oil temperature RENAULT TWINGO RS 2009 2.G Engine And Peripherals Owner's Manual
[x] Cancel search | Manufacturer: RENAULT, Model Year: 2009, Model line: TWINGO RS, Model: RENAULT TWINGO RS 2009 2.GPages: 652
Page 400 of 652
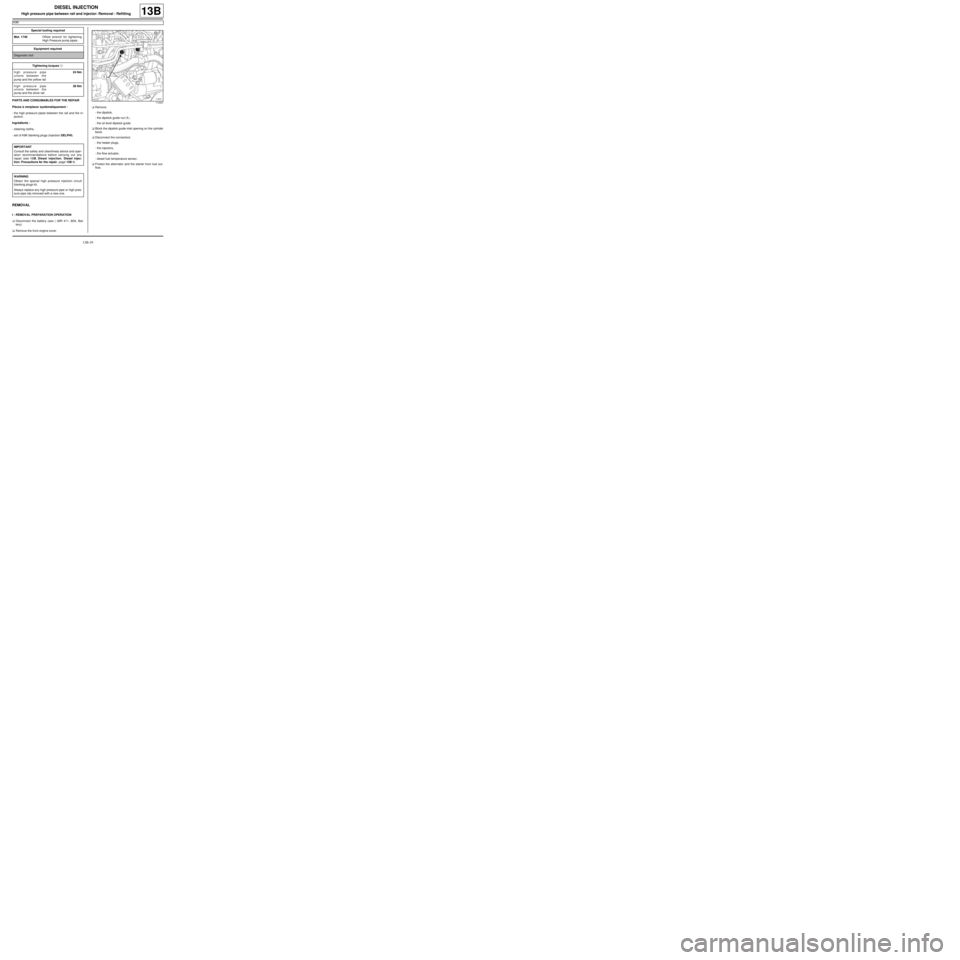
13B-39
DIESEL INJECTION
High pressure pipe between rail and injector: Removal - Refitting
K9K
13B
PARTS AND CONSUMABLES FOR THE REPAIR
Pièces à remplacer systématiquement :
-the high pressure pipes between the rail and the in-
jectors.
Ingrédients :
-cleaning cloths,
-set of K9K blanking plugs (injection DELPHI).
REMOVAL
I - REMOVAL PREPARATION OPERATION
aDisconnect the battery (see ) (MR 411, 80A, Bat-
tery).
aRemove the front engine cover.aRemove:
-the dipstick,
-the dipstick guide nut (1) ,
-the oil level dipstick guide.
aBlock the dipstick guide inlet opening on the cylinder
block.
aDisconnect the connectors:
-the heater plugs,
-the injectors,
-the flow actuator,
-diesel fuel temperature sensor.
aProtect the alternator and the starter from fuel out-
flow. Special tooling required
Mot. 1746Offset wrench for tightening
High Pressure pump pipes.
Equipment required
Diagnostic tool
Tightening torquesm
high pressure pipe
unions between the
pump and the yellow rail24 Nm
high pressure pipe
unions between the
pump and the silver rail28 Nm
IMPORTANT
Consult the safety and cleanliness advice and oper-
ation recommendations before carrying out any
repair (see 13B, Diesel injection, Diesel injec-
tion: Precautions for the repair, page 13B-1) .
WARNING
Obtain the special high pressure injection circuit
blanking plugs kit.
Always replace any high pressure pipe or high pres-
sure pipe clip removed with a new one.
114527
Page 403 of 652
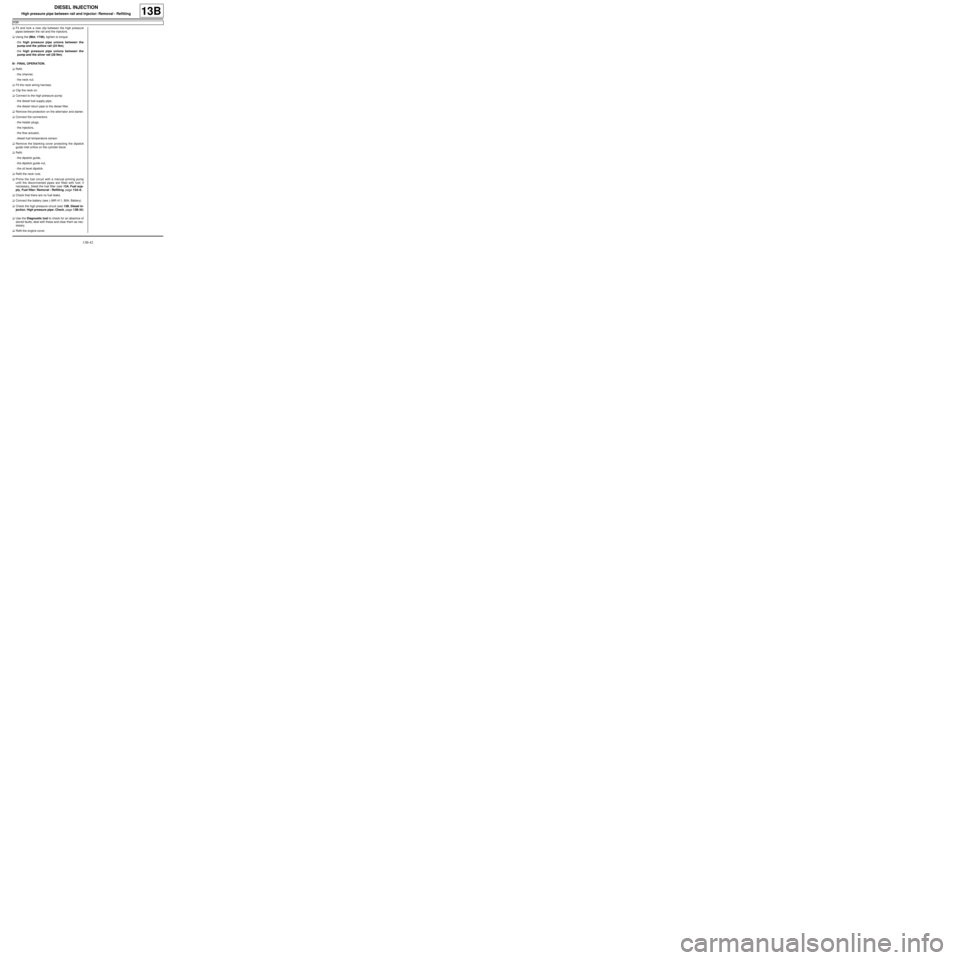
13B-42
DIESEL INJECTION
High pressure pipe between rail and injector: Removal - Refitting
K9K
13B
aFit and lock a new clip between the high pressure
pipes between the rail and the injectors.
aUsing the (Mot. 1746), tighten to torque:
-the high pressure pipe unions between the
pump and the yellow rail (24 Nm),
-the high pressure pipe unions between the
pump and the silver rail (28 Nm).
III - FINAL OPERATION.
aRefit:
-the channel,
-the neck nut.
aFit the neck wiring harness.
aClip the neck on.
aConnect to the high pressure pump:
-the diesel fuel supply pipe,
-the diesel return pipe to the diesel filter.
aRemove the protection on the alternator and starter.
aConnect the connectors:
-the heater plugs,
-the injectors,
-the flow actuator,
-diesel fuel temperature sensor.
aRemove the blanking cover protecting the dipstick
guide inlet orifice on the cylinder block.
aRefit:
-the dipstick guide,
-the dipstick guide nut,
-the oil level dipstick.
aRefit the neck nuts.
aPrime the fuel circuit with a manual priming pump
until the disconnected pipes are filled with fuel; if
necessary, bleed the fuel filter (see 13A, Fuel sup-
ply, Fuel filter: Removal - Refitting, page 13A-4) .
aCheck that there are no fuel leaks.
aConnect the battery (see ) (MR 411, 80A, Battery).
aCheck the high pressure circuit (see 13B, Diesel in-
jection, High pressure pipe: Check, page 13B-34)
.
aUse the Diagnostic tool to check for an absence of
stored faults; deal with these and clear them as nec-
essary.
aRefit the engine cover.
Page 405 of 652
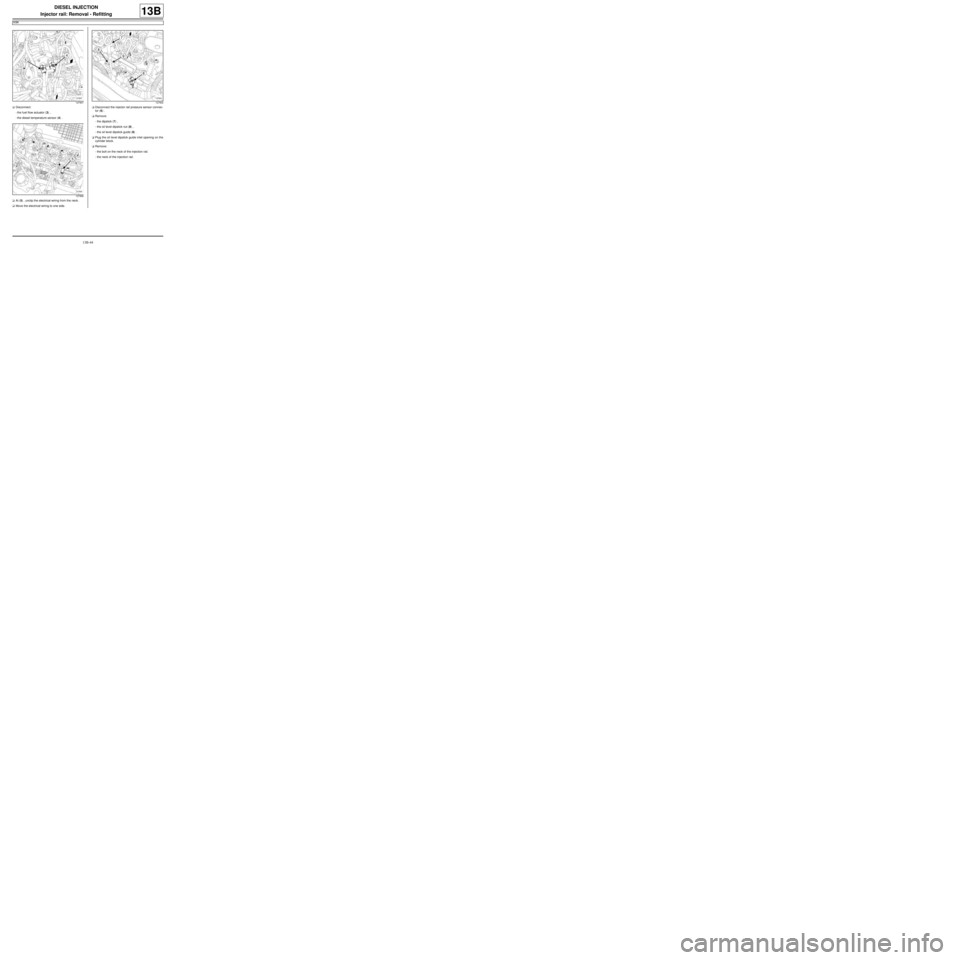
13B-44
DIESEL INJECTION
Injector rail: Removal - Refitting
K9K
13B
aDisconnect:
-the fuel flow actuator (3) ,
-the diesel temperature sensor (4) .
aAt (5) , unclip the electrical wiring from the neck.
aMove the electrical wiring to one side.aDisconnect the injector rail pressure sensor connec-
tor (6) .
aRemove:
-the dipstick (7) ,
-the oil level dipstick nut (8) ,
-the oil level dipstick guide (9) .
aPlug the oil level dipstick guide inlet opening on the
cylinder block.
aRemove:
-the bolt on the neck of the injection rail.
-the neck of the injection rail.
127907
127906127902
Page 408 of 652
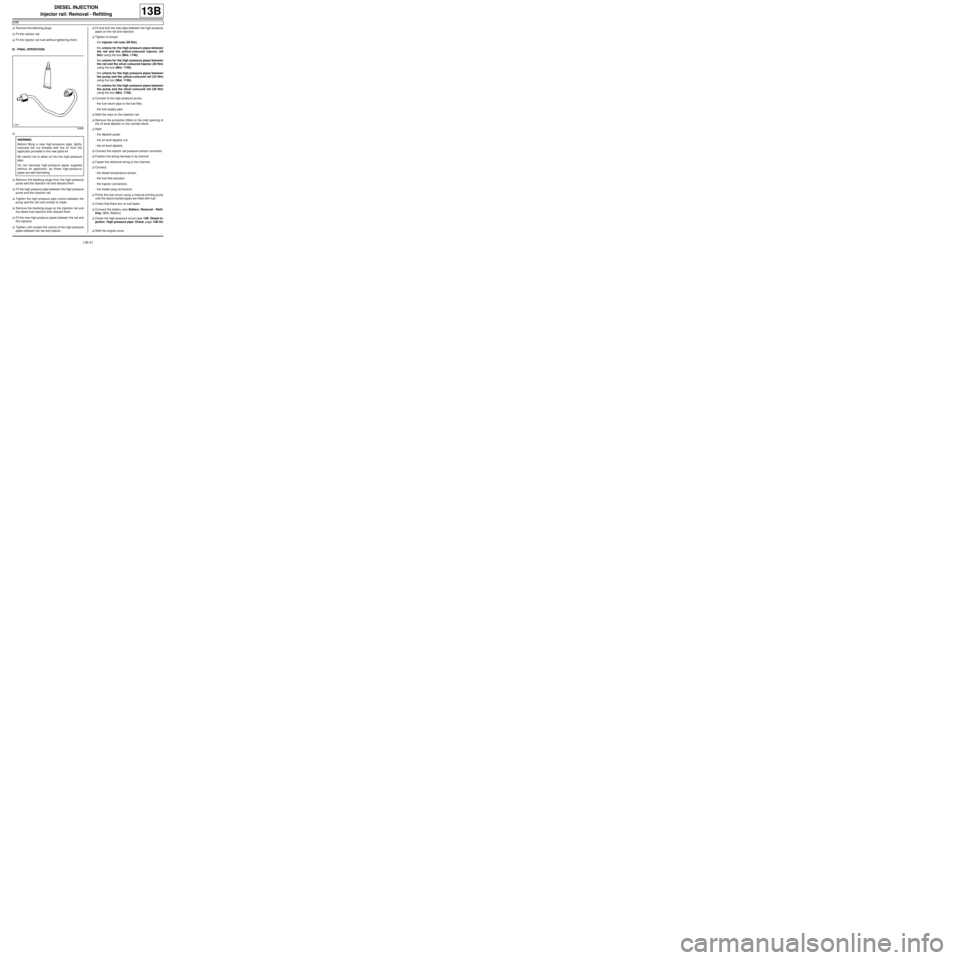
13B-47
DIESEL INJECTION
Injector rail: Removal - Refitting
K9K
13B
aRemove the blanking plugs.
aFit the injector rail.
aFit the injector rail nuts without tightening them.
III - FINAL OPERATION.
a
aRemove the blanking plugs from the high pressure
pump and the injection rail and discard them.
aFit the high pressure pipe between the high pressure
pump and the injection rail.
aTighten the high pressure pipe unions between the
pump and the rail until contact is made.
aRemove the blanking plugs on the injection rail and
the diesel fuel injectors then discard them.
aFit the new high-pressure pipes between the rail and
the injectors.
aTighten until contact the unions of the high pressure
pipes between the rail and injector.aFit and lock the new clips between the high pressure
pipes on the rail and injectors.
aTighten to torque:
-the injector rail nuts (28 Nm),
-the unions for the high pressure pipes between
the rail and the yellow-coloured injector (24
Nm) using the tool (Mot. 1746),
-the unions for the high pressure pipes between
the rail and the silver-coloured injector (28 Nm)
using the tool (Mot. 1746),
-the unions for the high pressure pipes between
the pump and the yellow-coloured rail (24 Nm)
using the tool (Mot. 1746),
-the unions for the high pressure pipes between
the pump and the silver-coloured rail (28 Nm)
using the tool (Mot. 1746),
aConnect to the high pressure pump:
-the fuel return pipe to the fuel filter,
-the fuel supply pipe.
aRefit the neck on the injection rail.
aRemove the protection fitted on the inlet opening of
the oil level dipstick on the cylinder block.
aRefit:
-the dipstick guide,
-the oil level dipstick nut,
-the oil level dipstick.
aConnect the injector rail pressure sensor connector.
aPosition the wiring harness in its channel.
aFasten the electrical wiring to the channel.
aConnect:
-the diesel temperature sensor,
-the fuel flow actuator,
-the injector connectors,
-the heater plug connectors.
aPrime the fuel circuit using a manual priming pump
until the disconnected pipes are filled with fuel.
aCheck that there are no fuel leaks.
aConnect the battery (see Battery: Removal - Refit-
ting) (80A, Battery).
aCheck the high pressure circuit (see 13B, Diesel in-
jection, High pressure pipe: Check, page 13B-34)
.
aRefit the engine cover.
20960
WARNING
Before fitting a new high-pressure pipe, lightly
lubricate the nut threads with the oil from the
applicator provided in the new parts kit.
Be careful not to allow oil into the high-pressure
pipe.
Do not lubricate high-pressure pipes supplied
without an applicator, as these high-pressure
pipes are self-lubricating.
Page 414 of 652
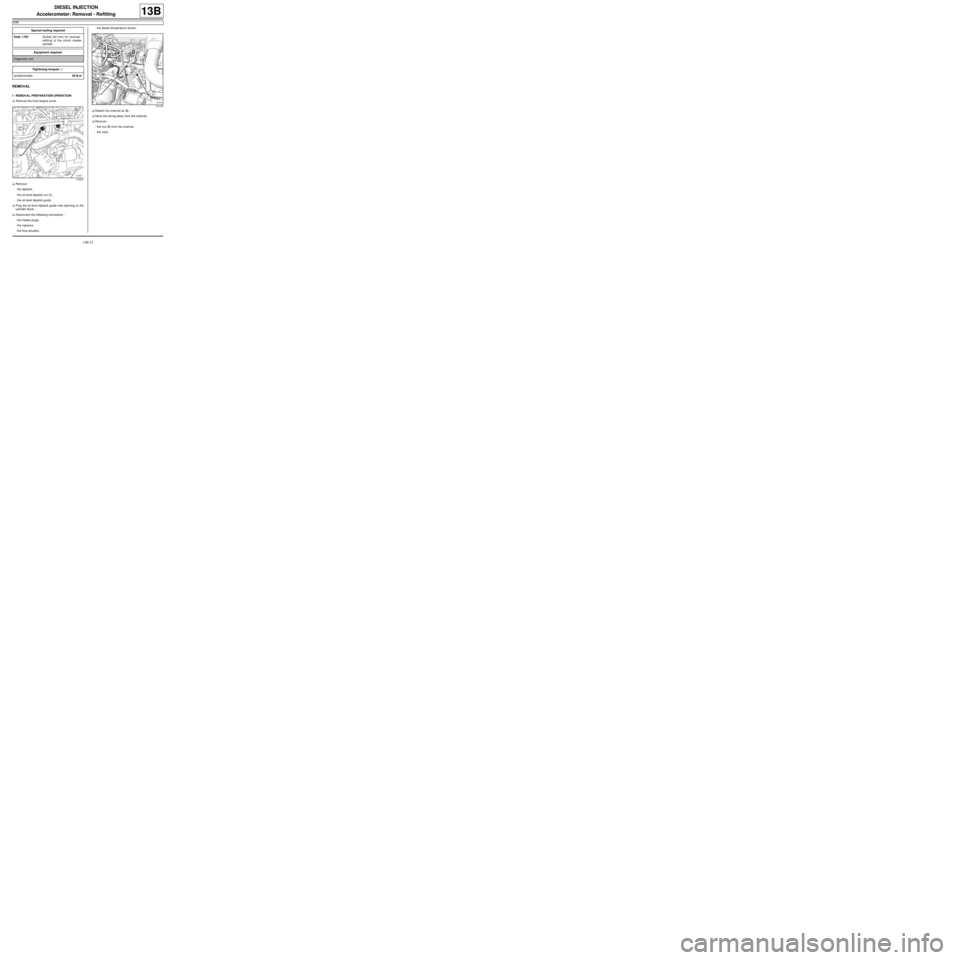
13B-53
DIESEL INJECTION
Accelerometer: Removal - Refitting
K9K
13B
REMOVAL
I - REMOVAL PREPARATION OPERATION
aRemove the front engine cover.
aRemove:
-the dipstick,
-the oil level dipstick nut (1) ,
-the oil level dipstick guide.
aPlug the oil level dipstick guide inlet opening on the
cylinder block.
aDisconnect the following connectors :
-the heater plugs,
-the injectors,
-the flow actuator,-the diesel temperature sensor.
aDetach the channel at (2) .
aMove the wiring away from the channel.
aRemove:
-the nut (3) from the channel,
-the neck. Special tooling required
Emb. 1797Socket (24 mm) for removal -
refitting of the clutch master
cylinder
Equipment required
Diagnostic tool
Tightening torquesm
accelerometer20 N.m
114527
121419
Page 415 of 652
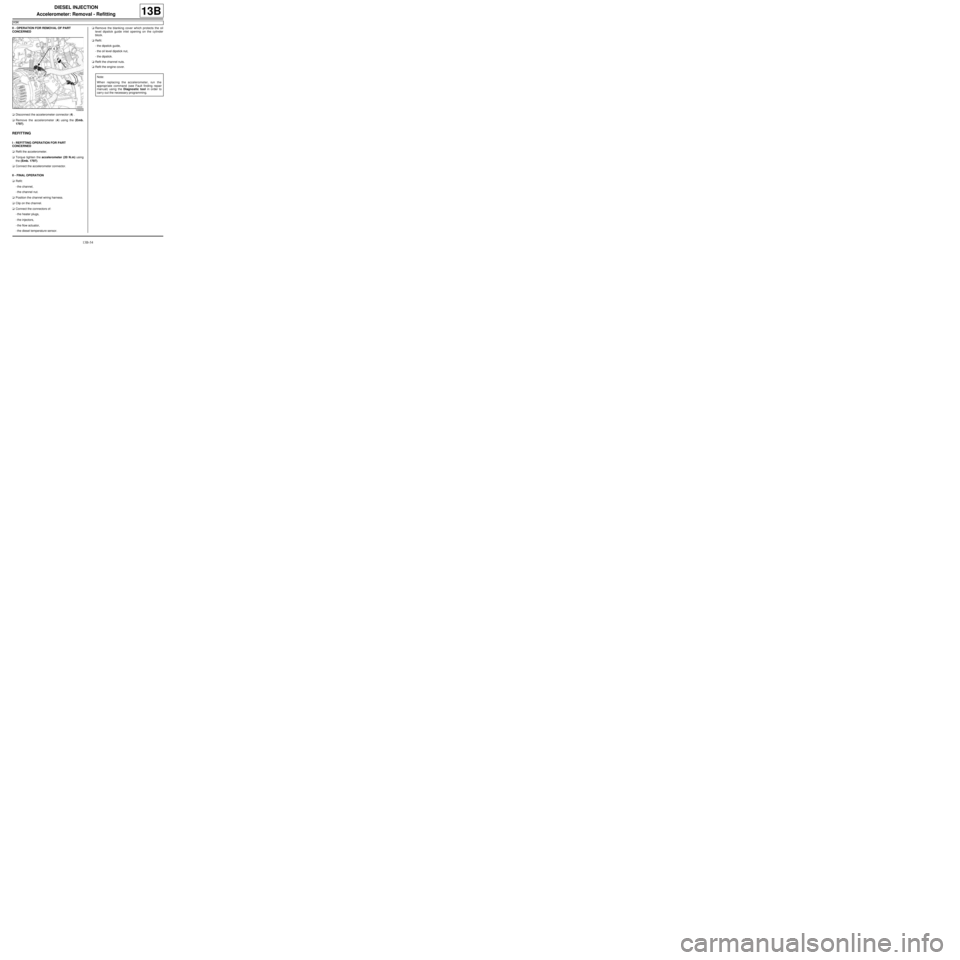
13B-54
DIESEL INJECTION
Accelerometer: Removal - Refitting
K9K
13B
II - OPERATION FOR REMOVAL OF PART
CONCERNED
aDisconnect the accelerometer connector (4) .
aRemove the accelerometer (4) using the (Emb.
1797).
REFITTING
I - REFITTING OPERATION FOR PART
CONCERNED
aRefit the accelerometer.
aTorque tighten the accelerometer (20 N.m) using
the (Emb. 1797).
aConnect the accelerometer connector.
II - FINAL OPERATION
aRefit:
-the channel,
-the channel nut.
aPosition the channel wiring harness.
aClip on the channel.
aConnect the connectors of:
-the heater plugs,
-the injectors,
-the flow actuator,
-the diesel temperature sensor.aRemove the blanking cover which protects the oil
level dipstick guide inlet opening on the cylinder
block.
aRefit:
-the dipstick guide,
-the oil level dipstick nut,
-the dipstick.
aRefit the channel nuts.
aRefit the engine cover.
109939
Note:
When replacing the accelerometer, run the
appropriate command (see Fault finding repair
manual) using the Diagnostic tool in order to
carr y out the necessary programming.
Page 476 of 652
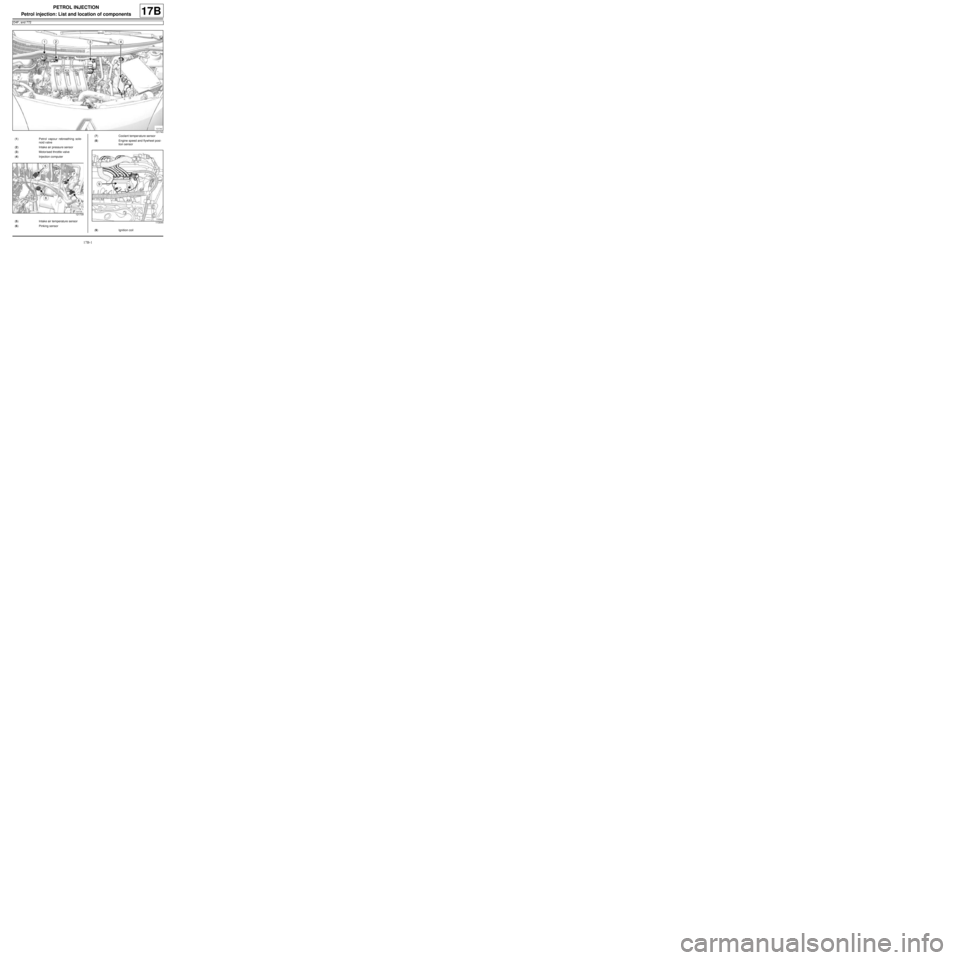
17B-1
PETROL INJECTION
Petrol injection: List and location of components
D4F, and 772
17B
121740
(1) Petrol vapour rebreathing sole-
noid valve
(2) Intake air pressure sensor
(3) Motorised throttle valve
(4) Injection computer
121739
(5) Intake air temperature sensor
(6) Pinking sensor
(7) Coolant temper ature sensor
(8) Engine speed and flywheel posi-
tion sensor
113044
(9) Ignition coil
Page 484 of 652
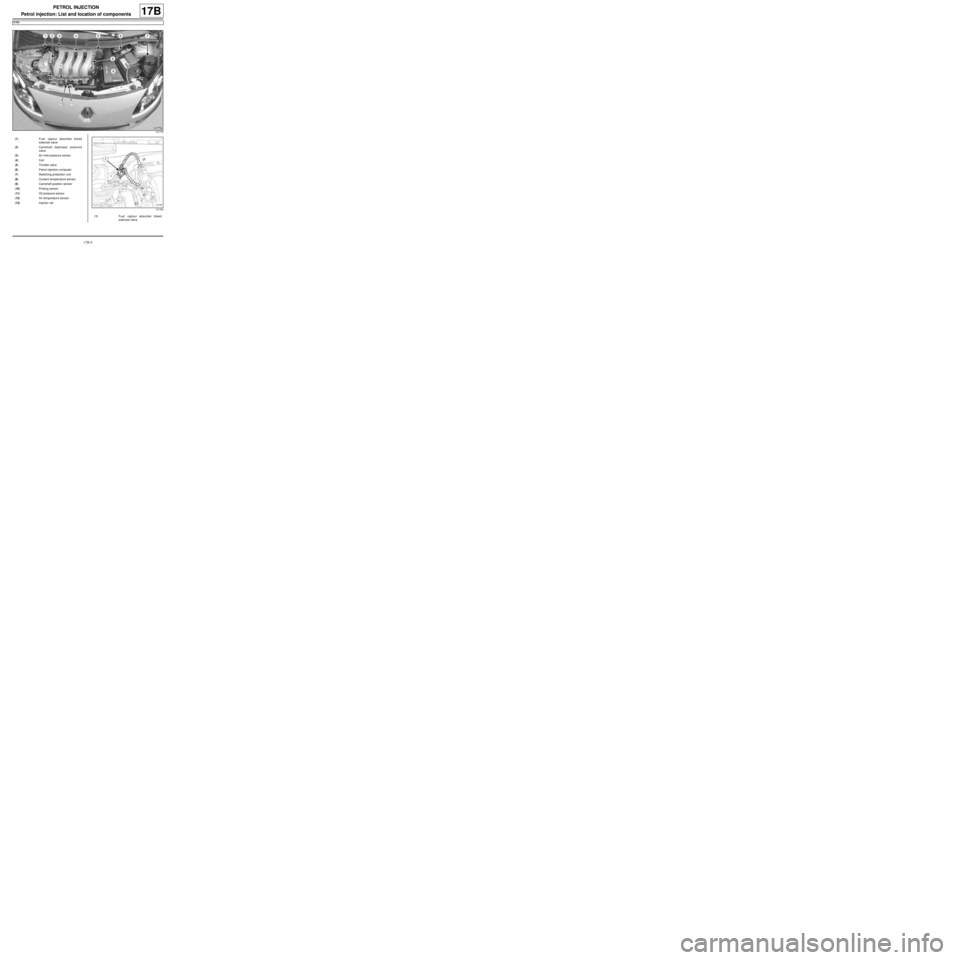
17B-9
PETROL INJECTION
Petrol injection: List and location of components
K4M
17B
131776
(1) Fuel vapour absorber bleed
solenoid valve
(2) Camshaft dephaser solenoid
valve
(3) Air inlet pressure sensor
(4) Coil
(5) Throttle valve
(6) Petrol injection computer
(7) Switching protection unit
(8) Coolant temper ature sensor
(9) Camshaft position sensor
(10) Pinking sensor
(11) Oil pressure sensor
(12) Air temperature sensor
(13) Injector rail
131766
(1) Fuel vapour absorber bleed
solenoid valve
Page 485 of 652
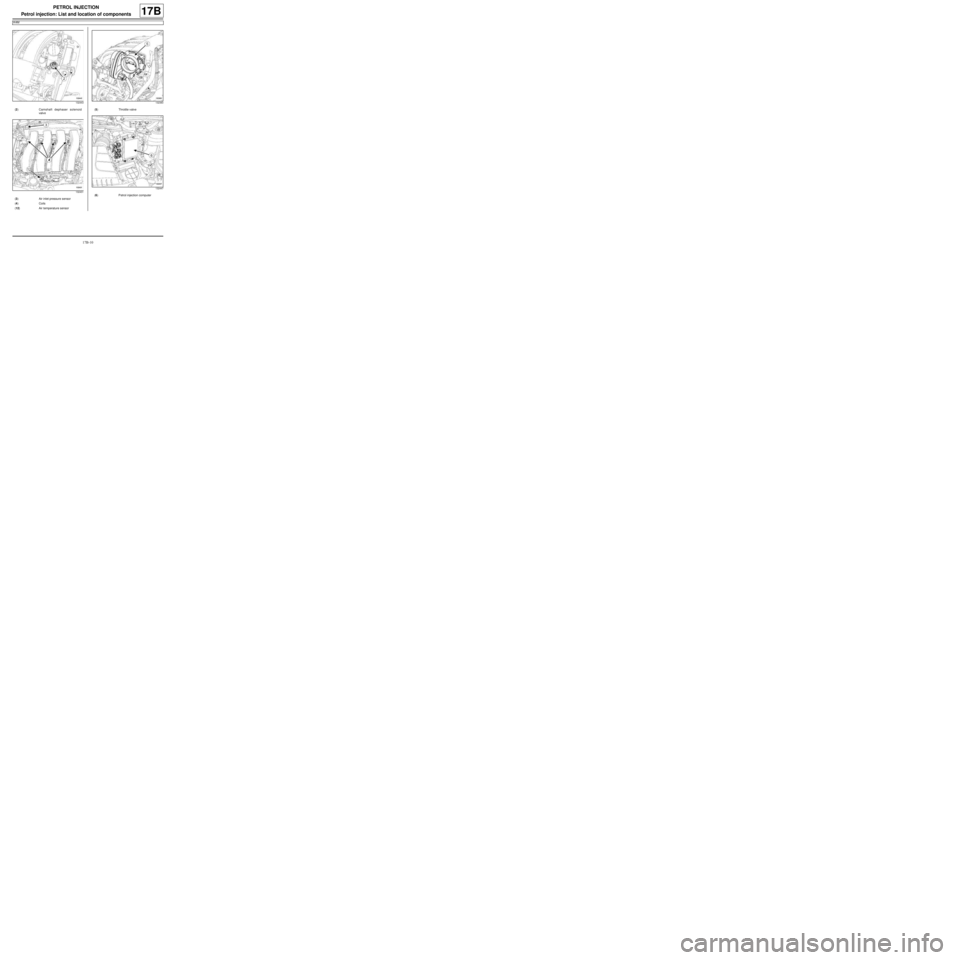
17B-10
PETROL INJECTION
Petrol injection: List and location of components
K4M
17B
132443
(2) Camshaft dephaser solenoid
valve
132431
(3) Air inlet pressure sensor
(4) Coils
(12) Air temperature sensor
132383
(5) Throttle valve
132447
(6) Petrol injection computer
Page 554 of 652
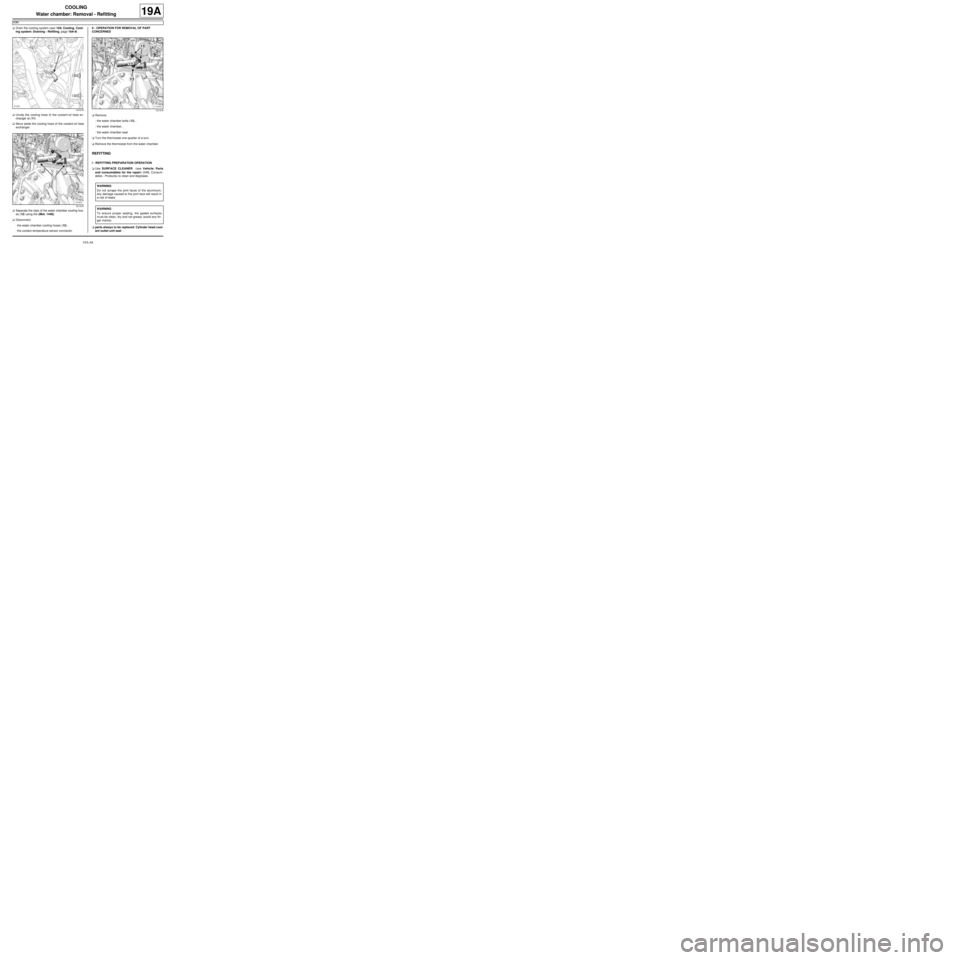
19A-44
COOLING
Water chamber: Removal - Refitting
K9K
19A
aDrain the cooling system (see 19A, Cooling, Cool-
ing system: Draining - Refilling, page 19A-9) .
aUnclip the cooling hose of the coolant-oil heat ex-
changer at (11) .
aMove aside the cooling hose of the coolant-oil heat
exchanger.
aSeparate the clips of the water chamber cooling hos-
es (12) using the (Mot. 1448).
aDisconnect:
-the water chamber cooling hoses (12) ,
-the coolant temperature sensor connector.II - OPERATION FOR REMOVAL OF PART
CONCERNED
aRemove:
-the water chamber bolts (13) ,
-the water chamber,
-the water chamber seal.
aTurn the thermostat one quarter of a turn.
aRemove the thermostat from the water chamber.
REFITTING
I - REFITTING PREPARATION OPERATION
aUse SURFACE CLEANER (see Vehicle: Parts
and consumables for the repair) (04B, Consum-
ables - Products) to clean and degrease.
aparts always to be replaced: Cylinder head cool-
ant outlet unit seal
141218
121416121416
WARNING
Do not scrape the joint faces of the aluminium,
any damage caused to the joint face will result in
a risk of leaks.
WARNING
To ensure proper sealing, the gasket surfaces
must be clean, dry and not greasy (avoid any fin-
ger mar ks).