiator top hose clip,
-the radiator degassing hose clip.
aDisconnect:
-the radiator top hose,
-the radiator degassing hose.
aUnclip:
-the lower hose from the engine cooling fan assem-
bly,
-the wiring harness from the engine cooling fan as-
sembly.
aDisconnect the engine cooling fan assembly con-
nectors.
II - REMOVAL OPERATION FOR PART
CONCERNED
aRemove:
-the radiator mounting cross member (see Radiator
mounting cross member: Removal - Refitting)
(MR 412, 41A, Front lower structure),
-the « radiator / engine cooling fan assembly » unit.
Stripping the cooling radiator
aRemove the radiator plastic deflectors.
aUnclip the engine cooling fan assembly.
REFITTING
I - REFITTING PREPARATIONS OPERATION
Rebuilding the cooling radiator
aClip the engine cooling fan assembly in place.
aRefit the radiator plastic deflectors.
II - REFITTING OPERATION FOR PART
CONCERNED
aRefit:
-the « radiator / engine cooling fan assembly » unit, Special tooling required
Mot. 1448Remote operation pliers for
hose clips .
D4F, and 780
122833
Page 530 of 652

19A-20
COOLING
Cooling radiator: Removal - Refitting
K4M
19A
REMOVAL
I - REMOVAL PREPARATION OPERATION
aPosition the vehicle on a two-post lift (see Vehicle:
Towing and lifting) (02A, Lifting equipment).
aDisconnect the battery (see Battery: Removal - Re-
fitting) (80A, Battery).
aDrain the air conditioning circuit using a refrigerant
charging station (see Refrigerant circuit: Drain-
ing - Filling) (62A, Air conditioning).
aRemove:
-the engine undertray bolts,
-the engine undertray,
-the front wheels (see Wheel: Removal - Refitting)
(35A, Wheels and tyres),
-the front wheel arch liners (see Front wheel arch
liner: Removal - Refitting) (55A, Exterior protec-
tion),
-the front bumper (see Front bumper: Removal -
Refitting) (55A, Exterior protection).
aDrain the cooling system (see 19A, Cooling, Cool-
ing system: Draining - Refilling, page 19A-9) . Special tooling required
Mot. 1448Remote operation pliers for
hose clips .
Equipment required
refrigerant charging station
safety strap(s)
Tightening torquesm
bolt of the dehydrator
reservoir - « expansion
valve connecting pipe » 8 N.m
compressor - con-
denser « connecting
pipe bolt » 8 N.m
air conditioning connect-
ing pipe bolts8 N.m
IMPORTANT
When working in the engine compartment, take
care as the radiator fan(s) may start up unexpect-
edly (risk of being cut).
To avoid any risk of serious burns when the engine
is hot:
-do not open the expansion bottle cap,
-do not drain the cooling system,
-do not open the bleed screw(s).
WARNING
Prepare for the flow of fluid, and protect the sur-
rounding components.
WARNING
When carr ying out a repair that requires a complete
change, it is essential to flush the circuit with clean
water, blast compressed air through the circuit to
drive out the water, fill and bleed the circuit and
then measure the effective protection.
The cr iteria to be met are:
-protection down to -25˚C ±± ± ±
2 for cold and temper-
ate countries,
-protection down to -40˚C ±± ± ±
2 for "extreme cold"
countries.