coolant temperature SSANGYONG KORANDO 2012 User Guide
[x] Cancel search | Manufacturer: SSANGYONG, Model Year: 2012, Model line: KORANDO, Model: SSANGYONG KORANDO 2012Pages: 1082, PDF Size: 96.1 MB
Page 229 of 1082
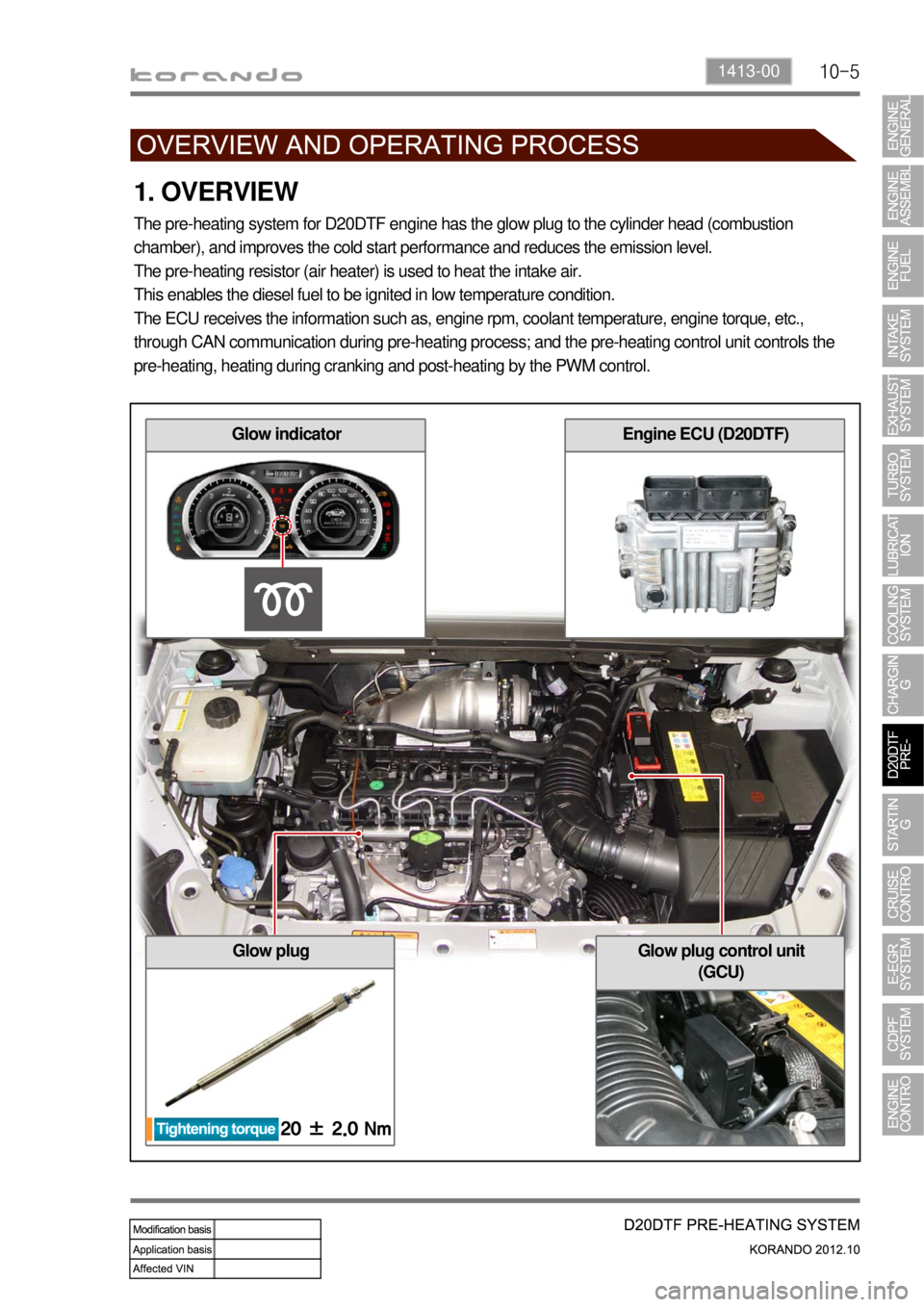
10-51413-00
1. OVERVIEW
The pre-heating system for D20DTF engine has the glow plug to the cylinder head (combustion
chamber), and improves the cold start performance and reduces the emission level.
The pre-heating resistor (air heater) is used to heat the intake air.
This enables the diesel fuel to be ignited in low temperature condition.
The ECU receives the information such as, engine rpm, coolant temperature, engine torque, etc.,
through CAN communication during pre-heating process; and the pre-heating control unit controls the
pre-heating, heating during cranking and post-heating by the PWM control.
Glow plugGlow plug control unit
(GCU)
Glow indicatorEngine ECU (D20DTF)
Page 234 of 1082
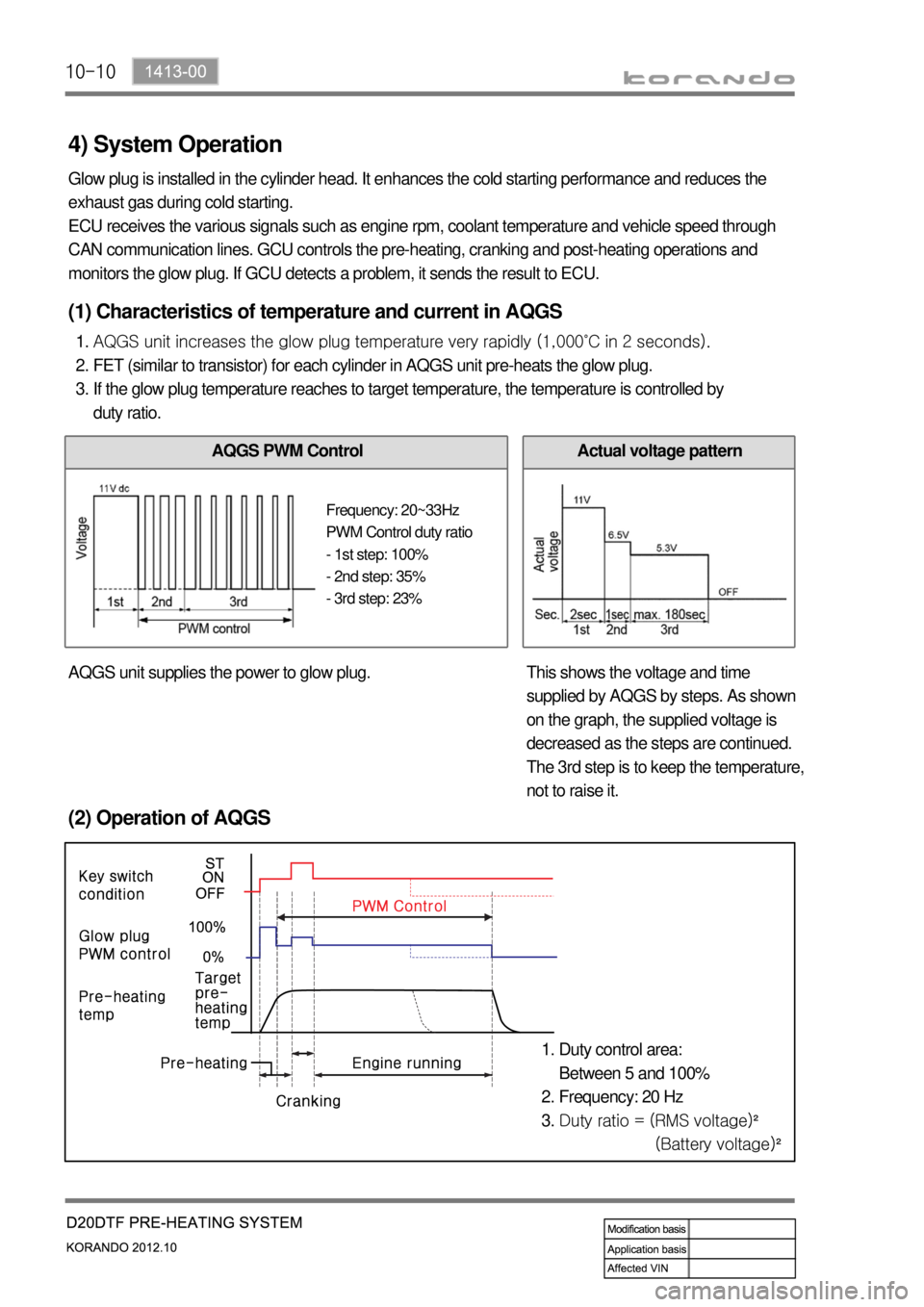
10-10
4) System Operation
Glow plug is installed in the cylinder head. It enhances the cold starting performance and reduces the
exhaust gas during cold starting.
ECU receives the various signals such as engine rpm, coolant temperature and vehicle speed through
CAN communication lines. GCU controls the pre-heating, cranking and post-heating operations and
monitors the glow plug. If GCU detects a problem, it sends the result to ECU.
(2) Operation of AQGS
Duty control area:
Between 5 and 100%
Frequency: 20 Hz
Duty ratio = (RMS voltage)²
(Battery voltage)² 1.
2.
3.
(1) Characteristics of temperature and current in AQGS
AQGS unit increases the glow plug temperature very rapidly (1,000˚C in 2 seconds).
FET (similar to transistor) for each cylinder in AQGS unit pre-heats the glow plug.
If the glow plug temperature reaches to target temperature, the temperature is controlled by
duty ratio. 1.
2.
3.
AQGS PWM ControlActual voltage pattern
AQGS unit supplies the power to glow plug. This shows the voltage and time
supplied by AQGS by steps. As shown
on the graph, the supplied voltage is
decreased as the steps are continued.
The 3rd step is to keep the temperature,
not to raise it.
Frequency: 20~33Hz
PWM Control duty ratio
- 1st step: 100%
- 2nd step: 35%
- 3rd step: 23%
Page 263 of 1082
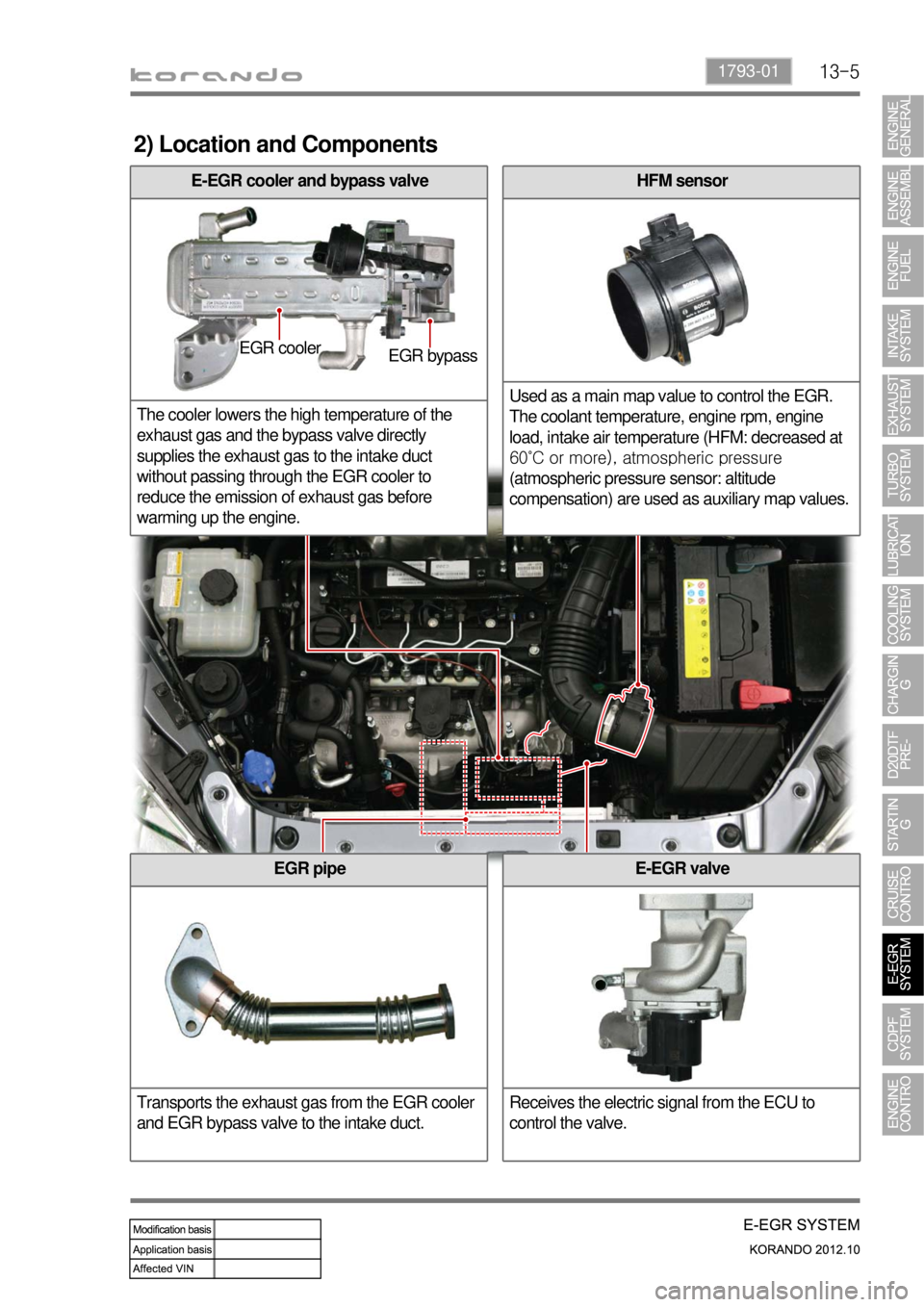
13-51793-01
2) Location and Components
HFM sensor
Used as a main map value to control the EGR.
The coolant temperature, engine rpm, engine
load, intake air temperature (HFM: decreased at
60˚C or more), atmospheric pressure
(atmospheric pressure sensor: altitude
compensation) are used as auxiliary map values.
EGR pipe
Transports the exhaust gas from the EGR cooler
and EGR bypass valve to the intake duct.
E-EGR cooler and bypass valve
The cooler lowers the high temperature of the
exhaust gas and the bypass valve directly
supplies the exhaust gas to the intake duct
without passing through the EGR cooler to
reduce the emission of exhaust gas before
warming up the engine.
E-EGR valve
Receives the electric signal from the ECU to
control the valve.
EGR cooler
EGR bypass
Page 265 of 1082
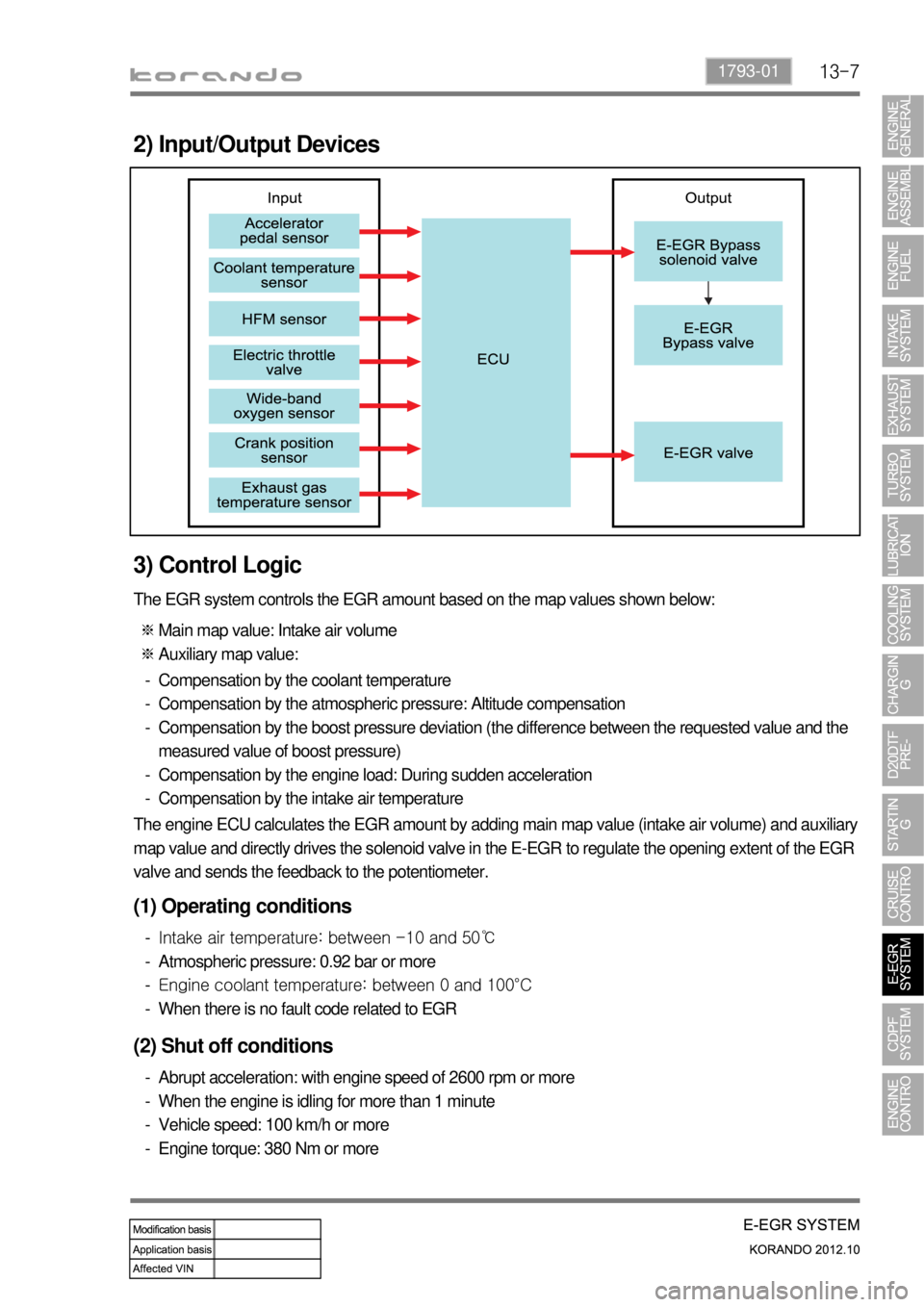
13-71793-01
2) Input/Output Devices
3) Control Logic
The EGR system controls the EGR amount based on the map values shown below:
Main map value: Intake air volume
Auxiliary map value: ※
※
Compensation by the coolant temperature
Compensation by the atmospheric pressure: Altitude compensation
Compensation by the boost pressure deviation (the difference between the requested value and the
measured value of boost pressure)
Compensation by the engine load: During sudden acceleration
Compensation by the intake air temperature -
-
-
-
-
The engine ECU calculates the EGR amount by adding main map value (intake air volume) and auxiliary
map value and directly drives the solenoid valve in the E-EGR to regulate the opening extent of the EGR
valve and sends the feedback to the potentiometer.
(1) Operating conditions
Intake air temperature: between -10 and 50℃
Atmospheric pressure: 0.92 bar or more
Engine coolant temperature: between 0 and 100°C
When there is no fault code related to EGR -
-
-
-
(2) Shut off conditions
Abrupt acceleration: with engine speed of 2600 rpm or more
When the engine is idling for more than 1 minute
Vehicle speed: 100 km/h or more
Engine torque: 380 Nm or more -
-
-
-
Page 279 of 1082
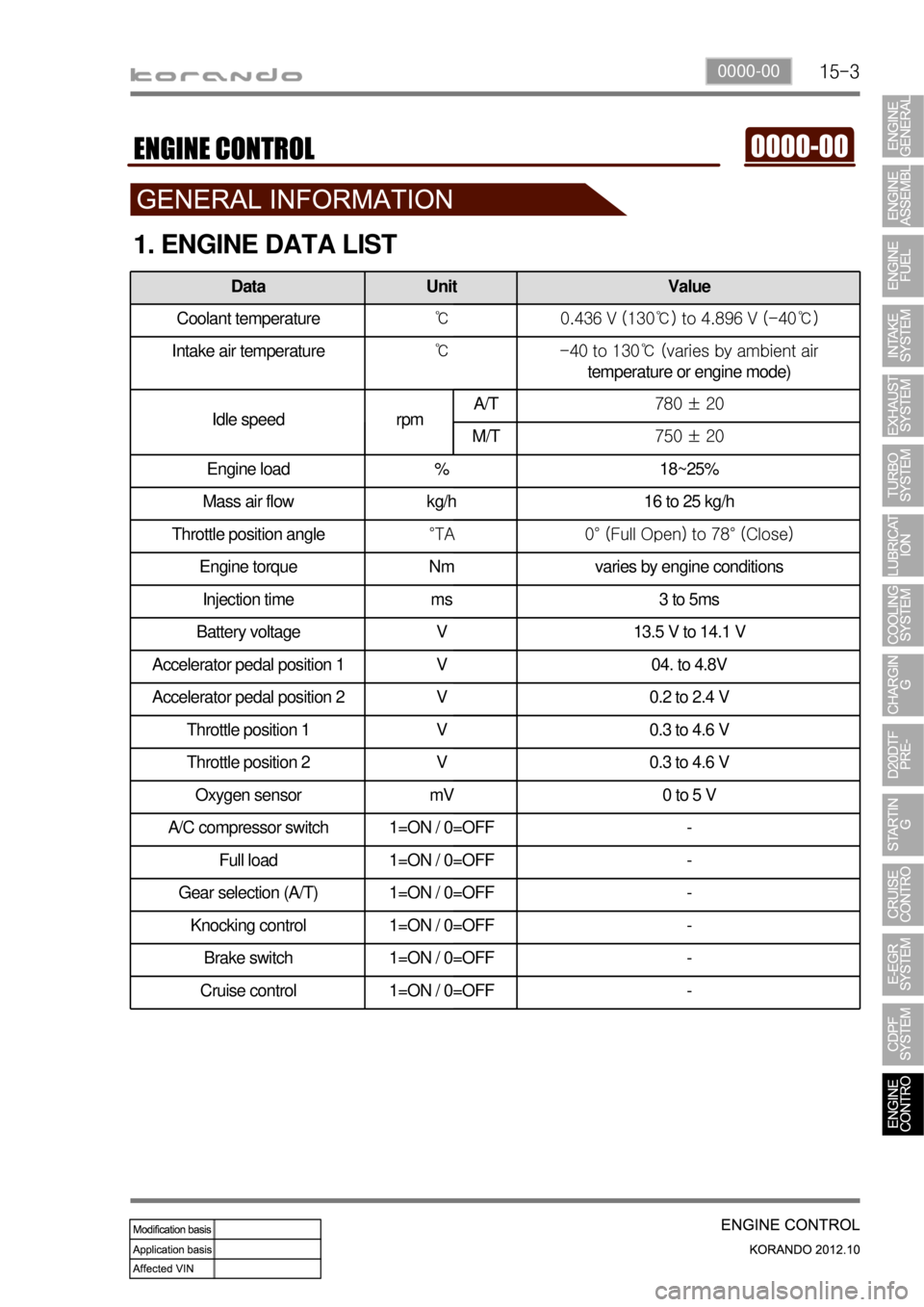
15-30000-00
1. ENGINE DATA LIST
Data Unit Value
Coolant temperature℃ 0.436 V (130℃) to 4.896 V (-40℃)
Intake air temperature℃ -40 to 130℃ (varies by ambient air
temperature or engine mode)
Idle speed rpmA/T780 ± 20
M/T750 ± 20
Engine load % 18~25%
Mass air flow kg/h 16 to 25 kg/h
Throttle position angle°TA 0° (Full Open) to 78° (Close)
Engine torque Nm varies by engine conditions
Injection time ms 3 to 5ms
Battery voltage V 13.5 V to 14.1 V
Accelerator pedal position 1 V 04. to 4.8V
Accelerator pedal position 2 V 0.2 to 2.4 V
Throttle position 1 V 0.3 to 4.6 V
Throttle position 2 V 0.3 to 4.6 V
Oxygen sensor mV 0 to 5 V
A/C compressor switch 1=ON / 0=OFF -
Full load 1=ON / 0=OFF -
Gear selection (A/T) 1=ON / 0=OFF -
Knocking control 1=ON / 0=OFF -
Brake switch 1=ON / 0=OFF -
Cruise control 1=ON / 0=OFF -
Page 281 of 1082
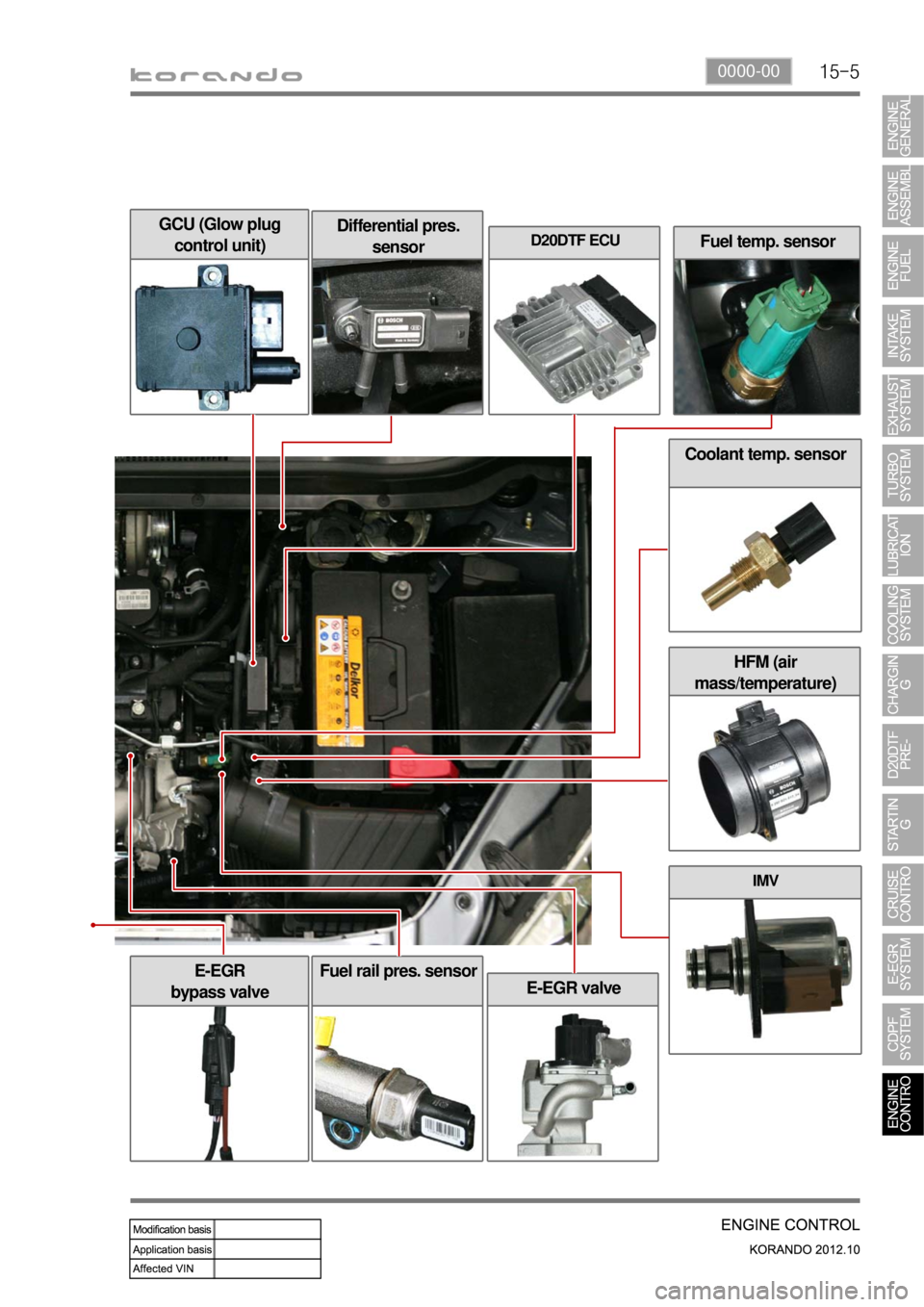
15-50000-00
HFM (air
mass/temperature)
Fuel temp. sensor
GCU (Glow plug
control unit)Differential pres.
sensorD20DTF ECU
Coolant temp. sensor
IMV
E-EGR
bypass valve
E-EGR valve
Fuel rail pres. sensor
Page 286 of 1082
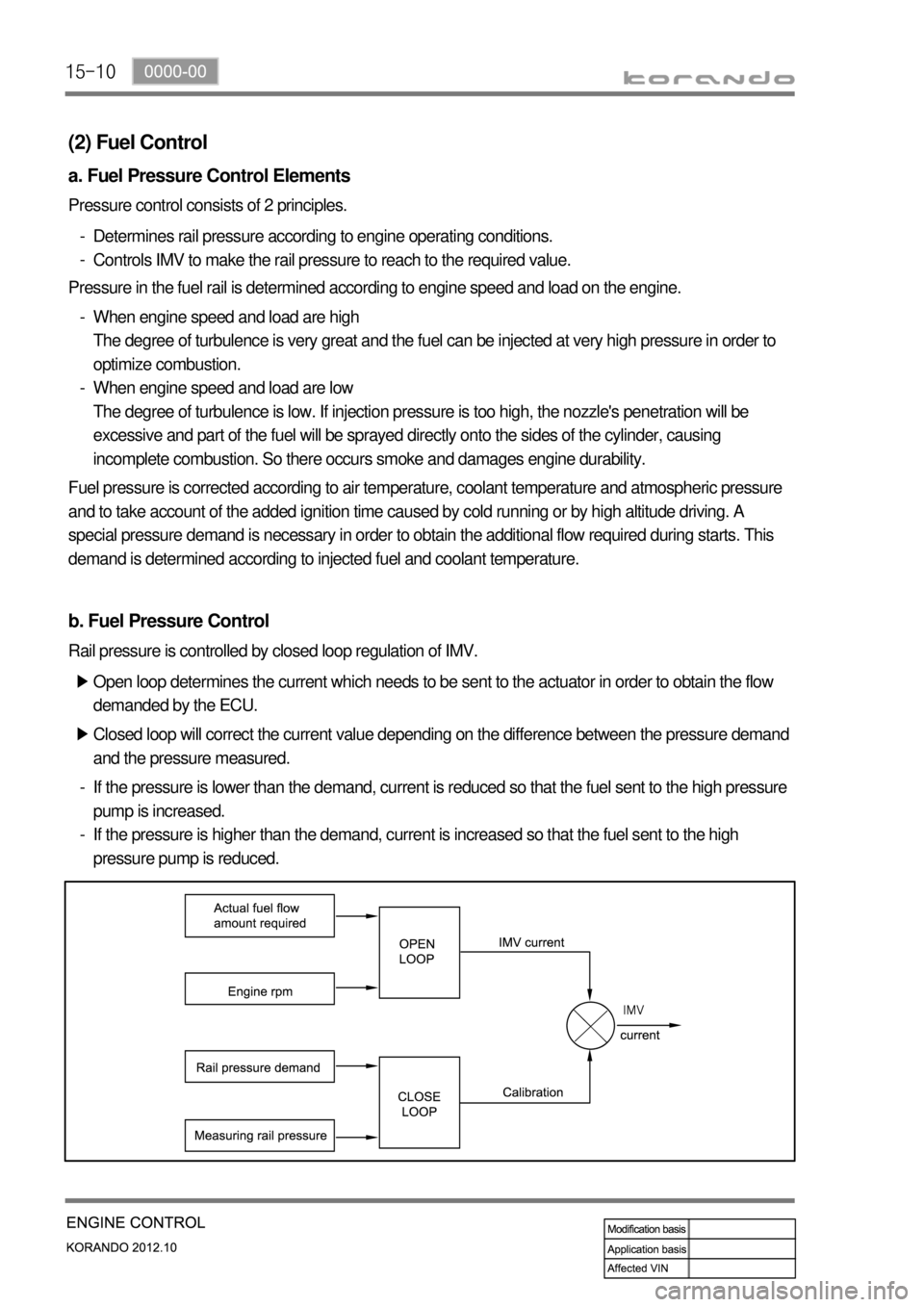
15-10
(2) Fuel Control
a. Fuel Pressure Control Elements
Pressure control consists of 2 principles.
Determines rail pressure according to engine operating conditions.
Controls IMV to make the rail pressure to reach to the required value. -
-
Pressure in the fuel rail is determined according to engine speed and load on the engine.
When engine speed and load are high
The degree of turbulence is very great and the fuel can be injected at very high pressure in order to
optimize combustion.
When engine speed and load are low
The degree of turbulence is low. If injection pressure is too high, the nozzle's penetration will be
excessive and part of the fuel will be sprayed directly onto the sides of the cylinder, causing
incomplete combustion. So there occurs smoke and damages engine durability. -
-
Fuel pressure is corrected according to air temperature, coolant temperature and atmospheric pressure
and to take account of the added ignition time caused by cold running or by high altitude driving. A
special pressure demand is necessary in order to obtain the additional flow required during starts. This
demand is determined according to injected fuel and coolant temperature.
b. Fuel Pressure Control
Open loop determines the current which needs to be sent to the actuator in order to obtain the flow
demanded by the ECU. ▶
Closed loop will correct the current value depending on the difference between the pressure demand
and the pressure measured. ▶
If the pressure is lower than the demand, current is reduced so that the fuel sent to the high pressure
pump is increased.
If the pressure is higher than the demand, current is increased so that the fuel sent to the high
pressure pump is reduced. -
-
Rail pressure is controlled by closed loop regulation of IMV.
Page 287 of 1082
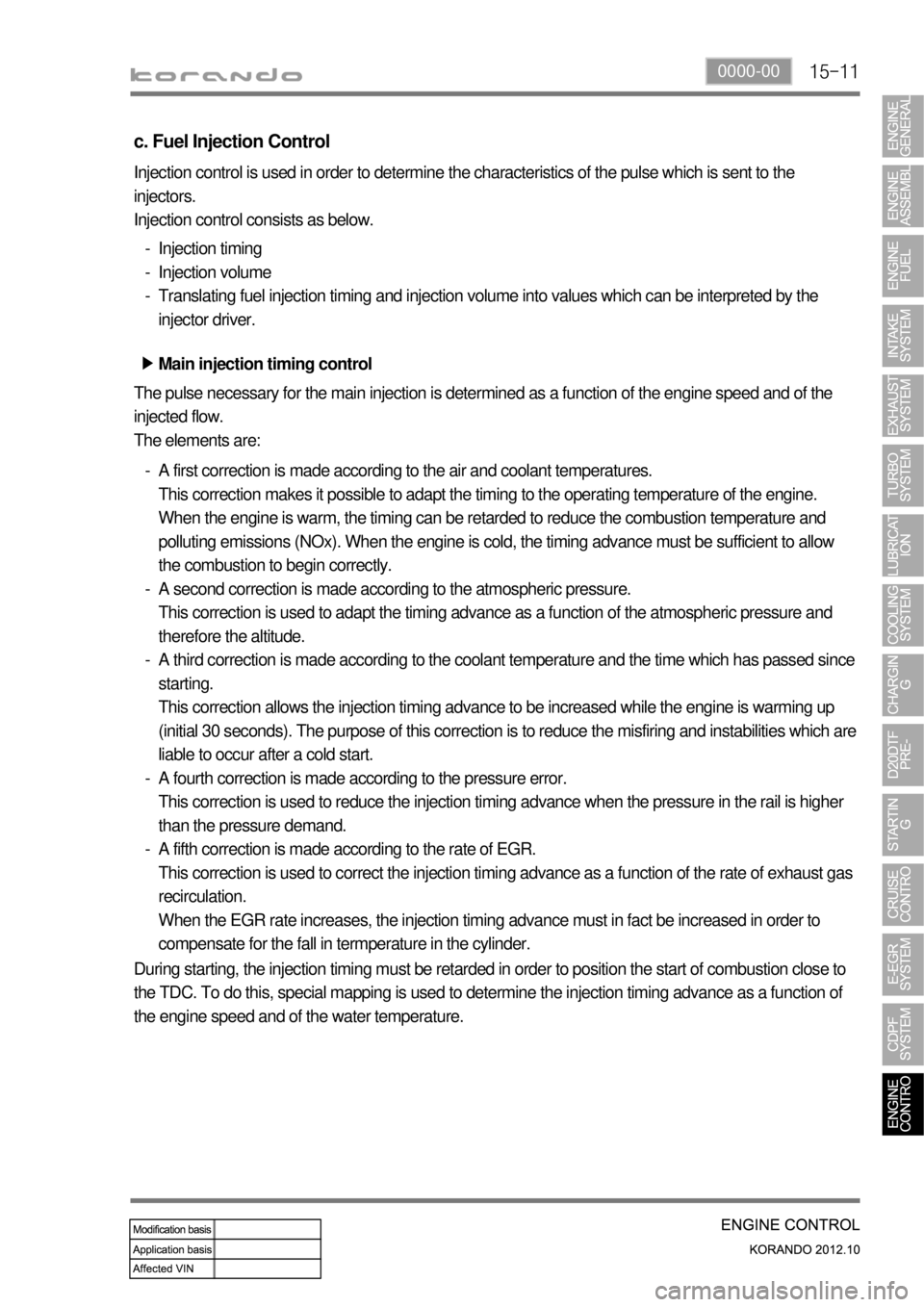
15-110000-00
c. Fuel Injection Control
Injection control is used in order to determine the characteristics of the pulse which is sent to the
injectors.
Injection control consists as below.
Injection timing
Injection volume
Translating fuel injection timing and injection volume into values which can be interpreted by the
injector driver. -
-
-
Main injection timing control ▶
The pulse necessary for the main injection is determined as a function of the engine speed and of the
injected flow.
The elements are:
A first correction is made according to the air and coolant temperatures.
This correction makes it possible to adapt the timing to the operating temperature of the engine.
When the engine is warm, the timing can be retarded to reduce the combustion temperature and
polluting emissions (NOx). When the engine is cold, the timing advance must be sufficient to allow
the combustion to begin correctly.
A second correction is made according to the atmospheric pressure.
This correction is used to adapt the timing advance as a function of the atmospheric pressure and
therefore the altitude.
A third correction is made according to the coolant temperature and the time which has passed since
starting.
This correction allows the injection timing advance to be increased while the engine is warming up
(initial 30 seconds). The purpose of this correction is to reduce the misfiring and instabilities which are
liable to occur after a cold start.
A fourth correction is made according to the pressure error.
This correction is used to reduce the injection timing advance when the pressure in the rail is higher
than the pressure demand.
A fifth correction is made according to the rate of EGR.
This correction is used to correct the injection timing advance as a function of the rate of exhaust gas
recirculation.
When the EGR rate increases, the injection timing advance must in fact be increased in order to
compensate for the fall in termperature in the cylinder. -
-
-
-
-
During starting, the injection timing must be retarded in order to position the start of combustion close to
the TDC. To do this, special mapping is used to determine the injection timing advance as a function of
the engine speed and of the water temperature.
Page 288 of 1082
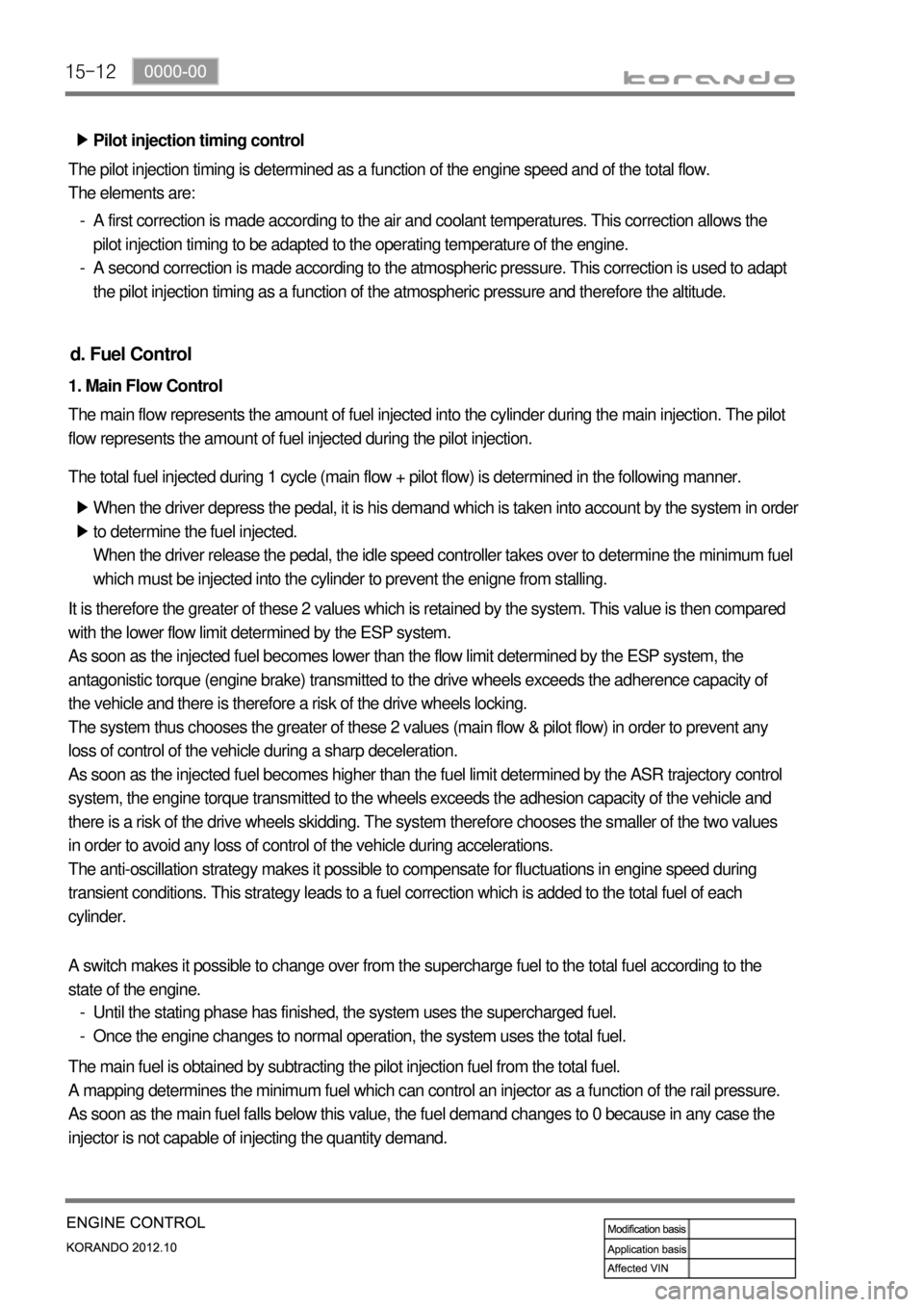
15-12
Pilot injection timing control ▶
The pilot injection timing is determined as a function of the engine speed and of the total flow.
The elements are:
A first correction is made according to the air and coolant temperatures. This correction allows the
pilot injection timing to be adapted to the operating temperature of the engine.
A second correction is made according to the atmospheric pressure. This correction is used to adapt
the pilot injection timing as a function of the atmospheric pressure and therefore the altitude. -
-
d. Fuel Control
1. Main Flow Control
The main flow represents the amount of fuel injected into the cylinder during the main injection. The pilot
flow represents the amount of fuel injected during the pilot injection.
The total fuel injected during 1 cycle (main flow + pilot flow) is determined in the following manner.
When the driver depress the pedal, it is his demand which is taken into account by the system in order
to determine the fuel injected.
When the driver release the pedal, the idle speed controller takes over to determine the minimum fuel
which must be injected into the cylinder to prevent the enigne from stalling. ▶
▶
It is therefore the greater of these 2 values which is retained by the system. This value is then compared
with the lower flow limit determined by the ESP system.
As soon as the injected fuel becomes lower than the flow limit determined by the ESP system, the
antagonistic torque (engine brake) transmitted to the drive wheels exceeds the adherence capacity of
the vehicle and there is therefore a risk of the drive wheels locking.
The system thus chooses the greater of these 2 values (main flow & pilot flow) in order to prevent any
loss of control of the vehicle during a sharp deceleration.
As soon as the injected fuel becomes higher than the fuel limit determined by the ASR trajectory control
system, the engine torque transmitted to the wheels exceeds the adhesion capacity of the vehicle and
there is a risk of the drive wheels skidding. The system therefore chooses the smaller of the two values
in order to avoid any loss of control of the vehicle during accelerations.
The anti-oscillation strategy makes it possible to compensate for fluctuations in engine speed during
transient conditions. This strategy leads to a fuel correction which is added to the total fuel of each
cylinder.
The main fuel is obtained by subtracting the pilot injection fuel from the total fuel.
A mapping determines the minimum fuel which can control an injector as a function of the rail pressure.
As soon as the main fuel falls below this value, the fuel demand changes to 0 because in any case the
injector is not capable of injecting the quantity demand. A switch makes it possible to change over from the supercharge fuel to the total fuel according to the
state of the engine.
Until the stating phase has finished, the system uses the supercharged fuel.
Once the engine changes to normal operation, the system uses the total fuel. -
-
Page 289 of 1082
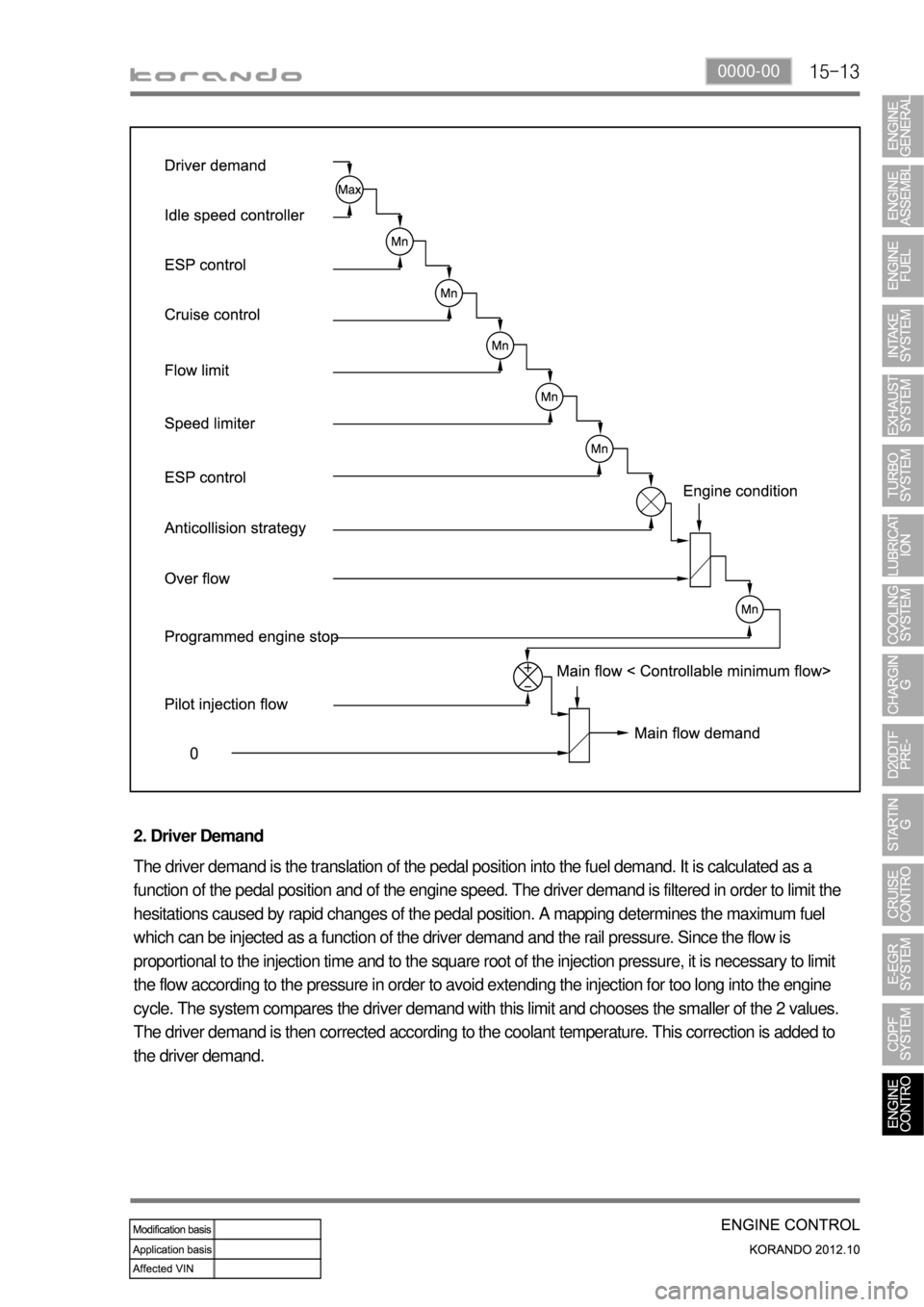
15-130000-00
2. Driver Demand
The driver demand is the translation of the pedal position into the fuel demand. It is calculated as a
function of the pedal position and of the engine speed. The driver demand is filtered in order to limit the
hesitations caused by rapid changes of the pedal position. A mapping determines the maximum fuel
which can be injected as a function of the driver demand and the rail pressure. Since the flow is
proportional to the injection time and to the square root of the injection pressure, it is necessary to limit
the flow according to the pressure in order to avoid extending the injection for too long into the engine
cycle. The system compares the driver demand with this limit and chooses the smaller of the 2 values.
The driver demand is then corrected according to the coolant temperature. This correction is added to
the driver demand.